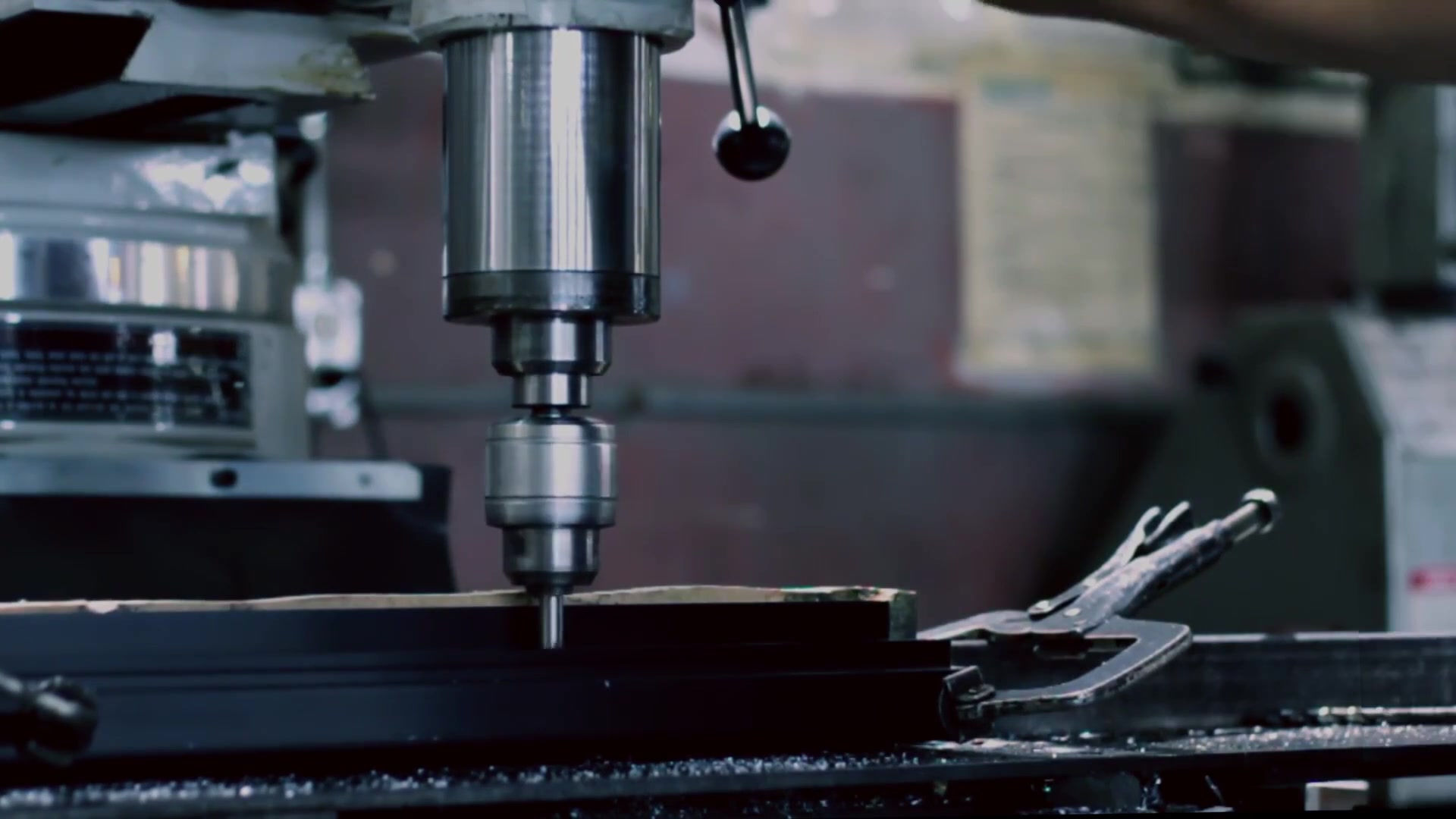
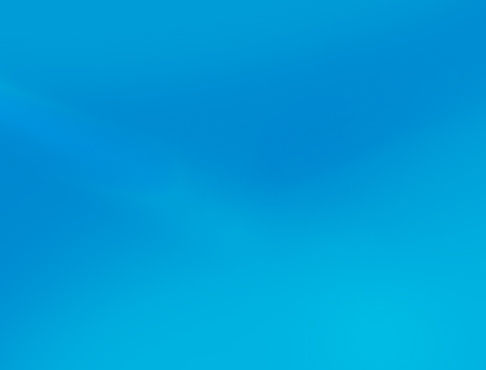
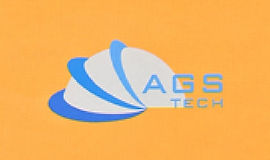
Globálny vlastný výrobca, integrátor, konsolidátor, partner outsourcingu pre širokú škálu produktov a služieb.
Sme váš komplexný zdroj pre výrobu, výrobu, inžinierstvo, konsolidáciu, integráciu, outsourcing zákazkovo vyrábaných a voľne predajných produktov a služieb.
Vyberte si jazyk
-
Zákazková výroba
-
Domáca a globálna zmluvná výroba
-
Outsourcing výroby
-
Domáce a globálne obstarávanie
-
Konsolidácia
-
Engineering Integration
-
Inžinierske služby
Search Results
164 results found with an empty search
- Micromanufacturing, Nanomanufacturing, Mesomanufacturing AGS-TECH Inc.
Micromanufacturing, Nanomanufacturing, Mesomanufacturing - Electronic & Magnetic Optical & Coatings, Thin Film, Nanotubes, MEMS, Microscale Fabrication Výroba v nanorozmeroch a v mikrorozsahoch a v mezomeradlách Čítaj viac Our NANOMANUFACTURING, MICROMANUFACTURING and MESOMANUFACTURING processes can be categorized as: Povrchové úpravy a úpravy Funkčné nátery / Dekoratívne nátery / Tenký film / Hrubý film Výroba v nanorozmeroch / Nanomanufacturing Microscale Manufacturing / Micromanufacturing / Mikroobrábanie Mesoscale Manufacturing / Mesomanufacturing Mikroelektronika & Semiconductor Manufacturing a Výroba Microfluidic Devices Manufacturing Výroba mikrooptiky Mikromontáž a balenie Mäkká litografia V každom dnes navrhnutom inteligentnom produkte možno uvažovať o prvku, ktorý zvýši účinnosť, všestrannosť, zníži spotrebu energie, zníži odpad, predĺži životnosť produktu a bude tak šetrný k životnému prostrediu. Na tento účel sa AGS-TECH zameriava na množstvo procesov a produktov, ktoré možno začleniť do zariadení a zariadení na dosiahnutie týchto cieľov. Napríklad low-friction FUNCTIONAL COATINGS môže znížiť spotrebu energie. Niektoré ďalšie príklady funkčných povlakov sú povlaky odolné proti poškriabaniu, anti-wetting SURFACE TREATMENTS and povlaky, hydrofóbne povrchové úpravy a povlaky podporujúce zmáčanie (hydrofóbna úprava) diamantové uhlíkové povlaky pre rezné a ryhovacie nástroje, THIN FILMeelektronické povlaky, tenkovrstvové magnetické povlaky, viacvrstvové optické povlaky. In NANOMANUFACTURING or_cc781905-5cde-311905-5cde-311905-5cde-311905-5cf58d_NANOMANUFACTURING or_cc781905-5cde-311905-5cde-311905-5cde-3194-fSCbad5NUc dĺžka dielov webbnuc V praxi sa to týka výrobných operácií pod mikrometrovou mierkou. Nanovýroba je v porovnaní s mikrovýrobou stále v plienkach, trend je však týmto smerom a nanovýroba je určite veľmi dôležitá pre blízku budúcnosť. Niektoré aplikácie nanovýroby sú dnes uhlíkové nanorúrky ako výstužné vlákna pre kompozitné materiály v rámoch bicyklov, bejzbalových pálkách a tenisových raketách. Uhlíkové nanorúrky v závislosti od orientácie grafitu v nanorúrke môžu pôsobiť ako polovodiče alebo vodiče. Uhlíkové nanorúrky majú veľmi vysokú schopnosť prenášať prúd, 1000-krát vyššiu ako striebro alebo meď. Ďalšou aplikáciou nanovýroby je nanofázová keramika. Použitím nanočastíc pri výrobe keramických materiálov môžeme súčasne zvýšiť pevnosť aj ťažnosť keramiky. Pre viac informácií kliknite na podponuku. MICROSCALE MANUFACTURING or MICROMANUFACTURING_cc781935-5c productions to the microSCALE WATERING on the microSCALE MANUFACTURING to the microSCALE MANUFACTURING or MICROMANUFACTURING_cc781935b-5de viditeľné on-cc781931b-5de viditeľné on-cc781931b-5de Pojmy mikrovýroba, mikroelektronika, mikroelektromechanické systémy nie sú obmedzené na takéto malé dĺžkové merítka, ale namiesto toho naznačujú materiál a výrobnú stratégiu. V našich mikrovýrobných operáciách niektoré populárne techniky, ktoré používame, sú litografia, mokré a suché leptanie, nanášanie tenkým filmom. Široká škála senzorov a ovládačov, sond, hláv s magnetickým pevným diskom, mikroelektronických čipov, zariadení MEMS, ako sú akcelerometre a tlakové senzory, sa okrem iného vyrába pomocou takýchto mikrovýrobných metód. Podrobnejšie informácie o nich nájdete v podponukách. MESOSCALE MANUFACTURING or MESOMANUFACTURING refers to our processes for fabrication of miniature devices such as hearing aids, medical stents, medical valves, mechanical watches and extremely small motory. Mesoscale výroba prekrýva makro aj mikrovýrobu. Miniatúrne sústruhy s 1,5 wattovým motorom a rozmermi 32 x 25 x 30,5 mm a hmotnosťou 100 gramov boli vyrobené s použitím mesoscale výrobných metód. Pomocou takýchto sústruhov bola mosadz obrobená na priemer tak malý ako 60 mikrónov a drsnosť povrchu rádovo v mikrónoch alebo dvoch. Iné takéto miniatúrne obrábacie stroje, ako sú frézky a lisy, sa tiež vyrábali pomocou mezomanufaktúry. In MICROELECTRONICS MANUFACTURING používame rovnaké techniky ako pri mikrovýrobe. Našimi najobľúbenejšími substrátmi sú kremík a používajú sa aj iné ako arzenid gália, fosfid india a germánium. Filmy/povlaky mnohých typov a najmä vodivé a izolačné tenkovrstvové povlaky sa používajú pri výrobe mikroelektronických zariadení a obvodov. Tieto zariadenia sa zvyčajne získavajú z viacerých vrstiev. Izolačné vrstvy sa vo všeobecnosti získavajú oxidáciou, ako je Si02. Dopanty (oba typy p a n) sú bežné a časti zariadení sú dopované, aby sa zmenili ich elektronické vlastnosti a získali sa oblasti typu p a n. Pomocou litografie, ako je ultrafialová, hlboká alebo extrémna ultrafialová fotolitografia alebo röntgenová litografia s elektrónovým lúčom, prenášame geometrické vzory definujúce zariadenia z fotomasky/masky na povrchy substrátu. Tieto litografické procesy sa niekoľkokrát aplikujú pri mikrovýrobe mikroelektronických čipov, aby sa dosiahli požadované štruktúry v dizajne. Vykonávajú sa aj procesy leptania, pri ktorých sa odstraňujú celé filmy alebo jednotlivé časti filmov alebo substrátu. Stručne povedané, pomocou rôznych krokov depozície, leptania a viacerých litografických krokov získame viacvrstvové štruktúry na nosných polovodičových substrátoch. Po spracovaní doštičiek a mikrovyrobení mnohých obvodov sa opakujúce časti vyrežú a získajú sa jednotlivé matrice. Každá matrica je potom zlepená drôtom, zabalená a testovaná a stáva sa komerčným mikroelektronickým produktom. Niektoré ďalšie podrobnosti o výrobe mikroelektroniky nájdete v našom podmenu, avšak téma je veľmi rozsiahla, a preto vás odporúčame, aby ste nás kontaktovali v prípade, že potrebujete špecifické informácie o produkte alebo ďalšie podrobnosti. Naše MICROFLUIDICS MANUFACTURING operations sú zamerané na výrobu zariadení a systémov, v ktorých sú malé objemy tekutín. Príkladmi mikrofluidných zariadení sú mikropohonné zariadenia, laboratórne systémy na čipe, mikrotepelné zariadenia, atramentové tlačové hlavy a ďalšie. V mikrofluidike sa musíme zaoberať presnou kontrolou a manipuláciou s tekutinami obmedzenými na submilimetrové oblasti. Kvapaliny sa presúvajú, miešajú, separujú a spracovávajú. V mikrofluidných systémoch sa tekutiny pohybujú a riadia buď aktívne pomocou malých mikropúmp a mikroventilov a podobne, alebo pasívne využívajúc výhody kapilárnych síl. Pri systémoch lab-on-a-chip sú procesy, ktoré sa bežne vykonávajú v laboratóriu, miniaturizované na jedinom čipe, aby sa zvýšila účinnosť a mobilita, ako aj znížili objemy vzoriek a činidiel. Máme schopnosť navrhnúť pre vás mikrofluidné zariadenia a ponúknuť prototypovanie mikrofluidík a mikrovýrobu na mieru pre vaše aplikácie. Ďalšou perspektívnou oblasťou mikrovýroby je MIKRO-OPTICS MANUFACTURING. Mikrooptika umožňuje manipuláciu so svetlom a riadenie fotónov s mikrónovými a submikrónovými štruktúrami a komponentmi. Mikrooptika nám umožňuje prepojiť makroskopický svet, v ktorom žijeme, s mikroskopickým svetom opto- a nano-elektronického spracovania údajov. Mikrooptické komponenty a subsystémy nachádzajú široké uplatnenie v nasledujúcich oblastiach: Informačné technológie: V mikrodispleji, mikroprojektoroch, optických dátových úložiskách, mikrokamerách, skeneroch, tlačiarňach, kopírkach atď. Biomedicína: Minimálne invazívna/bodová diagnostika, monitorovanie liečby, mikrozobrazovacie senzory, retinálne implantáty. Osvetlenie: Systémy založené na LED diódach a iných efektívnych svetelných zdrojoch Bezpečnostné a zabezpečovacie systémy: Infračervené systémy nočného videnia pre automobilové aplikácie, optické snímače odtlačkov prstov, skenery sietnice. Optická komunikácia a telekomunikácia: Vo fotonických prepínačoch, pasívnych optických komponentoch, optických zosilňovačoch, prepojovacích systémoch sálových počítačov a osobných počítačov Inteligentné štruktúry: V snímacích systémoch na báze optických vlákien a oveľa viac Ako najrozmanitejší poskytovateľ inžinierskej integrácie sme hrdí na našu schopnosť poskytnúť riešenie pre takmer všetky potreby v oblasti poradenstva, inžinierstva, reverzného inžinierstva, rýchleho prototypovania, vývoja produktov, výroby, výroby a montáže. Po mikrovýrobe našich komponentov veľmi často musíme pokračovať s MICRO MONTÁŽ A BALENIE. To zahŕňa procesy, ako je pripevnenie matrice, spájanie drôtov, konektorovanie, hermetické utesnenie balíkov, sondovanie, testovanie zabalených produktov z hľadiska environmentálnej spoľahlivosti... atď. Po mikrovýrobe zariadení na matrici pripevníme matricu k odolnejšiemu základu, aby sme zaistili spoľahlivosť. Na spojenie matrice s jej obalom často používame špeciálne epoxidové cementy alebo eutektické zliatiny. Po pripojení čipu alebo matrice k substrátu ich elektricky pripojíme k vývodom obalu pomocou drôteného spojenia. Jednou z metód je použitie veľmi tenkých zlatých drôtikov z balíčka k spojovacím podložkám umiestneným po obvode matrice. Nakoniec musíme urobiť konečné balenie pripojeného obvodu. V závislosti od aplikácie a operačného prostredia je k dispozícii množstvo štandardných a zákazkovo vyrábaných balení pre mikrovyrobené elektronické, elektrooptické a mikroelektromechanické zariadenia. Ďalšou mikrovýrobnou technikou, ktorú používame, je SOFT LITHOGRAPHY, termín používaný pre množstvo procesov na prenos vzorov. Vo všetkých prípadoch je potrebná hlavná forma a je mikrovyrobená pomocou štandardných litografických metód. Pomocou hlavnej formy vyrobíme elastomérny vzor / pečiatku. Jednou z variácií mäkkej litografie je „mikrokontaktná tlač“. Elastomérová pečiatka je potiahnutá atramentom a pritlačená k povrchu. Vrcholy vzoru sa dotýkajú povrchu a prenesie sa tenká vrstva približne 1 monovrstvy atramentu. Táto tenká monovrstva pôsobí ako maska na selektívne mokré leptanie. Druhým variantom je „mikrotransferové tvarovanie“, pri ktorom sú vybrania elastomérovej formy vyplnené kvapalným polymérnym prekurzorom a pritlačené k povrchu. Akonáhle polymér vytvrdne, odlepíme formu a zanecháme požadovaný vzor. Napokon treťou variáciou je „mikrotvarovanie v kapilárach“, kde vzor elastomérového razidla pozostáva z kanálikov, ktoré využívajú kapilárne sily na nasávanie tekutého polyméru do razidla z jeho strany. V zásade je malé množstvo kvapalného polyméru umiestnené vedľa kapilárnych kanálikov a kapilárne sily vťahujú kvapalinu do kanálikov. Prebytočný kvapalný polymér sa odstráni a polymér vo vnútri kanálikov sa nechá vytvrdnúť. Forma na pečiatku sa odlepí a výrobok je pripravený. Viac podrobností o našich mikrovýrobných technikách mäkkej litografie nájdete po kliknutí na súvisiace podmenu na bočnej strane tejto stránky. Ak vás namiesto výrobných kapacít väčšinou zaujímajú naše inžinierske a výskumné a vývojové schopnosti, potom vás pozývame navštíviť aj našu webovú stránku inžinierstva http://www.ags-engineering.com Čítaj viac Čítaj viac Čítaj viac Čítaj viac Čítaj viac Čítaj viac Čítaj viac Čítaj viac Čítaj viac CLICK Product Finder-Locator Service PREDCHÁDZAJÚCA STRANA
- Functional Decorative Coatings - Thin Film - Thick Films - AR Coating
Functional & Decorative Coatings, Thin Film, Thick Films, Antireflective and Reflective Mirror Coating - AGS-TECH Inc. Funkčné nátery / dekoratívne nátery / tenký film / hrubý film A COATING je krytina, ktorá sa nanáša na povrch predmetu. Coatings can be in the form of THIN FILM (less than 1 micron thick) or THICK FILM ( s hrúbkou nad 1 mikrón). Na základe účelu nanášania náteru vám môžeme ponúknuť DECORATIVE COATINGS and/or_bbc5193bad_a/or-5cc513d_Abbc-5190 Niekedy nanášame funkčné nátery, aby sme zmenili povrchové vlastnosti podkladu, ako je priľnavosť, zmáčavosť, odolnosť proti korózii alebo opotrebeniu. V niektorých iných prípadoch, ako napríklad pri výrobe polovodičových zariadení, aplikujeme funkčné povlaky, aby sme pridali úplne novú vlastnosť, ako je magnetizácia alebo elektrická vodivosť, ktoré sa stávajú nevyhnutnou súčasťou hotového výrobku. Naše najobľúbenejšie FUNCTIONAL COATINGS are: Lepiace nátery: Príkladmi sú lepiaca páska, nažehľovacia tkanina. Na zmenu adhéznych vlastností sa aplikujú ďalšie funkčné adhézne nátery, ako sú nepriľnavé panvice na varenie s PTFE, základné nátery, ktoré podporujú dobré priľnutie následných náterov. Tribologické povlaky: Tieto funkčné povlaky sa týkajú princípov trenia, mazania a opotrebovania. Akýkoľvek produkt, kde sa jeden materiál kĺže alebo trie po druhom, je ovplyvnený komplexnými tribologickými interakciami. Produkty, ako sú bedrové implantáty a iné umelé protézy, sú určitým spôsobom mazané, zatiaľ čo iné produkty sú nemazané, ako napríklad pri vysokoteplotných klzných komponentoch, kde nemožno použiť konvenčné mazivá. Ukázalo sa, že vytváranie zhutnených oxidových vrstiev chráni pred opotrebovaním takýchto posuvných mechanických častí. Tribologické funkčné povlaky majú obrovské výhody v priemysle, minimalizujú opotrebovanie strojných prvkov, minimalizujú opotrebenie a odchýlky tolerancií vo výrobných nástrojoch, ako sú matrice a formy, minimalizujú požiadavky na energiu a zvyšujú energetickú účinnosť strojov a zariadení. Optické nátery: Príkladmi sú antireflexné (AR) nátery, reflexné nátery na zrkadlá, nátery absorbujúce UV žiarenie na ochranu očí alebo na predĺženie životnosti podkladu, tónovanie používané pri niektorých farebných osvetleniach, tónované sklá a slnečné okuliare. Catalytic Coatings ako sú aplikované na samočistiace sklo. Nátery citlivé na svetlo používané na výrobu produktov, ako sú fotografické filmy Ochranné nátery: Farby možno považovať za ochranu výrobkov okrem toho, že majú dekoratívny účel. Tvrdé povlaky proti poškriabaniu na plastoch a iných materiáloch sú jedným z našich najpoužívanejších funkčných povlakov na zníženie poškriabania, zlepšenie odolnosti proti opotrebovaniu atď. Veľmi obľúbené sú aj antikorózne nátery ako pokovovanie. Ďalšie ochranné funkčné nátery sa nanášajú na vodeodolnú tkaninu a papier, antimikrobiálne povrchové nátery na chirurgické nástroje a implantáty. Hydrofilné / hydrofóbne nátery: Zmáčavé (hydrofilné) a nezmáčavé (hydrofóbne) funkčné tenké a hrubé filmy sú dôležité v aplikáciách, kde je absorpcia vody buď žiaduca alebo nežiaduca. Pomocou pokročilej technológie dokážeme upraviť povrchy vašich produktov tak, aby boli ľahko zmáčateľné alebo nezmáčateľné. Typické aplikácie sú v textíliách, obväzoch, kožených topánkach, farmaceutických alebo chirurgických výrobkoch. Hydrofilná povaha označuje fyzikálnu vlastnosť molekuly, ktorá sa môže prechodne viazať s vodou (H2O) prostredníctvom vodíkových väzieb. To je termodynamicky priaznivé a tieto molekuly sú rozpustné nielen vo vode, ale aj v iných polárnych rozpúšťadlách. Hydrofilné a hydrofóbne molekuly sú tiež známe ako polárne molekuly a nepolárne molekuly. Magnetické povlaky: Tieto funkčné povlaky pridávajú magnetické vlastnosti, ako je to v prípade magnetických diskiet, kaziet, magnetických prúžkov, magnetooptických úložísk, indukčných záznamových médií, magnetorezistentných senzorov a tenkovrstvových hláv na produktoch. Magnetické tenké vrstvy sú listy magnetického materiálu s hrúbkou niekoľkých mikrometrov alebo menej, používané predovšetkým v elektronickom priemysle. Magnetické tenké vrstvy môžu byť jednokryštalické, polykryštalické, amorfné alebo viacvrstvové funkčné povlaky v usporiadaní ich atómov. Používajú sa fero- aj ferimagnetické fólie. Feromagnetické funkčné povlaky sú zvyčajne zliatiny na báze prechodných kovov. Napríklad permalloy je zliatina niklu a železa. Ferimagnetické funkčné povlaky, ako sú granáty alebo amorfné filmy, obsahujú prechodné kovy ako železo alebo kobalt a vzácne zeminy a ferimagnetické vlastnosti sú výhodné v magnetooptických aplikáciách, kde je možné dosiahnuť nízky celkový magnetický moment bez výraznej zmeny Curieovej teploty. . Niektoré senzorové prvky fungujú na princípe zmeny elektrických vlastností, ako je elektrický odpor, s magnetickým poľom. V polovodičovej technológii funguje magnetorezistentná hlava používaná v technológii diskových pamätí na tomto princípe. Veľmi veľké magnetorezistentné signály (obrovská magnetorezistencia) sú pozorované v magnetických viacvrstvách a kompozitoch obsahujúcich magnetický a nemagnetický materiál. Elektrické alebo elektronické povlaky: Tieto funkčné povlaky pridávajú elektrické alebo elektronické vlastnosti, ako je vodivosť, pri výrobe produktov, ako sú odpory, izolačné vlastnosti, ako v prípade povlakov magnetických drôtov používaných v transformátoroch. DEKORATÍVNE NÁTERY: Keď hovoríme o dekoratívnych náteroch, možnosti sú obmedzené len vašou predstavivosťou. Nátery typu hrubého aj tenkého filmu boli úspešne skonštruované a aplikované v minulosti na produkty našich zákazníkov. Bez ohľadu na náročnosť geometrického tvaru a materiálu podkladu a aplikačných podmienok sme vždy schopní formulovať chémiu, fyzikálne aspekty, ako je presný Pantone kód farby a spôsob aplikácie pre vami požadované dekoratívne nátery. Možné sú aj zložité vzory zahŕňajúce tvary alebo rôzne farby. Vaše plastové polymérové diely môžeme vyrobiť ako kovové. Eloxované výlisky môžeme farbiť rôznymi vzormi a nebude to ani vyzerať ako elox. Časti zvláštneho tvaru môžeme zrkadlovo potiahnuť. Ďalej môžu byť formulované dekoratívne nátery, ktoré budú súčasne pôsobiť aj ako funkčné nátery. Na dekoratívne povlaky možno použiť ktorúkoľvek z nižšie uvedených techník nanášania tenkých a hrubých vrstiev používaných pre funkčné povlaky. Tu sú niektoré z našich obľúbených dekoratívnych náterov: - PVD tenkovrstvové dekoratívne nátery - Galvanizované dekoratívne nátery - Tenkovrstvové dekoratívne povlaky CVD a PECVD - Dekoratívne nátery s tepelným odparovaním - Roll-to-Roll dekoratívny náter - E-Beam Oxide Interference Coatings - Iónové pokovovanie - Katodické oblúkové odparovanie pre dekoratívne nátery - PVD + fotolitografia, ťažké pozlátenie na PVD - Aerosólové nátery na farbenie skla - Ochranný náter - Dekoratívne systémy meď-nikel-chróm - Dekoratívne práškové lakovanie - Dekoratívne maľovanie, formulácie farieb na mieru s použitím pigmentov, plnív, koloidného oxidu kremičitého... atď. Ak sa na nás obrátite so svojimi požiadavkami na dekoratívne nátery, vieme Vám poskytnúť náš odborný posudok. Máme pokročilé nástroje, ako sú čítačky farieb, porovnávače farieb... atď. aby bola zaručená stála kvalita vašich náterov. PROCESY NANÁŠANIA TENKOU A HRUBOU FILMOU: Tu sú najpoužívanejšie z našich techník. Galvanické pokovovanie / Chemické pokovovanie (tvrdý chróm, chemický nikel) Galvanické pokovovanie je proces pokovovania jedného kovu na druhý hydrolýzou na dekoratívne účely, zabránenie korózii kovu alebo na iné účely. Galvanické pokovovanie nám umožňuje použiť lacné kovy, ako je oceľ alebo zinok alebo plasty na väčšinu produktu a potom naniesť rôzne kovy na vonkajšiu stranu vo forme filmu pre lepší vzhľad, ochranu a ďalšie vlastnosti požadované pre produkt. Bezprúdové pokovovanie, tiež známe ako chemické pokovovanie, je metóda negalvanického pokovovania, ktorá zahŕňa niekoľko simultánnych reakcií vo vodnom roztoku, ktoré prebiehajú bez použitia vonkajšej elektrickej energie. Reakcia sa uskutoční, keď sa vodík uvoľní redukčným činidlom a oxiduje sa, čím sa vytvorí negatívny náboj na povrchu dielu. Výhodou týchto tenkých a hrubých vrstiev je dobrá odolnosť proti korózii, nízka teplota spracovania, možnosť nanášania do vrtov, štrbín... atď. Nevýhodami je obmedzený výber náterových materiálov, relatívne mäkký charakter náterov, potrebné upravovacie kúpele znečisťujúce životné prostredie vrátane chemikálií, ako je kyanid, ťažké kovy, fluoridy, oleje, obmedzená presnosť povrchovej replikácie. Difúzne procesy (Nitridácia, nitrokarburizácia, boronizácia, fosfátovanie atď.) V peciach na tepelné spracovanie difúzne prvky zvyčajne pochádzajú z plynov reagujúcich pri vysokých teplotách s kovovými povrchmi. Môže ísť o čistú tepelnú a chemickú reakciu ako dôsledok tepelnej disociácie plynov. V niektorých prípadoch difúzne prvky pochádzajú z pevných látok. Výhody týchto termochemických procesov poťahovania sú dobrá odolnosť proti korózii, dobrá reprodukovateľnosť. Ich nevýhodou sú relatívne mäkké povlaky, obmedzený výber základného materiálu (ktorý musí byť vhodný na nitridáciu), dlhé časy spracovania, environmentálne a zdravotné riziká, potreba dodatočnej úpravy. CVD (chemická depozícia z pár) CVD je chemický proces používaný na výrobu vysokokvalitných, vysokovýkonných pevných povlakov. Proces vytvára aj tenké filmy. Pri typickom CVD sú substráty vystavené jednému alebo viacerým prchavým prekurzorom, ktoré reagujú a/alebo sa rozkladajú na povrchu substrátu za vzniku požadovaného tenkého filmu. Výhodou týchto tenkých a hrubých fólií je ich vysoká odolnosť proti opotrebeniu, možnosť ekonomickej výroby hrubších povlakov, vhodnosť pre vyvŕtané otvory, drážky atď. Nevýhodami CVD procesov sú ich vysoké teploty spracovania, náročnosť alebo nemožnosť pokovovania viacerými kovmi (napr. TiAlN), zaoblenie hrán, používanie ekologicky nebezpečných chemikálií. PACVD / PECVD (Plazma-Assisted Chemical Vapour Deposition) PACVD sa tiež nazýva PECVD, čo znamená plazmou vylepšené CVD. Zatiaľ čo pri procese PVD povlaku sa tenkovrstvové materiály odparujú z pevnej formy, pri PECVD povlak vzniká z plynnej fázy. Prekurzorové plyny sú krakované v plazme, aby boli dostupné pre povlak. Výhodou tejto techniky nanášania tenkých a hrubých vrstiev je, že sú možné výrazne nižšie procesné teploty v porovnaní s CVD, nanášajú sa presné povlaky. Nevýhody PACVD spočívajú v tom, že má len obmedzenú vhodnosť pre vyvŕtané otvory, drážky atď. PVD (fyzikálne nanášanie pár) PVD procesy sú rôzne čisto fyzikálne metódy nanášania vo vákuu, ktoré sa používajú na nanášanie tenkých vrstiev kondenzáciou odparenej formy požadovaného filmového materiálu na povrchy obrobku. Príkladmi PVD sú povlaky naprašovaním a odparovaním. Výhody spočívajú v tom, že nevznikajú žiadne materiály a emisie poškodzujúce životné prostredie, je možné vyrábať veľké množstvo rôznych povlakov, teploty povlakov sú pod teplotou konečného tepelného spracovania väčšiny ocelí, presne reprodukovateľné tenké povlaky, vysoká odolnosť proti opotrebeniu, nízky koeficient trenia. Nevýhody sú vrty, štrbiny...atď. môže byť potiahnutý len do hĺbky rovnajúcej sa priemeru alebo šírke otvoru, odolný voči korózii len za určitých podmienok a na získanie rovnomernej hrúbky filmu sa musia diely počas nanášania otáčať. Priľnavosť funkčných a dekoratívnych náterov závisí od podkladu. Okrem toho životnosť tenkovrstvových a hrubých povlakov závisí od parametrov prostredia, ako je vlhkosť, teplota...atď. Pred zvažovaním funkčného alebo dekoratívneho náteru nás preto kontaktujte pre náš názor. Môžeme vybrať najvhodnejšie náterové materiály a techniku náteru, ktorá vyhovuje vašim podkladom a aplikácii a nanesieme ich podľa najprísnejších noriem kvality. Podrobnosti o možnostiach nanášania tenkých a hrubých vrstiev získate od spoločnosti AGS-TECH Inc. Potrebujete pomoc s dizajnom? Potrebujete prototypy? Potrebujete hromadnú výrobu? Sme tu, aby sme vám pomohli. CLICK Product Finder-Locator Service PREDCHÁDZAJÚCA STRANA
- Cable & Connector Assembly, Wire Harness, Cable Management Accessories
Cable Assembly - Wire Harness - Cable Management Accessories - Connectorization - Cable Fan Out - Interconnects Elektrické a elektronické káblové zostavy a prepojenia Ponúkame: • Rôzne druhy vodičov, káblov, káblové zostavy a príslušenstvo na správu káblov, netienené alebo tienené káble pre rozvody energie, vysokého napätia, nízkeho signálu, telekomunikácií... atď., prepojovacie a prepojovacie komponenty. • Konektory, zástrčky, adaptéry a spojovacie objímky, konektorový prepojovací panel, spojovacie puzdro. - Ak si chcete stiahnuť náš katalóg pre bežné prepojovacie komponenty a hardvér, KLIKNITE TU. - Svorkovnice a konektory - Všeobecný katalóg koncových blokov - Katalóg zásuviek-Power Entry-Connectors - Brožúra produktov káblových koncoviek (Trubice, izolácia, ochrana, tepelne zmrštiteľné, opravy káblov, vylamovacie čižmy, svorky, káblové zväzky a spony, značky drôtov, pásky, koncovky káblov, distribučné štrbiny) - Informácie o našom zariadení na výrobu keramických a kovových tvaroviek, hermetické tesnenia, vákuové priechodky, komponenty pre vysoké a ultravysoké vákuum, BNC, SHV adaptéry a konektory, vodiče a kontaktné kolíky, konektorové svorky nájdete tu:_cc781905-5cde-3194-bb3b- 136bad5cf58d_ Továrenská brožúra Stiahnite si brožúru pre našePROGRAM DIZAJNOVÉHO PARTNERSTVA Produkty prepojení a káblových montáží sa dodávajú v širokej škále. Uveďte prosím typ, aplikáciu, technické listy, ak sú k dispozícii, a my vám ponúkneme najvhodnejší produkt. Môžeme vám ich prispôsobiť na mieru v prípade, že nejde o bežný produkt. Naše káblové zostavy a prepojenia sú označené CE alebo UL autorizovanými organizáciami a vyhovujú priemyselným predpisom a normám ako IEEE, IEC, ISO...atď. Ak sa chcete dozvedieť viac o našich inžinierskych a výskumných a vývojových schopnostiach namiesto výrobných operácií, pozývame vás na návštevu našej technickej stránky http://www.ags-engineering.com CLICK Product Finder-Locator Service PREDCHÁDZAJÚCA STRANA
- Test Equipment for Testing Paper & Packaging Products
Test Equipment for Testing Paper & Packaging Products, Adhesive Tape Peel Test Machine, Carton Compressive Tester, Foam Compression Hardness Tester, Zero Drop Test Machine, Package Incline Impact Tester Elektronické testery Pod pojmom ELECTRONIC TESTER označujeme testovacie zariadenie, ktoré sa používa predovšetkým na testovanie, kontrolu a analýzu elektrických a elektronických komponentov a systémov. Ponúkame tie najpopulárnejšie v odbore: NAPÁJACIE ZDROJE A ZARIADENIA NA GENEROVANIE SIGNÁLU: NAPÁJACÍ ZDROJ, GENERÁTOR SIGNÁLU, FREKVENČNÝ SYNTEZÁTOR, GENERÁTOR FUNKCIÍ, GENERÁTOR DIGITÁLNEHO VZORKU, IMPULZNÝ GENERÁTOR, INJEKTOR SIGNÁLU METRE: DIGITÁLNE MULTIMETRE, LCR METER, EMF METER, METER KAPACITANCE, MOSTOVÝ NÁSTROJ, SVORNÝ METER, GAUSMETER / TESLAMETER/ MAGNETOMETER, METER UZEMNÉHO ODPORU ANALYZÁTORY: OSCILOSKOPY, LOGICKÝ ANALYZÁTOR, SPEKTRÁLNY ANALYZÁTOR, PROTOKOLOVÝ ANALYZÁTOR, ANALYZÁTOR VEKTOROVÉHO SIGNÁLU, ČASOVÝ REFLEKTOmeter, SEMINÁR POLOVODIČOVÝCH KRIVIEK, SIEŤOVÝ ANALYZÁTOR, FÁZOVÝ CYKLUS, FROTEKVENTEKTERNATÍN Podrobnosti a ďalšie podobné vybavenie nájdete na našej webovej stránke o vybavení: http://www.sourceindustrialsupply.com Pozrime sa stručne na niektoré z týchto zariadení pri každodennom používaní v celom odvetví: Nami dodávané elektrické zdroje pre metrologické účely sú diskrétne, stolové a samostatné zariadenia. NASTAVITEĽNÉ REGULOVANÉ ELEKTRICKÉ ZDROJE sú jedny z najpopulárnejších, pretože ich výstupné hodnoty je možné nastaviť a ich výstupné napätie alebo prúd je udržiavaný konštantný, aj keď dochádza k zmenám vstupného napätia alebo prúdu záťaže. IZOLOVANÉ NAPÁJACIE ZDROJE majú napájacie výstupy, ktoré sú elektricky nezávislé od ich napájacích vstupov. V závislosti od spôsobu premeny výkonu existujú LINEÁRNE a SPÍNANÉ NAPÁJACIE ZDROJE. Lineárne napájacie zdroje spracovávajú vstupný výkon priamo so všetkými svojimi aktívnymi komponentmi konverzie výkonu pracujúcimi v lineárnych oblastiach, zatiaľ čo spínané napájacie zdroje majú komponenty pracujúce prevažne v nelineárnych režimoch (ako sú tranzistory) a konvertujú energiu na striedavé alebo jednosmerné impulzy predtým. spracovanie. Spínané napájacie zdroje sú vo všeobecnosti efektívnejšie ako lineárne zdroje, pretože strácajú menej energie v dôsledku kratších časov, ktoré ich komponenty strávia v lineárnych prevádzkových oblastiach. V závislosti od aplikácie sa používa jednosmerné alebo striedavé napájanie. Ďalšími populárnymi zariadeniami sú PROGRAMOVATEĽNÉ NAPÁJACIE ZDROJE, kde je možné diaľkovo ovládať napätie, prúd alebo frekvenciu cez analógový vstup alebo digitálne rozhranie, ako je RS232 alebo GPIB. Mnohé z nich majú integrovaný mikropočítač na monitorovanie a riadenie operácií. Takéto nástroje sú nevyhnutné na účely automatizovaného testovania. Niektoré elektronické napájacie zdroje používajú obmedzenie prúdu namiesto odpojenia napájania pri preťažení. Elektronické obmedzovanie sa bežne používa na prístrojoch laboratórneho typu. GENERÁTORY SIGNÁLU sú ďalšie široko používané prístroje v laboratóriu a priemysle, ktoré generujú opakujúce sa alebo neopakujúce sa analógové alebo digitálne signály. Alternatívne sa nazývajú aj GENERÁTORY FUNKCIÍ, GENERÁTORY DIGITÁLNYCH VZORKOV alebo GENERÁTORY FREKVENCIE. Funkčné generátory generujú jednoduché opakujúce sa tvary vĺn, ako sú sínusové vlny, krokové impulzy, štvorcové a trojuholníkové a ľubovoľné tvary vĺn. Pomocou generátorov ľubovoľných priebehov môže používateľ generovať ľubovoľné tvary vĺn v rámci publikovaných limitov frekvenčného rozsahu, presnosti a výstupnej úrovne. Na rozdiel od funkčných generátorov, ktoré sú obmedzené na jednoduchý súbor priebehov, generátor ľubovoľného tvaru vlny umožňuje užívateľovi špecifikovať zdrojový tvar vlny rôznymi spôsobmi. RF a MIKROVLNNÉ GENERÁTORY SIGNÁLU sa používajú na testovanie komponentov, prijímačov a systémov v aplikáciách, ako sú mobilná komunikácia, WiFi, GPS, vysielanie, satelitná komunikácia a radary. Generátory RF signálu vo všeobecnosti pracujú medzi niekoľkými kHz až 6 GHz, zatiaľ čo generátory mikrovlnného signálu pracujú v oveľa širšom frekvenčnom rozsahu, od menej ako 1 MHz do najmenej 20 GHz a dokonca až do stoviek GHz s použitím špeciálneho hardvéru. Generátory RF a mikrovlnných signálov možno ďalej klasifikovať ako generátory analógových alebo vektorových signálov. GENERÁTORY AUDIOFREKVENČNÝCH SIGNÁLOV generujú signály vo frekvenčnom rozsahu a vyššie. Majú elektronické laboratórne aplikácie na kontrolu frekvenčnej odozvy audio zariadení. GENERÁTORY VEKTOROVÉHO SIGNÁLU, niekedy tiež označované ako GENERÁTORY DIGITÁLNEHO SIGNÁLU, sú schopné generovať digitálne modulované rádiové signály. Generátory vektorových signálov môžu generovať signály založené na priemyselných štandardoch, ako sú GSM, W-CDMA (UMTS) a Wi-Fi (IEEE 802.11). LOGICKÉ GENERÁTORY SIGNÁLU sa nazývajú aj GENERÁTOR DIGITÁLNYCH VZORKOV. Tieto generátory produkujú logické typy signálov, to znamená logické 1s a 0s vo forme konvenčných napäťových úrovní. Generátory logických signálov sa používajú ako stimulačné zdroje pre funkčné overovanie a testovanie digitálnych integrovaných obvodov a vstavaných systémov. Vyššie uvedené zariadenia sú určené na všeobecné použitie. Existuje však mnoho ďalších generátorov signálu navrhnutých pre vlastné špecifické aplikácie. INJEKTOR SIGNÁLU je veľmi užitočný a rýchly nástroj na riešenie problémov na sledovanie signálu v obvode. Technici dokážu veľmi rýchlo určiť poruchový stav zariadenia, akým je rádiový prijímač. Signálový injektor môže byť aplikovaný na výstup reproduktora a ak je signál počuteľný, je možné prejsť na predchádzajúci stupeň obvodu. V tomto prípade audio zosilňovač, a ak je injektovaný signál znova počuť, je možné posunúť injektovanie signálu nahor po stupňoch obvodu, kým signál prestane byť počuteľný. To bude slúžiť na účely lokalizácie miesta problému. MULTIMETER je elektronický merací prístroj, ktorý kombinuje niekoľko meracích funkcií v jednej jednotke. Vo všeobecnosti multimetre merajú napätie, prúd a odpor. K dispozícii je digitálna aj analógová verzia. Ponúkame prenosné ručné multimetrové jednotky, ako aj laboratórne modely s certifikovanou kalibráciou. Moderné multimetre dokážu merať mnoho parametrov, ako sú: Napätie (oba AC / DC), vo voltoch, Prúd (oba AC / DC), v ampéroch, Odpor v ohmoch. Niektoré multimetre navyše merajú: kapacitu vo faradoch, vodivosť v siemens, decibely, pracovný cyklus v percentách, frekvenciu v hertzoch, indukčnosť v henry, teplotu v stupňoch Celzia alebo Fahrenheita pomocou teplotnej testovacej sondy. Niektoré multimetre tiež zahŕňajú: Tester kontinuity; zvuky, keď obvod vedie, diódy (meranie dopredného poklesu prechodov diód), tranzistory (meranie zosilnenia prúdu a iných parametrov), funkcia kontroly batérie, funkcia merania úrovne osvetlenia, funkcia merania kyslosti a zásaditosti (pH) a funkcia merania relatívnej vlhkosti. Moderné multimetre sú často digitálne. Moderné digitálne multimetre majú často zabudovaný počítač, ktorý z nich robí veľmi výkonné nástroje v metrológii a testovaní. Zahŕňajú funkcie ako:: •Automatický rozsah, ktorý vyberie správny rozsah pre testované množstvo tak, aby sa zobrazili najvýznamnejšie číslice. •Automatická polarita pre odčítanie jednosmerného prúdu ukazuje, či je aplikované napätie kladné alebo záporné. • Odoberte a podržte, čím sa zablokuje posledný údaj na vyšetrenie po odstránení prístroja z testovaného okruhu. •Skúšky s obmedzením prúdu na pokles napätia cez polovodičové prechody. Aj keď nejde o náhradu za tester tranzistorov, táto vlastnosť digitálnych multimetrov uľahčuje testovanie diód a tranzistorov. • Stĺpcový graf reprezentácie testovanej veličiny pre lepšiu vizualizáciu rýchlych zmien nameraných hodnôt. • Osciloskop s nízkou šírkou pásma. • Testery automobilových obvodov s testami časovania automobilov a signálov zotrvania. • Funkcia získavania údajov na zaznamenávanie maximálnych a minimálnych hodnôt počas daného obdobia a na odoberanie množstva vzoriek v pevných intervaloch. •Kombinovaný LCR meter. Niektoré multimetre môžu byť prepojené s počítačmi, zatiaľ čo niektoré môžu ukladať merania a nahrávať ich do počítača. Ďalším veľmi užitočným nástrojom je LCR METER je metrologický prístroj na meranie indukčnosti (L), kapacity (C) a odporu (R) komponentu. Impedancia sa meria interne a prevádza sa na zobrazenie na zodpovedajúcu hodnotu kapacity alebo indukčnosti. Údaje budú primerane presné, ak testovaný kondenzátor alebo induktor nemá významnú odporovú zložku impedancie. Pokročilé LCR merače merajú skutočnú indukčnosť a kapacitu, ako aj ekvivalentný sériový odpor kondenzátorov a Q faktor indukčných komponentov. Testované zariadenie je vystavené zdroju striedavého napätia a merač meria napätie naprieč a prúd cez testované zariadenie. Z pomeru napätia k prúdu môže merač určiť impedanciu. V niektorých prístrojoch sa meria aj fázový uhol medzi napätím a prúdom. V kombinácii s impedanciou možno vypočítať a zobraziť ekvivalentnú kapacitu alebo indukčnosť a odpor testovaného zariadenia. LCR merače majú voliteľné testovacie frekvencie 100 Hz, 120 Hz, 1 kHz, 10 kHz a 100 kHz. Stolné LCR merače majú zvyčajne voliteľné testovacie frekvencie vyššie ako 100 kHz. Často zahŕňajú možnosti superponovania jednosmerného napätia alebo prúdu na striedavý merací signál. Zatiaľ čo niektoré merače ponúkajú možnosť externého napájania týchto jednosmerných napätí alebo prúdov, iné zariadenia ich dodávajú interne. EMF METER je testovací a metrologický prístroj na meranie elektromagnetických polí (EMF). Väčšina z nich meria hustotu toku elektromagnetického žiarenia (DC polia) alebo zmenu elektromagnetického poľa v čase (AC polia). Existujú jednoosové a trojosové verzie prístrojov. Jednoosové merače stoja menej ako trojosové merače, ale dokončenie testu trvá dlhšie, pretože merací prístroj meria iba jeden rozmer poľa. Meracie prístroje EMF s jednou osou sa musia nakloniť a otočiť na všetkých troch osiach, aby sa dokončilo meranie. Na druhej strane trojosové merače merajú všetky tri osi súčasne, sú však drahšie. Merač EMF môže merať striedavé elektromagnetické polia, ktoré vychádzajú zo zdrojov, ako je elektrické vedenie, zatiaľ čo GAUSSMETRE / TESLAMETRE alebo MAGNETOMETRE merajú jednosmerné polia vyžarované zo zdrojov, kde je prítomný jednosmerný prúd. Väčšina elektromerov EMF je kalibrovaná na meranie 50 a 60 Hz striedavých polí zodpovedajúcich frekvencii elektrickej energie v USA a Európe. Existujú aj iné merače, ktoré dokážu merať polia striedajúce sa už od 20 Hz. Merania EMF môžu byť širokopásmové v širokom rozsahu frekvencií alebo môžu frekvenčne selektívne monitorovať iba požadovaný frekvenčný rozsah. METER KAPACITANCE je testovacie zariadenie používané na meranie kapacity väčšinou diskrétnych kondenzátorov. Niektoré merače zobrazujú iba kapacitu, zatiaľ čo iné tiež zobrazujú únik, ekvivalentný sériový odpor a indukčnosť. Vyššie testovacie prístroje používajú techniky, ako je vloženie testovaného kondenzátora do mostíkového obvodu. Zmenou hodnôt ostatných ramien v mostíku tak, aby sa most dostal do rovnováhy, sa určí hodnota neznámeho kondenzátora. Táto metóda zaisťuje väčšiu presnosť. Mostík môže byť tiež schopný merať sériový odpor a indukčnosť. Môžu sa merať kondenzátory v rozsahu od pikofaradov po farady. Mostíkové obvody nemerajú zvodový prúd, ale môže sa použiť jednosmerné predpätie a únik priamo merať. Mnoho BRIDGE INSTRUMENTS môže byť pripojených k počítačom a môže sa uskutočniť výmena údajov na sťahovanie údajov alebo na externé ovládanie mosta. Takéto premosťovacie nástroje ponúkajú testovanie typu go/no go na automatizáciu testov v rýchlo sa rozvíjajúcom prostredí výroby a kontroly kvality. Ďalší testovací prístroj, CLAMP METER, je elektrický tester, ktorý kombinuje voltmeter s kliešťovým meračom prúdu. Väčšina moderných verzií kliešťových meračov je digitálnych. Moderné kliešťové merače majú väčšinu základných funkcií digitálneho multimetra, ale s pridanou funkciou prúdového transformátora zabudovaného do produktu. Keď zovriete „čeľuste“ prístroja okolo vodiča prenášajúceho veľký striedavý prúd, tento prúd je spojený cez čeľuste, podobne ako železné jadro výkonového transformátora, a do sekundárneho vinutia, ktoré je pripojené cez bočník vstupu merača. , princíp činnosti sa veľmi podobá na transformátor. Oveľa menší prúd sa dodáva na vstup merača v dôsledku pomeru počtu sekundárnych vinutí k počtu primárnych vinutí obalených okolo jadra. Primárny je reprezentovaný jedným vodičom, okolo ktorého sú upnuté čeľuste. Ak má sekundár 1000 vinutí, potom sekundárny prúd je 1/1000 prúdu tečúceho primárom, alebo v tomto prípade meraným vodičom. Teda 1 ampér prúdu v meranom vodiči by vyprodukoval 0,001 ampéra prúdu na vstupe meracieho prístroja. Pomocou kliešťových meračov je možné ľahko merať oveľa väčšie prúdy zvýšením počtu závitov v sekundárnom vinutí. Rovnako ako väčšina našich testovacích zariadení, pokročilé kliešťové merače ponúkajú možnosť zaznamenávania. TESTERY ODPORU UZEMNENIA sa používajú na testovanie uzemňovacích elektród a odporu pôdy. Požiadavky na prístroj závisia od rozsahu aplikácií. Moderné upínacie prístroje na uzemnenie zjednodušujú testovanie uzemňovacej slučky a umožňujú nerušivé merania unikajúceho prúdu. Medzi ANALYZÁTORY, ktoré predávame, patria bezpochyby osciloskopy jedným z najpoužívanejších zariadení. Osciloskop, tiež nazývaný OSCILLOGRAPH, je typ elektronického testovacieho prístroja, ktorý umožňuje pozorovanie neustále sa meniaceho napätia signálu ako dvojrozmerného grafu jedného alebo viacerých signálov ako funkcie času. Neelektrické signály ako zvuk a vibrácie môžu byť tiež prevedené na napätie a zobrazené na osciloskopoch. Osciloskopy sa používajú na pozorovanie zmeny elektrického signálu v čase, napätie a čas opisujú tvar, ktorý je kontinuálne vykreslený oproti kalibrovanej stupnici. Pozorovanie a analýza tvaru vlny nám odhaľuje vlastnosti, ako je amplitúda, frekvencia, časový interval, čas nábehu a skreslenie. Osciloskopy je možné nastaviť tak, aby bolo možné pozorovať opakujúce sa signály ako súvislý tvar na obrazovke. Mnohé osciloskopy majú funkciu ukladania, ktorá umožňuje zachytenie jednotlivých udalostí prístrojom a ich zobrazenie na relatívne dlhú dobu. To nám umožňuje pozorovať udalosti príliš rýchlo na to, aby boli priamo vnímateľné. Moderné osciloskopy sú ľahké, kompaktné a prenosné prístroje. Existujú aj miniatúrne batériou napájané prístroje pre aplikácie v teréne. Laboratórne osciloskopy sú vo všeobecnosti stolové zariadenia. Existuje široká škála sond a vstupných káblov na použitie s osciloskopmi. V prípade, že potrebujete poradiť, ktorý z nich použiť vo vašej aplikácii, kontaktujte nás. Osciloskopy s dvoma vertikálnymi vstupmi sa nazývajú dvojstopové osciloskopy. Pomocou CRT s jedným lúčom multiplexujú vstupy, zvyčajne medzi nimi prepínajú dostatočne rýchlo na to, aby zjavne zobrazili dve stopy naraz. Existujú aj osciloskopy s viacerými stopami; medzi nimi sú bežné štyri vstupy. Niektoré viacstopové osciloskopy používajú externý spúšťací vstup ako voliteľný vertikálny vstup a niektoré majú tretí a štvrtý kanál len s minimálnymi ovládacími prvkami. Moderné osciloskopy majú niekoľko vstupov pre napätie, a preto ich možno použiť na zobrazenie jedného meniaceho sa napätia oproti druhému. Toto sa používa napríklad na vykreslenie IV kriviek (charakteristiky prúdu versus napätie) pre komponenty, ako sú diódy. Pre vysoké frekvencie a rýchle digitálne signály musí byť šírka pásma vertikálnych zosilňovačov a vzorkovacia frekvencia dostatočne vysoká. Na všeobecné použitie zvyčajne postačuje šírka pásma aspoň 100 MHz. Oveľa menšia šírka pásma je dostatočná len pre audiofrekvenčné aplikácie. Užitočný rozsah rozmietania je od jednej sekundy do 100 nanosekúnd, s príslušným spúšťaním a oneskorením rozmietania. Pre stabilné zobrazenie je potrebný dobre navrhnutý, stabilný spúšťací obvod. Kvalita spúšťacieho obvodu je kľúčom pre dobré osciloskopy. Ďalším kľúčovým kritériom výberu je hĺbka pamäte vzoriek a vzorkovacia frekvencia. Moderné DSO základnej úrovne majú teraz 1 MB alebo viac pamäte vzoriek na kanál. Táto pamäť vzoriek je často zdieľaná medzi kanálmi a niekedy môže byť plne dostupná len pri nižších vzorkovacích frekvenciách. Pri najvyšších vzorkovacích frekvenciách môže byť pamäť obmedzená na niekoľko 10 kB. Akýkoľvek moderný DSO vzorkovacej frekvencie v reálnom čase bude mať typicky 5-10-násobok vstupnej šírky pásma vzorkovacej frekvencie. Takže DSO so šírkou pásma 100 MHz by malo vzorkovaciu frekvenciu 500 Ms/s - 1 Gs/s. Výrazne zvýšená vzorkovacia frekvencia do značnej miery eliminovala zobrazovanie nesprávnych signálov, ktoré boli niekedy prítomné v prvej generácii digitálnych osciloskopov. Väčšina moderných osciloskopov poskytuje jedno alebo viac externých rozhraní alebo zberníc, ako je GPIB, Ethernet, sériový port a USB, ktoré umožňujú diaľkové ovládanie prístroja pomocou externého softvéru. Tu je zoznam rôznych typov osciloskopov: KATÓDOVÝ OSCILOSKOP DUAL-BEAM OSCILOSKOP ANALOGOVÝ OSCILOSKOP UKLADANIA DIGITÁLNE OSCILOSKOPY OSCILOSKOPY ZMIEŠANÉHO SIGNÁLU RUČNÉ OSCILOSKOPY OSCILOSKOPY ZALOŽENÉ NA PC LOGICKÝ ANALYZÁTOR je prístroj, ktorý zachytáva a zobrazuje viaceré signály z digitálneho systému alebo digitálneho obvodu. Logický analyzátor môže konvertovať zachytené údaje do časových diagramov, dekódovania protokolov, sledovania stavu stroja, jazyka symbolických adries. Logické analyzátory majú pokročilé možnosti spúšťania a sú užitočné, keď používateľ potrebuje vidieť časové vzťahy medzi mnohými signálmi v digitálnom systéme. MODULÁRNE LOGICKÉ ANALYZÁTORY pozostávajú zo šasi alebo hlavného rámu a modulov logického analyzátora. Šasi alebo mainframe obsahuje displej, ovládacie prvky, riadiaci počítač a viacero slotov, do ktorých je nainštalovaný hardvér na zachytávanie údajov. Každý modul má špecifický počet kanálov a viaceré moduly možno kombinovať, aby sa získal veľmi vysoký počet kanálov. Schopnosť kombinovať viacero modulov na získanie vysokého počtu kanálov a všeobecne vyšší výkon modulárnych logických analyzátorov ich robí drahšími. V prípade veľmi špičkových modulárnych logických analyzátorov môže byť potrebné, aby používatelia poskytli svoje vlastné hostiteľské PC alebo si kúpili vstavaný ovládač kompatibilný so systémom. PRENOSNÉ LOGICKÉ ANALYZÁTORY integrujú všetko do jedného balíka s voliteľným príslušenstvom nainštalovaným vo výrobe. Vo všeobecnosti majú nižší výkon ako modulárne, ale sú to ekonomické metrologické nástroje na všeobecné ladenie. V PC-BASED LOGIC ANALYZERS sa hardvér pripája k počítaču prostredníctvom pripojenia USB alebo Ethernet a prenáša zachytené signály do softvéru v počítači. Tieto zariadenia sú vo všeobecnosti oveľa menšie a lacnejšie, pretože využívajú existujúcu klávesnicu, displej a procesor osobného počítača. Logické analyzátory môžu byť spustené na komplikovanej sekvencii digitálnych udalostí a potom zachytiť veľké množstvo digitálnych údajov z testovaných systémov. Dnes sa používajú špecializované konektory. Evolúcia sond logických analyzátorov viedla k spoločnej stope, ktorú podporujú viacerí predajcovia, čo poskytuje dodatočnú slobodu koncovým používateľom: Bezkonektorová technológia ponúkaná ako niekoľko obchodných názvov špecifických pre jednotlivých predajcov, ako napríklad Compression Probing; Jemný dotyk; Používa sa D-Max. Tieto sondy poskytujú odolné, spoľahlivé mechanické a elektrické spojenie medzi sondou a obvodovou doskou. SPEKTROVÝ ANALYZÁTOR meria veľkosť vstupného signálu oproti frekvencii v rámci celého frekvenčného rozsahu prístroja. Primárne použitie je na meranie sily spektra signálov. Existujú tiež optické a akustické spektrálne analyzátory, ale tu budeme diskutovať iba o elektronických analyzátoroch, ktoré merajú a analyzujú elektrické vstupné signály. Spektrá získané z elektrických signálov nám poskytujú informácie o frekvencii, výkone, harmonických, šírke pásma... atď. Frekvencia je zobrazená na vodorovnej osi a amplitúda signálu na zvislej. Spektrálne analyzátory sú široko používané v elektronickom priemysle na analýzu frekvenčného spektra rádiofrekvenčných, RF a audio signálov. Pri pohľade na spektrum signálu sme schopní odhaliť prvky signálu a výkon obvodu, ktorý ich vytvára. Spektrálne analyzátory sú schopné vykonávať širokú škálu meraní. Pri pohľade na metódy používané na získanie spektra signálu môžeme kategorizovať typy spektrálnych analyzátorov. - SWEPT-TUNED SPECTRUM ANALYZER používa superheterodynový prijímač na konverziu časti spektra vstupného signálu smerom nadol (pomocou napäťovo riadeného oscilátora a zmiešavača) na strednú frekvenciu pásmového filtra. Vďaka superheterodynnej architektúre sa napätím riadený oscilátor pohybuje cez rozsah frekvencií, pričom využíva celý frekvenčný rozsah nástroja. Analyzátory spektra s rozmietaným ladením pochádzajú z rádiových prijímačov. Preto sú analyzátory ladené s rozmietaním buď analyzátory s ladeným filtrom (analogické k rádiu TRF) alebo analyzátory superheterodyn. V skutočnosti, v ich najjednoduchšej forme, by ste si mohli predstaviť rozmietaný spektrálny analyzátor ako frekvenčne selektívny voltmeter s frekvenčným rozsahom, ktorý je ladený (swept) automaticky. Je to v podstate frekvenčne selektívny voltmeter reagujúci na špičku kalibrovaný na zobrazenie efektívnej hodnoty sínusovej vlny. Spektrálny analyzátor dokáže zobraziť jednotlivé frekvenčné zložky, ktoré tvoria komplexný signál. Neposkytuje však informácie o fáze, iba informácie o veľkosti. Moderné ladené analyzátory (najmä superheterodynné analyzátory) sú presné zariadenia, ktoré dokážu vykonávať širokú škálu meraní. Primárne sa však používajú na meranie ustálených alebo opakujúcich sa signálov, pretože nedokážu súčasne vyhodnotiť všetky frekvencie v danom rozsahu. Schopnosť vyhodnocovať všetky frekvencie súčasne je možná len s analyzátormi v reálnom čase. - SPEKTRÁLNE ANALYZÁTORY V REÁLNOM ČASE: FFT SPEKTROVÝ ANALYZÁTOR počíta diskrétnu Fourierovu transformáciu (DFT), matematický proces, ktorý transformuje tvar vlny na zložky jeho frekvenčného spektra vstupného signálu. Fourier alebo FFT spektrálny analyzátor je ďalšou implementáciou spektrálneho analyzátora v reálnom čase. Fourierov analyzátor využíva digitálne spracovanie signálu na vzorkovanie vstupného signálu a jeho konverziu do frekvenčnej oblasti. Táto konverzia sa vykonáva pomocou rýchlej Fourierovej transformácie (FFT). FFT je implementáciou diskrétnej Fourierovej transformácie, matematického algoritmu používaného na transformáciu údajov z časovej oblasti do frekvenčnej oblasti. Iný typ spektrálnych analyzátorov v reálnom čase, konkrétne ANALYZÁTORY PARALELNÝCH FILTROV, kombinujú niekoľko pásmových filtrov, každý s inou pásmovou frekvenciou. Každý filter zostáva neustále pripojený k vstupu. Po počiatočnom čase ustálenia môže analyzátor s paralelným filtrom okamžite detekovať a zobraziť všetky signály v rámci meracieho rozsahu analyzátora. Analyzátor s paralelným filtrom preto poskytuje analýzu signálu v reálnom čase. Analyzátor s paralelným filtrom je rýchly, meria prechodné a časovo premenné signály. Frekvenčné rozlíšenie analyzátora s paralelným filtrom je však oveľa nižšie ako u väčšiny analyzátorov ladených s rozmietaním, pretože rozlíšenie je určené šírkou pásmových filtrov. Na získanie jemného rozlíšenia vo veľkom frekvenčnom rozsahu by ste potrebovali veľa individuálnych filtrov, čo je nákladné a zložité. To je dôvod, prečo je väčšina analyzátorov s paralelným filtrom, okrem tých najjednoduchších na trhu, drahá. - ANALÝZA VEKTOROVÉHO SIGNÁLU (VSA): V minulosti pokrývali spektrálne analyzátory s rozmietaným ladením a superheterodynné široké frekvenčné rozsahy od zvukových, cez mikrovlnné až po milimetrové frekvencie. Okrem toho analyzátory rýchlej Fourierovej transformácie (FFT) s intenzívnym digitálnym spracovaním signálu (DSP) poskytovali spektrálnu a sieťovú analýzu s vysokým rozlíšením, ale boli obmedzené na nízke frekvencie kvôli limitom analógovo-digitálnej konverzie a technológií spracovania signálu. Dnešné širokopásmové, vektorovo modulované, časovo premenné signály ťažia z možností FFT analýzy a iných DSP techník. Vektorové analyzátory signálu kombinujú superheterodynovú technológiu s vysokorýchlostnými ADC a ďalšími technológiami DSP, aby ponúkali rýchle merania spektra s vysokým rozlíšením, demoduláciu a pokročilú analýzu v časovej oblasti. VSA je obzvlášť užitočný na charakterizáciu komplexných signálov, ako sú impulzné, prechodné alebo modulované signály používané v komunikačných, video, vysielacích, sonarových a ultrazvukových zobrazovacích aplikáciách. Podľa tvarových faktorov sú spektrálne analyzátory zoskupené ako stolové, prenosné, ručné a sieťové. Stolné modely sú užitočné pre aplikácie, kde je možné spektrálny analyzátor zapojiť do striedavého prúdu, napríklad v laboratórnom prostredí alebo vo výrobnej oblasti. Stolné spektrálne analyzátory vo všeobecnosti ponúkajú lepší výkon a špecifikácie ako prenosné alebo ručné verzie. Vo všeobecnosti sú však ťažšie a majú niekoľko ventilátorov na chladenie. Niektoré STOLNÉ SPEKTROVÉ ANALYZÁTORY ponúkajú voliteľné batérie, ktoré umožňujú ich použitie mimo sieťovej zásuvky. Tieto sa označujú ako PRENOSNÉ SPEKTRÁLNE ANALYZÁTORY. Prenosné modely sú užitočné pre aplikácie, kde je potrebné spektrálny analyzátor vziať von na vykonanie meraní alebo ho nosiť počas používania. Očakáva sa, že dobrý prenosný spektrálny analyzátor ponúkne voliteľnú prevádzku na batériu, ktorá používateľovi umožní pracovať na miestach bez elektrických zásuviek, jasne viditeľný displej, ktorý umožní čítanie obrazovky pri jasnom slnečnom svetle, v tme alebo prašnom prostredí, nízku hmotnosť. RUČNÉ SPEKTRÁLNE ANALYZÁTORY sú užitočné pre aplikácie, kde musí byť spektrálny analyzátor veľmi ľahký a malý. Ručné analyzátory ponúkajú v porovnaní s väčšími systémami obmedzené možnosti. Výhodou ručných spektrálnych analyzátorov je však ich veľmi nízka spotreba energie, prevádzka na batérie v teréne, ktorá umožňuje užívateľovi voľný pohyb vonku, veľmi malé rozmery a nízka hmotnosť. Napokon, SIEŤOVÉ SPECTRÁLNE ANALYZÁTORY neobsahujú displej a sú navrhnuté tak, aby umožňovali novú triedu geograficky distribuovaných aplikácií na monitorovanie a analýzu spektra. Kľúčovým atribútom je možnosť pripojiť analyzátor k sieti a monitorovať takéto zariadenia cez sieť. Zatiaľ čo mnohé spektrálne analyzátory majú ethernetový port na ovládanie, zvyčajne im chýbajú efektívne mechanizmy prenosu údajov a sú príliš objemné a/alebo drahé na to, aby boli nasadené takýmto distribuovaným spôsobom. Distribuovaná povaha takýchto zariadení umožňuje geografickú polohu vysielačov, monitorovanie spektra pre dynamický prístup k spektru a mnoho ďalších takýchto aplikácií. Tieto zariadenia sú schopné synchronizovať zachytené dáta cez sieť analyzátorov a umožňujú sieťovo efektívny prenos dát za nízku cenu. PROTOKOLOVÝ ANALYZÁTOR je nástroj zahŕňajúci hardvér a/alebo softvér používaný na zachytávanie a analýzu signálov a dátovej prevádzky cez komunikačný kanál. Protokolové analyzátory sa väčšinou používajú na meranie výkonu a riešenie problémov. Pripájajú sa k sieti, aby vypočítali kľúčové ukazovatele výkonu na monitorovanie siete a zrýchlenie činností pri riešení problémov. ANALYZÁTOR SIEŤOVÉHO PROTOKOLU je dôležitou súčasťou sady nástrojov správcu siete. Analýza sieťového protokolu sa používa na monitorovanie stavu sieťovej komunikácie. Aby správcovia zistili, prečo sieťové zariadenie funguje určitým spôsobom, používajú analyzátor protokolov na sledovanie prevádzky a odhalenie údajov a protokolov, ktoré prechádzajú po kábli. Používajú sa analyzátory sieťových protokolov - Riešenie ťažko riešiteľných problémov - Zistiť a identifikovať škodlivý softvér / malvér. Pracujte so systémom detekcie narušenia alebo s honeypotom. - Zhromažďujte informácie, ako sú základné vzorce návštevnosti a metriky využitia siete - Identifikujte nepoužívané protokoly, aby ste ich mohli odstrániť zo siete - Generovať návštevnosť pre penetračné testovanie - Odpočúvanie prevádzky (napr. lokalizácia neoprávnenej prevádzky okamžitých správ alebo bezdrôtových prístupových bodov) ČASOVÝ REFLEKTOmeter (TDR) je prístroj, ktorý využíva reflektometriu v časovej oblasti na charakterizáciu a lokalizáciu porúch v kovových kábloch, ako sú krútené dvojlinky a koaxiálne káble, konektory, dosky plošných spojov atď. Reflektometre v časovej oblasti merajú odrazy pozdĺž vodiča. Na ich meranie vysiela TDR signál dopadu na vodič a pozerá sa na jeho odrazy. Ak má vodič rovnomernú impedanciu a je správne zakončený, potom nebudú žiadne odrazy a zostávajúci dopadajúci signál bude absorbovaný na vzdialenom konci zakončením. Ak však niekde dôjde k odchýlke impedancie, časť signálu dopadu sa odrazí späť do zdroja. Odrazy budú mať rovnaký tvar ako dopadový signál, ale ich znamenie a veľkosť závisia od zmeny úrovne impedancie. Ak dôjde k skokovému zvýšeniu impedancie, odraz bude mať rovnaké znamienko ako dopadajúci signál a ak dôjde k skokovému poklesu impedancie, odraz bude mať opačné znamienko. Odrazy sa merajú na výstupe/vstupe reflektometra časovej domény a zobrazujú sa ako funkcia času. Alternatívne môže displej zobrazovať prenos a odrazy ako funkciu dĺžky kábla, pretože rýchlosť šírenia signálu je pre dané prenosové médium takmer konštantná. TDR možno použiť na analýzu impedancií a dĺžok káblov, strát a umiestnení konektorov a spojov. Merania impedancie TDR poskytujú dizajnérom príležitosť vykonávať analýzu integrity signálu systémových prepojení a presne predpovedať výkon digitálneho systému. Merania TDR sa široko používajú pri charakterizácii dosiek. Dizajnér dosiek plošných spojov môže určiť charakteristické impedancie stôp dosky, vypočítať presné modely komponentov dosky a presnejšie predpovedať výkon dosky. Existuje mnoho ďalších oblastí použitia reflektometrov v časovej oblasti. SEMICONDUCTOR CURVE TRACER je testovacie zariadenie používané na analýzu charakteristík diskrétnych polovodičových zariadení, ako sú diódy, tranzistory a tyristory. Prístroj je založený na osciloskope, ale obsahuje aj zdroje napätia a prúdu, ktoré je možné použiť na stimuláciu testovaného zariadenia. Na dve svorky testovaného zariadenia sa privedie rozkmitané napätie a meria sa množstvo prúdu, ktoré zariadenie umožňuje pretekať pri každom napätí. Na obrazovke osciloskopu sa zobrazí graf s názvom VI (napätie verzus prúd). Konfigurácia zahŕňa maximálne použité napätie, polaritu použitého napätia (vrátane automatickej aplikácie kladnej aj zápornej polarity) a odpor vložený do série so zariadením. Pre dve koncové zariadenia, ako sú diódy, to stačí na úplnú charakteristiku zariadenia. Sledovač kriviek môže zobraziť všetky zaujímavé parametre, ako je priepustné napätie diódy, spätný zvodový prúd, spätné prierazné napätie atď. Zariadenia s tromi terminálmi, ako sú tranzistory a FET, tiež používajú pripojenie k riadiacemu terminálu testovaného zariadenia, ako je terminál Base alebo Gate. Pre tranzistory a iné prúdové zariadenia je prúd bázy alebo iného ovládacieho terminálu stupňovitý. Pre tranzistory s efektom poľa (FET) sa namiesto stupňovitého prúdu používa stupňovité napätie. Prechádzaním napätia cez nakonfigurovaný rozsah napätí na hlavnej svorke sa pre každý krok napätia riadiaceho signálu automaticky generuje skupina kriviek VI. Táto skupina kriviek umožňuje veľmi jednoducho určiť zosilnenie tranzistora, alebo spúšťacie napätie tyristora alebo TRIAC. Moderné sledovače polovodičových kriviek ponúkajú mnoho atraktívnych funkcií, ako sú intuitívne používateľské rozhrania založené na Windowse, IV, CV a generovanie impulzov a impulz IV, knižnice aplikácií zahrnuté pre každú technológiu... atď. TESTER / INDIKÁTOR OTÁČANIA FÁZ: Ide o kompaktné a odolné testovacie prístroje na identifikáciu sledu fáz na trojfázových systémoch a otvorených/bez napätia. Sú ideálne na inštaláciu rotačných strojov, motorov a na kontrolu výkonu generátora. Medzi aplikácie patrí identifikácia správnych sledov fáz, detekcia chýbajúcich fáz vodičov, určenie správnych spojení pre rotujúce stroje, detekcia živých obvodov. FREKVENČNÝ POČÍTAČ je testovací prístroj, ktorý sa používa na meranie frekvencie. Frekvenčné počítadlá vo všeobecnosti používajú počítadlo, ktoré akumuluje počet udalostí vyskytujúcich sa v určitom časovom období. Ak je udalosť, ktorá sa má počítať, v elektronickej forme, stačí jednoduché prepojenie s prístrojom. Signály vyššej zložitosti môžu potrebovať určitú úpravu, aby boli vhodné na počítanie. Väčšina frekvenčných čítačov má na vstupe nejakú formu zosilňovača, filtrovania a tvarovania. Digitálne spracovanie signálu, riadenie citlivosti a hysterézia sú ďalšie techniky na zlepšenie výkonu. Iné typy periodických udalostí, ktoré nie sú svojou povahou elektronické, bude potrebné previesť pomocou prevodníkov. VF frekvenčné počítadlá pracujú na rovnakom princípe ako nízkofrekvenčné počítadlá. Pred pretečením majú väčší dosah. Pre veľmi vysoké mikrovlnné frekvencie mnoho návrhov používa vysokorýchlostnú preddeličku na zníženie frekvencie signálu na bod, kde môže fungovať normálny digitálny obvod. Mikrovlnné frekvenčné čítače dokážu merať frekvencie až do takmer 100 GHz. Nad týmito vysokými frekvenciami sa meraný signál kombinuje v zmiešavači so signálom z lokálneho oscilátora, čím sa vytvára signál s rozdielovou frekvenciou, ktorá je dostatočne nízka na priame meranie. Obľúbenými rozhraniami na frekvenčných čítačoch sú RS232, USB, GPIB a Ethernet podobne ako v iných moderných prístrojoch. Okrem odosielania výsledkov merania môže počítadlo upozorniť používateľa na prekročenie limitov merania definovaných používateľom. Podrobnosti a ďalšie podobné vybavenie nájdete na našej webovej stránke o vybavení: http://www.sourceindustrialsupply.com For other similar equipment, please visit our equipment website: http://www.sourceindustrialsupply.com CLICK Product Finder-Locator Service PREDCHÁDZAJÚCA STRANA
- Laser Machining, LM, Laser Cutting, CO2 Laser Processing, Nd-YAG Cut
Laser Machining - LM - Laser Cutting - Custom Parts Manufacturing - CO2 Laser Processing - Nd-YAG - Cutting - Boring Laserové obrábanie a rezanie a LBM aaplikácie LASER CUTTING is a HIGH-ENERGY-BEAM MANUFACTURING_cc-783d-výroba materiálov, pri ktorých sa používa laserové rezanie53bc-913-zlé materiály bbcf513bad. In LASER BEAM MACHINING (LBM), laserový zdroj sústreďuje optickú energiu na povrch obrobku. Laserové rezanie smeruje vysoko sústredený a vysokohustotný výstup vysokovýkonného lasera pomocou počítača na materiál, ktorý sa má rezať. Cielený materiál sa potom buď roztopí, spáli, vyparí alebo je odfúknutý prúdom plynu riadeným spôsobom, pričom zanechá hranu s vysoko kvalitnou povrchovou úpravou. Naše priemyselné laserové rezačky sú vhodné na rezanie plochých materiálov, ako aj konštrukčných a potrubných materiálov, kovových a nekovových obrobkov. Vo všeobecnosti nie je v procese obrábania a rezania laserovým lúčom potrebné žiadne vákuum. Pri rezaní a výrobe laserom sa používa niekoľko typov laserov. Pulzná alebo kontinuálna vlna CO2 LASER je vhodná na rezanie, vyvrtávanie a gravírovanie. The NEODYMIUM (Nd) and neodymium yttrium-aluminum-garnet (Nd-YAG) LASERS are identical v štýle a líšia sa len aplikáciou. Neodymový Nd sa používa na vyvrtávanie a tam, kde sa vyžaduje vysoká energia, ale nízka úroveň opakovania. Nd-YAG laser sa na druhej strane používa tam, kde sa vyžaduje veľmi vysoký výkon a na vyvrtávanie a gravírovanie. CO2 aj Nd/Nd-YAG lasery možno použiť na LASER WELDING. Medzi ďalšie lasery, ktoré používame pri výrobe patria Nd:GLASS, RUBY a EXCIMER. Pri obrábaní laserovým lúčom (LBM) sú dôležité tieto parametre: Odrazivosť a tepelná vodivosť povrchu obrobku a jeho špecifické teplo a latentné teplo tavenia a vyparovania. Efektívnosť procesu laserového obrábania (LBM) stúpa so znižovaním týchto parametrov. Hĺbka rezu môže byť vyjadrená ako: t ~ P / (vxd) To znamená, že hĺbka rezu „t“ je úmerná príkonu P a nepriamo úmerná rýchlosti rezu v a priemeru bodu laserového lúča d. Povrch vyrobený pomocou LBM je vo všeobecnosti drsný a má tepelne ovplyvnenú zónu. REZANIE A OBRÁBENIE LASEROM OXIDU UHLIČITÉHO (CO2): CO2 lasery s jednosmerným budením sa čerpajú prechodom prúdu cez zmes plynov, zatiaľ čo lasery s vysokofrekvenčným budením CO2 využívajú na budenie rádiofrekvenčnú energiu. Metóda RF je relatívne nová a stala sa populárnejšou. DC konštrukcie vyžadujú elektródy vo vnútri dutiny, a preto môžu mať elektródovú eróziu a pokovovanie elektródovým materiálom na optike. Naopak, RF rezonátory majú externé elektródy, a preto nie sú náchylné na tieto problémy. CO2 lasery používame pri priemyselnom rezaní mnohých materiálov, ako je mäkká oceľ, hliník, nehrdzavejúca oceľ, titán a plasty. YAG LASEROVÉ CUTTING and OBRÁBENIE: Na rezanie a ryhovanie kovov a keramiky používame YAG lasery. Laserový generátor a externá optika vyžadujú chladenie. Odpadové teplo sa vytvára a prenáša chladivom alebo priamo do vzduchu. Voda je bežné chladivo, ktoré zvyčajne cirkuluje cez chladič alebo systém prenosu tepla. REZANIE A OBRÁBENIE EXCIMEROVÝM LASEROM: Excimerový laser je druh lasera s vlnovými dĺžkami v ultrafialovej oblasti. Presná vlnová dĺžka závisí od použitých molekúl. Napríklad nasledujúce vlnové dĺžky sú spojené s molekulami uvedenými v zátvorkách: 193 nm (ArF), 248 nm (KrF), 308 nm (XeCl), 353 nm (XeF). Niektoré excimerové lasery sú laditeľné. Excimerové lasery majú atraktívnu vlastnosť, že dokážu odstrániť veľmi jemné vrstvy povrchového materiálu takmer bez zahrievania alebo zmeny zvyšku materiálu. Preto sú excimerové lasery vhodné na presné mikroobrábanie organických materiálov, ako sú niektoré polyméry a plasty. REZANIE LASEROM S POMOCOU PLYNU: Niekedy používame laserové lúče v kombinácii s prúdom plynu, ako je kyslík, dusík alebo argón na rezanie tenkých plechových materiálov. Toto sa vykonáva pomocou a LASER-BEAM TORCH. Pre nehrdzavejúcu oceľ a hliník používame vysokotlakové rezanie laserom s inertným plynom pomocou dusíka. Výsledkom sú hrany bez oxidov na zlepšenie zvárateľnosti. Tieto prúdy plynu tiež odfukujú roztavený a vyparovaný materiál z povrchov obrobku. V a LASER MICROJET CUTTING máme vodným lúčom navádzaný laser, v ktorom je pulzovaný vodný lúč spojený s nízkym tlakom. Používame ho na rezanie laserom, pričom vodným lúčom vedieme laserový lúč podobne ako optické vlákno. Výhody laserového mikrojetu spočívajú v tom, že voda tiež odstraňuje nečistoty a ochladzuje materiál, je rýchlejšie ako tradičné „suché“ rezanie laserom s vyššou rýchlosťou rezania kociek, paralelným rezom a všesmerovým rezaním. Používame rôzne metódy rezania pomocou laserov. Niektoré z metód sú odparovanie, tavenie a vyfukovanie, vyfukovanie a vypaľovanie taveniny, praskanie tepelným napätím, ryhovanie, rezanie za studena a vypaľovanie, stabilizované rezanie laserom. - Rezanie odparovaním: Sústredený lúč zahreje povrch materiálu na jeho bod varu a vytvorí otvor. Otvor vedie k náhlemu zvýšeniu nasiakavosti a rýchlo prehĺbi otvor. Keď sa diera prehlbuje a materiál vrie, vytvorená para eroduje roztavené steny, vyfukuje materiál von a ďalej zväčšuje dieru. Touto metódou sa zvyčajne režú netaviteľné materiály, ako je drevo, uhlík a termosetové plasty. - Rezanie tavením a vyfukovaním: Na vyfukovanie roztaveného materiálu z oblasti rezu používame vysokotlakový plyn, čím sa znižuje potrebný výkon. Materiál sa zahreje na teplotu topenia a potom prúd plynu vyfúkne roztavený materiál z rezu. To eliminuje potrebu ďalšieho zvyšovania teploty materiálu. Touto technikou režeme kovy. - Trhanie pri tepelnom namáhaní: Krehké materiály sú citlivé na tepelné lomy. Lúč je zaostrený na povrch, čo spôsobuje lokálne zahrievanie a tepelnú rozťažnosť. To má za následok trhlinu, ktorá môže byť potom vedená pohybom lúča. Túto techniku používame pri rezaní skla. - Neviditeľné krájanie kremíkových plátkov: Oddelenie mikroelektronických čipov od kremíkových plátkov sa vykonáva procesom utajeného krájania pomocou pulzného Nd:YAG lasera, vlnová dĺžka 1064 nm je dobre prispôsobená elektronickému zakázanému pásmu kremíka (1,11 eV resp. 1117 nm). Toto je populárne pri výrobe polovodičových zariadení. - Reaktívne rezanie: Tiež nazývané rezanie plameňom, táto technika môže byť podobná rezaniu kyslíkovým horákom, ale s laserovým lúčom ako zdrojom vznietenia. Používame ho na rezanie uhlíkovej ocele s hrúbkou nad 1 mm a dokonca aj veľmi hrubých oceľových plechov s malým výkonom lasera. PULSED LASERS poskytujú nám vysokovýkonný výboj energie na krátku dobu a sú veľmi účinné pri niektorých procesoch laserového rezania, ako je dierovanie, alebo keď sú potrebné veľmi malé otvory alebo veľmi nízke rezné rýchlosti. Ak by sa namiesto toho použil konštantný laserový lúč, teplo by mohlo dosiahnuť bod roztavenia celého obrábaného kusu. Naše lasery majú schopnosť pulzovať alebo rezať CW (Continuous Wave) pod NC (numerické riadenie) programovým riadením. Používame DOUBLE PULSE LASERS vyžarujúce sériu párov impulzov na zlepšenie rýchlosti úberu materiálu a kvality otvoru. Prvý impulz odoberá materiál z povrchu a druhý impulz bráni vyvrhnutému materiálu, aby sa prilepil na stranu otvoru alebo rezu. Tolerancie a povrchová úprava pri laserovom rezaní a obrábaní sú vynikajúce. Naše moderné laserové rezačky majú presnosť polohovania v blízkosti 10 mikrometrov a opakovateľnosť 5 mikrometrov. Štandardné drsnosti Rz sa zvyšujú s hrúbkou plechu, ale klesajú s výkonom lasera a rýchlosťou rezania. Procesy laserového rezania a obrábania sú schopné dosahovať tesné tolerancie, často s presnosťou 0,001 palca (0,025 mm) Geometria dielu a mechanické vlastnosti našich strojov sú optimalizované na dosiahnutie najlepších tolerančných schopností. Povrchové úpravy, ktoré môžeme získať rezaním laserovým lúčom, sa môžu pohybovať od 0,003 mm do 0,006 mm. Vo všeobecnosti ľahko dosiahneme otvory s priemerom 0,025 mm a otvory už od 0,005 mm a pomery hĺbky k priemeru otvoru 50 ku 1 boli vyrobené z rôznych materiálov. Naše najjednoduchšie a najštandardnejšie laserové rezačky budú rezať kov z uhlíkovej ocele s hrúbkou 0,020 – 0,5 palca (0,51 – 13 mm) a môžu byť ľahko až tridsaťkrát rýchlejšie ako štandardné pílenie. Obrábanie laserovým lúčom sa široko používa na vŕtanie a rezanie kovov, nekovov a kompozitných materiálov. Medzi výhody rezania laserom oproti mechanickému rezaniu patrí jednoduchšie držanie obrobku, čistota a znížené znečistenie obrobku (keďže tu nie je rezná hrana ako pri tradičnom frézovaní alebo sústružení, ktorá by sa mohla znečistiť materiálom alebo znečistiť materiál, napr. nánosy). Abrazívna povaha kompozitných materiálov môže sťažiť ich obrábanie konvenčnými metódami, ale ľahké obrábanie laserom. Pretože sa laserový lúč počas procesu neopotrebováva, získaná presnosť môže byť lepšia. Pretože laserové systémy majú malú zónu ovplyvnenú teplom, je tu tiež menšia šanca na deformáciu materiálu, ktorý je rezaný. Pre niektoré materiály môže byť laserové rezanie jedinou možnosťou. Procesy rezania laserovým lúčom sú flexibilné a dodávanie lúčov z optických vlákien, jednoduché upevnenie, krátke časy nastavenia, dostupnosť trojrozmerných CNC systémov umožňujú laserovému rezaniu a obrábaniu úspešne konkurovať iným procesom výroby plechov, ako je dierovanie. Ako už bolo povedané, laserová technológia môže byť niekedy kombinovaná s technológiami mechanickej výroby na zlepšenie celkovej účinnosti. Laserové rezanie plechov má výhody oproti plazmovému rezaniu v tom, že je presnejšie a využíva menej energie, avšak väčšina priemyselných laserov nedokáže prerezať väčšiu hrúbku kovu ako plazma. Lasery pracujúce pri vyšších výkonoch, ako je napríklad 6000 wattov, sa približujú plazmovým strojom v ich schopnosti prerezávať hrubé materiály. Avšak kapitálové náklady týchto 6000 W laserových rezačiek sú oveľa vyššie ako náklady na plazmové rezacie stroje schopné rezať hrubé materiály, ako je oceľový plech. Existujú aj nevýhody laserového rezania a obrábania. Laserové rezanie zahŕňa vysokú spotrebu energie. Účinnosť priemyselného lasera sa môže pohybovať od 5 % do 15 %. Spotreba energie a účinnosť každého konkrétneho lasera sa bude líšiť v závislosti od výstupného výkonu a prevádzkových parametrov. To bude závisieť od typu lasera a od toho, ako dobre sa laser zhoduje s vykonávanou prácou. Množstvo laserového rezného výkonu potrebného pre konkrétnu úlohu závisí od typu materiálu, hrúbky, použitého procesu (reaktívneho/inertného) a požadovanej rýchlosti rezania. Maximálna rýchlosť výroby pri rezaní a obrábaní laserom je obmedzená množstvom faktorov vrátane výkonu lasera, typu procesu (či už reaktívneho alebo inertného), vlastností materiálu a hrúbky. In LASER ABLATION odstraňujeme materiál z pevného povrchu ožiarením laserovým lúčom. Pri nízkom laserovom toku sa materiál ohrieva absorbovanou laserovou energiou a vyparuje sa alebo sublimuje. Pri vysokom laserovom toku sa materiál zvyčajne premieňa na plazmu. Vysokovýkonné lasery vyčistia veľké miesto jediným impulzom. Lasery s nižším výkonom používajú veľa malých impulzov, ktoré možno skenovať cez oblasť. Pri laserovej ablácii odoberáme materiál pulzným laserom alebo kontinuálnym laserovým lúčom, ak je intenzita lasera dostatočne vysoká. Impulzné lasery dokážu vyvŕtať extrémne malé, hlboké otvory cez veľmi tvrdé materiály. Veľmi krátke laserové impulzy odstraňujú materiál tak rýchlo, že okolitý materiál absorbuje veľmi málo tepla, preto je možné laserové vŕtanie vykonávať aj na jemných alebo tepelne citlivých materiáloch. Laserová energia môže byť selektívne absorbovaná nátermi, preto CO2 a Nd:YAG pulzné lasery môžu byť použité na čistenie povrchov, odstraňovanie náterov a náterov alebo prípravu povrchov na náter bez poškodenia podkladového povrchu. We use LASER ENGRAVING and LASER MARKING to engrave or mark an object. Tieto dve techniky sú v skutočnosti najpoužívanejšie aplikácie. Nepoužívajú sa žiadne atramenty ani sa netýkajú nástavcov nástrojov, ktoré sa dotýkajú gravírovaného povrchu a opotrebúvajú sa, čo je prípad tradičných metód mechanického gravírovania a označovania. Medzi materiály špeciálne navrhnuté na laserové gravírovanie a značenie patria polyméry citlivé na laser a špeciálne nové zliatiny kovov. Hoci sú zariadenia na laserové značenie a gravírovanie relatívne drahšie v porovnaní s alternatívami, ako sú dierovače, špendlíky, dotykové perá, leptacie pečiatky... atď., stali sa obľúbenejšími vďaka svojej presnosti, reprodukovateľnosti, flexibilite, jednoduchosti automatizácie a online aplikácii. v širokej škále výrobných prostredí. Nakoniec používame laserové lúče pre niekoľko ďalších výrobných operácií: - LASEROVÉ ZVÁRANIE - TEPELNÉ OŠETRENIE LASEROM: Drobné tepelné spracovanie kovov a keramiky na úpravu ich povrchových mechanických a tribologických vlastností. - LASEROVÁ POVRCHOVÁ ÚPRAVA / ÚPRAVA: Lasery sa používajú na čistenie povrchov, zavádzanie funkčných skupín, úpravu povrchov v snahe zlepšiť priľnavosť pred nanášaním povlaku alebo procesom spájania. CLICK Product Finder-Locator Service PREDCHÁDZAJÚCA STRANA
- Microwave Components & Subassembly, Microwave Circuits, RF Transformer
Microwave Components - Subassembly - Microwave Circuits - RF Transformer - LNA - Mixer - Fixed Attenuator - AGS-TECH Výroba a montáž mikrovlnných komponentov a systémov Vyrábame a dodávame: Mikrovlnná elektronika vrátane silikónových mikrovlnných diód, bodových dotykových diód, Schottkyho diód, PIN diód, varaktorových diód, stupňovitých obnovovacích diód, mikrovlnných integrovaných obvodov, rozdeľovačov/kombinátorov, zmiešavačov, smerových spojok, detektorov, I/Q modulátorov, filtrov, pevných atenuátorov, RF transformátory, simulačné posúvače fázy, LNA, PA, spínače, atenuátory a obmedzovače. Na mieru vyrábame aj mikrovlnné podzostavy a zostavy podľa požiadaviek užívateľov. Stiahnite si naše brožúry o komponentoch a systémoch pre mikrovlnné rúry z nižšie uvedených odkazov: RF a mikrovlnné komponenty Mikrovlnné vlnovody - Koaxiálne komponenty - Milimetrové antény 5G - LTE 4G - LPWA 3G - 2G - GPS - GNSS - WLAN - BT - Combo - Brožúra o anténe ISM Mäkké ferity - Jadrá - Toroidy - Produkty na potlačenie EMI - RFID transpondéry a brožúra príslušenstva Stiahnite si brožúru pre naše PROGRAM DIZAJNOVÉHO PARTNERSTVA Mikrovlny sú elektromagnetické vlny s vlnovými dĺžkami od 1 mm do 1 m alebo s frekvenciami medzi 0,3 GHz a 300 GHz. Mikrovlnný rozsah zahŕňa ultravysokú frekvenciu (UHF) (0,3–3 GHz), super vysokú frekvenciu (SHF) (3– 30 GHz) a extrémne vysokofrekvenčné (EHF) (30–300 GHz). Využitie mikrovlnnej technológie: KOMUNIKAČNÉ SYSTÉMY: Pred vynálezom technológie prenosu optických vlákien sa väčšina diaľkových telefónnych hovorov uskutočňovala prostredníctvom mikrovlnných spojení bod-bod cez stránky ako AT&T Long Lines. Od začiatku 50-tych rokov sa frekvenčné multiplexovanie používalo na odoslanie až 5 400 telefónnych kanálov na každý mikrovlnný rádiový kanál, pričom až desať rádiových kanálov skombinovaných do jednej antény pre skok na ďalšie miesto, ktoré bolo vzdialené až 70 km. . Protokoly bezdrôtovej siete LAN, ako napríklad Bluetooth a špecifikácie IEEE 802.11, tiež používajú mikrovlny v pásme 2,4 GHz ISM, hoci 802.11a používa pásmo ISM a frekvencie U-NII v pásme 5 GHz. Licencované služby bezdrôtového prístupu na internet s dlhým dosahom (do približne 25 km) možno nájsť v mnohých krajinách v pásme 3,5 – 4,0 GHz (nie však v USA). Metropolitan Area Networks: Protokoly MAN, ako napríklad WiMAX (Worldwide Interoperability for Microwave Access) založené na špecifikácii IEEE 802.16. Špecifikácia IEEE 802.16 bola navrhnutá tak, aby fungovala medzi 2 až 11 GHz frekvenciami. Komerčné implementácie sú vo frekvenčných rozsahoch 2,3 GHz, 2,5 GHz, 3,5 GHz a 5,8 GHz. Širokopásmový mobilný širokopásmový bezdrôtový prístup: Protokoly MBWA založené na štandardných špecifikáciách, ako je IEEE 802.20 alebo ATIS/ANSI HC-SDMA (napr. iBurst) sú navrhnuté tak, aby fungovali medzi 1,6 a 2,3 GHz, aby poskytli mobilitu a charakteristiky prieniku do budovy podobné mobilným telefónom. ale s oveľa väčšou spektrálnou účinnosťou. Časť nižšieho mikrovlnného frekvenčného spektra sa používa na káblovej televízii a prístupe na internet cez koaxiálny kábel, ako aj na televízne vysielanie. Niektoré siete mobilných telefónov, ako napríklad GSM, tiež používajú nižšie mikrovlnné frekvencie. Mikrovlnné rádio sa používa vo vysielaní a telekomunikačných prenosoch, pretože vysoko direktívne antény sú vďaka svojej krátkej vlnovej dĺžke menšie a teda praktickejšie, ako by boli pri nižších frekvenciách (dlhšie vlnové dĺžky). V mikrovlnnom spektre je tiež väčšia šírka pásma ako vo zvyšku rádiového spektra; využiteľná šírka pásma pod 300 MHz je menšia ako 300 MHz, zatiaľ čo mnohé GHz možno použiť nad 300 MHz. Mikrovlny sa zvyčajne používajú v televíznom spravodajstve na prenos signálu zo vzdialeného miesta do televíznej stanice v špeciálne vybavenej dodávke. Pásma C, X, Ka alebo Ku mikrovlnného spektra sa používajú pri prevádzke väčšiny satelitných komunikačných systémov. Tieto frekvencie umožňujú veľkú šírku pásma, pričom sa vyhýbajú preplneným UHF frekvenciám a zostávajú pod atmosférickou absorpciou EHF frekvencií. Satelitná televízia funguje buď v pásme C pre tradičnú veľkú anténu Pevná satelitná služba alebo v pásme Ku pre satelit s priamym vysielaním. Vojenské komunikačné systémy bežia primárne cez spojenia X alebo Ku Band, pričom pásmo Ka sa používa pre Milstar. DIAĽKOVÝ SNÍMAČ: Radary využívajú mikrovlnné frekvenčné žiarenie na detekciu dosahu, rýchlosti a iných charakteristík vzdialených objektov. Radary sú široko používané v aplikáciách vrátane riadenia letovej prevádzky, navigácie lodí a kontroly obmedzenia rýchlosti dopravy. Okrem ultrazvukových snímačov sa niekedy Gunnove diódové oscilátory a vlnovody používajú ako detektory pohybu pre automatické otvárače dverí. Veľká časť rádioastronómie využíva mikrovlnnú technológiu. NAVIGAČNÉ SYSTÉMY: Globálne navigačné satelitné systémy (GNSS) vrátane amerického globálneho pozičného systému (GPS), čínskeho Beidou a ruského GLONASS vysielajú navigačné signály v rôznych pásmach medzi približne 1,2 GHz a 1,6 GHz. MOC: Mikrovlnná rúra prechádza (neionizujúce) mikrovlnné žiarenie (s frekvenciou blízkou 2,45 GHz) cez potraviny, čo spôsobuje dielektrické zahrievanie absorpciou energie vo vode, tukoch a cukroch obsiahnutých v potravinách. Mikrovlnné rúry sa stali bežnými po vývoji lacných dutinových magnetrónov. Mikrovlnný ohrev je široko používaný v priemyselných procesoch na sušenie a vytvrdzovanie produktov. Mnoho techník spracovania polovodičov používa mikrovlny na generovanie plazmy na účely, ako je reaktívne iónové leptanie (RIE) a plazma-enhanced chemical vapor deposition (PECVD). Mikrovlny možno použiť na prenos energie na veľké vzdialenosti. NASA pracovala v 70. a začiatkom 80. rokov na výskume možností využitia systémov Solar Power Satellite (SPS) s veľkými solárnymi poľami, ktoré by prenášali energiu na zemský povrch prostredníctvom mikrovĺn. Niektoré ľahké zbrane používajú milimetrové vlny na zahriatie tenkej vrstvy ľudskej kože na netolerovateľnú teplotu, aby sa cieľová osoba vzdialila. Dvojsekundový impulz zaostreného lúča 95 GHz zahreje pokožku na teplotu 54 °C v hĺbke 1/64 palca (0,4 mm). Letectvo a námorná pechota Spojených štátov používajú tento typ systému aktívneho odmietnutia. Ak máte záujem o inžinierstvo a výskum a vývoj, navštívte našu stránku inžinierstva http://www.ags-engineering.com CLICK Product Finder-Locator Service PREDCHÁDZAJÚCA STRANA
- Mesh & Wire, USA, AGS-TECH Inc.
We supply wire and wire mesh, galvanized wires, metal wire, black annealed wire, wire mesh filters, wire cloth, perforated metal mesh, wire mesh fence and panels, conveyor belt mesh, wire mesh containers and customized wire mesh products to your specifications. Sieťovina a drôt Dodávame výrobky z drôtu a pletiva vrátane pozinkovaných železných drôtov, viazacích drôtov zo železa potiahnutých PVC, drôteného pletiva, drôteného pletiva, oplotenie drôtov, pletiva dopravníkových pásov, perforované kovové pletivo. Okrem našich hotových produktov z drôteného pletiva vyrábame pletivo na mieru a metal drôtené produkty podľa vašich špecifikácií a potrieb. Režeme na požadovanú veľkosť, etiketu a balenie podľa požiadaviek zákazníka. Kliknite na nižšie uvedené podponuky a prečítajte si viac o konkrétnom produkte z drôtu a pletiva. Pozinkované drôty a kovové drôty Tieto drôty sa používajú v mnohých aplikáciách v celom priemysle. Napríklad pozinkované železné drôty sa často používajú na účely viazania a pripevnenia ako laná so značnou pevnosťou v ťahu. Tieto kovové drôty môžu byť žiarovo pozinkované a majú kovový vzhľad alebo môžu byť potiahnuté PVC a môžu byť farbené. Ostnaté drôty majú rôzne typy holiacich strojčekov a používajú sa na udržanie votrelcov mimo obmedzených oblastí. Na sklade sú k dispozícii rôzne meradlá drôtov. Dlhé drôty come v cievkach. Ak to množstvo oprávňuje, môžeme ich vyrobiť vo vami požadovaných dĺžkach a rozmeroch cievok. Vlastné označovanie a balenie našich pozinkovaných drôtov, Metal Wires, Barbed Wire je možné. Stiahnite si brožúry: - Kovové drôty - Pozinkované - Čierne žíhané Filtre z drôteného pletiva Tieto sú väčšinou vyrobené z tenkého drôteného pletiva z nehrdzavejúcej ocele a široko používané v priemysle ako filtre na filtrovanie kvapalín, prachu, práškov... atď. Filtre z drôteného pletiva majú hrúbku v rozmedzí niekoľkých milimetrov. AGS-TECH dosiahla výrobu drôteného pletiva s priemerom drôtu menším ako 1 mm pre elektromagnetické tienenie vojenských námorných osvetľovacích systémov. Vyrábame drôtené filtre s rozmermi podľa špecifikácií zákazníka. Štvorcové, okrúhle a oválne sú bežne používané geometrie. Priemery drôtov a počet ôk našich filtrov si môžete vybrať sami. Narežeme ich na mieru a okraje orámujeme, aby sa sieťka filtra neskreslila alebo nepoškodila. Naše filtre z drôteného pletiva majú vysokú namáhateľnosť, dlhú životnosť, pevné a spoľahlivé okraje. Niektoré oblasti použitia našich drôtených filtrov sú chemický priemysel, farmaceutický priemysel, pivovarníctvo, nápoje, elektromagnetické tienenie, automobilový priemysel, mechanické aplikácie atď. - Brožúra z drôteného pletiva a látky (obsahuje drôtené filtre) Perforovaná kovová sieťovina Naše dierované plechy sú vyrábané z pozinkovanej ocele, nízkouhlíkovej ocele, nehrdzavejúcej ocele, medených plechov, niklových plechov alebo podľa požiadaviek zákazníka. Rôzne hole tvary a vzory môžu byť vyrazené podľa vášho želania. Naša perforovaná kovová sieť ponúka hladkosť, dokonalú rovinnosť povrchu, pevnosť a odolnosť a je vhodná pre mnoho aplikácií. Dodaním perforovaného kovového pletiva sme splnili potreby mnohých priemyselných odvetví a aplikácií vrátane vnútornej zvukovej izolácie, výroby tlmičov, baníctva, medicíny, spracovania potravín, vetrania, skladovania v poľnohospodárstve, mechanickej ochrany a ďalších. Zavolajte nám ešte dnes. Vašu perforovanú kovovú sieť s radosťou narežeme, vyrazíme, ohneme, vyrobíme podľa Vašich predstáv a potrieb. - Brožúra z drôteného pletiva a látky (obsahuje perforovanú kovovú sieťku) Plot z drôteného pletiva, panely a výstuž Drôtené pletivo je široko používané v stavebníctve, krajinnom dizajne, domácich úpravách, záhradníctve, stavbe ciest... atď., s populárne aplikácie drôteného pletiva ako plotové a výstužné panely v stavebníctve._cc781905-5cde-3194- bb3b-136bad5cf58d_Pozrite si naše brožúry na stiahnutie nižšie a vyberte si svoj preferovaný model otvárania pletiva, prierez drôtu, farbu a povrchovú úpravu. Všetky naše drôtené ploty a panely a výstužné produkty sú v súlade s medzinárodnými priemyselnými normami. Na sklade sú k dispozícii rôzne plotové konštrukcie z drôteného pletiva. - Brožúra z drôteného pletiva a látky (zahŕňa informácie o našom plote a paneloch a výstuži) Sieťka na dopravný pás Naša sieť dopravných pásov je zvyčajne vyrobená z vystuženého drôtu z nehrdzavejúcej ocele, drôtu z nehrdzavejúcej ocele, drôtu z nichrómu, drôtu s guľkou. Aplikácie sieťoviny dopravníkového pásu sú ako filter a ako dopravný pás na použitie v chemickom priemysle, ropa, hutníctvo, potravinárstvo, farmácia, sklársky priemysel, dodávka dielov v rámci závodu alebo zariadenia... atď. Weave Style väčšiny sietí dopravníkových pásov je predbežné ohýbanie na pružinu a potom vloženie drôtu. Priemery drôtov sú všeobecne: 0,8-2,5 mm Hrúbka drôtu je všeobecne: 5-13,2 mm Bežné farby sú vo všeobecnosti: Silver Vo všeobecnosti je šírka medzi 0,4 m - 3 m a dĺžka je medzi 0,5 - 100 m Sieťovina dopravného pásu je odolná voči teplu Typ reťaze, šírka a dĺžka pletiva dopravného pásu patrí medzi prispôsobiteľné parametre. - Brožúra z drôteného pletiva a látky (zahŕňa všeobecné informácie o našich možnostiach) Výrobky z drôteného pletiva na mieru (ako sú káblové žľaby, strmene.... atď.) Z drôteného pletiva a perforovaného kovového pletiva vieme vyrobiť rôzne zákazkové produkty, ako sú káblové žľaby, miešadlá, Faradayove klietky a EM tieniace konštrukcie, drôtené koše a vaničky, architektonické predmety, umelecké predmety, rukavice z oceľového pletiva používané v mäsovom priemysle na ochranu pred úrazmi...atď. Naše prispôsobené drôtené pletivo, perforované kovy a ťahokovy môžu byť narezané na veľkosť a sploštené pre vašu požadovanú aplikáciu. Sploštené drôtené pletivo sa bežne používa ako kryty strojov, ventilačné sitá, sitá horákov, bezpečnostné sitá, sitá na odvod kvapalín, stropné panely a mnoho ďalších aplikácií. Môžeme vytvoriť prispôsobené perforované kovy s tvarmi a veľkosťami otvorov, aby vyhovovali vašim požiadavkám na projekt a produkt. Dierované kovy majú všestranné využitie. Môžeme tiež poskytnúť potiahnuté drôtené pletivo. Nátery môžu zlepšiť životnosť vašich prispôsobených výrobkov z drôteného pletiva a tiež poskytnúť bariéru odolnú voči hrdzi. Vlastné nátery z drôteného pletiva zahŕňajú práškové lakovanie, elektrické leštenie, žiarové zinkovanie, nylon, lakovanie, hliníkovanie, elektrogalvanické zinkovanie, PVC, Kevlar atď. Či už sú tkané z drôtu ako prispôsobené drôtené pletivo, alebo lisované, dierované a sploštené z plechu ako perforované plechy, kontaktujte AGS-TECH pre vaše prispôsobené požiadavky na produkt. - Brožúra z drôteného pletiva a látky (zahŕňa veľa informácií o našich prispôsobených možnostiach výroby drôteného pletiva) - Brožúra káblových žľabov a košov z drôteného pletiva (okrem produktov v tejto brožúre môžete získať prispôsobené káblové žľaby podľa vašich špecifikácií) - Formulár cenovej ponuky pre kontajner z drôteného pletiva (kliknite na stiahnutie, vyplňte a pošlite nám e-mail) PREDCHÁDZAJÚCA STRANA
- Brazing, Soldering, Welding, Joining Processes, Assembly Services
Brazing - Soldering - Welding - Joining Processes - Assembly Services - Subassemblies - Assemblies - Custom Manufacturing - AGS-TECH Inc. - NM - USA Spájkovanie a zváranie Spomedzi mnohých techník SPÁJANIA, ktoré používame vo výrobe, sa osobitný dôraz kladie na ZVÁRANIE, SPÁJKOVANIE, SPÁJOVANIE, LEPENIE a MECHANICKÁ MONTÁŽ NA MIERU, pretože tieto techniky sa široko používajú v aplikáciách, ako je výroba hermetických zostáv, výroba špičkových produktov a špecializované tesnenie. Tu sa zameriame na špecializovanejšie aspekty týchto spájacích techník, keďže súvisia s výrobou pokročilých produktov a zostáv. FÚZNE ZVÁRANIE: Na roztavenie a spájanie materiálov využívame teplo. Teplo je dodávané elektrinou alebo vysokoenergetickými lúčmi. Typy tavného zvárania, ktoré nasadzujeme, sú ZVÁRANIE PLYNOVÝM PLYNOM, OBUKOVÉ ZVÁRANIE, VYSOKOENERGETICKÉ ZVÁRANIE LÚČOM. PEVNÉ ZVÁRANIE: Diely spájame bez tavenia a tavenia. Naše metódy zvárania v tuhom stave sú ZVÁRANIE STUDENÉ, ULTRAZVUKOVÉ, ODPOROVÉ, TRENÉ, EXPLOZNÉ ZVÁRANIE a DIFÚZNE ZVÁRANIE. SPÁJKOVANIE A SPÁJKOVANIE: Používajú prídavné kovy a poskytujú nám výhodu práce pri nižších teplotách ako pri zváraní, čím sa znižuje štrukturálne poškodenie výrobkov. Informácie o našom zariadení na spájkovanie, ktoré vyrába armatúry z keramiky na kov, hermetické tesnenia, vákuové priechodky, komponenty na riadenie vysokého a ultravysokého vákua a tekutiny nájdete tu:Brožúra továrne na spájkovanie LEPENIE LEPIDLA: Kvôli rôznorodosti lepidiel používaných v priemysle a tiež rôznorodosti aplikácií máme na to vyhradenú stránku. Ak chcete prejsť na našu stránku o lepení, kliknite sem. MECHANICKÁ MONTÁŽ NA MIERU: Používame rôzne upevňovacie prvky, ako sú skrutky, skrutky, matice, nity. Naše spojovacie prvky nie sú obmedzené na štandardné spojovacie prvky. Navrhujeme, vyvíjame a vyrábame špeciálne spojovacie prvky, ktoré sú vyrobené z neštandardných materiálov tak, aby spĺňali požiadavky pre špeciálne aplikácie. Niekedy je požadovaná elektrická alebo tepelná nevodivosť, zatiaľ čo niekedy vodivosť. Pre niektoré špeciálne aplikácie môže zákazník chcieť špeciálne spojovacie prvky, ktoré nemožno odstrániť bez zničenia produktu. Nápadov a aplikácií je nekonečne veľa. Máme to všetko pre vás, ak nie zo skladu, môžeme to rýchlo vyvinúť. Ak chcete prejsť na našu stránku o mechanickej montáži, kliknite sem . Preskúmajte naše rôzne techniky spájania podrobnejšie. ZVÁRANIE OXYFUEL GAS (OFW): Na vytvorenie zváracieho plameňa používame palivový plyn zmiešaný s kyslíkom. Keď používame acetylén ako palivo a kyslík, nazývame to zváranie kyslíkom a acetylénom. V procese spaľovania kyslíka a paliva prebiehajú dve chemické reakcie: C2H2 + O2 ------» 2CO + H2 + Teplo 2CO + H2 + 1,5 O2--------» 2 CO2 + H2O + teplo Prvá reakcia rozdeľuje acetylén na oxid uhoľnatý a vodík, pričom produkuje asi 33 % celkového vytvoreného tepla. Druhý vyššie uvedený proces predstavuje ďalšie spaľovanie vodíka a oxidu uhoľnatého pri výrobe asi 67 % celkového tepla. Teploty v plameni sú medzi 1533 až 3573 Kelvinmi. Percento kyslíka v zmesi plynov je dôležité. Ak je obsah kyslíka viac ako polovica, plameň sa stáva oxidačným činidlom. To je nežiaduce pre niektoré kovy, ale žiaduce pre iné. Príkladom, kedy je žiaduci oxidačný plameň, sú zliatiny na báze medi, pretože tvorí pasivačnú vrstvu na kovom. Na druhej strane pri znížení obsahu kyslíka nie je možné plné spaľovanie a plameň sa stáva redukčným (karburizačným) plameňom. Teploty v redukčnom plameni sú nižšie a preto je vhodný pre procesy ako spájkovanie a tvrdé spájkovanie. Iné plyny sú tiež potenciálne palivá, ale oproti acetylénu majú určité nevýhody. Prídavné kovy do zvarovej zóny príležitostne dodávame vo forme prídavných tyčí alebo drôtu. Niektoré z nich sú potiahnuté tavivom na spomalenie oxidácie povrchov a tým na ochranu roztaveného kovu. Ďalšou výhodou, ktorú nám tavidlo poskytuje, je odstránenie oxidov a iných látok zo zóny zvaru. To vedie k silnejšiemu spojeniu. Variantom zvárania kyslíkom a palivom je zváranie TLAKOVÝM PLYNOM, kde sa dva komponenty zahrievajú na svojom rozhraní pomocou horáka s kyslíkom a acetylénom a keď sa rozhranie začne topiť, horák sa stiahne a na stlačenie dvoch častí sa použije axiálna sila. kým rozhranie nestuhne. OBlúKOVÉ ZVÁRANIE: Používame elektrickú energiu na vytvorenie oblúka medzi špičkou elektródy a časťami, ktoré sa majú zvárať. Napájací zdroj môže byť striedavý alebo jednosmerný, pričom elektródy sú buď spotrebné alebo nespotrebiteľné. Prenos tepla pri oblúkovom zváraní možno vyjadriť nasledujúcou rovnicou: H / l = ex VI / v Tu H je tepelný príkon, l je dĺžka zvaru, V a I sú použité napätie a prúd, v je rýchlosť zvárania a e je účinnosť procesu. Čím vyššia je účinnosť „e“, tým výhodnejšie sa využíva dostupná energia na roztavenie materiálu. Tepelný príkon môže byť vyjadrený aj ako: H = ux (objem) = ux A xl Tu u je merná energia na roztavenie, A prierez zvaru a l dĺžka zvaru. Z dvoch vyššie uvedených rovníc môžeme získať: v = ex VI / u A Variantom oblúkového zvárania je SHIELDED METAL ARC WELDING (SMAW), ktoré predstavuje asi 50 % všetkých priemyselných a údržbárskych zváracích procesov. ZVÁRANIE ELEKTRICKÝM OBLÚKOM (ZVÁRANIE TYČOM) sa vykonáva tak, že sa špička obalenej elektródy dotkne obrobku a rýchlo sa odtiahne na vzdialenosť dostatočnú na udržanie oblúka. Tento proces nazývame aj zváraním tyčinkou, pretože elektródy sú tenké a dlhé tyčinky. Počas procesu zvárania sa hrot elektródy roztaví spolu s jej povlakom a základným kovom v blízkosti oblúka. Zmes základného kovu, elektródového kovu a látok z elektródového povlaku tuhne v oblasti zvaru. Povlak elektródy deoxiduje a poskytuje ochranný plyn v oblasti zvaru, čím ju chráni pred kyslíkom v prostredí. Preto sa tento proces nazýva oblúkové zváranie v tienidle. Pre optimálny výkon zvárania používame prúdy medzi 50 a 300 ampérmi a úrovne výkonu zvyčajne menšie ako 10 kW. Dôležitá je aj polarita jednosmerného prúdu (smer toku prúdu). Pri zváraní plechov sa uprednostňuje priama polarita, kde je obrobok kladný a elektróda záporná, pretože má plytký prienik a tiež pre spoje s veľmi širokými medzerami. Keď máme opačnú polaritu, tj elektróda je kladná a obrobok záporná, môžeme dosiahnuť hlbšie prieniky zvaru. So striedavým prúdom, keďže máme pulzujúce oblúky, môžeme zvárať hrubé časti pomocou elektród s veľkým priemerom a maximálnymi prúdmi. Metóda zvárania SMAW je vhodná pre hrúbku obrobku 3 až 19 mm a ešte viac s použitím viacprechodových techník. Troska vytvorená na povrchu zvaru sa musí odstrániť pomocou drôtenej kefy, aby nedochádzalo ku korózii a poruchám v oblasti zvaru. To samozrejme zvyšuje náklady na oblúkové zváranie kovov v tieni. Napriek tomu je SMAW najpopulárnejšou zváracou technikou v priemysle a opravárenských prácach. ZVÁRANIE POD BLOKOM (PÍLA): V tomto procese chránime zvarový oblúk použitím materiálov s granulovaným tavivom, ako je vápno, oxid kremičitý, fluorid vápenatý, oxid mangánu... atď. Granulované tavivo sa privádza do zóny zvaru gravitačne cez trysku. Tavidlo pokrývajúce zónu roztaveného zvaru výrazne chráni pred iskrami, výparmi, UV žiarením atď. a pôsobí ako tepelný izolátor, čím umožňuje prenikaniu tepla hlboko do obrobku. Netavené tavidlo sa získa, spracuje a znovu použije. Holá cievka sa používa ako elektróda a vedie cez rúrku do oblasti zvaru. Používame prúdy medzi 300 a 2000 ampérmi. Proces zvárania pod tavivom (SAW) je obmedzený na horizontálne a ploché polohy a kruhové zvary, ak je počas zvárania možná rotácia kruhovej konštrukcie (napríklad rúr). Rýchlosť môže dosiahnuť 5 m/min. Proces SAW je vhodný pre hrubé plechy a výsledkom sú vysokokvalitné, húževnaté, tvárne a rovnomerné zvary. Produktivita, to znamená množstvo zvarového materiálu uloženého za hodinu, je 4 až 10-násobok množstva v porovnaní s procesom SMAW. Iný proces oblúkového zvárania, menovite GAS METAL ARC WELDING (GMAW) alebo alternatívne označovaný ako METAL INERT GAS WELDING (MIG) je založený na tom, že oblasť zvaru je chránená vonkajšími zdrojmi plynov ako hélium, argón, oxid uhličitý... atď. V kove elektródy môžu byť prítomné ďalšie deoxidačné činidlá. Spotrebný drôt sa privádza cez trysku do zvarovej zóny. Výroba zahŕňajúca železné aj neželezné kovy sa vykonáva pomocou plynového oblúkového zvárania kovov (GMAW). Produktivita zvárania je približne 2-krát vyššia ako pri procese SMAW. Používa sa automatizované zváracie zariadenie. Kov sa v tomto procese prenáša jedným z troch spôsobov: „Prenos rozprašovaním“ zahŕňa prenos niekoľkých stoviek malých kovových kvapiek za sekundu z elektródy do oblasti zvaru. Na druhej strane pri „Globulárnom prenose“ sa používajú plyny bohaté na oxid uhličitý a guľôčky roztaveného kovu sú poháňané elektrickým oblúkom. Zváracie prúdy sú vysoké a zvar preniká hlbšie, rýchlosť zvárania je vyššia ako pri prenose sprejom. Guľový prenos je teda lepší pre zváranie ťažších profilov. Nakoniec, pri metóde „Short Circuiting“ sa hrot elektródy dotkne roztaveného zvarového kúpeľa, pričom ho skratuje ako kov rýchlosťou vyššou ako 50 kvapiek za sekundu sa prenáša v jednotlivých kvapkách. Používajú sa nízke prúdy a napätia spolu s tenším drôtom. Používané výkony sú približne 2 kW a relatívne nízke teploty, vďaka čomu je táto metóda vhodná pre tenké plechy s hrúbkou menšou ako 6 mm. Ďalšia variácia procesu FLUX-CORED ARC WELDING (FCAW) je podobná oblúkovému zváraniu plynom, s výnimkou toho, že elektróda je trubica naplnená tavivom. Výhodou použitia elektród s jadrom je, že vytvárajú stabilnejšie oblúky, dávajú nám možnosť zlepšiť vlastnosti zvarových kovov, menej krehký a flexibilný charakter jeho toku v porovnaní so zváraním SMAW, zlepšené obrysy zvárania. Samotienené elektródy obsahujú materiály, ktoré chránia zvarovú zónu pred atmosférou. Používame výkon cca 20 kW. Podobne ako proces GMAW, aj proces FCAW ponúka možnosť automatizácie procesov pre kontinuálne zváranie a je ekonomický. Pridaním rôznych zliatin do jadra taviva je možné vyvinúť rôzne chemické vlastnosti zvarových kovov. Pri ELEKTROPLYNOVOM ZVÁRANÍ (EGW) zvárame kusy umiestnené od okraja k okraju. Niekedy sa nazýva aj ZVÁRANIE NA TUPA. Zvarový kov sa vloží do zvarovej dutiny medzi dva kusy, ktoré sa majú spojiť. Priestor je uzavretý dvoma vodou chladenými priehradami, aby sa zabránilo vylievaniu roztavenej trosky. Hrádze sa pohybujú nahor mechanickými pohonmi. Keď je možné obrobok otáčať, môžeme použiť techniku elektroplynového zvárania aj na obvodové zváranie rúr. Elektródy sú vedené cez potrubie, aby sa udržal súvislý oblúk. Prúdy môžu byť okolo 400 ampérov alebo 750 ampérov a úrovne výkonu okolo 20 kW. Inertné plyny pochádzajúce buď z elektródy s tokom alebo z externého zdroja poskytujú tienenie. Elektroplynové zváranie (EGW) používame pre kovy ako sú ocele, titán….atď s hrúbkami od 12 mm do 75 mm. Táto technika je vhodná pre veľké konštrukcie. Pri inej technike nazývanej ELEKTROSLAGOVÉ ZVÁRANIE (ESW) sa oblúk zapáli medzi elektródou a spodkom obrobku a pridá sa tavidlo. Keď roztavená troska dosiahne hrot elektródy, oblúk zhasne. Energia je nepretržite dodávaná prostredníctvom elektrického odporu roztavenej trosky. Dokážeme zvárať plechy s hrúbkami od 50 mm do 900 mm a dokonca aj vyššie. Prúdy sú okolo 600 ampérov, zatiaľ čo napätia sú medzi 40 – 50 V. Rýchlosti zvárania sú okolo 12 až 36 mm/min. Aplikácie sú podobné zváraniu elektroplynom. Jeden z našich nekonzumovateľných elektródových procesov, GAS TUNGSTEN ARC WELDING (GTAW), tiež známy ako TUNGSTEN INERT GAS WELDING (TIG), zahŕňa dodávanie prídavného kovu drôtom. Na tesne priliehajúce spoje niekedy prídavný kov nepoužívame. V procese TIG nepoužívame tavivo, ale na tienenie používame argón a hélium. Volfrám má vysoký bod topenia a pri zváraní TIG sa nespotrebováva, preto je možné udržiavať konštantný prúd, ako aj medzery medzi oblúkmi. Úrovne výkonu sú medzi 8 až 20 kW a prúdy buď 200 ampérov (DC) alebo 500 ampérov (AC). Pre hliník a horčík používame striedavý prúd pre jeho funkciu čistenia oxidov. Aby sa zabránilo kontaminácii volfrámovej elektródy, vyhýbame sa jej kontaktu s roztavenými kovmi. Gas Tungsten Arc Welding (GTAW) je obzvlášť užitočné na zváranie tenkých kovov. Zvary GTAW sú veľmi kvalitné s dobrou povrchovou úpravou. Kvôli vyššej cene vodíkového plynu je menej často používanou technikou ATOMIC HYDROGEN WELDING (AHW), kde generujeme oblúk medzi dvoma volfrámovými elektródami v tieniacej atmosfére prúdiaceho vodíkového plynu. AHW je tiež proces zvárania elektródou bez spotrebováva. Dvojatómový vodíkový plyn H2 sa rozkladá na svoju atómovú formu v blízkosti zváracieho oblúka, kde sú teploty vyššie ako 6273 Kelvinov. Pri lámaní absorbuje veľké množstvo tepla z oblúka. Keď atómy vodíka zasiahnu zvarovú zónu, ktorá je relatívne studeným povrchom, rekombinujú sa do dvojatómovej formy a uvoľnia uložené teplo. Energiu je možné meniť zmenou vzdialenosti obrobku na oblúk. V ďalšom procese s nespotrebovateľnými elektródami, PLASMA ARC WELDING (PAW), máme koncentrovaný plazmový oblúk nasmerovaný do zóny zvaru. Teploty dosahujú 33 273 Kelvinov v PAW. Plazmový plyn tvorí takmer rovnaký počet elektrónov a iónov. Nízkoprúdový pilotný oblúk iniciuje plazmu, ktorá je medzi volfrámovou elektródou a otvorom. Prevádzkové prúdy sú zvyčajne okolo 100 ampérov. Môže sa privádzať prídavný kov. Pri zváraní plazmovým oblúkom sa tienenie dosiahne vonkajším tieniacim krúžkom a použitím plynov, ako je argón a hélium. Pri zváraní plazmovým oblúkom môže byť oblúk medzi elektródou a obrobkom alebo medzi elektródou a tryskou. Táto zváracia technika má oproti iným metódam výhody vyššej koncentrácie energie, hlbšej a užšej zváracej schopnosti, lepšej stability oblúka, vyššej rýchlosti zvárania až 1 meter/min, menšieho tepelného skreslenia. Vo všeobecnosti používame zváranie plazmovým oblúkom pre hrúbky menšie ako 6 mm a niekedy až do 20 mm pre hliník a titán. VYSOKOENERGETICKÉ ZVÁRANIE: Ďalší typ metódy tavného zvárania so zváraním elektrónovým lúčom (EBW) a laserovým zváraním (LBW) v dvoch variantoch. Tieto techniky majú mimoriadnu hodnotu pre našu prácu pri výrobe high-tech produktov. Pri zváraní elektrónovým lúčom dopadajú vysokorýchlostné elektróny na obrobok a ich kinetická energia sa premieňa na teplo. Úzky zväzok elektrónov sa ľahko pohybuje vo vákuovej komore. Vo všeobecnosti používame vysoké vákuum pri zváraní elektrickým lúčom. Je možné zvárať plechy s hrúbkou až 150 mm. Nie sú potrebné žiadne ochranné plyny, tavivo ani výplňový materiál. Elektrónové lúče majú výkon 100 kW. Možné sú hlboké a úzke zvary s vysokým pomerom strán až 30 a malými tepelne ovplyvnenými zónami. Rýchlosť zvárania môže dosiahnuť 12 m/min. Pri zváraní laserovým lúčom využívame ako zdroj tepla vysokovýkonné lasery. Laserové lúče už od 10 mikrónov s vysokou hustotou umožňujú hlboký prienik do obrobku. Pri zváraní laserovým lúčom je možný pomer hĺbky k šírke až 10. Používame tak pulzné, ako aj kontinuálne vlnové lasery, pričom prvý v aplikáciách pre tenké materiály a druhý väčšinou pre hrubé obrobky do cca 25 mm. Výkony sú do 100 kW. Zváranie laserovým lúčom nie je vhodné pre opticky veľmi reflexné materiály. Pri zváraní sa môžu použiť aj plyny. Metóda zvárania laserovým lúčom je vhodná pre automatizáciu a veľkoobjemovú výrobu a môže ponúknuť rýchlosť zvárania medzi 2,5 m/min a 80 m/min. Jednou z hlavných výhod, ktoré táto zváracia technika ponúka, je prístup do oblastí, kde nie je možné použiť iné techniky. Laserové lúče môžu ľahko cestovať do takýchto zložitých oblastí. Nie je potrebné žiadne vákuum ako pri zváraní elektrónovým lúčom. Zvary s dobrou kvalitou a pevnosťou, nízkym zmršťovaním, nízkym skreslením a nízkou pórovitosťou možno dosiahnuť zváraním laserovým lúčom. Laserové lúče možno ľahko manipulovať a tvarovať pomocou káblov z optických vlákien. Technika je teda vhodná na zváranie presných hermetických zostáv, elektronických obalov atď. Pozrime sa na naše techniky PEVNÉHO ZVÁRANIA. COLD WELDING (CW) je proces, pri ktorom sa namiesto tepla aplikuje tlak pomocou lisovníc alebo valcov na diely, ktoré sú spojené. Pri zváraní za studena musí byť aspoň jedna z protiľahlých častí tvárna. Najlepšie výsledky sa dosiahnu s dvoma podobnými materiálmi. Ak sú dva kovy, ktoré sa majú spojiť zváraním za studena, rozdielne, môžu vzniknúť slabé a krehké spoje. Metóda zvárania za studena je vhodná pre mäkké, tvárne a malé obrobky, ako sú elektrické spoje, okraje nádob citlivé na teplo, bimetalové pásy pre termostaty atď. Jednou z variácií studeného zvárania je spájanie valcovaním (alebo zváranie valcami), kde sa tlak aplikuje cez pár valcov. Niekedy vykonávame zváranie valcami pri zvýšených teplotách pre lepšiu medzipovrchovú pevnosť. Ďalší proces zvárania v tuhom stave, ktorý používame, je ULTRASONIC WELDING (USW), kde sú obrobky vystavené statickej normálovej sile a oscilačným šmykovým napätiam. Oscilačné šmykové napätia sú aplikované cez hrot prevodníka. Ultrazvukové zváranie využíva oscilácie s frekvenciami od 10 do 75 kHz. V niektorých aplikáciách, ako je švové zváranie, používame ako hrot rotujúci zvárací kotúč. Šmykové napätia pôsobiace na obrobky spôsobujú malé plastické deformácie, rozrušujú vrstvy oxidov, kontaminanty a vedú k lepeniu v tuhom stave. Teploty používané pri ultrazvukovom zváraní sú hlboko pod teplotou topenia kovov a nedochádza k žiadnej fúzii. Často používame proces ultrazvukového zvárania (USW) pre nekovové materiály, ako sú plasty. V termoplastoch však teploty dosahujú teploty topenia. Ďalšou populárnou technikou je pri FRICTION WELDING (FRW) teplo generované trením na rozhraní spájaných obrobkov. Pri zváraní trením udržujeme jeden z obrobkov nehybný, zatiaľ čo druhý obrobok je držaný v prípravku a otáča sa konštantnou rýchlosťou. Obrobky sa potom dostanú do kontaktu pôsobením axiálnej sily. Povrchová rýchlosť otáčania pri zváraní trením môže v niektorých prípadoch dosiahnuť 900 m/min. Po dostatočnom medziplošnom kontakte sa rotujúci obrobok náhle zastaví a axiálna sila sa zvýši. Zóna zvaru je vo všeobecnosti úzka oblasť. Technika zvárania trením sa môže použiť na spájanie pevných a rúrkových častí vyrobených z rôznych materiálov. Na rozhraní vo FRW sa môže vyvinúť nejaký záblesk, ale tento záblesk možno odstrániť sekundárnym obrábaním alebo brúsením. Existujú variácie procesu trecieho zvárania. Napríklad „zotrvačné trecie zváranie“ zahŕňa zotrvačník, ktorého rotačná kinetická energia sa využíva na zváranie dielov. Zvar je dokončený, keď sa zotrvačník zastaví. Rotujúca hmotnosť sa môže meniť a tým aj rotačná kinetická energia. Ďalšou variáciou je „lineárne trecie zváranie“, kde je lineárny vratný pohyb vnútený aspoň jednému z komponentov, ktoré sa majú spojiť. Pri lineárnom trecom zváraní časti nemusia byť kruhové, môžu byť pravouhlé, štvorcové alebo iného tvaru. Frekvencie môžu byť v desiatkach Hz, amplitúdy v rozsahu milimetrov a tlaky v desiatkach alebo stovkách MPa. Nakoniec „trecie zváranie s premiešavaním“ je trochu odlišné od ostatných dvoch vysvetlených vyššie. Zatiaľ čo pri zotrvačnom trecom zváraní a lineárnom trecom zváraní sa zahrievanie rozhraní dosahuje trením trením dvoch kontaktných povrchov, pri metóde trecieho miešania sa tretie teleso otiera o dva povrchy, ktoré sa majú spojiť. Do spoja sa privedie rotačný nástroj s priemerom 5 až 6 mm. Teploty sa môžu zvýšiť na hodnoty medzi 503 až 533 Kelvinmi. Dochádza k zahrievaniu, miešaniu a miešaniu hmoty v spoji. Zváranie trením používame na rôzne materiály vrátane hliníka, plastov a kompozitov. Zvary sú rovnomerné a kvalita je vysoká s minimálnymi pórmi. Pri trecom zváraní s premiešavaním nevznikajú žiadne výpary ani rozstreky a proces je dobre automatizovaný. ODPOROVÉ ZVÁRANIE (RW): Teplo potrebné na zváranie vzniká elektrickým odporom medzi dvomi spájanými dielmi. Pri odporovom zváraní sa nepoužívajú žiadne tavidlá, ochranné plyny ani spotrebné elektródy. Joule zahrievanie prebieha pri odporovom zváraní a možno ho vyjadriť ako: H = (štvorec I) x R xtx K H je teplo generované v jouloch (wattsekundách), prúd I v ampéroch, odpor R v ohmoch, t je čas v sekundách, ktorým prúd preteká. Faktor K je menší ako 1 a predstavuje časť energie, ktorá sa nestratí žiarením a vedením. Prúdy v procesoch odporového zvárania môžu dosiahnuť úrovne až 100 000 A, ale napätia sú zvyčajne 0,5 až 10 voltov. Elektródy sú zvyčajne vyrobené zo zliatin medi. Odporovým zváraním je možné spájať podobné aj rozdielne materiály. Pre tento proces existuje niekoľko variácií: „Odporové bodové zváranie“ zahŕňa dve protiľahlé okrúhle elektródy, ktoré sa dotýkajú povrchov preplátovaného spoja dvoch plechov. Tlak sa aplikuje, kým sa prúd nevypne. Zvarový nuget má spravidla priemer do 10 mm. Odporové bodové zváranie zanecháva na miestach zvaru mierne zafarbené vrúbkované stopy. Bodové zváranie je naša najobľúbenejšia technika odporového zvárania. Pri bodovom zváraní sa používajú rôzne tvary elektród, aby sa dosiahli ťažké miesta. Naše zariadenie na bodové zváranie je riadené CNC a má viacero elektród, ktoré možno použiť súčasne. Ďalšia variácia „odporového švového zvárania“ sa vykonáva pomocou kotúčových alebo valčekových elektród, ktoré vytvárajú súvislé bodové zvary vždy, keď prúd dosiahne dostatočne vysokú úroveň v striedavom napájacom cykle. Spoje vyrobené odporovým švovým zváraním sú vodotesné a plynotesné. Rýchlosť zvárania okolo 1,5 m/min je normálna pre tenké plechy. Je možné použiť prerušované prúdy, takže bodové zvary sa vytvárajú v požadovaných intervaloch pozdĺž švu. Pri „odporovom zváraní výstupkov“ razíme jeden alebo viac výstupkov (jamkov) na jeden z povrchov obrobku, ktorý sa má zvárať. Tieto výstupky môžu byť okrúhle alebo oválne. Na týchto vyrazených miestach, ktoré prichádzajú do kontaktu s protiľahlou časťou, sa dosahujú vysoké lokalizované teploty. Elektródy vyvíjajú tlak na stlačenie týchto výstupkov. Elektródy pri odporovom projekčnom zváraní majú ploché hroty a sú to vodou chladené zliatiny medi. Výhodou odporového premietacieho zvárania je naša schopnosť zvariť množstvo zvarov jedným ťahom, tým predĺžená životnosť elektródy, schopnosť zvárať plechy rôznych hrúbok, schopnosť zvárať matice a skrutky na plechy. Nevýhodou odporového projekčného zvárania sú dodatočné náklady na razenie jamiek. Ešte ďalšou technikou je pri „bleskovom zváraní“ teplo generované oblúkom na koncoch dvoch obrobkov, keď sa začnú dotýkať. Tento spôsob možno alternatívne považovať aj za oblúkové zváranie. Teplota na rozhraní stúpa a materiál mäkne. Aplikuje sa axiálna sila a v zmäkčenej oblasti sa vytvorí zvar. Po dokončení bleskového zvárania môže byť spoj opracovaný pre lepší vzhľad. Kvalita zvaru získaná bleskovým zváraním je dobrá. Výkonové stupne sú 10 až 1500 kW. Bleskové zváranie je vhodné na spájanie podobných alebo rozdielnych kovov do priemeru 75 mm a plechov s hrúbkou od 0,2 mm do 25 mm. „Zváranie pod oblúkom“ je veľmi podobné bleskovému zváraniu. Čap, ako je skrutka alebo závitová tyč, slúži ako jedna elektróda, zatiaľ čo je pripojený k obrobku, ako je doska. Na sústredenie vytvoreného tepla, zabránenie oxidácii a zadržanie roztaveného kovu v zóne zvaru je okolo spoja umiestnený jednorazový keramický krúžok. Nakoniec „príklepové zváranie“ ďalší proces odporového zvárania, ktorý využíva kondenzátor na dodávanie elektrickej energie. Pri príklepovom zváraní sa energia vybije v priebehu milisekúnd veľmi rýchlo, čím sa v spoji vytvorí vysoké lokalizované teplo. Nárazové zváranie široko používame v elektronickom výrobnom priemysle, kde je potrebné zabrániť zahrievaniu citlivých elektronických komponentov v blízkosti spoja. Technika nazývaná EXPLOSION WELDING zahŕňa detonáciu vrstvy výbušniny, ktorá sa položí na jeden z obrobkov, ktoré sa majú spojiť. Veľmi vysoký tlak vyvíjaný na obrobok vytvára turbulentné a zvlnené rozhranie a dochádza k mechanickému blokovaniu. Pevnosť spoja pri výbušnom zváraní je veľmi vysoká. Výbušné zváranie je dobrou metódou na opláštenie plechov odlišnými kovmi. Po opláštení môžu byť dosky valcované na tenšie časti. Niekedy používame zváranie výbuchom na roztiahnutie rúrok tak, aby boli tesne prilepené k doske. Našou poslednou metódou v oblasti spájania v tuhom stave je DIFFUSION BONDING alebo DIFFUSION WELDING (DFW), pri ktorej sa dobrý spoj dosiahne hlavne difúziou atómov cez rozhranie. K zváraniu prispieva aj určitá plastická deformácia na rozhraní. Príslušné teploty sú okolo 0,5 Tm, kde Tm je teplota topenia kovu. Pevnosť spoja pri difúznom zváraní závisí od tlaku, teploty, času kontaktu a čistoty kontaktných povrchov. Niekedy na rozhraní používame prídavné kovy. Teplo a tlak sú potrebné pri difúznom spájaní a sú dodávané elektrickým odporom alebo pecou a závažím, lisom alebo iným spôsobom. Podobné a rozdielne kovy je možné spájať difúznym zváraním. Proces je relatívne pomalý kvôli času, ktorý trvá migrácia atómov. DFW je možné automatizovať a široko sa používa pri výrobe zložitých dielov pre letecký, elektronický a medicínsky priemysel. Vyrábané produkty zahŕňajú ortopedické implantáty, senzory, letecké konštrukčné prvky. Difúzne spájanie je možné kombinovať so SUPERPLASTICKÝM TVÁRNÍM na výrobu zložitých plechov. Vybrané miesta na listoch sa najskôr spoja difúzne a potom sa nespojené oblasti roztiahnu do formy pomocou tlaku vzduchu. Pomocou tejto kombinácie metód sa vyrábajú letecké konštrukcie s vysokým pomerom tuhosti k hmotnosti. Kombinovaný proces difúzneho zvárania/superplastického tvarovania znižuje počet požadovaných dielov elimináciou potreby spojovacích prvkov, výsledkom čoho sú nízkonapäťové vysoko presné diely ekonomicky as krátkymi dodacími lehotami. SPÁJKOVANIE: Techniky spájkovania a spájkovania zahŕňajú nižšie teploty, ako sú teploty potrebné na zváranie. Teploty spájkovania sú však vyššie ako teploty spájkovania. Pri spájkovaní sa medzi povrchy, ktoré sa majú spojiť, vloží prídavný kov a teploty sa zvýšia na teplotu topenia prídavného materiálu nad 723 Kelvinov, ale pod teplotu tavenia obrobkov. Roztavený kov vypĺňa tesne priliehajúci priestor medzi obrobkami. Ochladzovanie a následné tuhnutie kovu pilníka má za následok pevné spoje. Pri spájkovaní natvrdo sa prídavný kov nanáša na spoj. Pri spájkovaní natvrdo sa používa podstatne viac prídavného kovu v porovnaní so spájkovaním. Oxyacetylénový horák s oxidačným plameňom sa používa na nanášanie prídavného kovu pri spájkovaní natvrdo. V dôsledku nižších teplôt pri spájkovaní sú problémy v oblastiach ovplyvnených teplom, ako sú deformácie a zvyškové napätia, menšie. Čím menšia je medzera pri spájkovaní, tým vyššia je pevnosť spoja v šmyku. Maximálna pevnosť v ťahu sa však dosiahne pri optimálnej medzere (špičková hodnota). Pod a nad touto optimálnou hodnotou sa pevnosť v ťahu pri spájkovaní znižuje. Typické vôle pri spájkovaní môžu byť medzi 0,025 a 0,2 mm. Používame rôzne spájkovacie materiály s rôznymi tvarmi, ako sú perá, prášok, krúžky, drôty, pásy... atď. a dokáže vyrobiť tieto prvky špeciálne pre váš dizajn alebo geometriu produktu. Tiež určujeme obsah spájkovacích materiálov podľa vašich základných materiálov a použitia. Na odstránenie nežiaducich oxidových vrstiev a zabránenie oxidácii často používame tavivá pri operáciách spájkovania. Aby sa predišlo následnej korózii, tavivá sa vo všeobecnosti odstránia po operácii spájania. AGS-TECH Inc. používa rôzne metódy spájkovania, vrátane: - Spájkovanie horákom - Spájkovanie v peci - Indukčné spájkovanie - Odporové spájkovanie - Spájkovanie ponorením - Infračervené spájkovanie - Difúzne spájkovanie - Vysokoenergetický lúč Naše najbežnejšie príklady spájkovaných spojov sú vyrobené z rôznych kovov s dobrou pevnosťou, ako sú karbidové vrtáky, vložky, optoelektronické hermetické obaly, tesnenia. SPÁJKOVANIE: Toto je jedna z našich najčastejšie používaných techník, pri ktorej spájka (výplňový kov) vypĺňa spoj ako pri spájkovaní medzi tesne priliehajúcimi komponentmi. Naše spájky majú bod topenia pod 723 Kelvinov. Vo výrobných prevádzkach nasadzujeme ručné aj automatizované spájkovanie. V porovnaní s tvrdým spájkovaním sú teploty spájkovania nižšie. Spájkovanie nie je veľmi vhodné pre vysokoteplotné alebo vysokopevnostné aplikácie. Na spájkovanie používame okrem iného bezolovnaté spájky, ako aj zliatiny cín-olovo, cín-zinok, olovo-striebro, kadmium-striebro, zinok-hliník. Ako tavidlo pri spájkovaní sa používajú nekorozívne živice, ako aj anorganické kyseliny a soli. Na spájkovanie kovov s nízkou spájkovateľnosťou používame špeciálne tavivá. V aplikáciách, kde musíme spájkovať keramické materiály, sklo alebo grafit, diely najskôr pokovujeme vhodným kovom pre zvýšenú spájkovateľnosť. Naše obľúbené techniky spájkovania sú: - Pretavenie alebo pastové spájkovanie - Spájkovanie vlnou - Spájkovanie v peci - spájkovanie horákom - Indukčné spájkovanie - Spájkovanie železa - Odporové spájkovanie - Spájkovanie ponorením - Ultrazvukové spájkovanie - Infračervené spájkovanie Ultrazvukové spájkovanie nám ponúka jedinečnú výhodu, kedy je eliminovaná potreba tavív vďaka ultrazvukovému kavitačnému efektu, ktorý odstraňuje oxidové filmy zo spájaných povrchov. Spájkovanie pretavením a vlnou sú naše priemyselne vynikajúce techniky pre veľkoobjemovú výrobu v elektronike, a preto stojí za to ich podrobnejšie vysvetliť. Pri spájkovaní pretavením používame polotuhé pasty, ktoré obsahujú častice spájkovacieho kovu. Pasta sa nanáša na spoj pomocou procesu sitovania alebo šablónovania. V doskách plošných spojov (PCB) túto techniku často používame. Keď sú elektrické komponenty umiestnené na tieto podložky z pasty, povrchové napätie udržuje obaly na povrchovú montáž zarovnané. Po umiestnení komponentov zohrejeme zostavu v peci, aby prebehlo spájkovanie pretavením. Počas tohto procesu sa rozpúšťadlá v paste odparia, tavidlo v paste sa aktivuje, komponenty sa predhrejú, častice spájky sa roztavia a zmáčajú spoj a nakoniec sa zostava DPS pomaly ochladí. Naša druhá populárna technika pre veľkoobjemovú výrobu dosiek plošných spojov, menovite vlnové spájkovanie, spočíva v tom, že roztavené spájky zmáčajú kovové povrchy a vytvárajú dobré spoje iba vtedy, keď je kov predhriaty. Stojatá laminárna vlna roztavenej spájky je najprv generovaná čerpadlom a predhriate a predtavené PCB sú dopravované cez túto vlnu. Spájka zmáča iba exponované kovové povrchy, ale nezmáča polymérové obaly IC ani dosky plošných spojov potiahnuté polymérom. Vysokorýchlostný prúd horúcej vody vyfukuje prebytočnú spájku zo spoja a zabraňuje premosteniu medzi susednými vodičmi. Pri vlnovom spájkovaní obalov na povrchovú montáž ich pred spájkovaním najskôr prilepíme na dosku plošných spojov. Opäť sa používa tienenie a šablóna, ale tentoraz pre epoxid. Po umiestnení komponentov na správne miesta sa epoxid vytvrdí, dosky sa obrátia a uskutoční sa spájkovanie vlnou. CLICK Product Finder-Locator Service PREDCHÁDZAJÚCA STRANA
- Metal Stamping, Sheet Metal Fabrication, Zinc Plated Metal Stamped
Metal Stamping & Sheet Metal Fabrication, Zinc Plated Metal Stamped Parts, Wire and Spring Forming Lisovanie a výroba plechov Pozinkované lisované diely Presné výlisky a tvarovanie drôtu Pozinkované presné kovové výlisky Presne lisované diely Presné lisovanie kovov AGS-TECH Inc Výroba plechu spoločnosťou AGS-TECH Inc. Rýchle prototypovanie plechu spoločnosťou AGS-TECH Inc. Lisovanie podložiek vo veľkom objeme Vývoj a výroba plechových krytov olejových filtrov Výroba plechových komponentov pre olejový filter a kompletná montáž Zákazková výroba a montáž výrobkov z plechu Výroba tesnenia hlavy spoločnosťou AGS-TECH Inc. Výroba súpravy tesnení v AGS-TECH Inc. Výroba plechových krytov - AGS-TECH Inc Jednoduché jednoduché a progresívne výlisky od AGS-TECH Inc. Výlisky z kovu a kovových zliatin - AGS-TECH Inc Plechové diely pred dokončením operácie Tvarovanie plechov - Elektrický kryt - AGS-TECH Inc Výroba rezacích čepelí potiahnutých titánom pre potravinársky priemysel Výroba skivingových čepelí pre potravinársky baliaci priemysel PREDCHÁDZAJÚCA STRANA
- Pneumatic and Hydraulic Actuators - Accumulators - AGS-TECH Inc. - NM
Pneumatic and Hydraulic Actuators - Accumulators - AGS-TECH Inc. - NM Akčné členy Akumulátory AGS-TECH je popredným výrobcom a dodávateľom PNEUMATIC a HYDRAULICKÉ AKTUÁTORY pre montáž, balenie, robotiku a priemyselnú automatizáciu. Naše pohony sú známe svojím výkonom, flexibilitou a extrémne dlhou životnosťou a vítajú výzvy mnohých rôznych typov prevádzkových prostredí. Dodávame aj HYDRAULICKÉ AKUMULÁTORY čo sú zariadenia, v ktorých sa ukladá potenciálna energia vo forme závažia, sily alebo stlačeného plynu alebo pružiny. proti relatívne nestlačiteľnej tekutine. Naša rýchla dodávka pneumatických a hydraulických pohonov a akumulátorov zníži vaše náklady na zásoby a udrží váš výrobný plán podľa plánu. AKTUÁTORY: Pohon je typ motora zodpovedného za pohyb alebo ovládanie mechanizmu alebo systému. Pohony sú poháňané zdrojom energie. Hydraulické pohony sú ovládané tlakom hydraulickej kvapaliny a pneumatické pohony sú ovládané pneumatickým tlakom a premieňajú túto energiu na pohyb. Akčné členy sú mechanizmy, ktorými riadiaci systém pôsobí na prostredie. Riadiacim systémom môže byť pevný mechanický alebo elektronický systém, softvérový systém, osoba alebo akýkoľvek iný vstup. Hydraulické pohony pozostávajú z valca alebo kvapalinového motora, ktorý využíva hydraulickú silu na uľahčenie mechanickej prevádzky. Mechanický pohyb môže poskytnúť výstup v zmysle lineárneho, rotačného alebo oscilačného pohybu. Keďže kvapaliny je takmer nemožné stlačiť, hydraulické pohony môžu vyvíjať značné sily. Hydraulické pohony však môžu mať obmedzené zrýchlenie. Hydraulický valec pohonu pozostáva z dutej valcovej rúrky, po ktorej sa môže posúvať piest. V jednočinných hydraulických pohonoch je tlak kvapaliny aplikovaný len na jednu stranu piesta. Piest sa môže pohybovať iba jedným smerom a na spätný zdvih piestu sa zvyčajne používa pružina. Dvojčinné ovládače sa používajú, keď tlak pôsobí na každú stranu piestu; akýkoľvek rozdiel v tlaku medzi dvoma stranami piesta posúva piest na jednu alebo druhú stranu. Pneumatické pohony premieňajú energiu vytvorenú vákuom alebo stlačeným vzduchom pri vysokom tlaku buď na lineárny alebo rotačný pohyb. Pneumatické pohony umožňujú vytvárať veľké sily z relatívne malých zmien tlaku. Tieto sily sa často používajú pri ventiloch na pohyb membrán, aby ovplyvnili prietok kvapaliny cez ventil. Pneumatická energia je žiaduca, pretože môže rýchlo reagovať pri štartovaní a zastavovaní, pretože zdroj energie nie je potrebné skladovať v rezerve pre prevádzku. Priemyselné aplikácie akčných členov zahŕňajú automatizáciu, logické a sekvenčné riadenie, upínacie prípravky a vysokovýkonné riadenie pohybu. Na druhej strane automobilové aplikácie ovládačov zahŕňajú posilňovač riadenia, posilňovacie brzdy, hydraulické brzdy a ovládanie ventilácie. Aerokozmické aplikácie ovládačov zahŕňajú systémy riadenia letu, systémy riadenia riadenia, klimatizácie a systémy riadenia bŕzd. POROVNANIE PNEUMATICKÝCH a HYDRAULICKÝCH POHONOV: Pneumatické lineárne pohony pozostávajú z piestu vo vnútri dutého valca. Tlak z externého kompresora alebo manuálneho čerpadla posúva piest vo vnútri valca. Keď sa tlak zvyšuje, valec ovládača sa pohybuje pozdĺž osi piestu a vytvára lineárnu silu. Piest sa vráti do svojej pôvodnej polohy buď spätnou pružinou alebo tekutinou privádzanou na druhú stranu piestu. Hydraulické lineárne pohony fungujú podobne ako pneumatické pohony, ale valec pohybuje nestlačiteľná kvapalina z čerpadla namiesto stlačeného vzduchu. Výhody pneumatických pohonov vyplývajú z ich jednoduchosti. Väčšina pneumatických hliníkových pohonov má maximálny menovitý tlak 150 psi s veľkosťou otvorov v rozmedzí od 1/2 do 8 palcov, ktoré možno premeniť na silu približne 30 až 7 500 lb. Oceľové pneumatické pohony majú na druhej strane maximálny tlak 250 psi s veľkosťou otvoru v rozmedzí od 1/2 do 14 palcov a vytvárajú sily v rozsahu od 50 do 38 465 lb. Pneumatické pohony generujú presný lineárny pohyb poskytovaním presností, ako je 0,1 palcov a opakovateľnosť do 0,001 palcov. Typické aplikácie pneumatických pohonov sú oblasti s extrémnymi teplotami, ako je -40 F až 250 F. Pomocou vzduchu sa pneumatické pohony vyhýbajú používaniu nebezpečných materiálov. Pneumatické pohony spĺňajú požiadavky na ochranu pred výbuchom a bezpečnosť stroja, pretože nevytvárajú žiadne magnetické rušenie kvôli nedostatku motorov. Cena pneumatických pohonov je v porovnaní s hydraulickými pohonmi nízka. Pneumatické pohony sú tiež ľahké, vyžadujú minimálnu údržbu a majú odolné komponenty. Na druhej strane sú nevýhody pneumatických pohonov: Tlakové straty a stlačiteľnosť vzduchu spôsobujú, že pneumatika je menej efektívna ako iné metódy lineárneho pohybu. Operácie pri nižších tlakoch budú mať nižšie sily a nižšie rýchlosti. Kompresor musí bežať nepretržite a vyvíjať tlak, aj keď sa nič nehýbe. Aby boli pneumatické pohony efektívne, musia byť dimenzované pre konkrétnu prácu a nemôžu byť použité na iné aplikácie. Presné riadenie a účinnosť si vyžaduje proporcionálne regulátory a ventily, čo je nákladné a zložité. Aj keď je vzduch ľahko dostupný, môže byť kontaminovaný olejom alebo mazaním, čo vedie k prestojom a údržbe. Stlačený vzduch je spotrebný materiál, ktorý je potrebné zakúpiť. Hydraulické pohony sú na druhej strane robustné a vhodné pre aplikácie s vysokou silou. Môžu vytvárať sily 25-krát väčšie ako pneumatické pohony rovnakej veľkosti a pracovať s tlakmi až 4 000 psi. Hydraulické motory majú vysoký pomer výkonu k hmotnosti o 1 až 2 hp/lb väčší ako pneumatický motor. Hydraulické pohony môžu udržiavať konštantnú silu a krútiaci moment bez toho, aby čerpadlo dodávalo viac tekutiny alebo tlaku, pretože tekutiny sú nestlačiteľné. Hydraulické pohony môžu mať čerpadlá a motory umiestnené v značnej vzdialenosti od seba s minimálnymi stratami výkonu. Z hydrauliky však uniká kvapalina a výsledkom je nižšia účinnosť. Úniky hydraulickej kvapaliny vedú k problémom s čistotou a potenciálnemu poškodeniu okolitých komponentov a oblastí. Hydraulické pohony vyžadujú veľa doplnkových dielov, ako sú zásobníky tekutín, motory, čerpadlá, vypúšťacie ventily a výmenníky tepla, zariadenia na zníženie hluku. V dôsledku toho sú hydraulické lineárne pohybové systémy veľké a ťažko sa prispôsobujú. AKUMULÁTORY: Používajú sa vo fluidných energetických systémoch na akumuláciu energie a na vyhladenie pulzácií. Hydraulický systém, ktorý využíva akumulátory, môže využívať menšie kvapalinové čerpadlá, pretože akumulátory akumulujú energiu z čerpadla počas období nízkej spotreby. Táto energia je k dispozícii na okamžité použitie, uvoľňuje sa na požiadanie rýchlosťou mnohonásobne vyššou, než by mohla byť dodaná samotným čerpadlom. Akumulátory môžu tiež pôsobiť ako tlmiče nárazov alebo pulzácií tým, že tlmia hydraulické kladivá, čím znižujú otrasy spôsobené rýchlou prevádzkou alebo náhlym spustením a zastavením výkonových valcov v hydraulickom okruhu. Existujú štyri hlavné typy akumulátorov: 1.) Závažne zaťažené piestové akumulátory, 2.) Membránové akumulátory, 3.) Pružinové akumulátory a 4.) Hydropneumatické piestové akumulátory. Typ zaťažený závažím je pre svoju kapacitu oveľa väčší a ťažší ako moderné typy s piestom a mechúrom. Závažný typ aj typ s mechanickou pružinou sa dnes používajú veľmi zriedkavo. Hydropneumatické akumulátory využívajú plyn ako pružinový vankúš v spojení s hydraulickou kvapalinou, pričom plyn a kvapalina sú oddelené tenkou membránou alebo piestom. Akumulátory majú nasledujúce funkcie: -Ukladanie energie - Pohlcovanie pulzácií - Tlmenie prevádzkových otrasov -Doplnenie dodávky čerpadla - Udržiavanie tlaku - Pôsobí ako dávkovači Hydropneumatické akumulátory obsahujú plyn v spojení s hydraulickou kvapalinou. Kvapalina má malú schopnosť uchovávať dynamickú energiu. Relatívna nestlačiteľnosť hydraulickej kvapaliny ju však robí ideálnou pre hydraulické systémy a poskytuje rýchlu odozvu na dopyt po energii. Na druhej strane plyn, partner hydraulickej kvapaliny v akumulátore, môže byť stlačený na vysoké tlaky a malé objemy. V stlačenom plyne sa ukladá potenciálna energia, ktorá sa v prípade potreby uvoľní. V akumulátoroch piestového typu vyvíja energia v stlačenom plyne tlak na piest oddeľujúci plyn a hydraulickú kvapalinu. Piest zase tlačí tekutinu z valca do systému a na miesto, kde je potrebné vykonať užitočnú prácu. Vo väčšine aplikácií s fluidným pohonom sa čerpadlá používajú na generovanie požadovaného výkonu, ktorý sa má použiť alebo uložiť v hydraulickom systéme, a čerpadlá dodávajú tento výkon v pulzujúcom toku. Piestové čerpadlo, ktoré sa bežne používa pre vyššie tlaky, vytvára pulzácie škodlivé pre vysokotlakový systém. Akumulátor správne umiestnený v systéme podstatne tlmí tieto zmeny tlaku. V mnohých aplikáciách s kvapalinovým pohonom sa poháňaný člen hydraulického systému náhle zastaví, čím sa vytvorí tlaková vlna, ktorá sa pošle späť cez systém. Táto rázová vlna môže vyvinúť špičkové tlaky niekoľkonásobne vyššie ako normálne pracovné tlaky a môže byť zdrojom zlyhania systému alebo rušivého hluku. Efekt plynového tlmenia v akumulátore minimalizuje tieto rázové vlny. Príkladom tejto aplikácie je tlmenie nárazov spôsobených náhlym zastavením nakladacej lyžice na hydraulickom čelnom nakladači. Akumulátor, schopný akumulovať energiu, môže dopĺňať kvapalinové čerpadlo pri dodávaní energie do systému. Čerpadlo ukladá potenciálnu energiu do akumulátora počas nečinnosti pracovného cyklu a akumulátor odovzdáva túto rezervnú energiu späť do systému, keď cyklus vyžaduje núdzový alebo špičkový výkon. To umožňuje systému využívať menšie čerpadlá, čo vedie k úspore nákladov a energie. Zmeny tlaku sa pozorujú v hydraulických systémoch, keď je kvapalina vystavená stúpajúcim alebo klesajúcim teplotám. Tiež môže dôjsť k poklesu tlaku v dôsledku úniku hydraulických kvapalín. Akumulátory kompenzujú takéto zmeny tlaku dodávaním alebo prijímaním malého množstva hydraulickej kvapaliny. V prípade, že by hlavný zdroj energie zlyhal alebo bol zastavený, akumulátory by fungovali ako pomocné zdroje energie udržiavajúce tlak v systéme. Nakoniec, akumulátory môžu byť použité na dávkovanie tekutín pod tlakom, ako sú mazacie oleje. Kliknutím na zvýraznený text nižšie si stiahnete naše produktové brožúry pre pohony a akumulátory: - Pneumatické valce - Hydraulický valec série YC - Akumulátory od AGS-TECH Inc CLICK Product Finder-Locator Service PREDCHÁDZAJÚCA STRANA
- Composite Stereo Microscopes, Metallurgical Microscope, Fiberscope
Composite Stereo Microscopes - Metallurgical Microscope - Fiberscope - Borescope - SADT -AGS-TECH Inc - New Mexico - USA Mikroskop, fibroskop, boroskop We supply MICROSCOPES, FIBERSCOPES and BORESCOPES from manufacturers like SADT, SINOAGE_cc781905-5cde -3194-bb3b-136bad5cf58d_pre priemyselné aplikácie. Existuje veľké množstvo mikroskopov založených na fyzikálnom princípe používaných na vytváranie obrazu a na základe ich oblasti použitia. Typy nástrojov, ktoré dodávame, sú OPTICAL MICROSKOPY (TYPY ZLOŽENÝCH / STEREO) a METALLURGICAL M.METALLURGICAL Ak si chcete stiahnuť katalóg pre naše metrologické a testovacie zariadenia značky SADT, KLIKNITE TU. V tomto katalógu nájdete niektoré vysoko kvalitné metalurgické mikroskopy a inverzné mikroskopy. We offer both FLEXIBLE and RIGID FIBERSCOPE and BORESCOPE_cc781905-5cde-3194-bb3b -136bad5cf58d_models a primárne sa používajú pre NONDESTRUKTÍVNE TESTOVANIE in motory v niektorých betónových konštrukciách, ako sú motory v betónových konštrukciách Oba tieto optické prístroje sa používajú na vizuálnu kontrolu. Medzi fibroskopy a boroskopmi sú však rozdiely: Jedným z nich je aspekt flexibility. Fibroskopy sú vyrobené z flexibilných optických vlákien a majú na hlave pripevnenú pozorovaciu šošovku. Operátor môže otočiť šošovku po vložení fibroskopu do štrbiny. To zvyšuje výhľad operátora. Naopak, boroskopy sú vo všeobecnosti pevné a umožňujú používateľovi pozerať sa len priamo dopredu alebo v pravom uhle. Ďalším rozdielom je zdroj svetla. Fibroskop prenáša svetlo po svojich optických vláknach, aby osvetlil oblasť pozorovania. Na druhej strane má boroskop zrkadlá a šošovky, takže svetlo sa môže odrážať medzi zrkadlami a osvetľovať pozorovaciu oblasť. Napokon, prehľadnosť je iná. Zatiaľ čo fibroskopy sú obmedzené na rozsah 6 až 8 palcov, boroskopy môžu poskytnúť širší a jasnejší pohľad v porovnaní s fibroskopy. OPTICKÉ MIKROSKOPY : Tieto optické prístroje používajú na vytvorenie obrazu viditeľné svetlo (alebo UV svetlo v prípade fluorescenčnej mikroskopie). Na lom svetla sa používajú optické šošovky. Prvé mikroskopy, ktoré boli vynájdené, boli optické. Optické mikroskopy možno ďalej rozdeliť do niekoľkých kategórií. Našu pozornosť sústreďujeme na dva z nich: 1.) COMPOUND MICROSCOPE : Tieto mikroskopy sa skladajú z dvoch očných objektívov a dvoch šošovkových Maximálne užitočné zväčšenie je asi 1000x. 2.) STEREO MICROSCOPE (tiež známe ako_cc781905-5cde-319GB1bbc781905-5cde-319Tieto zobrazenie 10bb magneSCRODISK8445cde-31 exemplár. Sú užitočné na pozorovanie nepriehľadných predmetov. METALLURGICAL MICROSCOPES : Náš katalóg SADT na stiahnutie s vyššie uvedeným odkazom obsahuje metalurgické a inverzné metalografické mikroskopy. Podrobnosti o produkte nájdete v našom katalógu. Ak chcete získať základné vedomosti o týchto typoch mikroskopov, prejdite na našu stránku NÁSTROJE NA TESTOVANIE POVRCHU POVRCHU. FIBERSCOPES : Fibrescopes obsahujú zväzky optických vlákien, ktoré pozostávajú z mnohých káblov z optických vlákien. Káble z optických vlákien sú vyrobené z opticky čistého skla a sú tenké ako ľudský vlas. Hlavné komponenty kábla s optickými vláknami sú: Jadro, ktoré je stredom vyrobené z vysoko čistého skla, plášť, čo je vonkajší materiál obklopujúci jadro, ktorý zabraňuje úniku svetla a nakoniec nárazník, ktorým je ochranný plastový povlak. Vo fibroskope sú vo všeobecnosti dva rôzne zväzky optických vlákien: Prvý je zväzok osvetlenia, ktorý je určený na prenášanie svetla zo zdroja do okuláru a druhý je zväzok zobrazovania určený na prenášanie obrazu zo šošovky do okuláru. . Typický fibroskop sa skladá z nasledujúcich komponentov: -Okulár: Toto je časť, odkiaľ pozorujeme obraz. Zväčšuje obraz prenášaný zobrazovacím zväzkom pre ľahké prezeranie. -Imaging Bundle: Prameň flexibilných sklenených vlákien prenášajúcich obrazy do okuláru. -Distal Lens: Kombinácia viacerých mikrošošoviek, ktoré snímajú obrázky a zaostrujú ich do malého obrazového balíka. - Systém osvetlenia: Svetlovod z optických vlákien, ktorý posiela svetlo zo zdroja do cieľovej oblasti (okulár) -Artikulačný systém: Systém poskytujúci používateľovi možnosť ovládať pohyb ohybovej časti fibroskopu, ktorá je priamo pripevnená k distálnej šošovke. - Fibrescope Body: Ovládacia časť navrhnutá na uľahčenie ovládania jednou rukou. - Vkladacia trubica: Táto flexibilná a odolná trubica chráni zväzok optických vlákien a kĺbové káble. -Ohýbacia sekcia – Najflexibilnejšia časť fibroskopu spájajúca zavádzaciu trubicu s distálnou pozorovacou sekciou. -Distálna časť: koncové miesto pre zväzok iluminačných aj zobrazovacích vlákien. BOROSCOPES / BOROSCOPES : Boroskop je optické zariadenie pozostávajúce z pevnej alebo ohybnej trubice s okulárom na jednom konci a šošovkou objektívu na druhom konci, ktoré sú navzájom spojené optickým systémom prenášajúcim svetlo. . Optické vlákna obklopujúce systém sa vo všeobecnosti používajú na osvetlenie objektu, ktorý sa má sledovať. Vnútorný obraz osvetleného objektu tvorí šošovka objektívu, zväčšená okulárom a prezentovaná oku diváka. Mnohé moderné boroskopy môžu byť vybavené zobrazovacími a video zariadeniami. Boroskopy sa používajú podobne ako fibroskopy na vizuálnu kontrolu tam, kde oblasť, ktorá sa má kontrolovať, je neprístupná inými prostriedkami. Boroskopy sa považujú za nedeštruktívne testovacie nástroje na prezeranie a skúmanie defektov a nedokonalostí. Oblasti použitia sú obmedzené len vašou predstavivosťou. Termín FLEXIBLE BORESCOPE sa niekedy používa zameniteľne s pojmom fibroscope. Jedna nevýhoda flexibilných boroskopov pochádza z pixelácie a presluchu pixelov v dôsledku vedenia obrazu vlákna. Kvalita obrazu sa medzi rôznymi modelmi flexibilných boroskopov značne líši v závislosti od počtu vlákien a konštrukcie použitej v obrazovom sprievodcovi vlákien. Špičkové boroskopy ponúkajú vizuálnu mriežku na snímkach, ktorá pomáha pri hodnotení veľkosti kontrolovanej oblasti. Pre flexibilné boroskopy sú dôležité aj komponenty kĺbového mechanizmu, rozsah artikulácie, zorné pole a zorné uhly šošovky objektívu. Obsah vlákien vo flexibilnom relé je tiež dôležitý pre poskytnutie najvyššieho možného rozlíšenia. Minimálne množstvo je 10 000 pixelov, zatiaľ čo najlepšie snímky sa získajú s vyšším počtom vlákien v rozsahu 15 000 až 22 000 pixelov pre boroskopy s väčším priemerom. Schopnosť ovládať svetlo na konci zavádzacej trubice umožňuje užívateľovi vykonávať úpravy, ktoré môžu výrazne zlepšiť čistotu zhotovených snímok. Na druhej strane, RIGID BORESCOPES vo všeobecnosti poskytuje vynikajúci obraz a nižšie náklady v porovnaní s flexibilným vŕtacím ďalekohľadom. Nedostatkom pevných boroskopov je obmedzenie, že prístup k tomu, čo sa má pozerať, musí byť v priamej línii. Preto majú tuhé boroskopy obmedzenú oblasť použitia. Pre nástroje podobnej kvality poskytuje najlepší obraz najväčší pevný boroskop, ktorý sa zmestí do otvoru. A VIDEO BORESCOPE je podobný flexibilnému boroskopu, ale používa miniatúrnu videokameru na konci ohybnej trubice. Koniec zavádzacej trubice obsahuje svetlo, ktoré umožňuje zachytiť video alebo statické obrázky hlboko v oblasti vyšetrovania. Schopnosť videoboroskopov zachytiť video a statické snímky na neskoršiu kontrolu je veľmi užitočná. Pozíciu pohľadu je možné zmeniť pomocou joysticku a zobraziť ju na obrazovke namontovanej na rukoväti. Pretože zložitý optický vlnovod je nahradený lacným elektrickým káblom, videoboroskopy môžu byť oveľa lacnejšie a potenciálne ponúkajú lepšie rozlíšenie. Niektoré boroskopy ponúkajú pripojenie cez USB kábel. Podrobnosti a ďalšie podobné vybavenie nájdete na našej webovej stránke o vybavení: http://www.sourceindustrialsupply.com CLICK Product Finder-Locator Service PREDCHÁDZAJÚCA STRANA
- Thermal Infrared Test Equipment, Thermal Camera, Differential Scanning
Thermal Infrared Test Equipment, Thermal Camera, Differential Scanning Calorimeter, Thermo Gravimetric Analyzer, Thermo Mechanical Analyzer, Dynamic Mechanical Tepelné a IR testovacie zariadenia CLICK Product Finder-Locator Service Spomedzi many TERMAL ANALYSIS EQUIPMENT sústredíme našu pozornosť na tie populárne v priemysle, konkrétne the DIFRIING, TGAMO -MECHANICKÁ ANALÝZA (TMA), DILATOMETRIA,DYNAMICKÁ MECHANICKÁ ANALÝZA (DMA), DIFERENCIÁLNA TEPELNÁ ANALÝZA (DTA). Naše INFRAČERVENÉ TESTOVACIE ZARIADENIA zahŕňajú TERMOZOBRAZOVACIE PRÍSTROJE, INFRAČERVENÉ TERMOGRAFY, INFRAČERVENÉ KAMERY. Niektoré aplikácie pre naše termovízne prístroje sú kontrola elektrických a mechanických systémov, kontrola elektronických komponentov, poškodenie koróziou a riedenie kovov, detekcia chýb. DIFERENCIÁLNE SKENOVACIE KALORIMETRY (DSC) : Technika, pri ktorej sa meria rozdiel v množstve tepla potrebného na zvýšenie teploty vzorky a referencie ako funkcia teploty. Vzorka aj referencia sa počas experimentu udržiavajú na takmer rovnakej teplote. Teplotný program pre DSC analýzu je nastavený tak, že teplota držiaka vzorky sa zvyšuje lineárne ako funkcia času. Referenčná vzorka má dobre definovanú tepelnú kapacitu v rozsahu teplôt, ktoré sa majú snímať. Experimenty DSC poskytujú ako výsledok krivku tepelného toku proti teplote alebo proti času. Diferenciálne skenovacie kalorimetre sa často používajú na štúdium toho, čo sa stane s polymérmi, keď sa zahrejú. Pomocou tejto techniky možno študovať tepelné prechody polyméru. Tepelné prechody sú zmeny, ku ktorým dochádza v polyméri pri jeho zahrievaní. Príkladom je tavenie kryštalického polyméru. Sklený prechod je tiež tepelný prechod. Tepelná analýza DSC sa vykonáva na stanovenie zmien tepelnej fázy, teploty tepelného sklovitého prechodu (Tg), teplôt kryštalickej taveniny, endotermických účinkov, exotermických účinkov, tepelnej stability, tepelnej stability formulácie, oxidačnej stability, javov prechodu, štruktúr v tuhom stave. DSC analýza určuje Tg Glass Transition Temperature, teplotu, pri ktorej amorfné polyméry alebo amorfná časť kryštalického polyméru prechádzajú z tvrdého krehkého stavu do mäkkého gumovitého stavu, bod topenia, teplotu, pri ktorej sa kryštalický polymér topí, Hm absorbovaná energia (joule /gram), množstvo energie, ktorú vzorka absorbuje pri tavení, Tc kryštalizačný bod, teplota, pri ktorej polymér kryštalizuje pri zahrievaní alebo ochladzovaní, Hc energia uvoľnená (joule/gram), množstvo energie, ktorú vzorka uvoľní pri kryštalizácii. Diferenciálne skenovacie kalorimetre možno použiť na stanovenie tepelných vlastností plastov, lepidiel, tmelov, kovových zliatin, farmaceutických materiálov, voskov, potravín, olejov a mazív a katalyzátorov... atď. DIFERENCIÁLNE TEPELNÉ ANALYZÁTORY (DTA): Alternatívna technika k DSC. Pri tejto technike tok tepla do vzorky a referencie zostáva rovnaký namiesto teploty. Keď sa vzorka a referencia zahrievajú identicky, fázové zmeny a iné tepelné procesy spôsobujú rozdiel v teplote medzi vzorkou a referenciou. DSC meria energiu potrebnú na udržanie referenčnej vzorky a vzorky na rovnakej teplote, zatiaľ čo DTA meria rozdiel v teplote medzi vzorkou a referenčnou vzorkou, keď sú obe vystavené rovnakému teplu. Sú to teda podobné techniky. THERMOMECHANICAL ANALYZER (TMA) : TMA odhaľuje zmenu rozmerov vzorky ako funkciu teploty. TMA možno považovať za veľmi citlivý mikrometer. TMA je zariadenie, ktoré umožňuje presné meranie polohy a je možné ho kalibrovať podľa známych noriem. Vzorky obklopuje systém regulácie teploty pozostávajúci z pece, chladiča a termočlánku. Kremenné, invarové alebo keramické prípravky držia vzorky počas testov. Merania TMA zaznamenávajú zmeny spôsobené zmenami voľného objemu polyméru. Zmeny voľného objemu sú objemové zmeny v polyméri spôsobené absorpciou alebo uvoľňovaním tepla spojeného s touto zmenou; strata tuhosti; zvýšený prietok; alebo zmenou relaxačného času. Je známe, že voľný objem polyméru súvisí s viskoelasticitou, starnutím, penetráciou rozpúšťadiel a rázovými vlastnosťami. Teplota skleného prechodu Tg v polyméri zodpovedá expanzii voľného objemu umožňujúceho väčšiu pohyblivosť reťazca nad týmto prechodom. Túto zmenu v TMA možno považovať za inflexiu alebo ohyb krivky tepelnej rozťažnosti, ktorá pokrýva rozsah teplôt. Teplota skleného prechodu Tg sa vypočíta dohodnutou metódou. Dokonalá zhoda nie je okamžite svedkom hodnoty Tg pri porovnávaní rôznych metód, ak však pozorne preskúmame dohodnuté metódy pri určovaní hodnôt Tg, pochopíme, že v skutočnosti existuje dobrá zhoda. Šírka Tg je okrem absolútnej hodnoty indikátorom zmien materiálu. TMA je pomerne jednoduchá technika na vykonanie. TMA sa často používa na meranie Tg materiálov, ako sú vysoko zosieťované termosetové polyméry, pre ktoré je ťažké použiť diferenciálny skenovací kalorimeter (DSC). Okrem Tg sa z termomechanickej analýzy získava aj koeficient tepelnej rozťažnosti (CTE). CTE sa vypočíta z lineárnych úsekov kriviek TMA. Ďalším užitočným výsledkom, ktorý nám TMA môže poskytnúť, je zistenie orientácie kryštálov alebo vlákien. Kompozitné materiály môžu mať tri odlišné koeficienty tepelnej rozťažnosti v smeroch x, y a z. Zaznamenaním CTE v smeroch x, y a z možno pochopiť, v ktorom smere sú vlákna alebo kryštály prevažne orientované. Na meranie objemovej expanzie materiálu možno použiť techniku s názvom DILATOMETRY . Vzorka sa ponorí do tekutiny, ako je silikónový olej alebo prášok Al2O3 v dilatometri, nechá sa prejsť teplotným cyklom a expanzia vo všetkých smeroch sa prevedie na vertikálny pohyb, ktorý sa meria pomocou TMA. Moderné termomechanické analyzátory to používateľom uľahčujú. Ak sa použije čistá kvapalina, dilatometer sa naplní touto kvapalinou namiesto kremíkového oleja alebo oxidu hlinitého. Pomocou diamantového TMA môžu používatelia vykonávať krivky deformácie napätia, experimenty s relaxáciou stresu, zotavenie po dotvarovaní a dynamické mechanické teplotné skeny. TMA je nevyhnutné testovacie zariadenie pre priemysel a výskum. TERMOGRAVIMETRICKÉ ANALYZÁTORY ( TGA ) : Termogravimetrická analýza je technika, pri ktorej sa hmotnosť látky alebo vzorky monitoruje ako funkcia teploty alebo času. Vzorka sa podrobí programu s riadenou teplotou v kontrolovanej atmosfére. TGA meria hmotnosť vzorky, keď sa zahrieva alebo chladí v peci. Prístroj TGA pozostáva z misky na vzorky, ktorá je podopretá presnými váhami. Táto panvica sa nachádza v peci a počas testu sa zahrieva alebo chladí. Počas testu sa monitoruje hmotnosť vzorky. Prostredie vzorky sa prepláchne inertným alebo reaktívnym plynom. Termogravimetrické analyzátory dokážu kvantifikovať stratu vody, rozpúšťadla, zmäkčovadla, dekarboxyláciu, pyrolýzu, oxidáciu, rozklad, hmotnostné % plniaceho materiálu a hmotnostné % popola. V závislosti od prípadu je možné získať informácie o zahrievaní alebo chladení. Typická teplotná krivka TGA sa zobrazuje zľava doprava. Ak teplotná krivka TGA klesá, znamená to stratu hmotnosti. Moderné TGA sú schopné vykonávať izotermické experimenty. Niekedy môže používateľ chcieť použiť reaktívnu vzorku preplachovacích plynov, ako je kyslík. Keď používate kyslík ako čistiaci plyn, používateľ môže chcieť počas experimentu prepnúť plyny z dusíka na kyslík. Táto technika sa často používa na identifikáciu percent uhlíka v materiáli. Termogravimetrický analyzátor možno použiť na porovnanie dvoch podobných produktov, ako nástroj kontroly kvality na zabezpečenie toho, aby produkty spĺňali ich materiálové špecifikácie, na zabezpečenie toho, aby produkty spĺňali bezpečnostné normy, na určenie obsahu uhlíka, identifikáciu falšovaných produktov, na identifikáciu bezpečných prevádzkových teplôt v rôznych plynoch, zlepšiť procesy formulácie produktu, aby sa produkt spätne analyzoval. Nakoniec stojí za zmienku, že sú dostupné kombinácie TGA s GC/MS. GC je skratka pre Gas Chromatography a MS je skratka pre Mass Spectrometry. DYNAMICKÝ MECHANICKÝ ANALYZÁTOR (DMA) : Toto je technika, pri ktorej sa cyklickým spôsobom aplikuje malá sínusová deformácia na vzorku známej geometrie. Potom sa študuje odozva materiálov na napätie, teplotu, frekvenciu a ďalšie hodnoty. Vzorka môže byť vystavená riadenému namáhaniu alebo riadenému namáhaniu. Pri známom napätí sa vzorka o určitú mieru zdeformuje v závislosti od jej tuhosti. DMA meria tuhosť a tlmenie, tieto sú uvádzané ako modul a tan delta. Pretože aplikujeme sínusovú silu, môžeme modul vyjadriť ako súčasnú zložku (akumulačný modul) a mimofázovú zložku (stratový modul). Akumulačný modul, buď E' alebo G', je mierou elastického správania vzorky. Pomer straty k zásobe je tan delta a nazýva sa tlmenie. Považuje sa za mieru rozptylu energie materiálu. Tlmenie sa mení v závislosti od stavu materiálu, jeho teploty a frekvencie. DMA sa niekedy nazýva DMTA stojaci pre_cc781905-5cde-3194-CDE-31936bad5DYNADYRM Termomechanická analýza aplikuje na materiál konštantnú statickú silu a zaznamenáva zmeny rozmerov materiálu, keď sa mení teplota alebo čas. Na druhej strane DMA aplikuje na vzorku oscilačnú silu s nastavenou frekvenciou a hlási zmeny v tuhosti a tlmení. Údaje DMA nám poskytujú informácie o module, zatiaľ čo údaje TMA nám poskytujú koeficient tepelnej rozťažnosti. Obe techniky detegujú prechody, ale DMA je oveľa citlivejšia. Hodnoty modulu sa menia s teplotou a prechody v materiáloch možno vnímať ako zmeny v krivkách E' alebo tan delta. To zahŕňa sklený prechod, tavenie a iné prechody, ktoré sa vyskytujú v sklovitom alebo gumovom plató, ktoré sú indikátormi jemných zmien v materiáli. TERMOZOBRAZOVACIE PRÍSTROJE, INFRAČERVENÉ TERMOGRAFY, INFRAČERVENÉ KAMERY : Ide o zariadenia, ktoré vytvárajú obraz pomocou infračerveného žiarenia. Štandardné každodenné fotoaparáty vytvárajú obrázky pomocou viditeľného svetla v rozsahu vlnových dĺžok 450 – 750 nanometrov. Infračervené kamery však pracujú v rozsahu infračervených vlnových dĺžok až do 14 000 nm. Vo všeobecnosti platí, že čím vyššia je teplota objektu, tým viac infračerveného žiarenia sa vyžaruje ako žiarenie čierneho telesa. Infračervené kamery fungujú aj v úplnej tme. Snímky z väčšiny infračervených kamier majú jeden farebný kanál, pretože kamery vo všeobecnosti používajú obrazový snímač, ktorý nerozlišuje rôzne vlnové dĺžky infračerveného žiarenia. Na rozlíšenie vlnových dĺžok farebné obrazové snímače vyžadujú komplexnú konštrukciu. V niektorých testovacích prístrojoch sú tieto monochromatické obrázky zobrazené v pseudofarbách, kde sa na zobrazenie zmien signálu používajú skôr zmeny farby ako zmeny intenzity. Najjasnejšie (najteplejšie) časti obrázkov sú zvyčajne zafarbené bielou farbou, stredné teploty červené a žlté a najtmavšie (najchladnejšie) časti čiernou farbou. Stupnica sa zvyčajne zobrazuje vedľa obrázka s falošnými farbami, aby sa farby spojili s teplotami. Termokamery majú rozlíšenie podstatne nižšie ako optické kamery, s hodnotami v blízkosti 160 x 120 alebo 320 x 240 pixelov. Drahšie infračervené kamery dokážu dosiahnuť rozlíšenie 1280 x 1024 bodov. Existujú dve hlavné kategórie termografických kamier: COOLED INFRAČERVENÝ OBRAZOVÝ DETEKTOR SYSTEMS_cc781905-5cde-3194-bb3b-136LEDbad5cf58d-136LEDbad5cf58d-and_and_35cc-77 Chladené termografické kamery majú detektory obsiahnuté vo vákuovo uzavretom puzdre a sú kryogénne chladené. Chladenie je nevyhnutné pre činnosť použitých polovodičových materiálov. Bez chladenia by boli tieto senzory zaplavené vlastným žiarením. Chladené infračervené kamery sú však drahé. Chladenie vyžaduje veľa energie a je časovo náročné, pričom pred prácou si vyžaduje niekoľko minút chladenia. Hoci je chladiace zariadenie objemné a drahé, chladené infračervené kamery ponúkajú používateľom vynikajúcu kvalitu obrazu v porovnaní s nechladenými kamerami. Lepšia citlivosť chladených fotoaparátov umožňuje použitie objektívov s vyššou ohniskovou vzdialenosťou. Na chladenie je možné použiť plynný dusík vo fľašiach. Nechladené termokamery využívajú snímače pracujúce pri okolitej teplote, alebo snímače stabilizované pri teplote blízkej okolitej teplote pomocou prvkov regulácie teploty. Nechladené infračervené senzory nie sú chladené na nízke teploty, a preto nevyžadujú objemné a drahé kryogénne chladiče. Ich rozlíšenie a kvalita obrazu je však nižšia v porovnaní s chladenými detektormi. Termografické kamery ponúkajú veľa možností. Prehrievajúce sa miesta je možné lokalizovať a opraviť elektrické vedenie. Je možné pozorovať elektrické obvody a nezvyčajne horúce miesta môžu naznačovať problémy, ako je skrat. Tieto kamery sú tiež široko používané v budovách a energetických systémoch na lokalizáciu miest, kde dochádza k významným tepelným stratám, takže v týchto miestach je možné zvážiť lepšiu tepelnú izoláciu. Termovízne prístroje slúžia ako nedeštruktívne testovacie zariadenie. Podrobnosti a ďalšie podobné vybavenie nájdete na našej webovej stránke o vybavení: http://www.sourceindustrialsupply.com PREDCHÁDZAJÚCA STRANA