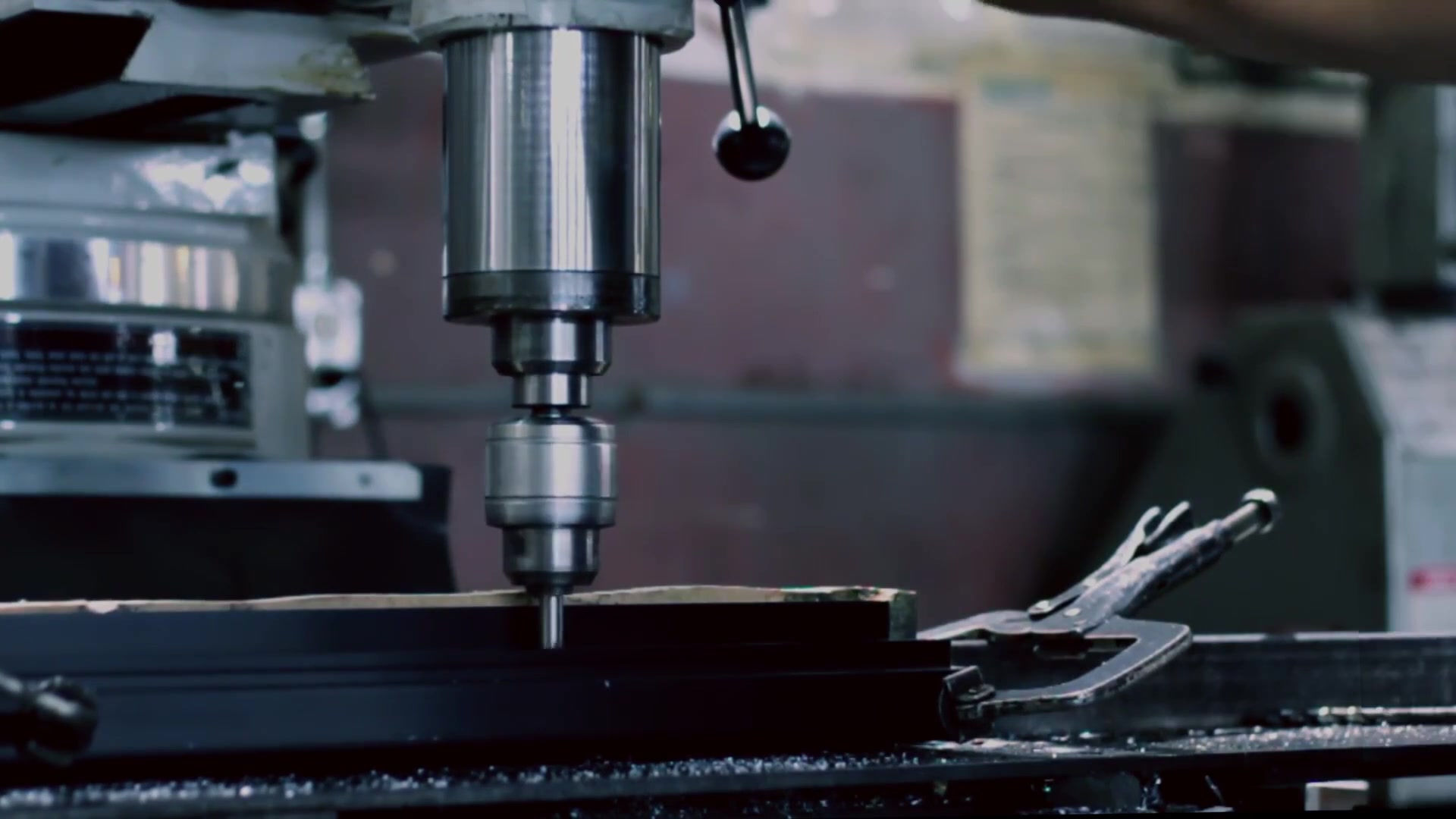
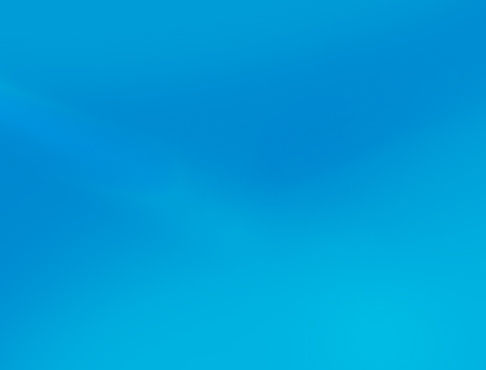
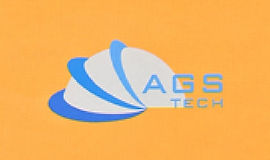
Globalni proizvajalec po meri, integrator, konsolidator, zunanji partner za široko paleto izdelkov in storitev.
Smo vaš vir na enem mestu za proizvodnjo, izdelavo, inženiring, konsolidacijo, integracijo, zunanje izvajanje izdelkov in storitev, izdelanih po meri in standardnih izdelkov.
Izberite svoj jezik
-
Izdelava po meri
-
Domača in globalna pogodbena proizvodnja
-
Zunanje izvajanje proizvodnje
-
Domača in svetovna javna naročila
-
Konsolidacija
-
Inženirska integracija
-
Inženirske storitve
ELECTRICAL DISCHARGE MACHINING (EDM), also referred to as SPARK-EROSION or ELECTRODISCHARGE MACHINING, SPARK ERODING, DIE SINKING_cc781905-5cde-3194-bb3b -136bad5cf58d_or WIRE EROSION, is a NON-CONVENTIONAL MANUFACTURING process where erosion of metals takes place and desired shape is obtained using electrical discharges in the form iskric. Ponujamo tudi nekatere različice EDM, in sicer NO-WEAR EDM, ŽIČNO EDM (WEDM), EDM GRINDING (EDG), DIE-SINKING EDM, ELEKTRIČNO RAZKRENJENO REZKANJE, mikro-EDM, m-EDM_cc781905 -5cde-3194-bb3b-136bad5cf58d_and ELEKTROKEMIJSKO-PRAZNJENJE BRUSENJE (ECDG). Naši sistemi EDM so sestavljeni iz oblikovanih orodij/elektrod in obdelovanca, priključenih na enosmerne napajalnike in vstavljenih v električno neprevodno dielektrično tekočino. Po letu 1940 je strojna obdelava z električnim praznjenjem postala ena najpomembnejših in priljubljenih proizvodnih tehnologij v predelovalni industriji.
Ko se razdalja med elektrodama zmanjša, postane jakost električnega polja v prostornini med elektrodama na nekaterih točkah večja od jakosti dielektrika, ki se zlomi in sčasoma tvori most za pretok toka med obema elektrodama. Ustvari se močan električni oblok, ki povzroči znatno segrevanje, da stopi del obdelovanca in nekaj materiala orodja. Posledično se material odstrani z obeh elektrod. Istočasno se dielektrična tekočina hitro segreje, kar povzroči izhlapevanje tekočine v obločni reži. Ko se tok ustavi ali se ustavi, plinskemu mehurčku okoliška dielektrična tekočina odvzame toploto in mehurček kavitira (sesede). Udarni val, ki nastane zaradi sesedanja mehurčka in toka dielektrične tekočine, odplakne ostanke s površine obdelovanca in v dielektrično tekočino potegne ves staljeni material obdelovanca. Hitrost ponavljanja teh razelektritev je med 50 do 500 kHz, napetosti med 50 do 380 V in tokovi med 0,1 in 500 amperov. Nov tekoči dielektrik, kot so mineralna olja, kerozin ali destilirana in deionizirana voda, se običajno prenese v prostornino med elektrodami, ki odnaša trdne delce (v obliki ostankov) in ponovno vzpostavi izolacijske lastnosti dielektrika. Po pretoku toka se potencialna razlika med obema elektrodama povrne na tisto, kar je bila pred razpadom, zato lahko pride do novega preboja tekočega dielektrika. Naši sodobni stroji z električnim praznjenjem (EDM) ponujajo numerično krmiljene premike in so opremljeni s črpalkami in filtrirnimi sistemi za dielektrične tekočine.
Obdelava z električnim praznjenjem (EDM) je metoda obdelave, ki se uporablja predvsem za trde kovine ali tiste, ki bi jih bilo zelo težko obdelati s konvencionalnimi tehnikami. EDM običajno deluje z vsemi materiali, ki so električni prevodniki, čeprav so bile predlagane tudi metode za strojno obdelavo izolacijske keramike z EDM. Tališče in latentna toplota taljenja sta lastnosti, ki določata prostornino odstranjene kovine na izpust. Višje kot so te vrednosti, počasnejša je hitrost odstranjevanja materiala. Ker postopek obdelave z električnim praznjenjem ne vključuje mehanske energije, trdota, trdnost in žilavost obdelovanca ne vplivajo na hitrost odstranjevanja. Frekvenca praznjenja ali energija na praznjenje, napetost in tok se spreminjajo za nadzor hitrosti odstranjevanja materiala. Hitrost odstranjevanja materiala in hrapavost površine se povečata z večanjem gostote toka in zmanjševanjem frekvence iskre. Z EDM lahko izrežemo zapletene konture ali votline v predhodno kaljeno jeklo brez potrebe po toplotni obdelavi za njihovo mehčanje in ponovno utrjevanje. To metodo lahko uporabimo s katero koli kovino ali kovinskimi zlitinami, kot so titan, hastelloy, kovar in inconel. Uporaba postopka EDM vključuje oblikovanje polikristalnih diamantnih orodij. EDM velja za netradicionalno ali nekonvencionalno metodo obdelave skupaj s postopki, kot so elektrokemijska obdelava (ECM), rezanje z vodnim curkom (WJ, AWJ), lasersko rezanje. Po drugi strani konvencionalne metode obdelave vključujejo struženje, rezkanje, brušenje, vrtanje in druge postopke, katerih mehanizem za odstranjevanje materiala v bistvu temelji na mehanskih silah. Elektrode za elektroerozijske obdelave (EDM) so izdelane iz grafita, medenine, bakra in bakrovo-volframove zlitine. Možni so premeri elektrod do 0,1 mm. Ker je obraba orodja nezaželen pojav, ki negativno vpliva na dimenzijsko natančnost pri EDM, izkoriščamo prednosti postopka, imenovanega NO-WEAR EDM, z obračanjem polaritete in uporabo bakrenih orodij za zmanjšanje obrabe orodja.
V idealnem primeru lahko obdelavo z električnim praznjenjem (EDM) obravnavamo kot serijo razgradnje in obnavljanja dielektrične tekočine med elektrodama. V resnici pa je odstranitev ostankov iz območja med elektrodama skoraj vedno delna. To povzroči, da se električne lastnosti dielektrika v območju med elektrodama razlikujejo od njihovih nominalnih vrednosti in se spreminjajo s časom. Razdalja med elektrodama (iskrilna reža) je prilagojena s krmilnimi algoritmi določenega uporabljenega stroja. Iskrišče v EDM lahko na žalost včasih povzroči kratek stik zaradi ostankov. Nadzorni sistem elektrode se morda ne bo odzval dovolj hitro, da bi preprečil kratek stik obeh elektrod (orodja in obdelovanca). Ta nezaželen kratek stik prispeva k odstranitvi materiala drugače kot v idealnem primeru. Izjemno pomembnost posvečamo izpiranju, da obnovimo izolacijske lastnosti dielektrika, tako da se tok vedno dogaja v točki medelektrodnega območja, s čimer se zmanjša možnost neželene spremembe oblike (poškodbe) orodja-elektrode. in obdelovanec. Za pridobitev določene geometrije se EDM orodje vodi po želeni poti zelo blizu obdelovanca, ne da bi se ga dotaknilo. Največjo pozornost posvečamo učinkovitosti krmiljenja gibanja pri uporabi. Na ta način pride do velikega števila tokovnih razelektritev/isker, ki prispevajo k odstranitvi materiala tako z orodja kot obdelovanca, kjer nastanejo majhni kraterji. Velikost kraterjev je funkcija tehnoloških parametrov, nastavljenih za določeno opravilo, dimenzije pa lahko segajo od nanometrov (kot na primer v primeru operacij mikro-EDM) do nekaj sto mikrometrov v pogojih grobe obdelave. Ti majhni kraterji na orodju povzročajo postopno erozijo elektrode, imenovano "obraba orodja". Da bi preprečili škodljiv učinek obrabe na geometrijo obdelovanca, nenehno menjamo elektrodo orodja med obdelavo. Včasih to dosežemo z uporabo nenehno menjane žice kot elektrode (ta postopek EDM se imenuje tudi WIRE EDM ). Včasih uporabljamo orodje-elektrodo tako, da le majhen del dejansko sodeluje pri obdelavi in ta del sproti menjamo. To je na primer pri uporabi vrtljivega diska kot orodja-elektrode. Ta postopek se imenuje EDM BRUŠENJE. Še ena tehnika, ki jo uporabljamo, je sestavljena iz uporabe niza elektrod različnih velikosti in oblik med isto operacijo EDM za kompenzacijo obrabe. To imenujemo tehnika več elektrod in se najpogosteje uporablja, ko elektroda orodja v negativu posnema želeno obliko in se pomika proti surovcu v eni smeri, običajno v navpični smeri (tj. osi z). To spominja na pogrezanje orodja v dielektrično tekočino, v katero je potopljen obdelovanec, zato se imenuje DIE-SINKING EDM (včasih imenovan _cc781905-5c 3194-bb3b-136bad5cf58d_CONVENTIONAL EDM or RAM EDM). Stroji za to operacijo se imenujejo SINKER EDM. Elektrode za to vrsto EDM so kompleksne oblike. Če je končna geometrija pridobljena z običajno preprosto oblikovano elektrodo, premikano v več smereh in je tudi podvržena vrtenju, imenujemo to EDM REZKANJE. Količina obrabe je strogo odvisna od tehnoloških parametrov, uporabljenih pri delovanju (polarnost, največji tok, napetost odprtega tokokroga). Na primer, in micro-EDM, znan tudi kot m-EDM, so ti parametri običajno nastavljeni na vrednosti, ki povzročajo močno obrabo. Zato je obraba na tem področju velik problem, ki ga minimiziramo z našim zbranim znanjem in izkušnjami. Da bi na primer zmanjšali obrabo grafitnih elektrod, digitalni generator, ki ga je mogoče nadzorovati v milisekundah, obrne polarnost, ko pride do elektroerozije. Posledica tega je učinek, podoben galvaniziranju, pri katerem se erodirani grafit nenehno odlaga nazaj na elektrodo. Pri drugi metodi, tako imenovanem vezju ''Zero Wear'', zmanjšamo, kako pogosto se praznjenje začne in ustavi, tako da ostane vključeno čim dlje. Hitrost odvzema materiala pri strojni obdelavi z električnim praznjenjem je mogoče oceniti iz:
MRR = 4 x 10 exp(4) x I x Tw exp (-1,23)
Tukaj je MRR v mm3/min, I je tok v amperih, Tw je tališče obdelovanca v K-273,15K. exp pomeni eksponent.
Po drugi strani pa lahko stopnjo obrabe Wt elektrode dobimo iz:
Wt = (1,1 x 10exp(11)) x I x Ttexp(-2,38)
Tukaj je Wt v mm3/min in Tt je tališče materiala elektrode v K-273,15K
Končno lahko razmerje obrabe obdelovanca in elektrode R dobimo iz:
R = 2,25 x Trexp (-2,38)
Tu je Tr razmerje med tališči obdelovanca in elektrode.
SINKER EDM :
Grezilo EDM, imenovano tudi CAVITY TYPE EDM or EDM, sestavljeno iz obdelovanca v tekočini in subsumerted elektrodi VOLUME. Elektroda in obdelovanec sta priključena na napajanje. Napajalnik ustvarja električni potencial med obema. Ko se elektroda približa obdelovancu, v tekočini pride do preboja dielektrika, ki tvori plazemski kanal, in majhna iskra preskoči. Iskre običajno udarijo ena za drugo, ker je zelo malo verjetno, da imajo različne lokacije v medelektrodnem prostoru enake lokalne električne značilnosti, ki bi omogočile, da se iskra pojavi na vseh takih lokacijah hkrati. Na stotisoče teh isker se zgodi na naključnih točkah med elektrodo in obdelovancem na sekundo. Ko osnovna kovina erodira in se iskrišče posledično poveča, naš CNC stroj samodejno spusti elektrodo, tako da se lahko proces nemoteno nadaljuje. Naša oprema ima kontrolne cikle, znane kot "čas vklopa" in "čas izklopa". Nastavitev časa vklopa določa dolžino ali trajanje iskre. Daljši čas delovanja povzroči globljo votlino za to iskro in vse naslednje iskre za ta cikel, kar ustvari grobejšo končno obdelavo obdelovanca in obratno. Čas izklopa je čas, ko eno iskro zamenja druga. Daljši čas izklopa omogoča, da se dielektrična tekočina splakne skozi šobo, da očisti erodirane ostanke in se tako izogne kratkemu stiku. Te nastavitve se prilagodijo v mikro sekundah.
WIRE EDM :
In WIRE ELECTRICAL DISCHARGE MACHINING (WEDM), also called WIRE-CUT EDM or WIRE CUTTING, we feed a tanka enožilna kovinska žica iz medenine skozi obdelovanec, ki je potopljen v posodo z dielektrično tekočino. Žična EDM je pomembna različica EDM. Občasno uporabljamo žično erozijo za rezanje plošč do debeline 300 mm in za izdelavo lukenj, orodij in matric iz trdih kovin, ki jih je težko obdelati z drugimi proizvodnimi metodami. V tem procesu, ki je podoben konturnemu rezanju s tračno žago, se žica, ki se nenehno dovaja iz koluta, drži med zgornjim in spodnjim diamantnim vodilom. CNC-krmiljena vodila se premikajo v ravnini x–y, zgornje vodilo pa se lahko premika tudi neodvisno v osi z–u–v, kar daje možnost rezanja stožčastih in prehodnih oblik (kot je krog na dnu in kvadrat na vrh). Zgornje vodilo lahko nadzoruje premike osi v x–y–u–v–i–j–k–l–. To omogoča WEDM rezanje zelo zapletenih in občutljivih oblik. Povprečni rezalni rez naše opreme, ki dosega najboljše ekonomske stroške in čas obdelave, je 0,335 mm z uporabo Ø 0,25 medeninaste, bakrene ali volframove žice. Vendar pa so zgornja in spodnja diamantna vodila naše CNC opreme natančna do približno 0,004 mm in imajo lahko rezalno pot ali zarezo tako majhno kot 0,021 mm z uporabo žice Ø 0,02 mm. Možni so torej res ozki kroji. Širina reza je večja od širine žice, ker prihaja do iskrenja od strani žice do obdelovanca, kar povzroča erozijo. Ta "presek" je potreben, za mnoge aplikacije je predvidljiv in ga je zato mogoče nadomestiti (v mikro-EDM to ni pogosto). Žični koluti so dolgi - 8 kg kolut žice 0,25 mm je dolg nekaj več kot 19 kilometrov. Premer žice je lahko le 20 mikrometrov, natančnost geometrije pa je v bližini +/- 1 mikrometra. Žico običajno uporabimo samo enkrat in jo recikliramo, ker je razmeroma poceni. Potuje s konstantno hitrostjo od 0,15 do 9 m/min in med rezanjem se vzdržuje stalen zarez (reža). V postopku žične elektroerozije uporabljamo vodo kot dielektrično tekočino, njeno upornost in druge električne lastnosti pa nadzorujemo s filtri in deionizacijskimi enotami. Voda odplakne odrezane ostanke stran od območja rezanja. Splakovanje je pomemben dejavnik pri določanju največje hitrosti podajanja za določeno debelino materiala, zato jo ohranjamo dosledno. Hitrost rezanja pri žični EDM je navedena kot površina prečnega prereza na časovno enoto, na primer 18.000 mm2/uro za orodno jeklo D2 debeline 50 mm. Linearna hitrost rezanja v tem primeru bi bila 18.000/50 = 360 mm/h Hitrost odstranjevanja materiala pri žični EDM je:
MRR = Vf xhxb
Tu je MRR v mm3/min, Vf je hitrost podajanja žice v obdelovanec v mm/min, h je debelina ali višina v mm, b pa je rez, ki je:
b = dw + 2s
Tukaj je dw premer žice in s je razmik med žico in obdelovancem v mm.
Skupaj z strožjimi tolerancami so naši sodobni večosni obdelovalni centri za žično rezanje EDM dodali funkcije, kot so večglave za rezanje dveh delov hkrati, krmiljenje za preprečevanje zloma žice, funkcije samodejnega vrezovanja navojev v primeru zloma žice in programirano strategije obdelave za optimizacijo delovanja, zmogljivosti ravnega in kotnega rezanja.
Wire-EDM nam ponuja nizke zaostale napetosti, saj ne zahteva velikih rezalnih sil za odstranjevanje materiala. Kadar je energija/moč na impulz razmeroma nizka (kot pri končnih postopkih), se zaradi nizkih preostalih napetosti pričakuje majhna sprememba mehanskih lastnosti materiala.
ELEKTRIČNO BRUŠENJE (EDG) : Brusi ne vsebujejo abrazivov, izdelani so iz grafita ali medenine. Ponavljajoče se iskre med vrtljivim kolesom in obdelovancem odstranjujejo material s površin obdelovanca. Stopnja odstranitve materiala je:
MRR = K x I
Tukaj je MRR v mm3/min, I je tok v amperih, K pa je faktor materiala obdelovanca v mm3/A-min. Za žaganje ozkih rež na komponentah pogosto uporabljamo elektroerozijsko brušenje. Včasih združujemo postopek EDG (električno razelektritveno mletje) s postopkom ECG (elektrokemijsko mletje), kjer material odstranimo s kemičnim delovanjem, pri čemer električne razelektritve iz grafitnega kolesa razbijejo oksidni film in ga spere elektrolit. Postopek se imenuje ELECTROCHEMICAL-DISCHARGE GRINDING (ECDG). Čeprav postopek ECDG porabi sorazmerno več energije, je hitrejši postopek od EDG. S to tehniko večinoma brusimo orodja iz karbidne trdine.
Uporaba obdelave z električnim praznjenjem:
Proizvodnja prototipa:
Postopek EDM uporabljamo pri izdelavi kalupov, orodij in matric, pa tudi za izdelavo prototipov in proizvodnih delov, zlasti za vesoljsko, avtomobilsko in elektronsko industrijo, kjer so proizvodne količine relativno majhne. Pri grezilu EDM je grafitna, bakrena volframova ali čista bakrena elektroda obdelana v želeno (negativno) obliko in dovedena v obdelovanec na koncu navpičnega bata.
Izdelava kovancev:
Za izdelavo matric za izdelavo nakita in značk s postopkom kovanja (žigosanja) se lahko pozitivni master izdela iz srebra, saj je (ob ustreznih strojnih nastavitvah) master močno erodiran in se uporablja samo enkrat. Nastala negativna matrica se nato utrdi in uporabi v udarnem kladivu za izdelavo žigosanih plošč iz izrezanih surovcev iz bronaste, srebrne ali zlate zlitine z nizko trdnostjo. Pri značkah se lahko te ravnine dodatno oblikujejo v ukrivljeno površino z drugo matrico. Ta vrsta EDM se običajno izvaja potopljena v dielektrik na oljni osnovi. Končni predmet je mogoče dodatno oplemenititi s trdim (steklo) ali mehkim (barva) emajliranjem in/ali galvanizirati s čistim zlatom ali nikljem. Mehkejši materiali, kot je srebro, so lahko ročno vgravirani kot izboljšava.
Vrtanje majhnih lukenj:
Na naših strojih za žično erozijo uporabljamo erozijo z vrtanjem majhnih lukenj, da naredimo skoznjo luknjo v obdelovancu, skozi katero napeljemo žico za postopek erozije z žico. Ločene glave EDM, posebej za vrtanje majhnih lukenj, so nameščene na naših strojih za rezanje z žico, kar omogoča, da se iz velikih utrjenih plošč po potrebi in brez predhodnega vrtanja erodirajo končni deli. EDM z majhnimi luknjami uporabljamo tudi za vrtanje vrst lukenj v robove turbinskih lopatic, ki se uporabljajo v reaktivnih motorjih. Pretok plina skozi te majhne luknje omogoča, da motorji uporabljajo višje temperature, kot bi bile sicer možne. Visokotemperaturne, zelo trde monokristalne zlitine, iz katerih so izdelana ta rezila, otežujejo in celo onemogočajo običajno strojno obdelavo teh lukenj z visokim razmerjem stranic. Druga področja uporabe EDM z majhnimi luknjami so ustvarjanje mikroskopskih odprtin za komponente sistema za gorivo. Poleg integriranih EDM glav uvajamo samostojne EDM stroje za vrtanje majhnih lukenj z osemi x–y za obdelavo slepih ali skoznjih lukenj. EDM vrta luknje z dolgo elektrodo iz medenine ali bakrene cevi, ki se vrti v vpenjalni glavi s stalnim tokom destilirane ali deionizirane vode, ki teče skozi elektrodo kot sredstvo za izpiranje in dielektrik. Nekateri EDM za vrtanje majhnih lukenj lahko izvrtajo 100 mm mehkega ali celo utrjenega jekla v manj kot 10 sekundah. Pri tem postopku vrtanja je mogoče doseči luknje med 0,3 mm in 6,1 mm.
Strojna obdelava razpadanja kovin:
Imamo tudi posebne EDM stroje, namenjene odstranjevanju pokvarjenega orodja (svedrov ali svedrov) z obdelovancev. Ta postopek se imenuje "strojna obdelava z razpadom kovin".
Prednosti in slabosti obdelave z električnim praznjenjem:
Prednosti EDM vključujejo strojno obdelavo:
- Kompleksne oblike, ki bi jih sicer težko izdelali z običajnimi rezalnimi orodji
- Izjemno trd material z zelo majhnimi tolerancami
- Zelo majhni obdelovanci, pri katerih lahko običajna rezalna orodja poškodujejo del zaradi prekomernega pritiska rezalnega orodja.
- Med orodjem in obdelovancem ni neposrednega stika. Zato je mogoče občutljive dele in šibke materiale strojno obdelati brez popačenja.
- Lahko se doseže dobra površinska obdelava.
- Zelo fine luknje je mogoče enostavno izvrtati.
Slabosti EDM vključujejo:
- Počasna hitrost odstranjevanja materiala.
- Dodatni čas in stroški, porabljeni za izdelavo elektrod za EDM bata/grezila.
- Reprodukcija ostrih kotov na obdelovancu je težavna zaradi obrabe elektrod.
- Poraba energije je visoka.
- Nastane ''Overcut''.
- Med obdelavo pride do prekomerne obrabe orodja.
- Električno neprevodne materiale je možno strojno obdelovati le s posebno nastavitvijo procesa.