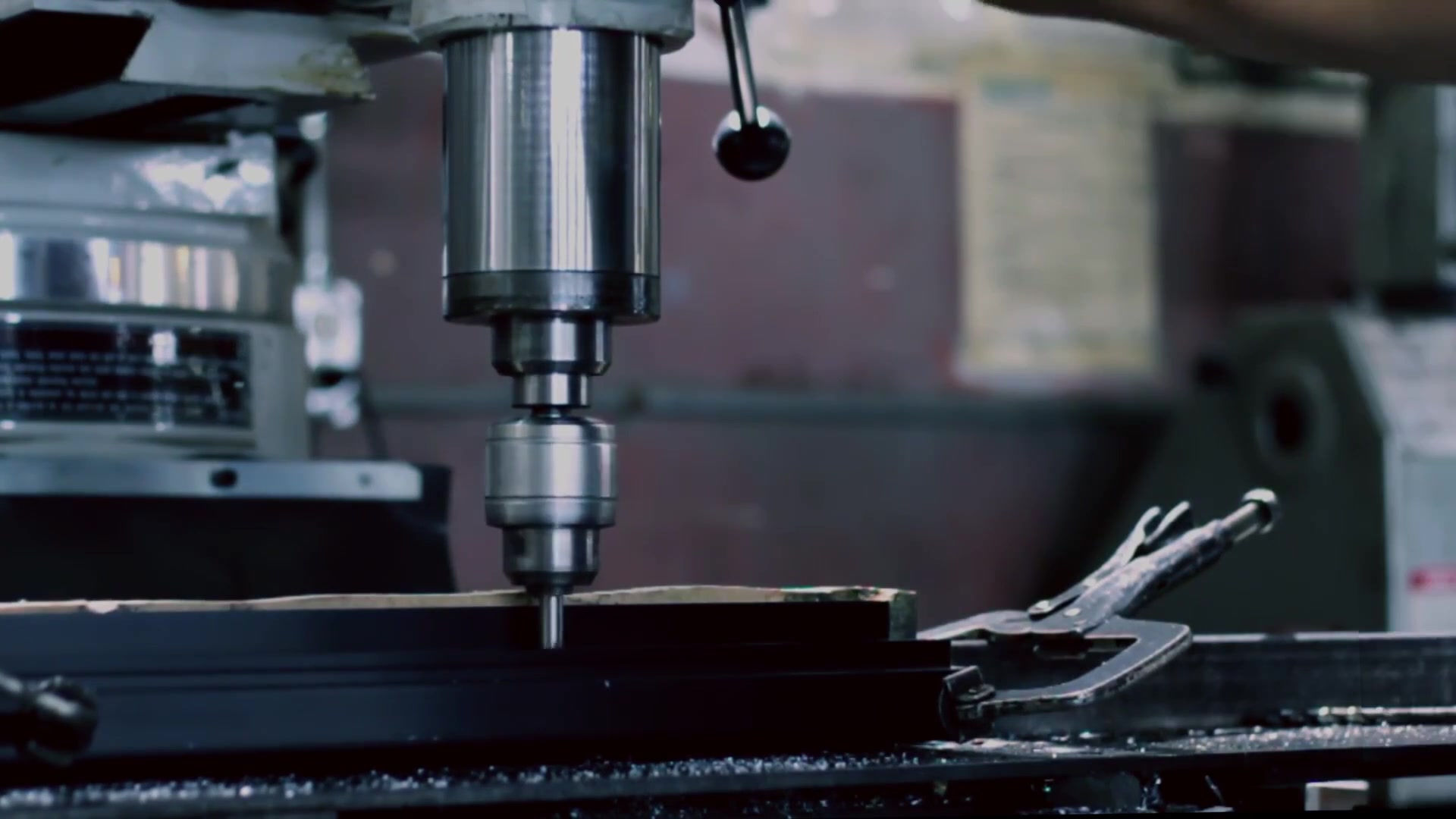
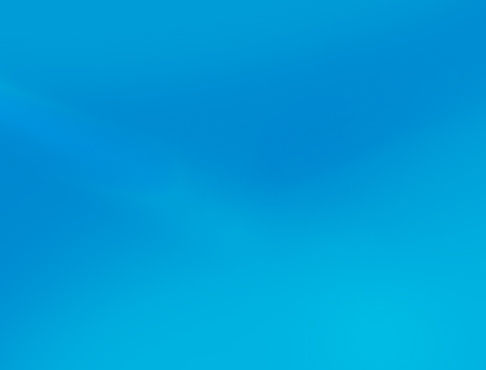
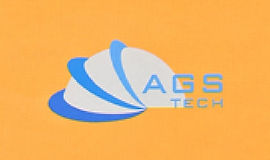
Globalni proizvajalec po meri, integrator, konsolidator, zunanji partner za široko paleto izdelkov in storitev.
Smo vaš vir na enem mestu za proizvodnjo, izdelavo, inženiring, konsolidacijo, integracijo, zunanje izvajanje izdelkov in storitev, izdelanih po meri in standardnih izdelkov.
Izberite svoj jezik
-
Izdelava po meri
-
Domača in globalna pogodbena proizvodnja
-
Zunanje izvajanje proizvodnje
-
Domača in svetovna javna naročila
-
Konsolidacija
-
Inženirska integracija
-
Inženirske storitve
Vrsta proizvodnje stekla, ki jo ponujamo, je steklena posoda, pihanje stekla, steklena vlakna, cevi in palice, gospodinjska in industrijska steklena posoda, svetilke in žarnice, natančno oblikovanje stekla, optične komponente in sklopi, ravno in ploščato steklo ter float steklo. Izvajamo tako ročno kot tudi strojno preoblikovanje.
Naši priljubljeni postopki izdelave tehnične keramike so stiskanje, izostatično stiskanje, vroče izostatično stiskanje, vroče stiskanje, drsno litje, litje trakov, ekstrudiranje, brizganje, zelena strojna obdelava, sintranje ali žganje, diamantno brušenje, hermetični sklopi.
Priporočamo, da kliknete tukaj
PRENESITE naše shematske ilustracije procesov oblikovanja in oblikovanja stekla podjetja AGS-TECH Inc.
PRENESITE naše shematične ilustracije proizvodnih procesov tehnične keramike podjetja AGS-TECH Inc.
Te prenosljive datoteke s fotografijami in skicami vam bodo pomagale bolje razumeti informacije, ki vam jih posredujemo spodaj.
• PROIZVODNJA EMBALAŽNEGA STEKLA: Za proizvodnjo imamo avtomatizirane linije PRESS AND BLOW ter BLOW AND BLOW. V procesu pihanja in pihanja spustimo kepico v prazen kalup in oblikujemo vrat s pihanjem stisnjenega zraka od zgoraj. Takoj za tem se stisnjen zrak drugič vpihne iz druge smeri skozi vrat posode, da se oblikuje predoblika steklenice. Ta predoblika se nato prenese v dejanski kalup, ponovno segreje, da se zmehča, in uporabi stisnjen zrak, da predoblika dobi končno obliko posode. Natančneje, pod pritiskom je in potisnjen proti stenam votline kalupa za pihanje, da zavzame želeno obliko. Končno se izdelana steklena posoda prenese v žarilno peč za naknadno ponovno segrevanje in odstranitev napetosti, ki nastanejo med oblikovanjem, in se kontrolirano ohladi. Pri metodi stiskanja in pihanja se staljene kepe dajo v kalup za parison (prazni kalup) in stisnejo v obliko parison (prazna oblika). Surovci se nato prenesejo v kalupe za pihanje in jih pihajo podobno kot postopek, opisan zgoraj pod “Postopek pihanja in pihanja”. Nadaljnji koraki, kot sta žarjenje in razbremenitev napetosti, so podobni ali enaki.
• PIHANJE STEKLA: Izdelke iz stekla izdelujemo tako z običajnim ročnim pihanjem kot tudi s stisnjenim zrakom z avtomatsko opremo. Za nekatera naročila je potrebno običajno pihanje, kot so projekti, ki vključujejo umetnine iz stekla, ali projekti, ki zahtevajo manjše število delov z ohlapnimi tolerancami, izdelava prototipov/demo projekti… itd. Običajno pihanje stekla vključuje potopitev votle kovinske cevi v posodo s staljenim steklom in vrtenje cevi za zbiranje določene količine steklenega materiala. Steklo, nabrano na konici cevi, valjamo po ploščatem železu, oblikujemo po želji, podolgujemo, ponovno segrejemo in pihamo. Ko je pripravljen, se vstavi v kalup in vpihne zrak. Votlina kalupa je mokra, da preprečite stik stekla s kovino. Vodni film deluje kot blazina med njimi. Ročno pihanje je delovno intenziven počasen postopek in primeren samo za izdelavo prototipov ali predmetov visoke vrednosti, ni primeren za poceni naročila velikih količin na kos.
• PROIZVODNJA STEKLENIH IZDELKOV ZA GOSPODINJSTVO IN INDUSTRIJO: Z uporabo različnih vrst steklenih materialov se izdeluje veliko različnih steklenih izdelkov. Nekateri kozarci so odporni na vročino in primerni za laboratorijsko stekleno posodo, nekateri pa so dovolj dobri, da zdržijo večkrat pomivanje v pomivalnem stroju in so primerni za izdelavo domačih izdelkov. Z uporabo strojev Westlake se proizvede na desettisoče kosov kozarcev na dan. Če poenostavimo, staljeno steklo zbiramo z vakuumom in ga vstavimo v kalupe za izdelavo predoblik. Nato se v kalupe vpihne zrak, ti se prenesejo v drug kalup in spet se vpihne zrak in steklo dobi končno obliko. Tako kot pri ročnem pihanju se ti kalupi ohranjajo mokri z vodo. Nadaljnje raztezanje je del končne operacije, kjer se oblikuje vrat. Odvečno steklo sežge. Nato sledi postopek nadzorovanega ponovnega segrevanja in hlajenja, opisan zgoraj.
• OBLIKOVANJE STEKLENIH CEV IN PALIC: Glavni postopki, ki jih uporabljamo za proizvodnjo steklenih cevi, sta postopka DANNER in VELLO. Pri Dannerjevem postopku steklo iz peči teče in pade na nagnjen tulec iz ognjevzdržnih materialov. Tulec se prenaša na vrteči se votli gredi ali pihalniku. Steklo se nato ovije okoli tulca in tvori gladko plast, ki teče navzdol po tulcu in čez konico gredi. Pri cevastem preoblikovanju zrak vpihujemo skozi pihalo z votlo konico, pri paličastem pa uporabljamo polne konice na gredi. Cevi ali palice se nato potegnejo čez nosilne valje. Dimenzije, kot sta debelina stene in premer steklenih cevi, se prilagodijo želenim vrednostim z nastavitvijo premera tulca in zračnega tlaka pihanja na želeno vrednost, prilagajanjem temperature, hitrosti pretoka stekla in hitrosti vlečenja. Po drugi strani postopek izdelave steklene cevi Vello vključuje steklo, ki potuje iz peči in v skledo z votlim trnom ali zvonom. Steklo gre nato skozi zračni prostor med trnom in skledo ter dobi obliko cevi. Nato potuje preko valjev do risalnega stroja in se ohladi. Na koncu hladilne linije poteka razrez in končna obdelava. Dimenzije cevi se lahko prilagajajo tako kot pri Dannerjevem postopku. Ko primerjamo postopek Danner s postopkom Vello, lahko rečemo, da je postopek Vello bolj primeren za proizvodnjo velikih količin, medtem ko je postopek Danner morda bolj primeren za natančna naročila cevi manjše prostornine.
• PREDELAVA PLOŠČASTEGA & PLOŠČANEGA & FLOAT STEKLA: Imamo velike količine ravnega stekla v debelinah od submilimetrskih debelin do nekaj centimetrov. Naša ravna stekla so skoraj optično popolna. Nudimo steklo s posebnimi premazi, kot so optični premazi, kjer se s tehniko kemičnega naparjevanja nanesejo premazi, kot je antirefleks ali zrcalni premaz. Pogosti so tudi prozorni prevodni premazi. Na voljo so tudi hidrofobni ali hidrofilni premazi na steklu ter premazi, ki poskrbijo, da se steklo samočisti. Kaljena, neprebojna in laminirana stekla so še drugi priljubljeni izdelki. Steklo razrežemo v želene oblike z želenimi tolerancami. Na voljo so tudi drugi sekundarni postopki, kot je krivljenje ali krivljenje ravnega stekla.
• PRECIZNO VLIVANJE STEKLA: to tehniko večinoma uporabljamo za izdelavo natančnih optičnih komponent brez potrebe po dražjih in dolgotrajnejših tehnikah, kot so brušenje, lepljenje in poliranje. Ta tehnika ni vedno zadostna za izdelavo najboljšega iz najboljše optike, toda v nekaterih primerih, kot so potrošniški izdelki, digitalni fotoaparati, medicinska optika, je lahko cenejša dobra možnost za velikoserijsko proizvodnjo. Prav tako ima prednost pred drugimi tehnikami oblikovanja stekla, kjer so potrebne zapletene geometrije, na primer v primeru kroglic. Osnovni proces vključuje nalaganje spodnje strani našega kalupa s steklenim surovcem, praznjenje procesne komore za odstranitev kisika, bližnje zaprtje kalupa, hitro in izotermno segrevanje matrice in stekla z infrardečo svetlobo, nadaljnje zapiranje polovic kalupa. počasno kontrolirano stiskanje zmehčanega stekla do želene debeline in na koncu ohlajanje stekla in polnjenje komore z dušikom ter odstranitev produkta. Natančen nadzor temperature, razdalja zapiranja kalupa, sila zapiranja kalupa, ujemanje koeficientov razteznosti kalupa in steklenega materiala so ključni pri tem procesu.
• PROIZVODNJA STEKLENIH OPTIČNIH KOMPONENT IN SKLOPOV : Poleg natančnega oblikovanja stekla obstaja vrsta dragocenih postopkov, ki jih uporabljamo za izdelavo visoko kakovostnih optičnih komponent in sklopov za zahtevne aplikacije. Brušenje, lepljenje in poliranje stekel optičnega razreda v finih posebnih abrazivnih goščah je umetnost in znanost za izdelavo optičnih leč, prizem, plošč in še več. Ploskost, valovitost, gladkost in optične površine brez napak zahtevajo veliko izkušenj s takšnimi postopki. Majhne spremembe v okolju lahko povzročijo izdelke, ki ne ustrezajo specifikacijam, in zaustavitev proizvodne linije. Obstajajo primeri, ko lahko z enim samim brisanjem optične površine s čisto krpo dosežete, da izdelek izpolnjuje specifikacije ali pa ne uspe na preizkusu. Nekateri uporabljeni priljubljeni stekleni materiali so taljeni silicijev dioksid, kremen, BK7. Tudi sestavljanje takšnih komponent zahteva specializirane nišne izkušnje. Včasih se uporabljajo posebna lepila. Vendar je včasih tehnika, imenovana optični kontakt, najboljša izbira in ne vključuje nobenega materiala med pritrjenimi optičnimi stekli. Sestoji iz fizičnega stika ravnih površin, ki se med seboj pritrdijo brez lepila. V nekaterih primerih se uporabljajo mehanski distančniki, natančne steklene palice ali kroglice, objemke ali strojno obdelane kovinske komponente za sestavljanje optičnih komponent na določenih razdaljah in v določeni geometrijski orientaciji ena glede na drugo. Oglejmo si nekaj naših priljubljenih tehnik za izdelavo vrhunske optike.
BRUŠENJE IN LEPANJE IN POLIRANJE: Grobo obliko optične komponente dobimo z brušenjem surovca stekla. Nato se izvede lepljenje in poliranje z vrtenjem in drgnjenjem hrapavih površin optičnih komponent ob orodja želene oblike površine. Med optiko in orodja za oblikovanje se vlijejo gošče z drobnimi abrazivnimi delci in tekočino. Velikosti abrazivnih delcev v takih goščah se lahko izberejo glede na želeno stopnjo ravnosti. Odstopanja kritičnih optičnih površin od želenih oblik so izražena z valovno dolžino uporabljene svetlobe. Naša visoko natančna optika ima tolerance desetinke valovne dolžine (valovna dolžina/10) ali pa so možne tudi manjše. Poleg površinskega profila se kritične površine skenirajo in ovrednotijo za druge površinske značilnosti in napake, kot so dimenzije, praske, odrezki, jamice, lise ... itd. Zaradi strogega nadzora okoljskih pogojev v optični proizvodnji ter obsežnih meroslovnih in preskusnih zahtev z najsodobnejšo opremo je to zahtevna panoga industrije.
• SEKUNDARNI POSTOPKI V PROIZVODNJI STEKLA: Ponovno smo omejeni le z vašo domišljijo, ko gre za sekundarne in dodelavne postopke stekla. Tukaj navajamo nekaj izmed njih:
-Prevleke na steklu (optične, električne, tribološke, termične, funkcionalne, mehanske...). Kot primer lahko spremenimo površinske lastnosti stekla, tako da na primer odseva toploto, tako da ohranja notranjost stavbe hladno, ali naredimo enostransko infrardečo absorbcijo z uporabo nanotehnologije. To pomaga ohranjati toploto v notranjosti stavb, saj bo najbolj zunanja površinska plast stekla absorbirala infrardeče sevanje znotraj stavbe in ga sevala nazaj v notranjost.
-Jedkanje na steklu
-Aplicirano keramično označevanje (ACL)
-Graviranje
- Plameno poliranje
- Kemično poliranje
-barvanje
IZDELAVA TEHNIČNE KERAMIKE
• STISKANJE MADRE: Sestoji iz enoosnega stiskanja zrnatih praškov, zaprtih v matrici
• VROČE STISANJE: Podobno stiskanju, vendar z dodatkom temperature za izboljšanje zgostitve. Prah ali stisnjena predoblika se postavi v grafitno matrico in uporabi se enoosni tlak, medtem ko se matrica vzdržuje pri visokih temperaturah, kot je 2000 C. Temperature so lahko različne, odvisno od vrste keramičnega prahu, ki se obdeluje. Za zapletene oblike in geometrije bo morda potrebna druga naknadna obdelava, kot je diamantno brušenje.
• IZOSTATIČNO STISKANJE: zrnati prah ali stisnjene zgoščenke se dajo v nepredušne posode in nato v zaprto tlačno posodo s tekočino v notranjosti. Nato se stisnejo s povečanjem tlaka v tlačni posodi. Tekočina v posodi enakomerno prenaša tlačne sile po celotni površini nepredušne posode. Material je tako enakomerno stisnjen in prevzame obliko svoje fleksibilne posode ter njegov notranji profil in značilnosti.
• VROČE IZOSTATIČNO STISKANJE: Podobno izostatičnemu stiskanju, vendar poleg atmosfere plina pod tlakom sintramo kompakten pri visoki temperaturi. Vroče izostatično stiskanje povzroči dodatno zgostitev in povečano trdnost.
• SLIP CITY / DREN CASTING : Kalup napolnimo s suspenzijo mikrometrskih keramičnih delcev in nosilne tekočine. Ta mešanica se imenuje "slip". Kalup ima pore in zato se tekočina v mešanici filtrira v kalup. Posledično se na notranjih površinah kalupa oblikuje odlitek. Po sintranju lahko dele vzamemo iz kalupa.
• ULIVANJE TRAKOV: Keramične trakove izdelujemo z ulivanjem keramične brozge na ravne premikajoče se nosilne površine. Gnojnice vsebujejo keramične prahove, pomešane z drugimi kemikalijami za namene vezave in prenašanja. Ko topila izhlapevajo, ostanejo gosti in upogljivi listi keramike, ki jih je mogoče poljubno rezati ali zvijati.
• EKSTRUZIJSKO OBLIKOVANJE: Kot pri drugih postopkih ekstrudiranja se mehka zmes keramičnega prahu z vezivi in drugimi kemikalijami spusti skozi matrico, da pridobi obliko prečnega prereza, nato pa se razreže na želene dolžine. Postopek izvajamo s hladnimi ali segretimi keramičnimi mešanicami.
• NIZKTLAČNO BRIZGANJE: Pripravimo mešanico keramičnega prahu z vezivi in topili ter jo segrejemo na temperaturo, kjer jo lahko enostavno stisnemo in potisnemo v votlino orodja. Ko je cikel oblikovanja končan, se del izvrže in vezivna kemikalija sežge. Z brizganjem lahko ekonomično pridobimo zapletene dele v velikih količinah. Možne so luknje , ki obsegajo majhen delček milimetra na 10 mm debeli steni, navoji so možni brez nadaljnje obdelave, možne so tolerance do +/- 0,5 % in celo nižje, ko so deli strojno obdelani , možne so debeline sten od 0,5 mm do dolžine 12,5 mm, kot tudi debeline sten od 6,5 mm do dolžine 150 mm.
• ZELENA OBDELAVA: Z istimi orodji za obdelavo kovin lahko obdelujemo stisnjene keramične materiale, medtem ko so še mehki kot kreda. Možna so toleranca +/- 1 %. Za boljše tolerance uporabljamo diamantno brušenje.
• SINTRANJE ali ŽGANJE: Sintranje omogoča popolno zgostitev. Na zelenih kompaktnih delih pride do znatnega krčenja, vendar to ni velik problem, saj te dimenzijske spremembe upoštevamo pri načrtovanju dela in orodja. Delci prahu so med seboj povezani in poroznost, ki jo povzroča postopek stiskanja, je v veliki meri odstranjena.
• DIAMANTNO BRUŠENJE : najtrši material na svetu "diamant" se uporablja za brušenje trdih materialov, kot je keramika, in pridobijo se natančni deli. Dosegajo se tolerance v mikrometrskem območju in zelo gladke površine. Zaradi stroškov se o tej tehniki odločimo le, ko jo res potrebujemo.
• HERMETIČNI SESTAVI so tisti, ki praktično ne omogočajo izmenjave snovi, trdnih snovi, tekočin ali plinov med vmesniki. Hermetično tesnjenje je zrakotesno. Hermetična elektronska ohišja so na primer tista, ki ohranjajo občutljivo notranjo vsebino zapakirane naprave nepoškodovano zaradi vlage, onesnaževalcev ali plinov. Nič ni 100-odstotno hermetično, toda ko govorimo o hermetičnosti, mislimo, da v praktičnem smislu obstaja hermetičnost do te mere, da je stopnja puščanja tako nizka, da so naprave varne v normalnih okoljskih pogojih zelo dolgo časa. Naši hermetični sklopi so sestavljeni iz kovinskih, steklenih in keramičnih komponent, kovinsko-keramičnih, keramike-kovinsko-keramičnih, kovinsko-keramičnih-kovinskih, kovinsko-kovinskih, kovinsko-steklo, kovinsko-steklo-kovinskih, steklo-kovinsko-steklo, steklo- kovina in steklo na steklo ter vse ostale kombinacije lepljenja kovina-steklo-keramika. Keramične komponente lahko na primer prevlečemo s kovino, tako da se lahko močno vežejo na druge komponente v sklopu in imajo odlično sposobnost tesnjenja. Imamo znanje in izkušnje za prevleko optičnih vlaken ali dovodnih kanalov s kovino in njihovo spajkanje ali spajkanje na ohišje, tako da plini ne prehajajo ali uhajajo v ohišja. Zato se uporabljajo za izdelavo elektronskih ohišij za kapsuliranje občutljivih naprav in njihovo zaščito pred zunanjim ozračjem. Poleg odličnih tesnilnih lastnosti, druge lastnosti, kot so koeficient toplotnega raztezanja, odpornost proti deformacijam, narava brez sproščanja plinov, zelo dolga življenjska doba, narava neprevodnosti, lastnosti toplotne izolacije, antistatičnost ... itd. naredijo steklene in keramične materiale izbiro za določene aplikacije. Informacije o našem obratu za proizvodnjo keramičnih in kovinskih fitingov, hermetičnega tesnjenja, vakuumskih dovodov, visokega in ultravisokega vakuuma in komponent za nadzor tekočin lahko najdete tukaj:Brošura tovarne hermetičnih komponent