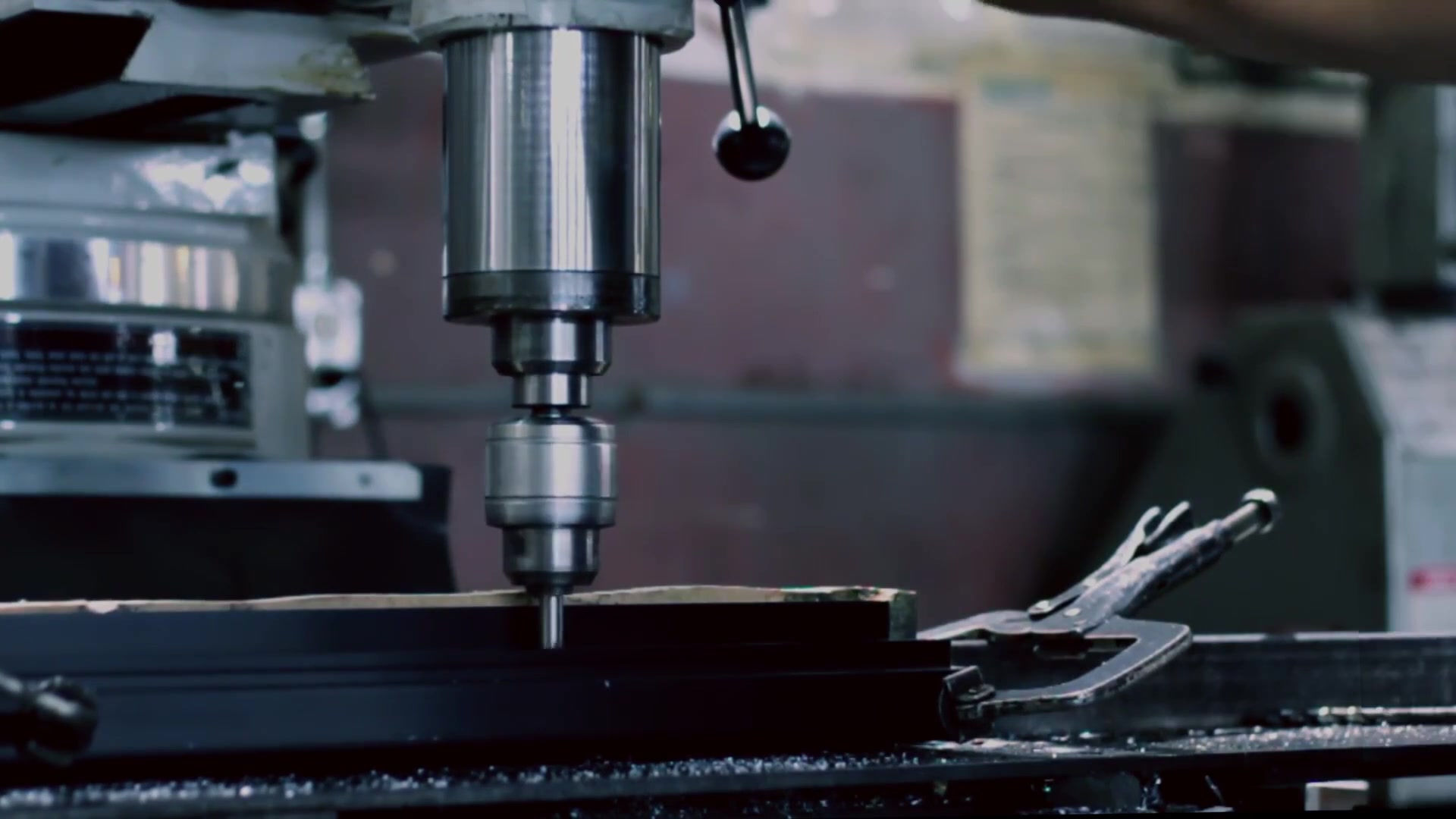
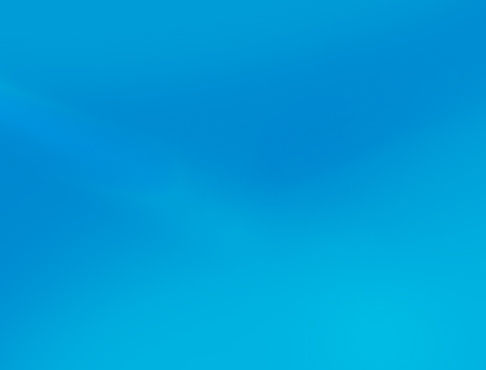
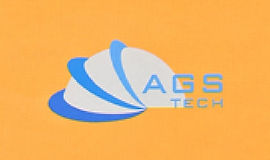
Globalni proizvajalec po meri, integrator, konsolidator, zunanji partner za široko paleto izdelkov in storitev.
Smo vaš vir na enem mestu za proizvodnjo, izdelavo, inženiring, konsolidacijo, integracijo, zunanje izvajanje izdelkov in storitev, izdelanih po meri in standardnih izdelkov.
Izberite svoj jezik
-
Izdelava po meri
-
Domača in globalna pogodbena proizvodnja
-
Zunanje izvajanje proizvodnje
-
Domača in svetovna javna naročila
-
Konsolidacija
-
Inženirska integracija
-
Inženirske storitve
Search Results
164 najdenih rezultatov s praznim iskanjem
- Composites, Composite Materials Manufacturing, Fiber Reinforced
Composites, Composite Materials Manufacturing, Particle and Fiber Reinforced, Cermets, Ceramic & Metal Composite, Glass Fiber Reinforced Polymer, Lay-Up Process Kompoziti in proizvodnja kompozitnih materialov Preprosto definirani, KOMPOZITI ali KOMPOZITNI MATERIALI so materiali, sestavljeni iz dveh ali več materialov z različnimi fizikalnimi ali kemijskimi lastnostmi, vendar ko se združijo, postanejo material, ki je drugačen od sestavnih materialov. Poudariti moramo, da sestavni materiali ostanejo ločeni in različni v strukturi. Cilj pri izdelavi kompozitnega materiala je pridobiti izdelek, ki je boljši od svojih sestavin in združuje želene lastnosti vsake sestavine. Kot primer; moč, majhna teža ali nižja cena so lahko motivacija za načrtovanje in izdelavo kompozita. Vrste kompozitov, ki jih ponujamo, so kompoziti, ojačani z delci, kompoziti, ojačani z vlakni, vključno s kompoziti s keramično matriko / polimerno matriko / kovinsko matriko / ogljik-ogljik / hibridnimi kompoziti, strukturnimi, laminiranimi in sendvič-strukturiranimi kompoziti ter nanokompoziti. Tehnike izdelave, ki jih uporabljamo pri proizvodnji kompozitnih materialov, so: pultruzija, proizvodni procesi preprega, napredno polaganje vlaken, navijanje filamentov, prilagojeno polaganje vlaken, postopek polaganja s pršenjem iz steklenih vlaken, taftanje, lanksidni postopek, z-pinning. Številni kompozitni materiali so sestavljeni iz dveh faz, matrice, ki je neprekinjena in obdaja drugo fazo; in razpršeno fazo, ki je obdana z matriko. Priporočamo, da kliknete tukajPRENESITE naše shematske ilustracije kompozitov in proizvodnje kompozitnih materialov podjetja AGS-TECH Inc. To vam bo pomagalo bolje razumeti informacije, ki vam jih posredujemo spodaj. • KOMPOZITI, OJAČANI Z DELCI: To kategorijo sestavljata dve vrsti: kompoziti z velikimi delci in kompoziti, utrjeni z disperzijo. Pri prvem tipu interakcij med delci in matriko ni mogoče obravnavati na atomski ali molekularni ravni. Namesto tega velja mehanika kontinuuma. Po drugi strani pa so v disperzijsko utrjenih kompozitih delci na splošno veliko manjši v razponih desetin nanometrov. Primer kompozita z velikimi delci so polimeri, ki so jim dodana polnila. Polnila izboljšajo lastnosti materiala in lahko nadomestijo del volumna polimera z bolj ekonomičnim materialom. Volumski deleži obeh faz vplivajo na obnašanje kompozita. Kompoziti z velikimi delci se uporabljajo s kovinami, polimeri in keramiko. KERMETI so primeri keramičnih/kovinskih kompozitov. Naš najpogostejši kermet je cementni karbid. Sestavljen je iz ognjevarne karbidne keramike, kot so delci volframovega karbida, v matrici iz kovine, kot je kobalt ali nikelj. Ti karbidni kompoziti se pogosto uporabljajo kot rezalna orodja za kaljeno jeklo. Trdi karbidni delci so odgovorni za rezalno delovanje, njihova žilavost pa je povečana z duktilno kovinsko matriko. Tako pridobimo prednosti obeh materialov v enem kompozitu. Drug pogost primer kompozita z velikimi delci, ki ga uporabljamo, so delci saj, pomešani z vulkanizirano gumo, da dobimo kompozit z visoko natezno trdnostjo, žilavostjo, odpornostjo na trganje in obrabo. Primer disperzijsko utrjenega kompozita so kovine in kovinske zlitine, ojačane in utrjene z enotno disperzijo drobnih delcev zelo trdega in inertnega materiala. Ko kovinski matrici aluminija dodamo zelo majhne kosmiče aluminijevega oksida, dobimo sintran aluminijev prah, ki ima izboljšano trdnost pri visokih temperaturah. • KOMPOZITI OJAČANI Z VLAKNI : Ta kategorija kompozitov je pravzaprav najpomembnejša. Cilj, ki ga je treba doseči, je visoka trdnost in togost na enoto teže. Sestava vlaken, dolžina, orientacija in koncentracija v teh kompozitih so ključni pri določanju lastnosti in uporabnosti teh materialov. Uporabljamo tri skupine vlaken: vlakna, vlakna in žice. BČKI so zelo tanki in dolgi monokristali. So med najmočnejšimi materiali. Nekateri primeri materialov za brke so grafit, silicijev nitrid, aluminijev oksid. VLAKNA pa so večinoma polimeri ali keramika in so v polikristalnem ali amorfnem stanju. Tretja skupina so fine ŽICE, ki imajo relativno velike premere in so pogosto sestavljene iz jekla ali volframa. Primer kompozita, ojačanega z žico, so avtomobilske pnevmatike, ki vsebujejo jekleno žico znotraj gume. Glede na material matrice imamo naslednje kompozite: KOMPOZITI IZ POLIMERNE MATRIKE: Izdelani so iz polimerne smole in vlaken kot ojačitvene sestavine. Podskupina teh imenovanih polimernih kompozitov, ojačanih s steklenimi vlakni (GFRP), vsebuje neprekinjena ali prekinjena steklena vlakna znotraj polimerne matrice. Steklo nudi visoko trdnost, je ekonomično, enostavno ga je predelati v vlakna in je kemično inertno. Pomanjkljivosti so njihova omejena togost in togost, delovne temperature pa le do 200 – 300 stopinj. Steklena vlakna so primerna za avtomobilske karoserije in transportno opremo, karoserije ladijskih vozil, skladiščne zabojnike. Zaradi omejene togosti niso primerni za letalstvo ali izdelavo mostov. Druga podskupina se imenuje polimerni kompozit, ojačan z ogljikovimi vlakni (CFRP). Tu je ogljik naš vlaknati material v polimerni matrici. Ogljik je znan po svojem visokem specifičnem modulu in trdnosti ter sposobnosti, da ju vzdržuje pri visokih temperaturah. Ogljikova vlakna nam lahko ponudijo standardne, srednje, visoke in ultravisoke natezne module. Poleg tega ogljikova vlakna ponujajo različne fizikalne in mehanske lastnosti in so zato primerna za različne inženirske aplikacije po meri. CFRP kompoziti se lahko štejejo za proizvodnjo športne in rekreacijske opreme, tlačnih posod in letalskih strukturnih komponent. Še ena podskupina, polimerni kompoziti, ojačani z aramidnimi vlakni, so prav tako materiali visoke trdnosti in modula. Njihovo razmerje med trdnostjo in težo je izjemno visoko. Aramidna vlakna poznamo tudi pod trgovskima imenoma KEVLAR in NOMEX. Pod napetostjo delujejo bolje kot drugi materiali iz polimernih vlaken, vendar so šibki pri stiskanju. Aramidna vlakna so močna, odporna na udarce, odporna na lezenje in utrujenost, stabilna pri visokih temperaturah, kemično inertna, razen proti močnim kislinam in bazam. Aramidna vlakna se pogosto uporabljajo v športni opremi, neprebojnih jopičih, pnevmatikah, vrveh, plaščih optičnih kablov. Drugi materiali za ojačitev vlaken obstajajo, vendar se uporabljajo v manjši meri. To so predvsem bor, silicijev karbid, aluminijev oksid. Polimerni matrični material je na drugi strani prav tako kritičen. Določa najvišjo delovno temperaturo kompozita, ker ima polimer na splošno nižjo temperaturo taljenja in razgradnje. Poliestri in vinil estri se pogosto uporabljajo kot polimerna matrica. Uporabljajo se tudi smole, ki imajo odlično odpornost na vlago in mehanske lastnosti. Na primer, poliimidno smolo je mogoče uporabiti do približno 230 stopinj Celzija. KOMPOZITI KOVINSKE MATRIKE: V teh materialih uporabljamo duktilno kovinsko matriko in delovne temperature so na splošno višje od njihovih sestavnih delov. V primerjavi s kompoziti iz polimerne matrice imajo lahko višje delovne temperature, niso vnetljivi in imajo lahko boljšo odpornost proti razgradnji proti organskim tekočinam. Vendar so dražji. Ojačitveni materiali, kot so lasje, delci, neprekinjena in prekinjena vlakna; pogosto se uporabljajo matrični materiali, kot so baker, aluminij, magnezij, titan in superzlitine. Primeri uporabe so komponente motorja iz matrice iz aluminijeve zlitine, ojačane z aluminijevim oksidom in ogljikovimi vlakni. KERAMIČNO-MATRIČNI KOMPOZITI: keramični materiali so znani po izjemno dobri visokotemperaturni zanesljivosti. Vendar so zelo krhki in imajo nizke vrednosti za lomno žilavost. Z vdelavo delcev, vlaken ali laskov ene keramike v matrico druge lahko dosežemo kompozite z višjo lomno žilavostjo. Ti vdelani materiali v bistvu zavirajo širjenje razpok znotraj matrice z nekaterimi mehanizmi, kot je odklon konic razpok ali oblikovanje mostov čez ploskve razpok. Na primer, aluminijev oksid, ki je ojačan s SiC lasmi, se uporablja kot vložki za rezalna orodja za obdelavo trdih kovinskih zlitin. Ti lahko pokažejo boljše rezultate v primerjavi s cementnimi karbidi. OGLJIK-OGLJIK KOMPOZITI : Tako ojačitev kot tudi matrica sta iz ogljika. Imajo visoke natezne module in trdnosti pri visokih temperaturah nad 2000 stopinj Celzija, odpornost proti lezenju, visoko lomno žilavost, nizke koeficiente toplotnega raztezanja, visoko toplotno prevodnost. Zaradi teh lastnosti so idealni za aplikacije, ki zahtevajo odpornost na toplotne udarce. Slabost kompozitov ogljik-ogljik pa je njihova občutljivost na oksidacijo pri visokih temperaturah. Tipični primeri uporabe so kalupi za vroče stiskanje, izdelava naprednih komponent turbinskih motorjev. HIBRIDNI KOMPOZITI: Dve ali več različnih vrst vlaken sta zmešani v eni sami matrici. Tako lahko s kombinacijo lastnosti oblikujemo nov material. Primer je, ko so v polimerno smolo vključena tako ogljikova kot steklena vlakna. Ogljikova vlakna zagotavljajo togost in trdnost nizke gostote, vendar so draga. Po drugi strani je steklo poceni, vendar nima togosti ogljikovih vlaken. Hibridni kompozit stekla in ogljika je močnejši in trši in ga je mogoče izdelati po nižji ceni. PREDELAVA KOMPOZITOV, OJAČANIH Z VLAKNI : Za neprekinjene plastike, ojačane z vlakni, z enakomerno razporejenimi vlakni, usmerjenimi v isto smer, uporabljamo naslednje tehnike. PULTRUZIJA: Izdelujemo palice, nosilce in cevi zveznih dolžin in konstantnih prerezov. Rovingi iz neprekinjenih vlaken so impregnirani s termoreaktivno smolo in povlečeni skozi jekleno matrico, da se oblikujejo v želeno obliko. Nato gredo skozi natančno obdelano matrico za strjevanje, da dosežejo svojo končno obliko. Ker je utrjevalna matrica segreta, utrjuje smolno matrico. Izvleki vlečejo material skozi matrice. Z vstavljenimi votlimi jedri lahko dobimo cevi in votle geometrije. Metoda pultruzije je avtomatizirana in nam omogoča visoke proizvodne stopnje. Možna je izdelava poljubne dolžine izdelka. PROIZVODNI PROCES PREPREGA: Prepreg je ojačitev iz neprekinjenih vlaken, predhodno impregnirana z delno utrjeno polimerno smolo. Široko se uporablja za strukturne aplikacije. Material je na voljo v obliki traku in se pošilja kot trak. Proizvajalec ga neposredno oblikuje in popolnoma strdi brez dodajanja smole. Ker se prepregi strdijo pri sobni temperaturi, jih hranimo pri 0 stopinjah Celzija ali nižjih temperaturah. Po uporabi se preostali trakovi shranijo nazaj pri nizkih temperaturah. Uporabljajo se termoplastične in termoreaktivne smole, pogosta pa so ojačitvena vlakna iz ogljika, aramida in stekla. Za uporabo prepregov se najprej odstrani nosilni papir, nato pa se izvede izdelava s polaganjem prepreg traku na površino, obdelano z orodjem (postopek polaganja). Za doseganje želene debeline lahko položite več plasti. Pogosta praksa je zamenjava usmeritve vlaken za izdelavo križnega ali kotnega laminata. Nazadnje se za utrjevanje uporabi toplota in pritisk. Za rezanje prepregov in polaganje se uporabljajo tako ročna obdelava kot tudi avtomatizirani postopki. ZAVIJANJE FILAMENTOV: Neprekinjena ojačitvena vlakna so natančno nameščena v vnaprej določenem vzorcu, da sledijo votli in običajno okrogli obliki. Vlakna gredo najprej skozi smolno kopel, nato pa jih avtomatiziran sistem navije na trn. Po več ponovitvah navijanja dosežemo želeno debelino in strjevanje izvedemo pri sobni temperaturi ali v pečici. Sedaj je trn odstranjen in izdelek iz kalupa. Navijanje filamentov lahko ponudi zelo visoko razmerje med trdnostjo in težo z navijanjem vlaken v obodnih, spiralnih in polarnih vzorcih. Cevi, rezervoarji, ohišja so izdelani s to tehniko. • STRUKTURNI KOMPOZITI: Na splošno so sestavljeni iz homogenih in kompozitnih materialov. Zato so njihove lastnosti določene s sestavnimi materiali in geometrijsko zasnovo elementov. Tukaj so glavne vrste: LAMINARNI KOMPOZITI: Ti strukturni materiali so izdelani iz dvodimenzionalnih listov ali plošč s prednostnimi smermi visoke trdnosti. Plasti so zložene in cementirane skupaj. Z menjavanjem smeri visoke trdnosti v obeh pravokotnih oseh dobimo kompozit, ki ima v dvodimenzionalni ravnini visoko trdnost v obeh smereh. S prilagajanjem kotov plasti lahko izdelamo kompozit z močjo v želenih smereh. Sodobne smuči so izdelane na ta način. SENDVIČ PANELI: ti strukturni kompoziti so lahki, vendar imajo visoko togost in moč. Sendvič plošče so sestavljene iz dveh zunanjih plošč iz togega in močnega materiala, kot so aluminijeve zlitine, plastike, ojačane z vlakni, ali jekla in jedra med zunanjima ploščama. Jedro mora biti lahko in ima večinoma nizek modul elastičnosti. Priljubljeni osnovni materiali so toge polimerne pene, les in satje. Sendvič plošče se pogosto uporabljajo v gradbeništvu kot strešni material, talni ali stenski material, pa tudi v vesoljski industriji. • NANOKOMPOZITI: Ti novi materiali so sestavljeni iz delcev nano velikosti, vgrajenih v matriko. Z uporabo nanokompozitov lahko izdelamo gumijaste materiale, ki so zelo dobre ovire za prodiranje zraka, hkrati pa ohranijo nespremenjene gumijaste lastnosti. CLICK Product Finder-Locator Service PREJŠNJA STRAN
- Rapid Prototyping, Desktop Manufacturing, Additive Manufacturing, FDM
Rapid Prototyping, Desktop Manufacturing, Additive Manufacturing, Stereolithography, Polyjet, Fused Deposition Modeling, Selective Laser Sintering, FDM, SLS Dodatna in hitra proizvodnja V zadnjih letih opažamo povečano povpraševanje po HITRI PROIZVODNJI ali HITRI PROTOTIPI. Ta proces se lahko imenuje tudi IZDELAVA NAMIZNIH RAČUNALNIKOV ali IZDELAVA PROSTIH OBLIK. V bistvu je trdni fizični model dela izdelan neposredno iz tridimenzionalne risbe CAD. Za te različne tehnike, kjer sestavljamo dele v plasteh, uporabljamo izraz ADITIVNA PROIZVODNJA. Z integrirano računalniško vodeno strojno in programsko opremo izvajamo aditivno proizvodnjo. Naše hitre tehnike izdelave prototipov in izdelave so STEREOLITOGRAFIJA, POLYJET, MODELIRANJE S TALJENIM NAPADANJEM, SELEKTIVNO LASERSKO SINTRANJE, TALJENJE Z ELEKTRONSKIM ŽARKOM, TRIDEMENZIONALNO TISKANJE, NEPOSREDNA PROIZVODNJA, HITRO ORODJANJE. Priporočamo, da kliknete tukajPRENESITE naše shematske ilustracije aditivne proizvodnje in hitre proizvodne procese podjetja AGS-TECH Inc. To vam bo pomagalo bolje razumeti informacije, ki vam jih posredujemo spodaj. Hitra izdelava prototipov nam zagotavlja: 1.) Idejni dizajn izdelka si ogledamo iz različnih zornih kotov na monitorju s pomočjo 3D/CAD sistema. 2.) Prototipi iz nekovinskih in kovinskih materialov so izdelani in proučeni s funkcionalnega, tehničnega in estetskega vidika. 3.) Izdelava nizkocenovnih prototipov v zelo kratkem času. Aditivna proizvodnja je lahko podobna izdelavi štruce kruha z zlaganjem in lepljenjem posameznih rezin eno na drugo. Z drugimi besedami, izdelek se izdeluje rezino za rezino ali plast za plastjo nalaga eno na drugo. Večino delov je mogoče izdelati v nekaj urah. Tehnika je dobra, če so deli potrebni zelo hitro ali če so potrebne količine majhne in je izdelava kalupa in orodja predraga in dolgotrajna. Vendar pa je strošek dela drag zaradi dragih surovin. • STEREOLITOGRAFIJA: Ta tehnika, skrajšano tudi STL, temelji na strjevanju in strjevanju tekočega fotopolimera v določeno obliko z fokusiranjem laserskega žarka nanj. Laser polimerizira fotopolimer in ga strdi. S skeniranjem UV-laserskega žarka glede na programirano obliko vzdolž površine fotopolimerne mešanice se del izdela od spodaj navzgor v posameznih rezinah, kaskadno postavljenih ena na drugo. Skeniranje laserske točke se večkrat ponovi, da se doseže geometrija, programirana v sistemu. Ko je del popolnoma izdelan, ga odstranimo s ploščadi, popivnamo in očistimo z ultrazvokom in alkoholno kopeljo. Nato je za nekaj ur izpostavljen UV-sevanju, da se zagotovi, da je polimer popolnoma strjen in strjen. Če povzamemo postopek, se ploščad, ki je potopljena v mešanico fotopolimera, in UV-laserski žarek krmilita in premikata skozi servo-krmilni sistem glede na obliko želenega dela, del pa se pridobi s fotoutrjevanjem polimera plast za plastjo. Seveda so največje dimenzije izdelanega dela določene z opremo za stereolitografijo. • POLYJET: Podobno kot pri brizgalnem tiskanju imamo pri polijetu osem tiskalnih glav, ki fotopolimer odlagajo na vgradni pladenj. Ultravijolična svetloba, nameščena poleg curkov, takoj strdi in utrdi vsako plast. V polijetu sta uporabljena dva materiala. Prvi material je za izdelavo dejanskega modela. Drugi material, gelasta smola, se uporablja za podporo. Oba materiala se naneseta plast za plastjo in istočasno strdita. Po končani izdelavi modela nosilni material odstranimo z vodno raztopino. Uporabljene smole so podobne stereolitografiji (STL). Polyjet ima naslednje prednosti pred stereolitografijo: 1.) Ni potrebe po čistilnih delih. 2.) Ni potrebe po postprocesnem strjevanju 3.) Možne so manjše debeline plasti in tako dobimo boljšo ločljivost in lahko izdelujemo finejše dele. • MODELIRANJE NANAŠANJA Z TALJENIM NAPAJANJEM: Skrajšano tudi kot FDM, pri tej metodi se robotsko vodena glava ekstruderja premika v dveh glavnih smereh nad mizo. Kabel se po potrebi spušča in dviguje. Iz odprtine segrete matrice na glavi se iztisne termoplastični filament in začetni sloj se nanese na penasto podlago. To doseže glava ekstruderja, ki sledi vnaprej določeni poti. Po začetni plasti se miza spusti, naslednje plasti pa se položijo ena na drugo. Včasih so pri izdelavi zapletenega dela potrebne podporne strukture, da se lahko nanašanje nadaljuje v določenih smereh. V teh primerih se nosilni material ekstrudira z manj gosto razdaljo filamentov na plasti, tako da je ta šibkejši od materiala modela. Te podporne strukture se lahko kasneje po dokončanju dela razpustijo ali odlomijo. Dimenzije matrice ekstruderja določajo debelino ekstrudiranih plasti. Postopek FDM proizvaja dele s stopničastimi površinami na poševnih zunanjih ravninah. Če je ta hrapavost nesprejemljiva, jih lahko za glajenje uporabite za poliranje s kemično paro ali segreto orodje. Celo polirni vosek je na voljo kot premazni material za odpravo teh korakov in doseganje razumnih geometrijskih toleranc. • SELEKTIVNO LASERSKO SINTRANJE: Označen tudi kot SLS, postopek temelji na selektivnem sintranju polimera, keramike ali kovinskega prahu v predmet. Dno obdelovalne komore ima dva cilindra: delni cilinder in cilinder za dovajanje prahu. Prvi se postopoma spušča do mesta, kjer se oblikuje sintrani del, drugi pa se postopoma dviguje, da dovaja prah v valj za izdelavo dela skozi valjčni mehanizem. Najprej se v valj delne zgradbe nanese tanka plast prahu, nato se na to plast usmeri laserski žarek, ki sledi in tali/sintra določen prerez, ki se nato ponovno strdi v trdno snov. Puder je na mestih, ki jih laserski žarek ne zadene, ohlapna, vendar še vedno podpira trdni del. Nato se nanese še ena plast prahu in postopek se večkrat ponovi, da se pridobi del. Na koncu delce prahu otresemo. Vse to izvaja računalnik za nadzor procesa z uporabo navodil, ki jih generira program 3D CAD dela, ki se izdeluje. Deponiramo lahko različne materiale, kot so polimeri (kot so ABS, PVC, poliester), vosek, kovine in keramika z ustreznimi polimernimi vezivi. • ELEKTRONSKI ŽAREK TALJENJE: Podobno selektivnemu laserskemu sintranju, vendar z uporabo elektronskega žarka za taljenje titanovega ali kobalt-kromovega prahu za izdelavo prototipov v vakuumu. Za izvedbo tega postopka na nerjavnih jeklih, aluminiju in bakrovih zlitinah je bilo narejenih nekaj napredkov. Če je treba povečati utrujenost izdelanih delov, kot sekundarni postopek uporabimo vroče izostatično stiskanje po izdelavi delov. • TRIDEMENZIONALNO TISKANJE: pri tej tehniki, označeni tudi s 3DP, tiskalna glava nanese anorgansko vezivo na plast nekovinskega ali kovinskega prahu. Bat, ki nosi plast prahu, se postopoma spušča in na vsakem koraku se vezivo odlaga plast za plastjo in zlije z vezivom. Uporabljeni praškasti materiali so mešanice polimerov in vlaken, livarski pesek, kovine. S hkratno uporabo različnih registratorskih glav in različnih barvnih veziv lahko dobimo različne barve. Postopek je podoben brizgalnemu tiskanju, vendar namesto barvnega lista dobimo barvni tridimenzionalni predmet. Proizvedeni deli so lahko porozni in zato lahko zahtevajo sintranje in infiltracijo kovine, da povečajo svojo gostoto in trdnost. Sintranje bo zgorelo vezivo in spojilo kovinske prahove skupaj. Kovine, kot so nerjaveče jeklo, aluminij, titan, se lahko uporabljajo za izdelavo delov, kot material za infiltracijo pa običajno uporabljamo baker in bron. Lepota te tehnike je v tem, da je mogoče zelo hitro izdelati tudi zapletene in premikajoče se sklope. Izdelati je mogoče na primer sklop zobnikov, ključ kot orodje, ki bo imel gibljive in vrtljive dele, pripravljene za uporabo. Različne komponente sklopa je mogoče izdelati v različnih barvah in vse v enem posnetku. Prenesite našo brošuro na:Osnove kovinskega 3D tiskanja • NEPOSREDNA PROIZVODNJA in HITRO IZDELAVA ORODJA: Poleg ocene dizajna, odpravljanja težav uporabljamo hitro izdelavo prototipov za neposredno izdelavo izdelkov ali neposredno uporabo v izdelkih. Z drugimi besedami, hitro izdelavo prototipov je mogoče vključiti v običajne procese, da postanejo boljši in konkurenčnejši. Na primer, s hitro izdelavo prototipov lahko ustvarite vzorce in kalupe. Vzorce talilnega in gorečega polimera, ustvarjenega s hitrimi postopki izdelave prototipov, je mogoče sestaviti za vlivanje in vložiti. Še en primer, ki ga je treba omeniti, je uporaba 3DP za izdelavo lupine za ulivanje keramike in uporaba tega za operacije ulivanja lupine. Tudi kalupe za brizganje in kalupne vložke je mogoče izdelati s hitro izdelavo prototipov in prihraniti lahko več tednov ali mesecev časa za izdelavo kalupov. Samo z analizo datoteke CAD želenega dela lahko s pomočjo programske opreme izdelamo geometrijo orodja. Tukaj je nekaj naših priljubljenih metod hitrega orodja: RTV (vulkaniziranje pri sobni temperaturi) LITVE/ULITKE IZ URETANA: Za izdelavo vzorca želenega dela je mogoče uporabiti hitro izdelavo prototipov. Nato je ta vzorec prevlečen z ločilnim sredstvom in tekoča RTV guma se prelije čez vzorec, da se izdelajo polovice kalupa. Nato se te polovice kalupa uporabijo za brizganje tekočih uretanov. Življenjska doba kalupa je kratka, le približno 0 ali 30 ciklov, vendar dovolj za proizvodnjo majhnih serij. ACES (Acetal Clear Epoxy Solid) BRIZGANJE: z uporabo hitrih tehnik izdelave prototipov, kot je stereolitografija, izdelujemo kalupe za brizganje. Ti kalupi so lupine z odprtim koncem, ki omogočajo polnjenje z materiali, kot je epoksi, epoksid, polnjen z aluminijem, ali kovine. Življenjska doba kalupa je spet omejena na desetine ali največ stotine delov. POSTOPEK IZDELAVE ORODJA ZA brizgano kovino: uporabljamo hitro izdelavo prototipov in izdelamo vzorec. Na površino vzorca nabrizgamo cink-aluminijevo zlitino in jo premažemo. Vzorec s kovinsko prevleko se nato postavi v bučko in prelije z epoksidom ali epoksidom, polnjenim z aluminijem. Na koncu ga odstranimo in z izdelavo dveh takih polovic kalupa dobimo celoten kalup za brizganje. Ti kalupi imajo daljšo življenjsko dobo, v nekaterih primerih pa lahko, odvisno od materiala in temperatur, proizvedejo na tisoče delov. POSTOPEK KEELTOOL: Ta tehnika lahko izdela kalupe z življenjsko dobo od 100.000 do 10 milijonov ciklov. S hitro izdelavo prototipov izdelamo RTV kalup. Nato se kalup napolni z mešanico, sestavljeno iz prahu orodnega jekla A6, volframovega karbida, polimernega veziva in pusti, da se strdi. Ta kalup se nato segreje, da polimer zgori in kovinski prah stopi. Naslednji korak je infiltracija bakra za izdelavo končnega kalupa. Če je potrebno, je mogoče na kalupu izvesti sekundarne postopke, kot sta strojna obdelava in poliranje, za večjo dimenzijsko natančnost. CLICK Product Finder-Locator Service PREJŠNJA STRAN
- Joining & Assembly & Fastening Processes, Welding, Brazing, Soldering
Joining & Assembly & Fastening Processes, Welding, Brazing, Soldering, Sintering, Adhesive Bonding, Press Fitting, Wave and Reflow Solder Process, Torch Furnace Postopki spajanja, sestavljanja in pritrjevanja Vaše izdelane dele spajamo, sestavljamo in pritrjujemo ter jih predelamo v končne ali polizdelke s pomočjo VARJENJA, TRDNEGA SPAJKANJA, SINTRANJA, LEPLJENJA, PRITRJEVANJA, PREŠANJA. Nekateri naši najbolj priljubljeni postopki varjenja so obločno varjenje, varjenje s kisikovim plinom, varjenje z uporom, projekcija, varjenje z šivi, varjenje z udarcem, varjenje v trdnem stanju, varjenje z elektronskim žarkom, lasersko, termično varjenje, indukcijsko varjenje. Naši priljubljeni postopki trdega spajkanja so spajkanje z baklo, indukcija, peč in spajkanje po potopu. Naše metode spajkanja so spajkanje z železom, vročo ploščo, pečico, indukcijsko spajkanje, spajkanje potopno, valovito, reflow in ultrazvočno spajkanje. Za lepljenje pogosto uporabljamo termoplaste in termo strjevalce, epokside, fenole, poliuretane, lepilne zlitine ter nekatere druge kemikalije in trakove. Končno naše postopke pritrjevanja sestavljajo žeblji, vijačenje, matice in vijaki, kovičenje, vpenjanje, zatikanje, šivanje in spenjanje ter stiskanje. • VARJENJE: Varjenje vključuje spajanje materialov s taljenjem obdelovancev in vnosom dodajnih materialov, ki prav tako spajajo staljeno zvarno bazo. Ko se območje ohladi, dobimo močan spoj. V nekaterih primerih se izvaja pritisk. V nasprotju z varjenjem postopki trdo spajkanja vključujejo samo taljenje materiala z nižjim tališčem med obdelovancama, obdelovanci pa se ne stopijo. Priporočamo, da kliknete tukajPRENESITE naše shematske ilustracije varilnih postopkov podjetja AGS-TECH Inc. To vam bo pomagalo bolje razumeti informacije, ki vam jih posredujemo spodaj. Pri OBLOČNEM VARJENJU uporabljamo napajalnik in elektrodo za ustvarjanje električnega obloka, ki tali kovine. Varilno mesto je zaščiteno z zaščitnim plinom ali paro ali drugim materialom. Ta postopek je priljubljen pri varjenju avtomobilskih delov in jeklenih konstrukcij. Pri varjenju s kovinskim oblokom (SMAW) ali znanem tudi kot paličasto varjenje se palica elektrode približa osnovnemu materialu in med njima nastane električni oblok. Palica elektrode se stopi in deluje kot polnilni material. Elektroda vsebuje tudi fluks, ki deluje kot plast žlindre in oddaja hlape, ki delujejo kot zaščitni plin. Ti ščitijo območje zvara pred onesnaženjem okolja. Nobena druga polnila se ne uporabljajo. Slabosti tega postopka so njegova počasnost, potreba po pogosti menjavi elektrod, potreba po sesekljanju ostankov žlindre, ki izvirajo iz talila. Številne kovine, kot so železo, jeklo, nikelj, aluminij, baker … itd. Lahko varjen. Njegove prednosti so poceni orodja in enostavna uporaba. Plinsko obločno varjenje (GMAW), znano tudi kot kovinsko-inertni plin (MIG), imamo neprekinjeno dovajanje polnila žice potrošne elektrode in inertnega ali delno inertnega plina, ki teče okoli žice proti onesnaženju območja zvara iz okolja. Variti je mogoče jeklo, aluminij in druge neželezne kovine. Prednosti MIG so visoke hitrosti varjenja in dobra kakovost. Slabosti so njegova zapletena oprema in izzivi, s katerimi se soočamo v vetrovnem zunanjem okolju, ker moramo vzdrževati stabilen zaščitni plin okoli območja varjenja. Različica GMAW je obločno varjenje s talilom (FCAW), ki je sestavljeno iz fine kovinske cevi, napolnjene s talilnimi materiali. Včasih pretok znotraj cevi zadostuje za zaščito pred onesnaženjem okolja. Obločno varjenje pod praškom (SAW) je avtomatiziran postopek, ki vključuje neprekinjeno dovajanje žice in oblok, ki je udarjen pod plastjo talila. Stopnje proizvodnje in kakovost so visoki, varilna žlindra se enostavno odstrani in imamo delovno okolje brez dima. Pomanjkljivost je, da se lahko uporablja samo za varjenje delov v določenih položajih. Pri obločnem varjenju z volframovim plinom (GTAW) ali varjenju z volframom in inertnim plinom (TIG) uporabljamo volframovo elektrodo skupaj z ločenim polnilom in inertnimi ali skoraj inertnimi plini. Kot vemo, ima volfram visoko tališče in je zelo primerna kovina za zelo visoke temperature. V nasprotju z drugimi zgoraj razloženimi metodami se volfram v TIG ne porabi. Počasna, a kakovostna varilna tehnika, ki ima prednost pred drugimi tehnikami pri varjenju tankih materialov. Primerno za številne kovine. Varjenje s plazemskim oblokom je podobno, vendar za ustvarjanje obloka uporablja plazemski plin. Oblok pri varjenju s plazemskim oblokom je relativno bolj koncentriran v primerjavi z GTAW in se lahko uporablja za širši razpon debelin kovin pri veliko višjih hitrostih. GTAW in plazemsko obločno varjenje lahko uporabimo za bolj ali manj enake materiale. VARJENJE S KISIKOM / OXYFUEL VARJENJE imenovano tudi oksiacetilensko varjenje, varjenje s kisikom, plinsko varjenje se izvaja z uporabo plinskih goriv in kisika za varjenje. Ker ne uporablja električne energije, je prenosen in se lahko uporablja tam, kjer ni elektrike. Z varilnim gorilnikom segrevamo kose in polnilni material, da ustvarimo skupni bazen staljene kovine. Uporabljajo se lahko različna goriva, kot so acetilen, bencin, vodik, propan, butan itd. Pri varjenju s kisikom uporabljamo dve posodi, eno za gorivo in drugo za kisik. Kisik oksidira gorivo (sežge). UPOROVNO VARJENJE: Ta vrsta varjenja izkorišča joulsko segrevanje in toplota nastane na mestu, kjer določen čas teče električni tok. Skozi kovino prehajajo visoki tokovi. Na tem mestu se oblikujejo bazeni staljene kovine. Metode uporovnega varjenja so priljubljene zaradi svoje učinkovitosti in majhnega potenciala onesnaževanja. Vendar pa so slabosti razmeroma visoki stroški opreme in inherentna omejitev na relativno tanke obdelovance. TOČKO VARJENJE je ena glavnih vrst uporovnega varjenja. Tukaj združimo dve ali več prekrivajočih se plošč ali obdelovancev z uporabo dveh bakrenih elektrod, da pločevine stisnemo skupaj in skozi njih spustimo močan tok. Material med bakrenimi elektrodami se segreje in na tem mestu nastane staljena plast. Tok se nato ustavi in konice bakrenih elektrod ohladijo mesto zvara, ker so elektrode hlajene z vodo. Za to tehniko je ključnega pomena dovajanje prave količine toplote na pravi material in debelino, saj bo spoj šibek, če ga nanesete napačno. Točkovno varjenje ima prednosti, saj ne povzroča večjih deformacij obdelovancev, ima energetsko učinkovitost, enostavnost avtomatizacije in izjemne proizvodne stopnje ter ne zahteva nobenih polnil. Pomanjkljivost je, da ker varjenje poteka na točkah in ne tvori neprekinjenega šiva, je lahko splošna trdnost relativno nižja v primerjavi z drugimi metodami varjenja. VARJENJE ŠIVOV na drugi strani ustvarja zvare na sosednjih površinah podobnih materialov. Šiv je lahko čelni ali prekrivni. Varjenje šivov se začne na enem koncu in se postopoma pomika na drugega. Ta metoda uporablja tudi dve bakreni elektrodi za ustvarjanje pritiska in toka na območju zvara. Elektrode v obliki diska se vrtijo s stalnim stikom vzdolž linije šiva in ustvarjajo neprekinjen zvar. Tudi tukaj se elektrode hladijo z vodo. Zvari so zelo močni in zanesljivi. Druge metode so tehnike projekcije, bliskovnega varjenja in varjenja z vzmetnim varjenjem. VARJENJE V TRDNEM PREVODNIŠTVU je nekoliko drugačno od prejšnjih metod, razloženih zgoraj. Koalescenca poteka pri temperaturah pod temperaturo taljenja spojenih kovin in brez uporabe kovinskega polnila. Pri nekaterih postopkih se lahko uporablja tlak. Različne metode so KOEKSTRUZIJSKO VARJENJE, kjer se različne kovine ekstrudirajo skozi isto matrico, HLADNO TLAČNO VARJENJE, kjer spajamo mehke zlitine pod njihovim tališčem, DIFUZIJSKO VARJENJE tehnika brez vidnih zvarnih linij, EKSPLOZIJSKO VARJENJE za spajanje različnih materialov, npr. korozijsko odpornih zlitin na strukturne jekla, ELEKTROMAGNETNO IMPULZNO VARJENJE, pri katerem cevi in pločevine pospešimo z elektromagnetnimi silami, KOVAŠKO VARJENJE, ki je sestavljeno iz segrevanja kovin na visoke temperature in njihovo udarjanje skupaj, TORNO VARJENJE, pri katerem se izvaja varjenje z zadostnim trenjem, TORNO MEŠALNO VARJENJE, ki vključuje rotacijsko ne- potrošno orodje, ki prečka spojno linijo, VROČE TLAČNO VARJENJE, kjer stisnemo kovine skupaj pri povišanih temperaturah pod temperaturo taljenja v vakuumu ali inertnih plinih, VROČE IZOSTATIČNO TLAČNO VARJENJE postopek, pri katerem izvajamo pritisk z uporabo inertnih plinov znotraj posode, VALJNO VARJENJE, kjer spajamo različne materiale tako, da jih potisnete med dve vrtljivi kolesi, ULTRAZVOČNO VARJENJE, kjer se tanke kovinske ali plastične plošče varijo z uporabo visokofrekvenčne vibracijske energije. Naši drugi postopki varjenja so VARJENJE Z ELEKTRONSKIM ŽARKOM z globokim prebojem in hitro obdelavo, vendar je draga metoda, zato jo upoštevamo za posebne primere, VARJENJE NA ŽLINDRO je metoda, ki je primerna samo za težke debele plošče in obdelovance iz jekla, INDUKCIJSKO VARJENJE, kjer uporabljamo elektromagnetno indukcijo in segrevajo naše električno prevodne ali feromagnetne obdelovance, VARJENJE Z LASERSKIM ŽARKOM tudi z globokim prebojem in hitro obdelavo, a draga metoda, LASERSKO HIBRIDNO VARJENJE, ki združuje LBW z GMAW v isti varilni glavi in je zmožno premostiti vrzeli 2 mm med ploščami, UDARNO VARJENJE, ki vključuje električno razelektritev, ki ji sledi kovanje materialov z uporabljenim pritiskom, TERMITNO VARJENJE, ki vključuje eksotermno reakcijo med prahom aluminija in železovega oksida, ELEKTROPLINSKO VARJENJE s potrošnimi elektrodami, ki se uporablja le z jeklom v navpičnem položaju, in končno OBLOČNO VARJENJE STROJA za spajanje čepa z osnovo material s toploto in pritiskom. Priporočamo, da kliknete tukajPRENESITE naše shematske ilustracije postopkov trdega spajkanja, spajkanja in lepljenja, ki jih izvaja AGS-TECH Inc. To vam bo pomagalo bolje razumeti informacije, ki vam jih posredujemo spodaj. • TRDNO SPAJKANJE: Dve ali več kovin spojimo tako, da dodajne kovine med njimi segrejemo nad njihovo tališče in uporabimo kapilarno delovanje za širjenje. Postopek je podoben spajkanju, vendar so temperature, potrebne za taljenje polnila, višje pri spajkanju. Tako kot pri varjenju talilo ščiti dodajni material pred atmosfersko kontaminacijo. Po ohlajanju se obdelovanci združijo. Postopek vključuje naslednje ključne korake: dobro prileganje in zračnost, pravilno čiščenje osnovnih materialov, pravilno pritrjevanje, pravilno izbiro fluksa in atmosfere, segrevanje sklopa in končno čiščenje spajkanega sklopa. Nekateri naši postopki trdega spajkanja so SPAJKANJE Z GORILNIKOM, priljubljena metoda, ki se izvaja ročno ali avtomatizirano. Primeren je za naročila majhnega obsega proizvodnje in posebne primere. Toplota se dovaja s pomočjo plinskih plamenov v bližini spoja, ki ga spajkamo. SPAJKANJE V PEČI zahteva manj spretnosti operaterja in je polavtomatski postopek, primeren za industrijsko množično proizvodnjo. Tako regulacija temperature kot regulacija atmosfere v peči sta prednosti te tehnike, saj nam prva omogoča nadzorovane toplotne cikle in odpravo lokalnega segrevanja, kot je to v primeru spajkanja z baklo, druga pa ščiti del pred oksidacijo. Z uporabo jigginga lahko zmanjšamo stroške izdelave na minimum. Pomanjkljivosti so visoka poraba energije, stroški opreme in zahtevnejši načrtovalski vidiki. VAKUMSKO SPAJKANJE poteka v vakuumski peči. Ohranja se enakomernost temperature in dobimo zelo čiste spoje brez fluksa z zelo majhnimi preostalimi napetostmi. Toplotna obdelava lahko poteka med vakuumskim spajkanjem zaradi nizkih preostalih napetosti, ki so prisotne med počasnimi cikli segrevanja in ohlajanja. Glavna pomanjkljivost je visoka cena, saj je ustvarjanje vakuumskega okolja drag postopek. Še ena tehnika DIP BRAZING združuje fiksne dele, kjer se spojina za spajkanje nanese na spojne površine. Nato se pritrjeni deli potopijo v kopel s staljeno soljo, kot je natrijev klorid (kuhinjska sol), ki deluje kot medij za prenos toplote in fluks. Zrak je izključen in zato ne pride do tvorbe oksidov. Pri INDUKCIJSKEM SPAJKANJU spajamo materiale z dodano kovino, ki ima nižje tališče kot osnovni materiali. Izmenični tok iz indukcijske tuljave ustvarja elektromagnetno polje, ki inducira indukcijsko segrevanje večinoma železnih magnetnih materialov. Metoda zagotavlja selektivno segrevanje, dobre spoje s polnili, ki tečejo le na želenih območjih, malo oksidacije, ker ni prisotnih plamenov in hlajenje je hitro, hitro segrevanje, konsistenco in primernost za velikoserijsko proizvodnjo. Za pospešitev naših procesov in zagotavljanje doslednosti pogosto uporabljamo predoblike. Informacije o našem obratu za trdo spajkanje, ki izdeluje fitinge iz keramike v kovino, hermetično tesnjenje, vakuumske dovode, komponente za visok in ultravisok vakuum in tekočino najdete tukaj: Brošura tovarne za spajkanje • SPAJKANJE : Pri spajkanju nimamo taljenja obdelovancev, temveč dodajno kovino z nižjim tališčem od spojnih delov, ki teče v spoj. Dodatna kovina pri spajkanju se tali pri nižji temperaturi kot pri spajkanju. Za spajkanje uporabljamo zlitine brez svinca in imamo skladnost z RoHS, za različne aplikacije in zahteve pa imamo različne in primerne zlitine, kot je srebrova zlitina. Spajkanje nam nudi spoje, ki so neprepustni za pline in tekočine. Pri MEHKEM SPAJKANJU ima naša dodana kovina tališče pod 400 stopinj Celzija, medtem ko pri SREBRNEM SPAJKANJU in TRDNEM SPAJKANJU potrebujemo višje temperature. Mehko spajkanje uporablja nižje temperature, vendar ne povzroči močnih spojev za zahtevne aplikacije pri povišanih temperaturah. Spajkanje srebra na drugi strani zahteva visoke temperature, ki jih zagotavlja gorilnik, in nam daje močne spoje, primerne za uporabo pri visokih temperaturah. Spajkanje zahteva najvišje temperature in običajno se uporablja gorilnik. Ker so spajkalni spoji zelo močni, so dobri kandidati za popravilo težkih železnih predmetov. V naših proizvodnih linijah uporabljamo tako ročno ročno spajkanje kot tudi avtomatizirane spajkalne linije. INDUKCIJSKO SPAJKANJE uporablja visokofrekvenčni izmenični tok v bakreni tuljavi za olajšanje indukcijskega ogrevanja. V spajkanem delu se inducirajo tokovi in posledično nastane toplota pri visokem uporu joint. Ta toplota stopi polnilno kovino. Uporablja se tudi fluks. Indukcijsko spajkanje je dobra metoda za spajkanje cilindrov in cevi v neprekinjenem procesu z ovijanjem tuljav okoli njih. Spajkanje nekaterih materialov, kot sta grafit in keramika, je težje, ker zahteva prevleko obdelovancev z ustrezno kovino pred spajkanjem. To olajša medfazno lepljenje. Takšne materiale spajkamo zlasti za aplikacije hermetične embalaže. Naša tiskana vezja (PCB) izdelujemo v velikem obsegu večinoma z uporabo VALOVNEGA SPAJKANJA. Samo za majhne količine prototipov uporabljamo ročno spajkanje s spajkalnikom. Uporabljamo valovito spajkanje tako za sklope tiskanih vezij za skoznjo kot za površinsko montažo (PCBA). Začasno lepilo ohranja komponente pritrjene na vezje, sklop pa je postavljen na tekoči trak in se premika skozi opremo, ki vsebuje staljeno spajko. Najprej se PCB fluksira in nato vstopi v območje predgretja. Staljena spajka je v posodi in ima na površini vzorec stoječih valov. Ko se tiskano vezje premika čez te valove, se ti valovi dotaknejo dna tiskanega vezja in se prilepijo na spajkalne ploščice. Spajka ostane samo na zatičih in blazinicah, ne pa na samem tiskanem vezju. Valovi v staljeni spajki morajo biti dobro nadzorovani, da ne pride do brizganja in da se vrhovi valov ne dotikajo in onesnažijo nezaželenih področij plošč. Pri SPAJKANJU REFLOW uporabljamo lepljivo spajkalno pasto za začasno pritrditev elektronskih komponent na plošče. Nato se plošče dajo skozi reflow peč z nadzorom temperature. Tu se spajka stopi in komponente trajno poveže. To tehniko uporabljamo tako za komponente za površinsko montažo kot tudi za komponente s skoznjo luknjo. Ustrezen nadzor temperature in prilagoditev temperatur pečice je bistvenega pomena, da preprečite uničenje elektronskih komponent na plošči zaradi njihovega pregrevanja nad najvišjo temperaturno mejo. V procesu reflow spajkanja imamo dejansko več območij ali stopenj, od katerih ima vsaka poseben toplotni profil, kot so korak predgretja, korak termičnega namakanja, korak reflowa in hlajenja. Ti različni koraki so bistveni za nepoškodovano reflow spajkanje sklopov tiskanih vezij (PCBA). ULTRAZVOČNO SPAJKANJE je še ena pogosto uporabljena tehnika z edinstvenimi zmogljivostmi – uporablja se lahko za spajkanje stekla, keramike in nekovinskih materialov. Na primer, fotovoltaične plošče, ki niso kovinske, potrebujejo elektrode, ki jih je mogoče pritrditi s to tehniko. Pri ultrazvočnem spajkanju uporabljamo ogrevano spajkalno konico, ki prav tako oddaja ultrazvočne vibracije. Te vibracije proizvajajo kavitacijske mehurčke na meji substrata s staljenim materialom spajke. Implozivna energija kavitacije modificira površino oksida in odstrani umazanijo in okside. V tem času nastane tudi plast zlitine. Spajka na vezni površini vsebuje kisik in omogoča nastanek močne skupne vezi med steklom in spajko. DIP SPAJKANJE lahko obravnavamo kot enostavnejšo različico valovnega spajkanja, ki je primerno samo za proizvodnjo v majhnem obsegu. Kot pri drugih postopkih se uporabi prvi čistilni tok. PCB z nameščenimi komponentami se ročno ali polavtomatsko potopijo v posodo s staljeno spajko. Staljena spajka se prilepi na izpostavljena kovinska področja, ki niso zaščitena s spajkalno masko na plošči. Oprema je preprosta in poceni. • LEPLJENJE Z LEPILOM: To je še ena priljubljena tehnika, ki jo pogosto uporabljamo in vključuje lepljenje površin z uporabo lepil, epoksijev, plastičnih sredstev ali drugih kemikalij. Lepljenje se izvede bodisi z izhlapevanjem topila, s strjevanjem s toploto, s strjevanjem z UV svetlobo, s strjevanjem pod pritiskom ali čakanjem določen čas. V naših proizvodnih linijah uporabljamo različna visoko zmogljiva lepila. S pravilno zasnovanimi postopki nanosa in strjevanja lahko lepljenje z lepilom povzroči zelo nizke napetosti, ki so močne in zanesljive. Lepilne vezi so lahko dobra zaščita pred okoljskimi dejavniki, kot so vlaga, onesnaževalci, korozivi, vibracije ... itd. Prednosti lepljenja z lepilom so: nanesejo se lahko na materiale, ki bi jih sicer težko spajkali, varili ali spajkali. Prav tako je lahko boljša za toplotno občutljive materiale, ki bi jih poškodovalo varjenje ali drugi visokotemperaturni postopki. Druge prednosti lepil so, da jih je mogoče nanesti na površine nepravilnih oblik in povečati težo sklopa za zelo zelo majhne količine v primerjavi z drugimi metodami. Tudi spremembe dimenzij v delih so zelo minimalne. Nekatera lepila imajo lastnosti ujemanja indeksov in jih je mogoče uporabiti med optičnimi komponentami, ne da bi bistveno zmanjšali svetlobo ali moč optičnega signala. Slabosti na drugi strani so daljši časi strjevanja, ki lahko upočasnijo proizvodne linije, zahteve glede pritrditve, zahteve glede priprave površine in težave pri razstavljanju, ko je potrebna predelava. Večina naših postopkov lepljenja z lepilom vključuje naslednje korake: - Površinska obdelava: Posebni postopki čiščenja, kot so čiščenje z deionizirano vodo, čiščenje z alkoholom, plazemsko ali koronsko čiščenje, so običajni. Po čiščenju lahko na površine nanesemo sredstva za pospeševanje oprijema, da zagotovimo najboljše možne stike. - Pritrjevanje delov: tako za nanos lepila kot tudi za utrjevanje oblikujemo in uporabljamo vpenjala po meri. -Nanašanje lepila: včasih uporabljamo ročne, včasih pa odvisno od primera avtomatizirane sisteme, kot so robotika, servo motorji, linearni aktuatorji za dostavo lepila na pravo lokacijo in uporabljamo razpršilnike za dostavo v pravi količini in količini. -Utrjevanje: Odvisno od lepila lahko uporabimo preprosto sušenje in utrjevanje ter utrjevanje pod UV lučmi, ki delujejo kot katalizator, ali toplotno strjevanje v pečici ali z uporabo uporovnih grelnih elementov, nameščenih na šablone in napeljave. Priporočamo, da kliknete tukajPRENESITE naše shematske ilustracije postopkov pritrjevanja podjetja AGS-TECH Inc. To vam bo pomagalo bolje razumeti informacije, ki vam jih posredujemo spodaj. • POSTOPKI PRITRJEVANJA: Naši postopki mehanskega spajanja spadajo v dve kategoriji: PRITRDILNI DELI in INTEGRALNI SKLOPI. Primeri pritrdilnih elementov, ki jih uporabljamo, so vijaki, zatiči, matice, sorniki, zakovice. Primeri integralnih spojev, ki jih uporabljamo, so zaskočne in skrčne spojke, šivi, zavihki. Z različnimi načini pritrjevanja poskrbimo, da so naši mehanski spoji močni in zanesljivi za dolgoletno uporabo. VIJAKI in SORNIKI so nekateri najpogosteje uporabljeni pritrdilni elementi za držanje predmetov skupaj in pozicioniranje. Naši vijaki in sorniki izpolnjujejo standarde ASME. Uporabljajo se različne vrste vijakov in sornikov, vključno z vijaki s šestrobo glavo in šestrobimi vijaki, vijaki in vijaki z zatičem, dvojnim vijakom, vijakom z zatičem, vijakom z očesom, vijakom za ogledalo, vijakom za pločevino, vijakom za fino nastavitev, samovrtalnimi in samoreznimi vijaki , nastavitveni vijak, vijaki z vgrajenimi podložkami,…in še več. Imamo različne vrste vijačnih glav, kot so ugreznjena, kupolasta, okrogla, s prirobnično glavo in različne vrste vijačnih pogonov, kot so utorni, križni, kvadratni, šestrobi. RIVET na drugi strani je trajno mehansko pritrjevanje, sestavljeno iz gladke valjaste gredi in glave na eni strani. Po vstavitvi se drugi konec zakovice deformira in njen premer razširi, tako da ostane na mestu. Z drugimi besedami, pred vgradnjo ima zakovica eno glavo, po vgradnji pa dve. Vgradimo različne vrste zakovic glede na uporabo, moč, dostopnost in ceno, kot so zakovice s polno/okroglo glavo, strukturne, polcevaste, slepe, oscar, pogonske, podometne, torne zakovice, samoprebojne. Kovičenje ima prednost v primerih, ko se je treba izogniti toplotni deformaciji in spremembi lastnosti materiala zaradi toplote varjenja. Kovičenje ponuja tudi majhno težo in še posebej dobro trdnost in vzdržljivost proti strižnim silam. Proti nateznim obremenitvam pa so morda bolj primerni vijaki, matice in sorniki. Pri postopku CLINCHING uporabljamo posebne luknjače in matrice za oblikovanje mehanske zapore med pločevinami, ki jih spajamo. Prebijač potisne plasti pločevine v votlino matrice in povzroči nastanek trajnega spoja. V klinču ni potrebno ogrevanje in hlajenje in gre za hladen delovni proces. Je ekonomičen postopek, ki lahko v nekaterih primerih nadomesti točkovno varjenje. Pri PININGU uporabljamo zatiče, ki so strojni elementi, ki se uporabljajo za varovanje položajev strojnih delov med seboj. Glavne vrste so zatiči, razcepni zatiči, vzmetni zatiči, vtični zatiči, in razcepni zatiči. Pri SPENANJU uporabljamo spenjalne pištole in sponke, ki so dvokraki pritrdilni elementi, ki se uporabljajo za spajanje ali vezavo materialov. Spenjanje ima naslednje prednosti: Ekonomično, preprosto in hitro za uporabo, krono sponk je mogoče uporabiti za premostitev materialov, stisnjenih skupaj, Krona sponke lahko olajša premostitev kosa, kot je kabel, in njegovo pritrditev na površino brez prebadanja oz. poškodovana, razmeroma enostavna odstranitev. PRESS FITTING se izvede tako, da se deli potisnejo skupaj in se zaradi trenja med njimi deli pritrdijo. Pritrjeni deli, ki so sestavljeni iz prevelike gredi in premajhne luknje, so na splošno sestavljeni na enega od dveh načinov: z uporabo sile ali izkoriščanjem toplotnega raztezanja ali krčenja delov. Ko je stiskalni fiting vzpostavljen z uporabo sile, uporabimo hidravlično ali ročno stiskalnico. Po drugi strani pa, ko je stiskanje vzpostavljeno s toplotnim raztezanjem, segrejemo ovojne dele in jih vroče sestavimo na svoje mesto. Ko se ohladijo, se skrčijo in dobijo svoje običajne dimenzije. Posledica tega je dobro stiskanje. Temu alternativno pravimo KRČLJIVO. Drugi način za to je, da ohladite ovojne dele pred sestavljanjem in jih nato potisnete v ustrezne dele. Ko se sklop segreje, se razširijo in dosežemo tesno prileganje. Ta zadnja metoda je morda boljša v primerih, ko segrevanje predstavlja tveganje za spremembo lastnosti materiala. Hlajenje je v teh primerih varnejše. Pnevmatski in hidravlični sestavni deli in sklopi • Ventili, hidravlične in pnevmatske komponente, kot so O-obroč, podložka, tesnila, tesnilo, obroč, podložka. Ker je ventilov in pnevmatskih komponent veliko, tukaj ne moremo našteti vsega. Glede na fizična in kemična okolja vaše aplikacije imamo za vas posebne izdelke. Navedite nam uporabo, vrsto komponente, specifikacije, okoljske pogoje, kot so tlak, temperatura, tekočine ali plini, ki bodo v stiku z vašimi ventili in pnevmatskimi komponentami; in izbrali bomo najprimernejši izdelek za vas ali ga izdelali posebej za vašo aplikacijo. CLICK Product Finder-Locator Service PREJŠNJA STRAN
- Transmission Components, Belts, Chains, Cable Drives, Pulleys,AGS-TECH
Transmission Components, Belts, Chains and Cable Drives, Conventional & Grooved or Serrated, Positive Drive, Pulleys Jermeni in verige ter kabelski pogon AGS-TECH Inc. vam ponuja komponente za prenos moči, vključno z jermeni in verigami ter sestavom kabelskega pogona. Z leti izpopolnjevanja so naši gumijasti, usnjeni in drugi jermenski pogoni postali lažji in kompaktnejši ter sposobni prenašati večje obremenitve po nižji ceni. Podobno so se naši verižni pogoni skozi čas zelo razvijali in našim strankam ponujajo več prednosti. Nekatere prednosti uporabe verižnih pogonov so relativno neomejene razdalje med središči gredi, kompaktnost, enostavnost montaže, elastičnost pri napetosti brez zdrsa ali lezenja, sposobnost delovanja v okoljih z visoko temperaturo. Naši kabelski pogoni ponujajo tudi prednosti, kot je preprostost v nekaterih aplikacijah pred drugimi vrstami komponent prenosa. Na voljo so tako standardni, jermenski, verižni in kabelski pogoni kot tudi po meri izdelane in sestavljene različice. Te komponente prenosa lahko izdelamo v pravi velikosti za vašo uporabo in iz najprimernejših materialov. JERMENI IN JERMENSKI POGON: - Običajni ploski jermeni: To so navadni ploski jermeni brez zob, utorov ali nazobčanj. Pogon s ploščatim jermenom nudi fleksibilnost, dobro blaženje udarcev, učinkovit prenos moči pri visokih hitrostih, odpornost proti obrabi in nizke stroške. Pasovi so lahko spojeni ali povezani v večje pasove. Druge prednosti običajnih ploščatih jermenov so, da so tanki, niso izpostavljeni velikim centrifugalnim obremenitvam (zaradi česar so dobri za operacije pri visokih hitrostih z majhnimi jermenicami). Po drugi strani povzročajo velike nosilne obremenitve, ker ploščati jermeni zahtevajo visoko napetost. Druge slabosti pogonov s ploščatim jermenom so lahko zdrs, hrupno delovanje in relativno nižji izkoristki pri nizkih in zmernih hitrostih delovanja. Imamo dve vrsti običajnih jermenov: ojačane in nearmirane. Ojačani jermeni imajo v svoji strukturi natezni element. Konvencionalni ploščati pasovi so na voljo kot usnje, gumirana tkanina ali vrvica, nearmirana guma ali plastika, tkanina, ojačano usnje. Usnjeni pasovi nudijo dolgo življenjsko dobo, fleksibilnost, odličen koeficient trenja, enostavno popravilo. Vendar so usnjeni pasovi razmeroma dragi, potrebujejo obdelavo in čiščenje pasu, odvisno od atmosfere pa se lahko skrčijo ali raztegnejo. Pasovi iz gumirane tkanine ali vrvice so odporni na vlago, kisline in alkalije. Pasovi iz gumirane tkanine so sestavljeni iz vložkov bombaža ali sintetične race, impregnirane z gumo, in so najbolj ekonomični. Pasovi iz gumirane vrvice so sestavljeni iz niza vložkov vrvi, impregnirane z gumo. Pasovi z gumirano vrvico nudijo visoko natezno trdnost ter skromno velikost in maso. Neojačani gumijasti ali plastični jermeni so primerni za lahke pogone z nizko hitrostjo. Neojačane gumijaste in plastične jermene je mogoče raztegniti na svoje mesto preko jermenic. Plastični nearmirani pasovi lahko prenašajo večjo moč v primerjavi z gumijastimi pasovi. Ojačani usnjeni pasovi so sestavljeni iz plastičnega nateznega elementa, stisnjenega med zgornji in spodnji sloj usnja. Nazadnje, naši pasovi iz blaga so lahko sestavljeni iz enega samega kosa bombaža ali race, zloženega in šivanega z vrstami vzdolžnih šivov. Tkaninski pasovi lahko sledijo enakomerno in delujejo pri visoki hitrosti. - Žlebasti ali nazobčani jermeni (kot so klinasti jermeni): To so osnovni ploski jermeni, spremenjeni tako, da zagotavljajo prednosti druge vrste prenosnega izdelka. To so ploščati pasovi z vzdolžno narebreno spodnjo stranjo. Poliklinasti jermeni so vzdolžno žlebasti ali nazobčani ploski jermeni z nateznim odsekom in nizom sosednjih utorov v obliki črke V za sledenje in stiskanje. Moč je odvisna od širine traku. Klinasti jermen je vlečni konj v industriji in je na voljo v različnih standardiziranih velikostih in vrstah za prenos skoraj vseh moči obremenitve. Pogon s klinastim jermenom dobro deluje med 1500 in 6000 ft/min, vendar bodo ozki klinasti jermeni delovali do 10.000 ft/min. Pogoni s klinastim jermenom ponujajo dolgo življenjsko dobo, kot je 3 do 5 let, in omogočajo velika razmerja hitrosti, jih je enostavno namestiti in odstraniti, nudijo tiho delovanje, nizke stroške vzdrževanja, dobro blaženje udarcev med pogonom jermena in gnanimi gredmi. Pomanjkljivost klinastih jermenov je njihov določen zdrs in lezenje, zato morda niso najboljša rešitev, kjer so potrebne sinhrone hitrosti. Imamo industrijske, avtomobilske in kmetijske pasove. Na zalogi so na voljo standardne dolžine pasov in pasovi po meri. Vsi standardni prerezi klinastih jermenov so na zalogi. Obstajajo tabele, kjer lahko izračunate neznane parametre, kot so dolžina jermena, presek jermena (širina in debelina), če poznate nekatere parametre vašega sistema, kot so premeri pogonskih in gnanih jermenic, sredinska razdalja med jermenicami in vrtilne hitrosti jermenic. Uporabite lahko takšne tabele ali pa nas prosite, da izberemo pravi klinasti jermen za vas. - Pozitivni pogonski jermeni (zobati jermen): Ti jermeni so prav tako ploščatega tipa z nizom enakomerno razporejenih zob na notranjem obodu. Pozitivni pogonski ali zobati jermeni združujejo prednosti ploskih jermenov z lastnostmi pozitivnega oprijema verig in zobnikov. Pozitivni pogonski jermeni ne odkrivajo zdrsa ali sprememb hitrosti. Možna je široka paleta razmerij hitrosti. Obremenitve ležajev so majhne, ker lahko delujejo pri nizki napetosti. Vendar so bolj dovzetni za neskladja v jermenicah. - Jermenice, jermenice, pesta za jermene: Različne vrste jermenic se uporabljajo z ravnimi, rebrastimi (nazobčanimi) in pozitivnimi pogonskimi jermeni. Vse jih izdelujemo. Večina naših jermenic s ploščatim jermenom je izdelana z ulivanjem železa, vendar so na voljo tudi jeklene različice v različnih kombinacijah platišča in pesta. Naše jermenice za ploščate jermene imajo lahko polna, naperasta ali deljena pesta ali pa jih izdelamo po vaši želji. Rebrasti jermeni in jermeni s pozitivnim pogonom so na voljo v različnih velikostih in širinah. Vsaj ena jermenica pri pogonih z zobatim jermenom mora imeti prirobnico, da zadrži jermen na pogonu. Pri pogonskih sistemih z dolgim središčem je priporočljivo, da sta oba jermenica prirobljena. Vrvenice so žlebičasta kolesa jermenic in so običajno izdelane z litjem železa, oblikovanjem jekla ali plastičnim vlivanjem. Oblikovanje jekla je primeren postopek za izdelavo avtomobilskih in kmetijskih snopov. Izdelujemo snope z navadnimi in globokimi utori. Vrvenice z globokimi utori so zelo primerne, kadar klinasti jermen vstopi v kolut pod kotom, kot je to v primeru četrtobratnih pogonov. Globoki utori so zelo primerni tudi za pogone z navpično gredjo in aplikacije, kjer lahko tresenje jermenov predstavlja težavo. Naše proste jermenice so žlebičaste ali ploščate jermenice, ki ne služijo prenosu mehanske moči. Prosti jermeni se uporabljajo predvsem za napenjanje jermenov. - Enojni in večjermenski pogoni: enojermenski pogoni imajo en sam utor, medtem ko imajo več jermenski pogoni več utorov. S klikom na ustrezno barvno besedilo spodaj lahko prenesete naše kataloge: - Jermeni za prenos moči (vključno s klinastimi jermeni, zobatimi jermeni, jermeni z neobdelanimi robovi, zavitimi jermeni in posebnimi jermeni) - tekoči trakovi - V-jermenice - Jermenice za krmiljenje VERIGE & VERIŽNI POGONI: Naše verige za prenos moči imajo nekatere prednosti, kot so razmeroma neomejene središčne razdalje gredi, enostavna montaža, kompaktnost, elastičnost pod napetostjo brez zdrsa ali lezenja, sposobnost delovanja pri visokih temperaturah. Tukaj so glavne vrste naših verig: - Snemljive verige: Naše snemljive verige so izdelane v različnih velikostih, naklonih in končni trdnosti ter na splošno iz tempranega železa ali jekla. Tvorne verige so izdelane v različnih velikostih od 0,902 (23 mm) do 4,063 palca (103 mm) koraka in končne trdnosti od 700 do 17.000 lb/kvadratni palec. Po drugi strani so naše snemljive jeklene verige izdelane v velikostih od 0,904 palca (23 mm) do približno 3,00 palca (76 mm) v koraku, s končno trdnostjo od 760 do 5000 lb/kvadratni palec._cc781905-5cde-3194-bb3b- 136bad5cf58d_ - Zobne verige: Te verige se uporabljajo za težja bremena in nekoliko višje hitrosti do približno 450 čevljev/min (2,2 m/s). Verige z iglami so izdelane iz posameznih litih členov, ki imajo poln, okrogel konec cevi z zamaknjenimi stranskimi prečkami. Ti členi verige so povezani z jeklenimi zatiči. Te verige imajo naklon od približno 1,00 palca (25 mm) do 6,00 palca (150 mm) in končne trdnosti med 3600 in 30.000 lb/kvadratni palec. - Verige s stranskim drogom: Te so priljubljene v pogonskih verigah gradbenih strojev. Te verige delujejo pri hitrosti do 1000 ft/min in prenašajo obremenitve do približno 250 KM. Na splošno ima vsak člen dve zamaknjeni stranski prečki, eno pušo, en valj, en zatič, razcepko. - Valjčne verige: Na voljo so v korakih od 0,25 (6 mm) do 3,00 (75 mm) palcev. Končna trdnost valjčnih verig z enojno širino je med 925 in 130.000 lb/kvadratni palec. Na voljo so različice valjčnih verig z več širinami, ki prenašajo večjo moč pri višjih hitrostih. Valjčne verige z več širinami ponujajo tudi bolj gladko delovanje z zmanjšanim hrupom. Valjčne verige so sestavljene iz valjčnih členov in čepnih členov. Razcepke se uporabljajo v snemljivih različicah valjčnih verig. Zasnova valjčnih verižnih pogonov zahteva strokovno znanje. Medtem ko jermenski pogoni temeljijo na linearnih hitrostih, verižni pogoni temeljijo na vrtilni hitrosti manjšega zobnika, ki je v večini naprav gnani člen. Poleg konjskih moči in hitrosti vrtenja zasnova verižnih pogonov temelji na številnih drugih dejavnikih. - Verige z dvojnim korakom: v osnovi enake verigam z valji, le da je korak dvakrat daljši. - Verige z obrnjenimi zobmi (tihe): Verige za visoke hitrosti, ki se večinoma uporabljajo za pogone s pogonom na odgonu moči. Verižni pogoni z obrnjenimi zobmi lahko prenašajo moč do 1200 KM in so sestavljeni iz niza zobatih členov, izmenično sestavljenih bodisi s čepi bodisi s kombinacijo komponent spoja. Sredinska vodilna veriga ima vodilne člene za vpenjanje utorov v verižniku, stranska vodilna veriga pa ima vodila za vpetje ob straneh verižnika. - Bead ali drsne verige: te verige se uporabljajo za počasne vožnje in tudi pri ročnem delovanju. S klikom na ustrezno barvno besedilo spodaj lahko prenesete naše kataloge: - Pogonske verige - Transportne verige - Transportne verige z velikim korakom - Valjčne verige iz nerjavečega jekla - Dvižne verige - Verige za motorna kolesa - Verige kmetijskih strojev - Verižniki: Naši standardni zobniki ustrezajo standardom ANSI. Ploščati zobniki so ploščati zobniki brez pesta. Naši mali in srednje veliki zobniki pesta so struženi iz paličastega materiala ali odkovkov ali izdelani z varjenjem paličastega pesta na vroče valjano ploščo. AGS-TECH Inc. lahko dobavi verižnike, strojno izdelane iz litin iz sive litine, jeklenih litin in varjenih konstrukcij pest, sintrane praškaste kovine, oblikovane ali strojno obdelane plastike. Za nemoteno delovanje pri visokih hitrostih je bistvena pravilna izbira velikosti zobnikov. Prostorska omejitev je seveda dejavnik, ki ga pri izbiri zobnika ne smemo zanemariti. Priporočljivo je, da razmerje med gonilnimi in gnanimi zobniki ne sme biti večje od 6:1, ovitek verige na gonilniku pa 120 stopinj. Sredinske razdalje med manjšimi in večjimi verižniki, dolžine verige in napetost verige morajo biti izbrane v skladu z nekaterimi priporočenimi inženirskimi izračuni in smernicami in ne naključno. Prenesite naše kataloge s klikom na barvno besedilo spodaj: - Zobniki in ploščata kolesa - Puše menjalnika - Verižna sklopka - Verižne ključavnice KABELSKI POGONI: V nekaterih primerih imajo svoje prednosti pred jermenskimi in verižnimi pogoni. Kabelski pogoni lahko opravljajo enako funkcijo kot jermeni in so lahko enostavnejši in bolj ekonomični za uporabo v nekaterih aplikacijah. Na primer, nova serija kabelskih pogonov Synchromesh je zasnovana za pozitivno vleko, ki nadomesti običajne vrvi, preproste kable in zobate pogone, zlasti v ozkih prostorih. Nov kabelski pogon je zasnovan tako, da zagotavlja visoko natančno pozicioniranje v elektronski opremi, kot so fotokopirni stroji, risalniki, pisalni stroji, tiskalniki itd. Ključna značilnost novega kabelskega pogona je njegova zmožnost uporabe v 3D serpentinastih konfiguracijah, ki omogočajo izjemno miniaturne oblike. Synchromesh kabli se lahko uporabljajo z nižjo napetostjo v primerjavi z vrvmi, kar zmanjša porabo energije. Kontaktirajte AGS-TECH za vprašanja in mnenja o jermenih, verižnih in kabelskih pogonih. CLICK Product Finder-Locator Service PREJŠNJA STRAN
- Machine Elements Manufacturing, Gears, Gear Drives, Bearings, Keys, Splines
Machine Elements Manufacturing, Gears, Gear Drives, Bearings, Keys, Splines, Pins, Shafts, Seals, Fasteners, Clutch, Cams, Followers, Belts, Couplings, Shafts Izdelava strojnih elementov Preberi več Jermeni in verige ter kabelski pogon Preberi več Zobniki in pogonski sklop Preberi več Proizvodnja sklopk in ležajev Preberi več Proizvodnja ključev, zatičev in zatičev Preberi več Izdelava odmikačev in sledilnikov ter povezav in zaskočnih koles Preberi več Izdelava gredi Preberi več Proizvodnja mehanskih tesnil Preberi več Sklopka in zavora Preberi več Proizvodnja pritrdilnih elementov Preberi več Simple Machines Montaža STROJNI ELEMENTI so osnovni sestavni deli stroja. Ti elementi so sestavljeni iz treh osnovnih vrst: 1.) Strukturne komponente, vključno s členi ogrodja, ležaji, osmi, čepi, pritrdilnimi elementi, tesnili in mazivi. 2.) Mehanizmi za krmiljenje gibanja na različne načine, kot so menjalniki, jermenski ali verižni pogoni, povezave, odmični in sledilni sistemi, zavore in sklopke. 3.) Krmilne komponente, kot so gumbi, stikala, indikatorji, senzorji, aktuatorji in računalniški krmilniki. Večina strojnih elementov, ki vam jih ponujamo, je standardiziranih na običajne velikosti, vendar so na voljo tudi strojni elementi po meri za vaše specializirane aplikacije. Prilagajanje strojnih elementov lahko poteka na obstoječih modelih, ki so v naših katalogih za prenos, ali na popolnoma novih dizajnih. Izdelava prototipov in proizvodnja strojnih elementov se lahko nadaljujeta, ko obe strani odobrita načrt. Če je treba zasnovati in izdelati nove strojne elemente, nam naše stranke po e-pošti pošljejo lastne načrte in jih pregledamo za odobritev, ali pa nas prosijo, da oblikujemo strojne elemente za njihovo uporabo. V slednjem primeru uporabimo vse prispevke naših strank in oblikujemo strojne elemente ter pošljemo končne načrte našim strankam v odobritev. Po odobritvi izdelamo prve artikle in nato izdelamo strojne elemente po končnem dizajnu. V katerikoli fazi tega dela, v primeru, da se določen strojni element na terenu ne obnese zadovoljivo (kar je redko), pregledamo celoten projekt in po potrebi skupaj z našimi naročniki izvedemo spremembe. Naša običajna praksa je, da z našimi strankami podpišemo pogodbe o nerazkritju (NDA) za načrtovanje strojnih elementov ali katerega koli drugega izdelka, kadar koli je to potrebno ali potrebno. Ko so strojni elementi za določeno stranko zasnovani in izdelani po meri, ji dodelimo kodo izdelka in jih proizvajamo in prodajamo le naši stranki, ki je lastnik izdelka. Strojne elemente reproduciramo z razvitimi orodji, kalupi in postopki tolikokrat, kot je potrebno, in kadar koli jih naša stranka ponovno naroči. Z drugimi besedami, ko je strojni element po meri zasnovan in izdelan za vas, intelektualno lastnino ter vsa orodja in kalupe rezerviramo in hranimo za nedoločen čas za vas in izdelke reproduciramo, kot želite. Našim strankam nudimo tudi inženirske storitve s kreativnim združevanjem strojnih elementov v komponento ali sklop, ki služi aplikaciji in izpolnjuje ali presega pričakovanja naših strank. Obrati, ki izdelujejo naše strojne elemente, so kvalificirani bodisi po ISO9001, QS9000 ali TS16949. Poleg tega ima večina naših izdelkov oznako CE ali UL in ustreza mednarodnim standardom, kot so ISO, SAE, ASME, DIN. Kliknite na podmenije, če želite pridobiti podrobne informacije o elementih našega stroja, vključno z: - Jermeni, verige in kabelski pogoni - Zobniki in zobniški pogoni - Spojke in ležaji - Ključi, zatiči in zatiči - Odmikače in povezave - Jaški - Mehanska tesnila - Industrijska sklopka in zavora - Pritrdilni elementi - Simple Machines Za naše kupce, oblikovalce in razvijalce novih izdelkov, vključno s strojnimi elementi, smo pripravili referenčno brošuro. Seznanite se lahko z nekaterimi pogosto uporabljenimi izrazi pri načrtovanju strojnih komponent: Prenesite brošuro za splošne izraze strojništva, ki jih uporabljajo oblikovalci in inženirji Naši strojni elementi najdejo uporabo na različnih področjih, kot so industrijski stroji, sistemi za avtomatizacijo, oprema za testiranje in meroslovje, transportna oprema, gradbeni stroji in praktično kjer koli. AGS-TECH razvija in proizvaja strojne elemente iz različnih materialov glede na uporabo. Materiali, ki se uporabljajo za strojne elemente, lahko segajo od oblikovane plastike, ki se uporablja za igrače, do kaljenega in posebej prevlečenega jekla za industrijske stroje. Naši oblikovalci uporabljajo najsodobnejšo profesionalno programsko opremo in oblikovalska orodja za razvoj strojnih elementov, pri čemer upoštevajo podrobnosti, kot so koti zobnikov, vključene napetosti, stopnje obrabe ... itd. Prosimo, pobrskajte po naših podmenijih in prenesite naše brošure in kataloge izdelkov, da vidite, ali lahko poiščete strojne elemente za vašo aplikacijo. Če ne najdete primernega za vašo aplikacijo, nam to sporočite in skupaj z vami bomo razvili in izdelali strojne elemente, ki bodo ustrezali vašim potrebam. Če vas namesto proizvodnih zmogljivosti zanimajo predvsem naše inženirske in raziskovalno-razvojne zmogljivosti, vas vabimo, da obiščete našo spletno stran http://www.ags-engineering.com kjer lahko najdete podrobnejše informacije o našem dizajnu, razvoju izdelkov, razvoju procesov, inženirskih svetovalnih storitvah in več CLICK Product Finder-Locator Service PREJŠNJA STRAN
- Glass and Ceramic Manufacturing, Hermetic Packages, Seals, Bonding
Glass and Ceramic Manufacturing, Hermetic Packages Seals and Bonding, Tempered Bulletproof Glass, Blow Moulding, Optical Grade Glass, Conductive Glass, Molding Oblikovanje stekla in keramike Vrsta proizvodnje stekla, ki jo ponujamo, je steklena posoda, pihanje stekla, steklena vlakna, cevi in palice, gospodinjska in industrijska steklena posoda, svetilke in žarnice, natančno oblikovanje stekla, optične komponente in sklopi, ravno in ploščato steklo ter float steklo. Izvajamo tako ročno kot tudi strojno preoblikovanje. Naši priljubljeni postopki izdelave tehnične keramike so stiskanje, izostatično stiskanje, vroče izostatično stiskanje, vroče stiskanje, drsno litje, litje trakov, ekstrudiranje, brizganje, zelena strojna obdelava, sintranje ali žganje, diamantno brušenje, hermetični sklopi. Priporočamo, da kliknete tukaj PRENESITE naše shematske ilustracije procesov oblikovanja in oblikovanja stekla podjetja AGS-TECH Inc. PRENESITE naše shematične ilustracije proizvodnih procesov tehnične keramike podjetja AGS-TECH Inc. Te prenosljive datoteke s fotografijami in skicami vam bodo pomagale bolje razumeti informacije, ki vam jih posredujemo spodaj. • PROIZVODNJA EMBALAŽNEGA STEKLA: Za proizvodnjo imamo avtomatizirane linije PRESS AND BLOW ter BLOW AND BLOW. V procesu pihanja in pihanja spustimo kepico v prazen kalup in oblikujemo vrat s pihanjem stisnjenega zraka od zgoraj. Takoj za tem se stisnjen zrak drugič vpihne iz druge smeri skozi vrat posode, da se oblikuje predoblika steklenice. Ta predoblika se nato prenese v dejanski kalup, ponovno segreje, da se zmehča, in uporabi stisnjen zrak, da predoblika dobi končno obliko posode. Natančneje, pod pritiskom je in potisnjen proti stenam votline kalupa za pihanje, da zavzame želeno obliko. Končno se izdelana steklena posoda prenese v žarilno peč za naknadno ponovno segrevanje in odstranitev napetosti, ki nastanejo med oblikovanjem, in se kontrolirano ohladi. Pri metodi stiskanja in pihanja se staljene kepe dajo v kalup za parison (prazni kalup) in stisnejo v obliko parison (prazna oblika). Surovci se nato prenesejo v kalupe za pihanje in jih pihajo podobno kot postopek, opisan zgoraj pod “Postopek pihanja in pihanja”. Nadaljnji koraki, kot sta žarjenje in razbremenitev napetosti, so podobni ali enaki. • PIHANJE STEKLA: Izdelke iz stekla izdelujemo tako z običajnim ročnim pihanjem kot tudi s stisnjenim zrakom z avtomatsko opremo. Za nekatera naročila je potrebno običajno pihanje, kot so projekti, ki vključujejo umetnine iz stekla, ali projekti, ki zahtevajo manjše število delov z ohlapnimi tolerancami, izdelava prototipov/demo projekti… itd. Običajno pihanje stekla vključuje potopitev votle kovinske cevi v posodo s staljenim steklom in vrtenje cevi za zbiranje določene količine steklenega materiala. Steklo, nabrano na konici cevi, valjamo po ploščatem železu, oblikujemo po želji, podolgujemo, ponovno segrejemo in pihamo. Ko je pripravljen, se vstavi v kalup in vpihne zrak. Votlina kalupa je mokra, da preprečite stik stekla s kovino. Vodni film deluje kot blazina med njimi. Ročno pihanje je delovno intenziven počasen postopek in primeren samo za izdelavo prototipov ali predmetov visoke vrednosti, ni primeren za poceni naročila velikih količin na kos. • PROIZVODNJA STEKLENIH IZDELKOV ZA GOSPODINJSTVO IN INDUSTRIJO: Z uporabo različnih vrst steklenih materialov se izdeluje veliko različnih steklenih izdelkov. Nekateri kozarci so odporni na vročino in primerni za laboratorijsko stekleno posodo, nekateri pa so dovolj dobri, da zdržijo večkrat pomivanje v pomivalnem stroju in so primerni za izdelavo domačih izdelkov. Z uporabo strojev Westlake se proizvede na desettisoče kosov kozarcev na dan. Če poenostavimo, staljeno steklo zbiramo z vakuumom in ga vstavimo v kalupe za izdelavo predoblik. Nato se v kalupe vpihne zrak, ti se prenesejo v drug kalup in spet se vpihne zrak in steklo dobi končno obliko. Tako kot pri ročnem pihanju se ti kalupi ohranjajo mokri z vodo. Nadaljnje raztezanje je del končne operacije, kjer se oblikuje vrat. Odvečno steklo sežge. Nato sledi postopek nadzorovanega ponovnega segrevanja in hlajenja, opisan zgoraj. • OBLIKOVANJE STEKLENIH CEV IN PALIC: Glavni postopki, ki jih uporabljamo za proizvodnjo steklenih cevi, sta postopka DANNER in VELLO. Pri Dannerjevem postopku steklo iz peči teče in pade na nagnjen tulec iz ognjevzdržnih materialov. Tulec se prenaša na vrteči se votli gredi ali pihalniku. Steklo se nato ovije okoli tulca in tvori gladko plast, ki teče navzdol po tulcu in čez konico gredi. Pri cevastem preoblikovanju zrak vpihujemo skozi pihalo z votlo konico, pri paličastem pa uporabljamo polne konice na gredi. Cevi ali palice se nato potegnejo čez nosilne valje. Dimenzije, kot sta debelina stene in premer steklenih cevi, se prilagodijo želenim vrednostim z nastavitvijo premera tulca in zračnega tlaka pihanja na želeno vrednost, prilagajanjem temperature, hitrosti pretoka stekla in hitrosti vlečenja. Po drugi strani postopek izdelave steklene cevi Vello vključuje steklo, ki potuje iz peči in v skledo z votlim trnom ali zvonom. Steklo gre nato skozi zračni prostor med trnom in skledo ter dobi obliko cevi. Nato potuje preko valjev do risalnega stroja in se ohladi. Na koncu hladilne linije poteka razrez in končna obdelava. Dimenzije cevi se lahko prilagajajo tako kot pri Dannerjevem postopku. Ko primerjamo postopek Danner s postopkom Vello, lahko rečemo, da je postopek Vello bolj primeren za proizvodnjo velikih količin, medtem ko je postopek Danner morda bolj primeren za natančna naročila cevi manjše prostornine. • PREDELAVA PLOŠČASTEGA & PLOŠČANEGA & FLOAT STEKLA: Imamo velike količine ravnega stekla v debelinah od submilimetrskih debelin do nekaj centimetrov. Naša ravna stekla so skoraj optično popolna. Nudimo steklo s posebnimi premazi, kot so optični premazi, kjer se s tehniko kemičnega naparjevanja nanesejo premazi, kot je antirefleks ali zrcalni premaz. Pogosti so tudi prozorni prevodni premazi. Na voljo so tudi hidrofobni ali hidrofilni premazi na steklu ter premazi, ki poskrbijo, da se steklo samočisti. Kaljena, neprebojna in laminirana stekla so še drugi priljubljeni izdelki. Steklo razrežemo v želene oblike z želenimi tolerancami. Na voljo so tudi drugi sekundarni postopki, kot je krivljenje ali krivljenje ravnega stekla. • PRECIZNO VLIVANJE STEKLA: to tehniko večinoma uporabljamo za izdelavo natančnih optičnih komponent brez potrebe po dražjih in dolgotrajnejših tehnikah, kot so brušenje, lepljenje in poliranje. Ta tehnika ni vedno zadostna za izdelavo najboljšega iz najboljše optike, toda v nekaterih primerih, kot so potrošniški izdelki, digitalni fotoaparati, medicinska optika, je lahko cenejša dobra možnost za velikoserijsko proizvodnjo. Prav tako ima prednost pred drugimi tehnikami oblikovanja stekla, kjer so potrebne zapletene geometrije, na primer v primeru kroglic. Osnovni proces vključuje nalaganje spodnje strani našega kalupa s steklenim surovcem, praznjenje procesne komore za odstranitev kisika, bližnje zaprtje kalupa, hitro in izotermno segrevanje matrice in stekla z infrardečo svetlobo, nadaljnje zapiranje polovic kalupa. počasno kontrolirano stiskanje zmehčanega stekla do želene debeline in na koncu ohlajanje stekla in polnjenje komore z dušikom ter odstranitev produkta. Natančen nadzor temperature, razdalja zapiranja kalupa, sila zapiranja kalupa, ujemanje koeficientov razteznosti kalupa in steklenega materiala so ključni pri tem procesu. • PROIZVODNJA STEKLENIH OPTIČNIH KOMPONENT IN SKLOPOV : Poleg natančnega oblikovanja stekla obstaja vrsta dragocenih postopkov, ki jih uporabljamo za izdelavo visoko kakovostnih optičnih komponent in sklopov za zahtevne aplikacije. Brušenje, lepljenje in poliranje stekel optičnega razreda v finih posebnih abrazivnih goščah je umetnost in znanost za izdelavo optičnih leč, prizem, plošč in še več. Ploskost, valovitost, gladkost in optične površine brez napak zahtevajo veliko izkušenj s takšnimi postopki. Majhne spremembe v okolju lahko povzročijo izdelke, ki ne ustrezajo specifikacijam, in zaustavitev proizvodne linije. Obstajajo primeri, ko lahko z enim samim brisanjem optične površine s čisto krpo dosežete, da izdelek izpolnjuje specifikacije ali pa ne uspe na preizkusu. Nekateri uporabljeni priljubljeni stekleni materiali so taljeni silicijev dioksid, kremen, BK7. Tudi sestavljanje takšnih komponent zahteva specializirane nišne izkušnje. Včasih se uporabljajo posebna lepila. Vendar je včasih tehnika, imenovana optični kontakt, najboljša izbira in ne vključuje nobenega materiala med pritrjenimi optičnimi stekli. Sestoji iz fizičnega stika ravnih površin, ki se med seboj pritrdijo brez lepila. V nekaterih primerih se uporabljajo mehanski distančniki, natančne steklene palice ali kroglice, objemke ali strojno obdelane kovinske komponente za sestavljanje optičnih komponent na določenih razdaljah in v določeni geometrijski orientaciji ena glede na drugo. Oglejmo si nekaj naših priljubljenih tehnik za izdelavo vrhunske optike. BRUŠENJE IN LEPANJE IN POLIRANJE: Grobo obliko optične komponente dobimo z brušenjem surovca stekla. Nato se izvede lepljenje in poliranje z vrtenjem in drgnjenjem hrapavih površin optičnih komponent ob orodja želene oblike površine. Med optiko in orodja za oblikovanje se vlijejo gošče z drobnimi abrazivnimi delci in tekočino. Velikosti abrazivnih delcev v takih goščah se lahko izberejo glede na želeno stopnjo ravnosti. Odstopanja kritičnih optičnih površin od želenih oblik so izražena z valovno dolžino uporabljene svetlobe. Naša visoko natančna optika ima tolerance desetinke valovne dolžine (valovna dolžina/10) ali pa so možne tudi manjše. Poleg površinskega profila se kritične površine skenirajo in ovrednotijo za druge površinske značilnosti in napake, kot so dimenzije, praske, odrezki, jamice, lise ... itd. Zaradi strogega nadzora okoljskih pogojev v optični proizvodnji ter obsežnih meroslovnih in preskusnih zahtev z najsodobnejšo opremo je to zahtevna panoga industrije. • SEKUNDARNI POSTOPKI V PROIZVODNJI STEKLA: Ponovno smo omejeni le z vašo domišljijo, ko gre za sekundarne in dodelavne postopke stekla. Tukaj navajamo nekaj izmed njih: -Prevleke na steklu (optične, električne, tribološke, termične, funkcionalne, mehanske...). Kot primer lahko spremenimo površinske lastnosti stekla, tako da na primer odseva toploto, tako da ohranja notranjost stavbe hladno, ali naredimo enostransko infrardečo absorbcijo z uporabo nanotehnologije. To pomaga ohranjati toploto v notranjosti stavb, saj bo najbolj zunanja površinska plast stekla absorbirala infrardeče sevanje znotraj stavbe in ga sevala nazaj v notranjost. -Jedkanje na steklu -Aplicirano keramično označevanje (ACL) -Graviranje - Plameno poliranje - Kemično poliranje -barvanje IZDELAVA TEHNIČNE KERAMIKE • STISKANJE MADRE: Sestoji iz enoosnega stiskanja zrnatih praškov, zaprtih v matrici • VROČE STISANJE: Podobno stiskanju, vendar z dodatkom temperature za izboljšanje zgostitve. Prah ali stisnjena predoblika se postavi v grafitno matrico in uporabi se enoosni tlak, medtem ko se matrica vzdržuje pri visokih temperaturah, kot je 2000 C. Temperature so lahko različne, odvisno od vrste keramičnega prahu, ki se obdeluje. Za zapletene oblike in geometrije bo morda potrebna druga naknadna obdelava, kot je diamantno brušenje. • IZOSTATIČNO STISKANJE: zrnati prah ali stisnjene zgoščenke se dajo v nepredušne posode in nato v zaprto tlačno posodo s tekočino v notranjosti. Nato se stisnejo s povečanjem tlaka v tlačni posodi. Tekočina v posodi enakomerno prenaša tlačne sile po celotni površini nepredušne posode. Material je tako enakomerno stisnjen in prevzame obliko svoje fleksibilne posode ter njegov notranji profil in značilnosti. • VROČE IZOSTATIČNO STISKANJE: Podobno izostatičnemu stiskanju, vendar poleg atmosfere plina pod tlakom sintramo kompakten pri visoki temperaturi. Vroče izostatično stiskanje povzroči dodatno zgostitev in povečano trdnost. • SLIP CITY / DREN CASTING : Kalup napolnimo s suspenzijo mikrometrskih keramičnih delcev in nosilne tekočine. Ta mešanica se imenuje "slip". Kalup ima pore in zato se tekočina v mešanici filtrira v kalup. Posledično se na notranjih površinah kalupa oblikuje odlitek. Po sintranju lahko dele vzamemo iz kalupa. • ULIVANJE TRAKOV: Keramične trakove izdelujemo z ulivanjem keramične brozge na ravne premikajoče se nosilne površine. Gnojnice vsebujejo keramične prahove, pomešane z drugimi kemikalijami za namene vezave in prenašanja. Ko topila izhlapevajo, ostanejo gosti in upogljivi listi keramike, ki jih je mogoče poljubno rezati ali zvijati. • EKSTRUZIJSKO OBLIKOVANJE: Kot pri drugih postopkih ekstrudiranja se mehka zmes keramičnega prahu z vezivi in drugimi kemikalijami spusti skozi matrico, da pridobi obliko prečnega prereza, nato pa se razreže na želene dolžine. Postopek izvajamo s hladnimi ali segretimi keramičnimi mešanicami. • NIZKTLAČNO BRIZGANJE: Pripravimo mešanico keramičnega prahu z vezivi in topili ter jo segrejemo na temperaturo, kjer jo lahko enostavno stisnemo in potisnemo v votlino orodja. Ko je cikel oblikovanja končan, se del izvrže in vezivna kemikalija sežge. Z brizganjem lahko ekonomično pridobimo zapletene dele v velikih količinah. Možne so luknje , ki obsegajo majhen delček milimetra na 10 mm debeli steni, navoji so možni brez nadaljnje obdelave, možne so tolerance do +/- 0,5 % in celo nižje, ko so deli strojno obdelani , možne so debeline sten od 0,5 mm do dolžine 12,5 mm, kot tudi debeline sten od 6,5 mm do dolžine 150 mm. • ZELENA OBDELAVA: Z istimi orodji za obdelavo kovin lahko obdelujemo stisnjene keramične materiale, medtem ko so še mehki kot kreda. Možna so toleranca +/- 1 %. Za boljše tolerance uporabljamo diamantno brušenje. • SINTRANJE ali ŽGANJE: Sintranje omogoča popolno zgostitev. Na zelenih kompaktnih delih pride do znatnega krčenja, vendar to ni velik problem, saj te dimenzijske spremembe upoštevamo pri načrtovanju dela in orodja. Delci prahu so med seboj povezani in poroznost, ki jo povzroča postopek stiskanja, je v veliki meri odstranjena. • DIAMANTNO BRUŠENJE : najtrši material na svetu "diamant" se uporablja za brušenje trdih materialov, kot je keramika, in pridobijo se natančni deli. Dosegajo se tolerance v mikrometrskem območju in zelo gladke površine. Zaradi stroškov se o tej tehniki odločimo le, ko jo res potrebujemo. • HERMETIČNI SESTAVI so tisti, ki praktično ne omogočajo izmenjave snovi, trdnih snovi, tekočin ali plinov med vmesniki. Hermetično tesnjenje je zrakotesno. Hermetična elektronska ohišja so na primer tista, ki ohranjajo občutljivo notranjo vsebino zapakirane naprave nepoškodovano zaradi vlage, onesnaževalcev ali plinov. Nič ni 100-odstotno hermetično, toda ko govorimo o hermetičnosti, mislimo, da v praktičnem smislu obstaja hermetičnost do te mere, da je stopnja puščanja tako nizka, da so naprave varne v normalnih okoljskih pogojih zelo dolgo časa. Naši hermetični sklopi so sestavljeni iz kovinskih, steklenih in keramičnih komponent, kovinsko-keramičnih, keramike-kovinsko-keramičnih, kovinsko-keramičnih-kovinskih, kovinsko-kovinskih, kovinsko-steklo, kovinsko-steklo-kovinskih, steklo-kovinsko-steklo, steklo- kovina in steklo na steklo ter vse ostale kombinacije lepljenja kovina-steklo-keramika. Keramične komponente lahko na primer prevlečemo s kovino, tako da se lahko močno vežejo na druge komponente v sklopu in imajo odlično sposobnost tesnjenja. Imamo znanje in izkušnje za prevleko optičnih vlaken ali dovodnih kanalov s kovino in njihovo spajkanje ali spajkanje na ohišje, tako da plini ne prehajajo ali uhajajo v ohišja. Zato se uporabljajo za izdelavo elektronskih ohišij za kapsuliranje občutljivih naprav in njihovo zaščito pred zunanjim ozračjem. Poleg odličnih tesnilnih lastnosti, druge lastnosti, kot so koeficient toplotnega raztezanja, odpornost proti deformacijam, narava brez sproščanja plinov, zelo dolga življenjska doba, narava neprevodnosti, lastnosti toplotne izolacije, antistatičnost ... itd. naredijo steklene in keramične materiale izbiro za določene aplikacije. Informacije o našem obratu za proizvodnjo keramičnih in kovinskih fitingov, hermetičnega tesnjenja, vakuumskih dovodov, visokega in ultravisokega vakuuma in komponent za nadzor tekočin lahko najdete tukaj:Brošura tovarne hermetičnih komponent CLICK Product Finder-Locator Service PREJŠNJA STRAN
- Wire & Spring Forming, Shaping, Welding, Assembly of Wires, Coil, CNC
Wire & Spring Forming, Shaping, Welding, Assembly of Wires, Coil Compression Extension Torsion Flat Springs, Custom Wires, Helical Springs at AGS-TECH Inc. Oblikovanje žice in vzmeti Izdelujemo žice po meri, montažo žice, žice oblikovane v želene 2D in 3D oblike, žične mreže, mreže, ograde, košaro, ograjo, žično vzmet, ploščato vzmet; torzija, stiskanje, napetost, ravne vzmeti in drugo. Naši postopki so oblikovanje žice in vzmeti, vlečenje žice, oblikovanje, upogibanje, varjenje, trdo spajkanje, spajkanje, prebadanje, stiskanje, vrtanje, posnemanje robov, brušenje, rezanje navojev, nanašanje prevlek, štiri drsenje, oblikovanje drsnikov, navijanje, zvijanje, vrtanje. Priporočamo, da kliknete tukaj PRENESITE naše shematske ilustracije procesov oblikovanja žice in vzmeti podjetja AGS-TECH Inc. Ta datoteka s fotografijami in skicami, ki jo lahko prenesete, vam bo pomagala bolje razumeti informacije, ki vam jih ponujamo spodaj. • VLEČENJE ŽICE: Z uporabo nateznih sil raztegnemo kovinski material in ga potegnemo skozi matrico, da zmanjšamo premer in povečamo njegovo dolžino. Včasih uporabimo vrsto matric. Sposobni smo izdelati matrice za vsak premer žice. Z materialom visoke natezne trdnosti vlečemo zelo tanke žice. Ponujamo tako hladno kot vroče obdelane žice. • OBLIKOVANJE ŽICE: Zvitek merjene žice se upogne in oblikuje v uporaben izdelek. Imamo sposobnost oblikovanja žic iz vseh premerov, vključno s tankimi filamenti in tudi debelimi žicami, kot so tiste, ki se uporabljajo kot vzmeti pod avtomobilsko šasijo. Oprema, ki jo uporabljamo za preoblikovanje žice, je ročni in CNC oblikovalnik žice, navijalka, močne stiskalnice, fourslide, multi-slide. Naši postopki so vlečenje, upogibanje, ravnanje, ravnanje, raztezanje, rezanje, napenjanje, spajkanje in varjenje ter trdo spajkanje, sestavljanje, zvijanje, valjčenje (ali kriljenje), prebadanje, vrezovanje navojev v žice, vrtanje, posnemanje, brušenje, premazovanje in površinske obdelave. Našo najsodobnejšo opremo je mogoče nastaviti za razvoj zelo kompleksnih modelov poljubnih oblik in majhnih toleranc. Ponujamo različne vrste koncev kot so sferični, koničasti ali posneti konci za vaše žice. Večina naših projektov oblikovanja žice ima minimalne ali ničelne stroške orodja. Vzorčni časi obdelave so običajno dnevi. Spremembe oblikovanja/konfiguracije žičnih oblik je mogoče narediti zelo hitro. • OBLIKOVANJE VZMETI: AGS-TECH proizvaja široko paleto vzmeti, vključno z: - Torzijska / dvojna torzijska vzmet - Natezna / kompresijska vzmet -Konstantna / spremenljiva vzmet - Vijačna in vijačna vzmet -Ravna in listnata vzmet -Ravnotežna vzmet - Pralni stroj Belleville -Negatorska pomlad - Vijačna vzmet s progresivno stopnjo -Valovna pomlad - Volute Spring -Koničaste vzmeti -Vzmetni prstani -Clock Springs -Sponke Izdelujemo vzmeti iz različnih materialov in vas lahko vodimo glede na vašo uporabo. Najpogostejši materiali so nerjavno jeklo, krom silicij, visokoogljično jeklo, nizkoogljično kaljeno jeklo, krom vanadij, fosforjev bron, titan, berilijeva bakrova zlitina, visokotemperaturna keramika. Pri izdelavi vzmeti uporabljamo različne tehnike, vključno s CNC navijanjem, hladnim navijanjem, vročim navijanjem, kaljenjem, dodelavo. Druge tehnike, ki so že omenjene zgoraj pod oblikovanjem žice, so prav tako pogoste v naših postopkih izdelave vzmeti. • ZAKLJUČNE STORITVE ŽIC IN VZMETI: Vaše izdelke lahko dokončamo na več načinov, odvisno od vaše izbire in potreb. Nekaj pogostih postopkov, ki jih ponujamo, je: barvanje, prašno lakiranje, galvanizacija, potapljanje v vinil, eloksiranje, razbremenitev, toplotna obdelava, peen, vrtanje, kromatiranje, brezelektrični nikelj, pasivacija, pečen emajl, plastična prevleka , čiščenje s plazmo. CLICK Product Finder-Locator Service PREJŠNJA STRAN
- Forging and Powdered Metallurgy, Die Forging, Heading, Hot Forging
Forging and Powdered Metallurgy, Die Forging, Heading, Hot Forging, Impression Die, Near Net Shape, Swaging, Metal Hobbing, Riveting, Coining from AGS-TECH Inc. Kovanje kovin in praškasta metalurgija Vrste postopkov KOVANJA KOVIN, ki jih ponujamo, so vroče in hladno matrico, odprta matrica in zaprta matrica, odkovki z odtisi in odkovki brez vžiga, cogging, polnjenje, robljenje in natančno kovanje, skoraj neto oblika, naslov , valjčenje, kovanje z zasukom, rezkanje kovin, stiskanje in valjanje ter radialno in orbitalno ter obročasto in izotermično kovanje, kovanje, kovičenje, kovanje s kovinsko kroglo, prebadanje kovine, dimenzioniranje, kovanje z visoko energijsko hitrostjo. Naše tehnike PRAŠNE METALURGIJE in PREDELAVE PRAŠKA so stiskanje in sintranje prahu, impregnacija, infiltracija, vroče in hladno izostatično stiskanje, brizganje kovin, stiskanje v valjih, valjanje prahu, ekstrudiranje prahu, sintranje v razsutem stanju, sintranje z iskro, vroče stiskanje. Priporočamo, da kliknete tukaj PRENESITE naše shematske ilustracije postopkov kovanja podjetja AGS-TECH Inc. PRENESITE naše shematske ilustracije procesov metalurgije prahu podjetja AGS-TECH Inc. Te prenosljive datoteke s fotografijami in skicami vam bodo pomagale bolje razumeti informacije, ki vam jih posredujemo spodaj. Pri kovanju kovin delujejo tlačne sile in material se deformira ter dobi želeno obliko. Najpogostejši kovani materiali v industriji so železo in jeklo, vendar so tudi številni drugi, kot so aluminij, baker, titan, magnezij. Kovani kovinski deli imajo poleg zatesnjenih razpok in zaprtih praznih prostorov izboljšano zrnato strukturo, zato je trdnost s tem postopkom pridobljenih delov večja. Kovanje proizvaja dele, ki so znatno močnejši glede na svojo težo kot deli, izdelani z ulivanjem ali strojno obdelavo. Ker so kovani deli oblikovani tako, da kovina teče v svojo končno obliko, kovina prevzame usmerjeno zrnato strukturo, ki je odgovorna za vrhunsko trdnost delov. Z drugimi besedami, deli, pridobljeni s postopkom kovanja, kažejo boljše mehanske lastnosti v primerjavi s preprostimi ulitimi ali strojno obdelanimi deli. Teža kovinskih odkovkov se lahko giblje od majhnih lahkih delov do več sto tisoč funtov. Izdelujemo odkovke večinoma za mehansko zahtevne aplikacije, kjer so dele, kot so avtomobilski deli, zobniki, delovna orodja, ročna orodja, turbinske gredi, motorna kolesa, izpostavljeni visokim obremenitvam. Ker so stroški orodja in nastavitev razmeroma visoki, priporočamo ta proizvodni postopek le za velikoserijsko proizvodnjo in za kritične komponente majhnega obsega, vendar visoke vrednosti, kot je podvozje za letalstvo. Poleg stroškov orodja so lahko proizvodni časi za velike količine kovanih delov daljši v primerjavi z nekaterimi preprostimi strojno obdelanimi deli, vendar je tehnika ključnega pomena za dele, ki zahtevajo izjemno trdnost, kot so vijaki, matice, posebna uporaba pritrdilni elementi, deli za avtomobile, viličarje, žerjave. • KOVANJE VROČEGA in HLADNEGA KOVANJA: Vroče kovanje, kot pove ime, se izvaja pri visokih temperaturah, zato je duktilnost visoka in trdnost materiala nizka. To omogoča enostavno deformacijo in kovanje. Nasprotno, hladno kovanje se izvaja pri nižjih temperaturah in zahteva višje sile, kar povzroči deformacijsko utrjevanje, boljšo površinsko obdelavo in natančnost izdelanih delov. • KOVANJE Z ODPRTIM MATRU in VTISKANJEM: Pri kovanju z odprtim kovanjem matrice ne omejujejo stisnjenega materiala, medtem ko pri kovanju z vtiskovalnim kovanjem votline v matricah omejujejo pretok materiala, medtem ko se kuje v želeno obliko. UPSET FORGING ali imenovan tudi UPSETTING, ki pravzaprav ni enak, ampak zelo podoben postopek, je postopek odprtega matrice, pri katerem je obdelovanec stisnjen med dve ploščati matrici in tlačna sila zmanjša njegovo višino. Ko je višina reduced, se širina obdelovanca poveča. HEADING, postopek kovanega valja, ki vključuje valjast material, ki je na svojem koncu upregnjen, njegov presek pa se lokalno poveča. V poglavju se material dovaja skozi matrico, kuje in nato razreže na dolžino. Operacija je sposobna hitro proizvesti velike količine pritrdilnih elementov. Večinoma gre za postopek hladne obdelave, ker se uporablja za izdelavo koncev žebljev, koncev vijakov, matic in vijakov, kjer je treba material utrditi. Drug postopek odprte matrice je COGGING, kjer se obdelovanec kuje v nizu korakov, pri čemer vsak korak povzroči stiskanje materiala in posledično gibanje odprte matrice po dolžini obdelovanca. Na vsakem koraku se debelina zmanjša in dolžina poveča za majhno količino. Postopek spominja na živčnega študenta, ki z majhnimi koraki ves čas grize svoj svinčnik. Postopek, imenovan FULLERING, je še ena odprta metoda kovanja, ki jo pogosto uporabljamo kot zgodnejši korak za porazdelitev materiala v obdelovancu, preden se izvedejo drugi postopki kovanja kovin. Uporabljamo ga, ko obdelovanec zahteva več forging operacij. Med delovanjem se matrica s konveksnimi površinami deformira in povzroči iztekanje kovine na obe strani. Podoben postopek kot polnjenje, EDGING na drugi strani vključuje odprto matrico s konkavnimi površinami za deformacijo obdelovanca. Robljenje je tudi pripravljalni postopek za nadaljnje operacije kovanja, zaradi česar material teče z obeh strani v območje v sredini. IMPRESSION DIE FORGING ali CLOSED DIE FORGING, kot ga tudi imenujemo, uporablja matrico/kalup, ki stisne material in omejuje njegov tok v sebi. Matrica se zapre in material prevzame obliko votline kalupa/kalupa. PRECIZNO KOVANJE, postopek, ki zahteva posebno opremo in kalup, izdeluje dele brez ali z zelo malo bliskavice. Z drugimi besedami, deli bodo imeli skoraj končne dimenzije. V tem procesu se dobro nadzorovana količina materiala previdno vstavi in postavi v kalup. To metodo uporabljamo za kompleksne oblike s tankimi deli, majhnimi tolerancami in koti ugreza ter ko so količine dovolj velike, da upravičijo stroške kalupa in opreme. • KOVANJE BREZ PLOŠČE: Obdelovanec je nameščen v matrico tako, da noben material ne more iztekati iz votline, da bi oblikoval plast. Neželeno obrezovanje bliskavice torej ni potrebno. To je natančen postopek kovanja in zato zahteva natančno kontrolo količine uporabljenega materiala. • VALJANJE KOVINE ali RADIALNO KOVANJE: Na obdelovanec obodno deluje matrica in se kuje. Za kovanje notranje geometrije obdelovanca se lahko uporabi tudi trn. Pri operaciji stiskanja obdelovanec običajno prejme več gibov na sekundo. Tipični predmeti, izdelani s stiskanjem, so orodja s koničasto konico, stožčaste palice, izvijači. • PREBIJANJE KOVIN: To operacijo pogosto uporabljamo kot dodatno operacijo pri izdelavi delov. Luknja ali votlina se ustvari s prebadanjem na površini obdelovanca, ne da bi jo prebili. Upoštevajte, da se prebadanje razlikuje od vrtanja, ki ima za posledico skoznjo luknjo. • REZKANJE: Prebijač z želeno geometrijo se vtisne v obdelovanec in ustvari votlino želene oblike. Temu luknjaču rečemo HOB. Operacija vključuje visoke pritiske in se izvaja pri mrazu. Posledično je material hladno obdelan in deformacijsko utrjen. Zato je ta postopek zelo primeren za izdelavo kalupov, kalupov in votlin za druge proizvodne procese. Ko je kuhalna plošča izdelana, je mogoče preprosto izdelati veliko enakih votlin, ne da bi jih bilo treba obdelati eno za drugo. • KOVANJE V VALJU ali OBLIKOVANJE V VALJU: Za oblikovanje kovinskega dela se uporabljata dva nasproti ležeča valja. Obdelovanec se dovaja v zvitke, zvitki se obrnejo in potegnejo obdelovanec v režo, obdelovanec se nato dovaja skozi utorni del zvitkov in tlačne sile dajo materialu želeno obliko. Ne gre za postopek valjanja, ampak za postopek kovanja, ker gre za diskretno in ne kontinuirano operacijo. Geometrija na valjih nasadih kuje material v zahtevano obliko in geometrijo. Izvaja se vroče. Ker gre za postopek kovanja, proizvaja dele z izjemnimi mehanskimi lastnostmi, zato ga uporabljamo za proizvodnjo avtomobilskih delov, kot so gredi, ki morajo imeti izjemno vzdržljivost v težkih delovnih okoljih. • ORBITALNO KOVANJE: obdelovanec se postavi v votlino kovaške matrice in kuje zgornja matrica, ki potuje po orbitalni poti, ko se vrti okoli nagnjene osi. Z vsakim vrtljajem zgornja matrica preneha izvajati tlačne sile na celoten obdelovanec. Z večkratnim ponavljanjem teh vrtljajev se opravi zadostno kovanje. Prednosti te proizvodne tehnike so nizek hrup in nižje potrebne sile. Z drugimi besedami, z majhnimi silami lahko vrtimo težko matrico okoli osi, da izvajamo velike pritiske na del obdelovanca, ki je v stiku z matrico. Deli v obliki diska ali stožčaste oblike so včasih primerni za ta postopek. • KOVANJE PRSTANOV : Pogosto uporabljamo za izdelavo brezšivnih prstanov. Zaloga je razrezana na dolžino, raztegnjena in nato preluknjana do konca, da se ustvari osrednja luknja. Nato se namesti na trn in kovaška matrica ga udari od zgoraj, medtem ko se obroč počasi vrti, dokler ne dosežemo želenih dimenzij. • KOVIČENJE: Običajen postopek za spajanje delov se začne z ravnim kovinskim kosom, ki se vstavi v predhodno narejene luknje skozi dele. Nato sta dva konca kovinskega kosa kovana s stiskanjem spoja med zgornjo in spodnjo matrico. • KOVANJE: Še en priljubljen postopek, ki se izvaja z mehansko stiskalnico, ki izvaja velike sile na kratki razdalji. Ime "kovanec" izhaja iz drobnih detajlov, ki so vkovani na površine kovinskih kovancev. Večinoma gre za postopek končne obdelave izdelka, pri katerem nastanejo drobni detajli na površinah kot posledica velike sile, ki jo izvaja matrica, ki te detajle prenese na obdelovanec. • KOVANJE KOVINSKIH KROG: Izdelki, kot so kroglični ležaji, zahtevajo visokokakovostne natančno izdelane kovinske krogle. Pri eni tehniki, imenovani SKEW ROLLING, uporabljamo dva nasprotna valja, ki se nenehno vrtita, medtem ko se material neprekinjeno dovaja v zvitke. Na enem koncu obeh zvitkov se kovinske krogle izvržejo kot izdelek. Druga metoda za kovanje s kovinsko kroglo je uporaba matrice, ki stisne zalogo materiala, ki je nameščena med njimi, tako da prevzame sferično obliko votline kalupa. Proizvedene žoge pogosto zahtevajo nekaj dodatnih korakov, kot sta končna obdelava in poliranje, da postanejo visokokakovosten izdelek. • IZOTERMIČNO KOVANJE / VROČE KOVANJE: drag postopek, ki se izvaja le, če je vrednost koristi / stroškov upravičena. Postopek vroče obdelave, pri katerem se matrica segreje na približno enako temperaturo kot obdelovanec. Ker imata matrica in obdelovanec približno enako temperaturo, ni hlajenja in lastnosti pretoka kovine so izboljšane. Operacija je primerna za super zlitine in materiale s slabšo kovljivostjo ter materiale, katerih mehanske lastnosti so zelo občutljive na majhne temperaturne gradiente in spremembe. • VELIKOST KOVINE: Je postopek hladne končne obdelave. Tok materiala je neomejen v vseh smereh, razen v smeri delovanja sile. Rezultat je zelo dobra površinska obdelava in natančne dimenzije. • KOVANJE Z VISOKO ENERGIJSKO STOPNJO: Tehnika vključuje zgornji kalup, pritrjen na roko bata, ki se hitro potisne, ko se mešanica goriva in zraka vžge z vžigalno svečko. Podobno je delovanju batov v avtomobilskem motorju. Kalup zelo hitro udari ob obdelovanec in se nato zaradi protitlaka zelo hitro vrne v prvotni položaj. Delo je skovano v nekaj milisekundah in zato ni časa, da bi se delo ohladilo. To je uporabno za dele, ki jih je težko kovati in imajo temperaturno zelo občutljive mehanske lastnosti. Z drugimi besedami, proces je tako hiter, da se del oblikuje pri konstantni temperaturi vseskozi in da na vmesnikih kalupa/obdelovanca ne bo temperaturnih gradientov. • Pri KOVANJU KOVANJA je kovina udarjena med dvema ujemajočima se jeklenima blokoma s posebnimi oblikami v njih, imenovanimi matrice. Ko kovino zabijemo med matrice, zavzame enako obliko kot oblike v matrici. Ko doseže končno obliko, ga vzamemo ven, da se ohladi. Ta postopek proizvaja močne dele, ki so natančne oblike, vendar zahteva večjo naložbo za specializirane matrice. Ukrivljeno kovanje poveča premer kosa kovine tako, da ga splošči. Običajno se uporablja za izdelavo majhnih delov, zlasti za oblikovanje glav na pritrdilnih elementih, kot so sorniki in žeblji. • PRAŠNA METALURGIJA / PREDELAVA PRAHA: Kot že ime pove, vključuje proizvodne postopke za izdelavo trdnih delov določenih geometrij in oblik iz prahu. Če se za ta namen uporabljajo kovinski prahovi, je to področje prašne metalurgije, če se uporabljajo nekovinski prahovi, pa je to področje obdelave prahov. Trdni deli so izdelani iz praškov s stiskanjem in sintranjem. STISKANJE PRAHOV se uporablja za stiskanje prahov v želene oblike. Prvič, primarni material fizično uprašimo in ga razdelimo na številne majhne posamezne delce. Mešanica prahu se napolni v matrico in udarec se premika proti prahu in ga stisne v želeno obliko. Večinoma se izvaja pri sobni temperaturi, s stiskanjem prahu dobimo trden del in ga imenujemo zeleni kompakt. Veziva in maziva se običajno uporabljajo za izboljšanje kompaktnosti. Sposobni smo preoblikovati prah s pomočjo hidravličnih stiskalnic z več tisoč ton zmogljivosti. Imamo tudi stiskalnice z dvojnim delovanjem z nasprotnimi zgornjimi in spodnjimi luknjači ter stiskalnice z več delovanjem za zelo zapletene geometrije delov. Enotnost, ki je pomemben izziv za številne obrate za metalurgijo prahu / predelavo prahu, za AGS-TECH ni velik problem zaradi naših dolgoletnih obsežnih izkušenj pri izdelavi takih delov po meri. Tudi pri debelejših delih, kjer enotnost predstavlja izziv, nam je uspelo. Če se zavežemo vašemu projektu, bomo izdelali vaše dele. Če opazimo morebitna tveganja, vas bomo obvestili in vnaprej. SINTRANJE PRAHA, ki je drugi korak, vključuje dvig temperature na določeno stopnjo in vzdrževanje temperature na tej ravni določen čas, da se delci prahu v stisnjenem delu lahko povežejo. Posledica tega so veliko močnejše vezi in ojačitev obdelovanca. Sintranje poteka blizu temperature taljenja prahu. Med sintranjem pride do krčenja, poveča se trdnost materiala, gostota, duktilnost, toplotna prevodnost, električna prevodnost. Imamo šaržne in kontinuirne peči za sintranje. Ena izmed naših zmožnosti je prilagajanje stopnje poroznosti delov, ki jih izdelujemo. Na primer, lahko izdelamo kovinske filtre tako, da ohranimo dele do neke mere porozne. S tehniko, imenovano IMPREGNACIJA, zapolnimo pore v kovini s tekočino, kot je olje. Izdelujemo na primer ležaje, impregnirane z oljem, ki so samomazalni. V procesu INFILTRACIJE zapolnimo pore kovine z drugo kovino z nižjim tališčem od osnovnega materiala. Zmes se segreje na temperaturo med tališčima obeh kovin. Posledično je mogoče pridobiti nekatere posebne lastnosti. Pogosto izvajamo tudi sekundarne postopke, kot sta strojna obdelava in kovanje na delih, izdelanih v prahu, kadar je treba pridobiti posebne značilnosti ali lastnosti ali ko je del mogoče izdelati z manj procesnimi koraki. IZOSTATIČNO STISKANJE: V tem procesu se tlak tekočine uporablja za stiskanje dela. Kovinski praški so postavljeni v kalup, izdelan iz zaprte fleksibilne posode. Pri izostatičnem stiskanju se pritisk izvaja od vsepovsod, v nasprotju z aksialnim pritiskom, ki ga opazimo pri običajnem stiskanju. Prednosti izostatičnega stiskanja so enakomerna gostota znotraj dela, predvsem pri večjih ali debelejših delih, vrhunske lastnosti. Njegova slabost so dolgi časi ciklov in relativno nizka geometrijska natančnost. HLADNO IZOSTATIČNO STISKANJE se izvaja pri sobni temperaturi, upogljivi kalup pa je izdelan iz gume, PVC ali uretana ali podobnih materialov. Tekočina, ki se uporablja za tlačenje in stiskanje, je olje ali voda. Temu sledi konvencionalno sintranje zelene zgoščenke. VROČE IZOSTATIČNO STISKANJE pa se izvaja pri visokih temperaturah, material kalupa pa je pločevina ali keramika z dovolj visokim tališčem, ki je odporno na temperature. Tlačna tekočina je običajno inertni plin. Postopek stiskanja in sintranja poteka v enem koraku. Poroznost je skoraj popolnoma odpravljena, pridobljena je enotna zrnata struktura. Prednost vročega izostatičnega stiskanja je, da lahko izdela dele, ki so primerljivi z ulivanjem in kovanjem, hkrati pa omogoča uporabo materialov, ki niso primerni za ulivanje in kovanje. Pomanjkljivost vročega izostatičnega stiskanja je dolg čas cikla in s tem cena. Primeren je za kritične dele majhne količine. BRIZANJE KOVIN: Zelo primeren postopek za izdelavo kompleksnih delov s tankimi stenami in podrobno geometrijo. Najbolj primeren za manjše dele. Praške in polimerno vezivo zmešamo, segrejemo in vbrizgamo v kalup. Polimerno vezivo prekrije površine delcev prahu. Po oblikovanju se vezivo odstrani bodisi s segrevanjem pri nizki temperaturi ali raztopljeno s topilom. KOMPAKCIJA V VALJU / VALJANJE PRAHA: Praški se uporabljajo za izdelavo neprekinjenih trakov ali listov. Prah se dovaja iz podajalnika in stisne z dvema vrtečima se valjema v pločevino ali trakove. Operacija se izvaja hladno. Pločevina se prenese v peč za sintranje. Postopek sintranja se lahko ponovi še drugič. EKSTRUDIJA PRAHA: Deli z velikim razmerjem med dolžino in premerom so izdelani z ekstrudiranjem posode iz tanke pločevine s prahom. RAZHAPLJENO SINTRANJE: Kot že ime pove, je to metoda stiskanja in sintranja brez tlaka, primerna za izdelavo zelo poroznih delov, kot so kovinski filtri. Prah se dovaja v votlino kalupa brez stiskanja. RAZHAPLJENO SINTRANJE: Kot že ime pove, je to metoda stiskanja in sintranja brez tlaka, primerna za izdelavo zelo poroznih delov, kot so kovinski filtri. Prah se dovaja v votlino kalupa brez stiskanja. ISKRIČNO SINTRANJE: Prah se v kalupu stisne z dvema nasprotnima udarcem, na udarec pa se uporabi močan električni tok, ki prehaja skozi stisnjen prah, stisnjen med njima. Visok tok sežge površinske filme z delcev prahu in jih sintra z ustvarjeno toploto. Postopek je hiter, ker se toplota ne dovaja od zunaj, temveč se proizvaja znotraj kalupa. VROČE STISKANJE: praški se stisnejo in sintrajo v enem samem koraku v kalupu, ki lahko prenese visoke temperature. Ko se matrica stisne, se nanjo dovaja toplota prahu. Zaradi dobre natančnosti in mehanskih lastnosti, ki jih doseže ta metoda, je privlačna možnost. Tudi ognjevzdržne kovine je mogoče obdelati z uporabo materialov za kalupe, kot je grafit. CLICK Product Finder-Locator Service PREJŠNJI MENI
- Sheet Metal Forming Fabrication, Stamping, Punching, Deep Drawing, CNC
Sheet Metal Forming and Fabrication, Stamping, Punching, Bending, Progressive Die, Spot Welding, Deep Drawing, Metal Blanking and Slitting at AGS-TECH Inc. Štancanje in izdelava pločevine Nudimo vtiskovanje pločevine, oblikovanje, preoblikovanje, upogibanje, izsekavanje, rezanje, rezanje, perforiranje, zarezovanje, grizljanje, britje, stiskanje, izdelavo, globoko vlečenje z uporabo matric z enim prebijanjem/enim udarcem, kot tudi progresivne matrice in predenje, oblikovanje gume in hidroformiranje; razrez pločevine z vodnim curkom, plazmo, laserjem, žago, plamenom; montaža pločevine z varjenjem, točkovno varjenje; izbočenje in krivljenje pločevinastih cevi; končna obdelava pločevine, vključno z barvanjem s potapljanjem ali pršenjem, elektrostatičnim praškastim premazom, eloksiranjem, galvanizacijo, brizganjem in več. Naše storitve segajo od hitre izdelave prototipov iz pločevine do proizvodnje velikih količin. Priporočamo, da kliknete tukajPRENESITE naše shematske ilustracije izdelave pločevine in postopkov žigosanja podjetja AGS-TECH Inc. To vam bo pomagalo bolje razumeti informacije, ki vam jih posredujemo spodaj. • RAZREZ PLOČEVINE : Nudimo ODREZE in ODREZBE. Odrezki režejo pločevino po eni poti naenkrat in v bistvu ni izgube materiala, medtem ko se pri odrezkih oblike ne da natančno ugnezditi in zato pride do določene količine materiala. Eden naših najbolj priljubljenih postopkov je PREBANJE, kjer iz pločevine izrežemo kos materiala okrogle ali druge oblike. Kos, ki je izrezan, je odpadek. Druga različica luknjanja je ŽELEZANJE, kjer se luknjajo pravokotne ali podolgovate luknje. Po drugi strani pa je BLANKING enak postopek kot luknjanje, pri čemer je razlika v tem, da je izrezan kos delo in se ohrani. FINE BLANKING, vrhunska različica rezanja, ustvarja reze s tesnimi tolerancami in ravnimi gladkimi robovi ter ne zahteva sekundarnih operacij za popolnost obdelovanca. Drug postopek, ki ga pogosto uporabljamo, je REZANJE, ki je postopek striženja, pri katerem pločevino režeta dve nasprotni krožni rezili po ravni ali ukrivljeni poti. Odpirač za pločevinke je preprost primer postopka rezanja. Še en priljubljen proces pri nas je LUKANJE, kjer se v pločevino preluknja veliko lukenj okrogle ali druge oblike po določenem vzorcu. Tipičen primer perforiranega izdelka so kovinski filtri z veliko luknjami za tekočine. Pri ZAREZANJU, drugem postopku rezanja pločevine, odstranjujemo material z obdelovanca, začenši na robu ali drugje in režemo navznoter, dokler ne dobimo želene oblike. To je progresiven proces, pri katerem se z vsako operacijo odstrani še en kos, dokler ni dosežena želena kontura. Pri majhnih proizvodnih serijah včasih uporabljamo razmeroma počasnejši postopek, imenovan NIBBLING, ki je sestavljen iz številnih hitrih prebijanj prekrivajočih se lukenj, da naredimo večji, bolj zapleten rez. Pri PROGRESIVNEM REZANJU uporabljamo vrsto različnih operacij, da dobimo en rez ali določeno geometrijo. Končno BRITJE sekundarni postopek nam pomaga izboljšati robove že narejenih ureznin. Uporablja se za rezanje ostružkov, grobih robov na pločevini. • KRIVLJENJE PLOČEVINE : Upogibanje je poleg rezanja bistven proces, brez katerega ne bi mogli izdelati večine izdelkov. Večinoma gre za hladno obdelavo, včasih pa tudi v toplem ali vročem stanju. Za to operacijo največkrat uporabljamo matrice in stiskalnico. Pri PROGRESIVNEM KRIVLJENJU uporabljamo niz različnih operacij prebijanja in matrice, da dobimo en sam upogib ali določeno geometrijo. AGS-TECH uporablja različne postopke upogibanja in izbira glede na material obdelovanca, njegovo velikost, debelino, želeno velikost upogiba, polmer, ukrivljenost in kot upogiba, mesto upogibanja, ekonomičnost delovanja, količine za izdelavo… itd. Upogibamo V-UPOGILJANJE, kjer luknjač v obliki črke V potisne pločevino v matrico v obliki črke V in jo upogne. Primerno tako za zelo ostre kot tupe kote in vmesne kote, vključno z 90 stopinjami. Z brisalnimi matricami izvajamo KRIVANJE ROBOV. Naša oprema nam omogoča pridobivanje kotov tudi večjih od 90 stopinj. Pri krivljenju robov je obdelovanec stisnjen med tlačno blazinico in matrico, območje za upogibanje se nahaja na robu matrice, preostali del obdelovanca pa drži nad space kot konzolni nosilec. Ko udarec deluje na konzolni del, se upogne čez rob matrice. PRIROBLJENJE je postopek krivljenja robov, ki povzroči kot 90 stopinj. Glavni cilji operacije so odprava ostrih robov in pridobitev geometrijskih površin za lažje spajanje delov. BEADING, drug pogost postopek upogibanja robov oblikuje zvitek čez rob dela. OBROB na drugi strani povzroči rob pločevine, ki je popolnoma upognjen vase. Pri ŠIVANJU sta robova dveh delov upognjena drug na drugega in spojena. DVOJNI ŠIVI pa zagotavljajo vodotesne in zrakotesne spoje pločevine. Podobno kot pri upogibanju robov se pri postopku, imenovanem ROTACIJSKO UPOGILJANJE, postavi valj z izrezanim želenim kotom, ki služi kot udarec. Ko se sila prenese na udarec, se zapre z obdelovancem. Utor valja daje konzolnemu delu želeni kot. Utor ima lahko kot manjši ali večji od 90 stopinj. Pri ZRAČNEM KRIVLJENJU ni potrebno, da ima spodnja matrica poševni utor. Pločevina je podprta z dvema površinama na nasprotnih straneh in na določeni razdalji. Izbijač nato uporabi silo na pravem mestu in upogne obdelovanec. KANALNO KRIVLJENJE se izvaja z uporabo kanalastega luknjača in matrice, U-KRIVANJE pa se doseže z udarcem v obliki črke U. OFSET BENDING izdela zamike na pločevini. ROLL BENDING, tehnika, primerna za debela dela in krivljenje velikih kosov kovinskih plošč, uporablja tri valje za podajanje in upogibanje plošč do želenih ukrivljenosti. Zvitki so razporejeni tako, da dobimo želeno krivino dela. Razdalja in kot med zvitki sta nadzorovana, da se doseže želeni rezultat. Premični valj omogoča nadzor ukrivljenosti. OBLIKOVANJE CEVI je še en priljubljen postopek krivljenja pločevine, ki vključuje več matric. Cevi so pridobljene po več dejanjih. VALOVANJE se izvaja tudi z operacijami upogibanja. V bistvu gre za simetrično upogibanje v enakomernih intervalih čez celoten kos pločevine. Za valovitost lahko uporabite različne oblike. Valovita pločevina je bolj toga in ima boljšo odpornost proti upogibanju in se zato uporablja v gradbeništvu. OBLIKOVANJE PLOČEVINE V VALJIH, neprekinjen proizvodni postopek se uporablja za upogibanje prečnih prerezov določene geometrije z uporabo valjev in delo se upogne v zaporednih korakih, pri čemer končni zvitek dokonča delo. V nekaterih primerih se uporabi en zvitek, v nekaterih primerih pa več zvitkov. • KOMBINIRANI POSTOPKI REZANJA IN KRIVLJENJA PLOČEVINE: To so postopki, ki režejo in krivijo hkrati. Pri PIERCINGU se luknja ustvari s koničastim luknjačem. Ko luknjač razširi luknjo v plošči, se material hkrati upogne v notranjo prirobnico za luknjo. Dobljena prirobnica ima lahko pomembne funkcije. Operacija LANCING na drugi strani reže in upogne list, da ustvari dvignjeno geometrijo. • IZBOLČENJE IN UPOGIB KOVINSKE CEVI: Pri IZBOLČEVANJU je v nekaterih notranjih delih votle cevi pritisk, zaradi česar se cev izboči navzven. Ker je cev znotraj matrice, je geometrija izbokline nadzorovana z obliko matrice. Pri RAZTEZNEM UPOGIBANJU je kovinska cev raztegnjena z uporabo sil, vzporednih z osjo cevi, in upogibnih sil, da se cev potegne čez oblikovni blok. Pri DRAW BENDING vpnemo cev blizu njenega konca na vrteči se blok, ki med vrtenjem upogne cev. Nazadnje, pri STISKANJEM UPOGIBANJE je cev s silo držana na bloku fiksne oblike, matrica pa jo upogne čez blok oblike. • GLOBOKI VLEK: V eni izmed naših najbolj priljubljenih operacij se uporabljajo luknjač, ujemajoča se matrica in prazno držalo. Pločevinast surovec se položi čez odprtino matrice in udarec se premakne proti surovcu, ki ga drži držalo surovca. Ko pridejo v stik, udarec potisne pločevino v votlino matrice, da se oblikuje izdelek. Postopek globokega vlečenja je podoben rezanju, vendar razdalja med luknjačem in matrico preprečuje rezanje pločevine. Še en dejavnik, ki zagotavlja, da je pločevina globoko vlečena in ne rezana, so zaobljeni vogali na matrici in luknjaču, ki preprečujejo striženje in rezanje. Da bi dosegli večji obseg globokega vlečenja, se uporablja postopek PONOVNEGA RISANJA, pri katerem se naknadno globoko vlečenje izvaja na delu, ki je že bil podvržen postopku globokega vlečenja. Pri REVERSE REDRAWING se globoko narisan del obrne in nariše v nasprotni smeri. Globoko vlečenje lahko zagotovi predmete nepravilnih oblik, kot so kupolaste, stožčaste ali stopničaste skodelice, Pri VTISKOVANJU uporabljamo par moških in ženskih matric, da na pločevino vtisnemo vzorec ali pisavo. • SPINNING : Postopek, pri katerem se ploski ali predoblikovani obdelovanec drži med vrtljivim trnom in zadnjim delom, orodje pa izvaja lokalni pritisk na delo, ko se postopoma premika navzgor po trnu. Posledično se obdelovanec ovije preko trna in zavzame svojo obliko. To tehniko uporabljamo kot alternativo globokemu vleku, kjer je količina naročila majhna, deli so veliki (premeri do 20 čevljev) in imajo edinstvene krivulje. Čeprav so cene na kos na splošno višje, so stroški nastavitve CNC predenja nizki v primerjavi z globokim vlekom. Nasprotno, globoko vlečenje zahteva visoko začetno naložbo za nastavitev, vendar so stroški na kos nizki, če se proizvede velika količina delov. Druga različica tega postopka je STRIŽNO PREDENJE, kjer je tudi tok kovine znotraj obdelovanca. Tok kovine bo med izvajanjem postopka zmanjšal debelino obdelovanca. Še en soroden postopek je PREDENJE CEVI, ki se uporablja na cilindričnih delih. Tudi v tem procesu pride do toka kovine znotraj obdelovanca. Tako se zmanjša debelina in poveča dolžina cevi. Orodje je mogoče premakniti, da ustvarite funkcije na notranji ali zunanji strani cevi. • GUMASTO OBLIKOVANJE PLOČEVINE: Guma ali poliuretanski material se vstavi v posodico in obdelovanec se položi na površino gume. Nato udarec deluje na obdelovanec in ga potisne v gumo. Ker je tlak, ki ga ustvarja guma, nizek, je globina izdelanih delov omejena. Ker so stroški orodja nizki, je postopek primeren za proizvodnjo majhnih količin. • HIDROFORMIRANJE: Podobno kot pri oblikovanju gume se v tem procesu pločevina stisne z udarcem v tekočino pod pritiskom znotraj komore. Pločevina je stisnjena med luknjač in gumijasto membrano. Membrana popolnoma obdaja obdelovanec in pritisk tekočine ga prisili, da se oblikuje na udarec. S to tehniko je mogoče doseči zelo globoke vrise, še globlje kot pri procesu globokega vleka. Izdelujemo matrice z enim udarcem in progresivne matrice, odvisno od vašega dela. Matrice za vtiskovanje z enim udarcem so stroškovno učinkovita metoda za hitro izdelavo velikih količin preprostih pločevinastih delov, kot so podložke. Progresivne matrice ali tehnika globokega vlečenja se uporabljajo za izdelavo kompleksnejših geometrij. Odvisno od vašega primera lahko za poceni, hitro in natančno izdelavo pločevinastih delov uporabite vodni curek, laser ali plazemsko rezanje. Številni dobavitelji nimajo pojma o teh alternativnih tehnikah ali pa jih nimajo, zato se lotevajo dolgotrajnih in dragih načinov izdelave matric in orodij, ki strankam samo zapravljajo čas in denar. Če potrebujete po meri izdelane komponente iz pločevine, kot so ohišja, elektronska ohišja ... itd., kar hitro v nekaj dneh, se obrnite na nas za našo storitev HITRO PROTOTIPIRANJE PLOČEVINE. CLICK Product Finder-Locator Service PREJŠNJI MENI
- Plastic Rubber Metal Extrusions, Extrusion Dies, Aluminum Extruding
Plastic Rubber Metal Extrusions, Extrusion Dies, Aluminum Extruding, Pipe Tube Forming, Plastic Profiles, Metal Profiles Manufacturing, PVC at AGS-TECH Inc. Ekstrudiranje, ekstrudirani izdelki, ekstrudati Uporabljamo proces EXTRUSION process za izdelavo izdelkov s fiksnim profilom preseka, kot so cevi, cevi in hladilna telesa. Čeprav je mogoče iztisniti veliko materialov, so naši najpogostejši iztiski iz kovine, polimerov/plastike, keramike, pridobljeni z metodo hladnega, toplega ali vročega iztiskanja. Ekstrudirane dele imenujemo ekstrudat ali ekstrudati v množini. Nekatere specializirane različice postopka, ki jih tudi izvajamo, so prevleka, koekstruzija in sestavljena ekstruzija. Priporočamo, da kliknete tukaj na PRENESITE naše shematske ilustracije postopkov iztiskanja kovinske keramike in plastike podjetja AGS-TECH Inc. To vam bo pomagalo bolje razumeti informacije, ki vam jih posredujemo spodaj. Pri iztiskanju se material za ekstrudiranje potisne ali vleče skozi matrico, ki ima želeni profil prečnega prereza. Postopek se lahko uporablja za izdelavo kompleksnih prerezov z odlično površinsko obdelavo in za obdelavo krhkega materiala. S tem postopkom lahko izdelamo dele poljubne dolžine. Za poenostavitev korakov postopka: 1.) Pri toplem ali vročem iztiskanju se material segreje in naloži v posodo v stiskalnici. Material se stisne in potisne iz matrice. 2.) Izdelani ekstrudat je raztegnjen za ravnanje, toplotno obdelan ali hladno obdelan za izboljšanje njegovih lastnosti. Po drugi strani COLD EXTRUSION poteka pri približno sobni temperaturi in ima prednosti manjše oksidacije, visoke trdnosti, manjših toleranc, dobrega zaključka površine in obstojnosti. WARM EXTRUSION se izvaja nad sobno temperaturo, vendar pod rekristalizacijsko točko. Ponuja kompromis in ravnotežje za zahtevane sile, duktilnost in lastnosti materiala, zato je izbira za nekatere aplikacije. HOT EXTRUSION poteka nad temperaturo rekristalizacije materiala. Na ta način je lažje potisniti material skozi matrico. Vendar so stroški opreme visoki. Bolj kompleksen kot je ekstrudirani profil, dražja je matrica (orodje) in nižja je stopnja proizvodnje. Prečni prerezi in debeline imajo omejitve, ki so odvisne od materiala, ki ga je treba iztisniti. Ostri vogali ekstruzijskih matric so vedno nezaželeni in se jim je treba izogibati, razen če so potrebni. Glede na material, ki se ekstrudira, nudimo: • KOVINSKI IZTISKI : Najpogostejši izdelki, ki jih izdelujemo, so aluminij, medenina, cink, baker, jeklo, titan, magnezij • PLASTIC EXTRUSION : Plastika se stopi in oblikuje v neprekinjen profil. Naši običajni materiali, ki jih obdelujemo, so polietilen, najlon, polistiren, polivinilklorid, polipropilen, ABS plastika, polikarbonat, akril. Tipični izdelki, ki jih izdelujemo, vključujejo cevi in plastične okvirje. V procesu se majhne plastične kroglice/smola gravitacijsko dovajajo iz lijaka v sod ekstruzijskega stroja. Pogosto v lijak vmešamo tudi barvila ali druge dodatke, da damo izdelku zahtevane specifikacije in lastnosti. Material, ki vstopa v ogrevan sod, je zaradi vrtljivega vijaka prisiljen, da zapusti sod na koncu in se premakne skozi sito za odstranitev kontaminantov v staljeni plastiki. Po prehodu sita plastika vstopi v ekstruzijsko matrico. Matrica daje premikajoči se mehki plastiki obliko profila, ko gre skozi. Zdaj gre ekstrudat skozi vodno kopel za hlajenje. Druge tehnike, ki jih AGS-TECH Inc. uporablja že vrsto let, so: • PIPE & TUBING EXTRUSION : Plastične cevi se oblikujejo, ko je plastika ekstrudirana skozi okroglo oblikovno matrico in ohlajena v vodni kopeli, nato razrezana na dolžino ali zvita/navita. Prozorni ali barvni, črtasti, z eno ali dvema stenama, fleksibilni ali togi, PE, PP, poliuretan, PVC, najlon, PC, silikon, vinil ali drugo, imamo vse. Imamo založene cevi in zmožnost izdelave po vaših specifikacijah. AGS-TECH proizvaja cevi v skladu z zahtevami FDA, UL in LE za medicinske, električne in elektronske, industrijske in druge aplikacije. • PREKROVNI PLAŠČ / PREKO PLAŠČA EXTRUSION : Ta tehnika nanese zunanjo plast plastike na obstoječo žico ali kabel. Naše izolacijske žice so izdelane s to metodo. • COEXTRUSION : Več plasti materiala se ekstrudira hkrati. Več plasti se dostavi z več ekstruderji. Različne debeline plasti je mogoče prilagoditi zahtevam kupca. Ta postopek omogoča uporabo več polimerov, od katerih ima vsak drugačno funkcionalnost v izdelku. Posledično je mogoče optimizirati vrsto lastnosti. • EKSTRUDIJA SPOJINE: Posamezen ali več polimerov se zmeša z dodatki, da dobimo plastično zmes. Naši ekstruderji z dvojnim polžem proizvajajo mešane ekstruzije. Ekstruzijske matrice so na splošno poceni v primerjavi s kovinskimi kalupi. Če plačujete veliko več kot nekaj tisoč dolarjev za majhno ali srednje veliko ekstruzijsko matrico za ekstrudiranje aluminija, verjetno plačujete preveč. Smo strokovnjaki za določanje, katera tehnika je stroškovno najučinkovitejša, najhitrejša in najprimernejša za vašo aplikacijo. Včasih lahko z ekstrudiranjem in nato strojno obdelavo dela prihranite veliko denarja. Preden se trdno odločite, nas najprej vprašajte za naše mnenje. Številnim strankam smo pomagali sprejeti prave odločitve. Za nekatere široko uporabljene kovinske ekstruzije lahko prenesete naše brošure in kataloge s klikom na spodnje barvno besedilo. Če gre za standardni izdelek, ki ustreza vašim zahtevam, bo bolj ekonomičen. Prenesite naše zmogljivosti za iztiskanje medicinskih cevi Prenesite naše ekstrudirane hladilnike • SEKUNDARNI PROIZVODNI IN PROCESI IZDELAVE ZA EKSTRUZIJE : Med postopki z dodano vrednostjo, ki jih ponujamo za ekstrudirane izdelke, so: - Upogibanje, oblikovanje in oblikovanje cevi po meri, rezanje cevi, oblikovanje koncev cevi, zvijanje cevi, strojna obdelava in končna obdelava, vrtanje lukenj, prebadanje in prebijanje, -Sklopi cevi po meri, sestavljanje cevi, varjenje, trdo spajkanje in spajkanje - Krivljenje, oblikovanje in oblikovanje po meri - Čiščenje, razmaščevanje, luženje, pasiviranje, poliranje, eloksiranje, galvanizacija, barvanje, toplotna obdelava, žarjenje in kaljenje, označevanje, graviranje in etiketiranje, pakiranje po meri. CLICK Product Finder-Locator Service PREJŠNJA STRAN
- Casting and Machined Parts, CNC Manufacturing, Milling, Turning, Swiss
Casting and Machined Parts, CNC Manufacturing, Milling, Turning, Swiss Type Machining, Die Casting, Investment Casting, Lost Foam Cast Parts from AGS-TECH Inc. Ulivanje in strojna obdelava Naše tehnike litja in strojne obdelave po meri so odlitki za potrošni in nepotrošni material, železni in neželezni ulitki, pesek, tlačno litje, centrifugalni, kontinuirani, keramični kalupi, vložek, izgubljena pena, skoraj mrežaste oblike, trajni kalupi (gravitacijsko tlačno litje), mavec kalupi (mavčni ulitki) in lupinasti ulitki, strojno obdelani deli, izdelani z rezkanjem in struženjem z uporabo konvencionalne in CNC opreme, švicarska obdelava za visoko zmogljive poceni majhne natančne dele, obdelava vijakov za pritrdilne elemente, nekonvencionalna obdelava. Upoštevajte, da poleg kovin in kovinskih zlitin obdelujemo tudi keramične, steklene in plastične komponente v nekaterih primerih, ko izdelava kalupa ni zanimiva ali ni možnost. Strojna obdelava polimernih materialov zahteva specializirane izkušnje, ki jih imamo zaradi izziva, ki ga predstavljata plastika in guma zaradi svoje mehkobe, netrdosti itd. Za strojno obdelavo keramike in stekla si oglejte našo stran o nekonvencionalni izdelavi. AGS-TECH Inc. proizvaja in dobavlja lahke in težke ulitke. Dobavljamo kovinske ulitke in strojno obdelane dele za kotle, toplotne izmenjevalnike, avtomobile, mikromotorje, vetrne turbine, opremo za pakiranje hrane in drugo. Priporočamo, da kliknete tukaj na PRENESITE naše shematske ilustracije procesov obdelave in litja podjetja AGS-TECH Inc. To vam bo pomagalo bolje razumeti informacije, ki vam jih posredujemo spodaj. Oglejmo si podrobneje nekatere izmed različnih tehnik, ki jih ponujamo: • POTROŠNI ULITKI V KALUP: Ta široka kategorija se nanaša na metode, ki vključujejo začasne kalupe za enkratno uporabo. Primeri so pesek, mavec, školjka, vložek (imenovan tudi izgubljeni vosek) in mavčni ulitek. • ULITJE V PESEK: postopek, pri katerem se pesek uporablja kot material za kalupe. Zelo stara metoda in še vedno zelo priljubljena do te mere, da je večina proizvedenih kovinskih ulitkov izdelanih s to tehniko. Nizki stroški tudi pri majhni količini proizvodnje. Primerno za izdelavo majhnih in velikih delov. Tehniko je mogoče uporabiti za izdelavo delov v nekaj dneh ali tednih z zelo malo naložbe. Vlažen pesek se poveže z glino, vezivi ali posebnimi olji. Pesek se običajno nahaja v kalupnih škatlah, sistem votlin in vrat pa se ustvari s stiskanjem peska okoli modelov. Postopki so: 1.) Postavitev modela v pesek za izdelavo kalupa 2.) Vključitev modela in peska v zaporni sistem 3.) Odstranitev modela 4.) Polnjenje kalupne votline s staljeno kovino 5.) Hlajenje kovine 6.) Razbijanje peščenega kalupa in odstranitev odlitka • ODLIVANJE MAVCNIH KALUPOV: Podobno litju v pesek, namesto peska pa se kot material za kalupe uporablja pariški mavec. Kratki proizvodni časi, kot je ulivanje v pesek, in poceni. Dobre dimenzijske tolerance in površinska obdelava. Njegova glavna pomanjkljivost je, da se lahko uporablja samo s kovinami z nizkim tališčem, kot sta aluminij in cink. • LITJE V KALUP: Podobno tudi litju v pesek. Kalupna votlina, pridobljena z utrjeno lupino iz peska in veziva iz termoreaktivne smole, namesto bučke, napolnjene s peskom, kot pri postopku litja v pesek. Skoraj vsako kovino, ki je primerna za ulivanje s peskom, je mogoče uliti z lupinastim oblikovanjem. Postopek lahko povzamemo kot: 1.) Izdelava lupine. Uporabljeni pesek ima veliko manjšo velikost zrn v primerjavi s peskom, ki se uporablja pri litju v pesek. Drobni pesek se zmeša s termoreaktivno smolo. Kovinski vzorec je prevlečen z ločilnim sredstvom za lažje odstranjevanje lupine. Nato se kovinski vzorec segreje in mešanica peska se pore ali vpiha na vroč vzorec za ulivanje. Na površini vzorca se oblikuje tanka lupina. Debelino te lupine je mogoče prilagoditi s spreminjanjem dolžine časa, ko je mešanica peščene smole v stiku s kovinskim vzorcem. Razsuti pesek se nato odstrani, pri čemer ostane vzorec, prekrit s školjko. 2.) Nato lupino in vzorec segrejemo v pečici, da se lupina strdi. Po končanem strjevanju se lupina izvrže iz vzorca s pomočjo zatičev, ki so vgrajeni v vzorec. 3.) Dve taki lupini sta sestavljeni skupaj z lepljenjem ali vpenjanjem in sestavljata celoten kalup. Zdaj je kalup za lupino vstavljen v posodo, v kateri je med postopkom ulivanja podprt s peskom ali kovinskimi drobci. 4.) Sedaj lahko vročo kovino vlijemo v kalup. Prednosti lupinastega litja so izdelki z zelo dobro površinsko obdelavo, možnost izdelave kompleksnih delov z visoko dimenzijsko natančnostjo, proces je enostaven za avtomatizacijo, ekonomičen za velikoserijsko proizvodnjo. Slabosti so, da kalupi zahtevajo dobro prezračevanje zaradi plinov, ki nastanejo, ko staljena kovina pride v stik z vezivno kemikalijo, termoreaktivne smole in kovinski vzorci so dragi. Zaradi stroškov kovinskih vzorcev tehnika morda ne bo primerna za majhne količine proizvodnje. • LITJE ZA VLAKANJE (znano tudi kot LITJE IZ IZGUBLJENEGA VOSKA): Prav tako zelo stara tehnika in primerna za izdelavo kakovostnih delov z visoko natančnostjo, ponovljivostjo, vsestranskostjo in celovitostjo iz številnih kovin, ognjevzdržnih materialov in posebnih visoko zmogljivih zlitin. Izdelujejo se lahko tako majhni kot tudi veliki deli. Drag postopek v primerjavi z nekaterimi drugimi metodami, vendar je glavna prednost možnost izdelave delov skoraj neto oblike, zapletenih kontur in detajlov. Tako se stroški nekoliko izravnajo z odpravo predelave in strojne obdelave v nekaterih primerih. Čeprav lahko obstajajo različice, je tukaj povzetek splošnega postopka vlitja: 1.) Izdelava originalnega glavnega vzorca iz voska ali plastike. Vsak odlitek potrebuje en vzorec, saj se ti med postopkom uničijo. Potreben je tudi kalup, iz katerega se izdelujejo vzorci in večinoma je kalup ulit ali strojno obdelan. Ker kalupa ni treba odpreti, je mogoče doseči kompleksne ulitke, številne voščene vzorce je mogoče povezati kot veje drevesa in zliti skupaj ter tako omogočiti izdelavo več delov iz enega samega ulitka kovine ali kovinske zlitine. 2.) Nato se vzorec potopi ali prelije z ognjevarno brozgo, sestavljeno iz zelo drobnozrnatega silicijevega dioksida, vode in veziva. Posledica tega je keramična plast na površini vzorca. Ognjevarni premaz na vzorcu pustimo, da se posuši in strdi. Iz tega koraka izvira ime vložni ulitek: ognjevzdržna brozga se vloži čez vzorec voska. 3.) Pri tem koraku strjeni keramični kalup obrnemo na glavo in ga segrejemo, da se vosek stopi in izlije iz kalupa. Ostala je votlina za kovinski odlitek. 4.) Ko je vosek izpuščen, se keramični kalup segreje na še višjo temperaturo, kar povzroči ojačitev kalupa. 5.) Kovinski odlitek se vlije v vroč kalup in zapolni vse zapletene dele. 6.) Pustimo, da se ulitek strdi 7.) Končno se keramični kalup razbije in izdelani deli se izrežejo z drevesa. Tukaj je povezava do brošure o obratu za investicijsko litje • ULITJE IZHAPELNEGA VZORCA: Postopek uporablja vzorec iz materiala, kot je polistirenska pena, ki izhlapi, ko se vroča staljena kovina vlije v kalup. Obstajata dve vrsti tega postopka: LITJE IZ IZGUBLJENE PENE, pri katerem se uporablja nevezan pesek, in POLNO ULITJE, pri katerem se uporablja vezan pesek. Tukaj so splošni koraki postopka: 1.) Izdelajte vzorec iz materiala, kot je polistiren. Ko bodo izdelane velike količine, se vzorec oblikuje. Če ima del zapleteno obliko, bo morda treba zlepiti več delov takega penastega materiala, da se oblikuje vzorec. Vzorec pogosto premažemo z ognjevzdržno zmesjo, da ustvarimo dobro površinsko obdelavo ulitka. 2.) Vzorec nato damo v kalupni pesek. 3.) Staljena kovina se vlije v kalup, pri čemer izhlapi penasti vzorec, tj. polistiren v večini primerov, ko teče skozi votlino kalupa. 4.) Staljeno kovino pustimo v peščenem kalupu, da se strdi. 5.) Ko se strdi, odlitek odstranimo. V nekaterih primerih izdelek, ki ga izdelujemo, zahteva jedro znotraj vzorca. Pri litju z izhlapevanjem ni treba namestiti in pritrditi jedra v votlino kalupa. Tehnika je primerna za izdelavo zelo kompleksnih geometrij, jo je mogoče enostavno avtomatizirati za velikoserijsko proizvodnjo, v ulitem delu pa ni ločilnih linij. Osnovni postopek je preprost in ekonomičen za izvedbo. Ker je za izdelavo vzorcev iz polistirena potrebna matrica ali kalup, je to lahko pri proizvodnji velikih količin nekoliko drago. • ULITKE IZ NERAZŠIRNEGA KALUPA: Ta široka kategorija se nanaša na metode, pri katerih kalupa ni treba preoblikovati po vsakem proizvodnem ciklu. Primeri so trajno, tlačno, kontinuirano in centrifugalno litje. Dosežena je ponovljivost in deli se lahko označijo kot SKOZI NETO OBLIKE. • TRAJNO ULITJE V KALUP: Kalupi za večkratno uporabo iz kovine se uporabljajo za večkratne ulitke. Trajni kalup je na splošno mogoče uporabiti več deset tisočkrat, preden se obrabi. Za polnjenje kalupa se običajno uporabljajo gravitacija, tlak plina ali vakuum. Kalupi (imenovani tudi kalupi) so na splošno izdelani iz železa, jekla, keramike ali drugih kovin. Splošni postopek je: 1.) Strojno obdelajte in ustvarite kalup. Običajno je obdelati kalup iz dveh kovinskih blokov, ki se prilegata skupaj in ju je mogoče odpirati in zapirati. Tako deli kot tudi sistem vrat so na splošno obdelani v livarski kalup. 2.) Notranje površine kalupa so prevlečene z zmesjo, ki vsebuje ognjevzdržne materiale. To pomaga nadzorovati pretok toplote in deluje kot mazivo za enostavno odstranitev ulitega dela. 3.) Nato se trajne polovice kalupa zaprejo in kalup segreje. 4.) Staljeno kovino vlijemo v kalup in pustimo, da se strdi. 5.) Preden se močno ohladi, odstranimo del iz trajnega kalupa z uporabo ejektorjev, ko se polovice kalupa odprejo. Pogosto uporabljamo trajno litje v kalupe za kovine z nizkim tališčem, kot sta cink in aluminij. Za jeklene ulitke uporabljamo grafit kot kalupni material. Včasih dobimo zapletene geometrije z uporabo jeder v trajnih kalupih. Prednosti te tehnike so ulitki z dobrimi mehanskimi lastnostmi, pridobljenimi s hitrim ohlajanjem, enakomernost lastnosti, dobra natančnost in končna obdelava površine, nizka stopnja zavrženja, možnost avtomatizacije procesa in ekonomična proizvodnja velikih količin. Pomanjkljivosti so visoki začetni stroški namestitve, zaradi česar ni primeren za operacije z majhnim obsegom, in omejitve glede velikosti izdelanih delov. • TLAČNO LITJE: Matrica je strojno obdelana in staljena kovina se pod visokim pritiskom potisne v votline kalupa. Možni so tlačni ulitki iz neželeznih in železnih kovin. Postopek je primeren za velike količine proizvodnih serij majhnih do srednje velikih delov z detajli, izjemno tankimi stenami, dimenzijsko doslednostjo in dobro površinsko obdelavo. AGS-TECH Inc. je sposoben izdelati stene debeline do 0,5 mm s to tehniko. Kot pri trajnem litju v kalup mora biti kalup sestavljen iz dveh polovic, ki se lahko odpirata in zapirata za odstranitev proizvedenega dela. Kalup za tlačno litje ima lahko več votlin, da omogoči proizvodnjo več ulitkov v vsakem ciklu. Kalupi za tlačno litje so zelo težki in veliko večji od delov, ki jih proizvajajo, zato tudi dragi. Našim strankam brezplačno popravimo in zamenjamo obrabljene matrice, če pri nas znova naročijo svoje dele. Naše matrice imajo dolgo življenjsko dobo v razponu nekaj sto tisoč ciklov. Tukaj so osnovni poenostavljeni koraki postopka: 1.) Izdelava kalupov na splošno iz jekla 2.) Kalup, nameščen na stroju za tlačno litje 3.) Bat prisili staljeno kovino, da teče v votlinah matrice in zapolni zapletene elemente in tanke stene 4.) Po polnjenju kalupa s staljeno kovino pustimo, da se ulitek strdi pod pritiskom 5.) Kalup se odpre in ulitek odstrani s pomočjo ejektorskih zatičev. 6.) Zdaj je prazna matrica ponovno namazana in vpeta za naslednji cikel. Pri tlačnem litju pogosto uporabljamo vložek, kjer v kalup vgradimo dodaten del in okoli njega ulijemo kovino. Po strjevanju ti deli postanejo del litega izdelka. Prednosti tlačnega litja so dobre mehanske lastnosti delov, možnost zapletenih lastnosti, fini detajli in dobra površinska obdelava, visoke proizvodne stopnje, enostavna avtomatizacija. Slabosti so: Ni zelo primerno za majhne prostornine zaradi visokih stroškov matrice in opreme, omejitev oblik, ki jih je mogoče uliti, majhne okrogle sledi na ulitih delih, ki so posledica stika izmetalnih zatičev, tanek kovinski odtis, iztisnjen na ločilni črti, potreba za zračnike vzdolž ločilne črte med matrico je treba vzdrževati nizke temperature kalupa z uporabo kroženja vode. • CENTRIFUGALNO LITJE: Staljena kovina se vlije v sredino vrtljivega kalupa na osi vrtenja. Centrifugalne sile vržejo kovino proti obrobju in pustijo, da se strdi, ko se kalup še naprej vrti. Uporabite lahko tako vodoravno kot navpično rotacijo osi. Ulivamo lahko dele z okroglo notranjo površino in druge neokrogle oblike. Postopek lahko povzamemo kot: 1.) Staljeno kovino vlijemo v centrifugalni kalup. Kovina se nato zaradi vrtenja kalupa potisne na zunanje stene. 2.) Ko se kalup vrti, se kovinski odlitek strdi Centrifugalno litje je primerna tehnika za proizvodnjo votlih cilindričnih delov, kot so cevi, ni potrebe po ulivih, dvižnih vodih in zapornih elementih, dobra površinska obdelava in podrobne lastnosti, brez težav s krčenjem, možnost izdelave dolgih cevi z zelo velikimi premeri, zmogljivost visoke hitrosti proizvodnje . • KONTINUIRNO LITJE (STRAND CASTING): Uporablja se za ulivanje neprekinjene dolžine kovine. V bistvu se staljena kovina vlije v dvodimenzionalni profil kalupa, vendar je njena dolžina nedoločena. Nova staljena kovina se nenehno dovaja v kalup, ko ulitek potuje navzdol, njegova dolžina pa se s časom povečuje. Kovine, kot so baker, jeklo, aluminij, se vlijejo v dolge pramene s postopkom kontinuiranega litja. Postopek ima lahko različne konfiguracije, vendar je skupno mogoče poenostaviti kot: 1.) Staljena kovina se vlije v posodo, ki se nahaja visoko nad kalupom, pri dobro izračunanih količinah in hitrostih pretoka ter teče skozi vodno hlajen kalup. Kovinski ulitek, vlit v kalup, se strdi v začetno palico, nameščeno na dnu kalupa. Ta začetna palica daje valjem nekaj, za kar se na začetku oprimejo. 2.) Dolgo kovinsko nit prenašajo valji s konstantno hitrostjo. Valji tudi spreminjajo smer toka kovinskega pramena iz navpične v vodoravno. 3.) Ko kontinuirni ulitek prepotuje določeno vodoravno razdaljo, ga gorilnik ali žaga, ki se premika z ulitkom, hitro razreže na želene dolžine. Postopek kontinuirnega litja je mogoče integrirati s POSTOPKOM VALJANJA, kjer je mogoče neprekinjeno lito kovino dovajati neposredno v valjarno za izdelavo I-nosilcev, T-nosilcev ... itd. Kontinuirano litje zagotavlja enotne lastnosti celotnega izdelka, ima visoko stopnjo strjevanja, zmanjšuje stroške zaradi zelo nizke izgube materiala, ponuja postopek, pri katerem nalaganje kovine, vlivanje, strjevanje, rezanje in odstranjevanje ulitkov potekajo v neprekinjenem delovanju in kar ima za posledico visoko stopnjo produktivnosti in visoko kakovost. Pomemben dejavnik pa so visoka začetna naložba, stroški postavitve in prostorske zahteve. • STORITVE STROJNE OBDELAVE: Nudimo tri, štiri in petosno obdelavo. Vrste obdelovalnih procesov, ki jih uporabljamo, so STRUGENJE, REZKANJE, VRTANJE, SVRTANJE, PREBIRANJE, SKOBLJANJE, ŽAGANJE, BRUŠENJE, LEPANJE, POLIRANJE in NETRADICIONALNA STROJNA OBDELAVA, ki je podrobneje opisana v drugem meniju na naši spletni strani. Za večino naše proizvodnje uporabljamo CNC stroje. Vendar pa so za nekatere operacije običajne tehnike bolj primerne, zato se zanašamo tudi nanje. Naše zmogljivosti strojne obdelave dosegajo najvišjo možno raven in nekateri najzahtevnejši deli so izdelani v tovarni s certifikatom AS9100. Rezila reaktivnih motorjev zahtevajo visoko specializirane proizvodne izkušnje in ustrezno opremo. Letalska industrija ima zelo stroge standarde. Nekatere komponente s kompleksno geometrijsko strukturo je najlažje izdelati s petosno obdelavo, ki jo najdemo le v nekaterih obdelovalnih obratih, vključno z našim. Naša certificirana tovarna za vesoljsko industrijo ima potrebne izkušnje za izpolnjevanje obsežnih dokumentacijskih zahtev letalske in vesoljske industrije. Pri operacijah STRUŽENJA se obdelovanec vrti in premika proti rezalnemu orodju. Za ta postopek se uporablja stroj, imenovan stružnica. Pri REZKANJU ima stroj, imenovan rezkalni stroj, vrteče se orodje, s katerim se rezalni robovi prilegajo obdelovancu. VRTANJE vključuje vrtljivi rezkar z rezalnimi robovi, ki ob stiku z obdelovancem naredi luknje. Običajno se uporabljajo vrtalne stiskalnice, stružnice ali rezkarji. Pri vrtanju se orodje z eno samo upognjeno koničasto konico premakne v grobo luknjo v vrtečem se obdelovancu, da rahlo poveča luknjo in izboljša natančnost. Uporablja se za fino končno obdelavo. VIGANJE vključuje zobato orodje za odstranjevanje materiala z obdelovanca v enem prehodu vlečenja (zobčano orodje). Pri linearnem vlečenju vlečenje teče linearno proti površini obdelovanca, da povzroči rez, medtem ko se pri rotacijskem vlečenju vlečenje zavrti in pritisne v obdelovanec, da izreže osno simetrično obliko. SWISS TYPE MACHINING je ena od naših dragocenih tehnik, ki jih uporabljamo za velikoserijsko proizvodnjo majhnih visoko natančnih delov. S stružnico švicarskega tipa poceni stružimo majhne, kompleksne, natančne dele. Za razliko od običajnih stružnic, kjer obdelovanec miruje in se orodje premika, se lahko v stružnih centrih švicarskega tipa obdelovanec premika v osi Z, orodje pa miruje. Pri obdelavi švicarskega tipa se palica zadrži v stroju in napreduje skozi vodilno pušo v osi z, pri čemer je izpostavljen samo del, ki ga je treba obdelati. Tako je zagotovljen tesen oprijem in visoka natančnost. Razpoložljivost aktivnih orodij omogoča rezkanje in vrtanje, ko material napreduje od vodilne puše. Y-os opreme švicarskega tipa zagotavlja polne zmogljivosti rezkanja in prihrani veliko časa pri proizvodnji. Poleg tega imajo naši stroji svedre in vrtalna orodja, ki delujejo na delu, ko ga držijo v pomožnem vretenu. Naša zmogljivost obdelave švicarskega tipa nam daje popolnoma avtomatizirano popolno možnost obdelave v eni sami operaciji. Strojna obdelava je eden največjih segmentov poslovanja AGS-TECH Inc. Uporabljamo ga bodisi kot primarno operacijo bodisi kot sekundarno operacijo po litju ali ekstrudiranju dela, tako da so izpolnjene vse specifikacije risb. • STORITVE ZAKLJUČNE POVRŠINE: Nudimo široko paleto površinskih obdelav in končne obdelave površin, kot je kondicioniranje površine za izboljšanje oprijema, nanašanje tanke oksidne plasti za izboljšanje oprijema premaza, peskanje, kemični film, eloksiranje, nitriranje, prašno lakiranje, lakiranje z brizganjem , različne napredne tehnike metalizacije in prevleke, vključno z naprševanjem, elektronskim žarkom, izhlapevanjem, prevleko, trdimi prevlekami, kot je diamantu podoben ogljik (DLC) ali prevleka iz titana za orodja za vrtanje in rezanje. • STORITVE OZNAČEVANJA IN OZNAČEVANJA IZDELKOV: veliko naših strank potrebuje označevanje in etiketiranje, lasersko označevanje, graviranje na kovinske dele. Če imate takšno potrebo, se pogovorimo o tem, katera možnost bi bila najboljša za vas. Tukaj je nekaj pogosto uporabljenih kovinskih litih izdelkov. Ker so že pripravljeni, lahko prihranite pri stroških kalupov, če kateri koli od teh ustreza vašim zahtevam: KLIKNITE TUKAJ ZA PRENOS naših 11 serij škatel iz tlačno litega aluminija iz AGS-Electronics CLICK Product Finder-Locator Service PREJŠNJA STRAN
- Custom Manufactured Parts, Assemblies, Plastic Mold, Casting,Machining
Custom Manufactured Parts, Assemblies, Plastic Mold, Rubber Molding, Metal Casting, CNC Machining, Turning, Milling, Electrical Electronic Optical Assembly PCBA Deli, sklopi in izdelki po meri izdelani Preberi več Plastični in gumijasti kalupi in vlivanje Preberi več Ulivanje in strojna obdelava Preberi več Ekstrudiranje, ekstrudirani izdelki Preberi več Štancanje in izdelava pločevine Preberi več Kovanje kovin in praškasta metalurgija Preberi več Oblikovanje žice in vzmeti Preberi več Oblikovanje stekla in keramike Preberi več Dodatna in hitra proizvodnja Preberi več Kompoziti in proizvodnja kompozitnih materialov Preberi več Postopki spajanja, sestavljanja in pritrjevanja Za vas izdelujemo dele in sklope ter ponujamo naslednje proizvodne procese: • Plastični in gumijasti kalupi ter oblikovani deli. Brizganje, toplotno oblikovanje, duroplastno oblikovanje, vakuumsko oblikovanje, pihanje, rotacijsko oblikovanje, vlivanje, vstavljanje in drugo. • Ekstruzije iz plastike, gume in kovine • Železni in neželezni ulitki ter strojno obdelani deli, izdelani s tehnikami rezkanja in struženja, švicarska strojna obdelava. • Deli za prašno metalurgijo • Štancanje kovin in nekovin, preoblikovanje pločevine, varjeni sklopi pločevine • Hladno in vroče kovanje • Žice, sklopi varjene žice, preoblikovanje žice • Različne vrste vzmeti, oblikovanje vzmeti • Proizvodnja zobnikov, menjalnik, sklopka, polž, reduktor hitrosti, cilinder, transmisijski jermeni, transmisijske verige, transmisijske komponente • Prilagojeno kaljeno in neprebojno steklo, skladno z NATO in vojaškimi standardi • Kroglice, ležaji, jermenice in jermenice • Ventili in pnevmatske komponente, kot so O-tesnila, podložke in tesnila • Stekleni in keramični deli in sklopi, vakuumsko neprepustne in hermetične komponente, kovinsko-keramična in keramično-keramična lepitev. • Različne vrste mehanskih, optomehanskih, elektromehanskih, optoelektronskih sklopov. • Vezava kovina-guma, kovina-plastika • Cevi, preoblikovanje cevi, krivljenje in cevni sklopi po meri, proizvodnja mehov. • Proizvodnja steklenih vlaken • Varjenje z različnimi tehnikami kot so točkovno varjenje, lasersko varjenje, MIG, TIG. Ultrazvočno varjenje plastičnih delov. • Velika izbira površinskih obdelav in končnih površin, kot je kondicioniranje površin za izboljšanje oprijema, nanašanje tanke oksidne plasti za izboljšanje oprijema premaza, peskanje, kemični film, eloksiranje, nitriranje, praškasto lakiranje, pršenje, različne napredne tehnike metalizacije in premazovanja vključno z razprševanjem, elektronskim žarkom, izhlapevanjem, galvanizacijo, trdimi prevlekami, kot je diamantu podoben ogljik (DLC) ali titan za orodja za rezanje in vrtanje. • Označevanje in etiketiranje, lasersko označevanje kovinskih delov, tisk na plastične in gumijaste dele Prenesite brošuro za splošne izraze strojništva, ki jih uporabljajo oblikovalci in inženirji Izdelke izdelujemo po vaših posebnih specifikacijah in zahtevah. Da bi vam ponudili najboljšo kakovost, dostavo in cene, proizvajamo izdelke po vsem svetu na Kitajskem, v Indiji, Tajvanu, Filipinih, Južni Koreji, Maleziji, Šrilanki, Turčiji, ZDA, Kanadi, Nemčiji, Veliki Britaniji in na Japonskem. To nas dela veliko močnejše in globalno bolj konkurenčne kot kateri koli drug custom proizvajalec. Naši izdelki so izdelani v certificiranih okoljih ISO9001:2000, QS9000, ISO14001, TS16949 in imajo oznako CE, UL ter izpolnjujejo druge industrijske standarde. Ko smo imenovani za vaš projekt, lahko po vaši želji poskrbimo za celotno proizvodnjo, montažo, testiranje, kvalifikacijo, pošiljanje in carino. Če želite, lahko skladiščimo vaše dele, sestavimo komplete po meri, natisnemo in označimo ime in blagovno znamko vašega podjetja ter pošljemo vašim strankam. Z drugimi besedami, po želji smo lahko tudi vaš skladiščni in distribucijski center. Ker se naša skladišča nahajajo v bližini večjih morskih pristanišč, nam to daje logistično prednost. Na primer, ko vaši izdelki prispejo v glavno morsko pristanišče v ZDA, jih lahko prepeljemo neposredno v bližnje skladišče, kjer jih lahko shranimo, sestavimo, izdelamo komplete, ponovno označimo, natisnemo, zapakiramo po vaši izbiri in oddamo pošiljanje vašim strankam. Ne dobavljamo le izdelkov. Naše podjetje dela na podlagi pogodb po meri, kjer pridemo na vašo spletno stran, ocenimo vaš projekt na lokaciji in razvijemo predlog projekta, prilagojen za vas. Nato pošljemo svojo izkušeno ekipo za izvedbo projekta. Več informacij o našem inženirskem delu najdete na http://www.ags-engineering.com -Sprejemamo majhne in velike projekte v industrijskem obsegu. Kot prvi korak vas lahko prek telefona, telekonference ali MSN messengerja povežemo s člani naše strokovne skupine, tako da lahko neposredno komunicirate s strokovnjakom, postavljate vprašanja in razpravljate o svojem projektu. Pokličite nas in po potrebi vas pridemo obiskat. PREJŠNJA STRAN