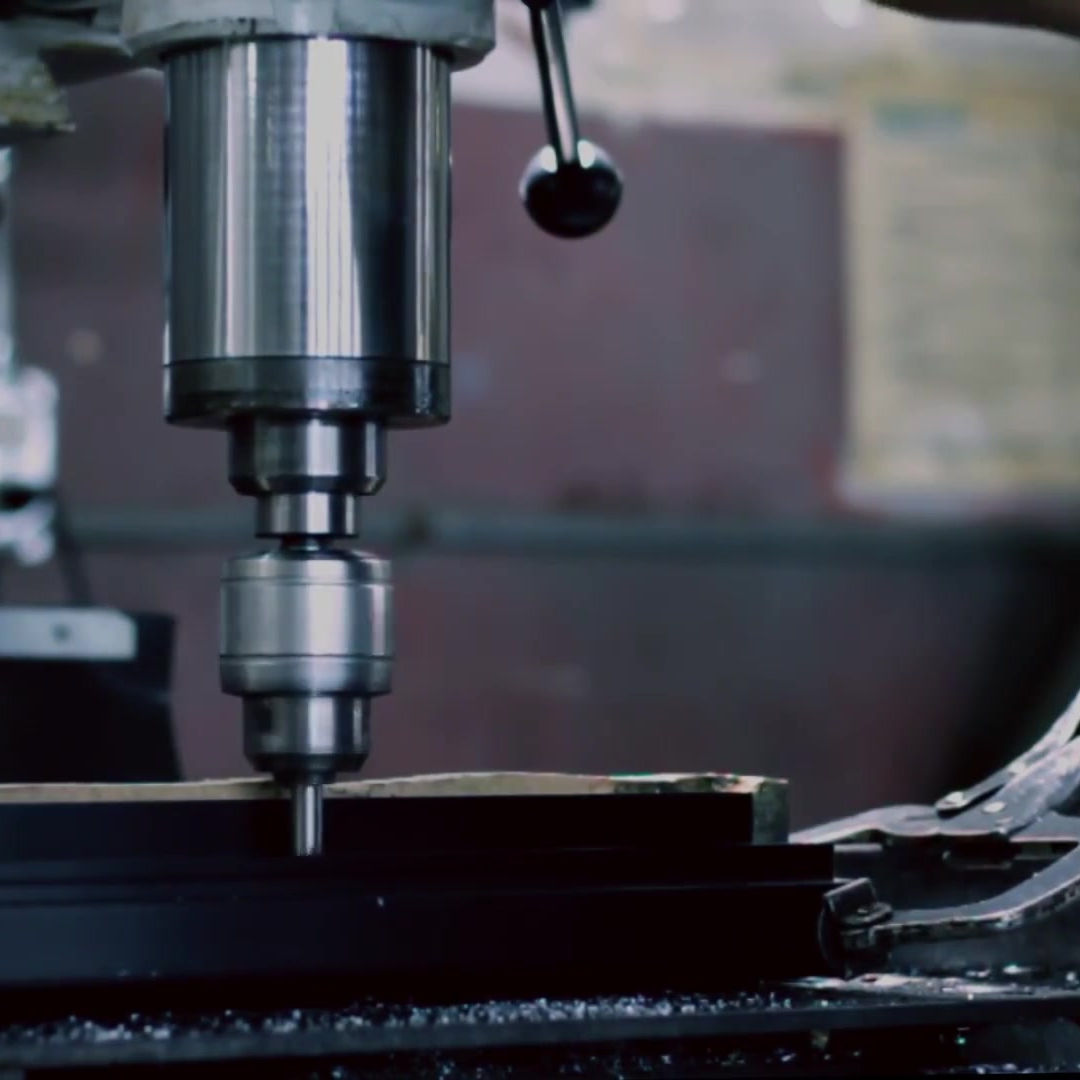
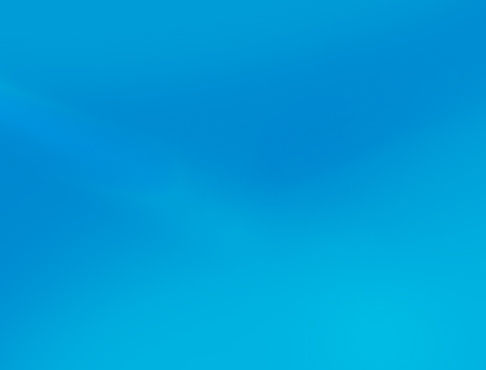
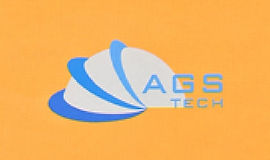
Prodhues global me porosi, integrues, konsolidues, partner kontraktues për një shumëllojshmëri të gjerë produktesh dhe shërbimesh.
Ne jemi burimi juaj i vetëm për prodhim, fabrikim, inxhinieri, konsolidim, integrim, kontraktim të jashtëm të produkteve dhe shërbimeve të prodhuara me porosi dhe jashtë raftit.
Zgjidhni gjuhën tuaj
-
Prodhim me porosi
-
Prodhim i brendshëm dhe global me kontratë
-
Prodhim i jashtëm
-
Prokurimet e Brendshme dhe Globale
-
Konsolidimi
-
Integrimi inxhinierik
-
Shërbime Inxhinierike
Search Results
164 results found with an empty search
- Transmission Components, Belts, Chains, Cable Drives, Pulleys,AGS-TECH
Transmission Components, Belts, Chains and Cable Drives, Conventional & Grooved or Serrated, Positive Drive, Pulleys Rripa dhe zinxhirë dhe montim i kabllove AGS-TECH Inc. ju ofron komponentë të transmetimit të energjisë, duke përfshirë rripat dhe zinxhirët dhe montimin e kabllove. Me vite të rafinimit, disqet tona prej gome, lëkure dhe rripa të tjerë janë bërë më të lehtë dhe më kompakt, të aftë për të mbajtur ngarkesa më të larta me kosto më të ulët. Në mënyrë të ngjashme, disqet tona zinxhirore kanë kaluar shumë zhvillim me kalimin e kohës dhe u ofrojnë klientëve tanë disa avantazhe. Disa avantazhe të përdorimit të disqeve me zinxhir janë distancat e tyre relativisht të pakufizuara në qendër të boshtit, kompaktësia, lehtësia e montimit, elasticiteti në tension pa rrëshqitje ose zvarritje, aftësia për të vepruar në mjedise me temperaturë të lartë. Disqet tona kabllore ofrojnë gjithashtu avantazhe të tilla si thjeshtësia në disa aplikacione ndaj llojeve të tjera të komponentëve të transmetimit. Janë të disponueshme si rripat jashtë raftit, disqet me zinxhir dhe kabllo, si dhe versionet e fabrikuara dhe të montuara me porosi. Ne mund t'i prodhojmë këto komponentë transmisioni në madhësinë e duhur për aplikimin tuaj dhe nga materialet më të përshtatshme. RRIPA DHE RRIPA: - Rripa të sheshtë konvencionale: Këta janë rripa të sheshtë të thjeshtë pa dhëmbë, brazda ose dhëmbëza. Drejtuesit e rripit të sheshtë ofrojnë fleksibilitet, thithje të mirë të goditjeve, transmetim efikas të energjisë me shpejtësi të lartë, rezistencë ndaj gërryerjes, kosto të ulët. Rripat mund të bashkohen ose lidhen për të bërë rripa më të mëdhenj. Përparësi të tjera të rripave të sheshtë konvencionale janë ata janë të hollë, ata nuk i nënshtrohen ngarkesave të larta centrifugale (i bën ata të mirë për operacione me shpejtësi të lartë me rrotulla të vogla). Nga ana tjetër ato imponojnë ngarkesa të larta mbajtëse sepse rripat e sheshtë kërkojnë tension të lartë. Disavantazhe të tjera të ngasjeve me rripa të sheshtë mund të jenë rrëshqitja, funksionimi i zhurmshëm dhe efikasiteti relativisht më i ulët në shpejtësi të ulët dhe të moderuar të funksionimit. Ne kemi dy lloje të rripave konvencionale: të përforcuar dhe jo të përforcuar. Rripat e përforcuar kanë një pjesë tërheqëse në strukturën e tyre. Rripat e sheshtë konvencionale janë në dispozicion si lëkure, pëlhurë ose kordon të gomuar, gome ose plastikë jo të përforcuar, pëlhurë, lëkurë të përforcuar. Rripat prej lëkure ofrojnë jetë të gjatë, fleksibilitet, koeficient të shkëlqyer të fërkimit, riparim të lehtë. Megjithatë rripat prej lëkure janë relativisht të shtrenjta, kanë nevojë për veshjen dhe pastrimin e rripave, dhe në varësi të atmosferës ato mund të tkurren ose shtrihen. Rripat e pëlhurave ose kordonit të gomuar janë rezistente ndaj lagështirës, acidit dhe alkaleve. Rripat prej pëlhure të gomuar përbëhen nga shtresa pambuku ose rosë sintetike të ngopura me gome dhe janë më ekonomiket. Rripat e kordonit të gomuar përbëhen nga një seri litarësh të ngopur me gomë. Rripat e kordonit të gomuar ofrojnë rezistencë të lartë në tërheqje dhe madhësi dhe masë modeste. Rripat e gomës ose plastikës jo të përforcuar janë të përshtatshëm për përdorime të lehta dhe me shpejtësi të ulët. Rripat e gomës dhe plastikës jo të përforcuar mund të shtrihen në vend mbi rrotullat e tyre. Rripat plastikë jo të përforcuar mund të transmetojnë fuqi më të lartë në krahasim me rripat e gomës. Rripat prej lëkure të përforcuar përbëhen nga një pjesë plastike elastike e vendosur midis shtresave të sipërme dhe të poshtme të lëkurës. Së fundi, rripat tanë prej pëlhure mund të përbëhen nga një copë e vetme pambuku ose rosë e palosur dhe e qepur me rreshta qepjesh gjatësore. Rripat prej pëlhure janë në gjendje të gjurmojnë në mënyrë të njëtrajtshme dhe të funksionojnë me shpejtësi të lartë. - Rripa me brazdë ose dhëmbëzim (të tillë si rripat V): Këto janë rripa bazë të sheshtë të modifikuar për të ofruar avantazhet e një lloji tjetër produkti të transmetimit. Këto janë rripa të sheshtë me një pjesë të poshtme me brinjë gjatësore. Rripat Poly-V janë rrip të sheshtë me brazda gjatësore ose të dhëmbëzuara me seksion tërheqës dhe një seri brazdash ngjitur në formë V për qëllime gjurmimi dhe ngjeshjeje. Kapaciteti i fuqisë varet nga gjerësia e rripit. Rripi V është kali i punës i industrisë dhe është i disponueshëm në një sërë madhësish dhe llojesh të standardizuara për transmetimin e pothuajse çdo fuqie ngarkese. Makinat e rripave V funksionojnë mirë midis 1500 dhe 6000 ft/min, megjithatë rripat e ngushtë V do të funksionojnë deri në 10,000 ft/min. Makinat me rripa V ofrojnë jetë të gjatë, si p.sh. 3 deri në 5 vjet dhe lejojnë raporte të mëdha shpejtësie, ato janë të lehta për t'u instaluar dhe hequr, ofrojnë funksionim të qetë, mirëmbajtje të ulët, thithje të mirë të goditjeve midis drejtuesit të rripit dhe boshteve të shtyrë. Disavantazhi i rripave V është rrëshqitja dhe zvarritja e tyre e sigurt dhe për këtë arsye ata mund të mos jenë zgjidhja më e mirë kur kërkohen shpejtësi sinkrone. Kemi breza industriale, automobilistike dhe bujqësore. Janë të disponueshme gjatësitë standarde të pajisura si dhe gjatësitë me porosi të rripave. Të gjitha seksionet standarde të tërthortë të rripit V janë në dispozicion në stok. Ka tabela ku mund të llogarisni parametra të panjohur si gjatësia e rripit, seksioni i rripit (gjerësia dhe trashësia) me kusht që të njihni disa parametra të sistemit tuaj si diametrat e rrotullës së lëvizjes dhe të rrotullimit, distancën qendrore midis rrotullave dhe shpejtësinë e rrotullimit të rrotullave. Ju mund të përdorni tabela të tilla ose të na kërkoni të zgjedhim rripin e duhur V-V për ju. - Rripat e drejtimit pozitiv (rripi i kohës): Këta rripa janë gjithashtu të tipit të sheshtë me një seri dhëmbësh të vendosur në mënyrë të barabartë në perimetrin e brendshëm. Rripat pozitivë të lëvizjes ose të kohës kombinojnë avantazhet e rripave të sheshtë me karakteristikat e kapjes pozitive të zinxhirëve dhe marsheve. Rripat pozitivë të lëvizjes nuk tregojnë asnjë rrëshqitje ose ndryshime në shpejtësi. Një gamë e gjerë e raporteve të shpejtësisë është e mundur. Ngarkesat mbajtëse janë të ulëta sepse mund të funksionojnë me tension të ulët. Megjithatë, ato janë më të ndjeshme ndaj shtrembërimeve në rrotulla. - Rripat, Duajet, Rripat për rripa: Lloje të ndryshme rrotullash përdoren me rripa lëvizës të sheshtë, me brinjë (të dhëmbëzuar) dhe pozitiv. Ne i prodhojmë të gjitha. Shumica e rrotullave tona të rripave të sheshta janë bërë nga derdhja e hekurit, por versionet e çelikut janë gjithashtu të disponueshme në kombinime të ndryshme buzësh dhe qendrash. Rrotullat tona me rripa të sheshtë mund të kenë qendra të forta, me fole ose të ndara ose ne mund t'i prodhojmë sipas dëshirës tuaj. Rripat me shirita dhe me lëvizje pozitive janë të disponueshme në një sërë madhësish dhe gjerësish stok. Të paktën një rrotull në ngasjet e rripit të kohës duhet të jetë me fllanxha për të mbajtur rripin në makinë. Për sistemet e lëvizjes qendrore të gjata, rekomandohet që të dy rrotullat të jenë me fllanxha. Duajet janë rrota me brazda të rrotullave dhe në përgjithësi prodhohen nga derdhja e hekurit, formimi i çelikut ose derdhja plastike. Formimi i çelikut është proces i përshtatshëm për prodhimin e duajve të automobilave dhe bujqësisë. Prodhojmë duaj me brazda të rregullta dhe të thella. Duajet me brazdë të thellë janë të përshtatshme kur rripi V futet në tufë me një kënd, siç është rasti në makinat me kthesë çerek. Brazdat e thella janë gjithashtu të përshtatshme për ngasjet me bosht vertikal dhe aplikimet ku dridhja e rripave mund të jetë problem. Rrotullat tona përtaci janë duaj me brazda ose rrotulla të sheshta që nuk shërbejnë për transmetimin e fuqisë mekanike. Rripat boshe përdoren kryesisht për shtrëngimin e rripave. - Ngasjet me rrip të vetëm dhe të shumëfishtë: Makinat me një rrip të vetëm kanë një brazdë të vetme, ndërsa disqet me rripa të shumëfishtë kanë kanale të shumta. Duke klikuar tekstin me ngjyra përkatëse më poshtë, mund të shkarkoni katalogët tanë: - Rripat e transmetimit të energjisë (përfshin rripat V-V, rripat e kohës, rripat e skajeve të papërpunuara, rripat e mbështjellë dhe rripat speciale) - Rripa transportues - Rrotullat V - Rrobat e kohës ZINXHIRËT DHE DREJTAT E ZINXIRIT: Zinxhirët tanë të transmetimit të energjisë kanë disa avantazhe të tilla si distanca relativisht të pakufizuara në qendër të boshtit, montimi i lehtë, kompaktësia, elasticiteti nën tension pa rrëshqitje ose zvarritje, aftësia e funksionimit në temperatura të larta. Këtu janë llojet kryesore të zinxhirëve tanë: - Zinxhirët e shkëputshëm: Zinxhirët tanë të shkëputshëm janë bërë në një sërë madhësish, lartësie dhe fortësie përfundimtare dhe në përgjithësi nga hekuri ose çeliku i lakueshëm. Zinxhirët e lakueshëm janë bërë në një gamë madhësish nga 0,902 (23 mm) deri në 4,063 inç (103 mm) hapësire dhe forcë përfundimtare nga 700 në 17,000 lb/inç katror. Zinxhirët tanë të çelikut të shkëputshëm nga ana tjetër janë bërë në madhësi nga 0,904 inç (23 mm) deri në rreth 3,00 inç (76 mm) në hap, me forcën përfundimtare nga 760 në 5000 lb/inç katror._cc781905-5cde-3194-bb3b- 136bad5cf58d_ - Zinxhirët pintle: Këto zinxhirë përdoren për ngarkesa më të rënda dhe shpejtësi pak më të larta në rreth 450 këmbë/min (2.2 m/sek). Zinxhirët e gjilpërave janë bërë nga lidhje individuale të derdhura që kanë fund fuçi të plotë, të rrumbullakët me shirita anësor të zhvendosur. Këto lidhje zinxhirësh janë të ndërlidhura me kunjat e çelikut. Këta zinxhirë variojnë në hap nga rreth 1,00 inç (25 mm) në 6,00 inç (150 mm) dhe fuqia përfundimtare midis 3600 dhe 30,000 lb/inç katror. - Zinxhirët Offset-Sidebar: Këto janë të njohura në zinxhirët lëvizës të makinerive të ndërtimit. Këto zinxhirë punojnë me shpejtësi deri në 1000 ft/min dhe transmetojnë ngarkesa në rreth 250 kf. Në përgjithësi, çdo lidhje ka dy shirita anësor të zhvendosur, një tufë, një rul, një gjilpërë, një gjilpërë. - Zinxhirët me rul: Ato janë të disponueshme në hapa nga 0,25 (6 mm) deri në 3,00 (75 mm) inç. Fortësia përfundimtare e zinxhirëve të rrotullës me një gjerësi të vetme varion nga 925 në 130,000 lb/inç katror. Janë të disponueshme versionet me gjerësi të shumëfishtë të zinxhirëve të rrotullave dhe transmetojnë fuqi më të madhe me shpejtësi më të larta. Zinxhirët rrotullues me gjerësi të shumëfishtë ofrojnë gjithashtu veprim më të butë me zhurmë të reduktuar. Zinxhirët e rulit janë mbledhur nga lidhjet e rulit dhe lidhjet e kunjave. Kunjat cotter përdoren në zinxhirët e rulit të versionit të ndashëm. Dizajni i disqeve të zinxhirit të rrotullës kërkon ekspertizë të subjektit. Ndërsa ngasjet e rripit bazohen në shpejtësi lineare, ngasjet e zinxhirit bazohen në shpejtësinë e rrotullimit të rrotullës më të vogël, e cila është në shumicën e instalimeve anëtari i drejtuar. Përveç vlerësimeve të kuajfuqive dhe shpejtësisë së rrotullimit, dizajni i disqeve me zinxhir bazohet në shumë faktorë të tjerë. - Zinxhirët me dy hapa: Në thelb janë të njëjta si zinxhirët me rul, përveç se hapi është dy herë më i gjatë. - Zinxhirët e dhëmbëve të përmbysur (të heshtur): Zinxhirët me shpejtësi të lartë të përdorura kryesisht për makineritë kryesore lëvizëse, me ngritje të energjisë. Drejtuesit e zinxhirit të dhëmbëve të përmbysur mund të transmetojnë fuqi deri në 1200 kf dhe përbëhen nga një seri lidhjesh dhëmbësh, të montuara në mënyrë alternative ose me kunja ose një kombinim të komponentëve të nyjeve. Zinxhiri udhëzues qendror ka lidhje udhëzuese për të futur brazdat në dhëmbëzë dhe zinxhiri i udhëzuesit anësor ka udhëzues për të kyçur anët e rrotullës. - Zinxhirët me rruaza ose rrëshqitës: Këto zinxhirë përdoren për ngasje me shpejtësi të ngadaltë dhe gjithashtu në operacione manuale. Duke klikuar tekstin me ngjyra përkatëse më poshtë, mund të shkarkoni katalogët tanë: - Zinxhirët e drejtimit - Zinxhirët transportues - Zinxhirë transportues me katran të madh - Zinxhirë me rul prej çeliku inox - Zinxhirë ngritës - Zinxhirë motoçikletash - Zinxhirët e Makinave Bujqësore - Gjurmët: Gjurmët tanë standardë përputhen me standardet ANSI. Gjurmët e pllakave janë dhëmbëza të sheshta, pa hub. Rrotullat tona të përmasave të vogla dhe të mesme janë kthyer nga stoku i shufrave ose farkëtimi ose bëhen duke salduar një shpërndarës shufrash në një pllakë të mbështjellë të nxehtë. AGS-TECH Inc. mund të furnizojë me dhëmbëza të përpunuara nga derdhjet me hekur gri, çeliku të derdhur dhe konstruksionet e qendrës së salduar, metalin pluhur të sinteruar, plastikë të derdhur ose të përpunuar. Për funksionimin e qetë me shpejtësi të lartë, është thelbësore zgjedhja e duhur e madhësisë së dhëmbëzave. Kufizimet e hapësirës janë sigurisht një faktor që nuk mund ta injorojmë kur zgjedhim një rrota. Rekomandohet që raporti i shoferit me rrotat e drejtuara të jetë jo më shumë se 6:1, dhe mbështjellja e zinxhirit në drejtues është 120 gradë. Distancat e qendrës ndërmjet dhëmbëzave më të vogla dhe më të mëdha, gjatësia e zinxhirit dhe tensioni i zinxhirit duhet gjithashtu të zgjidhen sipas disa llogaritjeve dhe udhëzimeve inxhinierike të rekomanduara dhe jo rastësisht. Shkarkoni katalogët tanë duke klikuar tekstin me ngjyra më poshtë: - Me dhëmbëza dhe rrota me pllaka - Tufat e transmisionit - Bashkim zinxhir - Brava me zinxhir MJETET E KABLLOVE: Këto kanë avantazhet e tyre ndaj rripave dhe zinxhirëve në disa raste. Disqet e kabllove mund të kryejnë të njëjtin funksion si rripat dhe gjithashtu mund të jenë më të thjeshtë dhe më ekonomik për t'u zbatuar në disa aplikacione. Për shembull, një seri e re e disqeve kabllosh Synchromesh janë projektuar për tërheqje pozitive për të zëvendësuar litarët konvencionalë, kabllot e thjeshta dhe disqet me dhëmbëza, veçanërisht në hapësira të ngushta. Disku i ri kabllor është projektuar për të siguruar pozicionim me precizion të lartë në pajisjet elektronike si makinat kopjuese, komplotuesit, makinat e shkrimit, printerët,….. etj. Një tipar kryesor i disqeve të reja kabllore është aftësia e tij për t'u përdorur në konfigurimet 3D serpentine që mundësojnë dizajne jashtëzakonisht miniaturë. Kabllot Synchromesh mund të përdoren me tension më të ulët në krahasim me litarët, duke reduktuar kështu konsumin e energjisë. Kontaktoni AGS-TECH për pyetje dhe opinione mbi rripat, zinxhirët dhe kabllot. CLICK Product Finder-Locator Service FAQJA E MEPARSHME
- Rapid Prototyping, Desktop Manufacturing, Additive Manufacturing, FDM
Rapid Prototyping, Desktop Manufacturing, Additive Manufacturing, Stereolithography, Polyjet, Fused Deposition Modeling, Selective Laser Sintering, FDM, SLS Prodhim shtesë dhe të shpejtë Vitet e fundit, kemi parë një rritje të kërkesës për PRODHIM TË SHPEJTË ose PROTOTIPIM TË SHPEJTË. Ky proces mund të quhet gjithashtu PRODHIM TASPOPIT ose FABRIKIM TË FORMAVE TË LIRA. Në thelb, një model i fortë fizik i një pjese është bërë direkt nga një vizatim tredimensional CAD. Ne përdorim termin MANUFACTURING SHTESËS për këto teknika të ndryshme ku ndërtojmë pjesë në shtresa. Duke përdorur pajisje dhe softuer të integruar të drejtuar nga kompjuteri, ne kryejmë prodhim shtesë. Teknikat tona të shpejta të prototipizimit dhe prodhimit janë STEREOLITOGRAFIA, POLYJET, MODELIMI ME DEPOZIM ME FUSHË, SINTERING SELEKTIVE me lazer, shkrirja me rreze ELEKTRONE, PRINTI TREDIMENSIONAL, PRODHIM DIREKT. Ne ju rekomandojmë që të klikoni këtu për tëSHKARKO Ilustrimet tona Skematike të Prodhimit të Aditivëve dhe Proceseve të Shpejtë të Prodhimit nga AGS-TECH Inc. Kjo do t'ju ndihmojë të kuptoni më mirë informacionin që po ju ofrojmë më poshtë. Prototipi i shpejtë na ofron: 1.) Dizajni konceptual i produktit shikohet nga këndvështrime të ndryshme në një monitor duke përdorur një sistem 3D / CAD. 2.) Prototipe nga materiale jometalike dhe metalike janë prodhuar dhe studiuar nga aspekti funksional, teknik dhe estetik. 3.) Prototipi me kosto të ulët në një kohë shumë të shkurtër është realizuar. Prodhimi i aditivëve mund t'i ngjajë ndërtimit të një copë buke duke grumbulluar dhe ngjitur feta individuale njëra mbi tjetrën. Me fjalë të tjera, produkti prodhohet fetë pas feta, ose shtresë pas shtrese depozitohet mbi njëri-tjetrin. Shumica e pjesëve mund të prodhohen brenda disa orësh. Teknika është e mirë nëse pjesët nevojiten shumë shpejt ose nëse sasitë e nevojshme janë të ulëta dhe bërja e një kallëpi dhe vegla pune është shumë e shtrenjtë dhe kërkon kohë. Megjithatë kostoja e një pjese është e shtrenjtë për shkak të lëndëve të para të shtrenjta. • STEREOLITOGRAFIA: Kjo teknikë e shkurtuar edhe si STL, bazohet në forcimin dhe forcimin e një fotopolimeri të lëngshëm në një formë specifike duke fokusuar një rreze lazer mbi të. Lazeri polimerizon fotopolimerin dhe e kuron atë. Duke skanuar rreze lazer UV sipas formës së programuar përgjatë sipërfaqes së përzierjes fotopolimerike, pjesa prodhohet nga poshtë lart në feta individuale të kaskaduara njëra mbi tjetrën. Skanimi i pikës lazer përsëritet shumë herë për të arritur gjeometritë e programuara në sistem. Pasi pjesa të jetë prodhuar plotësisht, ajo hiqet nga platforma, fshihet dhe pastrohet me ultratinguj dhe me banjë alkooli. Më pas, ai ekspozohet ndaj rrezatimit UV për disa orë për t'u siguruar që polimeri është tharë dhe ngurtësuar plotësisht. Për të përmbledhur procesin, një platformë e zhytur në një përzierje fotopolimeri dhe një rreze lazer UV kontrollohen dhe lëvizen përmes një sistemi servo-kontrolli sipas formës së pjesës së dëshiruar dhe pjesa përftohet duke fotokuruar shtresën pas shtresës së polimerit. Sigurisht që përmasat maksimale të pjesës së prodhuar përcaktohen nga pajisjet stereolitografike. • POLYJET : Ngjashëm me printimin me bojë, në polijet ne kemi tetë koka printimi që depozitojnë fotopolimer në tabaka e ndërtimit. Drita ultravjollcë e vendosur pranë avionëve shëron dhe ngurtëson menjëherë secilën shtresë. Dy materiale përdoren në polijet. Materiali i parë është për prodhimin e modelit aktual. Materiali i dytë, një rrëshirë xhel-like përdoret për mbështetje. Të dyja këto materiale depozitohen shtresë pas shtrese dhe në të njëjtën kohë kurohen. Pas përfundimit të modelit, materiali mbështetës hiqet me një tretësirë ujore. Rrëshirat e përdorura janë të ngjashme me stereolithografinë (STL). Polijeti ka këto përparësi ndaj stereolithografisë: 1.) Nuk ka nevojë për pastrim të pjesëve. 2.) Nuk ka nevojë për shërim pas procesit 3.) Trashësi më të vogla të shtresave janë të mundshme dhe kështu marrim rezolucion më të mirë dhe mund të prodhojmë pjesë më të imta. • MODELIMI I DEPOZIMEVE TË FUSEDUR: Gjithashtu i shkurtuar si FDM, në këtë metodë një kokë ekstruderi e kontrolluar nga roboti lëviz në dy drejtime parimore mbi një tabelë. Kablloja ulet dhe ngrihet sipas nevojës. Nga vrima e një koke të nxehtë në kokë, një filament termoplastik nxirret dhe një shtresë fillestare depozitohet në një themel shkumë. Kjo realizohet nga koka e ekstruderit që ndjek një rrugë të paracaktuar. Pas shtresës fillestare, tabela ulet dhe shtresat pasuese vendosen njëra mbi tjetrën. Ndonjëherë kur prodhohet një pjesë e ndërlikuar, nevojiten struktura mbështetëse në mënyrë që depozitimi të vazhdojë në drejtime të caktuara. Në këto raste, një material mbështetës ekstrudohet me një ndarje më pak të dendur të filamentit në një shtresë në mënyrë që të jetë më i dobët se materiali model. Këto struktura mbështetëse më vonë mund të shpërbëhen ose shkëputen pas përfundimit të pjesës. Dimensionet e mbulesës së ekstruderit përcaktojnë trashësinë e shtresave të ekstruduara. Procesi FDM prodhon pjesë me sipërfaqe të shkallëzuara në plane të jashtme të pjerrëta. Nëse kjo ashpërsi është e papranueshme, mund të përdoret lustrimi me avull kimik ose një mjet i nxehtë për zbutjen e tyre. Edhe një dyll lustrimi është i disponueshëm si material mbulues për të eliminuar këto hapa dhe për të arritur toleranca të arsyeshme gjeometrike. • SINTERIMI SELEKTIVE me LAZER: I shënuar gjithashtu si SLS, procesi bazohet në sinterimin e një polimeri, pluhuri qeramik ose metalik në mënyrë selektive në një objekt. Fundi i dhomës së përpunimit ka dy cilindra: një cilindër pjesërisht i ndërtuar dhe një cilindër ushqimi me pluhur. E para ulet gradualisht në vendin ku formohet pjesa e sinterizuar dhe e dyta ngrihet gradualisht për të furnizuar me pluhur cilindrin e pjesës së ndërtimit përmes një mekanizmi rul. Fillimisht një shtresë e hollë pluhuri depozitohet në cilindrin e ndërtuar pjesërisht, më pas një rreze lazer fokusohet në atë shtresë, duke gjurmuar dhe shkrirë / shkrirë një seksion kryq të veçantë, i cili më pas ri-ngurtësohet në një të ngurtë. Pluhuri është zona që nuk goditet nga rrezja e lazerit, mbeten të lirshme, por ende mbështet pjesën e ngurtë. Pastaj depozitohet një shtresë tjetër pluhuri dhe procesi përsëritet shumë herë për të marrë pjesën. Në fund, grimcat e lirshme të pluhurit shkunden. Të gjitha këto kryhen nga një kompjuter i kontrollit të procesit duke përdorur udhëzime të krijuara nga programi 3D CAD i pjesës që po prodhohet. Mund të depozitohen materiale të ndryshme si polimere (si ABS, PVC, poliester), dylli, metale dhe qeramika me lidhës polimer të përshtatshëm. • ELECTRON-BEAM MELTING: Ngjashëm me shkrirjen selektive me lazer, por duke përdorur rreze elektronike për shkrirjen e pluhurave të kromit titan ose kobalt për të bërë prototipe në vakum. Janë bërë disa zhvillime për të kryer këtë proces në çelik inox, alumini dhe lidhjet e bakrit. Nëse forca e lodhjes së pjesëve të prodhuara duhet të rritet, ne përdorim shtypjen e nxehtë izostatike pas prodhimit të pjesëve si një proces dytësor. • PRINTIME TREDIMENSIONALE: E shënuar gjithashtu me 3DP, në këtë teknikë një kokë printimi depoziton një lidhës inorganik në një shtresë pluhuri jometalik ose metalik. Një piston që mban shtratin e pluhurit ulet gradualisht dhe në çdo hap lidhësi depozitohet shtresë nga shtresa dhe shkrihet nga lidhësi. Materialet pluhur të përdorura janë përzierjet e polimereve dhe fibrave, rëra shkritore, metale. Duke përdorur koka të ndryshme lidhëse njëkohësisht dhe lidhëse me ngjyra të ndryshme mund të marrim ngjyra të ndryshme. Procesi është i ngjashëm me printimin me bojë, por në vend që të marrim një fletë me ngjyrë, ne marrim një objekt me ngjyrë tre-dimensionale. Pjesët e prodhuara mund të jenë poroze dhe për këtë arsye mund të kërkojnë sinterim dhe infiltrim metalik për të rritur densitetin dhe forcën e tij. Sinterizimi do të djegë lidhësin dhe do të shkrijë pluhurat metalikë së bashku. Metalet si inoksi, alumini, titan mund të përdoren për të bërë pjesët dhe si materiale infiltrimi zakonisht përdorim bakër dhe bronz. E bukura e kësaj teknike është se edhe montimet e ndërlikuara dhe lëvizëse mund të prodhohen shumë shpejt. Për shembull, një montim ingranazhesh, një çelës si mjet mund të bëhet dhe do të ketë pjesë lëvizëse dhe rrotulluese gati për t'u përdorur. Komponentët e ndryshëm të montimit mund të prodhohen me ngjyra të ndryshme dhe të gjitha në një foto. Shkarkoni broshurën tonë në:Bazat e printimit 3D metalik • PRODHIM DIREKT dhe MJETET E SHPEJTË: Përveç vlerësimit të dizajnit, zgjidhjes së problemeve, ne përdorim prototipizimin e shpejtë për prodhimin e drejtpërdrejtë të produkteve ose aplikimin e drejtpërdrejtë në produkte. Me fjalë të tjera, prototipizimi i shpejtë mund të përfshihet në proceset konvencionale për t'i bërë ato më të mira dhe më konkurruese. Për shembull, prototipi i shpejtë mund të prodhojë modele dhe kallëpe. Modelet e një polimeri të shkrirjes dhe djegies të krijuar nga operacionet e shpejta të prototipit mund të montohen për derdhje investimi dhe të investohen. Një shembull tjetër për t'u përmendur është përdorimi i 3DP për të prodhuar guaskën e derdhjes së qeramikës dhe përdorimin e saj për operacionet e derdhjes së guaskës. Edhe kallëpet e injektimit dhe futjet e mykut mund të prodhohen me prototipe të shpejta dhe mund të kurseni shumë javë ose muaj kohë të prodhimit të mykut. Duke analizuar vetëm një skedar CAD të pjesës së dëshiruar, ne mund të prodhojmë gjeometrinë e mjetit duke përdorur softuer. Këtu janë disa nga metodat tona të njohura të veglave të shpejta: RTV (Vulkanizimi i temperaturës së dhomës) DERDIMI / DERDHJA E URETANIT : Përdorimi i prototipit të shpejtë mund të përdoret për të bërë modelin e pjesës së dëshiruar. Më pas ky model lyhet me një agjent ndarës dhe goma e lëngshme RTV derdhet mbi model për të prodhuar gjysmat e mykut. Më pas, këto gjysma të mykut përdoren për të injektuar uretane të lëngshme të mykut. Jeta e mykut është e shkurtër, vetëm si 0 ose 30 cikle, por mjafton për prodhim të vogël në grup. ACES (Acetal Clear Epoxy Solid) DERDIMI ME INJEKTIM : Duke përdorur teknika të shpejta të prototipizimit si stereolithografia, ne prodhojmë kallëpe me injeksion. Këto kallëpe janë predha me një fund të hapur për të lejuar mbushjen me materiale të tilla si epoksi, epoksi i mbushur me alumin ose metale. Përsëri jeta e mykut është e kufizuar në dhjetëra ose maksimum qindra pjesë. PROCESI I PËRGATITJES SË METALIT TË SPRAKTUAR: Ne përdorim prototipimin e shpejtë dhe bëjmë një model. Spërkasim një aliazh zink-alumini në sipërfaqen e modelit dhe e lyejmë atë. Modeli me veshjen metalike më pas vendoset brenda një balone dhe futet në vazo me një epoksi ose epoksi të mbushur me alumin. Në fund hiqet dhe duke prodhuar dy gjysma të tilla kallëp fitojmë një kallëp të plotë për derdhje me injeksion. Këto kallëpe kanë jetë më të gjatë, në disa raste në varësi të materialit dhe temperaturave ato mund të prodhojnë pjesë në mijëra. PROCESI KEELTOOL: Kjo teknikë mund të prodhojë kallëpe me 100,000 deri në 10 milion jetë të cikleve. Duke përdorur prototipimin e shpejtë ne prodhojmë një kallëp RTV. Më pas kallëpi mbushet me një përzierje të përbërë nga pluhur çeliku për vegla A6, karabit tungsteni, lidhës polimer dhe lihet të thahet. Ky kallëp më pas nxehet për të djegur polimerin dhe për t'u shkrirë pluhurat metalikë. Hapi tjetër është infiltrimi i bakrit për të prodhuar kallëpin përfundimtar. Nëse është e nevojshme, operacionet dytësore si përpunimi dhe lustrimi mund të kryhen në kallëp për saktësi më të mira dimensionale. _cc781905-5cde-3194-bb3b-136bad5cf5 CLICK Product Finder-Locator Service FAQJA E MEPARSHME
- Joining & Assembly & Fastening Processes, Welding, Brazing, Soldering
Joining & Assembly & Fastening Processes, Welding, Brazing, Soldering, Sintering, Adhesive Bonding, Press Fitting, Wave and Reflow Solder Process, Torch Furnace Proceset e bashkimit dhe montimit dhe fiksimit Ne bashkojmë, montojmë dhe mbërthejmë pjesët tuaja të prodhuara dhe i kthejmë ato në produkte të gatshme ose gjysëm të gatshme duke përdorur SALDIM, BRAZHIM, SALDIM, SINTERIM, NGJITJE NGJITES, MBAJTJE, MONTIM PRESS. Disa nga proceset tona më të njohura të saldimit janë saldimi me hark, gaz oksigjeni, rezistenca, projeksioni, tegeli, mërzitja, perkusioni, gjendja e ngurtë, rrezja elektronike, lazeri, termiti, saldimi me induksion. Proceset tona popullore të ngjitjes janë pishtari, induksioni, furra dhe brazimi me zhytje. Metodat tona të saldimit janë saldimi me hekur, pllakë të nxehtë, furrë, induksion, zhytje, valë, rifluks dhe saldim tejzanor. Për ngjitjen me ngjitës ne përdorim shpesh termoplastikë dhe termo-fiksues, epokside, fenolikë, poliuretani, aliazhe ngjitëse si dhe disa kimikate dhe shirita të tjerë. Së fundi, proceset tona të fiksimit konsistojnë në gozhdimin, vidhosjen, dadot dhe bulonat, thumbat, mbërthimin, fiksimin, qepjen dhe kapjen dhe montimin me shtypje. • SALDIMI : Saldimi përfshin bashkimin e materialeve duke shkrirë pjesët e punës dhe futjen e materialeve mbushëse, të cilat gjithashtu bashkojnë pishinën e shkrirë të saldimit. Kur zona ftohet, fitojmë një nyje të fortë. Në disa raste ushtrohet presion. Ndryshe nga saldimi, operacionet e ngjitjes dhe saldimit përfshijnë vetëm shkrirjen e një materiali me pikë shkrirjeje më të ulët midis pjesëve të punës dhe pjesët e punës nuk shkrihen. Ne ju rekomandojmë që të klikoni këtu për tëSHKARKONI Ilustrimet tona Skematike të Proceseve të Saldimit nga AGS-TECH Inc. Kjo do t'ju ndihmojë të kuptoni më mirë informacionin që po ju ofrojmë më poshtë. Në SALDIM HARK, ne përdorim një furnizim me energji elektrike dhe një elektrodë për të krijuar një hark elektrik që shkrin metalet. Pika e saldimit mbrohet nga një gaz ose avull mbrojtës ose material tjetër. Ky proces është i popullarizuar për saldimin e pjesëve të automobilave dhe strukturave të çelikut. Në saldimin me hark metalik të mbrojtur (SMAW) ose i njohur edhe si saldimi me shkop, një shkop elektrodë afrohet pranë materialit bazë dhe midis tyre krijohet një hark elektrik. Shufra e elektrodës shkrihet dhe vepron si material mbushës. Elektroda gjithashtu përmban fluks që vepron si një shtresë skorje dhe lëshon avuj që veprojnë si gaz mbrojtës. Këto mbrojnë zonën e saldimit nga ndotja e mjedisit. Nuk përdoren mbushës të tjerë. Disavantazhet e këtij procesi janë ngadalësia e tij, nevoja për të zëvendësuar shpesh elektrodat, nevoja për të hequr skorjen e mbetur nga fluksi. Një sërë metalesh si hekuri, çeliku, nikeli, alumini, bakri… etj. Mund të saldohet. Përparësitë e tij janë mjetet e lira dhe lehtësia e përdorimit. Saldimi me hark metalik me gaz (GMAW) i njohur edhe si gaz metal-inert (MIG), kemi ushqim të vazhdueshëm të një mbushësi teli elektrodë të konsumueshëm dhe një gaz inert ose pjesërisht inert që rrjedh rreth telit kundër ndotjes mjedisore të rajonit të saldimit. Çeliku, alumini dhe metale të tjera me ngjyra mund të saldohen. Përparësitë e MIG janë shpejtësia e lartë e saldimit dhe cilësia e mirë. Disavantazhet janë pajisjet e tij të ndërlikuara dhe sfidat me të cilat përballen në mjediset e jashtme me erë, sepse ne duhet të mbajmë të qëndrueshme gazin mbrojtës rreth zonës së saldimit. Një variant i GMAW është saldimi me hark me fluks (FCAW) i cili përbëhet nga një tub metalik i imët i mbushur me materiale fluksi. Ndonjëherë fluksi brenda tubit është i mjaftueshëm për mbrojtjen nga ndotja e mjedisit. Saldimi me hark të zhytur (SAW) gjerësisht një proces i automatizuar, përfshin ushqyerjen e vazhdueshme të telit dhe harkun që goditet nën një shtresë mbulese fluksi. Normat e prodhimit dhe cilësia janë të larta, skorja e saldimit hiqet lehtë dhe kemi një mjedis pune pa tym. Disavantazhi është se mund të përdoret vetëm për të bashkuar pjesët në pozicione të caktuara. Në saldimin me hark të tungstenit me gaz (GTAW) ose saldimin me gaz inert tungsteni (TIG) ne përdorim një elektrodë tungsteni së bashku me një mbushës të veçantë dhe gazra inerte ose afër inerte. Siç e dimë tungsteni ka një pikë të lartë shkrirjeje dhe është një metal shumë i përshtatshëm për temperatura shumë të larta. Tungsteni në TIG nuk konsumohet në kundërshtim me metodat e tjera të shpjeguara më sipër. Një teknikë saldimi e ngadaltë, por me cilësi të lartë, e favorshme ndaj teknikave të tjera në saldimin e materialeve të holla. I përshtatshëm për shumë metale. Saldimi me hark plazmatik është i ngjashëm, por përdor gaz plazmatik për të krijuar harkun. Harku në saldimin me hark plazmatik është relativisht më i përqendruar në krahasim me GTAW dhe mund të përdoret për një gamë më të gjerë të trashësive metalike me shpejtësi shumë më të larta. GTAW dhe saldimi me hark plazmatik mund të aplikohen në pak a shumë të njëjtat materiale. Saldimi OXY-KARBURANT / OXYFUEL i quajtur edhe saldimi me oksiacetileni, saldimi me oksigjen, saldimi me gaz kryhet duke përdorur lëndë djegëse me gaz dhe oksigjen për saldim. Meqenëse nuk përdoret energji elektrike, ai është i lëvizshëm dhe mund të përdoret aty ku nuk ka energji elektrike. Duke përdorur një pishtar saldimi, ne ngrohim pjesët dhe materialin mbushës për të prodhuar një pishinë të përbashkët metali të shkrirë. Mund të përdoren lëndë djegëse të ndryshme si acetilen, benzinë, hidrogjen, propan, butan, etj. Në saldimin me karburant me oksigjen ne përdorim dy kontejnerë, një për karburantin dhe tjetrin për oksigjen. Oksigjeni oksidon karburantin (e djeg atë). SALDIMI REZISTENCE: Ky lloj saldimi përfiton nga ngrohja me xhaul dhe nxehtësia gjenerohet në vendin ku aplikohet rryma elektrike për një kohë të caktuar. Rrymat e larta kalohen nëpër metal. Në këtë vend formohen pellgje me metal të shkrirë. Metodat e saldimit me rezistencë janë të njohura për shkak të efikasitetit të tyre, potencialit të vogël të ndotjes. Megjithatë, disavantazhet janë kostot e pajisjeve që janë relativisht të rëndësishme dhe kufizimi i qenësishëm për pjesët relativisht të holla të punës. SALDIMI POST është një lloj kryesor i saldimit me rezistencë. Këtu ne bashkojmë dy ose më shumë fletë ose pjesë pune të mbivendosura duke përdorur dy elektroda bakri për të shtrënguar fletët dhe për të kaluar një rrymë të lartë nëpër to. Materiali ndërmjet elektrodave të bakrit nxehet dhe në atë vend krijohet një pishinë e shkrirë. Rryma më pas ndalet dhe majat e elektrodave të bakrit ftohin vendin e saldimit sepse elektrodat janë të ftohura me ujë. Aplikimi i sasisë së duhur të nxehtësisë në materialin dhe trashësinë e duhur është çelësi për këtë teknikë, sepse nëse aplikohet gabimisht, fuga do të jetë e dobët. Saldimi në vend ka përparësitë e mos shkaktimit të deformimeve të rëndësishme të pjesëve të punës, efikasitetit të energjisë, lehtësisë së automatizimit dhe shkallëve të jashtëzakonshme të prodhimit dhe nuk kërkon asnjë mbushës. Disavantazhi është se meqenëse saldimi bëhet në pika në vend që të formojë një shtresë të vazhdueshme, forca e përgjithshme mund të jetë relativisht më e ulët në krahasim me metodat e tjera të saldimit. Saldimi me tegel nga ana tjetër prodhon saldime në sipërfaqet ngjitëse të materialeve të ngjashme. Tegeli mund të jetë nyje prapanicë ose mbivendosje. Saldimi me tegel fillon në njërin skaj dhe lëviz progresivisht në tjetrin. Kjo metodë përdor gjithashtu dy elektroda nga bakri për të ushtruar presion dhe rrymë në zonën e saldimit. Elektrodat në formë disku rrotullohen me kontakt të vazhdueshëm përgjatë vijës së tegelit dhe bëjnë një saldim të vazhdueshëm. Edhe këtu elektrodat ftohen me ujë. Saldimet janë shumë të forta dhe të besueshme. Metoda të tjera janë teknikat e saldimit me projeksion, blic dhe të mërzitur. Saldimi në gjendje të ngurtë është pak më ndryshe nga metodat e mëparshme të shpjeguara më sipër. Bashkimi ndodh në temperatura nën temperaturën e shkrirjes së metaleve të bashkuara dhe pa përdorimin e mbushësit metalik. Presioni mund të përdoret në disa procese. Metoda të ndryshme janë SALDIMI ME KOEKTRUSION ku metale të ndryshme ekstrudohen përmes të njëjtit material, saldimi me presion të ftohtë ku bashkojmë lidhjet e buta nën pikat e tyre të shkrirjes, SALDIMI DIFFUSION një teknikë pa vija saldimi të dukshme, SALDIMI ME EKSPLOZIM për bashkimin e materialeve të ndryshme korrozive me materiale të ndryshme, e. çeliqet, saldimi me puls ELEKTROMAGNETIK ku përshpejtojmë tubat dhe fletët me anë të forcave elektromagnetike, SALDIM ME FERKEQIM që konsiston në ngrohjen e metaleve në temperatura të larta dhe goditjen me çekan së bashku, SALDIM ME FËRKIM ku kryhet saldim me fërkim të mjaftueshëm, SALDIM ME FERKEZIM që përfshin një vegël harxhuese që përshkon vijën e bashkimit, SALDIM ME PRIRJE NË TË Nxehtë ku shtypim metalet së bashku në temperatura të ngritura nën temperaturën e shkrirjes në vakum ose gaze inerte, SALDIM NË SHQIPËRI ISOSTATIKE ME PRIRJE, një proces ku ushtrojmë presion duke përdorur gaze inerte brenda një ene, SALDIM RRULL ku bashkohemi materiale të ndryshme duke i detyruar ato ndërmjet dy rrota rrotulluese, SALDIM ULTRASONIK ku saldohen fletë të holla metalike ose plastike duke përdorur energji vibruese me frekuencë të lartë. Proceset tona të tjera të saldimit janë SALDIMI ME RREZ ELEKTRON me depërtim të thellë dhe përpunim të shpejtë, por si metodë e shtrenjtë e konsiderojmë për raste të veçanta, SALDIMI ELEKTROSLLAG një metodë e përshtatshme vetëm për pllaka të rënda të trasha dhe copa pune prej çeliku, SALDIM ME INDUKTIN ku përdorim induksion elektromagnetik dhe ngrohim pjesët tona të punës përçuese elektrike ose ferromagnetike, SALDIM ME RREZE LAZER gjithashtu me depërtim të thellë dhe përpunim të shpejtë, por një metodë e shtrenjtë, SALDIM HIBRID LAZER që kombinon LBW me GMAW në të njëjtën kokë saldimi dhe i aftë për të kapërcyer boshllëqet prej 2 mm midis pllakave, SALDIM ME PERKUSI përfshin një shkarkesë elektrike të ndjekur nga farkëtimi i materialeve me presion të ushtruar, saldimi TERMIT që përfshin reaksion ekzotermik midis pluhurave të aluminit dhe oksidit të hekurit., SALDIM ME ELEKTROGAZ me elektroda harxhuese dhe të përdorura vetëm me çelik në pozicion vertikal, dhe së fundi SALDIM ME HARK për bashkimin e stufës me bazën material me nxehtësi dhe presion. Ne ju rekomandojmë që të klikoni këtu për tëSHKARKONI Ilustrimet tona skematike të proceseve të ngjitjes, saldimit dhe ngjitjes nga AGS-TECH Inc Kjo do t'ju ndihmojë të kuptoni më mirë informacionin që po ju ofrojmë më poshtë. • BRIZIM : Ne bashkojmë dy ose më shumë metale duke ngrohur metalet mbushëse ndërmjet tyre mbi pikat e tyre të shkrirjes dhe duke përdorur veprimin kapilar për t'u përhapur. Procesi është i ngjashëm me saldimin, por temperaturat e përfshira për shkrirjen e mbushësit janë më të larta në brumosje. Ashtu si në saldim, fluksi mbron materialin mbushës nga ndotja atmosferike. Pas ftohjes, pjesët e punës bashkohen së bashku. Procesi përfshin hapat kryesorë të mëposhtëm: Përshtatje dhe pastrim i mirë, pastrim i duhur i materialeve bazë, fiksim i duhur, përzgjedhje e duhur e fluksit dhe atmosferës, ngrohja e montimit dhe së fundi pastrimi i montimit të brumosur. Disa nga proceset tona të ngjitjes janë BRAZING me TORCH, një metodë popullore e kryer me dorë ose në mënyrë të automatizuar. Është i përshtatshëm për porosi prodhimi me volum të ulët dhe raste të specializuara. Nxehtësia aplikohet duke përdorur flakët e gazit pranë bashkimit që po ngjitet. BRAZIMI I FURNËS kërkon më pak aftësi operatori dhe është një proces gjysmë automatik i përshtatshëm për prodhimin masiv industrial. Si kontrolli i temperaturës ashtu edhe kontrolli i atmosferës në furrë janë avantazhe të kësaj teknike, sepse e para na mundëson që të kemi cikle të kontrolluara të nxehtësisë dhe të eliminojmë ngrohjen lokale siç është rasti në brazimin me pishtar, dhe kjo e fundit mbron pjesën nga oksidimi. Duke përdorur jigging ne jemi në gjendje të reduktojmë kostot e prodhimit në minimum. Disavantazhet janë konsumi i lartë i energjisë, kostot e pajisjeve dhe konsideratat më sfiduese të projektimit. BRAZIMI ME VAKUUM ndodh në një furre me vakum. Ruhet uniformiteti i temperaturës dhe fitojmë fuga pa fluks, shumë të pastra me shumë pak strese të mbetura. Trajtimet me nxehtësi mund të kryhen gjatë brumosjes me vakum, për shkak të streseve të ulëta të mbetura të pranishme gjatë cikleve të ngadalta të ngrohjes dhe ftohjes. Disavantazhi kryesor është kostoja e lartë e tij, sepse krijimi i mjedisit vakum është një proces i kushtueshëm. Një teknikë tjetër DIP BRAZING bashkon pjesët e fiksuara ku përbërja e brazimit aplikohet në sipërfaqet çiftëzuese. Më pas, pjesët e fiksuara zhyten në një banjë me një kripë të shkrirë si klorur natriumi (kripa e tryezës) që vepron si një mjet për transferimin e nxehtësisë dhe fluks. Ajri është i përjashtuar dhe për këtë arsye nuk ndodh formimi i oksidit. Në BAZIMIN ME INDUKSION ne bashkojmë materialet me një metal mbushës që ka një pikë shkrirjeje më të ulët se materialet bazë. Rryma alternative nga spiralja e induksionit krijon një fushë elektromagnetike e cila nxit ngrohjen me induksion në materialet magnetike kryesisht me ngjyra. Metoda siguron ngrohje selektive, lidhje të mira me mbushës që rrjedhin vetëm në zonat e dëshiruara, pak oksidim sepse nuk ka flakë dhe ftohja është e shpejtë, ngrohje e shpejtë, konsistencë dhe përshtatshmëri për prodhim me volum të lartë. Për të përshpejtuar proceset tona dhe për të siguruar qëndrueshmëri, ne përdorim shpesh preforma. Informacioni mbi objektin tonë të ngjitjes që prodhon pajisje qeramike në metal, vulosje hermetike, hyrje vakum, vakum të lartë dhe tepër të lartë dhe komponentë kontrolli të lëngjeve mund të gjenden këtu:_cc781905-31-5cBroshurë Brazing Factory • SALIM : Në saldim nuk kemi shkrirje të pjesëve të punës, por një metal mbushës me pikë shkrirjeje më të ulët se pjesët e bashkimit që derdhet në bashkim. Metali mbushës në saldim shkrihet në temperaturë më të ulët se në saldim. Ne përdorim lidhje pa plumb për saldim dhe kemi përputhje me RoHS dhe për aplikime dhe kërkesa të ndryshme kemi lidhje të ndryshme dhe të përshtatshme si aliazh argjendi. Saldimi na ofron nyje që janë të papërshkueshme nga gazi dhe lëngjet. Në SOFT SOLDERING, metali ynë mbushës ka një pikë shkrirje nën 400 C, ndërsa në SILVER SOLDING dhe BRAZING ne kemi nevojë për temperatura më të larta. Saldimi i butë përdor temperatura më të ulëta, por nuk rezulton në lidhje të forta për aplikime të vështira në temperatura të larta. Nga ana tjetër, saldimi i argjendit kërkon temperatura të larta të siguruara nga pishtari dhe na jep lidhje të forta të përshtatshme për aplikime në temperatura të larta. Brazimi kërkon temperaturat më të larta dhe zakonisht përdoret një pishtar. Meqenëse nyjet e brumit janë shumë të forta, ato janë një kandidat i mirë për riparimin e objekteve të rënda hekuri. Në linjat tona të prodhimit ne përdorim si saldimin manual, ashtu edhe linjat e automatizuara të saldimit. INDUCTION SOLDERING përdor rrymë AC me frekuencë të lartë në një spirale bakri për të lehtësuar ngrohjen me induksion. Rrymat induktohen në pjesën e salduar dhe si rezultat gjenerohet nxehtësi në rezistencën e lartë joint. Kjo nxehtësi shkrin metalin mbushës. Përdoret gjithashtu Flux. Saldimi me induksion është një metodë e mirë për bashkimin e ciklinderëve dhe tubave në një proces të vazhdueshëm duke i mbështjellë bobinat rreth tyre. Saldimi i disa materialeve si grafiti dhe qeramika është më i vështirë, sepse kërkon veshjen e pjesëve të punës me një metal të përshtatshëm përpara bashkimit. Kjo lehtëson lidhjen ndërfaqe. Ne bëjmë saldim të materialeve të tilla veçanërisht për aplikime të paketimit hermetik. Ne i prodhojmë pllakat tona të qarkut të printuar (PCB) në volum të lartë, kryesisht duke përdorur saldimin me valë. Vetëm për një sasi të vogël të qëllimeve të prototipit ne përdorim saldim me dorë duke përdorur hekurin e saldimit. Ne përdorim saldimin me valë si për montimet e PCB me vrima, ashtu edhe për montimin në sipërfaqe (PCBA). Një ngjitës i përkohshëm i mban përbërësit të ngjitur në tabelën e qarkut dhe montimi vendoset në një transportues dhe lëviz nëpër një pajisje që përmban saldim të shkrirë. Fillimisht PCB-ja rrjedh dhe më pas hyn në zonën e paranxehjes. Lidhja e shkrirë është në një tigan dhe ka një model valësh në këmbë në sipërfaqen e saj. Kur PCB lëviz mbi këto valë, këto valë kontaktojnë pjesën e poshtme të PCB-së dhe ngjiten në jastëkët e saldimit. Saldimi qëndron vetëm në kunjat dhe jastëkët dhe jo në vetë PCB-në. Valët në saldimin e shkrirë duhet të kontrollohen mirë në mënyrë që të mos ketë spërkatje dhe majat e valëve të mos prekin dhe kontaminojnë zonat e padëshiruara të dërrasave. Në REFLOW SOLDERING, ne përdorim një pastë ngjitëse ngjitëse për të lidhur përkohësisht komponentët elektronikë në pllaka. Pastaj dërrasat futen në një furrë ripërtëritjeje me kontroll të temperaturës. Këtu saldimi shkrihet dhe lidh përgjithmonë përbërësit. Ne e përdorim këtë teknikë për të dy komponentët e montimit në sipërfaqe, si dhe për komponentët me vrima. Kontrolli i duhur i temperaturës dhe rregullimi i temperaturës së furrës është thelbësor për të shmangur shkatërrimin e komponentëve elektronikë në tabelë duke i mbinxehur ato mbi kufijtë e tyre maksimal të temperaturës. Në procesin e saldimit me rifluks, ne në fakt kemi disa rajone ose faza secila me një profil të veçantë termik, si hapi i parangrohjes, hapi i njomjes termike, hapat e rikthimit dhe ftohjes. Këta hapa të ndryshëm janë thelbësorë për një bashkim pa dëmtime të montimeve të pllakave të qarkut të printuar (PCBA). ALDIMI ULTRASONIK është një teknikë tjetër e përdorur shpesh me aftësi unike- Mund të përdoret për të bashkuar qelqin, qeramikën dhe materialet jometalike. Për shembull, panelet fotovoltaike të cilat janë jometalike kanë nevojë për elektroda të cilat mund të vendosen duke përdorur këtë teknikë. Në saldimin tejzanor, ne vendosim një majë saldimi të nxehtë që lëshon gjithashtu dridhje tejzanor. Këto dridhje prodhojnë flluska të kavitacionit në ndërfaqen e nënshtresës me materialin e shkrirë të saldimit. Energjia shpërthyese e kavitacionit modifikon sipërfaqen e oksidit dhe largon papastërtitë dhe oksidet. Gjatë kësaj kohe formohet edhe një shtresë aliazhi. Saldimi në sipërfaqen e lidhjes përfshin oksigjen dhe mundëson formimin e një lidhjeje të fortë të përbashkët midis xhamit dhe saldimit. DIP SOLDERING mund të konsiderohet si një version më i thjeshtë i saldimit me valë i përshtatshëm vetëm për prodhim në shkallë të vogël. Fluksi i parë i pastrimit aplikohet si në proceset e tjera. PCB-të me komponentë të montuar zhyten manualisht ose në një mënyrë gjysmë të automatizuar në një rezervuar që përmban saldim të shkrirë. Lidhja e shkrirë ngjitet në zonat metalike të ekspozuara të pambrojtura nga maska e saldimit në tabelë. Pajisjet janë të thjeshta dhe të lira. • NGJITJA NGJITES: Kjo është një teknikë tjetër popullore që ne përdorim shpesh dhe përfshin lidhjen e sipërfaqeve duke përdorur ngjitës, epoksid, agjentë plastikë ose kimikate të tjera. Lidhja realizohet ose duke avulluar tretësin, me tharjen me nxehtësi, me tharjen me rreze UV, me tharje nën presion ose duke pritur për një kohë të caktuar. Në linjat tona të prodhimit përdoren ngjitës të ndryshëm me performancë të lartë. Me proceset e aplikimit dhe të kurimit të dizajnuara siç duhet, ngjitja e ngjitësit mund të rezultojë në lidhje me stres shumë të ulët që janë të forta dhe të besueshme. Lidhjet ngjitëse mund të jenë mbrojtës të mirë kundër faktorëve mjedisorë si lagështia, ndotësit, gërryesit, dridhjet ... etj. Përparësitë e lidhjes ngjitëse janë: ato mund të aplikohen në materiale që përndryshe do të ishin të vështira për t'u bashkuar, salduar ose për t'u brumosur. Gjithashtu mund të preferohet për materiale të ndjeshme ndaj nxehtësisë që do të dëmtoheshin nga saldimi ose procese të tjera në temperaturë të lartë. Përparësi të tjera të ngjitësve janë se ato mund të aplikohen në sipërfaqe me formë të parregullt dhe të rrisin peshën e montimit me sasi shumë shumë të vogla në krahasim me metodat e tjera. Gjithashtu ndryshimet dimensionale në pjesë janë shumë minimale. Disa ngjitës kanë veti përputhshmërie të indeksit dhe mund të përdoren ndërmjet komponentëve optikë pa ulur ndjeshëm fuqinë e dritës ose të sinjalit optik. Disavantazhet nga ana tjetër janë kohët më të gjata të tharjes, të cilat mund të ngadalësojnë linjat e prodhimit, kërkesat e fiksimit, kërkesat për përgatitjen e sipërfaqes dhe vështirësia për t'u çmontuar kur nevojitet ripërpunimi. Shumica e operacioneve tona të ngjitjes së ngjitësit përfshijnë hapat e mëposhtëm: -Trajtimi i sipërfaqes: Procedurat speciale të pastrimit si pastrimi i ujit të dejonizuar, pastrimi me alkool, pastrimi i plazmës ose koronës janë të zakonshme. Pas pastrimit, ne mund të aplikojmë nxitës ngjitës mbi sipërfaqe për të siguruar nyjet më të mira të mundshme. -Rregullimi i pjesëve: Si për aplikimin e ngjitësit ashtu edhe për forcimin ne projektojmë dhe përdorim pajisje me porosi. -Aplikimi i ngjitësit: Ne përdorim ndonjëherë manuale, dhe nganjëherë në varësi të rastit sisteme të automatizuara si robotikë, servo motorë, aktivizues linearë për të dorëzuar ngjitësit në vendin e duhur dhe përdorim dispenzues për t'i dorëzuar ato në vëllimin dhe sasinë e duhur. -Kurimi: Në varësi të ngjitësit, ne mund të përdorim tharje dhe ngurtësim të thjeshtë, si dhe shërim nën dritat UV që veprojnë si katalizator ose shërim me nxehtësi në furrë ose duke përdorur elementë ngrohjeje rezistente të montuara në pajisje dhe pajisje. Ne ju rekomandojmë që të klikoni këtu për tëSHKARKONI Ilustrimet tona Skematike të Proceseve të Mbërthimit nga AGS-TECH Inc. Kjo do t'ju ndihmojë të kuptoni më mirë informacionin që po ju ofrojmë më poshtë. • PROCESET E MBAJTJES: Proceset tona të bashkimit mekanik ndahen në dy kategori brad: MIRËZIMET dhe NGJYJET INTEGRALE. Shembuj të lidhësve që përdorim janë vida, kunja, dado, bulonat, thumba. Shembuj të fugave integrale që ne përdorim janë montime të këputura dhe tkurrje, tegela, shtrëngime. Duke përdorur një shumëllojshmëri metodash fiksimi, ne sigurohemi që nyjet tona mekanike të jenë të forta dhe të besueshme për shumë vite përdorim. VIDA dhe BULONAT janë disa nga lidhësit më të përdorur për mbajtjen dhe pozicionimin e objekteve. Vidhat dhe bulonat tona plotësojnë standardet ASME. Lloje të ndryshme vidhash dhe bulonash janë vendosur duke përfshirë vidhat me kapakë gjashtëkëndor dhe bulonat gjashtëkëndor, vidhat dhe bulonat me vonesë, vidën me dy skaje, vidën e kunjit, vidën e syrit, vidën e pasqyrës, vidhën prej fletë metalike, vidhën rregulluese të imët, vida vetë-shpuese dhe vetë-përgjimi , vidë e vendosur, vida me rondele të integruara,…dhe më shumë. Kemi lloje të ndryshme të kokave të vidhave, si p.sh. me kokë të zhytur, kupolë, të rrumbullakët, me fllanxha dhe lloje të ndryshme vidhash si slot, phillips, katror, fole hex. Një RIVET nga ana tjetër është një mbërthyes mekanik i përhershëm i përbërë nga një bosht cilindrik i lëmuar dhe një kokë nga njëra anë. Pas futjes, skaji tjetër i ribatinës deformohet dhe diametri i saj zgjerohet në mënyrë që të qëndrojë në vend. Me fjalë të tjera, para instalimit një thumba ka një kokë dhe pas instalimit ka dy. Ne instalojmë lloje të ndryshme ribatinash në varësi të aplikimit, forcës, aksesueshmërisë dhe kostos, si ribatina me kokë të ngurtë/rrumbullakët, ribatina strukturore, gjysmë tuba, të verbër, oscar, me makinë, flush, fërkime, mbyllëse me fërkim, vetë-shpuese. Ribatina mund të preferohet në rastet kur duhet të shmanget deformimi i nxehtësisë dhe ndryshimi i vetive të materialit për shkak të nxehtësisë së saldimit. Riveting ofron gjithashtu peshë të lehtë dhe veçanërisht forcë dhe qëndrueshmëri të mirë ndaj forcave prerëse. Kundrejt ngarkesave tërheqëse, megjithatë, vidhat, dadot dhe bulonat mund të jenë më të përshtatshme. Në procesin CLINCHING ne përdorim punues të posaçëm dhe shufra për të formuar një ndërthurje mekanike midis fletëve të metaleve që bashkohen. Grushti i shtyn shtresat e llamarinës në zgavrën e mbulesës dhe rezulton në formimin e një bashkimi të përhershëm. Nuk kërkohet ngrohje dhe ftohje në mbyllje dhe është një proces pune i ftohtë. Është një proces ekonomik që mund të zëvendësojë saldimin në pika në disa raste. Në PINNING ne përdorim kunja të cilat janë elemente makinerie që përdoren për të siguruar pozicionet e pjesëve të makinës në lidhje me njëra-tjetrën. Llojet kryesore janë kunjat clevis, gjilpërat, kunjat me susta, kunjat me kunj, dhe kunja e ndarë. Në STAPLING ne përdorim pistoleta dhe kapëse të cilat janë lidhëse me dy krahë që përdoren për të bashkuar ose lidhur materiale. Kapja ka përparësitë e mëposhtme: Ekonomike, e thjeshtë dhe e shpejtë për t'u përdorur, kurora e kapëseve mund të përdoret për të lidhur materialet e lidhura së bashku, Kurora e kapëses mund të lehtësojë lidhjen e një pjese si kabllo dhe fiksimin e saj në një sipërfaqe pa shpuar ose dëmtuese, heqje relativisht e lehtë. PRESS FITTING kryhet duke i shtyrë pjesët së bashku dhe fërkimi ndërmjet tyre lidh pjesët. Pjesët e përshtatura me shtypje që përbëhen nga një bosht i madh dhe një vrimë e vogël zakonisht montohen me një nga dy metodat: Ose duke ushtruar forcë ose duke përfituar nga zgjerimi termik ose tkurrja e pjesëve. Kur një pajisje shtypëse krijohet duke ushtruar një forcë, ne përdorim ose një shtypje hidraulike ose një prese me dorë. Nga ana tjetër, kur montimi i presës vendoset nga zgjerimi termik, ne ngrohim pjesët mbështjellëse dhe i montojmë në vendin e tyre ndërsa janë të nxehta. Kur ftohen ato tkurren dhe kthehen në dimensionet e tyre normale. Kjo rezulton në një përshtatje të mirë të shtypit. Ne e quajmë këtë në mënyrë alternative SHRINK-FITTING. Mënyra tjetër për ta bërë këtë është duke i ftohur pjesët e mbështjella përpara montimit dhe më pas duke i rrëshqitur në pjesët e tyre të çiftëzimit. Kur montimi ngrohet ato zgjerohen dhe fitojmë një përshtatje të ngushtë. Kjo metodë e fundit mund të preferohet në rastet kur ngrohja paraqet rrezikun e ndryshimit të vetive të materialit. Ftohja është më e sigurt në ato raste. Komponentët dhe Asambletë Pneumatike & Hidraulike • Valvola, komponentë hidraulikë dhe pneumatikë si O-ring, rondele, vulosje, copë litari, unazë, shirit. Meqenëse valvulat dhe komponentët pneumatikë vijnë në një larmi të madhe, ne nuk mund të rendisim gjithçka këtu. Në varësi të mjediseve fizike dhe kimike të aplikacionit tuaj, ne kemi produkte speciale për ju. Ju lutemi të na specifikoni aplikimin, llojin e komponentit, specifikimet, kushtet mjedisore si presioni, temperatura, lëngjet ose gazrat që do të jenë në kontakt me valvulat dhe komponentët tuaj pneumatikë; dhe ne do të zgjedhim produktin më të përshtatshëm për ju ose do ta prodhojmë atë posaçërisht për aplikimin tuaj. CLICK Product Finder-Locator Service FAQJA E MEPARSHME
- Machine Elements Manufacturing, Gears, Gear Drives, Bearings, Keys, Splines
Machine Elements Manufacturing, Gears, Gear Drives, Bearings, Keys, Splines, Pins, Shafts, Seals, Fasteners, Clutch, Cams, Followers, Belts, Couplings, Shafts Prodhimi i Elementeve të Makinerisë Lexo më shumë Rripa dhe zinxhirë dhe montim i kabllove Lexo më shumë Montimi i ingranazheve dhe ingranazheve Lexo më shumë Lidhje dhe kushineta Prodhim Lexo më shumë Prodhim çelësash, splinash dhe kunjash Lexo më shumë Kamerat dhe ndjekësit dhe lidhjet dhe rrotat me rafte Prodhim Lexo më shumë Prodhim boshtesh Lexo më shumë Prodhim vulash mekanike Lexo më shumë Montimi i tufës dhe frenave Lexo më shumë Mbërthyes Prodhim Lexo më shumë Montimi i makinave të thjeshta Elementet e makinës janë komponentë elementare të një makine. Këta elementë përbëhen nga tre lloje themelore: 1.) Komponentët strukturorë duke përfshirë pjesët e kornizës, kushinetat, boshtet, shiritat, lidhësit, vulat dhe lubrifikantët. 2.) Mekanizmat që kontrollojnë lëvizjen në mënyra të ndryshme, si p.sh. trenat e ingranazheve, lëvizjet e rripave ose zinxhirëve, lidhjet, sistemet e kamerës dhe ndjekësit, frenat dhe kthetrat. 3.) Kontrolloni komponentët si butonat, çelsat, treguesit, sensorët, aktivizuesit dhe kontrollorët e kompjuterit. Shumica e elementeve të makinës që ju ofrojmë janë të standardizuara në madhësi të zakonshme, por elementët e makinës me porosi janë gjithashtu të disponueshme për aplikacionet tuaja të specializuara. Personalizimi i elementeve të makinës mund të bëhet në modelet ekzistuese që janë në katalogët tanë të shkarkueshëm ose në modele krejt të reja. Prototipi dhe prodhimi i elementeve të makinës mund të kryhen përpara pasi një dizajn të miratohet nga të dyja palët. Nëse elementë të rinj të makinës duhet të projektohen dhe prodhohen, klientët tanë ose na dërgojnë email projektet e tyre dhe ne i shqyrtojmë ato për miratim, ose ata na kërkojnë të projektojmë elementë të makinës për aplikimin e tyre. Në rastin e fundit ne përdorim të gjitha të dhënat nga klientët tanë dhe projektojmë elementët e makinës dhe dërgojmë projektet e përfunduara te klientët tanë për miratim. Pasi të miratohet, ne prodhojmë artikujt e parë dhe më pas prodhojmë elementët e makinës sipas dizajnit përfundimtar. Në çdo fazë të kësaj pune, në rast se një dizajn i veçantë i elementit të makinës nuk funksionon në mënyrë të kënaqshme në terren (gjë që është e rrallë), ne rishikojmë të gjithë projektin dhe bëjmë ndryshime së bashku me klientët tanë sipas nevojës. Është praktika jonë standarde për të nënshkruar marrëveshje moszbulimi (NDA) me klientët tanë për projektimin e elementeve të makinës ose çdo produkti tjetër sa herë që nevojitet ose kërkohet. Pasi elementët e makinës për një klient të caktuar janë projektuar dhe prodhuar me porosi, ne i caktojmë atij një kod produkti dhe i prodhojmë dhe ia shesim vetëm klientit tonë që zotëron produktin. Ne riprodhojmë elementët e makinës duke përdorur veglat, kallëpet dhe procedurat e zhvilluara sa herë që nevojitet dhe sa herë që klienti ynë i riporosit ato. Me fjalë të tjera, pasi një element makine me porosi është projektuar dhe prodhuar për ju, prona intelektuale, si dhe të gjitha veglat dhe kallëpet rezervohen dhe ruhen për një kohë të pacaktuar nga ne për ju dhe produktet riprodhohen sipas dëshirës tuaj. Ne gjithashtu u ofrojmë klientëve tanë shërbime inxhinierike duke kombinuar në mënyrë kreative elementet e makinës në një komponent ose montim që i shërben një aplikacioni dhe që plotëson ose tejkalon pritshmëritë e klientëve tanë. Impiantet që fabrikojnë elementët e makinerive tona janë të kualifikuara nga ISO9001, QS9000 ose TS16949. Për më tepër, shumica e produkteve tona kanë markën CE ose UL dhe plotësojnë standardet përkatëse ndërkombëtare si ISO, SAE, ASME, DIN. Ju lutemi klikoni në nënmenutë për të marrë informacion të detajuar rreth elementeve të makinës sonë, duke përfshirë: - Rripat, zinxhirët dhe kabllot - Ingranazhet dhe disqet e ingranazheve - Lidhjet dhe kushinetat - Çelësat & Splines & kunjat - Kamerat dhe lidhjet - Boshte - Vula mekanike - Klutch & Brake Industriale - Mbërthyes - Makina të thjeshta Ne kemi përgatitur një broshurë referimi për klientët tanë, projektuesit dhe zhvilluesit e produkteve të reja duke përfshirë elementët e makinerive. Ju mund të njiheni me disa terma të përdorur zakonisht në hartimin e komponentëve të makinës: Shkarkoni broshurën për termat e përbashkëta të inxhinierisë mekanike të përdorura nga projektuesit dhe inxhinierët Elementet tona të makinerive gjejnë aplikime në një sërë fushash si makineri industriale, sisteme automatizimi, pajisje testimi dhe metrologjie, pajisje transporti, makineri ndërtimi dhe praktikisht kudo që ju mund të mendoni. AGS-TECH zhvillon dhe prodhon elemente makinerie nga materiale të ndryshme në varësi të aplikimit. Materialet e përdorura për elementët e makinës mund të variojnë nga plastika e derdhur e përdorur për lodra deri te çeliku i ngurtësuar dhe i veshur posaçërisht për makineri industriale. Dizajnerët tanë përdorin softuer profesional dhe mjete projektimi më të avancuara për zhvillimin e elementeve të makinës, duke marrë parasysh detaje të tilla si këndet në dhëmbët e marsheve, sforcimet e përfshira, shkallët e konsumimit… etj. Ju lutemi, lëvizni nëpër nënmenytë tona dhe shkarkoni broshurat dhe katalogët tanë të produkteve për të parë nëse mund të gjeni elementë të makinës jashtë raftit për aplikacionin tuaj. Nëse nuk mund të gjeni një përputhje të mirë për aplikacionin tuaj, ju lutemi na njoftoni dhe ne do të punojmë me ju për të zhvilluar dhe prodhuar elementë makine që do të plotësojnë nevojat tuaja. Nëse jeni kryesisht të interesuar për aftësitë tona inxhinierike dhe kërkimore dhe zhvillimore në vend të aftësive prodhuese, atëherë ju ftojmë të vizitoni faqen tonë të internetit http://www.ags-engineering.com ku mund të gjeni informacion më të detajuar në lidhje me dizajnin tonë, zhvillimin e produktit, zhvillimin e procesit, shërbimet e këshillimit inxhinierik dhe më shumë CLICK Product Finder-Locator Service FAQJA E MEPARSHME
- Composites, Composite Materials Manufacturing, Fiber Reinforced
Composites, Composite Materials Manufacturing, Particle and Fiber Reinforced, Cermets, Ceramic & Metal Composite, Glass Fiber Reinforced Polymer, Lay-Up Process Përbërës & Materiale të Përbëra Prodhim E përkufizuar thjesht, KOMPOZITET ose MATERIALET E PËRBËRËS janë materiale që përbëhen nga dy ose shumë materiale me veti të ndryshme fizike ose kimike, por kur kombinohen ato bëhen një material që është i ndryshëm nga materialet përbërëse. Duhet të theksojmë se materialet përbërëse mbeten të ndara dhe të dallueshme në strukturë. Qëllimi në prodhimin e një materiali të përbërë është të përftohet një produkt që është më i lartë se përbërësit e tij dhe që kombinon veçoritë e dëshiruara të secilit përbërës. Si nje shembull; forca, pesha e ulët ose çmimi më i ulët mund të jenë motivuesi pas projektimit dhe prodhimit të një përbërjeje. Lloji i kompozitave që ne ofrojmë janë kompozita të përforcuara me grimca, kompozita të përforcuara me fibra, duke përfshirë përbërjet me matricë qeramike / matricë-polimer / matricë metalike / karbon-karbon / kompozita hibride, kompozita strukturore dhe të laminuara dhe të strukturuara me sanduiç dhe nanokompozite. Teknikat e fabrikimit që ne përdorim në prodhimin e materialeve të përbëra janë: Pultrusion, proceset e prodhimit të parapreg, vendosja e avancuar e fibrave, mbështjellja e filamentit, vendosja e përshtatur e fibrave, procesi i shtrimit me spërkatje me tekstil me fije qelqi, tufatimi, procesi i lanksidit, z-gozhdimi. Shumë materiale të përbëra përbëhen nga dy faza, matrica, e cila është e vazhdueshme dhe rrethon fazën tjetër; dhe faza e shpërndarë e cila është e rrethuar nga matrica. Ne ju rekomandojmë që të klikoni këtu për tëSHKARKONI Ilustrimet tona Skematike të Prodhimit të Përbërjeve dhe Materialeve të Përbëra nga AGS-TECH Inc. Kjo do t'ju ndihmojë të kuptoni më mirë informacionin që po ju ofrojmë më poshtë. • KOMPOSITET E PËRFORCUR ME GJERIMË: Kjo kategori përbëhet nga dy lloje: Kompozita me grimca të mëdha dhe kompozita të forcuara me dispersion. Në llojin e parë, ndërveprimet grimcë-matricë nuk mund të trajtohen në nivel atomik ose molekular. Në vend të kësaj, mekanika e vazhdueshme është e vlefshme. Nga ana tjetër, në përbërjet e përforcuara me dispersion, grimcat janë përgjithësisht shumë më të vogla në intervalin dhjetëra nanometër. Një shembull i përbërjes së grimcave të mëdha janë polimeret të cilave u janë shtuar mbushësit. Mbushësit përmirësojnë vetitë e materialit dhe mund të zëvendësojnë një pjesë të vëllimit të polimerit me një material më ekonomik. Fraksionet vëllimore të dy fazave ndikojnë në sjelljen e përbërjes. Kompozitat e grimcave të mëdha përdoren me metale, polimere dhe qeramikë. CERMETS janë shembuj të kompoziteve qeramike / metalike. Cermeti ynë më i zakonshëm është karabit i çimentuar. Përbëhet nga qeramika zjarrduruese e karabit si grimcat e karbitit të tungstenit në një matricë të një metali si kobalti ose nikeli. Këto përbërje karabit përdoren gjerësisht si mjete prerëse për çelikun e ngurtësuar. Grimcat e forta të karbitit janë përgjegjëse për veprimin e prerjes dhe qëndrueshmëria e tyre rritet nga matrica metalike duktile. Kështu ne marrim avantazhet e të dy materialeve në një përbërje të vetme. Një shembull tjetër i zakonshëm i përbërjes së grimcave të mëdha që përdorim janë grimcat e zeza të karbonit të përziera me gomë të vullkanizuar për të përftuar një përbërje me rezistencë të lartë në tërheqje, rezistencë, grisje dhe rezistencë ndaj gërryerjes. Një shembull i një përbërjeje të përforcuar me dispersion janë metalet dhe lidhjet metalike të forcuara dhe ngurtësuara nga shpërndarja uniforme e grimcave të imëta të një materiali shumë të fortë dhe inert. Kur thekon shumë të vogla të oksidit të aluminit shtohen në matricën metalike të aluminit, ne përftojmë pluhur alumini të sinterizuar i cili ka një forcë të përmirësuar në temperaturë të lartë. • KOMPOZITET E PËRFORCUR ME FIBRA: Kjo kategori kompozitesh është në fakt më e rëndësishmja. Qëllimi për t'u arritur është forca dhe ngurtësia e lartë për njësi të peshës. Përbërja, gjatësia, orientimi dhe përqendrimi i fibrave në këto kompozita janë kritike në përcaktimin e vetive dhe dobisë së këtyre materialeve. Ekzistojnë tre grupe fibrash që përdorim: mustaqet, fijet dhe telat. Mustaqet janë njëkristal shumë të hollë dhe të gjatë. Janë ndër materialet më të forta. Disa shembuj të materialeve të mustaqeve janë grafiti, nitridi i silikonit, oksidi i aluminit. FIBERS nga ana tjetër janë kryesisht polimere ose qeramikë dhe janë në gjendje polikristaline ose amorfe. Grupi i tretë janë TELA të imët që kanë diametra relativisht të mëdhenj dhe shpesh përbëhen prej çeliku ose tungsteni. Një shembull i përbërjes së përforcuar me tela janë gomat e makinave që përfshijnë tela çeliku brenda gomës. Në varësi të materialit të matricës, kemi përbërjet e mëposhtme: KOMPOZITET POLIMER-MATRICË: Këto janë bërë nga një rrëshirë polimer dhe fibra si përbërës përforcues. Një nëngrup i këtyre të quajtura Kompozita me polimer të përforcuar me fibra qelqi (GFRP) përmbajnë fibra qelqi të vazhdueshme ose të ndërprera brenda një matrice polimer. Xhami ofron forcë të lartë, është ekonomik, i lehtë për t'u fabrikuar në fibra dhe është kimikisht inerte. Disavantazhet janë ngurtësia dhe ngurtësia e tyre e kufizuar, temperaturat e shërbimit janë vetëm deri në 200 – 300 C. Tekstil me fije qelqi është i përshtatshëm për trupat e automobilave dhe pajisjet e transportit, trupat e automjeteve detare, kontejnerët e magazinimit. Ato nuk janë të përshtatshme për hapësirën ajrore dhe as për ndërtimin e urave për shkak të ngurtësisë së kufizuar. Nëngrupi tjetër quhet Kompozit me polimer të përforcuar me fibra karboni (CFRP). Këtu, karboni është materiali ynë fibër në matricën e polimerit. Karboni është i njohur për modulin dhe forcën e tij specifike të lartë dhe aftësinë e tij për t'i mbajtur ato në temperatura të larta. Fijet e karbonit mund të na ofrojnë moduli elastik standard, të ndërmjetëm, të lartë dhe ultra të lartë. Për më tepër, fibrat e karbonit ofrojnë karakteristika të ndryshme fizike dhe mekanike dhe për këtë arsye janë të përshtatshme për aplikime të ndryshme inxhinierike të përshtatura me porosi. Kompozitat CFRP mund të konsiderohen për të prodhuar pajisje sportive dhe rekreative, enë nën presion dhe komponentë strukturorë të hapësirës ajrore. Megjithatë, një nëngrup tjetër, Kompozitat polimer të përforcuar me fibra Aramid janë gjithashtu materiale me rezistencë të lartë dhe modul. Raportet e tyre të forcës ndaj peshës janë jashtëzakonisht të larta. Fijet Aramide njihen gjithashtu me emrat tregtarë KEVLAR dhe NOMEX. Nën tension, ato performojnë më mirë se materialet e tjera me fibra polimerike, por janë të dobëta në ngjeshje. Fijet Aramide janë të forta, rezistente ndaj goditjeve, rezistente ndaj zvarritjes dhe lodhjes, të qëndrueshme në temperatura të larta, kimikisht inerte, përveç kundër acideve dhe bazave të forta. Fijet Aramide përdoren gjerësisht në mallra sportive, jelek antiplumb, goma, litarë, mbulesa kabllosh me fibra optike. Materiale të tjera përforcuese me fibra ekzistojnë, por përdoren në një shkallë më të vogël. Këto janë kryesisht bor, karabit silikoni, oksid alumini. Materiali i matricës polimer nga ana tjetër është gjithashtu kritik. Përcakton temperaturën maksimale të shërbimit të përbërjes sepse polimeri në përgjithësi ka një temperaturë më të ulët të shkrirjes dhe degradimit. Poliesterët dhe esteret vinyl përdoren gjerësisht si matricë polimer. Përdoren gjithashtu rrëshira dhe ato kanë rezistencë të shkëlqyer ndaj lagështirës dhe veti mekanike. Për shembull, rrëshira poliimide mund të përdoret deri në rreth 230 gradë Celcius. KOMPOZITET METAL-MATRIKË: Në këto materiale ne përdorim një matricë metalike duktile dhe temperaturat e shërbimit janë përgjithësisht më të larta se përbërësit e tyre përbërës. Kur krahasohen me përbërjet me matricë polimer, këto mund të kenë temperatura më të larta funksionimi, të jenë të padjegshme dhe mund të kenë rezistencë më të mirë ndaj degradimit ndaj lëngjeve organike. Megjithatë ato janë më të shtrenjta. Materiale përforcuese si mustaqe, grimca, fibra të vazhdueshme dhe të ndërprera; dhe materialet e matricës si bakri, alumini, magnezi, titani, superaliazhet janë duke u përdorur zakonisht. Shembuj të aplikimeve janë komponentët e motorit të bërë nga matricë aliazh alumini të përforcuar me oksid alumini dhe fibra karboni. KOMPOZITET QERAMIK-MATRIKË : Materialet qeramike njihen për besueshmërinë e tyre jashtëzakonisht të mirë në temperaturë të lartë. Megjithatë ato janë shumë të brishta dhe kanë vlera të ulëta për qëndrueshmërinë në thyerje. Duke futur grimca, fibra ose mustaqe të një qeramike në matricën e një tjetre, ne jemi në gjendje të arrijmë përbërje me rezistencë më të lartë në thyerje. Këto materiale të ngulitura në thelb pengojnë përhapjen e plasaritjeve brenda matricës me disa mekanizma të tillë si devijimi i majave të plasaritjes ose formimi i urave nëpër faqet e çarjeve. Si shembull, aluminat që janë të përforcuara me mustaqe SiC përdoren si futje të veglave prerëse për përpunimin e lidhjeve të metaleve të forta. Këto mund të zbulojnë performanca më të mira në krahasim me karbitet e çimentuara. KOMPOZITET KARBON-KARBON: Si përforcimi ashtu edhe matrica janë karboni. Kanë module të larta tërheqëse dhe forcë në temperatura të larta mbi 2000 C, rezistencë ndaj zvarritjes, rezistencë të lartë ndaj thyerjes, koeficientë të ulët të zgjerimit termik, përçueshmëri të lartë termike. Këto veti i bëjnë ato ideale për aplikime që kërkojnë rezistencë ndaj goditjeve termike. Dobësia e përbërjeve karbon-karbon është megjithatë cenueshmëria e tyre ndaj oksidimit në temperatura të larta. Shembuj tipikë të përdorimit janë kallëpet me presion të nxehtë, prodhimi i avancuar i komponentëve të motorit të turbinës. KOMPOZITET HIBRID: Dy ose më shumë lloje të ndryshme fibrash janë të përziera në një matricë të vetme. Kështu mund të përshtatet një material i ri me një kombinim të vetive. Një shembull është kur të dy fijet e karbonit dhe të qelqit përfshihen në një rrëshirë polimerike. Fijet e karbonit ofrojnë ngurtësi dhe forcë me densitet të ulët, por janë të shtrenjta. Xhami nga ana tjetër është i lirë, por i mungon ngurtësia e fibrave të karbonit. Kompoziti hibrid qelqi-karbon është më i fortë dhe më i fortë dhe mund të prodhohet me një kosto më të ulët. PËRPUNIMI I KOMPOZITËVE TË PËRFORCUARA ME FIBRA: Për plastika të vazhdueshme të përforcuara me fibra me fibra të shpërndara uniforme të orientuara në të njëjtin drejtim, ne përdorim teknikat e mëposhtme. PULTRUSION: Prodhohen shufra, trarë dhe tuba me gjatësi të vazhdueshme dhe seksione tërthore konstante. Rrotullimet e vazhdueshme të fibrave janë të ngopura me një rrëshirë termofikse dhe tërhiqen përmes një kokte çeliku për t'i paraformuar ato në formën e dëshiruar. Më pas, ata kalojnë përmes një makinerie shërimi të përpunuar me saktësi për të marrë formën e saj përfundimtare. Meqenëse matrica e kurimit nxehet, ajo shëron matricën e rrëshirës. Tërheqësit e tërheqin materialin nëpër kapakë. Duke përdorur bërthama të zbrazëta të futura, ne jemi në gjendje të marrim tuba dhe gjeometri të zbrazëta. Metoda e pultrusionit është e automatizuar dhe na ofron ritme të larta prodhimi. Është e mundur të prodhohet çdo gjatësi produkti. PROCESI I PRODHIMIT TË PREPREG-ut: Prepreg është një përforcues me fibra të vazhdueshme i parangopur me një rrëshirë polimer të pjekur pjesërisht. Përdoret gjerësisht për aplikime strukturore. Materiali vjen në formë shiriti dhe dërgohet si shirit. Prodhuesi e formon atë drejtpërdrejt dhe e kuron plotësisht pa pasur nevojë të shtojë asnjë rrëshirë. Meqenëse prepregati i nënshtrohen reaksioneve të kurimit në temperaturën e dhomës, ato ruhen në temperatura 0 C ose më të ulëta. Pas përdorimit, shiritat e mbetur ruhen përsëri në temperatura të ulëta. Përdoren rrëshira termoplastike dhe termofikse dhe fibrat përforcuese të karbonit, aramidit dhe qelqit janë të zakonshme. Për të përdorur parapregat, fillimisht hiqet letra mbështetëse mbajtëse dhe më pas fabrikimi kryhet duke vendosur shiritin e parapregimit në një sipërfaqe të veglave (procesi i shtrimit). Mund të vendosen disa shtresa për të marrë trashësinë e dëshiruar. Praktika e shpeshtë është alternimi i orientimit të fibrës për të prodhuar një laminat me shtresa të kryqëzuara ose këndore. Së fundi, nxehtësia dhe presioni aplikohen për shërim. Si përpunimi me dorë ashtu edhe proceset e automatizuara përdoren për prerjen e parapregave dhe shtrimin. mbështjellja e FILAMENTIT: Fijet përforcuese të vazhdueshme pozicionohen me saktësi në një model të paracaktuar për të ndjekur një formë të zbrazët dhe zakonisht ciklindirike. Fijet fillimisht kalojnë nëpër një banjë rrëshirë dhe më pas mbështillen në një mandrelë nga një sistem i automatizuar. Pas disa përsëritjeve të mbështjelljes përftohen trashësitë e dëshiruara dhe shërimi kryhet ose në temperaturë dhome ose brenda furrës. Tani mandreli është hequr dhe produkti është çformuar. Dredha-dredha e filamentit mund të ofrojë raporte shumë të larta forcë-peshë duke mbështjellë fibrat në modele rrethore, spirale dhe polare. Tubat, rezervuarët, kafazet prodhohen duke përdorur këtë teknikë. • KOMPOZITET STRUKTURORE: Në përgjithësi këto përbëhen nga materiale homogjene dhe të përbëra. Prandaj vetitë e tyre përcaktohen nga materialet përbërëse dhe dizajni gjeometrik i elementeve të tij. Këtu janë llojet kryesore: KOMPOZITET LAMINAR: Këto materiale strukturore janë bërë nga fletë ose panele dydimensionale me drejtime të preferuara me rezistencë të lartë. Shtresat grumbullohen dhe çimentohen së bashku. Duke alternuar drejtimet e rezistencës së lartë në dy boshtet pingule, marrim një përbërje që ka rezistencë të lartë në të dy drejtimet në rrafshin dydimensional. Duke rregulluar këndet e shtresave mund të prodhohet një përbërje me forcë në drejtimet e preferuara. Ski modern është prodhuar në këtë mënyrë. PANELE SANDWICH: Këto përbërje strukturore janë të lehta, por megjithatë kanë ngurtësi dhe forcë të lartë. Panelet sanduiç përbëhen nga dy fletë të jashtme të bëra nga një material i fortë dhe i fortë si lidhjet e aluminit, plastika e përforcuar me fibra ose çeliku dhe një bërthamë midis fletëve të jashtme. Bërthama duhet të jetë e lehtë dhe shumicën e kohës të ketë një modul të ulët elasticiteti. Materialet kryesore të njohura janë shkume polimerike të ngurtë, druri dhe huall mjalti. Panelet sanduiç përdoren gjerësisht në industrinë e ndërtimit si material për çati, dysheme ose mur, si dhe në industrinë e hapësirës ajrore. • NANOKOMPOSITET: Këto materiale të reja përbëhen nga grimca të përmasave të nanozuara të ngulitura në një matricë. Duke përdorur nanokompozitët, ne mund të prodhojmë materiale gome që janë barriera shumë të mira për depërtimin e ajrit duke ruajtur të pandryshuara vetitë e tyre të gomës. CLICK Product Finder-Locator Service FAQJA E MEPARSHME
- Glass and Ceramic Manufacturing, Hermetic Packages, Seals, Bonding
Glass and Ceramic Manufacturing, Hermetic Packages Seals and Bonding, Tempered Bulletproof Glass, Blow Moulding, Optical Grade Glass, Conductive Glass, Molding Formimi dhe Formimi i Qelqit dhe Qeramikës Lloji i prodhimit të qelqit që ne ofrojmë janë qelqi kontejner, fryrje qelqi, fibra dhe tuba dhe shufra qelqi, enë qelqi shtëpiake dhe industriale, llambë dhe llambë, kallëp qelqi preciz, komponentë dhe montime optike, xhami të sheshtë dhe fletë dhe notues. Ne kryejmë si formimin me dorë ashtu edhe formimin e makinës. Proceset tona të njohura teknike të prodhimit të qeramikës janë presimi, presimi izostatik, presimi i nxehtë izostatik, presimi i nxehtë, derdhja me rrëshqitje, derdhja me shirit, nxjerrja, derdhja me injeksion, përpunimi i gjelbër, sinterizimi ose pjekja, bluarja e diamantit, montimet hermetike. Ne ju rekomandojmë që të klikoni këtu për të SHKARKONI Ilustrimet tona skematike të proceseve të formimit dhe formësimit të qelqit nga AGS-TECH Inc. SHKARKONI Ilustrimet tona Skematike të Proceseve Teknike të Prodhimit të Qeramikës nga AGS-TECH Inc. Këta skedarë të shkarkueshëm me foto dhe skica do t'ju ndihmojnë të kuptoni më mirë informacionin që po ju ofrojmë më poshtë. • PRODHIMI I XHAMIT TË KONTEINERIT: Ne kemi linja të automatizuara PRESS AND BLOW si dhe linja BLOW AND BLOW për prodhim. Në procesin e goditjes dhe fryrjes ne hedhim një gopë në kallëp të zbrazët dhe formojmë qafën duke aplikuar një goditje me ajër të ngjeshur nga lart. Menjëherë pas kësaj, ajri i kompresuar fryhet për herë të dytë nga drejtimi tjetër përmes qafës së kontejnerit për të formuar formën paraprake të shishes. Ky paraformë më pas transferohet në kallëpin aktual, ringrohet për t'u zbutur dhe ajri i ngjeshur aplikohet për t'i dhënë formës së paraformës formën e saj përfundimtare të enës. Në mënyrë më të qartë, ajo është nën presion dhe shtyhet kundër mureve të kavitetit të mykut të fryrjes për të marrë formën e dëshiruar. Së fundi, ena e prodhuar prej qelqi transferohet në një furrë pjekjeje për ringrohjen e mëvonshme dhe heqjen e sforcimeve të prodhuara gjatë derdhjes dhe ftohet në një mënyrë të kontrolluar. Në metodën e shtypjes dhe fryrjes, gomat e shkrirë futen në një kallëp parison (kallëp bosh) dhe shtypen në formën e parisonit (formë boshe). Më pas, boshllëqet transferohen në kallëpe për fryrje dhe fryhen në mënyrë të ngjashme me procesin e përshkruar më sipër nën "Procesi i fryrjes dhe fryrjes". Hapat e mëvonshëm si pjekja dhe lehtësimi i stresit janë të ngjashëm ose të njëjtë. • FRYRJA E GLASS: Ne kemi prodhuar produkte qelqi duke përdorur fryrje konvencionale me dorë si dhe duke përdorur ajër të kompresuar me pajisje të automatizuara. Për disa porosi është e nevojshme fryrja konvencionale, si p.sh. projekte që përfshijnë vepra arti prej xhami, ose projekte që kërkojnë një numër më të vogël pjesësh me toleranca të lirshme, projekte prototipi / demo… etj. Fryrja konvencionale e xhamit përfshin zhytjen e një tubi metalik të zbrazët në një tenxhere me qelq të shkrirë dhe rrotullimin e tubit për mbledhjen e një sasie të materialit qelqi. Xhami i mbledhur në majë të tubit mbështillet në hekur të sheshtë, formësohet sipas dëshirës, zgjatet, nxehet përsëri dhe fryhet me ajër. Kur të jetë gati, futet në një kallëp dhe fryhet ajri. Zgavra e mykut është e lagur për të shmangur kontaktin e xhamit me metalin. Filmi i ujit vepron si një jastëk midis tyre. Fryrja manuale është një proces i ngadalshëm intensiv i punës dhe i përshtatshëm vetëm për prototipa ose artikuj me vlerë të lartë, jo i përshtatshëm për porosi të lira për copë me volum të lartë. • PRODHIMI I ËNDËRVE TË QELQIT SHTETËSORE DHE INDUSTRIALE: Duke përdorur lloje të ndryshme të materialit qelqi, po prodhohet një shumëllojshmëri e madhe e qelqeve. Disa gota janë rezistente ndaj nxehtësisë dhe të përshtatshme për enë qelqi laboratorike, ndërsa disa janë mjaft të mira për t'i bërë ballë lavastoviljeve për shumë herë dhe janë të përshtatshme për prodhimin e produkteve shtëpiake. Duke përdorur makineritë Westlake prodhohen dhjetëra mijëra copë gotash për pije në ditë. Për të thjeshtuar, qelqi i shkrirë mblidhet me vakum dhe futet në kallëpe për të bërë paraformat. Pastaj fryhet ajri në kallëpe, këto transferohen në një kallëp tjetër dhe ajri fryhet përsëri dhe xhami merr formën e tij përfundimtare. Ashtu si në fryrjen me dorë, këto kallëpe mbahen të lagura me ujë. Shtrirja e mëtejshme është pjesë e operacionit të përfundimit ku po formohet qafa. Xhami i tepërt është djegur. Më pas vijon procesi i kontrolluar i rinxehjes dhe ftohjes i përshkruar më sipër. • FORMIMI I TUBEVE DHE SHTYPËVE QELQI: Proceset kryesore që përdorim për prodhimin e tubave të qelqit janë proceset DANNER dhe VELLO. Në procesin Danner, qelqi nga një furre rrjedh dhe bie mbi një mëngë të pjerrët të bërë nga materiale zjarrduruese. Mëngë mbahet në një bosht të zbrazët rrotullues ose tub. Xhami më pas mbështillet rreth mëngës dhe formon një shtresë të lëmuar që rrjedh poshtë mëngës dhe mbi majën e boshtit. Në rastin e formimit të tubit, ajri fryhet përmes një gypi me majë të zbrazët, dhe në rastin e formimit të shufrës ne përdorim maja të forta në bosht. Tubat ose shufrat tërhiqen më pas mbi rulat mbajtës. Dimensionet si trashësia e murit dhe diametri i tubave të qelqit rregullohen në vlerat e dëshiruara duke vendosur diametrin e mëngës dhe duke fryrë presionin e ajrit në një vlerë të dëshiruar, duke rregulluar temperaturën, shpejtësinë e rrjedhjes së xhamit dhe shpejtësinë e tërheqjes. Nga ana tjetër, procesi i prodhimit të tubave të qelqit Vello përfshin qelqin që kalon nga një furrë dhe futet në një tas me një mandrel të zbrazët ose zile. Më pas xhami kalon nëpër hapësirën ajrore midis mandrelit dhe tasit dhe merr formën e një tubi. Më pas ai udhëton mbi rrotulla në një makinë vizatimi dhe ftohet. Në fund të linjës së ftohjes bëhet prerja dhe përpunimi përfundimtar. Dimensionet e tubit mund të rregullohen ashtu si në procesin Danner. Kur krahasojmë procesin Danner me Vello, mund të themi se procesi Vello është më i përshtatshëm për prodhim në sasi të mëdha ndërsa procesi Danner mund të përshtatet më mirë për porositë e sakta të tubave me vëllim më të vogël. • PËRPUNIMI I XHAMIT FLETË & FLAT & FLOAT : Kemi sasi të mëdha xhami të sheshtë në trashësi që variojnë nga trashësia nënmilimetër deri në disa centimetra. Syzet tona të sheshta janë pothuajse të përsosurisë optike. Ofrojmë xhami me veshje speciale si veshje optike, ku përdoret teknika e depozitimit kimik të avullit për vendosjen e veshjeve të tilla si veshje kundër reflektimit ose pasqyrës. Gjithashtu janë të zakonshme veshjet përçuese transparente. Gjithashtu janë të disponueshme veshje hidrofobike ose hidrofile në xhami, dhe veshje që e bën qelqin të pastrohet vetë. Syzet e kalitur, antiplumb dhe të laminuara janë artikuj të tjerë të njohur. Presim gotën në formën e dëshiruar me tolerancat e dëshiruara. Operacione të tjera dytësore si lakimi ose përkulja e xhamit të sheshtë janë të disponueshme. • DERPJES ME XHAM PRECISION: Ne e përdorim këtë teknikë më së shumti për prodhimin e komponentëve optikë me precizion pa pasur nevojë për teknika më të shtrenjta dhe që kërkojnë kohë si bluarja, lakimi dhe lustrimi. Kjo teknikë nuk është gjithmonë e mjaftueshme për të bërë më të mirën e optikës më të mirë, por në disa raste si produktet e konsumit, kamerat dixhitale, optika mjekësore, mund të jetë një opsion i mirë më pak i kushtueshëm për prodhime me volum të lartë. Gjithashtu ka një avantazh ndaj teknikave të tjera të formimit të xhamit ku kërkohen gjeometri komplekse, si në rastin e asferave. Procesi bazë përfshin ngarkimin e pjesës së poshtme të kallëpit tonë me boshllëkun e xhamit, evakuimin e dhomës së procesit për heqjen e oksigjenit, afër mbylljes së kallëpit, ngrohjen e shpejtë dhe izotermale të mbulesës dhe xhamit me dritë infra të kuqe, mbylljen e mëtejshme të gjysmave të kallëpit. për të shtypur ngadalë xhamin e zbutur në mënyrë të kontrolluar në trashësinë e dëshiruar dhe në fund ftohjen e xhamit dhe mbushjen e dhomës me azot dhe heqjen e produktit. Kontrolli i saktë i temperaturës, distanca e mbylljes së mykut, forca e mbylljes së mykut, përputhja e koeficientëve të zgjerimit të materialit të kallëpit dhe qelqit janë çelësi në këtë proces. • PRODHIMI I KOMPONENTEVE DHE MONTETVE OPTIKE TË QELQIT: Përveç formimit të qelqit preciz, ekzistojnë një sërë procesesh të vlefshme që ne përdorim për të bërë komponentë dhe montime optike me cilësi të lartë për aplikime të vështira. Bluarja, mbështjellja dhe lustrimi i gotave të shkallës optike në llucë gërryese speciale të imta është një art dhe shkencë për prodhimin e lenteve optike, prizmave, rrafshët dhe më shumë. Sipërfaqet e sheshta, valëzimi, lëmimi dhe sipërfaqet optike pa defekte kërkojnë shumë përvojë me procese të tilla. Ndryshimet e vogla në mjedis mund të rezultojnë në produkte jashtë specifikimeve dhe të ndalojnë linjën e prodhimit. Ka raste kur një fshirje e vetme në sipërfaqen optike me një leckë të pastër mund të bëjë që një produkt të përmbushë specifikimet ose të dështojë në test. Disa materiale të njohura qelqi të përdorura janë silicë e shkrirë, kuarci, BK7. Gjithashtu, montimi i komponentëve të tillë kërkon përvojë të specializuar në kamare. Ndonjëherë përdoren ngjitës të veçantë. Megjithatë, ndonjëherë një teknikë e quajtur kontakti optik është zgjidhja më e mirë dhe nuk përfshin asnjë material midis syzeve optike të bashkangjitura. Ai përbëhet nga kontakti fizik i sipërfaqeve të sheshta për t'u lidhur me njëra-tjetrën pa ngjitës. Në disa raste, ndarës mekanikë, shufra qelqi precize ose topa, kapëse ose përbërës metalikë të përpunuar përdoren për të montuar komponentët optikë në distanca të caktuara dhe me orientime të caktuara gjeometrike me njëri-tjetrin. Le të shqyrtojmë disa nga teknikat tona të njohura për prodhimin e optikës së nivelit të lartë. BLUARJE DHE LAPOSJE DHE LISTRIM : Forma e përafërt e komponentit optik përftohet me bluarjen e një boshe xhami. Më pas, mbështjellja dhe lustrimi kryhen duke rrotulluar dhe fërkuar sipërfaqet e vrazhda të komponentëve optikë ndaj veglave me format e dëshiruara të sipërfaqes. Llojet me grimca të vogla gërryese dhe lëng po derdhen midis optikës dhe veglave të formësimit. Madhësitë e grimcave gërryese në llucë të tilla mund të zgjidhen sipas shkallës së rrafshësisë së dëshiruar. Devijimet e sipërfaqeve optike kritike nga format e dëshiruara shprehen në termat e gjatësive valore të dritës që përdoret. Optika jonë me precizion të lartë ka toleranca të dhjeta të gjatësisë së valës (Gjatësia e valës/10) ose është e mundur edhe më e ngushtë. Përveç profilit të sipërfaqes, sipërfaqet kritike skanohen dhe vlerësohen për veçori dhe defekte të tjera sipërfaqësore si dimensione, gërvishtje, gërvishtje, gropa, njolla etj. Kontrolli i rreptë i kushteve mjedisore në dyshemenë e prodhimit optik dhe kërkesat e gjera të metrologjisë dhe testimit me pajisjet më të avancuara e bëjnë këtë një degë sfiduese të industrisë. • PROCESET DYTËSORE NË PRODHIMIN E XHAMIT: Përsëri, ne jemi të kufizuar vetëm me imagjinatën tuaj kur bëhet fjalë për proceset dytësore dhe të mbarimit të qelqit. Këtu rendisim disa prej tyre: -Veshje në xhami (optike, elektrike, tribologjike, termike, funksionale, mekanike...). Si shembull, ne mund të ndryshojmë vetitë e sipërfaqes së qelqit duke e bërë atë, për shembull, të reflektojë nxehtësinë në mënyrë që të mbajë ambientet e brendshme të ndërtesave të freskëta, ose të bëjmë njërën anë thithëse infra të kuqe duke përdorur nanoteknologjinë. Kjo ndihmon në mbajtjen e brendshme të ndërtesave të ngrohta, sepse shtresa më e jashtme e sipërfaqes së xhamit do të thithë rrezatimin infra të kuqe brenda ndërtesës dhe do ta rrezatojë atë përsëri në brendësi. -Etching në xhami -Etiketimi i aplikuar i qeramikës (ACL) -Gdhendje -Lustrim me flakë -Lustrim kimik -Ngjyrosje PRODHIM I QERAMIKËS TEKNIKE • DIE PRESSING : Përbëhet nga ngjeshja njëaksiale e pluhurave të grimcuara të kufizuara në një masë • SHTYPJA E NXEHTË: Ngjashëm me shtypjen e lyerjes, por me shtimin e temperaturës për të rritur densifikimin. Pluhuri ose paraforma e ngjeshur vendoset në makinën e grafitit dhe ushtrohet presion njëaksial, ndërsa magazina mbahet në temperatura të larta si 2000 C. Temperaturat mund të jenë të ndryshme në varësi të llojit të pluhurit qeramik që përpunohet. Për forma dhe gjeometri të ndërlikuara mund të nevojiten përpunime të tjera të mëvonshme, si bluarja e diamantit. • SHTYPJA ISOSTATIKE : Pluhuri kokrrizor ose kompaktet e shtypura me prerje vendosen në enë hermetike dhe më pas në një enë presioni të mbyllur me lëng brenda. Më pas ato kompaktohen duke rritur presionin e enës nën presion. Lëngu brenda enës transferon forcat e presionit në mënyrë uniforme në të gjithë sipërfaqen e enës hermetike. Kështu, materiali ngjeshet në mënyrë të njëtrajtshme dhe merr formën e enës së tij fleksibël dhe profilin e tij të brendshëm dhe veçoritë. • SHTYPJA ISOSTATIKE HOT : Ngjashëm me presimin izostatik, por përveç atmosferës së gazit nën presion, ne sinterizojmë kompaktin në temperaturë të lartë. Shtypja e nxehtë izostatike rezulton në densitet shtesë dhe rritje të forcës. • DERDHJE ME RRËSHQITJE / DERDHJE ME KULLIM : Mbushim kallëpin me një suspension grimcash qeramike me madhësi mikrometrash dhe lëng mbartës. Kjo përzierje quhet "rrëshqitje". Myku ka pore dhe për këtë arsye lëngu në përzierje filtrohet në kallëp. Si rezultat, në sipërfaqet e brendshme të kallëpit formohet një gips. Pas sinterimit, pjesët mund të nxirren nga kallëpi. • DERDHJA SHIRIT : Ne prodhojmë shirita qeramike duke hedhur llucë qeramike në sipërfaqe të sheshta mbajtëse lëvizëse. Llurat përmbajnë pluhur qeramike të përzier me kimikate të tjera për qëllime lidhjeje dhe mbajtjeje. Me avullimin e tretësve, lihen fletë të dendura dhe fleksibël qeramike, të cilat mund të priten ose rrotullohen sipas dëshirës. • FORMIMI ME EKSTRUZION : Ashtu si në proceset e tjera të nxjerrjes, një përzierje e butë pluhuri qeramike me lidhës dhe kimikate të tjera kalohet përmes një forme për të marrë formën e saj të prerjes tërthore dhe më pas pritet në gjatësinë e dëshiruar. Procesi kryhet me përzierje qeramike të ftohta ose të ngrohura. • MOLDIMI ME INJEKT ME PRIRJE TË ULËT: Ne përgatisim një përzierje pluhuri qeramike me lidhës dhe tretës dhe e ngrohim në një temperaturë ku mund të shtypet lehtësisht dhe të futet me forcë në zgavrën e veglës. Pasi të përfundojë cikli i formimit, pjesa nxirret dhe kimikati lidhës digjet. Duke përdorur formimin me injeksion, ne mund të marrim pjesë të ndërlikuara në vëllime të larta ekonomikisht. Vrimat që janë një pjesë e vogël e milimetrit në një mur me trashësi 10 mm janë të mundshme, fijet janë të mundshme pa përpunim të mëtejshëm, toleranca aq të ngushta sa +/- 0,5% janë të mundshme dhe madje edhe më të ulëta kur pjesët janë të përpunuara , trashësi muri në rendin nga 0,5 mm deri në një gjatësi prej 12,5 mm janë të mundshme si dhe trashësi muri nga 6,5 mm deri në një gjatësi prej 150 mm. • MAKINIMI I GJELBËR : Duke përdorur të njëjtat vegla përpunimi metalik, ne mund të përpunojmë materiale qeramike të shtypura ndërsa ato janë ende të buta si shkumësa. Tolerancat prej +/- 1% janë të mundshme. Për toleranca më të mira ne përdorim bluarjen e diamantit. • SINTERING ose QYRJE : Sinterizimi bën të mundur densifikimin e plotë. Ndodh tkurrje e konsiderueshme në pjesët kompakte jeshile, por ky nuk është një problem i madh pasi ne marrim parasysh këto ndryshime dimensionale kur projektojmë pjesën dhe veglat. Grimcat e pluhurit janë të lidhura së bashku dhe poroziteti i shkaktuar nga procesi i ngjeshjes hiqet në masë të madhe. • BLUARJA ME DIAMAND: Materiali më i fortë në botë “diamanti” po përdoret për bluarjen e materialeve të forta si qeramika dhe përftohen pjesë precize. Po arrihen toleranca në diapazonin e mikrometrave dhe sipërfaqe shumë të lëmuara. Për shkak të shpenzimeve të saj, ne e konsiderojmë këtë teknikë vetëm kur na nevojitet vërtet. • MBLEDHJE HERMETIKE janë ato që praktikisht nuk lejojnë asnjë shkëmbim të lëndëve, lëndëve të ngurta, lëngjeve ose gazeve ndërmjet ndërfaqeve. Mbyllja hermetike është hermetike. Për shembull, mbylljet elektronike hermetike janë ato që mbajnë përmbajtjen e brendshme të ndjeshme të një pajisjeje të paketuar të padëmtuar nga lagështia, ndotësit ose gazrat. Asgjë nuk është 100% hermetike, por kur flasim për hermeticitet, nënkuptojmë që në terma praktikë, ka hermeticitet në atë masë sa shkalla e rrjedhjeve është aq e ulët saqë pajisjet janë të sigurta në kushte normale mjedisore për një kohë shumë të gjatë. Asambletë tona hermetike përbëhen nga metal, qelq dhe përbërës qeramikë, metal-qeramikë, qeramikë-metal-qeramikë, metal-qeramikë-metal, metal në metal, metal-xham, metal-xham-metal, qelq-metal-xham, qelq- metali dhe qelqi me qelqin dhe të gjitha kombinimet e tjera të lidhjes metal-qelq-qeramike. Për shembull, ne mund t'i lyejmë përbërësit prej qeramike metalike në mënyrë që ato të mund të lidhen fort me komponentët e tjerë në montim dhe të kenë aftësi të shkëlqyera vulosjeje. Ne kemi njohurinë e veshjes së fibrave optike ose hyrjeve me metal dhe saldimit ose ngjitjes së tyre me mbyllje, kështu që asnjë gaz të mos kalojë ose rrjedhë në mbyllje. Prandaj ato përdoren për prodhimin e mbylljeve elektronike për të kapsuluar pajisjet e ndjeshme dhe për t'i mbrojtur ato nga atmosfera e jashtme. Përveç karakteristikave të tyre të shkëlqyera të vulosjes, veçori të tjera si koeficienti i zgjerimit termik, rezistenca ndaj deformimit, natyra jo-gazuese, jetëgjatësia shumë e gjatë, natyra jopërçuese, vetitë termoizoluese, natyra antistatike...etj. bëjnë qelqin dhe materialet qeramike zgjedhjen për aplikime të caktuara. Informacioni mbi objektin tonë që prodhon pajisje qeramike në metal, vulosje hermetike, hyrje vakumi, komponentë të kontrollit të vakumit të lartë dhe tepër të lartë dhe lëngjeve mund të gjenden këtu:Broshura Hermetic Components Factory CLICK Product Finder-Locator Service FAQJA E MEPARSHME
- Wire & Spring Forming, Shaping, Welding, Assembly of Wires, Coil, CNC
Wire & Spring Forming, Shaping, Welding, Assembly of Wires, Coil Compression Extension Torsion Flat Springs, Custom Wires, Helical Springs at AGS-TECH Inc. Formimi i telave dhe sustave Ne prodhojmë tela me porosi, montim teli, tela të formuar në format e dëshiruara 2D dhe 3D, rrjeta teli, rrjetë, rrethime, shportë, gardh, susta teli, susta të sheshta; përdredhje, ngjeshje, tension, susta të sheshta dhe më shumë. Proceset tona janë formimi i telave dhe sustave, tërheqja e telit, formësimi, përkulja, saldimi, ngjitja, saldimi, shpimi, lëmimi, shpimi, gërshetimi, bluarja, filetimi, veshja, katërrrëshqitja, formimi i rrëshqitjes, mbështjellja, mbështjellja, prishja. Ne ju rekomandojmë që të klikoni këtu për të SHKARKONI Ilustrimet tona Skematike të Proceseve të Formimit të Telit dhe Pranverës nga AGS-TECH Inc. Ky skedar i shkarkueshëm me foto dhe skica do t'ju ndihmojë të kuptoni më mirë informacionin që po ju ofrojmë më poshtë. • VIZATIM ME TELA: Duke përdorur forcat tërheqëse, ne e shtrijmë stokun e metalit dhe e tërheqim atë përmes një diametër për të zvogëluar diametrin dhe për të rritur gjatësinë e tij. Ndonjëherë ne përdorim një seri magazinash. Ne jemi të aftë të bëjmë makineri për çdo matës teli. Duke përdorur materiale me rezistencë të lartë në tërheqje, ne tërheqim tela shumë të hollë. Ofrojme tela te punuar me te ftohte dhe te nxehte. • FORMIMI I TELIVE: Një rrotull teli me matës përkulet dhe formohet në një produkt të dobishëm. Ne kemi aftësinë për të formuar tela nga të gjitha matësit, duke përfshirë filamente të holla si dhe tela të trashë si ato që përdoren si susta nën shasinë e automobilave. Pajisjet që përdorim për formimin e telave janë formuesit manual dhe CNC teli, mbështjellës, presa me fuqi, katërrrëshqitës, shumërrëshqitës. Proceset tona janë vizatimi, përkulja, drejtimi, rrafshimi, shtrirja, prerja, prishja, saldimi dhe saldimi dhe ngjitja, montimi, mbështjellja, lëkundja (ose krahët), shpimi, filetimi i telit, shpimi, zbërthimi, bluarja, veshja dhe trajtimet sipërfaqësore. Pajisjet tona më të avancuara mund të vendosen për të zhvilluar dizajne shumë komplekse të çdo forme dhe toleranca të ngushta. Ne ofrojmë skaje të ndryshme të skajeve si skajet sferike, të mprehta ose të zbehta për telat tuaja. Shumica e projekteve tona të formimit të telit kanë kosto minimale deri në zero për vegla pune. Kohët e kthimit të mostrës janë përgjithësisht ditë. Ndryshimet në dizajnin/konfigurimin e formave të telit mund të bëhen shumë shpejt. • SPRING FORMING: AGS-TECH prodhon një shumëllojshmëri të madhe sustash duke përfshirë: -Torsion / Double Torsion Spring -Tensioni / Pranvera e ngjeshjes -Pranvera konstante / e ndryshueshme -Spirale & Pranga spirale - Spring & Leaf Spring -Bilanci i pranverës -Rondele Belleville -Pranvera mohuese -Spire spirale me normë progresive - Pranvera e valës -Volute Pranvera - Burimet e ngushta -Unaza pranverore -Shat Springs -Klipe Ne prodhojmë susta nga një shumëllojshmëri materialesh dhe mund t'ju udhëzojmë sipas aplikimit tuaj. Materialet më të zakonshme janë çelik inox, krom silikon, çeliku me karbon të lartë, vaj me karbon të ulët, krom vanadium, fosfor bronzi, titani, aliazh bakri berilium, qeramika me temperaturë të lartë. Ne përdorim teknika të ndryshme në prodhimin e sustave, duke përfshirë mbështjelljen me CNC, mbështjelljen e ftohtë, mbështjelljen e nxehtë, forcimin, përfundimin. Teknika të tjera të përmendura më lart në formimin e telit janë gjithashtu të zakonshme në operacionet tona të prodhimit të pranverës. • SHËRBIMET E PËRFUNDIMIT për TELA DHE SUSTA: Ne mund t'i përfundojmë produktet tuaja në shumë mënyra në varësi të zgjedhjes dhe nevojave tuaja. Disa procese të zakonshme që ne ofrojmë janë: lyerja, lyerja me pluhur, lyerja, zhytja e vinylit, anodizimi, lehtësimi i stresit, trajtimi me nxehtësi, shkrirja me llak, rrëshqitja, kromati, nikel pa elektro, pasivimi, plastika. , pastrimi i plazmës. CLICK Product Finder-Locator Service FAQJA E MEPARSHME
- Forging and Powdered Metallurgy, Die Forging, Heading, Hot Forging
Forging and Powdered Metallurgy, Die Forging, Heading, Hot Forging, Impression Die, Near Net Shape, Swaging, Metal Hobbing, Riveting, Coining from AGS-TECH Inc. Formëzimi i Metaleve dhe Metalurgjia e Pluhurit Lloji i proceseve të FARKESËS SË METALIVE që ne ofrojmë janë mallëra të nxehtë dhe të ftohtë, mbulesë e hapur dhe e mbyllur, farkë për shtypje dhe falsifikim pa ndezje, cogging, mbushje, bordurë dhe farkëtim preciz, thuajse rrjetë- , lëkundje, falsifikim i mërzitur, prerje metalike, shtypje dhe rrotullim dhe falsifikim radial dhe orbital dhe unazor dhe izotermik, prerje, thumba, falsifikim me top metalik, shpim metali, përmasa, falsifikim me shkallë të lartë energjie. Teknikat tona të METALURGJISË TË PLUHURIT dhe PËRPUNIMIT TË PLUHURIT janë presimi dhe sinterimi i pluhurit, impregnimi, infiltrimi, presimi izostatik i nxehtë dhe i ftohtë, derdhja me injeksion metalik, ngjeshja me rrotull, rrotullimi i pluhurit, nxjerrja e pluhurit, sinterizimi i lirë, sinterimi me shkëndijë, shtypja e nxehtë. Ne ju rekomandojmë që të klikoni këtu për të SHKARKO Ilustrimet tona skematike të proceseve të falsifikimit nga AGS-TECH Inc. SHKARKO Ilustrimet tona skematike të proceseve të metalurgjisë së pluhurit nga AGS-TECH Inc. Këta skedarë të shkarkueshëm me foto dhe skica do t'ju ndihmojnë të kuptoni më mirë informacionin që po ju ofrojmë më poshtë. Në farkëtimin e metaleve aplikohen forca shtypëse dhe deformohet materiali dhe fitohet forma e dëshiruar. Materialet më të zakonshme të falsifikuara në industri janë hekuri dhe çeliku, por shumë të tjerë si alumini, bakri, titani, magnezi janë gjithashtu të falsifikuara gjerësisht. Pjesët metalike të falsifikuara kanë struktura të përmirësuara të kokrrizave përveç çarjeve të mbyllura dhe hapësirave boshe të mbyllura, kështu që forca e pjesëve të përftuara nga ky proces është më e lartë. Formëzimi prodhon pjesë që janë dukshëm më të forta për peshën e tyre sesa pjesët e bëra nga derdhja ose përpunimi. Meqenëse pjesët e falsifikuara formohen duke bërë që metali të rrjedhë në formën e tij përfundimtare, metali merr një strukturë kokrrizë të drejtuar që llogarit forcën superiore të pjesëve. Me fjalë të tjera, pjesët e marra nga procesi i falsifikimit zbulojnë veti më të mira mekanike në krahasim me pjesët e thjeshta të derdhura ose të përpunuara. Pesha e farkëtimeve metalike mund të variojë nga pjesë të vogla të lehta deri në qindra mijëra paund. Ne prodhojmë falsifikime kryesisht për aplikime kërkuese mekanike ku sforcime të larta aplikohen në pjesë të tilla si pjesë automobilistike, ingranazhe, vegla pune, vegla dore, boshte turbinash, pajisje për motoçikleta. Për shkak se kostot e veglave dhe vendosjes janë relativisht të larta, ne e rekomandojmë këtë proces prodhimi vetëm për prodhim me volum të lartë dhe për komponentë kritikë me volum të ulët por me vlerë të lartë, siç janë pajisjet e uljes së hapësirës ajrore. Përveç kostos së veglave, kohëzgjatja e prodhimit për pjesë të farkëtuara në sasi të mëdha mund të jetë më e gjatë në krahasim me disa pjesë të thjeshta të përpunuara, por teknika është thelbësore për pjesët që kërkojnë forcë të jashtëzakonshme si bulonat, dadot, aplikim të veçantë, kapëse, automobila, forklift, pjesë vinçi. • FALLKIM ME METARE NË NXHET dhe FTOHTË : Formëzimi me llaç të nxehtë, siç nënkupton edhe emri, kryhet në temperatura të larta, prandaj duktiliteti është i lartë dhe forca e materialit të ulët. Kjo lehtëson deformimin dhe falsifikimin e lehtë. Përkundrazi, farkëtimi i ftohjes kryhet në temperatura më të ulëta dhe kërkon forca më të larta që rezulton në forcimin e sforcimeve, përfundimin më të mirë të sipërfaqes dhe saktësinë e pjesëve të prodhuara. • FALKSIONIMI I MURAVE TË HAPUR dhe MIRË MBROJTJES: Në falsifikimin e hapur me kësulë, kokrrat nuk e kufizojnë materialin që kompresohet, ndërsa në farkëtimin e mbulesës së impresionit, zgavrat brenda kokrrave kufizojnë rrjedhën e materialit ndërkohë që farkëtohet në formën e dëshiruar. FALKESIMI I SHPËRNDARJES ose i quajtur edhe UPSETTING, i cili në fakt nuk është i njëjti, por një proces shumë i ngjashëm, është një proces i hapur ku pjesa e punës vendoset midis dy kapave të sheshta dhe një forcë shtypëse zvogëlon lartësinë e saj. Ndërsa lartësia është reduced, gjerësia e pjesës së punës rritet. HEADING, një proces falsifikimi i prishur përfshin stokun cilindrik që prishet në fund dhe seksioni kryq i tij rritet në nivel lokal. Në krye, stoku ushqehet përmes kësulës, falsifikohet dhe më pas pritet në gjatësi. Operacioni është i aftë të prodhojë me shpejtësi sasi të mëdha fiksuese. Kryesisht është një operacion pune në të ftohtë, sepse përdoret për të bërë majat e thonjve, skajet e vidhave, dadot dhe bulonat ku materiali duhet të forcohet. Një tjetër proces i hapur i prerjes është COGGING, ku pjesa e punës farkëtohet në një seri hapash me secilin hap që rezulton në ngjeshjen e materialit dhe lëvizjen e mëvonshme të mbulesës së hapur përgjatë gjatësisë së pjesës së punës. Në çdo hap, trashësia zvogëlohet dhe gjatësia rritet me një sasi të vogël. Procesi i ngjan një studenti nervoz që kafshon lapsin gjatë gjithë kohës me hapa të vegjël. Një proces i quajtur FULLERING është një tjetër metodë tjetër e falsifikimit të hapur, që ne shpesh e përdorim si një hap më parë për të shpërndarë materialin në pjesën e punës përpara se të kryhen operacione të tjera të falsifikimit të metaleve. Ne e përdorim atë kur pjesa e punës kërkon disa operacione forging . Gjatë operimit, shufrat me sipërfaqe konvekse deformohen dhe shkaktojnë rrjedhje metalike në të dy anët. Një proces i ngjashëm me mbushjen e plotë, EDGING nga ana tjetër përfshin mbulimin e hapur me sipërfaqe konkave për të deformuar pjesën e punës. Krahja gjithashtu një proces përgatitor për operacionet e mëvonshme të falsifikimit bën që materiali të rrjedhë nga të dyja anët në një zonë në qendër. IMPRESSION DIE FORGING ose CLOSED DIE FORGING siç quhet edhe përdor një kërpudhë/kallëp që ngjesh materialin dhe kufizon rrjedhjen e tij brenda vetes. Mbulesa mbyllet dhe materiali merr formën e zgavrës së kallëpit / mykut. FALKSIMI I PAKESËT, një proces që kërkon pajisje dhe myk të posaçëm, prodhon pjesë pa blic ose shumë pak. Me fjalë të tjera, pjesët do të kenë përmasa afërsisht përfundimtare. Në këtë proces një sasi e mirë kontrolluar materiali futet me kujdes dhe vendoset brenda kallëpit. Ne e përdorim këtë metodë për forma komplekse me seksione të holla, toleranca të vogla dhe kënde të tërheqjes dhe kur sasitë janë mjaft të mëdha për të justifikuar kostot e kallëpit dhe pajisjeve. • FALKSIM PA FLAKSIM : Pjesa e punës vendoset në mallë në mënyrë të tillë që asnjë material të mos mund të rrjedhë nga zgavra për të formuar blic. Prandaj, nuk nevojitet prerje e padëshiruar e blicit. Është një proces falsifikimi preciz dhe prandaj kërkon kontroll të ngushtë të sasisë së materialit të përdorur. • LËNDËSIMI I METALIVE ose FALKESIMI RADIALE : Një pjesë e punës ndikohet në mënyrë rrethore nga magazina dhe falsifikimi. Një mandrelë mund të përdoret gjithashtu për të falsifikuar gjeometrinë e pjesës së brendshme të punës. Në operacionin e lëkundjes, pjesa e punës zakonisht merr disa goditje në sekondë. Artikujt tipikë të prodhuar nga lëkundja janë veglat me majë, shufrat me konik, kaçavidat. • SHPIM METAL: Ne e përdorim këtë operacion shpesh si një operacion shtesë në prodhimin e pjesëve. Një vrimë ose zgavër krijohet me shpim në sipërfaqen e pjesës së punës pa e thyer atë. Ju lutemi vini re se shpimi është i ndryshëm nga shpimi, i cili rezulton në një vrimë. • HOBING : Një grusht me gjeometrinë e dëshiruar shtypet në pjesën e punës dhe krijon një zgavër me formën e dëshiruar. Ne e quajmë këtë goditje një HOB. Operacioni përfshin presione të larta dhe kryhet në të ftohtë. Si rezultat, materiali punohet në të ftohtë dhe ngurtësohet. Prandaj, ky proces është shumë i përshtatshëm për prodhimin e kallëpeve, kallëpeve dhe zgavrave për procese të tjera të prodhimit. Pasi të jetë prodhuar pianurja, mund të prodhohen lehtësisht shumë zgavra identike pa qenë nevoja t'i përpunoni ato një nga një. • FORMIMI ROLL ose FORMIMI ROLL: Përdoren dy rrotulla të kundërta për t'i dhënë formë pjesës metalike. Pjesa e punës futet në rrotulla, rrotullat kthehen dhe e tërheqin veprën në boshllëk, më pas puna futet përmes pjesës me brazdë të rrotullave dhe forcat e shtypjes i japin materialit formën e dëshiruar. Nuk është një proces rrotullimi, por një proces falsifikimi, sepse është një operacion diskret dhe jo i vazhdueshëm. Gjeometria në korijet e rrotullave forcon materialin në formën dhe gjeometrinë e kërkuar. Ajo kryhet e nxehtë. Për shkak se është një proces falsifikimi, ai prodhon pjesë me veti mekanike të jashtëzakonshme dhe për këtë arsye ne e përdorim atë për manufacturing pjesëve të automobilave si boshtet që duhet të kenë qëndrueshmëri të jashtëzakonshme në mjedise të vështira pune. • FALKESIMI ORBITAL: Pjesa e punës vendoset në një zgavër të farkëtimit dhe farkëtohet nga një mallë e sipërme që udhëton në një rrugë orbitale ndërsa rrotullohet në një bosht të pjerrët. Në çdo rrotullim, koka e sipërme përfundon duke ushtruar forca shtypëse në të gjithë pjesën e punës. Duke i përsëritur këto rrotullime disa herë, kryhet falsifikim i mjaftueshëm. Përparësitë e kësaj teknike të prodhimit janë funksionimi i saj me zhurmë të ulët dhe forcat më të ulëta të nevojshme. Me fjalë të tjera, me forca të vogla, mund të rrotullohet një kaldajë e rëndë rreth një boshti për të ushtruar presione të mëdha në një pjesë të pjesës së punës që është në kontakt me makinen. Pjesët në formë disku ose konike janë ndonjëherë një përshtatje e mirë për këtë proces. • FALKESIMI I unazave: Ne përdorim shpesh për të prodhuar unaza pa probleme. Stoku pritet në gjatësi, mërzitet dhe më pas shpohet deri në fund për të krijuar një vrimë qendrore. Më pas vendoset në një mandrelë dhe një fortesë farkëtimi e godet me çekiç nga lart ndërsa unaza rrotullohet ngadalë derisa të fitohen dimensionet e dëshiruara. • RIVETIMI: Një proces i zakonshëm për bashkimin e pjesëve, fillon me një copë metalike të drejtë të futur në vrima të bëra paraprakisht nëpër pjesë. Më pas, të dy skajet e pjesës metalike farkëtohen duke shtrydhur nyjën midis një mbulese të sipërme dhe të poshtme. • MIDHJA : Një tjetër proces popullor i kryer nga shtypja mekanike, duke ushtruar forca të mëdha në një distancë të shkurtër. Emri "coining" vjen nga detajet e imëta që falsifikohen në sipërfaqet e monedhave metalike. Kryesisht është një proces përfundimi për një produkt ku detajet e imta përftohen në sipërfaqe si rezultat i forcës së madhe të aplikuar nga dieta që i transferon këto detaje në pjesën e punës. • FALKESIM ME TOPA METAL: Produkte të tilla si kushinetat e topit kërkojnë topa metalikë me cilësi të lartë, të prodhuara saktësisht. Në një teknikë të quajtur SKEW ROLLING, ne përdorim dy rrotulla të kundërta që rrotullohen vazhdimisht ndërsa stoku futet vazhdimisht në rrotulla. Në njërin skaj të dy rrotullave si produkt nxirren sfera metalike. Një metodë e dytë për falsifikimin e topave të metalit është përdorimi i mbulesës që shtrydh materialin e vendosur midis tyre duke marrë formën sferike të zgavrës së mykut. Shpesh topat e prodhuar kërkojnë disa hapa shtesë si përfundimi dhe lustrimi në mënyrë që të bëhen një produkt me cilësi të lartë. • FALKSIONIMI IZOTERMAL / FALKSIONIMI I NXEHTË ME DIES: Një proces i shtrenjtë që kryhet vetëm kur vlera e përfitimit/kostos është e justifikuar. Një proces i nxehtë pune, ku specat nxehen në të njëjtën temperaturë si pjesa e punës. Meqenëse të dy formatet dhe puna janë afërsisht të njëjtën temperaturë, nuk ka ftohje dhe karakteristikat e rrjedhës së metalit janë përmirësuar. Operacioni është i përshtatshëm për super aliazhet dhe materialet me falsifikim inferior dhe materialet who vetitë mekanike janë shumë të ndjeshme ndaj gradientëve dhe ndryshimeve të vogla të temperaturës. • RREGULLIMI I METALIT : Është një proces i ftohtë përfundimi. Rrjedha e materialit është e pakufizuar në të gjitha drejtimet me përjashtim të drejtimit në të cilin zbatohet forca. Si rezultat, fitohen përfundime shumë të mira të sipërfaqes dhe dimensione të sakta. • FALKESIM ME SHPËLSI TË LARTË ENERGJIKE: Teknika përfshin një kallëp të sipërm të ngjitur në krahun e një pistoni që shtyhet me shpejtësi ndërsa një përzierje karburant-ajër ndizet nga një kandele. I ngjan funksionimit të pistonëve në një motor makine. Forma godet pjesën e punës shumë shpejt dhe më pas kthehet në pozicionin e saj origjinal shumë shpejt falë presionit të kundërt. Puna farkëtohet brenda pak milisekondave dhe për këtë arsye nuk ka kohë që puna të ftohet. Kjo është e dobishme për pjesët e vështira për t'u falsifikuar që kanë veti mekanike shumë të ndjeshme ndaj temperaturës. Me fjalë të tjera, procesi është aq i shpejtë sa që pjesa formohet nën temperaturë konstante gjatë gjithë kohës dhe nuk do të ketë gradient të temperaturës në ndërfaqet e kallëpit/pjesës së punës. • Në DIE FORGING, metali rrihet midis dy blloqeve të çelikut që përputhen me forma të veçanta në to, të quajtura llamba. Kur metali goditet me çekiç në mes të kapave, ai merr të njëjtën formë si format në matrikë. Kur të arrijë formën përfundimtare, nxirret për t'u ftohur. Ky proces prodhon pjesë të forta që janë të një forme precize, por kërkon një investim më të madh për matricat e specializuara. Falsifikimi i mërzitur rrit diametrin e një pjese metali duke e rrafshuar atë. Përdoret përgjithësisht për të bërë pjesë të vogla, veçanërisht për të formuar koka në mbërthyes si bulona dhe gozhdë. • METALURGJIA E PLUHURAVE / PËRPUNIMI I PLUHURAVE: Siç nënkupton edhe emri, ai përfshin proceset e prodhimit për prodhimin e pjesëve të forta të gjeometrive dhe formave të caktuara nga pluhurat. Nëse përdoren pluhurat metalikë për këtë qëllim është sfera e metalurgjisë së pluhurit dhe nëse përdoren pluhurat jometalorë është përpunimi i pluhurit. Pjesët e ngurta prodhohen nga pluhurat duke shtypur dhe sinterizuar. POWDER PRESSING përdoret për të kompaktuar pluhurat në format e dëshiruara. Së pari, materiali parësor është pluhur fizikisht, duke e ndarë atë në shumë grimca të vogla individuale. Përzierja e pluhurit mbushet në formë dhe një grusht lëviz drejt pluhurit dhe e ngjesh atë në formën e dëshiruar. Kryesisht kryhet në temperaturën e dhomës, me shtypje pluhuri fitohet një pjesë e fortë dhe quhet kompakt jeshil. Lidhësit dhe lubrifikantët përdoren zakonisht për të rritur kompaktueshmërinë. Ne jemi në gjendje të formojmë presa pluhuri duke përdorur presa hidraulike me kapacitet disa mijëra ton. Gjithashtu kemi presa me veprim të dyfishtë me goditje të kundërta nga lart dhe poshtë, si dhe presa me veprim të shumëfishtë për gjeometri shumë komplekse të pjesëve. Uniformiteti i cili është një sfidë e rëndësishme për shumë fabrika të metalurgjisë së pluhurit/përpunimit të pluhurit nuk është problem i madh për AGS-TECH për shkak të përvojës sonë të gjerë në prodhimin me porosi të pjesëve të tilla për shumë vite. Edhe me pjesët më të trasha ku uniformiteti përbën një sfidë ne ia kemi dalë. Nëse angazhohemi për projektin tuaj, ne do të bëjmë pjesët tuaja. Nëse shohim ndonjë rrezik të mundshëm, do t'ju informojmë in avanconi. SINTERING PLUHURI, që është hapi i dytë, përfshin ngritjen e temperaturës në një shkallë të caktuar dhe ruajtjen e temperaturës në atë nivel për një kohë të caktuar në mënyrë që grimcat e pluhurit në pjesën e shtypur të mund të lidhen së bashku. Kjo rezulton në lidhje shumë më të forta dhe forcimin e pjesës së punës. Sinterizimi bëhet afër temperaturës së shkrirjes së pluhurit. Gjatë sinterimit do të ndodhë tkurrja, forca e materialit, dendësia, duktiliteti, përçueshmëria termike, përçueshmëria elektrike rriten. Ne kemi furra seri dhe të vazhdueshme për sinterim. Një nga aftësitë tona është rregullimi i nivelit të porozitetit të pjesëve që prodhojmë. Për shembull, ne jemi në gjendje të prodhojmë filtra metalikë duke i mbajtur pjesët poroze deri në një farë mase. Duke përdorur një teknikë të quajtur IMPREGNATION, ne mbushim poret në metal me një lëng si vaji. Ne prodhojmë për shembull kushineta të ngopura me vaj që janë vetë-lubrifikuese. Në procesin e INFILTRIMIT mbushim poret e një metali me një metal tjetër me pikë shkrirjeje më të ulët se materiali bazë. Përzierja nxehet në një temperaturë ndërmjet temperaturave të shkrirjes së dy metaleve. Si rezultat, mund të merren disa veti të veçanta. Ne gjithashtu kryejmë shpesh operacione dytësore të tilla si përpunimi dhe farkëtimi në pjesët e prodhuara nga pluhuri kur duhen marrë veçori ose veçori të veçanta ose kur pjesa mund të prodhohet me më pak hapa të procesit. SHTYPJA ISOSTATIKE: Në këtë proces presioni i lëngut përdoret për të kompaktuar pjesën. Pluhurat metalike vendosen në një kallëp të bërë nga një enë fleksibël e mbyllur. Në presimin izostatik, presioni aplikohet nga e gjithë rrethi, në kundërshtim me presionin aksial që shihet në presimin konvencional. Përparësitë e presimit izostatik janë dendësia uniforme brenda pjesës, veçanërisht për pjesët më të mëdha ose më të trasha, veti superiore. Disavantazhi i tij është koha e gjatë e ciklit dhe saktësia gjeometrike relativisht e ulët. SHTYPJA ISOSTATIKE E FTOHTË kryhet në temperaturën e dhomës dhe kallëpi fleksibël është prej gome, PVC ose uretani ose materiale të ngjashme. Lëngu që përdoret për presion dhe ngjeshje është vaji ose uji. Sinterimi konvencional i kompaktës së gjelbër pason këtë. SHTYPJA ISOSTATIKE HOT nga ana tjetër kryhet në temperatura të larta dhe materiali i kallëpit është fletë metalike ose qeramike me pikë shkrirjeje mjaft të lartë që i reziston temperaturave. Lëngu nën presion është zakonisht një gaz inert. Veprimet e presimit dhe sinterizimit kryhen në një hap. Poroziteti është eliminuar pothuajse plotësisht, fitohet një strukturë uniforme grin. Avantazhi i presimit izostatik të nxehtë është se mund të prodhojë pjesë të krahasueshme me derdhjen dhe farkëtimin e kombinuar, ndërkohë që bën të mundshme për t'u përdorur materiale që nuk janë të përshtatshme për derdhje dhe falsifikim. Disavantazhi i presimit izostatik të nxehtë është koha e lartë e ciklit dhe për rrjedhojë kostoja. Është i përshtatshëm për pjesë kritike me volum të ulët. DERDIMI ME INJEKTIM METAL: Proces shumë i përshtatshëm për prodhimin e pjesëve komplekse me mure të hollë dhe gjeometri të detajuara. Më e përshtatshme për pjesë të vogla. Pluhurat dhe lidhësi polimer përzihen, nxehen dhe injektohen në një kallëp. Lidhësi polimer mbulon sipërfaqet e grimcave të pluhurit. Pas formimit, lidhësi hiqet ose me ngrohje në temperaturë të ulët të tretur duke përdorur një tretës. NGËSHTJA E ROLLIT / RRETULLI ME PLUHUR : Pluhurat përdoren për të prodhuar shirita ose fletë të vazhdueshme. Pluhuri ushqehet nga një ushqyes dhe ngjeshet nga dy rrotulla rrotulluese në fletë ose shirita. Operacioni kryhet i ftohtë. Fleta bartet në një furrë sinterimi. Procesi i sinterizimit mund të përsëritet për herë të dytë. Nxjerrja me pluhur: Pjesët me raport të madh gjatësi ndaj diametrit prodhohen duke ekstruduar një enë të hollë llamarine me pluhur. SINTERIMI I LIRË: Siç nënkupton edhe emri, është një metodë ngjeshjeje dhe sinterimi pa presion, e përshtatshme për prodhimin e pjesëve shumë poroze si filtra metalikë. Pluhuri futet në zgavrën e kallëpit pa u ngjeshur. SINTERIMI I LIRË: Siç nënkupton edhe emri, është një metodë ngjeshjeje dhe sinterimi pa presion, e përshtatshme për prodhimin e pjesëve shumë poroze si filtra metalikë. Pluhuri futet në zgavrën e kallëpit pa u ngjeshur. SINTERING SPARK: Pluhuri është i ngjeshur në kallëp nga dy grushta të kundërta dhe një rrymë elektrike me fuqi të lartë aplikohet në shpuese dhe kalon nëpër pluhurin e ngjeshur të vendosur në mes tyre. Rryma e lartë djeg filmat sipërfaqësorë nga grimcat e pluhurit dhe i sinton ato me nxehtësinë e krijuar. Procesi është i shpejtë sepse nxehtësia nuk aplikohet nga jashtë, por përkundrazi gjenerohet nga brenda kallëpit. SHTYPJA E Nxehtë: Pluhurat shtypen dhe sinterohen në një hap të vetëm në një kallëp që mund t'i rezistojë temperaturave të larta. Me kompaktimin e matricës, nxehtësia e pluhurit aplikohet në të. Saktësia e mirë dhe vetitë mekanike të arritura me këtë metodë e bëjnë atë një opsion tërheqës. Edhe metalet zjarrduruese mund të përpunohen duke përdorur materiale myk si grafiti. CLICK Product Finder-Locator Service MENUA E MËPARSHME
- Sheet Metal Forming Fabrication, Stamping, Punching, Deep Drawing, CNC
Sheet Metal Forming and Fabrication, Stamping, Punching, Bending, Progressive Die, Spot Welding, Deep Drawing, Metal Blanking and Slitting at AGS-TECH Inc. Stampime & Fabrikim llamarine Ne ofrojmë stampim, formësimin, formimin, përkuljen, shpimin, zbrazjen, prerjen, shpimin, prerjen, gërvishtjen, rruajtjen, shtypjen, fabrikimin, vizatimin e thellë duke përdorur kapakë me një grusht / një goditje të vetme, si dhe shufra progresive dhe tjerrje, formim gome dhe hidroformim; prerje llamarine duke përdorur rrymë uji, plazma, lazer, sharrë, flakë; montim fletë metalike duke përdorur saldim, saldim në vend; tubi i llamarinës që fryhet dhe përkulet; Mbarimi i sipërfaqes së llamarinës duke përfshirë lyerjen me zhytje ose spërkatje, veshje elektrostatike me pluhur, anodizim, lyerje, spërkatje dhe më shumë. Shërbimet tona variojnë nga prototipi i shpejtë i llamarinës deri tek prodhimi me volum të lartë. Ne ju rekomandojmë që të klikoni këtu për tëSHKARKONI Ilustrimet tona skematike të proceseve të fabrikimit dhe stampimit të llamarinës nga AGS-TECH Inc. Kjo do t'ju ndihmojë të kuptoni më mirë informacionin që po ju ofrojmë më poshtë. • PRERJA E LAMERIT : Ofrojme PRERJE dhe NDARJE. Prerjet e presin llamarinën në një rrugë në të njëjtën kohë dhe në thelb nuk ka humbje të materialit, ndërsa me ndarje forma nuk mund të vendoset saktësisht dhe për këtë arsye një sasi e caktuar materiali humbet. Një nga proceset tona më të njohura është PUNCHING, ku një pjesë e materialit të rrumbullakët ose në formë tjetër pritet nga llamarina. Pjesa që pritet është mbeturinë. Një tjetër version i shpimit është SLOTTING, ku hapen vrima drejtkëndëshe ose të zgjatura. BLANKIMI nga ana tjetër është i njëjti proces si grushtimi, me dallimin e pjesës që pritet është puna dhe mbahet. FINE BLANKING, një version superior i boshllëkut, krijon prerje me toleranca të afërta dhe skaje të drejta të lëmuara dhe nuk kërkon operacione dytësore për përsosjen e pjesës së punës. Një proces tjetër që ne përdorim shpesh është SLITTING, i cili është një proces prerjeje ku fletë metalike pritet nga dy tehe rrethore të kundërta në një shteg të drejtë ose të lakuar. Hapësi i kanaçeve është një shembull i thjeshtë i procesit të prerjes. Një tjetër popullor proces për ne është PERFORATING, ku shumë vrima të rrumbullakëta ose në formë tjetër hapen në fletë metalike në një model të caktuar. Një shembull tipik për një produkt të shpuar janë filtrat metalikë me shumë vrima për lëngjet. Në NOTCHING, një proces tjetër prerjeje llamarine, heqim materialin nga pjesa e punës, duke filluar nga skaji ose gjetkë dhe presim nga brenda derisa të fitohet forma e dëshiruar. Është një proces progresiv ku çdo operacion heq një pjesë tjetër derisa të merret kontura e dëshiruar. Për prodhime të vogla, ne ndonjëherë përdorim një proces relativisht më të ngadaltë të quajtur NIBBLING i cili përbëhet nga shumë goditje të shpejta të vrimave të mbivendosura për të bërë një prerje më të madhe më komplekse. Në PRERJE PROGRESIVE ne përdorim një sërë operacionesh të ndryshme për të marrë një prerje të vetme ose një gjeometri të caktuar. Së fundi RRUJTJA e një procesi dytësor na ndihmon të përmirësojmë skajet e prerjeve që janë bërë tashmë. Përdoret për prerjen e ashklave, skajeve të ashpra në punimet e llamarinës. • LAKIMI I LAMARËVE : Përveç prerjes, përkulja është një proces thelbësor pa të cilin ne nuk do të mund të prodhonim shumicën e produkteve. Kryesisht një operacion pune i ftohtë, por ndonjëherë kryhet edhe kur është i ngrohtë ose i nxehtë. Ne përdorim dieta dhe shtypim shumicën e kohës për këtë operacion. Në LAKIM PROGRESIVE ne përdorim një sërë operacionesh të ndryshme me grusht dhe dia për të marrë një kthesë të vetme ose një gjeometri të caktuar. AGS-TECH përdor një sërë procesesh përkuljeje dhe bën zgjedhjen në varësi të materialit të pjesës së punës, madhësisë së tij, trashësisë, madhësisë së dëshiruar të kthesës, rrezes, lakimit dhe këndit të kthesës, vendndodhjes së kthesës, ekonomisë së funksionimit, sasive që do të prodhohen… etj. Ne përdorim V-BENDING ku një grusht në formë V e detyron llamarinën në mbulesën në formë V dhe e përkul atë. E mirë për kënde shumë të mprehta dhe të mprehta dhe në mes, duke përfshirë 90 gradë. Duke përdorur fshirëse ne kryejmë EDGE BENDING. Pajisjet tona na mundësojnë të marrim kënde edhe më të mëdha se 90 gradë. Në përkuljen e skajit, pjesa e punës vendoset midis një jastëku presioni dhe mbulesës, zona për lakimin ndodhet në skajin e mbulesës dhe pjesa tjetër e pjesës së punës mbahet mbi space si një rreze konsol. Kur grushti vepron në pjesën e konsolit, ai përkulet mbi skajin e mbulesës. FLANGING është një proces i përkuljes së skajeve që rezulton në një kënd 90 gradë. Qëllimet kryesore të operacionit janë eliminimi i skajeve të mprehta dhe marrja e sipërfaqeve gjeometrike për të lehtësuar bashkimin e pjesëve. BIRJA, një tjetër proces i zakonshëm i përkuljes së skajeve formon një kaçurrelë mbi buzën e një pjese. HEMMING nga ana tjetër rezulton me një skaj të fletës që është plotësisht i përkulur mbi vetveten. Në SEAMING, skajet e dy pjesëve janë të përkulura mbi njëra-tjetrën dhe të bashkuara. Nga ana tjetër, SHKURJA E DYFISHTE siguron lidhje të papërshkueshme nga uji dhe hermetike. Ngjashëm me lakimin e skajeve, një proces i quajtur LAKIMI ROTARY vendos një cilindër me këndin e dëshiruar të prerë dhe që shërben si grusht. Ndërsa forca transmetohet në grusht, ajo mbyllet me pjesën e punës. Brazda e cilindrit i jep pjesës së konsolit këndin e dëshiruar. Brazda mund të ketë një kënd më të vogël ose më të madh se 90 gradë. Në AIR BENDING, ne nuk kemi nevojë që dieta e poshtme të ketë një brazdë me kënd. Llamaria mbështetet nga dy sipërfaqe në anët e kundërta dhe në një distancë të caktuar. Më pas grushti zbaton një forcë në vendin e duhur dhe përkul pjesën e punës. LAKIMI I KANALIT kryhet duke përdorur një shpuese dhe die në formë kanali, dhe U-BEND arrihet me një grusht në formë U-je. OFFSET BENDING prodhon kompensime në llamarinën. LAKIMI ROLL, një teknikë e mirë për punime të trasha dhe përkulje të pjesëve të mëdha të pllakave metalike, përdor tre rrotulla për të ushqyer dhe përkulur pllakat në lakimet e dëshiruara. Rrotullat janë rregulluar në mënyrë që të merret kthesa e dëshiruar e punës. Distanca dhe këndi midis rrotullave kontrollohet për të marrë rezultatin e dëshiruar. Një rrotull i lëvizshëm bën të mundur kontrollin e lakimit. TUBE FORMING është një tjetër operacion i popullarizuar i përkuljes së fletës metalike që përfshin shumë shufra. Tubat merren pas veprimeve të shumta. KORRUGIMI kryhet edhe me operacione përkuljeje. Në thelb është përkulja simetrike në intervale të rregullta nëpër një copë të tërë llamarine. Forma të ndryshme mund të përdoren për valëzim. Llamari i valëzuar është më i ngurtë dhe ka rezistencë më të mirë ndaj përkuljes dhe për këtë arsye ka aplikime në industrinë e ndërtimit. FORMIMI I ROLLIT TË FLETËS, një proces i prodhimit të vazhdueshëm prodhohet për të përkulur seksione tërthore të një gjeometrie të caktuar duke përdorur rrotulla dhe puna përkulet në hapa të njëpasnjëshëm, me rrotullimin përfundimtar të punës. Në disa raste përdoret një rrotull dhe në disa raste një seri rrotullash. • PROCESET E KOMBINUARA E PRERJES DHE LAKIMIT TË LAMARËVE: Këto janë proceset që presin dhe përkulen në të njëjtën kohë. Në PIERCING, krijohet një vrimë duke përdorur një grusht me majë. Ndërsa hapet vrima në fletë, materiali përkulet njëkohësisht në një fllanxhë të brendshme për vrimën. Fllanxha e marrë mund të ketë funksione të rëndësishme. Operacioni LANCING nga ana tjetër pret dhe përkul fletën për të krijuar një gjeometri të ngritur. • FRYMËRIMI DHE LAKIMI I TUBIT METAL: Në FURMËRIME, një pjesë e brendshme e një tubi të zbrazët është nën presion, duke shkaktuar fryrjen e tubit nga jashtë. Meqenëse tubi është brenda një mbulesë, gjeometria e fryrjes kontrollohet nga forma e mbulesës. Në STRETCH BENDING, një tub metalik shtrihet duke përdorur forca paralele me boshtin e tubit dhe forca përkulëse për të tërhequr tubin mbi një bllok formë. Në BENDING DRAW, ne e shtrëngojmë tubin afër fundit të tij në një bllok formë rrotulluese që përkul tubin ndërsa rrotullohet. Së fundi, në PËRKAKSIM KOMPRESION, tubi mbahet me forcë në një bllok të formës fikse, dhe një diabet e përkul atë mbi bllokun e formës. • VIZATIM I THELLË: Në një nga operacionet tona më të njohura, përdoren një grusht, një bollëk që përputhet dhe një mbajtës bosh. Boshllëku i llamarinës vendoset mbi hapjen e mbulesës dhe grushti lëviz drejt boshllëkut të mbajtur nga mbajtësi i boshllëkut. Pasi të vijnë në kontakt, grushti e detyron llamarinën në zgavrën e mbulesës për të formuar produktin. Funksionimi i tërheqjes së thellë i ngjan prerjes, megjithatë hapësira midis shpueses dhe mbulesës parandalon prerjen e fletës. Një faktor tjetër që siguron që fleta të jetë tërhequr thellë dhe jo e prerë janë qoshet e rrumbullakosura në mallë dhe shpimi i cili parandalon qethjen dhe prerjen. Për të arritur një madhësi më të madhe të vizatimit të thellë, është duke u vendosur një proces RIVIZATUES ku kryhet një vizatim i thellë pasues në një pjesë që tashmë i është nënshtruar një procesi vizatimi të thellë. Në RIVIZATIMIN E KUNDËR, pjesa e tërhequr thellë kthehet dhe vizatohet në drejtim të kundërt. Vizatimi i thellë mund të ofrojë objekte me formë të parregullt si kupa me kube, të ngushta ose me shkallë. • SPINNING : Një operacion ku një pjesë pune e sheshtë ose e paraformuar mbahet midis një mandreli rrotulluese dhe shtyllës së bishtit dhe një vegël ushtron presion të lokalizuar në punë ndërsa lëviz gradualisht lart në mandrel. Si rezultat, pjesa e punës mbështillet mbi mandrelë dhe merr formën e saj. Ne e përdorim këtë teknikë si një alternativë ndaj vizatimit të thellë ku sasia e një porosie është e vogël, pjesët janë të mëdha (diametra deri në 20 këmbë) dhe kanë kthesa unike. Edhe pse çmimet për copë janë përgjithësisht më të larta, kostot e konfigurimit për funksionimin e rrotullimit CNC janë të ulëta në krahasim me vizatimin e thellë. Përkundrazi, vizatimi i thellë kërkon investim të lartë fillestar për montim, por kostot për copë janë të ulëta kur prodhohen një sasi e madhe pjesësh. Një version tjetër i këtij procesi është SHEAR SPINNING, ku ka edhe rrjedhje metalike brenda pjesës së punës. Rrjedha metalike do të zvogëlojë trashësinë e pjesës së punës ndërsa kryhet procesi. Një tjetër proces i ndërlidhur është TUBE SPINNING, i cili aplikohet në pjesë cilindrike. Gjithashtu në këtë proces ka rrjedhje metalike brenda pjesës së punës. Kështu, trashësia zvogëlohet dhe gjatësia e tubit rritet. Mjeti mund të zhvendoset për të krijuar veçori në pjesën e brendshme ose të jashtme të tubit. • FORMIMI ME GOME E LAMERËS : Materiali prej gome ose poliuretani futet në një mbulesë enë dhe pjesa e punës vendoset në sipërfaqen e gomës. Më pas, një grusht veprohet mbi pjesën e punës dhe e detyron atë në gomë. Meqenëse presioni i gjeneruar nga goma është i ulët, thellësia e pjesëve të prodhuara është e kufizuar. Meqenëse kostot e veglave janë të ulëta, procesi është i përshtatshëm për prodhim me sasi të ulët. • HIDROFORMIMI : Ngjashëm me formimin e gomës, në këtë proces llamarina shtypet nga një grusht në një lëng nën presion brenda një dhome. Punimi i llamarinës vendoset midis grushtit dhe një diafragme gome. Diafragma e rrethon plotësisht pjesën e punës dhe presioni i lëngut e detyron atë të formohet në grusht. Me këtë teknikë mund të merren tërheqje shumë të thella edhe më të thella se në procesin e vizatimit të thellë. Ne prodhojmë kapa me një grusht, si dhe materie progesive në varësi të pjesës suaj. Mbulesat e stampimit me një goditje të vetme janë një metodë me kosto efektive për prodhimin e shpejtë të sasive të mëdha të pjesëve të thjeshta prej llamarine si rondele. Mjetet progresive ose teknika e vizatimit të thellë përdoren për prodhimin e gjeometrive më komplekse. Në varësi të rastit tuaj, prerja me ujë, lazer ose plazma mund të përdoret për të prodhuar pjesët tuaja prej llamarine me çmim të lirë, të shpejtë dhe të saktë. Shumë furnitorë nuk e kanë idenë për këto teknika alternative ose nuk e kanë atë dhe për këtë arsye ata kalojnë nëpër mënyra të gjata dhe të shtrenjta për të bërë makineri dhe mjete që vetëm u humbasin klientëve kohë dhe para. Nëse keni nevojë për komponentë prej llamarine të ndërtuar me porosi, të tilla si mbyllje, strehë elektronike... etj, aq shpejt sa brenda disa ditësh, atëherë na kontaktoni për shërbimin tonë të PROTOTIPIMIT TË SHPEJTË TË LETËS. CLICK Product Finder-Locator Service MENUA E MËPARSHME
- Plastic Rubber Metal Extrusions, Extrusion Dies, Aluminum Extruding
Plastic Rubber Metal Extrusions, Extrusion Dies, Aluminum Extruding, Pipe Tube Forming, Plastic Profiles, Metal Profiles Manufacturing, PVC at AGS-TECH Inc. Ekstrudimet, Produktet e Ekstruduara, Ekstrudimet Ne përdorim the EXTRUSION process për të prodhuar produkte me një profil tërthore të fiksuar si tuba ngrohjeje, tuba. Edhe pse shumë materiale mund të ekstrudohen, nxjerrjet tona më të zakonshme janë prej metali, polimere/plastike, qeramike të përftuara me metodën e nxjerrjes së ftohtë, të ngrohtë ose të nxehtë. Pjesët e ekstruduara i quajmë ekstruduar ose ekstruduar nëse janë shumës. Disa versione të specializuara të procesit që ne kryejmë gjithashtu janë mbulimi i tepërt, bashkëekstrusioni dhe nxjerrja e përbërë. Ne ju rekomandojmë që të klikoni këtu për SHKARKONI Ilustrimet tona skematike të proceseve të nxjerrjes së qeramikës dhe plastikës së metaleve nga AGS-TECH Inc. Kjo do t'ju ndihmojë të kuptoni më mirë informacionin që po ju ofrojmë më poshtë. Në ekstrudion, materiali që do të ekstrudohet shtyhet ose tërhiqet përmes një koke që ka profilin e dëshiruar të prerjes tërthore. Procesi mund të përdoret për të prodhuar seksione tërthore komplekse me përfundim të shkëlqyer të sipërfaqes dhe për të punuar në material të brishtë. Dikush mund të prodhojë çdo gjatësi të pjesëve duke përdorur këtë proces. Për të thjeshtuar hapat e procesit: 1.) Në nxjerrje të ngrohta ose të nxehta, materiali nxehet dhe ngarkohet në një enë në pres. Materiali shtypet dhe nxirret nga koka. 2.) Ekstrudati i prodhuar shtrihet për t'u drejtuar, trajtohet me nxehtësi ose përpunohet në të ftohtë për të përmirësuar vetitë e tij. Nga ana tjetër COLD EXTRUSION zhvillohet në temperaturën e dhomës dhe ka avantazhet e oksidimit më të mirë, më afër sipërfaqes dhe përfundimit të lartë. WARM EXTRUSION kryhet mbi temperaturën e dhomës por nën pikën e rikristalizimit. Ai ofron një kompromis dhe ekuilibër për forcat e kërkuara, duktilitetin dhe vetitë e materialit dhe për këtë arsye është zgjedhja për disa aplikime. HOT EXTRUSION bëhet mbi temperaturën e rikristalizimit të materialit. Në këtë mënyrë është më e lehtë të shtyhet materiali përmes mbulesës. Sidoqoftë, kostoja e pajisjeve është e lartë. Sa më i ndërlikuar të jetë një profil i ekstruduar, aq më i kushtueshëm është diametri (instrumenti) dhe aq më i ulët është shkalla e prodhimit. Seksionet tërthore të bishtit si dhe trashësitë kanë kufizime që varen nga materiali që do të ekstrudohet. Këndet e mprehta në mbulesat e nxjerrjes janë gjithmonë të padëshirueshme dhe duhen shmangur nëse nuk është e nevojshme. Sipas materialit që është duke u ekstruduar, ne ofrojmë: • METAL EXTRUSIONS : Më të zakonshmet që prodhojmë janë alumini, bronzi, zinku, bakri, çeliku, titani, magnezi • EXTRUSION PLASTIC : Plastika shkrihet dhe formohet në një profil të vazhdueshëm. Materialet tona të zakonshme të përpunuara janë polietileni, najloni, polistireni, klorur polivinil, polipropileni, plastika ABS, polikarbonat, akrilik. Produktet tipike që ne prodhojmë përfshijnë tuba dhe tuba, korniza plastike. Në këtë proces, rruaza të vogla plastike / rrëshirë ushqehen nga graviteti nga pleshti në fuçinë e makinës së nxjerrjes. Shpesh ne gjithashtu përziejmë ngjyrues ose aditivë të tjerë në plesht për t'i dhënë produktit specifikimet dhe vetitë e kërkuara. Materiali që hyn në fuçinë e ngrohur detyrohet nga vidhosja rrotulluese të largohet nga fuçi në fund dhe të lëvizë nëpër paketimin e ekranit për heqjen e ndotësve në plastikën e shkrirë. Pas kalimit të paketës së ekranit, plastika futet në mbulesën e nxjerrjes. Mjeti i jep plastikes së butë lëvizëse formën e saj të profilit ndërsa kalon. Tani ekstrudati kalon nëpër një banjë uji për ftohje. Teknika të tjera që AGS-TECH Inc. ka përdorur për shumë vite janë: • EXTRUSION TUB & TUBING : Tubat dhe tubat plastikë formohen kur plastika nxirret përmes një mbulesë formësimi të rrumbullakët dhe ftohet në një banjë uji, pastaj pritet në gjatësi ose mbështillet / rrotullohet. E pastër ose me ngjyrë, me vija, me një mur të vetëm ose të dyfishtë, fleksibël ose të ngurtë, PE, PP, poliuretani, PVC, najlon, PC, silikoni, vinyl ose ndryshe, i kemi të gjitha. Ne kemi tuba të pajisur si dhe aftësinë për të prodhuar sipas specifikimeve tuaja. AGS-TECH prodhon tuba sipas kërkesave të FDA, UL dhe LE për aplikime mjekësore, elektrike dhe elektronike, industriale dhe të tjera. • OVERJACKETING / OVER JACKETING EXTRUSION : Kjo teknikë aplikon një shtresë të jashtme plastike mbi tela ose kabllo ekzistuese. Telat tanë izolues prodhohen me këtë metodë. • COEXTRUSION : Shtresa të shumta të materialit janë ekstruduar njëkohësisht. Shtresat e shumta dorëzohen nga ekstruderë të shumtë. Trashësi të ndryshme të shtresave mund të rregullohen për të përmbushur specifikimet e klientit. Ky proces bën të mundur përdorimin e polimerëve të shumtë që secili ka një funksionalitet të ndryshëm në produkt. Si rezultat, mund të optimizoni një sërë karakteristikash. • EKSTRUSIONI ME PËRBËRJE: Një polimer i vetëm ose i shumëfishtë përzihet me aditivë për të marrë një përbërje plastike. Ekstruduesit tanë me dy vida prodhojnë nxjerrje të përziera. Mjetet e nxjerrjes janë përgjithësisht të lira në krahasim me kallëpet metalike. Nëse po paguani shumë më tepër se disa mijëra dollarë për një alumin ekstrudues me madhësi të vogël ose të mesme, me siguri po paguani shumë. Ne jemi ekspertë në përcaktimin se cila teknikë është më kosto-efektive, më e shpejtë dhe më e përshtatshme për aplikimin tuaj. Ndonjëherë ekstrudimi dhe më pas përpunimi i një pjese mund t'ju kursejë shumë para. Përpara se të merrni një vendim të prerë, na kërkoni fillimisht mendimin tonë. Ne kemi ndihmuar shumë klientë të marrin vendimet e duhura. Për disa nxjerrje metalike të përdorura gjerësisht, mund të shkarkoni broshurat dhe katalogët tanë duke klikuar në tekstin me ngjyra më poshtë. Nëse është një produkt jashtë raftit që plotëson kërkesat tuaja, do të jetë më ekonomik. Shkarkoni aftësitë tona të nxjerrjes së tubave dhe tubave mjekësorë Shkarkoni lavamanët tanë të nxehtësisë së ekstruduar • PROCESET DESËM TË PRODHIMIT DHE FABRIKIMIT PËR EKSTRUZIONET : Ndër proceset me vlerë të shtuar që ne ofrojmë për produktet e ekstruduara janë: -Përkulja e tubave dhe tubave me porosi, formimi dhe formësimi, ndërprerja e tubit, formimi i skajit të tubit, mbështjellja e tubit, përpunimi dhe përfundimi, shpimi dhe shpimi dhe shpimi i vrimave, - Montimet e personalizuara të tubave dhe tubave, montimi tubular, saldimi, brazimi dhe saldimi -Përkulje, formim dhe formësim me ekstrudion me porosi -Pastrim, degreasing, turshi, pasivim, lustrim, anodizim, plasim, lyerje, trajtim termik, pjekje dhe forcim, markim, gdhendje dhe etiketim, paketim me porosi. CLICK Product Finder-Locator Service FAQJA E MEPARSHME
- Casting and Machined Parts, CNC Manufacturing, Milling, Turning, Swiss
Casting and Machined Parts, CNC Manufacturing, Milling, Turning, Swiss Type Machining, Die Casting, Investment Casting, Lost Foam Cast Parts from AGS-TECH Inc. Derdhja dhe përpunimi Teknikat tona të derdhjes dhe të përpunimit me porosi janë derdhje të shpenzueshme dhe jo të shpenzuara, derdhje me ngjyra dhe me ngjyra, rërë, mbulesë, centrifugale, të vazhdueshme, kallëp qeramik, investim, shkumë e humbur, formë afër rrjetës, myk i përhershëm (derdhje me gravitet), suva kallëp (derdhje suvaje) dhe kallëpe, pjesë të përpunuara të prodhuara nga bluarje dhe tornime duke përdorur pajisje konvencionale si dhe CNC, përpunim të tipit zviceran për pjesë të vogla precize të lira me xhiro të larta, përpunim me vidhos për mbërthyes, përpunim jo konvencional. Ju lutemi mbani në mend se përveç metaleve dhe lidhjeve metalike, ne përpunojmë përbërës qeramikë, qelqi dhe plastikë, si dhe në disa raste kur prodhimi i një kallëpi nuk është tërheqës ose jo opsioni. Përpunimi i materialeve polimer kërkon përvojën e specializuar që kemi për shkak të sfidës që paraqet plastika dhe goma për shkak të butësisë, jo ngurtësimit të tyre... etj. Për përpunimin e qeramikës dhe qelqit, ju lutemi shikoni faqen tonë mbi Fabrikimin Jo-Konvencional. AGS-TECH Inc. prodhon dhe furnizon aktrime të lehta dhe të rënda. Ne kemi furnizuar me derdhje metalike dhe pjesë të përpunuara për kaldaja, shkëmbyes nxehtësie, automobila, mikromotorë, turbina me erë, pajisje për paketimin e ushqimit dhe më shumë. Ne ju rekomandojmë që të klikoni këtu për SHKARKONI Ilustrimet tona skematike të proceseve të përpunimit dhe derdhjes nga AGS-TECH Inc. Kjo do t'ju ndihmojë të kuptoni më mirë informacionin që po ju ofrojmë më poshtë. Le të shohim në detaje disa nga teknikat e ndryshme që ofrojmë: • DERDHJA E MUNDIT TË SHPENZUESHME: Kjo kategori e gjerë i referohet metodave që përfshijnë kallëpe të përkohshme dhe jo të ripërdorshme. Shembuj janë rëra, suva, guaska, investimi (i quajtur edhe dylli i humbur) dhe derdhja e suvasë. • DERDHJA NË RËRË: Një proces ku rëra përdoret si material myku. Një metodë shumë e vjetër dhe ende shumë e popullarizuar në masën që shumica e derdhjeve metalike të prodhuara bëhen me këtë teknikë. Kosto e ulët edhe në prodhim me sasi të ulët. I përshtatshëm për prodhimin e pjesëve të vogla dhe të mëdha. Teknika mund të përdoret për të prodhuar pjesë brenda ditëve ose javëve me shumë pak investime. Rëra e lagësht lidhet së bashku duke përdorur argjilë, lidhës ose vajra të veçantë. Rëra përmbahet përgjithësisht në kutitë e mykut dhe sistemi i zgavrës dhe portave krijohen duke kompaktuar rërën rreth modeleve. Proceset janë: 1.) Vendosja e modelit në rërë për të bërë kallëpin 2.) Inkorporimi i modelit dhe rërës në një sistem portash 3.) Heqja e modelit 4.) Mbushja e zgavrës së kallëpit me metal të shkrirë 5.) Ftohja e metalit 6.) Thyerja e kallëpit të rërës dhe heqja e derdhjes • DERDHJA E MULAVE ME SUVA: Ngjashëm me derdhjen me rërë, dhe në vend të rërës, si material kallëp përdoret suva e parisit. Kohëzgjatja e shkurtër e prodhimit si derdhja e rërës dhe e lirë. Toleranca të mira dimensionale dhe përfundimi i sipërfaqes. Disavantazhi i tij kryesor është se mund të përdoret vetëm me metale me pikë shkrirjeje të ulët si alumini dhe zinku. • DERDHJA E MOLDIT SHELL: Gjithashtu e ngjashme me derdhjen me rërë. Zgavra e mykut e përftuar nga guaska e ngurtësuar e rërës dhe lidhësi me rrëshirë termike në vend të balonës së mbushur me rërë si në procesin e derdhjes me rërë. Pothuajse çdo metal i përshtatshëm për t'u derdhur me rërë mund të derdhet me formimin e guaskës. Procesi mund të përmblidhet si: 1.) Prodhimi i mykut të guaskës. Rëra e përdorur ka një madhësi kokrriza shumë më të vogël kur krahasohet me rërën e përdorur në derdhjen e rërës. Rëra e imët përzihet me rrëshirë termofikse. Modeli metalik është i veshur me një agjent ndarës për ta bërë më të lehtë heqjen e guaskës. Më pas, modeli metalik nxehet dhe përzierja e rërës derdhet ose fryhet në modelin e derdhjes së nxehtë. Një guaskë e hollë formohet në sipërfaqen e modelit. Trashësia e kësaj guaske mund të rregullohet duke ndryshuar gjatësinë e kohës kur përzierja e rrëshirës së rërës është në kontakt me modelin metalik. Rëra e lirshme hiqet më pas me modelin e mbuluar me guaskë të mbetur. 2.) Më pas, guaska dhe modeli nxehen në furrë në mënyrë që guaska të ngurtësohet. Pas përfundimit të ngurtësimit, guaska nxirret nga modeli duke përdorur kunjat e vendosura në model. 3.) Dy guaska të tilla mblidhen së bashku me ngjitje ose shtrëngim dhe përbëjnë formën e plotë. Tani kallëpi i guaskës futet në një enë në të cilën mbështetet nga rëra ose metali gjatë procesit të derdhjes. 4.) Tani metali i nxehtë mund të derdhet në kallëpin e guaskës. Përparësitë e derdhjes së guaskës janë produkte me finiturë shumë të mirë sipërfaqësore, mundësi prodhimi të pjesëve komplekse me saktësi të lartë dimensionale, proces i lehtë për t'u automatizuar, ekonomik për prodhim me volum të madh. Disavantazhet janë kallëpet që kërkojnë ajrim të mirë për shkak të gazrave që krijohen kur metali i shkrirë kontakton kimikatin lidhës, rrëshirat termofikse dhe modelet metalike janë të shtrenjta. Për shkak të kostos së modeleve metalike, teknika mund të mos përshtatet mirë për prodhime me sasi të ulët. • DERDHJA E INVESTIMEVE (e njohur edhe si DERDHJA E DYLLIT TË HUMBUR): Gjithashtu një teknikë shumë e vjetër dhe e përshtatshme për prodhimin e pjesëve cilësore me saktësi, përsëritshmëri, shkathtësi dhe integritet të lartë nga shumë metale, materiale zjarrduruese dhe lidhje speciale me performancë të lartë. Mund të prodhohen pjesë të vogla dhe të mëdha. Një proces i shtrenjtë në krahasim me disa nga metodat e tjera, por avantazhi kryesor është mundësia për të prodhuar pjesë me formë afër rrjetës, konturet e ndërlikuara dhe detajet. Pra, kostoja kompensohet disi nga eliminimi i ripërpunimit dhe përpunimit në disa raste. Edhe pse mund të ketë ndryshime, këtu është një përmbledhje e procesit të përgjithshëm të hedhjes së investimeve: 1.) Krijimi i modelit master origjinal nga dylli ose plastika. Çdo derdhje ka nevojë për një model pasi ato shkatërrohen gjatë procesit. Kallëpi nga i cili prodhohen modelet është gjithashtu i nevojshëm dhe shumicën e kohës myku derdhet ose përpunohet. Për shkak se kallëpi nuk ka nevojë të hapet, mund të arrihen derdhje komplekse, shumë modele dylli mund të lidhen si degët e një peme dhe të derdhen së bashku, duke mundësuar kështu prodhimin e pjesëve të shumta nga një derdhje e vetme e metalit ose aliazhit të metalit. 2.) Më pas, modeli zhytet ose derdhet me një lëng refraktar të përbërë nga silicë me kokrriza shumë të imta, ujë, lidhës. Kjo rezulton në një shtresë qeramike mbi sipërfaqen e modelit. Shtresa zjarrduruese në model lihet të thahet dhe të ngurtësohet. Nga ky hap vjen emri i derdhjes investuese: Lluri zjarrdurues investohet mbi modelin e dyllit. 3.) Në këtë hap, kallëpi i ngurtësuar i qeramikës kthehet përmbys dhe nxehet në mënyrë që dylli të shkrihet dhe të derdhet nga kallëpi. Një zgavër është lënë pas për derdhjen e metalit. 4.) Pasi dylli të dalë jashtë, kallëpi i qeramikës nxehet në një temperaturë edhe më të lartë që rezulton në forcimin e mykut. 5.) Derdhja e metalit derdhet në kallëpin e nxehtë duke mbushur të gjitha seksionet e ndërlikuara. 6.) Hedhja lejohet të ngurtësohet 7.) Më në fund kallëpi i qeramikës thyhet dhe pjesët e prodhuara priten nga pema. Këtu është një lidhje me broshurën e Investimeve Casting Plant • DERDHJA E MOBILIT AVAPORATIV : Procesi përdor një model të bërë nga një material si shkuma polistireni që do të avullojë kur metali i shkrirë i nxehtë derdhet në kallëp. Ekzistojnë dy lloje të këtij procesi: DERDHJA E HUMBUR SHKUMË e cila përdor rërë të palidhur dhe FULL MOULD casting e cila përdor rërë të lidhur. Këtu janë hapat e përgjithshëm të procesit: 1.) Prodhoni modelin nga një material si polistireni. Kur do të prodhohen sasi të mëdha, modeli formohet. Nëse pjesa ka një formë komplekse, disa pjesë të këtij materiali shkumë mund të duhet të ngjiten së bashku për të formuar modelin. Ne shpesh e lyejmë modelin me një përbërje zjarrduruese për të krijuar një përfundim të mirë të sipërfaqes në derdhje. 2.) Modeli më pas vendoset në rërë të derdhur. 3.) Metali i shkrirë derdhet në kallëp, duke avulluar modelin e shkumës, pra polistirenin në shumicën e rasteve teksa rrjedh nëpër zgavrën e kallëpit. 4.) Metali i shkrirë lihet në kallëp me rërë që të ngurtësohet. 5.) Pasi të jetë ngurtësuar, heqim derdhjen. Në disa raste, produkti që ne prodhojmë kërkon një bërthamë brenda modelit. Në derdhjen avulluese, nuk ka nevojë të vendoset dhe të sigurohet një bërthamë në zgavrën e kallëpit. Teknika është e përshtatshme për prodhimin e gjeometrive shumë komplekse, mund të automatizohet lehtësisht për prodhim me vëllim të madh dhe nuk ka linja ndarëse në pjesën e derdhjes. Procesi bazë është i thjeshtë dhe ekonomik për t'u zbatuar. Për prodhim me volum të madh, meqenëse nevojitet një model ose kallëp për të prodhuar modelet nga polistireni, kjo mund të jetë disi e kushtueshme. • DERDHJA E MUNDËS SË JO ZGJERUESHME: Kjo kategori e gjerë i referohet metodave ku kallëpi nuk ka nevojë të reformohet pas çdo cikli prodhimi. Shembujt janë derdhja e përhershme, me diabet, e vazhdueshme dhe centrifugale. Fitohet përsëritshmëria dhe pjesët mund të karakterizohen si FORMA AFËR RRJETA. • DERDHJA E PËRHERSHME MODEL : Kallëpet e ripërdorshme të bëra nga metali përdoren për derdhje të shumta. Një myk i përhershëm në përgjithësi mund të përdoret dhjetëra mijëra herë përpara se të konsumohet. Graviteti, presioni i gazit ose vakuumi zakonisht përdoren për të mbushur kallëpin. Kallëpet (të quajtura edhe kësulë) në përgjithësi janë bërë prej hekuri, çeliku, qeramike ose metale të tjera. Procesi i përgjithshëm është: 1.) Përpunoni dhe krijoni kallëpin. Është e zakonshme përpunimi i kallëpit nga dy blloqe metalike që përshtaten së bashku dhe mund të hapen dhe mbyllen. Si tiparet e pjesës ashtu edhe sistemi i portave në përgjithësi përpunohen në kallëpin e derdhjes. 2.) Sipërfaqet e brendshme të kallëpit janë të veshura me një llucë që përfshin materiale zjarrduruese. Kjo ndihmon për të kontrolluar rrjedhën e nxehtësisë dhe vepron si një lubrifikant për heqjen e lehtë të pjesës së derdhur. 3.) Më pas mbyllen gjysmat e përhershme të kallëpit dhe kallëpi nxehet. 4.) Metali i shkrirë derdhet në kallëp dhe lihet të ngurtësohet. 5.) Përpara se të ndodhë shumë ftohje, ne e heqim pjesën nga kallëpi i përhershëm duke përdorur ejektorë kur hapen gjysmat e mykut. Ne përdorim shpesh derdhje të përhershme të kallëpit për metale me pikë shkrirjeje të ulët si zinku dhe alumini. Për derdhjet e çelikut, ne përdorim grafit si material myk. Ne ndonjëherë marrim gjeometri komplekse duke përdorur bërthama brenda kallëpeve të përhershme. Përparësitë e kësaj teknike janë derdhjet me veti të mira mekanike të marra nga ftohja e shpejtë, uniformiteti në veti, saktësia e mirë dhe përfundimi i sipërfaqes, shkalla e ulët e refuzimit, mundësia e automatizimit të procesit dhe prodhimi ekonomik i vëllimeve të larta. Disavantazhet janë kostot e larta të konfigurimit fillestar që e bëjnë atë të papërshtatshëm për operacione me volum të ulët dhe kufizimet në madhësinë e pjesëve të prodhuara. • DERDHJA ME DIKE : Përpunohet një makineri dhe metali i shkrirë shtyhet nën presion të lartë në zgavrat e mykut. Janë të mundshme si derdhjet me ngjyra, ashtu edhe ato të metaleve me ngjyra. Procesi është i përshtatshëm për prodhime në sasi të lartë të pjesëve të vogla dhe të mesme me detaje, mure jashtëzakonisht të hollë, konsistencë dimensionale dhe përfundim të mirë të sipërfaqes. AGS-TECH Inc. është në gjendje të prodhojë trashësi muresh deri në 0,5 mm duke përdorur këtë teknikë. Ashtu si në derdhjen e përhershme të mykut, kallëpi duhet të përbëhet nga dy gjysma që mund të hapen dhe mbyllen për heqjen e pjesës së prodhuar. Një kallëp i derdhjes mund të ketë zgavra të shumta për të mundësuar prodhimin e derdhjeve të shumta me çdo cikël. Format e derdhjes janë shumë të rënda dhe shumë më të mëdha se pjesët që prodhojnë, prandaj edhe të shtrenjta. Ne riparojmë dhe zëvendësojmë kapakët e konsumuar pa pagesë për klientët tanë për sa kohë që ata i riporosin pjesët e tyre nga ne. Mjetet tona kanë jetëgjatësi të gjatë në rangun e disa qindra mijëra cikleve. Këtu janë hapat bazë të thjeshtuar të procesit: 1.) Prodhimi i kallëpit në përgjithësi nga çeliku 2.) Kallëp i instaluar në makinën e hedhjes 3.) Pistoni detyron metalin e shkrirë të rrjedhë në zgavrat e mbulesës duke plotësuar veçoritë e ndërlikuara dhe muret e hollë 4.) Pas mbushjes së kallëpit me metalin e shkrirë, derdhja lihet të ngurtësohet nën presion 5.) Myku hapet dhe derdhja hiqet me ndihmën e kunjave të ejektorit. 6.) Tani kokrrat e zbrazëta lubrifikohen përsëri dhe mbërthehen për ciklin tjetër. Në derdhjen me diake, ne shpesh përdorim formimin e futjes ku inkorporojmë një pjesë shtesë në kallëp dhe hedhim metalin rreth tij. Pas ngurtësimit, këto pjesë bëhen pjesë e produktit të derdhur. Përparësitë e derdhjes me diake janë vetitë e mira mekanike të pjesëve, mundësia e veçorive të ndërlikuara, detajet e imta dhe përfundimi i mirë i sipërfaqes, ritmet e larta të prodhimit, automatizimi i lehtë. Disavantazhet janë: Jo shumë i përshtatshëm për volum të ulët për shkak të kostos së lartë të kostumeve dhe pajisjeve, kufizimet në forma që mund të derdhen, shenja të vogla të rrumbullakëta në pjesët e derdhura që rezultojnë nga kontakti i kunjave të ejektorit, blic i hollë metali i shtrydhur në vijën e ndarjes, nevoja. për ndenjat përgjatë vijës së ndarjes midis mbulesës, nevoja për të mbajtur temperaturat e mykut të ulëta duke përdorur qarkullimin e ujit. • DERDHJE CENTRIFUGALE: Metali i shkrirë derdhet në qendër të kallëpit rrotullues në boshtin e rrotullimit. Forcat centrifugale e hedhin metalin drejt periferisë dhe lihet të ngurtësohet ndërsa myku vazhdon të rrotullohet. Mund të përdoren si rrotullime të boshtit horizontal ashtu edhe vertikal. Mund të derdhen pjesë me sipërfaqe të brendshme të rrumbullakëta si dhe forma të tjera jo të rrumbullakëta. Procesi mund të përmblidhet si: 1.) Metali i shkrirë derdhet në kallëp centrifugal. Metali më pas detyrohet në muret e jashtme për shkak të tjerrjes së mykut. 2.) Ndërsa kallëpi rrotullohet, derdhja e metalit ngurtësohet Derdhja centrifugale është një teknikë e përshtatshme për prodhimin e pjesëve cilindrike të zbrazëta si tubacionet, nuk ka nevojë për spruta, ngritës dhe elementë portash, përfundim i mirë i sipërfaqes dhe karakteristika të detajuara, pa probleme tkurrjeje, mundësi për të prodhuar tuba të gjatë me diametra shumë të mëdhenj, aftësi prodhimi me shpejtësi të lartë. . • DERDHJE E VAZHDUESHME ( DERDHJE ME FIJE ) : Përdoret për derdhjen e një gjatësie të vazhdueshme metali. Në thelb, metali i shkrirë derdhet në profilin dydimensional të kallëpit, por gjatësia e tij është e papërcaktuar. Metali i ri i shkrirë futet vazhdimisht në kallëp ndërsa derdhja udhëton poshtë me gjatësinë e tij duke u rritur me kalimin e kohës. Metalet si bakri, çeliku, alumini derdhen në fije të gjata duke përdorur procesin e derdhjes së vazhdueshme. Procesi mund të ketë konfigurime të ndryshme, por ai i zakonshëm mund të thjeshtohet si: 1.) Metali i shkrirë derdhet në një enë të vendosur lart mbi kallëp në sasi dhe shpejtësi rrjedhjeje të llogaritura mirë dhe rrjedh nëpër kallëpin e ftohur me ujë. Derdhja metalike e derdhur në kallëp ngurtësohet në një shirit fillestar të vendosur në fund të kallëpit. Ky shirit fillestar u jep rrotullave diçka për të kapur fillimisht. 2.) Fija e gjatë metalike bartet me rrotulla me shpejtësi konstante. Rolet gjithashtu ndryshojnë drejtimin e rrjedhës së fillesë metalike nga vertikale në horizontale. 3.) Pasi derdhja e vazhdueshme ka përshkuar një distancë të caktuar horizontale, një pishtar ose sharrë që lëviz me derdhjen e shkurton shpejt atë në gjatësitë e dëshiruara. Procesi i derdhjes së vazhdueshme mund të integrohet me PROCESIN ROLLING, ku metali i derdhur vazhdimisht mund të futet direkt në një mulli petëzimi për të prodhuar I-Beams, T-T-Beams… etj. Derdhja e vazhdueshme prodhon veti uniforme në të gjithë produktin, ka një shkallë të lartë ngurtësimi, zvogëlon koston për shkak të humbjes shumë të ulët të materialit, ofron një proces ku ngarkimi i metalit, derdhja, ngurtësimi, prerja dhe heqja e derdhjes ndodhin në një operacion të vazhdueshëm dhe duke rezultuar kështu në shkallë të lartë produktiviteti dhe cilësi të lartë. Megjithatë, një konsideratë kryesore është investimi i lartë fillestar, kostot e konfigurimit dhe kërkesat e hapësirës. • SHËRBIMET E MAKINIMIT: Ne ofrojmë përpunim me tre, katër dhe pesë boshte. Llojet e proceseve të përpunimit që ne përdorim janë TRËSIM, FREZIM, SHPIM, SHPËRIM, SHPËRJE, PLANIFIKIM, SHARRI, BLUARJE, LAPËSIM, LISTRIM dhe MAKINIMET JO TRADICIONALE, të cilat shtjellohen më tej në një menu tjetër të faqes sonë të internetit. Për pjesën më të madhe të prodhimit tonë, ne përdorim makina CNC. Megjithatë për disa operacione teknikat konvencionale janë më të përshtatshme dhe për këtë arsye ne mbështetemi edhe në to. Aftësitë tona të përpunimit arrijnë nivelin më të lartë të mundshëm dhe disa pjesë më të kërkuara prodhohen në një fabrikë të certifikuar AS9100. Tehet e motorit reaktiv kërkojnë përvojë shumë të specializuar në prodhim dhe pajisjet e duhura. Industria e hapësirës ajrore ka standarde shumë strikte. Disa komponentë me struktura komplekse gjeometrike prodhohen më lehtë nga përpunimi me pesë boshte, i cili gjendet vetëm në disa fabrika përpunimi, përfshirë këtu edhe tonën. Fabrika jonë e certifikuar për hapësirën ajrore ka përvojën e nevojshme në përputhje me kërkesat e dokumentacionit të gjerë të industrisë së hapësirës ajrore. Në operacionet e KTHYRJES, një pjesë e punës rrotullohet dhe zhvendoset kundër një mjeti prerës. Për këtë proces përdoret një makinë e quajtur torno. Në MILLING, një makinë e quajtur frezë ka një vegël rrotulluese për të vendosur skajet prerëse kundër një pjese të punës. Operacionet e shpimit përfshijnë një prerës rrotullues me skaje prerëse që prodhon vrima në kontakt me pjesën e punës. Në përgjithësi përdoren presa, torno ose mullinj. Në operacionet BORING, një vegël me një majë të vetme me majë të përkulur zhvendoset në një vrimë të përafërt në një pjesë pune që rrotullohet për të zgjeruar pak vrimën dhe për të përmirësuar saktësinë. Përdoret për qëllime përfundimi të imta. BROACHING përfshin një mjet me dhëmbë për të hequr materialin nga një pjesë e punës në një kalim të broshit (vegël me dhëmbë). Në hapjen lineare, hapja shkon në mënyrë lineare kundër një sipërfaqeje të pjesës së punës për të realizuar prerjen, ndërsa në hapjen me rrotullim, broshja rrotullohet dhe shtypet në pjesën e punës për të prerë një formë simetrike të boshtit. MAKINIMI I LLOJIT SWISS është një nga teknikat tona të vlefshme që ne përdorim për prodhimin e pjesëve të vogla me precizion të lartë. Duke përdorur torno të tipit zviceran, ne kthejmë pjesë të vogla, komplekse dhe precize me çmim të lirë. Ndryshe nga torno konvencionale ku pjesa e punës mbahet e palëvizshme dhe mjeti lëviz, në qendrat tornuese të tipit zviceran, pjesa e punës lejohet të lëvizë në boshtin Z dhe mjeti është i palëvizshëm. Në përpunimin e tipit zviceran, stoku i shufrave mbahet në makinë dhe avancohet përmes një mbështjellësi udhëzues në boshtin z, duke ekspozuar vetëm pjesën që do të përpunohet. Në këtë mënyrë sigurohet një shtrëngim i ngushtë dhe saktësia është shumë e lartë. Disponueshmëria e mjeteve të gjalla ofron mundësinë e bluarjes dhe shpimit ndërsa materiali përparon nga tufa udhëzuese. Boshti Y i pajisjeve të tipit zviceran ofron aftësi të plota bluarjeje dhe kursen shumë kohë në prodhim. Për më tepër, makinat tona kanë shpuese dhe vegla të mërzitshme që funksionojnë në pjesën kur ajo mbahet në nënbosht. Aftësia jonë e përpunimit të tipit zviceran na jep një mundësi përpunimi të plotë plotësisht të automatizuar në një operacion të vetëm. Përpunimi është një nga segmentet më të mëdha të biznesit të AGS-TECH Inc. Ne e përdorim atë si një operacion parësor ose një operacion dytësor pas derdhjes ose nxjerrjes së një pjese në mënyrë që të plotësohen të gjitha specifikimet e vizatimit. • SHËRBIMET E FINIKIMIT TË SIPËRFAQËSISË: Ne ofrojmë një shumëllojshmëri të gjerë trajtimesh sipërfaqësore dhe përfundime sipërfaqësore të tilla si kondicionimi i sipërfaqes për të rritur ngjitjen, depozitimi i shtresës së hollë oksidi për të rritur ngjitjen e veshjes, shpërthimi me rërë, filmi kimik, anodizimi, nitridimi, lyerja me pluhur, lyerja me spërkatje. , teknika të ndryshme të avancuara të metalizimit dhe veshjes duke përfshirë spërkatjen, rreze elektronike, avullimin, veshjen, veshjet e forta si diamanti si karboni (DLC) ose veshje me titan për veglat e shpimit dhe prerjes. • SHËRBIMET E SHËRBIMIT DHE ETETIMIT TË PRODUKTIT: Shumë prej klientëve tanë kërkojnë shënjimin dhe etiketimin, shënjimin me lazer, gdhendjen në pjesët metalike. Nëse keni ndonjë nevojë të tillë, na lejoni të diskutojmë se cili opsion do të jetë më i miri për ju. Këtu janë disa nga produktet e derdhura metalike të përdorura zakonisht. Meqenëse këto janë jashtë raftit, ju mund të kurseni në kostot e mykut në rast se ndonjë nga këto i përshtatet kërkesave tuaja: KLIKONI KETU PËR TË SHKARKONI kutitë tona të aluminit të serive 11 të derdhura nga AGS-Electronics CLICK Product Finder-Locator Service FAQJA E MEPARSHME
- Custom Manufactured Parts, Assemblies, Plastic Mold, Casting,Machining
Custom Manufactured Parts, Assemblies, Plastic Mold, Rubber Molding, Metal Casting, CNC Machining, Turning, Milling, Electrical Electronic Optical Assembly PCBA Pjesë dhe asamble dhe produkte të prodhuara me porosi Lexo më shumë Moulds Plastic & Rubber and Moulding Lexo më shumë Derdhja dhe përpunimi Lexo më shumë Nxjerrje, Produkte të Ekstruduara Lexo më shumë Stampime & Fabrikim llamarine Lexo më shumë Formëzimi i Metaleve dhe Metalurgjia e Pluhurit Lexo më shumë Formimi i telave dhe sustave Lexo më shumë Formimi dhe Formimi i Qelqit dhe Qeramikës Lexo më shumë Prodhim shtesë dhe të shpejtë Lexo më shumë Përbërës & Materiale të Përbëra Prodhim Lexo më shumë Proceset e bashkimit dhe montimit dhe fiksimit Ne prodhojmë pjesë dhe montime për ju dhe ofrojmë proceset e mëposhtme të prodhimit: • Kallëpe plastike dhe gome dhe pjesë të derdhura. Formimi me injeksion, termoformimi, derdhja termoset, formimi me vakum, derdhja me fryrje, derdhja rrotulluese, derdhja e derdhjes, derdhja e futjes dhe të tjera. • Nxjerrje plastike, gome dhe metali • Derdhje dhe pjesë të përpunuara me ngjyra dhe me ngjyra të prodhuara nga teknikat e bluarjes dhe tornimit, përpunimi i tipit zviceran. • Pjesët e metalurgjisë pluhur • Stampime metalike dhe jometale, formim llamarine, montime llamarine të salduara • Formëzimi i ftohtë dhe i nxehtë • Tela, montime teli të salduara, formim teli • Lloje të ndryshme sustash, susta forming • Prodhimi i marsheve, kuti ingranazhesh, bashkim, krimb, reduktues i shpejtësisë, cilindër, rripa transmisioni, zinxhirë transmisioni, komponentë transmisioni • Xhami i kalitur me porosi dhe antiplumb, në përputhje me standardet e NATO-s dhe ushtarake • Topat, kushinetat, rrotat dhe montimet e rrotullave • Valvulat dhe komponentët pneumatikë si unaza O, rondele dhe vula • Pjesë dhe montime qelqi dhe qeramike, komponentë rezistent ndaj vakumit dhe hermetik, lidhje metal-qeramike dhe qeramike-qeramike. • Lloje të ndryshme montimesh mekanike, optomekanike, elektromekanike, optoelektronike. • Lidhje metal-gome, metal-plastikë • Tuba dhe tuba, formim tubash, përkulje dhe montime tubash me porosi, prodhim më poshtë. • Prodhimi i tekstil me fije qelqi • Saldim duke përdorur teknika të ndryshme si saldim në vend, saldim me laser, MIG, TIG. Saldim tejzanor për pjesët plastike. • Shumëllojshmëri e madhe trajtimesh sipërfaqësore dhe përfundime sipërfaqësore si kondicionimi i sipërfaqes për të rritur ngjitjen, depozitimi i shtresës së hollë oksidi për të rritur ngjitjen e veshjes, shpërthimi me rërë, filmi kimik, anodizimi, nitridimi, lyerja me pluhur, lyerja me spërkatje, teknika të ndryshme të avancuara metalizimi dhe veshjeje duke përfshirë spërkatje, rreze elektronike, avullim, veshje, veshje të forta si diamanti si karboni (DLC) ose titan për veglat e prerjes dhe shpimit. • Shënimi dhe etiketimi, shënjimi me laser në pjesët metalike, printimi në pjesë plastike dhe gome Shkarkoni broshurën për termat e përbashkëta të inxhinierisë mekanike të përdorura nga projektuesit dhe inxhinierët Ne ndërtojmë produkte sipas specifikave dhe kërkesave tuaja të veçanta. Për t'ju ofruar cilësinë, dërgesën dhe çmimet më të mira, ne prodhojmë produkte globalisht në Kinë, Indi, Tajvan, Filipine, Korenë e Jugut, Malajzi, Sri Lanka, Turqi, SHBA, Kanada, Gjermani, Britani të Madhe dhe Japoni. Kjo na bën shumë më të fortë dhe më konkurrues globalisht se çdo custom manufacturer. Produktet tona prodhohen në mjedise të çertifikuara ISO9001:2000, QS9000, ISO14001, TS16949 dhe posedojnë markën CE, UL dhe plotësojnë standardet e tjera të industrisë. Pasi të jemi emëruar për projektin tuaj, ne mund të kujdesemi për të gjithë prodhimin, montimin, testimin, kualifikimin, transportin dhe doganën sipas dëshirës tuaj. Nëse preferoni, ne mund të depozitojmë pjesët tuaja, të montojmë komplete të personalizuara, të printojmë dhe etiketojmë emrin dhe markën e kompanisë suaj dhe t'ua dërgojmë klientëve tuaj. Me fjalë të tjera, ne mund të jemi edhe qendra juaj e magazinimit dhe shpërndarjes nëse preferoni. Duke qenë se magazinat tona ndodhen pranë porteve kryesore detare, kjo na jep përparësi logjistike. Për shembull, kur produktet tuaja mbërrijnë në një port të madh detar të SHBA-së, ne mund transportojmë drejtpërdrejt në një magazinë aty pranë ku mund të ruajmë, montojmë, bëjmë komplete, etiketojmë, printojmë, paketojmë sipas zgjedhjes suaj dhe hedhim dërgoni te klientët tuaj. Ne nuk furnizojmë vetëm produkte. Kompania jonë punon me kontrata me porosi ku ne vijmë në faqen tuaj, vlerësojmë projektin tuaj në vend dhe zhvillojmë një propozim projekti me porosi të krijuar për ju. Më pas ne dërgojmë ekipin tonë me përvojë për të zbatuar projektin. Më shumë informacion rreth punës sonë inxhinierike mund të gjeni në http://www.ags-engineering.com -Ne marrim projekte të vogla si dhe projekte të mëdha në shkallë industriale. Si hap i parë, ne mund t'ju lidhim ose me telefon, telekonferencë ose mesazher MSN me anëtarët e ekipit tonë të ekspertëve, në mënyrë që të mund të komunikoni drejtpërdrejt me një ekspert, të bëni pyetje dhe të diskutoni projektin tuaj. Na telefononi dhe nëse është e nevojshme do të vijmë dhe do t'ju vizitojmë. FAQJA E MEPARSHME