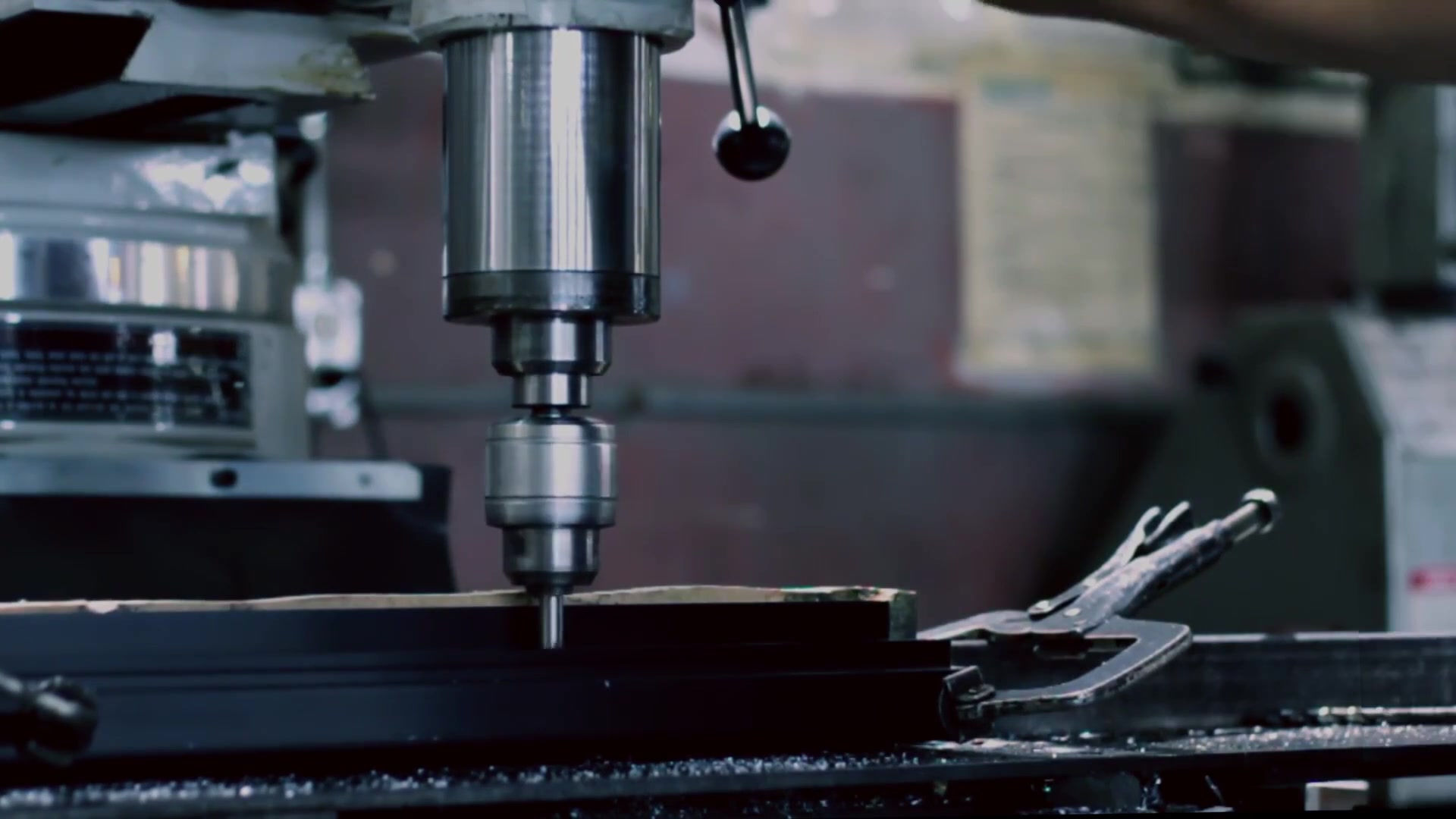
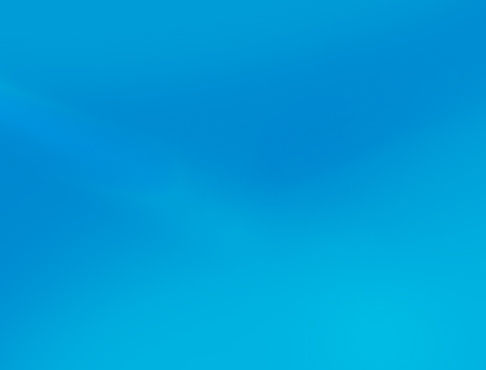
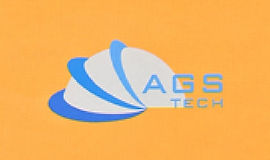
Pabrikan Custom Global, Integrator, Consolidator, Mitra Outsourcing pikeun Rupa-rupa Produk & Jasa.
Kami mangrupikeun sumber hiji-eureun anjeun pikeun manufaktur, fabrikasi, rékayasa, konsolidasi, integrasi, outsourcing produk & jasa anu diproduksi sareng kaluar-rak.
Pilih Basa anjeun
-
Manufaktur custom
-
Manufaktur Kontrak Domestik & Global
-
Manufaktur Outsourcing
-
Ngayakeun Doméstik & Global
-
Consolidation
-
Integrasi Téknik
-
Jasa Téknik
ELECTRICAL DISCHARGE MACHINING (EDM), also referred to as SPARK-EROSION or ELECTRODISCHARGE MACHINING, SPARK ERODING, DIE SINKING_cc781905-5cde-3194-bb3b -136bad5cf58d_or WIRE EROSION, is a NON-CONVENTIONAL MANUFACTURING process where erosion of metals takes place and desired shape is obtained using electrical discharges in the form tina sparks. Kami ogé nawiskeun sababaraha jinis EDM, nyaéta NO-WEAR EDM, WIRE EDM (WEDM), EDM GRINDING (EDG), DIE-SINKING EDM, ELECTRICAL-DISCHARGE MILLING, micro-EDM_cc7-81EDM -5cde-3194-bb3b-136bad5cf58d_and ELECTROCHEMICAL-DISCHARGE GRINDING (ECDG). Sistem EDM urang diwangun ku parabot ngawangun / éléktroda jeung workpiece disambungkeun ka catu daya DC sarta diselapkeun dina cairan diéléktrik nonconducting listrik. Saatos 1940, machining listrik parantos janten salah sahiji téknologi produksi anu paling penting sareng populér di industri manufaktur.
Nalika jarak antara dua éléktroda diréduksi, inténsitas médan listrik dina volume antara éléktroda jadi leuwih gede dibandingkeun kakuatan diéléktrik dina sababaraha titik, nu megatkeun, ahirna ngabentuk sasak pikeun arus ngalir antara dua éléktroda. Hiji busur listrik sengit dihasilkeun ngabalukarkeun pemanasan signifikan pikeun ngalembereh nyangkokkeun sabagian workpiece jeung sababaraha bahan tooling. Hasilna, bahan dikaluarkeun tina duanana éléktroda. Dina waktu nu sarua, cairan diéléktrik dipanaskeun gancang, hasilna évaporasi cairan dina celah arc. Sakali aliran ayeuna eureun atawa dieureunkeun panas dikaluarkeun tina gelembung gas ku cairan diéléktrik sabudeureun tur gelembung cavitates (runtuh). Gelombang shock dijieun ku runtuhna gelembung urang jeung aliran cairan diéléktrik siram lebu tina beungeut workpiece sarta entrain sagala bahan workpiece lebur kana cairan diéléktrik. Laju pengulangan pikeun discharges ieu antara 50 nepi ka 500 kHz, tegangan antara 50 nepi ka 380 V jeung arus antara 0,1 jeung 500 Ampere. Diéléktrik cair anyar kayaning minyak mineral, minyak tanah atawa sulingan & cai deionized biasana conveyed kana volume antar-éléktroda mawa jauh partikel padet (dina bentuk lebu) jeung proprieties insulating diéléktrik nu disimpen deui. Saatos aliran arus, bédana poténsial antara dua éléktroda dibalikeun deui sapertos sateuacan rusak, ku kituna tiasa ngarecahna diéléktrik cair énggal. Mesin pelepasan listrik modern (EDM) kami nawiskeun gerakan anu dikontrol sacara numerik sareng dilengkepan pompa sareng sistem nyaring pikeun cairan diéléktrik.
Electrical discharge machining (EDM) nyaéta métode machining utamana dipaké pikeun logam teuas atawa nu bakal hésé pisan mesin jeung téhnik konvensional. EDM ilaharna jalan kalawan sagala bahan anu konduktor listrik, sanajan métode pikeun machining insulating keramik jeung EDM ogé geus diusulkeun. Titik lebur sareng panas laten lebur mangrupikeun sipat anu nangtukeun volume logam anu dipiceun per sékrési. Nu leuwih luhur nilai ieu, nu laun laju ngaleupaskeun bahan. Kusabab prosés machining ngurangan listrik teu ngalibetkeun sagala énergi mékanis, karasa, kakuatan, jeung kateguhan workpiece nu teu mangaruhan laju panyabutan. Frékuénsi ngurangan atawa énergi per ngurangan, tegangan jeung arus variatif pikeun ngadalikeun ongkos panyabutan bahan. Laju panyabutan bahan sareng kakasaran permukaan ningkat kalayan ningkatna dénsitas arus sareng ngirangan frékuénsi percikan. Urang tiasa motong contours intricate atanapi cavities dina baja pre-hardened maké EDM tanpa merlukeun perlakuan panas pikeun soften na ulang heuras aranjeunna. Urang bisa make metoda ieu kalawan sagala logam atawa alloy logam kawas titanium, hastelloy, kovar, sarta inconel. Aplikasi tina prosés EDM ngawengku shaping of polycrystalline parabot inten. EDM dianggap métode machining non-tradisional atawa non-konvensional sapanjang kalawan prosés kayaning machining éléktrokimia (ECM), motong jet cai (WJ, AWJ), motong laser. Di sisi séjén métode machining konvensional kaasup péngkolan, panggilingan, grinding, pangeboran sarta prosés séjén anu mékanisme panyabutan bahan dasarna dumasar kana gaya mékanis. Éléktroda pikeun machining listrik-discharge (EDM) dijieun tina grafit, kuningan, tambaga jeung alloy tambaga-tungsten. Diaméter éléktroda handap ka 0.1mm mungkin. Kusabab maké alat mangrupa fenomena nu teu dipikahayang mangaruhan adversely akurasi diménsi dina EDM, urang ngamangpaatkeun prosés nu disebut NO-WEAR EDM, ku cara ngabalikeun polaritasna sarta ngagunakeun parabot tambaga pikeun ngaleutikan maké alat.
Ideally disebutkeun, nu electrical-discharge machining (EDM) bisa dianggap runtuyan ngarecahna tur restorasi cairan diéléktrik antara éléktroda. Dina kanyataanana kumaha oge, ngaleupaskeun lebu ti wewengkon antar-éléktroda ampir sok parsial. Ieu ngabalukarkeun proprieties listrik diéléktrik dina wewengkon antar-éléktroda jadi béda ti nilai nominal maranéhanana sarta robah kalawan waktu. Jarak antar-éléktroda, (spark-gap), disaluyukeun ku algoritma kontrol mesin husus dipaké. The spark-gap di EDM hanjakalna kadang jadi pondok-circuited ku lebu. Sistem kontrol éléktroda bisa jadi gagal pikeun meta cukup gancang pikeun nyegah dua éléktroda (alat jeung workpiece) tina sirkuit pondok. Sirkuit pondok anu teu dihoyongkeun ieu nyumbang kana panyabutan bahan béda ti kasus idéal. Urang mayar utmost pentingna mun flushing Peta guna mulangkeun sipat insulating tina diéléktrik ku kituna arus salawasna kajadian dina titik wewengkon antar-éléktroda, kukituna ngaminimalkeun kamungkinan robah dihoyongkeun bentuk (karusakan) tina alat-éléktroda. jeung workpiece. Pikeun ménta hiji géométri husus, alat EDM dipandu sapanjang jalur dipikahoyong deukeut pisan workpiece nu tanpa noel eta, Urang nengetan utmost kana kinerja kontrol gerak dina pamakéan. Ku cara ieu, sajumlah ageung discharges / sparks lumangsung, sarta masing-masing nyumbang kana ngaleupaskeun bahan tina duanana alat jeung workpiece, dimana kawah leutik kabentuk. Ukuran kawah mangrupa fungsi tina parameter téhnologis diatur pikeun pakasaban husus di leungeun jeung dimensi bisa rupa-rupa ti skala nano (saperti dina kasus operasi mikro-EDM) nepi ka sababaraha ratusan mikrométer dina kaayaan roughing. Kawah leutik ieu dina alat ngabalukarkeun erosi bertahap tina éléktroda disebut "pakaian alat". Pikeun counteract pangaruh detrimental tina maké dina géométri workpiece urang terus ngaganti alat-éléktroda salila operasi machining. Kadang-kadang urang ngahontal ieu ku ngagunakeun kawat terus diganti salaku éléktroda (prosés EDM ieu disebut oge WIRE EDM ). Kadang-kadang urang nganggo alat-éléktroda dina cara sapertos anu ngan sabagian leutik eta sabenerna kalibet dina prosés machining sarta porsi ieu dirobah rutin. Ieu, contona, dina kasus nalika nganggo disk puteran salaku alat-éléktroda. prosés ieu disebut EDM GRINDING. Acan téhnik séjén kami nyebarkeun diwangun ku ngagunakeun susunan éléktroda kalayan ukuran béda jeung wangun salila operasi EDM sarua pikeun ngimbangan maké. Kami nelepon téknik éléktroda sababaraha ieu, sareng paling sering dianggo nalika éléktroda alat ulangan dina bentuk négatip anu dipikahoyong sareng maju ka arah kosong sapanjang arah tunggal, biasana arah vertikal (ie z-sumbu). Ieu nyarupaan tilelep tina alat kana cairan diéléktrik nu workpiece nu immersed, sarta ku kituna eta disebut as DIE-SINKING EDM_cc781905-5cde-3194-bb3b5c-5c58d-1568d-5cde-3194-bb3b-5scc-time-1368d-1368d-1568d-136d5c5c5c 3194-bb3b-136bad5cf58d_KONVENSIONAL EDM or RAM EDM). Mesin pikeun operasi ieu disebut SINKER EDM. Éléktroda pikeun jinis EDM ieu ngagaduhan bentuk anu kompleks. Lamun géométri final dicandak ngagunakeun éléktroda biasana basajan ngawangun dipindahkeun sapanjang sababaraha arah sarta ogé tunduk kana rotations, urang nelepon eta EDM panggilingan. Jumlah maké éta mastikeun gumantung kana parameter téhnologis dipaké dina operasi (polaritas, arus maksimum, tegangan circuit kabuka). Contona, in micro-EDM, ogé katelah m-EDM, parameter ieu biasana diatur dina nilai nu dibangkitkeun maké parna. Ku alatan éta, ngagem mangrupikeun masalah utama di daérah éta anu urang ngaminimalkeun ngagunakeun akumulasi akumulasi. Contona pikeun ngaleutikan maké éléktroda grafit, generator digital, controllable dina milliseconds, reverses polaritasna sakumaha electro-erosi lumangsung. Ieu ngakibatkeun pangaruh sarupa electroplating nu terus deposit grafit eroded deui éléktroda nu. Dina metodeu anu sanés, anu disebut sirkuit "Zero Wear" kami ngaminimalkeun sabaraha sering discharge dimimitian sareng lirén, tetep salami mungkin. Laju panyabutan bahan dina machining listrik-discharge tiasa diperkirakeun tina:
MRR = 4 x 10 exp(4) x I x Tw exp (-1,23)
Di dieu MRR aya dina mm3 / mnt, I ayeuna di Amperes, Tw nyaéta titik lebur workpiece di K-273.15K. The exp nangtung pikeun exponent.
Di sisi anu sanésna, laju ngagem Wt éléktroda tiasa didapet tina:
Wt = ( 1,1 x 10exp(11) ) x I x Ttex(-2,38)
Di dieu Wt aya dina mm3 / mnt sareng Tt mangrupikeun titik lebur bahan éléktroda dina K-273.15K.
Tungtungna, babandingan maké workpiece ka éléktroda R bisa didapet tina:
R = 2,25 x Trexp(-2,38)
Di dieu Tr nyaéta babandingan titik lebur workpiece jeung éléktroda.
SINKER EDM :
Sinker EDM, disebut oge as CAVITY TYPE EDM or_cc781905-194ssssss5b3b3, sarta electrocde insulating in EDM_cc78. Éléktroda sareng workpiece disambungkeun ka catu daya. Catu daya ngahasilkeun poténsi listrik antara dua. Nalika éléktroda ngadeukeutan workpiece, ngarecahna diéléktrik lumangsung dina cairan, ngabentuk saluran plasma, sarta sparks leutik jumps. Percikan api biasana neunggeul hiji-hiji sabab teu mungkin lokasi anu beda-beda dina rohangan antar-éléktroda mibanda ciri-ciri listrik lokal anu idéntik anu bakal ngamungkinkeun hiji percikan lumangsung dina sakabéh lokasi éta sakaligus. Ratusan rébu sparks ieu lumangsung dina titik acak antara éléktroda jeung workpiece per detik. Salaku logam dasar erodes, sarta gap narik salajengna naek, éléktroda ieu lowered otomatis ku mesin CNC urang ku kituna prosés bisa neruskeun uninterrupted. Alat-alat kami ngagaduhan siklus pangendali anu katelah "on time" sareng "off time". Setélan on time nangtukeun panjang atawa lilana spark. Waktu anu langkung panjang ngahasilkeun rongga anu langkung jero pikeun narik éta sareng sadaya percikan anu salajengna pikeun siklus éta, nyiptakeun bérés anu langkung kasar dina workpiece sareng sabalikna. Waktu pareum nyaéta periode waktu anu hiji percikan diganti ku anu séjén. Waktu pareum anu langkung lami ngamungkinkeun cairan diéléktrik ngalir ngaliwatan nozzle pikeun ngabersihan lebu anu eroded, sahingga ngahindarkeun sirkuit pondok. Setelan ieu disaluyukeun dina mikro detik.
KAWAT EDM :
In WIRE ELECTRICAL DISCHARGE MACHINING (WEDM), also called WIRE-CUT EDM or WIRE CUTTING, we feed a ipis kawat logam single-strand tina kuningan ngaliwatan workpiece nu, nu submerged dina tank cairan diéléktrik. Kawat EDM mangrupa variasi penting EDM. Urang aya kalana ngagunakeun kawat-cut EDM pikeun motong pelat sakumaha kandel 300mm sarta nyieun punches, parabot, sarta maot tina logam teuas nu hese mesin jeung métode manufaktur lianna. Dina prosés ieu nu nyarupaan motong kontur ku band saw, kawat, nu terus fed ti spool a, dilaksanakeun antara Panungtun inten luhur jeung handap. Panungtun anu dikontrol CNC gerak dina pesawat x–y jeung pituduh luhur ogé bisa gerak sacara mandiri dina sumbu z–u–v, nimbulkeun kamampuhan pikeun motong wangun tapered jeung transisi (sapertos bunderan di handap jeung pasagi di luhur). Pituduh luhur bisa ngadalikeun gerakan sumbu dina x–y–u–v–i–j–k–l–. Hal ieu ngamungkinkeun WEDM motong bentuk pisan intricate tur hipu. Rata-rata motong kerf pakakas urang nu achieves ongkos ékonomi pangalusna sarta waktu machining nyaeta 0,335 mm ngagunakeun Ø 0,25 kuningan, tambaga atawa kawat tungsten. Sanajan kitu Panungtun inten luhur jeung handap alat CNC kami akurat ngeunaan 0,004 mm, sarta bisa boga jalur motong atanapi kerf sakumaha leutik 0,021 mm ngagunakeun Ø 0,02 mm kawat. Jadi motong bener sempit mungkin. Lebar motong leuwih badag batan lebar kawat sabab sparking lumangsung ti sisi kawat ka workpiece nu, ngabalukarkeun erosi. Ieu '' overcut '' perlu, pikeun loba aplikasi éta bisa diprediksi sahingga bisa diimbuhan pikeun (dina mikro-EDM ieu teu mindeng kasus). The spools kawat panjang-an 8 kg spool of 0,25 mm kawat panjangna ngan leuwih 19 kilométer. Diaméter kawat tiasa sakedik 20 mikrométer sareng akurasi géométri aya dina lingkungan +/- 1 mikrométer. Urang umumna ngagunakeun kawat ngan sakali jeung ngadaur mulangkeunana sabab relatif murah. Ieu ngumbara dina laju konstan 0,15 ka 9m / mnt sarta kerf konstan (slot) dijaga salila cut a. Dina prosés EDM kawat-cut kami ngagunakeun cai salaku cairan diéléktrik, ngadalikeun résistansi sarta sipat listrik lianna kalayan saringan jeung unit de-ionizer. caina flushes lebu cut jauh ti zone motong. Flushing mangrupa faktor penting dina nangtukeun laju feed maksimum pikeun ketebalan bahan tinangtu sahingga urang tetep konsisten. Motong speed dina kawat EDM dinyatakeun dina watesan cross-sectional aréa cut per Unit waktos, kayaning 18.000 mm2 / hr pikeun 50mm kandel D2 alat baja. Laju motong linier pikeun hal ieu bakal 18,000/50 = 360mm / hr Laju panyabutan bahan dina kawat EDM nyaéta:
MRR = Vf xhxb
Di dieu MRR aya dina mm3 / mnt, Vf nyaéta laju feed kawat kana workpiece dina mm / mnt, h nyaéta ketebalan atawa jangkungna dina mm, sarta b nyaéta kerf nu:
b = dw + 2s
Di dieu dw nyaéta diaméter kawat jeung s nyaéta celah antara kawat jeung workpiece dina mm.
Marengan tolerances tighter, modern kami multi sumbu EDM puseur machining kawat-motong geus ditambahkeun fitur kayaning multi huluna pikeun motong dua bagian dina waktos anu sareng, kadali pikeun nyegah pegatna kawat, fitur timer Threading otomatis bisi kawat megatkeun, sarta diprogram. strategi machining ngaoptimalkeun operasi, kamampuhan motong lempeng jeung sudut.
Kawat-EDM nawarkeun kami stresses residual low, sabab teu merlukeun gaya motong tinggi pikeun nyoplokkeun bahan. Lamun énergi / kakuatan per pulsa relatif low (saperti dina pagawean pagawean), saeutik parobahan dina sipat mékanis bahan diperkirakeun alatan stresses residual low.
ELECTRICAL-DISCHARGE GRINDING (EDG) : Roda grinding teu ngandung abrasives, aranjeunna dijieunna tina grafit atawa kuningan. Sparks repetitive antara kabayang puteran jeung workpiece miceun bahan tina surfaces workpiece. Laju ngaleupaskeun bahan nyaéta:
MRR = K x I
Di dieu MRR aya dina mm3 / mnt, I ayeuna di Amperes, sarta K nyaéta faktor bahan workpiece dina mm3 / A-mnt. Urang sering ngagunakeun grinding listrik-discharge pikeun nempo slits sempit on komponén. Urang kadang ngagabungkeun prosés EDG (Electrical-Discharge Grinding) sareng prosés ECG (Electrochemical Grinding) dimana bahan dileungitkeun ku tindakan kimia, pelepasan listrik tina kabayang grafit ngarobih pilem oksida sareng dikumbah ku éléktrolit. Prosésna disebut ELECTROCHEMICAL-DISCHARGE GRINDING (ECDG). Sanaos prosés ECDG nganggo kakuatan anu langkung ageung, éta mangrupikeun prosés anu langkung gancang tibatan EDG. Urang lolobana grind parabot carbide ngagunakeun téhnik ieu.
Aplikasi tina Mesin Discharge Listrik:
Produksi prototipe:
Kami nganggo prosés EDM dina pembuatan kapang, alat sareng manufaktur paeh, ogé pikeun ngadamel prototipe sareng bagian produksi, khususna pikeun industri aerospace, mobil sareng éléktronika dimana jumlah produksina relatif rendah. Dina Sinker EDM, a grafit, tungsten tambaga atawa éléktroda tambaga murni ieu machined kana bentuk dipikahoyong (négatip) jeung fed kana workpiece dina tungtung hiji ram nangtung.
Nyieun Coinage paeh:
Pikeun nyiptakeun paeh pikeun ngahasilkeun perhiasan sareng lencana ku prosés koin (stamping), master positip tiasa didamel tina pérak sterling, sabab (kalayan setélan mesin anu pas) master sacara signifikan eroded sareng dianggo ngan sakali. Paeh négatip hasilna ieu lajeng hardened sarta dipaké dina palu serelek pikeun ngahasilkeun flat dicap tina cutout lambar blanks tina parunggu, pérak, atawa low buktina emas alloy. Pikeun lencana, rumah susun ieu tiasa ngawangun deui kana permukaan anu melengkung ku paeh anu sanés. EDM jenis ieu biasana dipigawé dina submerged dina diéléktrik basis minyak. Obyék rengse bisa jadi salajengna disampurnakeun ku teuas (kaca) atawa lemes (cet) enameling jeung / atawa electroplated kalawan emas murni atawa nikel. Bahan anu langkung lemes sapertos pérak tiasa diukir ku tangan salaku perbaikan.
Pangeboran liang leutik:
Dina mesin EDM kawat-cut kami, kami nganggo EDM pangeboran liang leutik nyieun liang ngaliwatan dina workpiece ngaliwatan nu thread kawat pikeun operasi EDM kawat-cut. sirah EDM misah husus pikeun pangeboran liang leutik anu dipasang dina mesin kawat-cut kami nu ngidinan pelat hardened badag geus rengse bagian eroded ti aranjeunna sakumaha diperlukeun tur tanpa pre-pangeboran. Urang ogé ngagunakeun EDM liang leutik pikeun bor barisan liang kana edges of wilah turbin dipaké dina mesin jet. Aliran gas ngaliwatan liang-liang leutik ieu ngamungkinkeun mesin ngagunakeun suhu anu langkung luhur tibatan anu mungkin. The-suhu luhur, pisan teuas, alloy kristal tunggal wilah ieu dijieunna tina ngajadikeun machining konvensional liang ieu kalawan rasio aspék tinggi pisan hésé komo teu mungkin. wewengkon aplikasi séjén pikeun EDM liang leutik nyaéta nyieun orifices mikroskopis pikeun komponén sistem suluh. Di sagigireun huluna EDM terpadu, urang nyebarkeun stand-nyalira liang leutik pangeboran mesin EDM kalawan sumbu x-y kana mesin buta atawa ngaliwatan liang. EDM drills bore liang ku kuningan panjang atawa éléktroda tube tambaga nu rotates dina cuk kalawan aliran konstan cai sulingan atawa deionized ngalir ngaliwatan éléktroda salaku agén flushing na diéléktrik. Sababaraha EDMs pangeboran liang leutik anu bisa bor ngaliwatan 100 mm baja lemes atawa malah hardened kirang ti 10 detik. Liang antara 0,3 mm jeung 6,1 mm bisa dihontal dina operasi pangeboran ieu.
Mesin disintegrasi logam:
Kami ogé ngagaduhan mesin EDM khusus pikeun tujuan khusus pikeun ngaleungitkeun alat anu rusak (bor bit atanapi keran) tina potongan kerja. Prosés ieu disebut ''mesin disintegrasi logam''.
Kaunggulan jeung kalemahan Electrical-Discharge Machining:
Kaunggulan tina EDM ngawengku machining tina:
- Wangun kompléks nu disebutkeun bakal hésé pikeun ngahasilkeun kalawan parabot motong konvensional
- Bahan pisan teuas pikeun tolerances deukeut pisan
- Potongan karya leutik pisan dimana alat motong konvensional tiasa ngaruksak bagian tina kaleuwihan tekanan alat motong.
- Henteu aya kontak langsung antara alat sareng karya. Kituna bagian hipu jeung bahan lemah bisa machined tanpa distorsi nanaon.
- A finish permukaan alus bisa didapet.
- liang pisan rupa bisa gampang dibor.
Kelemahan EDM diantarana:
- Laju slow ngaleupaskeun bahan.
- The tambahan waktu jeung ongkos dipaké pikeun nyieun éléktroda pikeun ram / sinker EDM.
- Reproducing sudut seukeut dina workpiece nu hese alatan maké éléktroda.
- Konsumsi kakuatan tinggi.
- ''Overcut'' kabentuk.
- Pakakas alat kaleuleuwihan lumangsung salila machining.
- Bahan non-conductive sacara éléktrik ngan ukur tiasa didamel ku set-up prosés anu khusus.