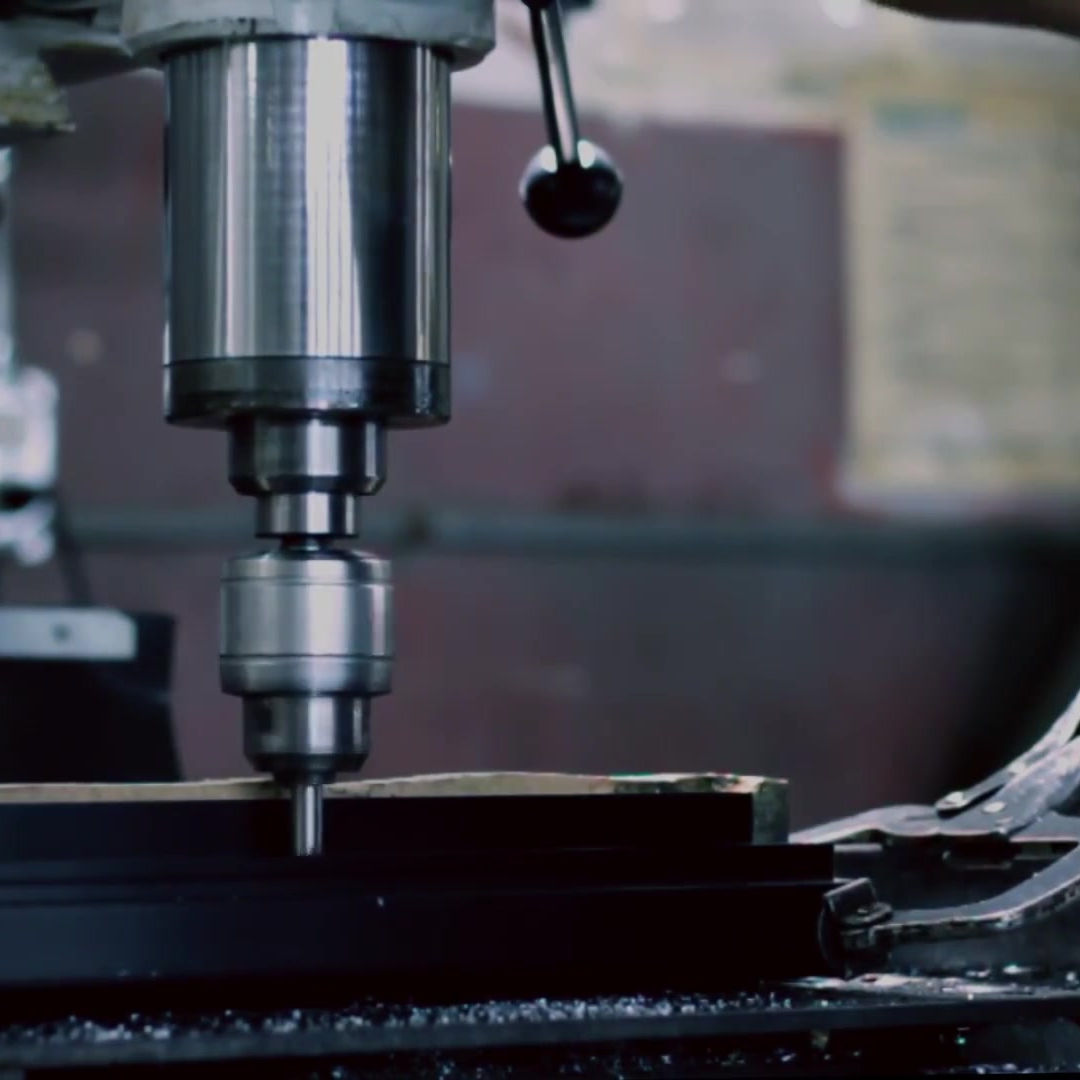
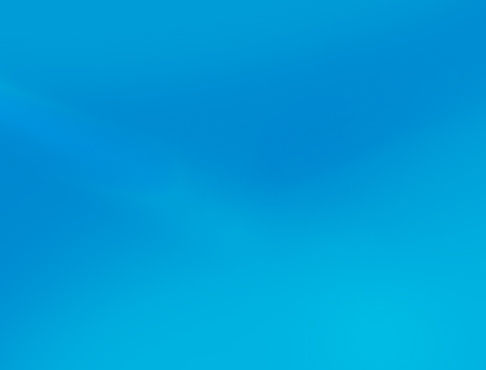
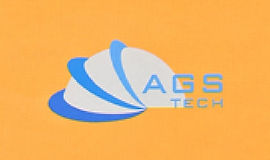
Global Custom Manufacturer, Integrator, Consolidator, Outsourcing Partner för ett brett utbud av produkter och tjänster.
Vi är din enda källa för tillverkning, tillverkning, ingenjörskonst, konsolidering, integration, outsourcing av specialtillverkade och off-shelfprodukter och tjänster.
Välj ditt språk
-
Custom Manufacturing
-
Inhemsk och global kontraktstillverkning
-
Outsourcing av tillverkning
-
Inhemsk och global upphandling
-
Consolidation
-
Engineering Integration
-
Ingenjörstjänster
Bland de många JOININGS-tekniker som vi använder i tillverkningen, läggs särskild tonvikt på SVETSNING, LÖDNING, LÖDNING, LIMBINDNING och ANPASSAD MEKANISK MONTERING eftersom dessa tekniker används i stor utsträckning i applikationer som tillverkning av hermetiska sammansättningar, högteknologisk produkttillverkning och specialiserad tätning. Här kommer vi att koncentrera oss på de mer specialiserade aspekterna av dessa sammanfogningstekniker eftersom de är relaterade till tillverkning av avancerade produkter och sammansättningar.
FUSIONSSVETSNING: Vi använder värme för att smälta och sammansmälta material. Värme tillförs av el eller högenergibalkar. De typer av smältsvetsning vi använder är OXYFUEL GASSVETNING, BÅGSvetsning, HÖGENERGISvetsning.
SOLID-STATE SVETS: Vi sammanfogar delar utan att smälta och smälta. Våra solid-state svetsmetoder är KALL, ULTRALJUD, MOTSTÅND, FRIKTION, EXPLOSIONSSVETSNING och DIFFUSIONSBINDNING.
LÖDNING & LÖDNING: De använder tillsatsmetaller och ger oss fördelen att arbeta vid lägre temperaturer än vid svetsning, vilket gör att produkterna inte skadas av strukturen. Information om vår hårdlödningsanläggning som producerar keramiska till metallbeslag, hermetisk tätning, vakuumgenomföringar, hög- och ultrahögvakuum och vätskekontrollkomponenter finns här:Broschyr för lödningsfabrik
ADHESIVBINDNING: På grund av mångfalden av lim som används inom industrin och även mångfalden av applikationer, har vi en särskild sida för detta. För att gå till vår sida om limning, klicka här.
ANPASSAD MEKANISK MONTERING: Vi använder en mängd olika fästelement som bultar, skruvar, muttrar, nitar. Våra fästelement är inte begränsade till standardfästen från hyllan. Vi designar, utvecklar och tillverkar specialfästen som är gjorda av icke-standardiserade material så att de kan uppfylla kraven för speciella applikationer. Ibland önskas elektrisk eller värme icke-konduktivitet medan ibland konduktivitet. För vissa speciella tillämpningar kan en kund vilja ha speciella fästelement som inte kan tas bort utan att förstöra produkten. Det finns oändliga idéer och tillämpningar. Vi har allt för dig, om inte från hyllan kan vi snabbt utveckla det. För att gå till vår sida om mekanisk montering, klicka här. Låt oss undersöka våra olika sammanfogningstekniker mer detaljerat.
OXYFUEL GAS WELDING (OFW): Vi använder en bränslegas blandad med syre för att producera svetslågan. När vi använder acetylen som bränsle och syre, kallar vi det oxyacetylengassvetsning. Två kemiska reaktioner inträffar i förbränningsprocessen av oxyfuel:
C2H2 + O2 ------» 2CO + H2 + Värme
2CO + H2 + 1,5 O2--------» 2 CO2 + H2O + Värme
Den första reaktionen dissocierar acetylenen till kolmonoxid och väte samtidigt som den producerar cirka 33 % av den totala värme som genereras. Den andra processen ovan representerar ytterligare förbränning av väte och kolmonoxid samtidigt som den producerar cirka 67 % av den totala värmen. Temperaturen i lågan är mellan 1533 och 3573 Kelvin. Syreprocenten i gasblandningen är viktig. Om syrehalten är mer än hälften blir lågan ett oxidationsmedel. Detta är inte önskvärt för vissa metaller men önskvärt för andra. Ett exempel när oxiderande låga är önskvärt är kopparbaserade legeringar eftersom det bildar ett passiveringsskikt över metallen. Å andra sidan, när syrehalten minskar är full förbränning inte möjlig och lågan blir en reducerande (förkolande) låga. Temperaturerna i en reducerande låga är lägre och därför är den lämplig för processer som lödning och hårdlödning. Andra gaser är också potentiella bränslen, men de har vissa nackdelar jämfört med acetylen. Ibland levererar vi tillsatsmetaller till svetszonen i form av tillsatsstavar eller tråd. Vissa av dem är belagda med flussmedel för att fördröja oxidation av ytor och på så sätt skydda den smälta metallen. En ytterligare fördel som flussmedlet ger oss är avlägsnandet av oxider och andra ämnen från svetszonen. Detta leder till starkare bindning. En variant av oxyfuel-gassvetsningen är TRYCKGASVETSNING, där de två komponenterna värms upp vid deras gränssnitt med hjälp av oxyacetylengasbrännare och när gränssnittet börjar smälta dras brännaren tillbaka och en axiell kraft appliceras för att pressa samman de två delarna tills gränssnittet stelnat.
BÅGSVETSNING: Vi använder elektrisk energi för att producera en båge mellan elektrodspetsen och de delar som ska svetsas. Strömförsörjningen kan vara AC eller DC medan elektroderna är antingen förbrukningsbara eller icke förbrukningsbara. Värmeöverföring vid bågsvetsning kan uttryckas med följande ekvation:
H/l = ex VI/v
Här är H värmetillförseln, l är svetslängden, V och I är spänningen och strömmen som appliceras, v är svetshastigheten och e är processeffektiviteten. Ju högre verkningsgrad "e" desto mer fördelaktigt används den tillgängliga energin för att smälta materialet. Värmetillförseln kan också uttryckas som:
H = ux (Volym) = ux A xl
Här är u den specifika energin för smältning, A svetsens tvärsnitt och l svetslängden. Från de två ekvationerna ovan kan vi få:
v = ex VI / u A
En variant av bågsvetsning är SHELDED METAL RC WELDING (SMAW) som utgör cirka 50 % av alla industri- och underhållssvetsprocesser. ELEKTRISK BÅGSVETSNING (STICK WELDING) utförs genom att röra spetsen på en belagd elektrod mot arbetsstycket och snabbt dra tillbaka det till ett tillräckligt avstånd för att bibehålla ljusbågen. Vi kallar denna process även stavsvetsning eftersom elektroderna är tunna och långa stift. Under svetsprocessen smälter elektrodens spets tillsammans med dess beläggning och basmetallen i närheten av bågen. En blandning av basmetallen, elektrodmetallen och ämnen från elektrodbeläggningen stelnar i svetsområdet. Beläggningen av elektroden deoxiderar och ger en skyddsgas i svetsområdet, vilket skyddar den från syret i miljön. Därför kallas processen skärmad metallbågsvetsning. Vi använder strömmar mellan 50 och 300 Ampere och effektnivåer i allmänhet mindre än 10 kW för optimal svetsprestanda. Också av betydelse är polariteten hos DC-strömmen (strömflödesriktningen). Rak polaritet där arbetsstycket är positivt och elektroden är negativ är att föredra vid svetsning av plåt på grund av dess ytliga penetration och även för fogar med mycket stora mellanrum. När vi har omvänd polaritet, dvs elektroden är positiv och arbetsstycket negativ kan vi uppnå djupare svetsgenomträngningar. Med växelström, eftersom vi har pulserande bågar, kan vi svetsa tjocka sektioner med elektroder med stor diameter och maximala strömmar. SMAW-svetsmetoden är lämplig för arbetsstyckestjocklekar på 3 till 19 mm och ännu mer med hjälp av flergångstekniker. Slaggen som bildas ovanpå svetsen måste avlägsnas med en stålborste, så att det inte uppstår korrosion och brott på svetsområdet. Detta ökar naturligtvis kostnaden för bågsvetsning av skärmad metall. Ändå är SMAW den mest populära svetstekniken inom industri och reparationsarbete.
DÄNKBÅGSVETSNING (SÅG): I denna process skyddar vi svetsbågen med hjälp av granulära flussmedel som kalk, kiseldioxid, kalciumflorid, manganoxid...etc. Det granulära flussmedlet matas in i svetszonen genom gravitationsflöde genom ett munstycke. Flussmedlet som täcker den smälta svetszonen skyddar avsevärt från gnistor, ångor, UV-strålning etc. och fungerar som en värmeisolator och låter värme tränga djupt in i arbetsstycket. Det osammansatta flödet återvinns, behandlas och återanvänds. En spole av blank används som elektrod och matas genom ett rör till svetsområdet. Vi använder strömmar mellan 300 och 2000 Ampere. Processen för nedsänkt bågsvetsning (SAW) är begränsad till horisontella och plana lägen och cirkulära svetsar om rotation av den cirkulära strukturen (såsom rör) är möjlig under svetsning. Hastigheterna kan nå 5 m/min. SAW-processen är lämplig för tjocka plåtar och resulterar i högkvalitativa, sega, formbara och enhetliga svetsar. Produktiviteten, det vill säga mängden svetsmaterial som avsätts per timme är 4 till 10 gånger mängden jämfört med SMAW-processen.
En annan bågsvetsprocess, nämligen GAS METAL RC WELDING (GMAW) eller alternativt kallad METAL INERT GAS WELDING (MIG) är baserad på att svetsområdet skyddas av externa gaskällor som helium, argon, koldioxid...etc. Det kan finnas ytterligare deoxidationsmedel närvarande i elektrodmetallen. Förbrukningsbar tråd matas genom ett munstycke in i svetszonen. Tillverkning som involverar både järnhaltiga och icke-järnhaltiga metaller utförs med hjälp av gasmetallbågsvetsning (GMAW). Svetsproduktiviteten är ungefär 2 gånger högre än SMAW-processen. Automatiserad svetsutrustning används. Metall överförs på ett av tre sätt i denna process: "Spray Transfer" innebär överföring av flera hundra små metalldroppar per sekund från elektroden till svetsområdet. I "Globular Transfer" å andra sidan används koldioxidrika gaser och kulor av smält metall drivs av den elektriska ljusbågen. Svetsströmmarna är höga och svetspenetrationen djupare, svetshastigheten högre än vid sprayöverföring. Den klotformade överföringen är således bättre för svetsning av tyngre sektioner. Slutligen, i "Short Circuiting"-metoden, vidrör elektrodspetsen den smälta svetsbassängen och kortsluter den då metall med hastigheter över 50 droppar/sekund överförs i individuella droppar. Låga strömmar och spänningar används tillsammans med tunnare tråd. Effekterna som används är cirka 2 kW och temperaturen är relativt låg, vilket gör denna metod lämplig för tunna plåtar som är mindre än 6 mm tjocka.
En annan variant av FLUX-CORED ARC WELDING (FCAW)-processen liknar gasmetallbågsvetsning, förutom att elektroden är ett rör fyllt med flussmedel. Fördelarna med att använda elektroder med kärnflux är att de ger mer stabila bågar, ger oss möjlighet att förbättra egenskaperna hos svetsmetaller, mindre spröd och flexibel karaktär hos dess flussmedel jämfört med SMAW-svetsning, förbättrade svetskonturer. Självskärmade elektroder med kärnor innehåller material som skyddar svetszonen mot atmosfären. Vi använder cirka 20 kW effekt. Precis som GMAW-processen erbjuder FCAW-processen också möjligheten att automatisera processer för kontinuerlig svetsning, och det är ekonomiskt. Olika svetsmetallkemier kan utvecklas genom att lägga till olika legeringar till flusskärnan.
I ELECTROGAS WELDING (EGW) svetsar vi de placerade bitarna kant i kant. Det kallas ibland även STUMSVETSNING. Svetsmetall placeras i en svetshålighet mellan två delar som ska sammanfogas. Utrymmet är omslutet av två vattenkylda dammar för att förhindra att den smälta slaggen rinner ut. Dammarna flyttas upp med mekaniska drivningar. När arbetsstycket kan roteras kan vi även använda elektrogassvetsningstekniken för omkretssvetsning av rör. Elektroder matas genom en ledning för att hålla en kontinuerlig båge. Strömmar kan vara cirka 400 Ampere eller 750 Ampere och effektnivåer cirka 20 kW. Inerta gaser som kommer från antingen en elektrod med flödeskärna eller extern källa ger avskärmning. Vi använder elektrogassvetsning (EGW) för metaller som stål, titan...etc med tjocklekar från 12 mm till 75 mm. Tekniken passar bra för stora strukturer.
Ändå, i en annan teknik som kallas ELECTROSLAG WELDING (ESW) antänds ljusbågen mellan elektroden och botten av arbetsstycket och flussmedel tillsätts. När smält slagg når elektrodspetsen släcks ljusbågen. Energi tillförs kontinuerligt genom den smälta slaggens elektriska motstånd. Vi kan svetsa plåtar med tjocklekar mellan 50 mm och 900 mm och ännu högre. Strömmarna är cirka 600 Ampere medan spänningarna ligger mellan 40 – 50 V. Svetshastigheterna är cirka 12 till 36 mm/min. Tillämpningar liknar elektrogassvetsning.
En av våra icke-förbrukningsbara elektrodprocesser, GAS TUNGSTEN ARC WELDING (GTAW) även känd som TUNGSTEN INERT GAS WELDING (TIG) involverar tillförsel av en tillsatsmetall genom en tråd. För täta fogar använder vi ibland inte tillsatsmetallen. I TIG-processen använder vi inte flux, utan använder argon och helium för avskärmning. Volfram har en hög smältpunkt och förbrukas inte i TIG-svetsprocessen, därför kan konstant ström såväl som båggap upprätthållas. Effektnivåer är mellan 8 till 20 kW och strömmar vid antingen 200 Ampere (DC) eller 500 Ampere (AC). För aluminium och magnesium använder vi växelström för dess oxidrengörande funktion. För att undvika kontaminering av volframelektroden undviker vi dess kontakt med smälta metaller. Gas Tungsten Arc Welding (GTAW) är särskilt användbar för svetsning av tunna metaller. GTAW-svetsar är av mycket hög kvalitet med god ytfinish.
På grund av den högre kostnaden för vätgas är en mindre ofta använd teknik ATOMIC HYDROGEN WELDING (AHW), där vi genererar en båge mellan två volframelektroder i en avskärmande atmosfär av strömmande vätgas. AHW är också en icke förbrukbar elektrodsvetsprocess. Den diatomiska vätgasen H2 bryts ner till sin atomform nära svetsbågen där temperaturen är över 6273 Kelvin. När den bryts ned absorberar den stora mängder värme från bågen. När väteatomerna träffar svetszonen som är en relativt kall yta, rekombinerar de till diatomisk form och frigör den lagrade värmen. Energi kan varieras genom att ändra arbetsstycket till bågavstånd.
I en annan icke förbrukningsbar elektrodprocess, PLASMA BÅGSVETSNING (PAW), har vi en koncentrerad plasmabåge riktad mot svetszonen. Temperaturerna når 33 273 Kelvin i PAW. Nästan lika många elektroner och joner utgör plasmagasen. En lågströmspilotbåge initierar plasman som finns mellan volframelektroden och öppningen. Driftströmmar är i allmänhet runt 100 Ampere. En tillsatsmetall kan matas. Vid plasmabågsvetsning åstadkoms skärmning av en yttre skärmring och med användning av gaser som argon och helium. Vid plasmabågsvetsning kan ljusbågen vara mellan elektroden och arbetsstycket eller mellan elektroden och munstycket. Denna svetsteknik har fördelarna jämfört med andra metoder med högre energikoncentration, djupare och smalare svetsförmåga, bättre bågstabilitet, högre svetshastigheter upp till 1 meter/min, mindre termisk distorsion. Vi använder vanligtvis plasmabågsvetsning för tjocklekar mindre än 6 mm och ibland upp till 20 mm för aluminium och titan.
HÖGENERGISvetsning: En annan typ av smältsvetsmetod med elektronstrålesvetsning (EBW) och lasersvetsning (LBW) som två varianter. Dessa tekniker är av särskilt värde för vårt högteknologiska produkttillverkningsarbete. Vid elektronstrålesvetsning träffar höghastighetselektroner arbetsstycket och deras kinetiska energi omvandlas till värme. Den smala elektronstrålen rör sig lätt i vakuumkammaren. Generellt använder vi högvakuum vid e-beam svetsning. Plattor så tjocka som 150 mm kan svetsas. Inga skyddsgaser, flussmedel eller fyllnadsmaterial behövs. Elektronstrålepistoler har en kapacitet på 100 kW. Djupa och smala svetsar med höga bildförhållanden upp till 30 och små värmepåverkade zoner är möjliga. Svetshastigheter kan nå 12 m/min. Vid laserstrålesvetsning använder vi högeffektlasrar som värmekälla. Laserstrålar så små som 10 mikron med hög densitet möjliggör djup penetrering i arbetsstycket. Djup-till-bredd-förhållanden så mycket som 10 är möjligt med laserstrålesvetsning. Vi använder både pulsade och kontinuerliga våglasrar, med den förra i applikationer för tunna material och den senare mest för tjocka arbetsstycken upp till ca 25 mm. Effektnivåerna är upp till 100 kW. Lasersvetsningen är inte väl lämpad för optiskt mycket reflekterande material. Gaser kan också användas i svetsprocessen. Laserstrålesvetsmetoden är väl lämpad för automation och tillverkning av hög volym och kan erbjuda svetshastigheter mellan 2,5 m/min och 80 m/min. En stor fördel med denna svetsteknik är tillgången till områden där andra tekniker inte kan användas. Laserstrålar kan lätt resa till sådana svåra områden. Inget vakuum som vid elektronstrålesvetsning behövs. Svetsar med bra kvalitet & styrka, låg krympning, låg distorsion, låg porositet kan erhållas med laserstrålesvetsning. Laserstrålar kan enkelt manipuleras och formas med fiberoptiska kablar. Tekniken är därför väl lämpad för svetsning av precisionshermetiska sammansättningar, elektroniska paket etc.
Låt oss titta på våra SOLID STATE WELDING-tekniker. KALLSvetsning (CW) är en process där tryck istället för värme appliceras med hjälp av stansar eller valsar till de delar som är sammankopplade. Vid kallsvetsning måste minst en av de passande delarna vara duktil. Bästa resultat erhålls med två liknande material. Om de två metallerna som ska sammanfogas med kallsvetsning är olika kan vi få svaga och spröda fogar. Kallsvetsmetoden är väl lämpad för mjuka, formbara och små arbetsstycken såsom elektriska anslutningar, värmekänsliga behållarkanter, bimetalllister för termostater...etc. En variant av kallsvetsning är rullbindning (eller rullsvetsning), där trycket appliceras genom ett par rullar. Ibland utför vi rullsvetsning vid förhöjda temperaturer för bättre gränsytstyrka.
En annan solid state-svetsprocess vi använder är ULTRASONIC WELDING (USW), där arbetsstyckena utsätts för en statisk normalkraft och oscillerande skjuvspänningar. De oscillerande skjuvspänningarna appliceras genom spetsen på en givare. Ultraljudssvetsning utlöser svängningar med frekvenser från 10 till 75 kHz. I vissa applikationer som sömsvetsning använder vi en roterande svetsskiva som spets. Skjuvspänningar som appliceras på arbetsstyckena orsakar små plastiska deformationer, bryter upp oxidskikt, föroreningar och leder till fast tillståndsbindning. Temperaturer involverade i ultraljudssvetsning ligger långt under smältpunktstemperaturerna för metaller och ingen smältning äger rum. Vi använder ofta ultraljudssvetsning (USW) process för icke-metalliska material som plast. I termoplaster når dock temperaturerna smältpunkter.
En annan populär teknik, i FRICTION WELDING (FRW) genereras värmen genom friktion vid gränsytan mellan arbetsstyckena som ska sammanfogas. Vid friktionssvetsning håller vi ett av arbetsstyckena stationärt medan det andra arbetsstycket hålls i en fixtur och roteras med konstant hastighet. Arbetsstyckena bringas sedan i kontakt under en axiell kraft. Ytrotationshastigheten vid friktionssvetsning kan i vissa fall nå 900 m/min. Efter tillräcklig kontakt med gränsytan stoppas det roterande arbetsstycket plötsligt och den axiella kraften ökas. Svetszonen är i allmänhet ett smalt område. Friktionssvetstekniken kan användas för att sammanfoga solida och rörformiga delar gjorda av en mängd olika material. Viss blixt kan utvecklas vid gränssnittet i FRW, men denna blixt kan tas bort genom sekundär bearbetning eller slipning. Variationer av friktionssvetsprocessen finns. Till exempel "tröghetsfriktionssvetsning" involverar ett svänghjul vars rotationskinetiska energi används för att svetsa delarna. Svetsen är klar när svänghjulet stannar. Den roterande massan kan varieras och därmed den roterande kinetiska energin. En annan variant är "linjär friktionssvetsning", där linjär fram- och återgående rörelse åläggs åtminstone en av komponenterna som ska sammanfogas. I linjär friktionssvetsning behöver inte delar vara cirkulära, de kan vara rektangulära, kvadratiska eller av annan form. Frekvenser kan vara i tiotals Hz, amplituder i millimeterområdet och tryck i tiotals eller hundratals MPa. Slutligen är "friction stir welding" något annorlunda än de andra två som förklaras ovan. Medan vid tröghetsfriktionssvetsning och linjär friktionssvetsning uppvärmning av gränssnitt uppnås genom friktion genom gnidning av två kontaktytor, gnids i friktionsomrörningssvetsningsmetoden en tredje kropp mot de två ytorna som ska sammanfogas. Ett roterande verktyg med 5 till 6 mm diameter bringas i kontakt med fogen. Temperaturerna kan öka till värden mellan 503 till 533 Kelvin. Uppvärmning, blandning och omrörning av materialet i fogen sker. Vi använder friktionssvetsning på en mängd olika material inklusive aluminium, plast och kompositer. Svetsar är enhetliga och kvaliteten är hög med minimala porer. Inga ångor eller stänk produceras vid friktionssvetsning och processen är väl automatiserad.
RESISTANSSVETSNING (RW): Värmen som krävs för svetsning produceras av det elektriska motståndet mellan de två arbetsstyckena som ska sammanfogas. Inget flussmedel, skyddsgaser eller förbrukningsbara elektroder används vid motståndssvetsning. Jouleuppvärmning sker vid motståndssvetsning och kan uttryckas som:
H = (kvadrat I) x R xtx K
H är värme som genereras i joule (watt-sekunder), I ström i ampere, R resistans i ohm, t är tiden i sekunder som strömmen flyter igenom. Faktorn K är mindre än 1 och representerar den del av energi som inte går förlorad genom strålning och ledning. Strömmar i motståndssvetsprocesser kan nå nivåer så höga som 100 000 A men spänningarna är vanligtvis 0,5 till 10 volt. Elektroder är vanligtvis gjorda av kopparlegeringar. Både liknande och olika material kan sammanfogas genom motståndssvetsning. Det finns flera variationer för denna process: "Resistenspunktsvetsning" innebär att två motsatta runda elektroder kommer i kontakt med ytorna på överlappsfogen på de två plåtarna. Tryck appliceras tills strömmen stängs av. Svetsklumpen är vanligtvis upp till 10 mm i diameter. Motståndspunktsvetsning lämnar lätt missfärgade fördjupningsmärken vid svetspunkter. Punktsvetsning är vår mest populära motståndssvetsteknik. Olika elektrodformer används vid punktsvetsning för att nå svåra områden. Vår punktsvetsutrustning är CNC-styrd och har flera elektroder som kan användas samtidigt. En annan variant av "motståndssömsvetsning" utförs med hjul- eller rullelektroder som producerar kontinuerliga punktsvetsar när strömmen når en tillräckligt hög nivå i växelströmscykeln. Fogar som produceras genom motståndssvetsning är vätske- och gastäta. Svetshastigheter på ca 1,5 m/min är normala för tunnplåt. Man kan applicera intermittenta strömmar så att punktsvetsar produceras med önskade intervall längs sömmen. Vid "motståndsprojektionssvetsning" präglar vi en eller flera utsprång (gropar) på en av arbetsstyckesytorna som ska svetsas. Dessa utsprång kan vara runda eller ovala. Höga lokaliserade temperaturer uppnås vid dessa präglade fläckar som kommer i kontakt med parningsdelen. Elektroder utövar tryck för att komprimera dessa utsprång. Elektroder i motståndsprojektionssvetsning har platta spetsar och är vattenkylda kopparlegeringar. Fördelen med resistansprojektionssvetsning är vår förmåga att svetsa ett antal svetsar i ett slag, alltså den förlängda elektrodens livslängd, förmågan att svetsa plåtar av olika tjocklekar, förmågan att svetsa muttrar och bultar till plåtar. Nackdelen med motståndsprojektionssvetsning är den extra kostnaden för att prägla fördjupningarna. Ännu en teknik, vid "blixtsvetsning" genereras värme från bågen i ändarna av de två arbetsstyckena när de börjar få kontakt. Denna metod kan också alternativt betraktas som bågsvetsning. Temperaturen vid gränssnittet stiger och materialet mjuknar. En axiell kraft appliceras och en svets bildas vid det uppmjukade området. Efter att snabbsvetsningen är klar kan fogen bearbetas för förbättrat utseende. Svetskvaliteten som erhålls genom snabbsvetsning är god. Effektnivåer är 10 till 1500 kW. Snabbsvetsning är lämplig för kant-till-kant sammanfogning av liknande eller olika metaller upp till 75 mm diameter och plåtar mellan 0,2 mm till 25 mm tjocklek. "Stud arc welding" är mycket lik snabbsvetsning. Tappen såsom en bult eller gängad stång tjänar som en elektrod medan den förenas med ett arbetsstycke såsom en platta. För att koncentrera den alstrade värmen, förhindra oxidation och hålla kvar den smälta metallen i svetszonen placeras en keramisk engångsring runt fogen. Slutligen "slagsvetsning", en annan motståndssvetsprocess, använder en kondensator för att tillföra den elektriska energin. Vid slagsvetsning urladdas kraften inom millisekunder mycket snabbt och utvecklar hög lokal värme vid fogen. Vi använder slagsvetsning i stor utsträckning inom elektroniktillverkningsindustrin där uppvärmning av känsliga elektroniska komponenter i närheten av fogen måste undvikas.
En teknik som kallas EXPLOSIONSSVETNING innebär att ett lager av sprängämne detoneras som läggs över ett av arbetsstyckena som ska sammanfogas. Det mycket höga trycket som utövas på arbetsstycket ger ett turbulent och vågigt gränssnitt och mekanisk låsning sker. Förbindningsstyrkorna vid explosiv svetsning är mycket höga. Explosionssvetsning är en bra metod för beklädnad av plåtar med olika metaller. Efter beklädnad kan plattorna rullas till tunnare sektioner. Ibland använder vi explosionsvetsning för att expandera rör så att de tätar tätt mot plattan.
Vår sista metod inom området solid state-fogning är DIFFUSION BONDING eller DIFFUSION WELDING (DFW) där en bra fog uppnås huvudsakligen genom diffusion av atomer över gränsytan. Viss plastisk deformation vid gränssnittet bidrar också till svetsningen. Inblandade temperaturer är runt 0,5 Tm där Tm är smälttemperaturen för metallen. Bindstyrkan vid diffusionssvetsning beror på tryck, temperatur, kontakttid och renheten hos kontaktytor. Ibland använder vi tillsatsmetaller vid gränssnittet. Värme och tryck krävs vid diffusionsbindning och tillförs av elektriskt motstånd eller ugn och dödvikter, press eller annat. Liknande och olika metaller kan sammanfogas med diffusionssvetsning. Processen är relativt långsam på grund av den tid det tar för atomer att migrera. DFW kan automatiseras och används i stor utsträckning vid tillverkning av komplexa delar för flyg-, elektronik- och medicinindustrin. Produkter som tillverkas inkluderar ortopediska implantat, sensorer, strukturella delar för flygindustrin. Diffusionsbindning kan kombineras med SUPERPLASTISK FORMNING för att tillverka komplexa plåtstrukturer. Utvalda platser på ark diffusionsbondas först och sedan expanderas de obundna områdena till en form med hjälp av lufttryck. Flygkonstruktioner med höga styvhet-till-vikt-förhållanden tillverkas med denna kombination av metoder. Den kombinerade processen för diffusionssvetsning/superplastformning minskar antalet delar som krävs genom att eliminera behovet av fästelement, vilket resulterar i lågspänning och mycket exakta delar ekonomiskt och med korta ledtider.
LÖDNING: Lödnings- och lödteknikerna innebär lägre temperaturer än de som krävs för svetsning. Lödningstemperaturerna är dock högre än lödtemperaturerna. Vid hårdlödning placeras en tillsatsmetall mellan ytorna som ska sammanfogas och temperaturen höjs till smälttemperaturen för tillsatsmaterialet över 723 Kelvin men under arbetsstyckenas smälttemperaturer. Den smälta metallen fyller det tätt passande utrymmet mellan arbetsstyckena. Kylning och efterföljande stelning av filarmetallen resulterar i starka fogar. Vid lödsvetsning avsätts tillsatsmetallen vid fogen. Avsevärt mer tillsatsmetall används vid lödsvetsning jämfört med lödning. Oxyacetylenbrännare med oxiderande låga används för att avsätta tillsatsmetallen vid lödsvetsning. På grund av lägre temperaturer vid hårdlödning är problemen i värmepåverkade zoner, såsom skevhet och kvarvarande spänningar, mindre. Ju mindre spelrum är vid lödning, desto högre är fogens skjuvhållfasthet. Maximal draghållfasthet uppnås dock vid ett optimalt gap (ett toppvärde). Under och över detta optimala värde minskar draghållfastheten vid hårdlödning. Typiska spelrum vid hårdlödning kan vara mellan 0,025 och 0,2 mm. Vi använder en mängd olika hårdlödningsmaterial med olika former såsom performs, puder, ringar, tråd, remsa...etc. och kan tillverka dessa utförs speciellt för din design eller produktgeometri. Vi bestämmer också innehållet i hårdlödningsmaterialen enligt dina basmaterial och tillämpningar. Vi använder ofta flussmedel i hårdlödningsoperationer för att avlägsna oönskade oxidlager och förhindra oxidation. För att undvika efterföljande korrosion avlägsnas flussmedel vanligtvis efter sammanfogningsoperationen. AGS-TECH Inc. använder olika hårdlödningsmetoder, inklusive:
- Fackellödning
- Ugnslödning
- Induktionslödning
- Motståndslödning
- Dopplödning
- Infraröd lödning
- Diffusionslödning
- Högenergistråle
Våra vanligaste exempel på lödfogar är gjorda av olika metaller med god hållfasthet såsom hårdmetallborr, skär, optoelektroniska hermetiska paket, tätningar.
LÖDNING: Detta är en av våra mest använda tekniker där lodet (tillsatsmetallen) fyller fogen som vid lödning mellan tättslutande komponenter. Våra lod har smältpunkter under 723 Kelvin. Vi använder både manuell och automatiserad lödning i tillverkningsoperationer. Jämfört med lödning är lödtemperaturen lägre. Lödning är inte särskilt lämplig för applikationer med hög temperatur eller hög hållfasthet. Vi använder såväl blyfria lod som tenn-bly, tenn-zink, bly-silver, kadmium-silver, zink-aluminiumlegeringar förutom andra för lödning. Både icke-korrosiva hartsbaserade såväl som oorganiska syror och salter används som flussmedel vid lödning. Vi använder speciella flussmedel för att löda metaller med låg lödbarhet. I applikationer där vi ska löda keramiska material, glas eller grafit, pläterar vi först delarna med en lämplig metall för ökad lödbarhet. Våra populära lödtekniker är:
-Reflow eller Paste Lödning
-Våglödning
-Ugnslödning
- Facklorlödning
-Induktionslödning
-Järnlödning
- Motståndslödning
-Dopplödning
-Ultraljudslödning
-Infraröd lödning
Ultraljudslödning ger oss en unik fördel där behovet av flussmedel elimineras på grund av ultraljudskavitationseffekt som tar bort oxidfilmer från ytorna som ska fogas. Reflow och Wave lödning är våra industriellt enastående tekniker för högvolymtillverkning inom elektronik och därför värda att förklara mer i detalj. Vid återflödeslödning använder vi halvfasta pastor som innehåller lödmetallpartiklar. Pastan placeras på fogen med hjälp av en screening- eller stencileringsprocess. I kretskort (PCB) använder vi ofta denna teknik. När elektriska komponenter placeras på dessa kuddar från pasta, håller ytspänningen de ytmonterade förpackningarna i linje. Efter att ha placerat komponenterna värmer vi sammansättningen i en ugn så att återflödeslödningen sker. Under denna process avdunstar lösningsmedlen i pastan, flussmedlet i pastan aktiveras, komponenterna förvärms, lodpartiklarna smälts och väter fogen och slutligen kyls PCB-enheten långsamt. Vår andra populära teknik för högvolymproduktion av PCB-skivor, nämligen våglödning förlitar sig på det faktum att smältlod väter metallytor och bildar bra bindningar först när metallen är förvärmd. En stående laminär våg av smält lod genereras först av en pump och de förvärmda och prefluxade PCB:erna transporteras över vågen. Lödet väter endast exponerade metallytor men väter inte IC-polymerpaketen eller de polymerbelagda kretskorten. En varmvattenstråle med hög hastighet blåser överflödigt lod från fogen och förhindrar överbryggning mellan intilliggande ledningar. Vid våglödning av ytmonterade paket binder vi dem först vid kretskortet innan lödning. Återigen används skärmning och stencilering men denna gång för epoxi. Efter att komponenterna har placerats på rätt plats, härdas epoxin, brädorna vänds upp och ner och våglödning sker.