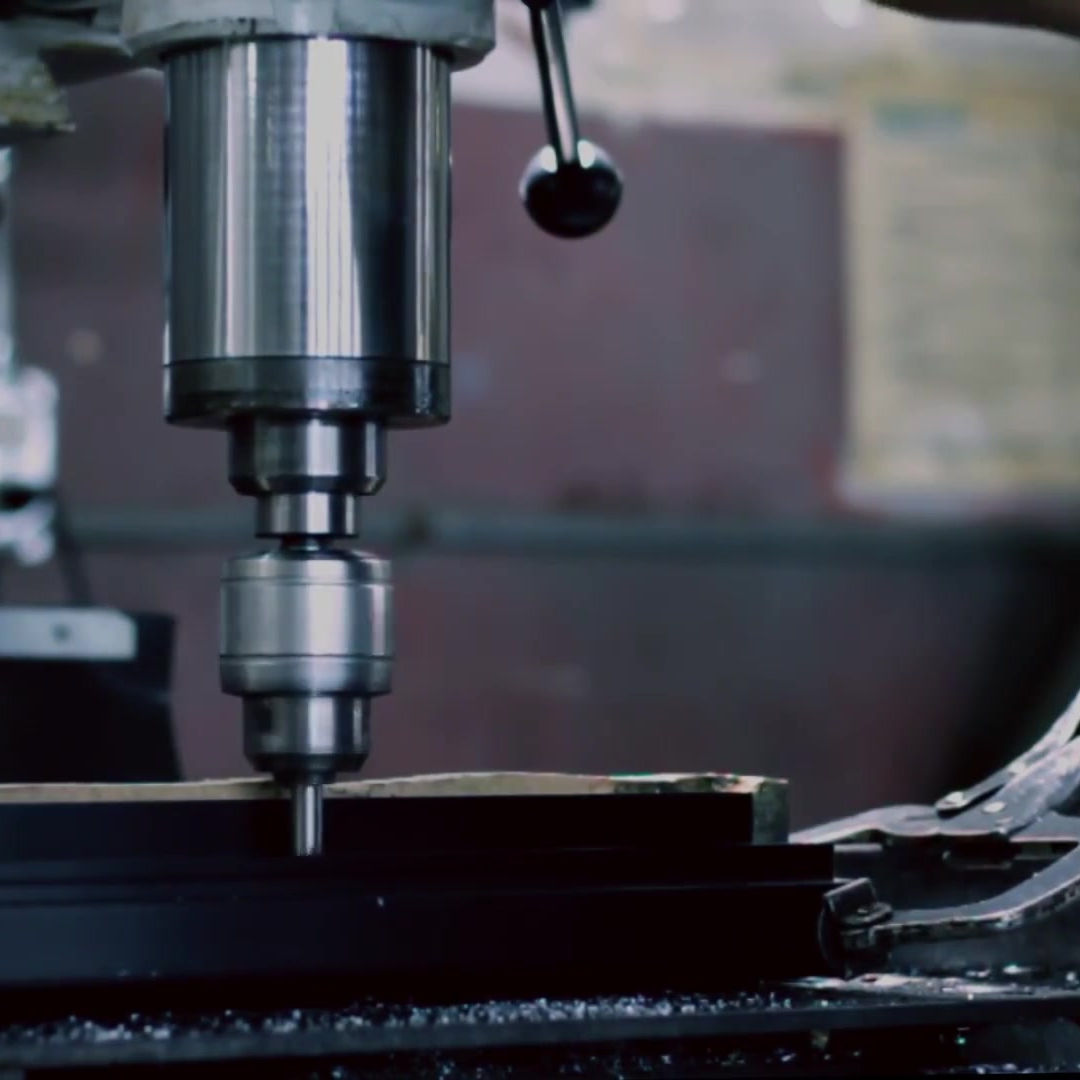
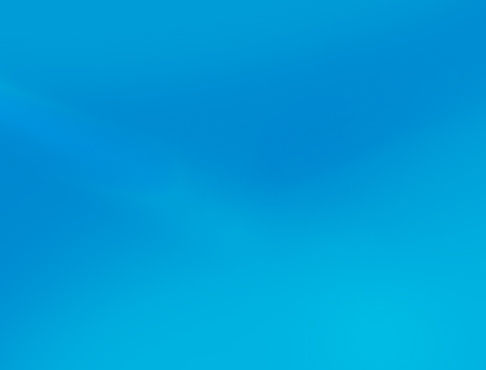
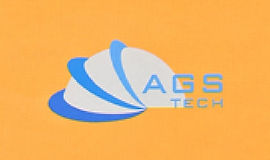
Global Custom Manufacturer, Integrator, Consolidator, Outsourcing Partner för ett brett utbud av produkter och tjänster.
Vi är din enda källa för tillverkning, tillverkning, ingenjörskonst, konsolidering, integration, outsourcing av specialtillverkade och off-shelfprodukter och tjänster.
Välj ditt språk
-
Custom Manufacturing
-
Inhemsk och global kontraktstillverkning
-
Outsourcing av tillverkning
-
Inhemsk och global upphandling
-
Consolidation
-
Engineering Integration
-
Ingenjörstjänster
ELECTRICAL DISCHARGE MACHINING (EDM), also referred to as SPARK-EROSION or ELECTRODISCHARGE MACHINING, SPARK ERODING, DIE SINKING_cc781905-5cde-3194-bb3b -136bad5cf58d_or WIRE EROSION, is a NON-CONVENTIONAL MANUFACTURING process where erosion of metals takes place and desired shape is obtained using electrical discharges in the form av gnistor. Vi erbjuder också några varianter av EDM, nämligen NO-WEAR EDM, WIRE EDM (WEDM), EDM-SLIPNING (EDG), DISTANSKÄNNING EDM, ELEKTRISKA URFLÄSNINGAR, 78-19EDM_cc -5cde-3194-bb3b-136bad5cf58d_and ELECTROCHEMICAL-URLADSLIPNING (ECDG). Våra EDM-system består av formade verktyg/elektrod och arbetsstycket anslutet till DC-strömförsörjning och infört i en elektriskt icke-ledande dielektrisk vätska. Efter 1940 har elektrisk urladdningsbearbetning blivit en av de viktigaste och mest populära produktionsteknikerna inom tillverkningsindustrin.
När avståndet mellan de två elektroderna minskas blir intensiteten av det elektriska fältet i volymen mellan elektroderna större än styrkan hos dielektrikumet i vissa punkter, vilket går sönder och så småningom bildar en brygga för ström att flyta mellan de två elektroderna. En intensiv elektrisk ljusbåge alstras som orsakar betydande uppvärmning för att smälta en del av arbetsstycket och en del av verktygsmaterialet. Som ett resultat avlägsnas material från båda elektroderna. Samtidigt värms den dielektriska vätskan upp snabbt, vilket resulterar i avdunstning av vätskan i båggapet. När strömflödet stannar eller det stoppas avlägsnas värme från gasbubblan av den omgivande dielektriska vätskan och bubblan kaviterar (kollapsar). Stötvågen som skapas av bubblans kollaps och flödet av dielektrisk vätska spolar bort skräp från arbetsstyckets yta och drar in eventuellt smält arbetsstyckesmaterial i den dielektriska vätskan. Upprepningshastigheten för dessa urladdningar är mellan 50 till 500 kHz, spänningar mellan 50 till 380 V och strömmar mellan 0,1 och 500 Ampere. Nytt flytande dielektrikum såsom mineraloljor, fotogen eller destillerat och avjoniserat vatten transporteras vanligtvis in i mellanelektrodvolymen och transporterar bort de fasta partiklarna (i form av skräp) och dielektrikets isolerande egenskaper återställs. Efter ett strömflöde återställs potentialskillnaden mellan de två elektroderna till vad den var före haveriet, så ett nytt vätskedielektriskt genombrott kan inträffa. Våra moderna elektriska urladdningsmaskiner (EDM) erbjuder numeriskt styrda rörelser och är utrustade med pumpar och filtreringssystem för de dielektriska vätskorna.
Elektrisk urladdningsbearbetning (EDM) är en bearbetningsmetod som främst används för hårdmetaller eller sådana som skulle vara mycket svåra att bearbeta med konventionella tekniker. EDM fungerar vanligtvis med alla material som är elektriska ledare, även om metoder för att bearbeta isolerande keramik med EDM också har föreslagits. Smältpunkten och latent smältvärme är egenskaper som bestämmer mängden metall som avlägsnas per utsläpp. Ju högre dessa värden är, desto långsammare är materialavlägsningshastigheten. Eftersom den elektriska urladdningsbearbetningsprocessen inte involverar någon mekanisk energi, påverkar hårdheten, styrkan och segheten hos arbetsstycket inte borttagningshastigheten. Urladdningsfrekvens eller energi per urladdning, spänningen och strömmen varieras för att kontrollera materialavlägsningshastigheten. Materialavlägsningshastigheten och ytråheten ökar med ökande strömtäthet och minskande gnistfrekvens. Vi kan skära intrikata konturer eller håligheter i förhärdat stål med hjälp av EDM utan behov av värmebehandling för att mjuka upp och återhärda dem. Vi kan använda denna metod med alla metaller eller metallegeringar som titan, hastelloy, kovar och inconel. Tillämpningar av EDM-processen inkluderar formning av polykristallina diamantverktyg. EDM anses vara en icke-traditionell eller icke-konventionell bearbetningsmetod tillsammans med processer som elektrokemisk bearbetning (ECM), vattenstråleskärning (WJ, AWJ), laserskärning. Å andra sidan inkluderar de konventionella bearbetningsmetoderna svarvning, fräsning, slipning, borrning och andra processer vars materialavlägsningsmekanism i huvudsak är baserad på mekaniska krafter. Elektroder för elektrisk urladdningsbearbetning (EDM) är gjorda av grafit, mässing, koppar och koppar-volframlegering. Elektroddiametrar ner till 0,1 mm är möjliga. Eftersom verktygsslitage är ett oönskat fenomen som negativt påverkar dimensionsnoggrannheten i EDM, drar vi fördel av en process som kallas NO-WEAR EDM, genom att vända polariteten och använda kopparverktyg för att minimera verktygsslitage.
Idealiskt sett kan elektrisk urladdningsbearbetning (EDM) betraktas som en serie av sammanbrott och återställande av den dielektriska vätskan mellan elektroderna. I verkligheten är dock borttagningen av skräpet från interelektrodområdet nästan alltid partiellt. Detta gör att de elektriska egenskaperna hos dielektrikumet i området mellan elektroderna skiljer sig från deras nominella värden och varierar med tiden. Avståndet mellan elektroderna, (gnistgap), justeras av kontrollalgoritmerna för den specifika maskinen som används. Gnistgapet i EDM kan tyvärr ibland kortslutas av skräpet. Elektrodens styrsystem kan misslyckas med att reagera tillräckligt snabbt för att förhindra att de två elektroderna (verktyg och arbetsstycke) kortsluts. Denna oönskade kortslutning bidrar till materialborttagning på ett annat sätt än det ideala fallet. Vi lägger stor vikt vid spolningsåtgärder för att återställa de isolerande egenskaperna hos dielektrikumet så att strömmen alltid sker i spetsen av interelektrodområdet, och därigenom minimera risken för oönskad formförändring (skada) av verktygselektroden och arbetsstycke. För att erhålla en specifik geometri, styrs EDM-verktyget längs den önskade banan mycket nära arbetsstycket utan att vidröra det. Vi är ytterst uppmärksamma på prestandan för rörelsekontroll vid användning. På så sätt sker ett stort antal strömurladdningar/gnistor, och var och en bidrar till att material avlägsnas från både verktyg och arbetsstycke, där små kratrar bildas. Kratrarnas storlek är en funktion av de tekniska parametrarna som ställts in för det specifika jobbet och dimensionerna kan variera från nanoskala (som i fallet med mikro-EDM-operationer) till några hundra mikrometer vid grovbearbetning. Dessa små kratrar på verktyget orsakar gradvis erosion av elektroden som kallas "verktygsslitage". För att motverka slitagets skadliga inverkan på arbetsstyckets geometri byter vi kontinuerligt ut verktygselektroden under en bearbetning. Ibland uppnår vi detta genom att använda en kontinuerligt ersatt tråd som elektrod (denna EDM-process kallas också WIRE EDM ). Ibland använder vi verktygselektroden på ett sådant sätt att endast en liten del av den faktiskt är engagerad i bearbetningsprocessen och denna del byts ut regelbundet. Detta är till exempel fallet när man använder en roterande skiva som verktygselektrod. Denna process kallas EDM GRINDING. Ytterligare en annan teknik vi använder består av att använda en uppsättning elektroder med olika storlekar och former under samma EDM-operation för att kompensera för slitage. Vi kallar denna teknik för flera elektroder, och används oftast när verktygselektroden replikerar negativt den önskade formen och förs fram mot ämnet längs en enda riktning, vanligtvis den vertikala riktningen (dvs. z-axeln). Detta påminner om verktygets sänkning i den dielektriska vätskan som arbetsstycket är nedsänkt i, och därför kallas det DIE-SINKING EDM_cc781905-5cde-3194-6bad_c5cc-f3sdc-15cd-5cd-15cd-5cd-5cd-5cd-5cde-781905-5cde-3194-6bad_5b-5cc-f3e-15cd 3194-bb3b-136bad5cf58d_CONVENTIONAL EDM or RAM EDM). Maskinerna för denna operation heter SINKER EDM. Elektroderna för denna typ av EDM har komplexa former. Om den slutliga geometrin erhålls med hjälp av en vanligen enkelformad elektrod som flyttas längs flera riktningar och även är föremål för rotationer, kallar vi it EDM FÄSNING. Mängden slitage är strikt beroende av de tekniska parametrarna som används i operationen (polaritet, maximal ström, öppen kretsspänning). Till exempel, in micro-EDM, även känd som m-EDM, är dessa parametrar vanligtvis inställda på värden som genererar hårt slitage. Därför är slitage ett stort problem inom det området som vi minimerar med vårt samlade kunnande. Till exempel för att minimera slitage på grafitelektroder, vänder en digital generator, styrbar inom millisekunder, polariteten när elektroerosion äger rum. Detta resulterar i en effekt som liknar elektroplätering som kontinuerligt avsätter den eroderade grafiten tillbaka på elektroden. I en annan metod, en så kallad ''Zero Wear''-krets, minimerar vi hur ofta urladdningen startar och stannar, och håller den på så länge som möjligt. Materialavlägsningshastigheten vid elektrisk urladdningsbearbetning kan uppskattas från:
MRR = 4 x 10 exp(4) x I x Tw exp (-1,23)
Här är MRR i mm3/min, I är ström i ampere, Tw är arbetsstyckets smältpunkt i K-273,15K. Exp står för exponent.
Å andra sidan kan slitagehastigheten Wt för elektroden erhållas från:
Wt = ( 1,1 x 10exp(11) ) x I x Ttexp(-2,38)
Här är Wt i mm3/min och Tt är smältpunkten för elektrodmaterialet i K-273.15K
Slutligen kan slitageförhållandet mellan arbetsstycket och elektroden R erhållas från:
R = 2,25 x Trexp(-2,38)
Här är Tr förhållandet mellan arbetsstyckets smältpunkter och elektrod.
SINKER EDM :
Sänke EDM, även kallad CAVITY TYPE EDM or_cc781905-5cde-3d-5cde och EDM or_cc781905-5cde-5cde-3d-3d-3d3, 1000000000000000000000000000000000000000000000000000000000002 Elektroden och arbetsstycket är anslutna till en strömkälla. Strömförsörjningen genererar en elektrisk potential mellan de två. När elektroden närmar sig arbetsstycket sker dielektrisk nedbrytning i vätskan, vilket bildar en plasmakanal och en liten gnista hoppar. Gnistorna slår vanligtvis en i taget eftersom det är högst osannolikt att olika platser i elektrodutrymmet har identiska lokala elektriska egenskaper som skulle göra det möjligt för en gnista att uppstå på alla sådana platser samtidigt. Hundratusentals av dessa gnistor uppstår vid slumpmässiga punkter mellan elektroden och arbetsstycket per sekund. När basmetallen eroderar och gnistgapet därefter ökar, sänks elektroden automatiskt av vår CNC-maskin så att processen kan fortsätta oavbrutet. Vår utrustning har kontrollcykler som kallas ''på tid'' och ''off time''. Tidsinställningen för påslag bestämmer gnistans längd eller varaktighet. En längre tid ger ett djupare hålrum för den gnistan och alla efterföljande gnistor för den cykeln, vilket skapar en grövre finish på arbetsstycket och vice versa. Avstängningstiden är den tidsperiod som en gnista ersätts av en annan. En längre avstängningstid tillåter den dielektriska vätskan att spola genom ett munstycke för att rensa ut det eroderade skräpet och därigenom undvika kortslutning. Dessa inställningar justeras i mikrosekunder.
WIRE EDM :
In WIRE ELECTRICAL DISCHARGE MACHINING (WEDM), also called WIRE-CUT EDM or WIRE CUTTING, we feed a tunn enkelsträngad metalltråd av mässing genom arbetsstycket, som är nedsänkt i en tank med dielektrisk vätska. Wire EDM är en viktig variant av EDM. Vi använder ibland trådskuren EDM för att skära plattor så tjocka som 300 mm och för att tillverka stansar, verktyg och stansar av hårdmetaller som är svåra att bearbeta med andra tillverkningsmetoder. I denna process, som liknar konturskärning med en bandsåg, hålls tråden, som ständigt matas från en spole, mellan övre och nedre diamantstyrningar. De CNC-styrda guiderna rör sig i x–y-planet och den övre guiden kan också röra sig oberoende i z–u–v-axeln, vilket ger upphov till möjligheten att skära avsmalnande och övergående former (som cirkel på botten och kvadrat vid toppen). Den övre styrningen kan styra axelrörelser i x–y–u–v–i–j–k–l–. Detta gör att WEDM kan skära mycket intrikata och ömtåliga former. Den genomsnittliga skärskär på vår utrustning som uppnår bästa ekonomiska kostnad och bearbetningstid är 0,335 mm med Ø 0,25 mässings-, koppar- eller volframtråd. De övre och nedre diamantstyrningarna på vår CNC-utrustning är dock exakta till cirka 0,004 mm och kan ha en skärbana eller skär så liten som 0,021 mm med en Ø 0,02 mm tråd. Så riktigt smala snitt är möjliga. Skärbredden är större än trådens bredd eftersom gnistor uppstår från sidorna av tråden till arbetsstycket, vilket orsakar erosion. Denna ''överskärning'' är nödvändig, för många applikationer är den förutsägbar och kan därför kompenseras för (i mikro-EDM är detta inte ofta fallet). Trådspolarna är långa — en 8 kg trådrulle på 0,25 mm tråd är drygt 19 kilometer lång. Tråddiametern kan vara så liten som 20 mikrometer och geometriprecisionen är i närheten av +/- 1 mikrometer. Vi använder vanligtvis tråden bara en gång och återvinner den eftersom den är relativt billig. Den färdas med en konstant hastighet av 0,15 till 9m/min och en konstant skärning (slits) bibehålls under ett snitt. I den trådklippta EDM-processen använder vi vatten som den dielektriska vätskan, och kontrollerar dess resistivitet och andra elektriska egenskaper med filter och avjoniseringsenheter. Vattnet spolar bort det avskurna skräpet från skärzonen. Spolning är en viktig faktor för att bestämma den maximala matningshastigheten för en given materialtjocklek och därför håller vi den konsekvent. Skärhastighet i tråd-EDM anges i termer av skärningsyta per tidsenhet, såsom 18 000 mm2/h för 50 mm tjockt D2 verktygsstål. Den linjära skärhastigheten för detta fall skulle vara 18 000/50 = 360 mm/h. Materialavlägsningshastigheten i tråd-EDM är:
MRR = Vf xhxb
Här är MRR i mm3/min, Vf är trådens matningshastighet till arbetsstycket i mm/min, h är tjocklek eller höjd i mm, och b är skäret, vilket är:
b = dw + 2s
Här är dw tråddiameter och s är gapet mellan tråd och arbetsstycke i mm.
Tillsammans med snävare toleranser har våra moderna fleraxliga EDM-trådskärningsmaskiner lagt till funktioner som multihuvuden för att skära två delar samtidigt, kontroller för att förhindra trådbrott, automatiska självgängande funktioner i händelse av trådbrott och programmerad bearbetningsstrategier för att optimera driften, raka och vinklade skärmöjligheter.
Wire-EDM ger oss låga restspänningar, eftersom det inte kräver höga skärkrafter för borttagning av material. När energin/effekten per puls är relativt låg (som vid efterbearbetning) förväntas liten förändring i de mekaniska egenskaperna hos ett material på grund av låga restspänningar.
ELEKTRISK URFLÖDNING (EDG) : Slipskivorna innehåller inga slipmedel, de är gjorda av grafit eller mässing. Upprepade gnistor mellan det roterande hjulet och arbetsstycket tar bort material från arbetsstyckets ytor. Materialavlägsningshastigheten är:
MRR = K x I
Här är MRR i mm3/min, I är ström i Ampere och K är arbetsstyckets materialfaktor i mm3/A-min. Vi använder ofta elektrisk urladdningsslipning för att såga smala slitsar på komponenter. Vi kombinerar ibland EDG (Electrical-Discharge Grinding) process med EKG (Electrochemical Grinding) process där material avlägsnas genom kemisk verkan, de elektriska urladdningarna från grafithjulet bryter upp oxidfilmen och tvättas bort av elektrolyten. Processen kallas ELECTROCHEMICAL-DISCHARGE GRINDING (ECDG). Även om ECGD-processen förbrukar relativt sett mer ström är det en snabbare process än EDG. Vi slipar mestadels hårdmetallverktyg med denna teknik.
Tillämpningar av elektrisk urladdningsbearbetning:
Prototyptillverkning:
Vi använder EDM-processen vid formtillverkning, verktygs- och formtillverkning, såväl som för tillverkning av prototyper och produktionsdelar, speciellt för flyg-, bil- och elektronikindustrin där produktionskvantiteterna är relativt små. I Sinker EDM bearbetas en elektrod av grafit, kopparvolfram eller ren koppar till önskad (negativ) form och matas in i arbetsstycket på änden av en vertikal kolv.
Tillverkning av myntformar:
För att skapa formar för att producera smycken och märken genom myntprocessen (stämpling) kan den positiva mästaren vara gjord av sterling silver, eftersom (med lämpliga maskininställningar) mästaren är avsevärt eroderad och används endast en gång. Den resulterande negativa formen härdas sedan och används i en hammare för att producera stansade plattor från utskurna arkämnen av brons, silver eller lågtät guldlegering. För märken kan dessa plattor formas ytterligare till en krökt yta av en annan form. Denna typ av EDM utförs vanligtvis nedsänkt i ett oljebaserat dielektrikum. Det färdiga föremålet kan förfinas ytterligare genom hård (glas) eller mjuk (färg) emaljering och/eller galvaniserad med rent guld eller nickel. Mjukare material som silver kan vara handgraverade som en förfining.
Borrning av små hål:
På våra trådskurna EDM-maskiner använder vi små hålsborrning EDM för att göra ett genomgående hål i ett arbetsstycke genom vilket vi trär tråden för den trådklippta EDM-operationen. Separata EDM-huvuden speciellt för småhålsborrning är monterade på våra trådkapsmaskiner som gör att stora härdade plåtar kan få färdiga delar eroderade från dem efter behov och utan förborrning. Vi använder även EDM med små hål för att borra rader av hål i kanterna på turbinblad som används i jetmotorer. Gasflödet genom dessa små hål gör att motorerna kan använda högre temperaturer än vad som annars är möjligt. De högtemperatur-, mycket hårda, enkristalllegeringar som dessa blad är gjorda av gör konventionell bearbetning av dessa hål med högt bildförhållande extremt svårt och till och med omöjligt. Andra användningsområden för EDM med små hål är att skapa mikroskopiska öppningar för bränslesystemkomponenter. Förutom de integrerade EDM-huvudena använder vi fristående EDM-maskiner för småhålsborrning med x–y-axlar för att bearbeta blinda eller genomgående hål. EDM borrar borrhål med en lång elektrod av mässing eller kopparrör som roterar i en chuck med ett konstant flöde av destillerat eller avjoniserat vatten som strömmar genom elektroden som spolmedel och dielektrikum. Vissa småhålsborrande EDM:er kan borra genom 100 mm mjukt eller till och med härdat stål på mindre än 10 sekunder. Hål mellan 0,3 mm och 6,1 mm kan uppnås vid denna borrning.
Metallsönderdelningsbearbetning:
Vi har även speciella EDM-maskiner för det specifika syftet att ta bort trasiga verktyg (borr eller kranar) från arbetsstycken. Denna process kallas ''metallsönderdelningsbearbetning''.
Fördelar och nackdelar Elektrisk urladdningsbearbetning:
Fördelarna med EDM inkluderar bearbetning av:
- Komplexa former som annars skulle vara svåra att tillverka med konventionella skärverktyg
- Extremt hårt material med mycket nära toleranser
- Mycket små arbetsstycken där konventionella skärverktyg kan skada delen på grund av överdrivet skärverktygstryck.
- Det finns ingen direkt kontakt mellan verktyg och arbetsstycke. Därför kan ömtåliga sektioner och svaga material bearbetas utan förvrängning.
- En bra ytfinish kan erhållas.
– Mycket fina hål kan enkelt borras.
Nackdelarna med EDM inkluderar:
- Den långsamma hastigheten för borttagning av material.
- Den extra tid och kostnad som används för att skapa elektroder för ram/sänke EDM.
- Att återge skarpa hörn på arbetsstycket är svårt på grund av elektrodslitage.
– Strömförbrukningen är hög.
- ''Overcut'' bildas.
- Överdrivet verktygsslitage uppstår vid bearbetning.
- Elektriskt icke-ledande material kan endast bearbetas med specifik uppställning av processen.