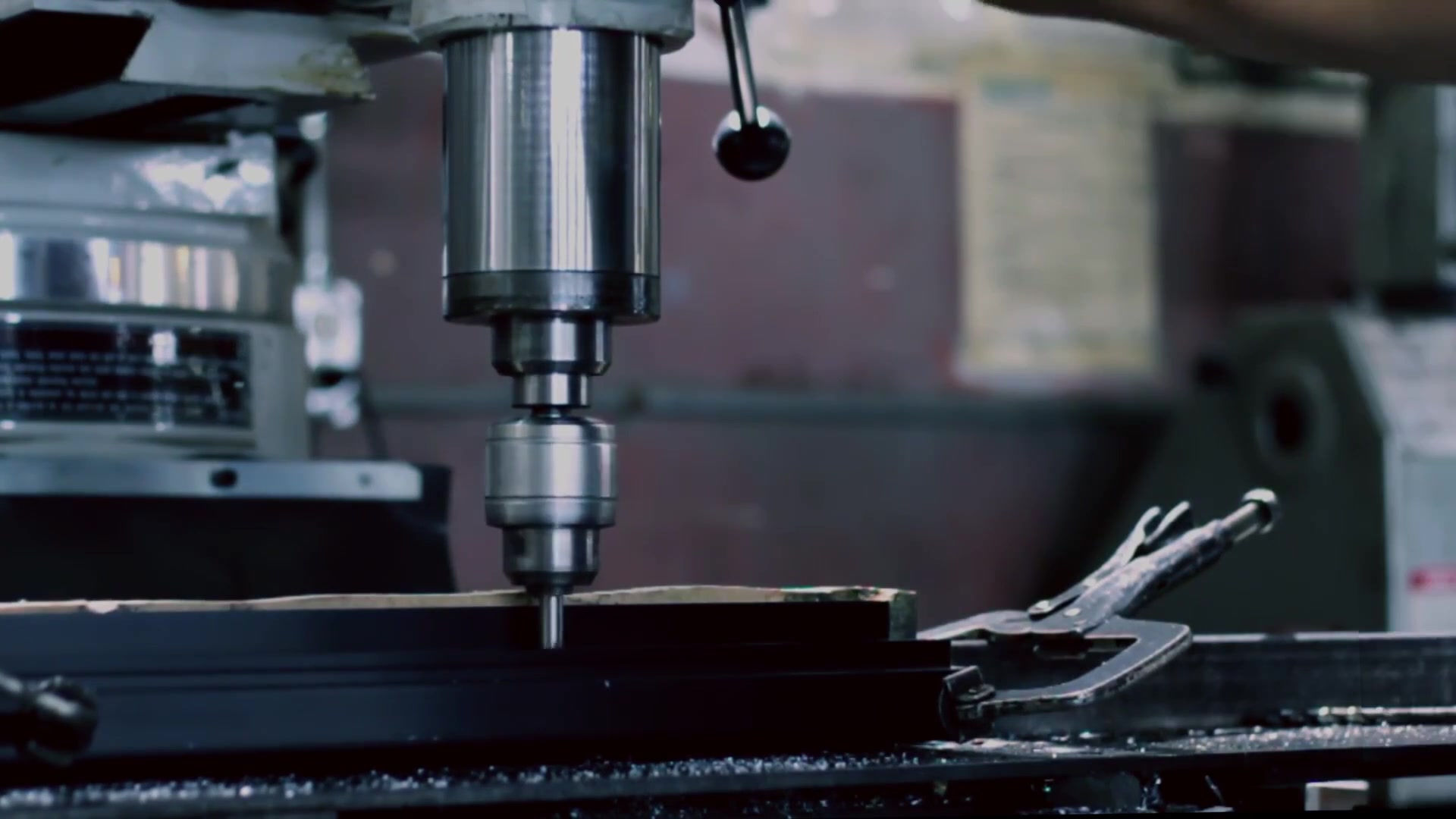
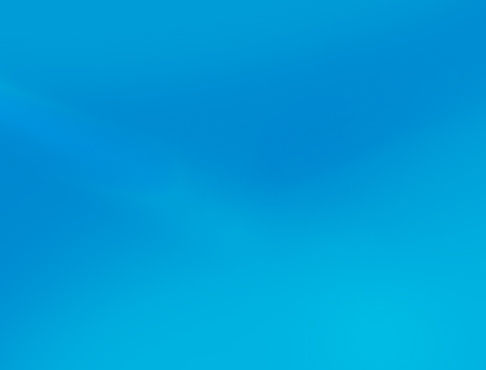
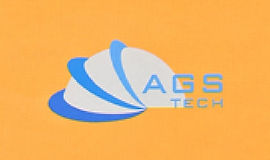
Global Custom Manufacturer, Integrator, Consolidator, Outsourcing Partner för ett brett utbud av produkter och tjänster.
Vi är din enda källa för tillverkning, tillverkning, ingenjörskonst, konsolidering, integration, outsourcing av specialtillverkade och off-shelfprodukter och tjänster.
Välj ditt språk
-
Custom Manufacturing
-
Inhemsk och global kontraktstillverkning
-
Outsourcing av tillverkning
-
Inhemsk och global upphandling
-
Consolidation
-
Engineering Integration
-
Ingenjörstjänster
Search Results
164 resultat hittades med en tom sökning
- Rapid Prototyping, Desktop Manufacturing, Additive Manufacturing, FDM
Rapid Prototyping, Desktop Manufacturing, Additive Manufacturing, Stereolithography, Polyjet, Fused Deposition Modeling, Selective Laser Sintering, FDM, SLS Additiv och snabb tillverkning De senaste åren har vi sett en ökad efterfrågan på RAPID MANUFACTURING eller RAPID PROTOTYPING. Denna process kan också kallas DESKTOP MANUFACTURING eller FRI-FORM FABRICATION. I grund och botten görs en solid fysisk modell av en del direkt från en tredimensionell CAD-ritning. Vi använder termen ADDITIVE MANUFACTURING för dessa olika tekniker där vi bygger delar i lager. Med hjälp av integrerad datordriven hårdvara och mjukvara utför vi additiv tillverkning. Våra snabba prototyp- och tillverkningstekniker är STEREOLITHOGRAFI, POLYJET, MODELLERING AV FUSED-DEPOSITION, SELECTIVE LASER SINTERING, ELEKTRONSMÄLTNING, TREDIMENSIONELL UTSKRIFT, DIREKT TILLVERKNING, SNABB VERKTYG. Vi rekommenderar att du klickar här för attLADDA NED våra schematiska illustrationer av additiv tillverkning och snabba tillverkningsprocesser av AGS-TECH Inc. Detta hjälper dig att bättre förstå informationen vi ger dig nedan. Rapid prototyping ger oss: 1.) Den konceptuella produktdesignen ses från olika vinklar på en monitor med hjälp av ett 3D/CAD-system. 2.) Prototyper från icke-metalliska och metalliska material tillverkas och studeras ur funktionella, tekniska och estetiska aspekter. 3.) Låg kostnad prototyper på mycket kort tid uppnås. Additiv tillverkning kan liknas vid konstruktionen av en brödlimpa genom att stapla och binda enskilda skivor ovanpå varandra. Med andra ord, produkten tillverkas skiva för skiva, eller lager för lager deponeras på varandra. De flesta delar kan tillverkas inom några timmar. Tekniken är bra om delar behövs mycket snabbt eller om det behövs små mängder och att göra en form och verktyg är för dyrt och tar tid. Men kostnaden för en del är dyr på grund av de dyra råvarorna. • STEREOLITHOGRAFI: Denna teknik även förkortad som STL, är baserad på härdning och härdning av en flytande fotopolymer till en specifik form genom att fokusera en laserstråle på den. Lasern polymeriserar fotopolymeren och härdar den. Genom att skanna UV-laserstrålen enligt den programmerade formen längs ytan av fotopolymerblandningen produceras delen nedifrån och upp i individuella skivor kaskaderade ovanpå varandra. Scanningen av laserpunkten upprepas många gånger för att uppnå de geometrier som programmerats in i systemet. Efter att delen är helt tillverkad tas den bort från plattformen, läts av och rengörs med ultraljud och med alkoholbad. Därefter utsätts den för UV-strålning i några timmar för att säkerställa att polymeren är helt härdad och härdad. För att sammanfatta processen styrs och förflyttas en plattform som doppas i en fotopolymerblandning och en UV-laserstråle genom ett servokontrollsystem enligt formen på den önskade delen och delen erhålls genom fotohärdning av polymeren lager för lager. Naturligtvis bestäms de maximala måtten för den producerade delen av stereolitografiutrustningen. • POLYJET: I likhet med bläckstråleutskrift har vi i polyjet åtta skrivhuvuden som lägger fotopolymer på byggfacket. Ultraviolett ljus placerat bredvid strålarna härdar omedelbart och härdar varje lager. Två material används i polyjet. Det första materialet är för tillverkning av själva modellen. Det andra materialet, ett gelliknande harts, används som stöd. Båda dessa material avsätts lager för lager och härdas samtidigt. Efter färdigställandet av modellen avlägsnas stödmaterialet med en vattenlösning. Hartser som används liknar stereolitografi (STL). Polyjet har följande fördelar jämfört med stereolitografi: 1.) Inget behov av rengöring av delar. 2.) Inget behov av efterbehandlingshärdning 3.) Mindre lagertjocklekar är möjliga och därmed får vi bättre upplösning och kan tillverka finare detaljer. • FUSED DEPOSITION MODELLING: Även förkortat som FDM, i denna metod rör sig ett robotstyrt extruderhuvud i två principiella riktningar över ett bord. Kabeln sänks och höjs vid behov. Från öppningen av en uppvärmd form på huvudet extruderas en termoplastfilament och ett första lager avsätts på en skumfundament. Detta åstadkommes av extruderhuvudet som följer en förutbestämd bana. Efter det första lagret sänks bordet och efterföljande lager läggs ovanpå varandra. Ibland vid tillverkning av en komplicerad del behövs stödstrukturer så att deponeringen kan fortsätta i vissa riktningar. I dessa fall extruderas ett stödmaterial med ett mindre tätt avstånd av filament på ett lager så att det är svagare än modellmaterialet. Dessa stödstrukturer kan senare lösas upp eller brytas av efter färdigställandet av delen. Extruderformens dimensioner bestämmer tjockleken på de extruderade skikten. FDM-processen producerar detaljer med trappstegsytor på sneda yttre plan. Om denna grovhet är oacceptabel kan kemisk ångpolering eller ett uppvärmt verktyg användas för att jämna ut dessa. Även ett polervax finns tillgängligt som beläggningsmaterial för att eliminera dessa steg och uppnå rimliga geometriska toleranser. • SELEKTIV LASERSINTERING: Även betecknad som SLS, är processen baserad på sintring av en polymer, keramik eller metallpulver selektivt till ett föremål. Bearbetningskammarens botten har två cylindrar: en delbyggd cylinder och en pulvermatningscylinder. Den förra sänks inkrementellt till där den sintrade delen formas och den senare höjs stegvis för att tillföra pulver till den delbyggda cylindern genom en rullmekanism. Först avsätts ett tunt lager av pulver i den delbyggda cylindern, sedan fokuseras en laserstråle på det lagret, spårar och smälter/sintrar ett visst tvärsnitt, som sedan åter stelnar till ett fast ämne. Pulvret är områden som inte träffas av laserstrålen förblir lösa men stöder fortfarande den fasta delen. Sedan avsätts ytterligare ett lager pulver och processen upprepas många gånger för att erhålla delen. I slutet skakas de lösa pulverpartiklarna av. Alla dessa utförs av en processkontrolldator med hjälp av instruktioner genererade av 3D CAD-programmet för den del som tillverkas. Olika material såsom polymerer (såsom ABS, PVC, polyester), vax, metaller och keramik med lämpliga polymerbindemedel kan avsättas. • ELECTRON-BEAM MELTING : Liknar selektiv lasersintring, men använder elektronstråle för att smälta titan- eller koboltkrompulver för att göra prototyper i vakuum. Vissa utvecklingar har gjorts för att utföra denna process på rostfria stål, aluminium och kopparlegeringar. Om utmattningshållfastheten hos de producerade delarna behöver ökas använder vi varm isostatisk pressning efter detaljtillverkningen som en sekundär process. • TREDIMENSIONELL UTSKRIVNING: Även betecknad med 3DP, i denna teknik avsätter ett skrivhuvud ett oorganiskt bindemedel på ett lager av antingen icke-metalliskt eller metalliskt pulver. En kolv som bär pulverbädden sänks stegvis och vid varje steg avsätts bindemedlet lager för lager och smälts samman av bindemedlet. Pulvermaterial som används är polymerblandningar och fibrer, gjutsand, metaller. Genom att använda olika pärmar samtidigt och olika färg pärmar kan vi få olika färger. Processen liknar bläckstråleutskrift men istället för att få ett färgat ark får vi ett färgat tredimensionellt objekt. De framställda delarna kan vara porösa och kan därför kräva sintring och metallinfiltration för att öka dess densitet och styrka. Sintring kommer att bränna bort bindemedlet och smälta samman metallpulvret. Metaller såsom rostfritt stål, aluminium, titan kan användas för att tillverka delarna och som infiltrationsmaterial använder vi vanligtvis koppar och brons. Det fina med denna teknik är att även komplicerade och rörliga enheter kan tillverkas mycket snabbt. Till exempel kan en växelenhet, en skiftnyckel som verktyg tillverkas och kommer att ha rörliga och vridbara delar redo att användas. Olika komponenter i aggregatet kan tillverkas med olika färger och allt i ett skott. Ladda ner vår broschyr på:Grundläggande om 3D-utskrift av metall • DIREKT TILLVERKNING och SNABB VERKTYG: Förutom designutvärdering, felsökning använder vi snabba prototyper för direkt tillverkning av produkter eller direkt applicering i produkter. Med andra ord kan rapid prototyping inkorporeras i konventionella processer för att göra dem bättre och mer konkurrenskraftiga. Till exempel kan rapid prototyping producera mönster och formar. Mönster av en smältande och brinnande polymer skapad av snabba prototypoperationer kan sättas ihop för investeringsgjutning och investeras. Ett annat exempel att nämna är att använda 3DP för att producera keramiskt gjutskal och använda det för gjutningsoperationer. Även formsprutningsformar och forminsatser kan tillverkas genom snabb prototypframställning och man kan spara många veckor eller månader av ledtid för formtillverkning. Genom att endast analysera en CAD-fil av den önskade delen kan vi producera verktygsgeometrin med hjälp av mjukvara. Här är några av våra populära snabba verktygsmetoder: RTV (Room-Temperature Vulcanizing) GJUTNING / URETAN GJUTNING: Använda snabb prototyping kan användas för att göra mönstret för den önskade delen. Därefter beläggs detta mönster med ett avskiljningsmedel och flytande RTV-gummi hälls över mönstret för att producera formhalvorna. Därefter används dessa formhalvor för att formspruta flytande uretaner. Formens livslängd är kort, bara som 0 eller 30 cykler men tillräckligt för produktion av små partier. ACES (Acetal Clear Epoxy Solid) SPRÖTJNING: Genom att använda snabba prototyptekniker som stereolitografi tillverkar vi formsprutor. Dessa formar är skal med en öppen ände för att kunna fyllas med material som epoxi, aluminiumfylld epoxi eller metaller. Återigen är formens livslängd begränsad till tiotals eller maximalt hundratals delar. SPRAYET METALLVERKTYG: Vi använder snabba prototyper och gör ett mönster. Vi sprayar en zink-aluminiumlegering på mönsterytan och belägger den. Mönstret med metallbeläggningen placeras sedan i en kolv och ingjuts med en epoxi- eller aluminiumfylld epoxi. Slutligen tas den bort och genom att tillverka två sådana formhalvor får vi en komplett form för formsprutning. Dessa formar har längre livslängd, i vissa fall beroende på material och temperaturer kan de producera delar i tusentals. KEELTOOL PROCESS: Denna teknik kan producera formar med 100 000 till 10 miljoner cykellivslängder. Med hjälp av rapid prototyping producerar vi en RTV-form. Formen fylls sedan med en blandning bestående av A6 verktygsstålspulver, volframkarbid, polymerbindemedel och låt härda. Denna form värms sedan upp för att få polymeren att bränna av och metallpulvret att smälta. Nästa steg är kopparinfiltration för att producera den slutliga formen. Vid behov kan sekundära operationer såsom bearbetning och polering utföras på formen för bättre dimensionsnoggrannhet. _cc781905-5cde-3194-bb3b-136dbad_5cf58 CLICK Product Finder-Locator Service FÖREGÅENDE SIDA
- Machine Elements Manufacturing, Gears, Gear Drives, Bearings, Keys, Splines
Machine Elements Manufacturing, Gears, Gear Drives, Bearings, Keys, Splines, Pins, Shafts, Seals, Fasteners, Clutch, Cams, Followers, Belts, Couplings, Shafts Tillverkning av maskinelement Läs mer Remmar & kedjor & kabeldrivning Läs mer Kugghjul och växeldrivenhet Läs mer Tillverkning av kopplingar och lager Läs mer Tillverkning av nycklar och splines och stift Läs mer Cams & Followers & Linkages & Ratchet Wheels Manufacturing Läs mer Tillverkning av axlar Läs mer Tillverkning av mekaniska tätningar Läs mer Kopplings- och bromsenhet Läs mer Tillverkning av fästelement Läs mer Enkel maskinmontering MACHINE ELEMENTS är elementära komponenter i en maskin. Dessa element består av tre grundläggande typer: 1.) Strukturella komponenter inklusive ramdelar, lager, axlar, splines, fästelement, tätningar och smörjmedel. 2.) Mekanismer som styr rörelser på olika sätt såsom växellåg, rem- eller kedjedrift, länkage, kam- och följarsystem, bromsar och kopplingar. 3.) Styrkomponenter som knappar, omkopplare, indikatorer, sensorer, ställdon och datorkontroller. De flesta av maskinelementen vi erbjuder dig är standardiserade till vanliga storlekar, men specialtillverkade maskinelement finns också tillgängliga för dina specialiserade applikationer. Anpassning av maskinelement kan ske på befintliga mönster som finns i våra nedladdningsbara kataloger eller på helt nya mönster. Prototypframställning och tillverkning av maskinelement kan föras vidare när en design har godkänts av båda parter. Om nya maskinelement behöver designas och tillverkas, mailar våra kunder oss antingen sina egna ritningar och vi granskar dem för godkännande, eller så ber de oss att designa maskinelement för deras applikation. I det senare fallet använder vi all input från våra kunder och designar maskinelementen och skickar de färdiga ritningarna till våra kunder för godkännande. När vi godkänts producerar vi de första artiklarna och tillverkar därefter maskinelementen enligt den slutliga designen. I vilket skede som helst av detta arbete, om en viss maskinelementkonstruktion fungerar otillfredsställande på fältet (vilket är sällsynt), granskar vi hela projektet och gör ändringar tillsammans med våra kunder efter behov. Det är vår standardpraxis att underteckna sekretessavtal (NDA) med våra kunder för design av maskinelement eller andra produkter närhelst det behövs eller krävs. När maskinelement för en viss kund är specialdesignade och tillverkade, tilldelar vi en produktkod till den och producerar och säljer dem endast till vår kund som äger produkten. Vi reproducerar maskinelementen med de utvecklade verktygen, formarna och procedurerna så många gånger som behövs och närhelst vår kund beställer om dem. Med andra ord, när ett anpassat maskinelement är designat och producerat för dig, är den immateriella egendomen såväl som alla verktyg och formar reserverade och lagrade på obestämd tid av oss för dig och produkterna reproduceras som du vill. Vi erbjuder också våra kunder ingenjörstjänster genom att kreativt kombinera maskinelement till en komponent eller sammansättning som tjänar en applikation och uppfyller eller överträffar våra kunders förväntningar. Anläggningar som tillverkar våra maskinelement är kvalificerade enligt antingen ISO9001, QS9000 eller TS16949. Dessutom har de flesta av våra produkter CE- eller UL-märkning och uppfyller internationellt relevanta standarder som ISO, SAE, ASME, DIN. Klicka på undermenyerna för att få detaljerad information om våra maskinelement inklusive: - Remmar, kedjor och kabeldrivningar - Kugghjul och växlar - Kopplingar och lager - Nycklar & Splines & stift - Kammar och länkar - Skaft - Mekaniska tätningar - Industriell koppling och broms - Fästelement - Enkla maskiner Vi har utarbetat en referensbroschyr för våra kunder, designers och utvecklare av nya produkter inklusive maskinelement. Du kan bekanta dig med några vanliga termer inom maskinkomponentdesign: Ladda ner broschyr för vanliga termer för maskinteknik som används av designers och ingenjörer Våra maskinelement kan användas inom en mängd olika områden såsom industrimaskiner, automationssystem, test- och mätutrustning, transportutrustning, entreprenadmaskiner och praktiskt taget var som helst du kan tänka dig. AGS-TECH utvecklar och tillverkar maskinelement av olika material beroende på applikation. Material som används för maskinelement kan vara allt från gjuten plast som används för leksaker till härdat och speciellt belagt stål för industrimaskiner. Våra designers använder den senaste professionella mjukvaran och designverktygen för att utveckla maskinelement, med hänsyn till detaljer som vinklar i kuggar, spänningar, slitage... etc. Bläddra igenom våra undermenyer och ladda ner våra produktbroschyrer och kataloger för att se om du kan hitta maskinelement från hyllan för din applikation. Om du inte kan hitta en bra matchning för din applikation, vänligen meddela oss så arbetar vi tillsammans med dig för att utveckla och tillverka maskinelement som uppfyller dina behov. Om du mest är intresserad av vår ingenjörs- och forsknings- och utvecklingskapacitet istället för tillverkningskapacitet, så inbjuder vi dig att besöka vår webbplats http://www.ags-engineering.com där du kan hitta mer detaljerad information om vår design, produktutveckling, processutveckling, ingenjörskonsulttjänster och mer CLICK Product Finder-Locator Service FÖREGÅENDE SIDA
- Transmission Components, Belts, Chains, Cable Drives, Pulleys,AGS-TECH
Transmission Components, Belts, Chains and Cable Drives, Conventional & Grooved or Serrated, Positive Drive, Pulleys Remmar & kedjor & kabeldrivning AGS-TECH Inc. erbjuder kraftöverföringskomponenter inklusive remmar & kedjor & kabeldrivning. Med år av förfining har våra gummi-, läder- och andra remdrifter blivit lättare och mer kompakta och kan bära högre belastning till lägre kostnad. På samma sätt har våra kedjedrev genomgått mycket utveckling över tid och de erbjuder våra kunder flera fördelar. Några fördelar med att använda kedjedrev är deras relativt obegränsade axelcentrumavstånd, kompakthet, enkel montering, elasticitet i spänningen utan glidning eller krypning, förmåga att arbeta i högtemperaturmiljöer. Våra kabeldrivningar erbjuder även fördelar som enkelhet i vissa applikationer jämfört med andra typer av transmissionskomponenter. Både standardremmar, kedje- och kabeldrivningar samt specialtillverkade och monterade versioner finns tillgängliga. Vi kan tillverka dessa transmissionskomponenter till rätt storlek för din applikation och av de mest lämpliga materialen. REMMAR OCH REMMAR: - Konventionella platta bälten: Dessa är vanliga platta bälten utan tänder, spår eller tandningar. Platta remdrifter erbjuder flexibilitet, bra stötdämpning, effektiv kraftöverföring vid höga hastigheter, nötningsbeständighet, låg kostnad. Bälten kan skarvas eller kopplas ihop för att göra större bälten. Andra fördelar med konventionella platta remmar är att de är tunna, de utsätts inte för höga centrifugalbelastningar (gör dem bra för höghastighetsoperationer med små remskivor). Å andra sidan ger de höga lagerbelastningar eftersom platta remmar kräver hög spänning. Andra nackdelar med platt remdrift kan vara slirning, bullrig drift och relativt lägre verkningsgrad vid låga och måttliga drifthastigheter. Vi har två typer av konventionella bälten: förstärkta och icke-förstärkta. Förstärkta bälten har ett dragelement i sin struktur. Konventionella platta bälten finns som läder, gummerat tyg eller snöre, oförstärkt gummi eller plast, tyg, förstärkt läder. Läderbälten erbjuder lång livslängd, flexibilitet, utmärkt friktionskoefficient, enkel reparation. Men läderbälten är relativt dyra, behöver göras om och rengöras, och beroende på atmosfären kan de krympa eller sträcka sig. Gummerade tyg- eller snörebälten är resistenta mot fukt, syra och alkalier. Gummerade tygbälten består av skikt av bomull eller syntetisk anka impregnerade med gummi och är de mest ekonomiska. Gummerade kordbälten består av en serie lager av gummiimpregnerade linor. Gummerade linbälten erbjuder hög draghållfasthet och blygsam storlek och massa. Oförstärkta gummi- eller plastremmar är lämpliga för lätta applikationer med låg hastighet. Oförstärkta gummi- och plastremmar kan sträckas på plats över sina remskivor. Oförstärkta plastbälten kan överföra högre kraft jämfört med gummibälten. Förstärkta läderbälten består av ett dragelement av plast som är inklämt mellan över- och underskikt av läder. Slutligen kan våra tygbälten bestå av ett enda stycke bomull eller anka vikta och sydda med rader av längsstygn. Tygbälten kan spåra jämnt och arbeta i hög hastighet. - Spårade eller tandade remmar (som kilremmar): Dessa är grundläggande platta remmar modifierade för att ge fördelarna med en annan typ av transmissionsprodukt. Dessa är platta bälten med en längsgående räfflad undersida. Poly-V-remmar är längsgående räfflade eller tandade platt rem med dragsektion och en serie intilliggande V-formade spår för spårnings- och kompressionsändamål. Effektkapaciteten beror på bältets bredd. Kilrem är industrins arbetshäst och finns i en mängd olika standardiserade storlekar och typer för överföring av nästan vilken lastkraft som helst. Kilremsdrifter fungerar bra mellan 1500 till 6000 ft/min, men smala kilremmar kommer att fungera upp till 10 000 ft/min. Kilremsdrifter erbjuder lång livslängd som 3 till 5 år och tillåter stora hastighetsförhållanden, de är lätta att installera och ta bort, erbjuder tyst drift, lågt underhåll, bra stötdämpning mellan remdrivare och drivna axlar. Nackdelen med kilremmarna är deras säkra slirning och krypning och därför kanske de inte är den bästa lösningen där synkrona hastigheter krävs. Vi har industri-, bil- och jordbruksbälten. Lagerförda standardlängder samt anpassade längder på bälten finns tillgängliga. Alla standardtvärsnitt av kilremmar finns i lager. Det finns tabeller där du kan beräkna okända parametrar som remlängd, remsektion (bredd & tjocklek) förutsatt att du känner till några parametrar för ditt system som drivande och drivna remskivors diametrar, centrumavstånd mellan remskivor och remskivors rotationshastigheter. Du kan använda sådana tabeller eller be oss välja rätt kilrem för dig. - Positiva drivremmar (kuggrem): Dessa remmar är också av platt typ med en serie jämnt fördelade tänder på insidans omkrets. Positiva driv- eller kuggremmar kombinerar fördelarna med platta remmar med de positiva greppegenskaperna hos kedjor och växlar. Positiva drivremmar visar ingen slirning eller hastighetsvariationer. Ett brett utbud av hastighetsförhållanden är möjligt. Lagerbelastningarna är låga eftersom de kan arbeta med låg spänning. De är dock mer mottagliga för feljusteringar i remskivor. - Remskivor, remskivor, nav för remmar: Olika typer av remskivor används med plana, räfflade (tandade) och positiva drivremmar. Vi tillverkar dem alla. De flesta av våra platta remskivor är tillverkade av gjutning av järn, men stålversioner finns även i olika fälg- och navkombinationer. Våra plattremskivor kan ha solida, ekrade eller delade nav eller så kan vi tillverka som du önskar. Ribbade och positiva drivremmar finns tillgängliga i en mängd olika lagerstorlekar och -bredder. Minst en remskiva i kamremsdrift måste vara flänsad för att hålla remmen på drivningen. För långa centerdrivsystem rekommenderas att båda remskivorna är flänsade. Skivor är de räfflade hjulen på remskivor och tillverkas vanligtvis genom gjutning av järn, stålformning eller plastgjutning. Stålformning är en lämplig process för tillverkning av bil- och jordbruksskivor. Vi tillverkar skivor med regelbundna och djupa spår. Djupspårskivor är väl lämpade när kilrem kommer in i skivan i vinkel, som är fallet vid kvartsvarvsdrifter. Djupa spår är också väl lämpade för drivningar med vertikala axlar och applikationer där vibrationer av remmar kan vara ett problem. Våra remskivor är räfflade remskivor eller platta remskivor som inte tjänar överföring av mekanisk kraft. Mellanremskivor används mest för att spänna remmar. - En- och flera remdrifter: Enkelremsdrifter har ett enda spår medan flera remdrifter har flera spår. Genom att klicka på relevant färgad text nedan kan du ladda ner våra kataloger: - Kraftöverföringsremmar (inkluderar kilremmar, kuggremmar, råa kantremmar, lindade remmar och specialremmar) - Transportband - V-remskivor - Tandremskivor KEDJOR OCH KEDJEDRIVNINGAR: Våra kraftöverföringskedjor har vissa fördelar såsom relativt obegränsade axelcentrumavstånd, enkel montering, kompakthet, elasticitet under spänning utan glidning eller krypning, funktionsförmåga under höga temperaturer. Här är de viktigaste typerna av våra kedjor: - Löstagbara kedjor: Våra löstagbara kedjor är gjorda i en mängd olika storlekar, stigning och maximal hållfasthet och i allmänhet av smidbart järn eller stål. Formbara kedjor tillverkas i en mängd storlekar från 0,902 (23 mm) till 4,063 tum (103 mm) stigning och maximal styrka från 700 till 17 000 lb/kvadrattum. Våra löstagbara stålkedjor är å andra sidan tillverkade i storlekar från 0,904 tum (23 mm) till cirka 3,00 tum (76 mm) i stigning, med maximal styrka från 760 till 5000 lb/square inch._cc781905-5cde-3194-bb3b- 136bad5cf58d_ - Pintle Chains: Dessa kedjor används för tyngre laster och något högre hastigheter till cirka 450 fot/min (2,2 m/sek). Pintle-kedjor är gjorda av individuella gjutna länkar som har en hel, rund cylinderände med förskjutna sidostänger. Dessa kedjelänkar är sammankopplade med stålstift. Dessa kedjor varierar i stigning från cirka 1,00 tum (25 mm) till 6,00 tum (150 mm) och slutliga styrkor mellan 3600 till 30 000 lb/square tum. - Förskjutna sidostångskedjor: Dessa är populära i drivkedjor till entreprenadmaskiner. Dessa kedjor arbetar i hastigheter till 1000 ft/min och överför belastningar till cirka 250 hk. I allmänhet har varje länk två förskjutna sidostänger, en bussning, en rulle, en tapp, en saxsprint. - Rullkedjor: De finns i delningar från 0,25 (6 mm) till 3,00 (75 mm) tum. Den ultimata styrkan hos rullkedjor med enkel bredd sträcker sig mellan 925 till 130 000 lb/kvadrattum. Flera breda versioner av rullkedjor finns tillgängliga och överför större kraft vid högre hastigheter. Rullkedjor med flera bredd ger också mjukare rörelse med minskat ljud. Rullkedjor är sammansatta av rulllänkar och stiftlänkar. Saxsprintar används i rullkedjor i avtagbar version. Konstruktionen av rullkedjedrifter kräver ämneskompetens. Medan remdrift är baserad på linjära hastigheter, baseras kedjedrivningar på rotationshastigheten för det mindre kedjehjulet, som i de flesta installationer är det drivna elementet. Förutom hästkrafter och rotationshastighet, är konstruktionen av kedjedrev baserad på många andra faktorer. - Double-Pitch Chains: I princip samma sak som rullkedjor förutom att stigningen är dubbelt så lång. - Inverterade kedjor (tysta) kedjor: Höghastighetskedjor som används mest för drivmotorer, kraftuttag. Inverterade kedjedrev kan överföra effekter upp till 1200 hk och består av en serie kugglänkar, växelvis sammansatta med antingen stift eller en kombination av ledkomponenter. Mittstyrningskedjan har styrlänkar för att fästa spår i kedjehjulet, och sidostyrningskedjan har styrningar för att koppla in sidorna av kedjehjulet. - Pärl- eller glidkedjor: Dessa kedjor används för låghastighetsdrifter och även för manuella operationer. Genom att klicka på relevant färgad text nedan kan du ladda ner våra kataloger: - Drivkedjor - Transportkedjor - Stora transportkedjor - Rullkedjor i rostfritt stål - Lyftkedjor - Motorcykelkedjor - Kedjor för jordbruksmaskiner - Kedjehjul: Våra standardkedjehjul överensstämmer med ANSI-standarder. Platthjul är platta, navlösa kedjehjul. Våra små och medelstora navhjul är svarvade från stångmaterial eller smide eller tillverkade genom att svetsa ett stångstångsnav till en varmvalsad plåt. AGS-TECH Inc. kan leverera kedjehjul bearbetade av gjutgods av gråjärn, gjutstål och svetsade navkonstruktioner, sintrad pulvermetall, gjuten eller bearbetad plast. För jämn drift vid höga hastigheter är korrekt val av storlek på kedjehjulen avgörande. Utrymmesbegränsningar är naturligtvis en faktor vi inte kan bortse från när vi väljer ett drev. Det rekommenderas att förhållandet mellan drivhjul och drivna kedjehjul inte bör vara mer än 6:1, och kedjans lindning på drivenheten är 120 grader. Centrumavstånd mellan de mindre och större kedjehjulen, kedjelängder och kedjespänning måste också väljas enligt några rekommenderade tekniska beräkningar & riktlinjer och inte slumpmässigt. Ladda ner våra kataloger genom att klicka på färgad text nedan: - Kedjehjul och plåthjul - Transmissionsbussningar - Kedjekoppling - Kedjelås KABELDRIVNINGAR: Dessa har sina fördelar jämfört med remmar och kedjedrift i vissa fall. Kabeldrivningar kan utföra samma funktion som remmar och kan också vara enklare och mer ekonomiska att implementera i vissa applikationer. Till exempel är en ny serie Synchromesh Cable Drives designade för positiv dragkraft för att ersätta konventionella linor, enkla kablar och kuggdrev, särskilt i trånga utrymmen. Den nya kabeldrivningen är designad för att ge hög precision positionering i elektronisk utrustning såsom kopieringsmaskiner, plottrar, skrivmaskiner, skrivare,….. etc. En nyckelfunktion hos den nya kabeldrivningen är dess förmåga att användas i 3D-serpentinkonfigurationer som möjliggör extremt miniatyrdesigner. Synchromesh-kablar kan användas med lägre spänning jämfört med rep, vilket minskar strömförbrukningen. Kontakta AGS-TECH för frågor och synpunkter på remmar, kedje- och kabeldrivningar. CLICK Product Finder-Locator Service FÖREGÅENDE SIDA
- Joining & Assembly & Fastening Processes, Welding, Brazing, Soldering
Joining & Assembly & Fastening Processes, Welding, Brazing, Soldering, Sintering, Adhesive Bonding, Press Fitting, Wave and Reflow Solder Process, Torch Furnace Fogning & Montering & Fästprocesser Vi sammanfogar, monterar och fäster dina tillverkade delar och förvandlar dem till färdiga eller halvfabrikat med hjälp av SVETSNING, LÖDNING, LÖDNING, SINTERING, LIMBINDNING, FÄSTNING, PRESSMASSNING. Några av våra mest populära svetsprocesser är båge, oxyfuel gas, resistans, projektion, söm, störning, slagverk, solid state, elektronstråle, laser, termit, induktionssvetsning. Våra populära hårdlödningsprocesser är brännare, induktion, ugn och dopplödning. Våra lödningsmetoder är järn, värmeplatta, ugn, induktion, dopp, våg, återflöde och ultraljudslödning. För limning använder vi ofta termoplaster och härdplaster, epoxi, fenoler, polyuretan, limlegeringar samt vissa andra kemikalier och tejper. Slutligen består våra fastsättningsprocesser av spikning, skruvning, muttrar och bultar, nitning, clinching, stiftning, sömnad & häftning och presspassning. • SVETSNING: Svetsning innebär sammanfogning av material genom att smälta arbetsstyckena och införa tillsatsmaterial, som också ansluter till den smälta svetsbassängen. När området svalnar får vi en stark fog. Tryck appliceras i vissa fall. I motsats till svetsning involverar hårdlödnings- och lödningsoperationerna endast smältning av ett material med lägre smältpunkt mellan arbetsstyckena, och arbetsstycken smälter inte. Vi rekommenderar att du klickar här för attLADDA NED våra schematiska illustrationer av svetsprocesser av AGS-TECH Inc. Detta hjälper dig att bättre förstå informationen vi ger dig nedan. I ARC WELDING använder vi en strömkälla och en elektrod för att skapa en ljusbåge som smälter metallerna. Svetspunkten är skyddad av en skyddsgas eller ånga eller annat material. Denna process är populär för svetsning av bildelar och stålkonstruktioner. Vid shelded metal arc welding (SMAW) eller även känd som stick welding, förs en elektrodsticka nära basmaterialet och en elektrisk ljusbåge genereras mellan dem. Elektrodstaven smälter och fungerar som fyllnadsmaterial. Elektroden innehåller även flussmedel som fungerar som ett lager av slagg och avger ångor som fungerar som skyddsgas. Dessa skyddar svetsområdet från miljöföroreningar. Inga andra fyllmedel används. Nackdelarna med denna process är dess långsamhet, behovet av att byta ut elektroder ofta, behovet av att flisa bort resterande slagg som härrör från flussmedel. Ett antal metaller som järn, stål, nickel, aluminium, koppar, etc. Kan svetsas. Dess fördelar är dess billiga verktyg och användarvänlighet. Gasmetallbågsvetsning (GMAW) även känd som metallinert gas (MIG), vi har kontinuerlig matning av ett förbrukningsbart elektrodtrådsfyllmedel och en inert eller delvis inert gas som strömmar runt tråden mot miljöförorening av svetsområdet. Stål, aluminium och andra icke-järnmetaller kan svetsas. Fördelarna med MIG är höga svetshastigheter och god kvalitet. Nackdelarna är dess komplicerade utrustning och utmaningar i blåsiga utomhusmiljöer eftersom vi måste hålla skyddsgasen runt svetsområdet stabil. En variant av GMAW är flux-coreed arc welding (FCAW) som består av ett fint metallrör fyllt med flussmaterial. Ibland är flödet inuti röret tillräckligt för att skydda mot miljöföroreningar. Submerged Arc Welding (SAW) är i stor utsträckning en automatiserad process, involverar kontinuerlig trådmatning och båge som slås under ett lager av flussmedelsskydd. Produktionstakten och kvaliteten är hög, svetsslagg lossnar lätt och vi har en rökfri arbetsmiljö. Nackdelen är att den endast kan användas för att svetsa parts i vissa positioner. Vid gas-volframbågsvetsning (GTAW) eller volfram-inert gassvetsning (TIG) använder vi en volframelektrod tillsammans med ett separat fyllmedel och inerta eller nära inerta gaser. Som vi vet har volfram en hög smältpunkt och det är en mycket lämplig metall för mycket höga temperaturer. Tungsten i TIG konsumeras inte i motsats till de andra metoderna som förklaras ovan. En långsam men högkvalitativ svetsteknik fördelaktig jämfört med andra tekniker vid svetsning av tunna material. Lämplig för många metaller. Plasmabågsvetsning är liknande men använder plasmagas för att skapa bågen. Bågen vid plasmabågsvetsning är relativt mer koncentrerad jämfört med GTAW och kan användas för ett bredare spektrum av metalltjocklekar vid mycket högre hastigheter. GTAW och plasmabågsvetsning kan appliceras på mer eller mindre samma material. OXY-FUEL / OXYFUEL WELDING även kallad oxyacetylensvetsning, oxysvetsning, gassvetsning utförs med gasbränslen och syre för svetsning. Eftersom ingen ström används är den bärbar och kan användas där det inte finns någon elektricitet. Med hjälp av en svetsbrännare värmer vi upp delarna och tillsatsmaterialet för att producera en gemensam smältmetallpool. Olika bränslen kan användas såsom acetylen, bensin, väte, propan, butan ... etc. Vid oxy-fuel-svetsning använder vi två behållare, en för bränslet och den andra för syre. Syret oxiderar bränslet (förbränner det). MOTSTÅNDSVETSNING: Denna typ av svetsning drar fördel av jouleuppvärmning och värme genereras på den plats där elektrisk ström appliceras under en viss tid. Höga strömmar passerar genom metallen. Pooler av smält metall bildas på denna plats. Motståndssvetsningsmetoder är populära på grund av deras effektivitet, låga föroreningspotential. Emellertid är nackdelarna att utrustningskostnaderna är relativt betydande och den inneboende begränsningen till relativt tunna arbetsstycken. PUNKTSVETSNING är en huvudtyp av motståndssvetsning. Här sammanfogar vi två eller flera överlappande ark eller arbetsstycken genom att använda två kopparelektroder för att klämma ihop arken och leda en hög ström genom dem. Materialet mellan kopparelektroderna värms upp och en smält pool genereras på den platsen. Strömmen stoppas sedan och kopparelektrodspetsarna kyler svetsplatsen eftersom elektroderna är vattenkylda. Att applicera rätt mängd värme på rätt material och tjocklek är nyckeln för denna teknik, eftersom fogen blir svag om den appliceras felaktigt. Punktsvetsning har fördelen att den inte orsakar någon betydande deformation av arbetsstycken, energieffektivitet, enkel automatisering och enastående produktionshastigheter och kräver inga fyllmedel. Nackdelen är att eftersom svetsning sker på punkter snarare än att bilda en kontinuerlig söm, kan den totala hållfastheten vara relativt lägre jämfört med andra svetsmetoder. SÖMSVETNING å andra sidan producerar svetsar vid de fasta ytorna av liknande material. Sömmen kan vara stum- eller överlappsfog. Sömsvetsning startar i ena änden och går gradvis till den andra. Denna metod använder också två elektroder från koppar för att applicera tryck och ström till svetsområdet. De skivformade elektroderna roterar med konstant kontakt längs sömlinjen och gör en kontinuerlig svetsning. Även här kyls elektroder av vatten. Svetsarna är mycket starka och pålitliga. Andra metoder är projektions-, blixt- och svetstekniker. SOLID-STATE WELDING är lite annorlunda än de tidigare metoderna som förklarats ovan. Koalescens sker vid temperaturer under smälttemperaturen för de sammanfogade metallerna och utan användning av metallfyllmedel. Tryck kan användas i vissa processer. Olika metoder är COEXTRUSION SVETSNING där olika metaller extruderas genom samma munstycke, KALLTRYCKSVETSNING där vi sammanfogar mjuka legeringar under deras smältpunkter, DIFFUSIONSSVETSNING en teknik utan synliga svetslinjer, EXPLOSIONSSvetsning för sammanfogning av olika material, t.ex. korrosionsbeständiga legeringar stål, ELEKTROMAGNETISK PULSSVETSNING där vi accelererar rör och plåt av elektromagnetiska krafter, SMIDSVETSNING som består av att värma metallerna till höga temperaturer och hamra ihop dem, FRIKTIONSSVETSNING där med tillräcklig friktionssvetsning utförs, FRIKTIONSSVETSNING som innebär en roterande icke- förbrukningsverktyg som korsar foglinjen, HETTRYCKSVETSNING där vi pressar samman metaller vid förhöjda temperaturer under smälttemperaturen i vakuum eller inerta gaser, HET ISOSTATISK TRYCKSVETSNING en process där vi applicerar tryck med hjälp av inerta gaser inuti ett kärl, RULLSvetsning där vi sammanfogar olika material genom att tvinga dem emellan två roterande hjul, ULTRASONIC WELDING där tunna metall- eller plastskivor svetsas med högfrekvent vibrationsenergi. Våra andra svetsprocesser är ELEKTRONBALKSVETSNING med djup inträngning och snabb bearbetning men eftersom det är en dyr metod anser vi det för speciella fall, ELEKTROSLAGSVETSNING en metod som lämpar sig endast för tunga tjocka plåtar och arbetsstycken av stål, INDUKTIONSSvetsning där vi använder elektromagnetisk induktion och värma våra elektriskt ledande eller ferromagnetiska arbetsstycken, LASERSTRALSSVETSNING även med djup penetration och snabb bearbetning men en dyr metod, LASER HYBRID WELDING som kombinerar LBW med GMAW i samma svetshuvud och kan överbrygga gap på 2 mm mellan plattorna, SLAGSVETSNING som involverar en elektrisk urladdning följt av smidning av materialen med applicerat tryck, THERMIT WELDING som involverar exoterm reaktion mellan aluminium- och järnoxidpulver., ELECTROGASWELDING med förbrukningsbara elektroder och används med endast stål i vertikalt läge, och slutligen STUD BÅGSvetsning för sammanfogning av bult till bas material med värme och tryck. Vi rekommenderar att du klickar här för attLADDA NED våra schematiska illustrationer av lödnings-, lödnings- och limningsprocesser av AGS-TECH Inc. Detta hjälper dig att bättre förstå informationen vi ger dig nedan. • LÖDNING : Vi sammanfogar två eller flera metaller genom att värma tillsatsmetaller mellan dem över deras smältpunkter och använda kapillärverkan för att spridas. Processen liknar lödning men de temperaturer som är involverade för att smälta fyllmedlet är högre vid lödning. Liksom vid svetsning, skyddar flussmedel tillsatsmaterialet från atmosfärisk förorening. Efter kylning sammanfogas arbetsstyckena. Processen innefattar följande nyckelsteg: Bra passform och frigång, korrekt rengöring av basmaterial, korrekt fixtur, korrekt val av flussmedel och atmosfär, uppvärmning av monteringen och slutligen rengöring av lödd montering. Några av våra hårdlödningsprocesser är TORCH BRAZING, en populär metod som utförs manuellt eller på ett automatiserat sätt. Den är lämplig för lågvolymproduktionsorder och specialiserade fall. Värme appliceras med gaslågor nära fogen som löds. UGNSLÖDNING kräver mindre operatörsskicklighet och är en halvautomatisk process lämplig för industriell massproduktion. Både temperaturkontroll och kontroll av atmosfären i ugnen är fördelar med denna teknik, eftersom den förra gör det möjligt för oss att ha kontrollerade värmecykler och eliminera lokal uppvärmning som är fallet vid brännarlödning, och den senare skyddar delen från oxidation. Genom att använda jigging kan vi reducera tillverkningskostnaderna till ett minimum. Nackdelarna är hög strömförbrukning, utrustningskostnader och mer utmanande designöverväganden. VAKUUMLODNING sker i en ugn av vakuum. Temperaturjämnheten bibehålls och vi får flödesfria, mycket rena fogar med mycket små restspänningar. Värmebehandlingar kan äga rum under vakuumlödning, på grund av de låga restspänningar som finns under långsamma uppvärmnings- och kylcykler. Den stora nackdelen är dess höga kostnad eftersom skapandet av vakuummiljö är en dyr process. Ännu en teknik DIP-LODNING förenar fixerade delar där lödmassa appliceras på matchande ytor. Därefter doppas de fixturerade delarna i ett bad av ett smält salt såsom natriumklorid (bordssalt) som fungerar som ett värmeöverföringsmedium och flussmedel. Luft utesluts och därför sker ingen oxidbildning. I INDUKTIONSLÖDNING sammanfogar vi material med en tillsatsmetall som har en lägre smältpunkt än basmaterialen. Växelströmmen från induktionsspolen skapar ett elektromagnetiskt fält som inducerar induktionsvärme på mestadels järnhaltiga magnetiska material. Metoden ger selektiv uppvärmning, bra fogar med fyllmedel som endast flyter i önskade områden, liten oxidation eftersom inga lågor finns och kylningen är snabb, snabb uppvärmning, konsistens och lämplighet för tillverkning av stora volymer. För att påskynda våra processer och för att säkerställa konsekvens använder vi ofta preforms. Information om vår hårdlödningsanläggning som producerar keramiska till metallbeslag, hermetisk försegling, vakuumgenomföringar, hög- och ultrahögvakuum och vätskekontrollkomponenter finns här:_cc781905-156-5cde_cc781905-916-5cde_cc781905-916-5cdBroschyr för lödningsfabrik • LÖDNING : Vid lödning har vi inte smältning av arbetsstyckena, utan en tillsatsmetall med lägre smältpunkt än fogdelarna som rinner in i fogen. Tillsatsmetallen vid lödning smälter vid lägre temperatur än vid lödning. Vi använder blyfria legeringar för lödning och har RoHS-överensstämmelse och för olika applikationer och krav har vi olika och lämpliga legeringar som silverlegering. Lödning ger oss skarvar som är gas- och vätsketäta. Vid MJUKLÖDNING har vår tillsatsmetall en smältpunkt under 400 Celsius, medan vi vid SILVERLÖDNING och LÖDNING behöver högre temperaturer. Mjuklödning använder lägre temperaturer men ger inte starka fogar för krävande applikationer vid förhöjda temperaturer. Silverlödning å andra sidan kräver höga temperaturer från brännaren och ger oss starka fogar lämpliga för högtemperaturapplikationer. Lödning kräver de högsta temperaturerna och vanligtvis används en ficklampa. Eftersom lödfogar är mycket starka är de en bra kandidat för att reparera tunga järnföremål. I våra tillverkningslinjer använder vi både manuell handlödning och automatiserade lödlinjer. INDUCTIONSLÖDNING använder högfrekvent växelström i en kopparspole för att underlätta induktionsuppvärmning. Strömmar induceras i den lödda delen och som ett resultat genereras värme vid det höga motståndet joint. Denna värme smälter tillsatsmetallen. Flux används också. Induktionslödning är en bra metod för att löda cyklinder och rör i en kontinuerlig process genom att linda spolarna runt dem. Att löda vissa material som grafit och keramik är svårare eftersom det kräver plätering av arbetsstyckena med en lämplig metall före lödning. Detta underlättar gränssnittsbindning. Vi löder sådana material speciellt för hermetiska förpackningsapplikationer. Vi tillverkar våra kretskort (PCB) i stora volymer, mestadels med hjälp av VÅGLÖDNING. Endast för små kvantiteter av prototypsyften använder vi handlödning med lödkolv. Vi använder våglödning för både genomgående hål och ytmonterade PCB-montage (PCBA). Ett tillfälligt lim håller komponenterna fästa på kretskortet och enheten placeras på en transportör och rör sig genom en utrustning som innehåller smält lod. Först fluxas kretskortet och går sedan in i förvärmningszonen. Det smälta lodet är i en panna och har ett mönster av stående vågor på sin yta. När kretskortet rör sig över dessa vågor kommer dessa vågor i kontakt med botten av kretskortet och fastnar på lödkuddarna. Lödet stannar bara på stift och kuddar och inte på själva kretskortet. Vågorna i det smälta lodet måste kontrolleras väl så att det inte stänks och vågtopparna inte berör och förorenar oönskade områden på brädorna. I REFLOW SOLDERING använder vi en klibbig lödpasta för att tillfälligt fästa de elektroniska komponenterna på korten. Därefter förs skivorna genom en återflödesugn med temperaturkontroll. Här smälter lodet och förbinder komponenterna permanent. Vi använder denna teknik för både ytmonteringskomponenter och för genomgående hålkomponenter. Korrekt temperaturkontroll och justering av ugnstemperaturer är avgörande för att undvika förstörelse av elektroniska komponenter på kortet genom att överhetta dem över deras maximala temperaturgränser. I processen med återflödeslödning har vi faktiskt flera regioner eller stadier var och en med en distinkt termisk profil, såsom förvärmningssteg, termiskt blötläggningssteg, återflödes- och kylsteg. Dessa olika steg är väsentliga för en skadefri återflödeslödning av kretskortsenheter (PCBA). ULTRASONIC LODERING är en annan ofta använd teknik med unika möjligheter- Den kan användas för att löda glas, keramiska och icke-metalliska material. Till exempel fotovoltaiska paneler som är icke-metalliska behöver elektroder som kan fästas med denna teknik. Vid ultraljudslödning använder vi en uppvärmd lödspets som även avger ultraljudsvibrationer. Dessa vibrationer producerar kavitationsbubblor vid gränsytan mellan substratet och det smälta lodmaterialet. Kavitationens implosiva energi modifierar oxidytan och tar bort smuts och oxider. Under denna tid bildas också ett legeringsskikt. Lödet vid bindningsytan innehåller syre och möjliggör bildandet av en stark delad bindning mellan glaset och lodet. DOPSLÖDNING kan betraktas som en enklare version av våglödning som endast lämpar sig för småskalig produktion. Första rengöringsflödet appliceras som i andra processer. PCB med monterade komponenter doppas manuellt eller på ett halvautomatiskt sätt i en tank som innehåller smält lod. Det smälta lodet fastnar på de exponerade metallområdena oskyddade av lödmasken på brädet. Utrustningen är enkel och billig. • ADHESIVBINDNING: Detta är en annan populär teknik som vi ofta använder och den involverar limning av ytor med lim, epoxi, plastmedel eller andra kemikalier. Bindning åstadkoms genom att antingen avdunsta lösningsmedlet, genom värmehärdning, genom UV-ljushärdning, genom tryckhärdning eller vänta en viss tid. Olika högpresterande lim används i våra produktionslinjer. Med korrekt konstruerade applicerings- och härdningsprocesser kan limbindning resultera i bindningar med mycket låg spänning som är starka och pålitliga. Limbindningar kan vara bra skydd mot miljöfaktorer som fukt, föroreningar, frätande ämnen, vibrationer etc. Fördelarna med limbindning är: de kan appliceras på material som annars skulle vara svåra att löda, svetsa eller hårdlöda. Det kan också vara att föredra för värmekänsliga material som skulle skadas av svetsning eller andra högtemperaturprocesser. Andra fördelar med lim är att de kan appliceras på oregelbundet formade ytor och ökar monteringsvikten med mycket mycket små mängder jämfört med andra metoder. Även dimensionsförändringar i delar är mycket minimala. Vissa lim har indexmatchande egenskaper och kan användas mellan optiska komponenter utan att minska ljuset eller den optiska signalstyrkan avsevärt. Nackdelar å andra sidan är längre härdningstider som kan sakta ner tillverkningslinjer, fixturkrav, krav på ytförberedelse och svårigheter att demontera när omarbetning behövs. De flesta av våra limningsoperationer innefattar följande steg: -Ytbehandling: Speciella rengöringsprocedurer som rengöring av avjoniserat vatten, alkoholrengöring, plasma- eller coronarengöring är vanliga. Efter rengöring kan vi applicera vidhäftningsfrämjande medel på ytorna för att säkerställa bästa möjliga fogar. -Delfixtur: För både limapplikation och för härdning designar och använder vi anpassade fixturer. - Limapplikation: Vi använder ibland manuella, och ibland beroende på fallet, automatiserade system som robotik, servomotorer, linjära ställdon för att leverera limmet till rätt plats och vi använder dispensrar för att leverera det i rätt volym och kvantitet. -Hardning: Beroende på limmet kan vi använda enkel torkning och härdning såväl som härdning under UV-ljus som fungerar som katalysator eller värmehärdning i en ugn eller med resistiva värmeelement monterade på jiggar och fixturer. Vi rekommenderar att du klickar här för attLADDA NED våra schematiska illustrationer av fästprocesser av AGS-TECH Inc. Detta hjälper dig att bättre förstå informationen vi ger dig nedan. • FÄSTPROCESSER: Våra mekaniska sammanfogningsprocesser delas in i två kategorier: FÄSTNINGAR och INTEGRALFOGAR. Exempel på fästelement vi använder är skruvar, stift, muttrar, bultar, nitar. Exempel på integrerade fogar vi använder är snäpp- och krymppassningar, sömmar, krympningar. Genom att använda en mängd olika fästmetoder ser vi till att våra mekaniska leder är starka och pålitliga för många års användning. SKRUVAR och BULTAR är några av de vanligaste fästelementen för att hålla ihop föremål och placera dem. Våra skruvar och bultar uppfyller ASME-standarder. Olika typer av skruvar och bultar används inklusive sexkantsskruvar och sexkantsskruvar, lagskruvar och bultar, dubbelskruv, pluggskruv, ögonskruv, spegelskruv, plåtskruv, finjusteringsskruv, självborrande och självgängande skruvar , ställskruv, skruvar med inbyggda brickor, ... och mer. Vi har olika typer av skruvhuvuden såsom försänkt, kupol, runt, flänshuvud och olika typer av skruvdragare såsom slits, phillips, fyrkant, insexhylsa. En RIVET å andra sidan är ett permanent mekaniskt fästelement som består av ett slätt cylindiriskt skaft och ett huvud å ena sidan. Efter insättningen deformeras den andra änden av niten och dess diameter utökas så att den stannar på plats. Med andra ord, före installationen har en nit ett huvud och efter installationen två. Vi installerar olika typer av nitar beroende på applikation, styrka, tillgänglighet och kostnad såsom solida/runda nitar, strukturella, semi-tubular, blind, oscar, drive, flush, friction-lock, självgenomträngande nitar. Nitning kan föredras i de fall värmedeformation och förändringar i materialegenskaper på grund av svetsvärme behöver undvikas. Nitning ger också lätt vikt och särskilt god styrka och uthållighet mot skjuvkrafter. Mot dragbelastningar kan dock skruvar, muttrar och bultar vara mer lämpliga. I CLINCHING-processen använder vi speciella stansar och stansar för att bilda en mekanisk förregling mellan plåt som sammanfogas. Stansen trycker in skikten av plåt i formhåligheten och resulterar i bildandet av en permanent fog. Ingen uppvärmning och ingen kylning krävs vid clinching och det är en kall arbetsprocess. Det är en ekonomisk process som i vissa fall kan ersätta punktsvetsning. I PINNING använder vi stift som är maskinelement som används för att säkra positioner av maskindelar i förhållande till varandra. Huvudtyperna är gaffelsprintar, saxstift, fjäderstift, pluggstift, och delad stift. I STAPLING använder vi häftpistoler och häftklamrar som är tvåsidiga fästelement som används för att sammanfoga eller binda material. Häftning har följande fördelar: Ekonomisk, enkel och snabb att använda, häftklamrarnas krona kan användas för att överbrygga sammansatta material, häftklammerns krona kan underlätta att överbrygga en bit som en kabel och fästa den på en yta utan att punktera eller skadlig, relativt enkel borttagning. PRESSMONTERING utförs genom att delarna trycks ihop och friktionen mellan dem fäster delarna. Presspassningsdelar som består av ett överdimensionerat skaft och ett underdimensionerat hål sätts vanligtvis ihop med en av två metoder: Antingen genom att applicera kraft eller dra fördel av termisk expansion eller sammandragning av delarna. När en presspassning upprättas genom att applicera en kraft, använder vi antingen en hydraulisk press eller en handmanövrerad press. Å andra sidan när presspassning etableras genom termisk expansion värmer vi de omslutande delarna och monterar dem på sin plats medan de är varma. När de svalnar drar de ihop sig och återgår till sina normala dimensioner. Detta resulterar i en bra presspassning. Vi kallar detta alternativt SHRINK-FITTING. Det andra sättet att göra detta är genom att kyla de omslutna delarna före montering och sedan skjuta in dem i deras passande delar. När monteringen värms upp expanderar de och vi får en tät passform. Den senare metoden kan vara att föredra i de fall uppvärmning innebär risk för att materialegenskaperna ändras. Kylning är säkrare i dessa fall. Pneumatiska och hydrauliska komponenter och sammansättningar • Ventiler, hydrauliska och pneumatiska komponenter såsom O-ring, bricka, tätningar, packning, ring, shim. Eftersom ventiler och pneumatiska komponenter finns i en stor variation kan vi inte lista allt här. Beroende på de fysiska och kemiska miljöerna för din applikation har vi specialprodukter för dig. Vänligen ange applikation, typ av komponent, specifikationer, miljöförhållanden såsom tryck, temperatur, vätskor eller gaser som kommer i kontakt med dina ventiler och pneumatiska komponenter; och vi kommer att välja den mest lämpliga produkten för dig eller tillverka den speciellt för din applikation. CLICK Product Finder-Locator Service FÖREGÅENDE SIDA
- Composites, Composite Materials Manufacturing, Fiber Reinforced
Composites, Composite Materials Manufacturing, Particle and Fiber Reinforced, Cermets, Ceramic & Metal Composite, Glass Fiber Reinforced Polymer, Lay-Up Process Tillverkning av kompositer och kompositmaterial Enkelt definierat är KOMPOSITET eller KOMPOSITMATERIAL material som består av två eller flera material med olika fysikaliska eller kemiska egenskaper, men när de kombineras blir de ett material som är annorlunda än de ingående materialen. Vi måste påpeka att de ingående materialen förblir separata och distinkta i strukturen. Målet med att tillverka ett kompositmaterial är att få en produkt som är överlägsen dess beståndsdelar och kombinerar varje beståndsdels önskade egenskaper. Som ett exempel; styrka, låg vikt eller lägre pris kan vara motivationen bakom att designa och producera en komposit. Den typ av kompositer vi erbjuder är partikelförstärkta kompositer, fiberarmerade kompositer inklusive keramisk-matris / polymer-matris / metall-matris / kol-kol / hybridkompositer, strukturella & laminerade & sandwich-strukturerade kompositer och nanokompositer. De tillverkningstekniker vi använder vid tillverkning av kompositmaterial är: Pultrusion, prepreg-produktionsprocesser, avancerad fiberplacering, filamentlindning, skräddarsydd fiberplacering, glasfiberspray-uppläggningsprocess, tuftning, lanxidprocess, z-pinning. Många kompositmaterial är uppbyggda av två faser, matrisen, som är kontinuerlig och omger den andra fasen; och den dispergerade fasen som omges av matrisen. Vi rekommenderar att du klickar här för attLADDA NED våra schematiska illustrationer av tillverkning av kompositer och kompositmaterial av AGS-TECH Inc. Detta hjälper dig att bättre förstå informationen vi ger dig nedan. • Partikelförstärkta kompositer: Denna kategori består av två typer: kompositer med stora partiklar och dispersionsförstärkta kompositer. I den förstnämnda typen kan partikel-matrisinteraktioner inte behandlas på atomär eller molekylär nivå. Istället är kontinuummekaniken giltig. Å andra sidan, i dispersionsförstärkta kompositer är partiklar i allmänhet mycket mindre inom tiotals nanometerintervall. Ett exempel på komposit med stora partiklar är polymerer till vilka fyllmedel har tillsatts. Fyllmedlen förbättrar materialets egenskaper och kan ersätta en del av polymervolymen med ett mer ekonomiskt material. Volymfraktionerna av de två faserna påverkar kompositens beteende. Stora partikelkompositer används med metaller, polymerer och keramik. CERMETS är exempel på keramik/metallkompositer. Vår vanligaste cermet är hårdmetall. Den består av eldfast karbidkeramik såsom volframkarbidpartiklar i en matris av en metall som kobolt eller nickel. Dessa hårdmetallkompositer används ofta som skärverktyg för härdat stål. De hårda hårdmetallpartiklarna är ansvariga för skärverkan och deras seghet förstärks av den formbara metallmatrisen. Därmed får vi fördelarna med båda materialen i en enda komposit. Ett annat vanligt exempel på en komposit med stora partiklar som vi använder är kimrökspartiklar blandade med vulkaniserat gummi för att erhålla en komposit med hög draghållfasthet, seghet, riv- och nötningsbeständighet. Ett exempel på en dispersionsförstärkt komposit är metaller och metallegeringar som stärkts och härdats genom den likformiga spridningen av fina partiklar av ett mycket hårt och inert material. När mycket små aluminiumoxidflingor tillsätts till aluminiummetallmatrisen får vi sintrat aluminiumpulver som har en förbättrad hållfasthet vid hög temperatur. • FIBERARMERADE KOMPOSITETER: Denna kategori av kompositer är faktiskt den viktigaste. Målet att uppnå är hög hållfasthet och styvhet per viktenhet. Fibersammansättningen, längden, orienteringen och koncentrationen i dessa kompositer är avgörande för att bestämma egenskaperna och användbarheten hos dessa material. Det finns tre grupper av fibrer vi använder: morrhår, fibrer och trådar. WHISKERS är mycket tunna och långa enkristaller. De är bland de starkaste materialen. Några exempel på whiskermaterial är grafit, kiselnitrid, aluminiumoxid. FIBERS å andra sidan är mestadels polymerer eller keramer och är i polykristallint eller amorft tillstånd. Den tredje gruppen är fina TRÅDAR som har relativt stora diametrar och ofta består av stål eller volfram. Ett exempel på trådförstärkt komposit är bildäck som innehåller ståltråd inuti gummi. Beroende på matrismaterialet har vi följande kompositer: POLYMER-MATRIX-KOMPOSITER: Dessa är gjorda av ett polymerharts och fibrer som förstärkningsingrediens. En undergrupp av dessa kallas glasfiberförstärkt polymer (GFRP) kompositer innehåller kontinuerliga eller diskontinuerliga glasfibrer i en polymermatris. Glas ger hög hållfasthet, det är ekonomiskt, lätt att tillverka till fibrer och är kemiskt inert. Nackdelarna är deras begränsade styvhet och styvhet, drifttemperaturer är endast upp till 200 – 300 Celsius. Glasfiber är lämpligt för karosser och transportutrustning för bilar, karosser för marina fordon, förvaringsbehållare. De är inte lämpliga för flyg- eller bryggtillverkning på grund av begränsad styvhet. Den andra undergruppen kallas Carbon Fiber-Reinforced Polymer (CFRP) Composite. Här är kol vårt fibermaterial i polymermatrisen. Kol är känt för sin höga specifika modul och styrka och dess förmåga att hålla dessa vid höga temperaturer. Kolfibrer kan erbjuda oss standard-, mellan-, hög- och ultrahög dragmoduler. Dessutom erbjuder kolfibrer olika fysiska och mekaniska egenskaper och är därför lämpliga för olika skräddarsydda tekniska tillämpningar. CFRP-kompositer kan anses användas för att tillverka sport- och fritidsutrustning, tryckkärl och strukturkomponenter för flygindustrin. Ändå, en annan undergrupp, Aramid Fiber-Reinforced Polymer Composites är också material med hög hållfasthet och modul. Deras förhållande mellan styrka och vikt är enastående höga. Aramidfibrer är också kända under handelsnamnen KEVLAR och NOMEX. Under spänning presterar de bättre än andra polymera fibermaterial, men de är svaga i kompression. Aramidfibrer är sega, slagtåliga, kryp- och utmattningsbeständiga, stabila vid höga temperaturer, kemiskt inerta förutom mot starka syror och baser. Aramidfibrer används ofta i sportartiklar, skottsäkra västar, däck, rep, fiberoptiska kabelskydd. Andra fiberförstärkningsmaterial finns men används i mindre grad. Dessa är främst bor, kiselkarbid, aluminiumoxid. Polymermatrismaterialet å andra sidan är också kritiskt. Den bestämmer den maximala driftstemperaturen för kompositen eftersom polymeren i allmänhet har en lägre smält- och nedbrytningstemperatur. Polyestrar och vinylestrar används ofta som polymermatris. Hartser används också och de har utmärkt fuktbeständighet och mekaniska egenskaper. Till exempel kan polyimidharts användas upp till cirka 230 grader Celsius. METALL-MATRIX-KOMPOSITER: I dessa material använder vi en seg metallmatris och servicetemperaturerna är i allmänhet högre än deras beståndsdelar. Jämfört med polymer-matriskompositer kan dessa ha högre driftstemperaturer, vara obrännbara och kan ha bättre nedbrytningsbeständighet mot organiska vätskor. Men de är dyrare. Förstärkningsmaterial såsom morrhår, partiklar, kontinuerliga och diskontinuerliga fibrer; och matrismaterial såsom koppar, aluminium, magnesium, titan, superlegeringar används vanligtvis. Exempel på applikationer är motorkomponenter gjorda av aluminiumlegeringsmatris förstärkt med aluminiumoxid och kolfibrer. CERAMIC-MATRIX COMPOSITES: Keramiska material är kända för sin enastående goda högtemperaturtillförlitlighet. De är dock mycket spröda och har låga värden för brottseghet. Genom att bädda in partiklar, fibrer eller whiskers av en keramik i matrisen av en annan kan vi uppnå kompositer med högre brottseghet. Dessa inbäddade material hämmar i princip sprickutbredning inuti matrisen genom vissa mekanismer som att avleda sprickspetsarna eller bilda broar över sprickytorna. Som ett exempel används aluminiumoxider som är förstärkta med SiC-whiskers som skärverktyg för bearbetning av hårdmetallegeringar. Dessa kan avslöja bättre prestanda jämfört med hårdmetaller. KOL-KOLKOMPOSITER: Både förstärkningen och matrisen är kol. De har höga dragmoduler och hållfastheter vid höga temperaturer över 2000 Celsius, krypmotstånd, hög brottseghet, låga värmeutvidgningskoefficienter, höga värmeledningsförmåga. Dessa egenskaper gör dem idealiska för applikationer som kräver värmechockbeständighet. Svagheten med kol-kol-kompositer är dock dess sårbarhet mot oxidation vid höga temperaturer. Typiska exempel på användning är varmpressande formar, avancerad tillverkning av turbinmotorkomponenter. HYBRIDKOMPOSITER: Två eller flera olika typer av fibrer blandas i en enda matris. Man kan alltså skräddarsy ett nytt material med en kombination av egenskaper. Ett exempel är när både kol- och glasfibrer inkorporeras i ett polymerharts. Kolfibrer ger styvhet och styrka med låg densitet men är dyra. Glaset å andra sidan är billigt men saknar styvheten hos kolfibrer. Glas-kolhybridkompositen är starkare och segare och kan tillverkas till en lägre kostnad. BEHANDLING AV FIBERARMERADE KOMPOSITER: För kontinuerliga fiberarmerade plaster med jämnt fördelade fibrer orienterade i samma riktning använder vi följande tekniker. PULTRUSION: Stavar, balkar och rör med kontinuerliga längder och konstanta tvärsnitt tillverkas. Kontinuerliga fiberrovings impregneras med ett värmehärdande harts och dras genom ett stålmunstycke för att förforma dem till önskad form. Därefter passerar de genom en precisionsbearbetad härdningsform för att uppnå sin slutliga form. Eftersom härdningsmunstycket upphettas härdar det hartsmatrisen. Avdragare drar materialet genom formarna. Med hjälp av insatta ihåliga kärnor kan vi erhålla rör och ihåliga geometrier. Pultrusionsmetoden är automatiserad och ger oss höga produktionshastigheter. Vilken längd av produkten som helst är möjlig att producera. TILLVERKNINGSPROCESS FÖR PREPREG: Prepreg är en kontinuerlig fiberarmering förimpregnerad med ett delvis härdat polymerharts. Det används ofta för strukturella applikationer. Materialet kommer i tejpform och skickas som tejp. Tillverkaren formar den direkt och härdar den helt utan att behöva tillsätta något harts. Eftersom prepregs genomgår härdningsreaktioner vid rumstemperatur, förvaras de vid 0 Celsius eller lägre temperaturer. Efter användning förvaras de återstående tejparna vid låga temperaturer. Termoplaster och härdplaster används och armeringsfibrer av kol, aramid och glas är vanliga. För att använda prepregs, tas bärarunderlaget först bort och sedan utförs tillverkningen genom att lägga prepreg-tejpen på en bearbetad yta (uppläggningsprocessen). Flera lager kan läggas upp för att erhålla önskad tjocklek. Frekvent praxis är att alternera fiberorienteringen för att framställa ett tvärskikts- eller vinkelskiktslaminat. Slutligen appliceras värme och tryck för härdning. Både handbearbetning och automatiserade processer används för att skära prepregs och lay-up. FILAMENTVINDNING: Kontinuerliga förstärkningsfibrer är noggrant placerade i ett förutbestämt mönster för att följa en ihålig och vanligtvis cyklindirisk form. Fibrerna går först genom ett hartsbad och lindas sedan på en dorn av ett automatiserat system. Efter flera lindningsupprepningar erhålls önskade tjocklekar och härdning utförs antingen vid rumstemperatur eller inuti en ugn. Nu tas dornen bort och produkten tas ur formen. Filamentlindning kan erbjuda mycket höga styrka-till-vikt-förhållanden genom att linda fibrerna i omkrets-, spiralformade och polära mönster. Rör, tankar, höljen tillverkas med denna teknik. • STRUKTURELLA KOMPOSITER: Generellt består dessa av både homogena och kompositmaterial. Därför bestäms egenskaperna hos dessa av de ingående materialen och den geometriska utformningen av dess element. Här är de viktigaste typerna: LAMINÄR KOMPOSITER: Dessa strukturella material är gjorda av tvådimensionella skivor eller paneler med föredragna höghållfasta riktningar. Skikten staplas och cementeras ihop. Genom att alternera de höghållfasta riktningarna i de två vinkelräta axlarna får vi en komposit som har hög hållfasthet i båda riktningarna i det tvådimensionella planet. Genom att justera skiktens vinklar kan man tillverka en komposit med styrka i de föredragna riktningarna. Moderna skidor är tillverkade på detta sätt. SANDWICH-PANELER: Dessa strukturella kompositer är lätta men har ändå hög styvhet och styrka. Sandwichpaneler består av två ytterplåtar av ett styvt och starkt material som aluminiumlegeringar, fiberförstärkt plast eller stål och en kärna mellan ytterplåtarna. Kärnan måste vara lätt och för det mesta ha en låg elasticitetsmodul. Populära kärnmaterial är styva polymerskum, trä och bikakor. Sandwichpaneler används i stor utsträckning inom byggindustrin som takmaterial, golv- eller väggmaterial, och även inom flygindustrin. • NANOKOMPOSITTER: Dessa nya material består av partiklar i nanostorlek inbäddade i en matris. Med hjälp av nanokompositer kan vi tillverka gummimaterial som är mycket bra barriärer mot luftinträngning samtidigt som de bibehåller sina gummiegenskaper oförändrade. CLICK Product Finder-Locator Service FÖREGÅENDE SIDA
- Glass and Ceramic Manufacturing, Hermetic Packages, Seals, Bonding
Glass and Ceramic Manufacturing, Hermetic Packages Seals and Bonding, Tempered Bulletproof Glass, Blow Moulding, Optical Grade Glass, Conductive Glass, Molding Formning och formning av glas och keramik Den typ av glastillverkning vi erbjuder är behållarglas, glasblåsning, glasfiber & rör & stav, hushålls- och industriglasvaror, lampa och glödlampa, precisionsgjutning av glas, optiska komponenter och sammansättningar, platt- & skiv- & floatglas. Vi utför både handformning och maskinformning. Våra populära tekniska keramiska tillverkningsprocesser är formpressning, isostatisk pressning, varm isostatisk pressning, varmpressning, slipgjutning, bandgjutning, extrudering, formsprutning, grönbearbetning, sintring eller bränning, diamantslipning, hermetiska sammansättningar. Vi rekommenderar att du klickar här för att LADDA NED våra schematiska illustrationer av glasformnings- och formningsprocesser av AGS-TECH Inc. LADDA NED våra schematiska illustrationer av tekniska keramiska tillverkningsprocesser av AGS-TECH Inc. Dessa nedladdningsbara filer med foton och skisser hjälper dig att bättre förstå informationen vi ger dig nedan. • TILLVERKNING AV CONTAINERGLAS: Vi har automatiserade PRESS AND BLOW samt BLÅS OCH BLÅS linjer för tillverkning. I blås- och blåsprocessen släpper vi en gob i en blank form och formar halsen genom att applicera ett tryck med tryckluft uppifrån. Omedelbart efter detta blåses tryckluft en andra gång från den andra riktningen genom behållarens hals för att bilda flaskans förform. Denna förform överförs sedan till själva formen, återupphettas för att mjukna och tryckluft appliceras för att ge förformen dess slutliga behållarform. Mer uttryckligen trycksätts den och skjuts mot väggarna i formblåsningshåligheten för att få sin önskade form. Slutligen överförs den tillverkade glasbehållaren till en glödgningsugn för efterföljande återuppvärmning och avlägsnande av spänningar som uppstår under formningen och kyls på ett kontrollerat sätt. I press- och blåsmetoden sätts smälta gobs i en formform (blank form) och pressas till formen (blank form). Ämnena överförs sedan till blåsformar och blåses på samma sätt som den process som beskrivs ovan under "Blow and Blow Process". Efterföljande steg som glödgning och avspänningsavlastning är liknande eller samma. • GLASBLÄSNING: Vi har tillverkat glasprodukter med hjälp av konventionell handblåsning samt med hjälp av tryckluft med automatiserad utrustning. För vissa beställningar är konventionell blåsning nödvändig, såsom projekt som involverar glaskonstverk, eller projekt som kräver ett mindre antal delar med lösa toleranser, prototyper/demoprojekt...etc. Konventionell glasblåsning involverar doppning av ett ihåligt metallrör i en kruka med smält glas och rotation av röret för att samla upp en viss mängd av glasmaterialet. Glaset som samlas på spetsen av röret rullas på plattjärn, formas efter önskemål, förlängs, värms upp igen och blåses i luften. När den är klar, sätts den in i en form och luft blåses. Formhålan är våt för att undvika kontakt mellan glaset och metall. Vattenfilmen fungerar som en kudde mellan dem. Manuell blåsning är en arbetsintensiv långsam process och endast lämplig för prototyper eller föremål av högt värde, inte lämplig för billiga per styck stora volymbeställningar. • TILLVERKNING AV HEMMA OCH INDUSTRIELLA GLASVAROR: Genom att använda olika typer av glasmaterial tillverkas ett stort urval av glasvaror. Vissa glas är värmebeständiga och lämpar sig för laboratorieglas medan vissa är tillräckligt bra för att tåla diskmaskiner många gånger och lämpar sig för tillverkning av hushållsprodukter. Med hjälp av Westlake-maskiner produceras tiotusentals bitar av dricksglas per dag. För att förenkla, samlas smält glas upp med vakuum och sätts in i formar för att göra förformarna. Sedan blåses luft in i formarna, dessa förs över till en annan form och luft blåser igen och glaset får sin slutgiltiga form. Liksom vid handblåsning hålls dessa formar våta med vatten. Ytterligare sträckning är en del av efterbehandlingsoperationen där halsen formas. Överskottsglas bränns av. Därefter följer den kontrollerade återuppvärmnings- och kylprocessen som beskrivs ovan. • FORMNING AV GLAS RÖR OCH STAV: De huvudsakliga processerna vi använder för tillverkning av glasrör är DANNER- och VELLO-processerna. I Danner-processen flyter glas från en ugn och faller på en lutande hylsa gjord av eldfasta material. Hylsan bärs på en roterande ihålig axel eller blåsrör. Glaset lindas sedan runt hylsan och bildar ett slätt skikt som rinner ner genom hylsan och över skaftets spets. Vid rörformning blåses luft genom ett blåsrör med ihålig spets, och vid stavformning använder vi fasta spetsar på axeln. Rören eller stängerna dras sedan över bärrullar. Dimensionerna som väggtjocklek och diameter på glasrören justeras till önskade värden genom att ställa in diametern på hylsan och blåsa lufttrycket till ett önskat värde, justera temperaturen, glasets flödeshastighet och dragningshastigheten. Tillverkningsprocessen för Vello glasrör å andra sidan involverar glas som går ut genom en ugn och in i en skål med en ihålig dorn eller klocka. Glaset går sedan genom luftrummet mellan dornen och skålen och får formen av ett rör. Därefter går den över rullar till en ritmaskin och kyls. I slutet av kyllinjen sker skärning och slutbehandling. Rördimensionerna kan justeras precis som i Danner-processen. När vi jämför Danner- och Vello-processen kan vi säga att Vello-processen passar bättre för produktion av stora kvantiteter medan Danner-processen kan passa bättre för exakta rörbeställningar med mindre volym. • BEHANDLING AV PLAN & FLAT & FLOAT GLAS: Vi har stora mängder planglas i tjocklekar som sträcker sig från submilimetertjocklekar till flera centimeter. Våra platta glasögon är av nästan optisk perfektion. Vi erbjuder glas med speciella beläggningar såsom optiska beläggningar, där kemisk ångavsättningsteknik används för att lägga beläggningar såsom antireflex eller spegelbeläggning. Även transparenta ledande beläggningar är vanliga. Det finns även hydrofoba eller hydrofila beläggningar på glas och beläggning som gör glaset självrengörande. Härdade, skottsäkra och laminerade glas är ännu andra populära föremål. Vi skär glas i önskad form med önskade toleranser. Andra sekundära operationer som att böja eller böja planglas är tillgängliga. • PRECISIONSGLASFORMNING: Vi använder denna teknik mestadels för att tillverka optiska precisionskomponenter utan behov av dyrare och tidskrävande tekniker som slipning, lappning och polering. Denna teknik är inte alltid tillräcklig för att göra det bästa av den bästa optiken, men i vissa fall som konsumentprodukter, digitalkameror, medicinsk optik kan det vara ett billigare bra alternativ för tillverkning av hög volym. Det har också en fördel gentemot andra glasformningstekniker där komplexa geometrier krävs, som i fallet med asfärer. Den grundläggande processen innebär laddning av undersidan av vår form med glasämnet, evakuering av processkammaren för syreborttagning, nära stängning av formen, snabb och isoterm uppvärmning av form och glas med infrarött ljus, ytterligare stängning av formhalvorna att pressa det mjukgjorda glaset långsamt på ett kontrollerat sätt till önskad tjocklek, och slutligen kyla glaset och fylla kammaren med kväve och avlägsnande av produkten. Exakt temperaturkontroll, formstängningsavstånd, formstängningskraft, matchning av expansionskoefficienterna för formen och glasmaterialet är nyckeln i denna process. • TILLVERKNING AV OPTISKA KOMPONENTER OCH MONTERINGAR AV GLAS: Förutom precisionsgjutning av glas finns det ett antal värdefulla processer vi använder för att tillverka optiska komponenter och sammansättningar av hög kvalitet för krävande applikationer. Slipning, lappning och polering av glasögon av optisk kvalitet i fina speciella slipslam är en konst och vetenskap för att göra optiska linser, prismor, plattor och mer. Ytans planhet, vågighet, jämnhet och defektfria optiska ytor kräver mycket erfarenhet av sådana processer. Små förändringar i miljön kan resultera i produkter som inte är specifikationer och få tillverkningslinjen att stanna. Det finns fall där en enkel avtorkning på den optiska ytan med en ren trasa kan få en produkt att uppfylla specifikationerna eller misslyckas i testet. Några populära glasmaterial som används är smält kiseldioxid, kvarts, BK7. Även monteringen av sådana komponenter kräver specialiserad nischerfarenhet. Ibland används speciella lim. Men ibland är en teknik som kallas optisk kontakt det bästa valet och involverar inget material mellan påsatta optiska glasögon. Den består av fysisk kontakt med plana ytor för att fästa vid varandra utan lim. I vissa fall används mekaniska distanser, precisionsglasstavar eller -kulor, klämmor eller bearbetade metallkomponenter för att montera de optiska komponenterna på vissa avstånd och med vissa geometriska orienteringar till varandra. Låt oss undersöka några av våra populära tekniker för tillverkning av avancerad optik. SLIPNING & LAPPNING & POLERNING: Den optiska komponentens grova form erhålls genom att slipa ett glasämne. Därefter utförs lappning och polering genom att de optiska komponenternas grova ytor roteras och gnuggas mot verktyg med önskad ytform. Uppslamningar med små slipande partiklar och vätska hälls in mellan optiken och formverktygen. Slipmedelspartikelstorlekarna i sådana uppslamningar kan väljas i enlighet med den önskade graden av planhet. Avvikelserna för kritiska optiska ytor från önskade former uttrycks i termer av våglängder för det ljus som används. Vår högprecisionsoptik har tiondels våglängdstolerans (Våglängd/10) eller ännu snävare är möjligt. Förutom ytprofil skannas de kritiska ytorna och utvärderas för andra ytegenskaper och defekter såsom dimensioner, repor, nagg, gropar, fläckar...etc. Den strikta kontrollen av miljöförhållandena i det optiska tillverkningsgolvet och omfattande mät- och testkrav med toppmodern utrustning gör detta till en utmanande industrigren. • SEKUNDÄRA PROCESSER I GLAS TILLVERKNING: Återigen, vi är bara begränsade med din fantasi när det gäller sekundära och efterbehandlingsprocesser av glas. Här listar vi några av dem: -Beläggningar på glas (optisk, elektrisk, tribologisk, termisk, funktionell, mekanisk...). Som ett exempel kan vi ändra ytegenskaperna hos glaset så att det till exempel reflekterar värme så att det håller byggnadens interiörer svalt, eller göra ena sidan infrarödabsorberande med nanoteknik. Detta hjälper till att hålla insidan av byggnader varm eftersom det yttersta ytskiktet av glas kommer att absorbera den infraröda strålningen inuti byggnaden och stråla tillbaka den till insidan. - Etsning på glas - Tillämpad keramisk märkning (ACL) -Gravyr - Flampolering -Kemisk polering -Fläckning TILLVERKNING AV TEKNISK KERAMIK • DRYCKPRESSNING: Består av enaxlig komprimering av granulärt pulver inneslutet i en form • VARMPRESSNING: Liknar formpressning men med tillägg av temperatur för att förbättra förtätningen. Pulver eller komprimerad förform placeras i grafitform och enaxligt tryck appliceras medan formen hålls vid höga temperaturer såsom 2000 C. Temperaturer kan variera beroende på vilken typ av keramiskt pulver som bearbetas. För komplicerade former och geometrier kan annan efterföljande bearbetning som diamantslipning behövas. • ISOSTATISK PRESSNING: Granulerat pulver eller pressade presskroppar placeras i lufttäta behållare och sedan i ett slutet tryckkärl med vätska inuti. Därefter komprimeras de genom att öka tryckkärlets tryck. Vätskan inuti kärlet överför tryckkrafterna jämnt över hela ytan av den lufttäta behållaren. Materialet komprimeras således enhetligt och tar formen av sin flexibla behållare och dess inre profil och egenskaper. • HET ISOSTATISK PRESSNING: Liknar isostatisk pressning, men förutom trycksatt gasatmosfär sinter vi presskroppen vid hög temperatur. Varm isostatisk pressning resulterar i ytterligare förtätning och ökad hållfasthet. • SLIPSGJUTNING / AVLOPPSGJUTNING: Vi fyller formen med en suspension av mikrometerstora keramiska partiklar och bärarvätska. Denna blandning kallas "slip". Formen har porer och därför filtreras vätskan i blandningen ner i formen. Som ett resultat bildas en gjutning på formens inre ytor. Efter sintring kan delarna tas ur formen. • TEJPGJUTNING: Vi tillverkar keramiska tejper genom att gjuta keramiska slam på plana, rörliga bärytor. Uppslamningarna innehåller keramiska pulver blandade med andra kemikalier för bindning och transport. När lösningsmedlen avdunstar lämnas täta och flexibla ark av keramik kvar som kan skäras eller rullas efter önskemål. • EXTRUSIONSFORMNING: Som i andra extruderingsprocesser, passerar en mjuk blandning av keramiskt pulver med bindemedel och andra kemikalier genom ett munstycke för att få dess tvärsnittsform och skärs sedan i önskade längder. Processen utförs med kalla eller uppvärmda keramiska blandningar. • LÅGTRYCKSPRÖTJNING: Vi förbereder en blandning av keramiskt pulver med bindemedel och lösningsmedel och värmer upp den till en temperatur där den lätt kan pressas och pressas in i verktygshåligheten. När formningscykeln är klar skjuts delen ut och den bindande kemikalien bränns av. Med hjälp av formsprutning kan vi erhålla intrikata delar med höga volymer ekonomiskt. Hål som är en liten bråkdel av en millimeter på en 10 mm tjock vägg är möjliga, gängor är möjliga utan vidare bearbetning, toleranser så snäva som +/- 0,5 % är möjliga och ännu lägre när delar bearbetas , väggtjocklekar i storleksordningen 0,5 mm till en längd av 12,5 mm är möjliga samt väggtjocklekar på 6,5 mm till en längd av 150 mm. • GRÖN BEARBETNING: Med samma metallbearbetningsverktyg kan vi bearbeta pressade keramiska material medan de fortfarande är mjuka som krita. Toleranser på +/- 1 % är möjliga. För bättre toleranser använder vi diamantslipning. • SINTERING eller BRAND: Sintring möjliggör full förtätning. Betydande krympning sker på de gröna kompaktdelarna, men detta är inget stort problem eftersom vi tar hänsyn till dessa dimensionsförändringar när vi designar detaljen och verktygen. Pulverpartiklar binds samman och porositeten som induceras av komprimeringsprocessen avlägsnas i stor utsträckning. • DIAMANTSLIPNING: Världens hårdaste material "diamant" används för att slipa hårda material som keramik och precisionsdetaljer erhålls. Toleranser i mikrometerområdet och mycket släta ytor uppnås. På grund av dess kostnad överväger vi bara denna teknik när vi verkligen behöver den. • HERMETISKA ENHETER är sådana som praktiskt taget inte tillåter utbyte av ämnen, fasta ämnen, vätskor eller gaser mellan gränssnitten. Hermetisk tätning är lufttät. Till exempel är hermetiska elektroniska höljen de som håller det känsliga inre innehållet i en förpackad enhet oskadd av fukt, föroreningar eller gaser. Ingenting är 100% hermetiskt, men när vi talar om hermeticitet menar vi att det rent praktiskt finns att det finns hermeticitet i den utsträckningen att läckaget är så lågt att enheterna är säkra under normala miljöförhållanden under mycket långa tider. Våra hermetiska sammansättningar består av metall, glas och keramiska komponenter, metall-keramik, keramik-metall-keramik, metall-keramik-metall, metall till metall, metall-glas, metall-glas-metall, glas-metall-glas, glas- metall och glas till glas och alla andra kombinationer av metall-glas-keramisk bindning. Vi kan till exempel metallbelägga de keramiska komponenterna så att de kan bindas starkt till andra komponenter i monteringen och har utmärkt tätningsförmåga. Vi har kunskapen om att belägga optiska fibrer eller genomföringar med metall och löda eller hårdlöda dem till kapslingarna, så att inga gaser passerar eller läcker in i kapslingarna. Därför används de för tillverkning av elektroniska höljen för att kapsla in känsliga enheter och skydda dem från den yttre atmosfären. Förutom deras utmärkta tätningsegenskaper, andra egenskaper såsom värmeutvidgningskoefficient, deformationsmotstånd, icke-avgasande natur, mycket lång livslängd, icke-ledande natur, värmeisoleringsegenskaper, antistatisk natur...etc. gör glas och keramiska material till valet för vissa applikationer. Information om vår anläggning som producerar keramiska till metallbeslag, hermetisk tätning, vakuumgenomföringar, hög- och ultrahögvakuum och vätskekontrollkomponenter finns här:Hermetic Components Factory Broschyr CLICK Product Finder-Locator Service FÖREGÅENDE SIDA
- Wire & Spring Forming, Shaping, Welding, Assembly of Wires, Coil, CNC
Wire & Spring Forming, Shaping, Welding, Assembly of Wires, Coil Compression Extension Torsion Flat Springs, Custom Wires, Helical Springs at AGS-TECH Inc. Tråd- och fjäderformning Vi tillverkar skräddarsydda trådar, trådmontering, trådar formade till önskade 2D- och 3D-former, trådnät, nät, höljen, korg, staket, trådfjäder, platt fjäder; vridning, kompression, spänning, platta fjädrar med mera. Våra processer är tråd- och fjäderformning, tråddragning, formning, bockning, svetsning, hårdlödning, lödning, håltagning, smidning, borrning, fasning, slipning, gängning, beläggning, fourslide, glidformning, lindning, lindning, upprullning. Vi rekommenderar att du klickar här för att LADDA NED våra schematiska illustrationer av tråd- och fjäderformningsprocesser av AGS-TECH Inc. Den här nedladdningsbara filen med foton och skisser hjälper dig att bättre förstå informationen vi ger dig nedan. • TRÅDDRAGNING: Med hjälp av dragkrafter sträcker vi metallmaterialet och drar det genom en form för att minska diametern och öka dess längd. Ibland använder vi en serie stansar. Vi kan tillverka stansar för varje tjocklek av tråd. Med material med hög draghållfasthet drar vi mycket tunna trådar. Vi erbjuder både kall- och varmarbetade ledningar. • WIREFORMING: En rulle med mättråd böjs och formas till en användbar produkt. Vi har förmågan att forma trådar från alla mätare, inklusive tunna trådar såväl som tjocka trådar som de som används som fjädrar under bilchassier. Utrustning vi använder för trådformning är manuella och CNC trådformare, coiler, kraftpressar, fourslide, multi-slide. Våra processer är dragning, bockning, rätning, tillplattning, sträckning, skärning, rubbning, lödning & svetsning & lödning, montering, lindning, smidning (eller vingning), håltagning, trådgängning, borrning, fasning, slipning, beläggning och ytbehandlingar. Vår toppmoderna utrustning kan ställas in för att utveckla mycket komplexa konstruktioner av alla former och snäva toleranser. Vi erbjuder olika ändtyper liknande sfäriska, spetsiga eller avfasade ändar för dina trådar. De flesta av våra trådformningsprojekt har minimala till noll verktygskostnader. Handläggningstider för prov är i allmänhet dagar. Ändringar av design/konfiguration av trådformer kan göras mycket snabbt. • FJÄDERFORMNING: AGS-TECH tillverkar ett stort utbud av fjädrar inklusive: -Vrid / dubbel vridfjäder - Spänning / tryckfjäder -Konstant / Variabel fjäder -Spiral & spiralfjäder -Flat & Leaf Spring -Balans våren -Belleville tvättmaskin -Negatorfjäder -Spiralfjäder med progressiv hastighet -Vågvår -Volut Spring -Tapered Springs - Vårringar -Clock Springs -Clips Vi tillverkar fjädrar av en mängd olika material och kan vägleda dig efter din applikation. De vanligaste materialen är rostfritt stål, kromkisel, högkolhaltigt stål, oljehärdat lågkolhalt, kromvanadin, fosforbrons, titan, berylliumkopparlegering, högtemperaturkeramik. Vi använder olika tekniker vid tillverkning av fjädrar, inklusive CNC-lindning, kalllindning, varmlindning, härdning, efterbehandling. Andra tekniker som redan nämnts ovan under trådformning är också vanliga i vår fjädertillverkningsverksamhet. • FÄRGBEHANDLINGSTJÄNSTER för WIRES & FJÄDRAR: Vi kan färdigställa dina produkter på många sätt beroende på ditt val och behov. Några vanliga processer som vi erbjuder är: målning, pulverlackering, plätering, vinyldoppning, anodisering, stressavlastning, värmebehandling, kulpen, tumling, kromat, elektrolöst nickel, passivering, bakad emalj, plast , plasmarengöring. CLICK Product Finder-Locator Service FÖREGÅENDE SIDA
- Sheet Metal Forming Fabrication, Stamping, Punching, Deep Drawing, CNC
Sheet Metal Forming and Fabrication, Stamping, Punching, Bending, Progressive Die, Spot Welding, Deep Drawing, Metal Blanking and Slitting at AGS-TECH Inc. Stämplar och plåttillverkning Vi erbjuder plåtstansning, formning, formning, bockning, stansning, stansning, slitsning, perforering, hackning, naggning, rakning, pressbearbetning, tillverkning, djupdragning med enkelstans-/entaktsformar samt progressiva formar och spinning, gummiformning och hydroformning; plåtskärning med vattenstråle, plasma, laser, såg, flamma; plåtmontering med hjälp av svetsning, punktsvetsning; utbuktning och böjning av plåtrör; ytbehandling av plåt inklusive dopp- eller spraymålning, elektrostatisk pulverlackering, anodisering, plätering, sputtering och mer. Våra tjänster sträcker sig från snabb plåtprototyptillverkning till högvolymtillverkning. Vi rekommenderar att du klickar här för attLADDA NED våra schematiska illustrationer av plåttillverkning och stämplingsprocesser av AGS-TECH Inc. Detta hjälper dig att bättre förstå informationen vi ger dig nedan. • SKÄRNING AV PLÅT: Vi erbjuder AVSkärningar och AVSKÄRNINGAR. Cutoffs skär plåten över en bana i taget och det finns i princip inget materialslöseri, medan formen inte kan nästlas in exakt och därför går en viss mängd material till spillo. En av våra mest populära processer är PUNCHING, där en bit material rund eller annan form skärs ut ur plåt. Biten som skärs ut är avfall. En annan version av stansning är SLOTTING, där rektangulära eller långsträckta hål stansas. BLANKNING å andra sidan är samma process som stansning, med skillnaden att den bit som skärs ut är arbetet och behålls. FINE BLANKNING, en överlägsen version av blankning, skapar snitt med snäva toleranser och raka släta kanter och kräver inga sekundära operationer för perfektion av arbetsstycket. En annan process som vi ofta använder är SLITTING, som är en klippprocess där plåt skärs av två motsatta cirkulära blad i en rak eller krökt bana. Burköppnare är ett enkelt exempel på skärningsprocessen. En annan populär process för oss är PERFORERING, där många hål runda eller annan form stansas i plåt i ett visst mönster. Ett typiskt exempel på en perforerad produkt är metallfilter med många hål för vätskor. I NOTCHING, en annan plåtskärningsprocess, tar vi bort material från ett arbetsstycke, med början vid kanten eller någon annanstans och skär inåt tills önskad form erhålls. Det är en progressiv process där varje operation tar bort ytterligare en bit tills önskad kontur erhålls. För små produktionsserier använder vi ibland en relativt långsammare process som kallas NIBBLING som består av många snabba stansningar av överlappande hål för att göra ett större och mer komplext snitt. I PROGRESSIVE CUTTING använder vi en serie olika operationer för att få ett enda snitt eller en viss geometri. Äntligen hjälper RAKA en sekundär process oss att förbättra kanterna på snitt som redan har gjorts. Den används för att skära av spånen, grova kanter på plåtarbeten. • BOCKNING AV PLÅT: Förutom skärning är bockning en viktig process utan vilken vi inte skulle kunna producera de flesta produkter. Mestadels en kall arbetsoperation men ibland även när den är varm eller varm. Vi använder stansar och pressar för det mesta för denna operation. I PROGRESSIVE BENDING använder vi en serie olika stans- och stansoperationer för att erhålla en enda böj eller en viss geometri. AGS-TECH använder en mängd olika bockningsprocesser och gör valet beroende på arbetsstyckets material, dess storlek, tjocklek, önskad krökningsstorlek, radie, krökning och krökningsvinkel, bockningsläge, driftsekonomi, kvantiteter som ska tillverkas... etc. Vi använder V-BENDING där en V-formad stans tvingar in plåten i den V-formade formen och böjer den. Bra för både mycket spetsiga och trubbiga vinklar och däremellan, inklusive 90 grader. Med hjälp av torkskivor utför vi KANTBÖJNING. Vår utrustning gör att vi kan erhålla vinklar ännu större än 90 grader. Vid kantböjning är arbetsstycket inklämt mellan en tryckdyna och formen, området för bockning är placerad på formkanten och resten av arbetsstycket hålls över space som en fribärande balk. När stansen verkar på den fribärande delen böjs den över kanten på formen. FLÄNGNING är en kantböjningsprocess som resulterar i en 90 graders vinkel. Huvudmålen för operationen är eliminering av skarpa kanter och erhållande av geometriska ytor för att underlätta sammanfogningen av delar. BEADING, en annan vanlig kantböjningsprocess bildar en böjning över en dels kant. FÅLNING å andra sidan resulterar med en kant på arket som böjs helt över sig själv. I SÖMNING böjs kanterna på två delar över på varandra och sammanfogas. DUBBEL SÖMNING å andra sidan ger vattentäta och lufttäta plåtfogar. I likhet med kantböjning använder en process som kallas ROTARY BENDING en cylinder med önskad vinkel utskuren och fungerar som stansen. När kraften överförs till stansen stängs den med arbetsstycket. Cylinderns spår ger konsoldelen den önskade vinkeln. Spåret kan ha en vinkel mindre eller större än 90 grader. I AIR BENDING behöver vi inte den nedre dynan för att ha ett vinklat spår. Plåten bärs av två ytor på motsatta sidor och på ett visst avstånd. Stansen applicerar sedan en kraft på rätt plats och böjer arbetsstycket. KANALBÖJNING utförs med en kanalformad stans och stans, och U-BÖJNING uppnås med en U-formad stans. OFFSET BENDING ger förskjutningar på plåten. ROLL BENDING, en teknik som är bra för tjockt arbete och bockning av stora bitar av metallplåtar, använder tre rullar för att mata och böja plåtarna till önskade krökningar. Rullar är anordnade så att önskad böjning av arbetet erhålls. Avståndet och vinkeln mellan rullarna styrs för att uppnå önskat resultat. En rörlig rulle gör det möjligt att kontrollera krökningen. RÖRFORMNING är en annan populär böjningsoperation av plåt som involverar flera stansar. Rör erhålls efter flera åtgärder. KORRUGERING utförs också genom bockningsoperationer. I grund och botten är det den symmetriska böjningen med jämna mellanrum över ett helt stycke plåt. Olika former kan användas för korrugering. Korrugerad plåt är styvare och har bättre motståndskraft mot böjning och har därför tillämpningar inom byggbranschen. PLÅTVALSFORMNING, en kontinuerlig tillverkningsprocess används för att böja tvärsnitt av en viss geometri med hjälp av valsar och arbetet böjs i sekventiella steg, varvid den sista valsen slutför arbetet. I vissa fall används en enda rulle och i vissa fall en serie rullar. • KOMBINERADE SKÄRNINGS- OCH BOCKNINGSPROCESSER AV Plåt: Det här är processerna som skär och böjer samtidigt. I PIERCING skapas ett hål med en spetsig stans. När stansen vidgar hålet i plåten, böjs materialet samtidigt till en inre fläns för hålet. Den erhållna flänsen kan ha viktiga funktioner. LANCER-operationen å andra sidan skär och böjer arket för att skapa en upphöjd geometri. • UTBUCKNING OCH BÖJNING AV METALLRÖR: Vid BULGING trycksätts en del inre delar av ett ihåligt rör, vilket gör att röret buktar utåt. Eftersom röret är inuti en form styrs utbuktningens geometri av formen på formen. Vid STRETCH BENDING sträcks ett metallrör med krafter parallella med rörets axel och böjningskrafter för att dra röret över ett formblock. I DRAW BENDING klämmer vi fast röret nära dess ände till ett roterande formblock som böjer röret medan det roterar. Slutligen, vid KOMPRESSIONSBÖJNING hålls röret med kraft mot ett fast formblock, och en form böjer det över formblocket. • DJUPDRAGNING: I en av våra mest populära operationer används en stans, en matchande tärning och en blankhållare. Plåtämnet placeras över stansöppningen och stansen rör sig mot ämnet som hålls av ämneshållaren. När de väl kommer i kontakt, tvingar stansen plåten in i formhåligheten för att bilda produkten. Djupdragningsoperationen liknar skärning, men spelet mellan stansen och formen förhindrar att arket skärs. En annan faktor som säkerställer att arket är djupdraget och inte skärs är de rundade hörnen på formen och stansen som förhindrar klippning och skärning. För att uppnå en större magnitud av djupritning, används en REDRAWING-process där en efterföljande djupritning sker på en del som redan har genomgått en djupritningsprocess. I REVERSE RITNING vänds den djupdragna delen över och ritas i motsatt riktning. Djupritning kan ge oregelbundet formade föremål som kupolformade, avsmalnande eller trappade koppar, I PRÄGNING använder vi ett han- och honformpar för att imponera på plåten med en design eller ett manus. • SPINNING : En operation där ett plant eller förformat arbetsstycke hålls mellan en roterande dorn och stjärtstock och ett verktyg applicerar lokalt tryck på arbetet när det gradvis rör sig uppåt i dornen. Som ett resultat lindas arbetsstycket över dornen och tar sin form. Vi använder denna teknik som ett alternativ till djupdragning där mängden av en beställning är liten, delarna är stora (diametrar upp till 20 fot) och har unika kurvor. Även om priserna per styck generellt är högre, är installationskostnaderna för CNC-spinning låga jämfört med djupdragning. Tvärtom kräver djupdragning hög initial investering för installation, men kostnaderna per styck är låga när stora mängder delar produceras. En annan version av denna process är SHEAR SPINNING, där det också finns metallflöde i arbetsstycket. Metallflödet kommer att minska tjockleken på arbetsstycket när processen utförs. Ytterligare en annan relaterad process är TUBE SPINNING, som appliceras på cylindiriska delar. Även i denna process finns det metallflöde inuti arbetsstycket. Tjockleken minskas därmed och rörets längd ökas. Verktyget kan flyttas för att skapa funktioner på insidan eller utsidan av röret. • GUMMIFORMNING AV PLÅT: Gummi eller polyuretanmaterial läggs i en behållarform och arbetsstycket placeras på gummiytan. En stans påverkas sedan på arbetsstycket och tvingar in det i gummit. Eftersom trycket som genereras av gummit är lågt, är djupet på de tillverkade delarna begränsat. Eftersom verktygskostnaderna är låga är processen lämplig för produktion av små kvantiteter. • HYDROFORMING: I likhet med gummiformning pressas plåtarbeten i denna process med en stans till en trycksatt vätska inuti en kammare. Plåtverket är inklämt mellan stansen och ett gummimembran. Membranet omger arbetsstycket helt och hållet och trycket från vätskan tvingar det att bildas på stansen. Mycket djupa drag kan erhållas med den här tekniken ännu djupare än i djupdragningsprocessen. Vi tillverkar enkelstansformar såväl som progressiva matriser beroende på din del. Enslagspressformar är en kostnadseffektiv metod för att snabbt producera stora mängder enkla plåtdelar som brickor. Progressiva stansar eller djupdragningstekniken används för att tillverka mer komplexa geometrier. Beroende på ditt fall kan vattenskärning, laser eller plasmaskärning användas för att producera dina plåtdelar billigt, snabbt och exakt. Många leverantörer har ingen aning om dessa alternativa tekniker eller har inte det och därför går de igenom långa och dyra sätt att tillverka stansar och verktyg som bara slösar kundernas tid och pengar. Om du behöver specialbyggda plåtkomponenter som kapslingar, elektroniska höljen...etc så fort som inom några dagar, kontakta oss då för vår RAPID PLANPROTOTYP-tjänst. CLICK Product Finder-Locator Service FÖREGÅENDE MENY
- Forging and Powdered Metallurgy, Die Forging, Heading, Hot Forging
Forging and Powdered Metallurgy, Die Forging, Heading, Hot Forging, Impression Die, Near Net Shape, Swaging, Metal Hobbing, Riveting, Coining from AGS-TECH Inc. Metallsmide & pulvermetallurgi Den typ av metallsmidningsprocesser som vi erbjuder är varm och kall form, öppen form och stängd form, avtrycksform & blixtfri smide, cogging, fullering, kant- och precisionssmidning, nästan nätform, rubrik , smidning, rubbad smide, metallsmidning, press & roll & radiell & orbital & ring & isotermisk smide, myntning, nitning, metallkulsmide, metallhål, limning, smide med hög energihastighet. Våra POWDER METALLURGY och POWDER PROCESSING tekniker är pulverpressning och sintring, impregnering, infiltration, varm och kall isostatisk pressning, metallformsprutning, valskomprimering, pulvervalsning, pulverextrudering, lössintring, gnistsintring, varmpressning. Vi rekommenderar att du klickar här för att LADDA NED våra schematiska illustrationer av smidesprocesser av AGS-TECH Inc. LADDA NED våra schematiska illustrationer av pulvermetallurgiprocesser av AGS-TECH Inc. Dessa nedladdningsbara filer med foton och skisser hjälper dig att bättre förstå informationen vi ger dig nedan. Vid metallsmide appliceras tryckkrafter och materialet deformeras och önskad form erhålls. De vanligaste smidda materialen inom industrin är järn och stål, men många andra såsom aluminium, koppar, titan, magnesium är också mycket smidda. Smidda metalldelar har förbättrade kornstrukturer förutom tätade sprickor och slutna tomma utrymmen, så hållfastheten hos delar som erhålls genom denna process är högre. Smide producerar delar som är betydligt starkare för sin vikt än delar gjorda genom gjutning eller bearbetning. Eftersom smidda delar formas genom att metallen flyter till sin slutliga form, antar metallen en riktad kornstruktur som står för delarnas överlägsna styrka. Med andra ord, delar som erhålls genom smidesprocess visar bättre mekaniska egenskaper jämfört med enkla gjutna eller bearbetade delar. Vikten av metallsmide kan variera från små lätta delar till hundratusentals pund. Vi tillverkar smide främst för mekaniskt krävande applikationer där höga påfrestningar appliceras på delar som bildelar, växlar, arbetsredskap, handverktyg, turbinaxlar, motorcykelredskap. Eftersom verktygs- och installationskostnaderna är relativt höga rekommenderar vi denna tillverkningsprocess endast för högvolymproduktion och för låga volymer men högt värde kritiska komponenter såsom landningsställ för flyg. Förutom kostnaden för verktyg kan tillverkningstiden för stora kvantiteter smidda delar vara längre jämfört med vissa enkla bearbetade delar, men tekniken är avgörande för delar som kräver extraordinär styrka såsom bultar, muttrar, speciell applikation fästelement, bilar, gaffeltruckar, krandelar. • HET- och KALLMÖDSMIDNING: Varmsmidning, som namnet antyder, utförs vid höga temperaturer, duktiliteten är därför hög och hållfastheten hos materialet låg. Detta underlättar lätt deformation och smide. Tvärtom, kallformsmidning utförs vid lägre temperaturer och kräver högre krafter vilket resulterar i töjningshärdning, bättre ytfinish och noggrannhet hos de tillverkade delarna. • ÖPPEN FORM- och IMPRESSIONSMIDNING: Vid öppen stanssmidning hindrar stansarna inte materialet som komprimeras, medan hålrummen i stansarna begränsar materialflödet medan det smides till önskad form. UPSET FORGING eller även kallad UPSETTING, vilket faktiskt inte är samma sak utan en väldigt lik process, är en öppen stansprocess där arbetsstycket är inklämt mellan två plana stansar och en tryckkraft minskar dess höjd. När höjden är reduced ökar arbetsstyckets bredd. HEADING, en rubbad smidesprocess involverar cylindriskt material som rubbas vid sin ände och dess tvärsnitt ökas lokalt. I rubrik matas mälden genom formen, smids och skärs sedan till längd. Operationen är kapabel att snabbt producera stora mängder fästelement. Oftast är det en kallbearbetning eftersom den används för att tillverka spikändar, skruvändar, muttrar och bultar där materialet behöver förstärkas. En annan öppen formprocess är COGGING, där arbetsstycket smides i en serie steg där varje steg resulterar i komprimering av materialet och den efterföljande rörelsen av den öppna formen längs arbetsstyckets längd. Vid varje steg minskas tjockleken och längden ökas med en liten mängd. Processen liknar en nervös student som hela tiden biter i sin penna i små steg. En process som kallas FULLERING är en annan öppen formsmidemetod som vi ofta använder som ett tidigare steg för att fördela materialet i arbetsstycket innan andra metallsmidningsoperationer äger rum. Vi använder det när arbetsstycket kräver flera smide operationer. Under operationen deformeras formen med konvexa ytor och orsakar metallflöde ut till båda sidor. En liknande process som fyllning, EDGING å andra sidan involverar öppen form med konkava ytor för att deformera arbetsstycket. Kantning är också en förberedande process för efterföljande smidesoperationer gör att materialet flyter från båda sidor till ett område i mitten. IMPRESSION DIE FORGING eller CLOSED DIE FORGING som det också kallas använder en form/form som komprimerar materialet och begränsar dess flöde inom sig själv. Formen stängs och materialet tar formen av formen / formhåligheten. PRECISIONSSMID, en process som kräver speciell utrustning och form, producerar delar med ingen eller mycket liten blixt. Med andra ord kommer delarna att ha nästan slutliga dimensioner. I denna process förs en väl kontrollerad mängd material försiktigt in och placeras inuti formen. Vi använder denna metod för komplexa former med tunna sektioner, små toleranser och dragvinklar och när kvantiteterna är tillräckligt stora för att motivera form- och utrustningskostnaderna. • FLASHLOPP SMID: Arbetsstycket placeras i formen på ett sådant sätt att inget material kan rinna ut ur hålrummet för att bilda flash. Ingen oönskad blixttrimning behövs alltså. Det är en precisionssmideprocess och kräver därför noggrann kontroll av mängden material som används. • METALLSMIDNING eller RADIALSMIDNING: Ett arbetsstycke påverkas i omkretsled av form och smides. En dorn kan likaväl användas för att smida den inre arbetsstyckets geometri. I sänkningsoperationen får arbetsstycket typiskt flera slag per sekund. Typiska föremål som produceras genom smidning är spetsverktyg, koniska stänger, skruvmejslar. • METALLPIERCING: Vi använder denna operation ofta som en extra operation vid tillverkning av delar. Ett hål eller hålrum skapas med piercing på arbetsstyckets yta utan att bryta igenom det. Observera att piercing är annorlunda än borrning som resulterar i ett genomgående hål. • HOBBING : En stans med önskad geometri pressas in i arbetsstycket och skapar en hålighet med önskad form. Vi kallar denna punch en HOB. Operationen innebär höga tryck och utförs vid kyla. Som ett resultat av detta är materialet kallbearbetat och töjningshärdat. Därför är denna process mycket lämplig för tillverkning av formar, formar och kaviteter för andra tillverkningsprocesser. När hällen väl är tillverkad kan man enkelt tillverka många identiska hålrum utan att behöva bearbeta dem en efter en. • RULLSMIDDNING eller VALSFORMNING: Två motsatta rullar används för att forma metalldelen. Arbetsstycket matas in i rullarna, rullarna vänder sig och drar verket in i springan, verket matas sedan genom den räfflade delen av rullarna och tryckkrafterna ger materialet dess önskade form. Det är inte en valsningsprocess utan en smidesprocess, eftersom det är en diskret snarare än en kontinuerlig operation. Geometrin på rullarnas spår smider materialet till önskad form och geometri. Det utförs varmt. Eftersom den är en smidesprocess producerar den delar med enastående mekaniska egenskaper och därför använder vi den för tillverkning av bildelar som axlar som behöver ha extraordinär uthållighet i tuffa arbetsmiljöer. • ORBITAL SMID: Arbetsstycket placeras i en smidd hålighet och smides av en övre stans som rör sig i en omloppsbana när den roterar på en lutande axel. Vid varje varv fullbordar den övre dynan utövandet av tryckkrafter på hela arbetsstycket. Genom att upprepa dessa varv ett antal gånger utförs tillräcklig smide. Fördelarna med denna tillverkningsteknik är dess låga ljudnivå och lägre krafter som behövs. Med andra ord kan man med små krafter vrida en tung dyna runt en axel för att applicera stora tryck på en del av arbetsstycket som är i kontakt med dynan. Skiva eller koniska delar passar ibland bra för denna process. • RINGSMIDNING: Vi använder ofta för att tillverka sömlösa ringar. Stock skärs till på längden, rubbas och sticks sedan igenom hela vägen för att skapa ett centralt hål. Sedan sätts den på en dorn och en smide hamrar den uppifrån när ringen långsamt roteras tills önskade dimensioner erhålls. • NITNING: En vanlig process för att sammanfoga delar, börjar med en rak metallbit som sätts in i färdiga hål genom delarna. Därefter smides de två ändarna av metallstycket genom att klämma ihop fogen mellan en övre och nedre dyna. • MYNTNING: En annan populär process som utförs av mekanisk press, som utövar stora krafter över en kort sträcka. Namnet "mynta" kommer från de fina detaljerna som är smidda på ytorna av metallmynt. Det är mest en efterbehandlingsprocess för en produkt där fina detaljer erhålls på ytorna som ett resultat av den stora kraft som appliceras av formen som överför dessa detaljer till arbetsstycket. • METALLKULSMIDDE: Produkter som kullager kräver högkvalitativa exakt tillverkade metallkulor. I en teknik som kallas SKEW ROLLING, använder vi två motsatta rullar som kontinuerligt roterar när materialet kontinuerligt matas in i rullarna. I den ena änden av de två rullarna sprutas metallsfärer ut som produkt. En andra metod för smidning av metallkulor är att använda munstycken som klämmer ihop materialbeståndet mellan dem och tar formhålighetens sfäriska form. Ofta kräver kulor som produceras några ytterligare steg som ytbehandling och polering för att bli en högkvalitativ produkt. • ISOTHERMAL SMIDING / HETSMIDNING: En dyr process som utförs endast när nyttan/kostnadsvärdet är motiverat. En varmbearbetningsprocess där formen värms upp till ungefär samma temperatur som arbetsstycket. Eftersom både formen och arbetsstycket har ungefär samma temperatur, sker ingen kylning och metallens flödesegenskaper förbättras. Funktionen passar bra för superlegeringar och material med sämre smidbarhet och material vars mekaniska egenskaper är mycket känsliga för små temperaturgradienter och förändringar. • METALLSIMERING: Det är en kall efterbehandlingsprocess. Materialflödet är obegränsat i alla riktningar med undantag för den riktning i vilken kraften appliceras. Som ett resultat erhålls mycket god ytfinish och noggranna dimensioner. • SMIDA MED HÖG ENERGI: Tekniken involverar en övre form fäst vid armen på en kolv som snabbt trycks när en bränsle-luftblandning antänds av ett tändstift. Det liknar driften av kolvar i en bilmotor. Formen träffar arbetsstycket mycket snabbt och återgår sedan till sitt ursprungliga läge mycket snabbt tack vare mottrycket. Arbetet smides inom några millisekunder och därför finns det ingen tid för arbetet att svalna. Detta är användbart för svårsmidda delar som har mycket temperaturkänsliga mekaniska egenskaper. Med andra ord är processen så snabb att delen formas under konstant temperatur hela tiden och det kommer inte att finnas temperaturgradienter vid gränssnitten form/arbetsstycke. • I DIE FORGING slås metall mellan två matchande stålblock med speciella former i dem, så kallade formar. När metallen hamras mellan formarna antar den samma form som formerna i formen. När den når sin slutliga form tas den ut för att svalna. Denna process ger starka delar som har en exakt form, men kräver en större investering för de specialiserade formarna. Upprörd smide ökar diametern på ett metallstycke genom att det plattas till. Det används vanligtvis för att tillverka små delar, särskilt för att forma huvuden på fästelement som bultar och spikar. • PULVERMETALLUGI / PULVERBEHANDLING: Som namnet antyder, innebär det tillverkningsprocesser för att tillverka fasta delar av vissa geometrier och former av pulver. Om metallpulver används för detta ändamål är det pulvermetallurgins område och om icke-metallpulver används är det pulverbearbetning. Fasta delar tillverkas av pulver genom pressning och sintring. POWDERPRESSING används för att pressa puder till önskade former. Först är det primära materialet fysiskt pulveriserat, vilket delar upp det i många små enskilda partiklar. Pulverblandningen fylls i formen och en stans rör sig mot pulvret och pressar ihop det till önskad form. Mestadels utförs i rumstemperatur, med pulverpressning erhålls en fast del och den kallas grön kompakt. Bindemedel och smörjmedel används vanligtvis för att förbättra kompakteringsförmågan. Vi kan pulverpressforma med hydrauliska pressar med flera tusen ton kapacitet. Vi har också dubbelverkande pressar med motsatta topp- och bottenstansar samt flerverkande pressar för mycket komplexa detaljgeometrier. Enhetlighet som är en viktig utmaning för många pulvermetallurgi/pulverbearbetningsanläggningar är inget stort problem för AGS-TECH på grund av vår långa erfarenhet av specialtillverkning av sådana delar under många år. Även med tjockare delar där enhetlighet utgör en utmaning har vi lyckats. Om vi engagerar oss i ditt projekt, kommer vi att tillverka dina delar. Om vi ser några potentiella risker kommer vi att informera dig in advance. PULVERSINTERING, som är det andra steget, innebär att temperaturen höjs till en viss grad och att temperaturen hålls på den nivån under en viss tid så att pulverpartiklarna i den pressade delen kan binda samman. Detta resulterar i mycket starkare bindningar och förstärkning av arbetsstycket. Sintring sker nära pulvrets smälttemperatur. Under sintring kommer krympning att inträffa, materialstyrka, densitet, duktilitet, värmeledningsförmåga, elektrisk ledningsförmåga ökas. Vi har batch- och kontinuerliga ugnar för sintring. En av våra möjligheter är att justera porositetsnivån för de delar vi producerar. Vi kan till exempel tillverka metallfilter genom att hålla delarna porösa till viss del. Med en teknik som kallas IMPREGNERING fyller vi porerna i metallen med en vätska som olja. Vi tillverkar till exempel oljeimpregnerade lager som är självsmörjande. I INFILTRATIONsprocessen fyller vi en metalls porer med en annan metall med lägre smältpunkt än basmaterialet. Blandningen upphettas till en temperatur mellan smälttemperaturerna för de två metallerna. Som ett resultat kan vissa speciella egenskaper erhållas. Vi utför också ofta sekundära operationer såsom bearbetning och smide på pulvertillverkade delar när speciella egenskaper eller egenskaper behöver erhållas eller när delen kan tillverkas med mindre processsteg. ISOSTATISK PRESSNING: I denna process används vätsketryck för att komprimera delen. Metallpulver placeras i en form gjord av en förseglad flexibel behållare. Vid isostatisk pressning appliceras tryck runt om, i motsats till axiellt tryck som ses vid konventionell pressning. Fördelarna med isostatisk pressning är enhetlig densitet inom delen, speciellt för större eller tjockare delar, överlägsna egenskaper. Dess nackdel är långa cykeltider och relativt låg geometrisk noggrannhet. KALL ISOSTATISK PRESSNING utförs i rumstemperatur och den flexibla formen är gjord av gummi, PVC eller uretan eller liknande material. Vätska som används för trycksättning och kompaktering är olja eller vatten. Konventionell sintring av den gröna presskroppen följer detta. HET ISOSTATISK PRESSNING å andra sidan utförs vid höga temperaturer och formmaterialet är plåt eller keramik med tillräckligt hög smältpunkt som står emot temperaturerna. Tryckvätska är vanligtvis en inert gas. Pressnings- och sintringsoperationerna utförs i ett steg. Porositeten är nästan helt eliminerad, en uniform kornstruktur erhålls. Fördelen med varmisostatisk pressning är att den kan producera delar jämförbara med gjutning och smide kombinerat samtidigt som material som inte är lämpliga för gjutning och smide kan användas. Nackdelen med varm isostatisk pressning är dess höga cykeltid och därmed kostnaden. Den är lämplig för kritiska delar med låg volym. METALLSPRUTNING: Mycket lämplig process för att tillverka komplexa delar med tunna väggar och detaljerade geometrier. Passar bäst för mindre delar. Pulver och polymerbindemedel blandas, värms upp och injiceras i en form. Polymerbindemedlet täcker ytorna på pulverpartiklarna. Efter formningen avlägsnas bindemedlet antingen genom lågtemperaturvärmning eller upplöst med hjälp av ett lösningsmedel. RULLKOMPAKTERING / PULVERRULLNING: Pulver används för att producera kontinuerliga remsor eller ark. Pulver matas från en matare och komprimeras av två roterande rullar till ark eller remsor. Operationen utförs kallt. Arket bärs in i en sintringsugn. Sintringsprocessen kan upprepas en andra gång. PULVEREXTRUSION: Delar med stora längd-till-diameter-förhållanden tillverkas genom att en tunn plåtbehållare extruderas med pulver. LÖS SINTERING: Som namnet antyder är det en trycklös komprimerings- och sintringsmetod, lämplig för att producera mycket porösa delar som metallfilter. Pulver matas in i formhålan utan att komprimeras. LÖS SINTERING: Som namnet antyder är det en trycklös kompakterings- och sintringsmetod, lämplig för att producera mycket porösa delar som metallfilter. Pulver matas in i formhålan utan att komprimeras. GNISTSINTERING: Pulvret komprimeras i formen av två motstående stansar och en högeffekts elektrisk ström appliceras på stansen och passerar genom det komprimerade pulvret mellan dem. Den höga strömmen bränner bort ytfilmer från pulverpartiklarna och sinter dem med den värme som genereras. Processen är snabb eftersom värme inte appliceras utifrån utan istället genereras inifrån formen. VARMPRESSNING : Pulvren pressas och sintras i ett enda steg i en form som tål de höga temperaturerna. När formen komprimeras appliceras pulvervärmen på den. Goda noggrannheter och mekaniska egenskaper som uppnås med denna metod gör det till ett attraktivt alternativ. Även eldfasta metaller kan bearbetas genom att använda formmaterial som grafit. CLICK Product Finder-Locator Service FÖREGÅENDE MENY
- Plastic Rubber Metal Extrusions, Extrusion Dies, Aluminum Extruding
Plastic Rubber Metal Extrusions, Extrusion Dies, Aluminum Extruding, Pipe Tube Forming, Plastic Profiles, Metal Profiles Manufacturing, PVC at AGS-TECH Inc. Extruderingar, extruderade produkter, extrudat Vi använder processen EXTRUSION processen för att tillverka produkter med en fast tvärsnittsprofil såsom rör, rör och kylflänsar. Även om många material kan extruderas, är våra vanligaste extruderingar gjorda av metall, polymerer/plast, keramik erhållen med antingen kall, varm eller varm extruderingsmetod. Vi kallar de extruderade delarna extrudat eller extrudates om plural. Några specialiserade versioner av processen vi också utför är övermantling, samextrudering och sammansatt extrudering. Vi rekommenderar att du klickar här för att LADDA NED våra schematiska illustrationer av metallkeramiska och plastextruderade processer av AGS-TECH Inc. Detta hjälper dig att bättre förstå informationen vi ger dig nedan. I extrudering skjuts eller dras material som ska extruderas genom en form som har önskad tvärsnittsprofil. Processen kan användas för att tillverka komplexa tvärsnitt med utmärkt ytfinish och för att arbeta på sprött material. Man kan tillverka vilken längd av delar som helst med denna process. För att förenkla processtegen: 1.) I varma eller varma extruderingar värms materialet och laddas i en behållare i pressen. Materialet pressas och trycks ut ur formen. 2.) Producerat extrudat är sträckt för uträtning, värmebehandlat eller kallbearbetat för att förbättra dess egenskaper. Å andra sidan COLD EXTRUSION äger rum vid runt rumstemperatur och har fördelarna med mindre god oxidation, hög ytbeständighet och hög yta. WARM EXTRUSION utförs över rumstemperatur men under omkristallisationspunkten. Den erbjuder en kompromiss och balans för erforderliga krafter, duktilitet och materialegenskaper och är därför valet för vissa applikationer. HOT EXTRUSION sker över materialets omkristallisationstemperatur. På så sätt är det lättare att trycka materialet genom formen. Utrustningskostnaden är dock hög. Ju mer komplex en extruderad profil är, desto dyrare är formen (verktyg) och desto lägre är produktionshastigheten. Formens tvärsnitt såväl som tjocklekar har begränsningar som beror på materialet som ska extruderas. Skarpa hörn i extruderingsformar är alltid oönskade och bör undvikas om det inte är nödvändigt. Beroende på materialet som extruderas erbjuder vi: • METALLEXTRUSIONS : De vanligaste vi tillverkar är aluminium, mässing, zink, koppar, stål, titan, magnesium • PLASTEXTRUSION : Plast smälts och formas till en kontinuerlig profil. Våra vanliga material som bearbetas är polyeten, nylon, polystyren, polyvinylklorid, polypropen, ABS-plast, polykarbonat, akryl. Typiska produkter vi tillverkar inkluderar rör och rör, plastramar. I processen matas små plastpärlor/harts genom tyngdkraften från behållaren in i cylindern på extruderingsmaskinen. Ofta blandar vi även färgämnen eller andra tillsatser i behållaren för att ge produkten de specifikationer och egenskaper som krävs. Materialet som kommer in i den uppvärmda tunnan tvingas av den roterande skruven att lämna tunnan i änden och röra sig genom silpaketet för att avlägsna föroreningar i den smälta plasten. Efter att ha passerat silpaketet kommer plasten in i extruderingsformen. Formen ger den rörliga mjuka plasten dess profilform när den passerar igenom. Nu går extrudatet genom ett vattenbad för kylning. Andra tekniker som AGS-TECH Inc. har använt i många år är: • RÖR & RÖR EXTRUSION : Plaströr och rör bildas när plast extruderas genom en rund formningsform och kyls i ett vattenbad, skärs sedan till längden eller lindas/spolas. Klar eller färgad, randig, enkel eller dubbelvägg, flexibel eller styv, PE, PP, polyuretan, PVC, nylon, PC, silikon, vinyl eller annat, vi har allt. Vi har lagerförda rör samt möjligheten att producera enligt dina specifikationer. AGS-TECH tillverkar slangar enligt FDA, UL och LE krav för medicinska, elektriska och elektroniska, industriella och andra tillämpningar. • OVERJACKETING / OVER JACKETING EXTRUSION : Denna teknik applicerar ett yttre lager av plast på befintlig tråd eller kabel. Våra isoleringstrådar tillverkas med denna metod. • COEXTRUSION : Flera lager av material extruderas samtidigt. De flera skikten levereras av flera extruderare. De olika lagertjocklekarna kan justeras för att möta kundens specifikationer. Denna process gör det möjligt att använda flera polymerer som var och en har olika funktionalitet i produkten. Som ett resultat kan man optimera en rad egenskaper. • EXTRUSION AV SAMMANSÄTTNING: En eller flera polymerer blandas med tillsatser för att erhålla en plastblandning. Våra strängsprutmaskiner med dubbelskruv tillverkar blandningsextruderingar. Extruderingsformar är i allmänhet billiga jämfört med metallformar. Om du betalar mycket mer än några tusen dollar för en liten eller medelstor extruderingsform som extruderar aluminium, betalar du förmodligen för mycket. Vi är experter på att avgöra vilken teknik som är den mest kostnadseffektiva, snabbaste och mest lämpade för din applikation. Ibland kan extrudering och sedan bearbetning av en del spara mycket pengar. Innan du fattar ett bestämt beslut, fråga oss först vår åsikt. Vi har hjälpt många kunder att fatta rätt beslut. För vissa mycket använda metallprofiler kan du ladda ner våra broschyrer och kataloger genom att klicka på den färgade texten nedan. Om det är en hyllprodukt som uppfyller dina krav blir den mer ekonomisk. Ladda ner våra medicinska tub- och rörextruderingsmöjligheter Ladda ner våra extruderade kylflänsar • SEKUNDÄRA TILLVERKNINGS- OCH TILLVERKNINGSPROCESSER FÖR EXTRUSIONER : Bland mervärdesprocesser vi erbjuder för extruderade produkter är: - Anpassad rör- och rörböjning, formning och formning, tubavskärning, rörändformning, rörlindning, bearbetning och efterbehandling, hålborrning och håltagning och stansning, - Anpassade rör- och rörmontage, rörmontage, svetsning, lödning och lödning - Anpassad extruderingsböjning, formning och formning -Rengöring, avfettning, betning, passivering, polering, anodisering, plätering, målning, värmebehandling, glödgning och härdning, märkning, gravering och märkning, specialförpackning. CLICK Product Finder-Locator Service FÖREGÅENDE SIDA
- Casting and Machined Parts, CNC Manufacturing, Milling, Turning, Swiss
Casting and Machined Parts, CNC Manufacturing, Milling, Turning, Swiss Type Machining, Die Casting, Investment Casting, Lost Foam Cast Parts from AGS-TECH Inc. Gjutning och bearbetning Våra skräddarsydda gjutnings- och bearbetningstekniker är förbrukningsbara och ej förbrukningsbara gjutgods, järn- och icke-järngjutning, sand, form, centrifugal, kontinuerlig, keramisk form, investering, förlorat skum, nästan nät-form, permanent form (gravitationspressgjutning), gips gjutform (gipsgjutning) och skalgjutgods, bearbetade delar framställda genom fräsning och svarvning med konventionell såväl som CNC-utrustning, bearbetning av schweizisk typ för högkapacitet och billiga små precisionsdetaljer, skruvbearbetning för fästelement, icke-konventionell bearbetning. Tänk på att förutom metaller och metallegeringar bearbetar vi keramik-, glas- och plastkomponenter också i vissa fall när tillverkning av en form inte är tilltalande eller inte är alternativet. Bearbetning av polymermaterial kräver den specialiserade erfarenhet vi har på grund av den utmaning som plast och gummi erbjuder på grund av deras mjukhet, ostyvhet...etc. För bearbetning av keramik och glas, se vår sida om icke-konventionell tillverkning. AGS-TECH Inc. tillverkar och levererar både lätta och tunga gjutgods. Vi har levererat metallgjutgods och bearbetade delar till pannor, värmeväxlare, bilar, mikromotorer, vindturbiner, matförpackningsutrustning och mer. Vi rekommenderar att du klickar här för att LADDA NED våra schematiska illustrationer av bearbetnings- och gjutprocesser av AGS-TECH Inc. Detta hjälper dig att bättre förstå informationen vi ger dig nedan. Låt oss titta på några av de olika teknikerna vi erbjuder i detalj: • FÖRBRUKNINGSBAR FORMGJUTNING: Denna breda kategori hänvisar till metoder som involverar tillfälliga och icke-återanvändbara formar. Exempel är sand, gips, skal, investering (även kallat tappat vax) och gipsgjutning. • SANDGJUTNING: En process där sand används som formmaterial. En mycket gammal metod och fortfarande mycket populär till den grad att majoriteten av metallgjutgods tillverkas med denna teknik. Låg kostnad även vid låg kvantitet produktion. Lämplig för tillverkning av små och stora delar. Tekniken kan användas för att tillverka delar inom dagar eller veckor med mycket små investeringar. Den fuktiga sanden binds samman med lera, bindemedel eller specialoljor. Sand finns vanligtvis i formlådor och kavitets- och grindsystem skapas genom att komprimera sanden runt modeller. Processerna är: 1.) Placering av modellen i sand för att göra formen 2.) Inbyggnad av modell och sand i ett grindsystem 3.) Borttagning av modell 4.) Fyllning av formhålighet med smält metall 5.) Kylning av metallen 6.) Brytning av sandformen och avlägsnande av gjutgodset • GIPSFORMGJUTNING: I likhet med sandgjutning, och istället för sand, används gips som formmaterial. Korta produktionsledtider som sandgjutning och billigt. Bra måtttoleranser och ytfinish. Dess största nackdel är att den endast kan användas med metaller med låg smältpunkt som aluminium och zink. • SKALFORMGJUTNING: Liknar även sandgjutning. Mögelhålighet erhållen genom ett härdat skal av sand och härdplastbindemedel istället för en kolv fylld med sand som i sandgjutningsprocessen. Nästan vilken metall som helst som är lämplig att gjutas med sand kan gjutas genom skalgjutning. Processen kan sammanfattas som: 1.) Tillverkning av skalformen. Sand som används har mycket mindre kornstorlek jämfört med sand som används vid sandgjutning. Den fina sanden blandas med härdplast. Metallmönstret är belagt med ett avskiljningsmedel för att underlätta borttagning av skalet. Därefter upphettas metallmönstret och sandblandningen poreras eller blåses på det varma gjutmönstret. Ett tunt skal bildas på ytan av mönstret. Tjockleken på detta skal kan justeras genom att variera hur lång tid sandhartsblandningen är i kontakt med metallmönstret. Den lösa sanden avlägsnas sedan med det skaltäckta mönstret kvar. 2.) Därefter värms skalet och mönstret i en ugn så att skalet stelnar. Efter att härdningen är klar kastas skalet ut från mönstret med hjälp av stift inbyggda i mönstret. 3.) Två sådana skal sätts ihop genom limning eller fastklämning och utgör hela formen. Nu sätts skalformen in i en behållare där den stöds av sand eller metallkulor under gjutningsprocessen. 4.) Nu kan den varma metallen hällas i skalformen. Fördelar med skalgjutning är produkter med mycket god ytfinish, möjlighet att tillverka komplexa detaljer med hög dimensionsnoggrannhet, process lätt att automatisera, ekonomiskt för storvolymproduktion. Nackdelar är att formarna kräver god ventilation på grund av gaser som skapas när smält metall kommer i kontakt med bindemedelskemikalien, de härdplasterna och metallmönstren är dyra. På grund av kostnaden för metallmönster, kanske tekniken inte lämpar sig bra för produktioner med låga kvantiteter. • INVESTERINGSGJUTNING (även känd som LOST-WAX CASTING): Också en mycket gammal teknik och lämplig för tillverkning av kvalitetsdetaljer med hög noggrannhet, repeterbarhet, mångsidighet och integritet från många metaller, eldfasta material och speciella högpresterande legeringar. Små såväl som stora delar kan tillverkas. En dyr process jämfört med några av de andra metoderna, men stor fördel är möjligheten att producera detaljer med nästan nettoform, intrikata konturer och detaljer. Så kostnaden kompenseras något av elimineringen av omarbetning och bearbetning i vissa fall. Även om det kan finnas variationer, här är en sammanfattning av den allmänna investeringsgjutningsprocessen: 1.) Skapande av original mastermönster från vax eller plast. Varje gjutning behöver ett mönster eftersom dessa förstörs i processen. Form som mönster tillverkas av behövs också och för det mesta gjuts eller bearbetas formen. Eftersom formen inte behöver öppnas kan komplexa gjutningar uppnås, många vaxmönster kan kopplas ihop som grenarna på ett träd och hällas ihop, vilket möjliggör produktion av flera delar från en enda gjutning av metallen eller metallegeringen. 2.) Därefter doppas eller hälls mönstret över med en eldfast slurry som består av mycket finkornig kiseldioxid, vatten, bindemedel. Detta resulterar i ett keramiskt lager över mönstrets yta. Den eldfasta beläggningen på mönstret får torka och härda. Det här steget är varifrån namnet investeringsgjutning kommer: Eldfast slurry placeras över vaxmönstret. 3.) I detta steg vänds den härdade keramiska formen upp och ner och värms upp så att vaxet smälter och häller ut ur formen. Ett hålrum lämnas kvar för metallgjutningen. 4.) Efter att vaxet är ute värms den keramiska formen till ännu högre temperatur vilket resulterar i att formen förstärks. 5.) Metallgjutning hälls i den varma formen som fyller alla intrikata sektioner. 6.) Gjutningen får stelna 7.) Till sist bryts den keramiska formen och tillverkade delar skärs från trädet. Här är en länk till Investment Casting Plant Brochure • INDUNSTNINGSMÖNSTER GJUTNING: Processen använder ett mönster tillverkat av ett material som polystyrenskum som kommer att avdunsta när varm smält metall hälls i formen. Det finns två typer av denna process: LOST FOAM CASTING som använder obunden sand och FULL MOLD CASTING som använder bunden sand. Här är de allmänna processtegen: 1.) Tillverka mönstret av ett material som polystyren. När stora kvantiteter kommer att tillverkas formas mönstret. Om en del har en komplex form kan flera sektioner av sådant skummaterial behöva häftas samman för att bilda mönstret. Vi belägger ofta mönstret med en eldfast blandning för att skapa en bra ytfinish på gjutgodset. 2.) Mönstret läggs sedan i formsand. 3.) Den smälta metallen hälls i formen, vilket avdunstar skummönstret, dvs polystyren i de flesta fall när det rinner genom formhålan. 4.) Den smälta metallen lämnas i sandformen för att härda. 5.) Efter att det har härdat tar vi bort gjutgodset. I vissa fall kräver produkten vi tillverkar en kärna i mönstret. Vid evaporativ gjutning finns det inget behov av att placera och säkra en kärna i formhåligheten. Tekniken lämpar sig för tillverkning av mycket komplexa geometrier, den kan enkelt automatiseras för högvolymproduktion och det finns inga skiljelinjer i den gjutna delen. Den grundläggande processen är enkel och ekonomisk att genomföra. För produktion av stora volymer, eftersom en form eller form behövs för att framställa mönstren av polystyren, kan detta bli något kostsamt. • ICKE-EXPANDERBAR FORMGJUTNING: Denna breda kategori avser metoder där formen inte behöver reformeras efter varje produktionscykel. Exempel är permanent-, form-, kontinuerlig och centrifugalgjutning. Repeterbarhet erhålls och delar kan karakteriseras som NEAR NET SHAPE. • PERMANENT FORMGJUTNING: Återanvändbara formar gjorda av metall används för flera gjutningar. En permanent form kan i allmänhet användas i tiotusentals gånger innan den slits ut. Tyngdkraft, gastryck eller vakuum används vanligtvis för att fylla formen. Formar (även kallade formar) är vanligtvis gjorda av järn, stål, keramik eller andra metaller. Den allmänna processen är: 1.) Bearbeta och skapa formen. Det är vanligt att man bearbetar formen av två metallblock som passar ihop och kan öppnas och stängas. Både delarnas egenskaper såväl som grindsystemet bearbetas vanligtvis i gjutformen. 2.) De inre formytorna är belagda med en slurry som innehåller eldfasta material. Detta hjälper till att kontrollera värmeflödet och fungerar som ett smörjmedel för att enkelt ta bort den gjutna delen. 3.) Därefter stängs de permanenta formhalvorna och formen värms upp. 4.) Smält metall hälls i formen och låt stå stilla för stelning. 5.) Innan mycket kylning inträffar tar vi bort delen från den permanenta formen med hjälp av ejektorer när formhalvorna öppnas. Vi använder ofta permanent formgjutning för metaller med låg smältpunkt som zink och aluminium. För stålgjutgods använder vi grafit som formmaterial. Vi får ibland komplexa geometrier med hjälp av kärnor i permanenta formar. Fördelar med denna teknik är gjutgods med goda mekaniska egenskaper erhållna genom snabb avkylning, enhetlighet i egenskaper, god noggrannhet och ytfinish, låga kasseringshastigheter, möjlighet att automatisera processen och producera höga volymer ekonomiskt. Nackdelar är höga initiala installationskostnader som gör den olämplig för lågvolymoperationer och begränsningar av storleken på de tillverkade delarna. • FORMGJUTNING: En form bearbetas och smält metall trycks under högt tryck in i formhåligheter. Både icke-järn- och järnmetallgjutgods är möjliga. Processen lämpar sig för stora kvantitetsproduktioner av små till medelstora detaljer med detaljer, extremt tunna väggar, dimensionell konsistens och god ytfinish. AGS-TECH Inc. kan tillverka väggtjocklekar så små som 0,5 mm med denna teknik. Liksom vid permanent formgjutning behöver formen bestå av två halvor som kan öppnas och stängas för borttagning av tillverkad del. En pressgjutform kan ha flera hålrum för att möjliggöra produktion av flera gjutgods med varje cykel. Pressgjutningsformar är mycket tunga och mycket större än de delar de tillverkar, därför också dyra. Vi reparerar och byter ut slitna matriser utan kostnad för våra kunder så länge de beställer om sina delar från oss. Våra matriser har lång livslängd inom flera hundra tusen cykler. Här är de grundläggande förenklade processtegen: 1.) Tillverkning av formen i allmänhet av stål 2.) Form installerad på pressgjutningsmaskin 3.) Kolven tvingar smält metall att flöda i formhåligheterna och fyller ut de intrikata detaljerna och tunna väggarna 4.) Efter att formen har fyllts med den smälta metallen, låter man gjutgodset härda under tryck 5.) Formen öppnas och gjutgodset tas bort med hjälp av utkastarstift. 6.) Nu smörjs den tomma dynan igen och kläms fast för nästa cykel. Vid pressgjutning använder vi ofta insatsgjutning där vi lägger in ytterligare en del i formen och gjuter metallen runt den. Efter stelning blir dessa delar en del av den gjutna produkten. Fördelar med pressgjutning är goda mekaniska egenskaper hos delarna, möjlighet till intrikata funktioner, fina detaljer och bra ytfinish, höga produktionshastigheter, enkel automatisering. Nackdelar är: Inte särskilt lämplig för låg volym på grund av höga stans- och utrustningskostnader, begränsningar i form som kan gjutas, små runda märken på gjutna delar till följd av kontakt med ejektorstift, tunna metallblixtar som pressats ut vid avskiljningslinjen, behov för ventiler längs skiljelinjen mellan formen, nödvändigheten att hålla formtemperaturerna låga med hjälp av vattencirkulation. • CENTRIFUGALTJUTNING: Smält metall hälls i mitten av den roterande formen vid rotationsaxeln. Centrifugalkrafter kastar metallen mot periferin och den låter stelna när formen fortsätter att rotera. Både horisontella och vertikala axelrotationer kan användas. Delar med runda inre ytor samt andra icke-runda former kan gjutas. Processen kan sammanfattas som: 1.) Smält metall hälls i centrifugalformen. Metallen tvingas sedan till ytterväggarna på grund av att formen snurrar. 2.) När formen roterar härdar metallgjutgodset Centrifugalgjutning är en lämplig teknik för produktion av ihåliga cylindiriska delar som rör, inget behov av inlopp, stigare och grindelement, bra ytfinish och detaljerade egenskaper, inga krympningsproblem, möjlighet att producera långa rör med mycket stora diametrar, hög produktionskapacitet . • KONTINUERLIG GJUTNING ( STRANDGJUTNING ): Används för att gjuta en kontinuerlig längd av metall. I grund och botten gjuts den smälta metallen till en tvådimensionell profil av formen men dess längd är obestämd. Ny smält metall matas ständigt in i formen när gjutgodset färdas nedåt och dess längd ökar med tiden. Metaller som koppar, stål, aluminium gjuts till långa strängar med kontinuerlig gjutning. Processen kan ha olika konfigurationer men den vanliga kan förenklas som: 1.) Smält metall hälls i en behållare belägen högt ovanför formen vid väl beräknade mängder och flödeshastigheter och strömmar genom den vattenkylda formen. Metallgjutgodset som hälls i formen stelnar till en startstång placerad i botten av formen. Denna startstång ger rullarna något att ta tag i från början. 2.) Den långa metallsträngen bärs av rullar med konstant hastighet. Rullarna ändrar också riktningen för flödet av metallsträng från vertikal till horisontell. 3.) Efter att stränggjutningen har tillryggalagt en viss horisontell sträcka, kapar en brännare eller såg som rör sig med gjutgodset snabbt till önskade längder. Stränggjutningsprocessen kan integreras med ROLLING PROCESS, där den kontinuerligt gjutna metallen kan matas direkt in i ett valsverk för att producera I-Beams, T-Beams...etc. Stränggjutning ger enhetliga egenskaper genom hela produkten, den har en hög stelningshastighet, minskar kostnaderna på grund av mycket låga materialförluster, erbjuder en process där lastning av metall, gjutning, stelning, skärning och gjutborttagning allt sker i en kontinuerlig drift och vilket resulterar i hög produktivitet och hög kvalitet. En viktig faktor är dock den höga initiala investeringen, installationskostnaderna och utrymmeskraven. • BEARBETNINGSTJÄNSTER: Vi erbjuder tre-, fyra- och femaxlig bearbetning. Den typ av bearbetningsprocesser vi använder är VARVNING, FÄSNING, BORRNING, BORRNING, BRUCKNING, HYVNING, SÅGNING, SLIPPNING, SLIPNING, POLERNING och ICKE-TRADITIONELL BEARBETNING, som vidareutvecklas under en annan meny på vår hemsida. För större delen av vår tillverkning använder vi CNC-maskiner. Men för vissa operationer passar konventionella tekniker bättre och därför förlitar vi oss också på dem. Våra bearbetningsförmåga når högsta möjliga nivå och några mest krävande delar tillverkas i en AS9100-certifierad fabrik. Jetmotorblad kräver mycket specialiserad tillverkningserfarenhet och rätt utrustning. Flygindustrin har mycket strikta standarder. Vissa komponenter med komplexa geometriska strukturer tillverkas enklast med femaxlig bearbetning, som bara finns i vissa bearbetningsanläggningar inklusive vår. Vår flygcertifierade anläggning har den nödvändiga erfarenheten av att uppfylla omfattande dokumentationskrav från flygindustrin. Vid SVVARVNING roteras ett arbetsstycke och förflyttas mot ett skärverktyg. För denna process används en maskin som kallas svarv. I FRÄSNING har en maskin som kallas fräsmaskin ett roterande verktyg för att få skäreggar att anligga mot ett arbetsstycke. BORRNING involverar en roterande fräs med skäreggar som producerar hål vid kontakt med arbetsstycket. Borrpressar, svarvar eller kvarnar används vanligtvis. I BRING-operationer flyttas ett verktyg med en enda böjd spetsig spets in i ett grovt hål i ett snurrande arbetsstycke för att förstora hålet något och förbättra noggrannheten. Den används för fina efterbehandlingsändamål. BRUCKNING involverar ett tandat verktyg för att ta bort material från ett arbetsstycke i en passage av broschen (tandat verktyg). Vid linjär broschning löper broschen linjärt mot en yta av arbetsstycket för att åstadkomma skärningen, medan vid roterande broschning roteras broschen och pressas in i arbetsstycket för att skära en symmetrisk axelform. SWISS TYPE MACHINING är en av våra värdefulla tekniker som vi använder för högvolymtillverkning av små högprecisionsdelar. Med hjälp av schweizisk svarv svarvar vi små, komplexa precisionsdetaljer billigt. Till skillnad från konventionella svarvar där arbetsstycket hålls stillastående och verktyg i rörelse, i svarvcentra av schweizisk typ, tillåts arbetsstycket att röra sig i Z-axeln och verktyget är stationärt. Vid bearbetning av schweizisk typ hålls stångbeståndet i maskinen och förs fram genom en styrbussning i z-axeln, vilket endast exponerar den del som ska bearbetas. På så sätt säkerställs ett tätt grepp och noggrannheten är mycket hög. Tillgängligheten av spänningsförande verktyg ger möjlighet att fräsa och borra när materialet matas fram från styrbussningen. Y-axeln hos utrustningen av schweizisk typ ger full fräsningskapacitet och sparar mycket tid vid tillverkning. Dessutom har våra maskiner borrar och borrverktyg som arbetar på delen när den hålls i underspindeln. Vår bearbetningsförmåga av schweizisk typ ger oss en helautomatisk komplett bearbetningsmöjlighet i en enda operation. Maskinbearbetning är ett av de största segmenten inom AGS-TECH Inc.s verksamhet. Vi använder den antingen som en primär operation eller en sekundär operation efter gjutning eller extrudering av en del så att alla ritningsspecifikationer uppfylls. • YTBEHANDLINGSTJÄNSTER: Vi erbjuder ett brett utbud av ytbehandlingar och ytbehandlingar såsom ytkonditionering för att förbättra vidhäftningen, avsättning av tunt oxidskikt för att förbättra vidhäftningen av beläggningen, sandblästring, kemisk film, anodisering, nitrering, pulverlackering, spraybeläggning , olika avancerade metalliserings- och beläggningstekniker inklusive sputtering, elektronstråle, förångning, plätering, hårda beläggningar som diamantliknande kol (DLC) eller titanbeläggning för borr- och skärverktyg. • PRODUKTMÄRKNING & ETIKETTERINGSTJÄNSTER: Många av våra kunder kräver märkning och märkning, lasermärkning, gravering på metalldelar. Om du har något sådant behov, låt oss diskutera vilket alternativ som är bäst för dig. Här är några av de vanligaste metallgjutna produkterna. Eftersom dessa är från hyllan kan du spara på mögelkostnader om någon av dessa passar dina krav: KLICKA HÄR FÖR ATT LADDA NED våra 11-serier pressgjutna aluminiumlådor från AGS-Electronics CLICK Product Finder-Locator Service FÖREGÅENDE SIDA
- Custom Manufactured Parts, Assemblies, Plastic Mold, Casting,Machining
Custom Manufactured Parts, Assemblies, Plastic Mold, Rubber Molding, Metal Casting, CNC Machining, Turning, Milling, Electrical Electronic Optical Assembly PCBA Specialtillverkade delar & sammansättningar & produkter Läs mer Plast & gummi formar och gjutning Läs mer Gjutning och bearbetning Läs mer Extruderingar, extruderade produkter Läs mer Stämplar och plåttillverkning Läs mer Metallsmide & pulvermetallurgi Läs mer Tråd- och fjäderformning Läs mer Formning och formning av glas och keramik Läs mer Additiv och snabb tillverkning Läs mer Tillverkning av kompositer och kompositmaterial Läs mer Fogning & Montering & Fästprocesser Vi producerar delar och sammansättningar åt dig och erbjuder följande tillverkningsprocesser: • Plast- och gummiformar och gjutna delar. Formsprutning, termoformning, härdplastgjutning, vakuumformning, formblåsning, rotationsformning, gjutformning, insatsgjutning och andra. • Profiler av plast, gummi och metall • Järnhaltiga och icke-järnhaltiga gjutgods och bearbetade delar framställda med fräs- och svarvteknik, bearbetning av schweizisk typ. • Pulvermetallurgiska delar • Metall- och icke-metallstansningar, plåtformning, svetsade plåtenheter • Kall och varm smide • Trådar, svetsade trådar, trådformning • Olika typer av fjädrar, fjäderformning • Växeltillverkning, växellåda, koppling, snäck, hastighetsreducerare, cylinder, transmissionsremmar, transmissionskedjor, transmissionskomponenter • Anpassat härdat och skottsäkert glas som överensstämmer med NATO och militära standarder • Kulor, lager, remskivor och remskivor • Ventiler och pneumatiska komponenter som O-ring, bricka och tätningar • Glas och keramiska delar och sammansättningar, vakuumsäkra och hermetiska komponenter, metall-keramik och keramik-keramik limning. • Olika typer av mekaniska, optomekaniska, elektromekaniska, optoelektroniska sammansättningar. • Metall-gummi, metall-plast limning • Rör och rör, rörformning, bockning och specialtillverkning av rör, bälgtillverkning. • Glasfibertillverkning • Svetsning med olika tekniker såsom punktsvetsning, lasersvetsning, MIG, TIG. Ultraljudssvetsning för plastdelar. • Stort utbud av ytbehandlingar och ytfinishar såsom ytkonditionering för att förbättra vidhäftningen, avsättning av tunt oxidskikt för att förbättra vidhäftning av beläggning, sandblästring, kemisk film, anodisering, nitrering, pulverlackering, spraybeläggning, olika avancerade metalliserings- och beläggningstekniker inklusive sputtering, elektronstråle, förångning, plätering, hårda beläggningar som diamantliknande kol (DLC) eller titan för skärande och borrverktyg. • Märkning och märkning, lasermärkning på metalldelar, tryck på plast- och gummidelar Ladda ner broschyr för vanliga termer för maskinteknik som används av designers och ingenjörer Vi bygger produkter enligt dina specifika specifikationer och krav. För att kunna erbjuda dig den bästa kvaliteten, leveransen och priserna tillverkar vi produkter globalt i Kina, Indien, Taiwan, Filippinerna, Sydkorea, Malaysia, Sri Lanka, Turkiet, USA, Kanada, Tyskland, Storbritannien och Japan. Detta gör oss mycket starkare och globalt mer konkurrenskraftiga än någon annan custom manufacturer. Våra produkter är tillverkade i ISO9001:2000, QS9000, ISO14001, TS16949 certifierade miljöer och har CE, UL-märkning och uppfyller andra industristandarder. När vi väl är utsedda för ditt projekt kan vi ta hand om hela tillverkningen, monteringen, provningen, kvalificeringen, frakten & tullen som du önskar. Om du föredrar det kan vi lagra dina delar, sätta ihop skräddarsydda kit, skriva ut och märka ditt företagsnamn och varumärke och skicka tillbaka till dina kunder. Med andra ord kan vi också vara ditt lager- och distributionscenter om så önskas. Eftersom våra lager ligger nära större hamnar, ger det oss logistiska fördelar. Till exempel, när dina produkter anländer till en större hamn i USA kan vi transportera den direkt till ett närliggande lager där vi kan lagra, montera, göra kit, märka om, skriva ut, paketera enligt ditt val och släppa skicka till dina kunder. Vi levererar inte bara produkter. Vårt företag arbetar med skräddarsydda kontrakt där vi kommer till din plats, utvärderar ditt projekt på plats och utvecklar ett projektförslag skräddarsytt för dig. Vi skickar sedan vårt erfarna team för att genomföra projektet. Mer information om vårt ingenjörsarbete finns på http://www.ags-engineering.com -Vi tar såväl små projekt som stora projekt i industriell skala. Som ett första steg kan vi koppla dig antingen via telefon, telefonkonferens eller MSN-meddelande till våra expertteammedlemmar, så att du kan kommunicera direkt med en expert, ställa frågor och diskutera ditt projekt. Ring oss så kommer vi vid behov och besöker dig. FÖREGÅENDE SIDA