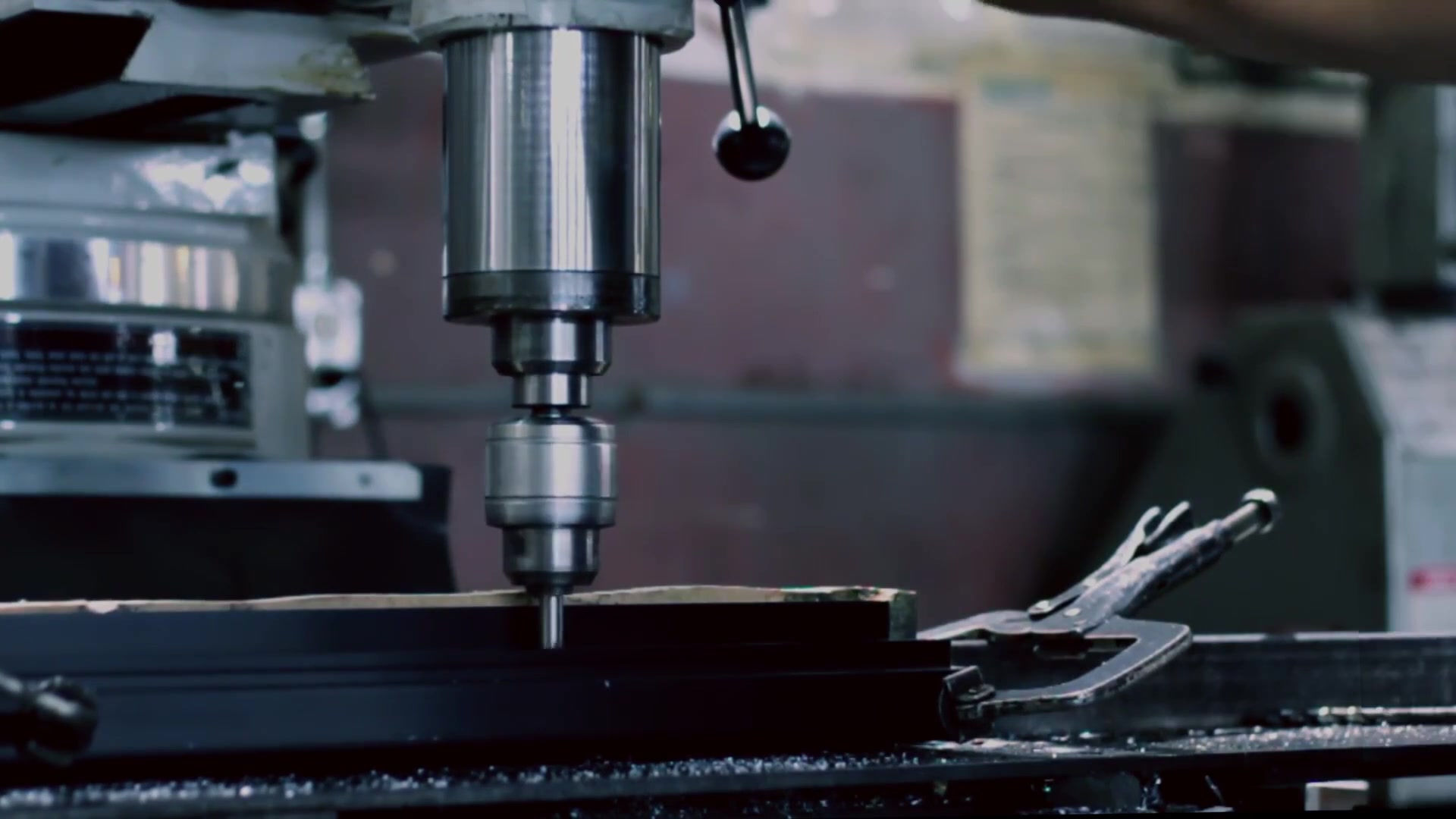
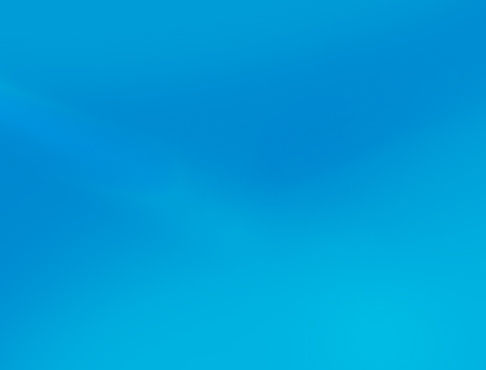
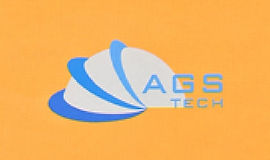
Global Custom Manufacturer, Integrator, Consolidator, Outsourcing Partner för ett brett utbud av produkter och tjänster.
Vi är din enda källa för tillverkning, tillverkning, ingenjörskonst, konsolidering, integration, outsourcing av specialtillverkade och off-shelfprodukter och tjänster.
Välj ditt språk
-
Custom Manufacturing
-
Inhemsk och global kontraktstillverkning
-
Outsourcing av tillverkning
-
Inhemsk och global upphandling
-
Consolidation
-
Engineering Integration
-
Ingenjörstjänster
Search Results
164 resultat hittades med en tom sökning
- Optical Coatings, Filter, Waveplates, Lenses, Prism, Mirrors, Etalons
Optical Coatings - Filter - Waveplates - Lenses - Prism - Mirrors - Beamsplitters - Windows - Optical Flat - Etalons Optiska beläggningar och filtertillverkning Vi erbjuder både hylltillverkade och specialtillverkade: • Optiska beläggningar och filter, vågplattor, linser, prismor, speglar, stråldelare, fönster, optiska plattor, etaloner, polarisatorer...etc. • Olika optiska beläggningar på dina föredragna substrat, inklusive antireflekterande, specialdesignade våglängdsspecifika transmissiva, reflekterande. Våra optiska beläggningar tillverkas med jonstråleförstoftningsteknik och andra lämpliga tekniker för att erhålla ljusa, hållbara, spektralt specifikationsmatchande filter och beläggningar. Om du föredrar det kan vi välja det mest lämpliga optiska substratmaterialet för din applikation. Berätta helt enkelt för oss om din applikation och våglängd, optisk effektnivå och andra nyckelparametrar så kommer vi att arbeta med dig för att utveckla och tillverka din produkt. Vissa optiska beläggningar, filter och komponenter har mognat under åren och blivit handelsvara. Vi tillverkar dessa i lågkostnadsländer i Sydostasien. Å andra sidan har vissa optiska beläggningar och komponenter snäva spektrala och geometriska krav, som vi tillverkar i USA med hjälp av vår design- och processkunskap och toppmodern utrustning. Betala inte för mycket i onödan för optiska beläggningar, filter och komponenter. Kontakta oss för att guida dig och få ut mesta möjliga för pengarna. Broschyr för optiska komponenter (inkluderar beläggningar, filter, linser, prismor...etc) CLICK Product Finder-Locator Service FÖREGÅENDE SIDA
- Functional Decorative Coatings - Thin Film - Thick Films - AR Coating
Functional & Decorative Coatings, Thin Film, Thick Films, Antireflective and Reflective Mirror Coating - AGS-TECH Inc. Funktionella beläggningar / Dekorativa beläggningar / Tunnfilm / Tjockfilm A COATING är en beläggning som appliceras på ytan av ett föremål. Coatings can be in the form of THIN FILM (less than 1 micron thick) or THICK FILM ( över 1 mikron tjock). Baserat på syftet med att applicera beläggningen kan vi erbjuda you DECORATIVE COATINGS and/eller_cc74cbb.FunC.FunC.FunC.Func.5cf58c Ibland applicerar vi funktionella beläggningar för att förändra underlagets ytegenskaper, såsom vidhäftning, vätbarhet, korrosionsbeständighet eller slitstyrka. I vissa andra fall, såsom vid tillverkning av halvledarenheter, applicerar vi de funktionella beläggningarna för att lägga till en helt ny egenskap som magnetisering eller elektrisk ledningsförmåga som blir en väsentlig del av den färdiga produkten. Våra mest populära FUNCTIONAL COATINGS are: Självhäftande beläggningar: Exempel är tejp, påstrykningstyg. Andra funktionella limbeläggningar appliceras för att ändra vidhäftningsegenskaperna, såsom non-stick PTFE-belagda kokkärl, primers som uppmuntrar efterföljande beläggningar att fästa bra. Tribologiska beläggningar: Dessa funktionella beläggningar relaterar till principerna för friktion, smörjning och slitage. Varje produkt där ett material glider eller gnuggar över ett annat påverkas av komplexa tribologiska interaktioner. Produkter som höftimplantat och andra konstgjorda proteser smörjs på vissa sätt medan andra produkter är osmorda som i högtemperaturglidkomponenter där konventionella smörjmedel inte kan användas. Bildandet av kompakterade oxidskikt har visat sig skydda mot slitage av sådana glidande mekaniska delar. Tribologiska funktionella beläggningar har enorma fördelar inom industrin, minimerar slitaget på maskinelement, minimerar slitage och toleransavvikelser i tillverkningsverktyg som formar och formar, minimerar effektbehov och gör maskiner och utrustning mer energieffektiva. Optiska beläggningar: Exempel är antireflekterande (AR) beläggningar, reflekterande beläggningar för speglar, UV-absorberande beläggningar för att skydda ögonen eller för att öka livslängden på substratet, toning som används i viss färgad belysning, tonade glas och solglasögon. Catalytic Coatings som appliceras på självrengörande glas. Light-Sensitive Coatings används för att göra produkter som fotografiska filmer Skyddsbeläggningar: Färger kan anses skydda produkterna förutom att vara dekorativa i syfte. Hårda anti-repbeläggningar på plast och andra material är en av våra mest använda funktionsbeläggningar för att minska repor, förbättra slitstyrkan, …etc. Anti-korrosionsbeläggningar som plätering är också mycket populära. Andra skyddande funktionella beläggningar sätts på vattentätt tyg och papper, antimikrobiella ytbeläggningar på kirurgiska verktyg och implantat. Hydrofila/hydrofobiska beläggningar: Vätande (hydrofila) och ovätande (hydrofobiska) funktionella tunna och tjocka filmer är viktiga i applikationer där vattenabsorption antingen är önskvärd eller oönskad. Med hjälp av avancerad teknik kan vi ändra dina produktytor, för att göra dem antingen lättvätbara eller ovätbara. Typiska applikationer är i textilier, förband, läderstövlar, farmaceutiska eller kirurgiska produkter. Hydrofil natur hänvisar till en fysisk egenskap hos en molekyl som övergående kan binda till vatten (H2O) genom vätebindning. Detta är termodynamiskt gynnsamt och gör dessa molekyler lösliga inte bara i vatten utan även i andra polära lösningsmedel. Hydrofila och hydrofoba molekyler är också kända som polära molekyler respektive opolära molekyler. Magnetiska beläggningar: Dessa funktionella beläggningar lägger till magnetiska egenskaper som är fallet för magnetiska disketter, kassetter, magnetremsor, magnetoptisk lagring, induktiva inspelningsmedia, magnetoresistsensorer och tunnfilmshuvuden på produkter. Magnetiska tunna filmer är ark av magnetiskt material med tjocklekar på några mikrometer eller mindre, som främst används inom elektronikindustrin. Magnetiska tunna filmer kan vara enkristallina, polykristallina, amorfa eller flerskiktiga funktionella beläggningar i arrangemanget av deras atomer. Både ferro- och ferrimagnetiska filmer används. De ferromagnetiska funktionella beläggningarna är vanligtvis övergångsmetallbaserade legeringar. Till exempel är permalloy en nickel-järnlegering. De ferrimagnetiska funktionella beläggningarna, såsom granater eller de amorfa filmerna, innehåller övergångsmetaller såsom järn eller kobolt och sällsynta jordartsmetaller och de ferrimagnetiska egenskaperna är fördelaktiga i magnetoptiska tillämpningar där ett lågt totalt magnetiskt moment kan uppnås utan en betydande förändring av Curie-temperaturen . Vissa sensorelement fungerar enligt principen om förändring av elektriska egenskaper, såsom det elektriska motståndet, med ett magnetfält. Inom halvledarteknik fungerar magnetoresisthuvudet som används i disklagringsteknik med denna princip. Mycket stora magnetoresistsignaler (gigantisk magnetoresistans) observeras i magnetiska flerskikt och kompositer som innehåller ett magnetiskt och omagnetiskt material. Elektriska eller elektroniska beläggningar: Dessa funktionella beläggningar lägger till elektriska eller elektroniska egenskaper som ledningsförmåga för att tillverka produkter som motstånd, isoleringsegenskaper som i fallet med magnettrådsbeläggningar som används i transformatorer. DEKORATIV BEläggning: När vi talar om dekorativa beläggningar begränsas alternativen endast av din fantasi. Beläggningar av både tjocka och tunna filmer har framgångsrikt konstruerats och applicerats tidigare på våra kunders produkter. Oavsett svårigheten i den geometriska formen och materialet hos underlaget och appliceringsförhållandena, kan vi alltid formulera kemin, fysikaliska aspekter såsom exakt Pantone-färgkod och appliceringsmetod för dina önskade dekorativa beläggningar. Komplexa mönster som involverar former eller olika färger är också möjliga. Vi kan få dina plastpolymerdelar att se metalliska ut. Vi kan färganodisera profiler med olika mönster och det ser inte ens anodiserat ut. Vi kan spegelbelägga en udda formad del. Dessutom kan dekorativa beläggningar formuleras som samtidigt fungerar som funktionella beläggningar. Vilken som helst av de nedan nämnda tunn- och tjockfilmsavsättningsteknikerna som används för funktionella beläggningar kan användas för dekorativa beläggningar. Här är några av våra populära dekorativa beläggningar: - PVD tunnfilm dekorativa beläggningar - Elektropläterade dekorativa beläggningar - CVD och PECVD tunnfilm dekorativa beläggningar - Termisk avdunstning dekorativa beläggningar - Roll-to-Roll dekorativ beläggning - E-Beam Oxide Interference Dekorativa beläggningar - Jonplätering - Katodisk bågeavdunstning för dekorativa beläggningar - PVD + fotolitografi, kraftig guldplätering på PVD - Aerosolbeläggningar för glasfärgning - Anti-lack beläggning - Dekorativa koppar-nickel-krom-system - Dekorativ pulverlackering - Dekorativ målning, skräddarsydda färgformuleringar med pigment, fyllmedel, kolloidalt kiseldispergeringsmedel ... etc. Om du kontaktar oss med dina krav på dekorativa beläggningar kan vi ge dig vårt expertutlåtande. Vi har avancerade verktyg som färgläsare, färgjämförare...etc. för att garantera konsekvent kvalitet på dina beläggningar. tunna och tjocka filmbeläggningsprocesser: Här är de mest använda av våra tekniker. Elektroplätering / kemisk plätering (hård krom, kemiskt nickel) Galvanisering är processen att plätera en metall på en annan genom hydrolys, för dekorativa ändamål, korrosionsskydd av en metall eller andra ändamål. Galvanisering låter oss använda billiga metaller som stål eller zink eller plast för huvuddelen av produkten och sedan applicera olika metaller på utsidan i form av en film för bättre utseende, skydd och för andra egenskaper som önskas för produkten. Elektrolös plätering, även känd som kemisk plätering, är en icke-galvanisk pläteringmetod som involverar flera samtidiga reaktioner i en vattenlösning, som sker utan användning av extern elektrisk kraft. Reaktionen åstadkommes när väte frigörs av ett reduktionsmedel och oxideras, vilket ger en negativ laddning på delens yta. Fördelarna med dessa tunna och tjocka filmer är god korrosionsbeständighet, låg bearbetningstemperatur, möjlighet att avsätta i borrhål, slitsar... etc. Nackdelar är det begränsade urvalet av beläggningsmaterial, beläggningarnas relativt mjuka karaktär, miljöförorenande behandlingsbad som behövs inklusive kemikalier som cyanid, tungmetaller, fluorider, oljor, begränsad noggrannhet av ytreplikering. Diffusion Processes (Nitrering, nitrokarburering, borering, fosfatering, etc.) I värmebehandlingsugnar kommer de diffusa elementen vanligtvis från gaser som reagerar vid höga temperaturer med metallytorna. Detta kan vara en ren termisk och kemisk reaktion som en konsekvens av den termiska dissociationen av gaserna. I vissa fall kommer diffusa element från fasta ämnen. Fördelarna med dessa termokemiska beläggningsprocesser är god korrosionsbeständighet, god reproducerbarhet. Nackdelarna med dessa är relativt mjuka beläggningar, begränsat urval av basmaterial (som måste vara lämpligt för nitrering), långa bearbetningstider, miljö- och hälsorisker inblandade, krav på efterbehandling. CVD (Chemical Vapor Deposition) CVD är en kemisk process som används för att producera högkvalitativa, högpresterande, solida beläggningar. Processen ger också tunna filmer. I en typisk CVD exponeras substraten för en eller flera flyktiga prekursorer, som reagerar och/eller sönderdelas på substratytan för att producera den önskade tunna filmen. Fördelarna med dessa tunna och tjocka filmer är deras höga slitstyrka, potential att ekonomiskt producera tjockare beläggningar, lämplighet för borrhål, slitsar ….etc. Nackdelar med CVD-processer är deras höga bearbetningstemperaturer, svårighet eller omöjlighet för beläggningar med flera metaller (som TiAlN), avrundning av kanter, användning av miljöfarliga kemikalier. PACVD / PECVD (Plasma-Assisted Chemical Vapor Deposition) PACVD kallas även PECVD som står för Plasma Enhanced CVD. Medan i en PVD-beläggningsprocess förångas de tunna och tjocka filmmaterialen från en fast form, i PECVD är beläggningen ett resultat av en gasfas. Prekursorgaser knäcks i plasman för att bli tillgängliga för beläggningen. Fördelarna med denna tunna och tjocka filmavsättningsteknik är att betydligt lägre processtemperaturer är möjliga jämfört med CVD, exakta beläggningar avsätts. Nackdelar med PACVD är att den endast har begränsad lämplighet för borrhål, slitsar mm. PVD (Physical Vapor Deposition) PVD-processer är en mängd rent fysiska vakuumavsättningsmetoder som används för att avsätta tunna filmer genom kondensation av en förångad form av det önskade filmmaterialet på arbetsstyckesytor. Sputtring och evaporativa beläggningar är exempel på PVD. Fördelar är att inga miljöskadliga material och utsläpp produceras, en stor mängd olika beläggningar kan produceras, beläggningstemperaturer är under den slutliga värmebehandlingstemperaturen för de flesta stål, exakt reproducerbara tunna beläggningar, hög slitstyrka, låg friktionskoefficient. Nackdelar är borrhål, slitsar ...etc. kan endast beläggas ner till ett djup som är lika med öppningens diameter eller bredd, korrosionsbeständig endast under vissa förhållanden, och för att erhålla enhetlig filmtjocklek måste delar roteras under deponering. Vidhäftningen av funktionella och dekorativa beläggningar är substratberoende. Dessutom beror livslängden på tunna och tjocka filmbeläggningar på miljöparametrar som fuktighet, temperatur...etc. Därför, innan du överväger en funktionell eller dekorativ beläggning, kontakta oss för vår åsikt. Vi kan välja de mest lämpliga beläggningsmaterialen och beläggningstekniken som passar dina underlag och applikation och deponera dem under de strängaste kvalitetsstandarderna. Kontakta AGS-TECH Inc. för detaljer om tunn och tjock filmavsättningsförmåga. Behöver du designhjälp? Behöver du prototyper? Behöver du masstillverkning? Vi är här för att hjälpa dig. CLICK Product Finder-Locator Service FÖREGÅENDE SIDA
- Panel PC - Industrial Computer - Multitouch Displays - Janz Tec
Panel PC - Industrial Computer - Multitouch Displays - Janz Tec - AGS-TECH Inc. - NM - USA Panel PC, Multitouch-skärmar, pekskärmar En delmängd av industridatorer är the PANEL PC där en skärm, såsom an_cc781905-51c är inbyggd i samma skärm, såsom an_cc781905-51c, som är inbyggd i samma skärm som an_cc781905-51c, som är inbyggd i samma skärm elektronik. These are typically panel mounted and often incorporate TOUCH SCREENS or MULTITOUCH DISPLAYS for interaction with users. De erbjuds i lågkostnadsversioner utan miljötätning, tyngre modeller förseglade enligt IP67-standarder för att vara vattentäta på frontpanelen och modeller som är explosionssäkra för installation i farliga miljöer. Här kan du ladda ner produktlitteratur för varumärkena JANZ TEC, DFI-ITOX_cc781905-4 Ladda ner vår kompakta produktbroschyr av märket JANZ TEC Ladda ner vår DFI-ITOX panel PC-broschyr Ladda ner våra industriella pekskärmar av märket DFI-ITOX Ladda ner vår broschyr av märket ICP DAS Industrial Touch Pad För att välja en lämplig panel-PC för ditt projekt, gå till vår industridatorbutik genom att KLICKA HÄR. Our JANZ TEC brand scalable product series of emVIEW systems offers a wide spectrum of processor performance and display sizes from 6.5 '' upp till för närvarande 19''. Skräddarsydda lösningar för optimal anpassning till din uppgiftsdefinition kan implementeras av oss. Några av våra populära panel PC-produkter är: HMI-system och fläktlösa industriella displaylösningar Multitouch-skärm Industriella TFT LCD-skärmar AGS-TECH Inc. som en etablerad ENGINEERING INTEGRATOR and_cc781905-4cde-6cUSTER-lösning för din PC-nyckel till en PC-nyckel till 5cde-6cUSTER-31c med din utrustning eller om du behöver våra pekskärmspaneler utformade på ett annat sätt. Ladda ner broschyr för vår DESIGN PARTNERSKAP PROGRAM CLICK Product Finder-Locator Service FÖREGÅENDE SIDA
- Brazing, Soldering, Welding, Joining Processes, Assembly Services
Brazing - Soldering - Welding - Joining Processes - Assembly Services - Subassemblies - Assemblies - Custom Manufacturing - AGS-TECH Inc. - NM - USA Lödning & Lödning & Svetsning Bland de många JOININGS-tekniker som vi använder i tillverkningen, läggs särskild tonvikt på SVETSNING, LÖDNING, LÖDNING, LIMBINDNING och ANPASSAD MEKANISK MONTERING eftersom dessa tekniker används i stor utsträckning i applikationer som tillverkning av hermetiska sammansättningar, högteknologisk produkttillverkning och specialiserad tätning. Här kommer vi att koncentrera oss på de mer specialiserade aspekterna av dessa sammanfogningstekniker eftersom de är relaterade till tillverkning av avancerade produkter och sammansättningar. FUSIONSSVETSNING: Vi använder värme för att smälta och sammansmälta material. Värme tillförs av el eller högenergibalkar. De typer av smältsvetsning vi använder är OXYFUEL GASSVETNING, BÅGSvetsning, HÖGENERGISvetsning. SOLID-STATE SVETS: Vi sammanfogar delar utan att smälta och smälta. Våra solid-state svetsmetoder är KALL, ULTRALJUD, MOTSTÅND, FRIKTION, EXPLOSIONSSVETSNING och DIFFUSIONSBINDNING. LÖDNING & LÖDNING: De använder tillsatsmetaller och ger oss fördelen att arbeta vid lägre temperaturer än vid svetsning, vilket gör att produkterna inte skadas av strukturen. Information om vår hårdlödningsanläggning som producerar keramiska till metallbeslag, hermetisk tätning, vakuumgenomföringar, hög- och ultrahögvakuum och vätskekontrollkomponenter finns här:Broschyr för lödningsfabrik ADHESIVBINDNING: På grund av mångfalden av lim som används inom industrin och även mångfalden av applikationer, har vi en särskild sida för detta. För att gå till vår sida om limning, klicka här. ANPASSAD MEKANISK MONTERING: Vi använder en mängd olika fästelement som bultar, skruvar, muttrar, nitar. Våra fästelement är inte begränsade till standardfästen från hyllan. Vi designar, utvecklar och tillverkar specialfästen som är gjorda av icke-standardiserade material så att de kan uppfylla kraven för speciella applikationer. Ibland önskas elektrisk eller värme icke-konduktivitet medan ibland konduktivitet. För vissa speciella tillämpningar kan en kund vilja ha speciella fästelement som inte kan tas bort utan att förstöra produkten. Det finns oändliga idéer och tillämpningar. Vi har allt för dig, om inte från hyllan kan vi snabbt utveckla det. För att gå till vår sida om mekanisk montering, klicka här . Låt oss undersöka våra olika sammanfogningstekniker mer detaljerat. OXYFUEL GAS WELDING (OFW): Vi använder en bränslegas blandad med syre för att producera svetslågan. När vi använder acetylen som bränsle och syre, kallar vi det oxyacetylengassvetsning. Två kemiska reaktioner inträffar i förbränningsprocessen av oxyfuel: C2H2 + O2 ------» 2CO + H2 + Värme 2CO + H2 + 1,5 O2--------» 2 CO2 + H2O + Värme Den första reaktionen dissocierar acetylenen till kolmonoxid och väte samtidigt som den producerar cirka 33 % av den totala värme som genereras. Den andra processen ovan representerar ytterligare förbränning av väte och kolmonoxid samtidigt som den producerar cirka 67 % av den totala värmen. Temperaturen i lågan är mellan 1533 och 3573 Kelvin. Syreprocenten i gasblandningen är viktig. Om syrehalten är mer än hälften blir lågan ett oxidationsmedel. Detta är inte önskvärt för vissa metaller men önskvärt för andra. Ett exempel när oxiderande låga är önskvärt är kopparbaserade legeringar eftersom det bildar ett passiveringsskikt över metallen. Å andra sidan, när syrehalten minskar är full förbränning inte möjlig och lågan blir en reducerande (förkolande) låga. Temperaturerna i en reducerande låga är lägre och därför är den lämplig för processer som lödning och hårdlödning. Andra gaser är också potentiella bränslen, men de har vissa nackdelar jämfört med acetylen. Ibland levererar vi tillsatsmetaller till svetszonen i form av tillsatsstavar eller tråd. Vissa av dem är belagda med flussmedel för att fördröja oxidation av ytor och på så sätt skydda den smälta metallen. En ytterligare fördel som flussmedlet ger oss är avlägsnandet av oxider och andra ämnen från svetszonen. Detta leder till starkare bindning. En variant av oxyfuel-gassvetsningen är TRYCKGASVETSNING, där de två komponenterna värms upp vid deras gränssnitt med hjälp av oxyacetylengasbrännare och när gränssnittet börjar smälta dras brännaren tillbaka och en axiell kraft appliceras för att pressa samman de två delarna tills gränssnittet stelnat. BÅGSVETSNING: Vi använder elektrisk energi för att producera en båge mellan elektrodspetsen och de delar som ska svetsas. Strömförsörjningen kan vara AC eller DC medan elektroderna är antingen förbrukningsbara eller icke förbrukningsbara. Värmeöverföring vid bågsvetsning kan uttryckas med följande ekvation: H/l = ex VI/v Här är H värmetillförseln, l är svetslängden, V och I är spänningen och strömmen som appliceras, v är svetshastigheten och e är processeffektiviteten. Ju högre verkningsgrad "e" desto mer fördelaktigt används den tillgängliga energin för att smälta materialet. Värmetillförseln kan också uttryckas som: H = ux (Volym) = ux A xl Här är u den specifika energin för smältning, A svetsens tvärsnitt och l svetslängden. Från de två ekvationerna ovan kan vi få: v = ex VI / u A En variant av bågsvetsning är SHELDED METAL RC WELDING (SMAW) som utgör cirka 50 % av alla industri- och underhållssvetsprocesser. ELEKTRISK BÅGSVETSNING (STICK WELDING) utförs genom att röra spetsen på en belagd elektrod mot arbetsstycket och snabbt dra tillbaka det till ett tillräckligt avstånd för att bibehålla ljusbågen. Vi kallar denna process även stavsvetsning eftersom elektroderna är tunna och långa stift. Under svetsprocessen smälter elektrodens spets tillsammans med dess beläggning och basmetallen i närheten av bågen. En blandning av basmetallen, elektrodmetallen och ämnen från elektrodbeläggningen stelnar i svetsområdet. Beläggningen av elektroden deoxiderar och ger en skyddsgas i svetsområdet, vilket skyddar den från syret i miljön. Därför kallas processen skärmad metallbågsvetsning. Vi använder strömmar mellan 50 och 300 Ampere och effektnivåer i allmänhet mindre än 10 kW för optimal svetsprestanda. Också av betydelse är polariteten hos DC-strömmen (strömflödesriktningen). Rak polaritet där arbetsstycket är positivt och elektroden är negativ är att föredra vid svetsning av plåt på grund av dess ytliga penetration och även för fogar med mycket stora mellanrum. När vi har omvänd polaritet, dvs elektroden är positiv och arbetsstycket negativ kan vi uppnå djupare svetsgenomträngningar. Med växelström, eftersom vi har pulserande bågar, kan vi svetsa tjocka sektioner med elektroder med stor diameter och maximala strömmar. SMAW-svetsmetoden är lämplig för arbetsstyckestjocklekar på 3 till 19 mm och ännu mer med hjälp av flergångstekniker. Slaggen som bildas ovanpå svetsen måste avlägsnas med en stålborste, så att det inte uppstår korrosion och brott på svetsområdet. Detta ökar naturligtvis kostnaden för bågsvetsning av skärmad metall. Ändå är SMAW den mest populära svetstekniken inom industri och reparationsarbete. DÄNKBÅGSVETSNING (SÅG): I denna process skyddar vi svetsbågen med hjälp av granulära flussmedel som kalk, kiseldioxid, kalciumflorid, manganoxid...etc. Det granulära flussmedlet matas in i svetszonen genom gravitationsflöde genom ett munstycke. Flussmedlet som täcker den smälta svetszonen skyddar avsevärt från gnistor, ångor, UV-strålning etc. och fungerar som en värmeisolator och låter värme tränga djupt in i arbetsstycket. Det osammansatta flödet återvinns, behandlas och återanvänds. En spole av blank används som elektrod och matas genom ett rör till svetsområdet. Vi använder strömmar mellan 300 och 2000 Ampere. Processen för nedsänkt bågsvetsning (SAW) är begränsad till horisontella och plana lägen och cirkulära svetsar om rotation av den cirkulära strukturen (såsom rör) är möjlig under svetsning. Hastigheterna kan nå 5 m/min. SAW-processen är lämplig för tjocka plåtar och resulterar i högkvalitativa, sega, formbara och enhetliga svetsar. Produktiviteten, det vill säga mängden svetsmaterial som avsätts per timme är 4 till 10 gånger mängden jämfört med SMAW-processen. En annan bågsvetsprocess, nämligen GAS METAL RC WELDING (GMAW) eller alternativt kallad METAL INERT GAS WELDING (MIG) är baserad på att svetsområdet skyddas av externa gaskällor som helium, argon, koldioxid...etc. Det kan finnas ytterligare deoxidationsmedel närvarande i elektrodmetallen. Förbrukningsbar tråd matas genom ett munstycke in i svetszonen. Tillverkning som involverar både järnhaltiga och icke-järnhaltiga metaller utförs med hjälp av gasmetallbågsvetsning (GMAW). Svetsproduktiviteten är ungefär 2 gånger högre än SMAW-processen. Automatiserad svetsutrustning används. Metall överförs på ett av tre sätt i denna process: "Spray Transfer" innebär överföring av flera hundra små metalldroppar per sekund från elektroden till svetsområdet. I "Globular Transfer" å andra sidan används koldioxidrika gaser och kulor av smält metall drivs av den elektriska ljusbågen. Svetsströmmarna är höga och svetspenetrationen djupare, svetshastigheten högre än vid sprayöverföring. Den klotformade överföringen är således bättre för svetsning av tyngre sektioner. Slutligen, i "Short Circuiting"-metoden, vidrör elektrodspetsen den smälta svetsbassängen och kortsluter den då metall med hastigheter över 50 droppar/sekund överförs i individuella droppar. Låga strömmar och spänningar används tillsammans med tunnare tråd. Effekterna som används är cirka 2 kW och temperaturen är relativt låg, vilket gör denna metod lämplig för tunna plåtar som är mindre än 6 mm tjocka. En annan variant av FLUX-CORED ARC WELDING (FCAW)-processen liknar gasmetallbågsvetsning, förutom att elektroden är ett rör fyllt med flussmedel. Fördelarna med att använda elektroder med kärnflux är att de ger mer stabila bågar, ger oss möjlighet att förbättra egenskaperna hos svetsmetaller, mindre spröd och flexibel karaktär hos dess flussmedel jämfört med SMAW-svetsning, förbättrade svetskonturer. Självskärmade elektroder med kärnor innehåller material som skyddar svetszonen mot atmosfären. Vi använder cirka 20 kW effekt. Precis som GMAW-processen erbjuder FCAW-processen också möjligheten att automatisera processer för kontinuerlig svetsning, och det är ekonomiskt. Olika svetsmetallkemier kan utvecklas genom att lägga till olika legeringar till flusskärnan. I ELECTROGAS WELDING (EGW) svetsar vi de placerade bitarna kant i kant. Det kallas ibland även STUMSVETSNING. Svetsmetall placeras i en svetshålighet mellan två delar som ska sammanfogas. Utrymmet är omslutet av två vattenkylda dammar för att förhindra att den smälta slaggen rinner ut. Dammarna flyttas upp med mekaniska drivningar. När arbetsstycket kan roteras kan vi även använda elektrogassvetsningstekniken för omkretssvetsning av rör. Elektroder matas genom en ledning för att hålla en kontinuerlig båge. Strömmar kan vara cirka 400 Ampere eller 750 Ampere och effektnivåer cirka 20 kW. Inerta gaser som kommer från antingen en elektrod med flödeskärna eller extern källa ger avskärmning. Vi använder elektrogassvetsning (EGW) för metaller som stål, titan...etc med tjocklekar från 12 mm till 75 mm. Tekniken passar bra för stora strukturer. Ändå, i en annan teknik som kallas ELECTROSLAG WELDING (ESW) antänds ljusbågen mellan elektroden och botten av arbetsstycket och flussmedel tillsätts. När smält slagg når elektrodspetsen släcks ljusbågen. Energi tillförs kontinuerligt genom den smälta slaggens elektriska motstånd. Vi kan svetsa plåtar med tjocklekar mellan 50 mm och 900 mm och ännu högre. Strömmarna är cirka 600 Ampere medan spänningarna ligger mellan 40 – 50 V. Svetshastigheterna är cirka 12 till 36 mm/min. Tillämpningar liknar elektrogassvetsning. En av våra icke-förbrukningsbara elektrodprocesser, GAS TUNGSTEN ARC WELDING (GTAW) även känd som TUNGSTEN INERT GAS WELDING (TIG) involverar tillförsel av en tillsatsmetall genom en tråd. För täta fogar använder vi ibland inte tillsatsmetallen. I TIG-processen använder vi inte flux, utan använder argon och helium för avskärmning. Volfram har en hög smältpunkt och förbrukas inte i TIG-svetsprocessen, därför kan konstant ström såväl som båggap upprätthållas. Effektnivåer är mellan 8 till 20 kW och strömmar vid antingen 200 Ampere (DC) eller 500 Ampere (AC). För aluminium och magnesium använder vi växelström för dess oxidrengörande funktion. För att undvika kontaminering av volframelektroden undviker vi dess kontakt med smälta metaller. Gas Tungsten Arc Welding (GTAW) är särskilt användbar för svetsning av tunna metaller. GTAW-svetsar är av mycket hög kvalitet med god ytfinish. På grund av den högre kostnaden för vätgas är en mindre ofta använd teknik ATOMIC HYDROGEN WELDING (AHW), där vi genererar en båge mellan två volframelektroder i en avskärmande atmosfär av strömmande vätgas. AHW är också en icke förbrukbar elektrodsvetsprocess. Den diatomiska vätgasen H2 bryts ner till sin atomform nära svetsbågen där temperaturen är över 6273 Kelvin. När den bryts ned absorberar den stora mängder värme från bågen. När väteatomerna träffar svetszonen som är en relativt kall yta, rekombinerar de till diatomisk form och frigör den lagrade värmen. Energi kan varieras genom att ändra arbetsstycket till bågavstånd. I en annan icke förbrukningsbar elektrodprocess, PLASMA BÅGSVETSNING (PAW), har vi en koncentrerad plasmabåge riktad mot svetszonen. Temperaturerna når 33 273 Kelvin i PAW. Nästan lika många elektroner och joner utgör plasmagasen. En lågströmspilotbåge initierar plasman som finns mellan volframelektroden och öppningen. Driftströmmar är i allmänhet runt 100 Ampere. En tillsatsmetall kan matas. Vid plasmabågsvetsning åstadkoms skärmning av en yttre skärmring och med användning av gaser som argon och helium. Vid plasmabågsvetsning kan ljusbågen vara mellan elektroden och arbetsstycket eller mellan elektroden och munstycket. Denna svetsteknik har fördelarna jämfört med andra metoder med högre energikoncentration, djupare och smalare svetsförmåga, bättre bågstabilitet, högre svetshastigheter upp till 1 meter/min, mindre termisk distorsion. Vi använder vanligtvis plasmabågsvetsning för tjocklekar mindre än 6 mm och ibland upp till 20 mm för aluminium och titan. HÖGENERGISvetsning: En annan typ av smältsvetsmetod med elektronstrålesvetsning (EBW) och lasersvetsning (LBW) som två varianter. Dessa tekniker är av särskilt värde för vårt högteknologiska produkttillverkningsarbete. Vid elektronstrålesvetsning träffar höghastighetselektroner arbetsstycket och deras kinetiska energi omvandlas till värme. Den smala elektronstrålen rör sig lätt i vakuumkammaren. Generellt använder vi högvakuum vid e-beam svetsning. Plattor så tjocka som 150 mm kan svetsas. Inga skyddsgaser, flussmedel eller fyllnadsmaterial behövs. Elektronstrålepistoler har en kapacitet på 100 kW. Djupa och smala svetsar med höga bildförhållanden upp till 30 och små värmepåverkade zoner är möjliga. Svetshastigheter kan nå 12 m/min. Vid laserstrålesvetsning använder vi högeffektlasrar som värmekälla. Laserstrålar så små som 10 mikron med hög densitet möjliggör djup penetrering i arbetsstycket. Djup-till-bredd-förhållanden så mycket som 10 är möjligt med laserstrålesvetsning. Vi använder både pulsade och kontinuerliga våglasrar, med den förra i applikationer för tunna material och den senare mest för tjocka arbetsstycken upp till ca 25 mm. Effektnivåerna är upp till 100 kW. Lasersvetsningen är inte väl lämpad för optiskt mycket reflekterande material. Gaser kan också användas i svetsprocessen. Laserstrålesvetsmetoden är väl lämpad för automation och tillverkning av hög volym och kan erbjuda svetshastigheter mellan 2,5 m/min och 80 m/min. En stor fördel med denna svetsteknik är tillgången till områden där andra tekniker inte kan användas. Laserstrålar kan lätt resa till sådana svåra områden. Inget vakuum som vid elektronstrålesvetsning behövs. Svetsar med bra kvalitet & styrka, låg krympning, låg distorsion, låg porositet kan erhållas med laserstrålesvetsning. Laserstrålar kan enkelt manipuleras och formas med fiberoptiska kablar. Tekniken är därför väl lämpad för svetsning av precisionshermetiska sammansättningar, elektroniska paket etc. Låt oss titta på våra SOLID STATE WELDING-tekniker. KALLSvetsning (CW) är en process där tryck istället för värme appliceras med hjälp av stansar eller valsar till de delar som är sammankopplade. Vid kallsvetsning måste minst en av de passande delarna vara duktil. Bästa resultat erhålls med två liknande material. Om de två metallerna som ska sammanfogas med kallsvetsning är olika kan vi få svaga och spröda fogar. Kallsvetsmetoden är väl lämpad för mjuka, formbara och små arbetsstycken såsom elektriska anslutningar, värmekänsliga behållarkanter, bimetalllister för termostater...etc. En variant av kallsvetsning är rullbindning (eller rullsvetsning), där trycket appliceras genom ett par rullar. Ibland utför vi rullsvetsning vid förhöjda temperaturer för bättre gränsytstyrka. En annan solid state-svetsprocess vi använder är ULTRASONIC WELDING (USW), där arbetsstyckena utsätts för en statisk normalkraft och oscillerande skjuvspänningar. De oscillerande skjuvspänningarna appliceras genom spetsen på en givare. Ultraljudssvetsning utlöser svängningar med frekvenser från 10 till 75 kHz. I vissa applikationer som sömsvetsning använder vi en roterande svetsskiva som spets. Skjuvspänningar som appliceras på arbetsstyckena orsakar små plastiska deformationer, bryter upp oxidskikt, föroreningar och leder till fast tillståndsbindning. Temperaturer involverade i ultraljudssvetsning ligger långt under smältpunktstemperaturerna för metaller och ingen smältning äger rum. Vi använder ofta ultraljudssvetsning (USW) process för icke-metalliska material som plast. I termoplaster når dock temperaturerna smältpunkter. En annan populär teknik, i FRICTION WELDING (FRW) genereras värmen genom friktion vid gränsytan mellan arbetsstyckena som ska sammanfogas. Vid friktionssvetsning håller vi ett av arbetsstyckena stationärt medan det andra arbetsstycket hålls i en fixtur och roteras med konstant hastighet. Arbetsstyckena bringas sedan i kontakt under en axiell kraft. Ytrotationshastigheten vid friktionssvetsning kan i vissa fall nå 900 m/min. Efter tillräcklig kontakt med gränsytan stoppas det roterande arbetsstycket plötsligt och den axiella kraften ökas. Svetszonen är i allmänhet ett smalt område. Friktionssvetstekniken kan användas för att sammanfoga solida och rörformiga delar gjorda av en mängd olika material. Viss blixt kan utvecklas vid gränssnittet i FRW, men denna blixt kan tas bort genom sekundär bearbetning eller slipning. Variationer av friktionssvetsprocessen finns. Till exempel "tröghetsfriktionssvetsning" involverar ett svänghjul vars rotationskinetiska energi används för att svetsa delarna. Svetsen är klar när svänghjulet stannar. Den roterande massan kan varieras och därmed den roterande kinetiska energin. En annan variant är "linjär friktionssvetsning", där linjär fram- och återgående rörelse åläggs åtminstone en av komponenterna som ska sammanfogas. I linjär friktionssvetsning behöver inte delar vara cirkulära, de kan vara rektangulära, kvadratiska eller av annan form. Frekvenser kan vara i tiotals Hz, amplituder i millimeterområdet och tryck i tiotals eller hundratals MPa. Slutligen är "friction stir welding" något annorlunda än de andra två som förklaras ovan. Medan vid tröghetsfriktionssvetsning och linjär friktionssvetsning uppvärmning av gränssnitt uppnås genom friktion genom gnidning av två kontaktytor, gnids i friktionsomrörningssvetsningsmetoden en tredje kropp mot de två ytorna som ska sammanfogas. Ett roterande verktyg med 5 till 6 mm diameter bringas i kontakt med fogen. Temperaturerna kan öka till värden mellan 503 till 533 Kelvin. Uppvärmning, blandning och omrörning av materialet i fogen sker. Vi använder friktionssvetsning på en mängd olika material inklusive aluminium, plast och kompositer. Svetsar är enhetliga och kvaliteten är hög med minimala porer. Inga ångor eller stänk produceras vid friktionssvetsning och processen är väl automatiserad. RESISTANSSVETSNING (RW): Värmen som krävs för svetsning produceras av det elektriska motståndet mellan de två arbetsstyckena som ska sammanfogas. Inget flussmedel, skyddsgaser eller förbrukningsbara elektroder används vid motståndssvetsning. Jouleuppvärmning sker vid motståndssvetsning och kan uttryckas som: H = (kvadrat I) x R xtx K H är värme som genereras i joule (watt-sekunder), I ström i ampere, R resistans i ohm, t är tiden i sekunder som strömmen flyter igenom. Faktorn K är mindre än 1 och representerar den del av energi som inte går förlorad genom strålning och ledning. Strömmar i motståndssvetsprocesser kan nå nivåer så höga som 100 000 A men spänningarna är vanligtvis 0,5 till 10 volt. Elektroder är vanligtvis gjorda av kopparlegeringar. Både liknande och olika material kan sammanfogas genom motståndssvetsning. Det finns flera variationer för denna process: "Resistenspunktsvetsning" innebär att två motsatta runda elektroder kommer i kontakt med ytorna på överlappsfogen på de två plåtarna. Tryck appliceras tills strömmen stängs av. Svetsklumpen är vanligtvis upp till 10 mm i diameter. Motståndspunktsvetsning lämnar lätt missfärgade fördjupningsmärken vid svetspunkter. Punktsvetsning är vår mest populära motståndssvetsteknik. Olika elektrodformer används vid punktsvetsning för att nå svåra områden. Vår punktsvetsutrustning är CNC-styrd och har flera elektroder som kan användas samtidigt. En annan variant av "motståndssömsvetsning" utförs med hjul- eller rullelektroder som producerar kontinuerliga punktsvetsar när strömmen når en tillräckligt hög nivå i växelströmscykeln. Fogar som produceras genom motståndssvetsning är vätske- och gastäta. Svetshastigheter på ca 1,5 m/min är normala för tunnplåt. Man kan applicera intermittenta strömmar så att punktsvetsar produceras med önskade intervall längs sömmen. Vid "motståndsprojektionssvetsning" präglar vi en eller flera utsprång (gropar) på en av arbetsstyckesytorna som ska svetsas. Dessa utsprång kan vara runda eller ovala. Höga lokaliserade temperaturer uppnås vid dessa präglade fläckar som kommer i kontakt med parningsdelen. Elektroder utövar tryck för att komprimera dessa utsprång. Elektroder i motståndsprojektionssvetsning har platta spetsar och är vattenkylda kopparlegeringar. Fördelen med resistansprojektionssvetsning är vår förmåga att svetsa ett antal svetsar i ett slag, alltså den förlängda elektrodens livslängd, förmågan att svetsa plåtar av olika tjocklekar, förmågan att svetsa muttrar och bultar till plåtar. Nackdelen med motståndsprojektionssvetsning är den extra kostnaden för att prägla fördjupningarna. Ännu en teknik, vid "blixtsvetsning" genereras värme från bågen i ändarna av de två arbetsstyckena när de börjar få kontakt. Denna metod kan också alternativt betraktas som bågsvetsning. Temperaturen vid gränssnittet stiger och materialet mjuknar. En axiell kraft appliceras och en svets bildas vid det uppmjukade området. Efter att snabbsvetsningen är klar kan fogen bearbetas för förbättrat utseende. Svetskvaliteten som erhålls genom snabbsvetsning är god. Effektnivåer är 10 till 1500 kW. Snabbsvetsning är lämplig för kant-till-kant sammanfogning av liknande eller olika metaller upp till 75 mm diameter och plåtar mellan 0,2 mm till 25 mm tjocklek. "Stud arc welding" är mycket lik snabbsvetsning. Tappen såsom en bult eller gängad stång tjänar som en elektrod medan den förenas med ett arbetsstycke såsom en platta. För att koncentrera den alstrade värmen, förhindra oxidation och hålla kvar den smälta metallen i svetszonen placeras en keramisk engångsring runt fogen. Slutligen "slagsvetsning", en annan motståndssvetsprocess, använder en kondensator för att tillföra den elektriska energin. Vid slagsvetsning urladdas kraften inom millisekunder mycket snabbt och utvecklar hög lokal värme vid fogen. Vi använder slagsvetsning i stor utsträckning inom elektroniktillverkningsindustrin där uppvärmning av känsliga elektroniska komponenter i närheten av fogen måste undvikas. En teknik som kallas EXPLOSIONSSVETNING innebär att ett lager av sprängämne detoneras som läggs över ett av arbetsstyckena som ska sammanfogas. Det mycket höga trycket som utövas på arbetsstycket ger ett turbulent och vågigt gränssnitt och mekanisk låsning sker. Förbindningsstyrkorna vid explosiv svetsning är mycket höga. Explosionssvetsning är en bra metod för beklädnad av plåtar med olika metaller. Efter beklädnad kan plattorna rullas till tunnare sektioner. Ibland använder vi explosionsvetsning för att expandera rör så att de tätar tätt mot plattan. Vår sista metod inom området solid state-fogning är DIFFUSION BONDING eller DIFFUSION WELDING (DFW) där en bra fog uppnås huvudsakligen genom diffusion av atomer över gränsytan. Viss plastisk deformation vid gränssnittet bidrar också till svetsningen. Inblandade temperaturer är runt 0,5 Tm där Tm är smälttemperaturen för metallen. Bindstyrkan vid diffusionssvetsning beror på tryck, temperatur, kontakttid och renheten hos kontaktytor. Ibland använder vi tillsatsmetaller vid gränssnittet. Värme och tryck krävs vid diffusionsbindning och tillförs av elektriskt motstånd eller ugn och dödvikter, press eller annat. Liknande och olika metaller kan sammanfogas med diffusionssvetsning. Processen är relativt långsam på grund av den tid det tar för atomer att migrera. DFW kan automatiseras och används i stor utsträckning vid tillverkning av komplexa delar för flyg-, elektronik- och medicinindustrin. Produkter som tillverkas inkluderar ortopediska implantat, sensorer, strukturella delar för flygindustrin. Diffusionsbindning kan kombineras med SUPERPLASTISK FORMNING för att tillverka komplexa plåtstrukturer. Utvalda platser på ark diffusionsbondas först och sedan expanderas de obundna områdena till en form med hjälp av lufttryck. Flygkonstruktioner med höga styvhet-till-vikt-förhållanden tillverkas med denna kombination av metoder. Den kombinerade processen för diffusionssvetsning/superplastformning minskar antalet delar som krävs genom att eliminera behovet av fästelement, vilket resulterar i lågspänning och mycket exakta delar ekonomiskt och med korta ledtider. LÖDNING: Lödnings- och lödteknikerna innebär lägre temperaturer än de som krävs för svetsning. Lödningstemperaturerna är dock högre än lödtemperaturerna. Vid hårdlödning placeras en tillsatsmetall mellan ytorna som ska sammanfogas och temperaturen höjs till smälttemperaturen för tillsatsmaterialet över 723 Kelvin men under arbetsstyckenas smälttemperaturer. Den smälta metallen fyller det tätt passande utrymmet mellan arbetsstyckena. Kylning och efterföljande stelning av filarmetallen resulterar i starka fogar. Vid lödsvetsning avsätts tillsatsmetallen vid fogen. Avsevärt mer tillsatsmetall används vid lödsvetsning jämfört med lödning. Oxyacetylenbrännare med oxiderande låga används för att avsätta tillsatsmetallen vid lödsvetsning. På grund av lägre temperaturer vid hårdlödning är problemen i värmepåverkade zoner, såsom skevhet och kvarvarande spänningar, mindre. Ju mindre spelrum är vid lödning, desto högre är fogens skjuvhållfasthet. Maximal draghållfasthet uppnås dock vid ett optimalt gap (ett toppvärde). Under och över detta optimala värde minskar draghållfastheten vid hårdlödning. Typiska spelrum vid hårdlödning kan vara mellan 0,025 och 0,2 mm. Vi använder en mängd olika hårdlödningsmaterial med olika former såsom performs, puder, ringar, tråd, remsa...etc. och kan tillverka dessa utförs speciellt för din design eller produktgeometri. Vi bestämmer också innehållet i hårdlödningsmaterialen enligt dina basmaterial och tillämpningar. Vi använder ofta flussmedel i hårdlödningsoperationer för att avlägsna oönskade oxidlager och förhindra oxidation. För att undvika efterföljande korrosion avlägsnas flussmedel vanligtvis efter sammanfogningsoperationen. AGS-TECH Inc. använder olika hårdlödningsmetoder, inklusive: - Fackellödning - Ugnslödning - Induktionslödning - Motståndslödning - Dopplödning - Infraröd lödning - Diffusionslödning - Högenergistråle Våra vanligaste exempel på lödfogar är gjorda av olika metaller med god hållfasthet såsom hårdmetallborr, skär, optoelektroniska hermetiska paket, tätningar. LÖDNING: Detta är en av våra mest använda tekniker där lodet (tillsatsmetallen) fyller fogen som vid lödning mellan tättslutande komponenter. Våra lod har smältpunkter under 723 Kelvin. Vi använder både manuell och automatiserad lödning i tillverkningsoperationer. Jämfört med lödning är lödtemperaturen lägre. Lödning är inte särskilt lämplig för applikationer med hög temperatur eller hög hållfasthet. Vi använder såväl blyfria lod som tenn-bly, tenn-zink, bly-silver, kadmium-silver, zink-aluminiumlegeringar förutom andra för lödning. Både icke-korrosiva hartsbaserade såväl som oorganiska syror och salter används som flussmedel vid lödning. Vi använder speciella flussmedel för att löda metaller med låg lödbarhet. I applikationer där vi ska löda keramiska material, glas eller grafit, pläterar vi först delarna med en lämplig metall för ökad lödbarhet. Våra populära lödtekniker är: -Reflow eller Paste Lödning -Våglödning -Ugnslödning - Facklorlödning -Induktionslödning -Järnlödning - Motståndslödning -Dopplödning -Ultraljudslödning -Infraröd lödning Ultraljudslödning ger oss en unik fördel där behovet av flussmedel elimineras på grund av ultraljudskavitationseffekt som tar bort oxidfilmer från ytorna som ska fogas. Reflow och Wave lödning är våra industriellt enastående tekniker för högvolymtillverkning inom elektronik och därför värda att förklara mer i detalj. Vid återflödeslödning använder vi halvfasta pastor som innehåller lödmetallpartiklar. Pastan placeras på fogen med hjälp av en screening- eller stencileringsprocess. I kretskort (PCB) använder vi ofta denna teknik. När elektriska komponenter placeras på dessa kuddar från pasta, håller ytspänningen de ytmonterade förpackningarna i linje. Efter att ha placerat komponenterna värmer vi sammansättningen i en ugn så att återflödeslödningen sker. Under denna process avdunstar lösningsmedlen i pastan, flussmedlet i pastan aktiveras, komponenterna förvärms, lodpartiklarna smälts och väter fogen och slutligen kyls PCB-enheten långsamt. Vår andra populära teknik för högvolymproduktion av PCB-skivor, nämligen våglödning förlitar sig på det faktum att smältlod väter metallytor och bildar bra bindningar först när metallen är förvärmd. En stående laminär våg av smält lod genereras först av en pump och de förvärmda och prefluxade PCB:erna transporteras över vågen. Lödet väter endast exponerade metallytor men väter inte IC-polymerpaketen eller de polymerbelagda kretskorten. En varmvattenstråle med hög hastighet blåser överflödigt lod från fogen och förhindrar överbryggning mellan intilliggande ledningar. Vid våglödning av ytmonterade paket binder vi dem först vid kretskortet innan lödning. Återigen används skärmning och stencilering men denna gång för epoxi. Efter att komponenterna har placerats på rätt plats, härdas epoxin, brädorna vänds upp och ner och våglödning sker. CLICK Product Finder-Locator Service FÖREGÅENDE SIDA
- Microfluidic Devices, Microfluidics,Micropumps,Microvalves,Lab-on-Chip
Microfluidic Devices - Microfluidics - Micropumps - Microvalves - Lab-on-a-Chip Systems - Microhydraulic - Micropneumatic - AGS-TECH Inc.- New Mexico - USA Microfluidic Devices Manufacturing Our MICROFLUIDIC DEVICES MANUFACTURING operationer är inriktade på tillverkning av små volymer och system som hanteras av enheter och system. Vi har förmågan att designa mikrofluidiska enheter åt dig och erbjuda prototyper och mikrotillverkning skräddarsydda för dina applikationer. Exempel på mikrofluidiska enheter är mikroframdrivningsenheter, lab-on-a-chip-system, mikrotermiska enheter, bläckstråleskrivhuvuden och mer. In MICROFLUIDICS vi måste ta itu med den exakta kontrollen och manipuleringen av vätskor som är begränsade till sub-milimeterregioner. Vätskor flyttas, blandas, separeras och bearbetas. I mikrofluidsystem flyttas och styrs vätskor antingen aktivt med hjälp av små mikropumpar och mikroventiler och liknande eller passivt utnyttjande av kapillärkrafter. Med lab-on-a-chip-system miniatyriseras processer som normalt utförs i ett labb på ett enda chip för att öka effektiviteten och rörligheten samt minska prov- och reagensvolymerna. Några stora tillämpningar av mikrofluidiska enheter och system är: - Laboratorier på ett chip - Narkotikascreening - Glukostest - Kemisk mikroreaktor - Mikroprocessorkylning - Mikrobränsleceller - Proteinkristallisation - Snabba läkemedelsförändringar, manipulering av enstaka celler - Encellsstudier - Avstämbara optofluidiska mikrolinsarrayer - Mikrohydrauliska och mikropneumatiska system (vätskepumpar, gasventiler, blandningssystem etc.) - Biochip tidig varningssystem - Detektering av kemiska arter - Bioanalytiska tillämpningar - On-chip DNA och proteinanalys - Munstyckssprutanordningar - Kvartsflödesceller för detektion av bakterier - Dubbla eller flera droppgenereringschips Våra konstruktionsingenjörer har många års erfarenhet av modellering, design och testning av mikrofluidiska enheter för en rad applikationer. Vår designexpertis inom området mikrofluidik inkluderar: • Lågtemperatur termisk bindningsprocess för mikrofluidik • Våtetsning av mikrokanaler med etsdjup på nm till mm djup i glas och borosilikat. • Slipning och polering för ett brett spektrum av underlagstjocklekar från så tunna som 100 mikron till över 40 mm. • Möjlighet att smälta flera lager för att skapa komplexa mikrofluidiska enheter. • Tekniker för borrning, tärning och ultraljudsbearbetning som är lämpliga för mikrofluidiska enheter • Innovativa tärningstekniker med exakt kantkoppling för sammankoppling av mikrofluidiska enheter • Noggrann uppriktning • Olika avsatta beläggningar, mikrofluidchips kan sputteras med metaller som platina, guld, koppar och titan för att skapa ett brett utbud av funktioner, såsom inbäddade RTD:er, sensorer, speglar och elektroder. Förutom våra anpassade tillverkningsmöjligheter har vi hundratals vanliga standardmikrofluidchipdesigner tillgängliga med hydrofoba, hydrofila eller fluorerade beläggningar och ett brett utbud av kanalstorlekar (100 nanometer till 1 mm), ingångar, utgångar, olika geometrier som cirkulärt kors , pelarmatriser och mikromixer. Våra mikrofluidiska enheter erbjuder utmärkt kemisk resistens och optisk transparens, hög temperaturstabilitet upp till 500 Celsius, högtrycksintervall upp till 300 Bar. Några populära mikrofluidiska off-shelf-chips är: MICROFLUIDIC DROPLET CHIPS: Glas Droplet Chips med olika kopplingsgeometrier, kanalstorlekar och ytegenskaper finns tillgängliga. Mikrofluidiska droppchips har utmärkt optisk transparens för tydlig avbildning. Avancerade hydrofoba beläggningsbehandlingar gör att vatten-i-olja-droppar kan genereras såväl som olja-i-vattendroppar som bildas i de obehandlade flisen. MICROFLUIDIC MIXER CHIPS: Möjliggör blandning av två vätskeströmmar inom millisekunder, mikromixerchips gynnar ett brett spektrum av applikationer inklusive reaktionskinetik, provspädning, snabb kristallisation och nanopartikelsyntes. ENKEL MIKROFLUIDISK KANAL-chips: AGS-TECH Inc. erbjuder enkanaliga mikrofluidchips med ett inlopp och ett utlopp för flera applikationer. Två olika spåndimensioner finns tillgängliga från hyllan (66x33 mm och 45x15 mm). Vi har även kompatibla chipshållare i lager. CROSS MICROFLUIDIC CHANNEL CHIPS: Vi erbjuder även mikrofluidiska chips med två enkla kanaler som korsar varandra. Idealisk för droppgenerering och flödesfokuseringstillämpningar. Standard spånmått är 45x15mm och vi har en kompatibel spånhållare. T-JUNCTION CHIPS: T-Junction är en grundläggande geometri som används i mikrofluidik för vätskekontakt och droppbildning. Dessa mikrofluidchip finns tillgängliga i ett antal former inklusive tunnskikts-, kvarts-, platinabelagda, hydrofoba och hydrofila versioner. Y-JUNCTION CHIPS: Dessa är mikroflödesanordningar av glas designade för ett brett spektrum av applikationer, inklusive vätske-vätskekontakt och diffusionsstudier. Dessa mikrofluidiska enheter har två anslutna Y-junctions och två raka kanaler för observation av mikrokanalflödet. MICROFLUIDIC REACTOR CHIPS: Mikroreaktorchips är kompakta mikrofluidiska glasanordningar utformade för snabb blandning och reaktion av två eller tre flytande reagensströmmar. WELLPLATE CHIPS: Detta är ett verktyg för analytisk forskning och kliniska diagnostiska laboratorier. Wellplate-chips är för att hålla små droppar av reagenser eller grupper av celler i nanolitersbrunnar. MEMBRANENHETER: Dessa membrananordningar är designade för att användas för vätske-vätskeseparation, kontakt eller extraktion, tvärflödesfiltrering och ytkemi. Dessa enheter drar nytta av en låg dödvolym och ett engångsmembran. MIKROFLUIDISKA ÅTERFÖRSÄLLA chips: Designade för mikrofluidiska chips som kan öppnas och återförslutas, de återförslutningsbara chipsen möjliggör upp till åtta fluidiska och åtta elektriska anslutningar och avsättning av reagenser, sensorer eller celler på kanalytan. Vissa applikationer är cellodling och analys, impedansdetektering och biosensortestning. POROUS MEDIA CHIPS: Detta är en mikrofluidisk anordning av glas designad för statistisk modellering av en komplex porös stenstruktur i sandsten. Bland tillämpningarna för detta mikrofluidiska chip finns forskning inom geovetenskap och teknik, petrokemisk industri, miljötester, grundvattenanalys. KAPILLÄR ELEKTROFORES-CHIP (CE-chip): Vi erbjuder kapillärelektroforeschips med och utan integrerade elektroder för DNA-analys och separation av biomolekyler. Kapillärelektroforeschips är kompatibla med inkapslar med dimensionerna 45x15 mm. Vi har CE-chips en med klassisk korsning och en med T-korsning. Alla nödvändiga tillbehör som chiphållare, kontakter finns tillgängliga. Förutom mikrofluidchip erbjuder AGS-TECH ett brett utbud av pumpar, slangar, mikrofluidsystem, kopplingar och tillbehör. Några vanliga mikrofluidsystem är: MICROFLUIDIC DROPLET STARTER SYSTEM: Sprutbaserat droppstartsystem ger en komplett lösning för generering av monodispergerade droppar som sträcker sig från 10 till 250 mikron diameter. Det kemiskt resistenta mikrofluidiksystemet fungerar över breda flödesintervall mellan 0,1 mikroliter/min och 10 mikroliter/min och är idealiskt för inledande konceptarbete och experiment. Det tryckbaserade droppstartsystemet är å andra sidan ett verktyg för förarbete inom mikrofluidik. Systemet tillhandahåller en komplett lösning som innehåller alla nödvändiga pumpar, kopplingar och mikrofluidchip som möjliggör produktion av mycket monodispergerade droppar från 10 till 150 mikron. Detta system fungerar över ett brett tryckområde mellan 0 och 10 bar och är kemiskt resistent och dess modulära design gör det enkelt att expandera för framtida applikationer. Genom att tillhandahålla ett stabilt vätskeflöde eliminerar denna modulära verktygssats dödvolym och provavfall för att effektivt minska associerade reagenskostnader. Detta mikrofluidsystem erbjuder möjligheten att ge en snabb vätskebyte. En låsbar tryckkammare och ett innovativt 3-vägs kammarlock tillåter samtidig pumpning av upp till tre vätskor. AVANCERAD MIKROFLUIDISKT DROPPESYSTEM: Ett modulärt mikrofluidsystem som möjliggör produktion av droppar, partiklar, emulsioner och bubblor i extremt konsekvent storlek. Det avancerade mikrofluidiska droppsystemet använder flödesfokuseringsteknik i ett mikrofluidchip med ett pulslöst vätskeflöde för att producera monodispergerade droppar mellan nanometer och hundratals mikron storlek. Väl lämpad för inkapsling av celler, framställning av pärlor, styrning av nanopartikelbildning etc. Droppstorlek, flödeshastigheter, temperaturer, blandningsövergångar, ytegenskaper och ordningsföljd för tillsatser kan snabbt varieras för processoptimering. Mikrofluidsystemet innehåller alla nödvändiga delar inklusive pumpar, flödessensorer, chips, kontakter och automationskomponenter. Tillbehör finns också tillgängliga, inklusive optiska system, större reservoarer och reagenssatser. Vissa mikrofluidikapplikationer för detta system är inkapsling av celler, DNA och magnetiska pärlor för forskning och analys, läkemedelsleverans via polymerpartiklar och läkemedelsformulering, precisionstillverkning av emulsioner och skum för livsmedel och kosmetika, produktion av färger och polymerpartiklar, mikrofluidikforskning om droppar, emulsioner, bubblor och partiklar. MICROFLUIDIC SMALL DROPLET SYSTEM: Ett idealiskt system för att producera och analysera mikroemulsioner som erbjuder ökad stabilitet, en högre gränsyta och förmågan att solubilisera både vattenhaltiga och oljelösliga föreningar. Små droppar mikrofluidiska chips tillåter generering av mycket monodispergerade mikrodroppar som sträcker sig från 5 till 30 mikron. MICROFLUIDIC PARALLELL DROPLET SYSTEM: Ett system med hög genomströmning för produktion av upp till 30 000 monodispergerade mikrodroppar per sekund från 20 till 60 mikron. Det mikrofluidiska parallella droppsystemet tillåter användare att skapa stabila vatten-i-olja- eller olja-i-vattendroppar som underlättar ett brett spektrum av tillämpningar inom läkemedels- och livsmedelsproduktion. MIKROFLUIDISKT DROPPSAMLINGSSYSTEM: Detta system är väl lämpat för generering, insamling och analys av monodispergerade emulsioner. Det mikrofluidiska droppuppsamlingssystemet har droppuppsamlingsmodulen som gör att emulsioner kan samlas upp utan flödesavbrott eller droppsammansättning. Den mikrofluidiska droppstorleken kan justeras exakt och snabbt ändras vilket möjliggör full kontroll över emulsionsegenskaperna. MICROFLUIDIC MICROMIXER SYSTEM: Detta system är tillverkat av en mikrofluidisk enhet, precisionspumpning, mikrofluidiska element och mjukvara för att erhålla utmärkt blandning. En lamineringsbaserad kompakt mikroblandningsglasmikrofluidanordning möjliggör snabb blandning av två eller tre vätskeströmmar i var och en av de två oberoende blandningsgeometrierna. Perfekt blandning kan uppnås med denna mikrofluidiska enhet vid både höga och låga flödesförhållanden. Den mikrofluidiska enheten och dess omgivande komponenter erbjuder utmärkt kemisk stabilitet, hög synlighet för optik och god optisk transmission. Mikromixersystemet fungerar exceptionellt snabbt, arbetar i kontinuerligt flödesläge och kan helt blanda två eller tre vätskeströmmar inom millisekunder. Vissa tillämpningar av denna mikrofluidiska blandningsanordning är reaktionskinetik, provspädning, förbättrad reaktionsselektivitet, snabb kristallisering och nanopartikelsyntes, cellaktivering, enzymreaktioner och DNA-hybridisering. MICROFLUIDIC DROPLET-ON-DEMAND-SYSTEM: Detta är ett kompakt och portabelt droplet-on-demand mikrofluidsystem för att generera droppar på upp till 24 olika prover och lagra upp till 1000 droppar med storlekar ner till 25 nanoliter. Det mikrofluidiska systemet erbjuder utmärkt kontroll av droppstorlek och frekvens samt tillåter användning av flera reagenser för att skapa komplexa analyser snabbt och enkelt. Mikrofluiddroppar kan lagras, termiskt cykla, slås samman eller delas från nanoliter till pikoliterdroppar. Vissa tillämpningar är generering av screeningbibliotek, cellinkapsling, inkapsling av organismer, automatisering av ELISA-tester, framställning av koncentrationsgradienter, kombinatorisk kemi, cellanalyser. NANOPARTIKEL SYNTESSYSTEM: Nanopartiklar är mindre än 100nm och gynnar en rad applikationer såsom syntes av kiselbaserade fluorescerande nanopartiklar (kvantprickar) för att märka biomolekyler för diagnostiska ändamål, läkemedelsleverans och cellulär avbildning. Mikrofluidikteknologi är idealisk för syntes av nanopartiklar. Den minskar reagensförbrukningen och möjliggör snävare partikelstorleksfördelningar, förbättrad kontroll över reaktionstider och temperaturer, samt bättre blandningseffektivitet. SYSTEM FÖR TILLVERKNING AV MIKROFLUIDISKA DROPPAR: Mikrofluidsystem med hög genomströmning som underlättar produktion av upp till ett ton höggradigt monodispergerade droppar, partiklar eller emulsion per månad. Detta modulära, skalbara och mycket flexibla mikrofluidsystem gör att upp till 10 moduler kan monteras parallellt, vilket möjliggör identiska förhållanden för upp till 70 mikrofluidiska chipdroppsövergångar. Massproduktion av mycket monodispergerade mikrofluiddroppar som sträcker sig mellan 20 mikron och 150 mikron är möjlig som kan rinna direkt från chipsen eller in i rör. Tillämpningar inkluderar partikelproduktion - PLGA, gelatin, alginat, polystyren, agaros, läkemedelsleverans i krämer, aerosoler, bulkprecisionstillverkning av emulsioner och skum i livsmedel, kosmetika, färgindustri, nanopartikelsyntes, parallell mikroblandning och mikroreaktioner. TRYCKDRIVT MIKROFLUIDISKT FLÖDESKONTROLLSYSTEM: Den smarta flödeskontrollen med sluten slinga ger kontroll av flödeshastigheter från nanoliter/min till milliliter/min, vid tryck från 10 bar ner till vakuum. En flödessensor ansluten in-line mellan pumpen och mikrofluidenheten gör det lättare för användare att ange ett flödesmål direkt på pumpen utan att behöva en PC. Användare kommer att få jämn tryck och repeterbarhet av volymetriskt flöde i sina mikrofluidiska enheter. Systemen kan utökas till flera pumpar, som alla styr flödeshastigheten oberoende av varandra. För att fungera i flödeskontrollläge måste flödessensorn vara ansluten till pumpen med antingen sensordisplayen eller sensorgränssnittet. CLICK Product Finder-Locator Service FÖREGÅENDE SIDA
- Micromanufacturing, Surface & Bulk Micromachining, Microscale, MEMS
Micromanufacturing - Surface & Bulk Micromachining - Microscale Manufacturing - MEMS - Accelerometers - AGS-TECH Inc. Microscale Manufacturing / Micromanufacturing / Micromachining / MEMS MICROMANUFACTURING, MICROSCALE MANUFACTURING, MICROFABRICATION or MICROMACHINING refers to our processes suitable for making tiny devices and products in the micron or microns of dimensions. Ibland kan de övergripande dimensionerna för en mikrotillverkad produkt vara större, men vi använder fortfarande denna term för att referera till de principer och processer som är involverade. Vi använder mikrotillverkningsmetoden för att tillverka följande typer av enheter: Mikroelektroniska enheter: Typiska exempel är halvledarchips som fungerar baserat på elektriska och elektroniska principer. Mikromekaniska enheter: Dessa är produkter som är rent mekaniska till sin natur, såsom mycket små växlar och gångjärn. Mikroelektromekaniska enheter: Vi använder mikrotillverkningstekniker för att kombinera mekaniska, elektriska och elektroniska element i mycket små skalor. De flesta av våra sensorer är i denna kategori. Mikroelektromekaniska system (MEMS): Dessa mikroelektromekaniska enheter innehåller också ett integrerat elektriskt system i en produkt. Våra populära kommersiella produkter i denna kategori är MEMS accelerometrar, krockkuddesensorer och digitala mikrospegelenheter. Beroende på produkten som ska tillverkas använder vi en av följande stora mikrotillverkningsmetoder: BULK MICROMACHINING: Detta är en relativt äldre metod som använder orienteringsberoende etsningar på enkristallkisel. Tillvägagångssättet för bulkmikrobearbetning är baserat på nedetsning i en yta och stopp på vissa kristallytor, dopade områden och etsbara filmer för att bilda den erforderliga strukturen. Typiska produkter som vi kan mikrotillverka med hjälp av bulkmikrobearbetningsteknik är: - Små konsoler - V-räfflor i kisel för uppriktning och fixering av optiska fibrer. YTMIKROMARBEJDNING: Tyvärr är bulkmikrobearbetning begränsad till enkristallmaterial, eftersom polykristallina material inte kommer att bearbetas med olika hastigheter i olika riktningar med våta etsmedel. Därför sticker ytmikrobearbetning ut som ett alternativ till bulkmikrobearbetning. Ett distans- eller offerskikt såsom fosfosilikatglas avsätts med användning av CVD-process på ett kiselsubstrat. Generellt sett avsätts strukturella tunna filmskikt av polykisel, metall, metallegeringar, dielektrikum på distansskiktet. Med hjälp av torretsningstekniker mönstras de strukturella tunna filmskikten och våtetsning används för att ta bort offerskiktet, vilket resulterar i fristående strukturer såsom konsoler. Det är också möjligt att använda kombinationer av bulk- och ytmikrobearbetningstekniker för att omvandla vissa mönster till produkter. Typiska produkter lämpliga för mikrotillverkning med en kombination av ovanstående två tekniker: - Mikrolampor av submilimetrisk storlek (i storleksordningen 0,1 mm) - Trycksensorer - Mikropumpar - Mikromotorer - Ställdon - Mikrovätskeflödesanordningar Ibland, för att erhålla höga vertikala strukturer, utförs mikrotillverkning på stora plana strukturer horisontellt och sedan roteras eller viks strukturerna till ett upprätt läge med hjälp av tekniker som centrifugering eller mikrosammansättning med sonder. Ändå kan mycket höga strukturer erhållas i enkristallkisel med användning av kiselfusionsbindning och djupreaktiv jonetsning. Deep Reactive Ion Etching (DRIE) mikrotillverkningsprocess utförs på två separata wafers, sedan inriktade och fusionsbundna för att producera mycket höga strukturer som annars skulle vara omöjliga. LIGA MICROMOMTILLVERKNINGSPROCESSER: LIGA-processen kombinerar röntgenlitografi, elektroavsättning, gjutning och involverar i allmänhet följande steg: 1. Ett par hundra mikrometer tjockt polymetylmetakrylat (PMMA) resistskikt avsätts på det primära substratet. 2. PMMA utvecklas med hjälp av kollimerad röntgenstrålning. 3. Metall avsätts elektrolytiskt på det primära substratet. 4. PMMA avskalas och en fristående metallstruktur finns kvar. 5. Vi använder den återstående metallstrukturen som form och utför formsprutning av plast. Om du analyserar de grundläggande fem stegen ovan, med hjälp av LIGA mikrotillverkning / mikrobearbetningstekniker kan vi få: - Fristående metallkonstruktioner - Formsprutade plaststrukturer - Med hjälp av formsprutad struktur som ett ämne kan vi placera gjutna metalldelar eller slipgjutna keramiska delar. LIGA mikrotillverkning / mikrobearbetningsprocesser är tidskrävande och dyra. Men LIGA mikrobearbetning producerar dessa submikron precisionsformar som kan användas för att replikera de önskade strukturerna med distinkta fördelar. LIGA mikrotillverkning kan till exempel användas för att tillverka mycket starka miniatyrmagneter från pulver av sällsynta jordartsmetaller. Pulvren av sällsynta jordartsmetaller blandas med ett epoxibindemedel och pressas till PMMA-formen, härdas under högt tryck, magnetiseras under starka magnetiska fält och slutligen löses PMMA och lämnar kvar de små starka sällsynta jordartsmagneterna som är ett av underverken i mikrotillverkning / mikrobearbetning. Vi är också kapabla att utveckla MEMS-mikrotillverkning/mikrobearbetningstekniker på flera nivåer genom diffusionsbindning i waferskala. I grund och botten kan vi ha överhängande geometrier inom MEMS-enheter, med hjälp av en batchdiffusionsbindning och frigöringsprocedur. Till exempel förbereder vi två PMMA-mönstrade och elektroformade skikt med PMMA släppt. Därefter riktas skivorna ansikte mot ansikte med styrstift och presspassas ihop i en varmpress. Offerskiktet på ett av substraten etsas bort vilket resulterar i att ett av skikten binds till det andra. Andra icke-LIGA-baserade mikrotillverkningstekniker är också tillgängliga för oss för tillverkning av olika komplexa flerskiktsstrukturer. SOLID FRIFORM MIKROFABBRIKATIONSPROCESSER: Additiv mikrotillverkning används för snabb prototypframställning. Komplexa 3D-strukturer kan erhållas med denna mikrobearbetningsmetod och ingen materialborttagning sker. Mikrostereolitografiprocessen använder flytande värmehärdande polymerer, fotoinitiator och en högfokuserad laserkälla till en diameter så liten som 1 mikron och skikttjocklek på cirka 10 mikron. Denna mikrotillverkningsteknik är emellertid begränsad till produktion av icke-ledande polymerstrukturer. En annan mikrotillverkningsmetod, nämligen "instant maskering" eller även känd som "elektrokemisk tillverkning" eller EFAB involverar tillverkning av en elastomer mask med hjälp av fotolitografi. Masken pressas sedan mot substratet i ett elektroavsättningsbad så att elasten anpassar sig till substratet och utesluter pläteringslösning i kontaktområden. Områden som inte är maskerade elektrodeponeras som spegelbilden av masken. Med hjälp av ett offerfyllmedel mikrotillverkas komplexa 3D-former. Denna "instant maskering" mikrotillverkning / mikrobearbetningsmetod gör det också möjligt att producera överhäng, bågar...etc. CLICK Product Finder-Locator Service FÖREGÅENDE SIDA
- Soft Lithography - Microcontact Printing - Microtransfer Molding
Soft Lithography - Microcontact Printing - Microtransfer Molding - Micromolding in Capillaries - AGS-TECH Inc. - NM - USA Mjuk litografi SOFT LITHOGRAPHY är en term som används för ett antal processer för mönsteröverföring. En masterform behövs i alla fall och är mikrotillverkad med standard litografimetoder. Med hjälp av masterformen producerar vi ett elastomermönster/stämpel som ska användas i mjuk litografi. Elastomerer som används för detta ändamål måste vara kemiskt inerta, ha god termisk stabilitet, styrka, hållbarhet, ytegenskaper och vara hygroskopiska. Silikongummi och PDMS (Polydimetylsiloxan) är två bra kandidatmaterial. Dessa stämplar kan användas många gånger i mjuk litografi. En variant av mjuk litografi är MICROCONTACT PRINTING. Elastomerstämpeln är belagd med bläck och pressas mot en yta. Mönstertopparna kommer i kontakt med ytan och ett tunt lager av cirka 1 monolager av bläcket överförs. Detta tunna filmmonoskikt fungerar som masken för selektiv våtetsning. En andra variant är MICROTRANSFER MOLDING, där urtagen i elastomerformen fylls med flytande polymerprekursor och trycks mot en yta. När polymeren härdar efter mikrotransferformning, skalar vi av formen och lämnar det önskade mönstret. Slutligen en tredje variant är MICROMOLDING IN CAPILLARIES, där elastomerstämpelmönstret består av kanaler som använder kapillärkrafter för att suga in en flytande polymer i stämpeln från dess sida. I grund och botten placeras en liten mängd av den flytande polymeren intill kapillärkanalerna och kapillärkrafterna drar vätskan in i kanalerna. Överskott av flytande polymer avlägsnas och polymer inuti kanalerna tillåts härda. Stämpelformen skalas av och produkten är klar. Om kanalbildförhållandet är måttligt och de tillåtna kanaldimensionerna beror på vilken vätska som används, kan en god mönsterreplikering garanteras. Vätskan som används vid mikrogjutning i kapillärer kan vara värmehärdande polymerer, keramisk sol-gel eller suspensioner av fasta ämnen i flytande lösningsmedel. Tekniken för mikrogjutning i kapillärer har använts vid sensortillverkning. Mjuk litografi används för att konstruera egenskaper som mäts på mikrometer till nanometerskala. Mjuk litografi har fördelar jämfört med andra former av litografi som fotolitografi och elektronstrålelitografi. Fördelarna inkluderar följande: • Lägre kostnad vid massproduktion än traditionell fotolitografi • Lämplighet för tillämpningar inom bioteknik och plastelektronik • Lämplighet för applikationer som involverar stora eller icke plana (icke platta) ytor • Mjuk litografi erbjuder fler mönsteröverföringsmetoder än traditionella litografitekniker (fler "bläck"-alternativ) • Mjuk litografi behöver ingen fotoreaktiv yta för att skapa nanostrukturer • Med mjuk litografi kan vi uppnå mindre detaljer än fotolitografi i laboratoriemiljöer (~30 nm vs ~100 nm). Upplösningen beror på vilken mask som används och kan nå värden ner till 6 nm. MJUK FLERLAGERSLITOGRAFI är en tillverkningsprocess där mikroskopiska kammare, kanaler, ventiler och vior gjuts i bundna lager av elastomerer. Användning av flerskikts mjuk litografianordningar som består av flera skikt kan tillverkas av mjuka material. Mjukheten hos dessa material gör att enhetens ytor kan reduceras med mer än två storleksordningar jämfört med silikonbaserade enheter. De andra fördelarna med mjuk litografi, såsom snabb prototypframställning, enkel tillverkning och biokompatibilitet, är också giltiga i mjuk litografi i flera lager. Vi använder den här tekniken för att bygga aktiva mikrofluidsystem med på-av-ventiler, omkopplingsventiler och pumpar helt av elastomerer. CLICK Product Finder-Locator Service FÖREGÅENDE SIDA
- Solar Power Modules, Rigid, Flexible Panels, Thin Film, Monocrystaline
Solar Power Modules - Rigid - Flexible Panels - Thin Film - Monocrystalline - Polycrystalline - Solar Connector available from AGS-TECH Inc. Tillverkning och montering av kundanpassade solenergisystem Vi levererar: • Solenergiceller och paneler, solenergidrivna enheter och anpassade sammansättningar för att skapa alternativ energi. Solenergiceller kan vara den bästa lösningen för fristående utrustning som är placerad i avlägsna områden genom att själv driva din utrustning eller enheter. Eliminering av högt underhåll på grund av batteribyte, eliminering av behovet av att installera strömkablar för att ansluta din utrustning till huvudkraftledningar kan ge ett stort marknadsföringslyft till dina produkter. Tänk på det när du designar fristående utrustning för att placeras i avlägsna områden. Dessutom kan solenergi spara pengar genom att minska ditt beroende av köpt elenergi. Kom ihåg att solenergiceller kan vara flexibla eller stela. Lovande forskning pågår om spray-on solceller. Energin som genereras av solenergiapparater lagras vanligtvis i batterier eller används direkt efter generering. Vi kan förse dig med solceller, paneler, solbatterier, växelriktare, solenergikontakter, kabelmontage, hela solenergisatser för dina projekt. Vi kan också hjälpa dig under designfasen av din solcellsenhet. Genom att välja rätt komponenter, rätt solcellstyp och kanske använda optiska linser, prismor...osv. vi kan maximera mängden energi som genereras av solcellerna. Att maximera solenergin när tillgängliga ytor på din enhet är begränsade kan vara en utmaning. Vi har rätt expertis och optiska designverktyg för att uppnå detta. Ladda ner broschyr för vår DESIGN PARTNERSKAP PROGRAM Se till att ladda ner vår omfattande katalog över elektriska och elektroniska komponenter för hyllprodukter genom att KLICKA HÄR . Denna katalog har produkter som solkontakter, batterier, omvandlare och mer för dina solenergirelaterade projekt. Om du inte hittar den där, kontakta oss så skickar vi information om vad vi har att tillgå. Om du mest är intresserad av våra storskaliga förnybara alternativa energiprodukter och system för inhemsk eller allmännyttig skala inklusive solsystem, då bjuder vi in dig att besöka vår energisajt http://www.ags-energy.com CLICK Product Finder-Locator Service FÖREGÅENDE SIDA
- Industrial Computers, Industrial PC, Rugged Computer, Janz Tec,Korenix
Industrial Computers - Industrial PC - Rugged Computer - Janz Tec - Korenix - AGS-TECH Inc. - New Mexico - USA Industriell PC Industriella datorer används mest för PROCESSKONTROLL och/eller DATAFÖRSÄMLING. Ibland används en INDUSTRI-PC helt enkelt som en front-end till en annan kontrolldator i en distribuerad bearbetningsmiljö. Anpassad programvara kan skrivas för en viss applikation, eller om tillgängligt kan ett paket från hyllan användas för att tillhandahålla en grundläggande programmeringsnivå. Bland de industriella PC-märken vi erbjuder är JANZ TEC från Tyskland. En applikation kan helt enkelt kräva I/O som den seriella porten som tillhandahålls av moderkortet. I vissa fall installeras expansionskort för att tillhandahålla analog och digital I/O, specifikt maskingränssnitt, utökade kommunikationsportar, etc., som krävs av applikationen. Industridatorer erbjuder funktioner som skiljer sig från konsumentdatorer när det gäller tillförlitlighet, kompatibilitet, expansionsmöjligheter och långsiktigt utbud. Industridatorer tillverkas i allmänhet i mindre volymer än hem- eller kontorsdatorer. En populär kategori av industriella PC är 19-tums RACKMOUNT FORM FACTOR. Industriella datorer är vanligtvis dyrare än jämförbara datorer i kontorsstil med liknande prestanda. SINGLE-BOARD DATORER och BACKPLANES används främst i industriella PC-system. Men majoriteten av industriella datorer är tillverkade med COTS MODERBORD. Konstruktion och funktioner för industriella datorer: Praktiskt taget alla industriella PC-datorer delar en underliggande designfilosofi att tillhandahålla en kontrollerad miljö för den installerade elektroniken för att överleva påfrestningarna på fabriksgolvet. De elektroniska komponenterna själva kan väljas för deras förmåga att motstå högre och lägre driftstemperaturer än typiska kommersiella komponenter. - Tyngre och robust metallkonstruktion jämfört med en typisk kontorsdator som inte är robust - Kapslingsformfaktor som inkluderar möjlighet för montering i den omgivande miljön (som 19-tumsställ, väggfäste, panelfäste, etc.) - Ytterligare kyla med luftfiltrering - Alternativa kylmetoder som att använda forcerad luft, en vätska och/eller ledning - Retention och support av expansionskort - Förbättrad elektromagnetisk störning (EMI) filtrering och packning - Förbättrat miljöskydd såsom dammskydd, vattenspray eller nedsänkningsskydd, etc. - Förseglade MIL-SPEC eller Circular-MIL-kontakter - Mer robusta kontroller och funktioner - Strömförsörjning av högre kvalitet - Lägre förbrukning 24 V strömförsörjning designad för användning med DC UPS - Kontrollerad åtkomst till kontrollerna genom användning av låsdörrar - Kontrollerad åtkomst till I/O genom användning av åtkomstskydd - Inkludering av en watchdog-timer för att återställa systemet automatiskt i händelse av en mjukvarulåsning Ladda ner vår ATOP TECHNOLOGIES kompakt produktbroschyr (Ladda ner ATOP Technologies Product List 2021) Ladda ner vår kompakta produktbroschyr av märket JANZ TEC Ladda ner vår kompakta produktbroschyr av märket KORENIX Ladda ner vårt varumärke DFI-ITOX Broschyr för industriella moderkort Ladda ner vår broschyr för inbyggda enkortsdatorer av märket DFI-ITOX Ladda ner vår ICP DAS varumärke PACs inbyggda styrenheter & DAQ broschyr För att välja en lämplig industriell PC för ditt projekt, gå till vår industridatorbutik genom att KLICKA HÄR. Ladda ner broschyr för vår DESIGN PARTNERSKAP PROGRAM Några av våra populära industriella PC-produkter från Janz Tec AG är: - FLEXIBLA 19'' RACK MONTERINGSSYSTEM: Arbetsområdena och kraven för 19'' system är mycket breda inom branschen. Du kan välja mellan industriell huvudkortsteknik och slot CPU-teknik med hjälp av ett passivt bakplan. - PLASSBESPARANDE VÄGGMONTERINGSSYSTEM: Vår ENDEAVOUR-serie är flexibla industridatorer som innehåller industriella komponenter. Som standard används slot CPU-kort med passiv bakplansteknik. Du kan välja den produkt som matchar dina krav, eller så kan du ta reda på mer om individuella varianter av denna produktfamilj genom att kontakta oss. Våra Janz Tec industridatorer kan kombineras med konventionella industriella styrsystem eller PLC-styrenheter. CLICK Product Finder-Locator Service FÖREGÅENDE SIDA
- Coating Thickness Gauge, Surface Roughness Tester, Nondestructive Test
Coating Thickness Gauge - Surface Roughness Tester - Nondestructive Testing - SADT - Mitech - AGS-TECH Inc. - NM - USA Beläggning Yttestinstrument Bland våra testinstrument för beläggning och ytutvärdering finns COATING THICKNESS METERS, YTGROVHETSTESTER, GLOSSMÄTARE, FÄRGSLÄSARE, FÄRGSKILDSMÄTARE, MICROLOGISK MÄTARE, MICROLOGISK META. Vårt huvudfokus ligger på NON-DESTRUCTIVE TESTMETODER. Vi har högkvalitativa märken såsom SADTand MITECH. En stor andel av alla ytor runt omkring oss är belagda. Beläggningar tjänar många syften, inklusive bra utseende, skydd och att ge produkterna viss önskad funktionalitet såsom vattenavvisande, förbättrad friktion, slitage- och nötningsbeständighet...etc. Därför är det av avgörande betydelse att kunna mäta, testa och utvärdera egenskaper och kvalitet hos beläggningar och ytor på produkter. Beläggningar kan i stort sett kategoriseras i två huvudgrupper om tjocklekar beaktas: _CC781905-5CDE-3194-BB3B-136BAD5CF58D_THICK FILM_CC781905-5CDE-3194-BAD5B-136BAD5CF588D_ANCD_CC7888811193131313313313313313133333333333333333333333333333333333333333333131313131336b.33136bg. För att ladda ner katalogen för vår SADT-märkesmätning och testutrustning, KLICKA HÄR. I den här katalogen hittar du några av dessa instrument för utvärdering av ytor och beläggningar. För att ladda ner broschyr för Coating Thickness Gauge Mitech Model MCT200, KLICKA HÄR. Några av de instrument och tekniker som används för sådana ändamål är: BEläggningstjockleksmätare : Olika typer av beläggningar kräver olika typer av beläggningstestare. En grundläggande förståelse för de olika teknikerna är därför väsentlig för att användaren ska kunna välja rätt utrustning. I Magnetisk induktionsmetod för beläggningstjockleksmätning mäter vi icke-magnetiska beläggningar över järnhaltiga beläggningssubstrat och magnetiska substrat. Sonden placeras på provet och det linjära avståndet mellan sondspetsen som kommer i kontakt med ytan och bassubstratet mäts. Inuti mätsonden finns en spole som genererar ett föränderligt magnetfält. När sonden placeras på provet, ändras den magnetiska flödestätheten för detta fält av tjockleken på en magnetisk beläggning eller närvaron av ett magnetiskt substrat. Förändringen i magnetisk induktans mäts av en sekundär spole på sonden. Utsignalen från den sekundära spolen överförs till en mikroprocessor, där den visas som en beläggningstjockleksmätning på den digitala displayen. Detta snabbtest är lämpligt för flytande eller pulverlackering, plätering som krom, zink, kadmium eller fosfat över stål- eller järnsubstrat. Beläggningar som färg eller pulver tjockare än 0,1 mm är lämpliga för denna metod. Den magnetiska induktionsmetoden är inte väl lämpad för nickel över stålbeläggningar på grund av nickels partiella magnetiska egenskaper. Faskänslig virvelströmsmetod är mer lämplig för dessa beläggningar. En annan typ av beläggning där den magnetiska induktionsmetoden är benägen att misslyckas är zinkgalvaniserat stål. Sonden kommer att läsa en tjocklek som är lika med den totala tjockleken. Nyare modellinstrument kan självkalibrera genom att detektera substratmaterialet genom beläggningen. Detta är naturligtvis till stor hjälp när ett bart substrat inte är tillgängligt eller när substratmaterialet är okänt. Billigare utrustningsversioner kräver dock kalibrering av instrumentet på ett blott och obelagt underlag. The Eddy Current Metod för beläggningstjockleksmätning measures vissa ledande beläggningar på icke ledande metallbeläggningar på icke-järnhaltiga substrat och icke ledande metallbeläggningar på icke ledande metaller och icke ledande metallbeläggningar på icke ledande metallbeläggningar och icke ledande metallbeläggningar på icke ledande metaller Den liknar den tidigare nämnda magnetiska induktiva metoden som innehåller en spole och liknande sonder. Spolen i virvelströmsmetoden har den dubbla funktionen av excitation och mätning. Denna sondspole drivs av en högfrekvent oscillator för att generera ett alternerande högfrekvent fält. När den placeras nära en metallisk ledare genereras virvelströmmar i ledaren. Impedansförändring sker i sondspolen. Avståndet mellan sondspolen och det ledande substratmaterialet bestämmer mängden impedansförändring, som kan mätas, korreleras till en beläggningstjocklek och visas i form av en digital avläsning. Tillämpningar inkluderar flytande eller pulverlackering på aluminium och icke-magnetiskt rostfritt stål, och anodisering över aluminium. Denna metods tillförlitlighet beror på detaljens geometri och beläggningens tjocklek. Substratet måste vara känt innan avläsningar görs. Virvelströmssonder bör inte användas för att mäta icke-magnetiska beläggningar över magnetiska substrat som stål och nickel över aluminiumsubstrat. Om användare måste mäta beläggningar över magnetiska eller icke-järnhaltiga ledande substrat är de bäst betjänta med en dubbel magnetisk induktions-/virvelströmmätare som automatiskt känner igen substratet. En tredje metod, kallad the Coulometric metod för beläggningstjockleksmätning, är en destruktiv testmetod som har många viktiga funktioner. Att mäta duplexa nickelbeläggningar inom bilindustrin är en av dess stora tillämpningar. I den kulometriska metoden bestäms vikten av ett område med känd storlek på en metallisk beläggning genom lokal anodisk strippning av beläggningen. Massan per ytenhet för beläggningstjockleken beräknas sedan. Denna mätning på beläggningen görs med användning av en elektrolyscell, som är fylld med en elektrolyt som är speciellt vald för att strippa den speciella beläggningen. En konstant ström går genom testcellen, och eftersom beläggningsmaterialet fungerar som anod, blir det deplaterat. Strömtätheten och ytarean är konstanta, och därmed är beläggningens tjocklek proportionell mot den tid det tar att skala och ta bort beläggningen. Denna metod är mycket användbar för att mäta elektriskt ledande beläggningar på ett ledande substrat. Den coulometriska metoden kan också användas för att bestämma beläggningstjockleken för flera skikt på ett prov. Till exempel kan tjockleken av nickel och koppar mätas på en del med en toppbeläggning av nickel och en mellanliggande kopparbeläggning på ett stålsubstrat. Ett annat exempel på en flerskiktsbeläggning är krom över nickel över koppar ovanpå ett plastsubstrat. Coulometrisk testmetod är populär i galvaniseringsanläggningar med ett litet antal slumpmässiga prover. Ännu en fjärde metod är Beta Backscatter-metoden för att mäta beläggningstjocklekar. En beta-emitterande isotop bestrålar ett testprov med beta-partiklar. En stråle av beta-partiklar riktas genom en öppning på den belagda komponenten, och en del av dessa partiklar sprids tillbaka som förväntat från beläggningen genom öppningen för att penetrera det tunna fönstret i ett Geiger Muller-rör. Gasen i Geiger Muller-röret joniseras, vilket orsakar en tillfällig urladdning över rörelektroderna. Urladdningen som är i form av en puls räknas och översätts till en beläggningstjocklek. Material med högt atomnummer sprider beta-partiklarna mer. För ett prov med koppar som substrat och en guldbeläggning på 40 mikron tjock, sprids beta-partiklarna av både substratet och beläggningsmaterialet. Om guldbeläggningens tjocklek ökar, ökar även återspridningshastigheten. Förändringen i graden av spridda partiklar är därför ett mått på beläggningens tjocklek. Applikationer som är lämpliga för beta-backscatter-metoden är de där atomnumret på beläggningen och substratet skiljer sig med 20 procent. Dessa inkluderar guld, silver eller tenn på elektroniska komponenter, beläggningar på verktygsmaskiner, dekorativa pläteringar på VVS-armaturer, ångavsatta beläggningar på elektroniska komponenter, keramik och glas, organiska beläggningar som olja eller smörjmedel över metaller. Beta-backscatter-metoden är användbar för tjockare beläggningar och för substrat- och beläggningskombinationer där magnetisk induktion eller virvelströmmetoder inte fungerar. Förändringar i legeringar påverkar beta-backscatter-metoden, och olika isotoper och flera kalibreringar kan behövas för att kompensera. Ett exempel skulle vara tenn/bly över koppar, eller tenn över fosfor/brons välkänt i kretskort och kontaktstift, och i dessa fall skulle förändringarna i legeringar mätas bättre med den dyrare röntgenfluorescensmetoden. The röntgenfluorescensmetoden för att mäta beläggningstjocklek är en beröringsfri metod som tillåter mätning av alla skikt av mycket tunna delar och mycket tunna delar. Delar utsätts för röntgenstrålning. En kollimator fokuserar röntgenstrålarna på ett exakt definierat område av testprovet. Denna röntgenstrålning orsakar karakteristisk röntgenstrålning (dvs. fluorescens) från både beläggningen och substratmaterialen på testprovet. Denna karakteristiska röntgenstrålning detekteras med en energidispersiv detektor. Med hjälp av lämplig elektronik är det möjligt att endast registrera röntgenstrålningen från beläggningsmaterialet eller substratet. Det är också möjligt att selektivt detektera en specifik beläggning när mellanskikt finns. Denna teknik används ofta på kretskort, smycken och optiska komponenter. Röntgenfluorescensen är inte lämplig för organiska beläggningar. Den uppmätta beläggningens tjocklek bör inte överstiga 0,5-0,8 mils. Men till skillnad från beta-backscatter-metoden kan röntgenfluorescens mäta beläggningar med liknande atomnummer (till exempel nickel över koppar). Som tidigare nämnts påverkar olika legeringar ett instruments kalibrering. Analys av basmaterial och beläggningstjocklek är avgörande för att säkerställa precisionsavläsningar. Dagens system och mjukvara minskar behovet av flera kalibreringar utan att ge avkall på kvaliteten. Slutligen är det värt att nämna att det finns mätare som kan fungera i flera av de ovan nämnda lägena. Vissa har löstagbara sonder för flexibilitet vid användning. Många av dessa moderna instrument erbjuder statistisk analysfunktioner för processkontroll och minimala kalibreringskrav även om de används på olika formade ytor eller olika material. YTGROVHETSTESTERS : Ytjämnhet kvantifieras av avvikelserna i riktningen för en ytas normalvektor från dess ideala form. Om dessa avvikelser är stora anses ytan vara grov; om de är små anses ytan vara slät. Kommersiellt tillgängliga instrument som heter SURFACE PROFILOMETERS används för att mäta och registrera ytjämnhet. Ett av de vanligaste instrumenten har en diamantpenna som rör sig längs en rak linje över ytan. Inspelningsinstrumenten kan kompensera för eventuell ytvågighet och indikerar endast grovhet. Ytjämnhet kan observeras genom a.) Interferometri och b.) Optisk mikroskopi, svepelektronmikroskopi, laser eller atomkraftsmikroskopi (AFM). Mikroskopitekniker är särskilt användbara för att avbilda mycket släta ytor för vilka egenskaper inte kan fångas av mindre känsliga instrument. Stereoskopiska fotografier är användbara för 3D-vyer av ytor och kan användas för att mäta ytjämnhet. 3D ytmätningar kan utföras med tre metoder. Light from an optical-interference microscope shines against a reflective surface and records the interference fringes resulting from the incident and reflected waves. Laser profilometers_cc781905- 5cde-3194-bb3b-136bad5cf58d_ används för att mäta ytor genom antingen interferometriska tekniker eller genom att flytta en objektivlins för att bibehålla en konstant brännvidd över en yta. Linsens rörelse är då ett mått på ytan. Slutligen används den tredje metoden, nämligen mikroskopet atomic-force, för att mäta extremt släta ytor på atomär skala. Med andra ord med denna utrustning kan även atomer på ytan urskiljas. Denna sofistikerade och relativt dyra utrustning skannar ytor på mindre än 100 mikrometer på provytor. GLANSMÄTARE, FÄRGLÄSARE, FÄRGSKILLNADSMÄTARE : A GLOSSMETER reflektion av spemea glans. Ett mått på glans erhålls genom att projicera en ljusstråle med fast intensitet och vinkel på en yta och mäta den reflekterade mängden i en lika stor men motsatt vinkel. Glansmätare används på en mängd olika material som färg, keramik, papper, metall och produktytor av plast. Att mäta glans kan hjälpa företag att kvalitetssäkra sina produkter. Goda tillverkningsmetoder kräver konsekventa processer och detta inkluderar konsekvent ytfinish och utseende. Glansmätningar utförs vid ett antal olika geometrier. Detta beror på ytmaterialet. Till exempel har metaller höga nivåer av reflektion och därför är vinkelberoendet mindre jämfört med icke-metaller som beläggningar och plaster där vinkelberoendet är högre på grund av diffus spridning och absorption. Konfiguration av belysningskälla och observationsmottagningsvinklar möjliggör mätning över ett litet område av den totala reflektionsvinkeln. Mätresultaten för en glansmätare är relaterade till mängden reflekterat ljus från en svart glasstandard med ett definierat brytningsindex. Förhållandet mellan det reflekterade ljuset och det infallande ljuset för testexemplaret, jämfört med förhållandet för glansstandarden, registreras som glansenheter (GU). Mätvinkel avser vinkeln mellan infallande och reflekterat ljus. Tre mätvinklar (20°, 60° och 85°) används för de flesta industriella beläggningar. Vinkeln väljs baserat på det förväntade glansområdet och följande åtgärder vidtas beroende på mätningen: Glansintervall...........60° Värde.......Aktion Högglans............>70 GU..........Om mätningen överstiger 70 GU, ändra testinställningen till 20° för att optimera mätnoggrannheten. Medium glans........10 - 70 GU Låg glans...............<10 GU..........Om mätningen är mindre än 10 GU, ändra testinställningen till 85° för att optimera mätnoggrannheten. Tre typer av instrument finns kommersiellt tillgängliga: 60° enkelvinkelinstrument, en dubbelvinkeltyp som kombinerar 20° och 60° och en trippelvinkeltyp som kombinerar 20°, 60° och 85°. För övriga material används ytterligare två vinklar, vinkeln 45° är specificerad för mätning av keramik, filmer, textil och anodiserad aluminium, medan mätvinkeln 75° är specificerad för papper och tryckta material. A COLOR READER or also referred to as COLORIMETER is a device that measures the absorbance of particular wavelengths of light by en specifik lösning. Kolorimetrar används oftast för att bestämma koncentrationen av ett känt löst ämne i en given lösning genom tillämpning av Beer-Lamberts lag, som säger att koncentrationen av ett löst ämne är proportionell mot absorbansen. Våra bärbara färgläsare kan också användas på plast, målning, plätering, textilier, tryckning, färgtillverkning, mat som smör, pommes frites, kaffe, bakverk och tomater...etc. De kan användas av amatörer som inte har professionell kunskap om färger. Eftersom det finns många typer av färgläsare är applikationerna oändliga. Vid kvalitetskontroll används de främst för att säkerställa att prover faller inom färgtoleranser som ställts in av användaren. För att ge dig ett exempel finns det handhållna tomatkolorimetrar som använder ett USDA-godkänt index för att mäta och gradera färgen på bearbetade tomatprodukter. Ytterligare ett exempel är handhållna kaffekolorimetrar speciellt utformade för att mäta färgen på hela gröna bönor, rostade bönor och rostat kaffe med hjälp av industristandardmätningar. Our COLOR DIFFERENCE METERS visa direkt färgskillnad med E*ab, L*a*b,*c,*CIE_CIE. Standardavvikelsen är inom E*ab0.2 De fungerar på alla färger och testning tar bara några sekunder. METALLURGICAL MICROSCOPES and INVERTED METALLOGRAPHIC MICROSCOPE : Metallurgical microscope is usually an optical microscope, but differs from others in the method of the specimen illumination. Metaller är ogenomskinliga ämnen och därför måste de belysas med frontalbelysning. Därför är ljuskällan placerad i mikroskopröret. Installerad i röret är en vanlig glasreflektor. Typiska förstoringar av metallurgiska mikroskop är i intervallet x50 – x1000. Ljus fältbelysning används för att producera bilder med ljus bakgrund och mörka icke-platta strukturegenskaper som porer, kanter och etsade korngränser. Mörkt fältbelysning används för att producera bilder med mörk bakgrund och ljusa icke-platta strukturfunktioner som porer, kanter och etsade korngränser. Polariserat ljus används för att se metaller med icke-kubisk kristallin struktur som magnesium, alfa-titan och zink, som svarar på korspolariserat ljus. Polariserat ljus produceras av en polarisator som är placerad före belysningsinstrumentet och analysatorn och placerad framför okularet. Ett Nomarsky-prisma används för differentiellt interferenskontrastsystem som gör det möjligt att observera särdrag som inte är synliga i ljusa fält. INVERTED METALLOGRAPHIC MICROSCOPES_cc781905-5cde-3b-136c condenser their source on top , ovanför scenen pekar nedåt, medan målen och tornet är under scenen pekar uppåt. Inverterade mikroskop är användbara för att observera särdrag på botten av en stor behållare under mer naturliga förhållanden än på ett objektglas, vilket är fallet med ett konventionellt mikroskop. Inverterade mikroskop används i metallurgiska applikationer där polerade prover kan placeras ovanpå scenen och ses underifrån med hjälp av reflekterande objektiv och även i mikromanipulationsapplikationer där utrymme ovanför provet krävs för manipulatormekanismer och mikroverktygen de håller. Här är en kort sammanfattning av några av våra testinstrument för utvärdering av ytor och beläggningar. Du kan ladda ner information om dessa från produktkataloglänkarna ovan. Ytgrovhetstestare SADT RoughScan : Detta är ett bärbart, batteridrivet instrument för att kontrollera ytjämnhet med de uppmätta värdena som visas på en digital avläsning. Instrumentet är lätt att använda och kan användas i labbet, tillverkningsmiljöer, i butiker och överallt där ytråhetstestning krävs. SADT GT-SERIEN Glansmätare : GT-seriens glansmätare är designade och tillverkade enligt internationella standarder ISO2813, ASTMD523 och DIN67530. De tekniska parametrarna överensstämmer med JJG696-2002. Glansmätaren GT45 är speciellt designad för att mäta plastfilmer och keramik, små ytor och krökta ytor. SADT GMS/GM60 SERIES Glansmätare : Dessa glansmätare är designade och tillverkade enligt internationella standarder ISO2813, ISO7668, ASTM D523, ASTM D2457. De tekniska parametrarna överensstämmer också med JJG696-2002. Våra glansmätare i GM-serien är väl lämpade för att mäta målning, beläggning, plast, keramik, läderprodukter, papper, trycksaker, golvbeläggningar...etc. Den har en tilltalande och användarvänlig design, trevinklar glansdata visas samtidigt, stort minne för mätdata, senaste bluetooth-funktion och löstagbart minneskort för att överföra data bekvämt, speciell glansmjukvara för att analysera datautgång, lågt batteri och minnesfullt indikator. Genom intern bluetooth-modul och USB-gränssnitt kan GM-glansmätare överföra data till PC eller exporteras till skrivare via utskriftsgränssnitt. Med hjälp av valfria SD-kort kan minnet utökas så mycket som behövs. Precise Color Reader SADT SC 80 : Denna färgläsare används mest på plast, målningar, pläteringar, textilier och kostymer, tryckta produkter och i färgämnesindustrin. Den är kapabel att utföra färganalys. Den 2,4-tums färgskärmen och den bärbara designen erbjuder bekväm användning. Tre typer av ljuskällor för användarval, SCI- och SCE-lägesomkopplare och metamerismanalys tillfredsställer dina testbehov under olika arbetsförhållanden. Toleransinställning, auto-judge färgskillnadsvärden och färgavvikelsefunktioner gör att du enkelt kan bestämma färgen även om du inte har någon professionell kunskap om färger. Med hjälp av professionell färganalysmjukvara kan användare utföra färgdataanalysen och observera färgskillnader på utdatadiagrammen. Tillvalet miniskrivare gör det möjligt för användare att skriva ut färgdata på plats. Bärbar färgskillnadsmätare SADT SC 20 : Denna bärbara färgskillnadsmätare används ofta i kvalitetskontroll av plast- och tryckprodukter. Den används för att fånga färg effektivt och exakt. Lätt att använda, visar färgskillnad med E*ab, L*a*b, CIE_L*a*b, CIE_L*c*h., standardavvikelse inom E*ab0.2, den kan anslutas till datorn via USB-expansionen gränssnitt för inspektion av programvara. Metallurgiskt mikroskop SADT SM500 : Det är ett fristående bärbart metallurgiskt mikroskop som är idealiskt lämpat för metallografisk utvärdering av metaller i laboratorier eller på plats. Bärbar design och unikt magnetiskt stativ, SM500 kan fästas direkt mot ytan av järnmetaller i alla vinklar, planhet, krökning och ytkomplexitet för oförstörande undersökning. SADT SM500 kan också användas med digitalkamera eller CCD bildbehandlingssystem för att ladda ner metallurgiska bilder till PC för dataöverföring, analys, lagring och utskrift. Det är i grunden ett bärbart metallurgiskt laboratorium, med provberedning på plats, mikroskop, kamera och inget behov av AC-strömförsörjning i fält. Naturliga färger utan behov av att ändra ljus genom att dämpa LED-belysningen ger den bästa bilden som observeras när som helst. Detta instrument har valfria tillbehör inklusive extra stativ för små prover, digitalkameraadapter med okular, CCD med gränssnitt, okular 5x/10x/15x/16x, objektiv 4x/5x/20x/25x/40x/100x, minislipmaskin, elektrolytisk polermaskin, en uppsättning hjulhuvuden, hjul för polerduk, replikfilm, filter (grön, blå, gul), glödlampa. Bärbart metallurgrafiskt mikroskop SADT modell SM-3 : Detta instrument erbjuder en speciell magnetisk bas som fixerar enheten stadigt på arbetsstyckena, den är lämplig för storskalig rulltest och direkt observation, ingen skärning och provtagning behövs, LED-belysning, enhetlig färgtemperatur, ingen uppvärmning, framåt/bakåt och vänster/höger rörelsemekanism, bekväm för justering av inspektionspunkten, adapter för att ansluta digitalkameror och observera inspelningarna direkt på PC. Valfria tillbehör liknar SADT SM500-modellen. För detaljer, ladda ner produktkatalogen från länken ovan. Metallurgiskt mikroskop SADT modell XJP-6A : Detta metalloskop kan lätt användas i fabriker, skolor, vetenskapliga forskningsinstitutioner för att identifiera och analysera mikrostrukturen hos alla typer av metaller och legeringar. Det är det idealiska verktyget för att testa metallmaterial, verifiera kvaliteten på gjutgods och analysera metallografiska strukturer hos de metalliserade materialen. Inverterat metallografiskt mikroskop SADT modell SM400 : Designen gör det möjligt att inspektera korn av metallurgiska prover. Enkel installation vid produktionslinjen och lätt att bära. SM400 är lämplig för högskolor och fabriker. En adapter för att fästa digitalkameran på trinokulärt rör finns också. Detta läge kräver MI för den metallografiska bildutskriften med fasta storlekar. Vi har ett urval av CCD-adaptrar för datorutskrift med standardförstoring och över 60 % observationsvy. Inverterat metallografiskt mikroskop SADT-modell SD300M : Oändlig fokuseringsoptik ger högupplösta bilder. Betraktningsobjektiv på långa avstånd, 20 mm brett synfält, treplattors mekaniskt steg som accepterar nästan alla provstorlekar, tunga belastningar och tillåter oförstörande mikroskopundersökning av stora komponenter. Strukturen med tre plattor ger mikroskopets stabilitet och hållbarhet. Optiken ger hög NA och långt betraktningsavstånd, vilket ger ljusa, högupplösta bilder. Den nya optiska beläggningen på SD300M är damm- och fuktsäker. För detaljer och annan liknande utrustning, besök vår utrustningswebbplats: http://www.sourceindustrialsupply.com CLICK Product Finder-Locator Service FÖREGÅENDE SIDA
- Embedded Systems, Embedded Computer, Industrial Computers, Janz Tec
Embedded Systems, Embedded Computer, Industrial Computers, Janz Tec, Korenix, Industrial Workstations, Servers, Computer Rack, Single Board Computer Inbyggda system & industridatorer & panel PC Läs mer Inbyggda system och datorer Läs mer Panel PC, Multitouch-skärmar, pekskärmar Läs mer Industriell PC Läs mer Industriella arbetsstationer Läs mer Nätverksutrustning, nätverksenheter, mellansystem, samverkande enhet Läs mer Lagringsenheter, diskarrayer och lagringssystem, SAN, NAS Läs mer Industriella servrar Läs mer Chassi, rack, fästen för industridatorer Läs mer Tillbehör, moduler, bärkort för industridatorer Läs mer Automation och intelligenta system Som en leverantör av industriprodukter erbjuder vi dig några av de mest oumbärliga industridatorer & servrar & nätverks- och lagringsenheter, inbäddade datorer och system, enkelkortsdatorer, panel-PC, industriell PC, robust dator, pekskärm datorer, industriell arbetsstation, industriella datorkomponenter och tillbehör, digitala och analoga I/O-enheter, routrar, brygga, växlingsutrustning, nav, repeater, proxy, brandvägg, modem, nätverksgränssnittskontroller, protokollomvandlare, nätverksanslutna lagringsuppsättningar (NAS) , Storage Area Network (SAN) arrayer, flerkanaliga relämoduler, Full-CAN-styrenhet för MODULbus-uttag, MODULbus-bärarkort, inkrementell kodarmodul, intelligent PLC-länkkoncept, motorstyrenhet för DC-servomotorer, seriell gränssnittsmodul, VMEbus-prototypkort, intelligent profibus DP slavgränssnitt, mjukvara, relaterad elektronik, chassi-rack-fästen. Vi tar med det bästa av t världens industriella datorprodukter från fabrik till din dörr. Vår fördel är att vi kan erbjuda dig olika märkesnamn som t.ex. Janz Tec and_cc781905-58d_Janz Tec and_cc781905-58c lowerd store_bad5cf58d_and_cc781905-58c. Det som också gör oss speciella är vår förmåga att erbjuda dig varianter av produkter / anpassade konfigurationer / integration med andra system som du inte kan skaffa från andra källor. Vi erbjuder dig märkesutrustning av hög kvalitet för listpriset eller lägre. Det finns betydande rabatter på de angivna priserna om din orderkvantitet är betydande. Det mesta av vår utrustning finns i lager. Om det inte finns i lager, eftersom vi är en föredragen återförsäljare och distributör kan vi fortfarande leverera det inom en kortare ledtid till dig. Utöver lagervaror kan vi erbjuda dig specialprodukter designade och tillverkade efter dina behov. Låt oss bara veta vilka skillnader du behöver på ditt industriella datorsystem så fixar vi det enligt dina behov och önskemål. We offer you CUSTOM MANUFACTURING and ENGINEERING INTEGRATION capability. We also build CUSTOM AUTOMATION SYSTEMS, MONITORING and PROCESS CONTROL SYSTEMS by integrating datorer, översättningssteg, rotationssteg, motoriserade komponenter, armar, datainsamlingskort, processkontrollkort, sensorer, ställdon och andra nödvändiga hårdvaru- och mjukvarukomponenter. Oavsett var du befinner dig på jorden skickar vi inom några dagar till din dörr. Vi har rabatterade leveransavtal med UPS, FEDEX, TNT, DHL och standard air. Du kan beställa online med alternativ som kreditkort med vårt PayPal-konto, banköverföring, certifierad check eller postanvisning. Om du vill prata med oss innan du fattar ett beslut eller om du har några frågor behöver du bara ringa oss så hjälper en av våra erfarna data- och automationsingenjörer dig. För att vara närmare dig har vi kontor och lager på olika globala platser. Klicka på relevanta undermenyer ovan för att läsa mer om våra produkter i kategorin industridator. Ladda ner broschyr för vår DESIGN PARTNERSKAP PROGRAM För mer detaljerad information inbjuder vi dig också att besöka vår industriella datorbutikhttp://www.agsindustrialcomputers.com CLICK Product Finder-Locator Service FÖREGÅENDE SIDA
- Laser Machining, LM, Laser Cutting, CO2 Laser Processing, Nd-YAG Cut
Laser Machining - LM - Laser Cutting - Custom Parts Manufacturing - CO2 Laser Processing - Nd-YAG - Cutting - Boring Laserbearbetning & skärning & LBM LASER CUTTING is a HIGH-ENERGY-BEAM MANUFACTURING technology that uses a laser to cut materials, and is typically used for industrial manufacturing applications. In LASERBEAM MACHINING (LBM), fokuserar en laserkälla optisk energi på arbetsstyckets yta. Laserskärning riktar den mycket fokuserade och högdensitetsuteffekten från en högeffektlaser, via dator, mot materialet som ska skäras. Det riktade materialet smälter sedan antingen, bränns, förångas bort eller blåses bort av en gasstråle, på ett kontrollerat sätt och lämnar en kant med en ytfinish av hög kvalitet. Våra industriella laserskärare är lämpliga för skärning av platt-plåtmaterial samt struktur- och rörmaterial, metalliska och icke-metalliska arbetsstycken. I allmänhet krävs inget vakuum i laserstrålebearbetnings- och skärprocesserna. Det finns flera typer av lasrar som används vid laserskärning och tillverkning. Den pulserade eller kontinuerliga vågen CO2 LASER är lämplig för skärning, borrning och gravering. The NEODYMIUM (Nd) and neodymium yttrium-aluminum-garnet (Nd-YAG) LASERS are identical i stil och skiljer sig endast i tillämpning. Neodymium Nd används för borrning och där hög energi men låg upprepning krävs. Nd-YAG-lasern å andra sidan används där mycket hög effekt krävs och för borrning och gravering. Både CO2- och Nd/Nd-YAG-lasrar kan användas för LASERSVETSNING. Andra lasrar vi använder i tillverkningen inkluderar Nd:GLASS, RUBY och EXCIMER. I Laser Beam Machining (LBM) är följande parametrar viktiga: Reflexionsförmågan och värmeledningsförmågan hos arbetsstyckets yta och dess specifika värme och latenta värme från smältning och förångning. Effektiviteten hos laserstrålebearbetningsprocessen (LBM) ökar med minskningen av dessa parametrar. Skärdjupet kan uttryckas som: t ~ P / (vxd) Detta betyder att skärdjupet "t" är proportionellt mot effekttillförseln P och omvänt proportionellt mot skärhastigheten v och laserstrålens punktdiameter d. Ytan som produceras med LBM är i allmänhet grov och har en värmepåverkad zon. KOLDIOXID (CO2) LASERSKÄRNING och BEARBETNING: De DC-exciterade CO2-lasrarna pumpas genom att passera en ström genom gasblandningen medan de RF-exciterade CO2-lasrarna använder radiofrekvensenergi för excitation. RF-metoden är relativt ny och har blivit mer populär. DC-konstruktioner kräver elektroder inuti kaviteten, och därför kan de ha elektroderosion och plätering av elektrodmaterial på optiken. Tvärtom har RF-resonatorer externa elektroder och därför är de inte utsatta för dessa problem. Vi använder CO2-lasrar vid industriell skärning av många material såsom mjukt stål, aluminium, rostfritt stål, titan och plast. YAG LASER CUTTING and MACHINING: Vi använder YAG-lasrar för att skära och rita metaller och keramiska metaller. Lasergeneratorn och extern optik kräver kylning. Spillvärme genereras och överförs av en kylvätska eller direkt till luft. Vatten är en vanlig kylvätska, vanligtvis cirkuleras genom en kylare eller värmeöverföringssystem. EXCIMER LASER Skärning och bearbetning: En excimer laser är en sorts laser med våglängder i det ultravioletta området. Den exakta våglängden beror på vilka molekyler som används. Till exempel är följande våglängder associerade med molekylerna som visas inom parentes: 193 nm (ArF), 248 nm (KrF), 308 nm (XeCl), 353 nm (XeF). Vissa excimerlasrar är avstämbara. Excimerlasrar har den attraktiva egenskapen att de kan ta bort mycket fina lager av ytmaterial nästan utan uppvärmning eller byta till resten av materialet. Därför är excimerlasrar väl lämpade för precisionsmikrobearbetning av organiska material som vissa polymerer och plaster. GASASSISTERAD LASERSKÄRNING: Ibland använder vi laserstrålar i kombination med en gasström, som syre, kväve eller argon för att skära tunna plåtmaterial. Detta görs med hjälp av a LASER-BEAM TORCH. För rostfritt stål och aluminium använder vi högtrycks inertgasassisterad laserskärning med kväve. Detta resulterar i oxidfria kanter för att förbättra svetsbarheten. Dessa gasströmmar blåser också bort smält och förångat material från arbetsstyckets ytor. I a LASER MICROJET CUTTING har vi en vattenstrålestyrd laser i vilken en tryckpulsad laserstråle kopplas in i en lågstråle. Vi använder den för att utföra laserskärning medan vi använder vattenstrålen för att styra laserstrålen, liknande en optisk fiber. Fördelarna med lasermikrojet är att vattnet också tar bort skräp och kyler materialet, det är snabbare än traditionell "torr" laserskärning med högre tärningshastigheter, parallella snitt och rundstrålande skärningsförmåga. Vi använder olika metoder för att skära med laser. Några av metoderna är förångning, smältning och blås, smältblåsning och bränning, termisk spänningssprickning, ritsning, kallskärning och bränning, stabiliserad laserskärning. - Förångningsskärning: Den fokuserade strålen värmer materialets yta till sin kokpunkt och skapar ett hål. Hålet leder till en plötslig ökning av absorptionsförmågan och fördjupar snabbt hålet. När hålet blir djupare och materialet kokar, eroderar den alstrade ångan de smälta väggarna och blåser ut material och förstorar hålet ytterligare. Icke-smältande material som trä, kol och härdplast skärs vanligtvis med denna metod. - Smält- och blåsskärning: Vi använder högtrycksgas för att blåsa smält material från skärområdet, vilket minskar den erforderliga effekten. Materialet värms upp till sin smältpunkt och sedan blåser en gasstråle ut det smälta materialet ur snittet. Detta eliminerar behovet av att höja temperaturen på materialet ytterligare. Vi skär metaller med denna teknik. - Termisk sprickbildning: Spröda material är känsliga för termiska brott. En stråle fokuseras på ytan och orsakar lokal uppvärmning och termisk expansion. Detta resulterar i en spricka som sedan kan styras genom att förflytta balken. Vi använder denna teknik vid glasskärning. - Stealth-tärning av kiselskivor: Separationen av mikroelektroniska chip från kiselskivor utförs genom smyg-tärningsprocessen, med användning av en pulsad Nd:YAG-laser, våglängden på 1064 nm är väl anpassad till det elektroniska bandgapet hos kisel (1,11 eV eller 1117 nm). Detta är populärt vid tillverkning av halvledarenheter. - Reaktiv skärning: Kallas även flamskärning, denna teknik kan liknas vid skärning med syrgasbrännare men med en laserstråle som tändkälla. Vi använder detta för att skära kolstål i tjocklekar över 1 mm och även mycket tjocka stålplåtar med liten laserkraft. PULSED LASERS ger oss en kraftfull energiskur under en kort period och är mycket effektiva i vissa laserskärningsprocesser, såsom piercing, eller när mycket små hål eller mycket låga skärhastigheter krävs. Om en konstant laserstråle användes istället, kunde värmen nå punkten att smälta hela stycket som bearbetas. Våra lasrar har förmågan att pulsera eller skära CW (Continuous Wave) under NC (numerisk kontroll) programkontroll. Vi använder DOUBLE PULSE LASERS emitterar en serie pulspar för att förbättra materialavlägsningshastigheten och hålkvaliteten. Den första pulsen tar bort material från ytan och den andra pulsen förhindrar att det utsprutade materialet återhämtar sig vid sidan av hålet eller skär. Toleranser och ytfinish vid laserskärning och bearbetning är enastående. Våra moderna laserskärare har positioneringsnoggrannhet i närheten av 10 mikrometer och repeterbarheter på 5 mikrometer. Standardråheter Rz ökar med plåttjockleken, men minskar med laserkraft och skärhastighet. Laserskärnings- och bearbetningsprocesserna kan uppnå nära toleranser, ofta inom 0,001 tum (0,025 mm). Delarnas geometri och de mekaniska egenskaperna hos våra maskiner är optimerade för att uppnå bästa toleranskapacitet. Ytfinish som vi kan erhålla från laserstråleskärning kan variera mellan 0,003 mm till 0,006 mm. I allmänhet uppnår vi lätt hål med 0,025 mm diameter, och hål så små som 0,005 mm och håldjup-till-diameter-förhållanden på 50 till 1 har tillverkats i olika material. Våra enklaste och vanligaste laserskärare skär kolstålmetall från 0,020–0,5 tum (0,51–13 mm) i tjocklek och kan lätt vara upp till trettio gånger snabbare än standardsågning. Laserstrålebearbetning används i stor utsträckning för borrning och skärning av metaller, icke-metaller och kompositmaterial. Fördelar med laserskärning framför mekanisk skärning är bland annat enklare arbetshållning, renhet och minskad nedsmutsning av arbetsstycket (eftersom det inte finns någon skäregg som vid traditionell fräsning eller svarvning som kan bli förorenad av materialet eller kontaminera materialet, dvs. Den nötande naturen hos kompositmaterial kan göra dem svåra att bearbeta med konventionella metoder men lätta med laserbearbetning. Eftersom laserstrålen inte slits under processen kan den erhållna precisionen bli bättre. Eftersom lasersystem har en liten värmepåverkad zon är det också mindre risk att materialet som skärs skev. För vissa material kan laserskärning vara det enda alternativet. Laserstråleskärningsprocesser är flexibla, och fiberoptisk strålleverans, enkel fixtur, korta inställningstider, tillgänglighet av tredimensionella CNC-system gör det möjligt för laserskärning och bearbetning att konkurrera framgångsrikt med andra plåttillverkningsprocesser såsom stansning. Med detta sagt kan laserteknik ibland kombineras med mekanisk tillverkningsteknik för förbättrad total effektivitet. Laserskärning av plåt har fördelarna jämfört med plasmaskärning att den är mer exakt och använder mindre energi, men de flesta industriella lasrar kan inte skära igenom den större metalltjocklek som plasma kan. Lasrar som arbetar med högre effekt som 6000 Watt närmar sig plasmamaskiner i sin förmåga att skära igenom tjocka material. Men kapitalkostnaden för dessa 6000 Watt laserskärare är mycket högre än för plasmaskärmaskiner som kan skära tjocka material som stålplåt. Det finns också nackdelar med laserskärning och bearbetning. Laserskärning innebär hög strömförbrukning. Industriell lasereffektivitet kan variera från 5 % till 15 %. Strömförbrukningen och effektiviteten för en viss laser kommer att variera beroende på uteffekt och driftsparametrar. Detta beror på typen av laser och hur väl lasern matchar det aktuella arbetet. Mängden laserskärkraft som krävs för en viss uppgift beror på materialtyp, tjocklek, process (reaktiv/inert) som används och önskad skärhastighet. Den maximala produktionshastigheten vid laserskärning och bearbetning begränsas av ett antal faktorer, inklusive lasereffekt, processtyp (oavsett om den är reaktiv eller inert), materialegenskaper och tjocklek. In LASER ABLATION tar vi bort material från en fast yta genom att bestråla det med en laserstråle. Vid lågt laserflöde värms materialet upp av den absorberade laserenergin och förångas eller sublimeras. Vid högt laserflöde omvandlas materialet vanligtvis till ett plasma. Högeffektslasrar rengör en stor fläck med en enda puls. Lasrar med lägre effekt använder många små pulser som kan skannas över ett område. Vid laserablation tar vi bort material med en pulsad laser eller med en kontinuerlig våg laserstråle om laserintensiteten är tillräckligt hög. Pulserande lasrar kan borra extremt små, djupa hål genom mycket hårda material. Mycket korta laserpulser tar bort material så snabbt att det omgivande materialet absorberar väldigt lite värme, därför kan laserborrning göras på ömtåliga eller värmekänsliga material. Laserenergi kan absorberas selektivt av beläggningar, därför kan CO2 och Nd:YAG pulsade lasrar användas för att rengöra ytor, ta bort färg och beläggning, eller förbereda ytor för målning utan att skada den underliggande ytan. We use LASER ENGRAVING and LASER MARKING to engrave or mark an object. Dessa två tekniker är faktiskt de mest använda tillämpningarna. Inga bläck används och inte heller involverar det verktygsbitar som kommer i kontakt med den graverade ytan och slits ut, vilket är fallet med traditionella mekaniska gravyr- och märkningsmetoder. Material speciellt utformade för lasergravering och märkning inkluderar laserkänsliga polymerer och speciella nya metallegeringar. Även om utrustning för lasermärkning och gravering är relativt dyrare jämfört med alternativ som stansar, stift, styli, etsstämplar, etc., har de blivit mer populära på grund av sin noggrannhet, reproducerbarhet, flexibilitet, enkla automatisering och on-line applicering i en mängd olika tillverkningsmiljöer. Slutligen använder vi laserstrålar för flera andra tillverkningsoperationer: - LASERSVETSNING - LASER VÄRMEBEHANDLING: Småskalig värmebehandling av metaller och keramik för att modifiera deras ytmekaniska och tribologiska egenskaper. - LASER YTBEHANDLING/MODIFIKATION: Lasrar används för att rengöra ytor, införa funktionella grupper, modifiera ytor i ett försök att förbättra vidhäftningen före beläggningsavsättning eller sammanfogningsprocesser. CLICK Product Finder-Locator Service FÖREGÅENDE SIDA