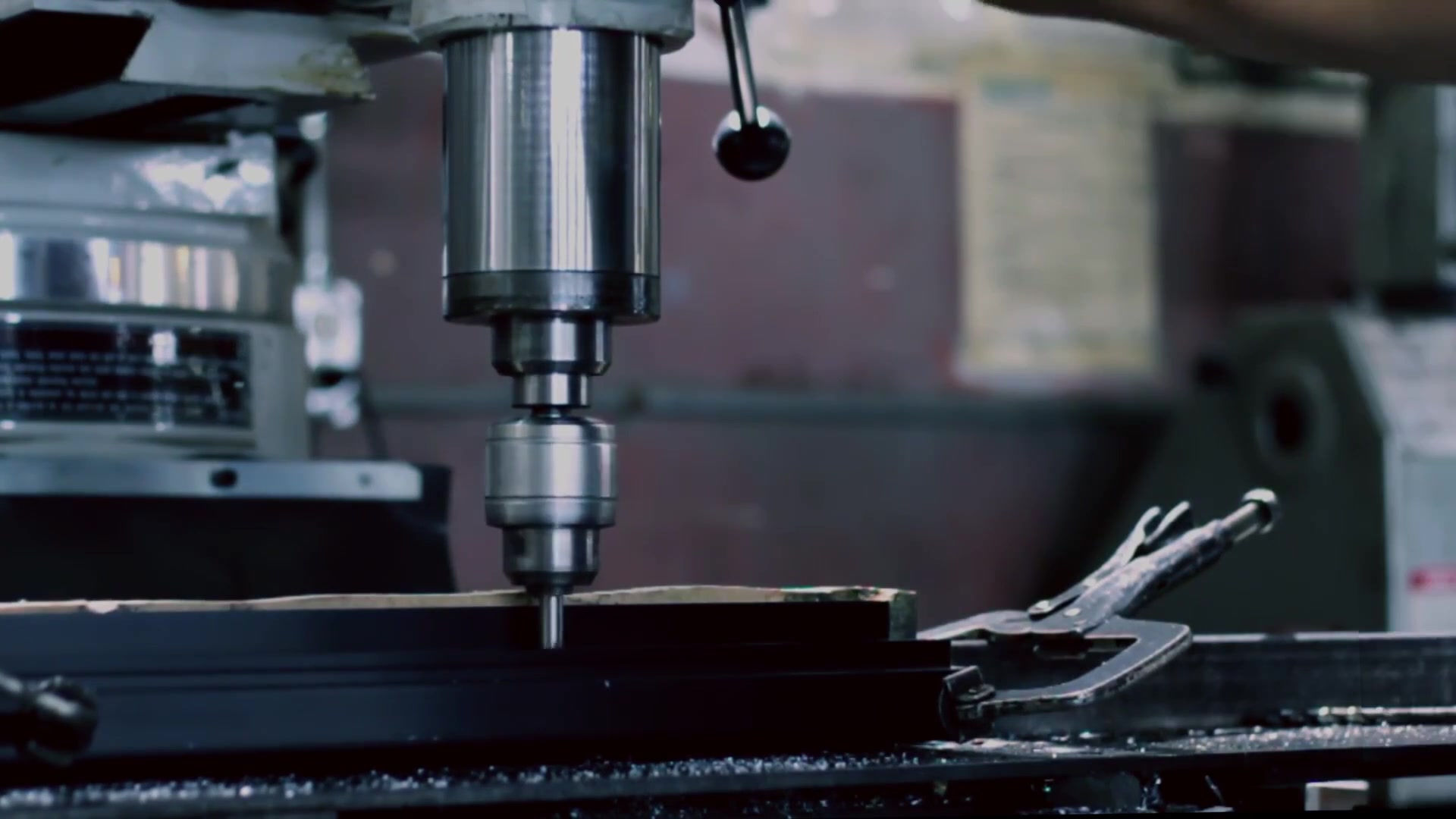
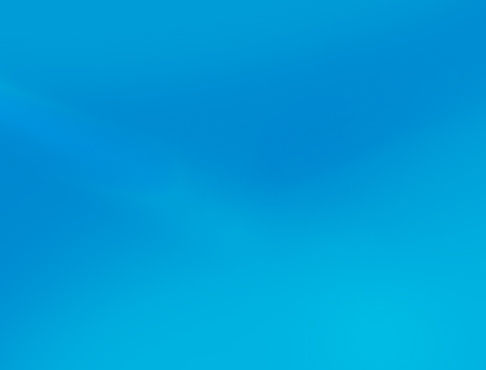
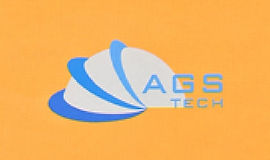
గ్లోబల్ కస్టమ్ మ్యానుఫ్యాక్చరర్, ఇంటిగ్రేటర్, కన్సాలిడేటర్, అనేక రకాల ఉత్పత్తులు & సేవల కోసం అవుట్సోర్సింగ్ భాగస్వామి.
కస్టమ్ తయారీ మరియు ఆఫ్-షెల్ఫ్ ఉత్పత్తులు & సేవల తయారీ, కల్పన, ఇంజనీరింగ్, కన్సాలిడేషన్, ఇంటిగ్రేషన్, అవుట్సోర్సింగ్ కోసం మేము మీ వన్-స్టాప్ మూలం.
మీ భాషను ఎంచుకోండి
-
కస్టమ్ తయారీ
-
దేశీయ & గ్లోబల్ కాంట్రాక్ట్ తయారీ
-
తయారీ అవుట్సోర్సింగ్
-
దేశీయ & ప్రపంచ సేకరణ
-
కన్సాలిడేషన్
-
ఇంజనీరింగ్ ఇంటిగ్రేషన్
-
ఇంజనీరింగ్ సేవలు
Search Results
164 results found with an empty search
- Composites, Composite Materials Manufacturing, Fiber Reinforced
Composites, Composite Materials Manufacturing, Particle and Fiber Reinforced, Cermets, Ceramic & Metal Composite, Glass Fiber Reinforced Polymer, Lay-Up Process కాంపోజిట్స్ & కాంపోజిట్ మెటీరియల్స్ తయారీ సరళంగా నిర్వచించబడినవి, మిశ్రమాలు లేదా మిశ్రమ పదార్థాలు అనేవి విభిన్న భౌతిక లేదా రసాయన లక్షణాలతో రెండు లేదా బహుళ పదార్థాలతో కూడిన పదార్థాలు, కానీ వాటిని కలిపినప్పుడు అవి రాజ్యాంగ పదార్థాల కంటే భిన్నమైన పదార్థంగా మారుతాయి. రాజ్యాంగ పదార్థాలు నిర్మాణంలో వేరుగా మరియు విభిన్నంగా ఉంటాయని మనం ఎత్తి చూపాలి. మిశ్రమ పదార్థాన్ని తయారు చేయడంలో లక్ష్యం ఏమిటంటే, దాని భాగాల కంటే ఉన్నతమైన మరియు ప్రతి భాగం యొక్క కావలసిన లక్షణాలను మిళితం చేసే ఉత్పత్తిని పొందడం. ఉదాహరణకు; బలం, తక్కువ బరువు లేదా తక్కువ ధర మిశ్రమ రూపకల్పన మరియు ఉత్పత్తి వెనుక ప్రేరణ కావచ్చు. మేము అందించే మిశ్రమాల రకం పార్టికల్-రీన్ఫోర్స్డ్ కాంపోజిట్లు, ఫైబర్-రీన్ఫోర్స్డ్ కాంపోజిట్లతో సహా సిరామిక్-మ్యాట్రిక్స్ / పాలిమర్-మ్యాట్రిక్స్ / మెటల్-మ్యాట్రిక్స్ / కార్బన్-కార్బన్ / హైబ్రిడ్ కాంపోజిట్లు, స్ట్రక్చరల్ & లామినేటెడ్ & శాండ్విచ్-స్ట్రక్చర్డ్ కాంపోజిట్లు మరియు నానోకంపొజిట్లు. కాంపోజిట్ మెటీరియల్ తయారీలో మేము ఉపయోగించే ఫ్యాబ్రికేషన్ టెక్నిక్లు: పల్ట్రషన్, ప్రిప్రెగ్ ప్రొడక్షన్ ప్రాసెస్లు, అడ్వాన్స్డ్ ఫైబర్ ప్లేస్మెంట్, ఫిలమెంట్ వైండింగ్, టైలర్డ్ ఫైబర్ ప్లేస్మెంట్, ఫైబర్గ్లాస్ స్ప్రే లే-అప్ ప్రాసెస్, టఫ్టింగ్, లాంక్సైడ్ ప్రాసెస్, z-పిన్నింగ్. అనేక మిశ్రమ పదార్థాలు రెండు దశలతో రూపొందించబడ్డాయి, మాతృక, ఇది నిరంతరాయంగా ఉంటుంది మరియు ఇతర దశను చుట్టుముడుతుంది; మరియు మాతృక చుట్టూ ఉన్న చెదరగొట్టబడిన దశ. మీరు ఇక్కడ క్లిక్ చేయాలని మేము సిఫార్సు చేస్తున్నాముAGS-TECH Inc ద్వారా కంపోజిట్స్ మరియు కాంపోజిట్ మెటీరియల్స్ తయారీకి సంబంధించిన మా స్కీమాటిక్ ఇలస్ట్రేషన్లను డౌన్లోడ్ చేయండి. మేము మీకు దిగువ అందిస్తున్న సమాచారాన్ని బాగా అర్థం చేసుకోవడంలో ఇది మీకు సహాయం చేస్తుంది. • కణ-పటిష్ట మిశ్రమాలు : ఈ వర్గం రెండు రకాలను కలిగి ఉంటుంది: పెద్ద-కణ మిశ్రమాలు మరియు వ్యాప్తి-బలపరిచిన మిశ్రమాలు. మునుపటి రకంలో, పార్టికల్-మ్యాట్రిక్స్ పరస్పర చర్యలను పరమాణు లేదా పరమాణు స్థాయిలో చికిత్స చేయడం సాధ్యం కాదు. బదులుగా కంటినమ్ మెకానిక్స్ చెల్లుతుంది. మరోవైపు, వ్యాప్తి-బలపరిచిన మిశ్రమాలలో కణాలు సాధారణంగా పదుల నానోమీటర్ పరిధులలో చాలా చిన్నవిగా ఉంటాయి. పెద్ద కణ సమ్మేళనానికి ఉదాహరణ పాలిమర్లు, వీటికి ఫిల్లర్లు జోడించబడ్డాయి. ఫిల్లర్లు పదార్థం యొక్క లక్షణాలను మెరుగుపరుస్తాయి మరియు కొంత పాలిమర్ వాల్యూమ్ను మరింత పొదుపుగా ఉండే పదార్థంతో భర్తీ చేయవచ్చు. రెండు దశల వాల్యూమ్ భిన్నాలు మిశ్రమం యొక్క ప్రవర్తనను ప్రభావితం చేస్తాయి. లోహాలు, పాలిమర్లు మరియు సెరామిక్స్తో పెద్ద కణ మిశ్రమాలను ఉపయోగిస్తారు. CERMETS సిరామిక్ / మెటల్ మిశ్రమాలకు ఉదాహరణలు. మా అత్యంత సాధారణ సెర్మెట్ సిమెంట్ కార్బైడ్. ఇది కోబాల్ట్ లేదా నికెల్ వంటి లోహం యొక్క మాతృకలో టంగ్స్టన్ కార్బైడ్ కణాల వంటి వక్రీభవన కార్బైడ్ సిరామిక్ను కలిగి ఉంటుంది. ఈ కార్బైడ్ మిశ్రమాలు గట్టిపడిన ఉక్కు కోసం కట్టింగ్ సాధనాలుగా విస్తృతంగా ఉపయోగించబడుతున్నాయి. గట్టి కార్బైడ్ కణాలు కట్టింగ్ చర్యకు బాధ్యత వహిస్తాయి మరియు డక్టైల్ మెటల్ మ్యాట్రిక్స్ ద్వారా వాటి మొండితనాన్ని పెంచుతుంది. ఈ విధంగా మేము రెండు పదార్థాల ప్రయోజనాలను ఒకే మిశ్రమంలో పొందుతాము. అధిక తన్యత బలం, మొండితనం, కన్నీటి మరియు రాపిడి నిరోధకత కలిగిన మిశ్రమాన్ని పొందడానికి వల్కనైజ్డ్ రబ్బరుతో కలిపిన కార్బన్ బ్లాక్ పార్టికులేట్లను మేము ఉపయోగించే పెద్ద కణ మిశ్రమానికి మరొక సాధారణ ఉదాహరణ. ఒక విక్షేపణ-బలపరిచిన మిశ్రమానికి ఉదాహరణ లోహాలు మరియు లోహ మిశ్రమాలు చాలా కఠినమైన మరియు జడ పదార్థం యొక్క సూక్ష్మ కణాల ఏకరీతి వ్యాప్తి ద్వారా బలోపేతం చేయబడతాయి మరియు గట్టిపడతాయి. అల్యూమినియం మెటల్ మ్యాట్రిక్స్కు చాలా చిన్న అల్యూమినియం ఆక్సైడ్ రేకులు జోడించబడినప్పుడు, మేము మెరుగైన అధిక-ఉష్ణోగ్రత శక్తిని కలిగి ఉన్న సింటెర్డ్ అల్యూమినియం పౌడర్ని పొందుతాము. • ఫైబర్-రీన్ఫోర్స్డ్ కాంపోజిట్లు: ఈ మిశ్రమాల వర్గం నిజానికి అత్యంత ముఖ్యమైనది. సాధించే లక్ష్యం యూనిట్ బరువుకు అధిక బలం మరియు దృఢత్వం. ఈ పదార్ధాల యొక్క లక్షణాలు మరియు ఉపయోగాన్ని నిర్ణయించడంలో ఫైబర్ కూర్పు, పొడవు, ధోరణి మరియు ఈ మిశ్రమాలలో ఏకాగ్రత కీలకం. మేము ఉపయోగించే ఫైబర్స్ యొక్క మూడు సమూహాలు ఉన్నాయి: మీసాలు, ఫైబర్లు మరియు వైర్లు. WHISKERS చాలా సన్నని మరియు పొడవైన ఒకే స్ఫటికాలు. అవి బలమైన పదార్థాలలో ఒకటి. గ్రాఫైట్, సిలికాన్ నైట్రైడ్, అల్యూమినియం ఆక్సైడ్ వంటి కొన్ని ఉదాహరణ మీసాలు. మరోవైపు FIBERS ఎక్కువగా పాలిమర్లు లేదా సిరామిక్లు మరియు పాలీక్రిస్టలైన్ లేదా నిరాకార స్థితిలో ఉంటాయి. మూడవ సమూహం సాపేక్షంగా పెద్ద వ్యాసాలను కలిగి ఉండే చక్కటి వైర్లు మరియు తరచుగా ఉక్కు లేదా టంగ్స్టన్ను కలిగి ఉంటుంది. వైర్ రీన్ఫోర్స్డ్ కాంపోజిట్కి ఉదాహరణ రబ్బరు లోపల ఉక్కు వైర్ను కలిగి ఉండే కార్ టైర్లు. మాతృక పదార్థంపై ఆధారపడి, మనకు ఈ క్రింది మిశ్రమాలు ఉన్నాయి: పాలిమర్-మ్యాట్రిక్స్ మిశ్రమాలు: ఇవి పాలిమర్ రెసిన్ మరియు ఫైబర్లతో ఉపబల పదార్ధంగా తయారు చేయబడ్డాయి. గ్లాస్ ఫైబర్-రీన్ఫోర్స్డ్ పాలిమర్ (GFRP) కంపోజిట్లు అని పిలువబడే ఒక ఉప సమూహం పాలిమర్ మ్యాట్రిక్స్లో నిరంతర లేదా నిరంతరాయ గ్లాస్ ఫైబర్లను కలిగి ఉంటుంది. గ్లాస్ అధిక బలాన్ని అందిస్తుంది, ఇది పొదుపుగా ఉంటుంది, ఫైబర్లుగా తయారు చేయడం సులభం మరియు రసాయనికంగా జడమైనది. ప్రతికూలతలు వాటి పరిమిత దృఢత్వం మరియు దృఢత్వం, సేవా ఉష్ణోగ్రతలు 200 - 300 సెంటీగ్రేడ్ వరకు మాత్రమే ఉంటాయి. ఫైబర్గ్లాస్ ఆటోమోటివ్ బాడీలు మరియు రవాణా పరికరాలు, సముద్ర వాహన వస్తువులు, నిల్వ కంటైనర్లకు అనుకూలంగా ఉంటుంది. పరిమిత దృఢత్వం కారణంగా అవి ఏరోస్పేస్ లేదా వంతెన తయారీకి తగినవి కావు. ఇతర ఉప సమూహాన్ని కార్బన్ ఫైబర్-రీన్ఫోర్స్డ్ పాలిమర్ (CFRP) కాంపోజిట్ అంటారు. ఇక్కడ, కార్బన్ అనేది పాలిమర్ మ్యాట్రిక్స్లో మన ఫైబర్ పదార్థం. కార్బన్ దాని అధిక నిర్దిష్ట మాడ్యులస్ మరియు బలం మరియు అధిక ఉష్ణోగ్రతల వద్ద వీటిని నిర్వహించగల సామర్థ్యానికి ప్రసిద్ధి చెందింది. కార్బన్ ఫైబర్లు మాకు స్టాండర్డ్, ఇంటర్మీడియట్, హై మరియు అల్ట్రాహై తన్యత మాడ్యులిని అందించగలవు. ఇంకా, కార్బన్ ఫైబర్లు విభిన్న భౌతిక మరియు యాంత్రిక లక్షణాలను అందిస్తాయి మరియు అందుచేత వివిధ కస్టమ్ టైలర్డ్ ఇంజనీరింగ్ అప్లికేషన్లకు అనుకూలం. CFRP మిశ్రమాలను క్రీడలు మరియు వినోద పరికరాలు, పీడన నాళాలు మరియు ఏరోస్పేస్ నిర్మాణ భాగాల తయారీకి పరిగణించవచ్చు. అయినప్పటికీ, మరొక ఉప సమూహం, అరామిడ్ ఫైబర్-రీన్ఫోర్స్డ్ పాలిమర్ మిశ్రమాలు కూడా అధిక-బలం మరియు మాడ్యులస్ పదార్థాలు. బరువు నిష్పత్తులకు వారి బలం అసాధారణంగా ఎక్కువగా ఉంటుంది. అరామిడ్ ఫైబర్లను వాణిజ్య పేర్లతో కూడా పిలుస్తారు KEVLAR మరియు NOMEX. ఉద్రిక్తతలో అవి ఇతర పాలీమెరిక్ ఫైబర్ పదార్థాల కంటే మెరుగ్గా పనిచేస్తాయి, అయితే అవి కుదింపులో బలహీనంగా ఉంటాయి. అరామిడ్ ఫైబర్స్ కఠినమైనవి, ప్రభావ నిరోధకమైనవి, క్రీప్ మరియు అలసట నిరోధకత, అధిక ఉష్ణోగ్రతల వద్ద స్థిరంగా ఉంటాయి, బలమైన ఆమ్లాలు మరియు స్థావరాలు మినహా రసాయనికంగా జడత్వం కలిగి ఉంటాయి. అరామిడ్ ఫైబర్లను క్రీడా వస్తువులు, బుల్లెట్ ప్రూఫ్ దుస్తులు, టైర్లు, తాళ్లు, ఫైబర్ ఆప్టిక్ కేబుల్ షీట్లలో విస్తృతంగా ఉపయోగిస్తారు. ఇతర ఫైబర్ ఉపబల పదార్థాలు ఉన్నాయి కానీ తక్కువ స్థాయిలో ఉపయోగించబడతాయి. ఇవి ప్రధానంగా బోరాన్, సిలికాన్ కార్బైడ్, అల్యూమినియం ఆక్సైడ్. మరోవైపు పాలిమర్ మ్యాట్రిక్స్ పదార్థం కూడా కీలకం. పాలిమర్ సాధారణంగా తక్కువ ద్రవీభవన మరియు క్షీణత ఉష్ణోగ్రతను కలిగి ఉన్నందున ఇది మిశ్రమం యొక్క గరిష్ట సేవా ఉష్ణోగ్రతను నిర్ణయిస్తుంది. పాలిస్టర్లు మరియు వినైల్ ఈస్టర్లు పాలిమర్ మ్యాట్రిక్స్గా విస్తృతంగా ఉపయోగించబడుతున్నాయి. రెసిన్లు కూడా ఉపయోగించబడతాయి మరియు అవి అద్భుతమైన తేమ నిరోధకత మరియు యాంత్రిక లక్షణాలను కలిగి ఉంటాయి. ఉదాహరణకు పాలిమైడ్ రెసిన్ దాదాపు 230 డిగ్రీల సెల్సియస్ వరకు ఉపయోగించవచ్చు. మెటల్-మ్యాట్రిక్స్ కాంపోజిట్లు: ఈ మెటీరియల్లలో మనం డక్టైల్ మెటల్ మ్యాట్రిక్స్ని ఉపయోగిస్తాము మరియు సేవా ఉష్ణోగ్రతలు సాధారణంగా వాటి కాంపోనెంట్ల కంటే ఎక్కువగా ఉంటాయి. పాలిమర్-మ్యాట్రిక్స్ మిశ్రమాలతో పోల్చినప్పుడు, ఇవి అధిక ఆపరేటింగ్ ఉష్ణోగ్రతలను కలిగి ఉంటాయి, మంటలేనివి మరియు సేంద్రీయ ద్రవాలకు వ్యతిరేకంగా మెరుగైన క్షీణత నిరోధకతను కలిగి ఉండవచ్చు. అయితే అవి మరింత ఖరీదైనవి. మీసాలు, కణాలు, నిరంతర మరియు నిరంతర ఫైబర్స్ వంటి ఉపబల పదార్థాలు; మరియు రాగి, అల్యూమినియం, మెగ్నీషియం, టైటానియం, సూపర్లాయ్లు వంటి మాతృక పదార్థాలు సాధారణంగా ఉపయోగించబడుతున్నాయి. ఉదాహరణ అనువర్తనాలు అల్యూమినియం ఆక్సైడ్ మరియు కార్బన్ ఫైబర్లతో బలోపేతం చేయబడిన అల్యూమినియం అల్లాయ్ మ్యాట్రిక్స్తో తయారు చేయబడిన ఇంజిన్ భాగాలు. సిరామిక్-మ్యాట్రిక్స్ మిశ్రమాలు: సిరామిక్ పదార్థాలు వాటి అత్యుత్తమ అధిక ఉష్ణోగ్రత విశ్వసనీయతకు ప్రసిద్ధి చెందాయి. అయినప్పటికీ అవి చాలా పెళుసుగా ఉంటాయి మరియు ఫ్రాక్చర్ మొండితనానికి తక్కువ విలువలను కలిగి ఉంటాయి. ఒక సిరామిక్లోని కణాలు, ఫైబర్లు లేదా మీసాలను మరొక దాని మాతృకలో పొందుపరచడం ద్వారా మేము అధిక ఫ్రాక్చర్ దృఢత్వంతో మిశ్రమాలను సాధించగలుగుతాము. ఈ ఎంబెడెడ్ మెటీరియల్స్ ప్రాథమికంగా పగుళ్ల చిట్కాలను తిప్పికొట్టడం లేదా క్రాక్ ముఖాలపై వంతెనలను ఏర్పరచడం వంటి కొన్ని యంత్రాంగాల ద్వారా మాతృక లోపల పగుళ్లు వ్యాప్తి చెందడాన్ని నిరోధిస్తాయి. ఉదాహరణగా, SiC మీసాలతో బలోపేతం చేయబడిన అల్యూమినాలు హార్డ్ మెటల్ మిశ్రమాలను మ్యాచింగ్ చేయడానికి కట్టింగ్ టూల్ ఇన్సర్ట్లుగా ఉపయోగించబడతాయి. ఇవి సిమెంట్ కార్బైడ్లతో పోలిస్తే మెరుగైన పనితీరును వెల్లడిస్తాయి. కార్బన్-కార్బన్ మిశ్రమాలు: ఉపబల మరియు మాతృక రెండూ కార్బన్. అవి 2000 సెంటీగ్రేడ్ కంటే ఎక్కువ ఉష్ణోగ్రతల వద్ద అధిక తన్యత మాడ్యులి మరియు బలాన్ని కలిగి ఉంటాయి, క్రీప్ రెసిస్టెన్స్, అధిక ఫ్రాక్చర్ దృఢత్వం, తక్కువ ఉష్ణ విస్తరణ గుణకాలు, అధిక ఉష్ణ వాహకత. ఈ లక్షణాలు థర్మల్ షాక్ రెసిస్టెన్స్ అవసరమయ్యే అనువర్తనాలకు వాటిని ఆదర్శంగా చేస్తాయి. కార్బన్-కార్బన్ మిశ్రమాల బలహీనత అయితే అధిక ఉష్ణోగ్రతల వద్ద ఆక్సీకరణకు వ్యతిరేకంగా దాని దుర్బలత్వం. వినియోగానికి సాధారణ ఉదాహరణలు హాట్-ప్రెసింగ్ అచ్చులు, అధునాతన టర్బైన్ ఇంజిన్ భాగాల తయారీ. హైబ్రిడ్ మిశ్రమాలు : రెండు లేదా అంతకంటే ఎక్కువ విభిన్న రకాల ఫైబర్లు ఒకే మాతృకలో మిళితం చేయబడతాయి. ఈ విధంగా లక్షణాల కలయికతో ఒక కొత్త పదార్థాన్ని రూపొందించవచ్చు. కార్బన్ మరియు గ్లాస్ ఫైబర్లు రెండింటినీ పాలీమెరిక్ రెసిన్లో చేర్చడం ఒక ఉదాహరణ. కార్బన్ ఫైబర్స్ తక్కువ సాంద్రత కలిగిన దృఢత్వం మరియు బలాన్ని అందిస్తాయి కానీ ఖరీదైనవి. మరోవైపు గాజు చవకైనది కానీ కార్బన్ ఫైబర్ల దృఢత్వం లేదు. గ్లాస్-కార్బన్ హైబ్రిడ్ కాంపోజిట్ బలంగా మరియు పటిష్టంగా ఉంటుంది మరియు తక్కువ ఖర్చుతో తయారు చేయవచ్చు. ఫైబర్-రీన్ఫోర్స్డ్ కాంపోజిట్ల ప్రాసెసింగ్: ఒకే దిశలో ఒకే విధంగా పంపిణీ చేయబడిన ఫైబర్లతో నిరంతర ఫైబర్-రీన్ఫోర్స్డ్ ప్లాస్టిక్ల కోసం మేము క్రింది పద్ధతులను ఉపయోగిస్తాము. PULTRUSION: రాడ్లు, కిరణాలు మరియు నిరంతర పొడవు మరియు స్థిరమైన క్రాస్-సెక్షన్ల గొట్టాలు తయారు చేయబడతాయి. నిరంతర ఫైబర్ రోవింగ్లు థర్మోసెట్టింగ్ రెసిన్తో కలిపి ఉంచబడతాయి మరియు వాటిని కావలసిన ఆకృతికి ముందుగా రూపొందించడానికి స్టీల్ డై ద్వారా లాగబడతాయి. తరువాత, అవి దాని తుది ఆకారాన్ని పొందడానికి ఖచ్చితమైన యంత్రంతో కూడిన క్యూరింగ్ డై గుండా వెళతాయి. క్యూరింగ్ డై వేడి చేయబడినందున, ఇది రెసిన్ మాతృకను నయం చేస్తుంది. పుల్లర్లు డైస్ ద్వారా పదార్థాన్ని గీస్తారు. చొప్పించిన బోలు కోర్లను ఉపయోగించి, మేము ట్యూబ్లు మరియు బోలు జ్యామితిలను పొందగలుగుతాము. పల్ట్రూషన్ పద్ధతి స్వయంచాలకంగా ఉంది మరియు మాకు అధిక ఉత్పత్తి రేట్లను అందిస్తుంది. ఉత్పత్తి యొక్క ఏదైనా పొడవును ఉత్పత్తి చేయడం సాధ్యమవుతుంది. ప్రిప్రెగ్ ఉత్పత్తి ప్రక్రియ: ప్రీప్రెగ్ అనేది పాక్షికంగా నయం చేయబడిన పాలిమర్ రెసిన్తో ముందుగా కలిపిన నిరంతర-ఫైబర్ రీన్ఫోర్స్మెంట్. ఇది నిర్మాణాత్మక అనువర్తనాలకు విస్తృతంగా ఉపయోగించబడుతుంది. పదార్థం టేప్ రూపంలో వస్తుంది మరియు టేప్గా రవాణా చేయబడుతుంది. తయారీదారు దానిని నేరుగా అచ్చు మరియు రెసిన్ జోడించాల్సిన అవసరం లేకుండా పూర్తిగా నయం చేస్తాడు. ప్రిప్రెగ్స్ గది ఉష్ణోగ్రతల వద్ద క్యూరింగ్ ప్రతిచర్యలకు లోనవుతాయి కాబట్టి, అవి 0 సెంటీగ్రేడ్ లేదా తక్కువ ఉష్ణోగ్రతల వద్ద నిల్వ చేయబడతాయి. ఉపయోగం తర్వాత మిగిలిన టేపులు తక్కువ ఉష్ణోగ్రతల వద్ద తిరిగి నిల్వ చేయబడతాయి. థర్మోప్లాస్టిక్ మరియు థర్మోసెట్టింగ్ రెసిన్లు ఉపయోగించబడతాయి మరియు కార్బన్, అరామిడ్ మరియు గాజు యొక్క ఉపబల ఫైబర్లు సాధారణం. ప్రిప్రెగ్లను ఉపయోగించడానికి, క్యారియర్ బ్యాకింగ్ పేపర్ మొదట తీసివేయబడుతుంది మరియు టూల్డ్ ఉపరితలంపై ప్రిప్రెగ్ టేప్ను వేయడం ద్వారా తయారీ జరుగుతుంది (లే-అప్ ప్రక్రియ). కావలసిన మందాన్ని పొందడానికి అనేక ప్లైలు వేయవచ్చు. క్రాస్-ప్లై లేదా యాంగిల్-ప్లై లామినేట్ను ఉత్పత్తి చేయడానికి ఫైబర్ ఓరియంటేషన్ను ప్రత్యామ్నాయంగా మార్చడం తరచుగా అభ్యాసం. చివరగా వేడి మరియు ఒత్తిడి క్యూరింగ్ కోసం వర్తించబడుతుంది. ప్రిప్రెగ్లు మరియు లే-అప్లను కత్తిరించడానికి హ్యాండ్ ప్రాసెసింగ్ అలాగే ఆటోమేటెడ్ ప్రాసెస్లు రెండూ ఉపయోగించబడతాయి. ఫిలమెంట్ వైండింగ్ : బోలు మరియు సాధారణంగా సైక్లిండిరికల్ ఆకారాన్ని అనుసరించడానికి నిరంతర ఉపబల ఫైబర్లు ముందుగా నిర్ణయించిన నమూనాలో ఖచ్చితంగా ఉంచబడతాయి. ఫైబర్లు మొదట రెసిన్ బాత్ ద్వారా వెళ్లి, ఆపై ఆటోమేటెడ్ సిస్టమ్ ద్వారా మాండ్రెల్పై గాయపడతాయి. అనేక వైండింగ్ పునరావృత్తులు తర్వాత కావలసిన మందాలు పొందబడతాయి మరియు గది ఉష్ణోగ్రత వద్ద లేదా ఓవెన్ లోపల క్యూరింగ్ చేయబడుతుంది. ఇప్పుడు మాండ్రెల్ తొలగించబడింది మరియు ఉత్పత్తిని తొలగించారు. ఫిలమెంట్ వైండింగ్ ఫైబర్లను చుట్టుకొలత, హెలికల్ మరియు ధ్రువ నమూనాలలో వైండింగ్ చేయడం ద్వారా చాలా ఎక్కువ బలం-బరువు నిష్పత్తులను అందిస్తుంది. పైపులు, ట్యాంకులు, కేసింగ్లు ఈ సాంకేతికతను ఉపయోగించి తయారు చేస్తారు. • నిర్మాణాత్మక మిశ్రమాలు : సాధారణంగా ఇవి సజాతీయ మరియు మిశ్రమ పదార్థాలతో రూపొందించబడ్డాయి. అందువల్ల వీటి యొక్క లక్షణాలు దాని మూలకాల యొక్క రాజ్యాంగ పదార్థాలు మరియు రేఖాగణిత రూపకల్పన ద్వారా నిర్ణయించబడతాయి. ఇక్కడ ప్రధాన రకాలు ఉన్నాయి: లామినార్ మిశ్రమాలు : ఈ నిర్మాణాత్మక పదార్థాలు రెండు డైమెన్షనల్ షీట్లు లేదా ప్యానెళ్లతో తయారు చేయబడ్డాయి. పొరలు పేర్చబడి సిమెంటుతో కలుపుతారు. రెండు లంబ అక్షాలలో అధిక-బలం దిశలను ప్రత్యామ్నాయం చేయడం ద్వారా, మేము ద్విమితీయ విమానంలో రెండు దిశలలో అధిక శక్తిని కలిగి ఉన్న మిశ్రమాన్ని పొందుతాము. లేయర్ల కోణాలను సర్దుబాటు చేయడం ద్వారా ఇష్టపడే దిశల్లో బలంతో కూడిన మిశ్రమాన్ని తయారు చేయవచ్చు. ఆధునిక స్కీ ఈ విధంగా తయారు చేయబడింది. శాండ్విచ్ ప్యానెల్లు: ఈ నిర్మాణాత్మక మిశ్రమాలు తేలికైనవి అయినప్పటికీ అధిక దృఢత్వం మరియు బలాన్ని కలిగి ఉంటాయి. శాండ్విచ్ ప్యానెల్లు అల్యూమినియం మిశ్రమాలు, ఫైబర్ రీన్ఫోర్స్డ్ ప్లాస్టిక్లు లేదా స్టీల్ వంటి గట్టి మరియు బలమైన పదార్థంతో తయారు చేయబడిన రెండు బయటి షీట్లను కలిగి ఉంటాయి మరియు బయటి షీట్ల మధ్య ఒక కోర్. కోర్ తేలికగా ఉండాలి మరియు ఎక్కువ సమయం స్థితిస్థాపకత తక్కువ మాడ్యులస్ కలిగి ఉండాలి. జనాదరణ పొందిన ప్రధాన పదార్థాలు దృఢమైన పాలీమెరిక్ ఫోమ్స్, కలప మరియు తేనెగూడులు. శాండ్విచ్ ప్యానెల్లు నిర్మాణ పరిశ్రమలో రూఫింగ్ మెటీరియల్, ఫ్లోర్ లేదా వాల్ మెటీరియల్గా మరియు ఏరోస్పేస్ పరిశ్రమలలో కూడా విస్తృతంగా ఉపయోగించబడుతున్నాయి. • NANOCOMPOSITES : ఈ కొత్త పదార్థాలు మాతృకలో పొందుపరిచిన నానోసైజ్డ్ కణాల కణాలను కలిగి ఉంటాయి. నానోకంపొజిట్లను ఉపయోగించి మనం రబ్బరు పదార్థాలను తయారు చేయవచ్చు, ఇవి గాలి వ్యాప్తికి చాలా మంచి అవరోధాలను కలిగి ఉంటాయి మరియు వాటి రబ్బరు లక్షణాలను మార్చకుండా ఉంచవచ్చు. CLICK Product Finder-Locator Service ముందు పేజి
- Machine Elements Manufacturing, Gears, Gear Drives, Bearings, Keys, Splines
Machine Elements Manufacturing, Gears, Gear Drives, Bearings, Keys, Splines, Pins, Shafts, Seals, Fasteners, Clutch, Cams, Followers, Belts, Couplings, Shafts మెషిన్ ఎలిమెంట్స్ తయారీ ఇంకా చదవండి బెల్ట్లు & చైన్లు & కేబుల్ డ్రైవ్ అసెంబ్లీ ఇంకా చదవండి గేర్లు & గేర్ డ్రైవ్ అసెంబ్లీ ఇంకా చదవండి కప్లింగ్స్ & బేరింగ్స్ తయారీ ఇంకా చదవండి కీలు & స్ప్లైన్స్ & పిన్స్ తయారీ ఇంకా చదవండి కెమెరాలు & అనుచరులు & లింకేజీలు & రాట్చెట్ వీల్స్ తయారీ ఇంకా చదవండి షాఫ్ట్స్ తయారీ ఇంకా చదవండి మెకానికల్ సీల్స్ తయారీ ఇంకా చదవండి క్లచ్ & బ్రేక్ అసెంబ్లీ ఇంకా చదవండి ఫాస్టెనర్లు తయారీ ఇంకా చదవండి సాధారణ యంత్రాల అసెంబ్లీ MACHINE ELEMENTS ఒక యంత్రం యొక్క ప్రాథమిక భాగాలు. ఈ అంశాలు మూడు ప్రాథమిక రకాలను కలిగి ఉంటాయి: 1.) ఫ్రేమ్ సభ్యులు, బేరింగ్లు, యాక్సిల్స్, స్ప్లైన్లు, ఫాస్టెనర్లు, సీల్స్ మరియు లూబ్రికెంట్లతో సహా నిర్మాణ భాగాలు. 2.) గేర్ రైళ్లు, బెల్ట్ లేదా చైన్ డ్రైవ్లు, లింకేజీలు, క్యామ్ మరియు ఫాలోయర్ సిస్టమ్లు, బ్రేక్లు & క్లచ్లు వంటి వివిధ మార్గాల్లో కదలికను నియంత్రించే మెకానిజమ్స్. 3.) బటన్లు, స్విచ్లు, సూచికలు, సెన్సార్లు, యాక్యుయేటర్లు మరియు కంప్యూటర్ కంట్రోలర్లు వంటి భాగాలను నియంత్రించండి. మేము మీకు అందించే చాలా మెషిన్ ఎలిమెంట్లు సాధారణ పరిమాణాలకు ప్రామాణికం చేయబడ్డాయి, అయితే మీ ప్రత్యేక అప్లికేషన్ల కోసం అనుకూలీకరించిన మెషిన్ ఎలిమెంట్లు కూడా అందుబాటులో ఉన్నాయి. మెషీన్ మూలకాల అనుకూలీకరణ మా డౌన్లోడ్ చేయదగిన కేటలాగ్లలో లేదా సరికొత్త డిజైన్లలో ఇప్పటికే ఉన్న డిజైన్లపై జరుగుతుంది. డిజైన్ను రెండు పార్టీలు ఆమోదించిన తర్వాత మెషిన్ ఎలిమెంట్ల ప్రోటోటైపింగ్ మరియు తయారీని ముందుకు తీసుకెళ్లవచ్చు. కొత్త మెషీన్ ఎలిమెంట్లను డిజైన్ చేసి తయారు చేయవలసి వస్తే, మా కస్టమర్లు వారి స్వంత బ్లూప్రింట్లను మాకు ఇమెయిల్ చేయండి మరియు మేము వాటిని ఆమోదం కోసం సమీక్షిస్తాము లేదా వారి అప్లికేషన్ కోసం మెషిన్ ఎలిమెంట్లను డిజైన్ చేయమని మమ్మల్ని అడుగుతారు. తరువాతి సందర్భంలో మేము మా కస్టమర్ల నుండి అన్ని ఇన్పుట్లను ఉపయోగిస్తాము మరియు మెషిన్ ఎలిమెంట్లను డిజైన్ చేస్తాము మరియు ఆమోదం కోసం మా క్లయింట్లకు ఖరారు చేసిన బ్లూప్రింట్లను పంపుతాము. ఆమోదించబడిన తర్వాత, మేము మొదటి కథనాలను ఉత్పత్తి చేస్తాము మరియు తరువాత తుది రూపకల్పన ప్రకారం యంత్ర మూలకాలను తయారు చేస్తాము. ఈ పని యొక్క ఏ దశలోనైనా, ఒక నిర్దిష్ట మెషిన్ ఎలిమెంట్ డిజైన్ ఫీల్డ్లో సంతృప్తికరంగా లేనట్లయితే (ఇది చాలా అరుదు), మేము మొత్తం ప్రాజెక్ట్ను సమీక్షిస్తాము మరియు మా క్లయింట్లతో అవసరమైన విధంగా సంయుక్తంగా మార్పులు చేస్తాము. అవసరమైనప్పుడు లేదా అవసరమైనప్పుడు మెషిన్ ఎలిమెంట్స్ లేదా ఏదైనా ఇతర ఉత్పత్తి రూపకల్పన కోసం మా కస్టమర్లతో నాన్డిస్క్లోజర్ ఒప్పందాలపై (NDA) సంతకం చేయడం మా ప్రామాణిక పద్ధతి. నిర్దిష్ట కస్టమర్ కోసం మెషిన్ ఎలిమెంట్స్ అనుకూల రూపకల్పన మరియు తయారు చేయబడిన తర్వాత, మేము దానికి ఉత్పత్తి కోడ్ను కేటాయిస్తాము మరియు ఉత్పత్తిని కలిగి ఉన్న మా కస్టమర్కు మాత్రమే వాటిని ఉత్పత్తి చేసి విక్రయిస్తాము. మేము అభివృద్ధి చేసిన సాధనాలు, అచ్చులు మరియు విధానాలను ఉపయోగించి అవసరమైనన్ని సార్లు మరియు మా కస్టమర్ వాటిని తిరిగి ఆర్డర్ చేసినప్పుడల్లా యంత్ర మూలకాలను పునరుత్పత్తి చేస్తాము. మరో మాటలో చెప్పాలంటే, మీ కోసం కస్టమ్ మెషిన్ ఎలిమెంట్ని రూపొందించి, ఉత్పత్తి చేసిన తర్వాత, మేధో సంపత్తి అలాగే అన్ని సాధనాలు మరియు అచ్చులు మీ కోసం మరియు మీరు కోరుకున్న విధంగా పునరుత్పత్తి చేయబడిన ఉత్పత్తుల కోసం మా ద్వారా నిరవధికంగా నిల్వ చేయబడతాయి. మేము మా క్లయింట్లకు ఇంజనీరింగ్ సేవలను సృజనాత్మకంగా మెషిన్ ఎలిమెంట్లను ఒక అప్లికేషన్ను అందించే కాంపోనెంట్ లేదా అసెంబ్లీలో కలపడం ద్వారా మరియు మా కస్టమర్ల అంచనాలను అందుకోవడం లేదా మించిపోవడం ద్వారా అందిస్తాము. మా మెషీన్ మూలకాలను రూపొందించే మొక్కలు ISO9001, QS9000 లేదా TS16949 ద్వారా అర్హత పొందాయి. అదనంగా, మా ఉత్పత్తులు చాలా వరకు CE లేదా UL గుర్తును కలిగి ఉంటాయి మరియు ISO, SAE, ASME, DIN వంటి అంతర్జాతీయంగా సంబంధిత ప్రమాణాలకు అనుగుణంగా ఉంటాయి. మా మెషిన్ ఎలిమెంట్స్ గురించి సవివరమైన సమాచారాన్ని పొందడానికి దయచేసి సబ్మెనులపై క్లిక్ చేయండి: - బెల్ట్లు, గొలుసులు మరియు కేబుల్ డ్రైవ్లు - గేర్లు మరియు గేర్ డ్రైవ్లు - కప్లింగ్స్ & బేరింగ్స్ - కీలు & స్ప్లైన్లు & పిన్స్ - కెమెరాలు & లింకేజీలు - షాఫ్ట్స్ - మెకానికల్ సీల్స్ - ఇండస్ట్రియల్ క్లచ్ & బ్రేక్ - ఫాస్టెనర్లు - సాధారణ యంత్రాలు మేము మా కస్టమర్లు, డిజైనర్లు మరియు మెషిన్ ఎలిమెంట్లతో సహా కొత్త ఉత్పత్తుల డెవలపర్ల కోసం రిఫరెన్స్ బ్రోచర్ను సిద్ధం చేసాము. మీరు యంత్ర భాగాల రూపకల్పనలో సాధారణంగా ఉపయోగించే కొన్ని పదాలను మీకు పరిచయం చేసుకోవచ్చు: డిజైనర్లు మరియు ఇంజనీర్లు ఉపయోగించే సాధారణ మెకానికల్ ఇంజనీరింగ్ నిబంధనల కోసం బ్రోచర్ను డౌన్లోడ్ చేయండి పారిశ్రామిక యంత్రాలు, ఆటోమేషన్ సిస్టమ్లు, టెస్ట్ మరియు మెట్రాలజీ పరికరాలు, రవాణా పరికరాలు, నిర్మాణ యంత్రాలు మరియు ఆచరణాత్మకంగా ఎక్కడైనా మీరు ఆలోచించగలిగే వివిధ రంగాలలో మా మెషీన్ అంశాలు అప్లికేషన్లను కనుగొంటాయి. AGS-TECH అప్లికేషన్ను బట్టి వివిధ పదార్థాల నుండి మెషిన్ ఎలిమెంట్లను అభివృద్ధి చేస్తుంది మరియు తయారు చేస్తుంది. మెషిన్ ఎలిమెంట్స్ కోసం ఉపయోగించే పదార్థాలు బొమ్మల కోసం ఉపయోగించే అచ్చు ప్లాస్టిక్ల నుండి పారిశ్రామిక యంత్రాల కోసం గట్టిపడిన మరియు ప్రత్యేకంగా పూత పూసిన ఉక్కు వరకు ఉంటాయి. మా డిజైనర్లు మెషిన్ ఎలిమెంట్లను అభివృద్ధి చేయడానికి అత్యాధునిక వృత్తిపరమైన సాఫ్ట్వేర్ మరియు డిజైన్ టూల్స్ను ఉపయోగిస్తారు, గేర్ పళ్లలోని కోణాలు, ప్రమేయం ఉన్న ఒత్తిళ్లు, ధరల ధరలు మొదలైనవి వంటి వివరాలను పరిగణనలోకి తీసుకుంటారు. దయచేసి మా ఉపమెనుల ద్వారా స్క్రోల్ చేయండి మరియు మీరు మీ అప్లికేషన్ కోసం ఆఫ్-ది-షెల్ఫ్ మెషిన్ ఎలిమెంట్లను గుర్తించగలరో లేదో చూడటానికి మా ఉత్పత్తి బ్రోచర్లు మరియు కేటలాగ్లను డౌన్లోడ్ చేయండి. మీరు మీ అప్లికేషన్కు మంచి సరిపోలికను కనుగొనలేకపోతే, దయచేసి మాకు తెలియజేయండి మరియు మీ అవసరాలను తీర్చే మెషిన్ ఎలిమెంట్లను అభివృద్ధి చేయడానికి మరియు తయారు చేయడానికి మేము మీతో కలిసి పని చేస్తాము. మీరు తయారీ సామర్థ్యాలకు బదులుగా మా ఇంజనీరింగ్ మరియు పరిశోధన & అభివృద్ధి సామర్థ్యాలపై ఎక్కువగా ఆసక్తి కలిగి ఉన్నట్లయితే, మా వెబ్సైట్ ని సందర్శించమని మేము మిమ్మల్ని ఆహ్వానిస్తున్నాముhttp://www.ags-engineering.com ఇక్కడ మీరు మా డిజైన్, ఉత్పత్తి అభివృద్ధి, ప్రక్రియ అభివృద్ధి, ఇంజనీరింగ్ కన్సల్టింగ్ సేవలు మరియు మరిన్నింటి గురించి మరింత వివరణాత్మక సమాచారాన్ని పొందవచ్చు CLICK Product Finder-Locator Service ముందు పేజి
- Transmission Components, Belts, Chains, Cable Drives, Pulleys,AGS-TECH
Transmission Components, Belts, Chains and Cable Drives, Conventional & Grooved or Serrated, Positive Drive, Pulleys బెల్ట్లు & చైన్లు & కేబుల్ డ్రైవ్ అసెంబ్లీ AGS-TECH Inc. మీకు బెల్ట్లు & చైన్లు & కేబుల్ డ్రైవ్ అసెంబ్లీతో సహా పవర్ ట్రాన్స్మిషన్ భాగాలను అందిస్తుంది. సంవత్సరాల శుద్ధీకరణతో, మా రబ్బరు, తోలు మరియు ఇతర బెల్ట్ డ్రైవ్లు తేలికగా మరియు మరింత కాంపాక్ట్గా మారాయి, తక్కువ ఖర్చుతో ఎక్కువ లోడ్లను మోయగల సామర్థ్యం కలిగి ఉంటుంది. అదేవిధంగా, మా చైన్ డ్రైవ్లు కాలక్రమేణా చాలా అభివృద్ధి చెందాయి మరియు అవి మా కస్టమర్లకు అనేక ప్రయోజనాలను అందిస్తాయి. చైన్ డ్రైవ్లను ఉపయోగించడం వల్ల కలిగే కొన్ని ప్రయోజనాలు వాటి సాపేక్షంగా అనియంత్రిత షాఫ్ట్ సెంటర్ దూరాలు, కాంపాక్ట్నెస్, అసెంబ్లీ సౌలభ్యం, స్లిప్ లేదా క్రీప్ లేకుండా ఉద్రిక్తతలో స్థితిస్థాపకత, అధిక-ఉష్ణోగ్రత వాతావరణంలో పనిచేసే సామర్థ్యం. మా కేబుల్ డ్రైవ్లు ఇతర రకాల ట్రాన్స్మిషన్ భాగాల కంటే కొన్ని అప్లికేషన్లలో సరళత వంటి ప్రయోజనాలను కూడా అందిస్తాయి. ఆఫ్-షెల్ఫ్ బెల్ట్, చైన్ మరియు కేబుల్ డ్రైవ్లు అలాగే కస్టమ్ ఫ్యాబ్రికేటెడ్ మరియు అసెంబుల్డ్ వెర్షన్లు రెండూ అందుబాటులో ఉన్నాయి. మేము ఈ ప్రసార భాగాలను మీ అప్లికేషన్ కోసం సరైన పరిమాణంలో మరియు చాలా సరిఅయిన పదార్థాల నుండి తయారు చేయవచ్చు. బెల్ట్లు & బెల్ట్ డ్రైవ్లు: - సంప్రదాయ ఫ్లాట్ బెల్ట్లు: ఇవి దంతాలు, పొడవైన కమ్మీలు లేదా సెర్రేషన్లు లేని సాదా ఫ్లాట్ బెల్ట్లు. ఫ్లాట్ బెల్ట్ డ్రైవ్లు ఫ్లెక్సిబిలిటీ, మంచి షాక్ శోషణ, అధిక వేగంతో సమర్థవంతమైన పవర్ ట్రాన్స్మిషన్, రాపిడి నిరోధకత, తక్కువ ధరను అందిస్తాయి. పెద్ద బెల్ట్లను తయారు చేయడానికి బెల్ట్లను విభజించవచ్చు లేదా కనెక్ట్ చేయవచ్చు. సాంప్రదాయ ఫ్లాట్ బెల్ట్ల యొక్క ఇతర ప్రయోజనాలు అవి సన్నగా ఉంటాయి, అవి అధిక సెంట్రిఫ్యూగల్ లోడ్లకు లోబడి ఉండవు (చిన్న పుల్లీలతో అధిక వేగ కార్యకలాపాలకు వాటిని మంచిగా చేస్తుంది). మరోవైపు ఫ్లాట్ బెల్ట్లకు అధిక టెన్షన్ అవసరం కాబట్టి అవి అధిక బేరింగ్ లోడ్లను విధిస్తాయి. ఫ్లాట్ బెల్ట్ డ్రైవ్ల యొక్క ఇతర ప్రతికూలతలు జారడం, ధ్వనించే ఆపరేషన్ మరియు తక్కువ మరియు మితమైన ఆపరేషన్ వేగంతో సాపేక్షంగా తక్కువ సామర్థ్యాలు. మా వద్ద రెండు రకాల సంప్రదాయ బెల్ట్లు ఉన్నాయి: రీన్ఫోర్స్డ్ మరియు నాన్-రీన్ఫోర్స్డ్. రీన్ఫోర్స్డ్ బెల్ట్లు వాటి నిర్మాణంలో తన్యత సభ్యుడిని కలిగి ఉంటాయి. సాంప్రదాయ ఫ్లాట్ బెల్ట్లు లెదర్, రబ్బరైజ్డ్ ఫాబ్రిక్ లేదా కార్డ్, నాన్-రీన్ఫోర్స్డ్ రబ్బర్ లేదా ప్లాస్టిక్, ఫాబ్రిక్, రీన్ఫోర్స్డ్ లెదర్గా అందుబాటులో ఉన్నాయి. లెదర్ బెల్టులు సుదీర్ఘ జీవితం, వశ్యత, ఘర్షణ యొక్క అద్భుతమైన గుణకం, సులభంగా మరమ్మత్తును అందిస్తాయి. అయితే లెదర్ బెల్ట్లు చాలా ఖరీదైనవి, బెల్ట్ డ్రెస్సింగ్ మరియు క్లీనింగ్ అవసరం, మరియు వాతావరణాన్ని బట్టి అవి కుంచించుకుపోవచ్చు లేదా సాగవచ్చు. రబ్బరైజ్డ్ ఫాబ్రిక్ లేదా కార్డ్ బెల్ట్లు తేమ, యాసిడ్ మరియు ఆల్కాలిస్లకు నిరోధకతను కలిగి ఉంటాయి. రబ్బరైజ్డ్ ఫాబ్రిక్ బెల్ట్లు రబ్బరుతో కలిపిన కాటన్ లేదా సింథటిక్ డక్ ప్లైస్తో తయారు చేయబడ్డాయి మరియు అత్యంత పొదుపుగా ఉంటాయి. రబ్బరైజ్డ్ కార్డ్ బెల్ట్లు రబ్బరుతో కలిపిన త్రాడుల శ్రేణిని కలిగి ఉంటాయి. రబ్బరైజ్డ్ కార్డ్ బెల్ట్లు అధిక తన్యత బలం మరియు నిరాడంబరమైన పరిమాణం మరియు ద్రవ్యరాశిని అందిస్తాయి. నాన్-రీన్ఫోర్స్డ్ రబ్బరు లేదా ప్లాస్టిక్ బెల్ట్లు లైట్-డ్యూటీ, తక్కువ-స్పీడ్ డ్రైవ్ అప్లికేషన్లకు సరిపోతాయి. నాన్-రీన్ఫోర్స్డ్ రబ్బరు మరియు ప్లాస్టిక్ బెల్ట్లను వాటి పుల్లీల మీదుగా విస్తరించవచ్చు. రబ్బరు బెల్ట్లతో పోలిస్తే ప్లాస్టిక్ నాన్-రీన్ఫోర్స్డ్ బెల్ట్లు అధిక శక్తిని ప్రసారం చేయగలవు. రీన్ఫోర్స్డ్ లెదర్ బెల్ట్లు లెదర్ టాప్ మరియు బాటమ్ లేయర్ల మధ్య శాండ్విచ్ చేయబడిన ప్లాస్టిక్ టెన్సైల్ మెంబర్ని కలిగి ఉంటాయి. చివరగా, మా ఫాబ్రిక్ బెల్ట్లు ఒకే కాటన్ ముక్కను కలిగి ఉండవచ్చు లేదా డక్ మడతపెట్టి, రేఖాంశ కుట్లు వరుసలతో కుట్టినవి. ఫ్యాబ్రిక్ బెల్ట్లు ఏకరీతిగా ట్రాక్ చేయగలవు మరియు అధిక వేగంతో పని చేయగలవు. - గ్రూవ్డ్ లేదా సెరేటెడ్ బెల్ట్లు (V-బెల్ట్లు వంటివి): ఇవి మరొక రకమైన ప్రసార ఉత్పత్తి యొక్క ప్రయోజనాలను అందించడానికి సవరించిన ప్రాథమిక ఫ్లాట్ బెల్ట్లు. ఇవి రేఖాంశంగా పక్కటెముకలతో కూడిన ఫ్లాట్ బెల్ట్లు. పాలీ-V బెల్ట్లు ట్రాకింగ్ మరియు కుదింపు ప్రయోజనాల కోసం తన్యత విభాగం మరియు ప్రక్కనే ఉన్న V- ఆకారపు పొడవైన కమ్మీల శ్రేణితో రేఖాంశంగా గ్రూవ్డ్ లేదా సెరేటెడ్ ఫ్లాట్ బెల్ట్గా ఉంటాయి. శక్తి సామర్థ్యం బెల్ట్ వెడల్పుపై ఆధారపడి ఉంటుంది. V-బెల్ట్ అనేది పరిశ్రమ యొక్క వర్క్హోర్స్ మరియు దాదాపు ఏదైనా లోడ్ పవర్ను ప్రసారం చేయడానికి వివిధ రకాల ప్రామాణిక పరిమాణాలు మరియు రకాల్లో అందుబాటులో ఉంటుంది. V-బెల్ట్ డ్రైవ్లు 1500 నుండి 6000 ft/min మధ్య బాగా పనిచేస్తాయి, అయితే ఇరుకైన V-బెల్ట్లు 10,000 ft/min వరకు పనిచేస్తాయి. V-బెల్ట్ డ్రైవ్లు 3 నుండి 5 సంవత్సరాల వరకు సుదీర్ఘ జీవితాన్ని అందిస్తాయి మరియు పెద్ద వేగ నిష్పత్తులను అనుమతిస్తాయి, అవి ఇన్స్టాల్ చేయడం మరియు తీసివేయడం సులభం, నిశ్శబ్ద ఆపరేషన్, తక్కువ నిర్వహణ, బెల్ట్ డ్రైవర్ మరియు నడిచే షాఫ్ట్ల మధ్య మంచి షాక్ శోషణను అందిస్తాయి. V-బెల్ట్ల ప్రతికూలత వాటి నిర్దిష్ట స్లిప్ మరియు క్రీప్ మరియు అందువల్ల సింక్రోనస్ వేగం అవసరమయ్యే చోట అవి ఉత్తమ పరిష్కారం కాకపోవచ్చు. మాకు పారిశ్రామిక, ఆటోమోటివ్ మరియు వ్యవసాయ బెల్ట్లు ఉన్నాయి. స్టాండర్డ్ స్టాండర్డ్ లెంగ్త్లు అలాగే బెల్ట్ల కస్టమ్ పొడవులు అందుబాటులో ఉన్నాయి. అన్ని ప్రామాణిక V-బెల్ట్ క్రాస్ సెక్షన్లు స్టాక్ నుండి అందుబాటులో ఉన్నాయి. డ్రైవింగ్ మరియు నడిచే పుల్లీ డయామీటర్లు, పుల్లీల మధ్య దూరం మరియు పుల్లీల భ్రమణ వేగం వంటి మీ సిస్టమ్లోని కొన్ని పారామీటర్లు మీకు తెలిస్తే, బెల్ట్ పొడవు, బెల్ట్ విభాగం (వెడల్పు & మందం) వంటి తెలియని పారామితులను మీరు లెక్కించగల పట్టికలు ఉన్నాయి. మీరు అటువంటి పట్టికలను ఉపయోగించవచ్చు లేదా మీ కోసం సరైన V-బెల్ట్ని ఎంచుకోమని మమ్మల్ని అడగవచ్చు. - పాజిటివ్ డ్రైవ్ బెల్ట్లు (టైమింగ్ బెల్ట్): ఈ బెల్ట్లు కూడా ఫ్లాట్ టైప్గా ఉంటాయి, ఇవి లోపల చుట్టుకొలతపై సమానంగా ఉండే దంతాల శ్రేణితో ఉంటాయి. సానుకూల డ్రైవ్ లేదా టైమింగ్ బెల్ట్లు ఫ్లాట్ బెల్ట్ల ప్రయోజనాలను చైన్లు మరియు గేర్ల యొక్క పాజిటివ్-గ్రిప్ లక్షణాలతో మిళితం చేస్తాయి. సానుకూల డ్రైవ్ బెల్ట్లు జారడం లేదా వేగ వైవిధ్యాలను బహిర్గతం చేయవు. విస్తృత శ్రేణి వేగం నిష్పత్తులు సాధ్యమే. బేరింగ్ లోడ్లు తక్కువగా ఉంటాయి, ఎందుకంటే అవి తక్కువ ఉద్రిక్తతతో పనిచేయగలవు. అయితే అవి పుల్లీలలో తప్పుగా అమర్చడానికి ఎక్కువ అవకాశం ఉంది. - పుల్లీలు, షీవ్లు, బెల్ట్ల కోసం హబ్లు: ఫ్లాట్, రిబ్బెడ్ (సెరేటెడ్) మరియు పాజిటివ్ డ్రైవ్ బెల్ట్లతో వివిధ రకాల పుల్లీలు ఉపయోగించబడతాయి. మేము వాటన్నింటినీ తయారు చేస్తాము. మా ఫ్లాట్ బెల్ట్ పుల్లీలు చాలా వరకు ఇనుముతో తయారు చేయబడతాయి, అయితే ఉక్కు సంస్కరణలు వివిధ రిమ్ మరియు హబ్ కాంబినేషన్లలో కూడా అందుబాటులో ఉన్నాయి. మా ఫ్లాట్-బెల్ట్ పుల్లీలు ఘనమైన, స్పోక్డ్ లేదా స్ప్లిట్ హబ్లను కలిగి ఉండవచ్చు లేదా మీరు కోరుకున్నట్లు మేము తయారు చేయవచ్చు. Ribbed మరియు పాజిటివ్-డ్రైవ్ బెల్ట్లు వివిధ రకాల స్టాక్ పరిమాణాలు మరియు వెడల్పులలో అందుబాటులో ఉన్నాయి. బెల్ట్ను డ్రైవ్లో ఉంచడానికి టైమింగ్-బెల్ట్ డ్రైవ్లలో కనీసం ఒక కప్పి తప్పనిసరిగా ఫ్లాంగ్ చేయబడాలి. లాంగ్ సెంటర్ డ్రైవ్ సిస్టమ్ల కోసం, రెండు పుల్లీలు ఫ్లాంగ్డ్ను కలిగి ఉండాలని సిఫార్సు చేయబడింది. షీవ్లు పుల్లీల యొక్క గాడి చక్రాలు మరియు సాధారణంగా ఇనుప కాస్టింగ్, స్టీల్ ఫార్మింగ్ లేదా ప్లాస్టిక్ మౌల్డింగ్ ద్వారా తయారు చేయబడతాయి. ఆటోమోటివ్ మరియు వ్యవసాయ షీవ్లను తయారు చేయడానికి స్టీల్ ఫార్మింగ్ సరైన ప్రక్రియ. మేము సాధారణ మరియు లోతైన పొడవైన కమ్మీలతో షీవ్లను ఉత్పత్తి చేస్తాము. క్వార్టర్-టర్న్ డ్రైవ్లలో వలె V-బెల్ట్ ఒక కోణంలో షీవ్లోకి ప్రవేశించినప్పుడు డీప్-గ్రూవ్ షీవ్లు బాగా సరిపోతాయి. డీప్ గ్రూవ్లు నిలువు-షాఫ్ట్ డ్రైవ్లు మరియు బెల్ట్ల వైబ్రేషన్ సమస్యగా ఉండే అప్లికేషన్లకు కూడా బాగా సరిపోతాయి. మా ఇడ్లర్ పుల్లీలు గ్రూవ్డ్ షీవ్స్ లేదా ఫ్లాట్ పుల్లీలు యాంత్రిక శక్తిని ప్రసారం చేయవు. ఇడ్లర్ పుల్లీలు ఎక్కువగా బెల్ట్లను బిగించడానికి ఉపయోగిస్తారు. - సింగిల్ మరియు మల్టిపుల్ బెల్ట్ డ్రైవ్లు: సింగిల్ బెల్ట్ డ్రైవ్లు ఒకే గాడిని కలిగి ఉంటాయి, అయితే బహుళ బెల్ట్ డ్రైవ్లు బహుళ గ్రూవ్లను కలిగి ఉంటాయి. దిగువ సంబంధిత రంగుల వచనాన్ని క్లిక్ చేయడం ద్వారా మీరు మా కేటలాగ్లను డౌన్లోడ్ చేసుకోవచ్చు: - పవర్ ట్రాన్స్మిషన్ బెల్ట్లు (V-బెల్ట్లు, టైమింగ్ బెల్ట్లు, రా ఎడ్జ్ బెల్ట్లు, ర్యాప్డ్ బెల్ట్లు మరియు స్పెషాలిటీ బెల్ట్లు ఉన్నాయి) - కన్వేయర్ బెల్ట్ - V-పుల్లీలు - టైమింగ్ పుల్లీలు చైన్స్ & చైన్ డ్రైవ్లు: మా పవర్ ట్రాన్స్మిషన్ చెయిన్లు సాపేక్షంగా అనియంత్రిత షాఫ్ట్ సెంటర్ దూరాలు, సులభమైన అసెంబ్లీ, కాంపాక్ట్నెస్, స్లిప్ లేదా క్రీప్ లేకుండా టెన్షన్లో ఉండే స్థితిస్థాపకత, అధిక ఉష్ణోగ్రతల కింద పనిచేసే సామర్థ్యం వంటి కొన్ని ప్రయోజనాలను కలిగి ఉన్నాయి. మా గొలుసుల యొక్క ప్రధాన రకాలు ఇక్కడ ఉన్నాయి: - వేరు చేయగలిగిన గొలుసులు: మా వేరు చేయగలిగిన గొలుసులు పరిమాణాలు, పిచ్ మరియు అంతిమ బలం మరియు సాధారణంగా మెల్లబుల్ ఇనుము లేదా ఉక్కుతో తయారు చేయబడ్డాయి. సున్నిత గొలుసులు 0.902 (23 మిమీ) నుండి 4.063 అంగుళాల (103 మిమీ) పిచ్ వరకు మరియు అంతిమ బలం 700 నుండి 17,000 పౌండ్లు/చదరపు అంగుళం వరకు ఉంటాయి. మరోవైపు మా వేరు చేయగలిగిన ఉక్కు గొలుసులు 0.904 అంగుళాల (23 మిమీ) నుండి సుమారు 3.00 అంగుళాల (76 మిమీ) వరకు పిచ్లో తయారు చేయబడ్డాయి, అంతిమ బలం 760 నుండి 5000 lb/స్క్వేర్ అంగుళం._cc781905-5cde-3194-bb3bbb 136bad5cf58d_ - పింటిల్ చైన్లు: ఈ చైన్లు భారీ లోడ్లు మరియు కొంచెం ఎక్కువ వేగంతో సుమారు 450 అడుగుల/నిమి (2.2 మీ/సెకన్) వరకు ఉపయోగించబడతాయి. పింటిల్ చైన్లు ఆఫ్సెట్ సైడ్బార్లతో పూర్తి, గుండ్రని బారెల్ ముగింపును కలిగి ఉండే వ్యక్తిగత తారాగణం లింక్లతో తయారు చేయబడ్డాయి. ఈ చైన్ లింక్లు స్టీల్ పిన్స్తో ఒకదానితో ఒకటి అనుసంధానించబడి ఉంటాయి. ఈ గొలుసులు సుమారు 1.00 అంగుళాల (25 మిమీ) నుండి 6.00 అంగుళాల (150 మిమీ) వరకు పిచ్లో ఉంటాయి మరియు అంతిమ బలం 3600 నుండి 30,000 పౌండ్లు/చదరపు అంగుళం మధ్య ఉంటుంది. - ఆఫ్సెట్-సైడ్బార్ చెయిన్లు: ఇవి నిర్మాణ యంత్రాల డ్రైవ్ చెయిన్లలో ప్రసిద్ధి చెందాయి. ఈ గొలుసులు 1000 ft/min వేగంతో పని చేస్తాయి మరియు 250 hp వరకు లోడ్లను ప్రసారం చేస్తాయి. సాధారణంగా ప్రతి లింక్లో రెండు ఆఫ్సెట్ సైడ్బార్లు, ఒక బుషింగ్, ఒక రోలర్, ఒక పిన్, ఒక కాటర్ పిన్ ఉంటాయి. - రోలర్ చైన్స్: అవి 0.25 (6 మిమీ) నుండి 3.00 (75 మిమీ) అంగుళాల వరకు పిచ్లలో అందుబాటులో ఉంటాయి. సింగిల్-వెడల్పు రోలర్ గొలుసుల యొక్క అంతిమ బలం 925 నుండి 130,000 lb/చదరపు అంగుళం మధ్య ఉంటుంది. రోలర్ చైన్ల యొక్క బహుళ-వెడల్పు వెర్షన్లు అందుబాటులో ఉన్నాయి మరియు అధిక వేగంతో ఎక్కువ శక్తిని ప్రసారం చేస్తాయి. బహుళ-వెడల్పు రోలర్ గొలుసులు తగ్గిన శబ్దంతో సున్నితమైన చర్యను కూడా అందిస్తాయి. రోలర్ గొలుసులు రోలర్ లింక్లు మరియు పిన్ లింక్ల నుండి సమీకరించబడతాయి. కోటర్ పిన్స్ వేరు చేయగల వెర్షన్ రోలర్ గొలుసులలో ఉపయోగించబడతాయి. రోలర్ చైన్ డ్రైవ్ల రూపకల్పనకు సబ్జెక్ట్ నైపుణ్యం అవసరం. బెల్ట్ డ్రైవ్లు లీనియర్ స్పీడ్పై ఆధారపడి ఉంటాయి, చైన్ డ్రైవ్లు చిన్న స్ప్రాకెట్ యొక్క భ్రమణ వేగంపై ఆధారపడి ఉంటాయి, ఇది చాలా ఇన్స్టాలేషన్లలో నడిచే సభ్యుడు. హార్స్పవర్ రేటింగ్లు మరియు భ్రమణ వేగంతో పాటు, చైన్ డ్రైవ్ల రూపకల్పన అనేక ఇతర కారకాలపై ఆధారపడి ఉంటుంది. - డబుల్-పిచ్ చైన్లు: పిచ్ రెండు రెట్లు పొడవుగా ఉంటుంది తప్ప ప్రాథమికంగా రోలర్ చెయిన్ల మాదిరిగానే ఉంటుంది. - ఇన్వర్టెడ్ టూత్ (నిశ్శబ్ద) గొలుసులు: ప్రైమ్ మూవర్, పవర్-టేకాఫ్ డ్రైవ్ల కోసం ఎక్కువగా ఉపయోగించే హై స్పీడ్ చైన్లు. విలోమ టూత్ చైన్ డ్రైవ్లు 1200 hp వరకు శక్తిని ప్రసారం చేయగలవు మరియు టూత్ లింక్ల శ్రేణితో రూపొందించబడ్డాయి, ప్రత్యామ్నాయంగా పిన్లు లేదా ఉమ్మడి భాగాల కలయికతో సమీకరించబడతాయి. సెంటర్-గైడ్ చైన్ స్ప్రాకెట్లో గ్రూవ్లను ఎంగేజ్ చేయడానికి గైడ్ లింక్లను కలిగి ఉంది మరియు సైడ్-గైడ్ చైన్లో స్ప్రాకెట్ వైపులా ఎంగేజ్ చేయడానికి గైడ్లు ఉన్నాయి. - పూసలు లేదా స్లైడర్ గొలుసులు: ఈ గొలుసులు స్లో స్పీడ్ డ్రైవ్లకు మరియు మాన్యువల్ ఆపరేషన్లలో కూడా ఉపయోగించబడతాయి. దిగువ సంబంధిత రంగుల వచనాన్ని క్లిక్ చేయడం ద్వారా మీరు మా కేటలాగ్లను డౌన్లోడ్ చేసుకోవచ్చు: - డ్రైవింగ్ చైన్స్ - కన్వేయర్ చైన్స్ - పెద్ద పిచ్ కన్వేయర్ గొలుసులు - స్టెయిన్లెస్ స్టీల్ రోలర్ గొలుసులు - హాయిస్టింగ్ చైన్స్ - మోటార్ సైకిల్ గొలుసులు - వ్యవసాయ యంత్ర గొలుసులు - స్ప్రాకెట్లు: మా ప్రామాణిక స్ప్రాకెట్లు ANSI ప్రమాణాలకు అనుగుణంగా ఉంటాయి. ప్లేట్ స్ప్రాకెట్లు ఫ్లాట్, హబ్లెస్ స్ప్రాకెట్లు. మా చిన్న మరియు మధ్యస్థ-పరిమాణ హబ్ స్ప్రాకెట్లు బార్ స్టాక్ లేదా ఫోర్జింగ్ల నుండి మార్చబడతాయి లేదా బార్-స్టాక్ హబ్ను హాట్-రోల్డ్ ప్లేట్కు వెల్డింగ్ చేయడం ద్వారా తయారు చేయబడతాయి. AGS-TECH Inc. గ్రే-ఐరన్ కాస్టింగ్లు, తారాగణం ఉక్కు మరియు వెల్డెడ్ హబ్ నిర్మాణాలు, సింటెర్డ్ పౌడర్ మెటల్, మోల్డ్ లేదా మెషిన్డ్ ప్లాస్టిక్ల నుండి తయారు చేయబడిన స్ప్రాకెట్లను సరఫరా చేయగలదు. అధిక వేగంతో మృదువైన ఆపరేషన్ కోసం, స్ప్రాకెట్ల పరిమాణం యొక్క సరైన ఎంపిక అవసరం. స్ప్రాకెట్ని ఎంచుకునేటప్పుడు స్థల పరిమితులు మనం విస్మరించలేము. డ్రైవర్ మరియు నడిచే స్ప్రాకెట్ల నిష్పత్తి 6:1 కంటే ఎక్కువ ఉండకూడదని సిఫార్సు చేయబడింది మరియు డ్రైవర్పై చైన్ ర్యాప్ 120 డిగ్రీలు. చిన్న మరియు పెద్ద స్ప్రాకెట్లు, చైన్ పొడవులు మరియు చైన్ టెన్షన్ల మధ్య మధ్య దూరాలను కూడా తప్పనిసరిగా కొన్ని సిఫార్సు చేసిన ఇంజనీరింగ్ లెక్కలు & మార్గదర్శకాల ప్రకారం ఎంచుకోవాలి మరియు యాదృచ్ఛికంగా కాదు. దిగువన ఉన్న రంగుల వచనాన్ని క్లిక్ చేయడం ద్వారా మా కేటలాగ్లను డౌన్లోడ్ చేయండి: - స్ప్రాకెట్లు మరియు ప్లేట్ వీల్స్ - ట్రాన్స్మిషన్ బుషింగ్స్ - చైన్ కప్లింగ్ - చైన్ లాక్స్ కేబుల్ డ్రైవ్లు: ఇవి కొన్ని సందర్భాల్లో బెల్ట్లు మరియు చైన్ డ్రైవ్ల కంటే వాటి ప్రయోజనాలను కలిగి ఉంటాయి. కేబుల్ డ్రైవ్లు బెల్ట్ల వలె అదే పనితీరును సాధించగలవు మరియు కొన్ని అప్లికేషన్లలో అమలు చేయడానికి సరళంగా మరియు మరింత ఆర్థికంగా కూడా ఉండవచ్చు. ఉదాహరణకు, సింక్రోమెష్ కేబుల్ డ్రైవ్ల యొక్క కొత్త సిరీస్ సాంప్రదాయిక తాడులు, సాధారణ కేబుల్లు మరియు కాగ్ డ్రైవ్లను భర్తీ చేయడానికి సానుకూల ట్రాక్షన్ కోసం రూపొందించబడింది, ముఖ్యంగా ఇరుకైన ప్రదేశాలలో. కొత్త కేబుల్ డ్రైవ్ కాపీయింగ్ మెషీన్లు, ప్లాటర్లు, టైప్రైటర్లు, ప్రింటర్లు వంటి ఎలక్ట్రానిక్ పరికరాలలో అధిక ఖచ్చితత్వ స్థానాలను అందించడానికి రూపొందించబడింది. కొత్త కేబుల్ డ్రైవ్ యొక్క ముఖ్య లక్షణం 3D సర్పెంటైన్ కాన్ఫిగరేషన్లలో ఉపయోగించగల సామర్థ్యం. చాలా సూక్ష్మ నమూనాలు. తాడులతో పోల్చినప్పుడు సింక్రోమెష్ కేబుల్స్ తక్కువ టెన్షన్తో ఉపయోగించబడతాయి, తద్వారా విద్యుత్ వినియోగాన్ని తగ్గిస్తుంది. బెల్ట్లు, చైన్ మరియు కేబుల్ డ్రైవ్లపై ప్రశ్నలు మరియు అభిప్రాయాల కోసం AGS-TECHని సంప్రదించండి. CLICK Product Finder-Locator Service ముందు పేజి
- Rapid Prototyping, Desktop Manufacturing, Additive Manufacturing, FDM
Rapid Prototyping, Desktop Manufacturing, Additive Manufacturing, Stereolithography, Polyjet, Fused Deposition Modeling, Selective Laser Sintering, FDM, SLS సంకలిత మరియు వేగవంతమైన తయారీ ఇటీవలి సంవత్సరాలలో, ర్యాపిడ్ మాన్యుఫాక్చరింగ్ లేదా ర్యాపిడ్ ప్రోటోటైపింగ్ కోసం డిమాండ్ పెరగడాన్ని మేము చూశాము. ఈ ప్రక్రియను డెస్క్టాప్ తయారీ లేదా ఉచిత-ఫారమ్ ఫాబ్రికేషన్ అని కూడా పిలుస్తారు. ప్రాథమికంగా ఒక భాగం యొక్క ఘన భౌతిక నమూనా నేరుగా త్రిమితీయ CAD డ్రాయింగ్ నుండి తయారు చేయబడింది. మేము పొరలలో భాగాలను నిర్మించే ఈ వివిధ సాంకేతికతలకు సంకలిత తయారీ అనే పదాన్ని ఉపయోగిస్తాము. ఇంటిగ్రేటెడ్ కంప్యూటర్ ఆధారిత హార్డ్వేర్ మరియు సాఫ్ట్వేర్ ఉపయోగించి మేము సంకలిత తయారీని చేస్తాము. మా వేగవంతమైన ప్రోటోటైపింగ్ మరియు తయారీ పద్ధతులు స్టీరియోలిథోగ్రఫీ, పాలిజెట్, ఫ్యూజ్డ్-డిపోజిషన్ మోడలింగ్, సెలెక్టివ్ లేజర్ సింటరింగ్, ఎలక్ట్రాన్ బీమ్ మెల్టింగ్, త్రీ డైమెన్షనల్ ప్రింటింగ్, డైరెక్ట్ మ్యానుఫ్యాక్టరింగ్. మీరు ఇక్కడ క్లిక్ చేయాలని మేము సిఫార్సు చేస్తున్నాముAGS-TECH Inc. ద్వారా సంకలిత తయారీ మరియు వేగవంతమైన తయారీ ప్రక్రియల యొక్క మా స్కీమాటిక్ ఇలస్ట్రేషన్లను డౌన్లోడ్ చేయండి మేము మీకు దిగువ అందిస్తున్న సమాచారాన్ని బాగా అర్థం చేసుకోవడంలో ఇది మీకు సహాయం చేస్తుంది. రాపిడ్ ప్రోటోటైపింగ్ మాకు అందిస్తుంది: 1.) 3D / CAD సిస్టమ్ని ఉపయోగించి మానిటర్లో సంభావిత ఉత్పత్తి రూపకల్పన వివిధ కోణాల నుండి వీక్షించబడుతుంది. 2.) నాన్మెటాలిక్ మరియు మెటాలిక్ మెటీరియల్స్ నుండి ప్రోటోటైప్లు క్రియాత్మక, సాంకేతిక మరియు సౌందర్య అంశాల నుండి తయారు చేయబడతాయి మరియు అధ్యయనం చేయబడతాయి. 3.) చాలా తక్కువ సమయంలో తక్కువ ఖర్చుతో కూడిన ప్రోటోటైపింగ్ సాధించబడుతుంది. సంకలిత తయారీని ఒకదానిపై ఒకటి పేర్చడం మరియు బంధించడం ద్వారా బ్రెడ్ రొట్టె నిర్మాణాన్ని పోలి ఉంటుంది. మరో మాటలో చెప్పాలంటే, ఉత్పత్తిని స్లైస్ ద్వారా తయారు చేస్తారు, లేదా పొరల వారీగా ఒకదానికొకటి జమ చేస్తారు. చాలా భాగాలను గంటల వ్యవధిలో ఉత్పత్తి చేయవచ్చు. భాగాలు చాలా త్వరగా అవసరమైతే లేదా అవసరమైన పరిమాణం తక్కువగా ఉంటే మరియు అచ్చు మరియు సాధనాన్ని తయారు చేయడం చాలా ఖరీదైనది మరియు సమయం తీసుకుంటే సాంకేతికత మంచిది. అయితే ఖరీదైన ముడి పదార్థాల కారణంగా ఒక భాగం యొక్క ధర ఖరీదైనది. • స్టీరియోలిథోగ్రఫీ: ఈ టెక్నిక్ STL అని కూడా సంక్షిప్తీకరించబడింది, లిక్విడ్ ఫోటోపాలిమర్పై లేజర్ కిరణాన్ని కేంద్రీకరించడం ద్వారా ఒక నిర్దిష్ట ఆకృతిలోకి క్యూరింగ్ మరియు గట్టిపడటంపై ఆధారపడి ఉంటుంది. లేజర్ ఫోటోపాలిమర్ను పాలిమరైజ్ చేస్తుంది మరియు దానిని నయం చేస్తుంది. ఫోటోపాలిమర్ మిశ్రమం యొక్క ఉపరితలంతో పాటు ప్రోగ్రామ్ చేయబడిన ఆకృతి ప్రకారం UV లేజర్ పుంజం స్కాన్ చేయడం ద్వారా భాగం ఒకదానికొకటి క్యాస్కేడ్ చేయబడిన వ్యక్తిగత ముక్కలలో దిగువ నుండి పైకి ఉత్పత్తి చేయబడుతుంది. సిస్టమ్లోకి ప్రోగ్రామ్ చేయబడిన జ్యామితిని సాధించడానికి లేజర్ స్పాట్ యొక్క స్కానింగ్ చాలాసార్లు పునరావృతమవుతుంది. భాగం పూర్తిగా తయారు చేయబడిన తర్వాత, అది ప్లాట్ఫారమ్ నుండి తీసివేయబడుతుంది, బ్లాట్ చేయబడింది మరియు అల్ట్రాసోనిక్గా మరియు ఆల్కహాల్ బాత్తో శుభ్రం చేయబడుతుంది. తర్వాత, పాలిమర్ పూర్తిగా నయమైందని మరియు గట్టిపడిందని నిర్ధారించుకోవడానికి ఇది కొన్ని గంటలపాటు UV వికిరణానికి గురవుతుంది. ప్రక్రియను సంగ్రహంగా చెప్పాలంటే, ఫోటోపాలిమర్ మిశ్రమంలో ముంచిన ప్లాట్ఫారమ్ మరియు UV లేజర్ పుంజం నియంత్రించబడతాయి మరియు కావలసిన భాగం యొక్క ఆకృతిని బట్టి సర్వో-నియంత్రణ వ్యవస్థ ద్వారా తరలించబడతాయి మరియు పొర ద్వారా పాలిమర్ పొరను ఫోటోక్యూరింగ్ చేయడం ద్వారా భాగం పొందబడుతుంది. ఉత్పత్తి భాగం యొక్క గరిష్ట కొలతలు స్టీరియోలిథోగ్రఫీ పరికరాల ద్వారా నిర్ణయించబడతాయి. • POLYJET : ఇంక్జెట్ ప్రింటింగ్ లాగానే, పాలీజెట్లో మనకు ఎనిమిది ప్రింట్ హెడ్లు ఉన్నాయి, ఇవి బిల్డ్ ట్రేలో ఫోటోపాలిమర్ను డిపాజిట్ చేస్తాయి. జెట్ల పక్కన ఉంచిన అతినీలలోహిత కాంతి వెంటనే ప్రతి పొరను నయం చేస్తుంది మరియు గట్టిపరుస్తుంది. పాలీజెట్లో రెండు పదార్థాలు ఉపయోగించబడతాయి. మొదటి పదార్థం అసలు మోడల్ను తయారు చేయడం. రెండవ పదార్థం, జెల్ లాంటి రెసిన్ మద్దతు కోసం ఉపయోగించబడుతుంది. ఈ రెండు పదార్థాలు పొరల వారీగా జమ చేయబడతాయి మరియు ఏకకాలంలో నయం చేయబడతాయి. మోడల్ పూర్తయిన తర్వాత, సజల ద్రావణంతో సపోర్ట్ మెటీరియల్ తీసివేయబడుతుంది. ఉపయోగించిన రెసిన్లు స్టీరియోలిథోగ్రఫీ (STL) మాదిరిగానే ఉంటాయి. స్టీరియోలిథోగ్రఫీ కంటే పాలీజెట్ క్రింది ప్రయోజనాలను కలిగి ఉంది: 1.) భాగాలను శుభ్రపరచడం అవసరం లేదు. 2.) పోస్ట్ప్రాసెస్ క్యూరింగ్ అవసరం లేదు 3.) చిన్న పొర మందం సాధ్యమవుతుంది మరియు తద్వారా మనం మంచి రిజల్యూషన్ను పొందుతాము మరియు చక్కటి భాగాలను తయారు చేయగలము. • ఫ్యూజ్డ్ డిపోజిషన్ మోడలింగ్: FDM అని కూడా సంక్షిప్తీకరించబడింది, ఈ పద్ధతిలో రోబోట్-నియంత్రిత ఎక్స్ట్రూడర్ హెడ్ టేబుల్పై రెండు సూత్రాల దిశల్లో కదులుతుంది. అవసరమైన విధంగా కేబుల్ తగ్గించబడుతుంది మరియు పెంచబడుతుంది. తలపై వేడిచేసిన డై యొక్క రంధ్రం నుండి, ఒక థర్మోప్లాస్టిక్ ఫిలమెంట్ వెలికితీయబడుతుంది మరియు ప్రారంభ పొర నురుగు పునాదిపై జమ చేయబడుతుంది. ముందుగా నిర్ణయించిన మార్గాన్ని అనుసరించే ఎక్స్ట్రూడర్ హెడ్ ద్వారా ఇది సాధించబడుతుంది. ప్రారంభ పొర తర్వాత, పట్టిక తగ్గించబడుతుంది మరియు తదుపరి పొరలు ఒకదానిపై ఒకటి జమ చేయబడతాయి. కొన్నిసార్లు సంక్లిష్టమైన భాగాన్ని తయారు చేస్తున్నప్పుడు, నిర్దిష్ట దిశలలో నిక్షేపణ కొనసాగేలా సహాయక నిర్మాణాలు అవసరమవుతాయి. ఈ సందర్భాలలో, ఒక సపోర్టింగ్ మెటీరియల్ పొరపై తక్కువ దట్టమైన ఫిలమెంట్ అంతరాన్ని కలిగి ఉంటుంది, తద్వారా ఇది మోడల్ మెటీరియల్ కంటే బలహీనంగా ఉంటుంది. ఈ సపోర్టు స్ట్రక్చర్లను ఆ భాగం పూర్తయిన తర్వాత కరిగించవచ్చు లేదా విచ్ఛిన్నం చేయవచ్చు. ఎక్స్ట్రూడర్ డై కొలతలు వెలికితీసిన పొరల మందాన్ని నిర్ణయిస్తాయి. FDM ప్రక్రియ వాలుగా ఉన్న బాహ్య విమానాలపై స్టెప్డ్ ఉపరితలాలతో భాగాలను ఉత్పత్తి చేస్తుంది. ఈ కరుకుదనం ఆమోదయోగ్యం కానట్లయితే, వీటిని సున్నితంగా చేయడానికి రసాయన ఆవిరి పాలిషింగ్ లేదా వేడిచేసిన సాధనాన్ని ఉపయోగించవచ్చు. పాలిషింగ్ మైనపు కూడా ఈ దశలను తొలగించడానికి మరియు సహేతుకమైన రేఖాగణిత సహనాన్ని సాధించడానికి పూత పదార్థంగా అందుబాటులో ఉంది. • సెలెక్టివ్ లేజర్ సింటరింగ్ : SLSగా కూడా సూచించబడుతుంది, ఈ ప్రక్రియ పాలిమర్, సిరామిక్ లేదా మెటాలిక్ పౌడర్లను ఎంపిక చేసి ఒక వస్తువులోకి సింటరింగ్ చేయడంపై ఆధారపడి ఉంటుంది. ప్రాసెసింగ్ చాంబర్ దిగువన రెండు సిలిండర్లు ఉన్నాయి: పార్ట్-బిల్డ్ సిలిండర్ మరియు పౌడర్-ఫీడ్ సిలిండర్. మునుపటిది సిన్టర్డ్ భాగం ఏర్పడే చోటికి క్రమంగా తగ్గించబడుతుంది మరియు రెండోది రోలర్ మెకానిజం ద్వారా పార్ట్-బిల్డ్ సిలిండర్కు పౌడర్ను సరఫరా చేయడానికి క్రమంగా పెంచబడుతుంది. ముందుగా పౌడర్ యొక్క పలుచని పొర పార్ట్-బిల్డ్ సిలిండర్లో నిక్షిప్తం చేయబడుతుంది, తర్వాత లేజర్ పుంజం ఆ పొరపై కేంద్రీకరించబడుతుంది, ఒక నిర్దిష్ట క్రాస్ సెక్షన్ను గుర్తించడం మరియు కరిగించడం/సింటరింగ్ చేయడం, అది ఘన రూపంలోకి మారుతుంది. పౌడర్ అంటే లేజర్ పుంజం దెబ్బతినని ప్రాంతాలు వదులుగా ఉంటాయి కానీ ఇప్పటికీ ఘన భాగానికి మద్దతు ఇస్తాయి. అప్పుడు పొడి యొక్క మరొక పొర జమ చేయబడుతుంది మరియు భాగాన్ని పొందేందుకు ప్రక్రియ చాలాసార్లు పునరావృతమవుతుంది. చివర్లో, వదులుగా ఉన్న పొడి కణాలు కదిలించబడతాయి. తయారు చేయబడుతున్న భాగం యొక్క 3D CAD ప్రోగ్రామ్ ద్వారా రూపొందించబడిన సూచనలను ఉపయోగించి ఇవన్నీ ప్రాసెస్-కంట్రోల్ కంప్యూటర్ ద్వారా నిర్వహించబడతాయి. పాలిమర్లు (ABS, PVC, పాలిస్టర్ వంటివి), మైనపు, లోహాలు మరియు తగిన పాలిమర్ బైండర్లతో కూడిన సిరామిక్లు వంటి వివిధ పదార్థాలను డిపాజిట్ చేయవచ్చు. • ELECTRON-BEAM MELTING : సెలెక్టివ్ లేజర్ సింటరింగ్ లాగానే ఉంటుంది, అయితే వాక్యూమ్లో ప్రోటోటైప్లను తయారు చేయడానికి టైటానియం లేదా కోబాల్ట్ క్రోమ్ పౌడర్లను కరిగించడానికి ఎలక్ట్రాన్ బీమ్ని ఉపయోగించడం. స్టెయిన్లెస్ స్టీల్స్, అల్యూమినియం మరియు రాగి మిశ్రమాలపై ఈ ప్రక్రియను నిర్వహించడానికి కొన్ని అభివృద్ధి చేయబడింది. ఉత్పత్తి చేయబడిన భాగాల యొక్క అలసట బలాన్ని పెంచాల్సిన అవసరం ఉన్నట్లయితే, మేము ద్వితీయ ప్రక్రియగా పార్ట్ తయారీ తర్వాత హాట్ ఐసోస్టాటిక్ నొక్కడం ఉపయోగిస్తాము. • త్రీ-డైమెన్షనల్ ప్రింటింగ్ : 3DPతో కూడా సూచించబడుతుంది, ఈ టెక్నిక్లో ప్రింట్ హెడ్ ఒక అకర్బన బైండర్ను నాన్మెటాలిక్ లేదా మెటాలిక్ పౌడర్ పొరపై జమ చేస్తుంది. పౌడర్ బెడ్ను మోసే పిస్టన్ క్రమంగా తగ్గించబడుతుంది మరియు ప్రతి దశలోనూ బైండర్ layer ద్వారా పొరల వారీగా జమ చేయబడుతుంది మరియు బైండర్ ద్వారా ఫ్యూజ్ చేయబడుతుంది. ఉపయోగించిన పౌడర్ పదార్థాలు పాలిమర్ల మిశ్రమాలు మరియు ఫైబర్స్, ఫౌండరీ ఇసుక, లోహాలు. వేర్వేరు బైండర్ హెడ్లను ఏకకాలంలో మరియు విభిన్న రంగు బైండర్లను ఉపయోగించి మనం వివిధ రంగులను పొందవచ్చు. ఈ ప్రక్రియ ఇంక్జెట్ ప్రింటింగ్ను పోలి ఉంటుంది కానీ రంగు షీట్ను పొందే బదులు మనం రంగు త్రిమితీయ వస్తువును పొందుతాము. ఉత్పత్తి చేయబడిన భాగాలు పోరస్ కావచ్చు మరియు దాని సాంద్రత మరియు బలాన్ని పెంచడానికి సింటరింగ్ మరియు మెటల్ ఇన్ఫిల్ట్రేషన్ అవసరం కావచ్చు. సింటరింగ్ బైండర్ను కాల్చివేస్తుంది మరియు మెటల్ పౌడర్లను ఫ్యూజ్ చేస్తుంది. స్టెయిన్లెస్ స్టీల్, అల్యూమినియం, టైటానియం వంటి లోహాలు భాగాలను తయారు చేయడానికి ఉపయోగించవచ్చు మరియు చొరబాటు పదార్థాలుగా మనం సాధారణంగా రాగి మరియు కాంస్యాన్ని ఉపయోగిస్తాము. ఈ సాంకేతికత యొక్క అందం ఏమిటంటే సంక్లిష్టమైన మరియు కదిలే సమావేశాలు కూడా చాలా త్వరగా తయారు చేయబడతాయి. ఉదాహరణకు ఒక గేర్ అసెంబ్లీ, ఒక సాధనంగా ఒక రెంచ్ తయారు చేయవచ్చు మరియు కదిలే మరియు టర్నింగ్ భాగాలను ఉపయోగించడానికి సిద్ధంగా ఉంటుంది. అసెంబ్లీలోని వివిధ భాగాలను వేర్వేరు రంగులతో తయారు చేయవచ్చు మరియు అన్నింటినీ ఒకే షాట్లో తయారు చేయవచ్చు. మా బ్రోచర్ను ఇందులో డౌన్లోడ్ చేసుకోండి:మెటల్ 3D ప్రింటింగ్ బేసిక్స్ • ప్రత్యక్ష తయారీ మరియు రాపిడ్ టూలింగ్: డిజైన్ మూల్యాంకనం, ట్రబుల్షూటింగ్తో పాటు ఉత్పత్తుల యొక్క ప్రత్యక్ష తయారీకి లేదా ఉత్పత్తుల్లోకి నేరుగా దరఖాస్తు చేయడానికి మేము వేగవంతమైన నమూనాను ఉపయోగిస్తాము. మరో మాటలో చెప్పాలంటే, వేగవంతమైన ప్రోటోటైపింగ్ వాటిని మెరుగైన మరియు మరింత పోటీగా చేయడానికి సాంప్రదాయ ప్రక్రియలలో చేర్చబడుతుంది. ఉదాహరణకు, వేగవంతమైన ప్రోటోటైపింగ్ నమూనాలు మరియు అచ్చులను ఉత్పత్తి చేస్తుంది. వేగవంతమైన ప్రోటోటైపింగ్ కార్యకలాపాల ద్వారా సృష్టించబడిన ద్రవీభవన మరియు మండే పాలిమర్ యొక్క నమూనాలను పెట్టుబడి కాస్టింగ్ కోసం సమీకరించవచ్చు మరియు పెట్టుబడి పెట్టవచ్చు. ప్రస్తావించడానికి మరొక ఉదాహరణ సిరామిక్ కాస్టింగ్ షెల్ను ఉత్పత్తి చేయడానికి 3DPని ఉపయోగించడం మరియు షెల్ కాస్టింగ్ కార్యకలాపాలకు ఉపయోగించడం. ఇంజెక్షన్ అచ్చులు మరియు అచ్చు ఇన్సర్ట్లు కూడా వేగవంతమైన నమూనా ద్వారా ఉత్పత్తి చేయబడతాయి మరియు అనేక వారాలు లేదా నెలల అచ్చు తయారీకి ప్రధాన సమయాన్ని ఆదా చేయవచ్చు. కావలసిన భాగం యొక్క CAD ఫైల్ను మాత్రమే విశ్లేషించడం ద్వారా, మేము సాఫ్ట్వేర్ని ఉపయోగించి సాధనం జ్యామితిని ఉత్పత్తి చేయవచ్చు. ఇక్కడ మా ప్రసిద్ధ శీఘ్ర సాధన పద్ధతులు కొన్ని: RTV (గది-ఉష్ణోగ్రత వల్కనైజింగ్) మోల్డింగ్ / యూరేథేన్ కాస్టింగ్: త్వరిత నమూనాను ఉపయోగించి కావలసిన భాగం యొక్క నమూనాను తయారు చేయడానికి ఉపయోగించవచ్చు. అప్పుడు ఈ నమూనాను విడిపోయే ఏజెంట్తో పూత పూయాలి మరియు అచ్చు భాగాలను ఉత్పత్తి చేయడానికి ద్రవ RTV రబ్బరు నమూనాపై పోస్తారు. తరువాత, ఈ అచ్చు భాగాలు అచ్చు ద్రవ యురేథేన్లను ఇంజెక్షన్ చేయడానికి ఉపయోగిస్తారు. అచ్చు జీవితం చిన్నది, కేవలం 0 లేదా 30 సైకిల్స్ లాగా ఉంటుంది కానీ చిన్న బ్యాచ్ ఉత్పత్తికి సరిపోతుంది. ACES (ఎసిటల్ క్లియర్ ఎపోక్సీ సాలిడ్) ఇంజెక్షన్ మౌల్డింగ్: స్టీరియోలిథోగ్రఫీ వంటి వేగవంతమైన ప్రోటోటైపింగ్ పద్ధతులను ఉపయోగించి, మేము ఇంజెక్షన్ అచ్చులను ఉత్పత్తి చేస్తాము. ఈ అచ్చులు ఎపాక్సి, అల్యూమినియం-నిండిన ఎపాక్సి లేదా లోహాలు వంటి పదార్థాలతో నింపడానికి అనుమతించడానికి ఓపెన్ ఎండ్తో షెల్లు. మళ్లీ అచ్చు జీవితం పదుల లేదా గరిష్టంగా వందల భాగాలకు పరిమితం చేయబడింది. స్ప్రేడ్ మెటల్ టూలింగ్ ప్రాసెస్: మేము వేగవంతమైన నమూనాను ఉపయోగిస్తాము మరియు నమూనాను తయారు చేస్తాము. మేము నమూనా ఉపరితలంపై జింక్-అల్యూమినియం మిశ్రమాన్ని స్ప్రే చేస్తాము మరియు దానిని కోట్ చేస్తాము. లోహపు పూతతో ఉన్న నమూనా ఒక ఫ్లాస్క్ లోపల ఉంచబడుతుంది మరియు ఒక ఎపోక్సీ లేదా అల్యూమినియంతో నిండిన ఎపాక్సీతో కుండలో ఉంచబడుతుంది. చివరగా, అది తీసివేయబడుతుంది మరియు అలాంటి రెండు అచ్చు భాగాలను ఉత్పత్తి చేయడం ద్వారా మేము ఇంజెక్షన్ మోల్డింగ్ కోసం పూర్తి అచ్చును పొందుతాము. ఈ అచ్చులు ఎక్కువ కాలం జీవిస్తాయి, కొన్ని సందర్భాల్లో పదార్థం మరియు ఉష్ణోగ్రతల ఆధారంగా అవి వేలల్లో భాగాలను ఉత్పత్తి చేయగలవు. కీల్టూల్ ప్రక్రియ: ఈ సాంకేతికత 100,000 నుండి 10 మిలియన్ సైకిల్ జీవితాలతో అచ్చులను ఉత్పత్తి చేయగలదు. వేగవంతమైన నమూనాను ఉపయోగించి మేము RTV అచ్చును ఉత్పత్తి చేస్తాము. అచ్చు తదుపరి A6 టూల్ స్టీల్ పౌడర్, టంగ్స్టన్ కార్బైడ్, పాలిమర్ బైండర్తో కూడిన మిశ్రమంతో నింపబడి, నయం చేయడానికి వీలు కల్పిస్తుంది. ఈ అచ్చు పాలిమర్ను కాల్చివేయడానికి మరియు మెటల్ పౌడర్లను ఫ్యూజ్ చేయడానికి వేడి చేయబడుతుంది. తదుపరి దశ తుది అచ్చును ఉత్పత్తి చేయడానికి రాగి చొరబాటు. అవసరమైతే, మెరుగైన డైమెన్షనల్ ఖచ్చితత్వాల కోసం అచ్చుపై మ్యాచింగ్ మరియు పాలిషింగ్ వంటి ద్వితీయ కార్యకలాపాలను నిర్వహించవచ్చు. _cc781905-5cde-3194-bb3b-1358bad_5 CLICK Product Finder-Locator Service ముందు పేజి
- Joining & Assembly & Fastening Processes, Welding, Brazing, Soldering
Joining & Assembly & Fastening Processes, Welding, Brazing, Soldering, Sintering, Adhesive Bonding, Press Fitting, Wave and Reflow Solder Process, Torch Furnace చేరడం & అసెంబ్లీ & ఫాస్టెనింగ్ ప్రక్రియలు మేము మీ తయారు చేసిన భాగాలను కలుపుతాము, సమీకరించాము మరియు కట్టివేస్తాము మరియు వాటిని వెల్డింగ్, బ్రేజింగ్, సోల్డరింగ్, సింటరింగ్, అడెసివ్ బాండింగ్, ఫాస్టెనింగ్, ప్రెస్ ఫిట్టింగ్ ఉపయోగించి పూర్తి చేసిన లేదా సెమీ-ఫినిష్డ్ ఉత్పత్తులుగా మారుస్తాము. ఆర్క్, ఆక్సిఫ్యూయల్ గ్యాస్, రెసిస్టెన్స్, ప్రొజెక్షన్, సీమ్, అప్సెట్, పెర్కషన్, సాలిడ్ స్టేట్, ఎలక్ట్రాన్ బీమ్, లేజర్, థర్మిట్, ఇండక్షన్ వెల్డింగ్ వంటివి మా అత్యంత ప్రసిద్ధ వెల్డింగ్ ప్రక్రియలలో కొన్ని. మా ప్రసిద్ధ బ్రేజింగ్ ప్రక్రియలు టార్చ్, ఇండక్షన్, ఫర్నేస్ మరియు డిప్ బ్రేజింగ్. మా టంకం పద్ధతులు ఐరన్, హాట్ ప్లేట్, ఓవెన్, ఇండక్షన్, డిప్, వేవ్, రిఫ్లో మరియు అల్ట్రాసోనిక్ టంకం. అంటుకునే బంధం కోసం మేము తరచుగా థర్మోప్లాస్టిక్లు మరియు థర్మో-సెట్టింగ్, ఎపాక్సీలు, ఫినోలిక్స్, పాలియురేతేన్, అంటుకునే మిశ్రమాలు అలాగే కొన్ని ఇతర రసాయనాలు మరియు టేపులను ఉపయోగిస్తాము. చివరగా మా బందు ప్రక్రియలు నెయిలింగ్, స్క్రూయింగ్, నట్స్ మరియు బోల్ట్లు, రివెటింగ్, క్లిన్చింగ్, పిన్నింగ్, స్టిచింగ్ & స్టెప్లింగ్ మరియు ప్రెస్ ఫిట్టింగ్లను కలిగి ఉంటాయి. • వెల్డింగ్ : వెల్డింగ్ అనేది వర్క్ పీస్లను కరిగించడం మరియు పూరక పదార్థాలను పరిచయం చేయడం ద్వారా పదార్థాలను కలపడం, అది కూడా కరిగిన వెల్డ్ పూల్లో చేరడం. ప్రాంతం చల్లబడినప్పుడు, మేము బలమైన ఉమ్మడిని పొందుతాము. కొన్ని సందర్భాల్లో ఒత్తిడి ఉంటుంది. వెల్డింగ్కి విరుద్ధంగా, బ్రేజింగ్ మరియు టంకం ఆపరేషన్లు వర్క్పీస్ల మధ్య తక్కువ ద్రవీభవన స్థానం ఉన్న పదార్థం యొక్క ద్రవీభవనాన్ని మాత్రమే కలిగి ఉంటాయి మరియు వర్క్పీస్లు కరగవు. మీరు ఇక్కడ క్లిక్ చేయాలని మేము సిఫార్సు చేస్తున్నాముAGS-TECH ఇంక్ ద్వారా వెల్డింగ్ ప్రక్రియల మా స్కీమాటిక్ ఇలస్ట్రేషన్లను డౌన్లోడ్ చేయండి. మేము మీకు దిగువ అందిస్తున్న సమాచారాన్ని బాగా అర్థం చేసుకోవడంలో ఇది మీకు సహాయం చేస్తుంది. ARC వెల్డింగ్లో, లోహాలను కరిగించే విద్యుత్ ఆర్క్ను రూపొందించడానికి మేము విద్యుత్ సరఫరా మరియు ఎలక్ట్రోడ్ను ఉపయోగిస్తాము. వెల్డింగ్ పాయింట్ ఒక రక్షిత వాయువు లేదా ఆవిరి లేదా ఇతర పదార్థం ద్వారా రక్షించబడుతుంది. ఈ ప్రక్రియ వెల్డింగ్ ఆటోమోటివ్ భాగాలు మరియు ఉక్కు నిర్మాణాలకు ప్రసిద్ధి చెందింది. షెల్డ్ మెటల్ ఆర్క్ వెల్డింగ్ (SMAW)లో లేదా స్టిక్ వెల్డింగ్ అని కూడా పిలుస్తారు, ఒక ఎలక్ట్రోడ్ స్టిక్ బేస్ మెటీరియల్కు దగ్గరగా తీసుకురాబడుతుంది మరియు వాటి మధ్య ఎలక్ట్రిక్ ఆర్క్ ఉత్పత్తి అవుతుంది. ఎలక్ట్రోడ్ రాడ్ కరుగుతుంది మరియు పూరక పదార్థంగా పనిచేస్తుంది. ఎలక్ట్రోడ్ స్లాగ్ పొరగా పనిచేసే ఫ్లక్స్ను కూడా కలిగి ఉంటుంది మరియు రక్షిత వాయువుగా పనిచేసే ఆవిరిని ఇస్తుంది. ఇవి పర్యావరణ కాలుష్యం నుండి వెల్డ్ ప్రాంతాన్ని రక్షిస్తాయి. ఇతర ఫిల్లర్లు ఉపయోగించబడవు. ఈ ప్రక్రియ యొక్క ప్రతికూలతలు దాని మందగమనం, తరచుగా ఎలక్ట్రోడ్లను భర్తీ చేయడం, ఫ్లక్స్ నుండి ఉద్భవించే అవశేష స్లాగ్ను చిప్ చేయడం అవసరం. ఇనుము, ఉక్కు, నికెల్, అల్యూమినియం, రాగి... మొదలైన అనేక లోహాలు. వెల్డింగ్ చేయవచ్చు. దీని ప్రయోజనాలు దాని చవకైన సాధనాలు మరియు వాడుకలో సౌలభ్యం. గ్యాస్ మెటల్ ఆర్క్ వెల్డింగ్ (GMAW)ను మెటల్-ఇనర్ట్ గ్యాస్ (MIG) అని కూడా పిలుస్తారు, మేము వినియోగించదగిన ఎలక్ట్రోడ్ వైర్ ఫిల్లర్ మరియు వెల్డ్ ప్రాంతం యొక్క పర్యావరణ కాలుష్యానికి వ్యతిరేకంగా వైర్ చుట్టూ ప్రవహించే జడ లేదా పాక్షికంగా జడ వాయువును నిరంతరంగా అందిస్తాము. ఉక్కు, అల్యూమినియం మరియు ఇతర నాన్-ఫెర్రస్ లోహాలు వెల్డింగ్ చేయబడతాయి. MIG యొక్క ప్రయోజనాలు అధిక వెల్డింగ్ వేగం మరియు మంచి నాణ్యత. ప్రతికూలతలు దాని సంక్లిష్టమైన పరికరాలు మరియు గాలులతో కూడిన బహిరంగ వాతావరణంలో ఎదుర్కొనే సవాళ్లు, ఎందుకంటే మేము వెల్డింగ్ ప్రాంతం చుట్టూ ఉన్న షీల్డింగ్ గ్యాస్ను స్థిరంగా నిర్వహించాలి. GMAW యొక్క వైవిధ్యం ఫ్లక్స్-కోర్డ్ ఆర్క్ వెల్డింగ్ (FCAW), ఇది ఫ్లక్స్ మెటీరియల్తో నిండిన చక్కటి మెటల్ ట్యూబ్ను కలిగి ఉంటుంది. కొన్నిసార్లు పర్యావరణ కాలుష్యం నుండి రక్షణ కోసం ట్యూబ్ లోపల ఫ్లక్స్ సరిపోతుంది. సబ్మెర్జ్డ్ ఆర్క్ వెల్డింగ్ (SAW) విస్తృతంగా స్వయంచాలక ప్రక్రియ, నిరంతర వైర్ ఫీడింగ్ మరియు ఫ్లక్స్ కవర్ పొర కింద కొట్టబడిన ఆర్క్ను కలిగి ఉంటుంది. ఉత్పత్తి రేట్లు మరియు నాణ్యత ఎక్కువగా ఉన్నాయి, వెల్డింగ్ స్లాగ్ సులభంగా వస్తుంది మరియు మేము పొగ రహిత పని వాతావరణాన్ని కలిగి ఉన్నాము. ప్రతికూలత ఏమిటంటే ఇది partsని నిర్దిష్ట స్థానాల్లో వెల్డ్ చేయడానికి మాత్రమే ఉపయోగించబడుతుంది. గ్యాస్ టంగ్స్టన్ ఆర్క్ వెల్డింగ్ (GTAW) లేదా టంగ్స్టన్-జడ గ్యాస్ వెల్డింగ్ (TIG)లో మేము టంగ్స్టన్ ఎలక్ట్రోడ్ను ప్రత్యేక పూరకం మరియు జడ లేదా సమీపంలోని జడ వాయువులతో పాటు ఉపయోగిస్తాము. మనకు తెలిసినట్లుగా టంగ్స్టన్ అధిక ద్రవీభవన స్థానం కలిగి ఉంటుంది మరియు ఇది చాలా అధిక ఉష్ణోగ్రతలకు చాలా సరిఅయిన లోహం. TIGలోని టంగ్స్టన్ పైన వివరించిన ఇతర పద్ధతులకు విరుద్ధంగా వినియోగించబడదు. సన్నని పదార్థాల వెల్డింగ్లో ఇతర పద్ధతుల కంటే నెమ్మదిగా కానీ అధిక నాణ్యత గల వెల్డింగ్ టెక్నిక్ ప్రయోజనకరంగా ఉంటుంది. అనేక లోహాలకు అనుకూలం. ప్లాస్మా ఆర్క్ వెల్డింగ్ సారూప్యంగా ఉంటుంది కానీ ఆర్క్ను రూపొందించడానికి ప్లాస్మా వాయువును ఉపయోగిస్తుంది. ప్లాస్మా ఆర్క్ వెల్డింగ్లోని ఆర్క్ GTAWతో పోల్చితే సాపేక్షంగా ఎక్కువ కేంద్రీకృతమై ఉంటుంది మరియు చాలా ఎక్కువ వేగంతో విస్తృత శ్రేణి మెటల్ మందం కోసం ఉపయోగించవచ్చు. GTAW మరియు ప్లాస్మా ఆర్క్ వెల్డింగ్ ఎక్కువ లేదా తక్కువ ఒకే పదార్థాలకు వర్తించవచ్చు. OXY-FUEL / OXYFUEL వెల్డింగ్ను oxyacetylene వెల్డింగ్ అని కూడా పిలుస్తారు, oxy వెల్డింగ్, గ్యాస్ వెల్డింగ్ను వెల్డింగ్ కోసం గ్యాస్ ఇంధనాలు మరియు ఆక్సిజన్ ఉపయోగించి నిర్వహిస్తారు. విద్యుత్ శక్తి ఉపయోగించబడనందున ఇది పోర్టబుల్ మరియు విద్యుత్ లేని చోట ఉపయోగించవచ్చు. ఒక వెల్డింగ్ టార్చ్ ఉపయోగించి మేము పంచుకున్న కరిగిన మెటల్ పూల్ను ఉత్పత్తి చేయడానికి ముక్కలు మరియు పూరక పదార్థాన్ని వేడి చేస్తాము. ఎసిటిలీన్, గ్యాసోలిన్, హైడ్రోజన్, ప్రొపేన్, బ్యూటేన్... మొదలైన వివిధ ఇంధనాలను ఉపయోగించవచ్చు. ఆక్సి-ఇంధన వెల్డింగ్లో మనం రెండు కంటైనర్లను ఉపయోగిస్తాము, ఒకటి ఇంధనం కోసం మరియు మరొకటి ఆక్సిజన్ కోసం. ఆక్సిజన్ ఇంధనాన్ని ఆక్సీకరణం చేస్తుంది (దహనం చేస్తుంది). రెసిస్టెన్స్ వెల్డింగ్: ఈ రకమైన వెల్డింగ్ జౌల్ హీటింగ్ యొక్క ప్రయోజనాన్ని పొందుతుంది మరియు నిర్దిష్ట సమయం వరకు విద్యుత్ ప్రవాహాన్ని వర్తించే ప్రదేశంలో వేడి ఉత్పత్తి అవుతుంది. అధిక ప్రవాహాలు మెటల్ గుండా వెళతాయి. ఈ ప్రదేశంలో కరిగిన లోహపు కొలనులు ఏర్పడతాయి. రెసిస్టెన్స్ వెల్డింగ్ పద్ధతులు వాటి సామర్థ్యం, తక్కువ కాలుష్య సంభావ్యత కారణంగా ప్రసిద్ధి చెందాయి. అయితే నష్టాలు పరికరాల ఖర్చులు సాపేక్షంగా ముఖ్యమైనవి మరియు సాపేక్షంగా సన్నని పని ముక్కలకు స్వాభావిక పరిమితి. స్పాట్ వెల్డింగ్ అనేది రెసిస్టెన్స్ వెల్డింగ్లో ఒక ప్రధాన రకం. ఇక్కడ మనం రెండు లేదా అంతకంటే ఎక్కువ అతివ్యాప్తి చెందుతున్న షీట్లు లేదా వర్క్పీస్లను రెండు రాగి ఎలక్ట్రోడ్లను ఉపయోగించి షీట్లను బిగించి, వాటి ద్వారా అధిక కరెంట్ను పంపుతాము. రాగి ఎలక్ట్రోడ్ల మధ్య పదార్థం వేడెక్కుతుంది మరియు ఆ ప్రదేశంలో కరిగిన కొలను ఏర్పడుతుంది. కరెంట్ ఆగిపోతుంది మరియు రాగి ఎలక్ట్రోడ్ చిట్కాలు వెల్డ్ స్థానాన్ని చల్లబరుస్తాయి ఎందుకంటే ఎలక్ట్రోడ్లు నీరు చల్లబడతాయి. సరైన పదార్థం మరియు మందంతో సరైన మొత్తంలో వేడిని వర్తింపజేయడం ఈ సాంకేతికతకు కీలకం, ఎందుకంటే తప్పుగా దరఖాస్తు చేస్తే కీలు బలహీనంగా ఉంటుంది. స్పాట్ వెల్డింగ్ అనేది వర్క్పీస్లకు గణనీయమైన రూపాంతరం కలిగించకుండా ఉండటం, శక్తి సామర్థ్యం, ఆటోమేషన్ సౌలభ్యం మరియు అత్యుత్తమ ఉత్పత్తి రేట్లు మరియు ఎటువంటి ఫిల్లర్లు అవసరం లేని ప్రయోజనాలను కలిగి ఉంది. ప్రతికూలత ఏమిటంటే, వెల్డింగ్ అనేది ఒక నిరంతర సీమ్ను ఏర్పరచడం కంటే మచ్చల వద్ద జరుగుతుంది కాబట్టి, ఇతర వెల్డింగ్ పద్ధతులతో పోలిస్తే మొత్తం బలం సాపేక్షంగా తక్కువగా ఉంటుంది. మరోవైపు, సీమ్ వెల్డింగ్ సారూప్య పదార్థాల ఫేయింగ్ ఉపరితలాల వద్ద వెల్డ్స్ను ఉత్పత్తి చేస్తుంది. సీమ్ బట్ లేదా అతివ్యాప్తి ఉమ్మడిగా ఉంటుంది. సీమ్ వెల్డింగ్ ఒక చివరలో ప్రారంభమవుతుంది మరియు క్రమంగా మరొకదానికి కదులుతుంది. ఈ పద్ధతి వెల్డ్ ప్రాంతానికి ఒత్తిడి మరియు కరెంట్ను వర్తింపజేయడానికి రాగి నుండి రెండు ఎలక్ట్రోడ్లను కూడా ఉపయోగిస్తుంది. డిస్క్ ఆకారపు ఎలక్ట్రోడ్లు సీమ్ లైన్ వెంట స్థిరమైన పరిచయంతో తిరుగుతాయి మరియు నిరంతర వెల్డ్ చేస్తాయి. ఇక్కడ కూడా, ఎలక్ట్రోడ్లు నీటి ద్వారా చల్లబడతాయి. వెల్డ్స్ చాలా బలంగా మరియు నమ్మదగినవి. ఇతర పద్ధతులు ప్రొజెక్షన్, ఫ్లాష్ మరియు అప్సెట్ వెల్డింగ్ పద్ధతులు. SOLID-STATE వెల్డింగ్ అనేది పైన వివరించిన మునుపటి పద్ధతుల కంటే కొంచెం భిన్నంగా ఉంటుంది. కలపబడిన లోహాల ద్రవీభవన ఉష్ణోగ్రత కంటే తక్కువ ఉష్ణోగ్రతల వద్ద మరియు మెటల్ పూరకాన్ని ఉపయోగించకుండా కోలెసెన్స్ జరుగుతుంది. కొన్ని ప్రక్రియలలో ఒత్తిడిని ఉపయోగించవచ్చు. వివిధ పద్ధతులు కోఎక్స్ట్రూషన్ వెల్డింగ్, ఇక్కడ ఒకే డై ద్వారా అసమాన లోహాలు వెలికితీయబడతాయి, కోల్డ్ ప్రెజర్ వెల్డింగ్, మనం వాటి ద్రవీభవన బిందువుల క్రింద మృదువైన మిశ్రమాలను కలిపే చోట, డిఫ్యూజన్ వెల్డింగ్, కనిపించే వెల్డ్ లైన్లు లేకుండా ఒక టెక్నిక్, ఎక్స్ప్లోషన్ వెల్డింగ్, అసమానమైన అన్ని పదార్థాలను కలపడం. స్టీల్స్, విద్యుదయస్కాంత శక్తుల ద్వారా ట్యూబ్లు మరియు షీట్లను వేగవంతం చేసే విద్యుదయస్కాంత పల్స్ వెల్డింగ్, లోహాలను అధిక ఉష్ణోగ్రతలకు వేడి చేయడం మరియు వాటిని సుత్తితో కొట్టడం వంటి వాటిని కలిగి ఉండే ఫోర్జ్ వెల్డింగ్, తగినంత రాపిడితో వెల్డింగ్ చేసే చోట FRICTION వెల్డింగ్, భ్రమణం లేని చక్రాన్ని తిప్పడం వంటివి ఉంటాయి. ఉమ్మడి రేఖను దాటే వినియోగించదగిన సాధనం, వాక్యూమ్ లేదా జడ వాయువులలో ద్రవీభవన ఉష్ణోగ్రత కంటే తక్కువ ఉష్ణోగ్రతల వద్ద మనం లోహాలను కలిపి నొక్కే వేడి పీడన వెల్డింగ్, వేడి ఐసోస్టాటిక్ ప్రెషర్ వెల్డింగ్ అనేది ఒక పాత్రలో జడ వాయువులను ఉపయోగించి ఒత్తిడిని ప్రయోగించే ప్రక్రియ, రోల్ వెల్డింగ్ మధ్య బలవంతంగా అసమాన పదార్థాలు రెండు తిరిగే చక్రాలు, అల్ట్రాసోనిక్ వెల్డింగ్, ఇక్కడ సన్నని మెటల్ లేదా ప్లాస్టిక్ షీట్లను అధిక ఫ్రీక్వెన్సీ వైబ్రేషనల్ ఎనర్జీని ఉపయోగించి వెల్డింగ్ చేస్తారు. మా ఇతర వెల్డింగ్ ప్రక్రియలు లోతైన వ్యాప్తి మరియు వేగవంతమైన ప్రాసెసింగ్తో కూడిన ELECTRON BEAM వెల్డింగ్ అయితే ఖరీదైన పద్ధతిగా మేము దీనిని ప్రత్యేక సందర్భాలలో పరిగణిస్తాము, ELECTROSLAG వెల్డింగ్ అనేది భారీ మందపాటి ప్లేట్లు మరియు స్టీల్ ముక్కలకు మాత్రమే అనువైన పద్ధతి, మేము విద్యుదయస్కాంత ప్రేరణను ఉపయోగించే ఇండక్షన్ వెల్డింగ్ మరియు మా విద్యుత్ వాహక లేదా ఫెర్రో అయస్కాంత వర్క్పీస్లను వేడి చేయండి, లేజర్ బీమ్ వెల్డింగ్ కూడా లోతైన వ్యాప్తి మరియు వేగవంతమైన ప్రాసెసింగ్తో ఉంటుంది, అయితే ఖరీదైన పద్ధతి, LBWని GMAWతో కలిపి అదే వెల్డింగ్ హెడ్లో మరియు ప్లేట్ల మధ్య 2 mm అంతరాలను తగ్గించగల సామర్థ్యం ఉన్న లేజర్ హైబ్రిడ్ వెల్డింగ్ అప్లైడ్ ప్రెషర్తో మెటీరియల్లను ఫోర్జింగ్ చేయడం ద్వారా విద్యుత్ ఉత్సర్గను కలిగి ఉంటుంది, అల్యూమినియం మరియు ఐరన్ ఆక్సైడ్ పౌడర్ల మధ్య ఎక్సోథర్మిక్ రియాక్షన్తో కూడిన థర్మిట్ వెల్డింగ్., వినియోగించదగిన ఎలక్ట్రోడ్లతో కూడిన ఎలక్ట్రోగాస్ వెల్డింగ్ మరియు నిలువుగా ఉన్న ఉక్కుతో ఉపయోగించబడుతుంది మరియు చివరగా స్టడ్లో చేరడానికి స్టడ్ ఆర్క్ వెల్డింగ్ ఉంటుంది. వేడి మరియు ఒత్తిడితో కూడిన పదార్థం. మీరు ఇక్కడ క్లిక్ చేయాలని మేము సిఫార్సు చేస్తున్నాముAGS-TECH Inc ద్వారా బ్రేజింగ్, టంకం మరియు అంటుకునే బంధ ప్రక్రియల యొక్క మా స్కీమాటిక్ ఇలస్ట్రేషన్లను డౌన్లోడ్ చేయండి మేము మీకు దిగువ అందిస్తున్న సమాచారాన్ని బాగా అర్థం చేసుకోవడంలో ఇది మీకు సహాయం చేస్తుంది. • బ్రేజింగ్: మేము రెండు లేదా అంతకంటే ఎక్కువ లోహాలను వాటి ద్రవీభవన బిందువుల పైన వాటి మధ్యలో వేడి చేయడం ద్వారా మరియు వ్యాప్తి చెందడానికి కేశనాళిక చర్యను ఉపయోగించడం ద్వారా వాటిని కలుపుతాము. ప్రక్రియ టంకం వలె ఉంటుంది కానీ పూరకాన్ని కరిగించడానికి సంబంధించిన ఉష్ణోగ్రతలు బ్రేజింగ్లో ఎక్కువగా ఉంటాయి. వెల్డింగ్లో వలె, ఫ్లక్స్ పూరక పదార్థాన్ని వాతావరణ కాలుష్యం నుండి రక్షిస్తుంది. శీతలీకరణ తర్వాత వర్క్పీస్లు కలిసి ఉంటాయి. ఈ ప్రక్రియ క్రింది కీలక దశలను కలిగి ఉంటుంది: మంచి ఫిట్ మరియు క్లియరెన్స్, బేస్ మెటీరియల్స్ సరైన క్లీనింగ్, సరైన ఫిక్చర్, సరైన ఫ్లక్స్ మరియు వాతావరణ ఎంపిక, అసెంబ్లీని వేడి చేయడం మరియు చివరకు బ్రేజ్డ్ అసెంబ్లీని శుభ్రపరచడం. మా బ్రేజింగ్ ప్రక్రియలలో కొన్ని టార్చ్ బ్రేజింగ్, ఇది మాన్యువల్గా లేదా ఆటోమేటెడ్ పద్ధతిలో నిర్వహించబడే ఒక ప్రసిద్ధ పద్ధతి. ఇది తక్కువ వాల్యూమ్ ఉత్పత్తి ఆర్డర్లు మరియు ప్రత్యేక కేసులకు అనుకూలంగా ఉంటుంది. బ్రేజ్ చేయబడిన ఉమ్మడి దగ్గర గ్యాస్ జ్వాలలను ఉపయోగించి వేడి వర్తించబడుతుంది. ఫర్నేస్ బ్రేజింగ్కు తక్కువ ఆపరేటర్ నైపుణ్యం అవసరం మరియు పారిశ్రామిక భారీ ఉత్పత్తికి అనువైన సెమీ ఆటోమేటిక్ ప్రక్రియ. ఫర్నేస్లోని ఉష్ణోగ్రత నియంత్రణ మరియు వాతావరణం యొక్క నియంత్రణ రెండూ ఈ సాంకేతికత యొక్క ప్రయోజనాలు, ఎందుకంటే మొదటిది టార్చ్ బ్రేజింగ్లో ఉన్నట్లుగా ఉష్ణ చక్రాలను నియంత్రించడానికి మరియు స్థానిక తాపనాన్ని తొలగించడానికి మాకు వీలు కల్పిస్తుంది మరియు రెండోది ఆక్సీకరణం నుండి భాగాన్ని రక్షిస్తుంది. జిగ్గింగ్ని ఉపయోగించడం ద్వారా మేము తయారీ ఖర్చులను కనిష్ట స్థాయికి తగ్గించగలము. ప్రతికూలతలు అధిక విద్యుత్ వినియోగం, పరికరాల ఖర్చులు మరియు మరింత సవాలుగా ఉన్న డిజైన్ పరిగణనలు. వాక్యూమ్ బ్రేజింగ్ అనేది వాక్యూమ్ కొలిమిలో జరుగుతుంది. ఉష్ణోగ్రత ఏకరూపత నిర్వహించబడుతుంది మరియు మేము చాలా తక్కువ అవశేష ఒత్తిళ్లతో ఫ్లక్స్ ఫ్రీ, చాలా శుభ్రమైన కీళ్లను పొందుతాము. వాక్యూమ్ బ్రేజింగ్ సమయంలో వేడి చికిత్సలు జరుగుతాయి, ఎందుకంటే నెమ్మదిగా వేడి చేయడం మరియు శీతలీకరణ చక్రాల సమయంలో తక్కువ అవశేష ఒత్తిడి ఉంటుంది. ప్రధాన ప్రతికూలత దాని అధిక ధర ఎందుకంటే వాక్యూమ్ పర్యావరణాన్ని సృష్టించడం ఖరీదైన ప్రక్రియ. ఇంకొక సాంకేతికత DIP BRAZING అనేది సంభోగం ఉపరితలాలకు బ్రేజింగ్ సమ్మేళనం వర్తించే స్థిర భాగాలను కలుపుతుంది. ఆ తర్వాత fixtured భాగాలు ఉష్ణ బదిలీ మాధ్యమం మరియు ఫ్లక్స్గా పనిచేసే సోడియం క్లోరైడ్ (టేబుల్ సాల్ట్) వంటి కరిగిన ఉప్పు యొక్క స్నానంలో ముంచబడతాయి. గాలి మినహాయించబడింది మరియు అందువల్ల ఆక్సైడ్ ఏర్పడదు. ఇండక్షన్ బ్రేజింగ్లో మనం మూల పదార్థాల కంటే తక్కువ ద్రవీభవన స్థానం కలిగిన పూరక లోహం ద్వారా పదార్థాలను కలుపుతాము. ఇండక్షన్ కాయిల్ నుండి వచ్చే ఆల్టర్నేటింగ్ కరెంట్ విద్యుదయస్కాంత క్షేత్రాన్ని సృష్టిస్తుంది, ఇది ఎక్కువగా ఫెర్రస్ అయస్కాంత పదార్థాలపై ఇండక్షన్ హీటింగ్ను ప్రేరేపిస్తుంది. ఈ పద్ధతి సెలెక్టివ్ హీటింగ్, ఫిల్లర్లతో కూడిన మంచి జాయింట్లను కావలసిన ప్రదేశాలలో మాత్రమే ప్రవహిస్తుంది, తక్కువ ఆక్సీకరణను అందిస్తుంది ఎందుకంటే మంటలు ఉండవు మరియు శీతలీకరణ వేగంగా, వేగవంతమైన వేడి, స్థిరత్వం మరియు అధిక వాల్యూమ్ తయారీకి అనుకూలతను అందిస్తుంది. మా ప్రక్రియలను వేగవంతం చేయడానికి మరియు స్థిరత్వానికి భరోసా ఇవ్వడానికి మేము తరచుగా ప్రిఫార్మ్లను ఉపయోగిస్తాము. సిరామిక్ నుండి మెటల్ ఫిట్టింగ్లు, హెర్మెటిక్ సీలింగ్, వాక్యూమ్ ఫీడ్త్రూలు, హై మరియు అల్ట్రాహై వాక్యూమ్ మరియు ఫ్లూయిడ్ కంట్రోల్ కాంపోనెంట్స్ ఉత్పత్తి చేసే మా బ్రేజింగ్ సదుపాయం గురించి సమాచారాన్ని ఇక్కడ చూడవచ్చు:బ్రేజింగ్ ఫ్యాక్టరీ బ్రోచర్ • SOLDERING : టంకంలో మేము పని ముక్కలను కరిగించడం లేదు, కానీ ఉమ్మడిలోకి ప్రవహించే చేరిన భాగాల కంటే తక్కువ ద్రవీభవన స్థానంతో పూరక మెటల్. టంకంలోని పూరక లోహం బ్రేజింగ్ కంటే తక్కువ ఉష్ణోగ్రత వద్ద కరుగుతుంది. మేము టంకం కోసం సీసం-రహిత మిశ్రమాలను ఉపయోగిస్తాము మరియు RoHS సమ్మతిని కలిగి ఉంటాము మరియు వేర్వేరు అప్లికేషన్లు మరియు అవసరాల కోసం మేము వెండి మిశ్రమం వంటి విభిన్నమైన మరియు తగిన మిశ్రమాలను కలిగి ఉన్నాము. టంకం మాకు గ్యాస్ మరియు ద్రవ-గట్టిగా ఉండే కీళ్లను అందిస్తుంది. సాఫ్ట్ సోల్డరింగ్లో, మా పూరక లోహం 400 సెంటీగ్రేడ్ కంటే తక్కువ మెల్టింగ్ పాయింట్ను కలిగి ఉంటుంది, అయితే సిల్వర్ సోల్డరింగ్ మరియు బ్రేజింగ్లో మనకు అధిక ఉష్ణోగ్రతలు అవసరం. మృదువైన టంకం తక్కువ ఉష్ణోగ్రతలను ఉపయోగిస్తుంది కానీ ఎత్తైన ఉష్ణోగ్రతల వద్ద డిమాండ్ చేసే అప్లికేషన్లకు బలమైన కీళ్లను అందించదు. మరోవైపు సిల్వర్ టంకం, టార్చ్ ద్వారా అందించబడిన అధిక ఉష్ణోగ్రతలు అవసరం మరియు అధిక ఉష్ణోగ్రత అనువర్తనాలకు అనువైన బలమైన కీళ్లను మాకు అందిస్తుంది. బ్రేజింగ్కు అత్యధిక ఉష్ణోగ్రతలు అవసరం మరియు సాధారణంగా టార్చ్ ఉపయోగించబడుతుంది. బ్రేజింగ్ జాయింట్లు చాలా బలంగా ఉన్నందున, భారీ ఇనుప వస్తువులను రిపేర్ చేయడానికి అవి మంచి అభ్యర్థులు. మా తయారీ లైన్లలో మేము మాన్యువల్ హ్యాండ్ టంకం మరియు ఆటోమేటెడ్ టంకము లైన్లు రెండింటినీ ఉపయోగిస్తాము. INDUCTION SOLDERING ఇండక్షన్ హీటింగ్ను సులభతరం చేయడానికి రాగి కాయిల్లో అధిక ఫ్రీక్వెన్సీ AC కరెంట్ని ఉపయోగిస్తుంది. కరెంట్లు టంకం చేయబడిన భాగంలో ప్రేరేపించబడతాయి మరియు ఫలితంగా వేడి అధిక నిరోధకత joint వద్ద ఉత్పత్తి అవుతుంది. ఈ వేడి పూరక లోహాన్ని కరిగిస్తుంది. ఫ్లక్స్ కూడా ఉపయోగించబడుతుంది. సైక్లిండర్లు మరియు పైపుల చుట్టూ కాయిల్స్ను చుట్టడం ద్వారా నిరంతర ప్రక్రియలో టంకం చేయడానికి ఇండక్షన్ టంకం మంచి పద్ధతి. గ్రాఫైట్ మరియు సిరామిక్స్ వంటి కొన్ని పదార్థాలను టంకం చేయడం చాలా కష్టం, ఎందుకంటే దీనికి టంకం చేయడానికి ముందు తగిన లోహంతో వర్క్పీస్లను పూయడం అవసరం. ఇది ఇంటర్ఫేషియల్ బాండింగ్ను సులభతరం చేస్తుంది. మేము ప్రత్యేకంగా హెర్మెటిక్ ప్యాకేజింగ్ అప్లికేషన్ల కోసం అలాంటి పదార్థాలను టంకము చేస్తాము. మేము మా ప్రింటెడ్ సర్క్యూట్ బోర్డ్లను (PCB) అధిక వాల్యూమ్లో ఎక్కువగా WAVE SOLDERING ఉపయోగించి తయారు చేస్తాము. చిన్న పరిమాణంలో ప్రోటోటైపింగ్ ప్రయోజనాల కోసం మాత్రమే మేము టంకం ఇనుమును ఉపయోగించి చేతి టంకం ఉపయోగిస్తాము. మేము త్రూ-హోల్ మరియు ఉపరితల మౌంట్ PCB సమావేశాలు (PCBA) రెండింటికీ వేవ్ టంకం ఉపయోగిస్తాము. ఒక తాత్కాలిక జిగురు సర్క్యూట్ బోర్డ్కు జోడించిన భాగాలను ఉంచుతుంది మరియు అసెంబ్లీ కన్వేయర్పై ఉంచబడుతుంది మరియు కరిగిన టంకము ఉన్న పరికరం ద్వారా కదులుతుంది. మొదట పిసిబి ఫ్లక్స్ చేయబడి, ఆపై ప్రీహీటింగ్ జోన్లోకి ప్రవేశిస్తుంది. కరిగిన టంకము ఒక పాన్లో ఉంటుంది మరియు దాని ఉపరితలంపై నిలబడి ఉన్న తరంగాల నమూనాను కలిగి ఉంటుంది. ఈ తరంగాలపై PCB కదులుతున్నప్పుడు, ఈ తరంగాలు PCB దిగువన సంప్రదిస్తాయి మరియు టంకం ప్యాడ్లకు అంటుకుంటాయి. టంకము పిన్స్ మరియు ప్యాడ్లపై మాత్రమే ఉంటుంది మరియు PCBలోనే కాదు. కరిగిన టంకములోని తరంగాలను బాగా నియంత్రించాలి కాబట్టి స్ప్లాషింగ్ ఉండదు మరియు వేవ్ టాప్లు బోర్డుల యొక్క అవాంఛనీయ ప్రాంతాలను తాకవు మరియు కలుషితం చేయవు. రిఫ్లో సోల్డరింగ్లో, బోర్డులకు ఎలక్ట్రానిక్ భాగాలను తాత్కాలికంగా అటాచ్ చేయడానికి మేము స్టిక్కీ సోల్డర్ పేస్ట్ని ఉపయోగిస్తాము. అప్పుడు బోర్డులు ఉష్ణోగ్రత నియంత్రణతో రిఫ్లో ఓవెన్ ద్వారా ఉంచబడతాయి. ఇక్కడ టంకము కరుగుతుంది మరియు భాగాలను శాశ్వతంగా కలుపుతుంది. మేము ఈ సాంకేతికతను ఉపరితల మౌంట్ భాగాలు రెండింటికీ అలాగే త్రూ-హోల్ భాగాల కోసం ఉపయోగిస్తాము. బోర్డ్లోని ఎలక్ట్రానిక్ భాగాలను వాటి గరిష్ట ఉష్ణోగ్రత పరిమితుల కంటే ఎక్కువగా వేడెక్కడం ద్వారా నాశనం చేయకుండా ఉండటానికి సరైన ఉష్ణోగ్రత నియంత్రణ మరియు ఓవెన్ ఉష్ణోగ్రతల సర్దుబాటు అవసరం. రీఫ్లో టంకం ప్రక్రియలో, మేము వాస్తవానికి అనేక ప్రాంతాలు లేదా దశలను కలిగి ఉన్నాము, ప్రతి ఒక్కటి ప్రత్యేకమైన థర్మల్ ప్రొఫైల్తో ఉంటాయి, అవి ప్రీహీటింగ్ స్టెప్, థర్మల్ సోకింగ్ స్టెప్, రిఫ్లో మరియు కూలింగ్ స్టెప్స్ వంటివి. ప్రింటెడ్ సర్క్యూట్ బోర్డ్ అసెంబ్లీస్ (PCBA) యొక్క డ్యామేజ్ ఫ్రీ రిఫ్లో టంకం కోసం ఈ విభిన్న దశలు అవసరం. ULTRASONIC SOLDERING అనేది ప్రత్యేకమైన సామర్థ్యాలతో తరచుగా ఉపయోగించే మరొక సాంకేతికత- ఇది గాజు, సిరామిక్ మరియు నాన్-మెటాలిక్ పదార్థాలను టంకము చేయడానికి ఉపయోగించవచ్చు. ఉదాహరణకు ఫోటోవోల్టాయిక్ ప్యానెల్లు కాని లోహానికి ఈ సాంకేతికతను ఉపయోగించి అతికించబడే ఎలక్ట్రోడ్లు అవసరం. అల్ట్రాసోనిక్ టంకంలో, మేము అల్ట్రాసోనిక్ వైబ్రేషన్లను విడుదల చేసే వేడిచేసిన టంకం చిట్కాను అమలు చేస్తాము. ఈ కంపనాలు కరిగిన టంకము పదార్థంతో ఉపరితలం యొక్క ఇంటర్ఫేస్ వద్ద పుచ్చు బుడగలను ఉత్పత్తి చేస్తాయి. పుచ్చు యొక్క ప్రేరేపిత శక్తి ఆక్సైడ్ ఉపరితలాన్ని సవరించి, మురికి మరియు ఆక్సైడ్లను తొలగిస్తుంది. ఈ సమయంలో మిశ్రమం పొర కూడా ఏర్పడుతుంది. బంధం ఉపరితలం వద్ద ఉన్న టంకము ఆక్సిజన్ను కలిగి ఉంటుంది మరియు గాజు మరియు టంకము మధ్య బలమైన భాగస్వామ్య బంధాన్ని ఏర్పరుస్తుంది. DIP SOLDERING అనేది చిన్న తరహా ఉత్పత్తికి మాత్రమే సరిపోయే వేవ్ టంకం యొక్క సరళమైన వెర్షన్గా పరిగణించబడుతుంది. మొదటి శుభ్రపరిచే ఫ్లక్స్ ఇతర ప్రక్రియలలో వలె వర్తించబడుతుంది. మౌంట్ చేయబడిన భాగాలతో PCBలు మానవీయంగా లేదా సెమీ ఆటోమేటెడ్ పద్ధతిలో కరిగిన టంకము కలిగిన ట్యాంక్లో ముంచబడతాయి. కరిగిన టంకము బోర్డ్లోని టంకము ముసుగు ద్వారా అసురక్షిత లోహ ప్రాంతాలకు అంటుకుంటుంది. పరికరాలు సరళమైనవి మరియు చవకైనవి. • అంటుకునే బంధం : ఇది మనం తరచుగా ఉపయోగించే మరొక ప్రసిద్ధ టెక్నిక్ మరియు ఇది జిగురులు, ఎపాక్సీలు, ప్లాస్టిక్ ఏజెంట్లు లేదా ఇతర రసాయనాలను ఉపయోగించి ఉపరితలాల బంధాన్ని కలిగి ఉంటుంది. బంధం అనేది ద్రావకాన్ని ఆవిరి చేయడం ద్వారా, హీట్ క్యూరింగ్ ద్వారా, UV లైట్ క్యూరింగ్ ద్వారా, ప్రెజర్ క్యూరింగ్ ద్వారా లేదా నిర్దిష్ట సమయం వరకు వేచి ఉండటం ద్వారా సాధించబడుతుంది. మా ఉత్పత్తి లైన్లలో వివిధ అధిక పనితీరు గల గ్లూలు ఉపయోగించబడతాయి. సరిగ్గా రూపొందించబడిన అప్లికేషన్ మరియు క్యూరింగ్ ప్రక్రియలతో, అంటుకునే బంధం బలమైన మరియు నమ్మదగిన అతి తక్కువ ఒత్తిడి బంధాలకు దారి తీస్తుంది. అంటుకునే బంధాలు తేమ, కలుషితాలు, తినివేయు పదార్థాలు, కంపనం మొదలైన పర్యావరణ కారకాల నుండి మంచి రక్షకులుగా ఉంటాయి. అంటుకునే బంధం యొక్క ప్రయోజనాలు: అవి టంకము, వెల్డ్ లేదా బ్రేజ్ చేయడానికి కష్టంగా ఉండే పదార్థాలకు వర్తించవచ్చు. వెల్డింగ్ లేదా ఇతర అధిక ఉష్ణోగ్రత ప్రక్రియల వల్ల దెబ్బతినే వేడి సెన్సిటివ్ పదార్థాలకు కూడా ఇది ప్రాధాన్యతనిస్తుంది. సంసంజనాల యొక్క ఇతర ప్రయోజనాలు ఏమిటంటే అవి సక్రమంగా లేని ఆకారపు ఉపరితలాలకు వర్తించబడతాయి మరియు ఇతర పద్ధతులతో పోల్చినప్పుడు చాలా తక్కువ మొత్తంలో అసెంబ్లీ బరువును పెంచుతాయి. అలాగే భాగాలలో డైమెన్షనల్ మార్పులు చాలా తక్కువగా ఉంటాయి. కొన్ని గ్లూలు ఇండెక్స్ మ్యాచింగ్ లక్షణాలను కలిగి ఉంటాయి మరియు కాంతి లేదా ఆప్టికల్ సిగ్నల్ బలాన్ని గణనీయంగా తగ్గించకుండా ఆప్టికల్ భాగాల మధ్య ఉపయోగించవచ్చు. మరోవైపు ప్రతికూలతలు ఎక్కువ క్యూరింగ్ సమయాలు, ఇది తయారీ లైన్లు, ఫిక్చరింగ్ అవసరాలు, ఉపరితల తయారీ అవసరాలు మరియు రీవర్క్ అవసరమైనప్పుడు విడదీయడంలో ఇబ్బందిని తగ్గిస్తుంది. మా అంటుకునే బంధం కార్యకలాపాలు చాలా వరకు క్రింది దశలను కలిగి ఉంటాయి: -ఉపరితల చికిత్స: డీయోనైజ్డ్ వాటర్ క్లీనింగ్, ఆల్కహాల్ క్లీనింగ్, ప్లాస్మా లేదా కరోనా క్లీనింగ్ వంటి ప్రత్యేక శుభ్రపరిచే విధానాలు సర్వసాధారణం. శుభ్రపరిచిన తర్వాత మేము ఉత్తమమైన కీళ్లకు భరోసా ఇవ్వడానికి ఉపరితలాలపై అడెషన్ ప్రమోటర్లను వర్తింపజేయవచ్చు. -పార్ట్ ఫిక్చరింగ్: అంటుకునే అప్లికేషన్ రెండింటికీ అలాగే క్యూరింగ్ కోసం మేము కస్టమ్ ఫిక్చర్లను డిజైన్ చేసి ఉపయోగిస్తాము. -అంటుకునే అప్లికేషన్: మేము కొన్నిసార్లు మాన్యువల్ని ఉపయోగిస్తాము మరియు కొన్నిసార్లు రోబోటిక్స్, సర్వో మోటార్లు, లీనియర్ యాక్యుయేటర్ల వంటి ఆటోమేటెడ్ సిస్టమ్లను బట్టి అడెసివ్లను సరైన స్థానానికి పంపిణీ చేస్తాము మరియు సరైన వాల్యూమ్ మరియు పరిమాణంలో పంపిణీ చేయడానికి మేము డిస్పెన్సర్లను ఉపయోగిస్తాము. -క్యూరింగ్: అంటుకునే పదార్థంపై ఆధారపడి, మేము సాధారణ ఎండబెట్టడం మరియు క్యూరింగ్తో పాటు UV లైట్ల కింద క్యూరింగ్ను ఉపయోగించవచ్చు, ఇవి ఓవెన్లో ఉత్ప్రేరకం లేదా వేడి క్యూరింగ్గా పనిచేస్తాయి లేదా జిగ్లు మరియు ఫిక్చర్లపై అమర్చిన రెసిస్టివ్ హీటింగ్ ఎలిమెంట్లను ఉపయోగించవచ్చు. మీరు ఇక్కడ క్లిక్ చేయాలని మేము సిఫార్సు చేస్తున్నాముAGS-TECH ఇంక్ ద్వారా మా స్కీమాటిక్ ఇలస్ట్రేషన్స్ ఆఫ్ ఫాస్టెనింగ్ ప్రాసెస్లను డౌన్లోడ్ చేయండి. మేము మీకు దిగువ అందిస్తున్న సమాచారాన్ని బాగా అర్థం చేసుకోవడంలో ఇది మీకు సహాయం చేస్తుంది. • FASTENING ప్రక్రియలు : మా మెకానికల్ జాయినింగ్ ప్రక్రియలు రెండు బ్రాడ్ కేటగిరీలుగా ఉంటాయి: FASTENERS మరియు INTEGRAL JOINTS. మేము ఉపయోగించే ఫాస్టెనర్ల ఉదాహరణలు స్క్రూలు, పిన్స్, నట్స్, బోల్ట్లు, రివెట్లు. మేము ఉపయోగించే ఇంటిగ్రల్ కీళ్ల ఉదాహరణలు స్నాప్ మరియు ష్రింక్ ఫిట్స్, సీమ్స్, క్రింప్స్. అనేక రకాల బందు పద్ధతులను ఉపయోగించి, మా మెకానికల్ కీళ్ళు చాలా సంవత్సరాల ఉపయోగం కోసం బలంగా మరియు నమ్మదగినవిగా ఉన్నాయని మేము నిర్ధారించుకుంటాము. స్క్రూలు మరియు బోల్ట్లు అనేది వస్తువులను ఒకదానితో ఒకటి పట్టుకోవడానికి మరియు స్థానానికి అత్యంత సాధారణంగా ఉపయోగించే కొన్ని ఫాస్టెనర్లు. మా స్క్రూలు మరియు బోల్ట్లు ASME ప్రమాణాలకు అనుగుణంగా ఉంటాయి. హెక్స్ క్యాప్ స్క్రూలు మరియు హెక్స్ బోల్ట్లు, లాగ్ స్క్రూలు మరియు బోల్ట్లు, డబుల్ ఎండెడ్ స్క్రూ, డోవెల్ స్క్రూ, ఐ స్క్రూ, మిర్రర్ స్క్రూ, షీట్ మెటల్ స్క్రూ, ఫైన్ అడ్జస్ట్మెంట్ స్క్రూ, సెల్ఫ్ డ్రిల్లింగ్ మరియు సెల్ఫ్-ట్యాపింగ్ స్క్రూలతో సహా వివిధ రకాల స్క్రూలు మరియు బోల్ట్లు అమర్చబడి ఉంటాయి. , సెట్ స్క్రూ, అంతర్నిర్మిత వాషర్లతో కూడిన స్క్రూలు,…మరియు మరిన్ని. మేము కౌంటర్సంక్, డోమ్, రౌండ్, ఫ్లాంగ్డ్ హెడ్ వంటి వివిధ స్క్రూ హెడ్ రకాలు మరియు స్లాట్, ఫిలిప్స్, స్క్వేర్, హెక్స్ సాకెట్ వంటి వివిధ స్క్రూ డ్రైవ్ రకాలను కలిగి ఉన్నాము. మరోవైపు RIVET అనేది ఒక మృదువైన స్థూపాకార షాఫ్ట్ మరియు ఒక వైపు తలతో కూడిన శాశ్వత మెకానికల్ ఫాస్టెనర్. చొప్పించిన తరువాత, రివెట్ యొక్క ఇతర ముగింపు వైకల్యంతో ఉంటుంది మరియు దాని వ్యాసం విస్తరించబడుతుంది, తద్వారా అది స్థానంలో ఉంటుంది. మరో మాటలో చెప్పాలంటే, ఇన్స్టాలేషన్కు ముందు ఒక రివెట్కు ఒక తల ఉంటుంది మరియు ఇన్స్టాలేషన్ తర్వాత దానికి రెండు ఉంటుంది. మేము అప్లికేషన్, బలం, యాక్సెసిబిలిటీ మరియు సాలిడ్/రౌండ్ హెడ్ రివెట్లు, స్ట్రక్చరల్, సెమీ ట్యూబ్యులర్, బ్లైండ్, ఆస్కార్, డ్రైవ్, ఫ్లష్, ఫ్రిక్షన్-లాక్, సెల్ఫ్ పియర్సింగ్ రివెట్లు వంటి ధరల ఆధారంగా వివిధ రకాల రివెట్లను ఇన్స్టాల్ చేస్తాము. వెల్డింగ్ హీట్ కారణంగా హీట్ డిఫార్మేషన్ మరియు మెటీరియల్ ప్రాపర్టీలలో మార్పును నివారించాల్సిన సందర్భాల్లో రివెటింగ్కు ప్రాధాన్యత ఇవ్వబడుతుంది. రివెటింగ్ తక్కువ బరువు మరియు ముఖ్యంగా కోత శక్తులకు వ్యతిరేకంగా మంచి బలం మరియు ఓర్పును కూడా అందిస్తుంది. తన్యత భారాలకు వ్యతిరేకంగా అయితే స్క్రూలు, గింజలు మరియు బోల్ట్లు మరింత అనుకూలంగా ఉండవచ్చు. CLINCHING ప్రక్రియలో మేము ప్రత్యేక పంచ్ మరియు డైస్లను ఉపయోగించి షీట్ మెటల్లు చేరడం మధ్య యాంత్రిక ఇంటర్లాక్ను ఏర్పరుస్తాము. పంచ్ షీట్ మెటల్ పొరలను డై కుహరంలోకి నెట్టివేస్తుంది మరియు ఫలితంగా శాశ్వత ఉమ్మడి ఏర్పడుతుంది. క్లించింగ్లో వేడి చేయడం మరియు శీతలీకరణ అవసరం లేదు మరియు ఇది చల్లని పని ప్రక్రియ. ఇది కొన్ని సందర్భాల్లో స్పాట్ వెల్డింగ్ను భర్తీ చేయగల ఆర్థిక ప్రక్రియ. పిన్నింగ్లో మేము పిన్లను ఉపయోగిస్తాము, అవి ఒకదానికొకటి సాపేక్షంగా యంత్ర భాగాల స్థానాలను భద్రపరచడానికి ఉపయోగించే యంత్ర మూలకాలు. ప్రధాన రకాలు క్లెవిస్ పిన్లు, కాటర్ పిన్, స్ప్రింగ్ పిన్, డోవెల్ పిన్స్, మరియు స్ప్లిట్ పిన్. STAPLINGలో మేము స్టెప్లింగ్ గన్లు మరియు స్టేపుల్స్ని ఉపయోగిస్తాము, ఇవి మెటీరియల్లను చేరడానికి లేదా బైండ్ చేయడానికి ఉపయోగించే రెండు-వైపుల ఫాస్టెనర్లు. స్టాప్లింగ్ కింది ప్రయోజనాలను కలిగి ఉంది: ఆర్థికంగా, సరళంగా మరియు ఉపయోగించడానికి వేగవంతమైనది, స్టేపుల్స్ యొక్క కిరీటం ఒకదానితో ఒకటి కలపబడిన పదార్థాలను వంతెన చేయడానికి ఉపయోగించవచ్చు, ప్రధానమైన కిరీటం ఒక కేబుల్ వంటి భాగాన్ని వంతెన చేయడానికి మరియు పంక్చర్ లేకుండా ఉపరితలంపై బిగించడానికి వీలు కల్పిస్తుంది. హానికరమైన, సాపేక్షంగా సులభంగా తొలగింపు. భాగాలను ఒకదానితో ఒకటి నెట్టడం ద్వారా ప్రెస్ ఫిట్టింగ్ నిర్వహించబడుతుంది మరియు వాటి మధ్య ఘర్షణ భాగాలను కట్టివేస్తుంది. భారీ షాఫ్ట్ మరియు తక్కువ పరిమాణంలో ఉన్న రంధ్రంతో కూడిన ప్రెస్ ఫిట్ భాగాలు సాధారణంగా రెండు పద్ధతుల్లో ఒకదాని ద్వారా సమీకరించబడతాయి: శక్తిని ప్రయోగించడం ద్వారా లేదా ఉష్ణ విస్తరణ లేదా భాగాల సంకోచం యొక్క ప్రయోజనాన్ని పొందడం ద్వారా. శక్తిని వర్తింపజేయడం ద్వారా ప్రెస్ ఫిట్టింగ్ను ఏర్పాటు చేసినప్పుడు, మేము హైడ్రాలిక్ ప్రెస్ లేదా చేతితో పనిచేసే ప్రెస్ని ఉపయోగిస్తాము. మరోవైపు థర్మల్ విస్తరణ ద్వారా ప్రెస్ ఫిట్టింగ్ ఏర్పాటు చేయబడినప్పుడు మేము చుట్టుముట్టే భాగాలను వేడి చేస్తాము మరియు వేడిగా ఉన్నప్పుడు వాటి స్థానంలో వాటిని సమీకరించాము. అవి చల్లబడినప్పుడు, అవి సంకోచించబడతాయి మరియు వాటి సాధారణ పరిమాణాలకు తిరిగి వస్తాయి. ఇది మంచి ప్రెస్ ఫిట్కు దారి తీస్తుంది. మేము దీనిని ప్రత్యామ్నాయంగా SHRINK-FITTING అని పిలుస్తాము. దీన్ని చేయడానికి మరొక మార్గం ఏమిటంటే, అసెంబ్లీకి ముందు ఎన్వలప్ చేయబడిన భాగాలను చల్లబరుస్తుంది మరియు వాటిని వాటి సంభోగం భాగాలలోకి జారడం. అసెంబ్లీ వేడెక్కినప్పుడు అవి విస్తరిస్తాయి మరియు మేము గట్టి అమరికను పొందుతాము. వేడి చేయడం వల్ల పదార్థ లక్షణాలను మార్చే ప్రమాదం ఉన్న సందర్భాల్లో ఈ రెండో పద్ధతి ఉత్తమం. ఆ సందర్భాలలో శీతలీకరణ సురక్షితం. వాయు & హైడ్రాలిక్ భాగాలు మరియు అసెంబ్లీలు • O-రింగ్, వాషర్, సీల్స్, రబ్బరు పట్టీ, రింగ్, షిమ్ వంటి కవాటాలు, హైడ్రాలిక్ మరియు వాయు భాగాలు. కవాటాలు మరియు వాయు భాగాలు చాలా రకాలుగా ఉంటాయి కాబట్టి, మేము ఇక్కడ ప్రతిదీ జాబితా చేయలేము. మీ అప్లికేషన్ యొక్క భౌతిక మరియు రసాయన వాతావరణాలపై ఆధారపడి, మేము మీ కోసం ప్రత్యేక ఉత్పత్తులను కలిగి ఉన్నాము. దయచేసి మీ వాల్వ్లు మరియు వాయు భాగాలతో సంబంధం కలిగి ఉండే అప్లికేషన్, కాంపోనెంట్ రకం, స్పెసిఫికేషన్లు, పీడనం, ఉష్ణోగ్రత, ద్రవాలు లేదా వాయువుల వంటి పర్యావరణ పరిస్థితులను మాకు పేర్కొనండి; మరియు మేము మీ కోసం చాలా సరిఅయిన ఉత్పత్తిని ఎంచుకుంటాము లేదా మీ అప్లికేషన్ కోసం ప్రత్యేకంగా తయారు చేస్తాము. CLICK Product Finder-Locator Service ముందు పేజి
- Glass and Ceramic Manufacturing, Hermetic Packages, Seals, Bonding
Glass and Ceramic Manufacturing, Hermetic Packages Seals and Bonding, Tempered Bulletproof Glass, Blow Moulding, Optical Grade Glass, Conductive Glass, Molding గ్లాస్ & సిరామిక్ ఫార్మింగ్ & షేపింగ్ మేము అందించే గాజు తయారీ రకం కంటైనర్ గ్లాస్, గ్లాస్ బ్లోయింగ్, గ్లాస్ ఫైబర్ & ట్యూబింగ్ & రాడ్, డొమెస్టిక్ మరియు ఇండస్ట్రియల్ గ్లాస్వేర్, ల్యాంప్ మరియు బల్బ్, ప్రెసిషన్ గ్లాస్ మౌల్డింగ్, ఆప్టికల్ కాంపోనెంట్స్ మరియు అసెంబ్లీలు, ఫ్లాట్ & షీట్ & ఫ్లోట్ గ్లాస్. మేము హ్యాండ్ ఫార్మింగ్ మరియు మెషిన్ ఫార్మింగ్ రెండింటినీ నిర్వహిస్తాము. మా ప్రసిద్ధ సాంకేతిక సిరామిక్ తయారీ ప్రక్రియలు డై నొక్కడం, ఐసోస్టాటిక్ నొక్కడం, హాట్ ఐసోస్టాటిక్ నొక్కడం, వేడి నొక్కడం, స్లిప్ కాస్టింగ్, టేప్ కాస్టింగ్, ఎక్స్ట్రాషన్, ఇంజెక్షన్ మౌల్డింగ్, గ్రీన్ మ్యాచింగ్, సింటరింగ్ లేదా ఫైరింగ్, డైమండ్ గ్రౌండింగ్, హెర్మెటిక్ అసెంబ్లీలు. మీరు ఇక్కడ క్లిక్ చేయాలని మేము సిఫార్సు చేస్తున్నాము AGS-TECH Inc ద్వారా గ్లాస్ ఫార్మింగ్ మరియు షేపింగ్ ప్రాసెస్ల యొక్క మా స్కీమాటిక్ ఇలస్ట్రేషన్లను డౌన్లోడ్ చేయండి. AGS-TECH Inc ద్వారా టెక్నికల్ సిరామిక్ తయారీ ప్రక్రియల మా స్కీమాటిక్ ఇలస్ట్రేషన్లను డౌన్లోడ్ చేయండి. ఫోటోలు మరియు స్కెచ్లతో కూడిన ఈ డౌన్లోడ్ చేయదగిన ఫైల్లు మేము దిగువ మీకు అందిస్తున్న సమాచారాన్ని బాగా అర్థం చేసుకోవడంలో మీకు సహాయపడతాయి. • కంటైనర్ గ్లాస్ తయారీ: మేము తయారీ కోసం ఆటోమేటిక్ ప్రెస్ మరియు బ్లో అలాగే బ్లో మరియు బ్లో లైన్లను కలిగి ఉన్నాము. బ్లో మరియు బ్లో ప్రక్రియలో మేము ఒక గోబ్ను ఖాళీ అచ్చులో పడవేస్తాము మరియు పై నుండి కంప్రెస్డ్ గాలిని ప్రయోగించడం ద్వారా మెడను ఏర్పరుస్తాము. దీనిని అనుసరించిన వెంటనే, కంప్రెస్డ్ ఎయిర్ని రెండవ సారి ఇతర దిశ నుండి కంటైనర్ మెడ ద్వారా ఊదడం ద్వారా సీసా యొక్క పూర్వ రూపం ఏర్పడుతుంది. ఈ ప్రీ-ఫారమ్ అసలు అచ్చుకు బదిలీ చేయబడుతుంది, మృదువుగా చేయడానికి మళ్లీ వేడి చేయబడుతుంది మరియు ప్రీ-ఫారమ్కు దాని చివరి కంటైనర్ ఆకారాన్ని అందించడానికి కంప్రెస్డ్ ఎయిర్ వర్తించబడుతుంది. మరింత స్పష్టంగా, అది ఒత్తిడికి గురైంది మరియు దాని కావలసిన ఆకృతిని తీసుకోవడానికి బ్లో అచ్చు కుహరం యొక్క గోడలపైకి నెట్టబడుతుంది. చివరగా, తయారు చేయబడిన గాజు కంటైనర్ తదుపరి వేడి చేయడం మరియు అచ్చు సమయంలో ఉత్పన్నమయ్యే ఒత్తిడిని తొలగించడం కోసం ఎనియలింగ్ ఓవెన్లోకి బదిలీ చేయబడుతుంది మరియు నియంత్రిత పద్ధతిలో చల్లబడుతుంది. ప్రెస్ మరియు బ్లో పద్ధతిలో, కరిగిన గోబ్లను ప్యారిసన్ అచ్చులో (ఖాళీ అచ్చు) ఉంచారు మరియు పారిసన్ ఆకారంలో (ఖాళీ ఆకారం) నొక్కుతారు. ఖాళీలు బ్లో అచ్చులకు బదిలీ చేయబడతాయి మరియు "బ్లో అండ్ బ్లో ప్రాసెస్" కింద పైన వివరించిన ప్రక్రియ వలె ఊదబడతాయి. ఎనియలింగ్ మరియు స్ట్రెస్ రిలీవ్ వంటి తదుపరి దశలు సారూప్యమైనవి లేదా ఒకే విధంగా ఉంటాయి. • గ్లాస్ బ్లోయింగ్: మేము సాంప్రదాయిక హ్యాండ్ బ్లోయింగ్ని ఉపయోగించి అలాగే ఆటోమేటెడ్ పరికరాలతో కంప్రెస్డ్ ఎయిర్ని ఉపయోగించి గాజు ఉత్పత్తులను తయారు చేస్తున్నాము. గ్లాస్ ఆర్ట్ వర్క్తో కూడిన ప్రాజెక్ట్లు లేదా వదులుగా ఉండే టాలరెన్స్లతో తక్కువ సంఖ్యలో భాగాలు అవసరమయ్యే ప్రాజెక్ట్లు, ప్రోటోటైపింగ్ / డెమో ప్రాజెక్ట్లు....మొదలైన కొన్ని ఆర్డర్ల కోసం సంప్రదాయ బ్లోయింగ్ అవసరం. సాంప్రదాయిక గ్లాస్ బ్లోయింగ్లో ఒక బోలు మెటల్ పైపును కరిగిన గాజు కుండలో ముంచి, కొంత మొత్తంలో గాజు పదార్థాన్ని సేకరించేందుకు పైపును తిప్పడం జరుగుతుంది. పైపు యొక్క కొనపై సేకరించిన గాజును ఫ్లాట్ ఇనుముపై చుట్టి, కావలసిన ఆకారంలో, పొడిగించి, మళ్లీ వేడి చేసి, గాలిని ఎగిరింది. సిద్ధంగా ఉన్నప్పుడు, అది ఒక అచ్చులోకి చొప్పించబడుతుంది మరియు గాలి వీస్తుంది. లోహంతో గాజు సంబంధాన్ని నివారించడానికి అచ్చు కుహరం తడిగా ఉంటుంది. వాటర్ ఫిల్మ్ వాటి మధ్య కుషన్ లాగా పనిచేస్తుంది. మాన్యువల్ బ్లోయింగ్ అనేది లేబర్ ఇంటెన్సివ్ స్లో ప్రాసెస్ మరియు ప్రోటోటైపింగ్ లేదా అధిక విలువ కలిగిన వస్తువులకు మాత్రమే సరిపోతుంది, ఒక్కో ముక్కకు చవకైన అధిక వాల్యూమ్ ఆర్డర్లకు తగినది కాదు. • డొమెస్టిక్ & ఇండస్ట్రియల్ గ్లాస్వేర్ తయారీ: వివిధ రకాల గాజు పదార్థాలను ఉపయోగించి అనేక రకాల గాజుసామాను ఉత్పత్తి చేయబడుతోంది. కొన్ని అద్దాలు వేడిని తట్టుకోగలవు మరియు ప్రయోగశాల గాజుసామానుకు అనుకూలంగా ఉంటాయి, అయితే కొన్ని చాలా సార్లు డిష్వాషర్లను తట్టుకోవడానికి సరిపోతాయి మరియు దేశీయ ఉత్పత్తులను తయారు చేయడానికి సరిపోతాయి. వెస్ట్లేక్ యంత్రాలను ఉపయోగించి రోజుకు పదివేల డ్రింకింగ్ గ్లాసులను ఉత్పత్తి చేస్తున్నారు. సరళీకృతం చేయడానికి, కరిగిన గాజును వాక్యూమ్ ద్వారా సేకరించి, ముందస్తు రూపాలను తయారు చేయడానికి అచ్చుల్లోకి చొప్పించబడుతుంది. అప్పుడు గాలి అచ్చులలోకి ఎగిరిపోతుంది, ఇవి మరొక అచ్చుకు బదిలీ చేయబడతాయి మరియు గాలి మళ్లీ ఊదబడుతుంది మరియు గాజు దాని తుది రూపాన్ని తీసుకుంటుంది. చేతి బ్లోయింగ్లో వలె, ఈ అచ్చులను నీటితో తడిగా ఉంచుతారు. మరింత సాగదీయడం అనేది మెడ ఏర్పడుతున్న ముగింపు ఆపరేషన్లో భాగం. అదనపు గాజు కాలిపోతుంది. ఆ తర్వాత పైన వివరించిన నియంత్రిత రీ-హీటింగ్ మరియు శీతలీకరణ ప్రక్రియ క్రింది విధంగా ఉంటుంది. • గ్లాస్ ట్యూబ్ & రాడ్ ఫార్మింగ్ : గ్లాస్ ట్యూబ్ల తయారీకి మనం ఉపయోగించే ప్రధాన ప్రక్రియలు డానర్ మరియు వెల్లో ప్రక్రియలు. డానర్ ప్రక్రియలో, కొలిమి నుండి గాజు ప్రవహిస్తుంది మరియు వక్రీభవన పదార్థాలతో చేసిన వంపుతిరిగిన స్లీవ్పై పడుతుంది. స్లీవ్ తిరిగే బోలు షాఫ్ట్ లేదా బ్లోపైప్ మీద తీసుకువెళతారు. అప్పుడు గ్లాస్ స్లీవ్ చుట్టూ చుట్టబడి, స్లీవ్ నుండి మరియు షాఫ్ట్ యొక్క కొనపై ప్రవహించే మృదువైన పొరను ఏర్పరుస్తుంది. ట్యూబ్ ఏర్పడే సందర్భంలో, బోలు చిట్కాతో బ్లోపైప్ ద్వారా గాలి ఎగిరిపోతుంది మరియు రాడ్ ఏర్పడే సందర్భంలో మేము షాఫ్ట్పై ఘన చిట్కాలను ఉపయోగిస్తాము. గొట్టాలు లేదా రాడ్లు మోస్తున్న రోలర్లపైకి లాగబడతాయి. గ్లాస్ ట్యూబ్ల గోడ మందం మరియు వ్యాసం వంటి కొలతలు స్లీవ్ యొక్క వ్యాసాన్ని సెట్ చేయడం మరియు గాలి ఒత్తిడిని కావలసిన విలువకు అమర్చడం, ఉష్ణోగ్రత, గాజు ప్రవాహం రేటు మరియు డ్రాయింగ్ వేగాన్ని సర్దుబాటు చేయడం ద్వారా కావలసిన విలువలకు సర్దుబాటు చేయబడతాయి. మరోవైపు వెల్లో గ్లాస్ ట్యూబ్ తయారీ ప్రక్రియలో గ్లాస్ ఉంటుంది, అది కొలిమి నుండి బయటకు వెళ్లి బోలు మాండ్రెల్ లేదా బెల్ ఉన్న గిన్నెలోకి వెళుతుంది. గాజు అప్పుడు మాండ్రెల్ మరియు గిన్నె మధ్య గాలి ఖాళీ గుండా వెళుతుంది మరియు ట్యూబ్ ఆకారాన్ని తీసుకుంటుంది. ఆ తర్వాత అది రోలర్ల మీదుగా డ్రాయింగ్ మెషీన్కి వెళ్లి చల్లబడుతుంది. శీతలీకరణ రేఖ ముగింపులో కట్టింగ్ మరియు చివరి ప్రాసెసింగ్ జరుగుతుంది. ట్యూబ్ కొలతలు డానర్ ప్రక్రియలో వలె సర్దుబాటు చేయబడతాయి. డానర్ని వెల్లో ప్రాసెస్ని పోల్చినప్పుడు, పెద్ద పరిమాణ ఉత్పత్తికి వెల్లో ప్రాసెస్ బాగా సరిపోతుందని మేము చెప్పగలం, అయితే డానర్ ప్రక్రియ ఖచ్చితమైన చిన్న వాల్యూమ్ ట్యూబ్ ఆర్డర్లకు బాగా సరిపోతుంది. • షీట్ & ఫ్లాట్ & ఫ్లోట్ గ్లాస్ ప్రాసెసింగ్ : సబ్మిలిమీటర్ మందం నుండి అనేక సెంటీమీటర్ల వరకు మందం కలిగిన ఫ్లాట్ గ్లాస్ పెద్ద మొత్తంలో మా వద్ద ఉంది. మా ఫ్లాట్ గ్లాసెస్ దాదాపు ఆప్టికల్ పరిపూర్ణతను కలిగి ఉంటాయి. మేము ఆప్టికల్ పూతలు వంటి ప్రత్యేక పూతలతో గాజును అందిస్తాము, ఇక్కడ యాంటీరిఫ్లెక్షన్ లేదా మిర్రర్ కోటింగ్ వంటి పూతలను ఉంచడానికి రసాయన ఆవిరి నిక్షేపణ సాంకేతికత ఉపయోగించబడుతుంది. అలాగే పారదర్శక వాహక పూతలు సాధారణం. గాజుపై హైడ్రోఫోబిక్ లేదా హైడ్రోఫిలిక్ పూతలు మరియు గాజు స్వీయ శుభ్రపరిచే పూత కూడా అందుబాటులో ఉన్నాయి. టెంపర్డ్, బుల్లెట్ ప్రూఫ్ మరియు లామినేటెడ్ గ్లాసెస్ ఇంకా ఇతర ప్రసిద్ధ వస్తువులు. మేము కావలసిన సహనంతో కావలసిన ఆకారంలో గాజును కట్ చేస్తాము. ఫ్లాట్ గ్లాస్ వంపు లేదా వంగడం వంటి ఇతర ద్వితీయ కార్యకలాపాలు అందుబాటులో ఉన్నాయి. • PRECISION GLASS MOLDING : గ్రైండింగ్, ల్యాపింగ్ మరియు పాలిషింగ్ వంటి ఖరీదైన మరియు ఎక్కువ సమయం తీసుకునే టెక్నిక్ల అవసరం లేకుండా ఖచ్చితత్వంతో కూడిన ఆప్టికల్ భాగాలను తయారు చేయడానికి మేము ఈ సాంకేతికతను ఎక్కువగా ఉపయోగిస్తాము. అత్యుత్తమ ఆప్టిక్స్ను ఉత్తమంగా రూపొందించడానికి ఈ సాంకేతికత ఎల్లప్పుడూ సరిపోదు, కానీ వినియోగదారు ఉత్పత్తులు, డిజిటల్ కెమెరాలు, మెడికల్ ఆప్టిక్స్ వంటి కొన్ని సందర్భాల్లో ఇది అధిక వాల్యూమ్ తయారీకి తక్కువ ఖర్చుతో కూడిన మంచి ఎంపికగా ఉంటుంది. అలాగే ఆస్పియర్ల విషయంలో సంక్లిష్టమైన జ్యామితి అవసరమయ్యే ఇతర గ్లాస్ ఫార్మింగ్ టెక్నిక్ల కంటే ఇది ప్రయోజనాన్ని కలిగి ఉంది. ప్రాథమిక ప్రక్రియలో గ్లాస్ ఖాళీతో మా అచ్చు దిగువ భాగాన్ని లోడ్ చేయడం, ఆక్సిజన్ తొలగింపు కోసం ప్రాసెస్ చాంబర్ని ఖాళీ చేయడం, అచ్చును మూసివేయడం, ఇన్ఫ్రారెడ్ లైట్తో డై మరియు గ్లాస్ను వేగంగా మరియు ఐసోథర్మల్ హీటింగ్ చేయడం, అచ్చు భాగాలను మరింత మూసివేయడం వంటివి ఉంటాయి. కావలసిన మందానికి నియంత్రిత పద్ధతిలో మెత్తబడిన గాజును నెమ్మదిగా నొక్కడం మరియు చివరకు గాజును చల్లబరచడం మరియు నత్రజనితో గదిని నింపడం మరియు ఉత్పత్తిని తీసివేయడం. ఈ ప్రక్రియలో ఖచ్చితమైన ఉష్ణోగ్రత నియంత్రణ, అచ్చు మూసివేత దూరం, అచ్చు మూసివేత శక్తి, అచ్చు మరియు గాజు పదార్థం యొక్క విస్తరణ గుణకాలను సరిపోల్చడం కీలకం. • గ్లాస్ ఆప్టికల్ కాంపోనెంట్లు మరియు అసెంబ్లీల తయారీ : ఖచ్చితత్వంతో కూడిన గ్లాస్ మౌల్డింగ్తో పాటు, డిమాండ్ ఉన్న అప్లికేషన్ల కోసం అధిక నాణ్యత గల ఆప్టికల్ భాగాలు మరియు అసెంబ్లీల తయారీకి మేము ఉపయోగించే అనేక విలువైన ప్రక్రియలు ఉన్నాయి. ఆప్టికల్ గ్రేడ్ గ్లాసులను గ్రైండింగ్ చేయడం, ల్యాప్ చేయడం మరియు పాలిష్ చేయడం అనేది ఆప్టికల్ లెన్స్లు, ప్రిజమ్లు, ఫ్లాట్లు మరియు మరిన్నింటిని తయారు చేయడానికి ఒక కళ మరియు సైన్స్. ఉపరితల ఫ్లాట్నెస్, అలలు, మృదుత్వం మరియు లోపం లేని ఆప్టికల్ ఉపరితలాలకు ఇటువంటి ప్రక్రియలతో చాలా అనుభవం అవసరం. పర్యావరణంలో చిన్న మార్పులు స్పెసిఫికేషన్ ఉత్పత్తులకు దారితీస్తాయి మరియు తయారీ శ్రేణిని నిలిపివేస్తాయి. ఒక శుభ్రమైన గుడ్డతో ఆప్టికల్ ఉపరితలంపై ఒక్క తుడవడం వల్ల ఉత్పత్తి నిర్దేశాలకు అనుగుణంగా లేదా పరీక్షలో విఫలమయ్యే సందర్భాలు ఉన్నాయి. ఉపయోగించిన కొన్ని ప్రసిద్ధ గాజు పదార్థాలు ఫ్యూజ్డ్ సిలికా, క్వార్ట్జ్, BK7. అటువంటి భాగాల అసెంబ్లీకి ప్రత్యేక సముచిత అనుభవం అవసరం. కొన్నిసార్లు ప్రత్యేక గ్లూలు ఉపయోగించబడుతున్నాయి. అయితే, కొన్నిసార్లు ఆప్టికల్ కాంటాక్టింగ్ అనే టెక్నిక్ ఉత్తమ ఎంపిక మరియు జోడించిన ఆప్టికల్ గ్లాసుల మధ్య ఎటువంటి మెటీరియల్ను కలిగి ఉండదు. ఇది జిగురు లేకుండా ఒకదానికొకటి అటాచ్ చేయడానికి భౌతికంగా చదునైన ఉపరితలాలను కలిగి ఉంటుంది. కొన్ని సందర్భాల్లో మెకానికల్ స్పేసర్లు, ఖచ్చితమైన గాజు రాడ్లు లేదా బంతులు, క్లాంప్లు లేదా మెషిన్డ్ మెటల్ కాంపోనెంట్లు ఆప్టికల్ భాగాలను నిర్దిష్ట దూరాల్లో మరియు నిర్దిష్ట రేఖాగణిత ధోరణులతో సమీకరించడానికి ఉపయోగించబడుతున్నాయి. హై ఎండ్ ఆప్టిక్స్ తయారీకి సంబంధించి మా ప్రసిద్ధ పద్ధతుల్లో కొన్నింటిని పరిశీలిద్దాం. గ్రైండింగ్ & ల్యాపింగ్ & పాలిషింగ్: ఆప్టికల్ కాంపోనెంట్ యొక్క కఠినమైన ఆకారం గాజును ఖాళీగా గ్రౌండింగ్ చేయడం ద్వారా పొందబడుతుంది. ఆ తర్వాత ల్యాపింగ్ మరియు పాలిషింగ్ ఆప్టికల్ భాగాల యొక్క కఠినమైన ఉపరితలాలను కావలసిన ఉపరితల ఆకారాలతో సాధనాలకు వ్యతిరేకంగా తిప్పడం మరియు రుద్దడం ద్వారా నిర్వహించబడతాయి. ఆప్టిక్స్ మరియు షేపింగ్ టూల్స్ మధ్య చిన్న రాపిడి కణాలు మరియు ద్రవంతో కూడిన స్లర్రీలు పోయబడుతున్నాయి. అటువంటి స్లర్రీలలోని రాపిడి కణ పరిమాణాలను కావలసిన ఫ్లాట్నెస్ స్థాయికి అనుగుణంగా ఎంచుకోవచ్చు. కావలసిన ఆకారాల నుండి క్లిష్టమైన ఆప్టికల్ ఉపరితలాల యొక్క విచలనాలు ఉపయోగించబడుతున్న కాంతి తరంగదైర్ఘ్యాల పరంగా వ్యక్తీకరించబడతాయి. మా అధిక ఖచ్చితత్వ ఆప్టిక్స్ తరంగదైర్ఘ్యంలో పదవ వంతు (వేవ్లెంగ్త్/10) టాలరెన్స్లను కలిగి ఉంటుంది లేదా మరింత కఠినంగా ఉంటుంది. ఉపరితల ప్రొఫైల్తో పాటు, ఇతర ఉపరితల లక్షణాలు మరియు కొలతలు, గీతలు, చిప్స్, గుంటలు, మచ్చలు... మొదలైన వాటి కోసం క్లిష్టమైన ఉపరితలాలు స్కాన్ చేయబడతాయి మరియు మూల్యాంకనం చేయబడతాయి. ఆప్టికల్ మాన్యుఫ్యాక్చరింగ్ ఫ్లోర్లోని పర్యావరణ పరిస్థితులపై గట్టి నియంత్రణ మరియు అత్యాధునిక పరికరాలతో విస్తృతమైన మెట్రాలజీ మరియు టెస్టింగ్ అవసరాలు దీనిని పరిశ్రమలో ఒక సవాలుగా మార్చాయి. • గాజు తయారీలో ద్వితీయ ప్రక్రియలు: గాజు యొక్క ద్వితీయ మరియు ముగింపు ప్రక్రియల విషయానికి వస్తే మేము మీ ఊహకు మాత్రమే పరిమితం చేస్తాము. ఇక్కడ మేము వాటిలో కొన్నింటిని జాబితా చేస్తాము: -గ్లాస్పై పూతలు (ఆప్టికల్, ఎలక్ట్రికల్, ట్రైబోలాజికల్, థర్మల్, ఫంక్షనల్, మెకానికల్...). ఉదాహరణగా మనం గాజు యొక్క ఉపరితల లక్షణాలను మార్చవచ్చు, ఉదాహరణకు అది వేడిని ప్రతిబింబించేలా చేస్తుంది, తద్వారా ఇది భవనం లోపలి భాగాన్ని చల్లగా ఉంచుతుంది లేదా నానోటెక్నాలజీని ఉపయోగించి ఒక వైపు పరారుణ శోషణను చేస్తుంది. ఇది భవనాల లోపలి భాగాన్ని వెచ్చగా ఉంచడంలో సహాయపడుతుంది ఎందుకంటే గాజు యొక్క బయటి ఉపరితల పొర భవనం లోపల ఉన్న ఇన్ఫ్రారెడ్ రేడియేషన్ను గ్రహించి లోపలికి తిరిగి ప్రసరిస్తుంది. -ఎచింగ్ on glass -అప్లైడ్ సిరామిక్ లేబులింగ్ (ACL) - చెక్కడం - ఫ్లేమ్ పాలిషింగ్ -రసాయన పాలిషింగ్ - మరక టెక్నికల్ సిరమిక్స్ తయారీ • డై ప్రెస్సింగ్ : డైలో పరిమితమైన గ్రాన్యులర్ పౌడర్ల యూనియాక్సియల్ కాంపాక్షన్ను కలిగి ఉంటుంది • హాట్ ప్రెస్సింగ్ : డై నొక్కడం లాగానే ఉంటుంది కానీ డెన్సిఫికేషన్ను పెంచడానికి ఉష్ణోగ్రతను జోడించడం. పౌడర్ లేదా కుదించబడిన ప్రీఫార్మ్ను గ్రాఫైట్ డైలో ఉంచుతారు మరియు డైని 2000 C వంటి అధిక ఉష్ణోగ్రతల వద్ద ఉంచినప్పుడు ఏకకణ పీడనం వర్తించబడుతుంది. ప్రాసెస్ చేయబడిన సిరామిక్ పౌడర్ రకాన్ని బట్టి ఉష్ణోగ్రతలు భిన్నంగా ఉంటాయి. సంక్లిష్టమైన ఆకారాలు మరియు జ్యామితి కోసం డైమండ్ గ్రౌండింగ్ వంటి ఇతర తదుపరి ప్రాసెసింగ్ అవసరం కావచ్చు. • ఐసోస్టాటిక్ ప్రెస్సింగ్: గ్రాన్యులర్ పౌడర్ లేదా డై ప్రెస్డ్ కాంపాక్ట్లు గాలి చొరబడని కంటైనర్లలో ఉంచబడతాయి మరియు తర్వాత లోపల ద్రవంతో మూసివున్న పీడన పాత్రలో ఉంచబడతాయి. ఆ తర్వాత అవి పీడన నాళాల పీడనాన్ని పెంచడం ద్వారా కుదించబడతాయి. నౌకలోని ద్రవం గాలి చొరబడని కంటైనర్ యొక్క మొత్తం ఉపరితల వైశాల్యంపై ఒత్తిడి శక్తులను ఏకరీతిగా బదిలీ చేస్తుంది. ఈ విధంగా మెటీరియల్ ఏకరీతిగా కుదించబడుతుంది మరియు దాని సౌకర్యవంతమైన కంటైనర్ ఆకారాన్ని మరియు దాని అంతర్గత ప్రొఫైల్ మరియు లక్షణాలను తీసుకుంటుంది. • హాట్ ఐసోస్టాటిక్ ప్రెస్సింగ్ : ఐసోస్టాటిక్ నొక్కడం లాంటిదే, కానీ ఒత్తిడితో కూడిన వాయువు వాతావరణంతో పాటు, మేము అధిక ఉష్ణోగ్రత వద్ద కాంపాక్ట్ను సింటర్ చేస్తాము. వేడి ఐసోస్టాటిక్ నొక్కడం వలన అదనపు సాంద్రత మరియు బలం పెరుగుతుంది. • స్లిప్ కాస్టింగ్ / డ్రైన్ కాస్టింగ్ : మేము మైక్రోమీటర్ సైజు సిరామిక్ పార్టికల్స్ మరియు క్యారియర్ లిక్విడ్ సస్పెన్షన్తో అచ్చును నింపుతాము. ఈ మిశ్రమాన్ని "స్లిప్" అంటారు. అచ్చులో రంధ్రాలు ఉంటాయి కాబట్టి మిశ్రమంలోని ద్రవం అచ్చులోకి ఫిల్టర్ చేయబడుతుంది. ఫలితంగా, అచ్చు యొక్క అంతర్గత ఉపరితలాలపై ఒక తారాగణం ఏర్పడుతుంది. సింటరింగ్ తర్వాత, భాగాలను అచ్చు నుండి బయటకు తీయవచ్చు. • టేప్ కాస్టింగ్ : మేము ఫ్లాట్ మూవింగ్ క్యారియర్ ఉపరితలాలపై సిరామిక్ స్లర్రీలను ప్రసారం చేయడం ద్వారా సిరామిక్ టేపులను తయారు చేస్తాము. స్లర్రీలలో బైండింగ్ మరియు మోసే ప్రయోజనాల కోసం ఇతర రసాయనాలతో కలిపిన సిరామిక్ పౌడర్లు ఉంటాయి. ద్రావకాలు ఆవిరైనందున, సిరామిక్ యొక్క దట్టమైన మరియు సౌకర్యవంతమైన షీట్లు మిగిలి ఉంటాయి, వీటిని కావలసిన విధంగా కత్తిరించవచ్చు లేదా చుట్టవచ్చు. • ఎక్స్ట్రూషన్ ఫార్మింగ్ : ఇతర ఎక్స్ట్రాషన్ ప్రక్రియలలో వలె, బైండర్లు మరియు ఇతర రసాయనాలతో కూడిన సిరామిక్ పౌడర్ యొక్క మృదువైన మిశ్రమం దాని క్రాస్-సెక్షనల్ ఆకారాన్ని పొందేందుకు డై గుండా పంపబడుతుంది మరియు తర్వాత కావలసిన పొడవులో కత్తిరించబడుతుంది. ప్రక్రియ చల్లని లేదా వేడిచేసిన సిరామిక్ మిశ్రమాలతో నిర్వహించబడుతుంది. • తక్కువ పీడన ఇంజెక్షన్ మౌల్డింగ్: మేము బైండర్లు మరియు ద్రావకాలతో సిరామిక్ పౌడర్ మిశ్రమాన్ని సిద్ధం చేస్తాము మరియు దానిని సులభంగా నొక్కినప్పుడు మరియు సాధనం కుహరంలోకి బలవంతంగా ఉంచగల ఉష్ణోగ్రతకు వేడి చేస్తాము. అచ్చు చక్రం పూర్తయిన తర్వాత, భాగం బయటకు తీయబడుతుంది మరియు బైండింగ్ రసాయనం కాల్చివేయబడుతుంది. ఇంజెక్షన్ మౌల్డింగ్ ఉపయోగించి, మేము ఆర్థికంగా అధిక వాల్యూమ్లలో క్లిష్టమైన భాగాలను పొందవచ్చు. రంధ్రాలు అంటే 10 మి.మీ మందపాటి గోడపై ఒక మిల్లీమీటర్ యొక్క చిన్న భాగం సాధ్యమే, థ్రెడ్లు తదుపరి మ్యాచింగ్ లేకుండానే సాధ్యమవుతాయి, టాలరెన్స్లు +/- మెషిన్గా బిగుతుగా ఉంటాయి మరియు 0.5% భాగాలు సాధ్యమైనప్పుడు మరింత తక్కువగా ఉంటాయి. , గోడ మందం 0.5 మిమీ నుండి 12.5 మిమీ పొడవు వరకు సాధ్యమే అలాగే 6.5 మిమీ నుండి 150 మిమీ పొడవు వరకు గోడ మందం ఉంటుంది. • గ్రీన్ మ్యాచింగ్ : అదే మెటల్ మ్యాచింగ్ టూల్స్ ఉపయోగించి, సుద్దలాగా మృదువుగా ఉన్నప్పుడే మనం నొక్కిన సిరామిక్ పదార్థాలను మెషిన్ చేయవచ్చు. +/- 1% సహనం సాధ్యమే. మెరుగైన సహనం కోసం మేము డైమండ్ గ్రౌండింగ్ని ఉపయోగిస్తాము. • సింటరింగ్ లేదా ఫైరింగ్ : సింటరింగ్ పూర్తి సాంద్రతను సాధ్యం చేస్తుంది. ఆకుపచ్చ కాంపాక్ట్ భాగాలపై గణనీయమైన సంకోచం సంభవిస్తుంది, అయితే ఇది పెద్ద సమస్య కాదు, ఎందుకంటే మేము భాగాన్ని మరియు సాధనాన్ని రూపొందించినప్పుడు ఈ డైమెన్షనల్ మార్పులను పరిగణనలోకి తీసుకుంటాము. పొడి కణాలు ఒకదానితో ఒకటి బంధించబడతాయి మరియు సంపీడన ప్రక్రియ ద్వారా ప్రేరేపించబడిన సచ్ఛిద్రత చాలా వరకు తొలగించబడుతుంది. • డైమండ్ గ్రైండింగ్: ప్రపంచంలోని అత్యంత కఠినమైన పదార్థం "డైమండ్" సిరామిక్స్ వంటి గట్టి పదార్థాలను గ్రైండ్ చేయడానికి ఉపయోగించబడుతుంది మరియు ఖచ్చితమైన భాగాలు లభిస్తాయి. మైక్రోమీటర్ పరిధిలో టాలరెన్స్లు మరియు చాలా మృదువైన ఉపరితలాలు సాధించబడుతున్నాయి. దాని ఖర్చు కారణంగా, మేము ఈ సాంకేతికతను నిజంగా అవసరమైనప్పుడు మాత్రమే పరిగణిస్తాము. • హెర్మెటిక్ అసెంబ్లీలు అంటే ఆచరణాత్మకంగా చెప్పాలంటే ఇంటర్ఫేస్ల మధ్య పదార్థం, ఘనపదార్థాలు, ద్రవాలు లేదా వాయువుల మార్పిడిని అనుమతించవు. హెర్మెటిక్ సీలింగ్ గాలి చొరబడనిది. ఉదాహరణకు హెర్మెటిక్ ఎలక్ట్రానిక్ ఎన్క్లోజర్లు ప్యాక్ చేయబడిన పరికరంలోని సున్నితమైన అంతర్గత విషయాలను తేమ, కలుషితాలు లేదా వాయువుల ద్వారా క్షేమంగా ఉంచుతాయి. ఏదీ 100% హెర్మెటిక్ కాదు, కానీ మేము హెర్మెటిసిటీ గురించి మాట్లాడేటప్పుడు ఆచరణాత్మకంగా, లీక్ రేట్ చాలా తక్కువగా ఉండేంత వరకు హెర్మెటిసిటీ ఉందని అర్థం, సాధారణ పర్యావరణ పరిస్థితులలో పరికరాలు చాలా కాలం పాటు సురక్షితంగా ఉంటాయి. మా హెర్మెటిక్ సమావేశాలు మెటల్, గాజు మరియు సిరామిక్ భాగాలు, మెటల్-సిరామిక్, సిరామిక్-మెటల్-సిరామిక్, మెటల్-సిరామిక్-మెటల్, మెటల్ నుండి మెటల్, మెటల్-గ్లాస్, మెటల్-గ్లాస్-మెటల్, గ్లాస్-మెటల్-గ్లాస్, గ్లాస్- మెటల్ మరియు గాజు నుండి గాజు మరియు మెటల్-గ్లాస్-సిరామిక్ బంధం యొక్క అన్ని ఇతర కలయికలు. మేము ఉదాహరణకు సిరామిక్ భాగాలను మెటల్ కోట్ చేయవచ్చు, తద్వారా అవి అసెంబ్లీలోని ఇతర భాగాలతో బలంగా బంధించబడతాయి మరియు అద్భుతమైన సీలింగ్ సామర్థ్యాన్ని కలిగి ఉంటాయి. ఆప్టికల్ ఫైబర్లు లేదా ఫీడ్త్రూలను మెటల్తో పూయడం మరియు టంకం వేయడం లేదా వాటిని ఎన్క్లోజర్లకు బ్రేజింగ్ చేయడం ఎలాగో మాకు తెలుసు, కాబట్టి వాయువులు ఎన్క్లోజర్లలోకి వెళ్లవు లేదా లీక్ అవ్వవు. అందువల్ల సున్నితమైన పరికరాలను కప్పి ఉంచడానికి మరియు బాహ్య వాతావరణం నుండి వాటిని రక్షించడానికి ఎలక్ట్రానిక్ ఎన్క్లోజర్ల తయారీకి వీటిని ఉపయోగిస్తారు. వాటి అద్భుతమైన సీలింగ్ లక్షణాలతో పాటు, థర్మల్ ఎక్స్పాన్షన్ కోఎఫీషియంట్, డిఫార్మేషన్ రెసిస్టెన్స్, నాన్-ఔట్గ్యాసింగ్ స్వభావం, చాలా సుదీర్ఘ జీవితకాలం, నాన్కండక్టివ్ స్వభావం, థర్మల్ ఇన్సులేషన్ లక్షణాలు, యాంటిస్టాటిక్ స్వభావం... మొదలైన ఇతర లక్షణాలు. కొన్ని అనువర్తనాల కోసం గాజు మరియు సిరామిక్ పదార్థాలను ఎంపిక చేసుకోండి. సిరామిక్ నుండి మెటల్ ఫిట్టింగ్లు, హెర్మెటిక్ సీలింగ్, వాక్యూమ్ ఫీడ్త్రూలు, హై మరియు అల్ట్రాహై వాక్యూమ్ మరియు ఫ్లూయిడ్ కంట్రోల్ కాంపోనెంట్స్ వంటి మా సదుపాయంపై సమాచారాన్ని ఇక్కడ చూడవచ్చు:హెర్మెటిక్ కాంపోనెంట్స్ ఫ్యాక్టరీ బ్రోచర్ CLICK Product Finder-Locator Service ముందు పేజి
- Wire & Spring Forming, Shaping, Welding, Assembly of Wires, Coil, CNC
Wire & Spring Forming, Shaping, Welding, Assembly of Wires, Coil Compression Extension Torsion Flat Springs, Custom Wires, Helical Springs at AGS-TECH Inc. వైర్ & స్ప్రింగ్ ఫార్మింగ్ మేము కస్టమ్ వైర్లు, వైర్ అసెంబ్లీ, కావలసిన 2D మరియు 3D ఆకారాలుగా ఏర్పడిన వైర్లు, వైర్ నెట్లు, మెష్, ఎన్క్లోజర్లు, బాస్కెట్, ఫెన్స్, వైర్ స్ప్రింగ్, ఫ్లాట్ స్ప్రింగ్లను తయారు చేస్తాము; టోర్షన్, కంప్రెషన్, టెన్షన్, ఫ్లాట్ స్ప్రింగ్స్ మరియు మరిన్ని. మా ప్రక్రియలు వైర్ మరియు స్ప్రింగ్ ఫార్మింగ్, వైర్ డ్రాయింగ్, షేపింగ్, బెండింగ్, వెల్డింగ్, బ్రేజింగ్, టంకం, పియర్సింగ్, స్వేజింగ్, డ్రిల్లింగ్, చాంఫరింగ్, గ్రైండింగ్, థ్రెడింగ్, కోటింగ్, ఫోర్స్లైడ్, స్లైడ్ ఫార్మింగ్, వైండింగ్, కాయిలింగ్, అప్సెట్టింగ్. మీరు ఇక్కడ క్లిక్ చేయాలని మేము సిఫార్సు చేస్తున్నాము AGS-TECH Inc ద్వారా వైర్ మరియు స్ప్రింగ్ ఫార్మింగ్ ప్రాసెస్ల యొక్క మా స్కీమాటిక్ ఇలస్ట్రేషన్లను డౌన్లోడ్ చేయండి. ఫోటోలు మరియు స్కెచ్లతో కూడిన ఈ డౌన్లోడ్ చేయదగిన ఫైల్ మేము దిగువ మీకు అందిస్తున్న సమాచారాన్ని బాగా అర్థం చేసుకోవడంలో మీకు సహాయం చేస్తుంది. • వైర్ డ్రాయింగ్ : తన్యత శక్తులను ఉపయోగించి మనం మెటల్ స్టాక్ను సాగదీసి, వ్యాసాన్ని తగ్గించడానికి మరియు దాని పొడవును పెంచడానికి డై ద్వారా డ్రా చేస్తాము. కొన్నిసార్లు మేము డైస్ల శ్రేణిని ఉపయోగిస్తాము. మేము వైర్ యొక్క ప్రతి గేజ్ కోసం డైలను తయారు చేయగలము. అధిక తన్యత బలం యొక్క పదార్థాన్ని ఉపయోగించి మేము చాలా సన్నని వైర్లను గీస్తాము. మేము చల్లని మరియు వేడిగా పనిచేసే వైర్లను అందిస్తాము. • వైర్ ఫార్మింగ్ : గేజ్డ్ వైర్ యొక్క రోల్ వంగి మరియు ఉపయోగకరమైన ఉత్పత్తిగా ఆకృతి చేయబడింది. సన్నని తంతువులతో పాటు ఆటోమొబైల్ చట్రం కింద స్ప్రింగ్లుగా ఉపయోగించే మందపాటి వైర్లతో సహా అన్ని గేజ్ల నుండి వైర్లను రూపొందించే సామర్థ్యం మాకు ఉంది. వైర్ ఫార్మింగ్ కోసం మేము ఉపయోగించే పరికరాలు మాన్యువల్ మరియు CNC వైర్ ఫార్మర్స్, కాయిలర్, పవర్ ప్రెస్లు, ఫోర్స్లైడ్, మల్టీ-స్లైడ్. మా ప్రక్రియలు డ్రాయింగ్, బెండింగ్, స్ట్రెయిటెనింగ్, ఫ్లాట్నింగ్, స్ట్రెచింగ్, కటింగ్, అప్సెట్టింగ్, టంకం & వెల్డింగ్ & బ్రేజింగ్, అసెంబ్లీ, కాయిలింగ్, స్వేజింగ్ (లేదా రెక్కలు), పియర్సింగ్, వైర్ థ్రెడింగ్, డ్రిల్లింగ్, చాంఫరింగ్, గ్రైండింగ్, కోటింగ్ మరియు ఉపరితల చికిత్సలు. మా అత్యాధునిక పరికరాలను ఏదైనా ఆకృతి మరియు గట్టి సహనం యొక్క చాలా క్లిష్టమైన డిజైన్లను అభివృద్ధి చేయడానికి సెటప్ చేయవచ్చు. మేము మీ వైర్ల కోసం వివిధ రకాల ముగింపు రకాల వంటి గోళాకార, పాయింటెడ్ లేదా చాంఫెర్డ్ ఎండ్లను అందిస్తున్నాము. మా వైర్ ఫార్మింగ్ ప్రాజెక్ట్లలో చాలా వరకు తక్కువ నుండి సున్నా టూలింగ్ ఖర్చులు ఉంటాయి. నమూనా మలుపు సమయాలు సాధారణంగా రోజులు. వైర్ ఫారమ్ల డిజైన్/కాన్ఫిగరేషన్లో మార్పులు చాలా త్వరగా చేయవచ్చు. • స్ప్రింగ్ ఫార్మింగ్ : AGS-TECH అనేక రకాలైన స్ప్రింగ్లను తయారు చేస్తుంది: -టార్షన్ / డబుల్ టోర్షన్ స్ప్రింగ్ -టెన్షన్ / కంప్రెషన్ స్ప్రింగ్ - స్థిరమైన / వేరియబుల్ స్ప్రింగ్ -కాయిల్ & హెలికల్ స్ప్రింగ్ -ఫ్లాట్ & లీఫ్ స్ప్రింగ్ - బ్యాలెన్స్ స్ప్రింగ్ -బెల్విల్లే వాషర్ -నెగేటర్ స్ప్రింగ్ -ప్రోగ్రెసివ్ రేట్ కాయిల్ స్ప్రింగ్ -వేవ్ స్ప్రింగ్ -వాల్యూట్ స్ప్రింగ్ -టాపెర్డ్ స్ప్రింగ్స్ - స్ప్రింగ్ రింగ్స్ - క్లాక్ స్ప్రింగ్స్ -క్లిప్లు మేము వివిధ రకాల పదార్థాల నుండి స్ప్రింగ్లను తయారు చేస్తాము మరియు మీ అప్లికేషన్ ప్రకారం మీకు మార్గనిర్దేశం చేస్తాము. అత్యంత సాధారణ పదార్థాలు స్టెయిన్లెస్ స్టీల్, క్రోమ్ సిలికాన్, హై-కార్బన్ స్టీల్, ఆయిల్-టెంపర్డ్ లో-కార్బన్, క్రోమ్ వెనాడియం, ఫాస్ఫర్ కాంస్య, టైటానియం, బెరీలియం రాగి మిశ్రమం, అధిక-ఉష్ణోగ్రత సిరామిక్. మేము స్ప్రింగ్ల తయారీలో CNC కాయిలింగ్, కోల్డ్ వైండింగ్, హాట్ వైండింగ్, గట్టిపడటం, పూర్తి చేయడం వంటి వివిధ పద్ధతులను ఉపయోగిస్తాము. వైర్ ఫార్మింగ్ కింద ఇప్పటికే పైన పేర్కొన్న ఇతర పద్ధతులు మా వసంత తయారీ కార్యకలాపాలలో కూడా సాధారణం. • వైర్లు & స్ప్రింగ్ల కోసం సేవలను పూర్తి చేయడం : మీ ఎంపిక మరియు అవసరాలను బట్టి మేము మీ ఉత్పత్తులను అనేక మార్గాల్లో పూర్తి చేయవచ్చు. మేము అందించే కొన్ని సాధారణ ప్రక్రియలు: పెయింటింగ్, పౌడర్ కోటింగ్, ప్లేటింగ్, వినైల్ డిప్పింగ్, యానోడైజింగ్, స్ట్రెస్ రిలీవ్, హీట్ ట్రీట్మెంట్, షాట్ పీన్, టంబుల్, క్రోమేట్, electroless నికెల్, నిష్క్రియాత్మకమైన ప్లాస్టిక్, పాసివేషన్ , ప్లాస్మా క్లీనింగ్. CLICK Product Finder-Locator Service ముందు పేజి
- Sheet Metal Forming Fabrication, Stamping, Punching, Deep Drawing, CNC
Sheet Metal Forming and Fabrication, Stamping, Punching, Bending, Progressive Die, Spot Welding, Deep Drawing, Metal Blanking and Slitting at AGS-TECH Inc. స్టాంపింగ్లు & షీట్ మెటల్ ఫ్యాబ్రికేషన్ మేము షీట్ మెటల్ స్టాంపింగ్, షేపింగ్, ఫార్మింగ్, బెండింగ్, పంచింగ్, బ్లాంకింగ్, స్లిట్టింగ్, పెర్ఫొరేటింగ్, నోచింగ్, నిబ్లింగ్, షేవింగ్, ప్రెస్వర్కింగ్, ఫ్యాబ్రికేషన్, డీప్ డ్రాయింగ్ను సింగిల్ పంచ్ / సింగిల్ స్ట్రోక్ డైస్తో పాటు ప్రోగ్రెసివ్ డైస్ మరియు స్పిన్నింగ్, రబ్బర్ ఫార్మింగ్ మరియు హైడ్రోఫార్మింగ్; వాటర్ జెట్, ప్లాస్మా, లేజర్, రంపపు, జ్వాల ఉపయోగించి షీట్ మెటల్ కట్టింగ్; వెల్డింగ్, స్పాట్ వెల్డింగ్ ఉపయోగించి షీట్ మెటల్ అసెంబ్లీ; షీట్ మెటల్ ట్యూబ్ ఉబ్బిన మరియు బెండింగ్; డిప్ లేదా స్ప్రే పెయింటింగ్, ఎలెక్ట్రోస్టాటిక్ పౌడర్ కోటింగ్, యానోడైజింగ్, ప్లేటింగ్, స్పుట్టరింగ్ మరియు మరెన్నో సహా షీట్ మెటల్ ఉపరితల ముగింపు. మా సేవలు వేగవంతమైన షీట్ మెటల్ ప్రోటోటైపింగ్ నుండి అధిక వాల్యూమ్ తయారీ వరకు ఉంటాయి. మీరు ఇక్కడ క్లిక్ చేయాలని మేము సిఫార్సు చేస్తున్నాముAGS-TECH Inc ద్వారా షీట్ మెటల్ ఫాబ్రికేషన్ మరియు స్టాంపింగ్ ప్రక్రియల యొక్క మా స్కీమాటిక్ ఇలస్ట్రేషన్లను డౌన్లోడ్ చేయండి. మేము దిగువ మీకు అందిస్తున్న సమాచారాన్ని బాగా అర్థం చేసుకోవడంలో ఇది మీకు సహాయం చేస్తుంది. • షీట్ మెటల్ కట్టింగ్ : మేము కటాఫ్లు మరియు పార్టింగ్లను అందిస్తాము. కటాఫ్లు షీట్ మెటల్ను ఒకేసారి ఒక మార్గంలో కత్తిరించాయి మరియు ప్రాథమికంగా పదార్థం యొక్క వ్యర్థాలు లేవు, అయితే విభజనలతో ఆకారాన్ని ఖచ్చితంగా ఉంచడం సాధ్యం కాదు మరియు అందువల్ల కొంత మొత్తంలో పదార్థం వృధా అవుతుంది. మా అత్యంత జనాదరణ పొందిన ప్రక్రియలలో ఒకటి పంచింగ్, ఇక్కడ మెటీరియల్ గుండ్రని లేదా ఇతర ఆకారం షీట్ మెటల్ నుండి కత్తిరించబడుతుంది. కత్తిరించిన ముక్క వ్యర్థం. పంచింగ్ యొక్క మరొక సంస్కరణ SLOTTING, ఇక్కడ దీర్ఘచతురస్రాకార లేదా పొడుగు రంధ్రాలు పంచ్ చేయబడతాయి. మరోవైపు ఖాళీ చేయడం అనేది పంచ్తో సమానమైన ప్రక్రియ, కత్తిరించిన ముక్క యొక్క వ్యత్యాసం పని మరియు ఉంచబడుతుంది. FINE BLANKING, బ్లాంకింగ్ యొక్క అత్యుత్తమ వెర్షన్, దగ్గరి టాలరెన్స్లు మరియు నేరుగా మృదువైన అంచులతో కట్లను సృష్టిస్తుంది మరియు వర్క్పీస్ యొక్క పరిపూర్ణత కోసం ద్వితీయ కార్యకలాపాలు అవసరం లేదు. మేము తరచుగా ఉపయోగించే మరొక ప్రక్రియ SLITTING, ఇది షీట్ మెటల్ నేరుగా లేదా వక్ర మార్గంలో రెండు వ్యతిరేక వృత్తాకార బ్లేడ్ల ద్వారా కత్తిరించబడే మకా ప్రక్రియ. కెన్ ఓపెనర్ స్లిటింగ్ ప్రక్రియకు ఒక సాధారణ ఉదాహరణ. మరొక ప్రసిద్ధ process PERFORATING, ఇక్కడ అనేక రంధ్రాలు గుండ్రంగా లేదా ఇతర ఆకారంలో షీట్ మెటల్లో నిర్దిష్ట నమూనాలో పంచ్ చేయబడతాయి. చిల్లులు కలిగిన ఉత్పత్తికి ఒక సాధారణ ఉదాహరణ ద్రవాలకు అనేక రంధ్రాలతో మెటల్ ఫిల్టర్లు. NOTCHINGలో, మరొక షీట్ మెటల్ కట్టింగ్ ప్రక్రియ, మేము వర్క్ పీస్ నుండి పదార్థాన్ని తీసివేస్తాము, అంచు లేదా మరెక్కడైనా ప్రారంభించి, కావలసిన ఆకృతిని పొందే వరకు లోపలికి కట్ చేస్తాము. ఇది ఒక ప్రగతిశీల ప్రక్రియ, ఇక్కడ ప్రతి ఆపరేషన్ కావలసిన ఆకృతిని పొందే వరకు మరొక భాగాన్ని తొలగిస్తుంది. చిన్న ఉత్పత్తి పరుగుల కోసం మేము కొన్నిసార్లు NIBBLING అని పిలువబడే సాపేక్షంగా నెమ్మదిగా ఉండే ప్రక్రియను ఉపయోగిస్తాము, ఇది పెద్ద మరింత సంక్లిష్టమైన కట్ చేయడానికి అతివ్యాప్తి చెందుతున్న రంధ్రాల యొక్క అనేక వేగవంతమైన పంచ్లను కలిగి ఉంటుంది. ప్రోగ్రెస్సివ్ కట్టింగ్లో మేము ఒకే కోత లేదా నిర్దిష్ట జ్యామితిని పొందేందుకు వివిధ ఆపరేషన్ల శ్రేణిని ఉపయోగిస్తాము. చివరగా సెకండరీ ప్రాసెస్ను షేవింగ్ చేయడం ద్వారా ఇప్పటికే చేసిన కట్ల అంచులను మెరుగుపరచడంలో మాకు సహాయపడుతుంది. ఇది షీట్ మెటల్ పనిలో చిప్స్, కఠినమైన అంచులను కత్తిరించడానికి ఉపయోగించబడుతుంది. • షీట్ మెటల్ బెండింగ్ : కటింగ్ కాకుండా, బెండింగ్ అనేది ఒక ముఖ్యమైన ప్రక్రియ, ఇది లేకుండా మనం చాలా ఉత్పత్తులను ఉత్పత్తి చేయలేము. ఎక్కువగా చల్లగా పనిచేసే ఆపరేషన్ కానీ కొన్నిసార్లు వెచ్చగా లేదా వేడిగా ఉన్నప్పుడు కూడా నిర్వహిస్తారు. మేము ఈ ఆపరేషన్ కోసం ఎక్కువ సమయం డైస్ మరియు ప్రెస్లను ఉపయోగిస్తాము. ప్రోగ్రెస్సివ్ బెండింగ్లో మేము ఒకే వంపు లేదా నిర్దిష్ట జ్యామితిని పొందేందుకు వేర్వేరు పంచ్ మరియు డై ఆపరేషన్ల శ్రేణిని ఉపయోగిస్తాము. AGS-TECH అనేక రకాల బెండింగ్ ప్రక్రియలను ఉపయోగిస్తుంది మరియు వర్క్పీస్ మెటీరియల్, దాని పరిమాణం, మందం, బెండ్ యొక్క కావలసిన పరిమాణం, వ్యాసార్థం, వంపు మరియు వంపు యొక్క కోణం, బెండ్ యొక్క స్థానం, ఆపరేషన్ యొక్క ఆర్థిక వ్యవస్థ, తయారు చేయవలసిన పరిమాణాలపై ఆధారపడి ఎంపిక చేస్తుంది… మొదలైనవి మేము V-BENDINGని ఉపయోగిస్తాము, ఇక్కడ V ఆకారపు పంచ్ షీట్ మెటల్ను V ఆకారపు డైలోకి బలవంతం చేస్తుంది మరియు దానిని వంగి ఉంటుంది. 90 డిగ్రీలతో సహా చాలా తీవ్రమైన మరియు మందమైన కోణాలు మరియు మధ్యలో రెండింటికీ మంచిది. వైపింగ్ డైస్ని ఉపయోగించి మేము ఎడ్జ్ బెండింగ్ చేస్తాము. మా పరికరాలు 90 డిగ్రీల కంటే పెద్ద కోణాలను పొందగలుగుతాయి. ఎడ్జ్ బెండింగ్లో వర్క్పీస్ ప్రెజర్ ప్యాడ్ మరియు డై మధ్య శాండ్విచ్ చేయబడుతుంది, బెండింగ్ కోసం ప్రాంతం డై ఎడ్జ్లో ఉంటుంది మరియు మిగిలిన వర్క్పీస్ స్పేస్ లైక్ కాంటిలివర్ బీమ్పై ఉంచబడుతుంది. పంచ్ కాంటిలివర్ భాగంలో పనిచేసినప్పుడు, అది డై యొక్క అంచుపై వంగి ఉంటుంది. FLANGING అనేది 90 డిగ్రీల కోణంలో ఏర్పడే ఎడ్జ్ బెండింగ్ ప్రక్రియ. ఆపరేషన్ యొక్క ప్రధాన లక్ష్యాలు పదునైన అంచుల తొలగింపు మరియు భాగాల చేరికను సులభతరం చేయడానికి రేఖాగణిత ఉపరితలాలను పొందడం. బీడింగ్, మరొక సాధారణ అంచు బెండింగ్ ప్రక్రియ ఒక భాగం యొక్క అంచుపై కర్ల్ను ఏర్పరుస్తుంది. మరోవైపు హెమ్మింగ్ షీట్ యొక్క అంచుతో పూర్తిగా వంగి ఉంటుంది. సీమింగ్లో, రెండు భాగాల అంచులు ఒకదానికొకటి వంగి ఉంటాయి. మరోవైపు డబుల్ సీమింగ్ వాటర్టైట్ మరియు ఎయిర్టైట్ షీట్ మెటల్ కీళ్లను అందిస్తుంది. ఎడ్జ్ బెండింగ్ లాగానే, రోటరీ బెండింగ్ అని పిలవబడే ప్రక్రియ కావలసిన యాంగిల్ కట్ అవుట్తో కూడిన సిలిండర్ను అమర్చుతుంది మరియు పంచ్గా పనిచేస్తుంది. శక్తి పంచ్కు ప్రసారం చేయబడినందున, అది వర్క్పీస్తో మూసివేయబడుతుంది. సిలిండర్ యొక్క గాడి కాంటిలివర్ భాగానికి కావలసిన కోణాన్ని ఇస్తుంది. గాడి 90 డిగ్రీల కంటే చిన్న లేదా పెద్ద కోణాన్ని కలిగి ఉంటుంది. ఎయిర్ బెండింగ్లో, కోణీయ గాడిని కలిగి ఉండటానికి మనకు దిగువ డై అవసరం లేదు. షీట్ మెటల్కు వ్యతిరేక వైపులా మరియు నిర్దిష్ట దూరం వద్ద రెండు ఉపరితలాలు మద్దతునిస్తాయి. అప్పుడు పంచ్ సరైన ప్రదేశంలో బలాన్ని ప్రయోగిస్తుంది మరియు వర్క్పీస్ను వంగుతుంది. ఛానెల్ ఆకారపు పంచ్ మరియు డైని ఉపయోగించి ఛానెల్ బెండింగ్ నిర్వహించబడుతుంది మరియు U-ఆకారపు పంచ్తో U-BEND సాధించబడుతుంది. ఆఫ్సెట్ బెండింగ్ షీట్ మెటల్పై ఆఫ్సెట్లను ఉత్పత్తి చేస్తుంది. రోల్ బెండింగ్, మందపాటి పనికి మరియు పెద్ద మెటల్ ప్లేట్లను వంచడానికి మంచి టెక్నిక్, ప్లేట్లను ఫీడ్ చేయడానికి మరియు కావలసిన వక్రతలకు వంచడానికి మూడు రోల్స్ను ఉపయోగిస్తుంది. రోల్స్ అమర్చబడి ఉంటాయి, తద్వారా పని యొక్క కావలసిన బెండ్ పొందబడుతుంది. కావలసిన ఫలితాన్ని పొందడానికి రోల్స్ మధ్య దూరం మరియు కోణం నియంత్రించబడుతుంది. కదిలే రోల్ వక్రతను నియంత్రించడాన్ని సాధ్యం చేస్తుంది. ట్యూబ్ ఫార్మింగ్ అనేది మల్టిపుల్ డైస్తో కూడిన మరొక ప్రసిద్ధ షీట్ మెటల్ బెండింగ్ ఆపరేషన్. బహుళ చర్యల తర్వాత గొట్టాలు పొందబడతాయి. బెండింగ్ ఆపరేషన్ల ద్వారా ముడతలు కూడా నిర్వహించబడతాయి. ప్రాథమికంగా ఇది మొత్తం షీట్ మెటల్ ముక్కలో క్రమ వ్యవధిలో సుష్ట వంపు. ముడతలు పెట్టడానికి వివిధ ఆకృతులను ఉపయోగించవచ్చు. ముడతలు పెట్టిన షీట్ మెటల్ మరింత దృఢమైనది మరియు వంగడానికి వ్యతిరేకంగా మెరుగైన ప్రతిఘటనను కలిగి ఉంటుంది మరియు అందువల్ల నిర్మాణ పరిశ్రమలో అప్లికేషన్లు ఉన్నాయి. షీట్ మెటల్ రోల్ ఫార్మింగ్, రోల్స్ను ఉపయోగించి నిర్దిష్ట జ్యామితి యొక్క క్రాస్ సెక్షన్లను వంచడానికి ఒక కంటిన్యూన్ manufacturing ప్రక్రియ అమలు చేయబడుతుంది మరియు చివరి పని రోల్ పూర్తి చేయడంతో పని వరుస దశల్లో వంగి ఉంటుంది. కొన్ని సందర్భాల్లో ఒకే రోల్ మరియు కొన్ని సందర్భాల్లో వరుస రోల్స్ ఉపయోగించబడతాయి. • కంబైన్డ్ షీట్ మెటల్ కట్టింగ్ & బెండింగ్ ప్రాసెస్లు : ఇవి ఒకే సమయంలో కట్ మరియు బెండ్ చేసే ప్రక్రియలు. పియర్సింగ్లో, ఒక పాయింటెడ్ పంచ్ని ఉపయోగించి రంధ్రం సృష్టించబడుతుంది. షీట్లోని రంధ్రాన్ని పంచ్విడెన్స్ చేయడంతో, పదార్థం రంధ్రం కోసం అంతర్గత అంచులోకి ఏకకాలంలో వంగి ఉంటుంది. పొందిన అంచు ముఖ్యమైన విధులను కలిగి ఉండవచ్చు. మరొక వైపు LANCING ఆపరేషన్ పెరిగిన జ్యామితిని సృష్టించడానికి షీట్ను కత్తిరించి వంచి చేస్తుంది. • మెటల్ ట్యూబ్ ఉబ్బడం మరియు వంగడం : బోలు ట్యూబ్ యొక్క కొంత అంతర్గత భాగం ఒత్తిడికి గురవుతుంది, దీని వలన ట్యూబ్ బయటికి ఉబ్బుతుంది. ట్యూబ్ డై లోపల ఉన్నందున, ఉబ్బిన జ్యామితి డై ఆకారం ద్వారా నియంత్రించబడుతుంది. స్ట్రెచ్ బెండింగ్లో, ఒక మెటల్ ట్యూబ్ ట్యూబ్ యొక్క అక్షానికి సమాంతరంగా ఉండే శక్తులను ఉపయోగించి మరియు ట్యూబ్ను ఫారమ్ బ్లాక్పైకి లాగడానికి బెండింగ్ శక్తులను ఉపయోగించి విస్తరించబడుతుంది. డ్రా బెండింగ్లో, మేము ట్యూబ్ను దాని చివర చుట్టూ తిరిగే ఫారమ్ బ్లాక్కి బిగిస్తాము, అది తిరిగేటప్పుడు ట్యూబ్ను వంగి ఉంటుంది. చివరగా, కంప్రెషన్ బెండింగ్లో ట్యూబ్ ఒక స్థిర ఫారమ్ బ్లాక్కి బలవంతంగా ఉంచబడుతుంది మరియు ఒక డై దానిని ఫారమ్ బ్లాక్పై వంగుతుంది. • డీప్ డ్రాయింగ్: మా అత్యంత జనాదరణ పొందిన ఆపరేషన్లలో ఒక పంచ్, మ్యాచింగ్ డై మరియు ఖాళీ హోల్డర్ ఉపయోగించబడతాయి. షీట్ మెటల్ ఖాళీ డై ఓపెనింగ్పై ఉంచబడుతుంది మరియు పంచ్ ఖాళీ హోల్డర్ చేత పట్టుకున్న ఖాళీ వైపు కదులుతుంది. అవి పరిచయంలోకి వచ్చిన తర్వాత, పంచ్ షీట్ మెటల్ను డై కేవిటీలోకి ఉత్పత్తిని ఏర్పరుస్తుంది. డీప్ డ్రాయింగ్ ఆపరేషన్ కటింగ్ను పోలి ఉంటుంది, అయితే పంచ్ మరియు డై మధ్య క్లియరెన్స్ షీట్ను కత్తిరించకుండా నిరోధిస్తుంది. షీట్ లోతుగా డ్రా చేయబడిందని మరియు కత్తిరించబడదని భరోసా ఇచ్చే మరొక అంశం డై మరియు పంచ్లోని గుండ్రని మూలలు, ఇది మకా మరియు కత్తిరించడాన్ని నిరోధిస్తుంది. డీప్ డ్రాయింగ్ యొక్క ఎక్కువ పరిమాణాన్ని సాధించడానికి, ఒక రీడ్రాయింగ్ ప్రక్రియ అమలు చేయబడుతోంది, ఇక్కడ లోతైన డ్రాయింగ్ ప్రక్రియ ఇప్పటికే జరిగిన ఒక భాగంలో తదుపరి లోతైన డ్రాయింగ్ జరుగుతుంది. రివర్స్ రీడ్రాయింగ్లో, లోతుగా గీసిన భాగాన్ని తిప్పి, వ్యతిరేక దిశలో గీస్తారు. డీప్ డ్రాయింగ్ డోమ్, టేపర్డ్ లేదా స్టెప్డ్ కప్పులు, EMBOSSING వంటి క్రమరహిత ఆకారపు వస్తువులను అందిస్తుంది. • SPINNING : తిరిగే మాండ్రెల్ మరియు టెయిల్ స్టాక్ మధ్య ఫ్లాట్ లేదా ముందుగా రూపొందించిన వర్క్పీస్ ఉంచబడిన ఆపరేషన్ మరియు సాధనం క్రమంగా మాండ్రెల్ పైకి కదులుతున్నప్పుడు పనికి స్థానికీకరించిన ఒత్తిడిని వర్తింపజేస్తుంది. ఫలితంగా, వర్క్పీస్ మాండ్రేల్పై చుట్టబడి దాని ఆకారాన్ని తీసుకుంటుంది. మేము ఈ సాంకేతికతను డీప్ డ్రాయింగ్కు ప్రత్యామ్నాయంగా ఉపయోగిస్తాము, ఇక్కడ ఆర్డర్ పరిమాణం తక్కువగా ఉంటుంది, భాగాలు పెద్దవి (20 అడుగుల వరకు వ్యాసం) మరియు ప్రత్యేకమైన వక్రతలు ఉంటాయి. ఒక్కో ముక్క ధర సాధారణంగా ఎక్కువగా ఉన్నప్పటికీ, డీప్ డ్రాయింగ్తో పోలిస్తే CNC స్పిన్నింగ్ ఆపరేషన్ కోసం సెటప్ ఖర్చులు తక్కువగా ఉంటాయి. దీనికి విరుద్ధంగా, డీప్ డ్రాయింగ్కు సెటప్ కోసం అధిక ప్రారంభ పెట్టుబడి అవసరమవుతుంది, అయితే అధిక మొత్తంలో భాగాలు ఉత్పత్తి చేయబడినప్పుడు ఒక్కో ముక్క ఖర్చు తక్కువగా ఉంటుంది. ఈ ప్రక్రియ యొక్క మరొక వెర్షన్ షీర్ స్పిన్నింగ్, ఇక్కడ వర్క్పీస్లో మెటల్ ఫ్లో కూడా ఉంటుంది. ప్రక్రియ నిర్వహిస్తున్నందున మెటల్ ప్రవాహం వర్క్పీస్ యొక్క మందాన్ని తగ్గిస్తుంది. మరొక సంబంధిత ప్రక్రియ ట్యూబ్ స్పిన్నింగ్, ఇది స్థూపాకార భాగాలపై వర్తించబడుతుంది. ఈ ప్రక్రియలో వర్క్పీస్ లోపల లోహ ప్రవాహం ఉంటుంది. తద్వారా మందం తగ్గుతుంది మరియు ట్యూబ్ పొడవు పెరుగుతుంది. ట్యూబ్ లోపల లేదా వెలుపల లక్షణాలను సృష్టించడానికి సాధనాన్ని తరలించవచ్చు. • షీట్ మెటల్ యొక్క రబ్బరు ఏర్పాటు : రబ్బరు లేదా పాలియురేతేన్ పదార్థం ఒక కంటైనర్ డైలో ఉంచబడుతుంది మరియు పని భాగాన్ని రబ్బరు ఉపరితలంపై ఉంచబడుతుంది. వర్క్ పీస్పై ఒక పంచ్ పని చేయబడుతుంది మరియు దానిని రబ్బరులోకి బలవంతం చేస్తుంది. రబ్బరు ఉత్పత్తి చేసే ఒత్తిడి తక్కువగా ఉన్నందున, ఉత్పత్తి చేయబడిన భాగాల లోతు పరిమితంగా ఉంటుంది. సాధన ఖర్చులు తక్కువగా ఉన్నందున, ప్రక్రియ తక్కువ పరిమాణ ఉత్పత్తికి అనుకూలంగా ఉంటుంది. • హైడ్రాఫార్మింగ్ : రబ్బరు ఏర్పడినట్లే, ఈ ప్రక్రియలో షీట్ మెటల్ వర్క్ ఒక చాంబర్ లోపల ఒత్తిడితో కూడిన ద్రవంలోకి ఒక పంచ్ ద్వారా నొక్కబడుతుంది. షీట్ మెటల్ పని పంచ్ మరియు రబ్బరు డయాఫ్రాగమ్ మధ్య శాండ్విచ్ చేయబడింది. డయాఫ్రాగమ్ వర్క్పీస్ను పూర్తిగా చుట్టుముడుతుంది మరియు ద్రవం యొక్క ఒత్తిడి అది పంచ్పై ఏర్పడేలా చేస్తుంది. డీప్ డ్రాయింగ్ ప్రక్రియలో కంటే చాలా లోతైన డ్రాలను ఈ టెక్నిక్తో పొందవచ్చు. మేము మీ భాగాన్ని బట్టి సింగిల్-పంచ్ డైలను అలాగే ప్రోజెసివ్ డైలను తయారు చేస్తాము. సింగిల్ స్ట్రోక్ స్టాంపింగ్ డైస్ అనేది ఉతికే యంత్రాలు వంటి సాధారణ షీట్ మెటల్ భాగాలను పెద్ద మొత్తంలో త్వరగా ఉత్పత్తి చేయడానికి ఖర్చుతో కూడుకున్న పద్ధతి. ప్రోగ్రెసివ్ డైస్ లేదా డీప్ డ్రాయింగ్ టెక్నిక్ మరింత సంక్లిష్టమైన జ్యామితి తయారీకి ఉపయోగించబడతాయి. మీ కేసుపై ఆధారపడి, వాటర్జెట్, లేజర్ లేదా ప్లాస్మా కట్టింగ్ మీ షీట్ మెటల్ భాగాలను చౌకగా, వేగంగా మరియు ఖచ్చితంగా ఉత్పత్తి చేయడానికి ఉపయోగించవచ్చు. చాలా మంది సరఫరాదారులకు ఈ ప్రత్యామ్నాయ పద్ధతుల గురించి తెలియదు లేదా వాటిని కలిగి ఉండరు మరియు అందువల్ల వారు వినియోగదారుల సమయాన్ని మరియు డబ్బును మాత్రమే వృధా చేసే డైస్ మరియు సాధనాలను తయారు చేయడానికి సుదీర్ఘమైన మరియు ఖరీదైన మార్గాలను అనుసరిస్తారు. మీకు కస్టమ్ బిల్ట్ షీట్ మెటల్ కాంపోనెంట్లు అంటే ఎన్క్లోజర్లు, ఎలక్ట్రానిక్ హౌసింగ్లు...మొదలైనంత త్వరగా అవసరమైతే, మా ర్యాపిడ్ షీట్ మెటల్ ప్రోటోటైపింగ్ సర్వీస్ కోసం మమ్మల్ని సంప్రదించండి. CLICK Product Finder-Locator Service మునుపటి మెను
- Forging and Powdered Metallurgy, Die Forging, Heading, Hot Forging
Forging and Powdered Metallurgy, Die Forging, Heading, Hot Forging, Impression Die, Near Net Shape, Swaging, Metal Hobbing, Riveting, Coining from AGS-TECH Inc. మెటల్ ఫోర్జింగ్ & పౌడర్ మెటలర్జీ మేము అందించే మెటల్ ఫోర్జింగ్ ప్రక్రియల రకాలు హాట్ అండ్ కోల్డ్ డై, ఓపెన్ డై మరియు క్లోజ్డ్ డై, ఇంప్రెషన్ డై & ఫ్లాష్లెస్ ఫోర్జింగ్లు, cogging, ఫుల్లరింగ్, ఎడ్జింగ్ మరియు ప్రెసిషన్ ఫోర్జింగ్, హెడ్-నియర్-షేప్ , స్వేజింగ్, అప్సెట్ ఫోర్జింగ్, మెటల్ హాబింగ్, ప్రెస్ & రోల్ & రేడియల్ & ఆర్బిటల్ & రింగ్ & ఐసోథర్మల్ ఫోర్జింగ్లు, కాయినింగ్, రివెటింగ్, మెటల్ బాల్ ఫోర్జింగ్, మెటల్ పియర్సింగ్, సైజింగ్, హై ఎనర్జీ రేట్ ఫోర్జింగ్. మా పౌడర్ మెటలర్జీ మరియు పౌడర్ ప్రాసెసింగ్ టెక్నిక్లు పౌడర్ ప్రెస్సింగ్ మరియు సింటరింగ్, ఇంప్రెగ్నేషన్, ఇన్ఫిల్ట్రేషన్, హాట్ అండ్ కోల్డ్ ఐసోస్టాటిక్ ప్రెస్సింగ్, మెటల్ ఇంజెక్షన్ మోల్డింగ్, రోల్ కాంపాక్షన్, పౌడర్ రోలింగ్, పౌడర్ ఎక్స్ట్రాషన్, లూస్ సింటరింగ్, స్పార్క్ సింటరింగ్, హాట్ ప్రెస్సింగ్. మీరు ఇక్కడ క్లిక్ చేయాలని మేము సిఫార్సు చేస్తున్నాము AGS-TECH Inc. ద్వారా ఫోర్జింగ్ ప్రక్రియల మా స్కీమాటిక్ ఇలస్ట్రేషన్లను డౌన్లోడ్ చేయండి AGS-TECH Inc. ద్వారా పౌడర్ మెటలర్జీ ప్రక్రియల మా స్కీమాటిక్ ఇలస్ట్రేషన్లను డౌన్లోడ్ చేయండి ఫోటోలు మరియు స్కెచ్లతో కూడిన ఈ డౌన్లోడ్ చేయదగిన ఫైల్లు మేము దిగువ మీకు అందిస్తున్న సమాచారాన్ని బాగా అర్థం చేసుకోవడంలో మీకు సహాయపడతాయి. మెటల్ ఫోర్జింగ్లో, సంపీడన శక్తులు వర్తించబడతాయి మరియు పదార్థం వైకల్యంతో మరియు కావలసిన ఆకృతిని పొందుతుంది. పరిశ్రమలో అత్యంత సాధారణ నకిలీ పదార్థాలు ఇనుము మరియు ఉక్కు, అయితే అల్యూమినియం, రాగి, టైటానియం, మెగ్నీషియం వంటి అనేక ఇతర పదార్థాలు కూడా విస్తృతంగా నకిలీ చేయబడ్డాయి. నకిలీ మెటల్ భాగాలు మూసివున్న పగుళ్లు మరియు మూసివేసిన ఖాళీ స్థలాలకు అదనంగా ధాన్యం నిర్మాణాలను మెరుగుపరిచాయి, అందువలన ఈ ప్రక్రియ ద్వారా పొందిన భాగాల బలం ఎక్కువగా ఉంటుంది. ఫోర్జింగ్ అనేది కాస్టింగ్ లేదా మ్యాచింగ్ ద్వారా తయారు చేయబడిన భాగాల కంటే వాటి బరువు కోసం గణనీయంగా బలమైన భాగాలను ఉత్పత్తి చేస్తుంది. లోహాన్ని దాని తుది ఆకృతిలోకి ప్రవహించేలా చేయడం ద్వారా నకిలీ భాగాలు ఆకృతి చేయబడినందున, లోహం ఒక దిశాత్మక ధాన్యం నిర్మాణాన్ని తీసుకుంటుంది, ఇది భాగాల యొక్క ఉన్నతమైన బలానికి కారణమవుతుంది. మరో మాటలో చెప్పాలంటే, సాధారణ తారాగణం లేదా యంత్ర భాగాలతో పోలిస్తే ఫోర్జింగ్ ప్రక్రియ ద్వారా పొందిన భాగాలు మెరుగైన యాంత్రిక లక్షణాలను వెల్లడిస్తాయి. మెటల్ ఫోర్జింగ్ల బరువు చిన్న తేలికపాటి భాగాల నుండి వందల వేల పౌండ్ల వరకు ఉంటుంది. ఆటోమోటివ్ పార్ట్స్, గేర్లు, వర్క్ టూల్స్, హ్యాండ్ టూల్స్, టర్బైన్ షాఫ్ట్లు, మోటార్సైకిల్ గేర్ వంటి భాగాలపై అధిక ఒత్తిళ్లు వర్తించే యాంత్రికంగా డిమాండ్ ఉన్న అప్లికేషన్ల కోసం మేము ఎక్కువగా ఫోర్జింగ్లను తయారు చేస్తాము. టూలింగ్ మరియు సెటప్ ఖర్చులు సాపేక్షంగా ఎక్కువగా ఉన్నందున, మేము ఈ తయారీ ప్రక్రియను అధిక వాల్యూమ్ ఉత్పత్తికి మరియు తక్కువ వాల్యూమ్ కోసం మాత్రమే సిఫార్సు చేస్తున్నాము, అయితే ఏరోస్పేస్ ల్యాండింగ్ గేర్ వంటి అధిక విలువ కలిగిన కీలకమైన భాగాలు. టూలింగ్ ఖర్చుతో పాటు, కొన్ని సాధారణ యంత్ర భాగాలతో పోల్చితే పెద్ద పరిమాణంలో నకిలీ భాగాల తయారీ లీడ్ టైమ్లు ఎక్కువగా ఉంటాయి, అయితే టెక్నిక్ అనేది పార్ట్లకు చాలా కీలకం, ఇది అద్వితీయమైన బలం, ప్రత్యేకత, అప్లికేషన్లు, అప్లికేషన్లు ఫాస్టెనర్లు, ఆటోమోటివ్, ఫోర్క్లిఫ్ట్, క్రేన్ భాగాలు. • హాట్ డై మరియు కోల్డ్ డై ఫోర్జింగ్ : హాట్ డై ఫోర్జింగ్, పేరు సూచించినట్లుగా, అధిక ఉష్ణోగ్రతల వద్ద నిర్వహించబడుతుంది, డక్టిలిటీ ఎక్కువగా ఉంటుంది మరియు పదార్థం యొక్క బలం తక్కువగా ఉంటుంది. ఇది సులభంగా వైకల్యం మరియు ఫోర్జింగ్ను సులభతరం చేస్తుంది. దీనికి విరుద్ధంగా, కోల్డ్ డై ఫోర్జింగ్ తక్కువ ఉష్ణోగ్రతల వద్ద నిర్వహించబడుతుంది మరియు అధిక బలాలు అవసరమవుతాయి, దీని ఫలితంగా స్ట్రెయిన్ గట్టిపడటం, మెరుగైన ఉపరితల ముగింపు మరియు తయారు చేయబడిన భాగాల యొక్క ఖచ్చితత్వం. • ఓపెన్ డై మరియు ఇంప్రెషన్ డై ఫోర్జింగ్ : ఓపెన్ డై ఫోర్జింగ్లో, డైస్ కంప్రెస్ చేయబడిన మెటీరియల్ను నిరోధించదు, అయితే ఇంప్రెషన్లో డైస్లోని కావిటీస్ను ఫోర్జింగ్ చేయడం వల్ల అది కావలసిన ఆకృతిలో నకిలీ చేయబడినప్పుడు మెటీరియల్ ప్రవాహాన్ని నిరోధిస్తుంది. అప్సెట్ ఫోర్జింగ్ లేదా అప్సెట్టింగ్ అని కూడా పిలుస్తారు, ఇది వాస్తవానికి అదే కాదు కానీ చాలా సారూప్య ప్రక్రియ, అనేది ఓపెన్ డై ప్రక్రియ, ఇక్కడ వర్క్ పీస్ రెండు ఫ్లాట్ డైల మధ్య శాండ్విచ్ చేయబడుతుంది మరియు సంపీడన శక్తి దాని ఎత్తును తగ్గిస్తుంది. ఎత్తు reduced అయినందున, పని ముక్క వెడల్పు పెరుగుతుంది. హెడ్డింగ్, అప్సెట్ ఫోర్జింగ్ ప్రాసెస్లో స్థూపాకార స్టాక్ ఉంటుంది, అది దాని చివరలో కలత చెందుతుంది మరియు దాని క్రాస్ సెక్షన్ స్థానికంగా పెరుగుతుంది. హెడ్డింగ్లో స్టాక్ డై ద్వారా ఫీడ్ చేయబడి, నకిలీ చేసి, ఆపై పొడవుకు కత్తిరించబడుతుంది. ఆపరేషన్ అధిక మొత్తంలో ఫాస్టెనర్లను వేగంగా ఉత్పత్తి చేయగలదు. ఎక్కువగా ఇది ఒక చల్లని పని ఆపరేషన్, ఎందుకంటే ఇది గోరు చివరలను, స్క్రూ చివరలను, గింజలు మరియు బోల్ట్లను తయారు చేయడానికి ఉపయోగిస్తారు, ఇక్కడ పదార్థాన్ని బలోపేతం చేయాలి. మరొక ఓపెన్ డై ప్రక్రియ COGGING, ఇక్కడ వర్క్ పీస్ ప్రతి దశతో వరుస దశల్లో నకిలీ చేయబడుతుంది, దీని ఫలితంగా పదార్థం యొక్క కుదింపు మరియు వర్క్ పీస్ పొడవునా ఓపెన్ డై యొక్క తదుపరి కదలిక ఏర్పడుతుంది. ప్రతి దశలో, మందం తగ్గుతుంది మరియు పొడవు కొద్దిగా పెరుగుతుంది. ఈ ప్రక్రియ ఒక నాడీ విద్యార్థి తన పెన్సిల్ను చిన్న చిన్న దశల్లో కొరికినట్లుగా ఉంటుంది. FULLERING అని పిలవబడే ప్రక్రియ మరొక ఓపెన్ డై ఫోర్జింగ్ పద్ధతి, ఇతర మెటల్ ఫోర్జింగ్ కార్యకలాపాలు జరగడానికి ముందు వర్క్పీస్లోని మెటీరియల్ని పంపిణీ చేయడానికి మేము తరచుగా ప్రారంభ దశగా ఉపయోగిస్తాము. వర్క్ పీస్కి అనేక forging operations అవసరమైనప్పుడు మేము దానిని ఉపయోగిస్తాము. ఆపరేషన్లో, కుంభాకార ఉపరితలాలు వైకల్యంతో మరణిస్తాయి మరియు రెండు వైపులా లోహ ప్రవాహాన్ని కలిగిస్తాయి. ఫుల్లరింగ్కు సమానమైన ప్రక్రియ, మరోవైపు EDGING అనేది వర్క్పీస్ను వికృతీకరించడానికి పుటాకార ఉపరితలాలతో ఓపెన్ డైని కలిగి ఉంటుంది. అంచులు వేయడం అనేది తదుపరి ఫోర్జింగ్ ఆపరేషన్ల కోసం ఒక సన్నాహక ప్రక్రియ, పదార్థం రెండు వైపుల నుండి మధ్యలో ఉన్న ప్రాంతంలోకి ప్రవహిస్తుంది. ఇంప్రెషన్ డై ఫోర్జింగ్ లేదా క్లోజ్డ్ డై ఫోర్జింగ్ అని కూడా పిలుస్తారు, ఇది డై / అచ్చును ఉపయోగిస్తుంది, అది మెటీరియల్ను కుదిస్తుంది మరియు దాని ప్రవాహాన్ని దానిలోనే పరిమితం చేస్తుంది. డై మూసివేయబడుతుంది మరియు పదార్థం డై / అచ్చు కుహరం ఆకారాన్ని తీసుకుంటుంది. PRECISION FORGING, ప్రత్యేక పరికరాలు మరియు అచ్చు అవసరమయ్యే ప్రక్రియ, ఫ్లాష్ లేని లేదా చాలా తక్కువ భాగాలను ఉత్పత్తి చేస్తుంది. మరో మాటలో చెప్పాలంటే, భాగాలు చివరి కొలతలు కలిగి ఉంటాయి. ఈ ప్రక్రియలో బాగా నియంత్రిత మొత్తం పదార్థం జాగ్రత్తగా చొప్పించబడుతుంది మరియు అచ్చు లోపల ఉంచబడుతుంది. మేము ఈ పద్ధతిని సన్నని విభాగాలు, చిన్న టాలరెన్స్లు మరియు డ్రాఫ్ట్ యాంగిల్స్తో సంక్లిష్ట ఆకృతుల కోసం మరియు అచ్చు మరియు పరికరాల ఖర్చులను సమర్థించేంత పెద్ద పరిమాణంలో ఉన్నప్పుడు అమలు చేస్తాము. • ఫ్లాష్లెస్ ఫోర్జింగ్: వర్క్పీస్ డైలో ఉంచబడుతుంది, తద్వారా కుహరం నుండి ఫ్లాష్ని ఏర్పరచడానికి ఏ పదార్థం బయటకు ప్రవహించదు. కాబట్టి అవాంఛనీయ ఫ్లాష్ ట్రిమ్మింగ్ అవసరం లేదు. ఇది ఖచ్చితత్వంతో కూడిన నకిలీ ప్రక్రియ మరియు అందుచేత ఉపయోగించిన మెటీరియల్ మొత్తంపై నిశిత నియంత్రణ అవసరం. • మెటల్ స్వేజింగ్ లేదా రేడియల్ ఫోర్జింగ్ : ఒక వర్క్ పీస్ చుట్టుకొలతతో డై మరియు ఫోర్జ్ చేయడం ద్వారా పని చేస్తుంది. ఇంటీరియర్ వర్క్ పీస్ జ్యామితిని నకిలీ చేయడానికి మాండ్రెల్ కూడా ఉపయోగించవచ్చు. స్వేజింగ్ ఆపరేషన్లో పని భాగం సాధారణంగా సెకనుకు అనేక స్ట్రోక్లను అందుకుంటుంది. స్వేజింగ్ ద్వారా ఉత్పత్తి చేయబడిన సాధారణ వస్తువులు పాయింటెడ్ టిప్ టూల్స్, టేపర్డ్ బార్లు, స్క్రూడ్రైవర్లు. • మెటల్ పియర్సింగ్: మేము ఈ ఆపరేషన్ను విడిభాగాల తయారీలో అదనపు ఆపరేషన్గా తరచుగా ఉపయోగిస్తాము. ఒక రంధ్రం లేదా కుహరం ద్వారా బద్దలు లేకుండా పని ముక్క ఉపరితలంపై కుట్లు సృష్టించబడుతుంది. రంధ్రం ద్వారా రంధ్రం చేసే డ్రిల్లింగ్ కంటే పియర్సింగ్ భిన్నంగా ఉంటుందని దయచేసి గమనించండి. • హాబింగ్ : కావలసిన జ్యామితితో ఒక పంచ్ వర్క్ పీస్లో నొక్కబడుతుంది మరియు కావలసిన ఆకారంతో ఒక కుహరాన్ని సృష్టిస్తుంది. మేము ఈ పంచ్ను HOB అని పిలుస్తాము. ఆపరేషన్ అధిక ఒత్తిళ్లను కలిగి ఉంటుంది మరియు చల్లని వద్ద నిర్వహించబడుతుంది. ఫలితంగా, పదార్థం చల్లగా పని చేస్తుంది మరియు గట్టిపడుతుంది. అందువల్ల ఈ ప్రక్రియ ఇతర తయారీ ప్రక్రియలకు అచ్చులు, డై మరియు కావిటీస్ తయారీకి చాలా అనుకూలంగా ఉంటుంది. హాబ్ను తయారు చేసిన తర్వాత, వాటిని ఒక్కొక్కటిగా మెషిన్ చేయాల్సిన అవసరం లేకుండానే అనేక సారూప్య కావిటీలను సులభంగా తయారు చేయవచ్చు. • రోల్ ఫోర్జింగ్ లేదా రోల్ ఫార్మింగ్ : మెటల్ భాగాన్ని ఆకృతి చేయడానికి రెండు వ్యతిరేక రోల్స్ ఉపయోగించబడతాయి. వర్క్ పీస్ రోల్స్లోకి మృదువుగా ఉంటుంది, రోల్స్ మలుపు తిరుగుతాయి మరియు పనిని గ్యాప్లోకి లాగుతాయి, ఆ పనిని రోల్స్ యొక్క గాడి భాగం ద్వారా అందించబడుతుంది మరియు సంపీడన శక్తులు పదార్థానికి కావలసిన ఆకారాన్ని ఇస్తాయి. ఇది రోలింగ్ ప్రక్రియ కాదు, నకిలీ ప్రక్రియ, ఎందుకంటే ఇది నిరంతర ఆపరేషన్ కంటే వివిక్తమైనది. రోల్స్ గ్రోవ్స్లోని జ్యామితి అవసరమైన ఆకారం మరియు జ్యామితికి పదార్థాన్ని నకిలీ చేస్తుంది. ఇది వేడిగా నిర్వహించబడుతుంది. నకిలీ ప్రక్రియ అయినందున ఇది అత్యుత్తమ యాంత్రిక లక్షణాలతో భాగాలను ఉత్పత్తి చేస్తుంది మరియు అందువల్ల మేము దీనిని manufacturing ఆటోమోటివ్ భాగాలైన షాఫ్ట్ల వంటి కఠినమైన పని వాతావరణంలో అసాధారణమైన ఓర్పును కలిగి ఉండటానికి ఉపయోగిస్తాము. • ఆర్బిటల్ ఫోర్జింగ్: వర్క్ పీస్ ఒక ఫోర్జింగ్ డై కేవిటీలో ఉంచబడుతుంది మరియు ఒక వంపుతిరిగిన అక్షం మీద తిరుగుతున్నప్పుడు కక్ష్య మార్గంలో ప్రయాణించే ఎగువ డై ద్వారా నకిలీ చేయబడుతుంది. ప్రతి విప్లవం వద్ద, ఎగువ డై మొత్తం వర్క్ పీస్కు సంపీడన శక్తులను ప్రయోగించడం పూర్తి చేస్తుంది. ఈ విప్లవాలను అనేక సార్లు పునరావృతం చేయడం ద్వారా, తగినంత ఫోర్జింగ్ జరుగుతుంది. ఈ తయారీ సాంకేతికత యొక్క ప్రయోజనాలు దాని తక్కువ శబ్దం ఆపరేషన్ మరియు తక్కువ బలాలు అవసరం. మరో మాటలో చెప్పాలంటే, చిన్న శక్తులతో ఒక అక్షం చుట్టూ భారీ డైని తిప్పవచ్చు, ఇది డైతో సంబంధంలో ఉన్న వర్క్ పీస్లోని ఒక విభాగంపై పెద్ద ఒత్తిడిని వర్తింపజేయవచ్చు. డిస్క్ లేదా శంఖు ఆకారపు భాగాలు కొన్నిసార్లు ఈ ప్రక్రియకు బాగా సరిపోతాయి. • రింగ్ ఫోర్జింగ్: మేము తరచుగా అతుకులు లేని రింగులను తయారు చేయడానికి ఉపయోగిస్తాము. స్టాక్ పొడవుగా కత్తిరించబడుతుంది, కలత చెందుతుంది మరియు కేంద్ర రంధ్రం సృష్టించడానికి అన్ని మార్గం గుండా కుట్టబడుతుంది. అప్పుడు అది ఒక మాండ్రెల్పై ఉంచబడుతుంది మరియు కావలసిన కొలతలు పొందే వరకు రింగ్ నెమ్మదిగా తిప్పబడినందున దానిని పైనుండి ఫోర్జింగ్ డై సుత్తితో కొడుతుంది. • రివెటింగ్: భాగాలను కలపడం కోసం ఒక సాధారణ ప్రక్రియ, భాగాల ద్వారా ముందుగా తయారు చేయబడిన రంధ్రాలలో చొప్పించిన నేరుగా మెటల్ ముక్కతో ప్రారంభమవుతుంది. ఆ తర్వాత లోహపు ముక్క యొక్క రెండు చివరలు ఎగువ మరియు దిగువ డై మధ్య జాయింట్ను పిండడం ద్వారా నకిలీ చేయబడతాయి. • కాయినింగ్ : మెకానికల్ ప్రెస్ ద్వారా నిర్వహించబడే మరొక ప్రసిద్ధ ప్రక్రియ, తక్కువ దూరం వరకు పెద్ద బలగాలను ప్రయోగించడం. లోహపు నాణేల ఉపరితలాలపై నకిలీ చేయబడిన చక్కటి వివరాల నుండి "కాయినింగ్" అనే పేరు వచ్చింది. ఇది చాలావరకు ఒక ఉత్పత్తికి పూర్తి చేసే ప్రక్రియ, ఈ వివరాలను వర్క్ పీస్కి బదిలీ చేసే డై ద్వారా వర్తించే పెద్ద శక్తి ఫలితంగా ఉపరితలాలపై చక్కటి వివరాలు పొందబడతాయి. • మెటల్ బాల్ ఫోర్జింగ్ : బాల్ బేరింగ్ల వంటి ఉత్పత్తులకు అధిక నాణ్యతతో ఖచ్చితంగా తయారు చేయబడిన మెటల్ బాల్స్ అవసరం. SKEW ROLLING అని పిలువబడే ఒక టెక్నిక్లో, స్టాక్ను రోల్స్లోకి నిరంతరంగా అందించడం వలన మేము నిరంతరం తిరిగే రెండు వ్యతిరేక రోల్లను ఉపయోగిస్తాము. రెండు రోల్స్ యొక్క ఒక చివర లోహ గోళాలు ఉత్పత్తిగా బయటకు వస్తాయి. మెటల్ బాల్ ఫోర్జింగ్ కోసం రెండవ పద్ధతి అచ్చు కుహరం యొక్క గోళాకార ఆకారాన్ని తీసుకొని వాటి మధ్య ఉంచిన మెటీరియల్ స్టాక్ను పిండి వేయడాన్ని ఉపయోగించడం. తరచుగా ఉత్పత్తి చేయబడిన బంతులు అధిక నాణ్యత గల ఉత్పత్తిగా మారడానికి ఫినిషింగ్ మరియు పాలిషింగ్ వంటి కొన్ని అదనపు దశలు అవసరమవుతాయి. • ఐసోథర్మల్ ఫోర్జింగ్ / హాట్ డై ఫోర్జింగ్ : ప్రయోజనం / ఖర్చు విలువ సమర్థించబడినప్పుడు మాత్రమే ఖరీదైన ప్రక్రియ నిర్వహించబడుతుంది. వర్క్ పీస్ మాదిరిగానే డైని దాదాపు అదే ఉష్ణోగ్రతకు వేడి చేసే హాట్ వర్కింగ్ ప్రాసెస్. డై మరియు పని రెండూ ఒకే ఉష్ణోగ్రతలో ఉండటం వలన, శీతలీకరణ ఉండదు మరియు మెటల్ యొక్క ప్రవాహ లక్షణాలు మెరుగుపడతాయి. నాసిరకం ఫోర్జిబిలిటీ మరియు మెటీరియల్స్ ఉన్న సూపర్ అల్లాయ్లు మరియు మెటీరియల్లకు ఈ ఆపరేషన్ బాగా సరిపోతుంది. యాంత్రిక లక్షణాలు చిన్న ఉష్ణోగ్రత ప్రవణతలు మరియు మార్పులకు చాలా సున్నితంగా ఉంటాయి. • మెటల్ సైజింగ్ : ఇది కోల్డ్ ఫినిషింగ్ ప్రక్రియ. శక్తి వర్తించే దిశను మినహాయించి అన్ని దిశలలో మెటీరియల్ ప్రవాహం అనియంత్రితమైనది. ఫలితంగా, చాలా మంచి ఉపరితల ముగింపు మరియు ఖచ్చితమైన కొలతలు పొందబడతాయి. • HIGH ఎనర్జీ రేట్ ఫోర్జింగ్: టెక్నిక్లో పిస్టన్ చేతికి జోడించబడిన పై అచ్చు ఉంటుంది, ఇది ఒక స్పార్క్ ప్లగ్ ద్వారా మండించబడిన ఇంధన-గాలి మిశ్రమం వేగంగా నెట్టబడుతుంది. ఇది కారు ఇంజిన్లోని పిస్టన్ల ఆపరేషన్ను పోలి ఉంటుంది. అచ్చు వర్క్ పీస్ను చాలా వేగంగా తాకుతుంది మరియు బ్యాక్ప్రెజర్ కారణంగా చాలా వేగంగా దాని అసలు స్థానానికి తిరిగి వస్తుంది. పని కొన్ని మిల్లీసెకన్లలో నకిలీ చేయబడుతుంది మరియు అందువల్ల పనిని చల్లబరచడానికి సమయం లేదు. ఇది చాలా ఉష్ణోగ్రత సెన్సిటివ్ మెకానికల్ లక్షణాలను కలిగి ఉండే హార్డ్ టు ఫోర్జ్ భాగాలకు ఉపయోగపడుతుంది. మరో మాటలో చెప్పాలంటే, ప్రక్రియ చాలా వేగంగా ఉంటుంది, భాగం అంతటా స్థిరమైన ఉష్ణోగ్రతలో ఏర్పడుతుంది మరియు అచ్చు/వర్క్ పీస్ ఇంటర్ఫేస్ల వద్ద ఉష్ణోగ్రత ప్రవణతలు ఉండవు. • DIE FORGINGలో, డైస్ అని పిలువబడే ప్రత్యేక ఆకారాలతో సరిపోలే రెండు ఉక్కు దిమ్మెల మధ్య మెటల్ కొట్టబడుతుంది. డైస్ల మధ్య లోహాన్ని కొట్టినప్పుడు, అది డైలోని ఆకారాల మాదిరిగానే ఉంటుంది. ఇది దాని తుది ఆకృతికి చేరుకున్నప్పుడు, అది చల్లబరచడానికి బయటకు తీయబడుతుంది. ఈ ప్రక్రియ ఖచ్చితమైన ఆకారంలో ఉండే బలమైన భాగాలను ఉత్పత్తి చేస్తుంది, అయితే ప్రత్యేకమైన డైస్ల కోసం పెద్ద పెట్టుబడి అవసరం. అప్సెట్ ఫోర్జింగ్ ఒక మెటల్ ముక్కను చదును చేయడం ద్వారా దాని వ్యాసాన్ని పెంచుతుంది. ఇది సాధారణంగా చిన్న భాగాలను తయారు చేయడానికి, ముఖ్యంగా బోల్ట్లు మరియు నెయిల్స్ వంటి ఫాస్టెనర్లపై హెడ్లను రూపొందించడానికి ఉపయోగిస్తారు. • పౌడర్ మెటలర్జీ / పౌడర్ ప్రాసెసింగ్: పేరు సూచించినట్లుగా, ఇది నిర్దిష్ట జ్యామితి మరియు ఆకారాల యొక్క ఘన భాగాలను పౌడర్ల నుండి తయారు చేయడానికి తయారీ ప్రక్రియలను కలిగి ఉంటుంది. ఈ ప్రయోజనం కోసం మెటల్ పౌడర్లను ఉపయోగిస్తే అది పౌడర్ మెటలర్జీ రాజ్యం మరియు నాన్-మెటల్ పౌడర్లను ఉపయోగిస్తే అది పౌడర్ ప్రాసెసింగ్. నొక్కడం మరియు సింటరింగ్ చేయడం ద్వారా పౌడర్ల నుండి ఘన భాగాలు ఉత్పత్తి చేయబడతాయి. POWDER PRESSING అనేది పౌడర్లను కావలసిన ఆకారాలలో కుదించడానికి ఉపయోగించబడుతుంది. మొదట, ప్రాథమిక పదార్థం భౌతికంగా పొడిగా ఉంటుంది, దానిని అనేక చిన్న వ్యక్తిగత కణాలుగా విభజిస్తుంది. పౌడర్ మిశ్రమం డైలో నింపబడుతుంది మరియు ఒక పంచ్ పౌడర్ వైపు కదులుతుంది మరియు దానిని కావలసిన ఆకారంలో కుదించబడుతుంది. ఎక్కువగా గది ఉష్ణోగ్రత వద్ద నిర్వహిస్తారు, పొడిని నొక్కడం ద్వారా ఒక ఘన భాగం లభిస్తుంది మరియు దానిని గ్రీన్ కాంపాక్ట్ అంటారు. బైండర్లు మరియు కందెనలు సాధారణంగా కాంపాక్టబిలిటీని పెంచడానికి ఉపయోగిస్తారు. మేము అనేక వేల టన్నుల సామర్థ్యంతో హైడ్రాలిక్ ప్రెస్లను ఉపయోగించి పౌడర్ ప్రెస్ను రూపొందించగల సామర్థ్యం కలిగి ఉన్నాము. అలాగే అత్యంత సంక్లిష్టమైన పార్ట్ జ్యామితి కోసం మేము వ్యతిరేక టాప్ & బాటమ్ పంచ్లతో డబుల్ యాక్షన్ ప్రెస్లను అలాగే బహుళ యాక్షన్ ప్రెస్లను కలిగి ఉన్నాము. అనేక పౌడర్ మెటలర్జీ / పౌడర్ ప్రాసెసింగ్ ప్లాంట్లకు ఒక ముఖ్యమైన సవాలుగా ఉన్న ఏకరూపత AGS-TECHకి పెద్ద సమస్య కాదు ఎందుకంటే చాలా సంవత్సరాలుగా ఇటువంటి భాగాలను కస్టమ్ తయారీలో మా విస్తృతమైన అనుభవం ఉంది. ఏకరూపత సవాలుగా ఉన్న మందమైన భాగాలతో కూడా మేము విజయం సాధించాము. మేము మీ ప్రాజెక్ట్కు కట్టుబడి ఉంటే, మేము మీ భాగాలను తయారు చేస్తాము. మేము ఏవైనా సంభావ్య ప్రమాదాలను చూసినట్లయితే, మేము మీకు in తెలియజేస్తాము అడ్వాన్స్. రెండవ దశ అయిన POWDER SINTERING, ఉష్ణోగ్రతను ఒక నిర్దిష్ట స్థాయికి పెంచడం మరియు ఆ స్థాయిలో ఉష్ణోగ్రతను నిర్దిష్ట సమయం వరకు నిర్వహించడం, తద్వారా నొక్కిన భాగంలోని పొడి కణాలు ఒకదానితో ఒకటి బంధించబడతాయి. ఇది చాలా బలమైన బంధాలకు దారితీస్తుంది మరియు పని భాగాన్ని బలోపేతం చేస్తుంది. సింటరింగ్ పొడి యొక్క ద్రవీభవన ఉష్ణోగ్రతకు దగ్గరగా జరుగుతుంది. సింటరింగ్ సమయంలో సంకోచం సంభవిస్తుంది, పదార్థ బలం, సాంద్రత, డక్టిలిటీ, ఉష్ణ వాహకత, విద్యుత్ వాహకత పెరుగుతుంది. మేము సింటరింగ్ కోసం బ్యాచ్ మరియు నిరంతర ఫర్నేస్లను కలిగి ఉన్నాము. మేము ఉత్పత్తి చేసే భాగాల సచ్ఛిద్రత స్థాయిని సర్దుబాటు చేయడం మా సామర్థ్యాలలో ఒకటి. ఉదాహరణకు, మేము భాగాలను కొంత వరకు పోరస్గా ఉంచడం ద్వారా మెటల్ ఫిల్టర్లను ఉత్పత్తి చేయగలము. IMPREGNATION అనే టెక్నిక్ని ఉపయోగించి, మనం లోహంలోని రంధ్రాలను నూనె వంటి ద్రవంతో నింపుతాము. మేము ఉదాహరణకు స్వీయ కందెన చమురు కలిపిన బేరింగ్లు ఉత్పత్తి చేస్తాము. ఇన్ఫిల్ట్రేషన్ ప్రక్రియలో మనం ఒక లోహపు రంధ్రాలను ఆధార పదార్థం కంటే తక్కువ ద్రవీభవన స్థానం ఉన్న మరొక లోహంతో నింపుతాము. మిశ్రమం రెండు లోహాల ద్రవీభవన ఉష్ణోగ్రతల మధ్య ఉష్ణోగ్రతకు వేడి చేయబడుతుంది. ఫలితంగా కొన్ని ప్రత్యేక లక్షణాలను పొందవచ్చు. ప్రత్యేక లక్షణాలు లేదా లక్షణాలను పొందవలసి వచ్చినప్పుడు లేదా తక్కువ ప్రాసెస్ దశలతో భాగాన్ని తయారు చేయగలిగినప్పుడు మేము పౌడర్ తయారు చేసిన భాగాలపై మ్యాచింగ్ మరియు ఫోర్జింగ్ వంటి ద్వితీయ కార్యకలాపాలను కూడా తరచుగా చేస్తాము. ఐసోస్టాటిక్ ప్రెస్సింగ్: ఈ ప్రక్రియలో భాగాన్ని కుదించడానికి ద్రవ పీడనం ఉపయోగించబడుతుంది. మెటల్ పౌడర్లను మూసివున్న సౌకర్యవంతమైన కంటైనర్తో తయారు చేసిన అచ్చులో ఉంచుతారు. ఐసోస్టాటిక్ నొక్కడంలో, సాంప్రదాయిక నొక్కడంలో కనిపించే అక్షసంబంధ పీడనానికి విరుద్ధంగా, చుట్టుపక్కల నుండి ఒత్తిడి వర్తించబడుతుంది. ఐసోస్టాటిక్ నొక్కడం యొక్క ప్రయోజనాలు భాగం లోపల ఏకరీతి సాంద్రత, ప్రత్యేకించి పెద్ద లేదా మందమైన భాగాలకు, ఉన్నతమైన లక్షణాలు. దీని ప్రతికూలత దీర్ఘ చక్రాల సమయాలు మరియు సాపేక్షంగా తక్కువ రేఖాగణిత ఖచ్చితత్వం. కోల్డ్ ఐసోస్టాటిక్ ప్రెస్సింగ్ గది ఉష్ణోగ్రత వద్ద నిర్వహించబడుతుంది మరియు సౌకర్యవంతమైన అచ్చు రబ్బరు, PVC లేదా యురేథేన్ లేదా సారూప్య పదార్థాలతో తయారు చేయబడుతుంది. ఒత్తిడి మరియు కుదించడానికి ఉపయోగించే ద్రవం నూనె లేదా నీరు. ఆకుపచ్చ కాంపాక్ట్ యొక్క సాంప్రదాయిక సింటరింగ్ దీనిని అనుసరిస్తుంది. మరోవైపు హాట్ ఐసోస్టాటిక్ నొక్కడం అధిక ఉష్ణోగ్రతల వద్ద నిర్వహించబడుతుంది మరియు అచ్చు పదార్థం ఉష్ణోగ్రతలను నిరోధించే తగినంత అధిక ద్రవీభవన స్థానం కలిగిన షీట్ మెటల్ లేదా సిరామిక్. ఒత్తిడి కలిగించే ద్రవం సాధారణంగా జడ వాయువు. నొక్కడం మరియు సింటరింగ్ కార్యకలాపాలు ఒక దశలో నిర్వహించబడతాయి. సచ్ఛిద్రత దాదాపు పూర్తిగా తొలగించబడింది, ఏకరీతి grain నిర్మాణం పొందబడింది. హాట్ ఐసోస్టాటిక్ నొక్కడం యొక్క ప్రయోజనం ఏమిటంటే, ఇది కాస్టింగ్ మరియు ఫోర్జింగ్తో పోల్చదగిన భాగాలను ఉత్పత్తి చేయగలదు, అయితే కాస్టింగ్ మరియు ఫోర్జింగ్కు అనుకూలం కాని పదార్థాలను ఉపయోగించడం సాధ్యమవుతుంది. హాట్ ఐసోస్టాటిక్ నొక్కడం యొక్క ప్రతికూలత దాని అధిక చక్ర సమయం మరియు అందువలన ఖర్చు. ఇది తక్కువ వాల్యూమ్ యొక్క క్లిష్టమైన భాగాలకు అనుకూలంగా ఉంటుంది. మెటల్ ఇంజెక్షన్ మోల్డింగ్: సన్నని గోడలు మరియు వివరణాత్మక జ్యామితితో సంక్లిష్ట భాగాలను ఉత్పత్తి చేయడానికి చాలా సరిఅయిన ప్రక్రియ. చిన్న భాగాలకు అత్యంత అనుకూలమైనది. పొడులు మరియు పాలీమర్ బైండర్లను కలిపి, వేడి చేసి, అచ్చులోకి ఇంజెక్ట్ చేస్తారు. పాలిమర్ బైండర్ పొడి కణాల ఉపరితలాలను పూస్తుంది. మౌల్డింగ్ తర్వాత, బైండర్ ఒక ద్రావకం ఉపయోగించి కరిగిన తక్కువ ఉష్ణోగ్రత తాపన ద్వారా తొలగించబడుతుంది. రోల్ కంపాక్షన్ / పౌడర్ రోలింగ్: పొడులు నిరంతర స్ట్రిప్స్ లేదా షీట్ను ఉత్పత్తి చేయడానికి ఉపయోగిస్తారు. పౌడర్ ఫీడర్ నుండి ఫీడ్ చేయబడుతుంది మరియు షీట్ లేదా స్ట్రిప్స్లో రెండు తిరిగే రోల్స్ ద్వారా కుదించబడుతుంది. ఆపరేషన్ చల్లగా జరుగుతుంది. షీట్ సింటరింగ్ ఫర్నేస్లోకి తీసుకువెళతారు. సింటరింగ్ ప్రక్రియ రెండవసారి పునరావృతం కావచ్చు. పౌడర్ ఎక్స్ట్రూషన్: పెద్ద పొడవు మరియు వ్యాసం నిష్పత్తులు కలిగిన భాగాలు ఒక సన్నని షీట్ మెటల్ కంటైనర్ను పొడితో వెలికితీయడం ద్వారా తయారు చేయబడతాయి. లూస్ సింటరింగ్ : పేరు సూచించినట్లుగా, ఇది ఒత్తిడి లేని కుదింపు మరియు సింటరింగ్ పద్ధతి, మెటల్ ఫిల్టర్ల వంటి చాలా పోరస్ భాగాలను ఉత్పత్తి చేయడానికి అనుకూలంగా ఉంటుంది. పౌడర్ కుదించబడకుండా అచ్చు కుహరంలోకి అందించబడుతుంది. లూస్ సింటరింగ్ : పేరు సూచించినట్లుగా, ఇది ఒత్తిడి లేని కుదింపు మరియు సింటరింగ్ పద్ధతి, మెటల్ ఫిల్టర్ల వంటి చాలా పోరస్ భాగాలను ఉత్పత్తి చేయడానికి అనుకూలంగా ఉంటుంది. పౌడర్ కుదించబడకుండా అచ్చు కుహరంలోకి అందించబడుతుంది. SPARK SINTERING : పౌడర్ రెండు వ్యతిరేక పంచ్ల ద్వారా అచ్చులో కుదించబడుతుంది మరియు పంచ్కు అధిక శక్తి విద్యుత్ ప్రవాహాన్ని వర్తించబడుతుంది మరియు వాటి మధ్య శాండ్విచ్ చేయబడిన కాంపాక్ట్ పౌడర్ గుండా వెళుతుంది. అధిక విద్యుత్తు పొడి కణాల నుండి ఉపరితల పొరలను కాల్చివేస్తుంది మరియు ఉత్పన్నమైన వేడితో వాటిని సింటర్స్ చేస్తుంది. ప్రక్రియ వేగంగా ఉంటుంది ఎందుకంటే వేడిని బయటి నుండి వర్తించదు, బదులుగా అది అచ్చు లోపల నుండి ఉత్పత్తి చేయబడుతుంది. వేడి నొక్కడం: అధిక ఉష్ణోగ్రతలను తట్టుకోగల అచ్చులో పౌడర్లను ఒకే దశలో ఒత్తడం మరియు సిన్టర్ చేయడం జరుగుతుంది. డై కాంపాక్ట్ అయినప్పుడు పొడి వేడి దానికి వర్తించబడుతుంది. ఈ పద్ధతి ద్వారా సాధించిన మంచి ఖచ్చితత్వాలు మరియు యాంత్రిక లక్షణాలు ఆకర్షణీయమైన ఎంపికగా చేస్తాయి. గ్రాఫైట్ వంటి అచ్చు పదార్థాలను ఉపయోగించడం ద్వారా వక్రీభవన లోహాలను కూడా ప్రాసెస్ చేయవచ్చు. CLICK Product Finder-Locator Service మునుపటి మెను
- Plastic Rubber Metal Extrusions, Extrusion Dies, Aluminum Extruding
Plastic Rubber Metal Extrusions, Extrusion Dies, Aluminum Extruding, Pipe Tube Forming, Plastic Profiles, Metal Profiles Manufacturing, PVC at AGS-TECH Inc. ఎక్స్ట్రూషన్లు, ఎక్స్ట్రూడెడ్ ప్రొడక్ట్లు, ఎక్స్ట్రూడేట్స్ మేము సింక్లు, పైపులు మరియు హీట్ సెక్షనల్ ప్రొఫైల్తో స్థిరమైన క్రాస్ సెక్షనల్ ప్రొఫైల్తో ఉత్పత్తులను తయారు చేయడానికి EXTRUSION processని ఉపయోగిస్తాము. అనేక పదార్ధాలను వెలికితీసినప్పటికీ, మా అత్యంత సాధారణ ఎక్స్ట్రాషన్లు మెటల్, పాలిమర్లు / ప్లాస్టిక్, సిరామిక్తో తయారు చేయబడతాయి, వీటిని చల్లని, వెచ్చని లేదా వేడి ఎక్స్ట్రాషన్ పద్ధతి ద్వారా పొందవచ్చు. ఎక్స్ట్రూడెడ్ భాగాలను బహువచనం అయితే ఎక్స్ట్రూడేట్ లేదా ఎక్స్ట్రూడేట్ అని పిలుస్తాము. మేము నిర్వహించే ప్రక్రియ యొక్క కొన్ని ప్రత్యేక సంస్కరణలు ఓవర్జాకెటింగ్, కోఎక్స్ట్రూషన్ మరియు కాంపౌండ్ ఎక్స్ట్రాషన్. మీరు ఇక్కడ క్లిక్ చేయాలని మేము సిఫార్సు చేస్తున్నాము to AGS-TECH ఇంక్ ద్వారా మెటల్ సిరామిక్ మరియు ప్లాస్టిక్ ఎక్స్ట్రూషన్ ప్రాసెస్ల మా స్కీమాటిక్ ఇలస్ట్రేషన్లను డౌన్లోడ్ చేయండి. మేము దిగువ మీకు అందిస్తున్న సమాచారాన్ని బాగా అర్థం చేసుకోవడంలో ఇది మీకు సహాయం చేస్తుంది. ఎక్స్ట్రూషన్లో ఎక్స్ట్రూడ్ చేయాల్సిన పదార్థం కావలసిన క్రాస్-సెక్షనల్ ప్రొఫైల్ను కలిగి ఉన్న డై ద్వారా నెట్టబడుతుంది లేదా డ్రా చేయబడుతుంది. అద్భుతమైన ఉపరితల ముగింపుతో సంక్లిష్టమైన క్రాస్-సెక్షన్లను తయారు చేయడానికి మరియు పెళుసు పదార్థంపై పని చేయడానికి ఈ ప్రక్రియను ఉపయోగించవచ్చు. ఈ ప్రక్రియను ఉపయోగించి ఎవరైనా ఎంత పొడవు భాగాలనైనా ఉత్పత్తి చేయవచ్చు. ప్రక్రియ దశలను సులభతరం చేయడానికి: 1.) వెచ్చని లేదా వేడి ఎక్స్ట్రాషన్లలో పదార్థం వేడి చేయబడుతుంది మరియు ప్రెస్లోని కంటైనర్లో లోడ్ చేయబడుతుంది. పదార్థం నొక్కడం మరియు డై నుండి బయటకు నెట్టబడుతుంది. 2.) ఉత్పత్తి చేయబడిన ఎక్స్ట్రూడేట్ స్ట్రెయిటెనింగ్, హీట్ ట్రీట్మెంట్ లేదా కోల్డ్ దాని లక్షణాలను పెంచడం కోసం విస్తరించబడుతుంది. మరోవైపు COLD EXTRUSION గది ఉష్ణోగ్రత వద్ద జరుగుతుంది. ఇది గది ఉష్ణోగ్రత వద్ద జరుగుతుంది మరియు తక్కువ ఉపరితల బలం, తక్కువ ఆక్సీకరణ, ఆక్సీకరణం యొక్క మంచి ప్రయోజనాలను కలిగి ఉంటుంది. WARM EXTRUSION గది ఉష్ణోగ్రత కంటే ఎక్కువగా ప్రదర్శించబడుతుంది కానీ రీక్రిస్టలైజేషన్ పాయింట్ కంటే తక్కువగా ఉంటుంది. ఇది అవసరమైన శక్తులు, డక్టిలిటీ మరియు మెటీరియల్ ప్రాపర్టీల కోసం రాజీ మరియు బ్యాలెన్స్ను అందిస్తుంది మరియు కనుక ఇది కొన్ని అప్లికేషన్లకు ఎంపిక. HOT EXTRUSION మెటీరియల్ యొక్క రీక్రిస్టలైజేషన్ ఉష్ణోగ్రత కంటే ఎక్కువగా ఉంటుంది. ఈ విధంగా డై ద్వారా పదార్థాన్ని నెట్టడం సులభం. అయితే పరికరాల ధర ఎక్కువగా ఉంటుంది. ఎక్స్ట్రూడెడ్ ప్రొఫైల్ ఎంత క్లిష్టంగా ఉంటే, డై (టూలింగ్) మరింత ఖరీదైనది మరియు ఉత్పత్తి రేటు తక్కువగా ఉంటుంది. డై క్రాస్ సెక్షన్లు అలాగే మందాలు వెలికితీసే పదార్థంపై ఆధారపడి ఉండే పరిమితులను కలిగి ఉంటాయి. ఎక్స్ట్రాషన్ డైస్లోని పదునైన మూలలు ఎల్లప్పుడూ అవాంఛనీయమైనవి మరియు అవసరమైతే తప్ప నివారించబడతాయి. వెలికితీసే పదార్థం ప్రకారం, మేము అందిస్తున్నాము: • METAL EXTRUSIONS : మనం ఎక్కువగా ఉత్పత్తి చేసేవి అల్యూమినియం, ఇత్తడి, జింక్, రాగి, ఉక్కు, టైటానియం, మెగ్నీషియం • PLASTIC EXTRUSION : ప్లాస్టిక్ కరిగించి నిరంతర ప్రొఫైల్గా ఏర్పడుతుంది. ప్రాసెస్ చేయబడిన మా సాధారణ పదార్థాలు పాలిథిలిన్, నైలాన్, పాలీస్టైరిన్, పాలీ వినైల్ క్లోరైడ్, పాలీప్రొఫైలిన్, ABS ప్లాస్టిక్, పాలికార్బోనేట్, యాక్రిలిక్. మేము తయారు చేసే సాధారణ ఉత్పత్తులలో పైపులు మరియు గొట్టాలు, ప్లాస్టిక్ ఫ్రేమ్లు ఉన్నాయి. ప్రక్రియలో చిన్న ప్లాస్టిక్ పూసలు / రెసిన్ గురుత్వాకర్షణ తొట్టి నుండి వెలికితీత యంత్రం యొక్క బారెల్లోకి అందించబడుతుంది. ఉత్పత్తికి అవసరమైన లక్షణాలు మరియు లక్షణాలను అందించడానికి తరచుగా మేము రంగులు లేదా ఇతర సంకలనాలను హాప్పర్లో కలుపుతాము. వేడిచేసిన బారెల్లోకి ప్రవేశించే పదార్థం తిరిగే స్క్రూ ద్వారా కరిగిన ప్లాస్టిక్లోని కలుషితాలను తొలగించడం కోసం బారెల్ను చివరిలో వదిలి స్క్రీన్ ప్యాక్ ద్వారా తరలించడానికి బలవంతం చేయబడుతుంది. స్క్రీన్ ప్యాక్ను దాటిన తర్వాత ప్లాస్టిక్ ఎక్స్ట్రాషన్ డైలోకి ప్రవేశిస్తుంది. డై కదిలే మృదువైన ప్లాస్టిక్కు దాని ప్రొఫైల్ ఆకారాన్ని ఇస్తుంది. ఇప్పుడు ఎక్స్ట్రూడేట్ శీతలీకరణ కోసం నీటి స్నానం ద్వారా వెళుతుంది. AGS-TECH Inc. అనేక సంవత్సరాలుగా ఉపయోగిస్తున్న ఇతర పద్ధతులు: • PIPE & TUBING EXTRUSION : ప్లాస్టిక్ పైపులు మరియు ట్యూబ్లు ఏర్పడతాయి, ప్లాస్టిక్లను గుండ్రంగా షేపింగ్ డై ద్వారా బయటకు తీసి నీటి స్నానంలో చల్లబరిచి, ఆపై పొడవుగా కత్తిరించడం లేదా కాయిల్డ్/స్పూల్ చేయడం. క్లియర్ లేదా రంగు, చారలు, సింగిల్ లేదా డ్యూయల్ వాల్, ఫ్లెక్సిబుల్ లేదా రిజిడ్, PE, PP, పాలియురేతేన్, PVC, నైలాన్, PC, సిలికాన్, వినైల్ లేదా మన దగ్గర అన్నీ ఉన్నాయి. మేము నిల్వ చేసిన ట్యూబ్లతో పాటు మీ స్పెసిఫికేషన్ల ప్రకారం ఉత్పత్తి చేయగల సామర్థ్యాన్ని కలిగి ఉన్నాము. AGS-TECH వైద్య, విద్యుత్ & ఎలక్ట్రానిక్, పారిశ్రామిక మరియు ఇతర అనువర్తనాల కోసం FDA, UL మరియు LE అవసరాలకు గొట్టాలను తయారు చేస్తుంది. • ఓవర్జాకెటింగ్ / ఓవర్ జాకెటింగ్ EXTRUSION : ఈ సాంకేతికత ఇప్పటికే ఉన్న వైర్ లేదా కేబుల్పై ప్లాస్టిక్ బయటి పొరను వర్తింపజేస్తుంది. మా ఇన్సులేషన్ వైర్లు ఈ పద్ధతిలో తయారు చేయబడతాయి. • COEXTRUSION : మెటీరియల్ యొక్క బహుళ పొరలు ఏకకాలంలో వెలికితీయబడతాయి. బహుళ పొరలు బహుళ ఎక్స్ట్రూడర్ల ద్వారా పంపిణీ చేయబడతాయి. కస్టమర్ స్పెసిఫికేషన్లకు అనుగుణంగా వివిధ లేయర్ మందాలను సర్దుబాటు చేయవచ్చు. ఈ ప్రక్రియ ఉత్పత్తిలో విభిన్న కార్యాచరణను కలిగి ఉన్న బహుళ పాలిమర్లను ఉపయోగించడం సాధ్యం చేస్తుంది. ఫలితంగా, మీరు అనేక రకాలైన ప్రాపర్టీలను ఆప్టిమైజ్ చేయవచ్చు. • కాంపౌండ్ ఎక్స్ట్రూషన్: ప్లాస్టిక్ సమ్మేళనాన్ని పొందేందుకు ఒకే లేదా బహుళ పాలిమర్లను సంకలితాలతో కలుపుతారు. మా ట్విన్-స్క్రూ ఎక్స్ట్రూడర్లు సమ్మేళనం ఎక్స్ట్రూషన్లను ఉత్పత్తి చేస్తాయి. మెటల్ అచ్చులతో పోలిస్తే ఎక్స్ట్రూషన్ డైస్ సాధారణంగా చౌకగా ఉంటాయి. మీరు అల్యూమినియం వెలికితీసే చిన్న లేదా మీడియం సైజు ఎక్స్ట్రూషన్ డై కోసం కొన్ని వేల డాలర్ల కంటే ఎక్కువ చెల్లిస్తున్నట్లయితే, మీరు బహుశా చాలా ఎక్కువ చెల్లిస్తున్నారు. మీ అప్లికేషన్కు ఏ టెక్నిక్ అత్యంత ఖర్చుతో కూడుకున్నది, వేగవంతమైనది మరియు అత్యంత అనుకూలమైనదిగా నిర్ణయించడంలో మేము నిపుణులు. కొన్నిసార్లు ఒక భాగాన్ని వెలికితీసి, ఆపై మ్యాచింగ్ చేయడం వల్ల మీకు చాలా నగదు ఆదా అవుతుంది. దృఢమైన నిర్ణయం తీసుకునే ముందు, ముందుగా మా అభిప్రాయాన్ని అడగండి. మేము చాలా మంది కస్టమర్లు సరైన నిర్ణయాలు తీసుకోవడంలో సహాయం చేసాము. విస్తృతంగా ఉపయోగించే కొన్ని మెటల్ ఎక్స్ట్రాషన్ల కోసం, మీరు దిగువన ఉన్న రంగుల వచనంపై క్లిక్ చేయడం ద్వారా మా బ్రోచర్లు మరియు కేటలాగ్లను డౌన్లోడ్ చేసుకోవచ్చు. ఇది మీ అవసరాలను తీర్చే ఆఫ్-షెల్ఫ్ ఉత్పత్తి అయితే, అది మరింత పొదుపుగా ఉంటుంది. మా మెడికల్ ట్యూబ్ మరియు పైప్ ఎక్స్ట్రాషన్ సామర్థ్యాలను డౌన్లోడ్ చేయండి మా ఎక్స్ట్రూడెడ్ హీట్ సింక్లను డౌన్లోడ్ చేయండి • EXTRUSIONS కోసం సెకండరీ తయారీ & ఫ్యాబ్రికేషన్ ప్రక్రియలు: ఎక్స్ట్రూడెడ్ ఉత్పత్తుల కోసం మేము అందించే విలువ జోడించిన ప్రక్రియలలో ఇవి ఉన్నాయి: -కస్టమ్ ట్యూబ్ & పైపు బెండింగ్, ఫార్మింగ్ మరియు షేపింగ్, ట్యూబ్ కటాఫ్, ట్యూబ్ ఎండ్ ఫార్మింగ్, ట్యూబ్ కాయిలింగ్, మ్యాచింగ్ మరియు ఫినిషింగ్, హోల్ డ్రిల్లింగ్ & పియర్సింగ్ & పంచింగ్, -కస్టమ్ పైపు మరియు ట్యూబ్ అసెంబ్లీలు, గొట్టపు అసెంబ్లీ, వెల్డింగ్, బ్రేజింగ్ మరియు టంకం -కస్టమ్ ఎక్స్ట్రాషన్ బెండింగ్, ఫార్మింగ్ మరియు షేపింగ్ -క్లీనింగ్, డీగ్రేసింగ్, పిక్లింగ్, పాసివేషన్, పాలిషింగ్, యానోడైజింగ్, ప్లేటింగ్, పెయింటింగ్, హీట్ ట్రీటింగ్, ఎనియలింగ్ మరియు గట్టిపడటం, మార్కింగ్, చెక్కడం మరియు లేబులింగ్, కస్టమ్ ప్యాకేజింగ్. CLICK Product Finder-Locator Service ముందు పేజి
- Casting and Machined Parts, CNC Manufacturing, Milling, Turning, Swiss
Casting and Machined Parts, CNC Manufacturing, Milling, Turning, Swiss Type Machining, Die Casting, Investment Casting, Lost Foam Cast Parts from AGS-TECH Inc. కాస్టింగ్ మరియు మ్యాచింగ్ మా కస్టమ్ కాస్టింగ్ మరియు మ్యాచింగ్ టెక్నిక్లు ఖర్చు చేయదగినవి మరియు ఖర్చు చేయలేని కాస్టింగ్లు, ఫెర్రస్ మరియు నాన్ ఫెర్రస్ కాస్టింగ్, ఇసుక, డై, సెంట్రిఫ్యూగల్, కంటిన్యూస్, సిరామిక్ మోల్డ్, ఇన్వెస్ట్మెంట్, లాస్ట్ ఫోమ్, నియర్-నెట్-షేప్, శాశ్వత అచ్చు (గ్రావిటీ డై కాస్టింగ్), ప్లాస్టర్ అచ్చు (ప్లాస్టర్ కాస్టింగ్) మరియు షెల్ కాస్టింగ్లు, సాంప్రదాయిక అలాగే CNC పరికరాలను ఉపయోగించి మిల్లింగ్ మరియు టర్నింగ్ ద్వారా ఉత్పత్తి చేయబడిన యంత్ర భాగాలు, అధిక నిర్గమాంశ చవకైన చిన్న ఖచ్చితత్వ భాగాల కోసం స్విస్ రకం మ్యాచింగ్, ఫాస్టెనర్ల కోసం స్క్రూ మ్యాచింగ్, సాంప్రదాయేతర మ్యాచింగ్. దయచేసి లోహాలు మరియు లోహ మిశ్రమాలతో పాటు, మేము సిరామిక్, గాజు మరియు ప్లాస్టిక్ భాగాలను మెషిన్ చేస్తాము, అలాగే కొన్ని సందర్భాల్లో అచ్చును తయారు చేయడం ఆకర్షణీయంగా లేనప్పుడు లేదా ఎంపిక కానప్పుడు. ప్లాస్టిక్లు మరియు రబ్బరు బహుమతులు వాటి మృదుత్వం, దృఢత్వం మొదలైన వాటి కారణంగా పాలీమర్ మెటీరియల్ల మ్యాచింగ్కు ప్రత్యేకమైన అనుభవం అవసరం. సిరామిక్ మరియు గ్లాస్ మ్యాచింగ్ కోసం, దయచేసి నాన్ కన్వెన్షనల్ ఫ్యాబ్రికేషన్పై మా పేజీని చూడండి. AGS-TECH Inc. తేలికైన మరియు భారీ కాస్టింగ్లను తయారు చేస్తుంది మరియు సరఫరా చేస్తుంది. మేము బాయిలర్లు, ఉష్ణ వినిమాయకాలు, ఆటోమొబైల్స్, మైక్రోమోటర్లు, గాలి టర్బైన్లు, ఆహార ప్యాకేజింగ్ పరికరాలు మరియు మరిన్నింటి కోసం మెటల్ కాస్టింగ్లు మరియు యంత్ర భాగాలను సరఫరా చేస్తున్నాము. మీరు ఇక్కడ క్లిక్ చేయాలని మేము సిఫార్సు చేస్తున్నాము to AGS-TECH ఇంక్ ద్వారా మ్యాచింగ్ మరియు కాస్టింగ్ ప్రక్రియల యొక్క మా స్కీమాటిక్ ఇలస్ట్రేషన్లను డౌన్లోడ్ చేయండి. మేము దిగువ మీకు అందిస్తున్న సమాచారాన్ని బాగా అర్థం చేసుకోవడంలో ఇది మీకు సహాయం చేస్తుంది. మేము అందించే వివిధ పద్ధతుల్లో కొన్నింటిని వివరంగా చూద్దాం: • ఎక్స్పెండబుల్ మోల్డ్ కాస్టింగ్ : ఈ విస్తృత వర్గం తాత్కాలిక మరియు పునర్వినియోగం కాని అచ్చులను కలిగి ఉన్న పద్ధతులను సూచిస్తుంది. ఉదాహరణలు ఇసుక, ప్లాస్టర్, షెల్, పెట్టుబడి (లాస్ట్-వాక్స్ అని కూడా పిలుస్తారు) మరియు ప్లాస్టర్ కాస్టింగ్. • ఇసుక తారాగణం : ఇసుకను అచ్చు పదార్థంగా ఉపయోగించే ప్రక్రియ. చాలా పాత పద్ధతి మరియు ఇప్పటికీ చాలా ప్రజాదరణ పొందింది, ఈ సాంకేతికత ద్వారా ఉత్పత్తి చేయబడిన మెజారిటీ మెటల్ కాస్టింగ్లు తయారు చేయబడ్డాయి. తక్కువ పరిమాణంలో ఉత్పత్తిలో కూడా తక్కువ ఖర్చు. చిన్న మరియు పెద్ద భాగాల తయారీకి అనుకూలం. చాలా తక్కువ పెట్టుబడితో రోజులు లేదా వారాలలో భాగాలను తయారు చేయడానికి సాంకేతికతను ఉపయోగించవచ్చు. తేమతో కూడిన ఇసుక మట్టి, బైండర్లు లేదా ప్రత్యేక నూనెలను ఉపయోగించి బంధించబడుతుంది. ఇసుక సాధారణంగా అచ్చు పెట్టెలలో ఉంటుంది మరియు నమూనాల చుట్టూ ఇసుకను కుదించడం ద్వారా కుహరం & గేట్ వ్యవస్థ సృష్టించబడుతుంది. ప్రక్రియలు: 1.) అచ్చును తయారు చేయడానికి ఇసుకలో నమూనాను ఉంచడం 2.) గేటింగ్ వ్యవస్థలో మోడల్ మరియు ఇసుకను చేర్చడం 3.) మోడల్ యొక్క తొలగింపు 4.) కరిగిన లోహంతో అచ్చు కుహరం నింపడం 5.) మెటల్ యొక్క శీతలీకరణ 6.) ఇసుక అచ్చును బద్దలు కొట్టడం మరియు కాస్టింగ్ యొక్క తొలగింపు • ప్లాస్టర్ మోల్డ్ కాస్టింగ్ : ఇసుక కాస్టింగ్ లాగానే, ఇసుకకు బదులుగా ప్లాస్టర్ ఆఫ్ పారిస్ అచ్చు పదార్థంగా ఉపయోగించబడుతోంది. ఇసుక కాస్టింగ్ మరియు చవకైన తక్కువ ఉత్పత్తి ప్రధాన సమయాలు. మంచి డైమెన్షనల్ టాలరెన్స్ మరియు ఉపరితల ముగింపు. దీని ప్రధాన ప్రతికూలత ఏమిటంటే ఇది అల్యూమినియం మరియు జింక్ వంటి తక్కువ మెల్టింగ్ పాయింట్ లోహాలతో మాత్రమే ఉపయోగించబడుతుంది. • షెల్ మోల్డ్ కాస్టింగ్ : ఇసుక కాస్టింగ్ని కూడా పోలి ఉంటుంది. ఇసుక కాస్టింగ్ ప్రక్రియలో వలె ఇసుకతో నిండిన ఫ్లాస్క్కు బదులుగా గట్టిపడిన ఇసుక షెల్ మరియు థర్మోసెట్టింగ్ రెసిన్ బైండర్ ద్వారా పొందిన అచ్చు కుహరం. ఇసుకతో వేయడానికి అనువైన దాదాపు ఏదైనా లోహాన్ని షెల్ మౌల్డింగ్ ద్వారా వేయవచ్చు. ప్రక్రియను ఇలా సంగ్రహించవచ్చు: 1.) షెల్ అచ్చు తయారీ. ఇసుక కాస్టింగ్లో ఉపయోగించే ఇసుకతో పోల్చినప్పుడు ఉపయోగించిన ఇసుక చాలా చిన్న ధాన్యం పరిమాణంలో ఉంటుంది. చక్కటి ఇసుకను థర్మోసెట్టింగ్ రెసిన్తో కలుపుతారు. షెల్ యొక్క తొలగింపును సులభతరం చేయడానికి మెటల్ నమూనా ఒక విడిపోయే ఏజెంట్తో పూత పూయబడింది. ఆ తర్వాత మెటల్ నమూనా వేడి చేయబడుతుంది మరియు ఇసుక మిశ్రమం రంధ్రము చేయబడుతుంది లేదా వేడి కాస్టింగ్ నమూనాపైకి ఎగిరిపోతుంది. నమూనా యొక్క ఉపరితలంపై సన్నని షెల్ ఏర్పడుతుంది. ఈ షెల్ యొక్క మందం ఇసుక రెసిన్ మిశ్రమం లోహ నమూనాతో సంబంధంలో ఉన్న సమయాన్ని మార్చడం ద్వారా సర్దుబాటు చేయబడుతుంది. వదులుగా ఉన్న ఇసుక తరువాత షెల్ కప్పబడిన నమూనాతో తొలగించబడుతుంది. 2.) తరువాత, షెల్ మరియు నమూనా ఓవెన్లో వేడి చేయబడతాయి, తద్వారా షెల్ గట్టిపడుతుంది. గట్టిపడటం పూర్తయిన తర్వాత, నమూనాలో నిర్మించిన పిన్లను ఉపయోగించి షెల్ నమూనా నుండి బయటకు తీయబడుతుంది. 3.) అటువంటి రెండు గుండ్లు అతుక్కొని లేదా బిగించడం ద్వారా ఒకదానితో ఒకటి సమీకరించబడతాయి మరియు పూర్తి అచ్చును తయారు చేస్తాయి. ఇప్పుడు షెల్ అచ్చు ఒక కంటైనర్లోకి చొప్పించబడింది, దీనిలో కాస్టింగ్ ప్రక్రియలో ఇసుక లేదా మెటల్ షాట్ మద్దతు ఇవ్వబడుతుంది. 4.) ఇప్పుడు వేడి లోహాన్ని షెల్ అచ్చులో పోయవచ్చు. షెల్ కాస్టింగ్ యొక్క ప్రయోజనాలు చాలా మంచి ఉపరితల ముగింపుతో కూడిన ఉత్పత్తులు, అధిక డైమెన్షనల్ ఖచ్చితత్వంతో సంక్లిష్ట భాగాలను తయారు చేసే అవకాశం, ప్రక్రియను ఆటోమేట్ చేయడం సులభం, పెద్ద వాల్యూమ్ ఉత్పత్తికి ఆర్థికంగా ఉంటుంది. ప్రతికూలతలు ఏమిటంటే, కరిగిన లోహం బైండర్ రసాయనాన్ని సంప్రదించినప్పుడు ఏర్పడే వాయువుల కారణంగా అచ్చులకు మంచి వెంటిలేషన్ అవసరం, థర్మోసెట్టింగ్ రెసిన్లు మరియు మెటల్ నమూనాలు ఖరీదైనవి. మెటల్ నమూనాల ధర కారణంగా, సాంకేతికత తక్కువ పరిమాణంలో ఉత్పత్తి పరుగులకు సరిగ్గా సరిపోకపోవచ్చు. • ఇన్వెస్ట్మెంట్ కాస్టింగ్ (లాస్ట్-వాక్స్ కాస్టింగ్ అని కూడా పిలుస్తారు): చాలా పాత సాంకేతికత మరియు అనేక లోహాలు, వక్రీభవన పదార్థాలు మరియు ప్రత్యేక అధిక పనితీరు మిశ్రమాల నుండి అధిక ఖచ్చితత్వం, పునరావృతత, బహుముఖ ప్రజ్ఞ మరియు సమగ్రతతో నాణ్యమైన భాగాలను తయారు చేయడానికి అనుకూలం. చిన్న మరియు పెద్ద పరిమాణ భాగాలను ఉత్పత్తి చేయవచ్చు. కొన్ని ఇతర పద్ధతులతో పోల్చినప్పుడు ఖరీదైన ప్రక్రియ, కానీ ప్రధాన ప్రయోజనం ఏమిటంటే నికర ఆకారం, క్లిష్టమైన ఆకృతులు మరియు వివరాలతో భాగాలను ఉత్పత్తి చేసే అవకాశం. కాబట్టి కొన్ని సందర్భాల్లో రీవర్క్ మరియు మ్యాచింగ్ తొలగించడం ద్వారా ఖర్చు కొంతవరకు భర్తీ చేయబడుతుంది. వైవిధ్యాలు ఉన్నప్పటికీ, సాధారణ పెట్టుబడి కాస్టింగ్ ప్రక్రియ యొక్క సారాంశం ఇక్కడ ఉంది: 1.) మైనపు లేదా ప్లాస్టిక్ నుండి అసలు మాస్టర్ నమూనా యొక్క సృష్టి. ప్రతి కాస్టింగ్ ప్రక్రియలో ఇవి నాశనం చేయబడినందున ఒక నమూనా అవసరం. నమూనాలు తయారు చేయబడిన అచ్చు కూడా అవసరం మరియు ఎక్కువ సమయం అచ్చు తారాగణం లేదా యంత్రంతో తయారు చేయబడుతుంది. అచ్చును తెరవాల్సిన అవసరం లేనందున, సంక్లిష్టమైన కాస్టింగ్లను సాధించవచ్చు, అనేక మైనపు నమూనాలను చెట్టు కొమ్మల వలె అనుసంధానించవచ్చు మరియు ఒకదానితో ఒకటి పోయవచ్చు, తద్వారా లోహం లేదా లోహ మిశ్రమం యొక్క ఒకే పోయడం నుండి బహుళ భాగాలను ఉత్పత్తి చేయడం సాధ్యపడుతుంది. 2.) తర్వాత, నమూనా ముంచిన లేదా చాలా చక్కటి గ్రెయిన్డ్ సిలికా, నీరు, బైండర్లతో కూడిన వక్రీభవన స్లర్రీతో పోస్తారు. దీని ఫలితంగా నమూనా యొక్క ఉపరితలంపై సిరామిక్ పొర ఏర్పడుతుంది. నమూనాపై వక్రీభవన కోటు పొడిగా మరియు గట్టిపడటానికి వదిలివేయబడుతుంది. ఈ దశ నుండి పెట్టుబడి కాస్టింగ్ అనే పేరు వచ్చింది: వక్రీభవన స్లర్రీ మైనపు నమూనాపై పెట్టుబడి పెట్టబడుతుంది. 3.) ఈ దశలో, గట్టిపడిన సిరామిక్ అచ్చును తలక్రిందులుగా చేసి వేడి చేయబడుతుంది, తద్వారా మైనపు కరిగి అచ్చు నుండి బయటకు వస్తుంది. మెటల్ కాస్టింగ్ కోసం ఒక కుహరం మిగిలి ఉంది. 4.) మైనపు అయిపోయిన తర్వాత, సిరామిక్ అచ్చు మరింత ఎక్కువ ఉష్ణోగ్రతకు వేడి చేయబడుతుంది, దీని ఫలితంగా అచ్చు బలపడుతుంది. 5.) మెటల్ కాస్టింగ్ అన్ని క్లిష్టమైన విభాగాలను నింపి వేడి అచ్చులో పోస్తారు. 6.) కాస్టింగ్ పటిష్టం చేయడానికి అనుమతించబడుతుంది 7.) చివరగా సిరామిక్ అచ్చు విరిగిపోతుంది మరియు తయారు చేయబడిన భాగాలు చెట్టు నుండి కత్తిరించబడతాయి. ఇక్కడ పెట్టుబడి కాస్టింగ్ ప్లాంట్ బ్రోచర్ లింక్ ఉంది • బాష్పీభవన నమూనా తారాగణం: ప్రక్రియ పాలీస్టైరిన్ ఫోమ్ వంటి పదార్థంతో తయారు చేయబడిన నమూనాను ఉపయోగిస్తుంది, ఇది వేడి కరిగిన లోహాన్ని అచ్చులో పోసినప్పుడు ఆవిరైపోతుంది. ఈ ప్రక్రియలో రెండు రకాలు ఉన్నాయి: బంధం లేని ఇసుకను ఉపయోగించే లాస్ట్ ఫోమ్ కాస్టింగ్ మరియు బంధిత ఇసుకను ఉపయోగించే పూర్తి అచ్చు కాస్టింగ్. ఇక్కడ సాధారణ ప్రక్రియ దశలు ఉన్నాయి: 1.) పాలీస్టైరిన్ వంటి పదార్థం నుండి నమూనాను తయారు చేయండి. పెద్ద పరిమాణంలో తయారు చేయబడినప్పుడు, నమూనా అచ్చు వేయబడుతుంది. భాగం సంక్లిష్టమైన ఆకారాన్ని కలిగి ఉంటే, అటువంటి నురుగు పదార్థం యొక్క అనేక విభాగాలు నమూనాను రూపొందించడానికి కలిసి కట్టుబడి ఉండవలసి ఉంటుంది. కాస్టింగ్పై మంచి ఉపరితల ముగింపుని సృష్టించడానికి మేము తరచుగా వక్రీభవన సమ్మేళనంతో నమూనాను పూస్తాము. 2.) అప్పుడు నమూనా అచ్చు ఇసుకలో ఉంచబడుతుంది. 3.) కరిగిన లోహాన్ని అచ్చులోకి పోస్తారు, నురుగు నమూనాను ఆవిరి చేస్తుంది, అంటే పాలీస్టైరిన్ చాలా సందర్భాలలో అచ్చు కుహరం ద్వారా ప్రవహిస్తుంది. 4.) కరిగిన లోహం గట్టిపడటానికి ఇసుక అచ్చులో వదిలివేయబడుతుంది. 5.) అది గట్టిపడిన తర్వాత, మేము కాస్టింగ్ను తీసివేస్తాము. కొన్ని సందర్భాల్లో, మేము తయారు చేసే ఉత్పత్తికి నమూనాలో కోర్ అవసరం. బాష్పీభవన కాస్టింగ్లో, అచ్చు కుహరంలో ఒక కోర్ని ఉంచడం మరియు భద్రపరచడం అవసరం లేదు. సాంకేతికత చాలా క్లిష్టమైన జ్యామితి తయారీకి అనుకూలంగా ఉంటుంది, అధిక వాల్యూమ్ ఉత్పత్తికి సులభంగా ఆటోమేట్ చేయబడుతుంది మరియు తారాగణం భాగంలో విడిపోయే పంక్తులు లేవు. ప్రాథమిక ప్రక్రియ సరళమైనది మరియు అమలు చేయడానికి ఆర్థికంగా ఉంటుంది. పెద్ద వాల్యూమ్ ఉత్పత్తి కోసం, పాలీస్టైరిన్ నుండి నమూనాలను ఉత్పత్తి చేయడానికి డై లేదా అచ్చు అవసరం కాబట్టి, ఇది కొంత ఖర్చుతో కూడుకున్నది కావచ్చు. • నాన్-ఎక్స్పాండబుల్ మోల్డ్ కాస్టింగ్ : ఈ విస్తృత వర్గం ప్రతి ఉత్పత్తి చక్రం తర్వాత అచ్చును సంస్కరించాల్సిన అవసరం లేని పద్ధతులను సూచిస్తుంది. ఉదాహరణలు శాశ్వత, డై, నిరంతర మరియు సెంట్రిఫ్యూగల్ కాస్టింగ్. రిపీటబిలిటీ పొందబడుతుంది మరియు భాగాలను నియర్ నెట్ షేప్గా వర్గీకరించవచ్చు. • శాశ్వత అచ్చు కాస్టింగ్ : లోహంతో తయారు చేయబడిన పునర్వినియోగ అచ్చులు బహుళ కాస్టింగ్ల కోసం ఉపయోగించబడతాయి. శాశ్వత అచ్చు సాధారణంగా పదివేల సార్లు వాడి పోతుంది. గురుత్వాకర్షణ, వాయువు పీడనం లేదా వాక్యూమ్ సాధారణంగా అచ్చును పూరించడానికి ఉపయోగిస్తారు. అచ్చులను (డై అని కూడా పిలుస్తారు) సాధారణంగా ఇనుము, ఉక్కు, సిరామిక్ లేదా ఇతర లోహాలతో తయారు చేస్తారు. సాధారణ ప్రక్రియ: 1.) మెషిన్ మరియు అచ్చును సృష్టించండి. ఒకదానికొకటి సరిపోయే మరియు తెరవడం మరియు మూసివేయడం వంటి రెండు మెటల్ బ్లాక్ల నుండి అచ్చును తయారు చేయడం సాధారణం. పార్ట్ ఫీచర్లు అలాగే గేటింగ్ సిస్టమ్ రెండూ సాధారణంగా కాస్టింగ్ అచ్చులో అమర్చబడి ఉంటాయి. 2.) అంతర్గత అచ్చు ఉపరితలాలు వక్రీభవన పదార్థాలతో కూడిన స్లర్రితో పూత పూయబడి ఉంటాయి. ఇది ఉష్ణ ప్రవాహాన్ని నియంత్రించడంలో సహాయపడుతుంది మరియు తారాగణం భాగాన్ని సులభంగా తొలగించడానికి కందెనగా పనిచేస్తుంది. 3.) తరువాత, శాశ్వత అచ్చు భాగాలు మూసివేయబడతాయి మరియు అచ్చు వేడి చేయబడుతుంది. 4.) కరిగిన లోహాన్ని అచ్చులో పోస్తారు మరియు పటిష్టం కోసం ఇంకా ఉంచాలి. 5.) ఎక్కువ శీతలీకరణ జరగడానికి ముందు, అచ్చు భాగాలు తెరిచినప్పుడు ఎజెక్టర్లను ఉపయోగించి శాశ్వత అచ్చు నుండి భాగాన్ని తీసివేస్తాము. జింక్ మరియు అల్యూమినియం వంటి తక్కువ మెల్టింగ్ పాయింట్ లోహాల కోసం మేము తరచుగా శాశ్వత అచ్చు కాస్టింగ్ని ఉపయోగిస్తాము. ఉక్కు కాస్టింగ్ల కోసం, మేము గ్రాఫైట్ను అచ్చు పదార్థంగా ఉపయోగిస్తాము. మేము కొన్నిసార్లు శాశ్వత అచ్చులలోని కోర్లను ఉపయోగించి సంక్లిష్ట జ్యామితిని పొందుతాము. ఈ సాంకేతికత యొక్క ప్రయోజనాలు వేగవంతమైన శీతలీకరణ, లక్షణాలలో ఏకరూపత, మంచి ఖచ్చితత్వం మరియు ఉపరితల ముగింపు, తక్కువ తిరస్కరణ రేట్లు, ప్రక్రియను ఆటోమేట్ చేసే అవకాశం మరియు ఆర్థికంగా అధిక వాల్యూమ్లను ఉత్పత్తి చేయడం ద్వారా పొందిన మంచి యాంత్రిక లక్షణాలతో కూడిన కాస్టింగ్లు. ప్రతికూలతలు అధిక ప్రారంభ సెటప్ ఖర్చులు, ఇవి తక్కువ వాల్యూమ్ కార్యకలాపాలకు అనుచితమైనవి మరియు తయారు చేయబడిన భాగాల పరిమాణంపై పరిమితులు. • DIE CASTING : ఒక డై మెషిన్ చేయబడుతుంది మరియు కరిగిన లోహం అధిక పీడనంతో అచ్చు కావిటీస్లోకి నెట్టబడుతుంది. నాన్ ఫెర్రస్ మరియు ఫెర్రస్ మెటల్ డై కాస్టింగ్లు రెండూ సాధ్యమే. వివరాలు, చాలా సన్నని గోడలు, డైమెన్షనల్ అనుగుణ్యత మరియు మంచి ఉపరితల ముగింపుతో చిన్న మరియు మధ్యస్థ పరిమాణ భాగాల అధిక పరిమాణ ఉత్పత్తికి ఈ ప్రక్రియ అనుకూలంగా ఉంటుంది. AGS-TECH Inc. ఈ పద్ధతిని ఉపయోగించి 0.5 మిమీ వరకు చిన్న గోడ మందాన్ని తయారు చేయగలదు. శాశ్వత అచ్చు కాస్టింగ్లో వలె, అచ్చు రెండు భాగాలను కలిగి ఉండాలి, అవి ఉత్పత్తి చేయబడిన భాగాన్ని తొలగించడానికి తెరవగల మరియు మూసివేయగలవు. ప్రతి చక్రంతో బహుళ కాస్టింగ్ల ఉత్పత్తిని ప్రారంభించడానికి డై కాస్టింగ్ అచ్చు బహుళ కావిటీలను కలిగి ఉండవచ్చు. డై కాస్టింగ్ అచ్చులు చాలా బరువైనవి మరియు అవి ఉత్పత్తి చేసే భాగాల కంటే చాలా పెద్దవి, కాబట్టి ఖరీదైనవి కూడా. మా కస్టమర్లు మా నుండి వారి విడిభాగాలను తిరిగి ఆర్డర్ చేసినంత కాలం మేము వారికి అరిగిపోయిన డైలను ఉచితంగా రిపేర్ చేస్తాము మరియు భర్తీ చేస్తాము. మన మరణాలు అనేక వందల వేల చక్రాల పరిధిలో సుదీర్ఘ జీవితకాలం కలిగి ఉంటాయి. ఇక్కడ ప్రాథమిక సరళీకృత ప్రక్రియ దశలు ఉన్నాయి: 1.) సాధారణంగా ఉక్కు నుండి అచ్చు ఉత్పత్తి 2.) డై కాస్టింగ్ మెషీన్లో మోల్డ్ ఇన్స్టాల్ చేయబడింది 3.) పిస్టన్ కరిగిన లోహాన్ని డై కావిటీస్లో ప్రవహించేలా చేస్తుంది, ఇది క్లిష్టమైన లక్షణాలను మరియు సన్నని గోడలను నింపుతుంది. 4.) కరిగిన లోహంతో అచ్చును నింపిన తర్వాత, కాస్టింగ్ ఒత్తిడిలో గట్టిపడుతుంది 5.) ఎజెక్టర్ పిన్స్ సహాయంతో అచ్చు తెరవబడింది మరియు కాస్టింగ్ తీసివేయబడుతుంది. 6.) ఇప్పుడు ఖాళీ డై మళ్లీ లూబ్రికేట్ చేయబడుతుంది మరియు తదుపరి చక్రం కోసం బిగించబడుతుంది. డై కాస్టింగ్లో, మేము తరచుగా ఇన్సర్ట్ మోల్డింగ్ని ఉపయోగిస్తాము, అక్కడ మేము అదనపు భాగాన్ని అచ్చులో చేర్చి, దాని చుట్టూ లోహాన్ని వేస్తాము. ఘనీభవనం తర్వాత, ఈ భాగాలు తారాగణం ఉత్పత్తిలో భాగమవుతాయి. డై కాస్టింగ్ యొక్క ప్రయోజనాలు భాగాల యొక్క మంచి మెకానికల్ లక్షణాలు, క్లిష్టమైన లక్షణాల అవకాశం, చక్కటి వివరాలు మరియు మంచి ఉపరితల ముగింపు, అధిక ఉత్పత్తి రేట్లు, సులభమైన ఆటోమేషన్. ప్రతికూలతలు: అధిక డై మరియు పరికరాల ధర, తారాగణం చేయగల ఆకారాలలో పరిమితులు, ఎజెక్టర్ పిన్ల పరిచయం ఫలితంగా తారాగణం భాగాలపై చిన్న గుండ్రని గుర్తులు, విభజన రేఖ వద్ద పిండబడిన మెటల్ యొక్క సన్నని ఫ్లాష్, అవసరం కారణంగా తక్కువ వాల్యూమ్కు తగినది కాదు. డై మధ్య విభజన రేఖ వెంట వెంట్స్ కోసం, నీటి ప్రసరణను ఉపయోగించి అచ్చు ఉష్ణోగ్రతలను తక్కువగా ఉంచడం అవసరం. • సెంట్రిఫ్యూగల్ కాస్టింగ్ : కరిగిన లోహాన్ని భ్రమణ అక్షం వద్ద తిరిగే అచ్చు మధ్యలో పోస్తారు. సెంట్రిఫ్యూగల్ శక్తులు లోహాన్ని అంచు వైపుకు విసిరివేస్తాయి మరియు అచ్చు తిరుగుతున్నందున అది పటిష్టం అవుతుంది. క్షితిజ సమాంతర మరియు నిలువు అక్షం భ్రమణాలు రెండింటినీ ఉపయోగించవచ్చు. గుండ్రని లోపలి ఉపరితలాలతో పాటు ఇతర నాన్-రౌండ్ ఆకారాలు ఉన్న భాగాలను వేయవచ్చు. ప్రక్రియను ఇలా సంగ్రహించవచ్చు: 1.) కరిగిన లోహాన్ని సెంట్రిఫ్యూగల్ అచ్చులో పోస్తారు. అచ్చు యొక్క స్పిన్నింగ్ కారణంగా మెటల్ అప్పుడు బయటి గోడలకు బలవంతంగా ఉంటుంది. 2.) అచ్చు తిరిగేటప్పుడు, మెటల్ కాస్టింగ్ గట్టిపడుతుంది సెంట్రిఫ్యూగల్ కాస్టింగ్ అనేది పైపుల వంటి బోలు స్థూపాకార భాగాల ఉత్పత్తికి తగిన సాంకేతికత, స్ప్రూస్, రైజర్లు మరియు గేటింగ్ ఎలిమెంట్స్ అవసరం లేదు, మంచి ఉపరితల ముగింపు మరియు వివరణాత్మక లక్షణాలు, సంకోచ సమస్యలు లేవు, చాలా పెద్ద వ్యాసాలతో పొడవైన పైపులను ఉత్పత్తి చేసే అవకాశం, అధిక రేటు ఉత్పత్తి సామర్థ్యం . • నిరంతర తారాగణం ( స్ట్రాండ్ కాస్టింగ్ ) : మెటల్ యొక్క నిరంతర పొడవును ప్రసారం చేయడానికి ఉపయోగిస్తారు. ప్రాథమికంగా కరిగిన లోహం అచ్చు యొక్క రెండు డైమెన్షనల్ ప్రొఫైల్లో వేయబడుతుంది కానీ దాని పొడవు అనిశ్చితంగా ఉంటుంది. కొత్త కరిగిన లోహం నిరంతరం అచ్చులోకి అందించబడుతుంది, కాస్టింగ్ సమయంతో పాటు దాని పొడవు పెరుగుతుంది. రాగి, ఉక్కు, అల్యూమినియం వంటి లోహాలు నిరంతర కాస్టింగ్ ప్రక్రియను ఉపయోగించి పొడవైన తంతువులుగా వేయబడతాయి. ప్రక్రియ వివిధ కాన్ఫిగరేషన్లను కలిగి ఉండవచ్చు కానీ సాధారణమైనదిగా సరళీకృతం చేయవచ్చు: 1.) కరిగిన లోహాన్ని బాగా లెక్కించిన మొత్తంలో మరియు ప్రవాహం రేటులో అచ్చు పైన ఉన్న ఒక కంటైనర్లో పోస్తారు మరియు నీరు చల్లబడిన అచ్చు ద్వారా ప్రవహిస్తుంది. అచ్చులో కురిపించిన మెటల్ కాస్టింగ్ అచ్చు దిగువన ఉంచిన స్టార్టర్ బార్కి పటిష్టం అవుతుంది. ఈ స్టార్టర్ బార్ రోలర్లకు ప్రారంభంలో పట్టుకోవడానికి ఏదైనా ఇస్తుంది. 2.) పొడవైన మెటల్ స్ట్రాండ్ స్థిరమైన వేగంతో రోలర్లచే నిర్వహించబడుతుంది. రోలర్లు నిలువు నుండి క్షితిజ సమాంతరంగా మెటల్ స్ట్రాండ్ యొక్క ప్రవాహం యొక్క దిశను కూడా మారుస్తాయి. 3.) నిరంతర కాస్టింగ్ నిర్దిష్ట సమాంతర దూరం ప్రయాణించిన తర్వాత, కాస్టింగ్తో కదులుతున్న టార్చ్ లేదా రంపాన్ని త్వరగా కావలసిన పొడవుకు కట్ చేస్తుంది. నిరంతర కాస్టింగ్ ప్రక్రియను రోలింగ్ ప్రక్రియతో ఏకీకృతం చేయవచ్చు, ఇక్కడ నిరంతరంగా తారాగణం చేయబడిన లోహాన్ని నేరుగా రోలింగ్ మిల్లులోకి అందించి I-బీమ్లు, T-బీమ్లు....మొదలైనవి. నిరంతర కాస్టింగ్ ఉత్పత్తి అంతటా ఏకరీతి లక్షణాలను ఉత్పత్తి చేస్తుంది, ఇది అధిక ఘనీభవన రేటును కలిగి ఉంటుంది, చాలా తక్కువ పదార్థాన్ని కోల్పోవడం వల్ల ధరను తగ్గిస్తుంది, లోహాన్ని లోడ్ చేయడం, పోయడం, పటిష్టం చేయడం, కత్తిరించడం మరియు కాస్టింగ్ తొలగింపు అన్నీ నిరంతర ఆపరేషన్లో జరిగే ప్రక్రియను అందిస్తుంది. అందువలన అధిక ఉత్పాదకత రేటు మరియు అధిక నాణ్యత ఫలితంగా. అయితే అధిక ప్రారంభ పెట్టుబడి, సెటప్ ఖర్చులు మరియు స్థల అవసరాలు ప్రధాన పరిశీలన. • మ్యాచింగ్ సర్వీసెస్ : మేము మూడు, నాలుగు మరియు ఐదు - యాక్సిస్ మ్యాచింగ్ని అందిస్తాము. మేము ఉపయోగించే మ్యాచింగ్ ప్రక్రియల రకాలు టర్నింగ్, మిల్లింగ్, డ్రిల్లింగ్, బోరింగ్, బ్రాచింగ్, ప్లానింగ్, సావింగ్, గ్రైండింగ్, లాపింగ్, పాలిషింగ్ మరియు నాన్-సాంప్రదాయ మెషినింగ్, ఇవి మా వెబ్సైట్ యొక్క విభిన్న మెను క్రింద మరింత విశదీకరించబడ్డాయి. మా తయారీలో చాలా వరకు, మేము CNC యంత్రాలను ఉపయోగిస్తాము. అయితే కొన్ని కార్యకలాపాలకు సంప్రదాయ పద్ధతులు బాగా సరిపోతాయి కాబట్టి మేము వాటిపై కూడా ఆధారపడతాము. మా మ్యాచింగ్ సామర్థ్యాలు సాధ్యమైనంత ఎక్కువ స్థాయికి చేరుకుంటాయి మరియు కొన్ని అత్యంత డిమాండ్ ఉన్న భాగాలు AS9100 సర్టిఫైడ్ ప్లాంట్లో తయారు చేయబడతాయి. జెట్ ఇంజిన్ బ్లేడ్లకు అత్యంత ప్రత్యేకమైన తయారీ అనుభవం మరియు సరైన పరికరాలు అవసరం. ఏరోస్పేస్ పరిశ్రమ చాలా కఠినమైన ప్రమాణాలను కలిగి ఉంది. సంక్లిష్టమైన రేఖాగణిత నిర్మాణాలతో కూడిన కొన్ని భాగాలు ఐదు అక్షం మ్యాచింగ్ ద్వారా చాలా సులభంగా తయారు చేయబడతాయి, ఇది మనతో సహా కొన్ని మ్యాచింగ్ ప్లాంట్లలో మాత్రమే కనిపిస్తుంది. మా ఏరోస్పేస్ సర్టిఫైడ్ ప్లాంట్ ఏరోస్పేస్ పరిశ్రమ యొక్క విస్తృతమైన డాక్యుమెంటేషన్ అవసరాలకు అనుగుణంగా అవసరమైన అనుభవాన్ని కలిగి ఉంది. టర్నింగ్ ఆపరేషన్లలో, వర్క్పీస్ తిప్పబడుతుంది మరియు కట్టింగ్ టూల్కి వ్యతిరేకంగా తరలించబడుతుంది. ఈ ప్రక్రియ కోసం లాత్ అనే యంత్రాన్ని ఉపయోగిస్తున్నారు. మిల్లింగ్లో, మిల్లింగ్ మెషిన్ అని పిలువబడే యంత్రం వర్క్పీస్కు వ్యతిరేకంగా కట్టింగ్ అంచులను తీసుకురావడానికి తిరిగే సాధనాన్ని కలిగి ఉంటుంది. డ్రిల్లింగ్ కార్యకలాపాలలో కట్టింగ్ అంచులతో తిరిగే కట్టర్ ఉంటుంది, ఇది వర్క్పీస్తో పరిచయంపై రంధ్రాలను ఉత్పత్తి చేస్తుంది. డ్రిల్ ప్రెస్లు, లాత్లు లేదా మిల్లులు సాధారణంగా ఉపయోగించబడతాయి. బోరింగ్ ఆపరేషన్లలో, రంధ్రాన్ని కొద్దిగా పెంచడానికి మరియు ఖచ్చితత్వాన్ని మెరుగుపరచడానికి ఒక వంగిన కోణాల చిట్కాతో ఒక సాధనం స్పిన్నింగ్ వర్క్పీస్లోని ఒక కఠినమైన రంధ్రంలోకి తరలించబడుతుంది. ఇది చక్కటి ముగింపు ప్రయోజనాల కోసం ఉపయోగించబడుతుంది. బ్రాచింగ్ అనేది బ్రోచ్ (టూత్ టూల్) యొక్క ఒక పాస్లోని వర్క్పీస్ నుండి మెటీరియల్ని తీసివేయడానికి ఒక దంతాల సాధనాన్ని కలిగి ఉంటుంది. లీనియర్ బ్రోచింగ్లో, బ్రోచ్ కట్ను ప్రభావితం చేయడానికి వర్క్పీస్ యొక్క ఉపరితలంపై సరళంగా నడుస్తుంది, అయితే రోటరీ బ్రోచింగ్లో, బ్రోచ్ అక్షం సిమెట్రిక్ ఆకారాన్ని కత్తిరించడానికి వర్క్పీస్లోకి తిప్పబడుతుంది మరియు నొక్కబడుతుంది. SWISS TYPE MACHINING అనేది చిన్న అధిక ఖచ్చితత్వ భాగాల యొక్క అధిక వాల్యూమ్ తయారీకి మేము ఉపయోగించే మా విలువైన సాంకేతికతలలో ఒకటి. స్విస్-రకం లాత్ ఉపయోగించి మేము చిన్న, సంక్లిష్టమైన, ఖచ్చితమైన భాగాలను తక్కువ ఖర్చుతో మారుస్తాము. వర్క్పీస్ నిశ్చలంగా ఉంచి, టూల్ కదులుతున్న సంప్రదాయ లాత్ల వలె కాకుండా, స్విస్-రకం టర్నింగ్ సెంటర్లలో, వర్క్పీస్ Z-యాక్సిస్లో కదలడానికి అనుమతించబడుతుంది మరియు సాధనం స్థిరంగా ఉంటుంది. స్విస్-రకం మ్యాచింగ్లో, బార్ స్టాక్ మెషీన్లో ఉంచబడుతుంది మరియు z-యాక్సిస్లో గైడ్ బుషింగ్ ద్వారా ముందుకు సాగుతుంది, మెషిన్ చేయవలసిన భాగాన్ని మాత్రమే బహిర్గతం చేస్తుంది. ఈ విధంగా గట్టి పట్టు నిర్ధారించబడుతుంది మరియు ఖచ్చితత్వం చాలా ఎక్కువగా ఉంటుంది. ప్రత్యక్ష సాధనాల లభ్యత గైడ్ బుషింగ్ నుండి మెటీరియల్ పురోగమిస్తున్నప్పుడు మిల్ మరియు డ్రిల్ చేయడానికి అవకాశాన్ని అందిస్తుంది. స్విస్-రకం పరికరాల యొక్క Y- అక్షం పూర్తి మిల్లింగ్ సామర్థ్యాలను అందిస్తుంది మరియు తయారీలో ఎక్కువ సమయాన్ని ఆదా చేస్తుంది. ఇంకా, మా యంత్రాలు ఉప కుదురులో ఉంచినప్పుడు ఆ భాగంలో పనిచేసే డ్రిల్స్ మరియు బోరింగ్ సాధనాలను కలిగి ఉంటాయి. మా స్విస్-రకం మ్యాచింగ్ సామర్ధ్యం మాకు ఒకే ఆపరేషన్లో పూర్తిగా ఆటోమేటెడ్ పూర్తి మ్యాచింగ్ అవకాశాన్ని అందిస్తుంది. AGS-TECH Inc. వ్యాపారం యొక్క అతిపెద్ద విభాగాలలో మ్యాచింగ్ ఒకటి. అన్ని డ్రాయింగ్ స్పెసిఫికేషన్లకు అనుగుణంగా ఒక భాగాన్ని ప్రసారం చేసిన తర్వాత లేదా వెలికితీసిన తర్వాత మేము దానిని ప్రాథమిక ఆపరేషన్గా లేదా ద్వితీయ ఆపరేషన్గా ఉపయోగిస్తాము. • సర్ఫేస్ ఫినిషింగ్ సర్వీసెస్ : మేము అనేక రకాల ఉపరితల ట్రీట్మెంట్లు మరియు ఉపరితల కండిషనింగ్ను అందిస్తాము, అవి సంశ్లేషణను మెరుగుపరచడం, పూత యొక్క సంశ్లేషణను మెరుగుపరచడానికి సన్నని ఆక్సైడ్ పొరను జమ చేయడం, ఇసుక బ్లాస్టింగ్, కెమ్-ఫిల్మ్, యానోడైజింగ్, నైట్రైడింగ్, పౌడర్ కోటింగ్, స్ప్రే కోటింగ్ , స్పుట్టరింగ్, ఎలక్ట్రాన్ బీమ్, బాష్పీభవనం, లేపనం, డ్రిల్లింగ్ మరియు కట్టింగ్ టూల్స్ కోసం డైమండ్ వంటి కార్బన్ (DLC) లేదా టైటానియం పూత వంటి హార్డ్ కోటింగ్లతో సహా వివిధ అధునాతన మెటలైజేషన్ మరియు పూత పద్ధతులు. • ఉత్పత్తి మార్కింగ్ & లేబులింగ్ సేవలు : మా కస్టమర్లలో చాలా మందికి మెటల్ భాగాలపై మార్కింగ్ మరియు లేబులింగ్, లేజర్ మార్కింగ్, చెక్కడం అవసరం. మీకు అలాంటి అవసరం ఉంటే, మీకు ఏ ఎంపిక ఉత్తమంగా ఉంటుందో చర్చిద్దాం. ఇక్కడ సాధారణంగా ఉపయోగించే కొన్ని మెటల్ కాస్ట్ ఉత్పత్తులు ఉన్నాయి. ఇవి ఆఫ్-ది-షెల్ఫ్ అయినందున, వీటిలో ఏదైనా మీ అవసరాలకు సరిపోయే సందర్భంలో మీరు అచ్చు ఖర్చులను ఆదా చేసుకోవచ్చు: AGS-ఎలక్ట్రానిక్స్ నుండి మా 11 సిరీస్ డై-కాస్ట్ అల్యూమినియం బాక్స్లను డౌన్లోడ్ చేయడానికి ఇక్కడ క్లిక్ చేయండి CLICK Product Finder-Locator Service ముందు పేజి
- Custom Manufactured Parts, Assemblies, Plastic Mold, Casting,Machining
Custom Manufactured Parts, Assemblies, Plastic Mold, Rubber Molding, Metal Casting, CNC Machining, Turning, Milling, Electrical Electronic Optical Assembly PCBA కస్టమ్ తయారు చేసిన భాగాలు & అసెంబ్లీలు & ఉత్పత్తులు ఇంకా చదవండి ప్లాస్టిక్ & రబ్బరు అచ్చులు మరియు మౌల్డింగ్ ఇంకా చదవండి కాస్టింగ్ మరియు మ్యాచింగ్ ఇంకా చదవండి ఎక్స్ట్రూషన్లు, ఎక్స్ట్రూడెడ్ ఉత్పత్తులు ఇంకా చదవండి స్టాంపింగ్లు & షీట్ మెటల్ ఫ్యాబ్రికేషన్ ఇంకా చదవండి మెటల్ ఫోర్జింగ్ & పౌడర్ మెటలర్జీ ఇంకా చదవండి వైర్ & స్ప్రింగ్ ఫార్మ ింగ్ ఇంకా చదవండి గ్లాస్ & సిరామిక్ ఫార్మింగ్ & షేపింగ్ ఇంకా చదవండి సంకలిత మరియు వేగవంతమైన తయారీ ఇంకా చదవండి కాంపోజిట్స్ & కాంపోజిట్ మెటీరియల్స్ తయారీ ఇంకా చదవండి చేరడం & అసెంబ్లీ & ఫాస్టెనింగ్ ప్రక్రియలు మేము మీ కోసం భాగాలు మరియు అసెంబ్లీలను ఉత్పత్తి చేస్తాము మరియు క్రింది తయారీ ప్రక్రియలను అందిస్తాము: • ప్లాస్టిక్ మరియు రబ్బరు అచ్చులు మరియు అచ్చు భాగాలు. ఇంజెక్షన్ మౌల్డింగ్, థర్మోఫార్మింగ్, థర్మోసెట్ మౌల్డింగ్, వాక్యూమ్ ఫార్మింగ్, బ్లో మౌల్డింగ్, రొటేషనల్ మౌల్డింగ్, మౌల్డింగ్, ఇన్సర్ట్ మోల్డింగ్ మరియు ఇతరాలు. • ప్లాస్టిక్, రబ్బరు మరియు మెటల్ ఎక్స్ట్రాషన్లు • ఫెర్రస్ మరియు ఫెర్రస్ కాస్టింగ్లు మరియు మిల్లింగ్ మరియు టర్నింగ్ టెక్నిక్లు, స్విస్-రకం మ్యాచింగ్ ద్వారా ఉత్పత్తి చేయబడిన యంత్ర భాగాలు. • పౌడర్ మెటలర్జీ భాగాలు • మెటల్ మరియు నాన్మెటల్ స్టాంపింగ్లు, షీట్ మెటల్ ఫార్మింగ్, వెల్డెడ్ షీట్ మెటల్ అసెంబ్లీలు • చల్లని మరియు వేడి ఫోర్జింగ్ • వైర్లు, వెల్డెడ్ వైర్ అసెంబ్లీలు, వైర్ ఏర్పాటు • వివిధ రకాల స్ప్రింగ్లు, స్ప్రింగ్ forming • గేర్ తయారీ, గేర్బాక్స్, కప్లింగ్, వార్మ్, స్పీడ్ రిడ్యూసర్, సిలిండర్, ట్రాన్స్మిషన్ బెల్ట్లు, ట్రాన్స్మిషన్ చెయిన్లు, ట్రాన్స్మిషన్ భాగాలు • కస్టమ్ టెంపర్డ్ మరియు బుల్లెట్ ప్రూఫ్ గ్లాస్ NATO మరియు మిలిటరీ ప్రమాణాలకు అనుగుణంగా ఉంటుంది • బంతులు, బేరింగ్లు, పుల్లీలు మరియు పుల్లీ అసెంబ్లీలు • O-రింగ్, వాషర్ మరియు సీల్స్ వంటి కవాటాలు మరియు వాయు భాగాలు • గ్లాస్ మరియు సిరామిక్ భాగాలు మరియు అసెంబ్లీలు, వాక్యూమ్ ప్రూఫ్ మరియు హెర్మెటిక్ భాగాలు, మెటల్-సిరామిక్ మరియు సిరామిక్-సిరామిక్ బాండింగ్. • వివిధ రకాల మెకానికల్, ఆప్టోమెకానికల్, ఎలక్ట్రోమెకానికల్, ఆప్టోఎలక్ట్రానిక్ సమావేశాలు. • మెటల్-రబ్బరు, మెటల్-ప్లాస్టిక్ బంధం • పైప్ మరియు ట్యూబ్, పైప్ ఫార్మింగ్, బెండింగ్ మరియు కస్టమ్ పైప్ అసెంబ్లీలు, బెలో తయారీ. • ఫైబర్గ్లాస్ తయారీ • స్పాట్ వెల్డింగ్, లేజర్ వెల్డింగ్, MIG, TIG వంటి వివిధ పద్ధతులను ఉపయోగించి వెల్డింగ్. ప్లాస్టిక్ భాగాల కోసం అల్ట్రాసోనిక్ వెల్డింగ్. • సంశ్లేషణను పెంపొందించడానికి ఉపరితల కండిషనింగ్ వంటి అనేక రకాల ఉపరితల చికిత్సలు మరియు ఉపరితల ముగింపులు, పూత యొక్క సంశ్లేషణను మెరుగుపరచడానికి సన్నని ఆక్సైడ్ పొరను డిపాజిట్ చేయడం, ఇసుక బ్లాస్టింగ్, కెమ్-ఫిల్మ్, యానోడైజింగ్, నైట్రైడింగ్, పౌడర్ కోటింగ్, స్ప్రే కోటింగ్, వివిధ అధునాతన మెటలైజేషన్ మరియు పూత పద్ధతులు స్పుట్టరింగ్, ఎలక్ట్రాన్ బీమ్, బాష్పీభవనం, లేపనం, కటింగ్ మరియు డ్రిల్లింగ్ సాధనాల కోసం కార్బన్ (DLC) లేదా టైటానియం వంటి వజ్రం వంటి గట్టి పూతలతో సహా. • మార్కింగ్ మరియు లేబులింగ్, మెటల్ భాగాలపై లేజర్ మార్కింగ్, ప్లాస్టిక్ మరియు రబ్బరు భాగాలపై ముద్రించడం డిజైనర్లు మరియు ఇంజనీర్లు ఉపయోగించే సాధారణ మెకానికల్ ఇంజనీరింగ్ నిబంధనల కోసం బ్రోచర్ను డౌన్లోడ్ చేయండి మేము మీ నిర్దిష్ట లక్షణాలు మరియు అవసరాలకు అనుగుణంగా ఉత్పత్తులను రూపొందిస్తాము. మీకు ఉత్తమ నాణ్యత, డెలివరీ మరియు ధరలను అందించడానికి, మేము చైనా, భారతదేశం, తైవాన్, ఫిలిప్పీన్స్, దక్షిణ కొరియా, మలేషియా, శ్రీలంక, టర్కీ, USA, కెనడా, జర్మనీ, UK మరియు జపాన్లలో ప్రపంచవ్యాప్తంగా ఉత్పత్తులను తయారు చేస్తాము. ఇది ఏ ఇతర కస్టమ్ manufacturer కంటే మమ్మల్ని చాలా బలంగా మరియు ప్రపంచవ్యాప్తంగా మరింత పోటీగా చేస్తుంది. మా ఉత్పత్తులు ISO9001:2000, QS9000, ISO14001, TS16949 సర్టిఫైడ్ పరిసరాలలో తయారు చేయబడ్డాయి మరియు CE, UL గుర్తును కలిగి ఉంటాయి మరియు ఇతర పరిశ్రమ ప్రమాణాలకు అనుగుణంగా ఉంటాయి. మేము మీ ప్రాజెక్ట్ కోసం నియమించబడిన తర్వాత, మేము మొత్తం తయారీ, అసెంబ్లీ, టెస్టింగ్, అర్హత, షిప్పింగ్ & కస్టమ్స్ని మీరు కోరుకున్న విధంగా చూసుకోవచ్చు. మీరు కావాలనుకుంటే, మేము మీ భాగాలను నిల్వ చేయవచ్చు, అనుకూల కిట్లను సమీకరించవచ్చు, మీ కంపెనీ పేరు & బ్రాండ్ను ప్రింట్ చేసి లేబుల్ చేయవచ్చు మరియు మీ కస్టమర్లకు షిప్ను డ్రాప్ చేయవచ్చు. మరో మాటలో చెప్పాలంటే, మేము మీ గిడ్డంగి మరియు పంపిణీ కేంద్రం కావాలనుకుంటే అలాగే ఉండవచ్చు. మా గిడ్డంగులు ప్రధాన ఓడరేవుల సమీపంలో ఉన్నందున, ఇది మాకు లాజిస్టికల్ ప్రయోజనాన్ని ఇస్తుంది. ఉదాహరణకు, మీ ఉత్పత్తులు ప్రధాన USA నౌకాశ్రయానికి చేరుకున్నప్పుడు, మేము దానిని నేరుగా సమీపంలోని గిడ్డంగికి ట్రాన్స్పోర్ట్ చేయవచ్చు, ఇక్కడ మేము మీ ఎంపిక ప్రకారం నిల్వ చేయవచ్చు, సమీకరించవచ్చు, కిట్లు, రీలేబుల్, ప్రింట్, ప్యాకేజీని ఉంచవచ్చు మరియు డ్రాప్ చేయవచ్చు. మీ కస్టమర్లకు రవాణా చేయండి. మేము ఉత్పత్తులను సరఫరా చేయడమే కాదు. మేము మీ సైట్కు వచ్చే అనుకూల ఒప్పందాలపై మా కంపెనీ పని చేస్తుంది, సైట్లో మీ ప్రాజెక్ట్ను మూల్యాంకనం చేస్తుంది మరియు మీ కోసం రూపొందించిన ప్రాజెక్ట్ ప్రతిపాదన అనుకూలతను అభివృద్ధి చేస్తుంది. మేము ప్రాజెక్ట్ను అమలు చేయడానికి మా అనుభవజ్ఞులైన బృందాన్ని పంపుతాము. మా ఇంజనీరింగ్ పని గురించి మరింత సమాచారం ఇక్కడ చూడవచ్చు http://www.ags-engineering.com -మేము పారిశ్రామిక స్థాయిలో చిన్న ప్రాజెక్టులతో పాటు పెద్ద ప్రాజెక్టులను తీసుకుంటాము. మొదటి దశగా, మేము మిమ్మల్ని ఫోన్, టెలికాన్ఫరెన్సింగ్ లేదా MSN మెసెంజర్ ద్వారా మా నిపుణుల బృందం సభ్యులకు కనెక్ట్ చేయవచ్చు, కాబట్టి మీరు నేరుగా నిపుణులతో కమ్యూనికేట్ చేయవచ్చు, ప్రశ్నలు అడగవచ్చు మరియు మీ ప్రాజెక్ట్ గురించి చర్చించవచ్చు. మాకు కాల్ చేయండి మరియు అవసరమైతే మేము వచ్చి మిమ్మల్ని సందర్శిస్తాము. ముందు పేజి