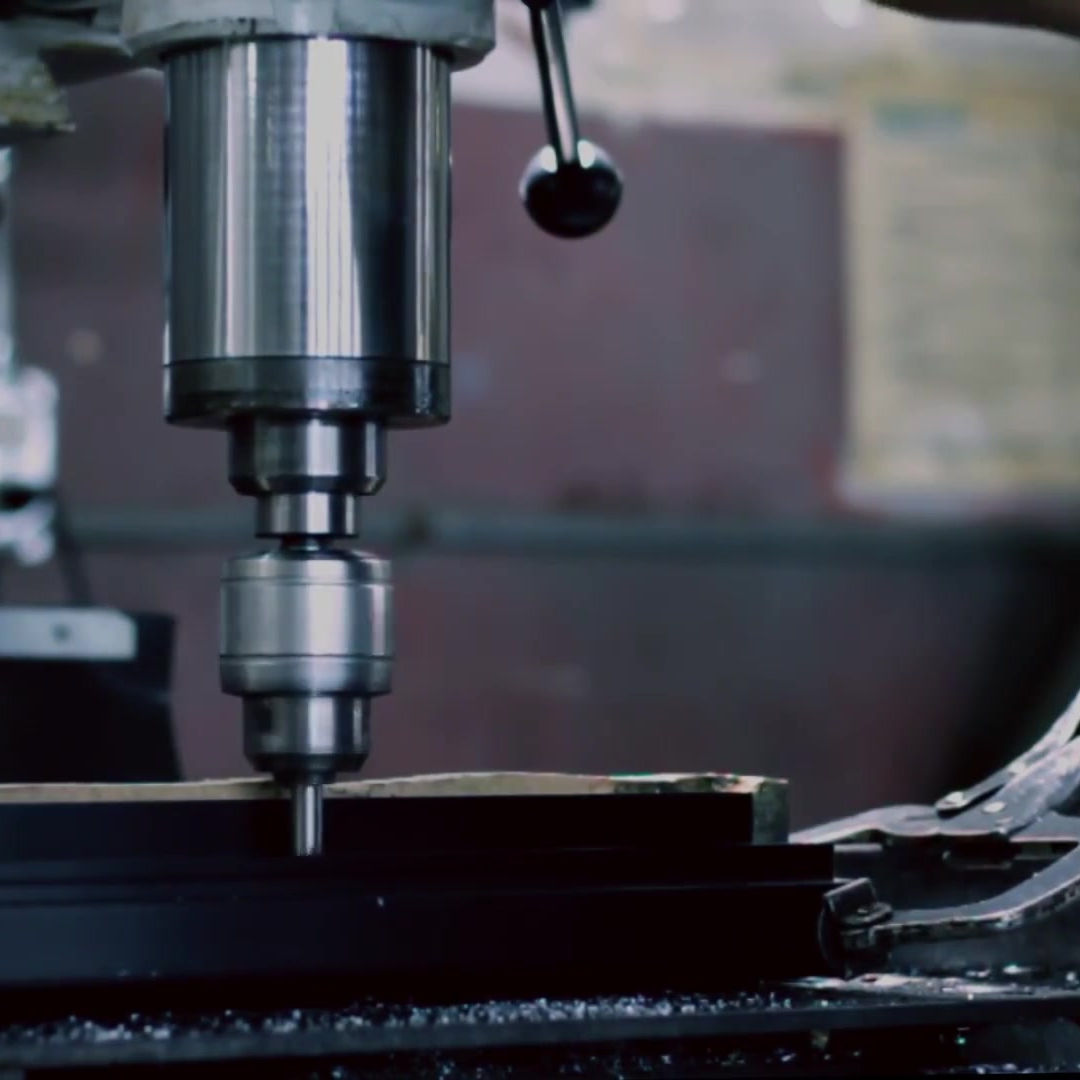
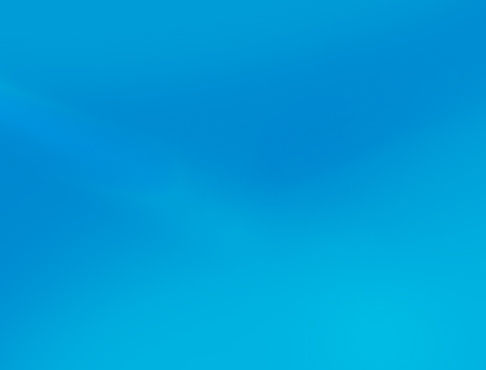
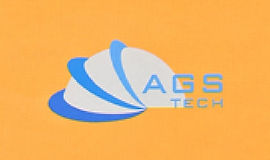
ผู้ผลิตที่กำหนดเองระดับโลก ผู้รวบรวม ผู้รวบรวม พันธมิตรเอาท์ซอร์สสำหรับผลิตภัณฑ์และบริการที่หลากหลาย
เราเป็นแหล่งข้อมูลครบวงจรสำหรับการผลิต การแปรรูป วิศวกรรม การรวมบัญชี การบูรณาการ การเอาท์ซอร์สผลิตภัณฑ์และบริการที่ผลิตขึ้นเองและนอกชั้นวาง
เลือกภาษาของคุณ
-
การผลิตแบบกำหนดเอง
-
การผลิตตามสัญญาในประเทศและทั่วโลก
-
การผลิตเอาท์ซอร์ส
-
การจัดซื้อจัดจ้างในประเทศและทั่วโลก
-
การรวมบัญชี
-
การรวมทางวิศวกรรม
-
บริการด้านวิศวกรรม
การตัดเฉือนด้วยไฟฟ้า (EDM) หรือเรียกอีกอย่างว่า SPARK-EROSION or_cc781905-5cde-3194-bb3bd_136bad5c DISCHARGE, SPAR5, DPAR3B-136bad5c DISCHARGE MACHINING -136bad5cf58d_or WIRE EROSION, is a NON-CONVENTIONAL MANUFACTURING_cc781905-5cde-3194-bbc3b-d. ของประกายไฟ นอกจากนี้เรายังนำเสนอ EDM บางประเภท ได้แก่ NO-WEAR EDM, WIRE EDM (WEDM), EDM GRINDING (EDG), DIE-SINKING EDM, ELECTRIC-DISCHARGE MILLING, micro-EDM, m-EDM_cc781905 -5cde-3194-bb3b-136bad5cf58d_and ELECTROCHEMICAL-DISCHARGE GRINDING (ECDG) ระบบ EDM ของเราประกอบด้วยเครื่องมือ/อิเล็กโทรดที่มีรูปร่างและชิ้นงานที่เชื่อมต่อกับแหล่งจ่ายไฟ DC และใส่ในของเหลวอิเล็กทริกที่ไม่นำไฟฟ้า หลังจากปี 1940 การตัดเฉือนด้วยไฟฟ้าได้กลายเป็นหนึ่งในเทคโนโลยีการผลิตที่สำคัญและเป็นที่นิยมมากที่สุดในอุตสาหกรรมการผลิต
เมื่อระยะห่างระหว่างอิเล็กโทรดทั้งสองลดลง ความเข้มของสนามไฟฟ้าในปริมาตรระหว่างอิเล็กโทรดจะมากกว่าความแรงของอิเล็กโทรดในบางจุด ซึ่งจะแตกออก ในที่สุดก็กลายเป็นสะพานสำหรับกระแสไหลระหว่างอิเล็กโทรดทั้งสอง เกิดอาร์กไฟฟ้าที่รุนแรงทำให้เกิดความร้อนอย่างมีนัยสำคัญเพื่อหลอมส่วนของชิ้นงานและวัสดุเครื่องมือบางส่วน เป็นผลให้วัสดุจะถูกลบออกจากอิเล็กโทรดทั้งสอง ในเวลาเดียวกัน ของเหลวอิเล็กทริกจะถูกทำให้ร้อนอย่างรวดเร็ว ส่งผลให้เกิดการระเหยของของเหลวในช่องว่างส่วนโค้ง เมื่อกระแสไฟหยุดหรือหยุด ความร้อนจะถูกลบออกจากฟองแก๊สโดยของเหลวอิเล็กทริกที่อยู่รอบๆ และฟองอากาศคาวิเทต (ยุบ) คลื่นกระแทกที่เกิดจากการยุบตัวของฟองสบู่และการไหลของของเหลวไดอิเล็กตริกจะชะล้างสิ่งสกปรกออกจากพื้นผิวของชิ้นงาน และกักวัสดุของชิ้นงานที่หลอมเหลวเข้าไปในของเหลวไดอิเล็กตริก อัตราการทำซ้ำสำหรับการคายประจุเหล่านี้อยู่ระหว่าง 50 ถึง 500 kHz แรงดันไฟฟ้าระหว่าง 50 ถึง 380 V และกระแสระหว่าง 0.1 ถึง 500 แอมแปร์ ไดอิเล็กตริกเหลวชนิดใหม่ เช่น น้ำมันแร่ น้ำมันก๊าด หรือน้ำกลั่นและปราศจากไอออน มักจะถูกลำเลียงไปยังปริมาตรระหว่างอิเล็กโทรดที่นำอนุภาคที่เป็นของแข็งออกไป (ในรูปของเศษขยะ) และคุณสมบัติที่เป็นฉนวนของไดอิเล็กตริกกลับคืนมา หลังจากกระแสไหล ความต่างศักย์ระหว่างอิเล็กโทรดทั้งสองจะกลับคืนสู่สภาพเดิมก่อนการสลาย ดังนั้นการสลายไดอิเล็กตริกของเหลวใหม่อาจเกิดขึ้นได้ เครื่องจ่ายไฟฟ้า (EDM) ที่ทันสมัยของเรามีการเคลื่อนไหวที่ควบคุมด้วยตัวเลขและติดตั้งปั๊มและระบบกรองสำหรับของเหลวอิเล็กทริก
การตัดเฉือนด้วยไฟฟ้า (EDM) เป็นวิธีการตัดเฉือนที่ใช้เป็นหลักสำหรับโลหะหนักหรือโลหะที่ยากต่อการตัดเฉือนด้วยเทคนิคทั่วไป โดยทั่วไปแล้ว EDM จะใช้งานได้กับวัสดุใดๆ ที่เป็นตัวนำไฟฟ้า แม้ว่าจะมีการเสนอวิธีการสำหรับการตัดเฉือนเซรามิกที่เป็นฉนวนด้วย EDM ด้วย จุดหลอมเหลวและความร้อนแฝงของการหลอมเป็นคุณสมบัติที่กำหนดปริมาตรของโลหะที่ถูกกำจัดออกต่อการปลดปล่อย ยิ่งค่าเหล่านี้สูงเท่าใด อัตราการขจัดวัสดุก็จะยิ่งช้าลง เนื่องจากกระบวนการตัดเฉือนด้วยกระแสไฟฟ้าไม่เกี่ยวข้องกับพลังงานกล ความแข็ง ความแข็งแรง และความเหนียวของชิ้นงานจึงไม่ส่งผลต่ออัตราการขจัด ความถี่ในการปล่อยหรือพลังงานต่อการคายประจุ แรงดันและกระแสจะแปรผันเพื่อควบคุมอัตราการกำจัดวัสดุ อัตราการขจัดวัสดุและความขรุขระของพื้นผิวเพิ่มขึ้นตามความหนาแน่นกระแสไฟที่เพิ่มขึ้นและความถี่ประกายไฟที่ลดลง เราสามารถตัดรูปทรงหรือฟันผุที่สลับซับซ้อนในเหล็กชุบแข็งล่วงหน้าโดยใช้ EDM โดยไม่ต้องผ่านการอบชุบด้วยความร้อนเพื่อทำให้นิ่มและแข็งตัวอีกครั้ง เราสามารถใช้วิธีนี้กับโลหะหรือโลหะผสมใดๆ เช่น ไททาเนียม ฮาสเทลลอย โควาร์ และอินโคเนล การประยุกต์ใช้กระบวนการ EDM รวมถึงการสร้างเครื่องมือเพชรคริสตัลไลน์ EDM ถือเป็นวิธีการตัดเฉือนที่ไม่ใช่แบบดั้งเดิมหรือไม่ใช่แบบธรรมดาร่วมกับกระบวนการต่างๆ เช่น การตัดเฉือนด้วยไฟฟ้าเคมี (ECM) การตัดด้วยแรงดันน้ำ (WJ, AWJ) การตัดด้วยเลเซอร์ ในทางกลับกัน วิธีการตัดเฉือนแบบเดิมรวมถึงการกลึง การกัด การเจียร การเจาะ และกระบวนการอื่นๆ ซึ่งกลไกการกำจัดวัสดุนั้นขึ้นอยู่กับแรงทางกลเป็นหลัก อิเล็กโทรดสำหรับการตัดเฉือนการคายประจุด้วยไฟฟ้า (EDM) ทำจากกราไฟท์ ทองเหลือง ทองแดง และโลหะผสมทองแดงทังสเตน เส้นผ่านศูนย์กลางของอิเล็กโทรดลดลงเหลือ 0.1 มม. เนื่องจากการสึกหรอของเครื่องมือเป็นปรากฏการณ์ที่ไม่พึงประสงค์ซึ่งส่งผลเสียต่อความแม่นยำของมิติใน EDM เราจึงใช้ประโยชน์จากกระบวนการที่เรียกว่า NO-WEAR EDM โดยการกลับขั้วและใช้เครื่องมือทองแดงเพื่อลดการสึกหรอของเครื่องมือ
ตามหลักการแล้วการตัดเฉือนด้วยไฟฟ้า (EDM) ถือได้ว่าเป็นชุดของการสลายและการฟื้นฟูของเหลวอิเล็กทริกระหว่างอิเล็กโทรด อย่างไรก็ตาม ในความเป็นจริง การกำจัดเศษซากออกจากบริเวณอิเล็กโทรดนั้นแทบจะเป็นบางส่วนเสมอ สิ่งนี้ทำให้คุณสมบัติทางไฟฟ้าของไดอิเล็กทริกในพื้นที่ระหว่างอิเล็กโทรดแตกต่างจากค่าที่ระบุและแปรผันตามเวลา ระยะห่างระหว่างขั้วไฟฟ้า (spark-gap) ถูกปรับโดยอัลกอริธึมการควบคุมของเครื่องเฉพาะที่ใช้ น่าเสียดายที่ Spark-gap ใน EDM นั้นบางครั้งอาจลัดวงจรโดยเศษซาก ระบบควบคุมของอิเล็กโทรดอาจล้มเหลวในการตอบสนองเร็วพอที่จะป้องกันไม่ให้อิเล็กโทรดทั้งสอง (เครื่องมือและชิ้นงาน) ลัดวงจร ไฟฟ้าลัดวงจรที่ไม่ต้องการนี้มีส่วนช่วยในการขจัดวัสดุที่แตกต่างจากเคสในอุดมคติ เราให้ความสำคัญสูงสุดกับการชะล้างเพื่อฟื้นฟูคุณสมบัติการเป็นฉนวนของไดอิเล็กตริก เพื่อให้กระแสเกิดขึ้นที่จุดระหว่างอิเล็กโทรดเสมอ ดังนั้นจึงลดความเป็นไปได้ของการเปลี่ยนแปลงรูปร่าง (ความเสียหาย) ที่ไม่ต้องการของอิเล็กโทรดเครื่องมือ และชิ้นงาน เพื่อให้ได้รูปทรงเฉพาะ เครื่องมือ EDM จะถูกนำทางไปตามเส้นทางที่ต้องการใกล้กับชิ้นงานโดยไม่ต้องสัมผัส เราให้ความสำคัญสูงสุดกับประสิทธิภาพของการควบคุมการเคลื่อนไหวในการใช้งาน ด้วยวิธีนี้จะมีการปล่อยกระแสไฟ / ประกายไฟจำนวนมาก และแต่ละส่วนมีส่วนช่วยในการกำจัดวัสดุออกจากทั้งเครื่องมือและชิ้นงานซึ่งมีการเกิดหลุมอุกกาบาตขนาดเล็ก ขนาดของหลุมอุกกาบาตเป็นหน้าที่ของพารามิเตอร์ทางเทคโนโลยีที่กำหนดไว้สำหรับงานเฉพาะที่อยู่ในมือ และขนาดอาจมีตั้งแต่ระดับนาโน (เช่น ในกรณีของการดำเนินการ micro-EDM) ไปจนถึงหลายร้อยไมโครเมตรในสภาพการหยาบ หลุมอุกกาบาตขนาดเล็กบนเครื่องมือทำให้เกิดการสึกกร่อนของอิเล็กโทรดที่เรียกว่า "การสึกหรอของเครื่องมือ" ทีละน้อย เพื่อป้องกันผลกระทบจากการสึกหรอต่อรูปทรงของชิ้นงาน เราจึงเปลี่ยนอิเล็กโทรดเครื่องมืออย่างต่อเนื่องในระหว่างการตัดเฉือน บางครั้งเราบรรลุเป้าหมายนี้โดยใช้ลวดที่เปลี่ยนอย่างต่อเนื่องเป็นอิเล็กโทรด (กระบวนการ EDM นี้เรียกอีกอย่างว่า WIRE EDM ) บางครั้งเราใช้ขั้วไฟฟ้าเครื่องมือในลักษณะที่มีส่วนน้อยเท่านั้นที่มีส่วนร่วมในกระบวนการตัดเฉือน และส่วนนี้มีการเปลี่ยนแปลงเป็นประจำ ตัวอย่างเช่น กรณีนี้เมื่อใช้จานหมุนเป็นขั้วไฟฟ้าเครื่องมือ กระบวนการนี้เรียกว่า EDM GRINDING อีกเทคนิคหนึ่งที่เราปรับใช้คือการใช้ชุดอิเล็กโทรดที่มีขนาดและรูปร่างต่างกันระหว่างการทำงาน EDM เดียวกันเพื่อชดเชยการสึกหรอ เราเรียกเทคนิคนี้ว่าหลายอิเล็กโทรด และมักใช้บ่อยที่สุดเมื่ออิเล็กโทรดของเครื่องมือทำซ้ำในเชิงลบของรูปร่างที่ต้องการ และเคลื่อนไปยังช่องว่างตามทิศทางเดียว โดยปกติแล้วจะเป็นทิศทางแนวตั้ง (เช่น แกน z) ซึ่งคล้ายกับอ่างของเครื่องมือในของเหลวไดอิเล็กทริกที่ชิ้นงานถูกแช่ ดังนั้นจึงเรียกว่า DIE-SINKING EDM (บางครั้งเรียกว่า_cc781905 3194-bb3b-136bad5cf58d_CONVENTIONAL EDM or RAM EDM) เครื่องสำหรับการดำเนินการนี้เรียกว่า SINKER EDM อิเล็กโทรดสำหรับ EDM ประเภทนี้มีรูปแบบที่ซับซ้อน หากได้รูปเรขาคณิตขั้นสุดท้ายโดยใช้อิเล็กโทรดรูปทรงเรียบง่ายซึ่งปกติจะเคลื่อนที่ไปตามหลายทิศทางและยังสามารถหมุนได้ เราเรียกว่า it EDM MILLING ปริมาณการสึกหรอขึ้นอยู่กับพารามิเตอร์ทางเทคโนโลยีที่ใช้ในการดำเนินการอย่างเคร่งครัด ( ขั้ว, กระแสสูงสุด, แรงดันวงจรเปิด) ตัวอย่างเช่น in micro-EDM หรือที่รู้จักในชื่อ m-EDM พารามิเตอร์เหล่านี้มักจะถูกตั้งค่าที่ก่อให้เกิดการสึกหรออย่างรุนแรง ดังนั้นการสึกหรอจึงเป็นปัญหาใหญ่ในพื้นที่นั้น ซึ่งเราลดการใช้ความรู้ที่สั่งสมมา ตัวอย่างเช่น เพื่อลดการสึกหรอของอิเล็กโทรดกราไฟต์ เครื่องกำเนิดไฟฟ้าแบบดิจิตอล สามารถควบคุมได้ภายในมิลลิวินาที จะกลับขั้วเมื่อเกิดการสึกกร่อนด้วยไฟฟ้า ซึ่งส่งผลให้เกิดผลกระทบที่คล้ายกับการชุบด้วยไฟฟ้าที่สะสมกราไฟต์ที่ถูกกัดเซาะกลับคืนบนอิเล็กโทรดอย่างต่อเนื่อง ในอีกวิธีหนึ่ง วงจรที่เรียกว่า ''Zero Wear'' เราลดความถี่ในการเริ่มและหยุดการคายประจุ โดยคงไว้เป็นระยะเวลานานที่สุด อัตราการขจัดวัสดุในการตัดเฉือนด้วยไฟฟ้า-การคายประจุสามารถประมาณได้จาก:
MRR = 4 x 10 exp(4) x I x Tw exp (-1.23)
โดยที่ MRR อยู่ในหน่วย mm3/min I เป็นกระแสในหน่วยแอมแปร์ Tw คือจุดหลอมเหลวของชิ้นงานใน K-273.15K exp หมายถึงเลขชี้กำลัง
ในทางกลับกัน อัตราการสึกหรอ Wt ของอิเล็กโทรดสามารถหาได้จาก:
Wt = ( 1.1 x 10exp(11) ) x I x Ttexp(-2.38)
โดยที่ Wt อยู่ในหน่วย mm3/min และ Tt คือจุดหลอมเหลวของวัสดุอิเล็กโทรดในหน่วย K-273.15K
สุดท้าย อัตราส่วนการสึกหรอของชิ้นงานต่ออิเล็กโทรด R สามารถหาได้จาก:
R = 2.25 x Trexp(-2.38)
โดยที่ T คืออัตราส่วนของจุดหลอมเหลวของชิ้นงานต่ออิเล็กโทรด
จม EDM :
Sinker EDM หรือที่เรียกอีกอย่างว่า CAVITY TYPE EDM or VOLUME EDM ที่เป็นของเหลวที่หลอมรวมเข้าด้วยกัน อิเล็กโทรดและชิ้นงานเชื่อมต่อกับแหล่งจ่ายไฟ แหล่งจ่ายไฟสร้างศักย์ไฟฟ้าระหว่างทั้งสอง เมื่ออิเล็กโทรดเข้าใกล้ชิ้นงาน การสลายไดอิเล็กตริกจะเกิดขึ้นในของเหลว ก่อตัวเป็นช่องพลาสมา และเกิดประกายไฟเล็กๆ กระโดดขึ้น ประกายไฟมักจะกระทบทีละครั้งเพราะไม่น่าเป็นไปได้สูงที่ตำแหน่งต่างๆ ในพื้นที่อิเล็กโทรดระหว่างขั้วไฟฟ้าจะมีลักษณะทางไฟฟ้าเฉพาะที่เหมือนกัน ซึ่งจะทำให้เกิดประกายไฟขึ้นในสถานที่ดังกล่าวทั้งหมดพร้อมกัน ประกายไฟเหล่านี้นับแสนครั้งเกิดขึ้นที่จุดสุ่มระหว่างอิเล็กโทรดกับชิ้นงานต่อวินาที เนื่องจากโลหะพื้นฐานกัดกร่อนและช่องว่างประกายไฟเพิ่มขึ้นในภายหลัง เครื่อง CNC ของเราจึงลดระดับอิเล็กโทรดลงโดยอัตโนมัติเพื่อให้กระบวนการทำงานต่อไปได้ไม่ขาดตอน อุปกรณ์ของเรามีวงจรการควบคุมที่เรียกว่า "ตรงเวลา" และ "ปิดเวลา" การตั้งค่าตรงเวลาจะกำหนดความยาวหรือระยะเวลาของประกายไฟ เวลาที่นานขึ้นจะสร้างโพรงที่ลึกขึ้นสำหรับประกายไฟนั้นและประกายไฟที่ตามมาทั้งหมดสำหรับรอบนั้น ทำให้เกิดผิวที่หยาบกว่าบนชิ้นงานและในทางกลับกัน เวลาปิดคือช่วงเวลาที่จุดประกายหนึ่งถูกแทนที่ด้วยอีกจุดหนึ่ง เวลาหยุดทำงานนานขึ้นจะช่วยให้ของเหลวอิเล็กทริกสามารถชะล้างผ่านหัวฉีดเพื่อทำความสะอาดเศษซากที่กัดเซาะ ดังนั้นจึงหลีกเลี่ยงไฟฟ้าลัดวงจร การตั้งค่าเหล่านี้จะถูกปรับในไมโครวินาที
ลวด EDM :
In WIRE ELECTRICAL DISCHARGE MACHINING (WEDM) หรือที่เรียกอีกอย่างว่า WIRE-CUT EDM_cc781905-5cde-3194-bbf3b-136badorcTING ลวดโลหะทองเหลืองเส้นเดียวบาง ๆ ผ่านชิ้นงานซึ่งจมอยู่ในถังของเหลวอิเล็กทริก Wire EDM เป็นรูปแบบที่สำคัญของ EDM บางครั้งเราใช้ EDM แบบตัดลวดเพื่อตัดแผ่นที่มีความหนาถึง 300 มม. และเจาะ เครื่องมือ และแม่พิมพ์จากโลหะแข็งที่ยากต่อการตัดเฉือนด้วยวิธีการผลิตอื่นๆ ในกระบวนการนี้ซึ่งคล้ายกับการตัดขอบด้วยเลื่อยวงเดือน ลวดซึ่งถูกป้อนจากแกนม้วนเป็นเส้นตลอดเวลา จะถูกยึดไว้ระหว่างไกด์เพชรบนและล่าง ไกด์ที่ควบคุมโดย CNC จะเคลื่อนที่ในระนาบ x–y และไกด์ด้านบนสามารถเคลื่อนที่ได้อย่างอิสระในแกน z–u–v ทำให้เกิดความสามารถในการตัดรูปทรงเรียวและการเปลี่ยนรูปร่าง (เช่น วงกลมที่ด้านล่างและสี่เหลี่ยมที่ ด้านบน). ไกด์ด้านบนสามารถควบคุมการเคลื่อนที่ของแกนใน x–y–u–v–i–j–k–l– วิธีนี้ช่วยให้ WEDM สามารถตัดรูปร่างที่ประณีตและละเอียดอ่อนได้ เส้นตัดเฉลี่ยของอุปกรณ์ของเราที่ให้ต้นทุนและเวลาในการตัดเฉือนที่ดีที่สุดคือ 0.335 มม. โดยใช้ Ø 0.25 ทองเหลือง ทองแดง หรือลวดทังสเตน อย่างไรก็ตาม ไดมอนด์ไกด์บนและล่างของอุปกรณ์ CNC ของเรามีความแม่นยำประมาณ 0.004 มม. และสามารถมีทางตัดหรือแนวตัดที่เล็กเพียง 0.021 มม. โดยใช้ลวด Ø 0.02 มม. การตัดที่แคบมากจึงเป็นไปได้ ความกว้างของการตัดมากกว่าความกว้างของเส้นลวด เนื่องจากเกิดประกายไฟจากด้านข้างของเส้นลวดไปยังชิ้นงานทำให้เกิดการกัดเซาะ ''โอเวอร์คัต'' นี้เป็นสิ่งจำเป็น สำหรับการใช้งานจำนวนมาก มันสามารถคาดการณ์ได้ ดังนั้นจึงสามารถชดเชยได้ (ใน micro-EDM มักไม่เป็นเช่นนั้น) แกนม้วนสายไฟยาว โดยม้วนละ 8 กก. ที่มีเส้นลวด 0.25 มม. มีความยาวเพียง 19 กิโลเมตรเท่านั้น เส้นผ่านศูนย์กลางของเส้นลวดอาจมีขนาดเล็กถึง 20 ไมโครเมตร และความแม่นยำของรูปทรงอยู่ที่ +/- 1 ไมโครเมตร โดยทั่วไปเราใช้ลวดเพียงครั้งเดียวและรีไซเคิลเพราะมีราคาไม่แพงนัก มันเคลื่อนที่ด้วยความเร็วคงที่ 0.15 ถึง 9 ม./นาที และคงเคอร์ฟ (ช่อง) คงที่ไว้ในระหว่างการตัด ในกระบวนการ EDM แบบตัดลวด เราใช้น้ำเป็นของเหลวไดอิเล็กตริก ควบคุมความต้านทานและคุณสมบัติทางไฟฟ้าอื่นๆ ด้วยตัวกรองและหน่วยกำจัดไอออน น้ำจะชะล้างเศษซากที่ถูกตัดออกจากบริเวณที่ตัด การชะล้างเป็นปัจจัยสำคัญในการกำหนดอัตราป้อนสูงสุดสำหรับความหนาของวัสดุที่กำหนด ดังนั้นเราจึงรักษาความสม่ำเสมอ ความเร็วตัดในลวด EDM ระบุไว้ในแง่ของพื้นที่หน้าตัดต่อหน่วยเวลา เช่น 18,000 มม./ชม. สำหรับเหล็กกล้าเครื่องมือ D2 หนา 50 มม. ความเร็วตัดเชิงเส้นสำหรับกรณีนี้คือ 18,000/50 = 360 มม./ชม. อัตราการขจัดวัสดุในลวด EDM คือ:
MRR = Vf xhxb
ในที่นี้ MRR อยู่ในหน่วย mm3/min Vf คืออัตราป้อนของลวดเข้าไปในชิ้นงานในหน่วย mm/min h คือความหนาหรือความสูงเป็น mm และ b คือ kerf ซึ่งก็คือ:
b = dw + 2s
โดยที่ dw คือเส้นผ่านศูนย์กลางของเส้นลวด และ s คือช่องว่างระหว่างเส้นลวดและชิ้นงานในหน่วย มม.
นอกจากค่าความคลาดเคลื่อนที่เข้มงวดขึ้นแล้ว ศูนย์การตัดเฉือนลวด EDM แบบหลายแกนที่ทันสมัยของเรายังได้เพิ่มคุณสมบัติต่างๆ เช่น หัวหลายหัวสำหรับการตัดสองส่วนพร้อมกัน การควบคุมเพื่อป้องกันการแตกหักของลวด คุณสมบัติการทำเกลียวอัตโนมัติในกรณีที่ลวดขาด และตั้งโปรแกรมไว้ กลยุทธ์การตัดเฉือนเพื่อเพิ่มประสิทธิภาพการทำงาน ความสามารถในการตัดแบบตรงและเชิงมุม
Wire-EDM ให้ความเค้นตกค้างต่ำแก่เรา เนื่องจากไม่ต้องใช้แรงตัดสูงในการขจัดวัสดุ เมื่อพลังงาน/กำลังต่อพัลส์ค่อนข้างต่ำ (เช่นเดียวกับในการดำเนินการเก็บผิวละเอียด) การเปลี่ยนแปลงคุณสมบัติทางกลของวัสดุจะเกิดขึ้นเพียงเล็กน้อยเนื่องจากความเค้นตกค้างต่ำ
การเจียรด้วยไฟฟ้า (EDG) : ล้อเจียรไม่มีสารกัดกร่อน ทำจากกราไฟต์หรือทองเหลือง การเกิดประกายไฟซ้ำๆ ระหว่างล้อหมุนและชิ้นงานจะขจัดวัสดุออกจากพื้นผิวของชิ้นงาน อัตราการกำจัดวัสดุคือ:
MRR = K x ฉัน
โดยที่ MRR อยู่ในหน่วย mm3/min I เป็นกระแสในหน่วย Amperes และ K คือตัวประกอบวัสดุของชิ้นงานในหน่วย mm3/A-min เรามักใช้การเจียรเพื่อคายประจุด้วยไฟฟ้าเพื่อเลื่อยร่องแคบๆ บนส่วนประกอบ บางครั้งเรารวมกระบวนการ EDG (Electrical-Discharge Grinding) กับกระบวนการ ECG (Electrochemical Grinding) ซึ่งวัสดุจะถูกลบออกโดยการกระทำทางเคมี การปล่อยไฟฟ้าจากล้อกราไฟท์จะทำลายฟิล์มออกไซด์และถูกชะล้างด้วยอิเล็กโทรไลต์ กระบวนการนี้เรียกว่า ELECTROCHEMICAL-DISCHARGE GRINDING (ECDG) แม้ว่ากระบวนการ ECDG จะใช้พลังงานค่อนข้างมาก แต่ก็เป็นกระบวนการที่เร็วกว่า EDG เราทำการบดเครื่องมือคาร์ไบด์เป็นส่วนใหญ่โดยใช้เทคนิคนี้
การใช้งานของการตัดเฉือนด้วยไฟฟ้า:
การผลิตต้นแบบ:
เราใช้กระบวนการ EDM ในการผลิตแม่พิมพ์ การผลิตเครื่องมือและแม่พิมพ์ ตลอดจนการผลิตชิ้นส่วนต้นแบบและการผลิต โดยเฉพาะอย่างยิ่งสำหรับอุตสาหกรรมการบินและอวกาศ ยานยนต์ และอิเล็กทรอนิกส์ซึ่งมีปริมาณการผลิตค่อนข้างต่ำ ใน Sinker EDM อิเล็กโทรดกราไฟต์ ทังสเตนทองแดง หรือทองแดงบริสุทธิ์จะถูกตัดเฉือนให้เป็นรูปร่างที่ต้องการ (เชิงลบ) และป้อนเข้าไปในชิ้นงานที่ส่วนท้ายของแรมแนวตั้ง
การทำเหรียญ:
สำหรับการสร้างแม่พิมพ์สำหรับการผลิตเครื่องประดับและตราสัญลักษณ์โดยกระบวนการสร้างเหรียญ (ปั๊ม) ต้นแบบในเชิงบวกอาจทำจากเงินสเตอร์ลิงเนื่องจาก (ด้วยการตั้งค่าเครื่องที่เหมาะสม) ต้นแบบถูกกัดกร่อนอย่างมีนัยสำคัญและใช้เพียงครั้งเดียว จากนั้นแม่พิมพ์เชิงลบที่เป็นผลลัพธ์จะถูกชุบแข็งและใช้ในค้อนกระแทกเพื่อผลิตแฟลตที่ประทับตราจากช่องว่างของแผ่นคัตเอาท์ที่เป็นทองแดง เงิน หรือโลหะผสมทองคำที่มีการพิสูจน์ต่ำ สำหรับตราสัญลักษณ์ แฟลตเหล่านี้อาจทำเป็นรูปทรงโค้งมนเพิ่มเติมด้วยดายอื่น โดยทั่วไปแล้ว EDM ประเภทนี้จะดำเนินการจุ่มลงในไดอิเล็กตริกที่ใช้น้ำมัน วัตถุที่ทำเสร็จแล้วอาจถูกขัดเกลาเพิ่มเติมด้วยการเคลือบแข็ง (แก้ว) หรือแบบอ่อน (สี) และ/หรือชุบด้วยไฟฟ้าด้วยทองคำบริสุทธิ์หรือนิกเกิล วัสดุที่นุ่มกว่า เช่น เงิน อาจถูกแกะสลักด้วยมือเพื่อเป็นการวิจิตรบรรจง
การเจาะรูขนาดเล็ก:
ในเครื่อง EDM แบบ Wire-cut เราใช้ EDM เจาะรูขนาดเล็กเพื่อสร้างรูทะลุในชิ้นงานเพื่อร้อยเกลียวลวดสำหรับการทำงานของ EDM แบบ Wire-cut หัว EDM แบบแยกเฉพาะสำหรับการเจาะรูขนาดเล็กจะติดตั้งอยู่บนเครื่องตัดลวดของเรา ซึ่งช่วยให้แผ่นชุบแข็งขนาดใหญ่มีชิ้นส่วนสำเร็จรูปกัดเซาะจากหัวเหล่านี้ได้ตามต้องการและไม่ต้องเจาะล่วงหน้า เรายังใช้ EDM รูเล็กๆ เพื่อเจาะแถวของรูเข้าไปในขอบของใบพัดกังหันที่ใช้ในเครื่องยนต์ไอพ่น ก๊าซที่ไหลผ่านรูเล็กๆ เหล่านี้ทำให้เครื่องยนต์ใช้อุณหภูมิที่สูงกว่าที่เป็นไปได้ โลหะผสมผลึกเดี่ยวที่อุณหภูมิสูง แข็งมาก ใบมีดเหล่านี้ทำขึ้นทำให้การตัดเฉือนรูแบบธรรมดาที่มีอัตราส่วนกว้างยาวสูงยากอย่างยิ่งและเป็นไปไม่ได้ การใช้งานอื่นๆ สำหรับ EDM รูขนาดเล็กคือการสร้างช่องเปิดขนาดเล็กมากสำหรับส่วนประกอบระบบเชื้อเพลิง นอกจากหัว EDM ในตัวแล้ว เรายังปรับใช้เครื่อง EDM เจาะรูขนาดเล็กแบบสแตนด์อโลนที่มีแกน x–y กับบลายด์ของเครื่องหรือรูทะลุ สว่าน EDM เจาะรูด้วยอิเล็กโทรดท่อทองเหลืองหรือทองแดงยาวที่หมุนในหัวจับที่มีการไหลของน้ำกลั่นหรือน้ำปราศจากไอออนอย่างต่อเนื่องที่ไหลผ่านอิเล็กโทรดเป็นสารชะล้างและไดอิเล็กทริก EDM สำหรับการเจาะรูขนาดเล็กบางรุ่นสามารถเจาะทะลุเหล็กอ่อนหรือแข็งขนาด 100 มม. ได้ภายในเวลาไม่ถึง 10 วินาที เจาะรูได้ตั้งแต่ 0.3 มม. ถึง 6.1 มม. ในการเจาะรูนี้
การตัดเฉือนโลหะ:
เรายังมีเครื่อง EDM พิเศษเพื่อวัตถุประสงค์เฉพาะในการถอดเครื่องมือที่ชำรุด (ดอกสว่านหรือต๊าป) ออกจากชิ้นงาน กระบวนการนี้เรียกว่า ''การตัดเฉือนโลหะสลาย''
ข้อดีและข้อเสียของการตัดเฉือนด้วยไฟฟ้าและการปล่อยประจุ:
ข้อดีของ EDM ได้แก่ การตัดเฉือนของ:
- รูปทรงที่ซับซ้อนซึ่งอาจผลิตได้ยากด้วยเครื่องมือตัดทั่วไป
- วัสดุแข็งมากจนถึงค่าความคลาดเคลื่อนที่ใกล้มาก
- ชิ้นงานขนาดเล็กมาก ซึ่งเครื่องมือตัดทั่วไปอาจทำให้ชิ้นงานเสียหายจากแรงกดของเครื่องมือตัดที่มากเกินไป
- ไม่มีการสัมผัสโดยตรงระหว่างเครื่องมือและชิ้นงาน ดังนั้นชิ้นงานที่ละเอียดอ่อนและวัสดุที่อ่อนแอจึงสามารถตัดเฉือนได้โดยไม่ผิดเพี้ยน
- สามารถสร้างพื้นผิวที่ดีได้
- รูที่ละเอียดมากสามารถเจาะได้ง่าย
ข้อเสียของ EDM ได้แก่:
- อัตราการกำจัดวัสดุช้า
- เวลาและค่าใช้จ่ายเพิ่มเติมที่ใช้ในการสร้างอิเล็กโทรดสำหรับ ram/sinker EDM
- การสร้างมุมแหลมบนชิ้นงานทำได้ยากเนื่องจากการสึกหรอของอิเล็กโทรด
- การใช้พลังงานสูง
- 'โอเวอร์คัต' ถูกสร้างขึ้น
- การสึกหรอของเครื่องมือมากเกินไปเกิดขึ้นระหว่างการตัดเฉือน
- วัสดุที่ไม่นำไฟฟ้าสามารถตัดเฉือนได้เฉพาะกับการตั้งค่าเฉพาะของกระบวนการเท่านั้น