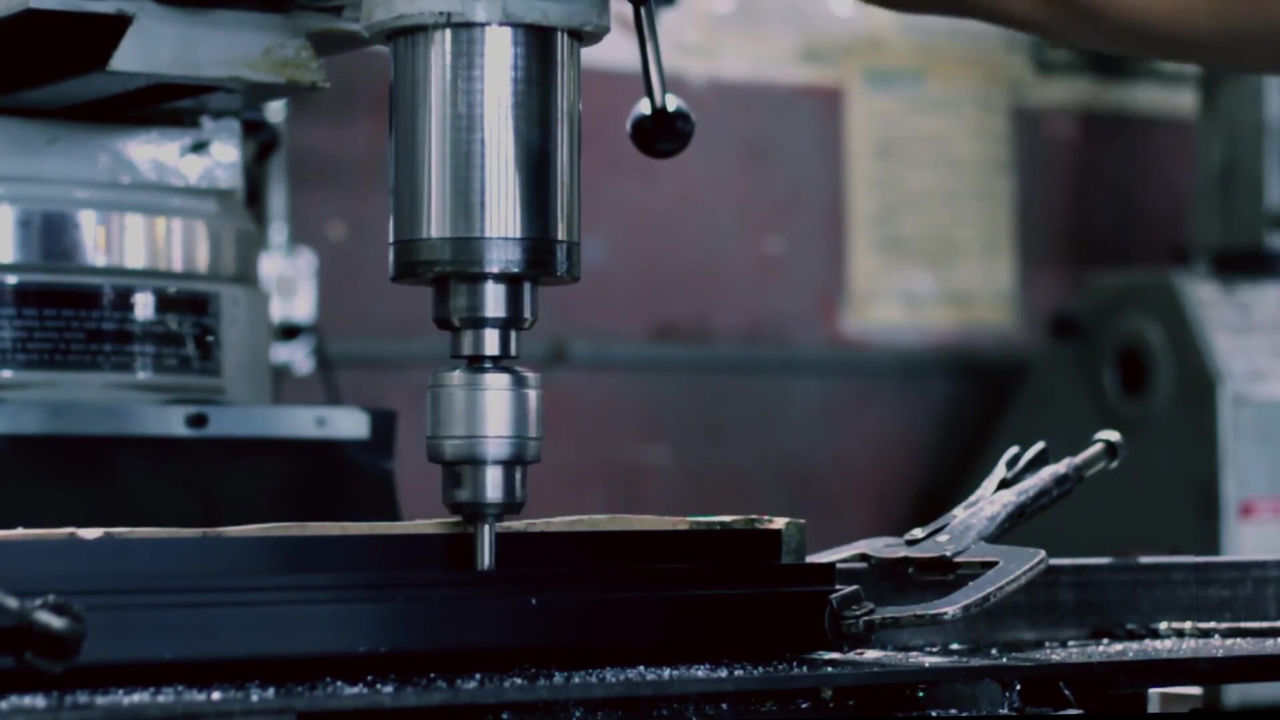
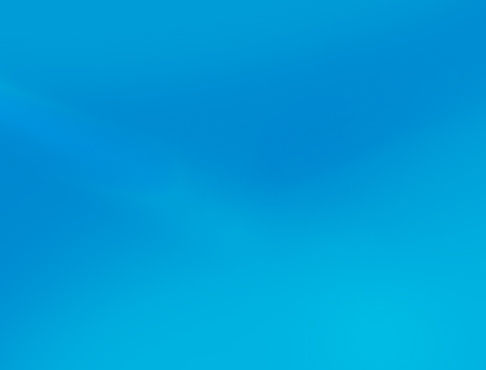
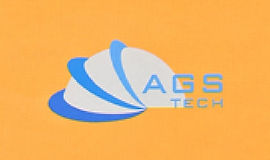
ผู้ผลิตที่กำหนดเองระดับโลก ผู้รวบรวม ผู้รวบรวม พันธมิตรเอาท์ซอร์สสำหรับผลิตภัณฑ์และบริการที่หลากหลาย
เราเป็นแหล่งข้อมูลครบวงจรสำหรับการผลิต การแปรรูป วิศวกรรม การรวมบัญชี การบูรณาการ การเอาท์ซอร์สผลิตภัณฑ์และบริการที่ผลิตขึ้นเองและนอกชั้นวาง
เลือกภาษาของคุณ
-
การผลิตแบบกำหนดเอง
-
การผลิตตามสัญญาในประเทศและทั่วโลก
-
การผลิตเอาท์ซอร์ส
-
การจัดซื้อจัดจ้างในประเทศและทั่วโลก
-
การรวมบัญชี
-
การรวมทางวิศวกรรม
-
บริการด้านวิศวกรรม
ประเภทของการผลิตแก้วที่เรานำเสนอ ได้แก่ แก้วคอนเทนเนอร์ การเป่าแก้ว ใยแก้ว & ท่อ & คัน, เครื่องแก้วในประเทศและอุตสาหกรรม, โคมไฟและหลอดไฟ, การขึ้นรูปแก้วที่มีความแม่นยำ, ส่วนประกอบและส่วนประกอบทางแสง, กระจกแบน & แผ่น & โฟลต เราทำการขึ้นรูปด้วยมือและการขึ้นรูปด้วยเครื่องจักร
กระบวนการผลิตเซรามิกทางเทคนิคที่เป็นที่นิยมของเรา ได้แก่ การอัดขึ้นรูป การอัดแบบไอโซสแตติก การกดไอโซสแตติกแบบร้อน การรีดร้อน การหล่อแบบสลิป การหล่อเทป การอัดรีด การฉีดขึ้นรูป การตัดเฉือนสีเขียว การเผาหรือเผา การเจียระไนเพชร การประกอบแบบสุญญากาศ
เราขอแนะนำให้คุณคลิกที่นี่เพื่อ
ดาวน์โหลดภาพประกอบแผนผังของกระบวนการขึ้นรูปและขึ้นรูปแก้วโดย AGS-TECH Inc.
ดาวน์โหลดภาพประกอบแผนผังของกระบวนการผลิตเซรามิกทางเทคนิคโดย AGS-TECH Inc.
ไฟล์ที่ดาวน์โหลดได้พร้อมรูปถ่ายและภาพสเก็ตช์เหล่านี้จะช่วยให้คุณเข้าใจข้อมูลที่เราให้ไว้ด้านล่างนี้ได้ดียิ่งขึ้น
• การผลิตกระจกคอนเทนเนอร์: เรามี PRESS AND BLOW แบบอัตโนมัติ เช่นเดียวกับสายการเป่าและเป่าสำหรับการผลิต ในกระบวนการเป่าและเป่า เราหยด gob ลงในแม่พิมพ์เปล่า และสร้างคอโดยการเป่าลมอัดจากด้านบน ต่อจากนี้ไป อากาศอัดจะถูกเป่าเป็นครั้งที่สองจากอีกทิศทางหนึ่งผ่านคอภาชนะเพื่อสร้างรูปแบบพรีฟอร์มของขวด จากนั้นพรีฟอร์มนี้จะถูกถ่ายโอนไปยังแม่พิมพ์จริง อุ่นให้นุ่มและอัดอากาศเพื่อให้พรีฟอร์มมีรูปร่างของคอนเทนเนอร์สุดท้าย ชัดเจนยิ่งขึ้น มันถูกอัดแรงดันและดันเข้ากับผนังของโพรงแม่พิมพ์เป่าเพื่อให้ได้รูปร่างที่ต้องการ สุดท้าย ภาชนะแก้วที่ผลิตขึ้นจะถูกถ่ายโอนไปยังเตาอบอบอ่อนเพื่อให้ความร้อนซ้ำและขจัดความเครียดที่เกิดขึ้นระหว่างการขึ้นรูปในภายหลัง และถูกทำให้เย็นในลักษณะที่ควบคุมได้ ในวิธีการกดและเป่า gobs ที่หลอมละลายจะถูกใส่ลงในแม่พิมพ์ parison (แม่พิมพ์เปล่า) และกดลงในรูปทรง parison (รูปร่างเปล่า) จากนั้นช่องว่างจะถูกถ่ายโอนไปยังแม่พิมพ์เป่าและเป่าคล้ายกับกระบวนการที่อธิบายไว้ข้างต้นภายใต้ "กระบวนการเป่าและเป่า" ขั้นตอนที่ตามมาเช่นการหลอมและการบรรเทาความเครียดมีความคล้ายคลึงหรือเหมือนกัน
• GLASS BLOWING : เราทำการผลิตผลิตภัณฑ์แก้วโดยใช้การเป่าด้วยมือแบบธรรมดาและแบบใช้ลมอัดด้วยอุปกรณ์อัตโนมัติ สำหรับคำสั่งซื้อบางรายการจำเป็นต้องมีการเป่าแบบธรรมดา เช่น โครงการที่เกี่ยวข้องกับงานศิลปะแก้ว หรือโครงการที่ต้องใช้ชิ้นส่วนจำนวนน้อยกว่าที่มีพิกัดความเผื่อหลวม โครงการสร้างต้นแบบ / สาธิต….เป็นต้น การเป่าแก้วแบบทั่วไปเกี่ยวข้องกับการจุ่มท่อโลหะกลวงลงในหม้อแก้วหลอมเหลวแล้วหมุนท่อเพื่อเก็บวัสดุแก้วจำนวนหนึ่ง แก้วที่เก็บที่ปลายท่อรีดด้วยเหล็กแบน มีรูปร่างตามต้องการ ยืดออก ให้ความร้อนซ้ำ และเป่าด้วยลม เมื่อพร้อมก็ใส่แม่พิมพ์และเป่าลม ช่องแม่พิมพ์เปียกเพื่อหลีกเลี่ยงไม่ให้กระจกสัมผัสกับโลหะ ฟิล์มน้ำทำหน้าที่เหมือนเบาะระหว่างพวกเขา การเป่าด้วยมือเป็นกระบวนการที่ช้าซึ่งใช้แรงงานคนมาก และเหมาะสำหรับการสร้างต้นแบบหรือสินค้าที่มีมูลค่าสูงเท่านั้น ไม่เหมาะสำหรับการสั่งซื้อปริมาณมากต่อชิ้นในราคาถูก
• การผลิตเครื่องแก้วในประเทศและอุตสาหกรรม : การใช้วัสดุแก้วประเภทต่างๆ ทำให้มีการผลิตเครื่องแก้วหลากหลายรูปแบบ แก้วบางชนิดทนความร้อนและเหมาะสำหรับเครื่องแก้วในห้องปฏิบัติการ ในขณะที่บางแก้วก็ทนทานต่อเครื่องล้างจานได้หลายครั้งและเหมาะสำหรับการผลิตผลิตภัณฑ์ในประเทศ การใช้เครื่อง Westlake มีการผลิตแก้วน้ำดื่มหลายหมื่นชิ้นต่อวัน เพื่อทำให้ง่ายขึ้น แก้วหลอมเหลวจะถูกรวบรวมโดยสุญญากาศและใส่เข้าไปในแม่พิมพ์เพื่อทำเป็นพรีฟอร์ม จากนั้นอากาศจะถูกเป่าเข้าไปในแม่พิมพ์ สิ่งเหล่านี้จะถูกถ่ายโอนไปยังแม่พิมพ์อื่นและอากาศจะถูกเป่าอีกครั้งและแก้วก็จะมีรูปร่างสุดท้าย เช่นเดียวกับการเป่าด้วยมือ แม่พิมพ์เหล่านี้จะเปียกด้วยน้ำ การยืดกล้ามเนื้อเพิ่มเติมเป็นส่วนหนึ่งของการดำเนินการเก็บผิวละเอียดที่เกิดคอ แก้วส่วนเกินถูกไฟไหม้ จากนั้นจึงควบคุมกระบวนการให้ความร้อนและความเย็นอีกครั้งตามที่อธิบายไว้ข้างต้นดังนี้
• GLASS TUBE & ROD FORMING : กระบวนการหลักที่เราใช้สำหรับการผลิตหลอดแก้วคือกระบวนการ DANNER และ VELLO ในกระบวนการ Danner แก้วจากเตาหลอมจะไหลและตกลงบนปลอกเอียงที่ทำจากวัสดุทนไฟ ปลอกสวมบนเพลากลวงที่หมุนได้หรือท่อเป่าลม จากนั้นนำแก้วมาพันรอบปลอกแขนและก่อตัวเป็นชั้นๆ เรียบๆ ไหลลงมาที่แขนเสื้อและเหนือปลายก้าน ในกรณีของการขึ้นรูปท่อ อากาศจะถูกเป่าผ่านท่อเป่าลมที่มีปลายกลวง และในกรณีของการขึ้นรูปก้าน เราใช้ปลายที่เป็นของแข็งบนก้าน จากนั้นท่อหรือแท่งจะถูกดึงทับลูกกลิ้ง ขนาดต่างๆ เช่น ความหนาของผนังและเส้นผ่านศูนย์กลางของหลอดแก้วจะถูกปรับให้เป็นค่าที่ต้องการโดยการตั้งค่าเส้นผ่านศูนย์กลางของปลอกและแรงดันลมเป่าให้เป็นค่าที่ต้องการ ปรับอุณหภูมิ อัตราการไหลของแก้ว และความเร็วในการวาด ในทางกลับกัน กระบวนการผลิตหลอดแก้วเวลโลนั้นเกี่ยวข้องกับแก้วที่เคลื่อนออกจากเตาหลอมและเข้าไปในชามที่มีแมนเดรลหรือกระดิ่งกลวง จากนั้นแก้วจะผ่านช่องว่างอากาศระหว่างแมนเดรลกับชาม แล้วทำเป็นหลอด หลังจากนั้นจะเคลื่อนผ่านลูกกลิ้งไปยังเครื่องวาดรูปและเย็นลง ในตอนท้ายของการตัดท่อระบายความร้อนและการประมวลผลขั้นสุดท้ายจะเกิดขึ้น ขนาดของท่อสามารถปรับได้เช่นเดียวกับในกระบวนการ Danner เมื่อเปรียบเทียบกระบวนการ Danner กับ Vello เราสามารถพูดได้ว่ากระบวนการ Vello นั้นเหมาะสมกว่าสำหรับการผลิตปริมาณมาก ในขณะที่กระบวนการ Danner อาจเหมาะสมกว่าสำหรับการสั่งซื้อหลอดที่มีปริมาตรน้อยกว่าที่แม่นยำกว่า
• การประมวลผลแผ่น & แบน & กระจกโฟลต : เรามีกระจกแบนจำนวนมากที่มีความหนาตั้งแต่ความหนา submilimeter ไปจนถึงหลายเซนติเมตร แว่นสายตาแบนของเรามีความสมบูรณ์แบบเกือบสมบูรณ์แบบ เรานำเสนอกระจกที่มีการเคลือบพิเศษ เช่น การเคลือบด้วยแสง ซึ่งใช้เทคนิคการสะสมไอเคมีเพื่อเคลือบสารเคลือบ เช่น สารป้องกันการสะท้อนหรือการเคลือบกระจก การเคลือบนำไฟฟ้าแบบโปร่งใสก็เป็นเรื่องปกติเช่นกัน นอกจากนี้ยังมีสารเคลือบที่ไม่ชอบน้ำหรือชอบน้ำบนกระจก และสารเคลือบที่ทำให้กระจกสามารถทำความสะอาดตัวเองได้ กระจกเทมเปอร์ กันกระสุน และลามิเนตเป็นสินค้ายอดนิยมอื่นๆ เราตัดกระจกเป็นรูปทรงที่ต้องการด้วยความคลาดเคลื่อนที่ต้องการ มีการทำงานรองอื่น ๆ เช่น การดัดโค้งหรือดัดกระจกแบน
• การขึ้นรูปกระจกที่แม่นยำ: เราใช้เทคนิคนี้เป็นหลักสำหรับการผลิตส่วนประกอบออปติคัลที่มีความแม่นยำ โดยไม่ต้องใช้เทคนิคที่มีราคาแพงกว่าและใช้เวลานาน เช่น การเจียร การขัด และการขัดเงา เทคนิคนี้ไม่เพียงพอเสมอสำหรับการสร้างเลนส์ที่ดีที่สุด แต่ในบางกรณี เช่น สินค้าอุปโภคบริโภค กล้องดิจิตอล เลนส์ทางการแพทย์ อาจเป็นทางเลือกที่ดีในราคาไม่แพงสำหรับการผลิตในปริมาณมาก นอกจากนี้ยังมีข้อได้เปรียบเหนือเทคนิคการขึ้นรูปแก้วอื่นๆ ที่ต้องการรูปทรงที่ซับซ้อน เช่น ในกรณีของทรงกลม กระบวนการพื้นฐานเกี่ยวข้องกับการโหลดด้านล่างของแม่พิมพ์ของเราด้วยช่องว่างแก้ว การอพยพของห้องกระบวนการเพื่อกำจัดออกซิเจน ใกล้ปิดของแม่พิมพ์ การให้ความร้อนอย่างรวดเร็วและความร้อนของแม่พิมพ์และแก้วด้วยแสงอินฟราเรด การปิดเพิ่มเติมของครึ่งแม่พิมพ์ เพื่อกดกระจกที่อ่อนนุ่มอย่างช้า ๆ ในแบบควบคุมให้ได้ความหนาที่ต้องการ และสุดท้ายทำให้แก้วเย็นลงและเติมไนโตรเจนลงในห้องและนำผลิตภัณฑ์ออก การควบคุมอุณหภูมิที่แม่นยำ ระยะการปิดแม่พิมพ์ แรงปิดแม่พิมพ์ การจับคู่ค่าสัมประสิทธิ์การขยายตัวของแม่พิมพ์และวัสดุแก้วเป็นสิ่งสำคัญในกระบวนการนี้
• การผลิตส่วนประกอบทางแสงของแก้วและการประกอบ : นอกจากการขึ้นรูปแก้วที่มีความแม่นยำแล้ว ยังมีกระบวนการที่มีคุณค่าหลายอย่างที่เราใช้ในการผลิตส่วนประกอบและส่วนประกอบทางแสงคุณภาพสูงสำหรับการใช้งานที่มีความต้องการสูง การเจียร การขัด และการขัดเงาของแว่นตาเกรดออปติคัลในสารละลายที่มีสารกัดกร่อนพิเศษชั้นดีเป็นศิลปะและวิทยาศาสตร์สำหรับการผลิตเลนส์ออพติคอล ปริซึม แฟลต และอื่นๆ ความเรียบของพื้นผิว เป็นคลื่น ความเรียบ และพื้นผิวออปติคัลที่ปราศจากข้อบกพร่องต้องอาศัยประสบการณ์มากมายในกระบวนการดังกล่าว การเปลี่ยนแปลงสภาพแวดล้อมเพียงเล็กน้อยอาจส่งผลให้ผลิตภัณฑ์ไม่ตรงตามข้อกำหนดและทำให้สายการผลิตต้องหยุดชะงัก มีหลายกรณีที่การเช็ดเพียงครั้งเดียวบนพื้นผิวออปติคัลด้วยผ้าสะอาดสามารถทำให้ผลิตภัณฑ์เป็นไปตามข้อกำหนดหรือไม่ผ่านการทดสอบ วัสดุแก้วที่นิยมใช้ ได้แก่ ซิลิกาหลอมรวม ควอทซ์ BK7 นอกจากนี้การประกอบส่วนประกอบดังกล่าวยังต้องการประสบการณ์เฉพาะทาง บางครั้งมีการใช้กาวพิเศษ อย่างไรก็ตาม บางครั้งเทคนิคที่เรียกว่าการสัมผัสด้วยแสงเป็นทางเลือกที่ดีที่สุด และไม่เกี่ยวข้องกับวัสดุใดๆ ระหว่างแว่นสายตาที่ต่ออยู่ ประกอบด้วยพื้นผิวเรียบสัมผัสทางกายภาพเพื่อยึดติดกันโดยไม่ต้องใช้กาว ในบางกรณี ตัวเว้นระยะเชิงกล แท่งแก้วหรือลูกแก้วที่มีความแม่นยำ แคลมป์หรือส่วนประกอบโลหะที่กลึงจะถูกนำมาใช้เพื่อประกอบส่วนประกอบออปติคัลในระยะทางที่แน่นอนและด้วยการวางแนวเรขาคณิตบางอย่างต่อกัน ให้เราตรวจสอบเทคนิคยอดนิยมบางอย่างของเราสำหรับการผลิตเลนส์ระดับไฮเอนด์
GRINDING & LAPPING & POLISHING : ได้รูปร่างหยาบของส่วนประกอบออปติคัลด้วยการเจียรแก้วเปล่า จากนั้นจึงทำการขัดและขัดเงาโดยการหมุนและถูพื้นผิวที่ขรุขระของส่วนประกอบออปติคัลกับเครื่องมือที่มีรูปร่างพื้นผิวที่ต้องการ สารละลายที่มีอนุภาคและของเหลวที่มีฤทธิ์กัดกร่อนเล็กๆ ถูกเทลงในระหว่างเลนส์กับเครื่องมือสร้างรูปร่าง ขนาดอนุภาคที่มีฤทธิ์กัดกร่อนในสารละลายดังกล่าวสามารถเลือกได้ตามระดับความเรียบที่ต้องการ ความเบี่ยงเบนของพื้นผิวทางแสงที่สำคัญจากรูปร่างที่ต้องการจะแสดงเป็นความยาวคลื่นของแสงที่ใช้ ออปติกความแม่นยำสูงของเรามีค่าความคลาดเคลื่อนที่ยอมรับได้ของความยาวคลื่น (ความยาวคลื่น/10) หนึ่งในสิบหรือเข้มงวดกว่านี้ก็ได้ นอกจากโปรไฟล์พื้นผิวแล้ว พื้นผิวที่สำคัญจะถูกสแกนและประเมินสำหรับคุณสมบัติพื้นผิวและข้อบกพร่องอื่นๆ เช่น ขนาด รอยขีดข่วน เศษ หลุม จุด...ฯลฯ การควบคุมสภาพแวดล้อมอย่างเข้มงวดในชั้นการผลิตเชิงแสงและข้อกำหนดด้านมาตรวิทยาและการทดสอบที่ครอบคลุมด้วยอุปกรณ์ที่ล้ำสมัยทำให้สาขานี้กลายเป็นสาขาที่ท้าทายของอุตสาหกรรม
• กระบวนการรองในการผลิตแก้ว: อีกครั้ง เราถูกจำกัดด้วยจินตนาการของคุณเท่านั้น เมื่อพูดถึงกระบวนการรองและการตกแต่งแก้ว เราแสดงรายการบางส่วน:
-การเคลือบบนกระจก (ออปติคัล ไฟฟ้า ไทรโบโลยี ความร้อน การทำงาน กลไก...) ตัวอย่างเช่น เราสามารถปรับเปลี่ยนคุณสมบัติพื้นผิวของกระจกได้ เช่น สะท้อนความร้อน เพื่อให้ภายในอาคารเย็น หรือทำให้ด้านหนึ่งดูดซับอินฟราเรดโดยใช้นาโนเทคโนโลยี ซึ่งช่วยให้ภายในอาคารอบอุ่นเพราะชั้นผิวนอกสุดของกระจกจะดูดซับรังสีอินฟราเรดภายในอาคารและแผ่รังสีกลับคืนสู่ภายใน
-แกะสลัก onแก้ว
- การติดฉลากเซรามิกประยุกต์ (ACL)
-แกะสลัก
- ขัดด้วยเปลวไฟ
- ขัดเคมี
-การย้อมสี
การผลิตเซรามิกทางเทคนิค
• DIE PRESSING : ประกอบด้วยการบดอัดแกนเดียวของผงเม็ดเล็ก ๆ ที่อยู่ในแม่พิมพ์
• HOT PRESSING : คล้ายกับแม่พิมพ์ฉีดขึ้นรูปแต่เพิ่มอุณหภูมิเพื่อเพิ่มความหนาแน่น ใส่ผงหรือพรีฟอร์มอัดลงในแม่พิมพ์กราไฟท์และใช้แรงดันแกนเดียวในขณะที่แม่พิมพ์ถูกเก็บไว้ที่อุณหภูมิสูง เช่น 2,000 องศาเซลเซียส อุณหภูมิอาจแตกต่างกันไปตามประเภทของผงเซรามิกที่กำลังดำเนินการ สำหรับรูปทรงและรูปทรงที่ซับซ้อน อาจจำเป็นต้องมีการประมวลผลอื่นๆ เช่น การเจียระไนเพชร
• ISOSTATIC PRESSING : บรรจุผงเม็ดหรือแม่พิมพ์อัดขึ้นรูปในภาชนะที่ปิดสนิทแล้วใส่ลงในภาชนะแรงดันปิดที่มีของเหลวอยู่ภายใน หลังจากนั้นจะถูกอัดแน่นโดยการเพิ่มแรงดันของถังแรงดัน ของเหลวภายในภาชนะจะถ่ายเทแรงดันอย่างสม่ำเสมอทั่วทั้งพื้นผิวของภาชนะบรรจุภัณฑ วัสดุจึงถูกบีบอัดให้เท่ากันและใช้รูปร่างของภาชนะที่ยืดหยุ่นและโปรไฟล์ภายในและคุณสมบัติต่างๆ
• HOT ISOSTATIC PRESSING : คล้ายกับการกดแบบไอโซสแตติก แต่นอกเหนือจากบรรยากาศของแก๊สที่มีแรงดันแล้ว เรายังเผาแบบอัดแน่นที่อุณหภูมิสูง การกดไอโซสแตติกแบบร้อนส่งผลให้มีความหนาแน่นเพิ่มขึ้นและความแข็งแรงเพิ่มขึ้น
• SLIP CASTING / DRAIN CASTING : เราเติมแม่พิมพ์ด้วยสารแขวนลอยของอนุภาคเซรามิกขนาดไมโครมิเตอร์และของเหลวตัวพา ส่วนผสมนี้เรียกว่า "สลิป" แม่พิมพ์มีรูพรุน ดังนั้นของเหลวในส่วนผสมจึงถูกกรองเข้าไปในแม่พิมพ์ เป็นผลให้มีการหล่อขึ้นบนพื้นผิวด้านในของแม่พิมพ์ หลังจากการเผาผนึกแล้ว สามารถนำชิ้นส่วนออกจากแม่พิมพ์ได้
• TAPE Casting : เราผลิตเทปเซรามิกโดยการหล่อสารละลายเซรามิกบนพื้นผิวที่เคลื่อนย้ายได้เรียบ สารละลายมีผงเซรามิกผสมกับสารเคมีอื่นๆ เพื่อการจับและขนย้าย เนื่องจากตัวทำละลายระเหยแผ่นเซรามิกที่มีความหนาแน่นและยืดหยุ่นเหลือทิ้งไว้ซึ่งสามารถตัดหรือรีดได้ตามต้องการ
• การอัดขึ้นรูป : เช่นเดียวกับในกระบวนการอัดรีดอื่นๆ ส่วนผสมที่อ่อนนุ่มของผงเซรามิกที่มีสารยึดเกาะและสารเคมีอื่นๆ จะถูกส่งผ่านแม่พิมพ์เพื่อให้ได้รูปทรงหน้าตัดและตัดตามความยาวที่ต้องการ กระบวนการนี้ดำเนินการด้วยส่วนผสมเซรามิกแบบเย็นหรือแบบร้อน
• การฉีดขึ้นรูปด้วยแรงดันต่ำ : เราเตรียมส่วนผสมของผงเซรามิกที่มีสารยึดเกาะและตัวทำละลาย และให้ความร้อนจนถึงอุณหภูมิที่สามารถกดและบังคับได้ง่ายในช่องเครื่องมือ เมื่อรอบการขึ้นรูปเสร็จสิ้น ชิ้นส่วนจะถูกขับออกมาและสารเคมีที่ยึดเกาะจะถูกเผาทิ้ง ด้วยการใช้การฉีดขึ้นรูป เราจะได้ชิ้นส่วนที่ซับซ้อนในปริมาณมากในเชิงเศรษฐกิจ รู ที่เป็นเศษเสี้ยวเล็กๆ ของมิลลิเมตรบนผนังหนา 10 มม. สามารถทำเกลียวได้โดยไม่ต้องใช้การตัดเฉือนเพิ่มเติม ความคลาดเคลื่อนแน่นถึง +/- 0.5% เป็นไปได้ และยิ่งต่ำลงเมื่อกลึงชิ้นส่วน , ความหนาของผนังตามลำดับ 0.5 มม. ถึงความยาว 12.5 มม. เช่นเดียวกับความหนาของผนัง 6.5 มม. ถึงความยาว 150 มม.
• GREEN MACHINING : โดยใช้เครื่องมือตัดเฉือนโลหะแบบเดียวกัน เราสามารถตัดเฉือนวัสดุเซรามิกที่กดแล้วได้ในขณะที่ยังคงนิ่มเหมือนชอล์ก ความคลาดเคลื่อน +/- 1% เป็นไปได้ เพื่อความคลาดเคลื่อนที่ดีขึ้น เราใช้การเจียรด้วยเพชร
• SINTERING หรือ FIRING : การเผาผนึกทำให้มีความหนาแน่นเต็มที่ การหดตัวที่สำคัญเกิดขึ้นกับชิ้นส่วนขนาดกะทัดรัดสีเขียว แต่นี่ไม่ใช่ปัญหาใหญ่ เนื่องจากเราคำนึงถึงการเปลี่ยนแปลงมิติเหล่านี้เมื่อเราออกแบบชิ้นส่วนและเครื่องมือ อนุภาคผงถูกยึดเข้าด้วยกันและความพรุนที่เกิดจากกระบวนการบดอัดจะถูกลบออกในระดับที่ดี..
• การเจียรด้วยเพชร : วัสดุที่แข็งที่สุดในโลก “เพชร” ถูกใช้เพื่อบดวัสดุแข็ง เช่น เซรามิก และชิ้นส่วนที่มีความแม่นยำ มีความคลาดเคลื่อนในช่วงไมโครมิเตอร์และพื้นผิวที่เรียบมาก เนื่องจากมีค่าใช้จ่าย เราจึงพิจารณาเทคนิคนี้เมื่อเราต้องการจริงๆ เท่านั้น
• HERMETIC ASSEMBLIES เป็นสิ่งที่ในทางปฏิบัติแล้วไม่อนุญาตให้มีการแลกเปลี่ยนสสาร ของแข็ง ของเหลว หรือก๊าซระหว่างส่วนต่อประสาน การปิดผนึกสุญญากาศเป็นแบบสุญญากาศ ตัวอย่างเช่น เปลือกหุ้มอิเล็กทรอนิคส์แบบสุญญากาศคือส่วนที่รักษาเนื้อหาภายในที่ละเอียดอ่อนของอุปกรณ์ที่บรรจุหีบห่อไว้ไม่เป็นอันตรายต่อความชื้น สารปนเปื้อน หรือก๊าซ ไม่มีสิ่งใดที่ผนึกแน่นได้ 100% แต่เมื่อเราพูดถึงความผนึกแน่น เราหมายความว่าในทางปฏิบัติ มีความผนึกแน่นจนอัตราการรั่วไหลต่ำจนอุปกรณ์มีความปลอดภัยภายใต้สภาวะแวดล้อมปกติเป็นเวลานานมาก ชุดประกอบสุญญากาศของเราประกอบด้วยโลหะ แก้วและส่วนประกอบเซรามิก โลหะ-เซรามิก, เซรามิก-โลหะ-เซรามิก, โลหะ-เซรามิก-โลหะ, โลหะกับโลหะ, โลหะ-แก้ว, โลหะ-แก้ว-โลหะ, แก้ว-โลหะ-แก้ว, แก้ว- โลหะและแก้วกับแก้ว และการผสมผสานอื่นๆ ทั้งหมดของการยึดติดระหว่างโลหะ-แก้ว-เซรามิก ตัวอย่างเช่น เราสามารถเคลือบส่วนประกอบเซรามิกด้วยโลหะ เพื่อให้สามารถยึดติดอย่างแน่นหนากับส่วนประกอบอื่นๆ ในชุดประกอบ และมีความสามารถในการปิดผนึกที่ดีเยี่ยม เรามีความรู้ในการเคลือบไฟเบอร์ออปติกหรือ feedthroughs ด้วยโลหะและการบัดกรีหรือประสานเข้ากับเปลือกหุ้ม ดังนั้นจึงไม่มีก๊าซผ่านหรือรั่วไหลเข้าไปในเปลือกหุ้ม ดังนั้นจึงใช้ในการผลิตกล่องหุ้มอิเล็กทรอนิกส์เพื่อห่อหุ้มอุปกรณ์ที่ละเอียดอ่อนและปกป้องจากบรรยากาศภายนอก นอกจากคุณสมบัติการปิดผนึกที่ยอดเยี่ยมแล้ว คุณสมบัติอื่นๆ เช่น ค่าสัมประสิทธิ์การขยายตัวทางความร้อน ความต้านทานการเปลี่ยนรูป ลักษณะที่ไม่ปล่อยก๊าซออก อายุการใช้งานยาวนานมาก ลักษณะที่ไม่นำไฟฟ้า คุณสมบัติของฉนวนความร้อน ลักษณะป้องกันไฟฟ้าสถิตย์...เป็นต้น ทำให้วัสดุแก้วและเซรามิกเป็นทางเลือกสำหรับการใช้งานบางประเภท ข้อมูลเกี่ยวกับโรงงานผลิตของเราที่ผลิตอุปกรณ์เซรามิกกับโลหะ การปิดผนึกอย่างแน่นหนา การป้อนผ่านสุญญากาศ ส่วนประกอบการควบคุมสุญญากาศและของเหลวสูงและสูงและสูงพิเศษ สามารถพบได้ที่นี่:โบรชัวร์โรงงานส่วนประกอบสุญญากาศ