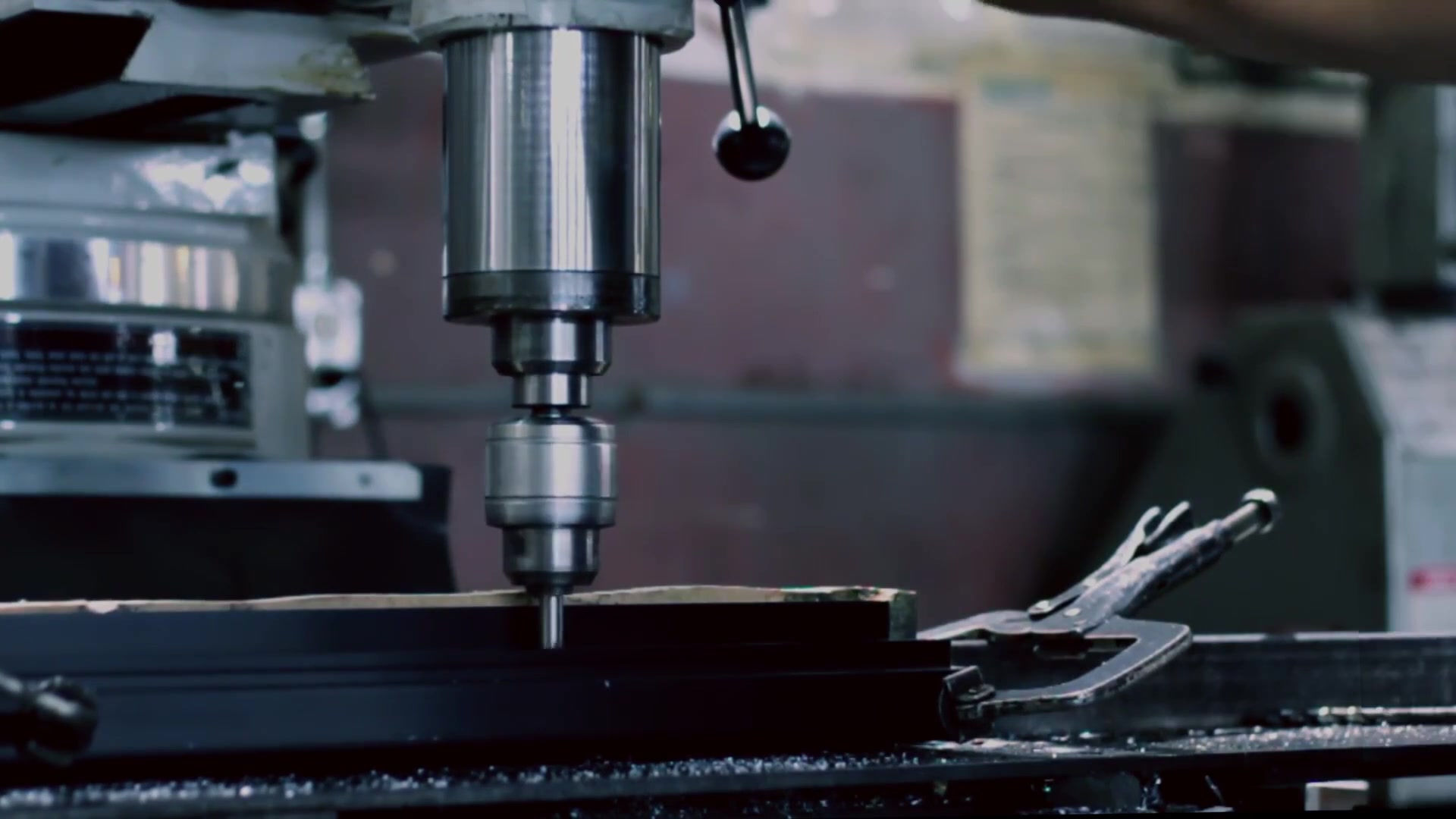
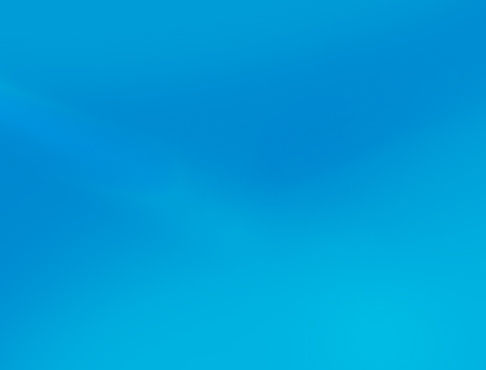
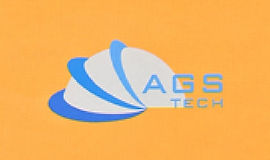
ผู้ผลิตที่กำหนดเองระดับโลก ผู้รวบรวม ผู้รวบรวม พันธมิตรเอาท์ซอร์สสำหรับผลิตภัณฑ์และบริการที่หลากหลาย
เราเป็นแหล่งข้อมูลครบวงจรสำหรับการผลิต การแปรรูป วิศวกรรม การรวมบัญชี การบูรณาการ การเอาท์ซอร์สผลิตภัณฑ์และบริการที่ผลิตขึ้นเองและนอกชั้นวาง
เลือกภาษาของคุณ
-
การผลิตแบบกำหนดเอง
-
การผลิตตามสัญญาในประเทศและทั่วโลก
-
การผลิตเอาท์ซอร์ส
-
การจัดซื้อจัดจ้างในประเทศและทั่วโลก
-
การรวมบัญชี
-
การรวมทางวิศวกรรม
-
บริการด้านวิศวกรรม
Search Results
พบ 164 ผลลัพธ์เมื่อไม่ระบุค่าการค้นหา
- Transmission Components, Belts, Chains, Cable Drives, Pulleys,AGS-TECH
Transmission Components, Belts, Chains and Cable Drives, Conventional & Grooved or Serrated, Positive Drive, Pulleys สายพาน & โซ่ & ชุดขับสายเคเบิล AGS-TECH Inc. ขอเสนอส่วนประกอบระบบส่งกำลังแก่คุณ รวมถึงสายพานและโซ่และชุดขับสายเคเบิล ด้วยการปรับแต่งเป็นเวลาหลายปี ยาง หนัง และสายพานไดรฟ์อื่นๆ ของเราจึงเบาลงและกะทัดรัดยิ่งขึ้น ซึ่งสามารถบรรทุกสัมภาระได้สูงขึ้นด้วยต้นทุนที่ต่ำลง ในทำนองเดียวกัน chain drive ของเราได้ผ่านการพัฒนาอย่างมากในช่วงเวลาหนึ่ง และให้ข้อได้เปรียบหลายประการแก่ลูกค้าของเรา ข้อดีบางประการของการใช้ตัวขับโซ่คือระยะห่างจากศูนย์กลางเพลาที่ค่อนข้างไม่จำกัด ความกะทัดรัด ความสะดวกในการประกอบ ความยืดหยุ่นในการตึงโดยไม่ลื่นหรือคืบ ความสามารถในการทำงานในสภาพแวดล้อมที่มีอุณหภูมิสูง เคเบิลไดรฟ์ของเรายังมีข้อดี เช่น ความเรียบง่ายในการใช้งานบางอย่างเหนือกว่าส่วนประกอบการส่งสัญญาณประเภทอื่นๆ มีทั้งแบบสายพาน แบบโซ่และแบบเคเบิล รวมทั้งแบบที่ประกอบขึ้นเองและแบบประกอบเอง เราสามารถผลิตส่วนประกอบระบบส่งกำลังเหล่านี้ได้ในขนาดที่เหมาะสมสำหรับการใช้งานของคุณและจากวัสดุที่เหมาะสมที่สุด สายพาน & สายพาน: - สายพานแบนทั่วไป: เป็นสายพานแบนเรียบไม่มีฟัน ร่อง หรือฟันปลา ตัวขับสายพานแบบแบนมีความยืดหยุ่น ดูดซับแรงกระแทกได้ดี ส่งกำลังได้อย่างมีประสิทธิภาพที่ความเร็วสูง ทนต่อการเสียดสี ต้นทุนต่ำ สายพานสามารถประกบหรือต่อเพื่อให้สายพานมีขนาดใหญ่ขึ้น ข้อดีอื่น ๆ ของสายพานแบนทั่วไปคือ สายพานบาง ไม่รับแรงเหวี่ยงหนีศูนย์กลางสูง (ทำให้ดีสำหรับการใช้งานความเร็วสูงด้วยรอกขนาดเล็ก) ในทางกลับกัน พวกเขากำหนดให้รับน้ำหนักบรรทุกสูง เนื่องจากสายพานแบบแบนต้องการแรงตึงสูง ข้อเสียอื่นๆ ของตัวขับสายพานแบนอาจลื่น การทำงานที่มีเสียงดัง และประสิทธิภาพค่อนข้างต่ำที่ความเร็วการทำงานต่ำและปานกลาง เรามีสายพานทั่วไปสองประเภท: สายพานเสริมและไม่เสริมแรง สายพานเสริมมีส่วนประกอบรับแรงดึงในโครงสร้าง สายพานแบบแบนทั่วไปมีให้เลือกทั้งแบบหนัง ผ้าหรือสายยาง ยางหรือพลาสติกที่ไม่เสริมแรง ผ้า หนังเสริมแรง เข็มขัดหนังมีอายุการใช้งานยาวนาน ยืดหยุ่น ค่าสัมประสิทธิ์การเสียดสีดีเยี่ยม ซ่อมแซมง่าย อย่างไรก็ตาม เข็มขัดหนังค่อนข้างแพง จำเป็นต้องตกแต่งและทำความสะอาดเข็มขัด และอาจหดตัวหรือยืดได้ขึ้นอยู่กับบรรยากาศ ผ้ายางหรือเข็มขัดรัดสายไฟทนต่อความชื้น กรดและด่าง เข็มขัดผ้ายางประกอบด้วยชั้นของผ้าฝ้ายหรือเป็ดสังเคราะห์ที่ชุบด้วยยางและเป็นวิธีที่ประหยัดที่สุด เข็มขัดรัดสายยางประกอบด้วยชั้นของสายที่หุ้มด้วยยาง เข็มขัดรัดสายยางมีความต้านทานแรงดึงสูงและขนาดและมวลที่พอเหมาะ สายพานยางหรือพลาสติกที่ไม่เสริมแรงเหมาะสำหรับงานเบาและขับด้วยความเร็วต่ำ สายพานยางและพลาสติกที่ไม่เสริมแรงสามารถยืดเข้าที่เหนือรอกได้ สายพานพลาสติกไม่เสริมแรงสามารถส่งกำลังได้สูงกว่าเมื่อเทียบกับสายพานยาง เข็มขัดหนังเสริมแรงประกอบด้วยชิ้นส่วนพลาสติกรับแรงดึงที่ประกบระหว่างชั้นบนและล่างของหนัง สุดท้าย เข็มขัดผ้าของเราอาจประกอบด้วยผ้าฝ้ายหรือเป็ดชิ้นเดียวพับและเย็บเป็นแถวของตะเข็บตามยาว สายพานผ้าสามารถติดตามได้อย่างสม่ำเสมอและทำงานด้วยความเร็วสูง - สายพานร่องหรือหยัก (เช่น สายพานร่องวี): สายพานเหล่านี้เป็นสายพานแบนพื้นฐานที่ดัดแปลงเพื่อให้มีข้อได้เปรียบของผลิตภัณฑ์เกียร์ประเภทอื่น เหล่านี้เป็นเข็มขัดแบนที่มีด้านล่างเป็นยางตามยาว สายพาน Poly-V เป็นสายพานแบนร่องตามยาวหรือหยักที่มีส่วนรับแรงดึงและร่องรูปตัววีที่อยู่ติดกันหลายชุดสำหรับการติดตามและการบีบอัด ความจุกำลังขึ้นอยู่กับความกว้างของสายพาน สายพานร่องวีเป็นตัวขับเคลื่อนของอุตสาหกรรมและมีจำหน่ายในขนาดและประเภทมาตรฐานที่หลากหลายสำหรับการส่งกำลังโหลดเกือบทุกประเภท ตัวขับสายพานรูปตัววีทำงานได้ดีระหว่าง 1500 ถึง 6000 ฟุต/นาที อย่างไรก็ตาม สายพานตัววีแบบแคบจะทำงานได้ถึง 10,000 ฟุต/นาที ตัวขับสายพานรูปตัววีมีอายุการใช้งานยาวนาน เช่น 3 ถึง 5 ปีและให้อัตราส่วนความเร็วที่มาก ง่ายต่อการติดตั้งและถอดออก ให้การทำงานที่เงียบ การบำรุงรักษาต่ำ การดูดซับแรงกระแทกที่ดีระหว่างตัวขับสายพานและเพลาขับ ข้อเสียของสายพานร่องวีคือการลื่นและการคืบ ดังนั้นอาจไม่ใช่ทางออกที่ดีที่สุดเมื่อต้องการความเร็วแบบซิงโครนัส เรามีสายพานอุตสาหกรรม ยานยนต์ และการเกษตร มีทั้งความยาวมาตรฐานและความยาวตามสั่งของสายพาน หน้าตัดสายพานร่องวีมาตรฐานทั้งหมดมีจำหน่ายในสต็อก มีตารางที่คุณสามารถคำนวณพารามิเตอร์ที่ไม่รู้จัก เช่น ความยาวสายพาน ส่วนของสายพาน (ความกว้าง & ความหนา) โดยให้คุณทราบพารามิเตอร์บางอย่างของระบบของคุณ เช่น เส้นผ่านศูนย์กลางของรอกขับและขับ ระยะกึ่งกลางระหว่างรอกและความเร็วรอบของรอก คุณสามารถใช้ตารางดังกล่าวหรือขอให้เราเลือกสายพานวีที่เหมาะกับคุณ - สายพานไดรฟ์ที่เป็นบวก (สายพานไทม์มิ่ง): สายพานเหล่านี้ยังเป็นแบบแบนด้วยชุดของฟันที่เว้นระยะเท่ากันบนเส้นรอบวงด้านใน สายพานไดรฟ์หรือสายพานไทม์มิ่งที่เป็นบวกรวมข้อดีของสายพานแบบแบนเข้ากับลักษณะการยึดเกาะที่เป็นบวกของโซ่และเฟือง สายพานไดรฟ์ที่เป็นบวกไม่เปิดเผยการลื่นไถลหรือการเปลี่ยนแปลงความเร็ว สามารถปรับอัตราส่วนความเร็วได้หลากหลาย ภาระแบริ่งต่ำเพราะสามารถทำงานได้ที่ความตึงเครียดต่ำ อย่างไรก็ตาม รอกเหล่านี้มีความอ่อนไหวต่อการวางแนวที่ไม่ถูกต้องในรอกมากขึ้น - รอก, มัด, ดุมสำหรับสายพาน: รอกประเภทต่างๆ ใช้กับสายพานไดรฟ์แบบแบน แบบยาง (หยัก) และแบบบวก เราผลิตทั้งหมด รอกสายพานแบบแบนส่วนใหญ่ของเราผลิตขึ้นจากการหล่อเหล็ก แต่รุ่นเหล็กก็มีให้เลือกหลากหลายแบบทั้งขอบล้อและดุมล้อ รอกสายพานแบนของเราอาจมีดุมล้อที่เป็นของแข็ง ซี่ล้อหรือดุมแยก หรือเราสามารถผลิตตามที่คุณต้องการ สายพานแบบมีซี่โครงและแบบไดรฟ์บวกมีให้เลือกหลายขนาดและความกว้างของสต็อก อย่างน้อยหนึ่งรอกในไดรฟ์ของสายพานราวลิ้นต้องติดหน้าแปลนเพื่อยึดสายพานไว้บนตัวขับ สำหรับระบบขับเคลื่อนตรงกลางแบบยาว ขอแนะนำให้ใช้หน้าแปลนรอกทั้งสองข้าง มัดเป็นล้อร่องของรอกและโดยทั่วไปผลิตโดยการหล่อเหล็ก การขึ้นรูปเหล็ก หรือการขึ้นรูปพลาสติก การขึ้นรูปเหล็กเป็นกระบวนการที่เหมาะสมในการผลิตม้วนยานยนต์และทางการเกษตร เราผลิตมัดที่มีร่องลึกและสม่ำเสมอ มู่เล่ร่องลึกมีความเหมาะสมอย่างยิ่งเมื่อสายพานร่องวีเข้าสู่มัดเป็นมุม เช่น กรณีในชุดขับสี่เลี้ยว ร่องลึกยังเหมาะอย่างยิ่งสำหรับการขับเคลื่อนเพลาแนวตั้งและการใช้งานที่อาจเกิดปัญหาการสั่นของสายพานได้ รอกคนเดินเตาะแตะของเราเป็นร่องรวงหรือรอกแบนที่ไม่ทำหน้าที่ส่งกำลังทางกล ส่วนใหญ่ใช้รอกคนเดินเตาะแตะเพื่อรัดเข็มขัด - ตัวขับสายพานเดี่ยวและหลายตัว: ตัวขับสายพานเดี่ยวมีร่องเดียวในขณะที่ตัวขับสายพานหลายตัวมีหลายร่อง คุณสามารถดาวน์โหลดแค็ตตาล็อกของเราได้โดยคลิกที่ข้อความสีที่เกี่ยวข้องด้านล่าง: - สายพานส่งกำลัง (รวมถึงสายพานร่องวี, สายพานราวลิ้น, สายพานขอบดิบ, สายพานแบบห่อและสายพานแบบพิเศษ) - สายพานลำเลียง - V-รอก - Timing Pulleys โซ่และตัวขับโซ่: โซ่ส่งกำลังของเรามีข้อดีบางประการ เช่น ระยะศูนย์กลางเพลาที่ค่อนข้างไม่จำกัด การประกอบที่ง่าย ความกะทัดรัด ความยืดหยุ่นภายใต้ความตึงเครียดโดยไม่เกิดการลื่นหรือคืบ ความสามารถในการทำงานภายใต้อุณหภูมิสูง ต่อไปนี้คือประเภทหลักของเครือข่ายของเรา: - โซ่ที่ถอดออกได้: โซ่ที่ถอดออกได้ของเราทำขึ้นในช่วงขนาด ระยะพิทช์ และความแข็งแกร่งสูงสุด และโดยทั่วไปแล้วจะทำมาจากเหล็กหรือเหล็กกล้าที่อ่อนนุ่ม โซ่แบบอ่อนได้ผลิตขึ้นในช่วงขนาดตั้งแต่ 0.902 (23 มม.) ถึง 4.063 นิ้ว (103 มม.) และความแข็งแกร่งสูงสุดตั้งแต่ 700 ถึง 17,000 ปอนด์/ตารางนิ้ว ในทางกลับกัน โซ่เหล็กที่ถอดออกได้ของเรามีขนาดตั้งแต่ 0.904 นิ้ว (23 มม.) ถึงประมาณ 3.00 นิ้ว (76 มม.) โดยมีความแข็งแรงสูงสุดตั้งแต่ 760 ถึง 5000 ปอนด์/ตารางนิ้ว_cc781905-5cde-3194-bb3b- 136bad5cf58d_ - Pintle Chains: โซ่เหล่านี้ใช้สำหรับการบรรทุกที่หนักกว่าและความเร็วที่สูงขึ้นเล็กน้อยถึงประมาณ 450 ฟุต/นาที (2.2 ม./วินาที) โซ่แบบ Pintle ทำจากข้อต่อแบบหล่อแต่ละอันที่มีปลายกระบอกกลมเต็มรูปแบบพร้อมแถบด้านข้างแบบออฟเซ็ต ตัวเชื่อมโซ่เหล่านี้เชื่อมต่อกันด้วยหมุดเหล็ก โซ่เหล่านี้มีระยะพิทช์ตั้งแต่ประมาณ 1.00 นิ้ว (25 มม.) ถึง 6.00 นิ้ว (150 มม.) และความแข็งแกร่งสูงสุดระหว่าง 3600 ถึง 30,000 ปอนด์/ตารางนิ้ว - Offset-Sidebar Chains: เป็นที่นิยมในกลุ่มขับเคลื่อนของเครื่องจักรก่อสร้าง โซ่เหล่านี้ทำงานด้วยความเร็ว 1,000 ฟุต/นาที และส่งน้ำหนักได้ประมาณ 250 แรงม้า โดยทั่วไปแล้ว แต่ละลิงก์จะมีแถบด้านข้างออฟเซ็ตสองอัน บูชหนึ่งอัน หนึ่งลูกกลิ้ง หนึ่งพิน และพินแบบผ่า - โซ่แบบลูกกลิ้ง: มีระยะพิทช์ตั้งแต่ 0.25 (6 มม.) ถึง 3.00 (75 มม.) นิ้ว ความแข็งแรงสูงสุดของโซ่แบบลูกกลิ้งความกว้างเดียวอยู่ระหว่าง 925 ถึง 130,000 ปอนด์/ตารางนิ้ว มีโซ่แบบลูกกลิ้งหลายรุ่นให้เลือกและส่งกำลังได้มากกว่าด้วยความเร็วสูงกว่า โซ่แบบลูกกลิ้งแบบหลายความกว้างยังให้การทำงานที่นุ่มนวลขึ้นพร้อมเสียงรบกวนที่ลดลง โซ่แบบลูกกลิ้งประกอบขึ้นจากลิงค์แบบลูกกลิ้งและแบบพินลิงค์ หมุดแบบ Cotter ใช้ในโซ่แบบลูกกลิ้งแบบถอดได้ การออกแบบตัวขับโซ่แบบลูกกลิ้งต้องใช้ความเชี่ยวชาญเฉพาะด้าน ในขณะที่ตัวขับสายพานขึ้นอยู่กับความเร็วเชิงเส้น ตัวขับโซ่จะขึ้นอยู่กับความเร็วในการหมุนของเฟืองที่เล็กกว่า ซึ่งอยู่ในการติดตั้งส่วนใหญ่เป็นตัวขับเคลื่อน นอกจากพิกัดแรงม้าและความเร็วในการหมุนแล้ว การออกแบบโซ่ขับเคลื่อนยังขึ้นอยู่กับปัจจัยอื่นๆ อีกมากมาย - Double-Pitch Chains: โดยทั่วไปจะเหมือนกับโซ่แบบลูกกลิ้ง เว้นแต่ระยะพิทช์จะยาวเป็นสองเท่า - Inverted Tooth (Silent) Chains: โซ่ความเร็วสูงที่ใช้เป็นหลักสำหรับตัวขับเคลื่อนหลัก ไดรฟ์โซ่ฟันแบบกลับด้านสามารถส่งกำลังได้ถึง 1200 แรงม้า และประกอบด้วยชุดข้อต่อฟัน ประกอบสลับกันด้วยหมุดหรือส่วนประกอบข้อต่อร่วมกัน โซ่ไกด์นำศูนย์มีลิงค์ไกด์เพื่อยึดร่องในเฟือง และโซ่ไกด์ข้างมีไกด์สำหรับยึดด้านข้างของเฟือง - Bead หรือ Slider Chains: โซ่เหล่านี้ใช้สำหรับไดรฟ์ความเร็วต่ำและในการใช้งานแบบแมนนวล คุณสามารถดาวน์โหลดแค็ตตาล็อกของเราได้โดยคลิกที่ข้อความสีที่เกี่ยวข้องด้านล่าง: - โซ่ขับ - โซ่ลำเลียง - โซ่ลำเลียงขนาดใหญ่ - โซ่ลูกกลิ้งสแตนเลส - รอกโซ่ - โซ่มอเตอร์ไซค์ - โซ่เครื่องจักรการเกษตร - เฟือง: เฟืองมาตรฐานของเราเป็นไปตามมาตรฐาน ANSI เฟืองจานเป็นเฟืองแบนไม่มีดุม เฟืองดุมขนาดเล็กและขนาดกลางของเราเปลี่ยนจากสต็อคแบบแท่งหรือการตีขึ้นรูป หรือทำโดยการเชื่อมดุมล้อแบบแท่งเข้ากับแผ่นรีดร้อน AGS-TECH Inc. สามารถจัดหาเฟืองที่กลึงจากการหล่อเหล็กสีเทา เหล็กหล่อและโครงสร้างดุมเชื่อม โลหะผงซินเตอร์ พลาสติกขึ้นรูปหรือกลึง เพื่อการทำงานที่ราบรื่นที่ความเร็วสูง การเลือกขนาดเฟืองที่เหมาะสมเป็นสิ่งสำคัญ แน่นอนว่าข้อจำกัดด้านพื้นที่เป็นปัจจัยที่เราไม่สามารถละเลยได้เมื่อเลือกเฟือง ขอแนะนำว่าอัตราส่วนของตัวขับต่อเฟืองขับไม่ควรเกิน 6:1 และพันโซ่ที่ตัวขับคือ 120 องศา ระยะห่างจากศูนย์กลางระหว่างเฟืองที่เล็กกว่าและใหญ่กว่า ความยาวโซ่ และความตึงโซ่ต้องถูกเลือกตามแนวทางและการคำนวณทางวิศวกรรมที่แนะนำบางประเภทด้วย ไม่ใช่แบบสุ่ม ดาวน์โหลดแคตตาล็อกของเราโดยคลิกข้อความสีด้านล่าง: - เฟืองและล้อจาน - บูชเกียร์ - ข้อต่อโซ่ - ล็อคโซ่ ตัวขับสายเคเบิล: สิ่งเหล่านี้มีข้อได้เปรียบเหนือสายพานและตัวขับโซ่ในบางกรณี ตัวขับสายเคเบิลสามารถทำหน้าที่เหมือนกับสายพานได้ และอาจใช้งานได้ง่ายกว่าและประหยัดกว่าในการใช้งานบางประเภท ตัวอย่างเช่น Synchromesh Cable Drives ซีรีส์ใหม่ได้รับการออกแบบมาเพื่อการยึดเกาะเชิงบวกเพื่อแทนที่เชือกทั่วไป สายเคเบิลธรรมดา และไดรฟ์ฟันเฟือง โดยเฉพาะอย่างยิ่งในพื้นที่แคบ เคเบิลไดรฟ์ใหม่ได้รับการออกแบบมาเพื่อให้ตำแหน่งที่มีความแม่นยำสูงในอุปกรณ์อิเล็กทรอนิกส์ เช่น เครื่องถ่ายเอกสาร เครื่องพล็อตเตอร์ เครื่องพิมพ์ดีด เครื่องพิมพ์….. เป็นต้น คุณสมบัติหลักของไดรฟ์สายเคเบิลใหม่คือความสามารถในการใช้ในการกำหนดค่า 3D Serpentine ซึ่งทำให้สามารถ การออกแบบที่เล็กมาก สายเคเบิล Synchromesh สามารถใช้กับความตึงเครียดที่ต่ำกว่าเมื่อเปรียบเทียบกับเชือกซึ่งช่วยลดการใช้พลังงาน ติดต่อ AGS-TECH สำหรับคำถามและความคิดเห็นเกี่ยวกับสายพาน โซ่ และตัวขับสายเคเบิล CLICK Product Finder-Locator Service หน้าก่อน
- Rapid Prototyping, Desktop Manufacturing, Additive Manufacturing, FDM
Rapid Prototyping, Desktop Manufacturing, Additive Manufacturing, Stereolithography, Polyjet, Fused Deposition Modeling, Selective Laser Sintering, FDM, SLS การผลิตสารเติมแต่งและรวดเร็ว ในช่วงไม่กี่ปีที่ผ่านมา เราได้เห็นความต้องการที่เพิ่มขึ้นสำหรับ RAPID MANUFACTURING หรือ RAPID PROTOTYPING กระบวนการนี้อาจเรียกอีกอย่างว่า DESKTOP MANUFACTURING หรือ FREE-FORM FABRICATION โดยพื้นฐานแล้ว โมเดลทางกายภาพที่เป็นของแข็งของชิ้นส่วนนั้นถูกสร้างขึ้นโดยตรงจากแบบร่าง CAD สามมิติ เราใช้คำว่า ADDITIVE MANUFACTURING สำหรับเทคนิคต่างๆ เหล่านี้ที่เราสร้างชิ้นส่วนในชั้นต่างๆ ด้วยการใช้ฮาร์ดแวร์และซอฟต์แวร์ที่ขับเคลื่อนด้วยคอมพิวเตอร์แบบบูรณาการ เราดำเนินการผลิตแบบเพิ่มเนื้อวัสดุ การสร้างต้นแบบอย่างรวดเร็วและเทคนิคการผลิตของเราคือ STEREOLITHOGRAPHY, POLYJET, FUSED-DEPOSITION MODELING, SELECTIVE LASER SINTERING, ELECTRON BEAM MELTING, การพิมพ์สามมิติ, การผลิตโดยตรง, RAPID TOOLING เราขอแนะนำให้คุณคลิกที่นี่เพื่อดาวน์โหลดภาพประกอบแผนผังของการผลิตสารเติมแต่งและกระบวนการผลิตที่รวดเร็วโดย AGS-TECH Inc. ข้อมูลนี้จะช่วยให้คุณเข้าใจข้อมูลที่เราให้ไว้ด้านล่างนี้ได้ดียิ่งขึ้น การสร้างต้นแบบอย่างรวดเร็วช่วยให้เรา: 1.) การออกแบบผลิตภัณฑ์ตามแนวคิดจะมองจากมุมต่างๆ บนจอภาพโดยใช้ระบบ 3D / CAD 2.) ต้นแบบจากวัสดุที่ไม่ใช่โลหะและโลหะได้รับการผลิตและศึกษาจากด้านการใช้งาน ด้านเทคนิค และด้านสุนทรียศาสตร์ 3.) การสร้างต้นแบบต้นทุนต่ำในเวลาอันสั้นทำได้สำเร็จ การผลิตแบบเติมเนื้อสามารถคล้ายกับการสร้างก้อนขนมปังโดยการซ้อนและพันแผ่นแต่ละชิ้นทับกัน กล่าวอีกนัยหนึ่งผลิตภัณฑ์ถูกผลิตขึ้นทีละชิ้นหรือทีละชั้นทีละชั้น ชิ้นส่วนส่วนใหญ่สามารถผลิตได้ภายในไม่กี่ชั่วโมง เทคนิคนี้ดีหากจำเป็นต้องใช้ชิ้นส่วนอย่างรวดเร็วหรือหากปริมาณที่ต้องการมีน้อย และการทำแม่พิมพ์และเครื่องมือมีราคาแพงเกินไปและต้องใช้เวลา อย่างไรก็ตามต้นทุนของชิ้นส่วนมีราคาแพงเนื่องจากวัตถุดิบราคาแพง • STEREOLITHOGRAPHY : เทคนิคนี้เรียกย่อ ๆ ว่า STL โดยอาศัยการบ่มและการชุบแข็งของโฟโตพอลิเมอร์เหลวให้เป็นรูปร่างเฉพาะโดยเน้นลำแสงเลเซอร์ไปที่นั้น เลเซอร์จะทำปฏิกิริยากับ photopolymer และรักษา โดยการสแกนลำแสงเลเซอร์ยูวีตามรูปร่างที่ตั้งโปรแกรมไว้ตามพื้นผิวของส่วนผสมโฟโตพอลิเมอร์ ชิ้นส่วนจะผลิตจากล่างขึ้นบนเป็นชิ้นๆ เรียงซ้อนกันเป็นชั้นๆ การสแกนจุดเลเซอร์ซ้ำหลายครั้งเพื่อให้ได้รูปทรงที่ตั้งโปรแกรมไว้ในระบบ หลังจากที่ผลิตชิ้นส่วนเสร็จแล้ว จะถูกลบออกจากแท่น ซับและทำความสะอาดด้วยคลื่นเสียงความถี่สูง และด้วยอ่างแอลกอฮอล์ ขั้นต่อไป จะสัมผัสกับรังสี UV เป็นเวลาสองสามชั่วโมงเพื่อให้แน่ใจว่าพอลิเมอร์ได้รับการบ่มและแข็งตัวเต็มที่ เพื่อสรุปกระบวนการ แท่นที่จุ่มลงในส่วนผสมโฟโตพอลิเมอร์และลำแสงเลเซอร์ยูวีจะถูกควบคุมและเคลื่อนผ่านระบบควบคุมเซอร์โวตามรูปร่างของชิ้นส่วนที่ต้องการ และได้ชิ้นส่วนโดยการโฟโตเคอร์ชั้นโพลิเมอร์ทีละชั้น แน่นอนว่าขนาดสูงสุดของชิ้นส่วนที่ผลิตขึ้นนั้นถูกกำหนดโดยอุปกรณ์สเตอริโอลิโธกราฟี • POLYJET : คล้ายกับการพิมพ์อิงค์เจ็ท ในโพลีเจ็ต เรามีหัวพิมพ์แปดหัวที่ติดโฟโตโพลีเมอร์บนถาดรองพิมพ์ แสงอัลตราไวโอเลตที่วางอยู่ข้างไอพ่นจะรักษาและแข็งตัวในแต่ละชั้นในทันที ใช้วัสดุสองชนิดในโพลิเจ็ท วัสดุชิ้นแรกสำหรับการผลิตแบบจำลองจริง วัสดุที่สอง ใช้เรซินคล้ายเจลเพื่อรองรับ วัสดุทั้งสองนี้ถูกฝากไว้ทีละชั้นและบ่มพร้อมกัน หลังจากสร้างแบบจำลองเสร็จแล้ว วัสดุสนับสนุนจะถูกลบออกด้วยสารละลายที่เป็นน้ำ เรซินที่ใช้มีความคล้ายคลึงกับ stereolithography (STL) โพลิเจ็ทมีข้อได้เปรียบเหนือ stereolithography ดังต่อไปนี้: 1.) ไม่จำเป็นต้องทำความสะอาดชิ้นส่วน 2.) ไม่จำเป็นต้องบ่มภายหลังกระบวนการ 3.) ความหนาของชั้นที่เล็กลงเป็นไปได้ ทำให้เราได้ความละเอียดที่ดีขึ้นและสามารถผลิตชิ้นส่วนที่ละเอียดกว่าได้ • FUSED DEPOSITION MODELING : ย่อมาจาก FDM ในวิธีนี้ หัวเครื่องอัดรีดที่ควบคุมด้วยหุ่นยนต์จะเคลื่อนที่ไปในทิศทางหลักสองทิศทางบนโต๊ะ สายเคเบิลถูกลดระดับและยกขึ้นตามต้องการ จากปากของแม่พิมพ์ที่ให้ความร้อนที่ศีรษะ เส้นใยเทอร์โมพลาสติกจะถูกอัดออกมาและชั้นเริ่มต้นจะวางอยู่บนฐานโฟม ทำได้โดยหัวเครื่องอัดรีดที่เป็นไปตามเส้นทางที่กำหนดไว้ หลังจากชั้นแรก ตารางจะลดลงและชั้นที่ตามมาจะถูกวางทับกัน บางครั้งเมื่อทำการผลิตชิ้นส่วนที่ซับซ้อน จำเป็นต้องมีโครงสร้างรองรับเพื่อให้การสะสมสามารถดำเนินต่อไปได้ในบางทิศทาง ในกรณีเหล่านี้ วัสดุรองรับจะถูกอัดด้วยระยะห่างของเส้นใยบนชั้นที่มีความหนาแน่นน้อยกว่าเพื่อให้มีความอ่อนแอกว่าวัสดุรุ่น โครงสร้างรองรับเหล่านี้สามารถละลายหรือแตกออกได้ในภายหลังหลังจากเสร็จสิ้นส่วน ขนาดแม่พิมพ์อัดรีดกำหนดความหนาของชั้นอัดรีด กระบวนการ FDM ผลิตชิ้นส่วนที่มีพื้นผิวเป็นขั้นบันไดบนระนาบภายนอกเฉียง หากไม่สามารถยอมรับความหยาบนี้ได้ สามารถใช้การขัดด้วยไอเคมีหรือเครื่องมือที่ให้ความร้อนเพื่อทำให้เรียบได้ แม้แต่ขี้ผึ้งขัดเงาก็สามารถใช้เป็นวัสดุเคลือบได้ เพื่อขจัดขั้นตอนเหล่านี้และบรรลุความคลาดเคลื่อนทางเรขาคณิตที่เหมาะสม • การเผาผนึกด้วยเลเซอร์แบบคัดเลือก : ยังแสดงเป็น SLS อีกด้วย กระบวนการนี้ขึ้นอยู่กับการเผาผนึกผงพอลิเมอร์ เซรามิก หรือโลหะที่คัดเลือกมาสู่วัตถุ ด้านล่างของห้องแปรรูปมีสองกระบอกสูบ: กระบอกสูบสำหรับประกอบชิ้นส่วนและกระบอกป้อนผง อันแรกถูกลดระดับทีละน้อยจนถึงตำแหน่งที่ส่วนซินเตอร์ถูกสร้างขึ้น และส่วนหลังถูกยกขึ้นทีละน้อยเพื่อส่งผงไปยังกระบอกสูบสำหรับสร้างชิ้นส่วนผ่านกลไกลูกกลิ้ง ขั้นแรก ผงแป้งบางๆ จะถูกสะสมในกระบอกสูบสำหรับประกอบชิ้นส่วน จากนั้นลำแสงเลเซอร์จะโฟกัสไปที่ชั้นนั้น ลากเส้นและหลอม/เผาส่วนตัดขวางเฉพาะ ซึ่งจะแข็งตัวเป็นของแข็ง ผงแป้งเป็นบริเวณที่ไม่โดนลำแสงเลเซอร์จะหลวมแต่ยังรองรับส่วนที่เป็นของแข็ง จากนั้นชั้นของผงอีกชั้นหนึ่งจะถูกฝากและกระบวนการซ้ำหลายครั้งเพื่อให้ได้ชิ้นส่วน ในตอนท้าย อนุภาคแป้งฝุ่นจะถูกสลัดออก ทั้งหมดนี้ดำเนินการโดยคอมพิวเตอร์ควบคุมกระบวนการโดยใช้คำแนะนำที่สร้างโดยโปรแกรม 3D CAD ของชิ้นส่วนที่ผลิต วัสดุต่างๆ เช่น โพลีเมอร์ (เช่น ABS, PVC, โพลีเอสเตอร์), ขี้ผึ้ง, โลหะและเซรามิกที่มีสารยึดเกาะโพลีเมอร์ที่เหมาะสมสามารถสะสมได้ • ELECTRON-BEAM MELTING : คล้ายกับการเผาผนึกด้วยเลเซอร์ แต่ใช้ลำแสงอิเล็กตรอนหลอมไททาเนียมหรือโคบอลต์โครมผงเพื่อสร้างต้นแบบในสุญญากาศ มีการพัฒนาบางอย่างเพื่อใช้ในกระบวนการนี้กับเหล็กกล้าไร้สนิม อะลูมิเนียม และโลหะผสมทองแดง หากจำเป็นต้องเพิ่มความแข็งแรงเมื่อยล้าของชิ้นส่วนที่ผลิตขึ้น เราใช้การกดไอโซสแตติกแบบร้อนภายหลังการผลิตชิ้นส่วนเป็นกระบวนการรอง • การพิมพ์สามมิติ : แสดงด้วย 3DP ในเทคนิคนี้ หัวพิมพ์จะเก็บสารยึดเกาะอนินทรีย์ไว้บนชั้นของผงโลหะหรืออโลหะ ลูกสูบที่บรรทุกเตียงผงจะถูกลดระดับทีละน้อยและในแต่ละขั้นตอน สารยึดเกาะจะถูกฝาก layer โดยชั้นและหลอมรวมโดยสารยึดเกาะ วัสดุผงที่ใช้ ได้แก่ โพลีเมอร์ผสมและเส้นใย ทรายโรงหล่อ โลหะ การใช้หัวยึดต่างๆ พร้อมกันและสารยึดเกาะสีต่างๆ ทำให้เราได้สีที่หลากหลาย กระบวนการนี้คล้ายกับการพิมพ์แบบอิงค์เจ็ต แต่แทนที่จะได้แผ่นสี เราได้วัตถุสามมิติที่มีสีแทน ชิ้นส่วนที่ผลิตได้อาจมีรูพรุน ดังนั้นจึงอาจต้องมีการเผาผนึกและการแทรกซึมของโลหะเพื่อเพิ่มความหนาแน่นและความแข็งแรง การเผาผนึกจะเผาสารยึดเกาะและหลอมผงโลหะเข้าด้วยกัน โลหะ เช่น สแตนเลส อะลูมิเนียม ไททาเนียม สามารถใช้ทำชิ้นส่วนได้ และโดยทั่วไปแล้วจะใช้ทองแดงและทองแดงเป็นวัสดุแทรกซึม ความงามของเทคนิคนี้คือการประกอบที่ซับซ้อนและเคลื่อนไหวได้นั้นสามารถผลิตได้อย่างรวดเร็ว ตัวอย่างเช่น การประกอบเฟือง สามารถทำประแจเป็นเครื่องมือได้ และจะมีชิ้นส่วนที่เคลื่อนที่และกลึงให้พร้อมใช้งาน ส่วนประกอบต่างๆ ของแอสเซมบลีสามารถผลิตได้ด้วยสีที่ต่างกันและทั้งหมดในครั้งเดียว ดาวน์โหลดโบรชัวร์ของเราได้ที่:พื้นฐานการพิมพ์ 3 มิติด้วยโลหะ • การผลิตโดยตรงและเครื่องมือด่วน : นอกจากการประเมินการออกแบบแล้ว การแก้ปัญหา เรายังใช้การสร้างต้นแบบอย่างรวดเร็วสำหรับการผลิตผลิตภัณฑ์โดยตรงหรือนำไปใช้ในผลิตภัณฑ์โดยตรง กล่าวอีกนัยหนึ่ง การสร้างต้นแบบอย่างรวดเร็วสามารถรวมเข้ากับกระบวนการทั่วไปเพื่อให้ดีขึ้นและแข่งขันได้มากขึ้น ตัวอย่างเช่น การสร้างต้นแบบอย่างรวดเร็วสามารถสร้างรูปแบบและแม่พิมพ์ได้ รูปแบบของพอลิเมอร์หลอมละลายและเผาไหม้ที่สร้างขึ้นโดยการดำเนินการสร้างต้นแบบอย่างรวดเร็วสามารถประกอบขึ้นเพื่อหล่อการลงทุนและลงทุนได้ อีกตัวอย่างหนึ่งที่กล่าวถึงคือการใช้ 3DP ในการผลิตเปลือกหล่อเซรามิกและใช้สำหรับการดำเนินการหล่อเปลือก แม้แต่แม่พิมพ์ฉีดและเม็ดมีดก็สามารถผลิตได้ด้วยการสร้างต้นแบบอย่างรวดเร็ว และสามารถช่วยประหยัดเวลาในการผลิตแม่พิมพ์ได้หลายสัปดาห์หรือหลายเดือน ด้วยการวิเคราะห์ไฟล์ CAD ของส่วนที่ต้องการเท่านั้น เราจึงสามารถผลิตรูปทรงของเครื่องมือโดยใช้ซอฟต์แวร์ได้ ต่อไปนี้คือวิธีการใช้เครื่องมือที่รวดเร็วซึ่งเป็นที่นิยมของเรา: RTV (Room-Temperature Vulcanizing) MOLDING / URETHANE CASTING : การใช้การสร้างต้นแบบอย่างรวดเร็วสามารถใช้เพื่อสร้างรูปแบบของชิ้นส่วนที่ต้องการได้ จากนั้นรูปแบบนี้เคลือบด้วยสารแยกส่วนและยาง RTV เหลวถูกเทลงบนลวดลายเพื่อผลิตแม่พิมพ์ครึ่งหนึ่ง ถัดไป แม่พิมพ์แบ่งครึ่งเหล่านี้ใช้สำหรับฉีดยูรีเทนเหลวสำหรับแม่พิมพ์ อายุการใช้งานของแม่พิมพ์สั้น เพียง 0 หรือ 30 รอบ แต่เพียงพอสำหรับการผลิตเป็นชุดเล็กๆ ACES (Acetal Clear Epoxy Solid) INJECTION MOLDING : การใช้เทคนิคการสร้างต้นแบบอย่างรวดเร็ว เช่น stereolithography เราผลิตแม่พิมพ์ฉีด แม่พิมพ์เหล่านี้เป็นเปลือกที่มีปลายเปิดเพื่อให้สามารถบรรจุวัสดุต่างๆ เช่น อีพ็อกซี่ อีพ็อกซี่ที่เติมอะลูมิเนียม หรือโลหะ อีกครั้งอายุการใช้งานของแม่พิมพ์ถูกจำกัดไว้ที่สิบหรือสูงสุดหลายร้อยชิ้นส่วน กระบวนการ SPRAYED METAL TOOLING : เราใช้การสร้างต้นแบบอย่างรวดเร็วและสร้างรูปแบบ เราพ่นโลหะผสมสังกะสีอลูมิเนียมลงบนพื้นผิวลวดลายแล้วเคลือบ ลวดลายที่เคลือบด้วยโลหะจะถูกวางไว้ในขวดและเคลือบด้วยอีพ็อกซี่หรืออีพ็อกซี่ที่เติมอลูมิเนียม ในที่สุด มันถูกเอาออกและโดยการผลิตแม่พิมพ์สองส่วนดังกล่าว เราจะได้แม่พิมพ์ที่สมบูรณ์สำหรับการฉีดขึ้นรูป แม่พิมพ์เหล่านี้มีอายุการใช้งานยาวนานขึ้น ในบางกรณีขึ้นอยู่กับวัสดุและอุณหภูมิที่พวกเขาสามารถผลิตชิ้นส่วนได้เป็นพันชิ้น KEELTOOL PROCESS : เทคนิคนี้สามารถผลิตแม่พิมพ์ที่มีอายุการใช้งาน 100,000 ถึง 10 ล้านรอบ การใช้การสร้างต้นแบบอย่างรวดเร็วทำให้เราผลิตแม่พิมพ์ RTV ต่อไปแม่พิมพ์จะเต็มไปด้วยส่วนผสมที่ประกอบด้วยผงเหล็กกล้าเครื่องมือ A6, ทังสเตนคาร์ไบด์, สารยึดเกาะโพลีเมอร์และปล่อยให้แห้ง แม่พิมพ์นี้จะถูกให้ความร้อนเพื่อให้พอลิเมอร์ถูกเผาและหลอมผงโลหะ ขั้นตอนต่อไปคือการแทรกซึมทองแดงเพื่อผลิตแม่พิมพ์ขั้นสุดท้าย หากจำเป็น สามารถใช้การทำงานรอง เช่น การตัดเฉือนและการขัดเงาบนแม่พิมพ์เพื่อให้ได้ขนาดที่แม่นยำยิ่งขึ้น CLICK Product Finder-Locator Service หน้าก่อน
- Composites, Composite Materials Manufacturing, Fiber Reinforced
Composites, Composite Materials Manufacturing, Particle and Fiber Reinforced, Cermets, Ceramic & Metal Composite, Glass Fiber Reinforced Polymer, Lay-Up Process การผลิตคอมโพสิตและวัสดุคอมโพสิต นิยามง่ายๆ ว่าคอมโพสิตหรือวัสดุคอมโพสิตเป็นวัสดุที่ประกอบด้วยวัสดุสองชนิดหรือหลายอย่างที่มีคุณสมบัติทางกายภาพหรือทางเคมีต่างกัน แต่เมื่อรวมกันแล้วจะกลายเป็นวัสดุที่แตกต่างจากวัสดุที่เป็นส่วนประกอบ เราต้องชี้ให้เห็นว่าวัสดุที่เป็นส่วนประกอบยังคงแยกจากกันและชัดเจนในโครงสร้าง เป้าหมายในการผลิตวัสดุคอมโพสิตคือการได้ผลิตภัณฑ์ที่เหนือกว่าส่วนประกอบและรวมคุณสมบัติที่ต้องการของแต่ละองค์ประกอบเข้าด้วยกัน ตัวอย่างเช่น; ความแข็งแรง น้ำหนักเบา หรือราคาที่ต่ำกว่า อาจเป็นแรงจูงใจเบื้องหลังการออกแบบและการผลิตคอมโพสิต ประเภทของคอมโพสิตที่เรานำเสนอ ได้แก่ คอมโพสิตเสริมแรงด้วยอนุภาค วัสดุคอมโพสิตเสริมแรงด้วยเส้นใย รวมถึงเซรามิก-เมทริกซ์ / พอลิเมอร์เมทริกซ์ / เมทัล-เมทริกซ์ / คาร์บอน-คาร์บอน / คอมโพสิตไฮบริด โครงสร้าง & ลามิเนต & คอมโพสิตที่มีโครงสร้างแบบแซนวิช และนาโนคอมโพสิต เทคนิคการผลิตที่เราปรับใช้ในการผลิตวัสดุคอมโพสิต ได้แก่ Pultrusion กระบวนการผลิตพรีเพก การจัดวางเส้นใยขั้นสูง การพันเส้นใย การจัดวางเส้นใยตามสั่ง กระบวนการวางสเปรย์ไฟเบอร์กลาส การทอ กระบวนการแลนไซด์ การตรึงซี วัสดุคอมโพสิตจำนวนมากประกอบด้วยสองเฟสคือเมทริกซ์ซึ่งต่อเนื่องและล้อมรอบอีกเฟสหนึ่ง และเฟสที่กระจัดกระจายซึ่งล้อมรอบด้วยเมทริกซ์ เราขอแนะนำให้คุณคลิกที่นี่เพื่อดาวน์โหลดภาพประกอบแผนผังของการผลิตคอมโพสิตและวัสดุคอมโพสิตโดย AGS-TECH Inc. ข้อมูลนี้จะช่วยให้คุณเข้าใจข้อมูลที่เราให้ไว้ด้านล่างนี้ได้ดียิ่งขึ้น • คอมโพสิตเสริมแรงด้วยอนุภาค : หมวดหมู่นี้ประกอบด้วยสองประเภท: คอมโพสิตอนุภาคขนาดใหญ่และคอมโพสิตเสริมแรงกระจาย ในประเภทเดิม ปฏิกิริยาระหว่างอนุภาคกับเมทริกซ์ไม่สามารถบำบัดได้ในระดับอะตอมหรือระดับโมเลกุล กลศาสตร์ความต่อเนื่องนั้นใช้ได้แทน ในทางกลับกัน ในอนุภาคคอมโพสิตที่มีการกระจายตัวเสริมมักจะมีขนาดเล็กกว่ามากในช่วงหลายสิบนาโนเมตร ตัวอย่างของคอมโพสิตอนุภาคขนาดใหญ่คือพอลิเมอร์ที่มีการเติมสารตัวเติม สารตัวเติมปรับปรุงคุณสมบัติของวัสดุและอาจแทนที่ปริมาณโพลีเมอร์บางส่วนด้วยวัสดุที่ประหยัดกว่า เศษส่วนปริมาตรของทั้งสองเฟสมีอิทธิพลต่อพฤติกรรมของคอมโพสิต วัสดุผสมอนุภาคขนาดใหญ่ใช้กับโลหะ โพลีเมอร์ และเซรามิก CERMETS เป็นตัวอย่างของวัสดุผสมเซรามิก/โลหะ เซอร์เม็ททั่วไปของเราคือซีเมนต์คาร์ไบด์ ประกอบด้วยเซรามิกคาร์ไบด์ทนไฟ เช่น อนุภาคทังสเตนคาร์ไบด์ในเมทริกซ์ของโลหะ เช่น โคบอลต์หรือนิกเกิล คาร์ไบด์คอมโพสิตเหล่านี้ใช้กันอย่างแพร่หลายเป็นเครื่องมือตัดสำหรับเหล็กชุบแข็ง อนุภาคของฮาร์ดคาร์ไบด์มีหน้าที่ในการตัด และความเหนียวของพวกมันก็เพิ่มขึ้นด้วยเมทริกซ์โลหะดัด ดังนั้นเราจึงได้รับประโยชน์จากวัสดุทั้งสองชนิดในคอมโพสิตชิ้นเดียว ตัวอย่างทั่วไปอีกตัวอย่างหนึ่งของคอมโพสิตอนุภาคขนาดใหญ่ที่เราใช้คืออนุภาคคาร์บอนแบล็คผสมกับยางวัลคาไนซ์เพื่อให้ได้คอมโพสิตที่มีความต้านทานแรงดึงสูง ความเหนียว การฉีกขาดและการขัดถู ตัวอย่างของคอมโพสิตเสริมแรงแบบกระจายคือ โลหะและโลหะผสมที่เสริมความแข็งแกร่งและชุบแข็งโดยการกระจายตัวของอนุภาคละเอียดที่สม่ำเสมอของวัสดุที่แข็งมากและเฉื่อย เมื่อเติมเกล็ดอะลูมิเนียมออกไซด์ขนาดเล็กมากลงในเมทริกซ์โลหะอะลูมิเนียม เราจะได้ผงอะลูมิเนียมเผาซึ่งมีความแข็งแรงในอุณหภูมิสูงมากขึ้น • คอมโพสิตเสริมไฟเบอร์ : หมวดหมู่ของคอมโพสิตนี้ในความเป็นจริงที่สำคัญที่สุด เป้าหมายที่จะบรรลุคือความแข็งแกร่งและความแข็งสูงต่อหน่วยน้ำหนัก องค์ประกอบของเส้นใย ความยาว การวางแนว และความเข้มข้นในคอมโพสิตเหล่านี้มีความสำคัญอย่างยิ่งในการพิจารณาคุณสมบัติและประโยชน์ของวัสดุเหล่านี้ เส้นใยที่เราใช้มีอยู่สามกลุ่ม: หนวดเครา เส้นใยและสายไฟ WHISKERS เป็นผลึกเดี่ยวที่บางและยาวมาก เป็นวัสดุที่แข็งแรงที่สุด ตัวอย่างวัสดุมัสสุ ได้แก่ กราไฟต์ ซิลิกอนไนไตรด์ อะลูมิเนียมออกไซด์ FIBERS ในทางกลับกัน ส่วนใหญ่เป็นโพลีเมอร์หรือเซรามิก และอยู่ในสถานะโพลีคริสตัลไลน์หรืออสัณฐาน กลุ่มที่สามคือ ลวดละเอียดที่มีเส้นผ่านศูนย์กลางค่อนข้างใหญ่ และมักประกอบด้วยเหล็กหรือทังสเตน ตัวอย่างของคอมโพสิตเสริมแรงด้วยลวดคือยางรถยนต์ที่มีลวดเหล็กอยู่ภายในยาง ขึ้นอยู่กับวัสดุเมทริกซ์ เรามีคอมโพสิตดังต่อไปนี้: คอมโพสิตโพลีเมอร์-เมทริกซ์ : ทำจากพอลิเมอร์เรซินและเส้นใยเป็นส่วนประกอบเสริมแรง กลุ่มย่อยของคอมโพสิตเหล่านี้เรียกว่า Glass Fiber-Reinforced Polymer (GFRP) ประกอบด้วยเส้นใยแก้วแบบต่อเนื่องหรือไม่ต่อเนื่องภายในพอลิเมอร์เมทริกซ์ แก้วมีความแข็งแรงสูง ประหยัด ง่ายต่อการประดิษฐ์เป็นเส้นใย และเฉื่อยทางเคมี ข้อเสียคือความแข็งแกร่งและความแข็งที่จำกัด อุณหภูมิการให้บริการอยู่ที่ 200 – 300 องศาเซลเซียสเท่านั้น ไฟเบอร์กลาสเหมาะสำหรับตัวถังรถยนต์และอุปกรณ์การขนส่ง ตัวถังยานพาหนะทางทะเล ภาชนะจัดเก็บ ไม่เหมาะสำหรับการทำการบินและอวกาศหรือสะพานเนื่องจากความแข็งแกร่งที่จำกัด กลุ่มย่อยอื่นเรียกว่า Carbon Fiber-Reinforced Polymer (CFRP) Composite คาร์บอนเป็นวัสดุเส้นใยของเราในเมทริกซ์พอลิเมอร์ คาร์บอนเป็นที่รู้จักสำหรับโมดูลัสและความแข็งแรงจำเพาะสูงและความสามารถในการรักษาอุณหภูมิเหล่านี้ไว้ที่อุณหภูมิสูง เส้นใยคาร์บอนสามารถนำเสนอโมดูลัสแรงดึงมาตรฐาน ปานกลาง สูง และสูงพิเศษแก่เรา นอกจากนี้ คาร์บอนไฟเบอร์ยังมีลักษณะทางกายภาพและทางกลที่หลากหลาย ดังนั้นจึงเหมาะสำหรับการใช้งานทางวิศวกรรมที่ปรับแต่งตามสั่งต่างๆ คอมโพสิต CFRP ถือได้ว่าเป็นการผลิตอุปกรณ์กีฬาและสันทนาการ ภาชนะรับความดัน และส่วนประกอบโครงสร้างการบินและอวกาศ อีกกลุ่มย่อยคือ Aramid Fiber-Reinforced Polymer Composites ยังเป็นวัสดุที่มีความแข็งแรงสูงและโมดูลัส อัตราส่วนความแข็งแรงต่อน้ำหนักสูงอย่างโดดเด่น เส้นใยอะรามิดมีชื่อทางการค้าว่า KEVLAR และ NOMEX ภายใต้ความตึงเครียด พวกมันทำงานได้ดีกว่าวัสดุเส้นใยโพลีเมอร์อื่น ๆ แต่พวกมันมีกำลังอัดน้อย เส้นใยอะรามิดมีความเหนียว ทนต่อแรงกระแทก ทนต่อการคืบคลานและเมื่อยล้า มีความเสถียรที่อุณหภูมิสูง เฉื่อยทางเคมี ยกเว้นกับกรดและเบสแก่ เส้นใยอะรามิดถูกนำมาใช้กันอย่างแพร่หลายในสินค้ากีฬา เสื้อเกราะกันกระสุน ยางรถยนต์ เชือก ปลอกสายไฟเบอร์ออปติก มีวัสดุเสริมแรงด้วยไฟเบอร์อื่นๆ อยู่แต่ใช้ในระดับที่น้อยกว่า เหล่านี้คือโบรอน, ซิลิกอนคาร์ไบด์, อะลูมิเนียมออกไซด์เป็นหลัก วัสดุพอลิเมอร์เมทริกซ์ก็มีความสำคัญเช่นกัน มันกำหนดอุณหภูมิการบริการสูงสุดของคอมโพสิตเนื่องจากพอลิเมอร์มีอุณหภูมิหลอมเหลวและการสลายตัวที่ต่ำกว่า โพลีเอสเตอร์และไวนิลเอสเทอร์ถูกนำมาใช้กันอย่างแพร่หลายในฐานะพอลิเมอร์เมทริกซ์ นอกจากนี้ยังใช้เรซินและมีความทนทานต่อความชื้นและคุณสมบัติทางกลที่ดีเยี่ยม ตัวอย่างเช่น เรซินโพลิอิไมด์สามารถใช้ได้สูงสุดประมาณ 230 องศาเซลเซียส. คอมโพสิตเมทัล-เมทริกซ์ : ในวัสดุเหล่านี้ เราใช้เมทริกซ์โลหะเหนียว และโดยทั่วไปอุณหภูมิการบริการจะสูงกว่าส่วนประกอบที่เป็นส่วนประกอบ เมื่อเปรียบเทียบกับคอมโพสิตพอลิเมอร์-เมทริกซ์ สิ่งเหล่านี้สามารถมีอุณหภูมิการทำงานที่สูงกว่า ไม่ติดไฟ และอาจต้านทานการย่อยสลายได้ดีกว่าสำหรับของเหลวอินทรีย์ อย่างไรก็ตามมีราคาแพงกว่า วัสดุเสริมแรง เช่น หนวดเครา อนุภาค เส้นใยต่อเนื่องและไม่ต่อเนื่อง และวัสดุเมทริกซ์ เช่น ทองแดง อลูมิเนียม แมกนีเซียม ไททาเนียม ซูเปอร์อัลลอย ตัวอย่างการใช้งาน ได้แก่ ส่วนประกอบเครื่องยนต์ที่ทำจากอลูมิเนียมอัลลอยด์เมทริกซ์เสริมด้วยอะลูมิเนียมออกไซด์และเส้นใยคาร์บอน CERAMIC-MATRIX COMPOSITES : วัสดุเซรามิกขึ้นชื่อเรื่องความน่าเชื่อถือในอุณหภูมิสูงที่ดีเยี่ยม อย่างไรก็ตามมีความเปราะบางและมีค่าความเหนียวแตกหักต่ำ ด้วยการฝังอนุภาค เส้นใย หรือเคราของเซรามิกหนึ่งเข้าไปในเมทริกซ์ของอีกเซรามิกหนึ่ง เราจึงสามารถบรรลุวัสดุคอมโพสิตที่มีความเหนียวในการแตกหักสูงขึ้น วัสดุฝังตัวเหล่านี้โดยทั่วไปจะยับยั้งการแพร่กระจายของรอยแตกภายในเมทริกซ์โดยกลไกบางอย่าง เช่น การเบี่ยงเบนปลายรอยแตกหรือการสร้างสะพานข้ามใบหน้ารอยแตก ตัวอย่างเช่น อลูมินาที่เสริมความแข็งแรงด้วยหนวดเครา SiC ถูกใช้เป็นเม็ดมีดเครื่องมือตัดสำหรับการตัดเฉือนโลหะผสมโลหะหนัก สิ่งเหล่านี้สามารถเปิดเผยประสิทธิภาพที่ดีขึ้นเมื่อเทียบกับซีเมนต์คาร์ไบด์ คาร์บอน-คาร์บอนคอมโพสิต : ทั้งการเสริมแรงและเมทริกซ์เป็นคาร์บอน มีโมดูลัสแรงดึงสูงและจุดแข็งที่อุณหภูมิสูงกว่า 2000 องศาเซลเซียส ความต้านทานการคืบ การแตกหักสูง ค่าสัมประสิทธิ์การขยายตัวทางความร้อนต่ำ การนำความร้อนสูง คุณสมบัติเหล่านี้ทำให้เหมาะอย่างยิ่งสำหรับการใช้งานที่ต้องการความต้านทานแรงกระแทกจากความร้อน จุดอ่อนของคอมโพสิตคาร์บอน - คาร์บอนคือความเสี่ยงต่อการเกิดออกซิเดชันที่อุณหภูมิสูง ตัวอย่างการใช้งานทั่วไป ได้แก่ แม่พิมพ์กดร้อน การผลิตชิ้นส่วนเครื่องยนต์กังหันขั้นสูง HYBRID COMPOSITES : เส้นใยที่แตกต่างกันตั้งแต่สองชนิดขึ้นไปผสมกันในเมทริกซ์เดียว เราสามารถปรับแต่งวัสดุใหม่ที่มีคุณสมบัติต่างๆ ร่วมกันได้ ตัวอย่างคือเมื่อทั้งคาร์บอนไฟเบอร์และเส้นใยแก้วรวมอยู่ในเรซินโพลีเมอร์ เส้นใยคาร์บอนให้ความแข็งและความแข็งแรงที่มีความหนาแน่นต่ำ แต่มีราคาแพง กระจกมีราคาถูกแต่ขาดความแข็งของเส้นใยคาร์บอน คอมโพสิตไฮบริดแบบแก้ว-คาร์บอนมีความแข็งแกร่งและแข็งแกร่งกว่า และสามารถผลิตได้ด้วยต้นทุนที่ต่ำลง การประมวลผลคอมโพสิตเสริมไฟเบอร์: สำหรับพลาสติกเสริมไฟเบอร์แบบต่อเนื่องที่มีเส้นใยกระจายสม่ำเสมอในทิศทางเดียวกัน เราใช้เทคนิคต่อไปนี้ PULTRUSION: ผลิตแท่ง คาน และท่อที่มีความยาวต่อเนื่องและหน้าตัดคงที่ เส้นใยเร่ร่อนอย่างต่อเนื่องถูกชุบด้วยเรซินเทอร์โมเซตติงและถูกดึงผ่านแม่พิมพ์เหล็กเพื่อเตรียมขึ้นรูปให้เป็นรูปร่างที่ต้องการ จากนั้น พวกเขาจะผ่านแม่พิมพ์สำหรับการบ่มด้วยเครื่องจักรที่มีความแม่นยำเพื่อให้ได้รูปร่างสุดท้าย เนื่องจากดายสำหรับบ่มถูกให้ความร้อน มันจึงทำการบ่มเมทริกซ์เรซิน ตัวดึงดึงวัสดุผ่านแม่พิมพ์ การใช้แกนกลวงที่สอดเข้าไป ทำให้เราได้ท่อและรูปทรงกลวง วิธีการพัลทรูชันเป็นแบบอัตโนมัติและให้อัตราการผลิตที่สูง สามารถผลิตผลิตภัณฑ์ความยาวเท่าใดก็ได้ กระบวนการผลิต PREPREG : Prepreg เป็นการเสริมแรงด้วยไฟเบอร์แบบต่อเนื่องที่เคลือบด้วยพอลิเมอร์เรซินที่บ่มบางส่วน ใช้กันอย่างแพร่หลายสำหรับงานโครงสร้าง วัสดุมาในรูปแบบเทปและจัดส่งเป็นเทป ผู้ผลิตหล่อขึ้นรูปโดยตรงและรักษาให้หายขาดโดยไม่ต้องเติมเรซินใดๆ เนื่องจากพรีเพกได้รับปฏิกิริยาการบ่มที่อุณหภูมิห้อง จึงถูกเก็บไว้ที่ 0 องศาเซลเซียสหรืออุณหภูมิต่ำกว่า หลังจากใช้เทปที่เหลือจะถูกเก็บไว้ที่อุณหภูมิต่ำ ใช้เรซินเทอร์โมพลาสติกและเทอร์โมเซตติงและเส้นใยเสริมแรงของคาร์บอน อะรามิดและแก้วเป็นเรื่องธรรมดา ในการใช้พรีเพรก จะต้องดึงกระดาษสำรองออกก่อน จากนั้นจึงทำการแปรรูปโดยการวางเทปพรีเพกลงบนพื้นผิวที่ใช้เครื่องมือ (กระบวนการวาง) สามารถวางซ้อนกันได้หลายชั้นเพื่อให้ได้ความหนาตามต้องการ การปฏิบัติบ่อยครั้งคือการสลับการวางแนวของเส้นใยเพื่อผลิตลามิเนตแบบ cross-ply หรือ angle-ply สุดท้ายใช้ความร้อนและแรงดันในการบ่ม ทั้งการประมวลผลด้วยมือและกระบวนการอัตโนมัติใช้สำหรับตัดพรีเพกและเลย์อัพ FILAMENT WINDING : เส้นใยเสริมแรงอย่างต่อเนื่องอยู่ในตำแหน่งที่ถูกต้องในรูปแบบที่กำหนดไว้ล่วงหน้าเพื่อให้เป็นไปตาม และมักจะมีรูปร่างเป็นวงกลม ขั้นแรก เส้นใยต้องผ่านอ่างเรซิน จากนั้นจึงพันบนแกนหมุนด้วยระบบอัตโนมัติ หลังจากการวนซ้ำหลายครั้งจะได้ความหนาที่ต้องการและทำการบ่มที่อุณหภูมิห้องหรือภายในเตาอบ ตอนนี้แมนเดรลจะถูกลบออกและผลิตภัณฑ์ถูกรื้อถอน การพันเส้นใยสามารถให้อัตราส่วนความแข็งแรงต่อน้ำหนักได้สูงมาก โดยการพันเส้นใยในรูปแบบเส้นรอบวง เกลียว และขั้ว ท่อ แท็งก์ ปลอก ผลิตด้วยเทคนิคนี้. • องค์ประกอบโครงสร้าง : โดยทั่วไปประกอบด้วยวัสดุที่เป็นเนื้อเดียวกันและวัสดุคอมโพสิต ดังนั้นคุณสมบัติของสิ่งเหล่านี้จึงถูกกำหนดโดยวัสดุที่เป็นส่วนประกอบและการออกแบบทางเรขาคณิตขององค์ประกอบต่างๆ นี่คือประเภทหลัก: ลามินาร์คอมโพสิต : วัสดุโครงสร้างเหล่านี้ทำจากแผ่นหรือแผงสองมิติที่มีทิศทางความแข็งแรงสูงที่ต้องการ ชั้นจะซ้อนกันและประสานเข้าด้วยกัน โดยการสลับทิศทางที่มีกำลังแรงสูงในแกนตั้งฉากสองแกน เราจะได้ส่วนประกอบที่มีความแข็งแรงสูงทั้งสองทิศทางในระนาบสองมิติ โดยการปรับมุมของชั้น เราสามารถผลิตคอมโพสิตที่มีความแข็งแรงในทิศทางที่ต้องการได้ สกีสมัยใหม่ผลิตด้วยวิธีนี้. แผงแซนวิช : โครงสร้างคอมโพสิตเหล่านี้มีน้ำหนักเบา แต่มีความแข็งและความแข็งแรงสูง แผงแซนวิชประกอบด้วยแผ่นชั้นนอกสองแผ่นที่ทำจากวัสดุที่แข็งและแข็งแรง เช่น โลหะผสมอลูมิเนียม พลาสติกเสริมเส้นใยหรือเหล็กกล้า และแกนกลางระหว่างแผ่นด้านนอก แกนกลางต้องมีน้ำหนักเบาและโดยส่วนใหญ่แล้วจะมีโมดูลัสความยืดหยุ่นต่ำ วัสดุหลักที่นิยมใช้ ได้แก่ โฟมโพลีเมอร์แข็ง ไม้ และรังผึ้ง แผงแซนวิชใช้กันอย่างแพร่หลายในอุตสาหกรรมก่อสร้าง เช่น วัสดุมุงหลังคา วัสดุพื้นหรือผนัง และในอุตสาหกรรมการบินและอวกาศ • NANOCOMPOSITES : วัสดุใหม่เหล่านี้ประกอบด้วยอนุภาคขนาดนาโนที่ฝังอยู่ในเมทริกซ์ การใช้นาโนคอมโพสิตทำให้เราสามารถผลิตวัสดุยางที่เป็นอุปสรรคต่อการซึมผ่านของอากาศได้ดีมาก ในขณะที่ยังคงรักษาคุณสมบัติของยางไว้ไม่เปลี่ยนแปลง CLICK Product Finder-Locator Service หน้าก่อน
- Machine Elements Manufacturing, Gears, Gear Drives, Bearings, Keys, Splines
Machine Elements Manufacturing, Gears, Gear Drives, Bearings, Keys, Splines, Pins, Shafts, Seals, Fasteners, Clutch, Cams, Followers, Belts, Couplings, Shafts การผลิตชิ้นส่วนเครื่องจักร อ่านเพิ่มเติม สายพาน & โซ่ & ชุดขับสายเคเบิล อ่านเพิ่มเติม ชุดเกียร์และเฟืองขับ อ่านเพิ่มเติม การผลิตข้อต่อและตลับลูกปืน อ่านเพิ่มเติม การผลิตกุญแจ & Splines & Pins อ่านเพิ่มเติม Cams & Followers & Linkages & Ratchet Wheels Manufacturing อ่านเพิ่มเติม การผลิตเพลา อ่านเพิ่มเติม การผลิตซีลเครื่องกล อ่านเพิ่มเติม ชุดคลัตช์และเบรก อ่านเพิ่มเติม การผลิตรัด อ่านเพิ่มเติม การประกอบเครื่องจักรอย่างง่าย MACHINE ELEMENTS are ส่วนประกอบพื้นฐานของเครื่อง องค์ประกอบเหล่านี้ประกอบด้วยสามประเภทพื้นฐาน: 1.) ส่วนประกอบโครงสร้าง ได้แก่ โครง แบริ่ง เพลา ร่องฟัน ตัวยึด ซีล และสารหล่อลื่น 2.) กลไกที่ควบคุมการเคลื่อนที่ในรูปแบบต่างๆ เช่น เกียร์เทรน สายพานหรือโซ่ ข้อต่อ ระบบลูกเบี้ยวและตัวตาม เบรกและคลัตช์ 3.) ส่วนประกอบควบคุม เช่น ปุ่ม สวิตช์ ไฟแสดง เซ็นเซอร์ แอคทูเอเตอร์ และตัวควบคุมคอมพิวเตอร์ องค์ประกอบของเครื่องจักรส่วนใหญ่ที่เรานำเสนอนั้นเป็นขนาดมาตรฐานทั่วไป แต่องค์ประกอบของเครื่องจักรที่สั่งทำขึ้นเองนั้นยังมีให้สำหรับการใช้งานเฉพาะทางของคุณ การปรับแต่งองค์ประกอบของเครื่องจักรสามารถเกิดขึ้นได้กับการออกแบบที่มีอยู่ซึ่งอยู่ในแค็ตตาล็อกที่ดาวน์โหลดได้ของเราหรือบนการออกแบบใหม่เอี่ยม การสร้างต้นแบบและการผลิตชิ้นส่วนเครื่องจักรสามารถดำเนินการต่อไปได้เมื่อการออกแบบได้รับการอนุมัติจากทั้งสองฝ่าย หากจำเป็นต้องออกแบบและผลิตส่วนประกอบของเครื่องจักรใหม่ ลูกค้าของเราอาจส่งอีเมลถึงพิมพ์เขียวของตนเองและเราจะตรวจสอบเพื่อขออนุมัติ หรือขอให้เราออกแบบองค์ประกอบของเครื่องจักรสำหรับการใช้งาน ในกรณีหลังนี้ เราใช้ข้อมูลทั้งหมดจากลูกค้าและออกแบบองค์ประกอบของเครื่องจักร และส่งพิมพ์เขียวที่สรุปผลไปยังลูกค้าของเราเพื่อขออนุมัติ เมื่อได้รับการอนุมัติแล้ว เราจะผลิตชิ้นส่วนแรกและต่อมาก็ผลิตส่วนประกอบของเครื่องจักรตามการออกแบบขั้นสุดท้าย ในทุกขั้นตอนของงานนี้ ในกรณีที่การออกแบบองค์ประกอบของเครื่องจักรทำงานได้อย่างไม่น่าพอใจในภาคสนาม (ซึ่งเกิดขึ้นได้ยาก) เราจะตรวจสอบโครงการทั้งหมดและทำการเปลี่ยนแปลงร่วมกับลูกค้าของเราตามความจำเป็น เป็นแนวทางปฏิบัติมาตรฐานของเราในการลงนามในข้อตกลงการไม่เปิดเผยข้อมูล (NDA) กับลูกค้าของเราสำหรับการออกแบบส่วนประกอบเครื่องจักรหรือผลิตภัณฑ์อื่นๆ เมื่อใดก็ตามที่จำเป็นหรือจำเป็น เมื่อองค์ประกอบของเครื่องจักรสำหรับลูกค้ารายใดรายหนึ่งได้รับการออกแบบและผลิตขึ้นเอง เราจะกำหนดรหัสผลิตภัณฑ์ให้กับส่วนประกอบนั้นและผลิตและขายให้กับลูกค้าที่เป็นเจ้าของผลิตภัณฑ์เท่านั้น เราทำซ้ำองค์ประกอบของเครื่องจักรโดยใช้เครื่องมือ แม่พิมพ์ และขั้นตอนที่พัฒนาขึ้นหลายครั้งตามความจำเป็นและทุกครั้งที่ลูกค้าสั่งซ้ำ กล่าวอีกนัยหนึ่ง เมื่อชิ้นส่วนเครื่องจักรแบบกำหนดเองได้รับการออกแบบและผลิตสำหรับคุณ ทรัพย์สินทางปัญญา ตลอดจนเครื่องมือและแม่พิมพ์ทั้งหมดจะถูกสงวนและจัดเก็บไว้อย่างไม่มีกำหนดโดยเราสำหรับคุณและผลิตภัณฑ์ที่ทำซ้ำได้ตามที่คุณต้องการ เรายังให้บริการด้านวิศวกรรมแก่ลูกค้าของเราด้วยการผสมผสานองค์ประกอบของเครื่องจักรเข้ากับส่วนประกอบหรือชุดประกอบที่สร้างสรรค์ซึ่งรองรับการใช้งานและตรงตามหรือเกินความคาดหวังของลูกค้า โรงงานที่ผลิตส่วนประกอบเครื่องจักรของเราผ่านการรับรองมาตรฐาน ISO9001, QS9000 หรือ TS16949 นอกจากนี้ ผลิตภัณฑ์ส่วนใหญ่ของเรามีเครื่องหมาย CE หรือ UL และเป็นไปตามมาตรฐานที่เกี่ยวข้องในระดับสากล เช่น ISO, SAE, ASME, DIN โปรดคลิกที่เมนูย่อยเพื่อรับข้อมูลโดยละเอียดเกี่ยวกับองค์ประกอบของเครื่องของเรา ซึ่งรวมถึง: - สายพาน โซ่ และตัวขับสายเคเบิล - เกียร์และเฟืองขับ - ข้อต่อและตลับลูกปืน - กุญแจ & Splines & หมุด - แคม & ลิงค์ - เพลา - ซีลเครื่องกล - คลัตช์และเบรกอุตสาหกรรม - รัด - เครื่องจักรง่าย ๆ เราได้เตรียมโบรชัวร์อ้างอิงสำหรับลูกค้า นักออกแบบ และผู้พัฒนาผลิตภัณฑ์ใหม่ ๆ รวมถึงองค์ประกอบของเครื่องจักร คุณสามารถทำความคุ้นเคยกับคำศัพท์ที่ใช้กันทั่วไปในการออกแบบส่วนประกอบเครื่องจักร: ดาวน์โหลดโบรชัวร์สำหรับข้อกำหนดทั่วไปทางวิศวกรรมเครื่องกลที่ใช้โดยนักออกแบบและวิศวกร องค์ประกอบของเครื่องจักรของเราค้นหาการใช้งานในหลากหลายสาขา เช่น เครื่องจักรอุตสาหกรรม ระบบอัตโนมัติ อุปกรณ์ทดสอบและมาตรวิทยา อุปกรณ์การขนส่ง เครื่องจักรก่อสร้าง และทุกที่ที่คุณนึกออก AGS-TECH พัฒนาและผลิตชิ้นส่วนเครื่องจักรจากวัสดุต่างๆ ขึ้นอยู่กับการใช้งาน วัสดุที่ใช้สำหรับชิ้นส่วนเครื่องจักรอาจมีตั้งแต่พลาสติกขึ้นรูปที่ใช้สำหรับของเล่น ไปจนถึงตัวเรือนชุบแข็งและเหล็กเคลือบพิเศษสำหรับเครื่องจักรอุตสาหกรรม นักออกแบบของเราใช้ซอฟต์แวร์ระดับมืออาชีพและเครื่องมือการออกแบบที่ทันสมัยสำหรับการพัฒนาองค์ประกอบของเครื่องจักร โดยคำนึงถึงรายละเอียดต่างๆ เช่น มุมของฟันเฟือง ความเค้นที่เกี่ยวข้อง อัตราการสึกหรอ….เป็นต้น โปรดเลื่อนดูเมนูย่อยของเราและดาวน์โหลดโบรชัวร์ผลิตภัณฑ์และแค็ตตาล็อกของเรา เพื่อดูว่าคุณสามารถค้นหาส่วนประกอบเครื่องนอกชั้นวางสำหรับแอปพลิเคชันของคุณได้หรือไม่ หากคุณไม่พบผลิตภัณฑ์ที่เหมาะกับการใช้งานของคุณ โปรดแจ้งให้เราทราบ แล้วเราจะทำงานร่วมกับคุณเพื่อพัฒนาและผลิตส่วนประกอบของเครื่องจักรที่จะตอบสนองความต้องการของคุณ หากคุณสนใจความสามารถด้านวิศวกรรมและการวิจัยและพัฒนามากกว่าความสามารถในการผลิต เราขอเชิญคุณเยี่ยมชมเว็บไซต์ของเรา http://www.ags-engineering.com ที่ซึ่งคุณสามารถค้นหาข้อมูลโดยละเอียดเพิ่มเติมเกี่ยวกับการออกแบบของเรา การพัฒนาผลิตภัณฑ์ การพัฒนากระบวนการ บริการให้คำปรึกษาด้านวิศวกรรม และอื่นๆ CLICK Product Finder-Locator Service หน้าก่อน
- Joining & Assembly & Fastening Processes, Welding, Brazing, Soldering
Joining & Assembly & Fastening Processes, Welding, Brazing, Soldering, Sintering, Adhesive Bonding, Press Fitting, Wave and Reflow Solder Process, Torch Furnace เข้าร่วม & ประกอบ & ยึดกระบวนการ เราเข้าร่วม ประกอบ และยึดชิ้นส่วนที่ผลิตขึ้นของคุณและเปลี่ยนให้เป็นผลิตภัณฑ์สำเร็จรูปหรือกึ่งสำเร็จรูปโดยใช้การเชื่อม การประสาน การบัดกรี การเผา การยึดติด การยึด การติดแน่น กระบวนการเชื่อมที่ได้รับความนิยมมากที่สุด ได้แก่ อาร์ค ก๊าซเชื้อเพลิงออกซี ความต้านทาน การฉายภาพ รอยต่อ การบิดเบี้ยว การกระทบกระแทก สถานะของแข็ง ลำแสงอิเล็กตรอน เลเซอร์ เทอร์มิท การเชื่อมแบบเหนี่ยวนำ กระบวนการประสานที่เป็นที่นิยมของเรา ได้แก่ การเชื่อมด้วยคบเพลิง การเหนี่ยวนำ เตาหลอม และการประสานแบบจุ่ม วิธีการบัดกรีของเราคือ การบัดกรีด้วยเหล็ก แผ่นร้อน เตาอบ การเหนี่ยวนำ การจุ่ม คลื่น การรีโฟลว์ และการบัดกรีด้วยอัลตราโซนิก สำหรับการยึดติดด้วยกาว เรามักใช้เทอร์โมพลาสติกและเทอร์โมเซ็ตติ้ง อีพ็อกซี่ ฟีนอลิก โพลียูรีเทน กาวอัลลอยด์ ตลอดจนสารเคมีและเทปอื่นๆ สุดท้าย กระบวนการยึดของเราประกอบด้วยการตอกตะปู การขันสกรู น็อตและโบลต์ การตอกย้ำ การรัด การตรึง การเย็บและการเย็บและการกด • การเชื่อม : การเชื่อมเกี่ยวข้องกับการเชื่อมวัสดุโดยการหลอมชิ้นงานและการแนะนำวัสดุตัวเติม ที่เชื่อมกับสระเชื่อมหลอมเหลวด้วย เมื่อบริเวณนั้นเย็นตัวลง เราก็จะได้ข้อต่อที่แข็งแรง ใช้แรงกดในบางกรณี ตรงกันข้ามกับการเชื่อม การประสานและการบัดกรีเกี่ยวข้องกับการหลอมของวัสดุที่มีจุดหลอมเหลวต่ำกว่าระหว่างชิ้นงานเท่านั้น และชิ้นงานจะไม่ละลาย เราขอแนะนำให้คุณคลิกที่นี่เพื่อดาวน์โหลดภาพประกอบแผนผังกระบวนการเชื่อมของเราโดย AGS-TECH Inc. ข้อมูลนี้จะช่วยให้คุณเข้าใจข้อมูลที่เราให้ไว้ด้านล่างนี้ได้ดียิ่งขึ้น ในการเชื่อมอาร์ค เราใช้แหล่งจ่ายไฟและอิเล็กโทรดเพื่อสร้างอาร์คไฟฟ้าที่หลอมโลหะ จุดเชื่อมมีการป้องกันด้วยก๊าซหรือไอระเหยหรือวัสดุอื่นๆ กระบวนการนี้เป็นที่นิยมสำหรับการเชื่อมชิ้นส่วนยานยนต์และโครงสร้างเหล็ก ในการเชื่อมอาร์กโลหะแบบ shelded (SMAW) หรือที่รู้จักในชื่อการเชื่อมแบบแท่ง แท่งอิเล็กโทรดจะถูกนำเข้ามาใกล้กับวัสดุฐานและอาร์กไฟฟ้าจะถูกสร้างขึ้นระหว่างกัน แท่งอิเล็กโทรดละลายและทำหน้าที่เป็นวัสดุตัวเติม อิเล็กโทรดยังมีฟลักซ์ที่ทำหน้าที่เป็นชั้นของตะกรันและปล่อยไอระเหยที่ทำหน้าที่เป็นก๊าซป้องกัน สิ่งเหล่านี้ปกป้องพื้นที่เชื่อมจากการปนเปื้อนสิ่งแวดล้อม ไม่มีการใช้สารตัวเติมอื่น ๆ ข้อเสียของกระบวนการนี้คือความช้า ต้องเปลี่ยนอิเล็กโทรดบ่อยๆ ความจำเป็นในการขจัดตะกรันที่ตกค้างที่เกิดจากฟลักซ์ โลหะหลายชนิด เช่น เหล็ก เหล็กกล้า นิกเกิล อะลูมิเนียม ทองแดง...เป็นต้น เชื่อมได้. ข้อดีของมันคือเครื่องมือราคาไม่แพงและใช้งานง่าย การเชื่อมอาร์กโลหะด้วยแก๊ส (GMAW) หรือที่เรียกว่าก๊าซเฉื่อยโลหะ (MIG) เรามีการป้อนลวดเติมอิเล็กโทรดแบบสิ้นเปลืองอย่างต่อเนื่องและก๊าซเฉื่อยหรือก๊าซเฉื่อยบางส่วนที่ไหลรอบลวดเพื่อป้องกันการปนเปื้อนของสิ่งแวดล้อมในบริเวณรอยเชื่อม สามารถเชื่อมเหล็ก อะลูมิเนียม และโลหะที่ไม่ใช่เหล็กอื่นๆ ได้ ข้อดีของ MIG คือความเร็วในการเชื่อมสูงและคุณภาพดี ข้อเสียคืออุปกรณ์ที่ซับซ้อนและความท้าทายที่ต้องเผชิญในสภาพแวดล้อมกลางแจ้งที่มีลมแรง เนื่องจากเราต้องรักษาก๊าซป้องกันรอบบริเวณเชื่อมให้คงที่ รูปแบบของ GMAW คือการเชื่อมอาร์กแบบใช้ฟลักซ์คอร์ (FCAW) ซึ่งประกอบด้วยท่อโลหะละเอียดที่บรรจุวัสดุฟลักซ์ บางครั้งฟลักซ์ภายในท่อก็เพียงพอสำหรับการป้องกันการปนเปื้อนของสิ่งแวดล้อม การเชื่อมอาร์กแบบจมอยู่ใต้น้ำ (SAW) เป็นกระบวนการอัตโนมัติอย่างกว้างขวาง ซึ่งเกี่ยวข้องกับการป้อนลวดอย่างต่อเนื่องและส่วนโค้งที่ถูกกระแทกภายใต้ชั้นของฝาครอบฟลักซ์ อัตราการผลิตและคุณภาพสูง ตะกรันเชื่อมหลุดออกมาได้ง่าย และเรามีสภาพแวดล้อมการทำงานที่ปลอดควัน ข้อเสียคือสามารถใช้เชื่อม parts ในบางตำแหน่งเท่านั้น ในการเชื่อมอาร์กทังสเตนก๊าซ (GTAW) หรือการเชื่อมก๊าซเฉื่อยทังสเตน (TIG) เราใช้อิเล็กโทรดทังสเตนพร้อมกับสารตัวเติมแยกต่างหากและก๊าซเฉื่อยหรือใกล้ก๊าซเฉื่อย ดังที่เราทราบ ทังสเตนมีจุดหลอมเหลวสูงและเป็นโลหะที่เหมาะสมมากสำหรับอุณหภูมิที่สูงมาก ทังสเตนใน TIG ไม่ถูกบริโภคโดยขัดกับวิธีอื่นๆ ที่อธิบายไว้ข้างต้น เทคนิคการเชื่อมที่ช้าแต่คุณภาพสูง ได้เปรียบกว่าเทคนิคอื่นๆ ในการเชื่อมวัสดุบาง เหมาะสำหรับโลหะหลายชนิด การเชื่อมอาร์กพลาสม่าจะคล้ายกันแต่ใช้แก๊สพลาสมาเพื่อสร้างอาร์ค ส่วนโค้งในการเชื่อมอาร์กพลาสมาค่อนข้างเข้มข้นกว่าเมื่อเปรียบเทียบกับ GTAW และสามารถใช้กับช่วงความหนาของโลหะได้กว้างกว่าด้วยความเร็วที่สูงกว่ามาก GTAW และการเชื่อมอาร์กพลาสมาสามารถนำไปใช้กับวัสดุที่เหมือนกันไม่มากก็น้อย OXY-FUEL / OXYFUEL WELDING เรียกอีกอย่างว่าการเชื่อมด้วย oxyacetylene, การเชื่อมด้วยออกซิเจน, การเชื่อมแก๊สจะดำเนินการโดยใช้เชื้อเพลิงก๊าซและออกซิเจนในการเชื่อม เนื่องจากไม่มีการใช้พลังงานไฟฟ้าจึงสามารถพกพาไปใช้ในที่ที่ไม่มีไฟฟ้าได้ การใช้หัวเชื่อมจะทำให้ชิ้นส่วนและวัสดุตัวเติมร้อนขึ้นเพื่อสร้างสระโลหะหลอมเหลวร่วมกัน สามารถใช้เชื้อเพลิงต่างๆ ได้ เช่น อะเซทิลีน น้ำมันเบนซิน ไฮโดรเจน โพรเพน บิวเทน...เป็นต้น ในการเชื่อมด้วยออกซิเจนเชื้อเพลิง เราใช้ภาชนะสองแบบ อันหนึ่งสำหรับเชื้อเพลิง และอีกอันสำหรับออกซิเจน ออกซิเจนออกซิไดซ์เชื้อเพลิง (เผาไหม้) การเชื่อมความต้านทาน: การเชื่อมประเภทนี้ใช้ประโยชน์จากความร้อนจูลและความร้อนจะถูกสร้างขึ้นที่ตำแหน่งที่ใช้กระแสไฟฟ้าในช่วงเวลาหนึ่ง กระแสสูงไหลผ่านโลหะ สระโลหะหลอมเหลวเกิดขึ้นที่ตำแหน่งนี้ วิธีการเชื่อมแบบต้านทานเป็นที่นิยมเนื่องจากมีประสิทธิภาพและมีโอกาสเกิดมลพิษน้อย อย่างไรก็ตาม ข้อเสียคือต้นทุนอุปกรณ์ค่อนข้างสำคัญและข้อจำกัดโดยธรรมชาติสำหรับชิ้นงานที่ค่อนข้างบาง SPOT WELDING เป็นการเชื่อมความต้านทานประเภทหนึ่งที่สำคัญ ที่นี่เราเชื่อมแผ่นหรือชิ้นงานที่ทับซ้อนกันตั้งแต่สองแผ่นขึ้นไปโดยใช้อิเล็กโทรดทองแดงสองตัวเพื่อยึดแผ่นเข้าด้วยกันและส่งกระแสสูงผ่านเข้าไป วัสดุระหว่างอิเล็กโทรดทองแดงจะร้อนขึ้นและเกิดแอ่งหลอมเหลวขึ้นที่ตำแหน่งนั้น จากนั้นกระแสไฟฟ้าจะหยุดและปลายอิเล็กโทรดทองแดงทำให้ตำแหน่งเชื่อมเย็นลงเนื่องจากอิเล็กโทรดระบายความร้อนด้วยน้ำ การใช้ความร้อนในปริมาณที่เหมาะสมกับวัสดุและความหนาที่เหมาะสมเป็นสิ่งสำคัญสำหรับเทคนิคนี้ เพราะหากใช้ผิดวิธีข้อต่อจะอ่อน การเชื่อมแบบจุดมีข้อดีที่ไม่ทำให้ชิ้นงานเสียรูปอย่างมีนัยสำคัญ ประหยัดพลังงาน ระบบอัตโนมัติที่ง่าย และอัตราการผลิตที่โดดเด่น และไม่ต้องมีสารเติมแต่งใดๆ ข้อเสียคือ เนื่องจากการเชื่อมเกิดขึ้นที่จุดแทนที่จะเป็นรอยต่อแบบต่อเนื่อง ความแข็งแรงโดยรวมจึงค่อนข้างต่ำเมื่อเทียบกับวิธีการเชื่อมอื่นๆ ในทางกลับกัน SEAM WELDING ทำให้เกิดรอยเชื่อมที่พื้นผิว faying ของวัสดุที่คล้ายคลึงกัน ตะเข็บสามารถชนหรือทับซ้อนกันได้ การเชื่อมตะเข็บเริ่มต้นที่ปลายด้านหนึ่งและค่อยๆ เคลื่อนไปยังอีกด้านหนึ่ง วิธีนี้ยังใช้อิเล็กโทรดสองขั้วจากทองแดงเพื่อใช้แรงดันและกระแสไปยังบริเวณรอยเชื่อม อิเล็กโทรดรูปแผ่นดิสก์หมุนด้วยการสัมผัสคงที่ตามแนวตะเข็บและทำการเชื่อมอย่างต่อเนื่อง ที่นี่เช่นกัน อิเล็กโทรดถูกระบายความร้อนด้วยน้ำ รอยเชื่อมมีความแข็งแรงและเชื่อถือได้ วิธีการอื่นๆ ได้แก่ เทคนิคการฉายภาพ การฉายแสง และเทคนิคการเชื่อมแบบบิดเบี้ยว การเชื่อมแบบ SOLID-STATE นั้นแตกต่างไปจากวิธีการก่อนหน้านี้ที่อธิบายข้างต้นเล็กน้อย การรวมตัวเกิดขึ้นที่อุณหภูมิต่ำกว่าอุณหภูมิหลอมเหลวของโลหะที่เชื่อมเข้าด้วยกันและไม่ใช้สารตัวเติมโลหะ อาจใช้แรงดันในบางกระบวนการ วิธีการต่างๆ คือ COEXTRUSION WELDING โดยที่โลหะที่แตกต่างกันจะถูกอัดรีดผ่านแม่พิมพ์เดียวกัน, COLD PRESSURE WELDING ซึ่งเราเชื่อมโลหะผสมอ่อนด้านล่างจุดหลอมเหลวของพวกมัน, DIFFUSION WELDING เทคนิคที่ไม่มีเส้นเชื่อมที่มองเห็นได้, EXPLOSION WELDING สำหรับการเชื่อมวัสดุที่ไม่เหมือนกัน เช่น โลหะผสมที่ทนต่อการกัดกร่อนเข้ากับโครงสร้าง เหล็กกล้า, ELECTROMAGNETIC PULSE WELDING ซึ่งเราเร่งความเร็วของท่อและแผ่นโดยแรงแม่เหล็กไฟฟ้า, FORGE WELDING ที่ประกอบด้วยการให้ความร้อนแก่โลหะจนถึงอุณหภูมิสูงและทุบเข้าด้วยกัน, FRICTION WELDING ซึ่งทำการเชื่อมด้วยแรงเสียดทานเพียงพอ, FRICTION STIR WELDING ที่เกี่ยวข้องกับการหมุนที่ไม่ เครื่องมือสิ้นเปลืองในแนวรอยต่อ HOT PRESSURE WELDING ซึ่งเรากดโลหะเข้าด้วยกันที่อุณหภูมิสูงกว่าอุณหภูมิหลอมเหลวในสุญญากาศหรือก๊าซเฉื่อย HOT ISOSTATIC PRESSURE WELDING กระบวนการที่เราใช้แรงดันโดยใช้ก๊าซเฉื่อยภายในภาชนะ ROLL WELDING ที่เราเข้าร่วม วัสดุที่ไม่เหมือนกันโดยการบังคับระหว่าง ล้อหมุนสองล้อ ULTRASONIC WELDING ซึ่งเชื่อมแผ่นโลหะหรือพลาสติกบาง ๆ โดยใช้พลังงานการสั่นสะเทือนความถี่สูง กระบวนการเชื่อมอื่นๆ ของเราคือ ELECTRON BEAM WELDING ที่มีการเจาะลึกและการประมวลผลที่รวดเร็ว แต่เป็นวิธีที่มีราคาแพง เราพิจารณาว่าเป็นกรณีพิเศษ ELECTROSLAG WELDING เป็นวิธีการที่เหมาะสมสำหรับแผ่นหนาหนักและชิ้นงานเหล็กเท่านั้น การเชื่อมแบบเหนี่ยวนำ ซึ่งเราใช้การเหนี่ยวนำแม่เหล็กไฟฟ้าและ ให้ความร้อนแก่ชิ้นงานที่เป็นสื่อกระแสไฟฟ้าหรือเฟอร์โรแมกเนติกของเรา LASER BEAM WELDING ด้วยการเจาะลึกและการประมวลผลที่รวดเร็ว แต่เป็นวิธีที่มีราคาแพง LASER HYBRID WELDING ที่รวม LBW กับ GMAW ในหัวเชื่อมเดียวกันและสามารถเชื่อมช่องว่างระหว่างเพลตได้ 2 มม. PERCUSSION WELDING ที่ เกี่ยวข้องกับการปล่อยไฟฟ้าตามด้วยการปลอมวัสดุด้วยแรงดันที่ใช้, THERMIT WELDING ซึ่งเกี่ยวข้องกับปฏิกิริยาคายความร้อนระหว่างผงอะลูมิเนียมและเหล็กออกไซด์, การเชื่อมด้วยไฟฟ้าด้วยอิเล็กโทรดสิ้นเปลืองและใช้กับเหล็กเฉพาะในตำแหน่งแนวตั้ง และสุดท้าย STUD ARC WELDING สำหรับการเชื่อมแบบสตั๊ดกับฐาน วัสดุที่มีความร้อนและแรงดัน เราขอแนะนำให้คุณคลิกที่นี่เพื่อดาวน์โหลดภาพประกอบแผนผังของกระบวนการประสาน การบัดกรี และการยึดติดด้วยกาวโดย AGS-TECH Inc ข้อมูลนี้จะช่วยให้คุณเข้าใจข้อมูลที่เราให้ไว้ด้านล่างนี้ได้ดียิ่งขึ้น • การประสาน : เราเชื่อมโลหะตั้งแต่สองชนิดขึ้นไปโดยการให้ความร้อนกับโลหะเติมระหว่างพวกมันเหนือจุดหลอมเหลวของพวกมัน และใช้การกระทำของเส้นเลือดฝอยเพื่อกระจาย กระบวนการนี้คล้ายกับการบัดกรี แต่อุณหภูมิที่เกี่ยวข้องกับการหลอมฟิลเลอร์จะสูงกว่าในการประสาน เช่นเดียวกับการเชื่อม ฟลักซ์จะปกป้องวัสดุตัวเติมจากการปนเปื้อนในชั้นบรรยากาศ หลังจากเย็นตัวแล้ว ชิ้นงานจะถูกเชื่อมเข้าด้วยกัน กระบวนการนี้เกี่ยวข้องกับขั้นตอนสำคัญดังต่อไปนี้: ความพอดีและระยะห่างที่ดี การทำความสะอาดวัสดุฐานที่เหมาะสม การติดตั้งที่เหมาะสม การเลือกฟลักซ์และบรรยากาศที่เหมาะสม การให้ความร้อนแก่ชุดประกอบ และสุดท้ายคือการทำความสะอาดชุดประกอบประสาน กระบวนการประสานบางส่วนของเราคือ TORCH BRAZING ซึ่งเป็นวิธีการยอดนิยมที่ดำเนินการด้วยตนเองหรือในลักษณะอัตโนมัติ เหมาะสำหรับใบสั่งผลิตปริมาณน้อยและกรณีพิเศษ ให้ความร้อนโดยใช้เปลวไฟแก๊สใกล้กับข้อต่อที่กำลังประสาน FURNACE BRAZING ต้องใช้ทักษะของผู้ปฏิบัติงานน้อยกว่า และเป็นกระบวนการกึ่งอัตโนมัติที่เหมาะสำหรับการผลิตจำนวนมากในภาคอุตสาหกรรม ทั้งการควบคุมอุณหภูมิและการควบคุมบรรยากาศในเตาเผาเป็นข้อดีของเทคนิคนี้ เนื่องจากวิธีแรกช่วยให้เราสามารถควบคุมวงจรความร้อนและขจัดความร้อนในท้องถิ่นได้เช่นเดียวกับในกรณีในการประสานด้วยหัวเทียน และส่วนหลังช่วยปกป้องชิ้นส่วนจากการเกิดออกซิเดชัน การใช้จิ๊กกิ้งทำให้เราสามารถลดต้นทุนการผลิตให้เหลือน้อยที่สุด ข้อเสียคือการใช้พลังงานสูง ต้นทุนอุปกรณ์ และการพิจารณาการออกแบบที่ท้าทายยิ่งขึ้น VACUUM BRAZING เกิดขึ้นในเตาสุญญากาศ รักษาความสม่ำเสมอของอุณหภูมิ และเราได้ข้อต่อที่สะอาดมาก ปราศจากฟลักซ์ และมีความเครียดตกค้างน้อยมาก การอบชุบด้วยความร้อนสามารถเกิดขึ้นได้ในระหว่างการประสานด้วยสุญญากาศ เนื่องจากความเค้นตกค้างต่ำเกิดขึ้นระหว่างรอบการให้ความร้อนและความเย็นที่ช้า ข้อเสียที่สำคัญคือค่าใช้จ่ายสูงเนื่องจากการสร้างสภาพแวดล้อมสูญญากาศเป็นกระบวนการที่มีราคาแพง อีกเทคนิคหนึ่ง DIP BRAZING รวมชิ้นส่วนที่ติดตั้งไว้ซึ่งใช้สารประสานกับพื้นผิวการผสมพันธุ์ จากนั้นจุ่มชิ้นส่วน fixtured ลงในอ่างที่มีเกลือหลอมเหลว เช่น โซเดียมคลอไรด์ (เกลือแกง) ซึ่งทำหน้าที่เป็นสื่อถ่ายเทความร้อนและฟลักซ์ ไม่รวมอากาศ ดังนั้นจึงไม่มีการเกิดออกไซด์ ในการประสานแบบเหนี่ยวนำ เราเชื่อมวัสดุด้วยโลหะเติมที่มีจุดหลอมเหลวต่ำกว่าวัสดุพื้นฐาน กระแสสลับจากขดลวดเหนี่ยวนำจะสร้างสนามแม่เหล็กไฟฟ้าซึ่งทำให้เกิดความร้อนเหนี่ยวนำบนวัสดุแม่เหล็กที่เป็นเหล็กเป็นส่วนใหญ่ วิธีการนี้ให้ความร้อนที่เลือกสรร ข้อต่อที่ดีกับสารตัวเติมที่ไหลเฉพาะในบริเวณที่ต้องการ เกิดปฏิกิริยาออกซิเดชันเพียงเล็กน้อยเนื่องจากไม่มีเปลวไฟ และการทำความเย็นทำได้รวดเร็ว ให้ความร้อนอย่างรวดเร็ว ความสม่ำเสมอ และความเหมาะสมสำหรับการผลิตในปริมาณมาก เพื่อเร่งกระบวนการของเราและเพื่อให้มั่นใจถึงความสม่ำเสมอ เรามักใช้พรีฟอร์ม ข้อมูลเกี่ยวกับโรงงานประสานของเราที่ผลิตอุปกรณ์เซรามิกกับโลหะ การปิดผนึกสุญญากาศ การป้อนผ่านสุญญากาศ ส่วนประกอบควบคุมสุญญากาศและของเหลวสูงและสูงและสูงพิเศษ สามารถพบได้ที่นี่: โบรชัวร์โรงงานประสาน • การบัดกรี : ในการบัดกรี เราไม่มีการหลอมของชิ้นงาน แต่เป็นโลหะเติมที่มีจุดหลอมเหลวต่ำกว่าส่วนเชื่อมที่ไหลเข้าสู่ข้อต่อ โลหะเติมในการบัดกรีหลอมที่อุณหภูมิต่ำกว่าในการประสาน เราใช้โลหะผสมไร้สารตะกั่วสำหรับการบัดกรีและเป็นไปตามข้อกำหนด RoHS และสำหรับการใช้งานและข้อกำหนดที่แตกต่างกัน เรามีโลหะผสมที่แตกต่างกันและเหมาะสม เช่น โลหะผสมเงิน การบัดกรีมีข้อต่อที่เป็นแก๊สและของเหลวแน่นหนา ใน SOFT SOLDERING โลหะเติมของเรามีจุดหลอมเหลวต่ำกว่า 400 องศาเซลเซียส ในขณะที่ SILVER SOLDERING และ BRAZING เราต้องการอุณหภูมิที่สูงขึ้น การบัดกรีอ่อนใช้อุณหภูมิที่ต่ำกว่า แต่ไม่ส่งผลให้มีข้อต่อที่แข็งแรงสำหรับการใช้งานที่ต้องการอุณหภูมิสูง ในทางกลับกัน การบัดกรีด้วยเงินต้องใช้อุณหภูมิสูงจากคบเพลิง และทำให้เรามีข้อต่อที่แข็งแรงเหมาะสำหรับการใช้งานที่อุณหภูมิสูง การประสานต้องใช้อุณหภูมิสูงสุดและมักใช้ไฟฉาย เนื่องจากข้อต่อประสานมีความแข็งแรงมาก จึงเหมาะสำหรับการซ่อมแซมวัตถุที่เป็นเหล็กหนัก ในสายการผลิตของเรา เราใช้ทั้งการบัดกรีด้วยมือและสายบัดกรีอัตโนมัติ INDUCTION SOLDERING ใช้กระแสไฟ AC ความถี่สูงในขดลวดทองแดงเพื่ออำนวยความสะดวกในการทำความร้อนแบบเหนี่ยวนำ กระแสไฟฟ้าถูกเหนี่ยวนำให้เกิดในส่วนที่บัดกรีและเป็นผลให้ความร้อนเกิดขึ้นที่ความต้านทานสูง joint ความร้อนนี้ทำให้โลหะฟิลเลอร์ละลาย นอกจากนี้ยังใช้ฟลักซ์ การบัดกรีแบบเหนี่ยวนำเป็นวิธีที่ดีสำหรับการบัดกรีไซเคิลเดอร์และท่อในกระบวนการต่อเนื่องโดยการพันคอยล์รอบๆ การบัดกรีวัสดุบางชนิด เช่น กราไฟต์และเซรามิกทำได้ยากกว่า เนื่องจากต้องชุบชิ้นงานด้วยโลหะที่เหมาะสมก่อนทำการบัดกรี สิ่งนี้อำนวยความสะดวกในการเชื่อมประสานระหว่างใบหน้า เราประสานวัสดุดังกล่าวโดยเฉพาะสำหรับการใช้งานบรรจุภัณฑ์แบบสุญญากาศ เราผลิตแผงวงจรพิมพ์ (PCB) ในปริมาณมากโดยส่วนใหญ่ใช้ WAVE SOLDERING สำหรับวัตถุประสงค์ในการสร้างต้นแบบเพียงเล็กน้อยเท่านั้น เราใช้การบัดกรีด้วยมือโดยใช้หัวแร้ง เราใช้การบัดกรีด้วยคลื่นสำหรับทั้งชุดประกอบ PCB แบบรูทะลุและแบบยึดพื้นผิว (PCBA) กาวชั่วคราวช่วยให้ส่วนประกอบติดอยู่กับแผงวงจรและวางส่วนประกอบไว้บนสายพานลำเลียงและเคลื่อนผ่านอุปกรณ์ที่มีสารบัดกรีหลอมเหลว ขั้นแรกให้ PCB ถูกฟลักซ์แล้วเข้าสู่โซนอุ่นล่วงหน้า บัดกรีหลอมเหลวอยู่ในกระทะและมีรูปแบบของคลื่นนิ่งบนพื้นผิว เมื่อ PCB เคลื่อนที่ผ่านคลื่นเหล่านี้ คลื่นเหล่านี้จะสัมผัสกับด้านล่างของ PCB และยึดติดกับแผ่นบัดกรี บัดกรีจะอยู่บนหมุดและแผ่นรองเท่านั้น ไม่ใช่บน PCB คลื่นในบัดกรีหลอมเหลวจะต้องได้รับการควบคุมอย่างดีเพื่อไม่ให้กระเด็นและยอดคลื่นไม่สัมผัสและปนเปื้อนบริเวณที่ไม่ต้องการของกระดาน ใน REFLOW SOLDERING เราใช้แท่งบัดกรีเหนียวเพื่อติดส่วนประกอบอิเล็กทรอนิกส์เข้ากับบอร์ดชั่วคราว จากนั้นนำแผงเข้าเตาอบรีโฟลว์ที่มีการควบคุมอุณหภูมิ ที่นี่ประสานละลายและเชื่อมต่อส่วนประกอบอย่างถาวร เราใช้เทคนิคนี้สำหรับทั้งส่วนประกอบยึดพื้นผิวและส่วนประกอบผ่านรู การควบคุมอุณหภูมิและการปรับอุณหภูมิเตาอบอย่างเหมาะสมเป็นสิ่งสำคัญเพื่อหลีกเลี่ยงการทำลายส่วนประกอบอิเล็กทรอนิกส์บนบอร์ดโดยทำให้อุณหภูมิสูงเกินขีดจำกัดอุณหภูมิสูงสุด ในกระบวนการบัดกรีแบบรีโฟลว์ จริง ๆ แล้วเรามีหลายส่วนหรือหลายขั้นตอน โดยแต่ละส่วนมีโปรไฟล์ความร้อนที่แตกต่างกัน เช่น ขั้นตอนการอุ่น ขั้นตอนการแช่ด้วยความร้อน การไหลซ้ำ และขั้นตอนการทำความเย็น ขั้นตอนต่างๆ เหล่านี้มีความจำเป็นสำหรับการบัดกรีแบบรีโฟลว์ของส่วนประกอบแผงวงจรพิมพ์ (PCBA) โดยปราศจากความเสียหาย ULTRASONIC SOLDERING เป็นอีกหนึ่งเทคนิคที่ใช้บ่อยซึ่งมีความสามารถเฉพาะตัว - สามารถใช้ในการบัดกรีแก้ว เซรามิก และวัสดุที่ไม่ใช่โลหะ ตัวอย่างเช่น แผงโซลาร์เซลล์ซึ่งเป็นอิเล็กโทรดแบบไม่ต้องใช้โลหะ ซึ่งสามารถติดโดยใช้เทคนิคนี้ ในการบัดกรีด้วยคลื่นเสียงความถี่สูง เราใช้ปลายหัวแร้งที่ให้ความร้อนซึ่งส่งเสียงสั่นสะเทือนด้วยคลื่นเสียงความถี่สูงด้วย การสั่นสะเทือนเหล่านี้ทำให้เกิดฟองอากาศคาวิเทชันที่ส่วนต่อประสานของซับสเตรตกับวัสดุประสานที่หลอมเหลว พลังงานระเบิดของการเกิดโพรงอากาศจะปรับเปลี่ยนพื้นผิวออกไซด์และขจัดสิ่งสกปรกและออกไซด์ ในช่วงเวลานี้จะเกิดชั้นโลหะผสมขึ้นด้วย ประสานที่พื้นผิวพันธะรวมออกซิเจนและทำให้เกิดพันธะร่วมที่แข็งแกร่งระหว่างแก้วและประสาน DIP SOLDERING ถือได้ว่าเป็นการบัดกรีแบบคลื่นที่ง่ายกว่าซึ่งเหมาะสำหรับการผลิตขนาดเล็กเท่านั้น ใช้ฟลักซ์การทำความสะอาดครั้งแรกเช่นเดียวกับกระบวนการอื่นๆ PCB ที่มีส่วนประกอบที่ติดตั้งอยู่จะถูกจุ่มด้วยมือหรือในลักษณะกึ่งอัตโนมัติลงในถังที่มีสารบัดกรีหลอมเหลว บัดกรีหลอมเหลวเกาะติดกับบริเวณที่เป็นโลหะที่ไม่มีการป้องกันโดยหน้ากากประสานบนกระดาน อุปกรณ์นั้นเรียบง่ายและราคาไม่แพง • การยึดติดด้วยกาว : นี่เป็นอีกหนึ่งเทคนิคยอดนิยมที่เราใช้บ่อยและเกี่ยวข้องกับการยึดติดของพื้นผิวโดยใช้กาว อีพ็อกซี่ สารพลาสติก หรือสารเคมีอื่นๆ พันธะทำได้โดยการระเหยตัวทำละลาย โดยการบ่มด้วยความร้อน โดยการบ่มด้วยแสงยูวี โดยการบ่มด้วยแรงดันหรือรอระยะเวลาหนึ่ง กาวประสิทธิภาพสูงหลายชนิดใช้ในสายการผลิตของเรา ด้วยการใช้งานทางวิศวกรรมที่เหมาะสมและกระบวนการบ่ม การยึดติดด้วยกาวอาจส่งผลให้พันธะความเค้นต่ำมากซึ่งมีความแข็งแรงและเชื่อถือได้ กาวยึดติดสามารถป้องกันปัจจัยแวดล้อมได้ดี เช่น ความชื้น สิ่งปนเปื้อน สารกัดกร่อน แรงสั่นสะเทือน...เป็นต้น ข้อดีของการยึดติดด้วยกาวคือ สามารถนำไปใช้กับวัสดุที่อาจบัดกรี เชื่อม หรือประสานได้ยาก นอกจากนี้ยังเหมาะสำหรับวัสดุที่ไวต่อความร้อนที่อาจได้รับความเสียหายจากการเชื่อมหรือกระบวนการที่มีอุณหภูมิสูงอื่นๆ ข้อดีอื่นๆ ของกาวคือสามารถนำไปใช้กับพื้นผิวที่มีรูปร่างไม่สม่ำเสมอ และเพิ่มน้ำหนักในการประกอบโดยใช้ปริมาณที่น้อยมากเมื่อเทียบกับวิธีอื่นๆ การเปลี่ยนแปลงมิติในส่วนต่างๆ ก็น้อยมากเช่นกัน กาวบางชนิดมีคุณสมบัติการจับคู่ดัชนีและสามารถใช้ระหว่างส่วนประกอบออปติคัลโดยไม่ลดความแรงของแสงหรือสัญญาณออปติคัลอย่างมีนัยสำคัญ ในทางกลับกัน ข้อเสียคือเวลาในการบ่มนานขึ้น ซึ่งอาจทำให้สายการผลิตช้าลง ข้อกำหนดในการตรึง การเตรียมพื้นผิว และความยากลำบากในการถอดประกอบเมื่อจำเป็นต้องทำใหม่ การยึดติดด้วยกาวส่วนใหญ่ของเรามีขั้นตอนดังต่อไปนี้: - การรักษาพื้นผิว: ขั้นตอนการทำความสะอาดพิเศษ เช่น การทำความสะอาดด้วยน้ำปราศจากไอออน การทำความสะอาดแอลกอฮอล์ การทำความสะอาดด้วยพลาสม่าหรือโคโรนาเป็นเรื่องปกติ หลังจากทำความสะอาดแล้ว เราอาจใช้โปรโมเตอร์การยึดเกาะบนพื้นผิวเพื่อให้มั่นใจว่าข้อต่อที่ดีที่สุด - การติดตั้งชิ้นส่วน: สำหรับการใช้งานทั้งการติดกาวและการบ่ม เราออกแบบและใช้ฟิกซ์เจอร์แบบกำหนดเอง - การติดกาว: บางครั้งเราใช้แบบแมนนวล และบางครั้งขึ้นอยู่กับกรณีของระบบอัตโนมัติ เช่น หุ่นยนต์ เซอร์โวมอเตอร์ ตัวกระตุ้นเชิงเส้น เพื่อส่งกาวไปยังตำแหน่งที่ถูกต้อง และเราใช้เครื่องจ่ายเพื่อส่งมอบในปริมาณและปริมาณที่เหมาะสม - การบ่ม: เราอาจใช้การทำให้แห้งและการบ่มอย่างง่าย รวมถึงการบ่มภายใต้แสงยูวีที่ทำหน้าที่เป็นตัวเร่งปฏิกิริยาหรือการบ่มด้วยความร้อนในเตาอบ หรือใช้องค์ประกอบความร้อนต้านทานที่ติดตั้งบนจิ๊กและฟิกซ์เจอร์ ทั้งนี้ขึ้นอยู่กับกาว เราขอแนะนำให้คุณคลิกที่นี่เพื่อดาวน์โหลดภาพประกอบแผนผังของกระบวนการยึดโดย AGS-TECH Inc. ข้อมูลนี้จะช่วยให้คุณเข้าใจข้อมูลที่เราให้ไว้ด้านล่างนี้ได้ดียิ่งขึ้น • กระบวนการยึด : กระบวนการเชื่อมต่อทางกลของเราแบ่งออกเป็นสองประเภทแบรด: FASTENERS และ INTEGRAL JOINTS ตัวอย่างของรัดที่เราใช้ ได้แก่ สกรู หมุด น็อต สลักเกลียว หมุดย้ำ ตัวอย่างของข้อต่อแบบอินทิกรัลที่เราใช้ ได้แก่ สแน็ปและหดตัว ตะเข็บ จีบ ด้วยวิธีการยึดที่หลากหลาย เราจึงมั่นใจได้ว่าข้อต่อทางกลของเราแข็งแรงและเชื่อถือได้ตลอดอายุการใช้งาน SCREWS และ BOLTS เป็นตัวยึดที่ใช้กันมากที่สุดสำหรับการยึดวัตถุเข้าด้วยกันและจัดตำแหน่ง สกรูและสลักเกลียวของเราเป็นไปตามมาตรฐาน ASME สกรูและโบลท์ประเภทต่างๆ ถูกนำมาใช้ รวมทั้งสกรูหัวหกเหลี่ยมและน๊อตฐานสิบหก สกรูและโบลต์แล็ก สกรูปลายคู่ สกรูเดือย สกรูตา สกรูกระจก สกรูโลหะแผ่น สกรูปรับละเอียด สกรูเจาะตัวเองและสกรูต๊าปตัวเอง , สกรูยึด, สกรูพร้อมแหวนรองในตัว,…และอีกมากมาย เรามีหัวสกรูหลายประเภท เช่น เคาเตอร์ซัน โดม กลม หัวมีปีก และสกรูไดรฟ์ประเภทต่างๆ เช่น สล็อต ฟิลลิป สี่เหลี่ยม ซ็อกเก็ตหกเหลี่ยม ในทางกลับกัน A RIVET เป็นตัวยึดเชิงกลแบบถาวรที่ประกอบด้วยเพลาทรงกระบอกเรียบและส่วนหัวหนึ่งข้าง หลังจากใส่เข้าไป ปลายอีกด้านของหมุดย้ำจะเสียรูปและขยายเส้นผ่านศูนย์กลางเพื่อให้เข้าที่ กล่าวอีกนัยหนึ่ง ก่อนการติดตั้ง หมุดย้ำมีหนึ่งหัว และหลังการติดตั้ง หมุดย้ำมีหัวสองหัว เราติดตั้งหมุดย้ำหลายประเภทขึ้นอยู่กับการใช้งาน ความแข็งแรง ความสามารถในการเข้าถึงและต้นทุน เช่น หมุดย้ำหัวตัน/แข็ง โครงสร้าง กึ่งท่อ บลายด์ ออสการ์ ไดรฟ์ ฟลัช ล็อคด้วยแรงเสียดทาน หมุดเจาะตัวเอง ควรใช้การตอกย้ำในกรณีที่ต้องหลีกเลี่ยงการเปลี่ยนรูปจากความร้อนและการเปลี่ยนแปลงคุณสมบัติของวัสดุเนื่องจากความร้อนจากการเชื่อม โลดโผนยังมีน้ำหนักเบาและมีความแข็งแรงและความทนทานเป็นพิเศษต่อแรงเฉือน เมื่อเทียบกับแรงดึง อย่างไรก็ตาม สกรู น็อต และสลักเกลียวอาจเหมาะสมกว่า ในกระบวนการ CLINCHING เราใช้หมัดและดายแบบพิเศษเพื่อสร้างการประสานทางกลระหว่างแผ่นโลหะที่เชื่อมเข้าด้วยกัน หมัดผลักชั้นของแผ่นโลหะเข้าไปในโพรงแม่พิมพ์และส่งผลให้เกิดข้อต่อถาวร ไม่ต้องใช้ความร้อนและความเย็นในการกอด และเป็นกระบวนการทำงานที่เย็น เป็นกระบวนการที่ประหยัดซึ่งสามารถทดแทนการเชื่อมแบบจุดได้ในบางกรณี ในการปักหมุด เราใช้หมุดซึ่งเป็นส่วนประกอบของเครื่องจักรที่ใช้เพื่อรักษาตำแหน่งของชิ้นส่วนเครื่องจักรให้สัมพันธ์กัน ประเภทหลักๆ ได้แก่ สลักเคลวิส สลักคอตเตอร์ หมุดสปริง หมุดเดือย และหมุดแยก ในการเย็บ เราใช้ปืนเย็บกระดาษและลวดเย็บซึ่งเป็นตัวยึดแบบสองง่ามที่ใช้ในการเชื่อมหรือเย็บวัสดุ การเย็บเล่มมีข้อดีดังต่อไปนี้: ประหยัด ใช้งานง่าย และรวดเร็ว เม็ดมะยมของลวดเย็บสามารถใช้เชื่อมวัสดุที่ชนเข้าด้วยกันได้ เม็ดมะยมของลวดเย็บช่วยให้เชื่อมชิ้นงาน เช่น สายเคเบิล และยึดเข้ากับพื้นผิวได้โดยไม่ต้องเจาะหรือ ทำลายล้างค่อนข้างง่าย PRESS FITTING ทำได้โดยการดันชิ้นส่วนเข้าด้วยกัน และการเสียดสีระหว่างกันจะยึดชิ้นส่วนเข้าด้วยกัน ชิ้นส่วนแบบกดประกอบด้วยเพลาขนาดใหญ่และรูขนาดเล็ก โดยทั่วไปจะประกอบขึ้นด้วยวิธีใดวิธีหนึ่งจากสองวิธี: โดยใช้กำลังหรือใช้ประโยชน์จากการขยายตัวทางความร้อนหรือการหดตัวของชิ้นส่วน เมื่อติดตั้งอุปกรณ์กดโดยใช้แรง เราจะใช้เครื่องกดไฮดรอลิกหรือเครื่องกดด้วยมือ ในทางกลับกัน เมื่อติดตั้งแบบกดด้วยการขยายตัวทางความร้อน เราจะให้ความร้อนแก่ชิ้นส่วนที่ห่อหุ้มและประกอบเข้าที่ในขณะที่ร้อน เมื่อเย็นตัวลงจะหดตัวและกลับสู่ขนาดปกติ ส่งผลให้กดได้พอดี เราเรียกสิ่งนี้ว่า SHRINK-FITTING วิธีอื่นในการทำเช่นนี้คือการทำให้ชิ้นส่วนที่ห่อหุ้มเย็นลงก่อนประกอบแล้วเลื่อนเข้าไปในส่วนที่ผสมพันธุ์ เมื่อชุดประกอบอุ่นขึ้น ส่วนประกอบก็จะขยายออกและเราจะได้ชุดที่กระชับพอดีตัว วิธีหลังนี้อาจเป็นวิธีที่ดีกว่าในกรณีที่ความร้อนมีความเสี่ยงต่อการเปลี่ยนแปลงคุณสมบัติของวัสดุ การระบายความร้อนจะปลอดภัยกว่าในกรณีเหล่านั้น ส่วนประกอบและส่วนประกอบนิวเมติกและไฮดรอลิก • วาล์ว ส่วนประกอบไฮดรอลิกและนิวแมติก เช่น โอริง แหวนรอง ซีล ปะเก็น แหวน ชิม เนื่องจากวาล์วและส่วนประกอบนิวเมติกมีให้เลือกหลากหลาย เราจึงไม่สามารถแสดงรายการทุกอย่างที่นี่ ขึ้นอยู่กับสภาพแวดล้อมทางกายภาพและทางเคมีของแอปพลิเคชันของคุณ เรามีผลิตภัณฑ์พิเศษสำหรับคุณ โปรดระบุการใช้งาน ประเภทของส่วนประกอบ ข้อกำหนด สภาวะแวดล้อม เช่น ความดัน อุณหภูมิ ของเหลวหรือก๊าซที่จะสัมผัสกับวาล์วและส่วนประกอบนิวเมติกของคุณ และเราจะเลือกผลิตภัณฑ์ที่เหมาะสมที่สุดสำหรับคุณหรือผลิตขึ้นเป็นพิเศษสำหรับการใช้งานของคุณ CLICK Product Finder-Locator Service หน้าก่อน
- Glass and Ceramic Manufacturing, Hermetic Packages, Seals, Bonding
Glass and Ceramic Manufacturing, Hermetic Packages Seals and Bonding, Tempered Bulletproof Glass, Blow Moulding, Optical Grade Glass, Conductive Glass, Molding การขึ้นรูปและการขึ้นรูปแก้วและเซรามิก ประเภทของการผลิตแก้วที่เรานำเสนอ ได้แก่ แก้วคอนเทนเนอร์ การเป่าแก้ว ใยแก้ว & ท่อ & คัน, เครื่องแก้วในประเทศและอุตสาหกรรม, โคมไฟและหลอดไฟ, การขึ้นรูปแก้วที่มีความแม่นยำ, ส่วนประกอบและส่วนประกอบทางแสง, กระจกแบน & แผ่น & โฟลต เราทำการขึ้นรูปด้วยมือและการขึ้นรูปด้วยเครื่องจักร กระบวนการผลิตเซรามิกทางเทคนิคที่เป็นที่นิยมของเรา ได้แก่ การอัดขึ้นรูป การอัดแบบไอโซสแตติก การกดไอโซสแตติกแบบร้อน การรีดร้อน การหล่อแบบสลิป การหล่อเทป การอัดรีด การฉีดขึ้นรูป การตัดเฉือนสีเขียว การเผาหรือเผา การเจียระไนเพชร การประกอบแบบสุญญากาศ เราขอแนะนำให้คุณคลิกที่นี่เพื่อ ดาวน์โหลดภาพประกอบแผนผังของกระบวนการขึ้นรูปและขึ้นรูปแก้วโดย AGS-TECH Inc. ดาวน์โหลดภาพประกอบแผนผังของกระบวนการผลิตเซรามิกทางเทคนิคโดย AGS-TECH Inc. ไฟล์ที่ดาวน์โหลดได้พร้อมรูปถ่ายและภาพสเก็ตช์เหล่านี้จะช่วยให้คุณเข้าใจข้อมูลที่เราให้ไว้ด้านล่างนี้ได้ดียิ่งขึ้น • การผลิตกระจกคอนเทนเนอร์: เรามี PRESS AND BLOW แบบอัตโนมัติ เช่นเดียวกับสายการเป่าและเป่าสำหรับการผลิต ในกระบวนการเป่าและเป่า เราหยด gob ลงในแม่พิมพ์เปล่า และสร้างคอโดยการเป่าลมอัดจากด้านบน ต่อจากนี้ไป อากาศอัดจะถูกเป่าเป็นครั้งที่สองจากอีกทิศทางหนึ่งผ่านคอภาชนะเพื่อสร้างรูปแบบพรีฟอร์มของขวด จากนั้นพรีฟอร์มนี้จะถูกถ่ายโอนไปยังแม่พิมพ์จริง อุ่นให้นุ่มและอัดอากาศเพื่อให้พรีฟอร์มมีรูปร่างของคอนเทนเนอร์สุดท้าย ชัดเจนยิ่งขึ้น มันถูกอัดแรงดันและดันเข้ากับผนังของโพรงแม่พิมพ์เป่าเพื่อให้ได้รูปร่างที่ต้องการ สุดท้าย ภาชนะแก้วที่ผลิตขึ้นจะถูกถ่ายโอนไปยังเตาอบอบอ่อนเพื่อให้ความร้อนซ้ำและขจัดความเครียดที่เกิดขึ้นระหว่างการขึ้นรูปในภายหลัง และถูกทำให้เย็นในลักษณะที่ควบคุมได้ ในวิธีการกดและเป่า gobs ที่หลอมละลายจะถูกใส่ลงในแม่พิมพ์ parison (แม่พิมพ์เปล่า) และกดลงในรูปทรง parison (รูปร่างเปล่า) จากนั้นช่องว่างจะถูกถ่ายโอนไปยังแม่พิมพ์เป่าและเป่าคล้ายกับกระบวนการที่อธิบายไว้ข้างต้นภายใต้ "กระบวนการเป่าและเป่า" ขั้นตอนที่ตามมาเช่นการหลอมและการบรรเทาความเครียดมีความคล้ายคลึงหรือเหมือนกัน • GLASS BLOWING : เราทำการผลิตผลิตภัณฑ์แก้วโดยใช้การเป่าด้วยมือแบบธรรมดาและแบบใช้ลมอัดด้วยอุปกรณ์อัตโนมัติ สำหรับคำสั่งซื้อบางรายการจำเป็นต้องมีการเป่าแบบธรรมดา เช่น โครงการที่เกี่ยวข้องกับงานศิลปะแก้ว หรือโครงการที่ต้องใช้ชิ้นส่วนจำนวนน้อยกว่าที่มีพิกัดความเผื่อหลวม โครงการสร้างต้นแบบ / สาธิต….เป็นต้น การเป่าแก้วแบบทั่วไปเกี่ยวข้องกับการจุ่มท่อโลหะกลวงลงในหม้อแก้วหลอมเหลวแล้วหมุนท่อเพื่อเก็บวัสดุแก้วจำนวนหนึ่ง แก้วที่เก็บที่ปลายท่อรีดด้วยเหล็กแบน มีรูปร่างตามต้องการ ยืดออก ให้ความร้อนซ้ำ และเป่าด้วยลม เมื่อพร้อมก็ใส่แม่พิมพ์และเป่าลม ช่องแม่พิมพ์เปียกเพื่อหลีกเลี่ยงไม่ให้กระจกสัมผัสกับโลหะ ฟิล์มน้ำทำหน้าที่เหมือนเบาะระหว่างพวกเขา การเป่าด้วยมือเป็นกระบวนการที่ช้าซึ่งใช้แรงงานคนมาก และเหมาะสำหรับการสร้างต้นแบบหรือสินค้าที่มีมูลค่าสูงเท่านั้น ไม่เหมาะสำหรับการสั่งซื้อปริมาณมากต่อชิ้นในราคาถูก • การผลิตเครื่องแก้วในประเทศและอุตสาหกรรม : การใช้วัสดุแก้วประเภทต่างๆ ทำให้มีการผลิตเครื่องแก้วหลากหลายรูปแบบ แก้วบางชนิดทนความร้อนและเหมาะสำหรับเครื่องแก้วในห้องปฏิบัติการ ในขณะที่บางแก้วก็ทนทานต่อเครื่องล้างจานได้หลายครั้งและเหมาะสำหรับการผลิตผลิตภัณฑ์ในประเทศ การใช้เครื่อง Westlake มีการผลิตแก้วน้ำดื่มหลายหมื่นชิ้นต่อวัน เพื่อทำให้ง่ายขึ้น แก้วหลอมเหลวจะถูกรวบรวมโดยสุญญากาศและใส่เข้าไปในแม่พิมพ์เพื่อทำเป็นพรีฟอร์ม จากนั้นอากาศจะถูกเป่าเข้าไปในแม่พิมพ์ สิ่งเหล่านี้จะถูกถ่ายโอนไปยังแม่พิมพ์อื่นและอากาศจะถูกเป่าอีกครั้งและแก้วก็จะมีรูปร่างสุดท้าย เช่นเดียวกับการเป่าด้วยมือ แม่พิมพ์เหล่านี้จะเปียกด้วยน้ำ การยืดกล้ามเนื้อเพิ่มเติมเป็นส่วนหนึ่งของการดำเนินการเก็บผิวละเอียดที่เกิดคอ แก้วส่วนเกินถูกไฟไหม้ จากนั้นจึงควบคุมกระบวนการให้ความร้อนและความเย็นอีกครั้งตามที่อธิบายไว้ข้างต้นดังนี้ • GLASS TUBE & ROD FORMING : กระบวนการหลักที่เราใช้สำหรับการผลิตหลอดแก้วคือกระบวนการ DANNER และ VELLO ในกระบวนการ Danner แก้วจากเตาหลอมจะไหลและตกลงบนปลอกเอียงที่ทำจากวัสดุทนไฟ ปลอกสวมบนเพลากลวงที่หมุนได้หรือท่อเป่าลม จากนั้นนำแก้วมาพันรอบปลอกแขนและก่อตัวเป็นชั้นๆ เรียบๆ ไหลลงมาที่แขนเสื้อและเหนือปลายก้าน ในกรณีของการขึ้นรูปท่อ อากาศจะถูกเป่าผ่านท่อเป่าลมที่มีปลายกลวง และในกรณีของการขึ้นรูปก้าน เราใช้ปลายที่เป็นของแข็งบนก้าน จากนั้นท่อหรือแท่งจะถูกดึงทับลูกกลิ้ง ขนาดต่างๆ เช่น ความหนาของผนังและเส้นผ่านศูนย์กลางของหลอดแก้วจะถูกปรับให้เป็นค่าที่ต้องการโดยการตั้งค่าเส้นผ่านศูนย์กลางของปลอกและแรงดันลมเป่าให้เป็นค่าที่ต้องการ ปรับอุณหภูมิ อัตราการไหลของแก้ว และความเร็วในการวาด ในทางกลับกัน กระบวนการผลิตหลอดแก้วเวลโลนั้นเกี่ยวข้องกับแก้วที่เคลื่อนออกจากเตาหลอมและเข้าไปในชามที่มีแมนเดรลหรือกระดิ่งกลวง จากนั้นแก้วจะผ่านช่องว่างอากาศระหว่างแมนเดรลกับชาม แล้วทำเป็นหลอด หลังจากนั้นจะเคลื่อนผ่านลูกกลิ้งไปยังเครื่องวาดรูปและเย็นลง ในตอนท้ายของการตัดท่อระบายความร้อนและการประมวลผลขั้นสุดท้ายจะเกิดขึ้น ขนาดของท่อสามารถปรับได้เช่นเดียวกับในกระบวนการ Danner เมื่อเปรียบเทียบกระบวนการ Danner กับ Vello เราสามารถพูดได้ว่ากระบวนการ Vello นั้นเหมาะสมกว่าสำหรับการผลิตปริมาณมาก ในขณะที่กระบวนการ Danner อาจเหมาะสมกว่าสำหรับการสั่งซื้อหลอดที่มีปริมาตรน้อยกว่าที่แม่นยำกว่า • การประมวลผลแผ่น & แบน & กระจกโฟลต : เรามีกระจกแบนจำนวนมากที่มีความหนาตั้งแต่ความหนา submilimeter ไปจนถึงหลายเซนติเมตร แว่นสายตาแบนของเรามีความสมบูรณ์แบบเกือบสมบูรณ์แบบ เรานำเสนอกระจกที่มีการเคลือบพิเศษ เช่น การเคลือบด้วยแสง ซึ่งใช้เทคนิคการสะสมไอเคมีเพื่อเคลือบสารเคลือบ เช่น สารป้องกันการสะท้อนหรือการเคลือบกระจก การเคลือบนำไฟฟ้าแบบโปร่งใสก็เป็นเรื่องปกติเช่นกัน นอกจากนี้ยังมีสารเคลือบที่ไม่ชอบน้ำหรือชอบน้ำบนกระจก และสารเคลือบที่ทำให้กระจกสามารถทำความสะอาดตัวเองได้ กระจกเทมเปอร์ กันกระสุน และลามิเนตเป็นสินค้ายอดนิยมอื่นๆ เราตัดกระจกเป็นรูปทรงที่ต้องการด้วยความคลาดเคลื่อนที่ต้องการ มีการทำงานรองอื่น ๆ เช่น การดัดโค้งหรือดัดกระจกแบน • การขึ้นรูปกระจกที่แม่นยำ: เราใช้เทคนิคนี้เป็นหลักสำหรับการผลิตส่วนประกอบออปติคัลที่มีความแม่นยำ โดยไม่ต้องใช้เทคนิคที่มีราคาแพงกว่าและใช้เวลานาน เช่น การเจียร การขัด และการขัดเงา เทคนิคนี้ไม่เพียงพอเสมอสำหรับการสร้างเลนส์ที่ดีที่สุด แต่ในบางกรณี เช่น สินค้าอุปโภคบริโภค กล้องดิจิตอล เลนส์ทางการแพทย์ อาจเป็นทางเลือกที่ดีในราคาไม่แพงสำหรับการผลิตในปริมาณมาก นอกจากนี้ยังมีข้อได้เปรียบเหนือเทคนิคการขึ้นรูปแก้วอื่นๆ ที่ต้องการรูปทรงที่ซับซ้อน เช่น ในกรณีของทรงกลม กระบวนการพื้นฐานเกี่ยวข้องกับการโหลดด้านล่างของแม่พิมพ์ของเราด้วยช่องว่างแก้ว การอพยพของห้องกระบวนการเพื่อกำจัดออกซิเจน ใกล้ปิดของแม่พิมพ์ การให้ความร้อนอย่างรวดเร็วและความร้อนของแม่พิมพ์และแก้วด้วยแสงอินฟราเรด การปิดเพิ่มเติมของครึ่งแม่พิมพ์ เพื่อกดกระจกที่อ่อนนุ่มอย่างช้า ๆ ในแบบควบคุมให้ได้ความหนาที่ต้องการ และสุดท้ายทำให้แก้วเย็นลงและเติมไนโตรเจนลงในห้องและนำผลิตภัณฑ์ออก การควบคุมอุณหภูมิที่แม่นยำ ระยะการปิดแม่พิมพ์ แรงปิดแม่พิมพ์ การจับคู่ค่าสัมประสิทธิ์การขยายตัวของแม่พิมพ์และวัสดุแก้วเป็นสิ่งสำคัญในกระบวนการนี้ • การผลิตส่วนประกอบทางแสงของแก้วและการประกอบ : นอกจากการขึ้นรูปแก้วที่มีความแม่นยำแล้ว ยังมีกระบวนการที่มีคุณค่าหลายอย่างที่เราใช้ในการผลิตส่วนประกอบและส่วนประกอบทางแสงคุณภาพสูงสำหรับการใช้งานที่มีความต้องการสูง การเจียร การขัด และการขัดเงาของแว่นตาเกรดออปติคัลในสารละลายที่มีสารกัดกร่อนพิเศษชั้นดีเป็นศิลปะและวิทยาศาสตร์สำหรับการผลิตเลนส์ออพติคอล ปริซึม แฟลต และอื่นๆ ความเรียบของพื้นผิว เป็นคลื่น ความเรียบ และพื้นผิวออปติคัลที่ปราศจากข้อบกพร่องต้องอาศัยประสบการณ์มากมายในกระบวนการดังกล่าว การเปลี่ยนแปลงสภาพแวดล้อมเพียงเล็กน้อยอาจส่งผลให้ผลิตภัณฑ์ไม่ตรงตามข้อกำหนดและทำให้สายการผลิตต้องหยุดชะงัก มีหลายกรณีที่การเช็ดเพียงครั้งเดียวบนพื้นผิวออปติคัลด้วยผ้าสะอาดสามารถทำให้ผลิตภัณฑ์เป็นไปตามข้อกำหนดหรือไม่ผ่านการทดสอบ วัสดุแก้วที่นิยมใช้ ได้แก่ ซิลิกาหลอมรวม ควอทซ์ BK7 นอกจากนี้การประกอบส่วนประกอบดังกล่าวยังต้องการประสบการณ์เฉพาะทาง บางครั้งมีการใช้กาวพิเศษ อย่างไรก็ตาม บางครั้งเทคนิคที่เรียกว่าการสัมผัสด้วยแสงเป็นทางเลือกที่ดีที่สุด และไม่เกี่ยวข้องกับวัสดุใดๆ ระหว่างแว่นสายตาที่ต่ออยู่ ประกอบด้วยพื้นผิวเรียบสัมผัสทางกายภาพเพื่อยึดติดกันโดยไม่ต้องใช้กาว ในบางกรณี ตัวเว้นระยะเชิงกล แท่งแก้วหรือลูกแก้วที่มีความแม่นยำ แคลมป์หรือส่วนประกอบโลหะที่กลึงจะถูกนำมาใช้เพื่อประกอบส่วนประกอบออปติคัลในระยะทางที่แน่นอนและด้วยการวางแนวเรขาคณิตบางอย่างต่อกัน ให้เราตรวจสอบเทคนิคยอดนิยมบางอย่างของเราสำหรับการผลิตเลนส์ระดับไฮเอนด์ GRINDING & LAPPING & POLISHING : ได้รูปร่างหยาบของส่วนประกอบออปติคัลด้วยการเจียรแก้วเปล่า จากนั้นจึงทำการขัดและขัดเงาโดยการหมุนและถูพื้นผิวที่ขรุขระของส่วนประกอบออปติคัลกับเครื่องมือที่มีรูปร่างพื้นผิวที่ต้องการ สารละลายที่มีอนุภาคและของเหลวที่มีฤทธิ์กัดกร่อนเล็กๆ ถูกเทลงในระหว่างเลนส์กับเครื่องมือสร้างรูปร่าง ขนาดอนุภาคที่มีฤทธิ์กัดกร่อนในสารละลายดังกล่าวสามารถเลือกได้ตามระดับความเรียบที่ต้องการ ความเบี่ยงเบนของพื้นผิวทางแสงที่สำคัญจากรูปร่างที่ต้องการจะแสดงเป็นความยาวคลื่นของแสงที่ใช้ ออปติกความแม่นยำสูงของเรามีค่าความคลาดเคลื่อนที่ยอมรับได้ของความยาวคลื่น (ความยาวคลื่น/10) หนึ่งในสิบหรือเข้มงวดกว่านี้ก็ได้ นอกจากโปรไฟล์พื้นผิวแล้ว พื้นผิวที่สำคัญจะถูกสแกนและประเมินสำหรับคุณสมบัติพื้นผิวและข้อบกพร่องอื่นๆ เช่น ขนาด รอยขีดข่วน เศษ หลุม จุด...ฯลฯ การควบคุมสภาพแวดล้อมอย่างเข้มงวดในชั้นการผลิตเชิงแสงและข้อกำหนดด้านมาตรวิทยาและการทดสอบที่ครอบคลุมด้วยอุปกรณ์ที่ล้ำสมัยทำให้สาขานี้กลายเป็นสาขาที่ท้าทายของอุตสาหกรรม • กระบวนการรองในการผลิตแก้ว: อีกครั้ง เราถูกจำกัดด้วยจินตนาการของคุณเท่านั้น เมื่อพูดถึงกระบวนการรองและการตกแต่งแก้ว เราแสดงรายการบางส่วน: -การเคลือบบนกระจก (ออปติคัล ไฟฟ้า ไทรโบโลยี ความร้อน การทำงาน กลไก...) ตัวอย่างเช่น เราสามารถปรับเปลี่ยนคุณสมบัติพื้นผิวของกระจกได้ เช่น สะท้อนความร้อน เพื่อให้ภายในอาคารเย็น หรือทำให้ด้านหนึ่งดูดซับอินฟราเรดโดยใช้นาโนเทคโนโลยี ซึ่งช่วยให้ภายในอาคารอบอุ่นเพราะชั้นผิวนอกสุดของกระจกจะดูดซับรังสีอินฟราเรดภายในอาคารและแผ่รังสีกลับคืนสู่ภายใน -แกะสลัก onแก้ว - การติดฉลากเซรามิกประยุกต์ (ACL) -แกะสลัก - ขัดด้วยเปลวไฟ - ขัดเคมี -การย้อมสี การผลิตเซรามิกทางเทคนิค • DIE PRESSING : ประกอบด้วยการบดอัดแกนเดียวของผงเม็ดเล็ก ๆ ที่อยู่ในแม่พิมพ์ • HOT PRESSING : คล้ายกับแม่พิมพ์ฉีดขึ้นรูปแต่เพิ่มอุณหภูมิเพื่อเพิ่มความหนาแน่น ใส่ผงหรือพรีฟอร์มอัดลงในแม่พิมพ์กราไฟท์และใช้แรงดันแกนเดียวในขณะที่แม่พิมพ์ถูกเก็บไว้ที่อุณหภูมิสูง เช่น 2,000 องศาเซลเซียส อุณหภูมิอาจแตกต่างกันไปตามประเภทของผงเซรามิกที่กำลังดำเนินการ สำหรับรูปทรงและรูปทรงที่ซับซ้อน อาจจำเป็นต้องมีการประมวลผลอื่นๆ เช่น การเจียระไนเพชร • ISOSTATIC PRESSING : บรรจุผงเม็ดหรือแม่พิมพ์อัดขึ้นรูปในภาชนะที่ปิดสนิทแล้วใส่ลงในภาชนะแรงดันปิดที่มีของเหลวอยู่ภายใน หลังจากนั้นจะถูกอัดแน่นโดยการเพิ่มแรงดันของถังแรงดัน ของเหลวภายในภาชนะจะถ่ายเทแรงดันอย่างสม่ำเสมอทั่วทั้งพื้นผิวของภาชนะบรรจุภัณฑ วัสดุจึงถูกบีบอัดให้เท่ากันและใช้รูปร่างของภาชนะที่ยืดหยุ่นและโปรไฟล์ภายในและคุณสมบัติต่างๆ • HOT ISOSTATIC PRESSING : คล้ายกับการกดแบบไอโซสแตติก แต่นอกเหนือจากบรรยากาศของแก๊สที่มีแรงดันแล้ว เรายังเผาแบบอัดแน่นที่อุณหภูมิสูง การกดไอโซสแตติกแบบร้อนส่งผลให้มีความหนาแน่นเพิ่มขึ้นและความแข็งแรงเพิ่มขึ้น • SLIP CASTING / DRAIN CASTING : เราเติมแม่พิมพ์ด้วยสารแขวนลอยของอนุภาคเซรามิกขนาดไมโครมิเตอร์และของเหลวตัวพา ส่วนผสมนี้เรียกว่า "สลิป" แม่พิมพ์มีรูพรุน ดังนั้นของเหลวในส่วนผสมจึงถูกกรองเข้าไปในแม่พิมพ์ เป็นผลให้มีการหล่อขึ้นบนพื้นผิวด้านในของแม่พิมพ์ หลังจากการเผาผนึกแล้ว สามารถนำชิ้นส่วนออกจากแม่พิมพ์ได้ • TAPE Casting : เราผลิตเทปเซรามิกโดยการหล่อสารละลายเซรามิกบนพื้นผิวที่เคลื่อนย้ายได้เรียบ สารละลายมีผงเซรามิกผสมกับสารเคมีอื่นๆ เพื่อการจับและขนย้าย เนื่องจากตัวทำละลายระเหยแผ่นเซรามิกที่มีความหนาแน่นและยืดหยุ่นเหลือทิ้งไว้ซึ่งสามารถตัดหรือรีดได้ตามต้องการ • การอัดขึ้นรูป : เช่นเดียวกับในกระบวนการอัดรีดอื่นๆ ส่วนผสมที่อ่อนนุ่มของผงเซรามิกที่มีสารยึดเกาะและสารเคมีอื่นๆ จะถูกส่งผ่านแม่พิมพ์เพื่อให้ได้รูปทรงหน้าตัดและตัดตามความยาวที่ต้องการ กระบวนการนี้ดำเนินการด้วยส่วนผสมเซรามิกแบบเย็นหรือแบบร้อน • การฉีดขึ้นรูปด้วยแรงดันต่ำ : เราเตรียมส่วนผสมของผงเซรามิกที่มีสารยึดเกาะและตัวทำละลาย และให้ความร้อนจนถึงอุณหภูมิที่สามารถกดและบังคับได้ง่ายในช่องเครื่องมือ เมื่อรอบการขึ้นรูปเสร็จสิ้น ชิ้นส่วนจะถูกขับออกมาและสารเคมีที่ยึดเกาะจะถูกเผาทิ้ง ด้วยการใช้การฉีดขึ้นรูป เราจะได้ชิ้นส่วนที่ซับซ้อนในปริมาณมากในเชิงเศรษฐกิจ รู ที่เป็นเศษเสี้ยวเล็กๆ ของมิลลิเมตรบนผนังหนา 10 มม. สามารถทำเกลียวได้โดยไม่ต้องใช้การตัดเฉือนเพิ่มเติม ความคลาดเคลื่อนแน่นถึง +/- 0.5% เป็นไปได้ และยิ่งต่ำลงเมื่อกลึงชิ้นส่วน , ความหนาของผนังตามลำดับ 0.5 มม. ถึงความยาว 12.5 มม. เช่นเดียวกับความหนาของผนัง 6.5 มม. ถึงความยาว 150 มม. • GREEN MACHINING : โดยใช้เครื่องมือตัดเฉือนโลหะแบบเดียวกัน เราสามารถตัดเฉือนวัสดุเซรามิกที่กดแล้วได้ในขณะที่ยังคงนิ่มเหมือนชอล์ก ความคลาดเคลื่อน +/- 1% เป็นไปได้ เพื่อความคลาดเคลื่อนที่ดีขึ้น เราใช้การเจียรด้วยเพชร • SINTERING หรือ FIRING : การเผาผนึกทำให้มีความหนาแน่นเต็มที่ การหดตัวที่สำคัญเกิดขึ้นกับชิ้นส่วนขนาดกะทัดรัดสีเขียว แต่นี่ไม่ใช่ปัญหาใหญ่ เนื่องจากเราคำนึงถึงการเปลี่ยนแปลงมิติเหล่านี้เมื่อเราออกแบบชิ้นส่วนและเครื่องมือ อนุภาคผงถูกยึดเข้าด้วยกันและความพรุนที่เกิดจากกระบวนการบดอัดจะถูกลบออกในระดับที่ดี.. • การเจียรด้วยเพชร : วัสดุที่แข็งที่สุดในโลก “เพชร” ถูกใช้เพื่อบดวัสดุแข็ง เช่น เซรามิก และชิ้นส่วนที่มีความแม่นยำ มีความคลาดเคลื่อนในช่วงไมโครมิเตอร์และพื้นผิวที่เรียบมาก เนื่องจากมีค่าใช้จ่าย เราจึงพิจารณาเทคนิคนี้เมื่อเราต้องการจริงๆ เท่านั้น • HERMETIC ASSEMBLIES เป็นสิ่งที่ในทางปฏิบัติแล้วไม่อนุญาตให้มีการแลกเปลี่ยนสสาร ของแข็ง ของเหลว หรือก๊าซระหว่างส่วนต่อประสาน การปิดผนึกสุญญากาศเป็นแบบสุญญากาศ ตัวอย่างเช่น เปลือกหุ้มอิเล็กทรอนิคส์แบบสุญญากาศคือส่วนที่รักษาเนื้อหาภายในที่ละเอียดอ่อนของอุปกรณ์ที่บรรจุหีบห่อไว้ไม่เป็นอันตรายต่อความชื้น สารปนเปื้อน หรือก๊าซ ไม่มีสิ่งใดที่ผนึกแน่นได้ 100% แต่เมื่อเราพูดถึงความผนึกแน่น เราหมายความว่าในทางปฏิบัติ มีความผนึกแน่นจนอัตราการรั่วไหลต่ำจนอุปกรณ์มีความปลอดภัยภายใต้สภาวะแวดล้อมปกติเป็นเวลานานมาก ชุดประกอบสุญญากาศของเราประกอบด้วยโลหะ แก้วและส่วนประกอบเซรามิก โลหะ-เซรามิก, เซรามิก-โลหะ-เซรามิก, โลหะ-เซรามิก-โลหะ, โลหะกับโลหะ, โลหะ-แก้ว, โลหะ-แก้ว-โลหะ, แก้ว-โลหะ-แก้ว, แก้ว- โลหะและแก้วกับแก้ว และการผสมผสานอื่นๆ ทั้งหมดของการยึดติดระหว่างโลหะ-แก้ว-เซรามิก ตัวอย่างเช่น เราสามารถเคลือบส่วนประกอบเซรามิกด้วยโลหะ เพื่อให้สามารถยึดติดอย่างแน่นหนากับส่วนประกอบอื่นๆ ในชุดประกอบ และมีความสามารถในการปิดผนึกที่ดีเยี่ยม เรามีความรู้ในการเคลือบไฟเบอร์ออปติกหรือ feedthroughs ด้วยโลหะและการบัดกรีหรือประสานเข้ากับเปลือกหุ้ม ดังนั้นจึงไม่มีก๊าซผ่านหรือรั่วไหลเข้าไปในเปลือกหุ้ม ดังนั้นจึงใช้ในการผลิตกล่องหุ้มอิเล็กทรอนิกส์เพื่อห่อหุ้มอุปกรณ์ที่ละเอียดอ่อนและปกป้องจากบรรยากาศภายนอก นอกจากคุณสมบัติการปิดผนึกที่ยอดเยี่ยมแล้ว คุณสมบัติอื่นๆ เช่น ค่าสัมประสิทธิ์การขยายตัวทางความร้อน ความต้านทานการเปลี่ยนรูป ลักษณะที่ไม่ปล่อยก๊าซออก อายุการใช้งานยาวนานมาก ลักษณะที่ไม่นำไฟฟ้า คุณสมบัติของฉนวนความร้อน ลักษณะป้องกันไฟฟ้าสถิตย์...เป็นต้น ทำให้วัสดุแก้วและเซรามิกเป็นทางเลือกสำหรับการใช้งานบางประเภท ข้อมูลเกี่ยวกับโรงงานผลิตของเราที่ผลิตอุปกรณ์เซรามิกกับโลหะ การปิดผนึกอย่างแน่นหนา การป้อนผ่านสุญญากาศ ส่วนประกอบการควบคุมสุญญากาศและของเหลวสูงและสูงและสูงพิเศษ สามารถพบได้ที่นี่:โบรชัวร์โรงงานส่วนประกอบสุญญากาศ CLICK Product Finder-Locator Service หน้าก่อน
- Wire & Spring Forming, Shaping, Welding, Assembly of Wires, Coil, CNC
Wire & Spring Forming, Shaping, Welding, Assembly of Wires, Coil Compression Extension Torsion Flat Springs, Custom Wires, Helical Springs at AGS-TECH Inc. การขึ้นรูปลวดและสปริง เราผลิตลวดแบบกำหนดเอง ประกอบลวด ลวดขึ้นรูปเป็นรูปร่าง 2D และ 3D ที่ต้องการ ตาข่ายลวด ตาข่าย เปลือก ตะกร้า รั้ว ลวดสปริง สปริงแบน แรงบิด แรงอัด แรงตึง สปริงเรียบ และอื่นๆ กระบวนการของเราได้แก่ การขึ้นรูปลวดและสปริง การดึงลวด การขึ้นรูป การดัด การเชื่อม การประสาน การบัดกรี การเจาะ การเหวี่ยง การเจาะ การลบมุม การเจียร การทำเกลียว การเคลือบ โฟร์สไลด์ การขึ้นรูปแบบสไลด์ การม้วน การม้วน การบิดเบี้ยว เราขอแนะนำให้คุณคลิกที่นี่เพื่อ ดาวน์โหลดภาพประกอบแผนผังของกระบวนการขึ้นรูปลวดและสปริงโดย AGS-TECH Inc. ไฟล์ที่ดาวน์โหลดได้พร้อมรูปถ่ายและภาพสเก็ตช์จะช่วยให้คุณเข้าใจข้อมูลที่เราให้ไว้ด้านล่างนี้ได้ดียิ่งขึ้น • WIRE DRAWING : ใช้แรงดึง เรายืดสต็อกโลหะและดึงผ่านแม่พิมพ์เพื่อลดขนาดเส้นผ่านศูนย์กลางและเพิ่มความยาว บางครั้งเราใช้ชุดแม่พิมพ์ เราสามารถสร้างแม่พิมพ์สำหรับเส้นลวดทุกเส้นได้ การใช้วัสดุที่มีความต้านทานแรงดึงสูงเราวาดเส้นลวดที่บางมาก เรามีสายไฟทั้งแบบเย็นและแบบร้อน. • WIRE FORMING : ม้วนลวดเกจเป็นม้วนและขึ้นรูปเป็นผลิตภัณฑ์ที่มีประโยชน์ เรามีความสามารถในการขึ้นรูปสายไฟจากเกจทั้งหมด รวมถึงเส้นใยบางและเส้นหนา เช่น ลวดที่ใช้เป็นสปริงใต้โครงรถยนต์ อุปกรณ์ที่เราใช้ในการขึ้นรูปลวดมีทั้งแบบ manual และแบบ CNC, coiler, power presss, fourslide, multi-slide กระบวนการของเรามีทั้งการวาด การดัด การยืด การทำให้แบน การยืด การตัด การทำให้เสียโฉม การบัดกรีและการเชื่อมและการประสาน การประกอบ การม้วน การเหวี่ยง (หรือการทำปีก) การเจาะ การทำเกลียวลวด การเจาะ การลบมุม การเจียร การเคลือบ และการปรับสภาพพื้นผิว อุปกรณ์ล้ำสมัยของเราสามารถตั้งค่าเพื่อพัฒนาการออกแบบที่ซับซ้อนมากสำหรับรูปร่างใดๆ และค่าความคลาดเคลื่อนที่เข้มงวด เรามีปลายสายประเภทต่างๆ like ปลายทรงกลม ปลายแหลม หรือมุมลบมุมสำหรับสายไฟของคุณ โครงการขึ้นรูปลวดส่วนใหญ่ของเรามีต้นทุนเครื่องมือขั้นต่ำถึงศูนย์ เวลาตอบสนองตัวอย่างโดยทั่วไปคือวัน การเปลี่ยนแปลงการออกแบบ/การกำหนดค่าของแบบฟอร์มลวดสามารถทำได้อย่างรวดเร็ว • การขึ้นรูปสปริง : AGS-TECH ผลิตสปริงหลากหลายประเภท ได้แก่: - สปริงทอร์ชั่น / สปริงทอร์ชั่นคู่ - สปริงแรงดึง / แรงอัด -สปริงคงที่ / แปรผัน -คอยล์และสปริงขด -สปริงแบนและแหนบ -สปริงบาลานซ์ - เครื่องซักผ้า Belleville -สปริงเนเกเตอร์ - สปริงคอยล์อัตราก้าวหน้า -คลื่นสปริง -สปริงโวลูท -สปริงเรียว -แหวนสปริง -นาฬิกาสปริง -คลิป เราผลิตสปริงจากวัสดุที่หลากหลาย และสามารถแนะนำคุณได้ตามการใช้งานของคุณ วัสดุที่ใช้กันทั่วไป ได้แก่ สแตนเลส โครเมียมซิลิกอน เหล็กกล้าคาร์บอนสูง คาร์บอนต่ำที่มีอุณหภูมิน้ำมัน โครเมียมวาเนเดียม ฟอสเฟอร์บรอนซ์ ไททาเนียม โลหะผสมทองแดงเบริลเลียม เซรามิกอุณหภูมิสูง เราใช้เทคนิคต่างๆ ในการผลิตสปริง รวมถึงการม้วน CNC, ม้วนเย็น, ม้วนร้อน, ชุบแข็ง, เก็บผิวละเอียด เทคนิคอื่นๆ ที่กล่าวถึงข้างต้นภายใต้การขึ้นรูปลวดก็เป็นเรื่องปกติในการดำเนินการผลิตสปริงของเราเช่นกัน • บริการตกแต่งสายไฟและสปริง : เราสามารถตกแต่งผลิตภัณฑ์ของคุณได้หลายวิธีขึ้นอยู่กับทางเลือกและความต้องการของคุณ กระบวนการทั่วไปที่เรานำเสนอ ได้แก่ การทาสี การเคลือบด้วยผง การชุบ การจุ่มไวนิล การชุบอโนไดซ์ การบรรเทาความเครียด การอบชุบด้วยความร้อน การพ่นสี การอบ โครเมต electroless นิกเกิล ทู่ เคลือบอบ เคลือบพลาสติก , พลาสม่าทำความสะอาด. CLICK Product Finder-Locator Service หน้าก่อน
- Forging and Powdered Metallurgy, Die Forging, Heading, Hot Forging
Forging and Powdered Metallurgy, Die Forging, Heading, Hot Forging, Impression Die, Near Net Shape, Swaging, Metal Hobbing, Riveting, Coining from AGS-TECH Inc. การตีขึ้นรูปโลหะและผงโลหะผสม ประเภทของกระบวนการหลอมโลหะที่เรานำเสนอ ได้แก่ แม่พิมพ์ร้อนและเย็น แม่พิมพ์แบบเปิดและแบบปิด แม่พิมพ์แบบอิมเพรสชั่นและการตีแบบไม่มีแฟลช cogging การทำให้ฟูลเลอร์ การทำขอบและการตีขึ้นรูปด้วยความแม่นยำ การตีขึ้นรูปใกล้ตาข่าย ส่วนหัว , การเหวี่ยง, การตีขึ้นรูปด้วยอารมณ์เสีย, การตีด้วยโลหะ, การกดและม้วน & การตีขึ้นรูปแนวรัศมีและแนวรัศมี & การตีขึ้นรูป, การโลดโผน, การตีลูกโลหะ, การเจาะโลหะ, การปรับขนาด, การตีด้วยอัตราพลังงานสูง เทคนิคการหลอมโลหะแบบผงและแบบผงของเราคือการอัดผงและการเผาผนึก การชุบ การแทรกซึม การกดแบบไอโซสแตติกแบบร้อนและเย็น การฉีดขึ้นรูปโลหะ การบดอัดแบบม้วน การรีดผง การรีดผง การเผาผนึกแบบหลวม การเผาผนึกด้วยประกายไฟ การอัดแบบร้อน เราขอแนะนำให้คุณคลิกที่นี่เพื่อ ดาวน์โหลดภาพประกอบแผนผังของกระบวนการตีขึ้นรูปโดย AGS-TECH Inc. ดาวน์โหลดภาพประกอบแผนผังของกระบวนการผสมผงโดย AGS-TECH Inc. ไฟล์ที่ดาวน์โหลดได้พร้อมรูปถ่ายและภาพสเก็ตช์เหล่านี้จะช่วยให้คุณเข้าใจข้อมูลที่เราให้ไว้ด้านล่างนี้ได้ดียิ่งขึ้น ในการตีขึ้นรูปโลหะ จะใช้แรงอัดและวัสดุจะเสียรูปและได้รูปทรงที่ต้องการ วัสดุหลอมที่พบมากที่สุดในอุตสาหกรรมคือเหล็กและเหล็กกล้า แต่วัสดุอื่นๆ เช่น อลูมิเนียม ทองแดง ไททาเนียม แมกนีเซียม ก็มีการหลอมอย่างกว้างขวางเช่นกัน ชิ้นส่วนโลหะหลอมได้ปรับปรุงโครงสร้างเกรนนอกเหนือจากรอยแตกที่ปิดสนิทและช่องว่างที่ปิดสนิท ดังนั้นความแข็งแรงของชิ้นส่วนที่ได้จากกระบวนการนี้จึงสูงขึ้น การตีขึ้นรูปทำให้ชิ้นส่วนมีขนาด มีน้ำหนักที่แข็งแรงกว่าชิ้นส่วนที่หล่อหรือขึ้นรูป เนื่องจากชิ้นส่วนปลอมแปลงถูกขึ้นรูปโดยการทำให้โลหะไหลเข้าสู่รูปทรงสุดท้าย โลหะจึงใช้โครงสร้างเกรนแบบมีทิศทางซึ่งคำนึงถึงความแข็งแรงที่เหนือกว่าของชิ้นส่วน กล่าวอีกนัยหนึ่ง ชิ้นส่วนที่ได้จากกระบวนการตีขึ้นรูปเผยให้เห็นคุณสมบัติทางกลที่ดีกว่าเมื่อเปรียบเทียบกับการหล่อแบบธรรมดาหรือชิ้นส่วนที่กลึง น้ำหนักของการตีขึ้นรูปโลหะมีตั้งแต่ชิ้นส่วนขนาดเล็กน้ำหนักเบาไปจนถึงหลายแสนปอนด์ เราผลิตการตีขึ้นรูปเป็นส่วนใหญ่สำหรับการใช้งานที่มีความต้องการทางกลซึ่งใช้แรงกดสูงกับชิ้นส่วนต่างๆ เช่น ชิ้นส่วนยานยนต์ เกียร์ เครื่องมือทำงาน เครื่องมือช่าง เพลากังหัน เกียร์รถจักรยานยนต์ เนื่องจากต้นทุนเครื่องมือและการตั้งค่าค่อนข้างสูง เราจึงแนะนำกระบวนการผลิตนี้สำหรับการผลิตที่มีปริมาณมากและสำหรับส่วนประกอบที่สำคัญในปริมาณน้อยแต่มีมูลค่าสูง เช่น เกียร์ลงจอดในอวกาศ นอกจากต้นทุนของเครื่องมือแล้ว เวลาในการผลิตสำหรับชิ้นส่วนปลอมแปลงปริมาณมากอาจยาวนานกว่าเมื่อเทียบกับชิ้นส่วนกลึงธรรมดาบางประเภท แต่เทคนิคนี้มีความสำคัญสำหรับชิ้นส่วนที่ ต้องการความแข็งแรงเป็นพิเศษ เช่น สลักเกลียว น็อต การใช้งานพิเศษ รัด, ยานยนต์, รถยก, ชิ้นส่วนรถเครน • HOT DIE and COLD DIE FORGING : การตีขึ้นรูปด้วยความร้อนเนื่องจากชื่อที่มีความหมายว่าดำเนินการที่อุณหภูมิสูง ความเหนียวจึงสูงและความแข็งแรงของวัสดุต่ำ สิ่งนี้อำนวยความสะดวกในการเสียรูปและการปลอมแปลงได้ง่าย ในทางตรงกันข้าม การตีขึ้นรูปเย็นจะดำเนินการที่อุณหภูมิต่ำกว่าและต้องใช้กำลังที่สูงขึ้นซึ่งส่งผลให้เกิดการแข็งตัวของความเครียด ผิวสำเร็จที่ดีขึ้น และความแม่นยำของชิ้นส่วนที่ผลิตขึ้น • การตีแบบเปิดและการตีขึ้นรูปด้วยความประทับใจ : ในการตีขึ้นรูปแบบเปิด แม่พิมพ์ไม่ได้จำกัดวัสดุที่ถูกบีบอัด ในขณะที่การตีขึ้นรูปด้วยแม่พิมพ์แบบพิมพ์ฟันจะทำให้ช่องว่างภายในแม่พิมพ์จำกัดการไหลของวัสดุในขณะที่หล่อขึ้นรูปตามต้องการ UPSET FORGING หรือเรียกอีกอย่างว่า UPSETTING ซึ่งจริง ๆ แล้วไม่เหมือนกัน แต่เป็นกระบวนการที่คล้ายกันมาก เป็นกระบวนการแม่พิมพ์แบบเปิดที่ชิ้นงานถูกประกบระหว่างแม่พิมพ์แบนสองตัวและแรงอัดจะลดความสูงลง เนื่องจากความสูง is reduced ความกว้างของชิ้นงานจะเพิ่มขึ้น HEADING กระบวนการตีขึ้นรูปแบบบิดเบี้ยวเกี่ยวข้องกับสต็อกทรงกระบอกที่มีการเสียดสีที่ส่วนท้ายและส่วนตัดขวางเพิ่มขึ้นในพื้นที่ ในการมุ่งหน้า สต็อกจะถูกป้อนผ่านแม่พิมพ์ หล่อขึ้นรูปแล้วตัดให้ยาว การดำเนินการนี้สามารถผลิตรัดปริมาณมากได้อย่างรวดเร็ว ส่วนใหญ่เป็นการทำงานที่เย็นเนื่องจากใช้ทำปลายตะปู ปลายสกรู น็อตและสลักเกลียวที่ต้องการเสริมความแข็งแรงของวัสดุ กระบวนการดายแบบเปิดอีกกระบวนการหนึ่งคือ COGGING ซึ่งชิ้นงานถูกหลอมเป็นชุดของขั้นตอนโดยแต่ละขั้นตอนส่งผลให้เกิดการบีบอัดของวัสดุและการเคลื่อนที่ของดายแบบเปิดตามความยาวของชิ้นงาน ในแต่ละขั้นตอน ความหนาจะลดลงและความยาวเพิ่มขึ้นเล็กน้อย กระบวนการนี้คล้ายกับนักเรียนประสาทกัดดินสอของเขาในขั้นตอนเล็กๆ กระบวนการที่เรียกว่า FULLERING เป็นวิธีการตีขึ้นรูปแบบเปิดอีกวิธีหนึ่งที่เรามักปรับใช้เป็นขั้นตอนก่อนหน้านี้ในการกระจายวัสดุในชิ้นงานก่อนที่จะมีการตีขึ้นรูปโลหะอื่นๆ เราใช้เมื่อชิ้นงานต้องการการตีขึ้นรูปหลายชิ้น operations ในการดำเนินการ ให้ตายด้วยพื้นผิวนูนที่บิดเบี้ยวและทำให้โลหะไหลออกทั้งสองข้าง กระบวนการที่คล้ายคลึงกันกับการฟูลเลอร์ ในทางกลับกัน EDGING เกี่ยวข้องกับดายแบบเปิดที่มีพื้นผิวเว้าเพื่อทำให้ชิ้นงานเสียรูป การตัดขอบยังเป็นกระบวนการเตรียมการสำหรับการตีขึ้นรูปในภายหลังทำให้วัสดุไหลจากทั้งสองด้านเข้าสู่พื้นที่ตรงกลาง IMPRESSION DIE FORGING หรือ CLOSED DIE FORGING เรียกอีกอย่างว่าใช้แม่พิมพ์ / แม่พิมพ์ที่บีบอัดวัสดุและ จำกัด การไหลภายในตัวเอง แม่พิมพ์ปิดลงและวัสดุจะเปลี่ยนรูปร่างของช่องแม่พิมพ์/แม่พิมพ์ PRECISION FORGING กระบวนการที่ต้องใช้อุปกรณ์และแม่พิมพ์พิเศษ ผลิตชิ้นส่วนที่ไม่มีแฟลชหรือน้อยมาก กล่าวอีกนัยหนึ่ง ชิ้นส่วนต่างๆ จะมีขนาดใกล้สุดท้าย ในขั้นตอนนี้จะมีการใส่วัสดุที่มีการควบคุมอย่างดีและวางตำแหน่งไว้ในแม่พิมพ์อย่างระมัดระวัง เราใช้วิธีนี้สำหรับรูปทรงที่ซับซ้อนที่มีส่วนบาง ความคลาดเคลื่อนน้อย และมุมร่าง และเมื่อปริมาณมากพอที่จะปรับต้นทุนของแม่พิมพ์และอุปกรณ์ • FLASHLESS FORGING : วางชิ้นงานลงในแม่พิมพ์ในลักษณะที่ไม่มีวัสดุใดไหลออกจากโพรงให้เกิดประกายไฟได้ ดังนั้นจึงไม่จำเป็นต้องตัดแต่งแฟลชที่ไม่ต้องการ เป็นกระบวนการตีขึ้นรูปที่แม่นยำและต้องควบคุมปริมาณวัสดุที่ใช้อย่างใกล้ชิด • การกลึงโลหะหรือการตีขึ้นรูปด้วยรัศมี : ชิ้นงานถูกตีและตีขึ้นรูปตามเส้นรอบวง อาจใช้แมนเดรลเพื่อสร้างรูปทรงเรขาคณิตของชิ้นงานภายในได้เช่นกัน ในการกวัดแกว่ง ชิ้นงานมักจะได้รับหลายครั้งต่อวินาที สิ่งของทั่วไปที่เกิดจากการกรีดคือเครื่องมือปลายแหลม แท่งเรียว ไขควง • การเจาะโลหะ : เราใช้การดำเนินการนี้บ่อยครั้งเป็นการดำเนินการเพิ่มเติมในการผลิตชิ้นส่วน รูหรือโพรงถูกสร้างขึ้นด้วยการเจาะบนพื้นผิวของชิ้นงานโดยไม่เจาะทะลุ โปรดทราบว่าการเจาะจะแตกต่างจากการเจาะซึ่งส่งผลให้เกิดรูทะลุ • HOBBING : กดหมัดที่มีรูปทรงที่ต้องการลงในชิ้นงานแล้วสร้างโพรงที่มีรูปร่างตามต้องการ เราเรียกหมัดนี้ว่า HOB การดำเนินการเกี่ยวข้องกับแรงกดดันสูงและดำเนินการในที่เย็น เป็นผลให้วัสดุทำงานเย็นและความเครียดแข็ง ดังนั้นกระบวนการนี้จึงเหมาะมากสำหรับการผลิตแม่พิมพ์ แม่พิมพ์ และฟันผุสำหรับกระบวนการผลิตอื่นๆ เมื่อทำการผลิตเตาแล้ว เราสามารถผลิตฟันผุที่เหมือนกันจำนวนมากได้อย่างง่ายดายโดยไม่ต้องตัดเฉือนทีละชิ้น • ROLL FORGING หรือ ROLL FORMING : ใช้ลูกกลิ้งตรงข้ามกัน 2 ม้วนเพื่อขึ้นรูปชิ้นส่วนโลหะ ชิ้นงานจะถูกป้อนเข้าในม้วน ลูกกลิ้งหมุนและดึงชิ้นงานเข้าไปในช่องว่าง จากนั้นจึงป้อนงานผ่านส่วนที่เป็นร่องของม้วน และแรงอัดจะทำให้วัสดุมีรูปร่างตามที่ต้องการ ไม่ใช่กระบวนการรีด แต่เป็นกระบวนการตีขึ้นรูป เนื่องจากเป็นกระบวนการที่ไม่ต่อเนื่องมากกว่าการดำเนินการต่อเนื่อง รูปทรงบนร่องม้วนขึ้นรูปวัสดุให้มีรูปร่างและรูปทรงตามต้องการ จะดำเนินการร้อน เนื่องจากเป็นกระบวนการตีขึ้นรูป มันจึงผลิตชิ้นส่วนที่มีคุณสมบัติทางกลที่โดดเด่น ดังนั้นเราจึงใช้มันสำหรับ การผลิตชิ้นส่วนยานยนต์ เช่น เพลาที่ต้องการความทนทานเป็นพิเศษในสภาพแวดล้อมการทำงานที่สมบุกสมบัน • ORBITAL FORGING : ชิ้นงานจะถูกใส่เข้าไปในช่องแม่พิมพ์การตีขึ้นรูปและหลอมด้วยดายบนที่เคลื่อนที่ในวิถีโคจรในขณะที่มันหมุนอยู่บนแกนเอียง ในการปฏิวัติแต่ละครั้ง ดายส่วนบนจะใช้แรงอัดกับชิ้นงานทั้งหมด การหมุนซ้ำหลายครั้งจะทำให้เกิดการตีขึ้นรูปที่เพียงพอ ข้อดีของเทคนิคการผลิตนี้คือการทำงานที่มีเสียงรบกวนต่ำและต้องใช้แรงที่ต่ำกว่า กล่าวอีกนัยหนึ่งด้วยแรงขนาดเล็กเราสามารถหมุนดายหนักรอบแกนเพื่อใช้แรงกดขนาดใหญ่บนส่วนของชิ้นงานที่สัมผัสกับดาย ชิ้นส่วนที่มีรูปร่างเป็นแผ่นหรือรูปทรงกรวยบางครั้งก็เหมาะสมสำหรับกระบวนการนี้ • RING FORGING : เรามักใช้ในการผลิตแหวนไร้ตะเข็บ สต็อกถูกตัดให้ยาว บิดเบี้ยวแล้วเจาะจนสุดเพื่อสร้างรูตรงกลาง จากนั้นวางบนแมนเดรลและค้อนตีขึ้นรูปจากด้านบนขณะที่วงแหวนหมุนช้าๆ จนกว่าจะได้ขนาดที่ต้องการ • โลดโผน : กระบวนการทั่วไปในการต่อชิ้นส่วน เริ่มต้นด้วยชิ้นโลหะตรงที่สอดเข้าไปในรูที่ทำไว้ล่วงหน้าผ่านชิ้นส่วนต่างๆ หลังจากนั้นปลายทั้งสองของชิ้นส่วนโลหะจะถูกหลอมโดยการบีบข้อต่อระหว่างแม่พิมพ์บนและล่าง • COINING : อีกกระบวนการยอดนิยมที่ดำเนินการโดยการกดแบบกลไก โดยออกแรงขนาดใหญ่ในระยะทางสั้นๆ ชื่อ “เหรียญ” มาจากรายละเอียดเล็กๆ น้อยๆ ที่หลอมบนพื้นผิวของเหรียญโลหะ ส่วนใหญ่เป็นกระบวนการตกแต่งสำหรับผลิตภัณฑ์ที่ได้รายละเอียดที่ดีบนพื้นผิวอันเป็นผลมาจากแรงขนาดใหญ่ที่ใช้โดยดายที่ถ่ายโอนรายละเอียดเหล่านี้ไปยังชิ้นงาน • การตีขึ้นรูปโลหะ : ผลิตภัณฑ์เช่นตลับลูกปืนต้องการลูกบอลโลหะที่ผลิตขึ้นอย่างแม่นยำคุณภาพสูง ในเทคนิคหนึ่งที่เรียกว่า SKEW ROLLING เราใช้ม้วนตรงข้ามสองม้วนที่หมุนอย่างต่อเนื่องในขณะที่ป้อนสต็อกเข้าในม้วนอย่างต่อเนื่อง ที่ปลายด้านหนึ่งของลูกกลิ้งโลหะสองม้วนจะถูกขับออกมาเป็นผลิตภัณฑ์ วิธีที่สองสำหรับการตีขึ้นรูปลูกโลหะคือการใช้แม่พิมพ์ที่บีบสต็อควัสดุที่วางไว้ระหว่างกันเพื่อให้ได้รูปทรงกลมของโพรงแม่พิมพ์ บ่อยครั้งการผลิตลูกบอลต้องมีขั้นตอนเพิ่มเติมบางอย่าง เช่น การเก็บผิวละเอียดและการขัดเงา เพื่อที่จะได้เป็นผลิตภัณฑ์คุณภาพสูง • ISOTHERMAL FORGING / HOT DIE FORGING : กระบวนการที่มีราคาแพงจะดำเนินการก็ต่อเมื่อผลประโยชน์ / มูลค่าต้นทุนเหมาะสมเท่านั้น กระบวนการทำงานที่ร้อนโดยที่แม่พิมพ์ได้รับความร้อนจนถึงอุณหภูมิเดียวกับชิ้นงาน เนื่องจากทั้งแม่พิมพ์และชิ้นงานมีอุณหภูมิใกล้เคียงกัน จึงไม่มีการหล่อเย็นและลักษณะการไหลของโลหะจึงดีขึ้น การดำเนินการนี้เหมาะอย่างยิ่งสำหรับซูเปอร์อัลลอยและวัสดุที่มีความสามารถในการหลอมและวัสดุที่ด้อยกว่าซึ่ง คุณสมบัติทางกลมีความไวต่อการเปลี่ยนแปลงและการเปลี่ยนแปลงของอุณหภูมิเล็กน้อย • METAL SIZING : เป็นกระบวนการจบงานแบบเย็น การไหลของวัสดุไม่มีข้อจำกัดในทุกทิศทาง ยกเว้นทิศทางที่ใช้แรง เป็นผลให้ได้พื้นผิวที่ดีมากและได้ขนาดที่แม่นยำ • HIGH ENERGY RATE FORGING : เทคนิคนี้เกี่ยวข้องกับแม่พิมพ์ด้านบนที่ติดกับแขนของลูกสูบซึ่งถูกผลักอย่างรวดเร็วเมื่อส่วนผสมของเชื้อเพลิงและอากาศถูกจุดไฟด้วยหัวเทียน คล้ายกับการทำงานของลูกสูบในเครื่องยนต์ของรถยนต์ แม่พิมพ์จะกระทบกับชิ้นงานอย่างรวดเร็ว จากนั้นจึงกลับสู่ตำแหน่งเดิมอย่างรวดเร็วด้วยแรงกดต้าน งานถูกปลอมแปลงภายในไม่กี่มิลลิวินาที ดังนั้นจึงไม่มีเวลาให้งานเย็นลง สิ่งนี้มีประโยชน์สำหรับชิ้นส่วนที่ขึ้นรูปยากซึ่งมีคุณสมบัติทางกลที่ไวต่ออุณหภูมิมาก กล่าวอีกนัยหนึ่ง กระบวนการนี้รวดเร็วมากจนทำให้ชิ้นส่วนเกิดขึ้นภายใต้อุณหภูมิคงที่ตลอด และไม่มีการไล่ระดับอุณหภูมิที่ส่วนต่อประสานของแม่พิมพ์/ชิ้นงาน • ใน DIE FORGING โลหะจะถูกตีระหว่างบล็อกเหล็กสองอันที่เข้าชุดกันซึ่งมีรูปร่างพิเศษอยู่ในนั้น เรียกว่าแม่พิมพ์ เมื่อโลหะถูกตอกระหว่างแม่พิมพ์ จะถือว่ารูปร่างเหมือนกับรูปร่างในแม่พิมพ์ เมื่อถึงรูปร่างสุดท้ายแล้ว นำออกมาผึ่งให้เย็น กระบวนการนี้ผลิตชิ้นส่วนที่แข็งแรงซึ่งมีรูปร่างที่แม่นยำ แต่ต้องใช้เงินลงทุนจำนวนมากสำหรับแม่พิมพ์เฉพาะทาง การตีขึ้นรูปด้วยอารมณ์เสียจะเพิ่มเส้นผ่านศูนย์กลางของชิ้นส่วนโลหะโดยการทำให้แบน โดยทั่วไปจะใช้ทำชิ้นส่วนขนาดเล็ก โดยเฉพาะอย่างยิ่งเพื่อสร้างหัวบนรัด เช่น สลักเกลียวและตะปู • โลหะผง / กระบวนการผลิตผง : ตามชื่อหมายถึง มันเกี่ยวข้องกับกระบวนการผลิตสำหรับการทำชิ้นส่วนที่เป็นของแข็งของรูปทรงและรูปร่างบางอย่างจากผง หากใช้ผงโลหะเพื่อจุดประสงค์นี้ จะเป็นขอบเขตของผงโลหะ และหากใช้ผงที่ไม่ใช่โลหะ ก็จะเป็นการแปรรูปผง ชิ้นส่วนที่เป็นของแข็งผลิตจากผงโดยการกดและการเผาผนึก. POWDER PRESSING ใช้อัดแป้งให้เป็นรูปทรงที่ต้องการ อย่างแรก วัสดุหลักจะถูกทำให้เป็นผง โดยแบ่งเป็นอนุภาคเล็กๆ จำนวนมาก ส่วนผสมของแป้งจะถูกเติมลงในแม่พิมพ์ จากนั้นหมัดจะเคลื่อนเข้าหาแป้งและอัดให้เป็นรูปร่างที่ต้องการ ส่วนใหญ่ดำเนินการที่อุณหภูมิห้องโดยได้ผงกดส่วนที่เป็นของแข็งและเรียกว่ากะทัดรัดสีเขียว สารยึดเกาะและสารหล่อลื่นมักใช้เพื่อเพิ่มความสามารถในการอัดแน่น เรามีความสามารถในการขึ้นรูปผงโดยใช้เครื่องอัดไฮดรอลิกที่มีความจุหลายพันตัน นอกจากนี้เรายังมีแท่นกดแบบดับเบิ้ลแอ็คชันพร้อมหมัดบนและล่างตรงข้าม เช่นเดียวกับแท่นกดหลายอันสำหรับรูปทรงชิ้นส่วนที่ซับซ้อนสูง ความสม่ำเสมอซึ่งเป็นความท้าทายที่สำคัญสำหรับโรงงานโลหะวิทยา / โรงงานแปรรูปผงหลายแห่งนั้นไม่ใช่ปัญหาใหญ่สำหรับ AGS-TECH เนื่องจากประสบการณ์ที่กว้างขวางของเราในการผลิตชิ้นส่วนดังกล่าวเป็นเวลาหลายปี แม้แต่ชิ้นส่วนที่หนากว่าซึ่งความสม่ำเสมอก่อให้เกิดความท้าทาย เราก็ประสบความสำเร็จ ถ้าเรามุ่งมั่นในโครงการของคุณ เราจะทำชิ้นส่วนของคุณ หากเราพบความเสี่ยงที่อาจเกิดขึ้น เราจะแจ้งให้คุณทราบใน ล่วงหน้า. POWDER SINTERING ซึ่งเป็นขั้นตอนที่สอง เกี่ยวข้องกับการเพิ่มอุณหภูมิในระดับหนึ่งและการรักษาอุณหภูมิที่ระดับนั้นเป็นระยะเวลาหนึ่งเพื่อให้อนุภาคผงในส่วนที่ถูกกดสามารถเกาะติดกันได้ ส่งผลให้มีการยึดเกาะและความแข็งแรงของชิ้นงานมากขึ้น การเผาผนึกเกิดขึ้นใกล้กับอุณหภูมิหลอมเหลวของผง ในระหว่างการเผาผนึกจะเกิดขึ้น ความแข็งแรงของวัสดุ ความหนาแน่น ความเหนียว การนำความร้อน การนำไฟฟ้าจะเพิ่มขึ้น เรามีเตาเผาแบบแบตช์และแบบต่อเนื่องสำหรับการเผาผนึก ความสามารถอย่างหนึ่งของเราคือปรับระดับความพรุนของชิ้นส่วนที่เราผลิต ตัวอย่างเช่น เราสามารถผลิตตัวกรองโลหะได้โดยการรักษาชิ้นส่วนที่มีรูพรุนในระดับหนึ่ง ใช้เทคนิคที่เรียกว่า IMPREGNATION เติมรูพรุนในโลหะด้วยของเหลว เช่น น้ำมัน เราผลิตตลับลูกปืนที่เคลือบด้วยน้ำมันที่หล่อลื่นตัวเองได้ ในกระบวนการ INFILTRATION เราเติมรูพรุนของโลหะด้วยโลหะอื่นที่มีจุดหลอมเหลวต่ำกว่าวัสดุฐาน ส่วนผสมจะถูกทำให้ร้อนจนถึงอุณหภูมิระหว่างอุณหภูมิหลอมเหลวของโลหะทั้งสอง เป็นผลให้สามารถรับคุณสมบัติพิเศษบางอย่างได้ เรายังดำเนินการขั้นที่สองอยู่บ่อยครั้ง เช่น การตัดเฉือนและการตีขึ้นรูปชิ้นส่วนที่ผลิตด้วยผงแป้ง เมื่อจำเป็นต้องได้รับคุณสมบัติหรือคุณสมบัติพิเศษ หรือเมื่อสามารถผลิตชิ้นส่วนได้โดยใช้ขั้นตอนกระบวนการน้อยลง ISOSTATIC PRESSING : ในกระบวนการนี้ แรงดันของของไหลถูกใช้เพื่อทำให้ชิ้นงานอัดแน่น ผงโลหะวางอยู่ในแม่พิมพ์ที่ทำจากภาชนะที่ปิดได้ยืดหยุ่นได้ ในการกดแบบไอโซสแตติก แรงดันจะถูกใช้จากทั่วทุกมุม ซึ่งตรงกันข้ามกับแรงดันตามแนวแกนที่พบในการกดแบบทั่วไป ข้อดีของการกดแบบไอโซสแตติกคือความหนาแน่นสม่ำเสมอภายในชิ้นงาน โดยเฉพาะอย่างยิ่งสำหรับชิ้นส่วนขนาดใหญ่หรือหนาขึ้น ซึ่งเป็นคุณสมบัติที่เหนือกว่า ข้อเสียคือรอบเวลานานและความแม่นยำทางเรขาคณิตค่อนข้างต่ำ การกด ISOSTATIC แบบเย็นจะดำเนินการที่อุณหภูมิห้องและแม่พิมพ์ที่ยืดหยุ่นได้นั้นทำจากยาง พีวีซี หรือยูรีเทนหรือวัสดุที่คล้ายกัน ของเหลวที่ใช้สำหรับอัดแรงดันและอัดแน่นคือน้ำมันหรือน้ำ การเผาผนึกแบบธรรมดาของคอมแพคสีเขียวเป็นไปตามนี้ ในทางกลับกัน การกด ISOSTATIC แบบร้อนจะดำเนินการที่อุณหภูมิสูงและวัสดุแม่พิมพ์คือโลหะแผ่นหรือเซรามิกที่มีจุดหลอมเหลวสูงพอที่จะทนต่ออุณหภูมิ ของเหลวอัดแรงดันมักเป็นก๊าซเฉื่อย การกดและการเผาจะดำเนินการในขั้นตอนเดียว ความพรุนถูกขจัดออกไปเกือบหมด ได้โครงสร้าง uniform grain ข้อดีของการกดไอโซสแตติกแบบร้อนคือสามารถผลิตชิ้นส่วนเทียบได้กับการหล่อและการตีขึ้นรูปรวมกัน ในขณะที่ทำวัสดุที่ไม่เหมาะสำหรับการหล่อและการตีขึ้นรูป ข้อเสียของการกดแบบไอโซสแตติกแบบร้อนคือรอบเวลาสูงและมีค่าใช้จ่าย เหมาะสำหรับชิ้นส่วนวิกฤตที่มีปริมาณน้อย การฉีดขึ้นรูปโลหะ : กระบวนการที่เหมาะสมมากสำหรับการผลิตชิ้นส่วนที่ซับซ้อนที่มีผนังบางและรูปทรงที่มีรายละเอียด เหมาะที่สุดสำหรับชิ้นส่วนขนาดเล็ก ผงและสารยึดเกาะโพลีเมอร์ถูกผสม ให้ความร้อน และฉีดเข้าไปในแม่พิมพ์ สารยึดเกาะโพลีเมอร์เคลือบพื้นผิวของอนุภาคผง หลังจากการขึ้นรูป สารยึดเกาะจะถูกลบออกโดยการให้ความร้อนที่อุณหภูมิต่ำของละลายโดยใช้ตัวทำละลาย ROLL COMPACTION / POWDER ROLLING : ผงใช้ในการผลิตแถบหรือแผ่นต่อเนื่อง ผงถูกป้อนจากตัวป้อนและบดอัดด้วยลูกกลิ้งหมุนสองม้วนเป็นแผ่นหรือแถบ การดำเนินการจะดำเนินการเย็น แผ่นถูกนำไปเผาในเตาเผา กระบวนการเผาผนึกอาจทำซ้ำเป็นครั้งที่สอง การอัดขึ้นรูปผง : ชิ้นส่วนที่มีอัตราส่วนความยาวต่อเส้นผ่านศูนย์กลางมากผลิตขึ้นโดยการอัดภาชนะโลหะแผ่นบางที่มีผง LOOSE SINTERING : ตามชื่อของมัน มันเป็นวิธีการอัดแน่นและการเผาผนึกแบบไม่มีแรงดัน เหมาะสำหรับการผลิตชิ้นส่วนที่มีรูพรุนมาก เช่น ตัวกรองโลหะ ผงถูกป้อนเข้าไปในโพรงแม่พิมพ์โดยไม่ต้องบดอัด LOOSE SINTERING : ตามชื่อของมัน มันเป็นวิธีการอัดแน่นและการเผาผนึกแบบไม่มีแรงดัน เหมาะสำหรับการผลิตชิ้นส่วนที่มีรูพรุนมาก เช่น ตัวกรองโลหะ ผงถูกป้อนเข้าไปในโพรงแม่พิมพ์โดยไม่ต้องบดอัด SPARK SINTERING : ผงถูกบีบอัดในแม่พิมพ์โดยใช้หมัดตรงข้ามสองตัวและกระแสไฟฟ้ากำลังสูงถูกนำไปใช้กับหมัดและผ่านผงอัดที่ประกบอยู่ระหว่างพวกเขา กระแสไฟสูงจะเผาฟิล์มพื้นผิวออกจากอนุภาคผงและเผามันด้วยความร้อนที่สร้างขึ้น กระบวนการนี้รวดเร็วเพราะไม่ได้ใช้ความร้อนจากภายนอก แต่สร้างจากภายในแม่พิมพ์แทน HOT PRESSING : ผงถูกกดและเผาในขั้นตอนเดียวในแม่พิมพ์ที่สามารถทนต่ออุณหภูมิสูง เมื่อแม่พิมพ์อัดแน่น ผงแป้งจะถูกใช้ความร้อน ความแม่นยำที่ดีและคุณสมบัติทางกลที่ได้จากวิธีนี้ทำให้เป็นตัวเลือกที่น่าสนใจ แม้แต่โลหะทนไฟก็สามารถแปรรูปได้โดยใช้วัสดุแม่พิมพ์ เช่น กราไฟต์ CLICK Product Finder-Locator Service เมนูก่อนหน้า
- Sheet Metal Forming Fabrication, Stamping, Punching, Deep Drawing, CNC
Sheet Metal Forming and Fabrication, Stamping, Punching, Bending, Progressive Die, Spot Welding, Deep Drawing, Metal Blanking and Slitting at AGS-TECH Inc. ปั๊มขึ้นรูปและโลหะแผ่น เรานำเสนอการปั๊มโลหะแผ่น การขึ้นรูป การขึ้นรูป การดัด การเจาะ การตัดขอบ การตัด การเจาะ การบาก การกัด การโกน การอัดขึ้นรูป การขึ้นรูป การวาดลึกโดยใช้ดายแบบเจาะเดี่ยว / จังหวะเดียว รวมถึงการดายและการปั่นแบบโปรเกรสซีฟ การขึ้นรูปยางและ ไฮโดรฟอร์ม; การตัดแผ่นโลหะโดยใช้วอเตอร์เจ็ท, พลาสม่า, เลเซอร์, เลื่อย, เปลวไฟ; การประกอบแผ่นโลหะโดยใช้การเชื่อม, การเชื่อมแบบจุด; โป่งและดัดท่อโลหะแผ่น; การตกแต่งพื้นผิวโลหะแผ่นรวมถึงการพ่นสีแบบจุ่มหรือแบบพ่นสี การเคลือบสีฝุ่นด้วยไฟฟ้าสถิต การชุบอโนไดซ์ การชุบ การสปัตเตอร์และอื่น ๆ บริการของเรามีตั้งแต่การสร้างต้นแบบแผ่นโลหะอย่างรวดเร็วไปจนถึงการผลิตในปริมาณมาก เราขอแนะนำให้คุณคลิกที่นี่เพื่อดาวน์โหลดภาพประกอบแผนผังของกระบวนการผลิตและปั๊มขึ้นรูปโลหะแผ่นโดย AGS-TECH Inc. วิธีนี้จะช่วยให้คุณเข้าใจข้อมูลที่เราให้ไว้ด้านล่างนี้ได้ดียิ่งขึ้น • การตัดแผ่นโลหะ : เรามีบริการตัดและแยกชิ้นส่วน การตัดแผ่นโลหะแผ่นในแต่ละครั้งและโดยพื้นฐานแล้วไม่มีการสูญเสียวัสดุ ในขณะที่การกลึงตัดรูปร่างไม่สามารถวางได้อย่างแม่นยำ ดังนั้นจึงสิ้นเปลืองวัสดุจำนวนหนึ่ง หนึ่งในกระบวนการที่ได้รับความนิยมมากที่สุดของเราคือ PUNCHING ซึ่งชิ้นส่วนของวัสดุทรงกลมหรือรูปทรงอื่นๆ ถูกตัดออกจากแผ่นโลหะ ชิ้นส่วนที่ถูกตัดออกคือของเสีย การเจาะอีกรูปแบบหนึ่งคือ SLOTTING ซึ่งเจาะรูสี่เหลี่ยมหรือยาว ในทางตรงกันข้าม BLANKING เป็นกระบวนการเดียวกับการต่อย โดยความแตกต่างของชิ้นงานที่ถูกตัดออกคืองานและเก็บรักษาไว้ FINE BLANKING ซึ่งเป็นรุ่นที่เหนือกว่าของ blanking สร้างการตัดด้วยความคลาดเคลื่อนอย่างใกล้ชิดและขอบเรียบตรง และไม่ต้องการการดำเนินการรองเพื่อความสมบูรณ์แบบของชิ้นงาน อีกกระบวนการหนึ่งที่เราใช้บ่อยคือ SLITTING ซึ่งเป็นกระบวนการตัดเฉือนโดยที่โลหะแผ่นถูกตัดด้วยใบมีดกลมสองใบที่ตรงข้ามกันในทางตรงหรือทางโค้ง ที่เปิดกระป๋องเป็นตัวอย่างง่ายๆ ของกระบวนการกรีด อีกรูปแบบหนึ่งที่ได้รับความนิยม process สำหรับเราคือ PERFORATING ซึ่งมีรูหลายรูกลมหรือรูปทรงอื่นๆ ถูกเจาะด้วยแผ่นโลหะในรูปแบบที่แน่นอน ตัวอย่างทั่วไปของผลิตภัณฑ์ที่มีรูพรุนคือตัวกรองโลหะที่มีรูจำนวนมากสำหรับของเหลว ในการตัดเฉือนเป็นกระบวนการตัดโลหะแผ่นแบบอื่น เราจะนำวัสดุออกจากชิ้นงานโดยเริ่มจากขอบหรือที่อื่นแล้วตัดเข้าด้านในจนกว่าจะได้รูปทรงที่ต้องการ เป็นกระบวนการที่ก้าวหน้าซึ่งการดำเนินการแต่ละครั้งจะนำชิ้นส่วนอื่นออกจนกว่าจะได้รูปทรงที่ต้องการ สำหรับการผลิตขนาดเล็ก บางครั้งเราใช้กระบวนการที่ค่อนข้างช้ากว่าที่เรียกว่า NIBBLING ซึ่งประกอบด้วยการเจาะรูที่ทับซ้อนกันอย่างรวดเร็วหลายๆ รู เพื่อทำให้การตัดมีขนาดใหญ่ขึ้นที่ซับซ้อนมากขึ้น ในการตัดแบบโปรเกรสซีฟ เราใช้ชุดของการดำเนินการต่างๆ เพื่อให้ได้การตัดครั้งเดียวหรือรูปทรงที่แน่นอน สุดท้าย การโกน กระบวนการรองช่วยให้เราปรับปรุงขอบของการตัดที่ได้ดำเนินการไปแล้ว ใช้สำหรับตัดเศษ ขอบหยาบ ในงานโลหะแผ่น • การดัดแผ่นโลหะ : นอกจากการตัด การดัดเป็นกระบวนการที่สำคัญโดยที่เราไม่สามารถผลิตผลิตภัณฑ์ส่วนใหญ่ได้ ส่วนใหญ่เป็นการทำงานที่เย็น แต่บางครั้งก็ทำเมื่ออุ่นหรือร้อน เราใช้แม่พิมพ์และกดเป็นส่วนใหญ่สำหรับการดำเนินการนี้ ในการดัดแบบโปรเกรสซีฟ เราใช้ชุดของการเจาะและดายแบบต่างๆ เพื่อให้ได้ส่วนโค้งเดียวหรือรูปทรงบางอย่าง AGS-TECH ใช้กระบวนการดัดที่หลากหลายและทำการเลือกโดยขึ้นอยู่กับวัสดุชิ้นงาน ขนาด ความหนา ขนาดโค้งที่ต้องการ รัศมี ความโค้งและมุมโค้งงอ ตำแหน่งของโค้งงอ ความประหยัดในการใช้งาน ปริมาณที่ผลิต... เป็นต้น เราใช้ V-BENDING โดยที่หมัดรูปตัว V บังคับให้แผ่นโลหะเข้าไปในแม่พิมพ์รูปตัว V แล้วดัดให้โค้ง เหมาะสำหรับทั้งมุมแหลมและมุมป้าน และมุมระหว่างมุม 90 องศา เราทำการดัดขอบโดยใช้การเช็ดดาย อุปกรณ์ของเราช่วยให้เราได้มุมที่ใหญ่กว่า 90 องศา ในการดัดขอบ ชิ้นงานจะถูกประกบระหว่างแผ่นแรงดันกับแม่พิมพ์ พื้นที่สำหรับการดัดจะอยู่ที่ขอบแม่พิมพ์ และส่วนที่เหลือของชิ้นงานจะถูกยึดไว้เหนือ space เหมือนคานคาน เมื่อหมัดทำงานบนส่วนคานยื่น มันจะงอเหนือขอบของดาย FLANGING เป็นกระบวนการดัดขอบทำให้เกิดมุม 90 องศา เป้าหมายหลักของการดำเนินการคือการกำจัดขอบที่แหลมคมและได้พื้นผิวทางเรขาคณิตเพื่อให้ประกอบชิ้นส่วนได้ง่ายขึ้น BEADING เป็นกระบวนการดัดขอบทั่วไปอีกรูปแบบหนึ่งทำให้เกิดการม้วนงอเหนือขอบของชิ้นส่วน ในทางกลับกัน HEMMING จะทำให้ขอบของแผ่นพับเข้าหาตัวเองจนสุด ใน SEAMING ขอบของทั้งสองส่วนจะงอเข้าหากันและต่อเข้าด้วยกัน ในทางกลับกัน DOUBLE SEAMING ให้ข้อต่อโลหะแผ่นที่กันน้ำและอากาศเข้า คล้ายกับการดัดขอบ กระบวนการที่เรียกว่า ROTARY BENDING จะใช้กระบอกสูบที่มีการตัดมุมที่ต้องการและทำหน้าที่เป็นหมัด เมื่อแรงถูกส่งไปยังหมัด มันปิดด้วยชิ้นงาน ร่องของกระบอกสูบทำให้ส่วนเท้าแขนมีมุมที่ต้องการ ร่องสามารถมีมุมที่เล็กกว่าหรือใหญ่กว่า 90 องศา ในการดัดแบบ AIR BENDING เราไม่จำเป็นต้องมีดายตัวล่างเพื่อให้ได้ร่องที่ทำมุม แผ่นโลหะรองรับ two พื้นผิวด้านตรงข้ามและในระยะทางที่กำหนด จากนั้นหมัดจะใช้แรงที่ตำแหน่งที่ถูกต้องและโค้งงอชิ้นงาน CHANNEL BENDING ทำได้โดยใช้หมัดและดายรูปแชนเนล และ U-BEND ทำได้ด้วยหมัดรูปตัว U OFFSET BENDING สร้างออฟเซ็ตบนแผ่นโลหะ ROLL BENDING เทคนิคที่ดีสำหรับงานหนาและการดัดแผ่นโลหะขนาดใหญ่ ใช้สามม้วนในการป้อนและดัดแผ่นให้โค้งตามต้องการ มีการจัดเรียงม้วนเพื่อให้ได้ส่วนโค้งที่ต้องการของงาน ระยะห่างและมุมระหว่างม้วนจะถูกควบคุมเพื่อให้ได้ผลลัพธ์ที่ต้องการ ม้วนที่เคลื่อนย้ายได้ทำให้สามารถควบคุมความโค้งได้ TUBE FORMING เป็นอีกหนึ่งวิธีการดัดขึ้นรูปโลหะแผ่นยอดนิยมที่เกี่ยวข้องกับการดายหลายแบบ หลอดจะได้รับหลังจากการกระทำหลายอย่าง CORRUGATION ทำได้โดยการดัด โดยทั่วไปจะเป็นการดัดแบบสมมาตรเป็นระยะสม่ำเสมอทั่วทั้งแผ่นโลหะ รูปทรงต่างๆ สามารถใช้ทำลอนลอนได้ แผ่นโลหะลูกฟูกมีความแข็งมากกว่าและทนต่อการดัดงอได้ดีกว่า ดังนั้นจึงมีการใช้งานในอุตสาหกรรมก่อสร้าง SHEET METAL ROLL FORMING กระบวนการผลิตแบบต่อเนื่อง manufacturing ถูกปรับใช้เพื่อโค้งงอตัดขวางของรูปทรงเรขาคณิตบางประเภทโดยใช้ม้วน และงานจะงอเป็นขั้นตอนตามลำดับ โดยม้วนสุดท้ายจะทำงานเสร็จ ในบางกรณีจะใช้ม้วนเดียวและในบางกรณีจะใช้ชุดม้วน • กระบวนการตัดและดัดแผ่นโลหะแบบผสมผสาน : กระบวนการเหล่านี้เป็นกระบวนการที่ตัดและโค้งงอในเวลาเดียวกัน ใน PIERCING หลุมจะถูกสร้างขึ้นโดยใช้หมัดปลายแหลม เมื่อหมัดขยายรูในแผ่น วัสดุจะงอพร้อมกันเป็นหน้าแปลนภายในของรู หน้าแปลนที่ได้รับอาจมีหน้าที่สำคัญ ในทางกลับกัน การทำงานของ LANCING จะตัดและดัดแผ่นเพื่อสร้างรูปทรงที่ยกขึ้น • METAL TUBE BULGING AND BENDING : ในการ BULGING บางส่วนภายในของท่อกลวงจะได้รับแรงดัน ทำให้ท่อนูนออกมาด้านนอก เนื่องจากท่ออยู่ภายในแม่พิมพ์ รูปทรงนูนจึงถูกควบคุมโดยรูปร่างของแม่พิมพ์ ในการดัดงอ ท่อโลหะถูกยืดออกโดยใช้แรงที่ขนานกับแกนของท่อและแรงดัดงอเพื่อดึงท่อเหนือบล็อกของแบบฟอร์ม ในการดึง DRAW BENDING เรายึดท่อไว้ใกล้ปลายท่อกับบล็อกแบบหมุนที่ดัดท่อขณะหมุน สุดท้าย ในการดัดด้วยแรงอัด ท่อจะถูกจับโดยแรงไปยังบล็อกแบบคงที่ และไดย์จะโค้งงอเหนือบล็อคฟอร์ม • DEEP DRAWING : หนึ่งในการดำเนินการที่ได้รับความนิยมมากที่สุดของเรา ใช้หมัด แม่พิมพ์ที่เข้าชุดกัน และที่ยึดเปล่า ช่องว่างโลหะแผ่นถูกวางไว้เหนือช่องเปิดของแม่พิมพ์และหมัดจะเคลื่อนไปทางช่องว่างที่ถือโดยที่ยึดช่องว่าง เมื่อสัมผัสกันแล้ว หมัดจะบังคับให้แผ่นโลหะเข้าไปในโพรงแม่พิมพ์เพื่อสร้างผลิตภัณฑ์ การดำเนินการดึงลึกคล้ายกับการตัด อย่างไรก็ตาม ระยะห่างระหว่างหมัดและดายทำให้แผ่นงานไม่ถูกตัด อีกปัจจัยที่ทำให้แผ่นงานดึงลึกและไม่ตัดคือมุมโค้งมนของดายและหมัดซึ่งป้องกันแรงเฉือนและการตัด เพื่อให้ได้ภาพที่ลึกยิ่งขึ้น กระบวนการ REDRAWING จะถูกปรับใช้โดยที่การวาดภาพลึกที่ตามมาจะเกิดขึ้นในส่วนที่ได้ผ่านกระบวนการวาดลึกแล้ว ใน REVERSE REDRAWING ส่วนที่วาดลึกจะพลิกและวาดไปในทิศทางตรงกันข้าม การวาดลึกสามารถให้วัตถุที่มีรูปร่างไม่ปกติ เช่น ถ้วยทรงโดม เทเปอร์ หรือขั้นบันได In EMBOSSING เราใช้ไดคู่ตัวผู้และตัวเมียเพื่อสร้างความประทับใจให้กับแผ่นโลหะด้วยการออกแบบหรือสคริปต์ • SPINNING : การดำเนินการที่ชิ้นงานเรียบหรือขึ้นรูปไว้ระหว่างแกนหมุนที่หมุนได้และสต็อกส่วนท้าย และเครื่องมือจะใช้แรงกดเฉพาะที่กับงานขณะที่ค่อยๆ เคลื่อนตัวขึ้นไปยังแกนกลาง เป็นผลให้ชิ้นงานถูกห่อด้วยแมนเดรลและมีรูปร่าง เราใช้เทคนิคนี้เป็นทางเลือกแทนการวาดแบบลึกซึ่งปริมาณการสั่งซื้อมีขนาดเล็ก ชิ้นส่วนมีขนาดใหญ่ (เส้นผ่านศูนย์กลางไม่เกิน 20 ฟุต) และมีเส้นโค้งที่เป็นเอกลักษณ์ แม้ว่าราคาต่อชิ้นโดยทั่วไปจะสูงกว่า แต่ค่าใช้จ่ายในการตั้งค่าสำหรับการหมุนด้วย CNC นั้นต่ำเมื่อเทียบกับการวาดลึก ในทางตรงกันข้าม การวาดลึกต้องใช้เงินลงทุนเริ่มต้นสูงสำหรับการติดตั้ง แต่ต้นทุนต่อชิ้นจะต่ำเมื่อมีการผลิตชิ้นส่วนในปริมาณมาก อีกเวอร์ชันหนึ่งของกระบวนการนี้คือ SHEAR SPINNING ซึ่งมีการไหลของโลหะภายในชิ้นงานด้วย การไหลของโลหะจะลดความหนาของชิ้นงานเมื่อดำเนินการ อีกกระบวนการที่เกี่ยวข้องคือ TUBE SPINNING ซึ่งใช้กับชิ้นส่วนทรงกระบอก นอกจากนี้ในกระบวนการนี้มีการไหลของโลหะภายในชิ้นงาน ความหนาจึงลดลงและความยาวของท่อเพิ่มขึ้น สามารถเคลื่อนย้ายเครื่องมือเพื่อสร้างลักษณะภายนอกหรือภายในท่อได้ • RUBBER FORMING OF SHEET METAL : ยางหรือวัสดุโพลียูรีเทนใส่ในแม่พิมพ์ภาชนะและวางชิ้นงานไว้บนพื้นผิวยาง จากนั้นใช้หมัดกับชิ้นงานและดันเข้าไปในยาง เนื่องจากแรงดันที่เกิดจากยางมีน้อย ความลึกของชิ้นส่วนที่ผลิตจึงมีจำกัด เนื่องจากต้นทุนเครื่องมือต่ำ กระบวนการนี้จึงเหมาะสำหรับการผลิตปริมาณน้อย • HYDROFORMING : คล้ายกับการขึ้นรูปยาง ในกระบวนการนี้ งานโลหะแผ่นถูกกดด้วยหมัดเข้าไปในของเหลวที่มีแรงดันภายในห้อง งานโลหะแผ่นถูกประกบระหว่างหมัดกับไดอะแฟรมยาง ไดอะแฟรมล้อมรอบชิ้นงานอย่างสมบูรณ์ และแรงดันของของไหลจะบังคับให้ขึ้นรูปบนหมัด การวาดภาพลึกมากยิ่งลึกกว่าในกระบวนการวาดลึกด้วยเทคนิคนี้ เราผลิตดายแบบเจาะเดี่ยวและดายโปรเจสซีฟขึ้นอยู่กับส่วนของคุณ แม่พิมพ์ปั๊มขึ้นรูปจังหวะเดียวเป็นวิธีที่ประหยัดต้นทุนสำหรับการผลิตชิ้นส่วนโลหะแผ่นอย่างง่ายปริมาณมาก เช่น แหวนรองอย่างรวดเร็ว แม่พิมพ์โปรเกรสซีฟหรือเทคนิคการวาดลึกใช้สำหรับการผลิตรูปทรงที่ซับซ้อนมากขึ้น สามารถใช้วอเตอร์เจ็ท เลเซอร์ หรือเครื่องตัดพลาสม่าเพื่อผลิตชิ้นส่วนโลหะแผ่นของคุณในราคาไม่แพง รวดเร็ว และแม่นยำ ทั้งนี้ขึ้นอยู่กับกรณีของคุณ ซัพพลายเออร์หลายรายไม่มีความคิดเกี่ยวกับเทคนิคทางเลือกเหล่านี้หรือไม่มี ดังนั้นพวกเขาจึงผ่านกรรมวิธีการผลิตแม่พิมพ์และเครื่องมือที่ใช้เวลานานและมีราคาแพง ซึ่งจะเสียเวลาและเงินของลูกค้าเท่านั้น หากคุณต้องการส่วนประกอบโลหะแผ่นที่สร้างขึ้นเอง เช่น เปลือกหุ้ม ตัวเรือนอิเล็กทรอนิกส์...ฯลฯ อย่างรวดเร็วภายในไม่กี่วัน ติดต่อเราเพื่อขอรับบริการ RAPID SHEET METAL PROTOTYPING ของเรา CLICK Product Finder-Locator Service เมนูก่อนหน้า
- Plastic Rubber Metal Extrusions, Extrusion Dies, Aluminum Extruding
Plastic Rubber Metal Extrusions, Extrusion Dies, Aluminum Extruding, Pipe Tube Forming, Plastic Profiles, Metal Profiles Manufacturing, PVC at AGS-TECH Inc. Extrusions, Extruded Products, Extrudates เราใช้ the EXTRUSION process เพื่อผลิตผลิตภัณฑ์ที่มีโปรไฟล์ตัดขวางคงที่ เช่น หลอด ท่อ และแผ่นระบายความร้อน แม้ว่าวัสดุจำนวนมากสามารถอัดรีดได้ แต่การอัดขึ้นรูปโดยทั่วไปของเราทำจากโลหะ โพลีเมอร์ / พลาสติก เซรามิกที่ได้จากวิธีการอัดรีดแบบเย็น แบบอุ่น หรือแบบร้อน เราเรียกว่าชิ้นส่วนที่อัดรีดหรืออัดรีดถ้าเป็นพหูพจน์ กระบวนการพิเศษบางอย่างที่เรายังดำเนินการอยู่ ได้แก่ การโอเวอร์แจ็คเก็ต การอัดรีดร่วม และการอัดรีดแบบผสม เราขอแนะนำให้คุณคลิกที่นี่ to ดาวน์โหลดภาพประกอบแผนผังของกระบวนการรีดขึ้นรูปโลหะเซรามิกและพลาสติกโดย AGS-TECH Inc. วิธีนี้จะช่วยให้คุณเข้าใจข้อมูลที่เราให้ไว้ด้านล่างนี้ได้ดียิ่งขึ้น ในวัสดุอัดรีดที่จะอัดรีดจะถูกผลักหรือดึงผ่านแม่พิมพ์ที่มีโปรไฟล์หน้าตัดที่ต้องการ กระบวนการนี้สามารถใช้ในการผลิตหน้าตัดที่ซับซ้อนพร้อมผิวสำเร็จที่ยอดเยี่ยมและทำงานกับวัสดุที่เปราะ สามารถผลิตชิ้นส่วนที่มีความยาวเท่าใดก็ได้โดยใช้กระบวนการนี้ เพื่อทำให้ขั้นตอนกระบวนการง่ายขึ้น: 1.) ในการรีดร้อนหรือร้อน วัสดุจะถูกทำให้ร้อนและบรรจุลงในภาชนะที่กด วัสดุถูกกดและผลักออกจากแม่พิมพ์ 2.) เครื่องอัดรีดที่ผลิตขึ้นจะถูกยืดสำหรับการยืดผม การอบชุบด้วยความร้อน หรืองานเย็นเพื่อเพิ่มคุณสมบัติ ในทางกลับกัน COLD EXTRUSION เกิดขึ้นที่อุณหภูมิห้องและมีข้อดีของการเกิดออกซิเดชันน้อย มีความแข็งแรงสูง มีความคลาดเคลื่อนที่ใกล้กว่า ผิวสำเร็จที่ดีและมีความคงทน WARM EXTRUSION is ดำเนินการเหนืออุณหภูมิห้องแต่ต่ำกว่าจุดที่เกิดซ้ำ นำเสนอการประนีประนอมและความสมดุลสำหรับแรงที่ต้องการ ความเหนียว และคุณสมบัติของวัสดุ ดังนั้นจึงเป็นตัวเลือกสำหรับการใช้งานบางประเภท HOT EXTRUSION เกิดขึ้นเหนืออุณหภูมิการตกผลึกใหม่ของวัสดุ วิธีนี้จะง่ายกว่าในการดันวัสดุผ่านแม่พิมพ์ แต่ค่าอุปกรณ์ก็สูง ยิ่งโปรไฟล์การอัดขึ้นรูปที่ซับซ้อนมากขึ้นเท่าใด แม่พิมพ์ (เครื่องมือ) ก็จะยิ่งมีราคาสูงขึ้น และอัตราการผลิตก็จะยิ่งต่ำลงเท่านั้น ส่วนตัดขวางของแม่พิมพ์และความหนามีข้อจำกัดที่ขึ้นอยู่กับวัสดุที่จะรีด มุมที่แหลมคมในแม่พิมพ์อัดรีดเป็นสิ่งที่ไม่พึงปรารถนาเสมอและควรหลีกเลี่ยงเว้นแต่จำเป็น ตามวัสดุที่กำลังอัดรีด เราขอเสนอ: • METAL EXTRUSIONS : ผลิตภัณฑ์ส่วนใหญ่ที่เราผลิต ได้แก่ อลูมิเนียม ทองเหลือง สังกะสี ทองแดง เหล็ก ไททาเนียม แมกนีเซียม • PLASTIC EXTRUSION : พลาสติกหลอมเหลวและขึ้นรูปเป็นโปรไฟล์ต่อเนื่อง วัสดุทั่วไปของเราในการประมวลผล ได้แก่ โพลิเอทิลีน ไนลอน โพลีสไตรีน โพลิไวนิลคลอไรด์ โพลิโพรพิลีน พลาสติก ABS โพลีคาร์บอเนต อะคริลิค ผลิตภัณฑ์ทั่วไปที่เราผลิต ได้แก่ ท่อและท่อ โครงพลาสติก ในกระบวนการนี้ เม็ดพลาสติกขนาดเล็ก / เรซินจะถูกป้อนด้วยแรงโน้มถ่วงจากถังบรรจุลงในถังของเครื่องอัดรีด บ่อยครั้งที่เรายังผสมสารให้สีหรือสารเติมแต่งอื่น ๆ ลงในถังเพื่อให้ผลิตภัณฑ์มีคุณสมบัติและคุณสมบัติที่จำเป็น วัสดุที่เข้าสู่ถังอบความร้อนจะถูกบังคับโดยสกรูหมุนเพื่อออกจากถังที่ส่วนท้าย และเคลื่อนผ่านชุดตะแกรงเพื่อขจัดสิ่งปลอมปนในพลาสติกหลอมเหลว หลังจากผ่านแพ็คหน้าจอแล้ว พลาสติกจะเข้าสู่แม่พิมพ์อัดรีด ดายทำให้พลาสติกอ่อนเคลื่อนที่มีรูปร่างเป็นโปรไฟล์เมื่อผ่านเข้าไป ตอนนี้เครื่องอัดรีดจะผ่านอ่างน้ำเพื่อระบายความร้อน เทคนิคอื่นๆ AGS-TECH Inc. ใช้มาหลายปีแล้ว ได้แก่: • PIPE & TUBING EXTRUSION : ท่อและท่อพลาสติกจะเกิดขึ้นเมื่อพลาสติกถูกอัดขึ้นรูปด้วยแม่พิมพ์ทรงกลมและระบายความร้อนในอ่างน้ำ จากนั้นตัดให้ยาวหรือม้วนเป็นม้วน ผนังใสหรือสี ลายทาง ผนังเดี่ยวหรือคู่ ยืดหยุ่นหรือแข็ง PE, PP, โพลียูรีเทน, พีวีซี, ไนลอน, พีซี, ซิลิโคน, ไวนิล หรืออื่นๆ เรามีครบ เรามีสต็อคหลอดและความสามารถในการผลิตตามข้อกำหนดของคุณ AGS-TECH ผลิตท่อตามข้อกำหนดของ FDA, UL และ LE สำหรับการใช้งานทางการแพทย์ ไฟฟ้าและอิเล็กทรอนิกส์ อุตสาหกรรม และการใช้งานอื่นๆ • OVERJACKETING / OVER JACKETING EXTRUSION : เทคนิคนี้ใช้พลาสติกชั้นนอกกับลวดหรือสายเคเบิลที่มีอยู่ ลวดฉนวนของเราผลิตขึ้นด้วยวิธีนี้ • COEXTRUSION : วัสดุหลายชั้นถูกอัดรีดพร้อมกัน หลายชั้นถูกส่งโดยเครื่องอัดรีดหลายตัว ความหนาของชั้นต่างๆ สามารถปรับได้ตามข้อกำหนดของลูกค้า กระบวนการนี้ทำให้สามารถใช้โพลีเมอร์หลายตัวซึ่งแต่ละชนิดมีฟังก์ชันการทำงานที่แตกต่างกันในผลิตภัณฑ์ ด้วยเหตุนี้ เราจึงสามารถเพิ่มประสิทธิภาพช่วงของคุณสมบัติได้ • การอัดรีดแบบผสม: โพลีเมอร์เดี่ยวหรือหลายตัวผสมกับสารเติมแต่งเพื่อให้ได้สารประกอบพลาสติก เครื่องอัดรีดแบบสกรูคู่ของเราผลิตการอัดขึ้นรูปแบบผสม แม่พิมพ์อัดรีดโดยทั่วไปมีราคาไม่แพงเมื่อเทียบกับแม่พิมพ์โลหะ หากคุณจ่ายเงินมากกว่าสองสามพันเหรียญสำหรับอลูมิเนียมอัดรีดขนาดเล็กหรือขนาดกลาง คุณอาจจะจ่ายมากเกินไป เราเป็นผู้เชี่ยวชาญในการพิจารณาว่าเทคนิคใดคุ้มค่าที่สุด เร็วที่สุด และเหมาะสมที่สุดสำหรับการใช้งานของคุณ บางครั้งการอัดรีดและการตัดเฉือนชิ้นส่วนสามารถช่วยให้คุณประหยัดเงินได้มาก ก่อนตัดสินใจอย่างแน่วแน่ ถามความคิดเห็นของเราก่อน เราได้ช่วยลูกค้าจำนวนมากในการตัดสินใจที่ถูกต้อง สำหรับการอัดขึ้นรูปโลหะที่ใช้กันอย่างแพร่หลาย คุณสามารถดาวน์โหลดโบรชัวร์และแคตตาล็อกของเราโดยคลิกที่ข้อความสีด้านล่าง หากเป็นผลิตภัณฑ์นอกชั้นวางที่ตรงตามข้อกำหนดของคุณจะประหยัดกว่า ดาวน์โหลดความสามารถในการอัดรีดท่อและท่อทางการแพทย์ของเรา ดาวน์โหลดแผ่นระบายความร้อนของเรา • กระบวนการผลิตขั้นที่สองและกระบวนการผลิตสำหรับการอัดขึ้นรูป : ในกระบวนการสร้างมูลค่าเพิ่มที่เรานำเสนอสำหรับผลิตภัณฑ์อัดขึ้นรูป ได้แก่: - การดัดท่อและท่อแบบกำหนดเอง การขึ้นรูปและการขึ้นรูป การตัดท่อ การขึ้นรูปปลายท่อ การม้วนท่อ การตัดเฉือนและการตกแต่ง การเจาะและการเจาะและการเจาะ - การประกอบท่อและท่อแบบกำหนดเอง การประกอบท่อ การเชื่อม การประสานและการบัดกรี - รีดขึ้นรูป ขึ้นรูป และขึ้นรูปตามต้องการ - ทำความสะอาด ล้างไขมัน ดอง ทู่ ขัดเงา อโนไดซ์ ชุบ ทาสี อบร้อน หลอมและชุบแข็ง ทำเครื่องหมาย แกะสลัก และติดฉลาก บรรจุภัณฑ์แบบกำหนดเอง CLICK Product Finder-Locator Service หน้าก่อน
- Casting and Machined Parts, CNC Manufacturing, Milling, Turning, Swiss
Casting and Machined Parts, CNC Manufacturing, Milling, Turning, Swiss Type Machining, Die Casting, Investment Casting, Lost Foam Cast Parts from AGS-TECH Inc. การหล่อและการตัดเฉือน เทคนิคการหล่อและการตัดเฉือนแบบกำหนดเองของเรานั้นเป็นการหล่อแบบใช้แล้วทิ้งและแบบใช้ไม่ได้ การหล่อแบบเหล็กและนอกกลุ่มเหล็ก ทราย ดาย แรงเหวี่ยง แบบต่อเนื่อง แม่พิมพ์เซรามิก การลงทุน โฟมที่สูญหาย รูปร่างใกล้ตาข่าย แม่พิมพ์ถาวร (การหล่อแบบแรงโน้มถ่วง) ปูนปลาสเตอร์ แม่พิมพ์ (การหล่อปูนปลาสเตอร์) และการหล่อเปลือก ชิ้นส่วนกลึงที่ผลิตโดยการกัดและกลึงโดยใช้อุปกรณ์ทั่วไปและ CNC การตัดเฉือนแบบสวิสสำหรับชิ้นส่วนที่มีความแม่นยำสูงราคาไม่แพงสำหรับปริมาณงานสูง การกลึงเกลียวสำหรับตัวยึด การตัดเฉือนแบบไม่ธรรมดา โปรดทราบว่านอกจากโลหะและโลหะผสมแล้ว เรายังตัดเฉือนส่วนประกอบเซรามิก แก้ว และพลาสติกด้วย ในบางกรณีเมื่อการผลิตแม่พิมพ์ไม่น่าสนใจหรือไม่มีตัวเลือก การตัดเฉือนวัสดุพอลิเมอร์ต้องใช้ประสบการณ์เฉพาะทางที่เรามี เนื่องจากความท้าทายที่พลาสติกและยางมีอยู่เนื่องจากความนุ่มนวล ไม่แข็งกระด้าง...ฯลฯ สำหรับการตัดเฉือนเซรามิกและแก้ว โปรดดูที่การแปรรูปแบบไม่ธรรมดาของเรา AGS-TECH Inc. ผลิตและจำหน่ายทั้งการหล่อแบบน้ำหนักเบาและแบบหนัก เราได้จัดหาการหล่อโลหะและชิ้นส่วนเครื่องจักรสำหรับหม้อไอน้ำ เครื่องแลกเปลี่ยนความร้อน รถยนต์ ไมโครมอเตอร์ กังหันลม อุปกรณ์บรรจุภัณฑ์อาหาร และอื่นๆ เราขอแนะนำให้คุณคลิกที่นี่ to ดาวน์โหลดภาพประกอบแผนผังของกระบวนการตัดเฉือนและการหล่อโดย AGS-TECH Inc. วิธีนี้จะช่วยให้คุณเข้าใจข้อมูลที่เราให้ไว้ด้านล่างนี้ได้ดียิ่งขึ้น มาดูเทคนิคต่างๆ ที่เรานำเสนอโดยละเอียด: • การหล่อแบบใช้ครั้งเดียวได้ : หมวดหมู่กว้างๆ นี้หมายถึงวิธีการที่เกี่ยวข้องกับแม่พิมพ์ชั่วคราวและแบบใช้ซ้ำไม่ได้ ตัวอย่าง ได้แก่ ทราย ปูนปลาสเตอร์ เปลือกหอย การลงทุน (เรียกอีกอย่างว่าขี้ผึ้งหาย) และการหล่อปูนปลาสเตอร์ • การหล่อทราย : กระบวนการที่ใช้ทรายเป็นวัสดุทำแม่พิมพ์ วิธีการแบบเก่าและยังคงได้รับความนิยมจนถึงขนาดที่การหล่อโลหะส่วนใหญ่ผลิตขึ้นโดยใช้เทคนิคนี้ ต้นทุนต่ำแม้ในการผลิตในปริมาณน้อย เหมาะสำหรับการผลิตชิ้นส่วนขนาดเล็กและขนาดใหญ่ เทคนิคนี้สามารถใช้ในการผลิตชิ้นส่วนได้ภายในไม่กี่วันหรือหลายสัปดาห์ด้วยการลงทุนเพียงเล็กน้อย ทรายชื้นถูกเชื่อมเข้าด้วยกันโดยใช้ดินเหนียว สารยึดเกาะ หรือน้ำมันชนิดพิเศษ โดยทั่วไปทรายจะบรรจุในกล่องแม่พิมพ์ และระบบช่องและประตูถูกสร้างขึ้นโดยการบดอัดทรายรอบๆ โมเดล กระบวนการคือ: 1.) วางโมเดลในทรายเพื่อทำแม่พิมพ์ 2.) การรวมตัวของแบบจำลองและทรายในระบบประตู 3.) การนำโมเดลออก 4.) การเติมโพรงแม่พิมพ์ด้วยโลหะหลอมเหลว 5.) การหล่อเย็นของโลหะ 6.) ทำลายแม่พิมพ์ทรายและถอดการหล่อ • การหล่อด้วยปูนปลาสเตอร์ : คล้ายกับการหล่อทราย แทนที่จะใช้ทราย ใช้ปูนของปารีสเป็นวัสดุทำแม่พิมพ์ ระยะเวลาในการผลิตสั้นเช่นการหล่อทรายและราคาไม่แพง ความคลาดเคลื่อนของมิติที่ดีและผิวสำเร็จ ข้อเสียที่สำคัญคือสามารถใช้ได้เฉพาะกับโลหะที่มีจุดหลอมเหลวต่ำ เช่น อะลูมิเนียมและสังกะสีเท่านั้น • SHELL MOLD CASTING : คล้ายกับการหล่อทราย โพรงแม่พิมพ์ที่ได้จากเปลือกแข็งของทรายและสารยึดเกาะเรซินเทอร์โมเซตติง แทนขวดที่เติมทรายด้วยกระบวนการหล่อทราย โลหะเกือบทุกชนิดที่เหมาะสมในการหล่อด้วยทรายสามารถหล่อได้ด้วยการขึ้นรูปเปลือก กระบวนการสามารถสรุปได้ดังนี้: 1.) การผลิตแม่พิมพ์เปลือก ทรายที่ใช้จะมีขนาดเม็ดเล็กกว่ามากเมื่อเทียบกับทรายที่ใช้ในการหล่อทราย ทรายละเอียดผสมกับเรซินเทอร์โมเซตติง ลวดลายโลหะเคลือบด้วยสารแยกส่วนเพื่อให้ถอดเปลือกออกได้ง่ายขึ้น หลังจากนั้นรูปแบบโลหะจะถูกทำให้ร้อนและส่วนผสมของทรายจะถูกรูพรุนหรือเป่าลงบนรูปแบบการหล่อแบบร้อน เปลือกบางก่อตัวขึ้นบนพื้นผิวของลวดลาย ความหนาของเปลือกนี้สามารถปรับได้โดยการเปลี่ยนระยะเวลาที่ส่วนผสมทรายเรซินสัมผัสกับลวดลายโลหะ ทรายที่หลวมจะถูกลบออกโดยเหลือลวดลายที่หุ้มเปลือกไว้ 2.) ถัดไป เปลือกและลวดลายถูกทำให้ร้อนในเตาอบเพื่อให้เปลือกแข็ง หลังจากการชุบแข็งเสร็จสิ้น เปลือกจะถูกขับออกจากลวดลายโดยใช้หมุดที่ติดอยู่กับลวดลาย 3.) เปลือกสองชิ้นดังกล่าวถูกประกอบเข้าด้วยกันโดยการติดกาวหรือหนีบและทำเป็นแม่พิมพ์ที่สมบูรณ์ ตอนนี้ แม่พิมพ์เปลือกถูกใส่ลงในภาชนะที่มีทรายหรือโลหะรองรับในระหว่างกระบวนการหล่อ 4.) ตอนนี้โลหะร้อนสามารถเทลงในแม่พิมพ์เปลือก ข้อดีของการหล่อเปลือกคือผลิตภัณฑ์ที่มีผิวสำเร็จที่ดีมาก ความเป็นไปได้ในการผลิตชิ้นส่วนที่ซับซ้อนด้วยความแม่นยำของมิติสูง กระบวนการอัตโนมัติที่ง่าย ประหยัดสำหรับการผลิตในปริมาณมาก ข้อเสียคือแม่พิมพ์ต้องการการระบายอากาศที่ดี เนื่องจากก๊าซที่สร้างขึ้นเมื่อโลหะหลอมเหลวสัมผัสกับสารเคมียึดเกาะ เรซินเทอร์โมเซตติงและลวดลายโลหะมีราคาแพง เนื่องจากต้นทุนของลวดลายโลหะ เทคนิคนี้อาจไม่เหมาะกับการผลิตที่มีปริมาณน้อย • การหล่อเพื่อการลงทุน (หรือที่รู้จักในชื่อ LOST-WAX CASTING): เป็นเทคนิคที่เก่าแก่และเหมาะสำหรับการผลิตชิ้นส่วนที่มีคุณภาพด้วยความแม่นยำสูง การทำซ้ำ ความคล่องตัวและความสมบูรณ์จากโลหะหลายชนิด วัสดุทนไฟ และโลหะผสมประสิทธิภาพสูงพิเศษ สามารถผลิตชิ้นส่วนขนาดเล็กและขนาดใหญ่ได้ กระบวนการที่มีราคาแพงเมื่อเทียบกับวิธีการอื่นๆ แต่ข้อดีที่สำคัญคือ ความเป็นไปได้ในการผลิตชิ้นส่วนที่มีรูปร่างใกล้เคียงกับตาข่าย รูปทรงที่ซับซ้อน และรายละเอียด ดังนั้นค่าใช้จ่ายจึงถูกชดเชยด้วยการตัดการทำงานซ้ำและการตัดเฉือนออกในบางกรณี แม้ว่าจะมีการเปลี่ยนแปลงได้ แต่นี่เป็นบทสรุปของกระบวนการหล่อการลงทุนทั่วไป: 1.) การสร้างต้นแบบต้นแบบจากขี้ผึ้งหรือพลาสติก การหล่อแต่ละครั้งต้องการรูปแบบเดียวเนื่องจากสิ่งเหล่านี้จะถูกทำลายในกระบวนการ แม่พิมพ์ที่ใช้ผลิตลวดลายก็จำเป็นเช่นกัน และโดยส่วนใหญ่แล้วแม่พิมพ์จะถูกหล่อหรือกลึง เนื่องจากไม่จำเป็นต้องเปิดแม่พิมพ์ การหล่อที่ซับซ้อนสามารถทำได้ ลวดลายขี้ผึ้งจำนวนมากสามารถเชื่อมต่อได้เหมือนกิ่งก้านของต้นไม้และเทเข้าด้วยกัน ซึ่งช่วยให้สามารถผลิตชิ้นส่วนได้หลายส่วนจากการเทโลหะหรือโลหะผสมเพียงครั้งเดียว 2.) ถัดไป รูปแบบจะถูกจุ่มหรือเทลงในสารละลายทนไฟซึ่งประกอบด้วยซิลิกาเนื้อละเอียดมาก น้ำ สารยึดเกาะ ส่งผลให้เกิดชั้นเซรามิกบนพื้นผิวของลวดลาย เคลือบวัสดุทนไฟบนลวดลายทิ้งไว้ให้แห้งและแข็งตัว ขั้นตอนนี้เป็นที่มาของการหล่อเพื่อการลงทุนชื่อ: ใช้สารละลายทนไฟบนรูปแบบขี้ผึ้ง 3.) ในขั้นตอนนี้ แม่พิมพ์เซรามิกชุบแข็งจะพลิกคว่ำและให้ความร้อนเพื่อให้ขี้ผึ้งละลายและเทออกจากแม่พิมพ์ โพรงถูกทิ้งไว้เบื้องหลังสำหรับการหล่อโลหะ 4.) หลังจากที่ขี้ผึ้งหมด แม่พิมพ์เซรามิกจะถูกทำให้ร้อนที่อุณหภูมิสูงขึ้นไปอีกซึ่งส่งผลให้แม่พิมพ์แข็งแรงขึ้น 5.) การหล่อโลหะถูกเทลงในแม่พิมพ์ร้อนเพื่อเติมส่วนที่ซับซ้อนทั้งหมด 6.) การหล่อได้รับอนุญาตให้แข็งตัว 7.) ในที่สุดแม่พิมพ์เซรามิกก็แตกและชิ้นส่วนที่ผลิตขึ้นก็ถูกตัดออกจากต้นไม้ นี่คือลิงค์ไปยังโบรชัวร์โรงหล่อการลงทุน • EVAPORATIVE PATTERN CASTING : กระบวนการใช้ลวดลายที่ทำจากวัสดุ เช่น โฟมโพลีสไตรีน ซึ่งจะระเหยเมื่อเทโลหะหลอมร้อนเทลงในแม่พิมพ์ กระบวนการนี้มีสองประเภท: LOST FOAM CASTING ซึ่งใช้ทรายที่ไม่ผูกมัด และ FULL MOLD CASTING ซึ่งใช้ทรายเชื่อมประสาน นี่คือขั้นตอนกระบวนการทั่วไป: 1.) ผลิตลวดลายจากวัสดุ เช่น พอลิสไตรีน เมื่อจะผลิตในปริมาณมาก ลวดลายจะถูกขึ้นรูป หากชิ้นส่วนมีรูปร่างซับซ้อน อาจต้องยึดหลายส่วนของวัสดุโฟมดังกล่าวเข้าด้วยกันเพื่อสร้างลวดลาย เรามักจะเคลือบลวดลายด้วยสารประกอบทนไฟเพื่อสร้างพื้นผิวที่ดีในการหล่อ 2.) จากนั้นนำลวดลายไปใส่ในแม่พิมพ์ทราย 3.) โลหะหลอมเหลวจะถูกเทลงในแม่พิมพ์ ทำให้รูปแบบโฟมระเหย เช่น โพลีสไตรีน ในกรณีส่วนใหญ่เมื่อไหลผ่านโพรงแม่พิมพ์ 4.) โลหะที่หลอมละลายจะถูกทิ้งไว้ในแม่พิมพ์ทรายเพื่อให้แข็งตัว 5.) หลังจากชุบแข็งแล้ว เราก็เอาการหล่อออก ในบางกรณี ผลิตภัณฑ์ที่เราผลิตต้องมีแกนกลางในลวดลาย ในการหล่อแบบระเหย ไม่จำเป็นต้องวางและยึดแกนไว้ในโพรงแม่พิมพ์ เทคนิคนี้เหมาะสำหรับการผลิตหน้าลายที่ซับซ้อนมาก สามารถทำแบบอัตโนมัติได้อย่างง่ายดายสำหรับการผลิตที่มีปริมาณมาก และไม่มีสายการกลึงตัดในส่วนที่หล่อ กระบวนการพื้นฐานนั้นง่ายและประหยัดในการนำไปใช้ สำหรับการผลิตในปริมาณมาก เนื่องจากจำเป็นต้องใช้แม่พิมพ์หรือแม่พิมพ์ในการผลิตลวดลายจากพอลิสไตรีน ซึ่งอาจมีค่าใช้จ่ายค่อนข้างสูง • การหล่อแบบไม่สามารถขยายได้ : หมวดหมู่กว้างๆ นี้หมายถึงวิธีการที่ไม่จำเป็นต้องปฏิรูปแม่พิมพ์หลังจากแต่ละรอบการผลิต ตัวอย่าง ได้แก่ การหล่อแบบถาวร การหล่อแบบต่อเนื่อง และการหล่อแบบแรงเหวี่ยง ได้รับความสามารถในการทำซ้ำและชิ้นส่วนต่างๆ สามารถกำหนดลักษณะเป็น NEAR NET SHAPE • การหล่อแบบถาวร : แม่พิมพ์ที่ใช้ซ้ำได้ที่ทำจากโลหะใช้สำหรับการหล่อหลายแบบ โดยทั่วไปแล้วแม่พิมพ์ถาวรสามารถใช้ได้หลายหมื่นครั้งก่อนที่มันจะเสื่อมสภาพ โดยทั่วไปจะใช้แรงโน้มถ่วง แรงดันแก๊ส หรือสุญญากาศเพื่อเติมแม่พิมพ์ แม่พิมพ์ (เรียกอีกอย่างว่าแม่พิมพ์) โดยทั่วไปทำจากเหล็ก เหล็ก เซรามิก หรือโลหะอื่นๆ กระบวนการทั่วไปคือ: 1.) เครื่องจักรและสร้างแม่พิมพ์ เป็นเรื่องปกติที่จะตัดเฉือนแม่พิมพ์จากบล็อกโลหะสองอันที่ประกอบเข้าด้วยกันและสามารถเปิดและปิดได้ โดยทั่วไปแล้วทั้งคุณลักษณะของชิ้นส่วนและระบบเกตติ้งจะถูกตัดเฉือนในแม่พิมพ์หล่อ 2.) พื้นผิวแม่พิมพ์ภายในเคลือบด้วยวัสดุทนไฟที่ผสมสารละลาย ซึ่งช่วยควบคุมการไหลของความร้อนและทำหน้าที่เป็นสารหล่อลื่นเพื่อให้ถอดชิ้นส่วนหล่อได้ง่าย 3.) ถัดไป ครึ่งแม่พิมพ์ถาวรปิดและแม่พิมพ์ถูกให้ความร้อน 4.) เทโลหะหลอมเหลวลงในแม่พิมพ์และปล่อยให้นิ่งเพื่อแข็งตัว 5.) ก่อนที่จะเย็นลงมาก เราจะนำชิ้นส่วนออกจากแม่พิมพ์ถาวรโดยใช้ตัวถอดเมื่อเปิดครึ่งแม่พิมพ์ เราใช้การหล่อแบบถาวรสำหรับโลหะที่มีจุดหลอมเหลวต่ำ เช่น สังกะสีและอลูมิเนียม สำหรับการหล่อเหล็ก เราใช้กราไฟท์เป็นวัสดุทำแม่พิมพ์ บางครั้งเราได้รูปทรงที่ซับซ้อนโดยใช้แกนภายในแม่พิมพ์ถาวร ข้อดีของเทคนิคนี้คือ การหล่อที่มีสมบัติเชิงกลที่ดีที่ได้จากการหล่อเย็นอย่างรวดเร็ว ความสม่ำเสมอในคุณสมบัติ ความแม่นยำและผิวสำเร็จที่ดี อัตราการคัดแยกต่ำ ความเป็นไปได้ของการทำให้กระบวนการเป็นอัตโนมัติ และการผลิตปริมาณมากในเชิงเศรษฐกิจ ข้อเสียคือต้นทุนการตั้งค่าเริ่มต้นที่สูง ซึ่งทำให้ไม่เหมาะสำหรับการใช้งานที่มีปริมาณน้อย และข้อจำกัดเกี่ยวกับขนาดของชิ้นส่วนที่ผลิต • DIE CASTING : แม่พิมพ์ถูกกลึงและโลหะหลอมเหลวถูกผลักภายใต้แรงดันสูงเข้าไปในโพรงแม่พิมพ์ สามารถหล่อได้ทั้งโลหะนอกกลุ่มเหล็กและโลหะเหล็ก กระบวนการนี้เหมาะสำหรับการผลิตปริมาณมากของชิ้นส่วนขนาดเล็กถึงขนาดกลางที่มีรายละเอียด ผนังบางมาก มีมิติสม่ำเสมอ และผิวสำเร็จที่ดี AGS-TECH Inc. สามารถผลิตความหนาของผนังได้เพียง 0.5 มม. โดยใช้เทคนิคนี้ เช่นเดียวกับการหล่อแบบถาวร แม่พิมพ์ต้องประกอบด้วยสองส่วนที่สามารถเปิดและปิดเพื่อกำจัดชิ้นส่วนที่ผลิตได้ แม่พิมพ์หล่อขึ้นรูปอาจมีหลายช่องเพื่อให้สามารถผลิตได้หลายแบบในแต่ละรอบ แม่พิมพ์หล่อขึ้นรูปมีน้ำหนักมากและมีขนาดใหญ่กว่าชิ้นส่วนที่ผลิตมาก ดังนั้นจึงมีราคาแพง เราซ่อมและเปลี่ยนแม่พิมพ์ที่สึกหรอฟรีสำหรับลูกค้าของเรา ตราบใดที่พวกเขาสั่งชิ้นส่วนจากเราใหม่ แม่พิมพ์ของเรามีอายุการใช้งานยาวนานในช่วงหลายแสนรอบ ขั้นตอนกระบวนการง่ายๆ พื้นฐานมีดังนี้ 1.) การผลิตแม่พิมพ์โดยทั่วไปจากเหล็กกล้า 2.) แม่พิมพ์ติดตั้งบนเครื่องหล่อขึ้นรูป 3.) ลูกสูบบังคับให้โลหะหลอมเหลวไหลในโพรงแม่พิมพ์เพื่อเติมเต็มคุณสมบัติที่ซับซ้อนและผนังบาง 4.) หลังจากเติมแม่พิมพ์ด้วยโลหะหลอมเหลวแล้ว การหล่อจะปล่อยให้แข็งตัวภายใต้แรงกด 5.) เปิดแม่พิมพ์และถอดหล่อออกโดยใช้หมุดอีเจ็คเตอร์ 6.) ตอนนี้แม่พิมพ์เปล่าได้รับการหล่อลื่นอีกครั้งและถูกยึดสำหรับรอบถัดไป ในการหล่อแบบหล่อ เรามักใช้การขึ้นรูปแบบเม็ดมีดโดยที่เรารวมชิ้นส่วนเพิ่มเติมเข้ากับแม่พิมพ์และหล่อโลหะรอบๆ หลังจากการแข็งตัว ชิ้นส่วนเหล่านี้จะกลายเป็นส่วนหนึ่งของผลิตภัณฑ์หล่อ ข้อดีของการหล่อแบบหล่อคือคุณสมบัติทางกลที่ดีของชิ้นส่วน ความเป็นไปได้ของคุณสมบัติที่ซับซ้อน รายละเอียดที่ละเอียดอ่อน และผิวสำเร็จที่ดี อัตราการผลิตสูง ระบบอัตโนมัติที่ง่ายดาย ข้อเสีย: ไม่เหมาะสำหรับงานปริมาณน้อยเนื่องจากแม่พิมพ์และต้นทุนอุปกรณ์สูง ข้อจำกัดของรูปทรงที่สามารถหล่อได้ รอยกลมเล็กๆ บนชิ้นส่วนหล่อที่เกิดจากการสัมผัสของหมุดอีเจ็คเตอร์ แฟลชบาง ๆ ของโลหะที่บีบออกที่เส้นแยก ต้องการ สำหรับช่องระบายอากาศตามเส้นแบ่งระหว่างแม่พิมพ์ จำเป็นต้องรักษาอุณหภูมิของแม่พิมพ์ให้ต่ำโดยใช้การหมุนเวียนของน้ำ • CENTRIFUGAL CASTING : โลหะหลอมเหลวจะถูกเทลงในศูนย์กลางของแม่พิมพ์ที่หมุนอยู่ที่แกนของการหมุน แรงเหวี่ยงเหวี่ยงเหวี่ยงโลหะไปทางขอบและปล่อยให้แข็งตัวในขณะที่แม่พิมพ์ยังคงหมุนอยู่ หมุนได้ทั้งแนวนอนและแนวตั้ง สามารถหล่อชิ้นส่วนที่มีพื้นผิวด้านในเป็นทรงกลมและรูปทรงอื่นๆ ที่ไม่ใช่ทรงกลมได้ กระบวนการสามารถสรุปได้ดังนี้: 1.) เทโลหะหลอมเหลวลงในแม่พิมพ์แบบแรงเหวี่ยง จากนั้นโลหะจะถูกผลักไปที่ผนังด้านนอกเนื่องจากการปั่นของแม่พิมพ์ 2.) เมื่อแม่พิมพ์หมุน การหล่อโลหะจะแข็งตัว การหล่อแบบแรงเหวี่ยงเป็นเทคนิคที่เหมาะสมสำหรับการผลิตชิ้นส่วนทรงกระบอกกลวง เช่น ท่อ ไม่จำเป็นต้องใช้สปรู๊ ตัวยกและตัวปิด ผิวสำเร็จที่ดีและคุณสมบัติที่มีรายละเอียด ไม่มีปัญหาเรื่องการหดตัว ความเป็นไปได้ในการผลิตท่อยาวที่มีเส้นผ่านศูนย์กลางขนาดใหญ่มาก ความสามารถในการผลิตที่มีอัตราสูง . • CONTINUOUS Casting ( STRAND CASTING ) : ใช้ในการหล่อโลหะที่มีความยาวต่อเนื่อง โดยทั่วไป โลหะหลอมเหลวจะถูกหล่อเป็นโปรไฟล์สองมิติของแม่พิมพ์ แต่ความยาวไม่แน่นอน โลหะหลอมเหลวใหม่จะถูกป้อนเข้าสู่แม่พิมพ์อย่างต่อเนื่องในขณะที่การหล่อเคลื่อนที่ลงตามความยาวที่เพิ่มขึ้นตามเวลา โลหะ เช่น ทองแดง เหล็ก อลูมิเนียม หล่อเป็นเส้นยาวโดยใช้กระบวนการหล่อแบบต่อเนื่อง กระบวนการอาจมีการกำหนดค่าต่าง ๆ แต่กระบวนการทั่วไปสามารถทำให้ง่ายขึ้นได้ดังนี้: 1.) โลหะหลอมเหลวจะถูกเทลงในภาชนะที่อยู่สูงเหนือแม่พิมพ์ด้วยปริมาณที่คำนวณไว้อย่างดีและอัตราการไหล และไหลผ่านแม่พิมพ์ที่ระบายความร้อนด้วยน้ำ การหล่อโลหะที่เทลงในแม่พิมพ์จะแข็งตัวเป็นแท่งสตาร์ทที่ด้านล่างของแม่พิมพ์ แถบสตาร์ทนี้ช่วยให้ลูกกลิ้งสามารถหยิบจับได้ในตอนแรก 2. ) เกลียวโลหะยาวถูกลำเลียงด้วยลูกกลิ้งด้วยความเร็วคงที่ ลูกกลิ้งยังเปลี่ยนทิศทางการไหลของเกลียวโลหะจากแนวตั้งเป็นแนวนอน 3.) หลังจากการหล่อแบบต่อเนื่องได้เดินทางในระยะทางแนวนอนที่กำหนด คบเพลิงหรือเลื่อยที่เคลื่อนที่ไปพร้อมกับการหล่อจะตัดให้มีความยาวที่ต้องการอย่างรวดเร็ว กระบวนการหล่อแบบต่อเนื่องสามารถรวมเข้ากับ ROLLING PROCESS ซึ่งโลหะหล่ออย่างต่อเนื่องสามารถป้อนเข้าในโรงรีดโดยตรงเพื่อผลิต I-Beams, T-Beams…. เป็นต้น การหล่อแบบต่อเนื่องทำให้เกิดคุณสมบัติที่สม่ำเสมอตลอดทั้งผลิตภัณฑ์ มีอัตราการแข็งตัวสูง ลดต้นทุนเนื่องจากการสูญเสียวัสดุต่ำมาก นำเสนอกระบวนการที่การบรรจุโลหะ การเท การแข็งตัว การตัดและการกำจัดการหล่อจะดำเนินการอย่างต่อเนื่องและ จึงทำให้ได้ผลผลิตสูงและคุณภาพสูง การพิจารณาที่สำคัญคืออย่างไรก็ตามการลงทุนเริ่มต้นสูง ค่าใช้จ่ายในการติดตั้ง และความต้องการพื้นที่ • บริการเครื่องจักร : เรามีเครื่องจักรสาม สี่ และห้าแกน ประเภทของกระบวนการตัดเฉือนที่เราใช้ ได้แก่ กลึง กัด เจาะ คว้าน เจาะ ไส เลื่อย เจียร ขัด ขัด และเครื่องจักรที่ไม่ใช่แบบดั้งเดิม ซึ่งมีรายละเอียดเพิ่มเติมในเมนูอื่นๆ ของเว็บไซต์ของเรา สำหรับการผลิตส่วนใหญ่ของเรา เราใช้เครื่อง CNC อย่างไรก็ตาม สำหรับการดำเนินการบางอย่าง เทคนิคทั่วไปนั้นเหมาะสมกว่า ดังนั้นเราจึงพึ่งพาพวกเขาเช่นกัน ความสามารถในการตัดเฉือนของเราถึงระดับสูงสุดเท่าที่จะเป็นไปได้ และชิ้นส่วนที่มีความต้องการสูงที่สุดบางส่วนผลิตขึ้นในโรงงานที่ได้รับการรับรอง AS9100 ใบพัดเครื่องยนต์เจ็ทต้องการประสบการณ์การผลิตที่เชี่ยวชาญเป็นพิเศษและอุปกรณ์ที่เหมาะสม อุตสาหกรรมการบินและอวกาศมีมาตรฐานที่เข้มงวดมาก ส่วนประกอบบางอย่างที่มีโครงสร้างทางเรขาคณิตที่ซับซ้อนสามารถผลิตได้ง่ายที่สุดโดยการตัดเฉือนแบบห้าแกน ซึ่งพบได้เฉพาะในโรงงานตัดเฉือนบางแห่งรวมถึงโรงงานของเราด้วย โรงงานที่ผ่านการรับรองด้านการบินและอวกาศของเรามีประสบการณ์ที่จำเป็นในการปฏิบัติตามข้อกำหนดด้านเอกสารที่ครอบคลุมของอุตสาหกรรมการบินและอวกาศ ในการกลึง ชิ้นงานจะถูกหมุนและเคลื่อนเข้าหาเครื่องมือตัด สำหรับกระบวนการนี้จะใช้เครื่องที่เรียกว่าเครื่องกลึง ในงาน MILLING เครื่องที่เรียกว่าเครื่องกัดมีเครื่องมือหมุนเพื่อให้คมตัดรับกับชิ้นงาน การขุดเจาะเกี่ยวข้องกับหัวกัดแบบหมุนที่มีคมตัดซึ่งทำให้เกิดรูเมื่อสัมผัสกับชิ้นงาน โดยทั่วไปจะใช้เครื่องเจาะ เครื่องกลึง หรือเครื่องกัด ในการทำงาน BORING เครื่องมือที่มีปลายแหลมงอเดียวจะถูกย้ายเข้าไปในรูหยาบในชิ้นงานที่หมุนเพื่อขยายรูเล็กน้อยและปรับปรุงความแม่นยำ ใช้สำหรับการตกแต่งชั้นดี BROACHING เป็นเครื่องมือที่มีฟันเพื่อขจัดวัสดุออกจากชิ้นงานในการเจาะครั้งเดียว (เครื่องมือที่มีฟัน) ในการโบรชัวร์แบบเส้นตรง โบรชัวร์จะทำงานเป็นเส้นตรงกับพื้นผิวของชิ้นงานเพื่อให้เกิดผลกระทบต่อการตัด ในขณะที่การเจาะแบบโรตารี่ โบรชัวร์จะหมุนและกดเข้าไปในชิ้นงานเพื่อตัดให้ได้รูปทรงสมมาตรของแกน SWISS TYPE MACHINING เป็นหนึ่งในเทคนิคที่มีค่าของเราที่เราใช้สำหรับการผลิตชิ้นส่วนขนาดเล็กที่มีความแม่นยำสูงในปริมาณมาก การใช้เครื่องกลึงแบบสวิสจะทำให้ชิ้นส่วนที่มีขนาดเล็ก ซับซ้อน และมีความเที่ยงตรงในราคาไม่แพง ต่างจากเครื่องกลึงทั่วไปที่ยึดชิ้นงานไว้กับที่และการเคลื่อนย้ายเครื่องมือ ในเครื่องกลึงแบบสวิส ชิ้นงานสามารถเคลื่อนที่ได้ในแกน Z และเครื่องมือจะอยู่กับที่ ในการตัดเฉือนแบบสวิส สต็อคแท่งจะอยู่ในเครื่องจักรและเคลื่อนผ่านปลอกไกด์ในแกน z โดยเปิดเผยเฉพาะส่วนที่จะตัดเฉือนเท่านั้น วิธีนี้ช่วยให้จับกระชับมือและมีความแม่นยำสูงมาก ความพร้อมของเครื่องมือที่ใช้อยู่ทำให้มีโอกาสกัดและเจาะเมื่อวัสดุเคลื่อนตัวจากบูชไกด์ แกน Y ของอุปกรณ์ประเภทสวิสให้ความสามารถในการกัดแบบเต็มรูปแบบและช่วยประหยัดเวลาในการผลิตได้มาก นอกจากนี้ เครื่องจักรของเรายังมีดอกสว่านและเครื่องมือคว้านที่ทำงานบนชิ้นส่วนเมื่อยึดไว้ในสปินเดิลย่อย ความสามารถในการตัดเฉือนแบบ Swiss-Type ทำให้เรามีโอกาสตัดเฉือนแบบอัตโนมัติอย่างสมบูรณ์ในการทำงานเพียงครั้งเดียว Machining เป็นหนึ่งในกลุ่มธุรกิจ AGS-TECH Inc. ที่ใหญ่ที่สุด เราใช้มันเป็นการดำเนินการหลักหรือการดำเนินการรองหลังจากการหล่อหรือการอัดขึ้นรูปชิ้นส่วนเพื่อให้เป็นไปตามข้อกำหนดการวาดภาพทั้งหมด • บริการตกแต่งพื้นผิว : เรานำเสนอการรักษาพื้นผิวและการตกแต่งพื้นผิวที่หลากหลาย เช่น การปรับสภาพพื้นผิวเพื่อเพิ่มการยึดเกาะ การฝากชั้นออกไซด์บางๆ เพื่อเพิ่มการยึดเกาะของสารเคลือบ การพ่นทราย เคมีฟิล์ม อโนไดซ์ ไนไตรดิ้ง เคลือบผง พ่นเคลือบ เทคนิคการเคลือบและการเคลือบโลหะขั้นสูงต่างๆ รวมถึงการสปัตเตอร์ ลำแสงอิเล็กตรอน การระเหย การชุบ การเคลือบแข็ง เช่น การเคลือบเพชรอย่างคาร์บอน (DLC) หรือการเคลือบไททาเนียมสำหรับเครื่องมือเจาะและตัด • บริการทำเครื่องหมายและติดฉลากผลิตภัณฑ์ : ลูกค้าจำนวนมากของเราต้องการการทำเครื่องหมายและการติดฉลาก การมาร์กด้วยเลเซอร์ การแกะสลักบนชิ้นส่วนโลหะ หากคุณมีความต้องการดังกล่าว ให้เราคุยกันว่าตัวเลือกใดดีที่สุดสำหรับคุณ ต่อไปนี้เป็นผลิตภัณฑ์หล่อโลหะที่ใช้กันทั่วไป เนื่องจากสิ่งเหล่านี้เป็นสินค้าที่ไม่มีวางจำหน่าย คุณจึงสามารถประหยัดต้นทุนแม่พิมพ์ได้ในกรณีที่สิ่งเหล่านี้ตรงกับความต้องการของคุณ: คลิกที่นี่เพื่อดาวน์โหลดกล่องอะลูมิเนียมหล่อขึ้นรูป 11 ซีรี่ส์ของเราจาก AGS-Electronics CLICK Product Finder-Locator Service หน้าก่อน
- Custom Manufactured Parts, Assemblies, Plastic Mold, Casting,Machining
Custom Manufactured Parts, Assemblies, Plastic Mold, Rubber Molding, Metal Casting, CNC Machining, Turning, Milling, Electrical Electronic Optical Assembly PCBA ชิ้นส่วนและส่วนประกอบที่ผลิตเอง & ผลิตภัณฑ์ อ่านเพิ่มเติม แม่พิมพ์และแม่พิมพ์พลาสติกและยาง อ่านเพิ่มเติม การหล่อและการตัดเฉือน อ่านเพิ่มเติม การอัดขึ้นรูป ผลิตภัณฑ์อัดรีด อ่านเพิ่มเติม ปั๊มขึ้นรูปและโลหะแผ่น อ่านเพิ่มเติม การตีขึ้นรูปโลหะและผงโลหะผสม อ่านเพิ่มเติม การขึ้นรูปลวดและสปริง อ่านเพิ่มเติม การขึ้นรูปและการขึ้นรูปแก้วและเซรามิก อ่านเพิ่มเติม การผลิตสารเติมแต่งและรวดเร็ว อ่านเพิ่มเติม การผลิตคอมโพสิตและวัสดุคอมโพสิต อ่านเพิ่มเติม เข้าร่วม & ประกอบ & ยึดกระบวนการ เราผลิตชิ้นส่วนและส่วนประกอบสำหรับคุณและนำเสนอกระบวนการผลิตดังต่อไปนี้: • แม่พิมพ์พลาสติกและยาง และชิ้นส่วนแม่พิมพ์ การฉีดขึ้นรูป การขึ้นรูปด้วยความร้อน การขึ้นรูปแบบเทอร์โมเซต การขึ้นรูปสูญญากาศ การเป่าขึ้นรูป การขึ้นรูปแบบหมุน การขึ้นรูปแบบเท การขึ้นรูปแบบเม็ดมีด และอื่นๆ • การอัดขึ้นรูปพลาสติก ยาง และโลหะ • การหล่อแบบเหล็กและนอกกลุ่มเหล็กและชิ้นส่วนกลึงที่ผลิตขึ้นโดยเทคนิคการกัดและการกลึง การตัดเฉือนแบบสวิส • ชิ้นส่วนโลหะผง • งานปั๊มโลหะและอโลหะ การขึ้นรูปโลหะแผ่น การประกอบแผ่นโลหะเชื่อม • การตีขึ้นรูปเย็นและร้อน • สายไฟ, ลวดเชื่อม, การขึ้นรูปลวด • สปริงประเภทต่างๆ สปริงขึ้นรูป • การผลิตเกียร์, กระปุกเกียร์, คัปปลิ้ง, ตัวหนอน, ตัวลดความเร็ว, กระบอกสูบ, สายพานส่งกำลัง, โซ่ส่งกำลัง, ส่วนประกอบเกียร์ • กระจกเทมเปอร์และกันกระสุนแบบกำหนดเองได้ตามมาตรฐาน NATO และการทหาร • ลูกปืน ลูกปืน ลูกรอก และลูกรอก • วาล์วและส่วนประกอบนิวเมติก เช่น โอริง แหวนรอง และซีล • ชิ้นส่วนและการประกอบแก้วและเซรามิก ส่วนประกอบป้องกันสุญญากาศและสุญญากาศ การเชื่อมโลหะ-เซรามิก และเซรามิก-เซรามิก • ประเภทต่างๆ ของส่วนประกอบทางกล • โลหะ-ยาง พันธะโลหะ-พลาสติก • ท่อและท่อ การขึ้นรูปท่อ การดัดและการประกอบท่อแบบกำหนดเอง การผลิตร้อง • การผลิตไฟเบอร์กลาส • การเชื่อมโดยใช้เทคนิคต่างๆ เช่น การเชื่อมแบบจุด, การเชื่อมด้วยเลเซอร์, MIG, TIG การเชื่อมด้วยอัลตราโซนิกสำหรับชิ้นส่วนพลาสติก • การทรีทเมนต์พื้นผิวและการตกแต่งพื้นผิวที่หลากหลาย เช่น การปรับสภาพพื้นผิวเพื่อเพิ่มการยึดเกาะ การฝากชั้นออกไซด์บางๆ เพื่อเพิ่มการยึดเกาะของสารเคลือบ การพ่นทราย เคมีฟิล์ม อโนไดซ์ ไนไตรดิ้ง การเคลือบผง การเคลือบแบบพ่นฝอย เทคนิคการเคลือบและการเคลือบขั้นสูงต่างๆ รวมทั้งสปัตเตอร์, ลำแสงอิเล็กตรอน, การระเหย, การชุบ, การเคลือบแข็งเช่นเพชรเช่นคาร์บอน (DLC) หรือไททาเนียมสำหรับเครื่องมือตัดและเจาะ • การทำเครื่องหมายและการติดฉลาก การมาร์กด้วยเลเซอร์บนชิ้นส่วนโลหะ การพิมพ์บนชิ้นส่วนพลาสติกและยาง ดาวน์โหลดโบรชัวร์สำหรับข้อกำหนดทั่วไปทางวิศวกรรมเครื่องกลที่ใช้โดยนักออกแบบและวิศวกร เราสร้างผลิตภัณฑ์ตามข้อกำหนดและข้อกำหนดเฉพาะของคุณ เพื่อนำเสนอคุณภาพ การจัดส่ง และราคาที่ดีที่สุดแก่คุณ เราผลิตผลิตภัณฑ์ทั่วโลกในประเทศจีน อินเดีย ไต้หวัน ฟิลิปปินส์ เกาหลีใต้ มาเลเซีย ศรีลังกา ตุรกี สหรัฐอเมริกา แคนาดา เยอรมนี สหราชอาณาจักร และญี่ปุ่น สิ่งนี้ทำให้เราแข็งแกร่งขึ้นมากและมีความสามารถในการแข่งขันระดับโลกมากกว่า custom manufacturer ผลิตภัณฑ์ของเราผลิตขึ้นในสภาพแวดล้อมที่ผ่านการรับรอง ISO9001:2000, QS9000, ISO14001, TS16949 และมีเครื่องหมาย CE, UL และตรงตามมาตรฐานอุตสาหกรรมอื่นๆ เมื่อเราได้รับการแต่งตั้งสำหรับโครงการของคุณแล้ว เราสามารถดูแลการผลิตทั้งหมด การประกอบ การทดสอบ คุณสมบัติ การจัดส่งและศุลกากรตามที่คุณต้องการ หากคุณต้องการ เราสามารถจัดเก็บชิ้นส่วนของคุณ ประกอบชุดที่กำหนดเอง พิมพ์และติดฉลากชื่อบริษัทและแบรนด์ของคุณ และส่งให้ลูกค้าของคุณ กล่าวอีกนัยหนึ่ง เราสามารถเป็นศูนย์คลังสินค้าและกระจายสินค้าของคุณได้เช่นกันหากต้องการ เนื่องจากคลังสินค้าของเราตั้งอยู่ใกล้ท่าเรือหลัก จึงทำให้เรามีความได้เปรียบด้านลอจิสติกส์ ตัวอย่างเช่น เมื่อผลิตภัณฑ์ของคุณมาถึงท่าเรือที่สำคัญของสหรัฐอเมริกา เราสามารถ transport ได้โดยตรงไปยังคลังสินค้าใกล้เคียง ซึ่งเราสามารถจัดเก็บ ประกอบ ทำชุด ฉลากใหม่ พิมพ์ บรรจุหีบห่อตามที่คุณต้องการและวาง จัดส่งให้กับลูกค้าของคุณ เราไม่เพียงแต่จัดหาผลิตภัณฑ์ บริษัทของเราทำงานบนสัญญาแบบกำหนดเองที่เรามาที่ไซต์ของคุณ ประเมินโครงการของคุณบนไซต์ และพัฒนาข้อเสนอโครงการแบบกำหนดเองที่ออกแบบมาสำหรับคุณ จากนั้นเราจะส่งทีมงานที่มีประสบการณ์ของเราไปดำเนินการตามโครงการ สามารถดูข้อมูลเพิ่มเติมเกี่ยวกับงานวิศวกรรมของเราได้ที่ http://www.ags-engineering.com -เราใช้โครงการขนาดเล็กและโครงการขนาดใหญ่ในระดับอุตสาหกรรม ในขั้นแรก เราสามารถเชื่อมต่อคุณทางโทรศัพท์ การประชุมทางไกล หรือ MSN Messenger กับสมาชิกในทีมผู้เชี่ยวชาญของเรา เพื่อให้คุณสามารถสื่อสารโดยตรงกับผู้เชี่ยวชาญ ถามคำถาม และหารือเกี่ยวกับโครงการของคุณ โทรหาเราถ้าจำเป็นเราจะไปหาคุณ. หน้าก่อน