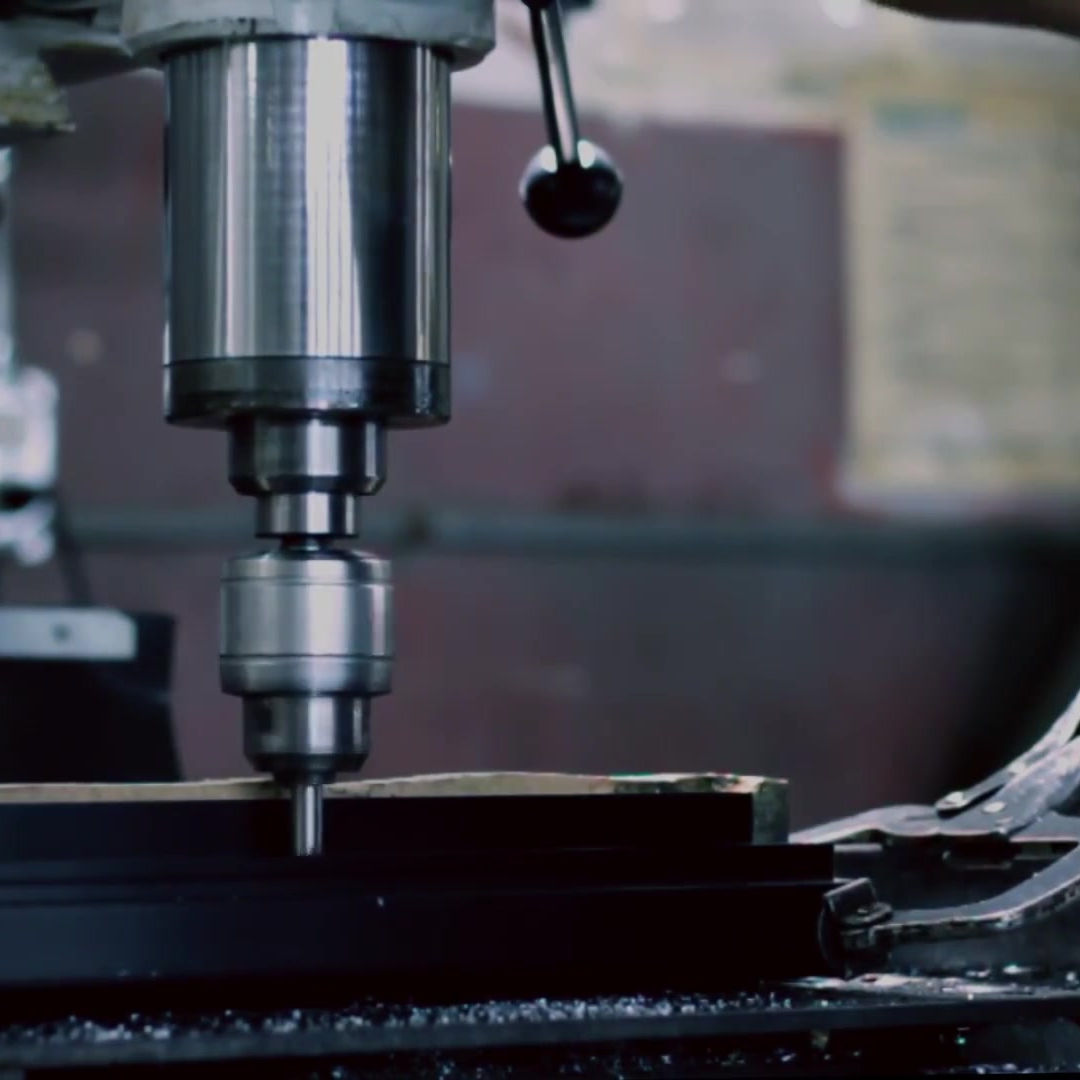
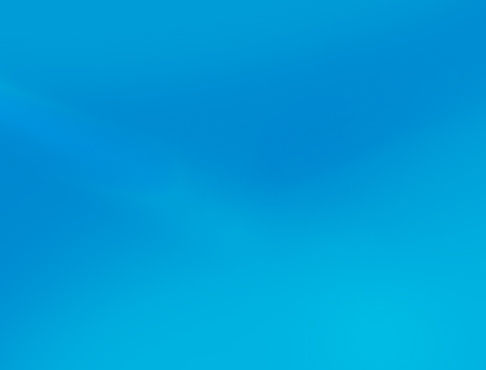
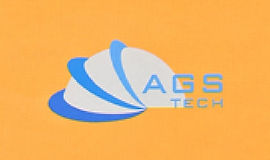
Global Custom Manufacturer, Integrator, Consolidator, Outsourcing Partner for a Wide Variety of Products & Services.
We are your one-stop source for manufacturing, fabrication, engineering, consolidation, integration, outsourcing of custom manufactured and off-shelf products & services. We also private label / white label your products with your brand name if you wish.
Choose your Language
-
Custom Manufacturing of Parts, Components, Assemblies, Finished Products, Machines and Industrial Equipment
-
Domestic & Global Contract Manufacturing
-
Manufacturing Outsourcing
-
Domestic, Global Procurement of Industrial Products
-
Private labeling / White Labeling your Products with your Brand Name
-
Product Finding & Locating Services
-
Global Design and Channel Partnership
-
Engineering Integration
-
Engineering Services
-
Global Consolidation, Warehousing, Logistics
Among the many THERMAL ANALYSIS EQUIPMENT, we focus our attention to the popular ones in industry, namely the DIFFERENTIAL SCANNING CALORIMETRY ( DSC ), THERMO-GRAVIMETRIC ANALYSIS ( TGA ), THERMO-MECHANICAL ANALYSIS ( TMA ), DILATOMETRY,DYNAMIC MECHANICAL ANALYSIS ( DMA ), DIFFERENTIAL THERMAL ANALYSIS ( DTA). Our INFRARED TEST EQUIPMENT involves THERMAL IMAGING INSTRUMENTS, INFRARED THERMOGRAPHERS, INFRARED CAMERAS. Some applications for our thermal imaging instruments are Electrical and Mechanical System Inspection, Electronic Component Inspection, Corrosion Damage and Metal Thinning, Flaw Detection.
Please download catalogs from colored links below and let us know your prefered brand and model number of the product. You can purchase brand new or refurbished / used Thermal & IR Test Equipment from us:
FLUKE Test Tools Catalog (includes Thermal Imagers, Thermometers)
HAIDA Color Assessment Cabinet
Private Label Hand Tools for Every Industry (This catalog contains a few thermal & IR test instruments. We can private label these hand tools if you wish. In other words, we can put your company name, brand and label on them. This way you can promote your brand by reselling these to your customers.)
DIFFERENTIAL SCANNING CALORIMETERS (DSC) : A technique in which the difference in the amount of heat required to increase the temperature of a sample and reference is measured as a function of temperature. Both the sample and reference are maintained at nearly the same temperature throughout the experiment. The temperature program for a DSC analysis is established so that the sample holder temperature increases linearly as a function of time. The reference sample has a well-defined heat capacity over the range of temperatures to be scanned. DSC experiments provide as a result a curve of heat flux versus temperature or versus time. Differential scanning calorimeters are frequently used to study what happens to polymers when they're heated. The thermal transitions of a polymer can be studied using this technique. Thermal transitions are changes that take place in a polymer when they are heated. The melting of a crystalline polymer is an example. The glass transition is also a thermal transition. DSC thermal analysis is carried out for determining Thermal Phase Changes, Thermal Glass Transition Temperature (Tg), Crystalline Melt Temperatures, Endothermic Effects, Exothermic Effects, Thermal Stabilities, Thermal Formulation Stabilities, Oxidative Stabilities, Transition Phenomena, Solid State Structures. DSC analysis determines the Tg Glass Transition Temperature, temperature at which amorphous polymers or an amorphous part of a crystalline polymer go from a hard brittle state to a soft rubbery state, melting point, temperature at which a crystalline polymer melts, Hm Energy Absorbed (joules/gram), amount of energy a sample absorbs when melting, Tc Crystallization Point, temperature at which a polymer crystallizes upon heating or cooling, Hc Energy Released (joules/gram), amount of energy a sample releases when crystallizing. Differential Scanning Calorimeters can be used to determine the thermal properties of plastics, adhesives, sealants, metal alloys, pharmaceutical materials, waxes, foods, oils and lubricants and catalysts….etc.
DIFFERENTIAL THERMAL ANALYZERS (DTA): An alternative technique to DSC. In this technique it is the heat flow to the sample and reference that remains the same instead of the temperature. When the sample and reference are heated identically, phase changes and other thermal processes cause a difference in temperature between the sample and reference. DSC measures the energy required to keep both the reference and the sample at the same temperature whereas DTA measures the difference in temperature between the sample and the reference when they are both put under the same heat. So they are similar techniques.
THERMOMECHANICAL ANALYZER (TMA) : The TMA reveals the change in the dimensions of a sample as a function of temperature. One can regard TMA as a very sensitive micrometer. The TMA is a device that allows precise measurements of position and can be calibrated against known standards. A temperature control system consisting of a furnace, heat sink and a thermocouple surrounds the samples. Quartz, invar or ceramic fixtures hold the samples during tests. TMA measurements record changes caused by changes in the free volume of a polymer. Changes in free volume are volumetric changes in the polymer caused by the absorption or release of heat associated with that change; the loss of stiffness; increased flow; or by the change in relaxation time. The free volume of a polymer is known to be related to viscoelasticity, aging, penetration by solvents, and impact properties. The glass transition temperature Tg in a polymer corresponds to the expansion of the free volume allowing greater chain mobility above this transition. Seen as an inflection or bending in the thermal expansion curve, this change in the TMA can be seen to cover a range of temperatures. The glass transition temperature Tg is calculated by an agreed upon method. Perfect agreement is not immediately witnessed in the value of the Tg when comparing different methods, however if we carefully examine the agreed upon methods in determining the Tg values then we understand that there is actually good agreement. Besides its absolute value, the width of the Tg is also an indicator of changes in the material. TMA is a relatively simple technique to carry out. TMA is often used for measuring Tg of materials such as highly cross-linked thermoset polymers for which the Differential Scanning Calorimeter (DSC) is difficult to use. In addition to Tg, the coefficient of thermal expansion (CTE) is obtained from thermomechanical analysis. The CTE is calculated from the linear sections of the TMA curves. Another useful result the TMA can provide us is finding out the orientation of crystals or fibers. Composite materials may have three distinct thermal expansion coefficients in the x, y and z directions. By recording the CTE in x, y and z directions one may understand in which direction fibers or crystals are predominantly oriented. To measure the bulk expansion of the material a technique called DILATOMETRY can be used. The sample is immersed in a fluid such as silicon oil or Al2O3 powder in the dilatometer, run thru the temperature cycle and the expansions in all directions are converted to a vertical movement, which is measured by the TMA. Modern thermomechanical analyzers make this easy for users. If a pure liquid is used, the dilatometer is filled with that liquid instead of the silicon oil or alumina oxide. Using diamond TMA the users can run stress strain curves, stress relaxation experiments, creep-recovery and dynamic mechanical temperature scans. The TMA is an indispensible test equipment for industry and research.
THERMOGRAVIMETRIC ANALYZERS ( TGA ) : Thermogravimetric Analysis is a technique where the mass of a substance or specimen is monitored as a function of temperature or time. The sample specimen is subjected to a controlled temperature program in a controlled atmosphere. The TGA measures a sample’s weight as it is heated or cooled in its furnace. A TGA instrument consists of a sample pan that is supported by a precision balance. That pan resides in a furnace and is heated or cooled during the test. The mass of the sample is monitored during the test. Sample environment is purged with an inert or a reactive gas. Thermogravimetric analyzers can quantify loss of water, solvent, plasticizer, decarboxylation, pyrolysis, oxidation, decomposition, weight % filler material, and weight % ash. Depending on the case, information may be obtained upon heating or cooling. A typical TGA thermal curve is displayed from left to right. If the TGA thermal curve descends, it indicates a weight loss. Modern TGAs are capable of conducting isothermal experiments. Sometimes the user may want to use a reactive sample purge gases, such as oxygen. When using oxygen as a purge gas user may want to switch gases from nitrogen to oxygen during the experiment. This technique is frequently used to identify the percent carbon in a material. Thermogravimetric analyzer can be used to compare two similar products, as a quality control tool to ensure products meet their material specifications, to ensure products meet safety standards, to determine carbon content, identifying counterfeit products, to identify safe operating temperatures in various gases, to enhance product formulation processes, to reverse engineer a product. Finally it is worth mentioning that combinations of a TGA with a GC/MS are available. GC is short for Gas Chromatography and MS is short for Mass Spectrometry.
DYNAMIC MECHANICAL ANALYZER ( DMA) : This is a technique where a small sinusoidal deformation is applied to a sample of known geometry in a cyclic manner. The materials response to stress, temperature, frequency and other values is then studied. The sample can be subjected to a controlled stress or a controlled strain. For a known stress, the sample will deform a certain amount, depending on its stiffness. DMA measures stiffness and damping, these are reported as modulus and tan delta. Because we are applying a sinusoidal force, we can express the modulus as an in-phase component (the storage modulus), and an out of phase component (the loss modulus). The storage modulus, either E’ or G’, is the measure of the sample’s elastic behavior. The ratio of the loss to the storage is the tan delta and is called damping. It is considered a measure of the energy dissipation of a material. Damping varies with the state of the material, its temperature, and with the frequency. DMA is sometimes called DMTA standing for DYNAMIC MECHANICAL THERMAL ANALYZER. Thermomechanical Analysis applies a constant static force to a material and records the material dimensional changes as temperature or time varies. The DMA on the other hand, applies an oscillatory force at a set frequency to the sample and reports changes in stiffness and damping. DMA data provides us modulus information whereas the TMA data gives us the coefficient of thermal expansion. Both techniques detect transitions, but DMA is much more sensitive. Modulus values change with temperature and transitions in materials can be seen as changes in the E’ or tan delta curves. This includes glass transition, melting and other transitions that occur in the glassy or rubbery plateau which are indicators of subtle changes in the material.
THERMAL IMAGING INSTRUMENTS, INFRARED THERMOGRAPHERS, INFRARED CAMERAS : These are devices that form an image using infrared radiation. Standard everyday cameras form images using visible light in the 450–750 nanometer wavelength range. Infrared cameras however operate in the infrared wavelength range as long as 14,000 nm. Generally, the higher an object's temperature, the more infrared radiation is emitted as black-body radiation. Infrared cameras work even in total darkness. Images from most infrared cameras have a single color channel because the cameras generally use an image sensor that does not distinguish different wavelengths of infrared radiation. To differentiate wavelengths color image sensors require a complex construction. In some test instruments these monochromatic images are displayed in pseudo-color, where changes in color are used rather than changes in intensity to display changes in the signal. The brightest (warmest) parts of images are customarily colored white, intermediate temperatures are colored red and yellow, and the dimmest (coolest) parts are colored black. A scale is generally shown next to a false color image to relate colors to temperatures. Thermal cameras have resolutions considerably lower than that of optical cameras, with values in the neighborhood of 160 x 120 or 320 x 240 pixels. More expensive infrared cameras can achieve a resolution of 1280 x 1024 pixels. There are two main categories of thermographic cameras: COOLED INFRARED IMAGE DETECTOR SYSTEMS and UNCOOLED INFRARED IMAGE DETECTOR SYSTEMS. Cooled thermographic cameras have detectors contained in a vacuum-sealed case and are cryogenically cooled. The cooling is necessary for the operation of the semiconductor materials used. Without cooling, these sensors would be flooded by their own radiation. Cooled infrared cameras are however expensive. Cooling requires much energy and is time-consuming, requiring several minutes of cooling time prior to working. Although the cooling apparatus is bulky and expensive, cooled infrared cameras offer users superior image quality compared to uncooled cameras. The better sensitivity of cooled cameras allows the use of lenses with higher focal length. Bottled nitrogen gas can be used for cooling. Uncooled thermal cameras use sensors operating at ambient temperature, or sensors stabilized at a temperature close to ambient using temperature control elements. Uncooled infrared sensors are not cooled to low temperatures and therefore do not require bulky and expensive cryogenic coolers. Their resolution and image quality however is lower as compared to cooled detectors. Thermographic cameras offer many opportunities. Overheating spots is power lines can be located and repaired. Electric circuitry can be observed and unusually hot spots can indicate problems such as short circuit. These cameras are also widely used in buildings and energy systems to locate places where there is significant heat loss so that better heat insulation can be considered at those points. Thermal imaging instruments serve as non-destructive test equipment.
For details and other similar equipment, please visit our equipment website: http://www.sourceindustrialsupply.com