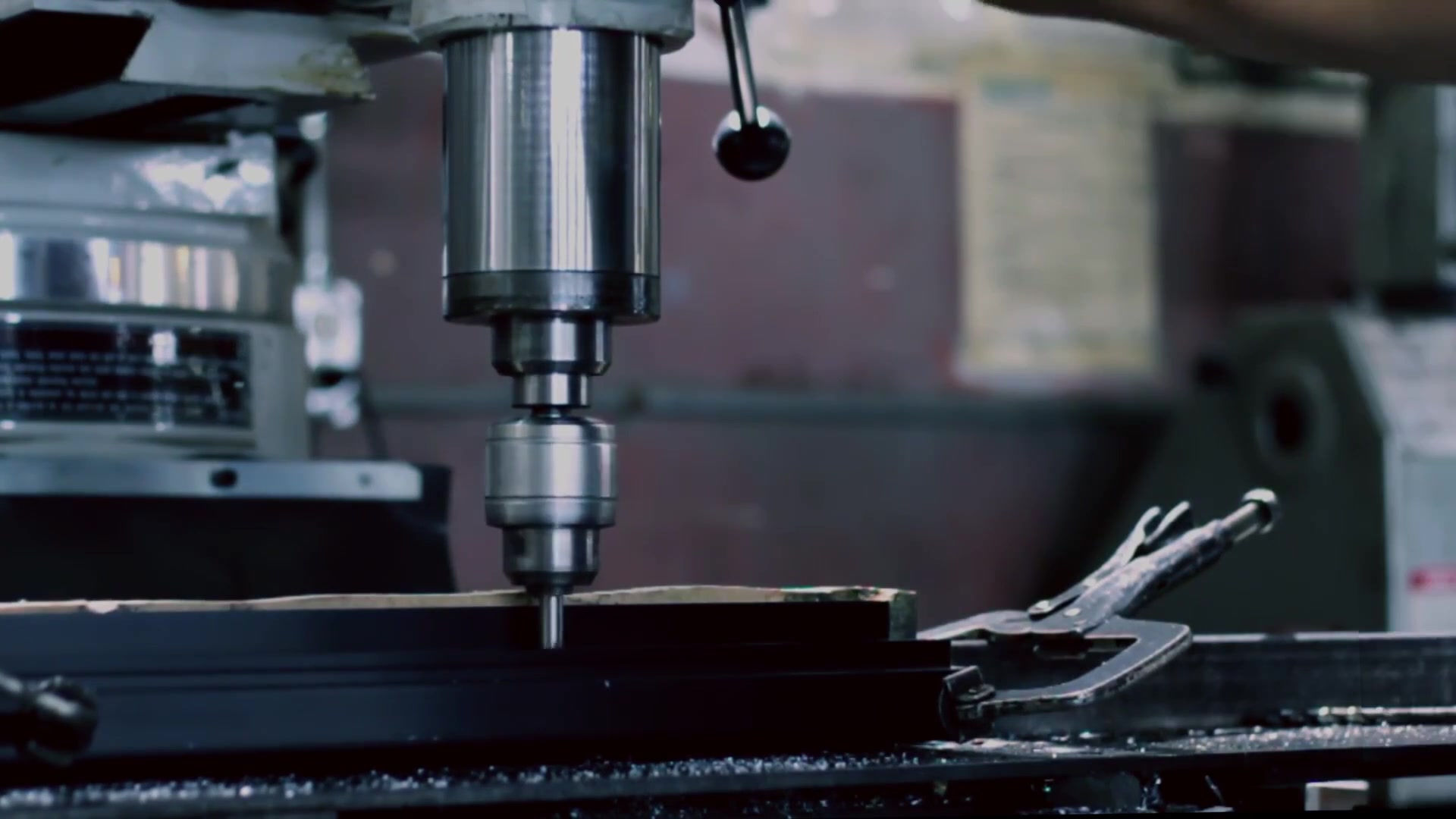
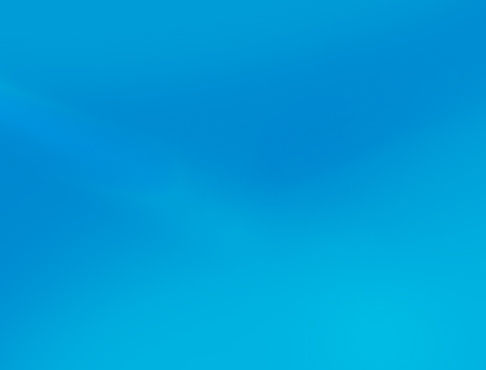
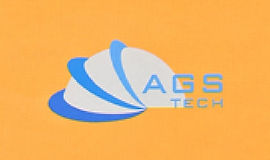
Pandaigdigang Custom na Manufacturer, Integrator, Consolidator, Outsourcing Partner para sa Maraming Iba't Ibang Produkto at Serbisyo.
Kami ang iyong one-stop source para sa pagmamanupaktura, fabrication, engineering, consolidation, integration, outsourcing ng custom na manufactured at off-shelf na mga produkto at serbisyo.
Piliin ang iyong Wika
-
Custom na Paggawa
-
Domestic at Global Contract Manufacturing
-
Paggawa ng Outsourcing
-
Domestic at Global Procurement
-
Consolidation
-
Pagsasama-sama ng Engineering
-
Serbisyong inhinyero
ELECTRICAL DISCHARGE MACHINING (EDM), also referred to as SPARK-EROSION or ELECTRODISCHARGE MACHINING, SPARK ERODING, DIE SINKING_cc781905-5cde-3194-bb3b -136bad5cf58d_or WIRE EROSION, is a NON-CONVENTIONAL MANUFACTURING process where erosion of metals takes place and desired shape is obtained using electrical discharges in the form ng sparks. Nag-aalok din kami ng ilang uri ng EDM, namely NO-WEAR EDM, WIRE EDM (WEDM), EDM GRINDING (EDG), DIE-SINKING EDM, ELECTRICAL-DISCHARGE MILLING, micro-EDM_cc7-19EDM -5cde-3194-bb3b-136bad5cf58d_and ELECTROCHEMICAL-DISCHARGE GRINDING (ECDG). Ang aming mga EDM system ay binubuo ng mga hugis na tool/electrode at ang workpiece na konektado sa DC power supply at ipinasok sa isang electrically nonconducting dielectric fluid. Pagkatapos ng 1940 ang electrical discharge machining ay naging isa sa pinakamahalaga at tanyag na teknolohiya ng produksyon sa mga industriya ng pagmamanupaktura.
Kapag ang distansya sa pagitan ng dalawang electrodes ay nabawasan, ang intensity ng electric field sa volume sa pagitan ng mga electrodes ay nagiging mas malaki kaysa sa lakas ng dielectric sa ilang mga punto, na break, sa huli ay bumubuo ng isang tulay para sa kasalukuyang daloy sa pagitan ng dalawang electrodes. Ang isang matinding electrical arc ay nabuo na nagiging sanhi ng makabuluhang pag-init upang matunaw ang isang bahagi ng workpiece at ilan sa tooling material. Bilang isang resulta, ang materyal ay tinanggal mula sa parehong mga electrodes. Kasabay nito, ang dielectric fluid ay mabilis na pinainit, na nagreresulta sa pagsingaw ng fluid sa arc gap. Kapag ang kasalukuyang daloy ay huminto o ito ay tumigil, ang init ay tinanggal mula sa gas bubble ng nakapalibot na dielectric fluid at ang bubble ay nag-cavitate (bumabagsak). Ang shock wave na nilikha ng pagbagsak ng bubble at ang daloy ng dielectric fluid ay nag-flush ng mga debris mula sa workpiece surface at ipasok ang anumang tinunaw na workpiece na materyal sa dielectric fluid. Ang rate ng pag-uulit para sa mga discharge na ito ay nasa pagitan ng 50 hanggang 500 kHz, mga boltahe sa pagitan ng 50 hanggang 380 V at ang mga alon sa pagitan ng 0.1 at 500 Amperes. Ang bagong likidong dielectric tulad ng mga mineral na langis, kerosene o distilled at deionized na tubig ay karaniwang dinadala sa inter-electrode volume na nagdadala ng mga solidong particle (sa anyo ng mga debris) at ang mga katangian ng insulating ng dielectric ay naibalik. Pagkatapos ng isang kasalukuyang daloy, ang potensyal na pagkakaiba sa pagitan ng dalawang electrodes ay naibalik sa kung ano ito bago ang pagkasira, kaya maaaring mangyari ang isang bagong likidong dielectric breakdown. Ang aming mga modernong electrical discharge machine (EDM) ay nag-aalok ng mga paggalaw na kinokontrol ayon sa numero at nilagyan ng mga pump at filtering system para sa mga dielectric fluid.
Ang Electrical discharge machining (EDM) ay isang paraan ng machining na pangunahing ginagamit para sa mga matitigas na metal o yaong napakahirap i-machine gamit ang mga kumbensyonal na pamamaraan. Karaniwang gumagana ang EDM sa anumang mga materyales na mga electrical conductor, bagama't iminungkahi din ang mga pamamaraan para sa machining insulating ceramics na may EDM. Ang punto ng pagkatunaw at nakatagong init ng pagkatunaw ay mga katangian na tumutukoy sa dami ng metal na inalis sa bawat paglabas. Kung mas mataas ang mga halagang ito, mas mabagal ang rate ng pag-alis ng materyal. Dahil ang proseso ng electrical discharge machining ay hindi nagsasangkot ng anumang mekanikal na enerhiya, ang tigas, lakas, at tigas ng workpiece ay hindi nakakaapekto sa rate ng pagtanggal. Ang dalas ng paglabas o enerhiya sa bawat paglabas, ang boltahe at kasalukuyang ay iba-iba upang makontrol ang mga rate ng pag-alis ng materyal. Ang rate ng pag-aalis ng materyal at pagkamagaspang sa ibabaw ay tumataas sa pagtaas ng kasalukuyang density at pagbaba ng dalas ng spark. Maaari naming i-cut ang mga masalimuot na contour o cavities sa pre-hardened steel gamit ang EDM nang hindi nangangailangan ng heat treatment para lumambot at muling tumigas ang mga ito. Maaari naming gamitin ang pamamaraang ito sa anumang metal o metal na haluang metal tulad ng titanium, hastelloy, kovar, at inconel. Kasama sa mga aplikasyon ng proseso ng EDM ang paghubog ng mga polycrystalline na tool na brilyante. Ang EDM ay itinuturing na isang hindi tradisyonal o hindi kumbensyonal na pamamaraan ng machining kasama ng mga proseso tulad ng electrochemical machining (ECM), water jet cutting (WJ, AWJ), laser cutting. Sa kabilang banda, ang mga karaniwang pamamaraan ng machining ay kinabibilangan ng pag-ikot, paggiling, paggiling, pagbabarena at iba pang proseso na ang mekanismo ng pag-alis ng materyal ay mahalagang batay sa mga puwersang mekanikal. Ang mga electrodes para sa electrical-discharge machining (EDM) ay gawa sa graphite, brass, copper at copper-tungsten alloy. Posible ang mga diameter ng electrode hanggang sa 0.1mm. Dahil ang pagsusuot ng tool ay isang hindi kanais-nais na phenomenon na negatibong nakakaapekto sa dimensional accuracy sa EDM, sinasamantala namin ang isang prosesong tinatawag na NO-WEAR EDM, sa pamamagitan ng pag-reverse ng polarity at paggamit ng mga copper tool upang mabawasan ang pagkasira ng tool.
Sa perpektong pagsasalita, ang electrical-discharge machining (EDM) ay maaaring ituring na isang serye ng pagkasira at pagpapanumbalik ng dielectric na likido sa pagitan ng mga electrodes. Gayunpaman, sa katotohanan, ang pag-alis ng mga labi mula sa inter-electrode area ay halos palaging bahagyang. Ito ay nagiging sanhi ng mga electrical propriety ng dielectric sa inter-electrodes area na naiiba sa kanilang mga nominal na halaga at nag-iiba sa oras. Ang distansya ng inter-electrode, (spark-gap), ay inaayos ng mga algorithm ng kontrol ng partikular na makina na ginamit. Sa kasamaang-palad, ang spark-gap sa EDM ay maaaring mai-short-circuited ng mga labi. Ang sistema ng kontrol ng elektrod ay maaaring mabigo sa sapat na mabilis na reaksyon upang maiwasan ang dalawang electrodes (tool at workpiece) mula sa short circuiting. Ang hindi ginustong maikling circuit na ito ay nag-aambag sa pag-alis ng materyal na naiiba mula sa perpektong kaso. Pinahahalagahan namin ang pagkilos ng pag-flush upang maibalik ang mga katangian ng insulating ng dielectric upang palaging nangyayari ang kasalukuyang sa punto ng inter-electrode area, at sa gayon ay pinapaliit ang posibilidad ng hindi gustong pagbabago ng hugis (pagkasira) ng tool-electrode at workpiece. Upang makakuha ng isang partikular na geometry, ang EDM tool ay ginagabayan sa nais na landas na napakalapit sa workpiece nang hindi ito hinahawakan, Lubos naming binibigyang pansin ang pagganap ng kontrol sa paggalaw na ginagamit. Sa ganitong paraan, ang isang malaking bilang ng mga kasalukuyang discharges / sparks ay nagaganap, at ang bawat isa ay nag-aambag sa pag-alis ng materyal mula sa parehong tool at workpiece, kung saan ang mga maliliit na crater ay nabuo. Ang laki ng mga craters ay isang function ng mga teknolohikal na parameter na itinakda para sa partikular na trabaho sa kamay at ang mga sukat ay maaaring mula sa nanoscale (tulad ng sa kaso ng micro-EDM operations) hanggang sa ilang daang micrometer sa mga roughing na kondisyon. Ang maliliit na bunganga na ito sa tool ay nagdudulot ng unti-unting pagguho ng elektrod na tinatawag na "tool wear". Upang malabanan ang masamang epekto ng pagsusuot sa geometry ng workpiece, patuloy naming pinapalitan ang tool-electrode sa panahon ng operasyon ng machining. Minsan nakakamit natin ito sa pamamagitan ng paggamit ng isang patuloy na pinapalitang wire bilang electrode ( ang prosesong ito ng EDM ay tinatawag ding WIRE EDM ). Minsan ginagamit namin ang tool-electrode sa paraang maliit na bahagi lamang nito ang aktwal na nakikibahagi sa proseso ng machining at ang bahaging ito ay regular na binago. Ito ay, halimbawa, ang kaso kapag gumagamit ng umiikot na disk bilang isang tool-electrode. Ang prosesong ito ay tinatawag na EDM GRINDING. Ang isa pang pamamaraan na aming idini-deploy ay binubuo ng paggamit ng isang hanay ng mga electrodes na may iba't ibang laki at hugis sa panahon ng parehong operasyon ng EDM upang mabayaran ang pagkasira. Tinatawag namin itong multiple electrode technique, at pinakakaraniwang ginagamit kapag ang tool electrode ay ginagaya sa negatibo ang nais na hugis at naka-advance patungo sa blangko kasama ang isang direksyon, kadalasan ang vertical na direksyon (ie z-axis). Ito ay kahawig ng lababo ng tool sa dielectric na likido kung saan ang workpiece ay inilubog, at samakatuwid ito ay tinutukoy bilang DIE-SINKING EDM_cc781905-5cde-3194-bb3b-1568d_d5cde-3194-bb3b-5scc-times 3194-bb3b-136bad5cf58d_CONVENTIONAL EDM or RAM EDM). Ang mga makina para sa operasyong ito ay tinatawag na SINKER EDM. Ang mga electrodes para sa ganitong uri ng EDM ay may mga kumplikadong anyo. Kung ang panghuling geometry ay nakuha gamit ang isang karaniwang simpleng hugis na electrode na inilipat sa ilang direksyon at napapailalim din sa mga pag-ikot, tinatawag namin itong EDM MILLING. Ang halaga ng pagsusuot ay mahigpit na nakasalalay sa mga teknolohikal na parameter na ginamit sa operasyon ( polarity, maximum na kasalukuyang, bukas na boltahe ng circuit). Halimbawa, in micro-EDM, na kilala rin bilang m-EDM, ang mga parameter na ito ay karaniwang itinatakda sa mga value na nagdudulot ng matinding pagkasira. Samakatuwid, ang pagsusuot ay isang malaking problema sa lugar na iyon na binabawasan namin gamit ang aming naipon na kaalaman. Halimbawa upang mabawasan ang pagkasira sa mga graphite electrodes, isang digital generator, na nakokontrol sa loob ng milliseconds, ay binabaligtad ang polarity habang nagaganap ang electro-erosion. Nagreresulta ito sa epektong katulad ng electroplating na patuloy na nagdedeposito ng eroded graphite pabalik sa electrode. Sa isa pang paraan, ang tinatawag na 'Zero Wear'' circuit ay pinaliit namin kung gaano kadalas nagsisimula at humihinto ang discharge, na pinapanatili itong naka-on hangga't maaari. Ang rate ng pag-alis ng materyal sa electrical-discharge machining ay maaaring tantiyahin mula sa:
MRR = 4 x 10 exp(4) x I x Tw exp (-1.23)
Narito ang MRR ay nasa mm3/min, ako ay kasalukuyang sa Amperes, ang Tw ay workpiece melting point sa K-273.15K. Ang exp ay nangangahulugang exponent.
Sa kabilang banda, ang wear rate Wt ng electrode ay maaaring makuha mula sa:
Wt = ( 1.1 x 10exp(11) ) x I x Ttexp(-2.38)
Narito ang Wt ay nasa mm3/min at ang Tt ay melting point ng electrode material sa K-273.15K
Sa wakas, ang wear ratio ng workpiece sa electrode R ay maaaring makuha mula sa:
R = 2.25 x Trexp(-2.38)
Narito ang Tr ay ang ratio ng mga natutunaw na punto ng workpiece sa elektrod.
SINKER EDM :
Sinker EDM, na tinutukoy din bilang CAVITY TYPE EDM or_cc781905-194 subtitle-6b5b3 at Electrocde na bahagi ng EDM_cc78. Ang elektrod at workpiece ay konektado sa isang power supply. Ang power supply ay bumubuo ng isang potensyal na elektrikal sa pagitan ng dalawa. Habang lumalapit ang elektrod sa workpiece, ang dielectric breakdown ay nangyayari sa fluid, na bumubuo ng plasma channel, at isang maliit na spark jumps. Ang mga spark ay karaniwang tumatama nang paisa-isa dahil ito ay lubos na hindi malamang na ang iba't ibang mga lokasyon sa inter-electrode space ay may magkaparehong mga lokal na katangiang elektrikal na magbibigay-daan sa isang spark na mangyari sa lahat ng naturang mga lokasyon nang sabay-sabay. Daan-daang libo ng mga spark na ito ang nangyayari sa mga random na punto sa pagitan ng elektrod at ng workpiece bawat segundo. Habang bumababa ang base metal, at kasunod na tumataas ang spark gap, ang elektrod ay awtomatikong ibinababa ng aming CNC machine upang ang proseso ay maaaring magpatuloy nang walang patid. Ang aming kagamitan ay may mga control cycle na kilala bilang ''on time'' at ''off time''. Tinutukoy ng setting ng on time ang haba o tagal ng spark. Ang mas matagal sa oras ay nagdudulot ng mas malalim na lukab para sa spark na iyon at lahat ng kasunod na spark para sa cycle na iyon, na lumilikha ng mas magaspang na pagtatapos sa workpiece at vice versa. Ang off time ay ang tagal ng panahon na ang isang spark ay pinalitan ng isa pa. Ang mas mahabang off time ay nagpapahintulot sa dielectric fluid na mag-flush sa isang nozzle upang linisin ang mga eroded debris, sa gayon ay maiwasan ang isang short circuit. Ang mga setting na ito ay inaayos sa loob ng micro segundo.
WIRE EDM :
In WIRE ELECTRICAL DISCHARGE MACHINING (WEDM), also called WIRE-CUT EDM or WIRE CUTTING, we feed a manipis na single-strand metal wire ng tanso sa pamamagitan ng workpiece, na nakalubog sa isang tangke ng dielectric fluid. Ang Wire EDM ay isang mahalagang variation ng EDM. Paminsan-minsan ay gumagamit kami ng wire-cut EDM para maghiwa ng mga plate na kasing kapal ng 300mm at gumawa ng mga suntok, tool, at dies mula sa matitigas na metal na mahirap i-machine sa iba pang paraan ng pagmamanupaktura. Sa prosesong ito na kahawig ng contour cutting na may band saw, ang wire, na patuloy na pinapakain mula sa isang spool, ay nakahawak sa pagitan ng upper at lower brilyante na gabay. Ang mga gabay na kinokontrol ng CNC ay gumagalaw sa x–y plane at ang itaas na gabay ay maaari ding gumalaw nang nakapag-iisa sa z–u–v axis, na nagbibigay ng kakayahang mag-cut ng mga tapered at transition na hugis (tulad ng bilog sa ibaba at parisukat sa sa itaas). Maaaring kontrolin ng itaas na gabay ang mga paggalaw ng axis sa x–y–u–v–i–j–k–l–. Nagbibigay-daan ito sa WEDM na mag-cut ng napakasalimuot at pinong mga hugis. Ang average na cutting kerf ng aming kagamitan na nakakamit ang pinakamahusay na gastos sa ekonomiya at oras ng machining ay 0.335 mm gamit ang Ø 0.25 brass, copper o tungsten wire. Gayunpaman ang upper at lower diamond guides ng aming CNC equipment ay tumpak sa humigit-kumulang 0.004 mm, at maaaring magkaroon ng cutting path o kerf na kasing liit ng 0.021 mm gamit ang Ø 0.02 mm wire. Kaya talagang makitid na pagbawas ay posible. Ang lapad ng pagputol ay mas malaki kaysa sa lapad ng wire dahil nangyayari ang sparking mula sa mga gilid ng wire hanggang sa workpiece, na nagiging sanhi ng pagguho. Ang "overcut" na ito ay kinakailangan, para sa maraming mga aplikasyon ito ay predictable at samakatuwid ay maaaring mabayaran para sa (sa micro-EDM ito ay hindi madalas na ang kaso). Mahaba ang mga wire spool—isang 8 kg na spool na 0.25 mm na wire ay mahigit 19 kilometro lang ang haba. Ang diameter ng wire ay maaaring kasing liit ng 20 micrometres at ang geometry precision ay nasa paligid ng +/- 1 micrometer. Karaniwan naming ginagamit ang wire nang isang beses lamang at nire-recycle ito dahil medyo mura ito. Ito ay naglalakbay sa isang pare-parehong bilis na 0.15 hanggang 9m/min at ang isang pare-parehong kerf (slot) ay pinananatili sa panahon ng isang hiwa. Sa proseso ng wire-cut EDM ginagamit namin ang tubig bilang dielectric fluid, na kinokontrol ang resistivity nito at iba pang mga electrical properties na may mga filter at de-ionizer units. Ang tubig ay nag-flush ng mga naputol na labi mula sa cutting zone. Ang pag-flush ay isang mahalagang kadahilanan sa pagtukoy ng maximum na rate ng feed para sa isang partikular na kapal ng materyal at samakatuwid ay pinapanatili namin itong pare-pareho. Ang bilis ng pagputol sa wire EDM ay nakasaad sa mga tuntunin ng cross-sectional area cut sa bawat yunit ng oras, tulad ng 18,000 mm2/hr para sa 50mm na kapal ng D2 na tool steel. Ang linear cutting speed para sa kasong ito ay magiging 18,000/50 = 360mm/hr Ang rate ng pag-alis ng materyal sa wire EDM ay:
MRR = Vf xhxb
Narito ang MRR ay nasa mm3/min, ang Vf ay ang feed rate ng wire sa workpiece sa mm/min, ang h ay ang kapal o taas sa mm, at ang b ay ang kerf, na:
b = dw + 2s
Narito ang dw ay diameter ng wire at ang s ay agwat sa pagitan ng wire at workpiece sa mm.
Kasama ng mas mahigpit na pagpapaubaya, ang aming modernong multi axis EDM wire-cutting machining center ay nagdagdag ng mga feature gaya ng multi heads para sa pagputol ng dalawang bahagi nang sabay, mga kontrol para maiwasan ang pagkabasag ng wire, mga feature na awtomatikong self-threading kung sakaling masira ang wire, at nakaprograma. mga diskarte sa machining upang ma-optimize ang operasyon, tuwid at angular na mga kakayahan sa pagputol.
Ang Wire-EDM ay nag-aalok sa amin ng mababang mga natitirang stress, dahil hindi ito nangangailangan ng mataas na puwersa ng pagputol para sa pag-alis ng materyal. Kapag ang enerhiya/kapangyarihan sa bawat pulso ay medyo mababa (tulad ng sa pagtatapos ng mga operasyon), ang maliit na pagbabago sa mga mekanikal na katangian ng isang materyal ay inaasahan dahil sa mababang mga natitirang stress.
ELECTRICAL-DISCHARGE GRINDING (EDG) : Ang mga grinding wheel ay hindi naglalaman ng mga abrasive, ang mga ito ay gawa sa grapayt o tanso. Ang mga paulit-ulit na spark sa pagitan ng umiikot na gulong at workpiece ay nag-aalis ng materyal mula sa mga ibabaw ng workpiece. Ang rate ng pag-alis ng materyal ay:
MRR = K x I
Narito ang MRR ay nasa mm3/min, ang I ay kasalukuyang sa Amperes, at ang K ay workpiece material factor sa mm3/A-min. Madalas kaming gumagamit ng electrical-discharge grinding upang makakita ng mga makitid na hiwa sa mga bahagi. Minsan ay pinagsasama-sama namin ang proseso ng EDG (Electrical-Discharge Grinding) sa proseso ng ECG (Electrochemical Grinding) kung saan ang materyal ay inaalis sa pamamagitan ng pagkilos ng kemikal, ang mga discharge ng kuryente mula sa graphite wheel ay sumisira sa oxide film at nahuhugasan ng electrolyte. Ang proseso ay tinatawag na ELECTROCHEMICAL-DISCHARGE GRINDING (ECDG). Kahit na ang proseso ng ECDG ay gumagamit ng medyo mas maraming kapangyarihan, ito ay isang mas mabilis na proseso kaysa sa EDG. Kadalasan ay gumiling kami ng mga tool ng carbide gamit ang diskarteng ito.
Mga Aplikasyon ng Electrical Discharge Machining:
Paggawa ng prototype:
Ginagamit namin ang proseso ng EDM sa paggawa ng amag, paggawa ng tool at die, gayundin sa paggawa ng prototype at mga bahagi ng produksyon, lalo na para sa mga industriya ng aerospace, sasakyan at electronics kung saan medyo mababa ang dami ng produksyon. Sa Sinker EDM, ang isang grapayt, tansong tungsten o purong tansong elektrod ay ginagawang makina sa nais (negatibong) hugis at ipinapasok sa workpiece sa dulo ng isang patayong ram.
Paggawa ng coinage die:
Para sa paglikha ng mga dies para sa paggawa ng mga alahas at mga badge sa pamamagitan ng proseso ng coinage (stamping), ang positibong master ay maaaring gawin mula sa sterling silver, dahil (na may naaangkop na mga setting ng makina) ang master ay makabuluhang nabubulok at ginagamit nang isang beses lamang. Ang resultang negatibong die ay pinatigas at ginagamit sa isang drop hammer upang makagawa ng mga naselyohang flat mula sa mga cutout sheet na blangko ng bronze, silver, o low proof na gintong haluang metal. Para sa mga badge, ang mga flat na ito ay maaaring higit pang hubugin sa isang hubog na ibabaw ng isa pang die. Ang ganitong uri ng EDM ay karaniwang ginagawa sa ilalim ng tubig sa isang oil-based na dielectric. Ang tapos na bagay ay maaaring higit pang pinuhin sa pamamagitan ng matigas (salamin) o malambot (pintura) enameling at/o electroplated na may purong ginto o nikel. Ang mas malambot na materyales tulad ng pilak ay maaaring iukit ng kamay bilang isang pagpipino.
Pagbabarena ng Maliit na mga Butas:
Sa aming mga wire-cut EDM machine, gumagamit kami ng small hole drilling EDM para gumawa ng through hole sa isang workpiece kung saan i-thread ang wire para sa wire-cut EDM operation. Ang mga hiwalay na EDM head na partikular para sa small hole drilling ay naka-mount sa aming wire-cut machine na nagpapahintulot sa malalaking hardened plate na matanggal ang mga bahagi mula sa mga ito kung kinakailangan at nang walang pre-drill. Gumagamit din kami ng maliit na butas na EDM upang mag-drill ng mga hanay ng mga butas sa mga gilid ng turbine blades na ginagamit sa mga jet engine. Ang daloy ng gas sa mga maliliit na butas na ito ay nagpapahintulot sa mga makina na gumamit ng mas mataas na temperatura kaysa sa posible. Ang mataas na temperatura, napakatigas, nag-iisang kristal na haluang metal na gawa sa mga blades na ito ay ginagawang napakahirap at imposible pa nga ang maginoo na machining ng mga butas na ito na may mataas na aspect ratio. Ang iba pang mga lugar ng aplikasyon para sa maliit na butas na EDM ay ang paglikha ng mga mikroskopikong orifice para sa mga bahagi ng fuel system. Bukod sa pinagsama-samang EDM head, nag-deploy kami ng stand-alone na small hole drilling EDM machine na may x–y axes sa machine blind o sa pamamagitan ng mga butas. Ang mga EDM drill ay may mga butas na may mahabang brass o copper tube electrode na umiikot sa isang chuck na may tuluy-tuloy na daloy ng distilled o deionized na tubig na dumadaloy sa electrode bilang flushing agent at dielectric. Nagagawa ng ilang small-hole drilling EDM na mag-drill sa 100 mm ng malambot o kahit na tumigas na bakal sa loob ng wala pang 10 segundo. Ang mga butas sa pagitan ng 0.3 mm at 6.1 mm ay maaaring makamit sa operasyong pagbabarena na ito.
Metal disintegration machining:
Mayroon din kaming mga espesyal na EDM machine para sa partikular na layunin ng pag-alis ng mga sirang tool (drill bits o taps) mula sa mga workpiece. Ang prosesong ito ay tinatawag na ''metal disintegration machining''.
Mga Kalamangan at Kahinaan ng Electrical-Discharge Machining:
Ang mga bentahe ng EDM ay kinabibilangan ng machining ng:
- Mga kumplikadong hugis na kung hindi man ay mahirap gawin gamit ang mga kumbensyonal na tool sa paggupit
- Lubhang matigas na materyal sa napakalapit na pagpapahintulot
- Napakaliit na mga piraso ng trabaho kung saan ang mga kumbensyonal na tool sa pagputol ay maaaring makapinsala sa bahagi mula sa labis na presyon ng tool sa pagputol.
- Walang direktang kontak sa pagitan ng tool at work piece. Samakatuwid ang mga maselang seksyon at mahihinang materyales ay maaaring makinang nang walang anumang pagbaluktot.
- Ang isang mahusay na pagtatapos sa ibabaw ay maaaring makuha.
- Ang napakahusay na mga butas ay madaling mabutas.
Kabilang sa mga disadvantages ng EDM ang:
- Ang mabagal na rate ng pag-alis ng materyal.
- Ang karagdagang oras at gastos na ginamit para sa paglikha ng mga electrodes para sa ram/sinker EDM.
- Ang pagpaparami ng mga matutulis na sulok sa workpiece ay mahirap dahil sa pagkasira ng elektrod.
- Mataas ang pagkonsumo ng kuryente.
- Nabuo ang ''Overcut''.
- Ang labis na pagkasira ng tool ay nangyayari sa panahon ng machining.
- Ang mga materyal na hindi konduktibong elektrikal ay maaaring makinabang lamang sa partikular na set-up ng proseso.