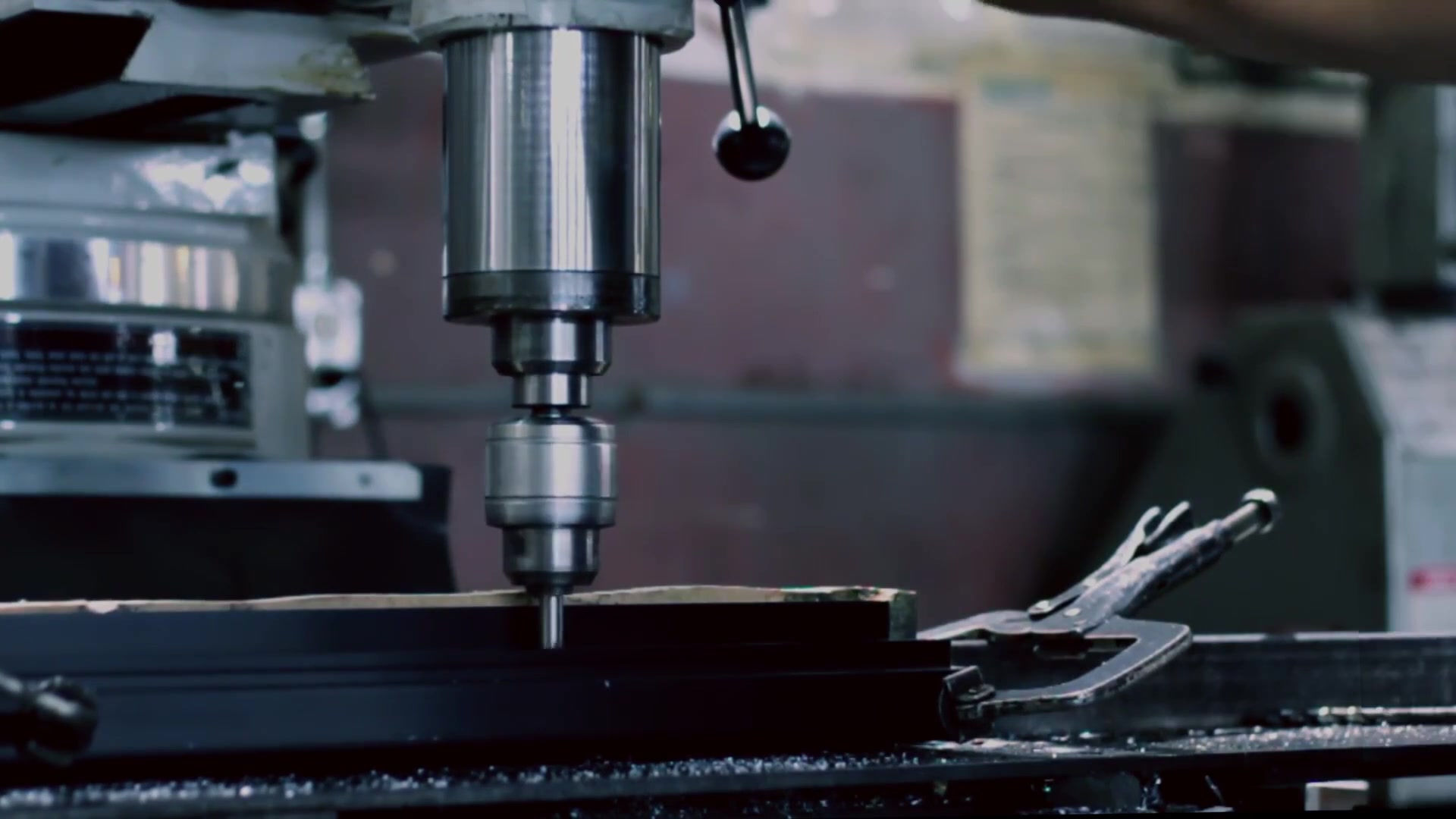
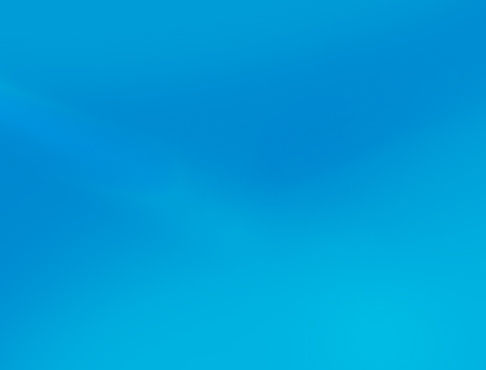
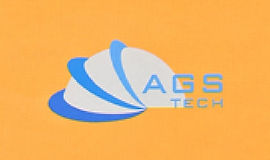
Pandaigdigang Custom na Manufacturer, Integrator, Consolidator, Outsourcing Partner para sa Maraming Iba't Ibang Produkto at Serbisyo.
Kami ang iyong one-stop source para sa pagmamanupaktura, fabrication, engineering, consolidation, integration, outsourcing ng custom na manufactured at off-shelf na mga produkto at serbisyo.
Piliin ang iyong Wika
-
Custom na Paggawa
-
Domestic at Global Contract Manufacturing
-
Paggawa ng Outsourcing
-
Domestic at Global Procurement
-
Consolidation
-
Pagsasama-sama ng Engineering
-
Serbisyong inhinyero
Search Results
164 resulta ang natagpuan na walang laman ng paghahanap
- Joining & Assembly & Fastening Processes, Welding, Brazing, Soldering
Joining & Assembly & Fastening Processes, Welding, Brazing, Soldering, Sintering, Adhesive Bonding, Press Fitting, Wave and Reflow Solder Process, Torch Furnace Mga Proseso ng Pagsali at Pagpupulong at Pangkabit Kami ay sumasali, nag-assemble at nag-fasten ng iyong mga manufactured parts at ginagawa itong mga tapos na o semi-finished na mga produkto gamit ang WELDING, BRAZING, SOLDERING, SINTERING, ADHESIVE BONDING, FASTENING, PRESS FITTING. Ang ilan sa aming pinakasikat na proseso ng welding ay arc, oxyfuel gas, resistance, projection, seam, upset, percussion, solid state, electron beam, laser, thermit, induction welding. Ang aming mga sikat na proseso ng pagpapatigas ay torch, induction, furnace at dip brazing. Ang aming mga paraan ng paghihinang ay iron, hot plate, oven, induction, dip, wave, reflow at ultrasonic soldering. Para sa adhesive bonding, madalas kaming gumagamit ng thermoplastics at thermo-setting, epoxies, phenolics, polyurethane, adhesive alloys pati na rin ang ilang iba pang kemikal at tape. Panghuli ang aming mga proseso ng pangkabit ay binubuo ng pagpapako, pag-stapling, nuts at bolts, riveting, clinching, pinning, stitching at stapling at press fitting. • WELDING : Ang welding ay nagsasangkot ng pagsasama ng mga materyales sa pamamagitan ng pagtunaw ng mga workpiece at pagpasok ng mga filler materials, na sumasali rin sa molten weld pool. Kapag lumamig ang lugar, nakakakuha tayo ng matibay na dugtungan. Ang presyon ay inilalapat sa ilang mga kaso. Taliwas sa hinang, ang pagpapatigas ng pagpapatigas at paghihinang ay kinabibilangan lamang ng pagtunaw ng isang materyal na may mas mababang punto ng pagkatunaw sa pagitan ng mga workpiece, at ang mga workpiece ay hindi natutunaw. Inirerekomenda namin na mag-click ka dito upangI-DOWNLOAD ang aming Schematic Illustrations ng Welding Processes ng AGS-TECH Inc. Makakatulong ito sa iyo na mas maunawaan ang impormasyong ibinibigay namin sa iyo sa ibaba. Sa ARC WELDING, gumagamit kami ng power supply at electrode para lumikha ng electric arc na tumutunaw sa mga metal. Ang welding point ay protektado ng isang shielding gas o singaw o iba pang materyal. Ang prosesong ito ay sikat para sa hinang mga bahagi ng automotive at mga istrukturang bakal. Sa shelded metal arc welding (SMAW) o kilala rin bilang stick welding, ang isang electrode stick ay inilapit sa base material at isang electric arc ang nabuo sa pagitan ng mga ito. Ang electrode rod ay natutunaw at nagsisilbing filler material. Ang electrode ay naglalaman din ng flux na nagsisilbing layer ng slag at nagbibigay ng mga singaw na nagsisilbing shielding gas. Pinoprotektahan ng mga ito ang lugar ng hinang mula sa kontaminasyon sa kapaligiran. Walang ibang mga filler ang ginagamit. Ang mga disadvantages ng prosesong ito ay ang kabagalan nito, kailangang palitan ang mga electrodes nang madalas, ang pangangailangan na alisin ang natitirang slag na nagmumula sa pagkilos ng bagay. Ang isang bilang ng mga metal tulad ng bakal, bakal, nikel, aluminyo, tanso...atbp. Maaaring welded. Ang mga bentahe nito ay ang murang mga tool at kadalian ng paggamit. Gas metal arc welding (GMAW) na kilala rin bilang metal-inert gas (MIG), mayroon kaming tuluy-tuloy na pagpapakain ng consumable electrode wire filler at isang inert o bahagyang inert na gas na dumadaloy sa paligid ng wire laban sa kontaminasyon sa kapaligiran ng weld region. Maaaring welded ang bakal, aluminyo at iba pang non-ferrous na metal. Ang mga bentahe ng MIG ay mataas na bilis ng hinang at magandang kalidad. Ang mga disadvantage nito ay ang mga kumplikadong kagamitan at mga hamon na kinakaharap sa mahangin na panlabas na kapaligiran dahil kailangan nating panatilihing matatag ang shielding gas sa paligid ng welding area. Ang isang variation ng GMAW ay flux-cored arc welding (FCAW) na binubuo ng isang pinong metal tube na puno ng mga flux na materyales. Minsan ang pagkilos ng bagay sa loob ng tubo ay sapat para sa proteksyon mula sa kontaminasyon sa kapaligiran. Ang Submerged Arc Welding (SAW) ay malawakang isang automated na proseso, nagsasangkot ng tuloy-tuloy na wire feeding at arc na hinampas sa ilalim ng isang layer ng flux cover. Ang mga rate at kalidad ng produksyon ay mataas, ang welding slag ay madaling natanggal, at mayroon kaming walang usok na kapaligiran sa trabaho. Ang kawalan ay magagamit lamang ito sa pagwelding ng parts sa ilang partikular na posisyon. Sa gas tungsten arc welding (GTAW) o tungsten-inert gas welding (TIG) gumagamit kami ng Tungsten electrode kasama ang isang hiwalay na filler at inert o malapit sa mga inert na gas. Tulad ng alam natin, ang Tungsten ay may mataas na punto ng pagkatunaw at ito ay isang napaka-angkop na metal para sa napakataas na temperatura. Ang Tungsten sa TIG ay hindi natupok salungat sa iba pang mga pamamaraan na ipinaliwanag sa itaas. Isang mabagal ngunit isang mataas na kalidad na pamamaraan ng hinang na kapaki-pakinabang sa iba pang mga pamamaraan sa hinang ng mga manipis na materyales. Angkop para sa maraming mga metal. Ang plasma arc welding ay magkatulad ngunit gumagamit ng plasma gas upang lumikha ng arko. Ang arc sa plasma arc welding ay medyo mas puro kumpara sa GTAW at maaaring gamitin para sa mas malawak na hanay ng mga kapal ng metal sa mas mataas na bilis. Ang GTAW at plasma arc welding ay maaaring ilapat sa higit pa o mas kaunting parehong mga materyales. Ang OXY-FUEL / OXYFUEL WELDING na tinatawag ding oxyacetylene welding, oxy welding, gas welding ay isinasagawa gamit ang mga gas fuel at oxygen para sa welding. Dahil walang electric power na ginagamit ito ay portable at maaaring gamitin kung saan walang kuryente. Gamit ang welding torch, pinapainit namin ang mga piraso at ang filler material para makagawa ng shared molten metal pool. Maaaring gamitin ang iba't ibang panggatong tulad ng acetylene, gasolina, hydrogen, propane, butane...atbp. Sa oxy-fuel welding gumagamit kami ng dalawang lalagyan, isa para sa gasolina at isa para sa oxygen. Ang oxygen ay nag-oxidize sa gasolina (sinusunog ito). RESISTANCE WELDING: Sinasamantala ng ganitong uri ng welding ang pag-init ng joule at nabubuo ang init sa lokasyon kung saan inilalapat ang electric current sa isang tiyak na oras. Ang mga matataas na alon ay dumaan sa metal. Ang mga pool ng tinunaw na metal ay nabuo sa lokasyong ito. Ang mga pamamaraan ng paglaban sa hinang ay popular dahil sa kanilang kahusayan, maliit na potensyal ng polusyon. Gayunpaman, ang mga kawalan ay ang mga gastos sa kagamitan na medyo makabuluhan at ang likas na limitasyon sa medyo manipis na mga piraso ng trabaho. Ang SPOT WELDING ay isang pangunahing uri ng resistance welding. Dito pinagsasama namin ang dalawa o higit pang magkakapatong na mga sheet o mga piraso ng trabaho sa pamamagitan ng paggamit ng dalawang tansong electrodes upang i-clamp ang mga sheet nang magkasama at magpasa ng isang mataas na kasalukuyang sa pamamagitan ng mga ito. Ang materyal sa pagitan ng mga electrodes na tanso ay umiinit at ang isang molten pool ay nabuo sa lokasyong iyon. Ang kasalukuyang ay huminto at ang mga tip ng tansong elektrod ay nagpapalamig sa lokasyon ng hinang dahil ang mga electrodes ay pinalamig ng tubig. Ang paglalapat ng tamang dami ng init sa tamang materyal at kapal ay susi para sa pamamaraang ito, dahil kung mali ang pagkakalapat ay magiging mahina ang kasukasuan. Ang spot welding ay may mga pakinabang na magdulot ng walang makabuluhang pagpapapangit sa mga workpiece, kahusayan sa enerhiya, kadalian ng automation at natitirang mga rate ng produksyon, at hindi nangangailangan ng anumang mga filler. Ang kawalan ay dahil ang welding ay nagaganap sa mga spot kaysa sa pagbuo ng tuloy-tuloy na tahi, ang kabuuang lakas ay maaaring medyo mas mababa kumpara sa iba pang mga pamamaraan ng welding. Ang SEAM WELDING sa kabilang banda ay gumagawa ng mga welds sa faying surface ng mga katulad na materyales. Ang tahi ay maaaring maging butt o overlap joint. Nagsisimula ang seam welding sa isang dulo at unti-unting gumagalaw sa kabilang dulo. Gumagamit din ang pamamaraang ito ng dalawang electrodes mula sa tanso upang ilapat ang presyon at kasalukuyang sa rehiyon ng hinang. Ang mga electrodes na hugis disc ay umiikot na may patuloy na pakikipag-ugnay sa linya ng tahi at gumagawa ng tuluy-tuloy na hinang. Dito rin, ang mga electrodes ay pinalamig ng tubig. Ang mga welds ay napakalakas at maaasahan. Ang iba pang mga pamamaraan ay projection, flash at upset welding techniques. Ang SOLID-STATE WELDING ay medyo naiiba kaysa sa mga naunang pamamaraan na ipinaliwanag sa itaas. Nagaganap ang coalescence sa mga temperaturang mas mababa sa temperatura ng pagkatunaw ng mga metal na pinagsama at walang paggamit ng metal filler. Maaaring gamitin ang presyon sa ilang proseso. Ang iba't ibang paraan ay ang COEXTRUSION WELDING kung saan ang mga di-magkatulad na metal ay na-extruded sa pamamagitan ng parehong die, COLD PRESSURE WELDING kung saan pinagsasama natin ang mga soft alloys sa ibaba ng kanilang mga melting point, DIFFUSION WELDING isang pamamaraan na walang nakikitang mga weld lines, EXPLOSION WELDING para sa pagsali sa magkaibang mga materyales, eg corrosion resistant alloys sa structural steels, ELECTROMAGNETIC PULSE WELDING kung saan pinapabilis natin ang mga tubo at sheet sa pamamagitan ng electromagnetic forces, FORGE WELDING na binubuo ng pag-init ng mga metal sa mataas na temperatura at pagsasama-sama ng mga ito, FRICTION WELDING kung saan may sapat na friction welding na ginagawa, FRICTION STIR WELDING na kinabibilangan ng rotating non- consumable tool na dumadaan sa magkasanib na linya, HOT PRESSURE WELDING kung saan pinagsasama-sama natin ang mga metal sa matataas na temperatura sa ibaba ng temperatura ng pagkatunaw sa vacuum o inert na mga gas, HOT ISOSTATIC PRESSURE WELDING isang proseso kung saan naglalagay tayo ng pressure gamit ang mga inert gas sa loob ng isang sisidlan, ROLL WELDING kung saan tayo sumasali. hindi magkatulad na mga materyales sa pamamagitan ng pagpilit sa kanila sa pagitan dalawang umiikot na gulong, ULTRASONIC WELDING kung saan hinangin ang manipis na metal o plastic sheet gamit ang high frequency vibrational energy. Ang aming iba pang proseso ng welding ay ang ELECTRON BEAM WELDING na may malalim na pagtagos at mabilis na pagproseso ngunit bilang isang mamahaling pamamaraan ay isinasaalang-alang namin ito para sa mga espesyal na kaso, ang ELECTROSLAG WELDING ay isang pamamaraan na angkop para sa mabibigat na makapal na mga plato at mga piraso ng bakal lamang, INDUCTION WELDING kung saan gumagamit kami ng electromagnetic induction at painitin ang ating electrically conductive o ferromagnetic workpieces, LASER BEAM WELDING din na may malalim na penetration at mabilis na pagproseso ngunit isang mamahaling paraan, LASER HYBRID WELDING na pinagsasama ang LBW sa GMAW sa parehong welding head at may kakayahang mag-bridging gaps ng 2 mm sa pagitan ng mga plate, PERCUSSION WELDING na nagsasangkot ng electric discharge na sinusundan ng pag-forging ng mga materyales na may inilapat na presyon, THERMIT WELDING na kinasasangkutan ng exothermic reaction sa pagitan ng aluminum at iron oxide powders., ELECTROGAS WELDING na may consumable electrodes at ginamit na may lamang bakal sa vertical na posisyon, at panghuli STUD ARC WELDING para sa pagsali sa stud sa base materyal na may init at presyon. Inirerekomenda namin na mag-click ka dito upangI-DOWNLOAD ang aming Schematic Illustrations ng Brazing, Soldering at Adhesive Bonding Processes ng AGS-TECH Inc Makakatulong ito sa iyo na mas maunawaan ang impormasyong ibinibigay namin sa iyo sa ibaba. • BRAZING : Pinagsasama namin ang dalawa o higit pang mga metal sa pamamagitan ng pag-init ng mga filler metal sa pagitan ng mga ito sa itaas ng kanilang mga natutunaw na punto at paggamit ng pagkilos ng capillary upang kumalat. Ang proseso ay katulad ng paghihinang ngunit ang mga temperatura na kasangkot upang matunaw ang tagapuno ay mas mataas sa pagpapatigas. Tulad ng sa welding, pinoprotektahan ng flux ang filler material mula sa atmospheric contamination. Pagkatapos ng paglamig ang mga workpiece ay pinagsama-sama. Ang proseso ay nagsasangkot ng mga sumusunod na pangunahing hakbang: Magandang pagkakasya at clearance, wastong paglilinis ng mga base na materyales, tamang fixturing, tamang flux at pagpili ng kapaligiran, pag-init ng assembly at panghuli ang paglilinis ng brazed assembly. Ang ilan sa aming mga proseso ng pagpapatigas ay TORCH BRAZING, isang tanyag na paraan na isinasagawa nang manu-mano o sa isang automated na paraan. Ito ay angkop para sa mababang dami ng mga order sa produksyon at mga espesyal na kaso. Inilapat ang init gamit ang mga apoy ng gas na malapit sa pinagsamang pinag-brazed. Ang FURNACE BRAZING ay nangangailangan ng mas kaunting kasanayan sa operator at ito ay isang semi-awtomatikong proseso na angkop para sa pang-industriyang mass production. Parehong mga bentahe ng pamamaraang ito ang pagkontrol sa temperatura at kontrol ng atmospera sa hurno, dahil ang una ay nagbibigay-daan sa atin na magkaroon ng kontroladong mga siklo ng init at alisin ang lokal na pag-init gaya ng kaso sa torch brazing, at pinoprotektahan ng huli ang bahagi mula sa oksihenasyon. Gamit ang jigging, nagagawa nating bawasan ang mga gastos sa pagmamanupaktura sa pinakamababa. Ang mga disadvantage ay ang mataas na pagkonsumo ng kuryente, mga gastos sa kagamitan at mas mapaghamong mga pagsasaalang-alang sa disenyo. Nagaganap ang VACUUM BRAZING sa isang furnace ng vacuum. Ang pagkakapareho ng temperatura ay pinananatili at nakakakuha kami ng flux free, napakalinis na joints na may napakakaunting natitirang stress. Maaaring maganap ang mga heat treatment sa panahon ng vacuum brazing, dahil sa mabababang natitirang stress sa panahon ng mabagal na pag-init at paglamig. Ang pangunahing kawalan ay ang mataas na gastos nito dahil ang paglikha ng vacuum na kapaligiran ay isang mamahaling proseso. Ang isa pang diskarteng DIP BRAZING ay sumasali sa mga naka-fix na bahagi kung saan ang brazing compound ay inilalapat sa mga ibabaw ng isinangkot. Pagkatapos nito, ang fixtured na mga bahagi ay isinasawsaw sa isang paliguan ng tinunaw na asin gaya ng Sodium Chloride (table salt) na nagsisilbing heat transfer medium at flux. Ang hangin ay hindi kasama at samakatuwid ay walang oxide formation na nagaganap. Sa INDUCTION BRAZING pinagsasama namin ang mga materyales sa pamamagitan ng isang filler metal na may mas mababang punto ng pagkatunaw kaysa sa mga base na materyales. Ang alternating current mula sa induction coil ay lumilikha ng isang electromagnetic field na nag-uudyok sa induction heating sa karamihan ng mga ferrous magnetic na materyales. Ang pamamaraan ay nagbibigay ng pumipili na pagpainit, magandang joints na may mga filler na dumadaloy lamang sa mga nais na lugar, maliit na oksihenasyon dahil walang apoy at mabilis ang paglamig, mabilis na pag-init, pagkakapare-pareho at pagiging angkop para sa paggawa ng mataas na dami. Upang mapabilis ang aming mga proseso at upang matiyak ang pagkakapare-pareho, madalas kaming gumagamit ng mga preform. Ang impormasyon sa aming brazing facility na gumagawa ng ceramic to metal fittings, hermetic sealing, vacuum feedthroughs, high at ultrahigh vacuum at fluid control components ay matatagpuan dito:_cc781905-5cde-bad5c914-bb_3194Brochure ng Brazing Factory • PAGSOLDER : Sa paghihinang wala kaming natutunaw na mga piraso ng trabaho, ngunit isang metal na tagapuno na may mas mababang punto ng pagkatunaw kaysa sa mga pinagdugtong na bahagi na dumadaloy sa magkasanib na bahagi. Ang metal na tagapuno sa paghihinang ay natutunaw sa mas mababang temperatura kaysa sa pagpapatigas. Gumagamit kami ng mga lead-free alloy para sa paghihinang at may pagsunod sa RoHS at para sa iba't ibang aplikasyon at kinakailangan mayroon kaming iba't ibang at angkop na mga haluang metal tulad ng silver alloy. Ang paghihinang ay nag-aalok sa amin ng mga joint na gas at likido-masikip. Sa SOFT SOLDERING, ang aming filler metal ay may melting point na mas mababa sa 400 Centigrade, samantalang sa SILVER SOLDERING at BRAZING kailangan namin ng mas mataas na temperatura. Ang malambot na paghihinang ay gumagamit ng mas mababang mga temperatura ngunit hindi nagreresulta sa malakas na mga joints para sa hinihingi na mga aplikasyon sa mataas na temperatura. Sa kabilang banda, ang paghihinang ng pilak, ay nangangailangan ng mataas na temperatura na ibinibigay ng sulo at nagbibigay sa amin ng matibay na mga joint na angkop para sa mga aplikasyon ng mataas na temperatura. Ang pagpapatigas ay nangangailangan ng pinakamataas na temperatura at kadalasang sulo ang ginagamit. Dahil ang mga brazing joint ay napakalakas, ang mga ito ay isang mahusay na kandidato para sa pag-aayos ng mabibigat na bagay na bakal. Sa aming mga linya ng pagmamanupaktura ginagamit namin ang parehong manu-manong paghihinang ng kamay pati na rin ang mga awtomatikong linya ng panghinang. Ang INDUCTION SOLDERING ay gumagamit ng high frequency AC current sa isang copper coil upang mapadali ang induction heating. Ang mga agos ay na-induce sa soldered part at bilang resulta, ang init ay nabuo sa mataas na resistensya joint. Ang init na ito ay natutunaw ang filler metal. Ginagamit din ang flux. Ang induction soldering ay isang magandang paraan para sa paghihinang ng mga cyclinder at pipe sa tuluy-tuloy na proseso sa pamamagitan ng pagbabalot ng mga coil sa paligid nila. Ang paghihinang ng ilang mga materyales tulad ng grapayt at ceramics ay mas mahirap dahil nangangailangan ito ng pagkakalupkop ng mga workpiece na may angkop na metal bago ang paghihinang. Pinapadali nito ang interfacial bonding. Ginagawa namin ang paghihinang ng mga naturang materyales lalo na para sa mga aplikasyon ng hermetic packaging. Ginagawa namin ang aming mga naka-print na circuit board (PCB) sa mataas na volume na kadalasang gumagamit ng WAVE SOLDERING. Para lamang sa maliit na dami ng mga layunin ng prototyping ginagamit namin ang hand soldering gamit ang soldering iron. Gumagamit kami ng wave soldering para sa parehong through-hole pati na rin ang surface mount PCB assemblies (PCBA). Ang isang pansamantalang pandikit ay nagpapanatili sa mga bahagi na nakakabit sa circuit board at ang pagpupulong ay inilalagay sa isang conveyor at gumagalaw sa isang kagamitan na naglalaman ng tinunaw na panghinang. Una ang PCB ay fluxed at pagkatapos ay pumasok sa preheating zone. Ang tinunaw na panghinang ay nasa isang kawali at may pattern ng mga nakatayong alon sa ibabaw nito. Kapag ang PCB ay gumagalaw sa mga alon na ito, ang mga alon na ito ay nakikipag-ugnayan sa ilalim ng PCB at dumidikit sa mga soldering pad. Ang panghinang ay nananatili sa mga pin at pad lamang at hindi sa mismong PCB. Ang mga alon sa tinunaw na panghinang ay dapat na mahusay na kontrolado upang walang splashing at ang mga tuktok ng alon ay hindi hawakan at mahawahan ang mga hindi gustong lugar ng mga tabla. Sa REFLOW SOLDERING, gumagamit kami ng sticky solder paste para pansamantalang ikabit ang mga electronic na bahagi sa mga board. Pagkatapos ang mga board ay inilalagay sa isang reflow oven na may kontrol sa temperatura. Dito natutunaw ang panghinang at permanenteng kumokonekta sa mga bahagi. Ginagamit namin ang diskarteng ito para sa parehong surface mount component gayundin para sa through-hole na mga bahagi. Ang wastong pagkontrol sa temperatura at pagsasaayos ng mga temperatura ng oven ay mahalaga upang maiwasan ang pagkasira ng mga elektronikong sangkap sa board sa pamamagitan ng sobrang pag-init sa mga ito nang higit sa kanilang pinakamataas na limitasyon sa temperatura. Sa proseso ng reflow soldering, mayroon talaga kaming ilang rehiyon o yugto bawat isa ay may natatanging thermal profile, tulad ng preheating step, thermal soaking step, reflow at cooling steps. Ang iba't ibang hakbang na ito ay mahalaga para sa isang walang pinsalang reflow na paghihinang ng mga printed circuit board assemblies (PCBA). Ang ULTRASONIC SOLDERING ay isa pang madalas na ginagamit na pamamaraan na may natatanging kakayahan- Maaari itong magamit upang maghinang ng salamin, ceramic at non-metallic na materyales. Halimbawa, ang mga photovoltaic panel na hindi metal ay nangangailangan ng mga electrodes na maaaring ikabit gamit ang pamamaraang ito. Sa ultrasonic na paghihinang, naglalagay kami ng pinainit na tip sa paghihinang na naglalabas din ng mga ultrasonic vibrations. Ang mga vibrations na ito ay gumagawa ng mga bula ng cavitation sa interface ng substrate na may tinunaw na materyal na panghinang. Binabago ng implosive energy ng cavitation ang ibabaw ng oxide at inaalis ang dumi at mga oxide. Sa panahong ito, nabuo din ang isang layer ng haluang metal. Ang panghinang sa ibabaw ng pagbubuklod ay nagsasama ng oxygen at nagbibigay-daan sa pagbuo ng isang malakas na pinagsamang bono sa pagitan ng salamin at panghinang. Ang DIP SOLDERING ay maaaring ituring bilang isang mas simpleng bersyon ng wave soldering na angkop para lamang sa small scale production. Ang unang pagkilos ng paglilinis ay inilapat tulad ng sa iba pang mga proseso. Ang mga PCB na may mga naka-mount na bahagi ay manu-manong inilubog o sa semi-automated na paraan sa isang tangke na naglalaman ng tinunaw na panghinang. Ang tinunaw na panghinang ay dumidikit sa mga nakalantad na metal na lugar na hindi protektado ng solder mask sa pisara. Ang kagamitan ay simple at mura. • ADHESIVE BONDING : Ito ay isa pang tanyag na pamamaraan na madalas naming ginagamit at ito ay nagsasangkot ng pagbubuklod ng mga ibabaw gamit ang mga pandikit, epoxies, plastic na ahente o iba pang mga kemikal. Ang pagbubuklod ay nagagawa sa pamamagitan ng alinman sa pagsingaw ng solvent, sa pamamagitan ng heat curing, sa pamamagitan ng UV light curing, sa pamamagitan ng pressure curing o paghihintay ng isang tiyak na oras. Iba't ibang high performance na pandikit ang ginagamit sa aming mga linya ng produksyon. Sa wastong engineered application at mga proseso ng paggamot, ang adhesive bonding ay maaaring magresulta sa napakababang stress bond na malakas at maaasahan. Ang mga malagkit na bono ay maaaring maging mahusay na mga tagapagtanggol laban sa mga salik sa kapaligiran tulad ng kahalumigmigan, mga contaminant, corrosive, vibration...atbp. Ang mga bentahe ng adhesive bonding ay: maaari silang ilapat sa mga materyales na kung hindi man ay mahirap maghinang, magwelding o mag-braze. Maaari rin itong maging mas mainam para sa mga materyal na sensitibo sa init na masisira ng hinang o iba pang proseso ng mataas na temperatura. Ang iba pang mga bentahe ng mga pandikit ay maaari silang ilapat sa hindi regular na hugis na mga ibabaw at dagdagan ang timbang ng pagpupulong sa pamamagitan ng napakaliit na halaga kapag inihambing sa iba pang mga pamamaraan. Gayundin ang mga pagbabago sa sukat sa mga bahagi ay napakaliit. Ang ilang mga pandikit ay may mga katangian ng pagtutugma ng index at maaaring gamitin sa pagitan ng mga optical na bahagi nang hindi binabawasan nang malaki ang liwanag o lakas ng optical signal. Sa kabilang banda, ang mga disadvantage ay ang mas mahabang panahon ng pagpapagaling na maaaring magpabagal sa mga linya ng pagmamanupaktura, mga kinakailangan sa pagsasaayos, mga kinakailangan sa paghahanda sa ibabaw at kahirapan sa pag-disassemble kapag kailangan ang muling paggawa. Karamihan sa aming mga operasyon ng adhesive bonding ay kinabibilangan ng mga sumusunod na hakbang: -Paggamot sa ibabaw: Pangkaraniwan ang mga espesyal na pamamaraan sa paglilinis gaya ng paglilinis ng deionized na tubig, paglilinis ng alkohol, paglilinis ng plasma o corona. Pagkatapos ng paglilinis maaari naming ilapat ang mga tagapagtaguyod ng adhesion sa mga ibabaw upang matiyak ang pinakamahusay na posibleng mga kasukasuan. -Part Fixturing: Para sa parehong adhesive application pati na rin para sa curing kami ay nagdidisenyo at gumagamit ng custom fixtures. -Adhesive Application: Kung minsan ay gumagamit kami ng manual, at kung minsan ay depende sa kaso ng mga automated system gaya ng robotics, servo motors, linear actuator upang maihatid ang mga adhesive sa tamang lokasyon at gumagamit kami ng mga dispenser para ihatid ito sa tamang volume at dami. -Pagpapagaling: Depende sa pandikit, maaari kaming gumamit ng simpleng pagpapatuyo at pagpapagaling pati na rin ang pagpapagaling sa ilalim ng mga ilaw ng UV na nagsisilbing catalyst o heat curing sa oven o gamit ang resistive heating elements na naka-mount sa mga jig at fixtures. Inirerekomenda namin na mag-click ka dito upangI-DOWNLOAD ang aming Schematic Illustrations ng Fastening Processes ng AGS-TECH Inc. Makakatulong ito sa iyo na mas maunawaan ang impormasyong ibinibigay namin sa iyo sa ibaba. • MGA PROSESO NG FASTENING : Ang aming mga mekanikal na proseso ng pagsali ay nahahati sa dalawang kategorya ng brad: FASTENERS at INTEGRAL JOINTS. Ang mga halimbawa ng mga fastener na ginagamit namin ay mga turnilyo, pin, nuts, bolts, rivets. Ang mga halimbawa ng integral joints na ginagamit namin ay snap and shrink fit, seams, crimps. Gamit ang iba't ibang paraan ng pangkabit, tinitiyak namin na ang aming mga mekanikal na kasukasuan ay malakas at maaasahan para sa maraming taon ng paggamit. Ang mga SCREW at BOLTS ay ilan sa mga karaniwang ginagamit na fastener para sa paghawak ng mga bagay nang magkasama at pagpoposisyon. Ang aming mga turnilyo at bolts ay nakakatugon sa mga pamantayan ng ASME. Ang iba't ibang uri ng mga turnilyo at bolts ay inilalagay kabilang ang mga hex cap screw at hex bolts, lag screws at bolts, double ended screw, dowel screw, eye screw, mirror screw, sheet metal screw, fine adjustment screw, self-drill at self-tapping screws , set screw, turnilyo na may mga built-in na washer,...at higit pa. Mayroon kaming iba't ibang uri ng screw head tulad ng countersunk, dome, round, flanged head at iba't ibang uri ng screw drive tulad ng slot, phillips, square, hex socket. Ang RIVET sa kabilang banda ay isang permanenteng mechanical fastener na binubuo ng isang makinis na cylindirical shaft at isang ulo sa isang banda. Pagkatapos ng pagpasok, ang kabilang dulo ng rivet ay deformed at ang diameter nito ay pinalawak upang ito ay manatili sa lugar. Sa madaling salita, bago ang pag-install ang isang rivet ay may isang ulo at pagkatapos ng pag-install ay mayroon itong dalawa. Nag-i-install kami ng iba't ibang uri ng rivets depende sa application, lakas, accessibility at gastos tulad ng solid/round head rivets, structural, semi-tubular, blind, oscar, drive, flush, friction-lock, self-piercing rivets. Maaaring mas gusto ang riveting sa mga kaso kung saan ang pagpapapangit ng init at pagbabago sa mga katangian ng materyal dahil sa init ng hinang ay kailangang iwasan. Nag-aalok din ang riveting ng magaan na timbang at lalo na ang mahusay na lakas at tibay laban sa mga puwersa ng paggugupit. Laban sa mga tensile load gayunpaman ang mga turnilyo, nuts at bolts ay maaaring mas angkop. Sa proseso ng CLINCHING gumagamit kami ng espesyal na suntok at namatay upang bumuo ng mekanikal na pagkakabit sa pagitan ng mga sheet na metal na pinagsasama. Tinutulak ng suntok ang mga layer ng sheet metal sa die cavity at nagreresulta sa pagbuo ng isang permanenteng joint. Walang pag-init at walang paglamig ang kinakailangan sa pag-clinching at ito ay isang malamig na proseso ng pagtatrabaho. Ito ay isang matipid na proseso na maaaring palitan ang spot welding sa ilang mga kaso. Sa PINNING gumagamit kami ng mga pin na mga elemento ng makina na ginagamit upang ma-secure ang mga posisyon ng mga bahagi ng makina na may kaugnayan sa isa't isa. Ang mga pangunahing uri ay mga clevis pin, cotter pin, spring pin, dowel pin, at split pin. Sa STAPLING gumagamit kami ng mga stapling gun at staples na dalawang-pronged fasteners na ginagamit upang pagdugtungan o pagbigkis ng mga materyales. Ang stapling ay may mga sumusunod na pakinabang: Matipid, simple at mabilis gamitin, ang korona ng mga staple ay maaaring gamitin upang tulay ang mga materyales na pinagdikit-dikit, Ang korona ng staple ay maaaring mapadali ang pag-bridging ng isang piraso tulad ng isang cable at ikabit ito sa isang ibabaw nang hindi nabubutas o nakakasira, medyo madaling tanggalin. Ang PRESS FITTING ay ginagawa sa pamamagitan ng pagtulak ng mga bahagi nang magkasama at ang alitan sa pagitan ng mga ito ay nagpapatibay sa mga bahagi. Ang mga press fit na bahagi na binubuo ng isang napakalaking baras at isang maliit na butas ay karaniwang binuo sa pamamagitan ng isa sa dalawang pamamaraan: Alinman sa pamamagitan ng paglalapat ng puwersa o pagsasamantala sa thermal expansion o contraction ng mga bahagi. Kapag ang isang press fitting ay itinatag sa pamamagitan ng paglalapat ng puwersa, kami ay gumagamit ng hydraulic press o isang hand operated press. Sa kabilang banda, kapag ang press fitting ay itinatag sa pamamagitan ng thermal expansion, pinapainit namin ang mga bahaging nakabalot at iniipon ang mga ito sa kanilang lugar habang mainit. Kapag lumamig sila, kumukontra sila at bumalik sa kanilang normal na sukat. Nagreresulta ito sa isang magandang press fit. Tinatawag namin itong alternatibong SHRINK-FITTING. Ang iba pang paraan ng paggawa nito ay sa pamamagitan ng paglamig sa mga bahaging nakabalot bago ang pagpupulong at pagkatapos ay i-slide ang mga ito sa kanilang mga bahagi ng isinangkot. Kapag uminit ang pagpupulong, lumalawak sila at nakakakuha kami ng mahigpit na pagkakasya. Ang huling pamamaraan na ito ay maaaring maging mas kanais-nais sa mga kaso kung saan ang pag-init ay nagdudulot ng panganib ng pagbabago ng mga katangian ng materyal. Ang paglamig ay mas ligtas sa mga kasong iyon. Mga Bahagi at Assemblies ng Pneumatic at Hydraulic • Mga balbula, hydraulic at pneumatic na bahagi tulad ng O-ring, washer, seal, gasket, ring, shim. Dahil ang mga balbula at mga bahagi ng pneumatic ay may malaking pagkakaiba-iba, hindi namin mailista ang lahat dito. Depende sa pisikal at kemikal na kapaligiran ng iyong aplikasyon, mayroon kaming mga espesyal na produkto para sa iyo. Mangyaring tukuyin sa amin ang aplikasyon, uri ng bahagi, mga detalye, mga kundisyon sa kapaligiran gaya ng presyon, temperatura, likido o gas na makikipag-ugnayan sa iyong mga balbula at mga bahagi ng pneumatic; at pipiliin namin ang pinaka-angkop na produkto para sa iyo o gagawin ito lalo na para sa iyong aplikasyon. CLICK Product Finder-Locator Service NAKARAANG PAHINA
- Composites, Composite Materials Manufacturing, Fiber Reinforced
Composites, Composite Materials Manufacturing, Particle and Fiber Reinforced, Cermets, Ceramic & Metal Composite, Glass Fiber Reinforced Polymer, Lay-Up Process Paggawa ng Composite at Composite Materials Sa madaling kahulugan, ang COMPOSITES o COMPOSITE MATERIALS ay mga materyales na binubuo ng dalawa o maramihang mga materyales na may iba't ibang pisikal o kemikal na katangian, ngunit kapag pinagsama sila ay nagiging isang materyal na naiiba kaysa sa mga sangkap na bumubuo. Kailangan nating ituro na ang mga sangkap na bumubuo ay nananatiling hiwalay at naiiba sa istraktura. Ang layunin sa paggawa ng isang pinagsama-samang materyal ay upang makakuha ng isang produkto na mas mataas kaysa sa mga nasasakupan nito at pinagsasama ang mga nais na katangian ng bawat nasasakupan. Bilang halimbawa; lakas, mababang timbang o mas mababang presyo ay maaaring ang motivator sa likod ng pagdidisenyo at paggawa ng composite. Ang uri ng mga composite na inaalok namin ay particle-reinforced composites, fiber-reinforced composites kabilang ang ceramic-matrix / polymer-matrix / metal-matrix / carbon-carbon / hybrid composites, structural & laminated & sandwich-structured composites at nanocomposites. Ang mga pamamaraan ng fabrication na idini-deploy namin sa composite material manufacturing ay: Pultrusion, prepreg production process, advanced fiber placement, filament winding, tailored fiber placement, fiberglass spray lay-up process, tufting, lanxide process, z-pinning. Maraming mga pinagsama-samang materyales ang binubuo ng dalawang yugto, ang matris, na tuluy-tuloy at pumapalibot sa kabilang yugto; at ang dispersed phase na napapalibutan ng matrix. Inirerekomenda namin na mag-click ka dito upangI-DOWNLOAD ang aming Schematic Illustrations ng Composites at Composite Materials Manufacturing ng AGS-TECH Inc. Makakatulong ito sa iyo na mas maunawaan ang impormasyong ibinibigay namin sa iyo sa ibaba. • PARTICLE-REINFORCED COMPOSITES : Ang kategoryang ito ay binubuo ng dalawang uri: Malaking particle composites at dispersion-strengthened composites. Sa dating uri, ang mga pakikipag-ugnayan ng particle-matrix ay hindi maaaring ituring sa atomic o molekular na antas. Sa halip ay may bisa ang continuum mechanics. Sa kabilang banda, sa dispersion-strengthened composites particle ay karaniwang mas maliit sa sampu-sampung mga hanay ng nanometer. Ang isang halimbawa ng malaking particle composite ay polymers kung saan ang mga filler ay idinagdag. Pinapabuti ng mga tagapuno ang mga katangian ng materyal at maaaring palitan ang ilan sa dami ng polimer ng mas matipid na materyal. Ang mga fraction ng volume ng dalawang phase ay nakakaimpluwensya sa pag-uugali ng composite. Ang malalaking particle composites ay ginagamit sa mga metal, polimer at keramika. Ang CERMETS ay mga halimbawa ng ceramic / metal composites. Ang aming pinakakaraniwang cermet ay cemented carbide. Binubuo ito ng refractory carbide ceramic tulad ng mga particle ng tungsten carbide sa isang matrix ng isang metal tulad ng cobalt o nickel. Ang mga carbide composite na ito ay malawakang ginagamit bilang mga tool sa pagputol para sa tumigas na bakal. Ang mga hard carbide particle ay may pananagutan para sa pagkilos ng pagputol at ang kanilang katigasan ay pinahusay ng ductile metal matrix. Kaya nakuha namin ang mga pakinabang ng parehong mga materyales sa isang solong composite. Ang isa pang karaniwang halimbawa ng malaking particle composite na ginagamit namin ay ang carbon black particulates na hinaluan ng vulcanized rubber upang makakuha ng composite na may mataas na tensile strength, toughness, luha at abrasion resistance. Ang isang halimbawa ng isang dispersion-strengthened composite ay ang mga metal at metal na haluang metal na pinalakas at pinatigas ng pare-parehong pagpapakalat ng mga pinong particle ng isang napakatigas at hindi gumagalaw na materyal. Kapag ang napakaliit na aluminum oxide flakes ay idinagdag sa aluminum metal matrix nakakakuha tayo ng sintered aluminum powder na may pinahusay na lakas ng mataas na temperatura. • FIBER-REINFORCED COMPOSITES : Ang kategoryang ito ng mga composite ay sa katunayan ang pinakamahalaga. Ang layunin na makamit ay ang mataas na lakas at higpit sa bawat yunit ng timbang. Ang komposisyon ng hibla, haba, oryentasyon at konsentrasyon sa mga composite na ito ay kritikal sa pagtukoy ng mga katangian at pagiging kapaki-pakinabang ng mga materyales na ito. May tatlong grupo ng mga hibla na ginagamit namin: whisker, fibers at wires. WHISKERS ay napakanipis at mahahabang solong kristal. Kabilang sila sa pinakamatibay na materyales. Ang ilang halimbawa ng mga materyales ng whisker ay grapayt, silikon nitride, aluminyo oksido. FIBERS sa kabilang banda ay karamihan sa mga polymer o ceramics at nasa polycrystalline o amorphous na estado. Ang pangatlong grupo ay pinong mga WIRES na may medyo malalaking diameters at kadalasang binubuo ng bakal o tungsten. Ang isang halimbawa ng wire reinforced composite ay ang mga gulong ng kotse na may kasamang steel wire sa loob ng goma. Depende sa materyal ng matrix, mayroon kaming mga sumusunod na composite: POLYMER-MATRIX COMPOSITES : Ang mga ito ay gawa sa polymer resin at fibers bilang reinforcement ingredient. Ang isang subgroup ng mga ito na tinatawag na Glass Fiber-Reinforced Polymer (GFRP) Composites ay naglalaman ng tuluy-tuloy o discontinuous glass fibers sa loob ng isang polymer matrix. Ang salamin ay nag-aalok ng mataas na lakas, ito ay matipid, madaling gawan ng mga hibla, at hindi chemically inert. Ang mga disadvantages ay ang kanilang limitadong higpit at higpit, ang mga temperatura ng serbisyo ay hanggang 200 – 300 Centigrade lamang. Ang Fiberglass ay angkop para sa mga automotive body at mga kagamitan sa transportasyon, marine vehicle body, storage container. Ang mga ito ay hindi angkop para sa aerospace o paggawa ng tulay dahil sa limitadong tigas. Ang ibang subgroup ay tinatawag na Carbon Fiber-Reinforced Polymer (CFRP) Composite. Dito, ang carbon ang aming fiber material sa polymer matrix. Ang Carbon ay kilala sa mataas na tiyak na modulus at lakas nito at ang kakayahan nitong mapanatili ang mga ito sa mataas na temperatura. Ang mga carbon fiber ay maaaring mag-alok sa amin ng standard, intermediate, high at ultrahigh tensile moduli. Higit pa rito, ang mga carbon fiber ay nag-aalok ng magkakaibang pisikal at mekanikal na katangian at samakatuwid ay angkop para sa iba't ibang custom na iniayon sa mga aplikasyon ng engineering. Maaaring isaalang-alang ang mga composite ng CFRP upang gumawa ng mga kagamitang pang-sports at recreational, mga pressure vessel at mga bahagi ng istruktura ng aerospace. Gayunpaman, ang isa pang subgroup, ang Aramid Fiber-Reinforced Polymer Composites ay mga high-strength at modulus na materyales din. Ang kanilang mga ratio ng lakas sa timbang ay napakataas. Ang Aramid fibers ay kilala rin sa mga trade name na KEVLAR at NOMEX. Sa ilalim ng pag-igting sila ay gumaganap ng mas mahusay kaysa sa iba pang mga polymeric fiber na materyales, ngunit sila ay mahina sa compression. Ang mga hibla ng Aramid ay matigas, lumalaban sa epekto, lumalaban sa kilabot at nakakapagod, matatag sa mataas na temperatura, hindi gumagalaw sa kemikal maliban sa mga malakas na acid at base. Ang mga hibla ng Aramid ay malawakang ginagamit sa mga gamit pang-sports, bulletproof vests, gulong, lubid, fiber optic cable sheat. Ang iba pang mga fiber reinforcement materials ay umiiral ngunit ginagamit sa mas mababang antas. Ang mga ito ay boron, silikon karbid, aluminyo oksido pangunahin. Ang materyal na polymer matrix sa kabilang banda ay kritikal din. Tinutukoy nito ang pinakamataas na temperatura ng serbisyo ng composite dahil ang polimer ay karaniwang may mas mababang temperatura ng pagkatunaw at pagkasira. Ang mga polyester at vinyl ester ay malawakang ginagamit bilang polymer matrix. Ginagamit din ang mga resin at mayroon silang mahusay na moisture resistance at mekanikal na mga katangian. Halimbawa polyimide resin ay maaaring gamitin hanggang sa humigit-kumulang 230 Degrees Celcius. METAL-MATRIX COMPOSITES : Sa mga materyales na ito ay gumagamit kami ng ductile metal matrix at ang mga temperatura ng serbisyo ay karaniwang mas mataas kaysa sa kanilang mga bumubuong bahagi. Kung ihahambing sa polymer-matrix composites, ang mga ito ay maaaring magkaroon ng mas mataas na operating temperature, maging nonflammable, at maaaring magkaroon ng mas mahusay na degradation resitance laban sa mga organic na likido. Gayunpaman, mas mahal ang mga ito. Mga materyales na pampalakas tulad ng whisker, particulates, tuluy-tuloy at hindi tuloy-tuloy na mga hibla; at mga materyales sa matrix tulad ng tanso, aluminyo, magnesiyo, titanium, superalloys ay karaniwang ginagamit. Ang mga halimbawang aplikasyon ay ang mga bahagi ng makina na gawa sa aluminum alloy matrix na pinalakas ng aluminum oxide at carbon fibers. CERAMIC-MATRIX COMPOSITES : Ang mga ceramic na materyales ay kilala sa kanilang napakahusay na pagiging maaasahan sa mataas na temperatura. Gayunpaman ang mga ito ay masyadong malutong at may mababang halaga para sa pagiging matigas ng bali. Sa pamamagitan ng pag-embed ng mga particulate, fibers o whisker ng isang ceramic sa matrix ng isa pa, nakakamit natin ang mga composite na may mas mataas na tibay ng bali. Ang mga naka-embed na materyales na ito ay karaniwang humahadlang sa pagpapalaganap ng crack sa loob ng matrix sa pamamagitan ng ilang mga mekanismo tulad ng pagpapalihis sa mga tip ng crack o pagbuo ng mga tulay sa mga mukha ng crack. Bilang halimbawa, ang mga alumina na pinalalakas ng mga whisker ng SiC ay ginagamit bilang mga pagsingit ng tool sa paggupit para sa paggawa ng mga hard metal na haluang metal. Ang mga ito ay maaaring magpakita ng mas mahusay na pagganap kumpara sa mga sementadong karbida. CARBON-CARBON COMPOSITES : Parehong carbon ang reinforcement pati na rin ang matrix. Mayroon silang mataas na tensile moduli at mga lakas sa mataas na temperatura na higit sa 2000 Centigrade, creep resistance, mataas na fracture toughnesses, mababang thermal expansion coefficients, mataas na thermal conductivity. Ginagawang perpekto ng mga katangiang ito para sa mga application na nangangailangan ng thermal shock resistance. Ang kahinaan ng carbon-carbon composites ay gayunpaman ang kahinaan nito laban sa oksihenasyon sa mataas na temperatura. Ang mga karaniwang halimbawa ng paggamit ay ang mga hot-pressing molds, advanced na paggawa ng mga bahagi ng turbine engine. HYBRID COMPOSITES : Dalawa o higit pang iba't ibang uri ng fibers ang pinaghalo sa iisang matrix. Kaya ang isa ay maaaring maiangkop ang isang bagong materyal na may kumbinasyon ng mga katangian. Ang isang halimbawa ay kapag ang parehong carbon at glass fibers ay isinama sa isang polymeric resin. Ang mga carbon fiber ay nagbibigay ng mababang densidad na higpit at lakas ngunit mahal. Ang salamin sa kabilang banda ay mura ngunit kulang sa higpit ng carbon fibers. Ang glass-carbon hybrid composite ay mas malakas at mas matigas at maaaring gawin sa mas mababang halaga. PAGPROSESO NG FIBER-REINFORCED COMPOSITES : Para sa tuluy-tuloy na fiber-reinforced na plastik na may pantay na distributed fibers na nakatuon sa parehong direksyon ginagamit namin ang mga sumusunod na pamamaraan. PULTRUSION: Ang mga rod, beam at tube na may tuluy-tuloy na haba at pare-pareho ang mga cross-section ay ginawa. Ang tuluy-tuloy na fiber roving ay pinapagbinhi ng isang thermosetting resin at hinihila sa isang bakal na die upang maporma ang mga ito sa nais na hugis. Susunod, dumaan sila sa isang precision machined curing die upang makuha ang huling hugis nito. Dahil pinainit ang curing die, pinapagaling nito ang resin matrix. Ang mga pullers ay gumuhit ng materyal sa pamamagitan ng mga dies. Gamit ang mga nakapasok na hollow core, nakakakuha kami ng mga tubo at hollow geometries. Ang paraan ng pultrusion ay awtomatiko at nag-aalok sa amin ng mataas na rate ng produksyon. Anumang haba ng produkto ay posibleng gawin. PREPREG PROCESSION PROCESS : Ang Prepreg ay isang tuluy-tuloy na fiber reinforcement na preimpregnated na may partially cured polymer resin. Ito ay malawakang ginagamit para sa mga istrukturang aplikasyon. Ang materyal ay dumating sa tape form at ipinadala bilang isang tape. Direkta itong hinuhubog ng tagagawa at ganap na nilulunasan ito nang hindi na kailangang magdagdag ng anumang dagta. Dahil ang mga prepreg ay sumasailalim sa mga reaksyon sa pagpapagaling sa temperatura ng silid, sila ay nakaimbak sa 0 Centigrade o mas mababang temperatura. Pagkatapos gamitin ang natitirang mga teyp ay iniimbak pabalik sa mababang temperatura. Ang mga thermoplastic at thermosetting resin ay ginagamit at ang mga reinforcement fibers ng carbon, aramid at salamin ay karaniwan. Upang gumamit ng prepreg, ang carrier backing paper ay unang aalisin at pagkatapos ay ang paggawa ay isinasagawa sa pamamagitan ng paglalagay ng prepreg tape sa isang tool na ibabaw (ang proseso ng lay-up). Ang ilang mga plies ay maaaring ilagay upang makuha ang nais na kapal. Ang madalas na pagsasanay ay ang paghalili ng hibla na oryentasyon upang makabuo ng cross-ply o angle-ply laminate. Sa wakas, inilapat ang init at presyon para sa paggamot. Ang parehong pagproseso ng kamay at pati na rin ang mga awtomatikong proseso ay ginagamit para sa pagputol ng mga prepregs at lay-up. FILAMENT WINDING : Ang tuluy-tuloy na reinforcing fibers ay tumpak na nakaposisyon sa isang paunang natukoy na pattern upang sundin ang isang guwang na at karaniwang cyclindirical na hugis. Ang mga hibla ay unang dumaan sa isang resin bath at pagkatapos ay nasugatan sa isang mandrel ng isang automated system. Pagkatapos ng ilang paikot-ikot na pag-uulit ay nakuha ang ninanais na mga kapal at ang paggamot ay isinasagawa alinman sa temperatura ng silid o sa loob ng oven. Ngayon ang mandrel ay tinanggal at ang produkto ay demolded. Ang filament winding ay maaaring mag-alok ng napakataas na strength-to-weight ratios sa pamamagitan ng winding ng fibers sa circumferential, helical at polar patterns. Ang mga tubo, tangke, casing ay ginawa gamit ang pamamaraang ito. • STRUCTURAL COMPOSITES : Kadalasan ang mga ito ay binubuo ng parehong homogenous at composite na mga materyales. Samakatuwid ang mga katangian ng mga ito ay natutukoy sa pamamagitan ng mga constituent na materyales at geometrical na disenyo ng mga elemento nito. Narito ang mga pangunahing uri: LAMINAR COMPOSITES : Ang mga istrukturang materyales na ito ay gawa sa dalawang dimensyong sheet o panel na may gustong mga direksyon na may mataas na lakas. Ang mga layer ay nakasalansan at pinagsasama-sama. Sa pamamagitan ng pagpapalit ng mga direksyon na may mataas na lakas sa dalawang perpendicular axes, nakakakuha kami ng isang composite na may mataas na lakas sa parehong direksyon sa two-dimensional na eroplano. Sa pamamagitan ng pagsasaayos ng mga anggulo ng mga layer ay maaaring gumawa ng isang composite na may lakas sa mga gustong direksyon. Ginagawa ang modernong ski sa ganitong paraan. MGA SANDWICH PANELS : Ang mga structural composite na ito ay magaan ngunit may mataas na higpit at lakas. Ang mga sandwich panel ay binubuo ng dalawang panlabas na sheet na gawa sa isang matigas at matibay na materyal tulad ng mga aluminyo na haluang metal, fiber reinforced plastic o bakal at isang core sa pagitan ng mga panlabas na sheet. Kailangang magaan ang core at kadalasan ay may mababang modulus of elasticity. Ang mga sikat na pangunahing materyales ay matibay na polymeric foams, kahoy at pulot-pukyutan. Ang mga sandwich panel ay malawakang ginagamit sa industriya ng konstruksiyon bilang materyales sa bubong, materyal sa sahig o dingding, at gayundin sa mga industriya ng aerospace. • NANOCOMPOSITES : Ang mga bagong materyales na ito ay binubuo ng mga nanosized na particle na mga particle na naka-embed sa isang matrix. Gamit ang mga nanocomposite maaari tayong gumawa ng mga materyales ng goma na napakahusay na hadlang sa pagtagos ng hangin habang pinapanatili ang kanilang mga katangian ng goma na hindi nagbabago. CLICK Product Finder-Locator Service NAKARAANG PAHINA
- Rapid Prototyping, Desktop Manufacturing, Additive Manufacturing, FDM
Rapid Prototyping, Desktop Manufacturing, Additive Manufacturing, Stereolithography, Polyjet, Fused Deposition Modeling, Selective Laser Sintering, FDM, SLS Additive at Mabilis na Paggawa Sa mga nakalipas na taon, nakita natin ang pagtaas ng demand para sa RAPID MANUFACTURING o RAPID PROTOTYPING. Ang prosesong ito ay maaari ding tawaging DESKTOP MANUFACTURING o FREE-FORM FABRICATION. Karaniwang isang solidong pisikal na modelo ng isang bahagi ay direktang ginawa mula sa isang three-dimensional na pagguhit ng CAD. Ginagamit namin ang terminong ADDITIVE MANUFACTURING para sa iba't ibang pamamaraan na ito kung saan gumagawa kami ng mga bahagi sa mga layer. Gamit ang pinagsama-samang computer-driven na hardware at software nagsasagawa kami ng additive manufacturing. Ang aming mabilis na prototyping at mga diskarte sa pagmamanupaktura ay STEREOLITHOGRAPHY, POLYJET, FUSED-DEPOSITION MODELING, SELECTIVE LASER SINTERING, ELECTRON BEAM MELTING, THREE-DIMENSIONAL PRINTING, DIRECT MANUFACTURING, RAPID TOOLING. Inirerekomenda namin na mag-click ka dito upangI-DOWNLOAD ang aming Schematic Illustrations ng Additive Manufacturing at Rapid Manufacturing Processes ng AGS-TECH Inc. Makakatulong ito sa iyo na mas maunawaan ang impormasyong ibinibigay namin sa iyo sa ibaba. Ang mabilis na prototyping ay nagbibigay sa amin ng: 1.) Ang konseptwal na disenyo ng produkto ay tinitingnan mula sa iba't ibang anggulo sa isang monitor gamit ang isang 3D / CAD system. 2.) Ang mga prototype mula sa nonmetallic at metallic na materyales ay ginawa at pinag-aaralan mula sa functional, teknikal at aesthetic na aspeto. 3.) Ang mababang gastos na prototyping sa napakaikling panahon ay nagagawa. Ang additive na pagmamanupaktura ay maaaring maitutulad sa paggawa ng isang tinapay sa pamamagitan ng pagsasalansan at pagbubuklod ng mga indibidwal na hiwa sa ibabaw ng bawat isa. Sa madaling salita, ang produkto ay ginawa ng hiwa-hiwa, o patong-patong na idineposito sa isa't isa. Karamihan sa mga bahagi ay maaaring gawin sa loob ng ilang oras. Ang pamamaraan ay mabuti kung ang mga bahagi ay kailangan nang napakabilis o kung ang dami ng kailangan ay mababa at ang paggawa ng amag at kasangkapan ay masyadong mahal at tumatagal ng oras. Gayunpaman ang halaga ng isang bahagi ay mahal dahil sa mamahaling hilaw na materyales. • STEREOLITHOGRAPHY : Ang pamamaraan na ito ay dinaglat din bilang STL, ay batay sa paggamot at pagpapatigas ng isang likidong photopolymer sa isang tiyak na hugis sa pamamagitan ng pagtutok ng isang laser beam dito. Pina-polymerize ng laser ang photopolymer at pinapagaling ito. Sa pamamagitan ng pag-scan sa UV laser beam ayon sa naka-program na hugis kasama ang ibabaw ng pinaghalong photopolymer ang bahagi ay ginawa mula sa ibaba pataas sa mga indibidwal na hiwa na naka-cascade sa ibabaw ng bawat isa. Ang pag-scan ng laser spot ay paulit-ulit nang maraming beses upang makamit ang mga geometry na naka-program sa system. Matapos ang bahagi ay ganap na ginawa, ito ay inalis mula sa platform, i-blotter at linisin ang ultrasonically at may alkohol na paliguan. Susunod, ito ay nakalantad sa UV irradiation sa loob ng ilang oras upang matiyak na ang polimer ay ganap na gumaling at tumigas. Upang ibuod ang proseso, ang isang platform na inilubog sa isang pinaghalong photopolymer at isang UV laser beam ay kinokontrol at inilipat sa pamamagitan ng isang servo-control system ayon sa hugis ng nais na bahagi at ang bahagi ay nakuha sa pamamagitan ng photocuring ng polymer layer sa pamamagitan ng layer. Siyempre, ang pinakamataas na sukat ng ginawang bahagi ay tinutukoy ng stereolithography equipment. • POLYJET : Katulad ng inkjet printing, sa polyjet mayroon kaming walong print head na nagdedeposito ng photopolymer sa build tray. Ang ultraviolet light na inilagay sa tabi ng mga jet ay agad na nagpapagaling at nagpapatigas sa bawat layer. Dalawang materyales ang ginagamit sa polyjet. Ang unang materyal ay para sa paggawa ng aktwal na modelo. Ang pangalawang materyal, isang gel-like resin ay ginagamit para sa suporta. Ang parehong mga materyales na ito ay idineposito sa bawat layer at sabay-sabay na gumaling. Pagkatapos ng pagkumpleto ng modelo, ang materyal ng suporta ay aalisin gamit ang isang may tubig na solusyon. Ang mga resin na ginamit ay katulad ng stereolithography (STL). Ang polyjet ay may mga sumusunod na pakinabang kaysa sa stereolithography: 1.) Hindi na kailangan para sa paglilinis ng mga bahagi. 2.) Hindi na kailangan para sa postprocess curing. • FUSED DEPOSITION MODELING : Dinaglat din bilang FDM, sa paraang ito ang isang ulo ng extruder na kontrolado ng robot ay gumagalaw sa dalawang prinsipyong direksyon sa ibabaw ng isang talahanayan. Ang cable ay ibinababa at itinaas kung kinakailangan. Mula sa orifice ng isang pinainit na die sa ulo, isang thermoplastic filament ay pinalabas at isang paunang layer ay idineposito sa isang foam foundation. Ito ay nagagawa ng extruder head na sumusunod sa isang paunang natukoy na landas. Pagkatapos ng paunang layer, ang talahanayan ay ibinababa at ang kasunod na mga layer ay idineposito sa ibabaw ng bawat isa. Minsan kapag gumagawa ng masalimuot na bahagi, kailangan ang mga istrukturang pangsuporta upang magpatuloy ang deposition sa ilang partikular na direksyon. Sa mga kasong ito, ang isang materyal na pangsuporta ay pinalalabas na may hindi gaanong siksik na espasyo ng filament sa isang layer upang ito ay mas mahina kaysa sa materyal na modelo. Ang mga istrukturang ito ng suporta ay maaaring matunaw o maputol pagkatapos makumpleto ang bahagi. Tinutukoy ng mga sukat ng extruder die ang kapal ng mga extruded na layer. Ang proseso ng FDM ay gumagawa ng mga bahagi na may mga stepped na ibabaw sa mga pahilig na panlabas na eroplano. Kung ang pagkamagaspang na ito ay hindi katanggap-tanggap, maaaring gamitin ang chemical vapor polishing o isang pinainit na tool para sa pagpapakinis ng mga ito. Kahit na ang isang polishing wax ay magagamit bilang isang materyal na patong upang maalis ang mga hakbang na ito at makamit ang mga makatwirang geometric tolerance. • SELECTIVE LASER SINTERING : Tinutukoy din bilang SLS, ang proseso ay nakabatay sa sintering ng isang polymer, ceramic o metallic powder na pili sa isang bagay. Ang ilalim ng processing chamber ay may dalawang cylinder: Isang part-build cylinder at isang powder-feed cylinder. Ang una ay incrementally ibinababa sa kung saan ang sintered bahagi ay nabuo at ang huli ay itinaas incrementally upang magbigay ng pulbos sa bahagi-build cylinder sa pamamagitan ng isang roller mekanismo. Una ang isang manipis na layer ng pulbos ay idineposito sa part-build cylinder, pagkatapos ay ang isang laser beam ay nakatutok sa layer na iyon, sinusubaybayan at natutunaw /sintering ang isang partikular na cross section, na pagkatapos ay muling nagresolid sa solid. Ang pulbos ay ang mga lugar na hindi tinamaan ng laser beam ay nananatiling maluwag ngunit sinusuportahan pa rin ang solidong bahagi. Pagkatapos ay isa pang layer ng pulbos ang idineposito at ang proseso ay paulit-ulit nang maraming beses upang makuha ang bahagi. Sa dulo, ang mga particle ng loose powder ay inalog off. Ang lahat ng ito ay isinasagawa ng isang computer na kontrol sa proseso gamit ang mga tagubiling nabuo ng 3D CAD program ng bahaging ginagawa. Maaaring ideposito ang iba't ibang materyales gaya ng polymer (gaya ng ABS, PVC, polyester), wax, metal at ceramics na may naaangkop na polymer binder. • ELECTRON-BEAM MELTING : Katulad ng selective laser sintering, ngunit gumagamit ng electron beam upang matunaw ang titanium o cobalt chrome powder upang makagawa ng mga prototype sa vacuum. Ang ilang mga pagpapaunlad ay ginawa upang maisagawa ang prosesong ito sa mga hindi kinakalawang na asero, aluminyo at tansong haluang metal. Kung ang lakas ng pagkapagod ng mga ginawang bahagi ay kailangang dagdagan, gumagamit kami ng mainit na isostatic pressing kasunod ng paggawa ng bahagi bilang pangalawang proseso. • THREE-DIMENSIONAL PRINTING : Tinutukoy din ng 3DP, sa pamamaraang ito ang isang print head ay nagdedeposito ng inorganic na binder sa isang layer ng alinman sa nonmetallic o metallic powder. Ang isang piston na nagdadala ng powder bed ay unti-unting ibinababa at sa bawat hakbang ang binder ay dineposito layer sa pamamagitan ng layer at pinagsama ng binder. Ang mga materyales na pulbos na ginamit ay mga polymer blends at fibers, foundry sand, mga metal. Gamit ang iba't ibang mga ulo ng panali nang sabay-sabay at iba't ibang mga panali ng kulay ay makakakuha tayo ng iba't ibang kulay. Ang proseso ay katulad ng pag-print ng inkjet ngunit sa halip na makakuha ng isang kulay na sheet ay nakakuha kami ng isang may kulay na tatlong dimensional na bagay. Ang mga bahaging ginawa ay maaaring porous at samakatuwid ay maaaring mangailangan ng sintering at metal infiltration upang mapataas ang density at lakas nito. Ang sintering ay masusunog ang binder at magsasama-sama ang mga metal powder. Ang mga metal tulad ng isang hindi kinakalawang na asero, aluminyo, titanium ay maaaring gamitin upang gawin ang mga bahagi at bilang mga materyales sa paglusot ay karaniwang ginagamit namin ang tanso at tanso. Ang kagandahan ng pamamaraang ito ay kahit na ang kumplikado at gumagalaw na mga asembliya ay maaaring gawin nang napakabilis. Halimbawa, isang gear assembly, isang wrench bilang isang tool ay maaaring gawin at magkakaroon ng mga gumagalaw at umiikot na bahagi na handa nang gamitin. Ang iba't ibang bahagi ng assembly ay maaaring gawin gamit ang iba't ibang kulay at lahat sa isang shot. I-download ang aming brochure sa:Mga Pangunahing Kaalaman sa Metal 3D Printing • DIRECT MANUFACTURING at RAPID TOOLING : Bukod sa pagsusuri ng disenyo, ang pag-troubleshoot ay gumagamit kami ng mabilis na prototyping para sa direktang paggawa ng mga produkto o direktang paggamit sa mga produkto. Sa madaling salita, ang mabilis na prototyping ay maaaring isama sa mga kumbensyonal na proseso upang gawing mas mahusay at mas mapagkumpitensya ang mga ito. Halimbawa, ang mabilis na prototyping ay maaaring makagawa ng mga pattern at molds. Ang mga pattern ng isang natutunaw at nasusunog na polimer na nilikha ng mabilis na mga operasyon ng prototyping ay maaaring tipunin para sa investment casting at mamuhunan. Ang isa pang halimbawang babanggitin ay ang paggamit ng 3DP upang makagawa ng ceramic casting shell at gamitin iyon para sa mga operasyon ng shell casting. Kahit na ang mga injection molds at mold insert ay maaaring gawin sa pamamagitan ng mabilis na prototyping at ang isa ay makakatipid ng maraming linggo o buwan ng paggawa ng amag na lead time. Sa pamamagitan lamang ng pagsusuri ng isang CAD file ng nais na bahagi, maaari naming gawin ang tool geometry gamit ang software. Narito ang ilan sa aming mga sikat na mabilis na paraan ng tooling: RTV (Room-Temperature Vulcanizing) MOLDING / URETHANE CASTING : Ang paggamit ng mabilis na prototyping ay maaaring gamitin upang gawin ang pattern ng nais na bahagi. Pagkatapos ang pattern na ito ay pinahiran ng isang ahente ng paghihiwalay at ang likidong RTV na goma ay ibinuhos sa pattern upang makagawa ng mga halves ng amag. Susunod, ang mga halves ng amag na ito ay ginagamit sa pag-iiniksyon ng mga likidong urethane. Maikli lang ang buhay ng amag, parang 0 o 30 cycle lang pero sapat na para sa small batch production. ACES (Acetal Clear Epoxy Solid) INJECTION MOLDING : Gamit ang mabilis na prototyping techniques gaya ng stereolithography, gumagawa kami ng injection molds. Ang mga hulma na ito ay mga shell na may bukas na dulo upang payagan ang pagpuno ng mga materyales tulad ng epoxy, epoxy na puno ng aluminyo o mga metal. Muli ang buhay ng amag ay limitado sa sampu o maximum na daan-daang bahagi. SPRAYED METAL TOOLING PROCESS : Gumagamit kami ng mabilis na prototyping at gumawa ng pattern. Nag-spray kami ng zinc-aluminum alloy sa ibabaw ng pattern at pinahiran ito. Ang pattern na may metal coating ay inilalagay sa loob ng isang flask at nilagyan ng epoxy o aluminum-filled na epoxy. Sa wakas, ito ay aalisin at sa pamamagitan ng paggawa ng dalawang tulad na halves ng amag ay nakakakuha tayo ng kumpletong amag para sa paghuhulma ng iniksyon. Ang mga amag na ito ay may mas mahabang buhay, sa ilang mga kaso depende sa materyal at temperatura maaari silang gumawa ng mga bahagi sa libu-libo. PROSESO NG KEELTOOL : Ang pamamaraan na ito ay maaaring gumawa ng mga hulma na may 100,000 hanggang 10 Milyong buhay sa pag-ikot. Gamit ang mabilis na prototyping gumagawa kami ng RTV mold. Ang amag ay susunod na puno ng isang halo na binubuo ng A6 tool steel powder, tungsten carbide, polymer binder at hayaang magaling. Ang amag na ito ay pagkatapos ay pinainit upang masunog ang polimer at ang mga metal na pulbos ay mag-fuse. Ang susunod na hakbang ay ang pagpasok ng tanso upang makagawa ng panghuling amag. Kung kinakailangan, ang mga pangalawang operasyon tulad ng machining at polishing ay maaaring gawin sa molde para sa mas mahusay na mga dimensional na katumpakan. _cc781905-5cde-3194-bb3b-136bad_cf5 CLICK Product Finder-Locator Service NAKARAANG PAHINA
- Machine Elements Manufacturing, Gears, Gear Drives, Bearings, Keys, Splines
Machine Elements Manufacturing, Gears, Gear Drives, Bearings, Keys, Splines, Pins, Shafts, Seals, Fasteners, Clutch, Cams, Followers, Belts, Couplings, Shafts Paggawa ng Mga Elemento ng Machine Magbasa pa Mga Belt at Chain at Cable Drive Assembly Magbasa pa Mga Gear at Gear Drive Assembly Magbasa pa Paggawa ng Couplings & Bearings Magbasa pa Paggawa ng Mga Susi at Spline at Pin Magbasa pa Cams & Followers & Linkages & Ratchet Wheels Manufacturing Magbasa pa Paggawa ng mga Shaft Magbasa pa Paggawa ng Mechanical Seals Magbasa pa Clutch at Brake Assembly Magbasa pa Paggawa ng Fasteners Magbasa pa Simpleng Machine Assembly MGA ELEMENTO NG MACHINE ay mga elementaryang bahagi ng isang makina. Ang mga elementong ito ay binubuo ng tatlong pangunahing uri: 1.) Mga istrukturang bahagi kabilang ang mga miyembro ng frame, bearings, axle, splines, fastener, seal, at lubricant. 2.) Mga mekanismong kumokontrol sa paggalaw sa iba't ibang paraan tulad ng mga gear train, belt o chain drive, linkage, cam at follower system, preno at clutches. 3.) Kontrolin ang mga bahagi tulad ng mga button, switch, indicator, sensor, actuator at computer controller. Karamihan sa mga elemento ng makina na inaalok namin sa iyo ay na-standardize sa mga karaniwang laki, ngunit magagamit din ang mga custom na elemento ng makina para sa iyong mga espesyal na application. Maaaring maganap ang pag-customize ng mga elemento ng makina sa mga kasalukuyang disenyo na nasa aming mga nada-download na katalogo o sa mga bagong disenyo. Ang prototyping at pagmamanupaktura ng mga elemento ng makina ay maaaring isulong kapag ang isang disenyo ay naaprubahan ng parehong partido. Kung ang mga bagong elemento ng makina ay kailangang idisenyo at gawin, ang aming mga customer ay maaaring mag-email sa amin ng kanilang sariling mga blueprint at susuriin namin ang mga ito para sa pag-apruba, o hinihiling nila sa amin na magdisenyo ng mga elemento ng makina para sa kanilang aplikasyon. Sa huling kaso, ginagamit namin ang lahat ng input mula sa aming mga customer at idinisenyo ang mga elemento ng makina at ipinapadala ang mga pinal na blueprint sa aming mga kliyente para sa pag-apruba. Kapag naaprubahan, gumagawa kami ng mga unang artikulo at pagkatapos ay gumagawa ng mga elemento ng makina ayon sa huling disenyo. Sa anumang yugto ng gawaing ito, kung sakaling ang isang partikular na disenyo ng elemento ng makina ay gumanap nang hindi kasiya-siya sa larangan (na bihira), sinusuri namin ang buong proyekto at gumawa ng mga pagbabago nang magkasama sa aming mga kliyente kung kinakailangan. Karaniwan nating kasanayan ang pumirma ng mga nondisclosure agreement (NDA) sa ating mga customer para sa disenyo ng mga elemento ng makina o anumang iba pang produkto kapag kinakailangan o kinakailangan. Kapag ang mga elemento ng makina para sa isang partikular na customer ay custom na idinisenyo at ginawa, nagtatalaga kami ng isang code ng produkto dito at ginagawa at ibinebenta lamang ang mga ito sa aming customer na nagmamay-ari ng produkto. Ginagawa namin ang mga elemento ng makina gamit ang mga binuo na tool, molde at pamamaraan nang maraming beses kung kinakailangan at sa tuwing muling i-order ng aming customer ang mga ito. Sa madaling salita, kapag ang isang custom na elemento ng makina ay idinisenyo at ginawa para sa iyo, ang intelektwal na pag-aari pati na ang lahat ng tool at molds ay inilalaan at iniimbak namin nang walang katapusan para sa iyo at sa mga produktong muling ginawa ayon sa gusto mo. Nag-aalok din kami sa aming mga kliyente ng mga serbisyo sa engineering sa pamamagitan ng malikhaing pagsasama-sama ng mga elemento ng makina sa isang bahagi o pagpupulong na nagsisilbi sa isang aplikasyon at nakakatugon o lumalampas sa inaasahan ng aming mga customer. Ang mga halamang gumagawa ng aming mga elemento ng makina ay kwalipikado ng alinman sa ISO9001, QS9000 o TS16949. Bilang karagdagan, karamihan sa aming mga produkto ay may markang CE o UL at nakakatugon sa mga pamantayang nauugnay sa internasyonal tulad ng ISO, SAE, ASME, DIN. Mangyaring mag-click sa mga submenu upang makakuha ng detalyadong impormasyon tungkol sa aming mga elemento ng makina kabilang ang: - Mga Sinturon, Chain at Cable Drive - Mga Gear at Gear Drive - Mga Coupling at Bearing - Mga Susi at Spline at pin - Mga Cam at Linkage - Mga baras - Mga Mechanical Seal - Industrial Clutch at Preno - Mga fastener - Mga Simpleng Makina Naghanda kami ng reference na brochure para sa aming mga customer, designer at developer ng mga bagong produkto kabilang ang mga elemento ng makina. Maaari mong pamilyar ang iyong sarili sa ilang karaniwang ginagamit na termino sa disenyo ng mga bahagi ng makina: Mag-download ng brochure para sa Mga Karaniwang Tuntunin ng Mechanical Engineering na ginagamit ng mga Designer at Engineer Ang aming mga elemento ng makina ay nakakahanap ng mga aplikasyon sa iba't ibang larangan tulad ng pang-industriyang makinarya, mga sistema ng automation, kagamitan sa pagsubok at metrology, kagamitan sa transportasyon, mga makina sa pagtatayo at halos kahit saan na maiisip mo. Ang AGS-TECH ay bubuo at gumagawa ng mga elemento ng makina mula sa iba't ibang materyales depende sa aplikasyon. Ang mga materyales na ginagamit para sa mga elemento ng makina ay maaaring mula sa mga hinubog na plastik na ginagamit para sa mga laruan hanggang sa pinatigas na case at espesyal na pinahiran na bakal para sa pang-industriyang makinarya. Gumagamit ang aming mga designer ng makabagong propesyonal na software at mga tool sa disenyo para sa pagbuo ng mga elemento ng makina, na isinasaalang-alang ang mga detalye tulad ng mga anggulo sa mga ngipin ng gear, mga stress na kasangkot, mga rate ng pagsusuot...atbp. Mangyaring mag-scroll sa aming mga submenus at i-download ang aming mga brochure ng produkto at mga katalogo upang makita kung maaari mong mahanap ang mga elemento ng makina na wala sa istante para sa iyong aplikasyon. Kung hindi ka makahanap ng magandang tugma para sa iyong aplikasyon, mangyaring ipaalam sa amin at makikipagtulungan kami sa iyo upang bumuo at gumawa ng mga elemento ng makina na tutugon sa iyong mga pangangailangan. Kung halos interesado ka sa aming mga kakayahan sa engineering at pananaliksik at pagpapaunlad sa halip na mga kakayahan sa pagmamanupaktura, inaanyayahan ka naming bisitahin ang aming website http://www.ags-engineering.com kung saan makakahanap ka ng mas detalyadong impormasyon tungkol sa aming disenyo, pagbuo ng produkto, pagbuo ng proseso, mga serbisyo sa pagkonsulta sa engineering at higit pa CLICK Product Finder-Locator Service NAKARAANG PAHINA
- Transmission Components, Belts, Chains, Cable Drives, Pulleys,AGS-TECH
Transmission Components, Belts, Chains and Cable Drives, Conventional & Grooved or Serrated, Positive Drive, Pulleys Mga Belt at Chain at Cable Drive Assembly Nag-aalok sa iyo ang AGS-TECH Inc. ng mga bahagi ng power transmission kabilang ang Belts & Chains at Cable Drive Assembly. Sa mga taon ng pagpipino, ang aming rubber, leather at iba pang belt drive ay naging mas magaan at mas compact, na may kakayahang magdala ng mas mataas na load sa mas mababang halaga. Katulad nito, ang aming mga chain drive ay dumaan sa maraming pag-unlad sa paglipas ng panahon at nag-aalok sila sa aming mga customer ng ilang mga pakinabang. Ang ilang mga bentahe ng paggamit ng mga chain drive ay ang kanilang medyo hindi pinigilan na mga distansya ng sentro ng baras, pagiging compact, kadalian ng pagpupulong, pagkalastiko sa pag-igting nang walang madulas o gumapang, kakayahang gumana sa mga kapaligiran na may mataas na temperatura. Ang aming mga cable drive ay nag-aalok din ng mga pakinabang tulad ng pagiging simple sa ilang mga aplikasyon kaysa sa iba pang mga uri ng mga bahagi ng transmission. Parehong available ang off-shelf belt, chain at cable drive pati na rin ang mga custom na fabricated at assembled na bersyon. Maaari naming gawin ang mga bahagi ng paghahatid na ito sa tamang sukat para sa iyong aplikasyon at mula sa mga pinaka-angkop na materyales. MGA SINTOS AT SINTOS NA DRIVE: - Conventional Flat Belts: Ito ay mga plain flat belt na walang ngipin, uka o serration. Ang mga flat belt drive ay nag-aalok ng flexibility, mahusay na shock absorption, mahusay na power transmission sa mataas na bilis, abrasion resistance, mababang gastos. Maaaring idugtong o ikonekta ang mga sinturon upang makagawa ng mas malalaking sinturon. Ang iba pang mga bentahe ng maginoo na flat belt ay ang mga ito ay manipis, ang mga ito ay hindi napapailalim sa mataas na sentripugal na pagkarga (ginagawang mabuti ang mga ito para sa mga high speed na operasyon na may maliliit na pulley). Sa kabilang banda, nagpapataw sila ng mga high bearing load dahil ang mga flat belt ay nangangailangan ng mataas na tensyon. Ang iba pang mga disadvantages ng flat belt drive ay maaaring madulas, maingay na operasyon, at medyo mas mababang kahusayan sa mababa at katamtamang bilis ng operasyon. Mayroon kaming dalawang uri ng conventional belt: Reinforced at Non-Reinforced. Ang mga reinforced belt ay may isang makunat na miyembro sa kanilang istraktura. Ang mga tradisyonal na flat belt ay available bilang leather, rubberized na tela o cord, non-reinforced rubber o plastic, fabric, reinforced leather. Ang mga leather belt ay nag-aalok ng mahabang buhay, flexibility, mahusay na koepisyent ng friction, madaling pagkumpuni. Gayunpaman, ang mga leather belt ay medyo mahal, nangangailangan ng pagbibihis at paglilinis ng sinturon, at depende sa kapaligiran na maaaring lumiit o mag-inat ang mga ito. Ang rubberized na tela o cord belt ay lumalaban sa moisture, acid at alkalis. Ang mga rubberized na sinturon ng tela ay binubuo ng mga sapin ng cotton o sintetikong pato na pinapagbinhi ng goma at ang pinaka-matipid. Ang mga rubberized cord belt ay binubuo ng isang serye ng mga plies ng rubber-impregnated cords. Ang mga rubberized na sinturon ng kurdon ay nag-aalok ng mataas na tensile strength at katamtamang laki at masa. Ang mga non-reinforced na goma o plastic na sinturon ay angkop para sa mga application na magaan at mababa ang bilis ng pagmamaneho. Ang mga non-reinforced na goma at plastik na sinturon ay maaaring iunat sa kanilang mga pulley. Ang mga plastik na non-reinforced na sinturon ay maaaring magpadala ng mas mataas na kapangyarihan kumpara sa mga sinturong goma. Ang mga reinforced leather belt ay binubuo ng isang plastic na tensile member na naka-sandwich sa pagitan ng leather top at bottom layers. Sa wakas, ang aming mga sinturon ng tela ay maaaring binubuo ng isang piraso ng koton o pato na nakatiklop at tinahi ng mga hilera ng mga longitudinal na tahi. Ang mga sinturon ng tela ay nakakapagsubaybay nang pare-pareho at nagpapatakbo sa mataas na bilis. - Mga Grooved o Serrated Belts (tulad ng V-Belts): Ito ang mga pangunahing flat belt na binago upang magbigay ng mga pakinabang ng isa pang uri ng transmission product. Ito ay mga flat belt na may longitudinally ribbed underside. Ang mga poly-V belt ay longitudinally grooved o serrated flat belt na may tensile section at isang serye ng mga katabing V-shaped grooves para sa mga layunin ng pagsubaybay at compression. Ang kapasidad ng kuryente ay nakasalalay sa lapad ng sinturon. Ang V-belt ay ang workhorse ng industriya at available sa iba't ibang standardized na laki at uri para sa paghahatid ng halos anumang load power. Ang mga V-belt drive ay gumagana nang maayos sa pagitan ng 1500 hanggang 6000 ft/min, gayunpaman ang makitid na V-belt ay gagana nang hanggang 10,000 ft/min. Ang mga V-belt drive ay nag-aalok ng mahabang buhay tulad ng 3 hanggang 5 taon at nagbibigay-daan sa malalaking ratio ng bilis, ang mga ito ay madaling i-install at alisin, nag-aalok ng tahimik na operasyon, mababang maintenance, mahusay na shock absorption sa pagitan ng belt driver at driven shafts. Ang kawalan ng V-belts ay ang kanilang tiyak na slip at creep at samakatuwid ay maaaring hindi sila ang pinakamahusay na solusyon kung saan kinakailangan ang mga kasabay na bilis. Mayroon kaming mga sinturong pang-industriya, sasakyan at pang-agrikultura. Available ang mga stock na karaniwang haba pati na rin ang mga custom na haba ng mga sinturon. Lahat ng karaniwang V-belt cross section ay available mula sa stock. May mga talahanayan kung saan maaari mong kalkulahin ang mga hindi kilalang parameter tulad ng haba ng sinturon, seksyon ng sinturon (lapad at kapal) kung alam mo ang ilang mga parameter ng iyong system tulad ng mga diameter ng pagmamaneho at hinihimok na pulley, distansya sa gitna sa pagitan ng mga pulley at bilis ng pag-ikot ng mga pulley. Maaari mong gamitin ang mga naturang talahanayan o hilingin sa amin na piliin ang tamang V-belt para sa iyo. - Positive Drive Belt (Timing Belt): Ang mga sinturong ito ay flat din na uri na may serye ng mga ngiping pantay-pantay sa loob ng circumference. Pinagsasama ng positibong drive o timing belt ang mga bentahe ng flat belt sa mga katangiang positive-grip ng mga chain at gear. Ang mga positibong drive belt ay nagpapakita ng walang slippage o mga pagkakaiba-iba ng bilis. Posible ang isang malawak na hanay ng mga ratio ng bilis. Mababa ang mga bearing load dahil maaari silang gumana sa mababang tensyon. Gayunpaman, mas madaling kapitan sila sa mga maling pagkakahanay sa mga pulley. - Mga Pulley, Sheaves, Hub para sa Mga Sinturon: Ang iba't ibang uri ng pulley ay ginagamit sa mga flat, ribbed (serrated) at positibong drive belt. Ginagawa namin silang lahat. Karamihan sa aming mga flat belt pulley ay ginawa sa pamamagitan ng paghahagis ng bakal, ngunit ang mga bersyon ng bakal ay available din sa iba't ibang kumbinasyon ng rim at hub. Ang aming mga flat-belt pulley ay maaaring may solid, spoked o split hub o maaari kaming gumawa ayon sa gusto mo. Ang mga ribbed at positive-drive belt ay available sa iba't ibang laki at lapad ng stock. Hindi bababa sa isang pulley sa timing-belt drive ay dapat na flanged upang panatilihin ang belt sa drive. Para sa mahabang sistema ng pagmamaneho sa gitna, inirerekomenda na magkaroon ng flanged ang parehong mga pulley. Ang mga sheaves ay ang mga ukit na gulong ng mga pulley at karaniwang ginagawa sa pamamagitan ng paghahagis ng bakal, pagbuo ng bakal o paghubog ng plastik. Ang pagbuo ng bakal ay angkop na proseso sa paggawa ng automotive at agricultural sheaves. Gumagawa kami ng mga bigkis na may regular at malalim na mga uka. Ang mga deep-groove sheaves ay angkop kapag pumapasok ang V-belt sa sheave sa isang anggulo, tulad ng kaso sa quarter-turn drive. Ang mga malalim na uka ay angkop din para sa mga vertical-shaft drive at mga application kung saan maaaring maging problema ang vibration ng mga sinturon. Ang aming mga idler pulley ay mga grooved sheaves o flat pulley na hindi nagsisilbi sa pagpapadala ng mekanikal na kapangyarihan. Ang mga idler pulley ay kadalasang ginagamit para sa paghihigpit ng mga sinturon. - Single at Multiple Belt Drives: Ang mga single belt drive ay may iisang groove samantalang ang maramihang belt drive ay may maraming groove. Sa pamamagitan ng pag-click sa may-katuturang may-kulay na teksto sa ibaba maaari mong i-download ang aming mga katalogo: - Power Transmission Belts (kasama ang V-Belts, Timing Belts, Raw Edge Belts, Wrapped Belts at Specialty Belts) - Mga Belt ng Conveyor - Mga V-Pulley - Mga Timing Pulley CHAIN & CHAIN DRIVES: Ang aming mga power transmission chain ay may ilang mga pakinabang tulad ng medyo hindi pinaghihigpitang distansya ng shaft center, madaling pag-assemble, compactness, elasticity sa ilalim ng tensyon nang walang slip o creep, kakayahan ng operasyon sa ilalim ng mataas na temperatura. Narito ang mga pangunahing uri ng aming mga chain: - Mga Nababakas na Chain: Ang aming mga nababakas na chain ay ginawa sa iba't ibang laki, pitch at ultimate strength at sa pangkalahatan ay mula sa malleable na bakal o bakal. Ang mga maluwag na chain ay ginawa sa iba't ibang laki mula 0.902 (23 mm) hanggang 4.063 pulgada (103 mm) na pitch at sukdulang lakas mula 700 hanggang 17,000 lb/square inch. Ang aming nababakas na mga bakal na chain sa kabilang banda ay ginawa sa mga sukat mula 0.904 pulgada (23 mm) hanggang humigit-kumulang 3.00 pulgada (76 mm) sa pitch, na may pinakamataas na lakas mula 760 hanggang 5000 lb/square inch._cc781905-5cde-3194-bb3b- 136bad5cf58d_ - Pintle Chain: Ang mga chain na ito ay ginagamit para sa mas mabibigat na load at bahagyang mas mataas na bilis sa humigit-kumulang 450 feet/min (2.2 m/sec). Ang mga pintle chain ay gawa sa mga indibidwal na cast link na may puno, bilog na dulo ng barrel na may mga offset na sidebar. Ang mga chain link na ito ay pinagsama sa mga bakal na pin. Ang mga chain na ito ay may saklaw mula sa humigit-kumulang 1.00 pulgada (25 mm) hanggang 6.00 pulgada (150 mm) at pinakamalakas sa pagitan ng 3600 hanggang 30,000 lb/square inch. - Offset-Sidebar Chains: Ang mga ito ay sikat sa mga drive chain ng construction machinery. Gumagana ang mga chain na ito sa bilis hanggang 1000 ft/min at nagpapadala ng mga load sa humigit-kumulang 250 hp. Sa pangkalahatan, ang bawat link ay may dalawang offset na sidebar, isang bushing, isang roller, isang pin, isang cotter pin. - Mga Roller Chain: Available ang mga ito sa mga pitch mula 0.25 (6 mm) hanggang 3.00 (75 mm) na pulgada. Ang sukdulang lakas ng single-width roller chain ay nasa pagitan ng 925 hanggang 130,000 lb/square inch. Available ang mga multiple-width na bersyon ng mga roller chain at nagpapadala ng mas malaking kapangyarihan sa mas mataas na bilis. Nag-aalok din ang mga multiple-width na roller chain ng mas maayos na pagkilos na may pinababang ingay. Ang mga roller chain ay binuo mula sa mga roller link at pin link. Ang mga cotter pin ay ginagamit sa nababakas na bersyon na mga roller chain. Ang disenyo ng mga roller chain drive ay nangangailangan ng kadalubhasaan sa paksa. Samantalang ang mga belt drive ay nakabatay sa mga linear na bilis, ang mga chain drive ay nakabatay sa bilis ng pag-ikot ng mas maliit na sprocket, na kung saan ay sa karamihan ng mga installation ang hinihimok na miyembro. Bukod sa mga rating ng horsepower at bilis ng pag-ikot, ang disenyo ng mga chain drive ay batay sa maraming iba pang mga kadahilanan. - Double-Pitch Chain: Karaniwang kapareho ng mga roller chain maliban na ang pitch ay dalawang beses ang haba. - Inverted Tooth (Silent) Chain: Mga high speed na chain na kadalasang ginagamit para sa prime mover, power-takeoff drives. Ang mga inverted tooth chain drive ay maaaring magpadala ng mga kapangyarihan hanggang sa 1200 hp at binubuo ng isang serye ng mga tooth link, na halili na pinagsama sa alinman sa mga pin o isang kumbinasyon ng magkasanib na mga bahagi. Ang center-guide chain ay may mga link ng gabay upang ipasok ang mga grooves sa sprocket, at ang side-guide chain ay may mga gabay upang ikonekta ang mga gilid ng sprocket. - Bead o Slider Chains: Ang mga chain na ito ay ginagamit para sa mabagal na bilis ng mga drive at gayundin sa mga manu-manong operasyon. Sa pamamagitan ng pag-click sa may-katuturang may-kulay na teksto sa ibaba maaari mong i-download ang aming mga katalogo: - Mga Kadena sa Pagmamaneho - Mga Kadena ng Conveyor - Malaking Pitch Conveyor Chain - Stainless Steel Roller Chain - Pagtaas ng mga Kadena - Mga Kadena ng Motorsiklo - Mga Kadena ng Makinang Pang-agrikultura - Mga Sprocket: Ang aming mga karaniwang sprocket ay umaayon sa mga pamantayan ng ANSI. Ang mga plate sprocket ay flat, hubless sprocket. Ang aming maliit at katamtamang laki na mga hub sprocket ay ginawa mula sa bar stock o forgings o ginawa sa pamamagitan ng pagwelding ng bar-stock hub sa isang hot-rolled plate. Ang AGS-TECH Inc. ay makakapagbigay ng mga sprocket na ginawa mula sa gray-iron castings, cast steel at welded hub constructions, sintered powder metal, molded o machined plastics. Para sa maayos na operasyon sa mataas na bilis, ang tamang pagpili ng laki ng mga sprocket ay mahalaga. Siyempre, ang mga limitasyon sa espasyo ay isang kadahilanan na hindi natin maaaring balewalain kapag pumipili ng sprocket. Inirerekomenda na ang ratio ng driver sa mga driven sprocket ay dapat na hindi hihigit sa 6:1, at ang chain wrap sa driver ay 120 degrees. Ang mga distansya sa gitna sa pagitan ng mas maliit at mas malalaking sprocket, haba ng chain at tensyon ng chain ay dapat ding piliin ayon sa ilang inirerekomendang kalkulasyon at alituntunin ng engineering at hindi random. I-download ang aming mga katalogo sa pamamagitan ng pag-click sa may kulay na teksto sa ibaba: - Mga Sprocket at Plate Wheels - Transmission Bushings - Pagkabit ng Kadena - Mga Chain Lock CABLE DRIVES: Ang mga ito ay may kanilang mga pakinabang kaysa sa mga belt at chain drive sa ilang mga kaso. Maaaring magawa ng mga cable drive ang parehong function tulad ng mga belt at maaari ding maging mas simple at mas matipid upang ipatupad sa ilang mga application. Halimbawa, ang isang bagong serye ng Synchromesh Cable Drives ay idinisenyo para sa positibong traksyon upang palitan ang mga kumbensyonal na lubid, simpleng cable at cog drive, lalo na sa mga masikip na espasyo. Ang bagong cable drive ay idinisenyo upang magbigay ng mataas na katumpakan na pagpoposisyon sa mga elektronikong kagamitan tulad ng mga makinang pangkopya, plotter, makinilya, printer,… .. atbp. Ang pangunahing tampok ng bagong cable drive ay ang kakayahang magamit sa mga 3D serpentine configuration na nagbibigay-daan sa napakaliit na disenyo. Maaaring gamitin ang mga syncromesh cable na may mas mababang pag-igting kung ihahambing sa mga lubid kaya binabawasan ang pagkonsumo ng kuryente. Makipag-ugnayan sa AGS-TECH para sa mga tanong at opinyon sa mga sinturon, chain at cable drive. CLICK Product Finder-Locator Service NAKARAANG PAHINA
- Glass and Ceramic Manufacturing, Hermetic Packages, Seals, Bonding
Glass and Ceramic Manufacturing, Hermetic Packages Seals and Bonding, Tempered Bulletproof Glass, Blow Moulding, Optical Grade Glass, Conductive Glass, Molding Salamin at Ceramic Forming & Shaping Ang uri ng pagmamanupaktura ng salamin na inaalok namin ay container glass, glass blowing, glass fiber & tubing & rod, domestic at industrial glassware, lamp at bulb, precision glass molding, optical component at assemblies, flat & sheet at float glass. Nagsasagawa kami ng parehong paghubog ng kamay gayundin ng paghubog ng makina. Ang aming sikat na teknikal na proseso ng pagmamanupaktura ng ceramic ay die pressing, isostatic pressing, hot isostatic pressing, hot pressing, slip casting, tape casting, extrusion, injection molding, green machining, sintering o firing, diamond grinding, hermetic assemblies. Inirerekomenda namin na mag-click ka dito upang I-DOWNLOAD ang aming Schematic Illustrations ng Glass Forming and Shaping Processes ng AGS-TECH Inc. I-DOWNLOAD ang aming Schematic Illustrations ng Technical Ceramic Manufacturing Processes ng AGS-TECH Inc. Ang mga nada-download na file na ito na may mga larawan at sketch ay makakatulong sa iyong mas maunawaan ang impormasyong ibinibigay namin sa iyo sa ibaba. • PAGGAWA NG CONTAINER GLASS: Mayroon kaming automated na PRESS AND BLOW pati na rin ang BLOW AND BLOW lines para sa pagmamanupaktura. Sa proseso ng suntok at suntok ay ibinabagsak namin ang isang gob sa blangkong amag at binubuo ang leeg sa pamamagitan ng paglalagay ng suntok ng naka-compress na hangin mula sa itaas. Kaagad pagkatapos nito, ang naka-compress na hangin ay hinihipan sa pangalawang pagkakataon mula sa kabilang direksyon sa pamamagitan ng leeg ng lalagyan upang mabuo ang pre-form ng bote. Ang pre-form na ito ay ililipat sa aktwal na molde, pinainit muli upang lumambot at inilapat ang naka-compress na hangin upang bigyan ang pre-form ng huling hugis ng lalagyan. Mas malinaw, ito ay may presyon at itinutulak sa mga dingding ng lukab ng blow mold upang makuha ang nais nitong hugis. Sa wakas, ang ginawang lalagyan ng salamin ay inililipat sa isang annealing oven para sa kasunod na pag-init at pag-alis ng mga stress na ginawa sa panahon ng paghuhulma at pinalamig sa isang kontroladong paraan. Sa paraan ng pagpindot at suntok, ang mga molten gob ay inilalagay sa isang parison mold (blangko na amag) at pinindot sa hugis ng parison (blangko na hugis). Ang mga blangko ay inililipat sa mga blow molds at hinipan katulad ng prosesong inilarawan sa itaas sa ilalim ng "Proseso ng Blow and Blow". Ang mga kasunod na hakbang tulad ng pagsusubo at pagtanggal ng stress ay magkatulad o pareho. • GLASS BLOWING : Kami ay gumagawa ng mga produktong salamin gamit ang conventional hand blowing pati na rin ang paggamit ng compressed air na may automated na kagamitan. Para sa ilang mga order, kinakailangan ang maginoo na pamumulaklak, gaya ng mga proyektong may kinalaman sa gawang gawa sa salamin, o mga proyektong nangangailangan ng mas maliit na bilang ng mga bahagi na may maluwag na pagpapaubaya, mga prototyping / demo na proyekto...atbp. Ang maginoo na pag-ihip ng salamin ay nagsasangkot ng paglubog ng isang guwang na metal pipe sa isang palayok ng tunaw na salamin at pag-ikot ng tubo para sa pagkolekta ng ilang halaga ng materyal na salamin. Ang salamin na nakolekta sa dulo ng tubo ay pinagsama sa flat iron, hugis ayon sa ninanais, pinahaba, muling pinainit at tinatangay ng hangin. Kapag handa na, ito ay ipinasok sa isang amag at hinipan ang hangin. Ang lukab ng amag ay basa upang maiwasan ang pagkakadikit ng salamin sa metal. Ang water film ay nagsisilbing unan sa pagitan nila. Ang manual blowing ay isang labor intensive mabagal na proseso at angkop lamang para sa prototyping o mga item na may mataas na halaga, hindi angkop para sa murang bawat piraso ng mataas na dami ng mga order. • PAGGAWA NG DOMESTIC & INDUSTRIAL GLASSWARE : Gamit ang iba't ibang uri ng glass material ay gumagawa ng malaking sari-saring glassware. Ang ilang baso ay lumalaban sa init at angkop para sa mga kagamitang babasagin sa laboratoryo samantalang ang ilan ay sapat na mahusay para sa pagtiis ng mga dishwasher nang maraming beses at akma para sa paggawa ng mga domestic na produkto. Gamit ang mga makina ng Westlake sampu-sampung libong piraso ng basong inumin ang ginagawa bawat araw. Upang gawing simple, ang tunaw na salamin ay kinokolekta sa pamamagitan ng vacuum at ipinasok sa mga hulma upang gawin ang mga pre-form. Pagkatapos ay hinipan ang hangin sa mga hulma, ang mga ito ay inililipat sa isa pang amag at ang hangin ay hinipan muli at ang salamin ay tumatagal ng huling hugis nito. Tulad ng pag-ihip ng kamay, ang mga amag na ito ay pinananatiling basa ng tubig. Ang karagdagang pag-inat ay bahagi ng pagtatapos ng operasyon kung saan ang leeg ay nabuo. Ang labis na salamin ay nasusunog. Pagkatapos nito, ang kinokontrol na muling pagpainit at proseso ng paglamig na inilarawan sa itaas ay sumusunod. • GLASS TUBE & ROD FORMING : Ang mga pangunahing proseso na ginagamit namin para sa paggawa ng mga glass tube ay ang DANNER at VELLO na mga proseso. Sa Proseso ng Danner, ang salamin mula sa isang hurno ay dumadaloy at nahuhulog sa isang hilig na manggas na gawa sa mga materyales na matigas ang ulo. Ang manggas ay dinadala sa isang umiikot na guwang na baras o blowpipe. Ang salamin ay pagkatapos ay balot sa paligid ng manggas at bumubuo ng isang makinis na layer na dumadaloy pababa sa manggas at sa ibabaw ng dulo ng baras. Sa kaso ng pagbubuo ng tubo, ang hangin ay hinipan sa pamamagitan ng isang blowpipe na may guwang na dulo, at sa kaso ng pagbubuo ng baras ay gumagamit kami ng mga solidong tip sa baras. Ang mga tubo o mga pamalo ay iginuhit sa ibabaw ng mga may dalang roller. Ang mga sukat tulad ng kapal ng dingding at diameter ng mga glass tube ay nababagay sa nais na mga halaga sa pamamagitan ng pagtatakda ng diameter ng manggas at pag-ihip ng presyon ng hangin sa nais na halaga, pagsasaayos ng temperatura, rate ng daloy ng salamin at bilis ng pagguhit. Ang proseso ng pagmamanupaktura ng Vello glass tube sa kabilang banda ay nagsasangkot ng salamin na naglalakbay palabas ng furnace at papunta sa isang mangkok na may guwang na mandrel o kampana. Ang baso ay dumaan sa espasyo ng hangin sa pagitan ng mandrel at ng mangkok at nagiging hugis ng isang tubo. Pagkatapos nito ay naglalakbay ito sa ibabaw ng mga roller patungo sa isang drawing machine at pinalamig. Sa dulo ng cooling line cutting at final processing ay nagaganap. Ang mga sukat ng tubo ay maaaring iakma tulad ng sa proseso ng Danner. Kapag ikinukumpara ang proseso ng Danner sa Vello, masasabi nating mas angkop ang proseso ng Vello para sa paggawa ng maraming dami samantalang maaaring mas angkop ang proseso ng Danner para sa mas tumpak na mga order ng tube na mas maliit na volume. • PAGPROSESO NG SHEET & FLAT & FLOAT GLASS : Mayroon kaming malaking dami ng flat glass sa mga kapal mula sa kapal ng submilimeter hanggang ilang sentimetro. Ang aming mga flat glass ay halos optical perfection. Nag-aalok kami ng salamin na may mga espesyal na coating tulad ng optical coatings, kung saan ginagamit ang chemical vapor deposition technique para maglagay ng mga coatings gaya ng antireflection o mirror coating. Gayundin ang mga transparent na conductive coating ay karaniwan. Available din ang hydrophobic o hydrophilic coatings sa salamin, at coating na gumagawa ng glass self-cleaning. Ang mga tempered, bulletproof at laminated glass ay iba pang sikat na item. Pinutol namin ang salamin sa nais na hugis na may nais na mga pagpapaubaya. Available ang iba pang mga pangalawang operasyon tulad ng curving o bending flat glass. • PRECISION GLASS MOLDING : Ginagamit namin ang diskarteng ito kadalasan para sa paggawa ng precision optical na mga bahagi nang hindi nangangailangan ng mas mahal at nakakaubos ng oras na mga diskarte tulad ng paggiling, paglaplap at pag-polish. Ang diskarteng ito ay hindi palaging sapat para sa paggawa ng pinakamahusay sa pinakamahusay na optika, ngunit sa ilang mga kaso tulad ng mga produkto ng consumer, mga digital camera, mga medikal na optika maaari itong maging isang mas mura magandang opsyon para sa mataas na dami ng pagmamanupaktura. Gayundin ito ay may kalamangan sa iba pang mga diskarte sa pagbuo ng salamin kung saan kinakailangan ang mga kumplikadong geometries, tulad ng sa kaso ng mga asphere. Ang pangunahing proseso ay nagsasangkot ng pag-load sa ibabang bahagi ng aming amag na may blangko na salamin, paglisan ng silid ng proseso para sa pag-alis ng oxygen, malapit sa pagsasara ng amag, mabilis at isothermal na pag-init ng die at salamin na may infrared na ilaw, karagdagang pagsasara ng mga kalahati ng amag upang pindutin nang dahan-dahan ang pinalambot na salamin sa isang kontroladong paraan sa nais na kapal, at sa wakas ay paglamig ng salamin at pagpuno sa silid ng nitrogen at pag-alis ng produkto. Ang tumpak na kontrol sa temperatura, distansya ng pagsasara ng amag, puwersa ng pagsasara ng amag, pagtutugma ng mga koepisyent ng pagpapalawak ng amag at materyal na salamin ay susi sa prosesong ito. • PAGGAWA NG MGA GLASS OPTICAL COMPONENT AT ASSEMBLIES : Bukod sa precision glass molding, may ilang mahahalagang proseso na ginagamit namin para sa paggawa ng matataas na kalidad na optical component at assemblies para sa mga demanding application. Ang paggiling, paghaplos at pag-polish ng optical grade glass sa pinong espesyal na abrasive slurries ay isang sining at agham para sa paggawa ng mga optical lens, prism, flat at higit pa. Ang flatness ng surface, waviness, smoothness at walang depektong optical surface ay nangangailangan ng maraming karanasan sa mga ganitong proseso. Ang mga maliliit na pagbabago sa kapaligiran ay maaaring magresulta sa labas ng mga produkto ng espesipikasyon at huminto sa linya ng pagmamanupaktura. May mga kaso kung saan ang isang solong pagpahid sa optical surface na may malinis na tela ay maaaring makatugon sa isang produkto sa mga detalye o mabibigo sa pagsubok. Ang ilang tanyag na materyales sa salamin na ginamit ay fused silica, quartz, BK7. Gayundin ang pagpupulong ng naturang mga bahagi ay nangangailangan ng dalubhasang karanasan sa angkop na lugar. Minsan ginagamit ang mga espesyal na pandikit. Gayunpaman, kung minsan ang isang pamamaraan na tinatawag na optical contacting ay ang pinakamahusay na pagpipilian at hindi nagsasangkot ng materyal sa pagitan ng mga nakakabit na optical glass. Binubuo ito ng pisikal na pakikipag-ugnay sa mga patag na ibabaw upang idikit sa isa't isa nang walang pandikit. Sa ilang mga kaso, ginagamit ang mga mechanical spacer, precision glass rod o bola, clamp o machined na bahagi ng metal upang i-assemble ang mga optical na bahagi sa ilang partikular na distansya at may ilang geometric na oryentasyon sa isa't isa. Suriin natin ang ilan sa aming mga sikat na diskarte para sa paggawa ng mga high end na optika. GRINDING & LAPPING & POLISHING : Ang magaspang na hugis ng optical component ay nakukuha sa paggiling ng basong blangko. Pagkatapos noon, ang paglalap at pagpapakintab ay isinasagawa sa pamamagitan ng pag-ikot at pagkuskos sa magaspang na ibabaw ng mga optical na bahagi laban sa mga tool na may gustong hugis sa ibabaw. Ang mga slurries na may maliliit na abrasive na particle at likido ay ibinubuhos sa pagitan ng mga optika at mga tool sa paghubog. Ang mga nakasasakit na laki ng particle sa naturang mga slurries ay maaaring mapili ayon sa antas ng flatness na nais. Ang mga paglihis ng mga kritikal na optical na ibabaw mula sa nais na mga hugis ay ipinahayag sa mga tuntunin ng mga wavelength ng liwanag na ginagamit. Ang aming mataas na katumpakan na optika ay may ikasampu ng isang wavelength (Wavelength/10) na mga tolerance o kahit na mas mahigpit ay posible. Bukod sa surface profile, ang mga kritikal na surface ay ini-scan at sinusuri para sa iba pang surface feature at depekto gaya ng mga sukat, gasgas, chips, pits, specks...atbp. Ang mahigpit na kontrol sa mga kondisyon sa kapaligiran sa optical manufacturing floor at malawak na metrology at mga kinakailangan sa pagsubok na may makabagong kagamitan ay ginagawa itong isang mapaghamong sangay ng industriya. • MGA PANGALAWANG PROSESO SA PAGGAWA NG GLASS: Muli, limitado lamang kami sa iyong imahinasyon pagdating sa pangalawang at pagtatapos ng mga proseso ng salamin. Dito ay inilista namin ang ilan sa mga ito: -Mga coatings sa salamin (optical, electrical, tribological, thermal, functional, mechanical...). Bilang isang halimbawa maaari nating baguhin ang mga katangian ng ibabaw ng salamin na ginagawa itong halimbawa na nagpapakita ng init upang mapanatiling malamig ang pagbuo ng mga interior, o gawing sumisipsip ng infrared ang isang panig gamit ang nanotechnology. Nakakatulong ito na panatilihing mainit ang loob ng mga gusali dahil ang pinakaibabaw na layer ng salamin ay sumisipsip ng infrared radiation sa loob ng gusali at i-radiate ito pabalik sa loob. -Etching sa salamin -Applied Ceramic Labeling (ACL) -Pag-uukit -Flame polishing -Kimika na buli -Pagmantsa PAGGAWA NG TECHNICAL CERAMICS • DIE PRESSING : Binubuo ng uniaxial compaction ng granular powders na nakakulong sa isang die • HOT PRESSING : Katulad ng die pressing ngunit may pagdaragdag ng temperatura upang mapahusay ang densification. Ang powder o compacted preform ay inilalagay sa graphite die at ang uniaxial pressure ay inilalapat habang ang die ay pinananatili sa mataas na temperatura tulad ng 2000 C. Ang mga temperatura ay maaaring mag-iba depende sa uri ng ceramic powder na pinoproseso. Para sa mga kumplikadong hugis at geometry ay maaaring kailanganin ang iba pang kasunod na pagproseso tulad ng paggiling ng brilyante. • ISOSTATIC PRESSING : Ang granular powder o die pressed compact ay inilalagay sa mga lalagyan ng airtight at pagkatapos ay sa isang closed pressure vessel na may likido sa loob. Pagkatapos noon ay siksikin ang mga ito sa pamamagitan ng pagtaas ng presyon ng pressure vessel. Ang likido sa loob ng sisidlan ay naglilipat ng mga puwersa ng presyon nang pantay-pantay sa buong ibabaw ng lalagyan na hindi tinatagusan ng hangin. Sa gayon, ang materyal ay pinagsama nang pantay-pantay at tumatagal ang hugis ng nababaluktot na lalagyan nito at ang panloob na profile at mga tampok nito. • HOT ISOSTATIC PRESSING : Katulad ng isostatic pressing, ngunit bilang karagdagan sa naka-pressure na gas atmosphere, sini-sinter namin ang compact sa mataas na temperatura. Ang hot isostatic pressing ay nagreresulta sa karagdagang densification at pagtaas ng lakas. • SLIP CASTING / DRAIN CASTING : Pinupunan namin ang amag ng isang suspensyon ng micrometer sized ceramic particles at carrier liquid. Ang timpla na ito ay tinatawag na "slip". Ang amag ay may mga pores at samakatuwid ang likido sa halo ay sinasala sa amag. Bilang isang resulta, ang isang cast ay nabuo sa mga panloob na ibabaw ng amag. Pagkatapos ng sintering, ang mga bahagi ay maaaring alisin sa amag. • TAPE CASTING : Gumagawa kami ng mga ceramic tape sa pamamagitan ng paghahagis ng mga ceramic slurries sa patag na gumagalaw na ibabaw ng carrier. Ang mga slurries ay naglalaman ng mga ceramic powder na hinaluan ng iba pang mga kemikal para sa mga layunin ng pagbubuklod at pagdadala. Habang ang mga solvent ay sumingaw ang siksik at nababaluktot na mga sheet ng ceramic ay naiwan na maaaring gupitin o igulong ayon sa gusto. • PAGBUO NG EXTRUSION : Tulad ng ibang mga proseso ng extrusion, ang malambot na pinaghalong ceramic powder na may mga binder at iba pang mga kemikal ay ipinapasa sa isang die upang makuha ang cross-sectional na hugis nito at pagkatapos ay gupitin sa nais na haba. Ang proseso ay ginagawa gamit ang malamig o pinainit na ceramic mixtures. • LOW PRESSURE INJECTION MOLDING : Naghahanda kami ng pinaghalong ceramic powder na may mga binder at solvents at pinainit ito sa temperatura kung saan madali itong maipit at mapipilitang pumasok sa tool cavity. Kapag nakumpleto na ang ikot ng paghubog, ilalabas ang bahagi at masusunog ang nagbubuklod na kemikal. Gamit ang injection molding, makakakuha tayo ng masalimuot na bahagi sa mataas na volume sa matipid. Ang mga butas na isang maliit na bahagi ng isang milimeter sa isang 10mm na kapal ng pader ay posible, ang mga thread ay posible nang walang forther machining, ang mga tolerance na kasing higpit ng +/- 0.5% ay posible at kahit na mas mababa kapag ang mga bahagi ay machined , posible ang kapal ng pader sa pagkakasunud-sunod na 0.5mm hanggang 12.5 mm pati na rin ang kapal ng pader na 6.5mm hanggang 150mm ang haba. • GREEN MACHINING : Gamit ang parehong mga metal machining tool, maaari tayong ma-machine pressed na mga ceramic na materyales habang malambot pa ang mga ito tulad ng chalk. Ang mga pagpapaubaya ng +/- 1% ay posible. Para sa mas mahusay na tolerances ginagamit namin ang brilyante paggiling. • SINTERING o FIRING : Ginagawang posible ng sintering ang buong densification. Nangyayari ang makabuluhang pag-urong sa mga berdeng compact na bahagi, ngunit hindi ito isang malaking problema dahil isinasaalang-alang namin ang mga pagbabagong ito sa dimensyon kapag nagdidisenyo kami ng bahagi at tooling. Ang mga particle ng pulbos ay pinagsama-sama at ang porosity na dulot ng proseso ng compaction ay inalis sa malaking lawak. • DIAMOND GRINDING : Ang pinakamahirap na materyal na "diamond" sa Mundo ay ginagamit sa paggiling ng matitigas na materyales tulad ng mga ceramics at precision parts na nakuha. Ang mga tolerance sa hanay ng micrometer at napakakinis na ibabaw ay nakakamit. Dahil sa gastos nito, isinasaalang-alang lamang namin ang pamamaraang ito kapag talagang kailangan namin ito. • Ang HERMETIC ASSEMBLIES ay yaong halos hindi pinapayagan ang anumang pagpapalitan ng bagay, solids, likido o gas sa pagitan ng mga interface. Ang hermetic sealing ay airtight. Halimbawa, ang mga hermetic electronic enclosure ay ang mga nagpapanatiling hindi napinsala ng kahalumigmigan, mga contaminant o gas ang mga sensitibong panloob na nilalaman ng isang nakabalot na device. Walang 100% hermetic, ngunit kapag pinag-uusapan natin ang hermeticity, ibig sabihin, sa mga praktikal na termino, mayroong hermeticity hanggang sa napakababa ng leak rate na ang mga device ay ligtas sa ilalim ng normal na mga kondisyon sa kapaligiran sa napakatagal na panahon. Ang aming mga hermetic assemblies ay binubuo ng metal, salamin at ceramic na mga bahagi, metal-ceramic, ceramic-metal-ceramic, metal-ceramic-metal, metal sa metal, metal-glass, metal-glass-metal, glass-metal-glass, glass- metal at salamin sa salamin at lahat ng iba pang kumbinasyon ng metal-glass-ceramic bonding. Halimbawa, maaari nating pahiran ng metal ang mga ceramic na bahagi upang madikit ang mga ito sa iba pang mga bahagi sa pagpupulong at magkaroon ng mahusay na kakayahan sa pagbubuklod. Mayroon kaming karunungan sa paglalagay ng mga optical fiber o feedthrough ng metal at paghihinang o pagpapatigas sa mga ito sa mga enclosure, kaya walang gas na dumadaan o tumagas sa mga enclosure. Samakatuwid, ginagamit ang mga ito para sa paggawa ng mga electronic enclosure upang i-encapsulate ang mga sensitibong device at protektahan ang mga ito mula sa panlabas na kapaligiran. Bukod sa kanilang mahusay na mga katangian ng sealing, iba pang mga katangian tulad ng thermal expansion coefficient, deformation resistance, non-outgassing nature, napakahabang buhay, nonconductive na katangian, thermal insulation properties, antistatic na kalikasan...atbp. gawing pagpipilian ang mga materyal na salamin at ceramic para sa ilang partikular na aplikasyon. Ang impormasyon sa aming pasilidad na gumagawa ng ceramic to metal fittings, hermetic sealing, vacuum feedthroughs, high at ultrahigh vacuum at fluid control components ay matatagpuan dito:Hermetic Components Factory Brochure CLICK Product Finder-Locator Service NAKARAANG PAHINA
- Wire & Spring Forming, Shaping, Welding, Assembly of Wires, Coil, CNC
Wire & Spring Forming, Shaping, Welding, Assembly of Wires, Coil Compression Extension Torsion Flat Springs, Custom Wires, Helical Springs at AGS-TECH Inc. Wire at Spring Forming Gumagawa kami ng mga custom na wire, wire assembly, wire na nabuo sa gustong 2D at 3D na hugis, wire nets, mesh, enclosures, basket, bakod, wire spring, flat spring; torsion, compression, tension, flat spring at higit pa. Ang aming mga proseso ay wire at spring forming, wire drawing, shaping, bending, welding, brazing, soldering, piercing, swaging, drilling, chamfering, grinding, threading, coating, fourslide, slide forming, winding, coiling, upsetting. Inirerekomenda namin na mag-click ka dito upang I-DOWNLOAD ang aming Schematic Illustrations ng Wire and Spring Forming Processes ng AGS-TECH Inc. Ang nada-download na file na ito na may mga larawan at sketch ay makakatulong sa iyong mas maunawaan ang impormasyong ibinibigay namin sa iyo sa ibaba. • WIRE DRAWING : Gamit ang tensile forces, ini-stretch namin ang metal stock at iginuhit ito sa isang die upang bawasan ang diameter at dagdagan ang haba nito. Minsan gumagamit kami ng isang serye ng mga dies. Kami ay may kakayahang gumawa ng mga dies para sa bawat gauge ng wire. Gamit ang materyal na may mataas na lakas ng makunat gumuhit kami ng napakanipis na mga wire. Nag-aalok kami ng malamig at mainit na mga wire. • WIRE FORMING : Ang isang roll ng gauged wire ay baluktot at hinuhubog sa isang kapaki-pakinabang na produkto. Mayroon kaming kakayahan na bumuo ng mga wire mula sa lahat ng gauge, kabilang ang mga manipis na filament pati na rin ang makapal na mga wire tulad ng mga ginagamit bilang spring sa ilalim ng chassis ng sasakyan. Ang mga kagamitan na ginagamit namin para sa pagbubuo ng wire ay manu-mano at CNC wire formers, coiler, power presses, fourslide, multi-slide. Ang aming mga proseso ay pagguhit, pagyuko, pagtuwid, pagyupi, pag-uunat, paggupit, pag-upset, paghihinang at pagwelding at pagpapatigas, pagpupulong, pag-coiling, pag-swaging (o pagpapapakpak), pagbubutas, pag-thread ng wire, pagbabarena, pag-chamfer, paggiling, patong at mga paggamot sa ibabaw. Ang aming makabagong kagamitan ay maaaring i-set-up upang bumuo ng napakakumplikadong mga disenyo ng anumang hugis at mahigpit na pagpapahintulot. Nag-aalok kami ng iba't ibang uri ng dulo tulad ng mga spherical, pointed o chamfered na dulo para sa iyong mga wire. Karamihan sa aming mga wire forming project ay may minimal hanggang zero na mga gastos sa tooling. Ang mga sample na oras ng turnaround ay karaniwang mga araw. Ang mga pagbabago sa disenyo/configuration ng mga wire form ay maaaring gawin nang napakabilis. • SPRING FORMING : Gumagawa ang AGS-TECH ng malaking iba't ibang mga bukal kabilang ang: -Torsion / Double Torsion Spring -Pag-igting / Compression Spring -Patuloy / Variable Spring -Coil at Helical Spring -Flat at Leaf Spring -Balanse Spring -Belleville Washer -Negator Spring -Progressive Rate Coil Spring -Wave Spring -Volute Spring -Tapered Springs -Spring Rings -Clock Springs -Mga clip Gumagawa kami ng mga bukal mula sa iba't ibang mga materyales at maaaring gabayan ka ayon sa iyong aplikasyon. Karamihan sa mga karaniwang materyales ay hindi kinakalawang na asero, chrome silicon, high-carbon steel, oil-tempered low-carbon, chrome vanadium, phosphor bronze, titanium, beryllium copper alloy, high-temperature ceramic. Gumagamit kami ng iba't ibang mga diskarte sa paggawa ng mga bukal, kabilang ang CNC coiling, cold winding, hot winding, hardening, finishing. Ang iba pang mga diskarteng nabanggit na sa itaas sa ilalim ng wire forming ay karaniwan din sa aming mga operasyon sa pagmamanupaktura ng tagsibol. • FINISHING SERVICES for WIRES & SPRINGS : Maaari naming tapusin ang iyong mga produkto sa maraming paraan depende sa iyong pinili at pangangailangan. Ang ilang karaniwang prosesong inaalok namin ay: pagpipinta, powder coating, plating, vinyl dipping, anodizing, stress relieve, heat treatment, shot peen, tumble, chromate, electroless nickel, passivation, baked enamel, plastic coat , paglilinis ng plasma. CLICK Product Finder-Locator Service NAKARAANG PAHINA
- Forging and Powdered Metallurgy, Die Forging, Heading, Hot Forging
Forging and Powdered Metallurgy, Die Forging, Heading, Hot Forging, Impression Die, Near Net Shape, Swaging, Metal Hobbing, Riveting, Coining from AGS-TECH Inc. Metal Forging at Powder Metallurgy Ang uri ng mga proseso ng METAL FORGING na inaalok namin ay hot and cold die, open die at closed die, impression die at flashless forgings, cogging, fullering, edging at precision forging, near-net-shape, heading , swaging, upset forging, metal hobbing, press & roll & radial & orbital & ring at isothermal forging, coining, riveting, metal ball forging, metal piercing, sizing, high energy rate forging. Ang aming POWDER METALLURGY at POWDER PROCESSING technique ay powder pressing at sintering, impregnation, infiltration, hot and cold isostatic pressing, metal injection molding, roll compaction, powder rolling, powder extrusion, loose sintering, spark sintering, hot pressing. Inirerekomenda namin na mag-click ka dito upang I-DOWNLOAD ang aming Schematic Illustrations of Forging Processes ng AGS-TECH Inc. I-DOWNLOAD ang aming Schematic Illustrations ng Powder Metallurgy Processes ng AGS-TECH Inc. Ang mga nada-download na file na ito na may mga larawan at sketch ay makakatulong sa iyong mas maunawaan ang impormasyong ibinibigay namin sa iyo sa ibaba. Sa pag-forging ng metal, ang mga puwersa ng compressive ay inilapat at ang materyal ay deformed at ang nais na hugis ay nakuha. Ang pinakakaraniwang mga huwad na materyales sa industriya ay bakal at bakal, ngunit marami pang iba tulad ng aluminyo, tanso, titanium, magnesiyo ay malawak ding pineke. Ang mga huwad na bahagi ng metal ay nagpabuti ng mga istruktura ng butil bilang karagdagan sa mga selyadong bitak at saradong mga bakanteng espasyo, kaya ang lakas ng mga bahagi na nakuha ng prosesong ito ay mas mataas. Ang pag-forging ay gumagawa ng mga bahagi na na mas malakas para sa kanilang timbang kaysa sa mga bahaging ginawa sa pamamagitan ng casting o machining. Dahil ang mga huwad na bahagi ay hinuhubog sa pamamagitan ng paggawa ng metal na dumaloy sa huling hugis nito, ang metal ay kumukuha ng isang direksiyon na istraktura ng butil na tumutukoy sa higit na lakas ng mga bahagi. Sa madaling salita, ang mga bahagi na nakuha sa pamamagitan ng proseso ng forging ay nagpapakita ng mas mahusay na mga mekanikal na katangian kumpara sa simpleng cast o machined na mga bahagi. Ang bigat ng mga metal forging ay maaaring mula sa maliliit na magaan na bahagi hanggang sa daan-daang libong libra. Gumagawa kami ng mga forging na kadalasang para sa mekanikal na hinihingi na mga application kung saan inilalapat ang mataas na stress sa mga bahagi tulad ng mga piyesa ng sasakyan, gears, work tool, hand tools, turbine shaft, motorcycle gear. Dahil medyo mataas ang mga gastos sa tooling at set-up, inirerekomenda namin ang proseso ng pagmamanupaktura na ito para lang sa produksyon na may mataas na volume at para sa mababang volume ngunit may mataas na halaga na kritikal na bahagi tulad ng aerospace landing gear. Bukod sa gastos ng tooling, ang mga lead time ng pagmamanupaktura para sa malalaking dami ng mga huwad na bahagi ay maaaring mas mahaba kumpara sa ilang simpleng makinang bahagi, ngunit ang pamamaraan ay mahalaga para sa mga bahagi na nangangailangan ng pambihirang lakas tulad ng bolts, nuts, espesyal na paggamit mga fastener, automotive, forklift, mga bahagi ng crane. • HOT DIE at COLD DIE FORGING : Ang hot die forging, gaya ng ipinahihiwatig ng pangalan ay isinasagawa sa mataas na temperatura, kaya mataas ang ductility at mababa ang lakas ng materyal. Pinapadali nito ang madaling pagpapapangit at pag-forging. Sa kabaligtaran, ang cold die forging ay isinasagawa sa mas mababang temperatura at nangangailangan ng mas mataas na puwersa na nagreresulta sa strain hardening, mas mahusay na surface finish at katumpakan ng mga manufactured parts. • OPEN DIE at IMPRESSION DIE FORGING : Sa open die forging, hindi pinipigilan ng mga dies ang materyal na pini-compress, samantalang sa impression die forging, ang mga cavity sa loob ng dies ay naghihigpit sa daloy ng materyal habang ito ay pineke sa nais na hugis. UPSET FORGING o tinatawag ding UPSETTING, na talagang hindi pareho ngunit halos magkatulad na proseso, ay isang bukas na proseso ng die kung saan ang work piece ay nasa pagitan ng dalawang flat dies at binabawasan ng compressive force ang taas nito. Habang ang taas ay reduced, tumataas ang lapad ng work piece. HEADING, ang isang upset forging na proseso ay nagsasangkot ng cylindrical stock na nasira sa dulo nito at ang cross section nito ay lokal na nadagdagan. Sa heading ang stock ay pinapakain sa pamamagitan ng die, pineke at pagkatapos ay pinutol sa haba. Ang operasyon ay may kakayahang gumawa ng mataas na dami ng mga fastener nang mabilis. Kadalasan ito ay isang malamig na pagpapatakbo dahil ginagamit ito sa paggawa ng mga dulo ng kuko, mga dulo ng turnilyo, mga mani at bolts kung saan kailangang palakasin ang materyal. Ang isa pang proseso ng open die ay COGGING, kung saan ang work piece ay pineke sa isang serye ng mga hakbang sa bawat hakbang na nagreresulta sa compression ng materyal at ang kasunod na paggalaw ng open die kasama ang haba ng work piece. Sa bawat hakbang, ang kapal ay nababawasan at ang haba ay nadagdagan ng isang maliit na halaga. Ang proseso ay kahawig ng isang kinakabahang estudyante na kinakagat ang kanyang lapis sa maliliit na hakbang. Ang prosesong tinatawag na FULLERING ay isa pang paraan ng open die forging na madalas naming i-deploy bilang isang mas maagang hakbang upang ipamahagi ang materyal sa work piece bago maganap ang iba pang mga operasyon ng pag-forging ng metal. Ginagamit namin ito kapag ang work piece ay nangangailangan ng ilang forging operations. Sa operasyon, mamatay na may matambok na ibabaw na deform at magdulot ng daloy ng metal sa magkabilang panig. Ang isang katulad na proseso sa fullering, ang EDGING sa kabilang banda ay nagsasangkot ng bukas na die na may malukong ibabaw upang ma-deform ang work piece. Ang edging ay isang proseso din ng paghahanda para sa mga kasunod na operasyon ng forging na nagpapadaloy ng materyal mula sa magkabilang panig patungo sa isang lugar sa gitna. IMPRESSION DIE FORGING o CLOSED DIE FORGING na kung tawagin ay gumagamit ng die / mold na pumipilit sa materyal at naghihigpit sa daloy nito sa loob mismo. Nagsasara ang die at ang materyal ay nagiging hugis ng die / mold cavity. PRECISION FORGING, isang prosesong nangangailangan ng espesyal na kagamitan at amag, ay gumagawa ng mga bahagi na walang o napakakaunting flash. Sa madaling salita, ang mga bahagi ay magkakaroon ng malapit sa mga huling sukat. Sa prosesong ito ang isang mahusay na kinokontrol na dami ng materyal ay maingat na ipinasok at nakaposisyon sa loob ng amag. Inilalagay namin ang pamamaraang ito para sa mga kumplikadong hugis na may manipis na mga seksyon, maliliit na tolerance at draft na anggulo at kapag ang mga dami ay sapat na malaki upang bigyang-katwiran ang mga gastos sa amag at kagamitan. • FLASHLESS FORGING : Ang workpiece ay inilalagay sa die sa paraang walang materyal na maaaring dumaloy palabas ng cavity upang bumuo ng flash. Walang hindi gustong flash trimming ang kinakailangan. Ito ay isang precision forging na proseso at sa gayon ay nangangailangan ng malapit na kontrol sa dami ng materyal na ginamit. • METAL SWAGING o RADIAL FORGING : Ang isang piraso ng trabaho ay circumferentially acted sa pamamagitan ng die at forged. Ang isang mandrel ay maaari ring gamitin upang pekein ang panloob na workpiece geometry. Sa swaging operation ang work piece ay karaniwang tumatanggap ng ilang stroke kada segundo. Ang mga tipikal na bagay na ginawa sa pamamagitan ng swaging ay pointed tip tools, tapered bars, screwdrivers. • METAL PIERCING : Madalas naming ginagamit ang operasyong ito bilang karagdagang operasyon sa paggawa ng mga piyesa. Ang isang butas o lukab ay nilikha sa pamamagitan ng pagbubutas sa ibabaw ng piraso ng trabaho nang hindi lumalagpas dito. Pakitandaan na ang pagbubutas ay iba kaysa sa pagbabarena na nagreresulta sa isang through hole. • HOBBING : Ang isang suntok na may nais na geometry ay pinindot sa work piece at lumilikha ng isang lukab na may nais na hugis. Tinatawag naming HOB ang suntok na ito. Ang operasyon ay nagsasangkot ng mataas na presyon at isinasagawa sa malamig. Bilang isang resulta, ang materyal ay malamig na nagtrabaho at pinatigas. Samakatuwid ang prosesong ito ay napaka-angkop para sa pagmamanupaktura ng mga hulma, mamatay at mga lukab para sa iba pang mga proseso ng pagmamanupaktura. Kapag ang hob ay ginawa na, ang isa ay madaling makagawa ng maraming magkakahawig na mga cavity nang hindi na kailangang i-machine ang mga ito nang isa-isa. • ROLL FORGING o ROLL FORMING : Dalawang magkasalungat na rolyo ang ginagamit upang hubugin ang bahaging metal. Ang piraso ng trabaho ay pinapakain sa mga rolyo, ang mga rolyo ay umiikot at hinihila ang trabaho sa puwang, ang trabaho ay pagkatapos ay pinapakain sa pamamagitan ng ukit na bahagi ng mga rolyo at ang mga puwersa ng compressive ay nagbibigay sa materyal ng nais nitong hugis. Ito ay hindi isang rolling process ngunit isang forging process, dahil ito ay isang discrete sa halip na isang tuluy-tuloy na operasyon. Ang geometry sa mga roll groves ay nagpapanday ng materyal sa kinakailangang hugis at geometry. Ito ay ginanap na mainit. Dahil sa pagiging isang proseso ng forging, gumagawa ito ng mga piyesa na may natatanging mekanikal na katangian at samakatuwid ay ginagamit namin ito para sa manufacturing ng mga bahagi ng automotive tulad ng mga shaft na kailangang magkaroon ng pambihirang tibay sa mahihirap na kapaligiran sa trabaho. • ORBITAL FORGING : Ang piraso ng trabaho ay inilalagay sa isang forging die cavity at pineke ng isang upper die na naglalakbay sa isang orbital path habang ito ay umiikot sa isang inclined axis. Sa bawat rebolusyon, ang upper die ay kumpletuhin ang pagsasagawa ng compressive forces sa buong work piece. Sa pamamagitan ng pag-uulit ng mga rebolusyong ito ng ilang beses, sapat na ang pagpapanday ay ginaganap. Ang mga bentahe ng pamamaraan ng pagmamanupaktura na ito ay ang mababang operasyon ng ingay at mas mababang puwersa na kinakailangan. Sa madaling salita na may maliliit na pwersa ay maaaring umikot ang isang mabigat na die sa paligid ng isang axis upang maglapat ng malalaking pressure sa isang seksyon ng work piece na nakikipag-ugnayan sa die. Ang mga bahagi ng disc o conical na hugis ay kung minsan ay angkop para sa prosesong ito. • RING FORGING : Madalas naming ginagamit sa paggawa ng mga seamless ring. Ang stock ay pinuputol sa haba, nabalisa at pagkatapos ay tinusok hanggang sa makalikha ng gitnang butas. Pagkatapos ito ay ilagay sa isang mandrel at isang forging die martilyo ito mula sa itaas habang ang singsing ay dahan-dahang pinaikot hanggang sa makuha ang nais na mga sukat. • RIVETING : Ang isang karaniwang proseso para sa pagsali sa mga bahagi, ay nagsisimula sa isang tuwid na piraso ng metal na ipinasok sa mga paunang ginawang butas sa pamamagitan ng mga bahagi. Pagkatapos nito, ang dalawang dulo ng piraso ng metal ay huwad sa pamamagitan ng pagpiga sa magkasanib na pagitan ng upper at lower die. • COINING : Isa pang tanyag na proseso na isinagawa sa pamamagitan ng mekanikal na pagpindot, na nagbibigay ng malalaking puwersa sa isang maikling distansya. Ang pangalang "coining" ay nagmula sa mga magagandang detalye na napeke sa ibabaw ng mga metal na barya. Ito ay halos isang proseso ng pagtatapos para sa isang produkto kung saan ang mga pinong detalye ay nakukuha sa mga ibabaw bilang resulta ng malaking puwersa na inilapat ng die na naglilipat ng mga detalyeng ito sa work piece. • METAL BALL FORGING : Ang mga produkto tulad ng ball bearings ay nangangailangan ng mataas na kalidad na tumpak na gawang metal na mga bola. Sa isang pamamaraan na tinatawag na SKEW ROLLING, gumagamit kami ng dalawang magkasalungat na roll na patuloy na umiikot habang ang stock ay patuloy na ipinapasok sa mga roll. Sa isang dulo ng dalawang rolyo ay inilalabas ang mga metal sphere bilang produkto. Ang pangalawang paraan para sa pag-forging ng metal ball ay ang paggamit ng die na pumipiga sa materyal na stock na inilagay sa pagitan ng mga ito na kumukuha ng spherical na hugis ng mold cavity. Kadalasan ang mga bola na ginawa ay nangangailangan ng ilang karagdagang mga hakbang tulad ng pagtatapos at pagpapakintab upang maging isang de-kalidad na produkto. • ISOTHERMAL FORGING / HOT DIE FORGING : Isang mamahaling proseso na ginagawa lamang kapag nabigyang-katwiran ang halaga ng benepisyo / gastos. Isang mainit na proseso ng pagtatrabaho kung saan ang die ay pinainit sa halos kaparehong temperatura ng work piece. Dahil ang parehong mamatay at trabaho ay halos parehong temperatura, walang paglamig at ang mga katangian ng daloy ng metal ay napabuti. Ang operasyon ay angkop para sa mga sobrang haluang metal at materyales na may mababang kakayahang ma-forge at mga materyales na ang mga mekanikal na katangian ay napakasensitibo sa maliliit na gradient ng temperatura at mga pagbabago. • METAL SIZING : Ito ay isang malamig na proseso ng pagtatapos. Ang daloy ng materyal ay hindi pinaghihigpitan sa lahat ng direksyon maliban sa direksyon kung saan inilalapat ang puwersa. Bilang isang resulta, ang napakahusay na pagtatapos sa ibabaw at tumpak na mga sukat ay nakuha. • HIGH ENERGY RATE FORGING : Ang pamamaraan ay nagsasangkot ng pang-itaas na amag na nakakabit sa braso ng isang piston na mabilis na tinutulak habang ang pinaghalong gasolina-hangin ay sinindihan ng isang spark plug. Ito ay kahawig ng pagpapatakbo ng mga piston sa isang makina ng kotse. Ang amag ay tumama sa work piece nang napakabilis at pagkatapos ay bumalik sa orihinal nitong posisyon nang napakabilis salamat sa backpressure. Ang trabaho ay pineke sa loob ng ilang millisecond at samakatuwid ay walang oras para lumamig ang trabaho. Ito ay kapaki-pakinabang para sa mahirap na huwad na mga bahagi na may napaka-sensitibong temperatura na mga mekanikal na katangian. Sa madaling salita ang proseso ay napakabilis na ang bahagi ay nabuo sa ilalim ng pare-parehong temperatura sa kabuuan at ang hindi magkakaroon ng mga gradient ng temperatura sa mga interface ng mold/work piece. • Sa DIE FORGING, ang metal ay pinalo sa pagitan ng dalawang magkatugmang bakal na bloke na may mga espesyal na hugis sa mga ito, na tinatawag na dies. Kapag ang metal ay na-hammered sa pagitan ng mga dies, ipinapalagay nito ang parehong hugis tulad ng mga hugis sa die. Kapag naabot na nito ang huling hugis, inilalabas ito upang lumamig. Ang prosesong ito ay gumagawa ng matitibay na bahagi na may tumpak na hugis, ngunit nangangailangan ng mas malaking pamumuhunan para sa mga dalubhasang dies. Pinapataas ng upset forging ang diameter ng isang piraso ng metal sa pamamagitan ng pag-flatte nito. Ito ay karaniwang ginagamit upang gumawa ng maliliit na bahagi, lalo na upang bumuo ng mga ulo sa mga fastener tulad ng bolts at pako. • POWDER METALLURGY / POWDER PROCESSING : Gaya ng ipinahihiwatig ng pangalan, kinapapalooban nito ang mga proseso ng pagmamanupaktura para sa paggawa ng mga solidong bahagi ng ilang geometries at mga hugis mula sa mga pulbos. Kung ang mga metal na pulbos ay ginagamit para sa layuning ito ito ay ang larangan ng metalurhiya ng pulbos at kung ang mga di-metal na pulbos ay ginagamit ito ay ang pagproseso ng pulbos. Ang mga solidong bahagi ay ginawa mula sa mga pulbos sa pamamagitan ng pagpindot at sintering. Ang POWDER PRESSING ay ginagamit upang i-compact ang mga pulbos sa nais na hugis. Una, ang pangunahing materyal ay pisikal na pulbos, na hinahati ito sa maraming maliliit na indibidwal na mga particle. Ang pinaghalong pulbos ay pinupuno sa die at ang isang suntok ay gumagalaw patungo sa pulbos at pinupuno ito sa nais na hugis. Karamihan ay ginaganap sa temperatura ng silid, na may pulbos na pagpindot sa isang solidong bahagi ay nakuha at ito ay tinatawag na berdeng compact. Ang mga binder at lubricant ay karaniwang ginagamit upang mapahusay ang pagiging compact. Kami ay may kakayahang bumuo ng powder press gamit ang hydraulic presses na may ilang libong toneladang kapasidad. Mayroon din kaming dobleng pagpindot sa aksyon na may magkasalungat na mga suntok sa itaas at ibaba pati na rin ang maraming mga pagpindot sa aksyon para sa napakasalimuot na mga geometrie ng bahagi. Ang pagkakapareho na isang mahalagang hamon para sa maraming powder metalurgy / powder processing plant ay hindi malaking problema para sa AGS-TECH dahil sa aming malawak na karanasan sa custom na pagmamanupaktura ng mga naturang bahagi sa loob ng maraming taon. Kahit na may mas makapal na bahagi kung saan ang pagkakapareho ay nagdudulot ng hamon, nagtagumpay kami. Kung ibibigay namin ang iyong proyekto, gagawin namin ang iyong mga bahagi. Kung makakita kami ng anumang potensyal na panganib, ipapaalam namin sa iyo sa advance. Ang POWDER SINTERING, na siyang pangalawang hakbang, ay nagsasangkot ng pagtaas ng temperatura sa isang tiyak na antas at pagpapanatili ng temperatura sa antas na iyon para sa isang tiyak na oras upang ang mga particle ng pulbos sa pinindot na bahagi ay magkadikit. Nagreresulta ito sa mas malakas na mga bono at pagpapalakas ng work piece. Nagaganap ang sintering malapit sa temperatura ng pagkatunaw ng pulbos. Sa panahon ng sintering, ang pag-urong ay magaganap, ang lakas ng materyal, density, ductility, thermal conductivity, electrical conductivity ay nadagdagan. Mayroon kaming mga batch at tuloy-tuloy na furnace para sa sintering. Ang isa sa aming mga kakayahan ay ang pagsasaayos ng antas ng porosity ng mga bahagi na aming ginagawa. Halimbawa, nakakagawa kami ng mga metal na filter sa pamamagitan ng pagpapanatiling buhaghag ang mga bahagi sa ilang antas. Gamit ang isang pamamaraan na tinatawag na IMPREGNATION, pinupuno namin ang mga pores sa metal ng isang likido tulad ng langis. Gumagawa kami halimbawa ng oil impregnated bearings na self-lubricating. Sa proseso ng INFILTRATION, pinupuno namin ang mga pores ng metal ng isa pang metal na mas mababa ang temperatura ng pagkatunaw kaysa sa base material. Ang halo ay pinainit sa isang temperatura sa pagitan ng mga temperatura ng pagkatunaw ng dalawang metal. Bilang isang resulta, ang ilang mga espesyal na katangian ay maaaring makuha. Madalas din kaming nagsasagawa ng mga pangalawang operasyon tulad ng pagmachining at pag-forging sa mga bahaging gawa sa pulbos kapag kailangang makuha ang mga espesyal na katangian o katangian o kapag ang bahagi ay maaaring gawin nang may mas kaunting mga hakbang sa proseso. ISOSTATIC PRESSING : Sa prosesong ito, ang fluid pressure ay ginagamit para i-compact ang bahagi. Ang mga metal na pulbos ay inilalagay sa isang amag na gawa sa isang selyadong nababaluktot na lalagyan. Sa isostatic pressing, ang presyon ay inilalapat mula sa lahat sa paligid, salungat sa axial pressure na nakikita sa conventional pressing. Ang mga bentahe ng isostatic pressing ay pare-parehong density sa loob ng bahagi, lalo na para sa mas malaki o mas makapal na mga bahagi, higit na mataas na mga katangian. Ang kawalan nito ay mahaba ang mga oras ng pag-ikot at medyo mababa ang mga geometric na katumpakan. Ang COLD ISOSTATIC PRESSING ay isinasagawa sa temperatura ng silid at ang nababaluktot na amag ay gawa sa goma, PVC o urethane o mga katulad na materyales. Ang likidong ginagamit para sa pagpindot at pagsiksik ay langis o tubig. Ang conventional sintering ng green compact ay sumusunod dito. Ang HOT ISOSTATIC PRESSING sa kabilang banda ay isinasagawa sa mataas na temperatura at ang materyal ng amag ay sheet metal o ceramic na may sapat na mataas na punto ng pagkatunaw na lumalaban sa mga temperatura. Ang pressureurizing fluid ay karaniwang isang inert gas. Ang mga operasyon ng pagpindot at sintering ay isinasagawa sa isang hakbang. Ang porosity ay halos ganap na naalis, isang uniform grain na istraktura ay nakuha. Ang bentahe ng mainit na isostatic pressing ay na ito ay makagawa ng mga bahagi na maihahambing sa paghahagis at pag-forging na pinagsama habang ginagawa ang mga materyales na hindi angkop para sa paghahagis at pag-forging na posibleng magamit. Ang kawalan ng mainit na isostatic pressing ay ang mataas na cycle ng oras nito at samakatuwid ay nagkakahalaga. Ito ay angkop para sa mga kritikal na bahagi ng mababang volume. METAL INJECTION MOLDING : Napaka-angkop na proseso para sa paggawa ng mga kumplikadong bahagi na may manipis na pader at detalyadong geometries. Ang pinaka-angkop para sa mas maliliit na bahagi. Ang mga pulbos at polymer binder ay halo-halong, pinainit at iniksyon sa isang amag. Binabalot ng polymer binder ang mga ibabaw ng mga particle ng pulbos. Pagkatapos ng paghubog, ang panali ay tinanggal sa pamamagitan ng alinman sa mababang temperatura na pag-init ng natunaw gamit ang isang solvent. ROLL COMPACTION / POWDER ROLLING : Ang mga pulbos ay ginagamit upang makagawa ng tuluy-tuloy na mga piraso o sheet. Ang pulbos ay pinapakain mula sa isang feeder at sinisiksik ng dalawang umiikot na roll sa sheet o strips. Ang operasyon ay isinasagawa sa malamig. Ang sheet ay dinadala sa isang sintering furnace. Ang proseso ng sintering ay maaaring ulitin sa pangalawang pagkakataon. POWDER EXTRUSION : Ang mga bahagi na may malalaking ratio ng haba sa diameter ay ginawa sa pamamagitan ng pag-extrude ng isang manipis na lalagyan ng metal na may pulbos. LOOSE SINTERING : Gaya ng ipinahihiwatig ng pangalan, ito ay isang walang pressure na compaction at sintering na paraan, na angkop para sa paggawa ng napakabuhaghag na bahagi tulad ng mga metal na filter. Ang pulbos ay ipinapasok sa lukab ng amag nang hindi kumusiksik. LOOSE SINTERING : Gaya ng ipinahihiwatig ng pangalan, ito ay isang walang pressure na compaction at sintering na paraan, na angkop para sa paggawa ng napakabuhaghag na bahagi tulad ng mga metal na filter. Ang pulbos ay ipinapasok sa lukab ng amag nang hindi kumusiksik. SPARK SINTERING : Ang pulbos ay pinipiga sa amag sa pamamagitan ng dalawang magkasalungat na suntok at isang mataas na kapangyarihan na electric current ay inilapat sa suntok at dumadaan sa compacted powder na nasa pagitan ng mga ito. Ang mataas na agos ay sumusunog sa mga pelikula sa ibabaw mula sa mga particle ng pulbos at sinasala ang mga ito sa init na nabuo. Ang proseso ay mabilis dahil ang init ay hindi inilapat mula sa labas ngunit ito ay nabuo mula sa loob ng amag. HOT PRESSING : Ang mga pulbos ay pinindot at sintered sa isang hakbang sa isang amag na makatiis sa mataas na temperatura. Habang ang die ay siksik, ang init ng pulbos ay inilalapat dito. Ang mahusay na mga katumpakan at mekanikal na katangian na nakamit ng pamamaraang ito ay ginagawa itong isang kaakit-akit na pagpipilian. Kahit na ang mga refractory metal ay maaaring iproseso sa pamamagitan ng paggamit ng mga materyales sa amag tulad ng grapayt. CLICK Product Finder-Locator Service DATING MENU
- Sheet Metal Forming Fabrication, Stamping, Punching, Deep Drawing, CNC
Sheet Metal Forming and Fabrication, Stamping, Punching, Bending, Progressive Die, Spot Welding, Deep Drawing, Metal Blanking and Slitting at AGS-TECH Inc. Stamping at Sheet Metal Fabrication Nag-aalok kami ng sheet metal stamping, paghubog, pagbubuo, pagbaluktot, pagsuntok, pagbabalanko, paghiwa, pagbubutas, pagbingaw, pag-ahit, pag-ahit, pagpindot, paggawa, malalim na pagguhit gamit ang single punch / single stroke dies gayundin ang mga progressive dies at spinning, rubber forming at hydroforming; pagputol ng sheet metal gamit ang water jet, plasma, laser, saw, apoy; sheet metal assembly gamit ang welding, spot welding; sheet metal tube nakaumbok at baluktot; sheet metal surface finishing kabilang ang dip o spray painting, electrostatic powder coating, anodizing, plating, sputtering at higit pa. Ang aming mga serbisyo ay mula sa mabilis na sheet metal prototyping hanggang sa paggawa ng mataas na volume. Inirerekomenda namin na mag-click ka dito upangI-DOWNLOAD ang aming Schematic Illustrations ng Sheet Metal Fabrication and Stamping Processes ng AGS-TECH Inc. Makakatulong ito sa iyo na mas maunawaan ang impormasyong ibinibigay namin sa iyo sa ibaba. • SHEET METAL CUTTING : Nag-aalok kami ng CUTOFFS at PARTINGS. Pinutol ng mga cutoff ang sheet metal sa isang landas sa isang pagkakataon at sa pangkalahatan ay walang pag-aaksaya ng materyal, samantalang sa mga paghihiwalay ang hugis ay hindi maaaring ilagay nang tumpak at samakatuwid ay nasasayang ang ilang partikular na halaga ng materyal. Isa sa aming pinakasikat na proseso ay PUNCHING, kung saan ang isang piraso ng materyal na bilog o iba pang hugis ay pinutol mula sa sheet na metal. Ang piraso na pinutol ay basura. Ang isa pang bersyon ng pagsuntok ay SLOTTING, kung saan ang mga hugis-parihaba o pahabang butas ay nasusuntok. BLANKING sa kabilang banda ay ang parehong proseso ng pagsuntok, na may pagkakaiba sa piraso na pinutol ay ang trabaho at itinatago. Ang FINE BLANKING, isang superior na bersyon ng blanking, ay lumilikha ng mga cut na may malapit na tolerance at tuwid na makinis na mga gilid at hindi nangangailangan ng pangalawang operasyon para sa pagiging perpekto ng workpiece. Ang isa pang proseso na madalas naming ginagamit ay ang SLITTING, na isang proseso ng paggugupit kung saan ang sheet metal ay pinuputol ng dalawang magkasalungat na circular blades sa isang tuwid o hubog na landas. Ang opener ng lata ay isang simpleng halimbawa ng proseso ng slitting. Ang isa pang sikat na process para sa amin ay PERFORATING, kung saan maraming butas na bilog o iba pang hugis ang nasusuntok sa sheet metal sa isang tiyak na pattern. Ang karaniwang halimbawa para sa isang butas-butas na produkto ay ang mga metal na filter na may maraming butas para sa mga likido. Sa NOTCHING, isa pang proseso ng paggupit ng sheet metal, inaalis namin ang materyal mula sa isang piraso ng trabaho, simula sa gilid o sa ibang lugar at pinuputol papasok hanggang sa makuha ang nais na hugis. Ito ay isang progresibong proseso kung saan ang bawat operasyon ay nag-aalis ng isa pang piraso hanggang sa makuha ang nais na tabas. Para sa maliliit na pagpapatakbo ng produksyon, minsan ay gumagamit kami ng medyo mas mabagal na proseso na tinatawag na NIBBLING na binubuo ng maraming mabilis na suntok ng magkakapatong na mga butas upang makagawa ng mas malaking mas kumplikadong hiwa. Sa PROGRESSIVE CUTTING gumagamit kami ng isang serye ng iba't ibang mga operasyon upang makakuha ng isang solong hiwa o isang tiyak na geometry. Sa wakas, ang pag-ahit ng pangalawang proseso ay tumutulong sa amin na mapabuti ang mga gilid ng mga hiwa na nagawa na. Ito ay ginagamit para sa pagputol ng mga chips, magaspang na mga gilid sa sheet metal work. • SHEET METAL BENDING : Bukod sa pagputol, ang pagbaluktot ay isang mahalagang proseso kung wala ito hindi tayo makakagawa ng karamihan sa mga produkto. Kadalasan ay isang malamig na operasyon ngunit kung minsan ay ginagawa din kapag mainit o mainit. Gumagamit kami ng mga dies at madalas na pinindot para sa operasyong ito. Sa PROGRESSIVE BENDING gumagamit kami ng serye ng iba't ibang operasyon ng punch at die para makakuha ng isang liko o isang partikular na geometry. Gumagamit ang AGS-TECH ng iba't ibang proseso ng baluktot at gumagawa ng pagpili depende sa materyal ng workpiece, laki nito, kapal, nais na laki ng liko, radius, kurbada at anggulo ng liko, lokasyon ng liko, ekonomiya ng operasyon, dami na gagawin... atbp. Gumagamit kami ng V-BENDING kung saan pinipilit ng isang hugis V na suntok ang sheet metal sa hugis V na die at ibaluktot ito. Mabuti para sa parehong napakatalim at malabo na mga anggulo at sa pagitan, kabilang ang 90 degrees. Gamit ang wiping dies nagsasagawa kami ng EDGE BENDING. Ang aming kagamitan ay nagbibigay-daan sa amin na makakuha ng mga anggulo na mas malaki pa sa 90 degrees. Sa edge bending, ang workpiece ay na-sandwich sa pagitan ng pressure pad at die, ang lugar para sa bending ay matatagpuan sa die edge at ang natitirang bahagi ng workpiece ay nakahawak sa space like a cantilever beam. Kapag ang suntok ay kumilos sa bahagi ng cantilever, ito ay nakatungo sa gilid ng die. Ang FLANGING ay isang proseso ng pagbaluktot sa gilid na nagreresulta sa isang 90 degree na anggulo. Ang mga pangunahing layunin ng operasyon ay ang pag-aalis ng matutulis na mga gilid at pagkuha ng mga geometric na ibabaw upang mapagaan ang pagsasama ng mga bahagi. BEADING, isa pang karaniwang proseso ng pagbaluktot sa gilid ay bumubuo ng isang kulot sa gilid ng isang bahagi. Ang HEMMING sa kabilang banda ay nagreresulta sa isang gilid ng sheet na ganap na nakatungo sa sarili nito. Sa SEAMING, ang mga gilid ng dalawang bahagi ay nakatungo sa isa't isa at pinagdugtong. Ang DOUBLE SEAMING sa kabilang banda ay nagbibigay ng hindi tinatagusan ng tubig at airtight sheet metal joints. Katulad ng pagbaluktot sa gilid, ang prosesong tinatawag na ROTARY BENDING ay nagde-deploy ng cylinder na may gustong anggulo na gupitin at nagsisilbing suntok. Habang ang puwersa ay ipinapadala sa suntok, nagsasara ito sa workpiece. Ang uka ng silindro ay nagbibigay sa bahagi ng cantilever ng nais na anggulo. Ang uka ay maaaring magkaroon ng isang anggulo na mas maliit o mas malaki kaysa sa 90 degrees. Sa AIR BENDING, hindi natin kailangan ang lower die para magkaroon ng angled groove. Ang sheet metal ay sinusuportahan ng two surface sa magkabilang panig at sa isang tiyak na distansya. Ang suntok ay naglalapat ng puwersa sa tamang lokasyon at yumuko sa workpiece. Ang CHANNEL BENDING ay ginagawa gamit ang isang channel na hugis suntok at mamatay, at ang U-BEND ay nakakamit gamit ang isang hugis-U na suntok. Ang OFFSET BENDING ay gumagawa ng mga offset sa sheet metal. Ang ROLL BENDING, isang pamamaraan na mahusay para sa makapal na trabaho at pagyuko ng malalaking piraso ng metal plate, ay gumagamit ng tatlong roll upang pakainin at ibaluktot ang mga plato sa nais na mga kurbada. Ang mga roll ay nakaayos upang ang nais na liko ng trabaho ay makuha. Ang distansya at anggulo sa pagitan ng mga rolyo ay kinokontrol upang makuha ang nais na kinalabasan. Ginagawang posible ng nagagalaw na roll na kontrolin ang kurbada. Ang TUBE FORMING ay isa pang sikat na sheet metal bending operation na kinasasangkutan ng maraming dies. Ang mga tubo ay nakuha pagkatapos ng maraming pagkilos. Ang CORRUGATION ay ginagawa rin sa pamamagitan ng mga operasyong baluktot. Karaniwang ito ay ang simetriko na baluktot sa mga regular na pagitan sa isang buong piraso ng sheet metal. Maaaring gamitin ang iba't ibang mga hugis para sa corrugating. Ang corrugated sheet metal ay mas matibay at may mas mahusay na pagtutol laban sa baluktot at samakatuwid ay may mga aplikasyon sa industriya ng konstruksiyon. SHEET METAL ROLL FORMING, isang tuluy-tuloy na manufacturing na proseso ay naka-deploy upang yumuko ang mga cross section ng isang partikular na geometry gamit ang mga rolyo at ang trabaho ay nakabaluktot sa sunud-sunod na mga hakbang, kasama ang huling roll na kumukumpleto sa trabaho. Sa ilang mga kaso isang solong roll at sa ilang mga kaso isang serye ng mga roll ay ginagamit. • SHEET METAL CUTTING & BENDING PROCESSES : Ito ang mga prosesong naghihiwa at yumuko nang sabay. Sa PIERCING, isang butas ang nilikha gamit ang isang matulis na suntok. Habang pinapalawak ng suntok ang butas sa sheet, ang materyal ay sabay na baluktot sa isang panloob na flange para sa butas. Ang flange na nakuha ay maaaring may mahahalagang function. Ang operasyon ng LANCING sa kabilang banda ay pinuputol at binabaluktot ang sheet upang lumikha ng isang nakataas na geometry. • METAL TUBE BULGING AND BENDING : Sa BULGING ang ilang panloob na bahagi ng hollow tube ay may pressure, na nagiging sanhi ng pag-umbok ng tubo palabas. Dahil ang tubo ay nasa loob ng isang die, ang bulge geometry ay kinokontrol ng hugis ng die. Sa STRETCH BENDING, ang isang metal na tubo ay nakaunat gamit ang mga puwersang parallel sa axis ng tubo at mga puwersa ng baluktot upang hilahin ang tubo sa ibabaw ng isang form block. Sa DRAW BENDING, ikinakapit namin ang tubo malapit sa dulo nito sa isang umiikot na form block na nakayuko sa tubo habang umiikot. Panghuli, sa COMPRESSION BENDING ang tubo ay pinipigilan ng puwersa sa isang nakapirming form block, at ang isang die ay nakayuko sa ibabaw ng form block. • DEEP DRAWING : Sa isa sa aming pinakasikat na operasyon, isang suntok, isang katugmang die at isang blangko na may hawak ang ginagamit. Ang sheet metal na blangko ay inilalagay sa ibabaw ng die opening at ang suntok ay gumagalaw patungo sa blangko na hawak ng blank holder. Sa sandaling magkadikit ang mga ito, pinipilit ng suntok ang sheet metal sa die cavity upang mabuo ang produkto. Ang malalim na operasyon ng pagguhit ay kahawig ng pagputol, gayunpaman ang clearance sa pagitan ng suntok at mamatay ay pumipigil sa sheet na maputol. Ang isa pang kadahilanan sa pagtiyak na ang sheet ay malalim na iginuhit at hindi pinutol ay ang mga bilugan na sulok sa die at suntok na pumipigil sa paggugupit at pagputol. Upang makamit ang isang mas malaking magnitude ng malalim na pagguhit, isang proseso ng PAG-REDRAWING ay inilalagay kung saan ang isang kasunod na malalim na pagguhit ay nagaganap sa isang bahagi na sumailalim na sa isang malalim na proseso ng pagguhit. Sa REVERSE REDRAWING, ang malalim na iginuhit na bahagi ay binabaligtad at iginuhit sa kabilang direksyon. Ang malalim na pagguhit ay maaaring magbigay ng hindi regular na hugis na mga bagay tulad ng domed, tapered o stepped cups, Sa EMBOSSING gumagamit kami ng pares ng die na lalaki at babae upang mapabilib ang sheet metal na may disenyo o script. • SPINNING : Isang operasyon kung saan ang flat o preformed na workpiece ay inilalagay sa pagitan ng umiikot na mandrel at tail stock at ang isang tool ay naglalapat ng localized pressure sa trabaho habang unti-unti itong umaangat sa mandrel. Bilang isang resulta, ang workpiece ay nakabalot sa mandrel at kinuha ang hugis nito. Ginagamit namin ang diskarteng ito bilang isang alternatibo sa malalim na pagguhit kung saan ang dami ng isang order ay maliit, ang mga bahagi ay malalaki (mga diameter hanggang 20 talampakan) at may mga kakaibang kurba. Kahit na ang mga presyo ng bawat piraso ay karaniwang mas mataas, ang mga gastos sa set-up para sa operasyon ng pag-ikot ng CNC ay mababa kumpara sa malalim na pagguhit. Sa kabaligtaran, ang malalim na pagguhit ay nangangailangan ng mataas na paunang puhunan para sa pag-set-up, ngunit ang mga gastos sa bawat piraso ay mababa kapag ang mataas na dami ng mga bahagi ay ginawa. Ang isa pang bersyon ng prosesong ito ay SHEAR SPINNING, kung saan mayroon ding daloy ng metal sa loob ng workpiece. Ang daloy ng metal ay magbabawas sa kapal ng workpiece habang isinasagawa ang proseso. Ang isa pang kaugnay na proseso ay TUBE SPINNING, na inilalapat sa mga cylindirical na bahagi. Gayundin sa prosesong ito mayroong daloy ng metal sa loob ng workpiece. Ang kapal ay kaya nabawasan at ang haba ng tubo ay nadagdagan. Maaaring ilipat ang tool upang lumikha ng mga tampok sa loob o labas ng tubo. • PAGBUO NG RUBBER NG SHEET METAL : Ang goma o polyurethane na materyal ay inilalagay sa isang lalagyan ng die at ang piraso ng trabaho ay inilalagay sa ibabaw ng goma. Ang isang suntok ay pagkatapos ay kumilos sa work piece at pinipilit ito sa goma. Dahil ang presyon na nabuo ng goma ay mababa, ang lalim ng mga bahagi na ginawa ay limitado. Dahil mababa ang mga gastos sa tooling, ang proseso ay angkop para sa mababang dami ng produksyon. • HYDROFORMING : Katulad ng pagbubuo ng goma, sa prosesong ito, ang sheet metal work ay dinidiin ng suntok sa isang may presyon na likido sa loob ng isang silid. Ang sheet metal na gawa ay na-sandwich sa pagitan ng suntok at isang rubber diaphragm. Ang diaphragm ay ganap na pumapalibot sa workpiece at ang presyon ng likido ay pumipilit na mabuo ito sa suntok. Napakalalim na pagguhit kahit na mas malalim kaysa sa malalim na proseso ng pagguhit ay maaaring makuha sa pamamaraang ito. Gumagawa kami ng single-punch dies pati na rin ang progessive dies depende sa iyong bahagi. Ang single stroke stamping dies ay isang cost-effective na paraan para sa paggawa ng malalaking dami ng simpleng sheet metal parts gaya ng washers nang mabilis. Ang mga progresibong dies o ang deep drawing technique ay ginagamit para sa paggawa ng mas kumplikadong geometries. Depende sa iyong kaso, maaaring gamitin ang waterjet, laser o plasma cutting upang makagawa ng iyong mga bahagi ng sheet metal nang mura, mabilis at tumpak. Maraming mga supplier ang walang ideya tungkol sa mga alternatibong pamamaraan na ito o wala nito at samakatuwid dumaan sila sa mahaba at mamahaling paraan ng paggawa ng mga dies at mga tool na nag-aaksaya lamang ng oras at pera ng mga customer. Kung kailangan mo ng custom built sheet metal na mga bahagi tulad ng mga enclosure, electronic housing...at iba pa nang kasing bilis sa loob ng ilang araw, pagkatapos ay makipag-ugnayan sa amin para sa aming serbisyo ng RAPID SHEET METAL PROTOTYPING. CLICK Product Finder-Locator Service DATING MENU
- Casting and Machined Parts, CNC Manufacturing, Milling, Turning, Swiss
Casting and Machined Parts, CNC Manufacturing, Milling, Turning, Swiss Type Machining, Die Casting, Investment Casting, Lost Foam Cast Parts from AGS-TECH Inc. Casting at Machining Ang aming custom na casting at machining techniques ay expendable at non-expendable casting, ferrous at nonferrous casting, sand, die, centrifugal, continuous, ceramic mold, investment, lost foam, near-net-shape, permanent mold (gravity die casting), plaster mold (plaster casting) at shell casting, machined parts na ginawa sa pamamagitan ng milling at turning gamit ang conventional pati na rin ang CNC equipment, swiss type machining para sa high throughput na murang maliliit na precision parts, screw machining para sa fasteners, non-conventional machining. Mangyaring tandaan na bukod sa mga metal at metal na haluang metal, kami ay gumagawa ng mga ceramic, salamin at plastik na mga bahagi pati na rin sa ilang mga kaso kapag ang paggawa ng amag ay hindi kaakit-akit o hindi ang opsyon. Ang pagma-machine ng mga polymer na materyales ay nangangailangan ng espesyal na karanasan na mayroon kami dahil sa hamon ng mga plastik at goma na regalo dahil sa kanilang lambot, hindi tigas...atbp. Para sa machining ng ceramic at salamin, mangyaring tingnan ang aming pahina sa Non-Conventional Fabrication. Gumagawa at nagbibigay ng parehong magaan at mabibigat na casting ang AGS-TECH Inc. Nagsusuplay kami ng mga metal casting at machined parts para sa mga boiler, heat exchanger, sasakyan, micromotors, wind turbine, food packaging equipment at higit pa. Inirerekomenda namin na mag-click ka dito sa I-DOWNLOAD ang aming Schematic Illustrations ng Machining at Casting Processes ng AGS-TECH Inc. Makakatulong ito sa iyo na mas maunawaan ang impormasyong ibinibigay namin sa iyo sa ibaba. Tingnan natin ang ilan sa iba't ibang mga diskarte na inaalok namin nang detalyado: • MABIBIGAY NA PAGHATAG NG MOLDA : Ang malawak na kategoryang ito ay tumutukoy sa mga pamamaraan na may kasamang pansamantala at hindi magagamit muli na mga amag. Ang mga halimbawa ay buhangin, plaster, shell, investment (tinatawag ding lost-wax) at plaster casting. • SAND CASTING : Isang proseso kung saan ginagamit ang buhangin bilang materyal ng amag. Isang napakalumang pamamaraan at napakapopular pa rin hanggang sa ang karamihan sa mga metal castings na ginawa ay ginawa ng pamamaraang ito. Mababang gastos kahit na sa mababang dami ng produksyon. Angkop para sa paggawa ng maliliit at malalaking bahagi. Ang pamamaraan ay maaaring gamitin sa paggawa ng mga bahagi sa loob ng mga araw o linggo na may napakakaunting pamumuhunan. Ang basa-basa na buhangin ay pinagsama-sama gamit ang luad, mga binder o mga espesyal na langis. Karaniwang nakapaloob ang buhangin sa mga kahon ng amag at ang cavity at gate system ay ginagawa sa pamamagitan ng pagdikit ng buhangin sa paligid ng mga modelo. Ang mga proseso ay: 1.) Paglalagay ng modelo sa buhangin para gawin ang amag 2.) Pagsasama ng modelo at buhangin sa isang gating system 3.) Pag-alis ng modelo 4.) Pagpuno ng mold cavity ng tinunaw na metal 5.) Paglamig ng metal 6.) Pagbasag ng amag ng buhangin at pagtanggal ng paghahagis • PLASTER MOLD CASTING : Katulad ng sand casting, at sa halip na buhangin, plaster of paris ang ginagamit bilang mold material. Maiikling oras ng produksyon tulad ng sand casting at mura. Magandang dimensional tolerances at surface finish. Ang pangunahing kawalan nito ay maaari lamang itong gamitin sa mababang tuldok ng pagkatunaw ng mga metal tulad ng aluminyo at sink. • SHELL MOLD CASTING : Katulad din ng sand casting. Mould cavity na nakuha ng matigas na shell ng buhangin at thermosetting resin binder sa halip na flask na puno ng buhangin tulad ng sa proseso ng sand casting. Halos anumang metal na angkop na i-cast sa pamamagitan ng buhangin ay maaaring i-cast sa pamamagitan ng shell molding. Ang proseso ay maaaring i-summarize bilang: 1.) Paggawa ng shell mold. Ang buhangin na ginamit ay may mas maliit na laki ng butil kung ihahambing sa buhangin na ginamit sa paghahagis ng buhangin. Ang pinong buhangin ay hinaluan ng thermosetting resin. Ang pattern ng metal ay pinahiran ng isang ahente ng paghihiwalay upang gawing mas madali ang pag-alis ng shell. Pagkatapos nito, ang metal pattern ay pinainit at ang pinaghalong buhangin ay binubutas o hinipan sa mainit na pattern ng paghahagis. Ang isang manipis na shell ay bumubuo sa ibabaw ng pattern. Ang kapal ng shell na ito ay maaaring iakma sa pamamagitan ng pag-iiba-iba sa haba ng oras na ang pinaghalong sand resin ay nakikipag-ugnayan sa pattern ng metal. Ang maluwag na buhangin ay aalisin nang may natitirang pattern na natatakpan ng shell. 2.) Susunod, ang shell at pattern ay pinainit sa isang oven upang ang shell ay tumigas. Matapos makumpleto ang hardening, ang shell ay ilalabas mula sa pattern gamit ang mga pin na nakapaloob sa pattern. 3.) Ang dalawang tulad na shell ay pinagsama-sama sa pamamagitan ng gluing o clamping at bumubuo sa kumpletong amag. Ngayon ang shell mold ay ipinasok sa isang lalagyan kung saan ito ay sinusuportahan ng buhangin o metal shot sa panahon ng proseso ng paghahagis. 4.) Ngayon ang mainit na metal ay maaaring ibuhos sa shell mold. Ang mga bentahe ng paghahagis ng shell ay mga produkto na may napakahusay na pagtatapos sa ibabaw, posibilidad ng paggawa ng mga kumplikadong bahagi na may mataas na katumpakan ng dimensyon, madaling i-automate ang proseso, matipid para sa produksyon ng malaking dami. Ang mga disadvantages ay ang mga hulma ay nangangailangan ng mahusay na bentilasyon dahil sa mga gas na nalikha kapag ang tinunaw na metal ay nakipag-ugnay sa kemikal ng binder, ang mga thermosetting resin at mga pattern ng metal ay mahal. Dahil sa gastos ng mga pattern ng metal, ang pamamaraan ay maaaring hindi angkop para sa mababang dami ng produksyon na tumatakbo. • INVESTMENT CASTING (kilala rin bilang LOST-WAX CASTING ): Isa ring napakalumang pamamaraan at angkop para sa paggawa ng mga de-kalidad na bahagi na may mataas na katumpakan, repeatability, versatility at integridad mula sa maraming metal, refractory na materyales at espesyal na high performance alloys. Maliit pati na rin ang malalaking sukat na bahagi ay maaaring gawin. Isang mamahaling proseso kung ihahambing sa ilan sa iba pang mga pamamaraan, ngunit ang pangunahing bentahe ay ang posibilidad na makagawa ng mga bahagi na may malapit na hugis ng net, masalimuot na mga contour at mga detalye. Kaya ang gastos ay medyo na-offset sa pamamagitan ng pag-aalis ng rework at machining sa ilang mga kaso. Kahit na maaaring mayroong mga pagkakaiba-iba, narito ang isang buod ng pangkalahatang proseso ng paghahagis ng pamumuhunan: 1.) Paglikha ng orihinal na master pattern mula sa wax o plastic. Ang bawat paghahagis ay nangangailangan ng isang pattern dahil ang mga ito ay nawasak sa proseso. Ang amag mula sa kung saan ang mga pattern ay ginawa ay kailangan din at karamihan sa mga oras na ang amag ay inihagis o machined. Dahil hindi kailangang buksan ang amag, maaaring makamit ang mga kumplikadong paghahagis, maraming mga pattern ng waks ang maaaring ikonekta tulad ng mga sanga ng isang puno at ibuhos nang magkasama, kaya pinapagana ang paggawa ng maraming bahagi mula sa isang pagbuhos ng metal o metal na haluang metal. 2.) Susunod, ang pattern ay isawsaw o ibinuhos ng isang refractory slurry na binubuo ng napaka-pinong butil na silica, tubig, mga binder. Nagreresulta ito sa isang ceramic layer sa ibabaw ng pattern. Ang refractory coat sa pattern ay naiwan upang matuyo at tumigas. Ang hakbang na ito ay kung saan nagmula ang pangalang investment casting: Ang refractory slurry ay inilalagay sa ibabaw ng wax pattern. 3.) Sa hakbang na ito, ang tumigas na ceramic mold ay nakabaligtad at pinainit upang ang wax ay matunaw at bumuhos sa molde. Ang isang lukab ay naiwan para sa paghahagis ng metal. 4.) Matapos mawala ang wax, ang ceramic mold ay pinainit sa mas mataas na temperatura na nagreresulta sa pagpapalakas ng molde. 5.) Ang paghahagis ng metal ay ibinubuhos sa mainit na amag na pinupuno ang lahat ng masalimuot na seksyon. 6.) Hinahayaang tumigas ang paghahagis 7.) Sa wakas ay nasira ang ceramic mold at ang mga manufactured parts ay pinutol mula sa puno. Narito ang isang link sa Investment Casting Plant Brochure • EVAPORATIVE PATTERN CASTING : Ang proseso ay gumagamit ng pattern na ginawa mula sa isang materyal tulad ng polystyrene foam na sumingaw kapag ang mainit na tinunaw na metal ay ibinuhos sa molde. Mayroong dalawang uri ng prosesong ito: LOST FOAM CASTING na gumagamit ng unbonded sand at FULL MOLD CASTING na gumagamit ng bonded sand. Narito ang mga pangkalahatang hakbang sa proseso: 1.) Gumawa ng pattern mula sa isang materyal tulad ng polystyrene. Kapag maraming dami ang gagawin, ang pattern ay hinuhubog. Kung ang bahagi ay may isang kumplikadong hugis, ilang mga seksyon ng naturang foam na materyal ay maaaring kailangang idikit nang magkasama upang mabuo ang pattern. Madalas naming pinahiran ang pattern ng isang refractory compound upang lumikha ng isang mahusay na pagtatapos sa ibabaw sa paghahagis. 2.) Ang pattern ay pagkatapos ay ilagay sa molding buhangin. 3.) Ang tinunaw na metal ay ibinubuhos sa molde, sinisingaw ang pattern ng foam, ibig sabihin, polystyrene sa karamihan ng mga kaso habang ito ay dumadaloy sa lukab ng amag. 4.) Ang tinunaw na metal ay iniiwan sa amag ng buhangin upang tumigas. 5.) Matapos itong tumigas, inaalis namin ang casting. Sa ilang mga kaso, ang produktong ginagawa namin ay nangangailangan ng isang core sa loob ng pattern. Sa evaporative casting, hindi na kailangang maglagay at mag-secure ng core sa mold cavity. Ang pamamaraan ay angkop para sa pagmamanupaktura ng mga napaka-kumplikadong geometries, madali itong awtomatiko para sa mataas na dami ng produksyon, at walang mga linya ng paghihiwalay sa bahagi ng cast. Ang pangunahing proseso ay simple at matipid upang ipatupad. Para sa malaking dami ng produksyon, dahil ang isang mamatay o amag ay kailangan upang makagawa ng mga pattern mula sa polystyrene, ito ay maaaring medyo magastos. • NON-EXPANDABLE MOLD CASTING : Ang malawak na kategoryang ito ay tumutukoy sa mga pamamaraan kung saan ang amag ay hindi kailangang baguhin pagkatapos ng bawat yugto ng produksyon. Ang mga halimbawa ay permanente, die, tuluy-tuloy at centrifugal casting. Ang repeatability ay nakuha at ang mga bahagi ay maaaring mailalarawan bilang NEAR NET SHAPE. • PERMANENT MOLD CASTING : Ang mga reusable molds na gawa sa metal ay ginagamit para sa maraming casting. Ang isang permanenteng amag ay karaniwang maaaring gamitin ng sampu-sampung libong beses bago ito maubos. Ang gravity, gass pressure o vacuum ay karaniwang ginagamit upang punan ang amag. Ang mga amag (tinatawag ding die) ay karaniwang gawa sa bakal, bakal, ceramic o iba pang metal. Ang pangkalahatang proseso ay: 1.) Makina at gumawa ng molde. Karaniwang ginagawang makina ang amag mula sa dalawang bloke ng metal na magkasya at maaaring buksan at sarado. Ang parehong mga tampok ng bahagi pati na rin ang gating system ay karaniwang machined sa paghahagis amag. 2.) Ang panloob na mga ibabaw ng amag ay pinahiran ng isang slurry na may kasamang mga refractory na materyales. Nakakatulong ito na kontrolin ang daloy ng init at nagsisilbing pampadulas para sa madaling pagtanggal ng bahagi ng cast. 3.) Susunod, ang mga permanenteng halves ng amag ay sarado at ang amag ay pinainit. 4.) Ang tunaw na metal ay ibinubuhos sa molde at hayaang matahimik para sa solidification. 5.) Bago mangyari ang maraming paglamig, inaalis namin ang bahagi mula sa permanenteng amag gamit ang mga ejector kapag nabuksan ang mga bahagi ng amag. Madalas kaming gumagamit ng permanenteng paghahagis ng amag para sa mababang antas ng pagkatunaw ng mga metal tulad ng zinc at aluminyo. Para sa mga casting ng bakal, ginagamit namin ang grapayt bilang materyal ng amag. Minsan nakakakuha kami ng mga kumplikadong geometries gamit ang mga core sa loob ng mga permanenteng hulma. Ang mga bentahe ng pamamaraang ito ay ang mga paghahagis na may mahusay na mga mekanikal na katangian na nakuha sa pamamagitan ng mabilis na paglamig, pagkakapareho sa mga katangian, mahusay na katumpakan at pagtatapos ng ibabaw, mababang mga rate ng pagtanggi, posibilidad ng pag-automate ng proseso at paggawa ng mataas na volume sa matipid. Ang mga disadvantage ay ang mataas na mga paunang gastos sa pag-setup na ginagawang hindi angkop para sa mga pagpapatakbo ng mababang volume, at mga limitasyon sa laki ng mga bahaging ginawa. • DIE CASTING : Ang isang die ay ginagawang makina at ang tinunaw na metal ay itinutulak sa ilalim ng mataas na presyon sa mga butas ng amag. Ang parehong nonferrous pati na rin ang ferrous metal die castings ay posible. Ang proseso ay angkop para sa mataas na dami ng produksyon na tumatakbo ng maliit hanggang katamtamang laki ng mga bahagi na may mga detalye, napakanipis na pader, dimensional consistency at magandang surface finish. Ang AGS-TECH Inc. ay may kakayahang gumawa ng mga kapal ng pader na kasing liit ng 0.5 mm gamit ang pamamaraang ito. Tulad ng permanenteng paghahagis ng amag, ang amag ay kailangang binubuo ng dalawang halves na maaaring magbukas at magsara para maalis ang bahaging ginawa. Ang isang die casting mold ay maaaring magkaroon ng maraming cavity upang paganahin ang paggawa ng maraming casting sa bawat cycle. Ang mga die casting molds ay napakabigat at mas malaki kaysa sa mga bahagi na ginagawa nila, kaya mahal din. Nag-aayos at nagpapalit kami ng mga sira na dies nang walang bayad para sa aming mga customer hangga't muli nilang inaayos ang kanilang mga piyesa mula sa amin. Ang aming mga namatay ay may mahabang buhay sa ilang daang libong hanay ng mga siklo. Narito ang mga pangunahing pinasimpleng hakbang sa proseso: 1.) Ang paggawa ng amag sa pangkalahatan ay mula sa bakal 2.) Mould na naka-install sa die casting machine 3.) Pinipilit ng piston na dumaloy ang tinunaw na metal sa mga die cavity na pinupuno ang mga masalimuot na katangian at manipis na mga dingding 4.) Pagkatapos punan ang amag ng tinunaw na metal, ang paghahagis ay hahayaang tumigas sa ilalim ng presyon 5.) Binubuksan ang amag at tinanggal ang casting sa tulong ng mga ejector pin. 6.) Ngayon ang walang laman na die ay lubricated muli at clamped para sa susunod na cycle. Sa die casting, madalas naming ginagamit ang insert molding kung saan nagsasama kami ng karagdagang bahagi sa molde at inihagis ang metal sa paligid nito. Pagkatapos ng solidification, ang mga bahaging ito ay naging bahagi ng produkto ng cast. Ang mga bentahe ng die casting ay mahusay na mekanikal na mga katangian ng mga bahagi, posibilidad ng masalimuot na mga tampok, pinong mga detalye at magandang ibabaw na tapusin, mataas na mga rate ng produksyon, madaling automation. Ang mga disadvantage ay: Hindi masyadong angkop para sa mababang volume dahil sa mataas na halaga ng die at kagamitan, mga limitasyon sa mga hugis na maaaring i-cast, maliit na mga marka ng bilog sa mga bahagi ng cast na nagreresulta mula sa pagkakadikit ng mga pin ng ejector, manipis na flash ng metal na napiga sa linya ng paghihiwalay, kailangan para sa mga lagusan sa kahabaan ng linya ng paghihiwalay sa pagitan ng die, kinakailangang panatilihing mababa ang temperatura ng amag gamit ang sirkulasyon ng tubig. • CENTRIFUGAL CASTING : Ang tunaw na metal ay ibinubuhos sa gitna ng umiikot na amag sa axis ng pag-ikot. Ang mga puwersang sentripugal ay itinatapon ang metal patungo sa paligid at hinahayaang tumigas habang patuloy na umiikot ang amag. Maaaring gamitin ang parehong pahalang at patayong pag-ikot ng axis. Maaaring i-cast ang mga bahaging may bilog na panloob na ibabaw gayundin ang iba pang hindi bilog na hugis. Ang proseso ay maaaring i-summarize bilang: 1.) Ang tinunaw na metal ay ibinubuhos sa sentripugal na amag. Ang metal ay pagkatapos ay pinipilit sa mga panlabas na dingding dahil sa pag-ikot ng amag. 2.) Habang umiikot ang amag, tumitigas ang metal casting Ang centrifugal casting ay isang angkop na pamamaraan para sa paggawa ng mga guwang na cylindirical na bahagi tulad ng mga tubo, hindi na kailangan ng sprues, risers at gating elements, magandang surface finish at mga detalyadong feature, walang mga isyu sa pag-urong, posibilidad na makagawa ng mahahabang tubo na may napakalaking diameters, mataas na rate ng produksyon na kakayahan . • PATULOY NA PAG-CASTING ( STRAND CASTING ) : Ginagamit sa paghahagis ng tuluy-tuloy na haba ng metal. Karaniwang ang tinunaw na metal ay inihagis sa dalawang dimensional na profile ng amag ngunit ang haba nito ay hindi tiyak. Ang bagong tunaw na metal ay patuloy na pinapakain sa amag habang ang paghahagis ay naglalakbay pababa na ang haba nito ay tumataas sa paglipas ng panahon. Ang mga metal tulad ng tanso, bakal, aluminyo ay inihahagis sa mahabang hibla gamit ang tuluy-tuloy na proseso ng paghahagis. Ang proseso ay maaaring may iba't ibang mga pagsasaayos ngunit ang karaniwan ay maaaring gawing simple bilang: 1.) Ang nilusaw na metal ay ibinubuhos sa isang lalagyan na matatagpuan mataas sa itaas ng amag sa mahusay na kalkuladong dami at mga rate ng daloy at dumadaloy sa tubig na pinalamig ng amag. Ang paghahagis ng metal na ibinuhos sa amag ay nagpapatigas sa isang starter bar na inilagay sa ilalim ng amag. Ang starter bar na ito ay nagbibigay sa mga roller ng isang bagay na makukuha sa simula. 2.) Ang mahabang metal strand ay dinadala ng mga roller sa pare-pareho ang bilis. Binabago din ng mga roller ang direksyon ng daloy ng metal strand mula patayo hanggang pahalang. 3.) Matapos ang tuluy-tuloy na paghahagis ay maglakbay sa isang tiyak na pahalang na distansya, ang isang tanglaw o lagari na gumagalaw kasama ang paghahagis ay mabilis na pinuputol ito sa nais na haba. Ang tuluy-tuloy na proseso ng pag-cast ay maaaring isama sa ROLLING PROCESS, kung saan ang tuluy-tuloy na cast metal ay maaaring direktang ipasok sa isang rolling mill upang makagawa ng I-Beams, T-Beams....atbp. Ang tuluy-tuloy na paghahagis ay gumagawa ng magkakatulad na katangian sa buong produkto, ito ay may mataas na antas ng solidification, binabawasan ang gastos dahil sa napakababang pagkawala ng materyal, nag-aalok ng isang proseso kung saan ang paglo-load ng metal, pagbuhos, solidification, pagputol at pag-alis ng paghahagis lahat ay nagaganap sa tuluy-tuloy na operasyon at kaya nagreresulta sa mataas na rate ng produktibidad at mataas na kalidad. Gayunpaman, ang isang pangunahing pagsasaalang-alang ay ang mataas na paunang pamumuhunan, mga gastos sa pag-setup at mga kinakailangan sa espasyo. • MACHINING SERVICES : Nag-aalok kami ng tatlo, apat at limang - axis machining. Ang uri ng mga proseso ng machining na ginagamit namin ay TURNING, MILLING, DRILLING, BORING, BROACHING, PLANING, SAWING, GRINDING, LAPPING, POLISHING at NON-TRADITIONAL MACHINING na higit pang idinetalye sa ilalim ng ibang menu ng aming website. Para sa karamihan ng aming pagmamanupaktura, gumagamit kami ng mga CNC machine. Gayunpaman para sa ilang mga operasyon, ang mga nakasanayang pamamaraan ay mas angkop at samakatuwid ay umaasa rin kami sa kanila. Ang aming mga kakayahan sa machining ay umabot sa pinakamataas na antas na posible at ang ilang pinaka-hinihingi na bahagi ay ginawa sa isang AS9100 na sertipikadong planta. Ang mga blades ng jet engine ay nangangailangan ng lubos na dalubhasang karanasan sa pagmamanupaktura at tamang kagamitan. Ang industriya ng aerospace ay may napakahigpit na pamantayan. Ang ilang mga bahagi na may mga kumplikadong geometrical na istruktura ay pinakamadaling ginawa ng limang axis machining, na matatagpuan lamang sa ilang machining plant kabilang ang sa amin. Ang aming aerospace certified plant ay may kinakailangang karanasan sa pagsunod sa malawak na kinakailangan sa dokumentasyon ng industriya ng aerospace. Sa mga operasyon ng TURNING, ang isang workpiece ay iniikot at inilipat laban sa isang cutting tool. Para sa prosesong ito ginagamit ang isang makina na tinatawag na lathe. Sa MILLING, ang isang makina na tinatawag na milling machine ay may umiikot na tool upang dalhin ang mga cutting edge upang madala laban sa isang workpiece. Ang mga operasyon sa DRILLING ay nagsasangkot ng umiikot na pamutol na may mga cutting edge na gumagawa ng mga butas kapag nadikit sa workpiece. Karaniwang ginagamit ang mga drill press, lathe o gilingan. Sa mga BORING na operasyon, ang isang tool na may isang nakabaluktot na dulo ay inilipat sa isang magaspang na butas sa isang umiikot na workpiece upang bahagyang palakihin ang butas at pagbutihin ang katumpakan. Ginagamit ito para sa mga layunin ng pinong pagtatapos. Ang BROACHING ay nagsasangkot ng tool na may ngipin upang alisin ang materyal mula sa isang workpiece sa isang pass ng broach (tool na may ngipin). Sa linear broaching, ang broach ay tumatakbo nang linearly laban sa isang ibabaw ng workpiece upang ma-effect ang cut, samantalang sa rotary broaching, ang broach ay iniikot at pinindot sa workpiece upang gupitin ang isang axis na simetriko na hugis. Ang SWISS TYPE MACHINING ay isa sa aming mahalagang mga diskarte na ginagamit namin para sa mataas na dami ng pagmamanupaktura ng maliliit na mataas na katumpakan na bahagi. Gamit ang Swiss-type na lathe, ginagawa namin ang maliliit, kumplikado, mga precision na bahagi sa murang halaga. Hindi tulad ng maginoo na mga lathe kung saan ang workpiece ay pinananatiling nakatigil at ang tool ay gumagalaw, sa Swiss-type na mga turning center, ang workpiece ay pinapayagang lumipat sa Z-axis at ang tool ay nakatigil. Sa Swiss-type na machining, ang bar stock ay hawak sa makina at i-advance sa pamamagitan ng isang guide bushing sa z-axis, na inilalantad lamang ang bahaging gagawing makina. Sa ganitong paraan matitiyak ang mahigpit na pagkakahawak at napakataas ng katumpakan. Ang pagkakaroon ng mga live na tool ay nagbibigay ng pagkakataong mag-mill at mag-drill habang ang materyal ay umuusad mula sa guide bushing. Ang Y-axis ng Swiss-type na kagamitan ay nagbibigay ng ganap na kakayahan sa paggiling at nakakatipid ng malaking dami ng oras sa pagmamanupaktura. Higit pa rito, ang aming mga makina ay may mga drill at boring na tool na gumagana sa bahagi kapag ito ay nakahawak sa sub spindle. Ang aming Swiss-Type na kakayahan sa machining ay nagbibigay sa amin ng ganap na awtomatikong kumpletong pagkakataon sa machining sa iisang operasyon. Ang Machining ay isa sa pinakamalaking segment ng negosyo ng AGS-TECH Inc. Ginagamit namin ito bilang pangunahing operasyon o pangalawang operasyon pagkatapos i-cast o i-extruding ang isang bahagi upang matugunan ang lahat ng mga detalye ng pagguhit. • SURFACE FINISHING SERVICES : Nag-aalok kami ng malawak na iba't ibang mga surface treatment at surface finishing tulad ng surface conditioning para mapahusay ang adhesion, pagdedeposito ng manipis na oxide layer para mapahusay ang adhesion ng coating, sand blasting, chem-film, anodizing, nitriding, powder coating, spray coating , iba't ibang advanced na metallization at coating techniques kabilang ang sputtering, electron beam, evaporation, plating, hard coatings gaya ng diamond like carbon (DLC) o titanium coating para sa drilling at cutting tools. • MGA SERBISYO SA PAGMARKA AT LABEL NG PRODUKTO : Marami sa aming mga customer ang nangangailangan ng pagmamarka at pag-label, pagmamarka ng laser, pag-ukit sa mga bahaging metal. Kung mayroon kang anumang ganoong pangangailangan, pag-usapan natin kung aling opsyon ang pinakamainam para sa iyo. Narito ang ilan sa mga karaniwang ginagamit na produktong metal cast. Dahil off-the-shelf ang mga ito, makakatipid ka sa mga gastos sa molde kung sakaling magkasya ang alinman sa mga ito sa iyong mga kinakailangan: CLICK HERE PARA I-DOWNLOAD ang aming 11 Series Die-cast Aluminum Boxes mula sa AGS-Electronics CLICK Product Finder-Locator Service NAKARAANG PAHINA
- Custom Manufactured Parts, Assemblies, Plastic Mold, Casting,Machining
Custom Manufactured Parts, Assemblies, Plastic Mold, Rubber Molding, Metal Casting, CNC Machining, Turning, Milling, Electrical Electronic Optical Assembly PCBA Mga Custom na Ginawang Bahagi at Assemblies at Produkto Magbasa pa Plastic at Rubber Molds at Molding Magbasa pa Casting at Machining Magbasa pa Mga Extrusions, Mga Extruded na Produkto Magbasa pa Stamping at Sheet Metal Fabrication Magbasa pa Metal Forging at Powder Metallurgy Magbasa pa Wire at Spring Forming Magbasa pa Salamin at Ceramic Forming & Shaping Magbasa pa Additive at Mabilis na Paggawa Magbasa pa Paggawa ng Composite at Composite Materials Magbasa pa Mga Proseso ng Pagsali at Pagpupulong at Pangkabit Gumagawa kami ng mga bahagi at asembliya para sa iyo at nag-aalok ng mga sumusunod na proseso ng pagmamanupaktura: • Mga amag na plastik at goma at mga bahaging hinulma. Injection molding, thermoforming, thermoset molding, vacuum forming, blow molding, rotational molding, pour molding, insert molding at iba pa. • Mga plastik, goma at metal na extrusions • Ferrous at nonferrous casting at machined parts na ginawa ng milling at turning techniques, Swiss-type machining. • Mga bahagi ng powder metalurgy • Metal at nonmetal stampings, sheet metal forming, welded sheet metal assemblies • Malamig at mainit na forging • Mga wire, welded wire assemblies, wire forming • Iba't ibang uri ng bukal, spring forming • Paggawa ng gear, gearbox, coupling, worm, speed reducer, cylinder, transmission belt, transmission chain, transmission component • Custom na tempered at bulletproof na salamin na sumusunod sa mga pamantayan ng NATO at militar • Mga bola, bearings, pulley at pulley assemblies • Mga balbula at pneumatic na bahagi tulad ng O-ring, washer at seal • Glass at ceramic na mga bahagi at assemblies, vacuum proof at hermetic na mga bahagi, metal-ceramic at ceramic-ceramic bonding. • Iba't ibang uri ng mechanical, optomechanical, electromechanical, optoelectronic assemblies. • Metal-rubber, metal-plastic bonding • Pipe at tube, pipe forming, bending at custom pipe assemblies, bellow manufacturing. • Paggawa ng fiberglass • Welding gamit ang iba't ibang pamamaraan tulad ng spot welding, laser welding, MIG, TIG. Ultrasonic welding para sa mga plastik na bahagi. • Napakaraming iba't ibang surface treatment at surface finish gaya ng surface conditioning para mapahusay ang adhesion, pagdedeposito ng manipis na oxide layer para mapahusay ang adhesion ng coating, sand blasting, chem-film, anodizing, nitriding, powder coating, spray coating, iba't ibang advanced na metallization at coating techniques kabilang ang sputtering, electron beam, evaporation, plating, hard coatings gaya ng diamond like carbon (DLC) o titanium para sa cutting at drilling tools. • Pagmarka at pag-label, pagmamarka ng laser sa mga bahaging metal, pag-print sa mga bahaging plastik at goma Mag-download ng brochure para sa Mga Karaniwang Tuntunin ng Mechanical Engineering na ginagamit ng mga Designer at Engineer Bumubuo kami ng mga produkto ayon sa iyong partikular na mga detalye at kinakailangan. Upang mag-alok sa iyo ng pinakamahusay na kalidad, paghahatid at mga presyo, gumagawa kami ng mga produkto sa buong mundo sa China, India, Taiwan, Pilipinas, South Korea, Malaysia, Sri Lanka, Turkey, USA, Canada, Germany, UK at Japan. Ginagawa tayo nito na mas malakas at mas mapagkumpitensya sa buong mundo kaysa sa anumang iba pang custom manufacturer. Ang aming mga produkto ay ginawa sa ISO9001:2000, QS9000, ISO14001, TS16949 na mga sertipikadong kapaligiran at nagtataglay ng CE, UL na marka at nakakatugon sa iba pang mga pamantayan sa industriya. Kapag kami ay hinirang para sa iyong proyekto, maaari naming pangalagaan ang buong pagmamanupaktura, pagpupulong, pagsubok, kwalipikasyon, pagpapadala at customs ayon sa gusto mo. Kung gusto mo, maaari naming i-warehouse ang iyong mga piyesa, bumuo ng mga custom na kit, i-print at lagyan ng label ang pangalan at tatak ng iyong kumpanya at ihulog ang barko sa iyong mga customer. Sa madaling salita, maaari rin kaming maging warehousing at distribution center mo kung gusto mo. Dahil ang aming mga bodega ay matatagpuan malapit sa mga pangunahing daungan, nagbibigay ito sa amin ng logistical advantage. Halimbawa, kapag dumating ang iyong mga produkto sa isang pangunahing daungan ng USA, maaari naming transport ito nang direkta sa isang kalapit na bodega kung saan maaari kaming mag-imbak, mag-assemble, gumawa ng mga kit, magrelabel, mag-print, mag-package ayon sa iyong pinili at mag-drop ipadala sa iyong mga customer. Hindi lang kami nagsusuplay ng mga produkto. Gumagana ang aming kumpanya sa mga custom na kontrata kung saan kami pumupunta sa iyong site, suriin ang iyong proyekto sa site at bumuo ng isang panukalang proyekto na pasadyang idinisenyo para sa iyo. Pagkatapos ay ipinapadala namin ang aming nakaranasang koponan upang ipatupad ang proyekto. Ang higit pang impormasyon tungkol sa aming gawaing pang-inhinyero ay matatagpuan sa http://www.ags-engineering.com -Nagsasagawa kami ng maliliit na proyekto pati na rin ang malalaking proyekto sa antas ng industriya. Bilang unang hakbang, maaari ka naming ikonekta sa pamamagitan ng telepono , teleconferencing o MSN messenger sa aming mga miyembro ng ekspertong koponan, upang maaari kang direktang makipag-ugnayan sa isang eksperto, magtanong at talakayin ang iyong proyekto. Tawagan kami at kung kinakailangan ay pupunta kami at bibisitahin ka. NAKARAANG PAHINA
- Plastic And Rubber Molding | United States | AGS-TECH, Inc.
AGS-TECH Inc., Molding, Casting, Machining, Forging, Sheet Metal Fabrication, Mechanical Electrical Electronic Optical Assembly, PCBA, Powder Metallurgy, CNC AGS-TECH Inc. AGS-TECH Inc. Custom Manufacturing, Domestic & Global Outsourcing, Engineering Integration, Consolidation AGS-TECH Inc. 1/2 Ang AGS-TECH, Inc. ay ang iyong: Pandaigdigang Custom na Manufacturer, Integrator, Consolidator, Outsourcing Partner para sa Maraming Iba't Ibang Produkto at Serbisyo. Kami ang iyong one-stop source para sa pagmamanupaktura, fabrication, engineering, consolidation, outsourcing ng custom na manufactured at off-shelf na mga produkto. SERBISYO: Custom na Paggawa Domestic at Global Contract Manufacturing Paggawa ng Outsourcing Domestic at Global Procurement Consolidation Pagsasama-sama ng Engineering TUNGKOL SA AGS-TECH, Inc. - Ang Iyong Pandaigdigang Custom na Manufacturer, Engineering Integrator, Consolidator, Outsourcing Partner Ang AGS-TECH Inc. ay isang tagagawa, integrator ng engineering, pandaigdigang tagapagtustos ng mga produktong pang-industriya kabilang ang mga hulma, mga molded na bahagi ng plastik at goma, mga casting, mga extrusions, fabrication ng sheet metal, metal stamping at forging, CNC machining, mga elemento ng makina, powder metallurgy, ceramic at glass forming, wire / spring forming, jointing at assembly at fasteners, non-conventional fabrication, microfabrication, nanotechnology coatings at thin film, custom mechanical at electric electronic component at assemblies at PCB at PCBA at cable harness, optical & fiber optic na mga bahagi at assembly , mga kagamitan sa pagsubok at metrology tulad ng mga hardness tester, metalurgical microscope, ultrasonic fault detector, mga pang-industriya na computer, mga naka-embed na system, automation at panel PC, mga single board computer, quality control equipment. Bukod sa mga produkto, kasama ang aming pandaigdigang engineering, reverse engineering, pananaliksik at pagpapaunlad, pagbuo ng produkto, additive at mabilis na pagmamanupaktura, prototyping, mga kakayahan sa pamamahala ng proyekto ay nag-aalok kami ng teknikal, logistik at tulong sa negosyo upang gawin kang mas mapagkumpitensya at matagumpay sa mga pandaigdigang merkado. Ang aming misyon ay simple: Gawing magtagumpay at lumago ang aming mga customer. paano ? Sa pamamagitan ng pagbibigay ng 1.) Better Quality 2.) Better Price 3.) Better Delivery........ lahat mula sa iisang kumpanya at ang pinaka-diverse na global engineering integrator at supplier na AGS-TECH Inc. Maaari mong ibigay sa amin ang iyong mga blueprint at maaari kaming mag-machine ng mga hulma, dies at mga tool para sa paggawa ng iyong mga piyesa. Ginagawa namin ang mga ito sa pamamagitan ng alinman sa paghubog, paghahagis, pagpilit, pag-forging, paggawa ng sheet-metal, panlililak, metalurhiya ng pulbos, CNC machining, pagbubuo. Maaari kaming magpadala sa iyo ng mga piyesa at bahagi o magsagawa ng pagpupulong, paggawa at kumpletong mga operasyon sa pagmamanupaktura sa aming mga pasilidad. Ang aming mga operasyon sa pagpupulong ay kinabibilangan ng mekanikal, optical, electronic, fiber optic na mga produkto. Nagsasagawa kami ng mga operasyon ng pagsali gamit ang mga fastener, welding, brazing, soldering, adhesive bonding at higit pa. Ang aming mga proseso sa paghubog ay para sa iba't ibang plastic, goma, ceramic, salamin, powder metalurgy na materyales. Gayundin ang aming casting, CNC machining, forging, sheet metal fabrication, wire at spring forming na proseso na kinabibilangan ng mga metal, alloys, plastic, ceramic. Nag-aalok kami ng mga panghuling pagpapatakbo ng pagtatapos tulad ng mga coatings at manipis at makapal na pelikula, paggiling, paghampas, pag-polish at higit pa. Ang aming mga kakayahan sa pagmamanupaktura ay lumampas sa mekanikal na pagpupulong. Gumagawa kami ng mga de-kuryenteng elektronikong bahagi at asembliya at PCB at PCBA at cable harness, optical at fiber optic na bahagi at pagpupulong ayon sa iyong mga teknikal na guhit, BOM, Gerber file. Ang iba't ibang mga diskarte sa pagmamanupaktura ng PCB at PCBA kabilang ang paghihinang ng reflow at paghihinang ng alon bukod sa iba ay ipinakalat. Kami ay mga dalubhasa sa precision connectorization, pagsali, pag-assemble at pagse-sealing ng hermetic electronic at fiber optical packages at mga produkto. Bukod sa passive at aktibong mechanical assembly, sinasamantala namin ang mga espesyal na brazing at soldering na materyales at mga diskarte para sa pagmamanupaktura ng mga produkto na sumusunod sa Telcordia at iba pang mga pamantayan ng industriya. Hindi kami limitado sa paggawa at paggawa ng mataas na dami. Halos bawat proyekto ay nagsisimula sa isang pangangailangan para sa engineering, reverse engineering, pananaliksik at pag-unlad, pagbuo ng produkto, additive at mabilis na pagmamanupaktura, prototyping. Bilang pinaka-magkakaibang pandaigdigang custom na manufacturer, engineering integrator, consolidator, outsourcing partner, tinatanggap ka namin kahit na may mga ideya ka lang. Dadalhin ka namin mula doon at tinutulungan ka sa lahat ng mga yugto ng matagumpay na kumpletong pag-unlad ng produkto at ikot ng pagmamanupaktura. Ito man ay mabilis na paggawa ng sheet metal, mabilis na pagmachining at paghuhulma ng amag, mabilis na paghahagis, mabilis na pagpupulong ng PCB at PCBA o kung hindi, ang anumang mabilis na pamamaraan ng prototyping ay nasa iyong serbisyo. Nag-aalok kami sa iyo ng off-the-shelf pati na rin ang custom na ginawang kagamitan sa metrology tulad ng mga hardness tester, metallurgical microscope, ultrasonic fault detector; mga pang-industriyang computer, mga naka-embed na system, automation at panel PC, mga single board na computer at mga kagamitan sa pagkontrol ng kalidad na malawakang ginagamit sa mga pasilidad sa pagmamanupaktura at industriya. Sa pamamagitan ng pag-aalok sa iyo ng makabagong kagamitan sa metrology at pang-industriya na mga bahagi ng computer, pinupunan namin ang iyong mga pangangailangan bilang isang pinagmumulan ng tagagawa at supplier kung saan maaari mong pagkunan ang lahat ng kailangan mo. Kung walang malawak na spectrum ng mga serbisyo sa engineering, hindi tayo magiging iba sa karamihan ng iba pang mga tagagawa at nagbebenta na may limitadong custom na mga kakayahan sa pagmamanupaktura at pagpupulong na nasa merkado. Ang tagal ng aming mga serbisyo sa engineering ay nagpapakilala sa amin bilang ang pinaka-diverse na custom na manufacturer, contract manufacturer, engineering integrator, consolidator at outsourcing partner sa buong mundo. Ang mga serbisyo sa engineering ay maaaring ialok bilang nag-iisa o bilang bahagi ng bagong produkto o proseso ng pagbuo, o bilang bahagi ng isang umiiral na produkto o proseso ng pagbuo o bilang anumang bagay na pumapasok sa iyong isipan. Kami ay may kakayahang umangkop at ang aming mga serbisyo sa engineering ay maaaring gawin ang form na pinakaangkop sa iyong mga pangangailangan at kinakailangan. Ang mga maihahatid at output ng aming mga serbisyo sa engineering ay limitado lamang ng iyong imahinasyon at maaaring magkaroon ng anumang anyo na nababagay sa iyo. Ang pinakakaraniwang anyo ng output mula sa aming mga serbisyo sa engineering ay: Mga ulat sa konsultasyon, test sheet at ulat, ulat ng inspeksyon, blueprint, engineering drawing, assembly drawing, bill ng mga listahan ng materyal, datasheet, simulation, software program, graphics at chart, output mula sa dalubhasang optical, thermal o iba pang software program, sample at prototype, modelo, demonstrasyon…..atbp. Ang aming mga serbisyo sa engineering ay maaaring maihatid nang may pirma o ilang pirma ng mga sertipikadong propesyonal na inhinyero sa iyong estado. Minsan ang ilang mga propesyonal na inhinyero mula sa iba't ibang mga disiplina ay maaaring kailanganin na pumirma sa trabaho. Ang mga serbisyo ng outsourcing engineering sa amin ay maaaring magbigay sa iyo ng maraming benepisyo tulad ng pagtitipid sa gastos mula sa pagkuha ng isang full-time na inhinyero o mga inhinyero, mabilis na pagkuha sa ekspertong inhinyero na pagsilbihan ka sa loob ng iyong takdang panahon at badyet sa halip na maghanap upang kumuha ng isa, na nagbibigay sa iyo ng kakayahang huminto isang proyekto nang mabilis kung sakaling napagtanto mong hindi ito magagawa (ito ay napakamahal kung sakaling kumuha ka at tanggalin ang iyong sariling mga inhinyero), mabilis na makapagpalit ng mga inhinyero mula sa iba't ibang mga disiplina at background na nagbibigay sa iyo ng kakayahang magmaniobra anumang oras at yugto ng iyong mga proyekto…..etc. Mayroong maraming iba pang mga benepisyo sa pag-outsourcing ng mga serbisyo sa engineering bilang karagdagan sa pasadyang pagmamanupaktura at pagpupulong. Sa site na ito kami ay tumutuon sa pasadyang pagmamanupaktura, paggawa ng kontrata, pagpupulong, pagsasama-sama, pagsasama-sama at outsourcing ng mga produkto. Kung ang engineering side ng aming negosyo ay mas interesado sa iyo, mahahanap mo ang detalyadong impormasyon tungkol sa aming mga serbisyo sa engineering sa pamamagitan ng pagbisita sa http://www.ags-engineering.com Kami ay AGS-TECH Inc., ang iyong one-stop source para sa manufacturing at fabrication at engineering at outsourcing at consolidation. Kami ang pinaka-magkakaibang engineering integrator sa Mundo na nag-aalok sa iyo ng custom na pagmamanupaktura, subassembly, pagpupulong ng mga produkto at serbisyo sa engineering. Contact Us First Name Last Name Email Write a message Submit Thanks for submitting!