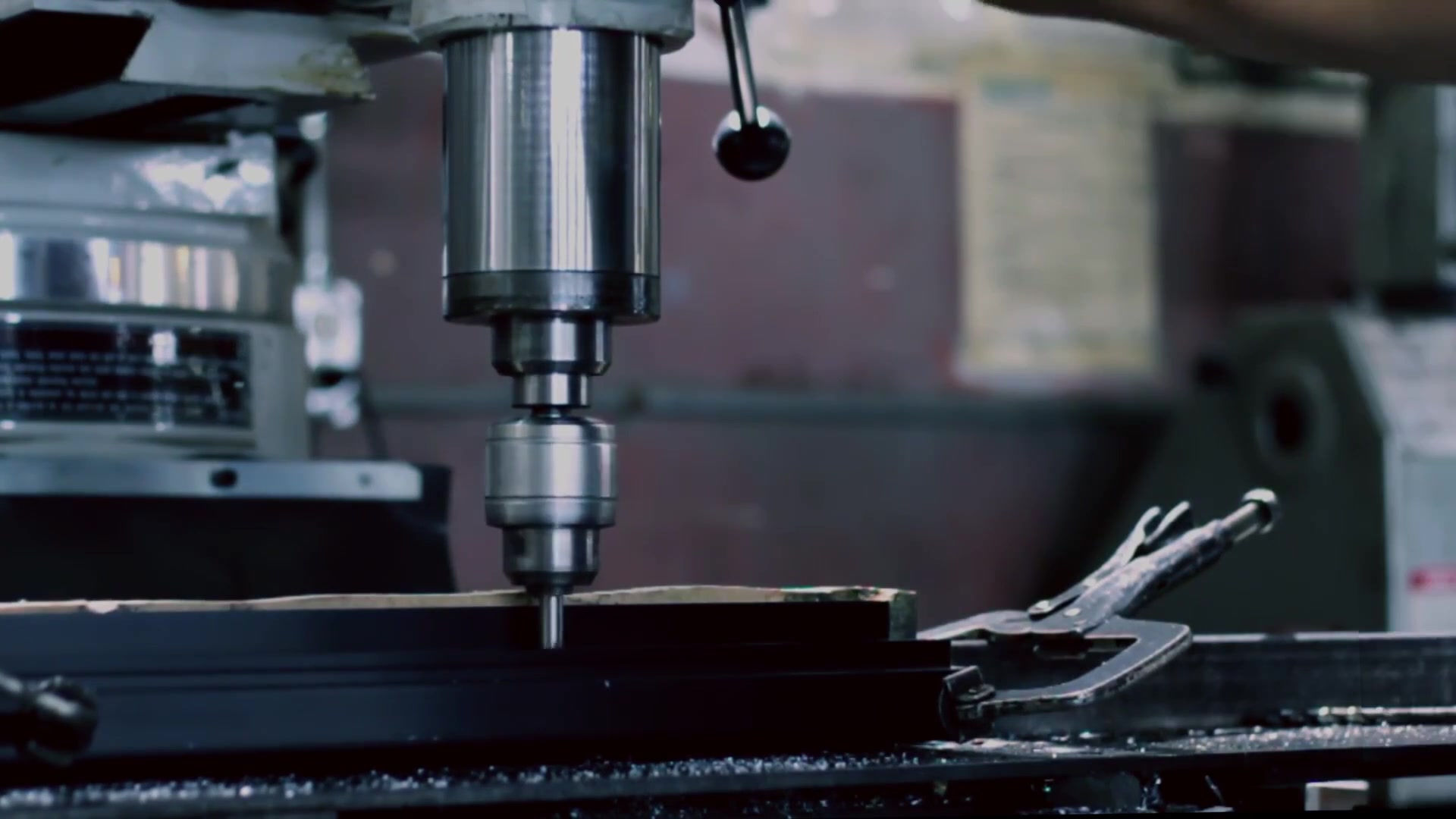
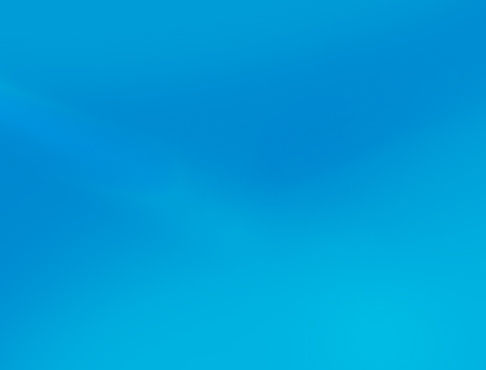
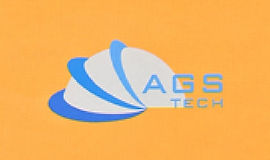
Çok Çeşitli Ürün ve Hizmetler için Küresel Özel Fason Üretici, Entegratör, Montaj Tedarikçisi, Global Imalat Ortağı.
Özel imal edilmiş ve kullanıma hazır fason ürün imalatı ve hizmetlerin tedariği, mühendisliği, konsolidasyonu, entegrasyonu, küresel fason üretim için tek durak kaynağınız biziz.
Choose your Language
-
Özel İmalatlar
-
Yerli & Global Fason Üretim
-
İmalat Dış Kaynak Kullanımı
-
Yurtiçi ve Küresel Tedarik
-
Konsolidasyon
-
Mühendislik Entegrasyonu
-
Mühendislik Hizmetleri
Özel döküm ve işleme tekniklerimiz, harcanabilir ve tükenmez dökümler, demirli ve demirsiz döküm, kum, kalıp, santrifüj, sürekli, seramik kalıp, revetman, kayıp köpük, net şekle yakın, kalıcı kalıp (yerçekimi döküm), alçıdır. kalıp (alçı döküm) ve kabuk dökümler, konvansiyonel ve CNC ekipmanları kullanılarak frezeleme ve tornalama ile üretilen işlenmiş parçalar, yüksek verimli ucuz küçük hassas parçalar için İsviçre tipi işleme, bağlantı elemanları için vida işleme, geleneksel olmayan işleme. Metallerin ve metal alaşımlarının yanı sıra, bazı durumlarda kalıp imalatının cazip olmadığı veya seçenek olmadığı durumlarda seramik, cam ve plastik bileşenleri de işliyoruz. Polimer malzemelerin işlenmesi, plastiklerin ve kauçuğun yumuşaklıkları, rijit olmamaları vb. nedeniyle sunduğu zorluklar nedeniyle sahip olduğumuz özel deneyim gerektirir. Seramik ve cam işleme için lütfen Konvansiyonel Olmayan İmalat sayfamıza bakın. AGS-TECH Inc. hem hafif hem de ağır dökümler üretir ve tedarik eder. Kazanlar, ısı eşanjörleri, otomobiller, mikro motorlar, rüzgar türbinleri, gıda paketleme ekipmanları ve daha fazlası için metal dökümler ve işlenmiş parçalar tedarik ediyoruz. Daha detaylı teknik bilgi sahibi olmak için buraya tıklamanızı tavsiye ederiz: AGS-TECH A.Ş.'de Talaşlı İmalat ve Metal Döküm İşlemlerinin Şematik Gösterimleri
Bu, aşağıda size sağladığımız bilgileri daha iyi anlamanıza yardımcı olacaktır. Sunduğumuz çeşitli tekniklerden bazılarına ayrıntılı olarak bakalım:
• HARCANAN KALIBA DÖKÜM : Bu geniş kategori, geçici ve tekrar kullanılamayan kalıpları içeren yöntemleri ifade eder. Örnekler kum, alçı, kabuk, revetman (kayıp mum da denir) ve alçı dökümdür.
• KUM DÖKÜM : Kalıp malzemesi olarak kumun kullanıldığı bir işlemdir. Çok eski bir yöntem ve üretilen metal dökümlerin çoğunluğu bu teknikle yapıldığı ölçüde hala çok popüler. Düşük adetli üretimde bile düşük maliyet. Küçük ve büyük parça üretimi için uygundur. Teknik, çok az yatırımla günler veya haftalar içinde parça üretmek için kullanılabilir. Nemli kum, kil, bağlayıcılar veya özel yağlar kullanılarak birbirine yapıştırılır. Kum genellikle kalıp kutularında bulunur ve modellerin etrafındaki kumun sıkıştırılmasıyla boşluk ve geçit sistemi oluşturulur. Süreçler:
1.) Kalıbın yapılması için modelin kuma yerleştirilmesi
2.) Bir yolluk sistemine model ve kumun dahil edilmesi
3.) Modelin kaldırılması
4.) Kalıp boşluğunun erimiş metal ile doldurulması
5.) Metalin soğutulması
6.) Kum kalıbın kırılması ve dökümün çıkarılması
• ALÇI KALIP DÖKÜM : Kum döküme benzer şekilde, kalıp malzemesi olarak kum yerine paris alçısı kullanılmaktadır. Kum dökümü gibi kısa üretim süreleri olur ve ucuzdur. İyi boyutsal toleranslar ve yüzey kalitesi. En büyük dezavantajı, yalnızca alüminyum ve çinko gibi düşük erime noktalı metallerle kullanılabilmesidir.
• KABUK KALIP DÖKÜM : Kum döküme benzer. Kum döküm işleminde olduğu gibi kumla doldurulmuş şişe yerine sertleştirilmiş kum kabuğu ve termoset reçine bağlayıcı ile elde edilen kalıp boşluğu. olur Kumla dökülmeye uygun hemen hemen her metal, kabuk kalıplama ile dökülebilir. Süreç şu şekilde özetlenebilir:
1.) Kabuk kalıbı imalatı. Kullanılan kum, kum dökümde kullanılan kumla karşılaştırıldığında çok daha küçük tane boyutundadır. İnce kum, termoset reçine ile karıştırılır. Metal desen, kabuğun çıkarılmasını kolaylaştırmak için bir ayırıcı madde ile kaplanmıştır. Daha sonra metal kalıp ısıtılır ve kum karışımı sıcak döküm kalıbının üzerine gözeneklenir veya üflenir. Desenin yüzeyinde ince bir kabuk oluşur. Bu kabuğun kalınlığı, kum reçine karışımının metal desenle temas halinde olduğu sürenin uzunluğu değiştirilerek ayarlanabilir. Gevşek kum daha sonra kalan kabuk kaplı desen ile çıkarılır.
2.) Daha sonra kabuk ve desen bir fırında ısıtılarak kabuğun sertleşmesi sağlanır. Sertleşme tamamlandıktan sonra, kalıp içine yerleştirilmiş pimler kullanılarak kabuk kalıptan çıkarılır.
3.) Bu tür iki kabuk yapıştırılarak veya sıkıştırılarak birleştirilir ve tüm kalıbı oluşturur. Şimdi kabuk kalıp, döküm işlemi sırasında kum veya metal bilye ile desteklendiği bir kaba yerleştirilir.
4.) Artık sıcak metal kabuk kalıba dökülebilir.
Kabuk dökümün avantajları, çok iyi yüzey kalitesine sahip ürünler, yüksek boyutsal doğrulukla karmaşık parçalar üretme imkanı, otomatikleştirme işlemi kolay, büyük hacimli üretim için ekonomiktir.
Dezavantajları ise, erimiş metalin bağlayıcı kimyasal ile temas ettiğinde oluşan gazlar nedeniyle kalıpların iyi havalandırma gerektirmesi, termoset reçineler ve metal kalıpların pahalı olmasıdır. Metal kalıpların maliyeti nedeniyle, teknik, düşük miktarlı üretim çalışmaları için uygun olmayabilir.
• YATIRIM DÖKÜM veya ERİYEN KALIPLA DÖKÜM ( KAYIP MUM DÖKÜM olarak da bilinir ): Ayrıca çok eski bir tekniktir ve birçok metalden, refrakter malzemelerden ve özel yüksek performanslı alaşımlardan yüksek doğruluk, tekrarlanabilirlik, çok yönlülük ve bütünlük ile kaliteli parça üretimi için uygundur. Küçük ve büyük boyutlu parçalar üretilebilir. Diğer yöntemlerden bazılarıyla karşılaştırıldığında pahalı bir süreç, ancak en büyük avantajı, neredeyse net şekle, karmaşık konturlara ve ayrıntılara sahip parçalar üretme olasılığıdır. Bu nedenle, bazı durumlarda yeniden işleme ve işlemenin ortadan kaldırılmasıyla maliyet bir şekilde dengelenir. Farklılıklar olsa da, genel hassas döküm sürecinin bir özeti aşağıdadır:
1.) Balmumu veya plastikten orijinal ana kalıbın oluşturulması. Her döküm, süreçte yok edildiğinden bir kalıba ihtiyaç duyar. Kalıpların üretildiği kalıba da ihtiyaç duyulur ve çoğu zaman kalıp dökülür veya işlenir. Kalıbın açılması gerekmediğinden, karmaşık dökümler elde edilebilir, birçok mum deseni bir ağacın dalları gibi birbirine bağlanabilir ve birlikte dökülebilir, böylece metal veya metal alaşımının tek bir dökümünden birden fazla parçanın üretilmesini sağlar.
2.) Daha sonra, desen, çok ince taneli silika, su, bağlayıcılardan oluşan bir ateşe dayanıklı bulamaç ile daldırılır veya üzerine dökülür. Bu, desenin yüzeyi üzerinde seramik bir tabaka ile sonuçlanır. Desen üzerindeki refrakter kaplama kurumaya ve sertleşmeye bırakılır. Bu adım, hassas döküm adının geldiği yerdir: Refrakter bulamaç, mum kalıbı üzerine yatırılır.
3.) Bu aşamada, sertleşen seramik kalıp ters çevrilir ve mum eriyip kalıptan dökülecek şekilde ısıtılır. Metal döküm için bir boşluk bırakılır.
4.) Mum çıktıktan sonra, seramik kalıp daha da yüksek bir sıcaklığa ısıtılır ve bu da kalıbın güçlenmesine neden olur.
5.) Metal döküm, tüm karmaşık bölümleri dolduran sıcak kalıba dökülür.
6.) Dökümün katılaşmasına izin verilir
7.) Son olarak seramik kalıp kırılır ve üretilen parçalar ağaçtan kesilir.
Buraya Tıklayınız: Yatırım Döküm / Eriyen Kalıpla Döküm Tesisi Broşürü için bir link
• EVAPORATİF MODEL DÖKÜM : Proses, kalıba sıcak erimiş metal döküldüğünde buharlaşacak olan polistiren köpük gibi bir malzemeden yapılmış bir model kullanır. Bu işlemin iki türü vardır: Bağsız kum kullanan KAYIP KÖPÜK DÖKÜM ve bağlı kum kullanan TAM KALIP DÖKÜM. İşte genel işlem adımları:
1.) Deseni polistiren gibi bir malzemeden üretin. Büyük miktarlarda üretilecekse, model kalıplanır. Parça karmaşık bir şekle sahipse, deseni oluşturmak için bu tür köpük malzemenin birkaç bölümünün birbirine yapıştırılması gerekebilir. Döküm üzerinde iyi bir yüzey kalitesi oluşturmak için kalıbı genellikle refrakter bir bileşikle kaplarız.
2.) Kalıp daha sonra kalıp kumu içine konur.
3.) Erimiş metal kalıba dökülür, köpük kalıbı buharlaştırılır, yani çoğu durumda polistiren kalıp boşluğundan akarken.
4.) Erimiş metal sertleşmesi için kum kalıpta bırakılır.
5.) Sertleştikten sonra dökümü çıkartıyoruz.
Bazı durumlarda, ürettiğimiz ürün, kalıp içinde bir çekirdek gerektirir. Evaporatif dökümde, kalıp boşluğuna maça yerleştirmeye ve sabitlemeye gerek yoktur. Teknik, çok karmaşık geometrilerin üretimi için uygundur, yüksek hacimli üretim için kolayca otomatikleştirilebilir ve döküm parçada ayırma hatları yoktur. Temel işlemin uygulanması basit ve ekonomiktir. Büyük hacimli üretim için, desenleri polistirenden üretmek için bir kalıp veya kalıba ihtiyaç duyulduğundan, bu biraz maliyetli olabilir.
• HARCANMAYAN KALIP DÖKÜMÜ : Bu geniş kategori, her üretim döngüsünden sonra kalıbın yeniden düzenlenmesinin gerekmediği yöntemleri ifade eder. Örnekler kalıcı, kalıp, sürekli ve santrifüj dökümdür. Tekrarlanabilirlik elde edilir ve parçalar YAKIN NET ŞEKİL olarak karakterize edilebilir.
• KALICI KALIP DÖKÜM : Çoklu dökümler için metalden yapılmış tekrar kullanılabilir kalıplar kullanılmaktadır. Kalıcı bir kalıp genellikle eskimeden on binlerce kez kullanılabilir. Kalıbı doldurmak için genellikle yerçekimi, gaz basıncı veya vakum kullanılır. Kalıplar (kalıp olarak da adlandırılır) genellikle demir, çelik, seramik veya diğer metallerden yapılır. Genel süreç:
1.) Makineyi işleyin ve kalıbı oluşturun. Kalıbın birbirine uyan ve açılıp kapatılabilen iki metal bloktan işlenmesi yaygındır. Hem parça özellikleri hem de yolluk sistemi genellikle döküm kalıbına işlenir.
2.) İç kalıp yüzeyleri, refrakter malzemeler içeren bir bulamaç ile kaplanmıştır. Bu, ısı akışını kontrol etmeye yardımcı olur ve döküm parçanın kolayca çıkarılması için bir yağlayıcı görevi görür.
3.) Daha sonra kalıcı kalıp yarımları kapatılır ve kalıp ısıtılır.
4.) Erimiş metal kalıba dökülür ve katılaşması için dinlenmeye bırakılır.
5.) Fazla soğuma olmadan kalıp yarımları açıldığında ejektörler kullanarak parçayı kalıcı kalıptan çıkarıyoruz.
Çinko ve alüminyum gibi düşük erime noktalı metaller için sıklıkla kalıcı kalıp dökümü kullanıyoruz. Çelik dökümler için kalıp malzemesi olarak grafit kullanıyoruz. Bazen kalıcı kalıplar içinde maçalar kullanarak karmaşık geometriler elde ederiz. Bu tekniğin avantajları, hızlı soğutma ile elde edilen iyi mekanik özelliklere sahip dökümler, özelliklerde homojenlik, iyi doğruluk ve yüzey kalitesi, düşük ıskarta oranları, prosesi otomatikleştirme ve ekonomik olarak yüksek hacimler üretme imkanıdır. Dezavantajları, düşük hacimli işlemler için uygun olmayan yüksek ilk kurulum maliyetleri ve üretilen parçaların boyutundaki sınırlamalardır.
• KALIP DÖKÜM : Bir kalıp işlenir ve erimiş metal yüksek basınç altında kalıp boşluklarına itilir. Hem demir dışı hem de demirli metal kalıp dökümleri mümkündür. İşlem, ayrıntılara, son derece ince duvarlara, boyutsal tutarlılığa ve iyi yüzey kalitesine sahip küçük ila orta büyüklükteki parçaların yüksek miktarda üretim çalışmaları için uygundur. AGS-TECH A.Ş., bu tekniği kullanarak 0,5 mm'ye kadar küçük et kalınlıkları üretebilmektedir. Kalıcı kalıba dökümde olduğu gibi, üretilen parçanın çıkarılması için kalıbın açılıp kapanabilen iki yarıdan oluşması gerekir. Bir kalıp döküm kalıbı, her döngüde birden fazla dökümün üretilmesini sağlamak için birden fazla boşluğa sahip olabilir. Döküm kalıpları çok ağırdır ve ürettikleri parçalardan çok daha büyüktür, bu nedenle de pahalıdır. Üretilen parçalarını bizden sipariş eden müşterilerimiz için yıpranmış kalıpları ücretsiz olarak onarıyor ve değiştiriyoruz ve müşterilerimizin kalıplarını yıllarca muhafaza ediyoruz. Kalıplarımızın birkaç yüz bin döngü aralığında uzun ömürleri vardır.
İşte basitleştirilmiş temel işlem adımları:
1.) Kalıbın genel olarak çelikten üretilmesi
2.) Kalıp döküm makinesine takılı kalıp
3.) Piston, erimiş metali, karmaşık özellikleri ve ince duvarları dolduran kalıp boşluklarında akmaya zorlar.
4.) Kalıbın ergimiş metal ile doldurulmasından sonra döküm basınç altında sertleşmeye bırakılır.
5.) Kalıp açılır ve ejektör pimleri yardımıyla döküm çıkarılır.
6.) Şimdi boş kalıp tekrar yağlanır ve bir sonraki çevrim için sıkıştırılır.
Dökümde, kalıba ek bir parça eklediğimiz ve metali etrafına döktüğümüz sık sık geçmeli kalıplama kullanırız. Katılaşmadan sonra bu parçalar döküm ürünün bir parçası haline gelir. Pres dökümün avantajları, parçaların iyi mekanik özellikleri, karmaşık özellikler olasılığı, ince detaylar ve iyi yüzey kalitesi, yüksek üretim oranları, kolay otomasyondur. Dezavantajları: Yüksek kalıp ve ekipman maliyeti nedeniyle düşük hacim için çok uygun değildir, dökülebilecek şekillerdeki kısıtlamalar, döküm parçalar üzerinde ejektör pimlerinin temasından kaynaklanan küçük yuvarlak izler, ayırma hattında sıkılmış ince metal çapaklar, kalıp yarıları arasındaki ayırma hattı boyunca havalandırma delikleri için, su sirkülasyonu kullanarak kalıp sıcaklıklarını düşük tutma zorunluluğu.
• SANTRİFÜJ DÖKÜM : Dönen kalıbın ortasına dönme ekseninde erimiş metal dökülür. Merkezkaç kuvvetleri metali çevreye doğru fırlatır ve kalıp dönmeye devam ettikçe katılaşmasına izin verilir. Hem yatay hem de dikey eksen dönüşleri kullanılabilir. Yuvarlak iç yüzeyli parçalar ve diğer yuvarlak olmayan şekiller dökülebilir. Süreç şu şekilde özetlenebilir:
1.) Erimiş metal santrifüj kalıba dökülür. Metal daha sonra kalıbın dönmesi nedeniyle dış duvarlara zorlanır.
2.) Kalıp döndükçe metal döküm sertleşir
Santrifüj döküm, boru gibi içi boş silindirik parçaların üretimi için uygun bir tekniktir, yolluk, yükseltici ve yolluk elemanlarına ihtiyaç yoktur, iyi yüzey kalitesi ve detay özellikleri, büzülme sorunu yoktur, çok büyük çaplı uzun borular üretebilme imkanı, yüksek oranlı üretim kabiliyeti .
• SÜREKLİ DÖKÜM ( SÜREKLİ DÖKÜM ) : Sürekli uzunluktaki metali dökmek için kullanılır. Temel olarak erimiş metal, kalıbın iki boyutlu profiline dökülür, ancak uzunluğu belirsizdir. Döküm, zamanla artan uzunluğu ile aşağı doğru hareket ederken, yeni erimiş metal sürekli olarak kalıba beslenir. Bakır, çelik, alüminyum gibi metaller, sürekli döküm işlemi kullanılarak uzun teller halinde dökülür. İşlem çeşitli konfigürasyonlara sahip olabilir, ancak ortak olanı şu şekilde basitleştirilebilir:
1.) Erimiş metal, kalıbın üzerinde bulunan bir kaba iyi hesaplanmış miktar ve debilerde dökülür ve su soğutmalı kalıbın içinden akar. Kalıbın içine dökülen metal döküm, kalıbın altına yerleştirilmiş bir başlangıç çubuğuna katılaşır. Bu başlangıç çubuğu, silindirlere başlangıçta tutunacak birşey verir.
2.) Uzun metal şerit, silindirler tarafından sabit bir hızda taşınır. Silindirler ayrıca metal telin akış yönünü dikeyden yataya değiştirir.
3.) Sürekli döküm, belirli bir yatay mesafe kat ettikten sonra, döküm ile birlikte hareket eden bir torç veya testere, hızlı bir şekilde istenen uzunluklarda keser.
Sürekli döküm işlemi, sürekli olarak dökülen metalin I-Kirişler, T-Kirişler….vb. üretmek için doğrudan bir haddehaneye beslenebildiği HADDELEME PROSESİ ile entegre edilebilir. Sürekli döküm, ürün boyunca tek tip özellikler üretir, yüksek katılaşma hızına sahiptir, çok düşük malzeme kaybı nedeniyle maliyeti düşürür, metal yükleme, dökme, katılaştırma, kesme ve döküm çıkarma işlemlerinin sürekli bir operasyonda gerçekleştiği bir süreç sunar ve böylece yüksek verimlilik oranı ve yüksek kalite elde edilir. Ancak önemli bir husus, yüksek ilk yatırım, kurulum maliyetleri ve alan gereksinimleridir.
• İŞLEME HİZMETLERİ : Üç, dört ve beş eksenli işleme sunuyoruz. TORNALAMA, FREZELEME, DELME, DELME, BROŞLEME, PLANLAMA, KESİM, TAŞLAMA, LAPLAMA, PARLATMA, PARLATMA ve GELENEKSEL OLMAYAN TALAŞLAMA talaşlı imalat yöntemlerini sitemizin farklı bir menüsü altında detaylandırıyoruz. İmalatımızın çoğunda CNC makineleri kullanıyoruz. Ancak bazı operasyonlar için geleneksel teknikler daha uygundur ve bu nedenle onlara da güveniyoruz. İşleme yeteneklerimiz mümkün olan en yüksek seviyeye ulaşır ve en zorlu parçaların bazıları AS9100 sertifikalı bir tesiste üretilir. Jet motoru kanatları, son derece uzmanlaşmış üretim deneyimi ve doğru ekipman gerektirir. Havacılık endüstrisinin çok katı standartları vardır. Karmaşık geometrik yapılara sahip bazı bileşenler, en kolay şekilde, bizimki de dahil olmak üzere bazı işleme tesislerinde bulunan beş eksenli işleme ile üretilir. Havacılık ve uzay sertifikalı tesisimiz, havacılık endüstrisinin kapsamlı dokümantasyon gereksinimlerine uygun gerekli deneyime sahiptir.
TORNALAMA işlemlerinde, bir iş parçası döndürülür ve bir kesici takıma karşı hareket ettirilir. Bu işlem için torna adı verilen bir makine kullanılmaktadır.
FREZELEME'de, freze makinesi adı verilen bir makinede, kesici kenarları bir iş parçasına dayanacak şekilde getirmek için dönen bir takım bulunur.
DELME operasyonları, iş parçasıyla temas ettiğinde delikler oluşturan kesici kenarları olan dönen bir kesici içerir. Genellikle matkap presleri, torna tezgahları veya değirmenler kullanılır.
BORALAMA operasyonlarında, deliği hafifçe büyütmek ve doğruluğu artırmak için tek bir bükülmüş sivri ucu olan bir takım, dönen bir iş parçasındaki kaba bir deliğe hareket ettirilir. İnce bitirme amaçları için kullanılır.
BROŞLAMA, broşun (dişli alet) bir geçişinde bir iş parçasından malzemeyi çıkarmak için dişli bir alet içerir. Doğrusal broşlamada, broş, kesimi gerçekleştirmek için iş parçasının yüzeyine karşı doğrusal olarak ilerler, oysa döner broşlamada, broş döndürülür ve eksen simetrik bir şekil kesmek için iş parçasına bastırılır.
SWISS TİPİ İŞLEME, küçük yüksek hassasiyetli parçaların yüksek hacimli üretimi için kullandığımız değerli tekniklerimizden biridir. İsviçre tipi torna tezgahı kullanarak küçük, karmaşık, hassas parçaları ucuza çeviriyoruz. İş parçasının sabit tutulduğu ve takımın hareket ettiği geleneksel torna tezgahlarından farklı olarak, İsviçre tipi tornalama merkezlerinde iş parçasının Z ekseninde hareket etmesine izin verilir ve takım sabittir. İsviçre tipi işlemede, çubuk stoğu makinede tutulur ve sadece işlenecek kısmı açığa çıkararak z eksenindeki bir kılavuz burç boyunca ilerletilir. Bu şekilde sıkı bir tutuş sağlanır ve doğruluk çok yüksektir. Hareketli takımların mevcudiyeti, kılavuz burçtan malzeme ilerledikçe frezeleme ve delme fırsatı sağlar. İsviçre tipi ekipmanın Y ekseni, tam frezeleme yetenekleri sağlar ve imalatta büyük miktarda zaman tasarrufu sağlar. Ayrıca makinelerimizde alt işmiline tutulduğunda parça üzerinde çalışan matkaplar ve delik işleme takımları bulunmaktadır. İsviçre Tipi işleme kabiliyetimiz, bize tek bir işlemde tam otomatik komple işleme fırsatı sunar.
İşleme, AGS-TECH Inc. işinin en büyük bölümlerinden biridir. Tüm çizim özelliklerinin karşılanması için bir parçayı döktükten veya ekstrüde ettikten sonra birincil işlem veya ikincil işlem olarak kullanırız.
• YÜZEY İŞLEM HİZMETLERİ : Yapışmayı artırmak için yüzey koşullandırma, kaplamanın yapışmasını artırmak için ince oksit tabakası yerleştirme, kum püskürtme, kimyasal film, anotlama (eloksal kaplama), nitrürleme, toz kaplama, sprey kaplama gibi çok çeşitli yüzey işlemleri ve yüzey bitirme işlemleri sunuyoruz. , püskürtme, elektron ışını, buharlaştırma, kaplama, elmas benzeri karbon (DLC) gibi sert kaplamalar veya delme ve kesme aletleri için titanyum kaplama dahil olmak üzere çeşitli gelişmiş metalizasyon ve kaplama teknikleri.
• ÜRÜN MARKALAMA VE ETİKETLEME HİZMETLERİ : Müşterilerimizin birçoğu markalama ve etiketleme, lazer markalama, metal parçalar üzerine kazıma talep etmektedir. Böyle bir ihtiyacınız varsa, hangi seçeneğin sizin için en iyi olacağını tartışalım.
İşte yaygın olarak kullanılan metal döküm ürünlerinden bazıları. Bunlar kullanıma hazır olduğundan, aşağıdakilerden herhangi birinin gereksinimlerinize uyması durumunda kalıp maliyetlerinden tasarruf edebilirsiniz:
AGS-Electronics'ten 11 Serisi Döküm Alüminyum Kutularımızı İNDİRMEK İÇİN TIKLAYINIZ