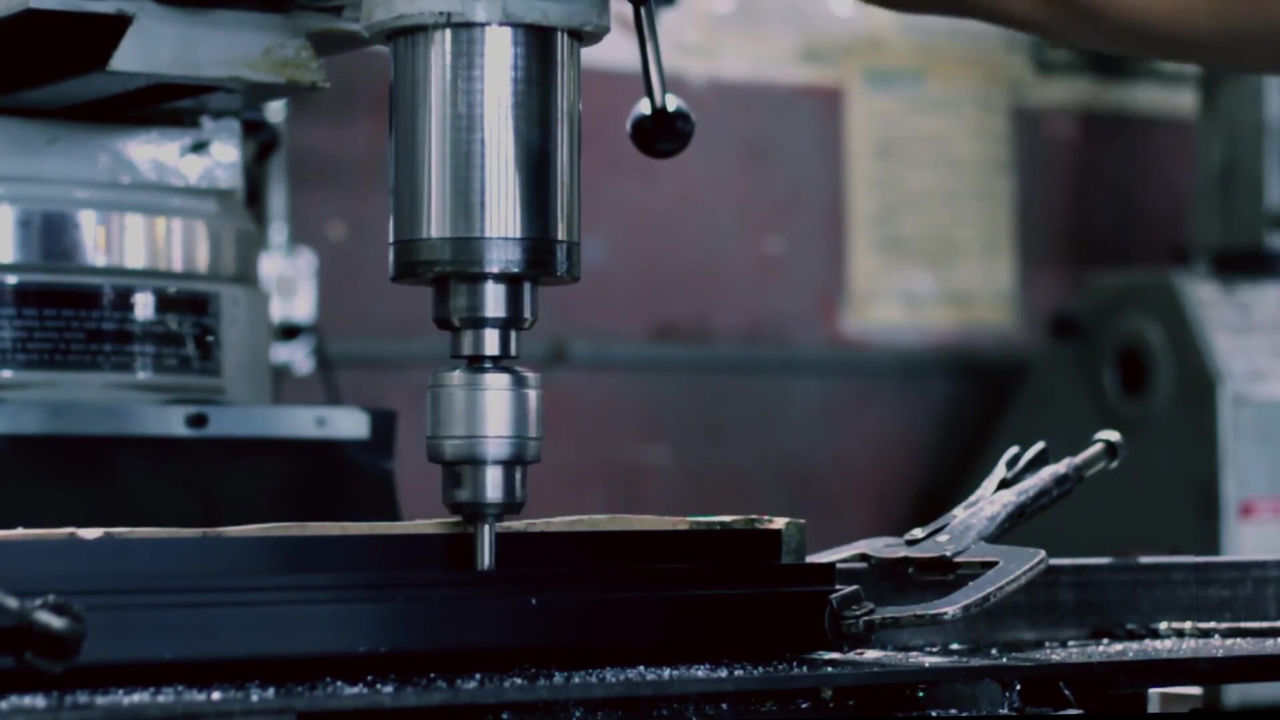
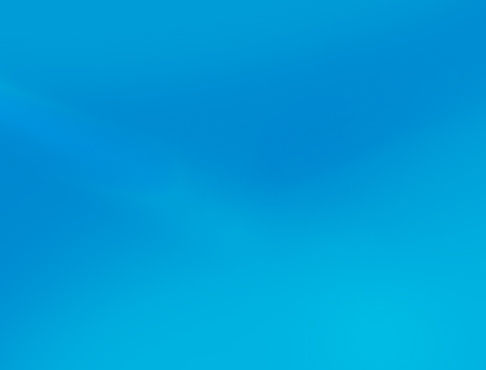
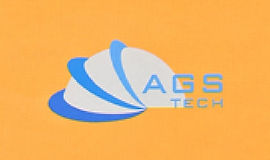
Çok Çeşitli Ürün ve Hizmetler için Küresel Özel Fason Üretici, Entegratör, Montaj Tedarikçisi, Global Imalat Ortağı.
Özel imal edilmiş ve kullanıma hazır fason ürün imalatı ve hizmetlerin tedariği, mühendisliği, konsolidasyonu, entegrasyonu, küresel fason üretim için tek durak kaynağınız biziz.
Choose your Language
-
Özel İmalatlar
-
Yerli & Global Fason Üretim
-
İmalat Dış Kaynak Kullanımı
-
Yurtiçi ve Küresel Tedarik
-
Konsolidasyon
-
Mühendislik Entegrasyonu
-
Mühendislik Hizmetleri
Üretilen parçalarınızı KAYNAK, LEHİM, LEHİM, SİNTER, YAPIŞTIRICI YAPIŞTIRMA, SABİTLEME, PRES FİTLEME kullanarak birleştirir, birleştirir ve sabitler ve bitmiş veya yarı mamul haline getiririz. En popüler kaynak süreçlerimizden bazıları ark, oksigaz, direnç, projeksiyon, dikiş, yığma, perküsyon, katı hal, elektron ışını, lazer, termit, endüksiyon kaynağıdır. Popüler lehimleme proseslerimiz torç, indüksiyon, fırın ve daldırma lehimlemedir. Lehimleme yöntemlerimiz demir, sıcak plaka, fırın, indüksiyon, daldırma, dalga, reflow ve ultrasonik lehimlemedir. Yapışkan bağlama için sıklıkla termoplastikler ve termoset, epoksiler, fenolikler, poliüretan, yapışkan alaşımlar ve ayrıca bazı diğer kimyasallar ve bantlar kullanıyoruz. Son olarak sabitleme işlemlerimiz; çivileme, vidalama, somun ve cıvata, perçinleme, perçinleme, iğneleme, dikiş ve zımbalama ve presle geçme işlemlerinden oluşmaktadır.
• KAYNAK : Kaynak, iş parçalarının eritilerek ve aynı zamanda erimiş kaynak havuzunu da birleştiren dolgu malzemelerinin eklenmesiyle malzemelerin birleştirilmesini içerir. Alan soğuduğunda güçlü bir derz elde ederiz. Bazı durumlarda basınç uygulanır. Kaynaktan farklı olarak, lehimleme ve lehimleme işlemleri, iş parçaları arasında yalnızca erime noktası daha düşük olan bir malzemenin eritilmesini içerir ve iş parçaları erimez. için buraya tıklamanızı öneririz.AGS-TECH Inc. tarafından hazırlanan Kaynak İşlemleri Şematik Gösterimlerimizi İNDİRİN
Bu, aşağıda size sağladığımız bilgileri daha iyi anlamanıza yardımcı olacaktır.
ARK KAYNAĞI'nda metalleri eriten bir elektrik arkı oluşturmak için bir güç kaynağı ve bir elektrot kullanıyoruz. Kaynak noktası bir koruyucu gaz veya buhar veya başka bir malzeme ile korunur. Bu işlem, otomotiv parçalarının ve çelik yapıların kaynağı için popülerdir. Shelted metal ark kaynağında (SMAW) veya çubuk kaynağı olarak da bilinir, ana malzemeye bir elektrot çubuğu yaklaştırılır ve aralarında bir elektrik arkı oluşturulur. Elektrot çubuğu erir ve dolgu malzemesi görevi görür. Elektrot ayrıca bir cüruf tabakası görevi gören ve koruyucu gaz görevi gören buharlar veren akı içerir. Bunlar, kaynak alanını çevresel kirlilikten korur. Başka hiçbir dolgu maddesi kullanılmamaktadır. Bu işlemin dezavantajları, yavaşlığı, elektrotları sık sık değiştirme ihtiyacı, akıdan kaynaklanan artık cürufu ufalama ihtiyacıdır. Demir, çelik, nikel, alüminyum, bakır vb. gibi bir dizi metal. Kaynak yapılabilir. Avantajları, ucuz araçları ve kullanım kolaylığıdır. Metal inert gaz (MIG) olarak da bilinen gaz metal ark kaynağı (GMAW), bir sarf malzemesi elektrot tel dolgusu ve kaynak bölgesinin çevresel kirlenmesine karşı telin etrafında akan bir asal veya kısmen asal gazın sürekli beslenmesine sahibiz. Çelik, alüminyum ve diğer demir dışı metaller kaynaklanabilir. MIG'nin avantajları, yüksek kaynak hızları ve kaliteli olmasıdır. Dezavantajları, karmaşık ekipmanı ve rüzgarlı dış ortamlarda karşılaşılan zorluklardır, çünkü kaynak alanı çevresindeki koruyucu gazı sabit tutmamız gerekir. GMAW'ın bir varyasyonu, akı malzemeleriyle doldurulmuş ince bir metal borudan oluşan akı özlü ark kaynağıdır (FCAW). Bazen tüpün içindeki akı, çevresel kontaminasyondan korunmak için yeterlidir. Tozaltı Ark Kaynağı (SAW), yaygın olarak otomatikleştirilmiş bir işlemdir, sürekli tel beslemeyi ve bir akı örtüsü tabakasının altına vurulan arkı içerir. Üretim oranları ve kalitesi yüksek, kaynak cürufu kolayca çıkıyor ve dumansız bir çalışma ortamımız var. Dezavantajı ise sadece parts'ı belirli konumlarda kaynaklamak için kullanılabilmesidir. Gaz tungsten ark kaynağında (GTAW) veya tungsten inert gaz kaynağında (TIG) ayrı bir dolgu maddesi ve atıl veya yakın soy gazlarla birlikte bir Tungsten elektrot kullanırız. Bildiğimiz gibi Tungsten yüksek bir erime noktasına sahiptir ve çok yüksek sıcaklıklar için çok uygun bir metaldir. TIG'deki Tungsten, yukarıda açıklanan diğer yöntemlerin aksine tüketilmez. İnce malzemelerin kaynağında diğer tekniklere göre avantajlı, yavaş fakat kaliteli bir kaynak tekniğidir. Birçok metal için uygundur. Plazma ark kaynağı benzerdir ancak ark oluşturmak için plazma gazı kullanır. Plazma ark kaynağındaki ark, GTAW'a kıyasla nispeten daha yoğundur ve çok daha yüksek hızlarda daha geniş bir metal kalınlık aralığı için kullanılabilir. GTAW ve plazma ark kaynağı aşağı yukarı aynı malzemelere uygulanabilir.
OXY-FUEL / OXYFUEL KAYNAK ayrıca oksiasetilen kaynağı, oksi kaynak, gaz kaynağı olarak da adlandırılan gaz yakıtları ve kaynak için oksijen kullanılarak gerçekleştirilir. Elektrik enerjisi kullanılmadığından portatiftir ve elektriğin olmadığı yerlerde kullanılabilir. Bir kaynak torcu kullanarak, ortak bir erimiş metal havuzu oluşturmak için parçaları ve dolgu malzemesini ısıtıyoruz. Asetilen, benzin, hidrojen, propan, bütan vb. gibi çeşitli yakıtlar kullanılabilir. Oksi-yakıt kaynağında biri yakıt, diğeri oksijen için olmak üzere iki kap kullanırız. Oksijen yakıtı oksitler (yakar).
DİRENÇ KAYNAĞI: Bu kaynak türü, joule ısıtmasından yararlanır ve elektrik akımının uygulandığı yerde belirli bir süre ısı üretilir. Metalden yüksek akımlar geçirilir. Bu yerde erimiş metal havuzları oluşur. Direnç kaynağı yöntemleri, verimlilikleri ve az kirlilik potansiyeli nedeniyle popülerdir. Bununla birlikte dezavantajlar, ekipman maliyetlerinin nispeten önemli olması ve nispeten ince iş parçalarının doğasında bulunan sınırlamadır. PUNTA KAYNAK, ana direnç kaynağı türlerinden biridir. Burada, iki veya daha fazla örtüşen levhayı veya iş parçasını, levhaları birbirine kenetlemek ve aralarından yüksek akım geçirmek için iki bakır elektrot kullanarak birleştiriyoruz. Bakır elektrotlar arasındaki malzeme ısınır ve o yerde erimiş bir havuz oluşur. Daha sonra akım durdurulur ve elektrotlar su ile soğutulduğu için bakır elektrot uçları kaynak yerini soğutur. Doğru malzemeye ve kalınlığa doğru miktarda ısı uygulamak bu tekniğin anahtarıdır, çünkü yanlış uygulanırsa bağlantı zayıf olacaktır. Punta kaynağı, iş parçalarında önemli bir deformasyona neden olmaması, enerji verimliliği, otomasyon kolaylığı ve üstün üretim oranları ve herhangi bir dolgu maddesi gerektirmemesi gibi avantajlara sahiptir. Dezavantajı ise, kaynak sürekli bir dikiş oluşturmak yerine noktalarda gerçekleştiğinden, diğer kaynak yöntemlerine kıyasla toplam mukavemet nispeten daha düşük olabilir. DİKİŞ KAYNAĞI ise benzer malzemelerin dökülen yüzeylerinde kaynaklar üretir. Dikiş, alın veya üst üste binen eklem olabilir. Dikiş kaynağı bir uçtan başlar ve kademeli olarak diğerine doğru hareket eder. Bu yöntem ayrıca kaynak bölgesine basınç ve akım uygulamak için bakırdan iki elektrot kullanır. Disk şeklindeki elektrotlar, dikiş hattı boyunca sabit temasla döner ve sürekli bir kaynak yapar. Burada da elektrotlar su ile soğutulur. Kaynaklar çok güçlü ve güvenilirdir. Diğer yöntemler projeksiyon, flaş ve yığma kaynak teknikleridir.
KATI HAL KAYNAK yukarıda açıklanan önceki yöntemlerden biraz farklıdır. Birleşme, birleştirilen metallerin erime sıcaklığının altındaki sıcaklıklarda ve metal dolgu maddesi kullanılmadan gerçekleşir. Bazı işlemlerde basınç kullanılabilir. Farklı metallerin aynı kalıptan ekstrüde edildiği KOEXTRÜZYON KAYNAK, yumuşak alaşımları erime noktalarının altında birleştirdiğimiz SOĞUK BASINÇ KAYNAĞI, görünür kaynak çizgileri olmayan bir teknik DİFÜZYON KAYNAK, farklı malzemelerin, örneğin korozyona dayanıklı alaşımların yapısal malzemelerle birleştirilmesi için PATLAMA KAYNAĞI çeşitli yöntemlerdir. çelikler, boru ve sacları elektromanyetik kuvvetlerle hızlandırdığımız ELEKTROMANYETİK DARBE KAYNAĞI, metallerin yüksek sıcaklıklara ısıtılıp bir araya getirilmesinden oluşan FORGE KAYNAĞI, yeterli sürtünme kaynağının yapıldığı SÜRTÜNME KAYNAĞI, Dönmeyen, dönmeyen bir sürtünme içeren SÜRTÜNME KAYNAĞI. bağlantı hattını geçen sarf malzemesi aracı, vakum veya soy gazlarda erime sıcaklığının altındaki yüksek sıcaklıklarda metalleri birbirine bastırdığımız SICAK BASINÇ KAYNAĞI, SICAK İZOSTATİK BASINÇ KAYNAĞI bir kap içinde soy gazlar kullanarak basınç uyguladığımız bir işlem, birleştiğimiz RULO KAYNAK aralarında zorlayarak farklı malzemeleri iki döner tekerlek, ince metal veya plastik levhaların yüksek frekanslı titreşim enerjisi kullanılarak kaynaklandığı ULTRASONİK KAYNAK.
Diğer kaynak yöntemlerimiz, derin nüfuziyetli ve hızlı işlemeli ancak pahalı bir yöntem olduğunu düşündüğümüz derin nüfuziyetli ELEKTRON KAYNAK KAYNAĞI, sadece ağır kalın levhalar ve çelik iş parçaları için uygun bir yöntem olan ELEKTROSLAG KAYNAK, elektromanyetik indüksiyon kullandığımız İNDÜKSİYON KAYNAK ve elektriksel olarak iletken veya ferromanyetik iş parçalarımızı ısıtır, ayrıca derin penetrasyon ve hızlı işleme ile LAZER IŞIN KAYNAK, ancak pahalı bir yöntem, LBW ile GMAW'ı aynı kaynak kafasında birleştiren ve plakalar arasında 2 mm'lik boşlukları köprüleyebilen LAZER HİBRİT KAYNAK, VURMALI KAYNAK bu Malzemelerin uygulanan basınçla dövülmesinin ardından elektrik deşarjı, alüminyum ve demir oksit tozları arasındaki ekzotermik reaksiyonu içeren THERMIT KAYNAĞI, sarf elektrotlarla ve sadece dikey konumda kullanılan ELEKTROGAZ KAYNAĞI ve son olarak saplamayı tabana birleştirmek için SAPLAMA ARK KAYNAĞI içerir. ısı ve basınç ile malzeme.
için buraya tıklamanızı öneririz.AGS-TECH Inc. tarafından sunulan Lehimleme, Lehimleme ve Yapıştırıcı Yapıştırma İşlemlerine ilişkin Şematik Çizimlerimizi İNDİRİN
Bu, aşağıda size sağladığımız bilgileri daha iyi anlamanıza yardımcı olacaktır.
• LEHİMLEME : İki veya daha fazla metali, aralarındaki dolgu metallerini erime noktalarının üzerinde ısıtarak ve yaymak için kılcal etki kullanarak birleştiririz. İşlem lehimlemeye benzer, ancak dolguyu eritmek için gerekli sıcaklıklar sert lehimlemede daha yüksektir. Kaynakta olduğu gibi, akı dolgu malzemesini atmosferik kirlenmeden korur. Soğuduktan sonra iş parçaları birleştirilir. Proses, aşağıdaki temel adımları içerir: İyi oturma ve boşluk, temel malzemelerin uygun şekilde temizlenmesi, uygun sabitleme, uygun akı ve atmosfer seçimi, montajın ısıtılması ve son olarak lehimli montajın temizlenmesi. Lehimleme süreçlerimizden bazıları, manuel veya otomatik bir şekilde gerçekleştirilen popüler bir yöntem olan TORCH LEHTARLAMADIR. Düşük hacimli üretim siparişleri ve özel durumlar için uygundur. Lehimlenen bağlantının yakınında gaz alevleri kullanılarak ısı uygulanır. FIRIN LEHİMLEME, daha az operatör becerisi gerektirir ve endüstriyel seri üretime uygun yarı otomatik bir işlemdir. Hem sıcaklık kontrolü hem de fırındaki atmosferin kontrolü bu tekniğin avantajlarıdır, çünkü birincisi kontrollü ısı döngülerine sahip olmamızı ve torç lehiminde olduğu gibi lokal ısıtmayı ortadan kaldırmamızı sağlar ve ikincisi parçayı oksidasyondan korur. Jigging kullanarak üretim maliyetlerini minimuma indirme yeteneğine sahibiz. Dezavantajları ise yüksek güç tüketimi, ekipman maliyetleri ve daha zorlu tasarım konularıdır. VAKUM LEHİMLEME, bir vakum fırınında gerçekleşir. Sıcaklık tekdüzeliği korunur ve çok az kalıntı gerilimi olan akıcı, çok temiz bağlantılar elde ederiz. Yavaş ısıtma ve soğutma döngüleri sırasında mevcut olan düşük kalıntı gerilimler nedeniyle, ısıl işlemler vakumlu sert lehimleme sırasında gerçekleştirilebilir. En büyük dezavantajı yüksek maliyetidir çünkü vakum ortamının oluşturulması pahalı bir işlemdir. Yine bir başka teknik DIP LEHTARLAMA, lehimleme bileşiğinin eşleşen yüzeylere uygulandığı sabitlenmiş parçaları birleştirir. Bundan sonra, fikstürlü parçalar, bir ısı transfer ortamı ve akış işlevi gören Sodyum Klorür (sofra tuzu) gibi bir erimiş tuz banyosuna daldırılır. Hava hariç tutulur ve bu nedenle oksit oluşumu gerçekleşmez. İNDÜKSİYON LEHİMİNDE, malzemeleri ana malzemelerden daha düşük bir erime noktasına sahip bir dolgu metali ile birleştiriyoruz. İndüksiyon bobininden gelen alternatif akım, çoğunlukla demir içeren manyetik malzemeler üzerinde indüksiyon ısıtmasını indükleyen bir elektromanyetik alan oluşturur. Yöntem, seçici ısıtma, dolgu maddelerinin sadece istenen alanlarda akan iyi derzler, alev olmadığı ve soğutmanın hızlı olması nedeniyle az oksidasyon, hızlı ısıtma, tutarlılık ve yüksek hacimli üretim için uygunluk sağlar. Süreçlerimizi hızlandırmak ve tutarlılığı sağlamak için sıklıkla preform kullanıyoruz. Seramikten metale bağlantı parçaları, hermetik sızdırmazlık, vakumlu geçişler, yüksek ve ultra yüksek vakum ve sıvı kontrol bileşenleri üreten lehimleme tesisimiz hakkında bilgiler burada bulunabilir: Lehimleme Fabrikası Broşürü
• LEHİM : Lehimlemede iş parçalarının erimesi değil, birleşme yerine akan birleştirme parçalarından daha düşük erime noktasına sahip bir dolgu metali vardır. Lehimlemedeki dolgu metali, sert lehimlemeden daha düşük sıcaklıkta erir. Lehimleme için kurşunsuz alaşımlar kullanıyoruz ve RoHS uyumluluğumuz var ve farklı uygulama ve gereksinimler için gümüş alaşımı gibi farklı ve uygun alaşımlarımız var. Lehimleme bize gaz ve sıvı geçirmez bağlantılar sunar. YUMUŞAK LEHİM'de dolgu metalimizin erime noktası 400 Santigrat'ın altındayken, GÜMÜŞ LEHİM ve LEHİM'de daha yüksek sıcaklıklara ihtiyacımız var. Yumuşak lehimleme daha düşük sıcaklıklar kullanır, ancak yüksek sıcaklıklarda zorlu uygulamalar için güçlü bağlantılarla sonuçlanmaz. Gümüş lehimleme ise torç tarafından sağlanan yüksek sıcaklıklar gerektirir ve bize yüksek sıcaklık uygulamalarına uygun güçlü bağlantılar sağlar. Lehimleme en yüksek sıcaklıkları gerektirir ve genellikle bir torç kullanılır. Sert lehim bağlantıları çok güçlü olduğundan, ağır demir nesnelerin onarımı için iyi bir adaydır. Üretim hatlarımızda hem manuel el lehimleme hem de otomatik lehim hatları kullanıyoruz. İNDÜKSİYON LEHİM, indüksiyonla ısıtmayı kolaylaştırmak için bir bakır bobinde yüksek frekanslı AC akımı kullanır. Lehimli kısımda akımlar indüklenir ve bunun sonucunda yüksek direnç joint'te ısı üretilir. Bu ısı dolgu metalini eritir. Akı da kullanılır. İndüksiyon lehimleme, silindirleri ve boruları sürekli bir işlemde, bobinleri etraflarına sararak lehimlemek için iyi bir yöntemdir. Grafit ve seramik gibi bazı malzemelerin lehimlenmesi, lehimleme öncesinde iş parçalarının uygun bir metal ile kaplanmasını gerektirdiğinden daha zordur. Bu, arayüzey yapışmasını kolaylaştırır. Bu tür malzemeleri özellikle hermetik paketleme uygulamaları için lehimliyoruz. Baskılı devre kartlarımızı (PCB) çoğunlukla DALGA LEHİM kullanarak yüksek hacimde üretiyoruz. Sadece küçük miktarda prototipleme amacıyla havya kullanarak elle lehimleme kullanıyoruz. Hem açık delik hem de yüzeye monte PCB düzenekleri (PCBA) için dalga lehimleme kullanıyoruz. Geçici bir yapıştırıcı, bileşenleri devre kartına bağlı tutar ve düzenek bir konveyöre yerleştirilir ve erimiş lehim içeren bir ekipman boyunca hareket eder. Önce PCB flukslanır ve ardından ön ısıtma bölgesine girer. Erimiş lehim bir tavadadır ve yüzeyinde duran dalgalardan oluşan bir desene sahiptir. PCB bu dalgalar üzerinde hareket ettiğinde, bu dalgalar PCB'nin alt kısmına temas eder ve lehim pedlerine yapışır. Lehim, PCB'nin kendisinde değil, yalnızca pimlerde ve pedlerde kalır. Erimiş lehimdeki dalgalar iyi kontrol edilmelidir, böylece sıçrama olmaz ve dalga tepeleri dokunmaz ve levhaların istenmeyen alanlarını kirletmez. REFLOW SOLDERING'de elektronik bileşenleri panolara geçici olarak tutturmak için yapışkan bir lehim pastası kullanıyoruz. Daha sonra levhalar, sıcaklık kontrollü bir yeniden akış fırınından geçirilir. Burada lehim erir ve bileşenleri kalıcı olarak bağlar. Bu tekniği hem yüzeye monteli bileşenler hem de delikten geçen bileşenler için kullanıyoruz. Kart üzerindeki elektronik bileşenlerin, maksimum sıcaklık sınırlarının üzerine çıkarak aşırı ısınmasını önlemek için, uygun sıcaklık kontrolü ve fırın sıcaklıklarının ayarlanması çok önemlidir. Yeniden akışlı lehimleme sürecinde aslında, ön ısıtma aşaması, termal ıslatma aşaması, yeniden akış ve soğutma aşamaları gibi her biri farklı bir termal profile sahip birkaç bölge veya aşamaya sahibiz. Bu farklı adımlar, baskılı devre kartı düzeneklerinin (PCBA) hasarsız yeniden akış lehimlemesi için gereklidir. ULTRASONİK LEHİM, benzersiz özelliklere sahip, sıklıkla kullanılan bir başka tekniktir- Cam, seramik ve metalik olmayan malzemeleri lehimlemek için kullanılabilir. Örneğin, metalik olmayan fotovoltaik paneller, bu teknik kullanılarak yapıştırılabilen elektrotlara ihtiyaç duyar. Ultrasonik lehimlemede, aynı zamanda ultrasonik titreşimler yayan ısıtılmış bir lehim ucu kullanırız. Bu titreşimler, alt tabakanın erimiş lehim malzemesi ile ara yüzeyinde kavitasyon kabarcıkları üretir. Kavitasyonun patlayıcı enerjisi oksit yüzeyini değiştirir ve kiri ve oksitleri giderir. Bu süre zarfında bir alaşım tabakası da oluşur. Yapıştırma yüzeyindeki lehim oksijen içerir ve cam ile lehim arasında güçlü bir ortak bağ oluşmasını sağlar. DIP SOLDERING, sadece küçük ölçekli üretime uygun dalga lehimlemenin daha basit bir versiyonu olarak kabul edilebilir. Diğer işlemlerde olduğu gibi ilk temizleme akısı uygulanır. Monte edilmiş bileşenlere sahip PCB'ler, erimiş lehim içeren bir tanka manuel veya yarı otomatik bir şekilde daldırılır. Erimiş lehim, tahtadaki lehim maskesi tarafından korunmayan açıkta kalan metalik alanlara yapışır. Ekipman basit ve ucuzdur.
• YAPIŞTIRICI YAPIŞTIRMA : Sık kullandığımız bir başka popüler tekniktir ve yapıştırıcılar, epoksiler, plastik maddeler veya diğer kimyasallar kullanılarak yüzeylerin yapıştırılmasını içerir. Yapışma, solventin buharlaştırılması, ısıyla kürleme, UV ışık kürleme, basınç kürleme veya belirli bir süre beklenerek gerçekleştirilir. Üretim hatlarımızda çeşitli yüksek performanslı yapıştırıcılar kullanılmaktadır. Uygun şekilde tasarlanmış uygulama ve kürleme süreçleriyle, yapıştırıcıyla yapıştırma, güçlü ve güvenilir olan çok düşük gerilimli bağlarla sonuçlanabilir. Yapışkan bağlar nem, kirleticiler, aşındırıcılar, titreşim vb. gibi çevresel faktörlere karşı iyi koruyucular olabilir. Yapıştırıcıyla birleştirmenin avantajları şunlardır: aksi takdirde lehimlenmesi, kaynaklanması veya sert lehimlenmesi zor olan malzemelere uygulanabilirler. Ayrıca kaynak veya diğer yüksek sıcaklık işlemlerinden zarar görecek ısıya duyarlı malzemeler için de tercih edilebilir. Yapıştırıcıların diğer avantajları, düzensiz şekilli yüzeylere uygulanabilmeleri ve diğer yöntemlere kıyasla montaj ağırlığını çok çok küçük miktarlarda artırabilmeleridir. Ayrıca parçalardaki boyutsal değişiklikler çok azdır. Bazı yapıştırıcılar, indeks eşleştirme özelliklerine sahiptir ve ışık veya optik sinyal gücünü önemli ölçüde azaltmadan optik bileşenler arasında kullanılabilir. Dezavantajları ise üretim hatlarını yavaşlatabilen daha uzun kürlenme süreleri, fikstür gereksinimleri, yüzey hazırlama gereksinimleri ve yeniden işleme gerektiğinde sökme zorluğudur. Yapıştırma operasyonlarımızın çoğu aşağıdaki adımları içerir:
-Yüzey işleme: Deiyonize su temizliği, alkol temizliği, plazma veya korona temizliği gibi özel temizleme prosedürleri yaygındır. Temizledikten sonra, mümkün olan en iyi derzleri sağlamak için yüzeylere yapışma arttırıcılar uygulayabiliriz.
- Parça Sabitleme: Hem yapıştırıcı uygulaması hem de kürleme için özel fikstürler tasarlıyor ve kullanıyoruz.
-Yapıştırıcı Uygulaması: Yapıştırıcıları doğru yere ulaştırmak için bazen manuel, bazen de duruma bağlı olarak robotik, servo motor, lineer aktüatör gibi otomatik sistemler, doğru hacim ve miktarda dağıtmak için dispenserler kullanıyoruz.
-Kürleme: Yapıştırıcıya bağlı olarak, basit kurutma ve kürlemenin yanı sıra katalizör görevi gören UV ışıkları altında kürleme veya bir fırında ısıl kürleme veya aparatlara ve fikstürlere monte edilmiş dirençli ısıtma elemanları kullanarak kürleme yapabiliriz.
için buraya tıklamanızı öneririz.AGS-TECH Inc.
Bu, aşağıda size sağladığımız bilgileri daha iyi anlamanıza yardımcı olacaktır.
• BAĞLAMA SÜREÇLERİ : Mekanik birleştirme işlemlerimiz iki farklı kategoriye ayrılır: BAĞLANTI ELEMANLARI ve ENTEGRAL KAYNAKLAR. Kullandığımız bağlantı elemanları örnekleri vidalar, pimler, somunlar, cıvatalar, perçinlerdir. Kullandığımız yekpare bağlantı örnekleri, geçmeli ve büzüşmeli geçmeler, dikişler, kıvrımlardır. Çeşitli sabitleme yöntemleri kullanarak mekanik bağlantılarımızın uzun yıllar kullanım için güçlü ve güvenilir olmasını sağlıyoruz. VİDALAR ve CIVATALAR, nesneleri bir arada tutmak ve konumlandırmak için en yaygın kullanılan bağlantı elemanlarından bazılarıdır. Vidalarımız ve cıvatalarımız ASME standartlarını karşılamaktadır. Altıgen başlı vidalar ve altıgen cıvatalar, gecikmeli vidalar ve cıvatalar, çift uçlu vida, dübel vidası, delikli vida, ayna vidası, sac vida, ince ayar vidası, matkap uçlu ve kendinden diş açan vidalar dahil olmak üzere çeşitli vida ve cıvata türleri kullanılır. , ayar vidası, yerleşik rondelalı vidalar… ve daha fazlası. Havşa başlı, kubbeli, yuvarlak, flanşlı gibi çeşitli vida başlı tiplerimiz ve slot, phillips, kare, altıgen soket gibi çeşitli vidalı tahrik çeşitlerimiz bulunmaktadır. A RIVET ise düz silindirik bir şaft ve bir kafadan oluşan kalıcı bir mekanik bağlantı elemanıdır. Yerleştirme işleminden sonra perçinin diğer ucu deforme olur ve çapı genişletilerek yerinde kalması sağlanır. Başka bir deyişle, perçin kurulumdan önce bir başlı ve kurulumdan sonra iki başlıdır. Masif/yuvarlak başlı perçinler, yapısal, yarı borulu, kör, oscar, tahrikli, gömme, sürtünme kilitli, kendinden delen perçinler gibi uygulamaya, mukavemete, erişilebilirliğe ve maliyete bağlı olarak çeşitli perçin çeşitlerini kuruyoruz. Kaynak ısısından kaynaklanan ısıl deformasyon ve malzeme özelliklerinde değişiklik olmaması gereken durumlarda perçinleme tercih edilebilir. Perçinleme ayrıca hafiflik ve özellikle kesme kuvvetlerine karşı iyi mukavemet ve dayanıklılık sunar. Çekme yüklerine karşı ise vida, somun ve civata daha uygun olabilir. CLINCHING işleminde, birleştirilmekte olan sac metaller arasında mekanik bir kilit oluşturmak için özel zımba ve kalıplar kullanıyoruz. Zımba, sac levha katmanlarını kalıp boşluğuna iter ve kalıcı bir bağlantı oluşumuna neden olur. Perçinlemede ısıtma ve soğutma gerekmez ve soğuk bir çalışma işlemidir. Bazı durumlarda punta kaynağının yerini alabilecek ekonomik bir işlemdir. PİMLEMEde, makine parçalarının birbirlerine göre konumlarını sabitlemek için kullanılan makine elemanları olan pimler kullanıyoruz. Başlıca türleri çatal pimler, kopilya pimleri, yaylı pimler, kavelalar, ve ayrık pimlerdir. ZIMBALAMA'da malzemeleri birleştirmek veya bağlamak için kullanılan iki uçlu bağlantı elemanları olan zımba tabancaları ve zımbalar kullanıyoruz. Zımbalamanın aşağıdaki avantajları vardır: Ekonomik, basit ve kullanımı hızlıdır, zımbaların tepesi, birbirine kenetlenmiş malzemeleri köprülemek için kullanılabilir, Zımbanın tepesi, kablo gibi bir parçayı köprülemeyi ve delmeden veya delmeden bir yüzeye sabitlemeyi kolaylaştırabilir. zarar verici, nispeten kolay çıkarılması. PRES TAKMA, parçaların birbirine itilmesiyle gerçekleştirilir ve aralarındaki sürtünme parçaları birbirine bağlar. Büyük boyutlu bir şaft ve küçük boyutlu bir delikten oluşan pres geçme parçalar genellikle iki yöntemden biriyle monte edilir: Ya kuvvet uygulayarak ya da parçaların ısıl genleşmesinden veya büzülmesinden yararlanarak. Bir pres bağlantısı kuvvet uygulanarak kurulduğunda ya hidrolik pres ya da elle çalıştırılan pres kullanırız. Öte yandan termal genleşme ile pres bağlantı kurulduğunda, saran parçaları ısıtıyoruz ve sıcakken yerlerine monte ediyoruz. Soğuduklarında kasılırlar ve normal boyutlarına dönerler. Bu, iyi bir baskı uyumu sağlar. Buna alternatif olarak SHRINK-FITTING diyoruz. Bunu yapmanın diğer yolu, montajdan önce zarflı parçaları soğutmak ve ardından eşleşen parçalarına kaydırmaktır. Montaj ısındığında genişler ve sıkı bir uyum elde ederiz. Bu ikinci yöntem, ısıtmanın malzeme özelliklerini değiştirme riski oluşturduğu durumlarda tercih edilebilir. Bu durumlarda soğutma daha güvenlidir.
Pnömatik & Hidrolik Bileşenler ve Montajlar
• Valfler, O-ring, rondela, contalar, conta, halka, şim gibi hidrolik ve pnömatik bileşenler.
Valfler ve pnömatik bileşenler çok çeşitli olduğu için burada her şeyi listeleyemeyiz. Uygulamanızın fiziksel ve kimyasal ortamlarına bağlı olarak size özel ürünlerimiz mevcuttur. Lütfen vanalarınız ve pnömatik bileşenlerinizle temas edecek uygulama, bileşen tipi, özellikler, basınç, sıcaklık, sıvı veya gazlar gibi ortam koşullarını belirtin; ve sizin için en uygun ürünü seçecek veya uygulamanıza özel üreteceğiz.