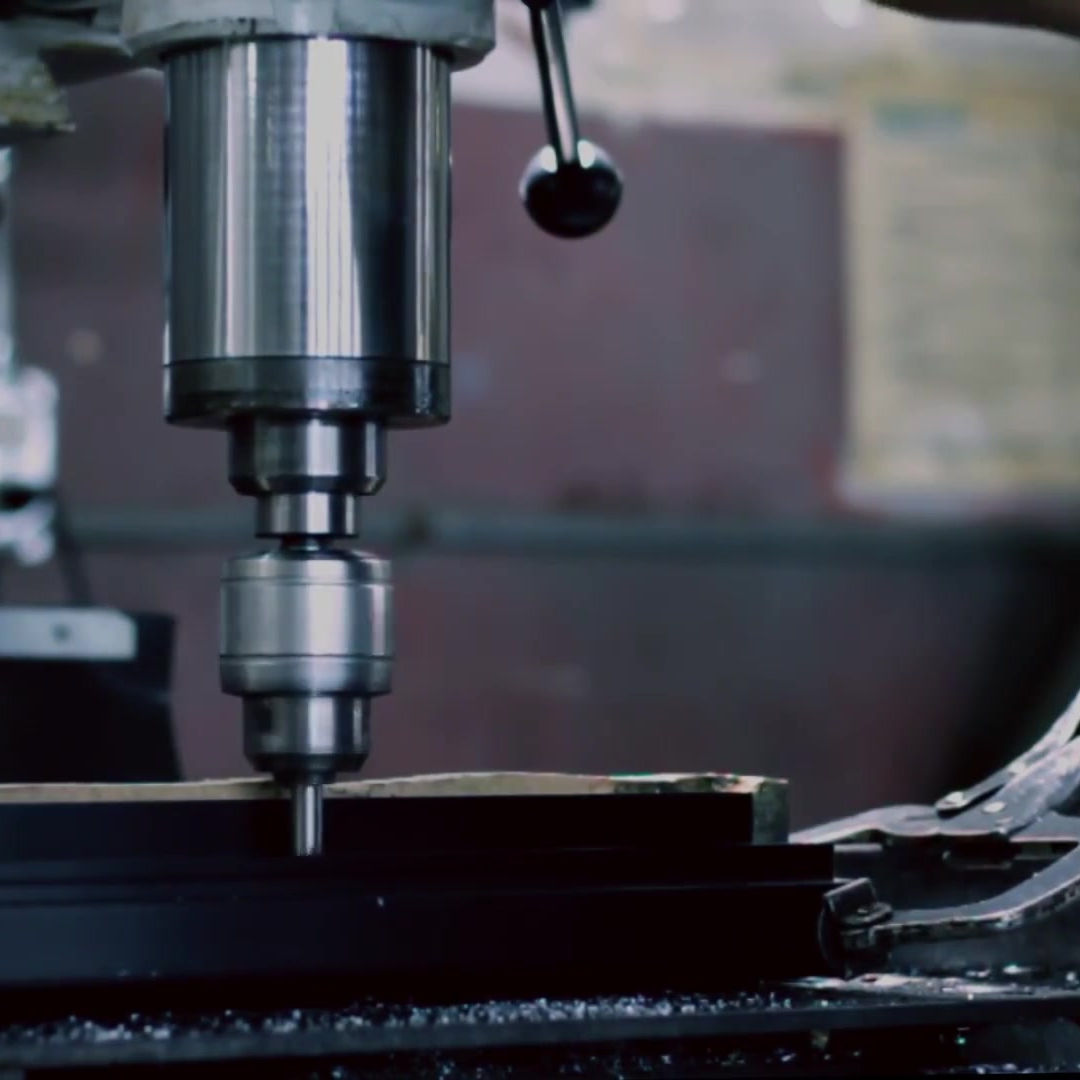
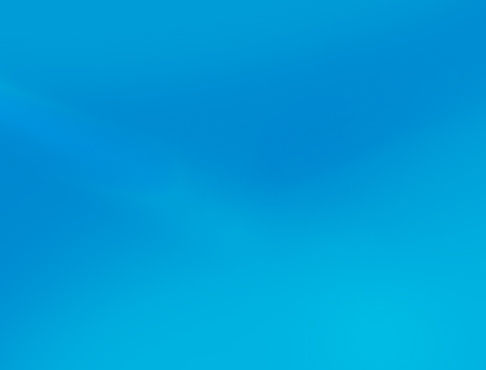
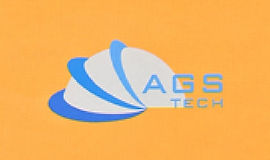
Çok Çeşitli Ürün ve Hizmetler için Küresel Özel Fason Üretici, Entegratör, Montaj Tedarikçisi, Global Imalat Ortağı.
Özel imal edilmiş ve kullanıma hazır fason ürün imalatı ve hizmetlerin tedariği, mühendisliği, konsolidasyonu, entegrasyonu, küresel fason üretim için tek durak kaynağınız biziz.
Choose your Language
-
Özel İmalatlar
-
Yerli & Global Fason Üretim
-
İmalat Dış Kaynak Kullanımı
-
Yurtiçi ve Küresel Tedarik
-
Konsolidasyon
-
Mühendislik Entegrasyonu
-
Mühendislik Hizmetleri
the PLASMA CUTTING and PLASMA MACHINING_cc781905-5cde ve diğer alüminyum, metal 136bad5cf58d_PLASMA MACHINING_cc319405-5cde malzemelerini kullanıyoruz. Plazma torcu kullanarak farklı kalınlıklar. Plazma kesmede (bazen PLASMA-ARC KESME olarak da adlandırılır), bir memeden yüksek hızda bir soy gaz veya sıkıştırılmış hava üflenir ve aynı anda bu gaz aracılığıyla memeden uçağa doğru bir elektrik arkı oluşturulur. kesilen yüzey, bu gazın bir kısmını plazmaya çeviriyor. Basitleştirmek gerekirse, plazma maddenin dördüncü hali olarak tanımlanabilir. Maddenin üç hali katı, sıvı ve gazdır. Yaygın bir örnek olarak su, bu üç durum buz, su ve buhardır. Bu durumlar arasındaki fark, enerji seviyeleri ile ilgilidir. Buza ısı şeklinde enerji eklediğimizde erir ve su oluşturur. Daha fazla enerji eklediğimizde, su buhar şeklinde buharlaşır. Buhar için daha fazla enerji ekleyerek bu gazlar iyonize olur. Bu iyonizasyon işlemi gazın elektriksel olarak iletken olmasına neden olur. Bu elektriksel olarak iletken, iyonize gaza “plazma” diyoruz. Plazma çok sıcaktır ve kesilen metali eritir ve aynı zamanda erimiş metali kesimden uzaklaştırır. Plazmayı ince ve kalın, demir içeren ve içermeyen malzemeleri aynı şekilde kesmek için kullanıyoruz. El torçlarımız genellikle 2 inç kalınlığa kadar çelik levhayı kesebilir ve daha güçlü bilgisayar kontrollü torçlarımız 6 inç kalınlığa kadar çelik kesebilir. Plazma kesiciler, kesmek için çok sıcak ve lokalize bir koni üretir ve bu nedenle metal levhaları kavisli ve açılı şekillerde kesmek için çok uygundur. Plazma ark kesmede üretilen sıcaklıklar çok yüksektir ve oksijen plazma torçunda 9673 Kelvin civarındadır. Bu bize hızlı bir işlem, küçük çentik genişliği ve iyi yüzey kalitesi sunar. Tungsten elektrotları kullanan sistemlerimizde plazma inerttir ve argon, argon-H2 veya nitrojen gazları kullanılarak oluşturulur. Bununla birlikte, bazen hava veya oksijen gibi oksitleyici gazlar da kullanırız ve bu sistemlerde elektrot, hafniyumlu bakırdır. Havalı plazma torçunun avantajı, pahalı gazlar yerine hava kullanması ve böylece potansiyel olarak toplam işleme maliyetini düşürmesidir.
HF-TYPE PLAZMA CUTTING makinelerimiz, torç kafasından havayı iyonize etmek ve arkları başlatmak için yüksek frekanslı, yüksek voltajlı bir kıvılcım kullanır. HF plazma kesicilerimiz, torcun başlangıçta iş parçası malzemesiyle temas halinde olmasını gerektirmez ve BİLGİSAYAR SAYISAL KONTROL (CNC) cutting ile ilgili uygulamalar için uygundur. Diğer üreticiler, başlamak için ana metal ile uç teması gerektiren ilkel makineler kullanıyor ve ardından boşluk ayrılması meydana geliyor. Bu daha ilkel plazma kesiciler, başlangıçta temas ucu ve kalkan hasarına karşı daha hassastır.
Bizim PILOT-ARC TİPİ PLAZMA makinelerimiz, ilk temasa gerek kalmadan plazma üretmek için iki aşamalı bir işlem kullanır. İlk adımda, torç gövdesi içinde çok küçük bir yüksek yoğunluklu kıvılcımı başlatmak için yüksek voltajlı, düşük akımlı bir devre kullanılır ve küçük bir plazma gazı cebi üretilir. Buna pilot ark denir. Pilot ark, torç kafasına yerleştirilmiş bir elektrik dönüş yoluna sahiptir. Pilot ark, iş parçasının yakınına getirilene kadar korunur ve korunur. Orada pilot ark, ana plazma kesme arkını ateşler. Plazma arkları aşırı derecede sıcaktır ve 25.000 °C = 45.000 °F aralığındadır.
Ayrıca uyguladığımız daha geleneksel bir yöntem is OXYFUEL-GAS CUTTING (OFC) burada kaynak yaparken olduğu gibi bir torç kullanıyoruz. İşlem çelik, dökme demir ve dökme çelik kesmede kullanılır. Oksiyakıt-gaz kesiminde kesme prensibi, çeliğin oksidasyonu, yanması ve eritilmesine dayanır. Oksiyakıt gaz kesiminde kerf genişlikleri 1,5 ila 10 mm civarındadır. Plazma ark prosesi, oksi-yakıt prosesine bir alternatif olarak görülmüştür. Plazma ark prosesi, metali eritmek için ark kullanarak çalıştığı için oksi-yakıt prosesinden farklıdır, oysa oksi-yakıt prosesinde oksijen metali oksitler ve ekzotermik reaksiyondan gelen ısı metali eritir. Bu nedenle, oksi-yakıt işleminden farklı olarak, paslanmaz çelik, alüminyum ve demir dışı alaşımlar gibi refrakter oksitler oluşturan metallerin kesilmesi için plazma işlemi uygulanabilir.
PLASMA GOUGING Plazma kesmeye benzer bir işlem, tipik olarak plazma kesme ile aynı ekipmanla gerçekleştirilir. Plazma oluk açma, malzemeyi kesmek yerine farklı bir torç konfigürasyonu kullanır. Torç nozulu ve gaz difüzörü genellikle farklıdır ve metali üflemek için torç ile iş parçası arasındaki mesafe daha uzundur. Plazma oluk açma, yeniden işleme için bir kaynağın çıkarılması da dahil olmak üzere çeşitli uygulamalarda kullanılabilir.
Plazma kesicilerimizden bazıları CNC tezgahına entegre edilmiştir. CNC tezgahlarında temiz keskin kesimler elde etmek için torç kafasını kontrol eden bir bilgisayar bulunur. Modern CNC plazma ekipmanımız, kalın malzemeleri çok eksenli kesme yeteneğine sahiptir ve başka türlü mümkün olmayan karmaşık kaynak dikişlerine olanak tanır. Plazma ark kesicilerimiz, programlanabilir kontrollerin kullanımıyla yüksek oranda otomatikleştirilmiştir. Daha ince malzemeler için, çoğunlukla lazer kesicimizin üstün delik kesme yetenekleri nedeniyle lazerle kesmeyi plazma kesmeye tercih ediyoruz. Ayrıca, bize daha küçük bir ayak izi, daha fazla esneklik, daha iyi güvenlik ve daha hızlı çalışma sunan dikey CNC plazma kesme makineleri kullanıyoruz. Plazma kesme kenarının kalitesi, oksi-yakıt kesme işlemleriyle elde edilene benzer. Bununla birlikte, plazma işlemi eriterek kestiği için, karakteristik bir özellik, metalin tepesine doğru daha yüksek derecede erime olup, bu da üst kenarın yuvarlanmasına, kenarların düzgün olmamasına veya kesme kenarında bir eğime neden olur. Kesimin üstünde ve altında daha homojen bir ısıtma sağlamak için ark daralmasını iyileştirmek için daha küçük bir ağızlığa ve daha ince bir plazma arkına sahip yeni plazma torç modelleri kullanıyoruz. Bu, plazma kesim ve işlenmiş kenarlarda lazere yakın hassasiyet elde etmemizi sağlar. Bizim YÜKSEK TOLERANSLI PLAZMA ARK KESME (HTPAC) systems son derece dar bir plazma ile çalışır. Plazmanın odaklanması, üretilen oksijenin plazma deliğine girerken girdap yapmaya zorlanmasıyla sağlanır ve plazma memesinin aşağı akışına ikincil bir gaz akışı enjekte edilir. Arkı çevreleyen ayrı bir manyetik alanımız var. Bu, dönen gazın neden olduğu dönüşü koruyarak plazma jetini stabilize eder. Hassas CNC kontrolünü bu daha küçük ve daha ince torçlarla birleştirerek çok az veya hiç son işlem gerektirmeyen parçalar üretebiliyoruz. Plazma işlemede malzeme kaldırma oranları, Elektrik-Deşarj-İşleme (EDM) ve Lazer-Işın-İşleme (LBM) süreçlerinden çok daha yüksektir ve parçalar iyi tekrarlanabilirlikle işlenebilir.
PLAZMA ARK KAYNAĞI (PAW) gaz tungsten ark kaynağına (GTAW) benzer bir işlemdir. Elektrik arkı, genellikle sinterlenmiş tungstenden yapılmış bir elektrot ile iş parçası arasında oluşturulur. GTAW'dan temel fark, PAW'da elektrotu torç gövdesi içine yerleştirerek plazma arkının koruyucu gaz zarfından ayrılabilmesidir. Plazma daha sonra, arkı daraltan ve plazmayı yüksek hızlarda ve 20.000 °C'ye yaklaşan sıcaklıklarda menfezden çıkan ince delikli bir bakır memeden geçirilir. Plazma ark kaynağı, GTAW işlemine göre bir ilerlemedir. PAW kaynak işlemi, tüketilmeyen bir tungsten elektrot ve ince delikli bir bakır meme aracılığıyla daraltılmış bir ark kullanır. PAW, GTAW ile kaynak yapılabilen tüm metal ve alaşımları birleştirmek için kullanılabilir. Akım, plazma gaz akış hızı ve menfez çapı değiştirilerek birkaç temel PAW proses varyasyonu mümkündür:
Mikroplazma (< 15 Amper)
Eritme modu (15–400 Amper)
Anahtar deliği modu (>100 Amper)
Plazma ark kaynağında (PAW) GTAW'a kıyasla daha yüksek bir enerji konsantrasyonu elde ederiz. Malzemeye bağlı olarak maksimum 12 ila 18 mm (0,47 ila 0,71 inç) derinlikte derin ve dar penetrasyon elde edilebilir. Daha yüksek ark kararlılığı, çok daha uzun bir ark uzunluğuna (ayrıklık) ve ark uzunluğu değişikliklerine karşı çok daha fazla toleransa izin verir.
Ancak bir dezavantaj olarak, PAW, GTAW'a kıyasla nispeten pahalı ve karmaşık ekipman gerektirir. Ayrıca torç bakımı kritik ve daha zorludur. PAW'ın diğer dezavantajları şunlardır: Kaynak prosedürleri daha karmaşık olma eğilimindedir ve yerleştirme, vb.'deki değişikliklere karşı daha az toleranslıdır. Gerekli operatör becerisi GTAW'dan biraz daha fazladır. Orifis değişimi gereklidir.