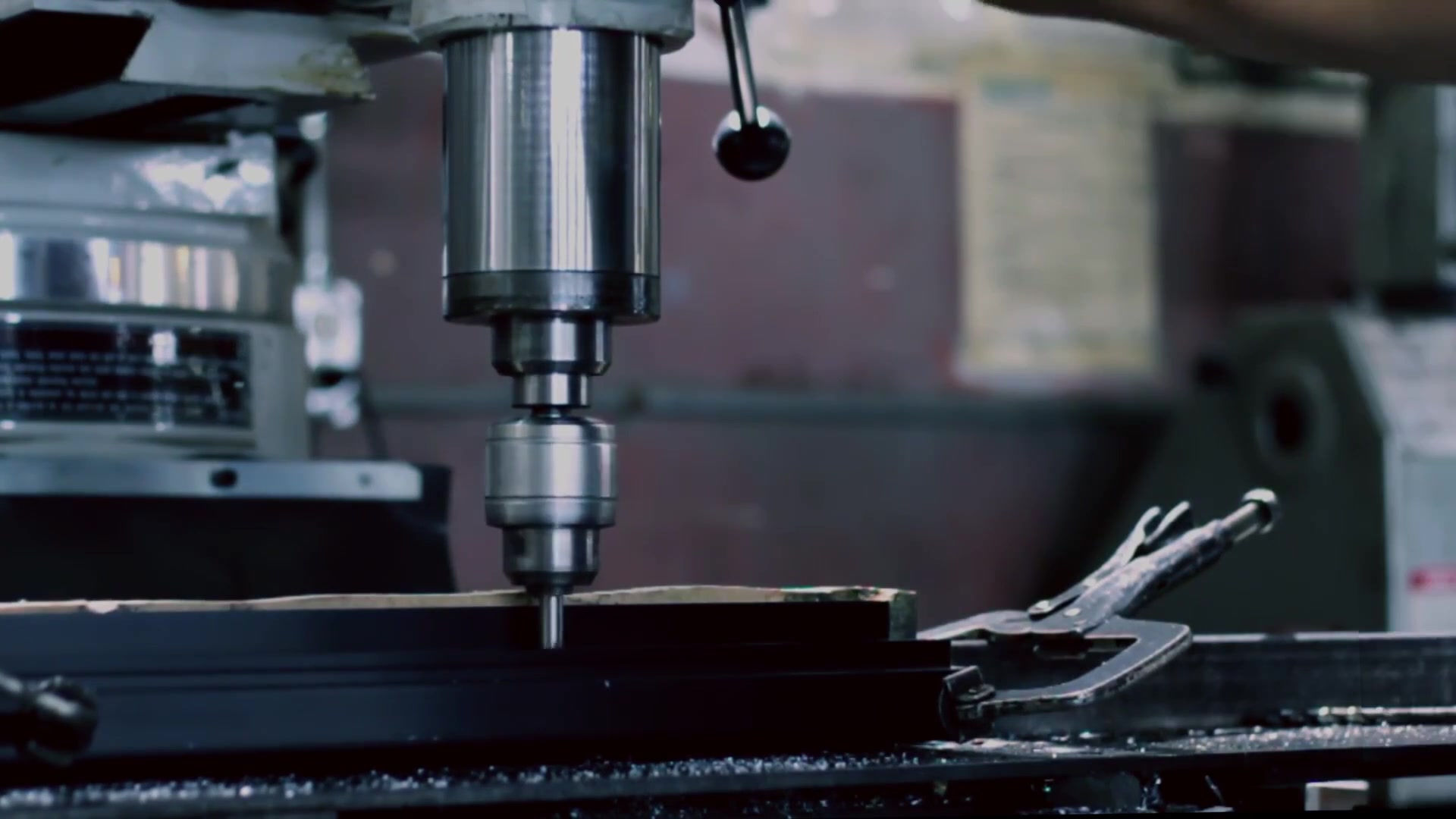
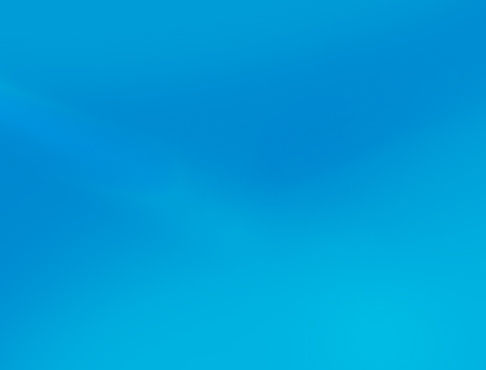
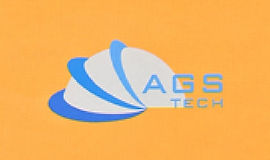
Çok Çeşitli Ürün ve Hizmetler için Küresel Özel Fason Üretici, Entegratör, Montaj Tedarikçisi, Global Imalat Ortağı.
Özel imal edilmiş ve kullanıma hazır fason ürün imalatı ve hizmetlerin tedariği, mühendisliği, konsolidasyonu, entegrasyonu, küresel fason üretim için tek durak kaynağınız biziz.
Choose your Language
-
Özel İmalatlar
-
Yerli & Global Fason Üretim
-
İmalat Dış Kaynak Kullanımı
-
Yurtiçi ve Küresel Tedarik
-
Konsolidasyon
-
Mühendislik Entegrasyonu
-
Mühendislik Hizmetleri
Search Results
Boş arama ile 161 sonuç bulundu
- Kayışlar, Zincirler, Kablo Tahrik Grubu, Kemerler, Kayış Tahrikleri, Yivli Kayışlar, Tırtıklı Kayışlar, Zaman Kayışı, Kasnaklar, Makaralı Zincirler
Kayışlar, Zincirler, Kablo Tahrik Grubu, Kemerler, Kayış Tahrikleri, Yivli Kayışlar, Tırtıklı Kayışlar, Zaman Kayışı, Kasnaklar, Makaralı Zincirler, Konveyör Zinciri, Ters Dişli Zincirler Kayışlar, Zincirler ve Kablo Tahrik Grubu AGS-TECH Inc. size Kayışlar ve Zincirler ve Kablo Tahrik Düzeneği dahil olmak üzere güç aktarım bileşenleri sunar. Yıllarca süren iyileştirme ile kauçuk, deri ve diğer kayış tahriklerimiz daha hafif ve daha kompakt hale geldi ve daha yüksek yükleri daha düşük maliyetle taşıyabiliyor. Benzer şekilde zincir tahriklerimiz de zaman içinde çok gelişti ve müşterilerimize çeşitli avantajlar sunuyorlar. Zincir tahrikleri kullanmanın bazı avantajları, nispeten sınırsız mil merkez mesafeleri, kompakt olmaları, montaj kolaylığı, kayma veya sürünme olmaksızın çekme esnekliği, yüksek sıcaklıklı ortamlarda çalışabilmeleridir. Kablo sürücülerimiz ayrıca bazı uygulamalarda diğer türdeki iletim bileşenlerine göre basitlik gibi avantajlar da sunar. Hem kullanıma hazır kayış, zincir ve kablo tahrikleri hem de özel olarak üretilmiş ve monte edilmiş versiyonlar mevcuttur. Bu şanzıman bileşenlerini uygulamanız için doğru boyutta ve en uygun malzemelerden üretebiliriz. KEMERLER VE KAYIŞ TAHRİKLERİ: - Konvansiyonel Düz Kayışlar: Dişsiz, yivsiz veya tırtıksız düz düz kayışlardır. Düz kayışlı tahrikler esneklik, iyi darbe emilimi, yüksek hızlarda verimli güç aktarımı, aşınma direnci ve düşük maliyet sunar. Daha büyük kayışlar yapmak için kayışlar eklenebilir veya bağlanabilir. Geleneksel düz kayışların diğer avantajları ince olmaları, yüksek merkezkaç yüklerine maruz kalmamalarıdır (küçük kasnaklarla yüksek hızlı işlemler için onları iyi yapar). Öte yandan, düz kayışlar yüksek gerilim gerektirdiğinden yüksek yatak yükleri uygularlar. Düz kayışlı tahriklerin diğer dezavantajları, kayma, gürültülü çalışma ve düşük ve orta çalışma hızlarında nispeten daha düşük verimlilik olabilir. İki tür geleneksel kayışımız var: Takviyeli ve Takviyesiz. Güçlendirilmiş kayışların yapısında bir germe elemanı bulunur. Konvansiyonel düz kayışlar, deri, lastikli kumaş veya kord, takviye edilmemiş kauçuk veya plastik, kumaş, takviyeli deri olarak mevcuttur. Deri kayışlar uzun ömür, esneklik, mükemmel sürtünme katsayısı, kolay onarım sunar. Ancak deri kemerler nispeten pahalıdır, kemerin giydirilmesi ve temizlenmesi gerekir ve atmosfere bağlı olarak küçülebilir veya esneyebilirler. Lastikli kumaş veya kord kayışları neme, aside ve alkalilere karşı dayanıklıdır. Lastikli kumaş kayışlar, kauçuk emdirilmiş pamuk veya sentetik ördek katlarından oluşur ve en ekonomik olanlardır. Lastikli kord kayışları, bir dizi kauçuk emdirilmiş kord katlarından oluşur. Lastikli kord kayışları, yüksek gerilme mukavemeti ve mütevazı boyut ve kütle sunar. Güçlendirilmemiş kauçuk veya plastik kayışlar, hafif hizmet, düşük hızlı tahrik uygulamaları için uygundur. Takviyesiz kauçuk ve plastik kayışlar, kasnakları üzerinden yerine gerdirilebilir. Takviyesiz plastik kayışlar, lastik kayışlara kıyasla daha yüksek güç iletebilir. Takviyeli deri kayışlar, deri üst ve alt katmanlar arasına sıkıştırılmış plastik bir gerdirme elemanından oluşur. Son olarak, kumaş kemerlerimiz tek parça pamuktan veya ördek katlanmış ve uzunlamasına dikişlerle dikilmiş olabilir. Kumaş kayışlar homojen bir şekilde izlenebilir ve yüksek hızda çalışabilir. - Yivli veya Tırtıklı Kayışlar (V-Kayışları gibi): Bunlar, başka bir tip transmisyon ürününün avantajlarını sağlamak için modifiye edilmiş temel düz kayışlardır. Bunlar, uzunlamasına nervürlü alt tarafı olan düz kayışlardır. Poly-V kayışları, izleme ve sıkıştırma amaçları için çekme bölümü ve bir dizi bitişik V-şekilli oluk ile uzunlamasına yivli veya tırtıklı düz kayışlardır. Güç kapasitesi kayış genişliğine bağlıdır. V-kayışı endüstrinin gücüdür ve hemen hemen her yük gücünün iletimi için çeşitli standart boyut ve tiplerde mevcuttur. V-kayış tahrikleri 1500 ila 6000 ft/dak arasında iyi çalışır, ancak dar V-kayışları 10.000 ft/dak'ya kadar çalışacaktır. V-kayışlı tahrikler 3 ila 5 yıl gibi uzun ömür sunar ve büyük hız oranlarına izin verir, takılması ve çıkarılması kolaydır, sessiz çalışma, düşük bakım, kayış sürücüsü ile tahrik edilen miller arasında iyi darbe emilimi sunar. V-kayışlarının dezavantajı, belirli kayma ve kaymalarıdır ve bu nedenle senkron hızların gerekli olduğu durumlarda en iyi çözüm olmayabilirler. Sanayi, otomotiv ve tarım kayışlarımız var. Stoklanan standart uzunlukların yanı sıra özel kayış uzunlukları da mevcuttur. Tüm standart V kayışı kesitleri stoktan temin edilebilir. Tahrik ve tahrik kasnak çapları, kasnaklar arasındaki merkez mesafesi ve kasnakların dönüş hızları gibi sisteminizin bazı parametrelerini biliyorsanız, kayış uzunluğu, kayış kesiti (genişlik ve kalınlık) gibi bilinmeyen parametreleri hesaplayabileceğiniz tablolar vardır. Bu tür tabloları kullanabilir veya sizin için doğru V-kayışını seçmemizi isteyebilirsiniz. - Pozitif Tahrik Kayışları (Zaman Kayışı): Bu kayışlar ayrıca iç çevresinde bir dizi eşit aralıklı dişe sahip düz tiptir. Pozitif tahrik veya triger kayışları, düz kayışların avantajlarını zincirlerin ve dişlilerin pozitif kavrama özellikleriyle birleştirir. Pozitif tahrik kayışları, hiçbir kayma veya hız değişikliği göstermez. Çok çeşitli hız oranları mümkündür. Düşük gerilimde çalışabildikleri için yatak yükleri düşüktür. Bununla birlikte, kasnaklardaki yanlış hizalamalara karşı daha hassastırlar. - Kasnaklar, Kasnaklar, Kayışlar için Göbekler: Düz, nervürlü (tırtıklı) ve pozitif tahrik kayışları ile farklı tipte kasnaklar kullanılır. Hepsini üretiyoruz. Yassı kayışlı kasnaklarımızın çoğu demir dökümden yapılır, ancak çeşitli jant ve göbek kombinasyonlarında çelik versiyonları da mevcuttur. Düz kayış kasnaklarımız yekpare, telli veya ayrık göbekli olabilir veya istediğiniz gibi üretebiliriz. Yivli ve pozitif tahrik kayışları, çeşitli stok boyutları ve genişliklerinde mevcuttur. Kayışı tahrik üzerinde tutmak için triger kayışı tahriklerindeki en az bir kasnak flanşlı olmalıdır. Uzun merkez tahrik sistemlerinde her iki kasnağın da flanşlı olması tavsiye edilir. Kasnaklar, kasnakların yivli çarklarıdır ve genellikle demir döküm, çelik şekillendirme veya plastik kalıplama ile üretilir. Çelik şekillendirme, otomotiv ve tarım kasnakları üretmek için uygun bir işlemdir. Düzenli ve derin oluklu kasnaklar üretiyoruz. Derin oluklu kasnaklar, V-kayışı kasnağa, çeyrek dönüşlü tahriklerde olduğu gibi bir açıyla girdiğinde çok uygundur. Derin oluklar ayrıca dikey milli tahrikler ve kayışların titreşiminin sorun olabileceği uygulamalar için çok uygundur. Avara kasnaklarımız, mekanik gücü aktarmaya hizmet etmeyen oluklu kasnak veya düz kasnaklardır. Avara kasnakları çoğunlukla kayışları sıkmak için kullanılır. - Tekli ve Çoklu Kayışlı Tahrikler: Tek kayışlı tahriklerde tek bir oluk bulunurken, çoklu kayışlı tahriklerde birden fazla oluk bulunur. Aşağıdaki ilgili renkli metne tıklayarak kataloglarımızı indirebilirsiniz: - Güç Aktarma Kayışları (V Kayışları, Zaman Kayışlarını, Ham Kenar Kayışlarını, Sargılı Kayışları ve Özel Kayışları içerir) - Konveyör Bantları - V-Kasnaklar - Zamanlama Kasnakları ZİNCİRLER & ZİNCİR TAHRİKLERİ: Güç aktarım zincirlerimiz, nispeten sınırsız mil merkez mesafeleri, kolay montaj, kompaktlık, gerilim altında kayma ve sürünme olmadan elastikiyet, yüksek sıcaklıklarda çalışabilme gibi avantajlara sahiptir. İşte zincirlerimizin başlıca türleri: - Sökülebilir Zincirler: Sökülebilir zincirlerimiz çeşitli ebatlarda, hatvelerde ve nihai mukavemette ve genellikle dövülebilir demir veya çelikten yapılır. Dövülebilir zincirler, 0,902 (23 mm) ila 4,063 inç (103 mm) arasında değişen boyutlarda ve 700 ila 17.000 lb/inç kare arası nihai mukavemette yapılır. Öte yandan, ayrılabilir çelik zincirlerimiz, 760 ila 5000 lb/inç kare arası nihai mukavemete sahip, 0,904 inç (23 mm) ila yaklaşık 3,00 inç (76 mm) arası boyutlarda üretilir._cc781905-5cde-3194-bb3b- 136bad5cf58d_ - İğneli Zincirler: Bu zincirler, daha ağır yükler ve yaklaşık 450 fit/dak'ya (2,2 m/sn) kadar biraz daha yüksek hızlar için kullanılır. İğne zincirleri, tam yuvarlak namlu ucuna sahip ayrı döküm bağlantılardan ve ofset kenar çubuklarından yapılmıştır. Bu zincir baklaları çelik pimlerle birbirine bağlanmıştır. Bu zincirler yaklaşık 1,00 inç (25 mm) ila 6,00 inç (150 mm) arasında bir aralıkta ve 3600 ila 30.000 libre/inç kare arasında nihai mukavemet aralığındadır. - Ofset-Yan Zincirleri: Bunlar, inşaat makinelerinin tahrik zincirlerinde popülerdir. Bu zincirler 1000 ft/dk'ya kadar hızlarda çalışır ve yükleri yaklaşık 250 hp'ye iletir. Genel olarak her bir bağlantının iki ofset kenar çubuğu, bir burç, bir makara, bir pim, bir kopilya bulunur. - Makaralı Zincirler: 0,25 (6 mm) ila 3,00 (75 mm) inç arası hatvelerde mevcuttur. Tek genişlikli makaralı zincirlerin nihai gücü 925 ila 130.000 lb/inç kare arasında değişir. Makaralı zincirlerin çok genişlikli versiyonları mevcuttur ve daha yüksek hızlarda daha fazla güç iletir. Çok genişlikli makaralı zincirler ayrıca azaltılmış gürültü ile daha yumuşak hareket sunar. Makaralı zincirler, makaralı bağlantılardan ve pim bağlantılarından monte edilir. Sökülebilir tip makaralı zincirlerde kopilyalar kullanılmaktadır. Makaralı zincir tahriklerinin tasarımı, konu uzmanlığı gerektirir. Kayışlı tahrikler lineer hızlara dayalıyken, zincir tahrikler, çoğu kurulumda tahrik edilen eleman olan daha küçük zincir dişlisinin dönüş hızına dayanır. Beygir gücü değerleri ve dönme hızının yanı sıra zincir tahriklerinin tasarımı birçok başka faktöre dayanmaktadır. - Çift Adımlı Zincirler: Hatvenin iki kat daha uzun olması dışında temel olarak makaralı zincirlerle aynıdır. - Ters Dişli (Sessiz) Zincirler: Çoğunlukla ana hareket ettirici, PTO tahrikleri için kullanılan yüksek hızlı zincirler. Tersine çevrilmiş dişli zincir tahrikleri, 1200 hp'ye kadar güç iletebilir ve bir dizi dişli bağlantıdan oluşur ve alternatif olarak ya pimlerle ya da eklem bileşenlerinin bir kombinasyonuyla birleştirilir. Merkez kılavuz zincirinde, dişlideki oluklara geçmek için kılavuz bağlantılar bulunur ve yan kılavuz zincirinde, dişlinin yanlarına geçecek kılavuzlar bulunur. - Boncuklu veya Sürgülü Zincirler: Bu zincirler, yavaş hızlarda ve ayrıca manuel işlemlerde kullanılır. Aşağıdaki ilgili renkli metne tıklayarak kataloglarımızı indirebilirsiniz: - Sürüş Zincirleri - Konveyör Zincirleri - Büyük Hatveli Konveyör Zincirleri - Paslanmaz Çelik Makaralı Zincirler - Kaldırma Zincirleri - Motosiklet Zincirleri - Tarım Makina Zincirleri - Dişliler: Standart dişlilerimiz ANSI standartlarına uygundur. Plaka dişlileri düz, göbeksiz dişlilerdir. Küçük ve orta boy göbek dişlilerimiz, çubuk stoktan veya dövme malzemelerden torna edilir veya çubuk stok göbeğinin sıcak haddelenmiş bir plakaya kaynaklanmasıyla yapılır. AGS-TECH Inc., gri demir dökümlerden, dökme çelikten ve kaynaklı göbek konstrüksiyonlarından, sinterlenmiş toz metalden, kalıplanmış veya işlenmiş plastiklerden işlenmiş zincir dişlileri tedarik edebilir. Yüksek hızlarda düzgün çalışma için, dişli boyutunun doğru seçilmesi çok önemlidir. Dişli seçimi yaparken yer sınırlaması elbette göz ardı edemeyeceğimiz bir faktördür. Sürücünün tahrik edilen dişlilere oranının 6:1'den fazla olmaması ve sürücü üzerindeki zincir sargısının 120 derece olması önerilir. Küçük ve büyük dişliler arasındaki merkez mesafeleri, zincir uzunlukları ve zincir gerilimi de rastgele değil, önerilen bazı mühendislik hesaplamaları ve yönergelerine göre seçilmelidir. Aşağıdaki renkli metne tıklayarak kataloglarımızı indirin: - Dişliler ve Plaka Tekerlekler - Şanzıman Burçları - Zincir Bağlantısı - Zincir Kilitleri KABLO TAHRİKLER: Bunların bazı durumlarda kayışlara ve zincir tahriklere göre avantajları vardır. Kablo tahrikleri, kayışlarla aynı işlevi görebilir ve ayrıca bazı uygulamalarda uygulanması daha basit ve daha ekonomik olabilir. Örneğin, yeni bir Synchromesh Kablo Sürücü serisi, özellikle dar alanlarda geleneksel halatların, basit kabloların ve dişli sürücülerin yerini alacak pozitif çekiş için tasarlanmıştır. Yeni kablo sürücü, fotokopi makineleri, çiziciler, daktilolar, yazıcılar, vb. gibi elektronik ekipmanlarda yüksek hassasiyette konumlandırma sağlamak için tasarlanmıştır. son derece minyatür tasarımlar. Senkromeç kablolar, halatlara göre daha düşük gerilim ile kullanılabilmekte ve bu sayede güç tüketimi azalmaktadır. Kayışlar, zincirler ve kablo tahrikleri hakkında soru ve görüşleriniz için AGS-TECH ile iletişime geçin. CLICK Product Finder-Locator Service ÖNCEKİ SAYFA
- Makine Elemanları İmalatı, Dişliler, Kayışlar, Kaplin, Rulman, Kamlar, Şaft İmalatı, Mekanik Salmastra, Basit Makineler
Makine Elemanları İmalatı, Dişliler, Kayışlar, Zincirler, Kaplin, Rulman, Kamlar, Takipçiler, Şaft İmalatı, Mekanik Salmastra, Debriyaj ve Fren, Bağlantı Elemanları, Basit Makineler Makine Elemanları İmalatı Devamını oku Kayışlar ve Zincirler ve Kablo Tahrik Grubu Devamını oku Dişliler ve Dişli Tahrik Grubu Devamını oku Kaplin, Rulman İmalatı Devamını oku Mil, Makine Kaması, Pim İmalatı Devamını oku Kamlar, Takipçiler, Mafsallar, Kilit Çarkı, Mandallı Çark ve Cırcır Tekerlek İmalatı Devamını oku Şaft İmalatı Devamını oku Mekanik Salmastra İmalatı Devamını oku Debriyaj ve Fren Grubu Devamını oku Bağlantı Elemanları İmalatı Devamını oku Basit Makineler Montajı MAKİNE ELEMANLARI bir makinenin temel bileşenleridir. Bu unsurlar üç temel türden oluşur: 1.) Çerçeve elemanları, yataklar, akslar, kamalar, bağlantı elemanları, contalar ve yağlayıcılar dahil olmak üzere yapısal bileşenler. 2.) Dişli dizileri, kayış veya zincir tahrikleri, bağlantılar, kam ve takipçi sistemleri, frenler ve debriyajlar gibi hareketi çeşitli şekillerde kontrol eden mekanizmalar. 3.) Düğmeler, anahtarlar, göstergeler, sensörler, aktüatörler ve bilgisayar denetleyicileri gibi kontrol bileşenleri. Size sunduğumuz makine elemanlarının çoğu ortak boyutlara göre standartlaştırılmıştır, ancak özel uygulamalarınız için özel yapım makine elemanları da mevcuttur. Makine elemanlarının özelleştirilmesi, indirilebilir kataloglarımızda bulunan mevcut tasarımlarda veya yepyeni tasarımlarda yer alabilir. Bir tasarım her iki tarafça onaylandıktan sonra, makine elemanlarının prototiplenmesi ve imalatı ileriye taşınabilir. Yeni makine elemanlarının tasarlanması ve üretilmesi gerekiyorsa, müşterilerimiz ya bize kendi planlarını e-posta ile gönderir ve biz de onları onay için inceleriz ya da bizden uygulamaları için makine elemanları tasarlamamızı isterler. İkinci durumda, müşterilerimizden gelen tüm girdileri kullanırız ve makine elemanlarını tasarlarız ve nihai planları müşterilerimize onay için göndeririz. Onaylandıktan sonra ilk ürünleri üretiyoruz ve ardından nihai tasarıma göre makine elemanlarını üretiyoruz. Bu çalışmanın herhangi bir aşamasında, belirli bir makine elemanı tasarımının sahada yetersiz performans göstermesi durumunda (ki bu nadirdir), tüm projeyi gözden geçirir ve gerektiğinde müşterilerimizle ortaklaşa değişiklikler yaparız. Gerektiğinde veya gerektiğinde makine elemanlarının veya başka herhangi bir ürünün tasarımı için müşterilerimizle gizlilik anlaşmaları (NDA) imzalamak standart uygulamamızdır. Belirli bir müşteri için makine elemanları özel olarak tasarlanıp üretildikten sonra ona bir ürün kodu atar ve sadece ürünün sahibi olan müşterimize üretip satarız. Geliştirilen takımlar, kalıplar ve prosedürleri kullanarak makine elemanlarını gerektiği kadar ve müşterimiz onları yeniden sipariş ettiğinde çoğaltıyoruz. Başka bir deyişle, sizin için özel bir makine elemanı tasarlanıp üretildiğinde, fikri mülkiyeti ile tüm alet ve kalıplar tarafımızca süresiz olarak saklı tutulmakta ve sizin ve dilediğiniz gibi çoğaltılan ürünler için tarafımızca stoklanmaktadır. Ayrıca, bir uygulamaya hizmet eden ve müşterilerimizin beklentilerini karşılayan veya aşan bir bileşen veya montajda makine elemanlarını yaratıcı bir şekilde birleştirerek müşterilerimize mühendislik hizmetleri sunuyoruz. Makine elemanlarımızı üreten tesisler, ISO9001, QS9000 veya TS16949 tarafından onaylanmıştır. Ayrıca ürünlerimizin çoğu CE veya UL işaretine sahiptir ve ISO, SAE, ASME, DIN gibi uluslararası ilgili standartları karşılamaktadır. Aşağıdakileri içeren makine elemanlarımız hakkında detaylı bilgi almak için lütfen alt menülere tıklayın: - Kayışlar, Zincirler ve Kablo Tahrikleri - Dişliler ve Dişli Tahrikler - Kaplinler ve Rulmanlar - Tuşlar ve Spline'lar ve pimler - Kameralar ve Bağlantılar - Şaftlar - Mekanik mühürler - Endüstriyel Debriyaj ve Fren - Bağlantı Elemanları - Basit makineler Müşterilerimiz, tasarımcılarımız ve makine elemanları da dahil olmak üzere yeni ürün geliştiricilerimiz için bir referans broşürü hazırladık. Makine bileşenleri tasarımında yaygın olarak kullanılan bazı terimlere aşina olabilirsiniz: Tasarımcılar ve Mühendisler tarafından kullanılan Ortak Makine Mühendisliği Terimleri için broşürü indirin Makine elemanlarımız endüstriyel makineler, otomasyon sistemleri, test ve metroloji ekipmanları, nakliye ekipmanları, inşaat makineleri gibi çeşitli alanlarda ve aklınıza gelebilecek hemen hemen her yerde uygulama bulur. AGS-TECH, uygulamaya bağlı olarak çeşitli malzemelerden makine elemanları geliştirmekte ve üretmektedir. Makine elemanları için kullanılan malzemeler, oyuncaklar için kullanılan kalıplanmış plastiklerden, endüstriyel makineler için sertleştirilmiş ve özel olarak kaplanmış çeliğe kadar değişebilir. Tasarımcılarımız, dişli dişlerindeki açılar, ilgili gerilimler, aşınma oranları vb. gibi ayrıntıları dikkate alarak makine elemanlarını geliştirmek için son teknoloji ürünü profesyonel yazılım ve tasarım araçlarını kullanır. Uygulamanız için hazır makine elemanlarını bulup bulamayacağınızı görmek için lütfen alt menülerimizde gezinin ve ürün broşürlerimizi ve kataloglarımızı indirin. Uygulamanız için uygun bir eşleşme bulamazsanız, lütfen bize bildirin, ihtiyaçlarınızı karşılayacak makine elemanlarını geliştirmek ve üretmek için sizinle birlikte çalışacağız. Üretim kapasitemiz yerine mühendislik ve araştırma-geliştirme yeteneklerimizle ilgileniyorsanız, sizi web sitemizi ziyaret etmeye davet ediyoruz http://www.ags-engineering.com Tasarım, ürün geliştirme, süreç geliştirme, mühendislik danışmanlık hizmetlerimiz ve daha fazlası hakkında daha ayrıntılı bilgi bulabileceğiniz yer CLICK Product Finder-Locator Service ÖNCEKİ SAYFA
- Hızlı Prototipleme, Masaüstü İmalat, Eklemeli Üretim, Katmanlı İmalat, FDM, Stereolitografi, Seçici Lazer Sinterleme, Üç Boyutlu Baskı
Eklemeli Üretim, Katmanlı İmalat, Hızlı İmalat, Hızlı Prototipleme, Stereolitografi, Polyjet, Seçici Lazer Sinterleme, Elektron Işınlı Eritme, Üç Boyutlu Baskı, Hızlı Kalıplama, Doğrudan Üretim, FDM, SLS, 3D Baskı Katmanlı ve Hızlı İmalat Son yıllarda HIZLI İMALAT veya HIZLI PROTOTİPLEME için talepte artış gördük. Bu süreç aynı zamanda MASAÜSTÜ ÜRETİM veya SERBEST FORM İMALAT olarak da adlandırılabilir. Temel olarak, bir parçanın katı bir fiziksel modeli, doğrudan üç boyutlu bir CAD çiziminden yapılır. Parçaları katmanlar halinde oluşturduğumuz bu çeşitli teknikler için KATKILI İMALAT terimini kullanıyoruz. Entegre bilgisayar destekli donanım ve yazılım kullanarak eklemeli üretim gerçekleştiriyoruz. Hızlı prototipleme ve üretim tekniklerimiz STEROLİTOGRAFİ, POLİJET, KAYNAKLI-DEPOZİSYON MODELLEME, SEÇİCİ LAZER SİNTERLEME, ELEKTRON IŞINI ERİTME, ÜÇ BOYUTLU BASKI, DOĞRUDAN ÜRETİM, HIZLI TAKIMLARDIR. için buraya tıklamanızı öneririz.AGS-TECH Inc. Katmanlı İmalat ve Hızlı İmalat Proseslerinin Şematik Gösterimlerimizi İNDİRİN Bu, aşağıda size sağladığımız bilgileri daha iyi anlamanıza yardımcı olacaktır. Hızlı prototipleme bize şunları sağlar: 1.) Konsept ürün tasarımı, bir 3D / CAD sistemi kullanılarak bir monitörde farklı açılardan görüntülenir. 2.) Metalik olmayan ve metalik olmayan malzemelerden prototipler üretilir ve fonksiyonel, teknik ve estetik açıdan incelenir. 3.) Çok kısa sürede düşük maliyetli prototipleme gerçekleştirilir. Eklemeli imalat, tek tek dilimlerin üst üste istiflenmesi ve yapıştırılmasıyla bir somun ekmek yapımına benzetilebilir. Yani ürün dilim dilim veya katman katman birbiri üzerine bırakılarak üretilir. Çoğu parça saatler içinde üretilebilir. Parçalara çok hızlı ihtiyaç duyuluyorsa veya ihtiyaç duyulan miktarlar düşükse ve kalıp ve alet yapımı çok pahalı ve zaman alıyorsa teknik iyidir. Ancak pahalı hammaddeler nedeniyle bir parçanın maliyeti pahalıdır. • STEREOLİTOGRAFİ : STL olarak da kısaltılan bu teknik, bir sıvı fotopolimerin üzerine bir lazer ışını odaklanarak sertleştirilmesi ve belirli bir şekle getirilmesine dayanır. Lazer fotopolimeri polimerize eder ve sertleştirir. UV lazer ışını fotopolimer karışımının yüzeyi boyunca programlanmış şekle göre taranarak parça, aşağıdan yukarıya, birbiri üzerine kademeli olarak ayrı ayrı dilimler halinde üretilir. Sistemde programlanan geometrileri elde etmek için lazer noktasının taranması birçok kez tekrarlanır. Parça tamamen imal edildikten sonra platformdan çıkarılır, lekelenir ve ultrasonik ve alkol banyosu ile temizlenir. Ardından, polimerin tamamen kürlendiğinden ve sertleştiğinden emin olmak için birkaç saat UV ışınlarına maruz bırakılır. İşlemi özetlemek gerekirse, fotopolimer karışımına daldırılan bir platform ve bir UV lazer ışını kontrol edilerek istenilen parçanın şekline göre servo kontrol sistemi ile hareket ettirilir ve polimer tabakası katman katman fotokürlenerek parça elde edilir. Elbette üretilen parçanın maksimum boyutları stereolitografi ekipmanı tarafından belirlenir. • POLYJET : Mürekkep püskürtmeli baskıya benzer şekilde, polijette, yapı tepsisine fotopolimer bırakan sekiz baskı kafamız var. Jetlerin yanına yerleştirilen ultraviyole ışık, her katmanı anında sertleştirir ve sertleştirir. Polijette iki malzeme kullanılmaktadır. İlk malzeme, gerçek modeli üretmek içindir. İkinci malzeme, destek için jel benzeri bir reçine kullanılır. Bu malzemelerin her ikisi de katman katman biriktirilir ve aynı anda kürlenir. Modelin tamamlanmasından sonra destek malzemesi sulu bir çözelti ile çıkarılır. Kullanılan reçineler stereolitografiye (STL) benzer. Polyjet, stereolitografiye göre aşağıdaki avantajlara sahiptir: 1.) Parçaların temizlenmesine gerek yoktur. 2.) İşlem sonrası kürlemeye gerek yok 3.) Daha küçük katman kalınlıkları mümkündür ve böylece daha iyi çözünürlük elde ederiz ve daha ince parçalar üretebiliriz. • FUSED DEPOSITION MODELING : FDM olarak da kısaltılır, bu yöntemde robot kontrollü bir ekstrüder kafası bir masa üzerinde iki ana yönde hareket eder. Kablo gerektiği gibi indirilir ve yükseltilir. Başlıktaki ısıtılmış bir kalıbın ağzından, termoplastik bir filament ekstrüde edilir ve bir köpük temel üzerine bir başlangıç tabakası biriktirilir. Bu, önceden belirlenmiş bir yolu izleyen ekstrüder kafası tarafından gerçekleştirilir. İlk katmandan sonra tabla indirilir ve sonraki katmanlar üst üste bırakılır. Bazen karmaşık bir parça üretirken, biriktirmenin belirli yönlerde devam edebilmesi için destek yapılarına ihtiyaç duyulur. Bu durumlarda, bir destek malzemesi, model malzemeden daha zayıf olacak şekilde bir katman üzerinde daha az yoğun bir filaman aralığı ile ekstrüde edilir. Bu destek yapıları daha sonra parçanın tamamlanmasından sonra çözülebilir veya kırılabilir. Ekstrüder kalıbı boyutları, ekstrüde edilmiş katmanların kalınlığını belirler. FDM işlemi, eğik dış düzlemlerde kademeli yüzeylere sahip parçalar üretir. Bu pürüzlülük kabul edilemez ise, bunları düzeltmek için kimyasal buharlı polisaj veya ısıtılmış bir alet kullanılabilir. Bu adımları ortadan kaldırmak ve makul geometrik toleransları elde etmek için bir kaplama malzemesi olarak bir cila mumu bile mevcuttur. • SEÇİCİ LAZER SİNTERLEME : SLS olarak da adlandırılan işlem, polimer, seramik veya metalik tozların seçici olarak bir nesneye sinterlenmesine dayanır. İşleme odasının alt kısmında iki silindir bulunur: Kısmi yapılı bir silindir ve bir toz besleme silindiri. İlki, sinterlenmiş parçanın oluşturulduğu yere aşamalı olarak indirilir ve ikincisi, bir silindir mekanizması aracılığıyla parça yapılı silindire toz tedarik etmek için aşamalı olarak yükseltilir. Önce parça yapılı silindirde ince bir toz tabakası biriktirilir, ardından bir lazer ışını bu tabakaya odaklanır, belirli bir enine kesiti izler ve eritir/sinterler ve ardından bir katı halinde yeniden katılaşır. Toz, lazer ışını tarafından vurulmayan alanlar gevşek kalır ancak yine de katı kısmı destekler. Daha sonra başka bir toz tabakası biriktirilir ve parçayı elde etmek için işlem birçok kez tekrarlanır. Sonunda, gevşek toz parçacıkları çalkalanır. Tüm bunlar, üretilen parçanın 3D CAD programı tarafından oluşturulan talimatlar kullanılarak bir süreç kontrol bilgisayarı tarafından gerçekleştirilir. Uygun polimer bağlayıcılarla polimerler (ABS, PVC, polyester gibi), mum, metaller ve seramikler gibi çeşitli malzemeler biriktirilebilir. • ELECTRON-BEAM MELTING : Seçici lazer sinterlemeye benzer, ancak vakumda prototip yapmak için titanyum veya kobalt krom tozlarını eritmek için elektron ışını kullanılır. Paslanmaz çelikler, alüminyum ve bakır alaşımları üzerinde bu işlemi gerçekleştirmek için bazı geliştirmeler yapılmıştır. Üretilen parçaların yorulma dayanımının arttırılması gerekiyorsa, ikincil işlem olarak parça imalatının ardından sıcak izostatik pres kullanıyoruz. • ÜÇ BOYUTLU BASKI : Yine 3DP ile gösterilir, bu teknikte bir yazıcı kafası, metalik olmayan veya metalik bir toz tabakası üzerine inorganik bir bağlayıcı bırakır. Toz yatağını taşıyan bir piston kademeli olarak alçaltılır ve her adımda bağlayıcı katman katman biriktirilir ve bağlayıcı tarafından kaynaştırılır. Kullanılan toz malzemeler polimer karışımları ve lifleri, döküm kumu, metallerdir. Farklı bağlayıcı kafaları ve farklı renk bağlayıcıları aynı anda kullanarak çeşitli renkler elde edebiliriz. İşlem mürekkep püskürtmeli baskıya benzer, ancak renkli bir tabaka elde etmek yerine renkli üç boyutlu bir nesne elde ederiz. Üretilen parçalar gözenekli olabilir ve bu nedenle yoğunluğunu ve mukavemetini arttırmak için sinterleme ve metal infiltrasyonu gerektirebilir. Sinterleme bağlayıcıyı yakacak ve metal tozlarını birbirine kaynatacaktır. Parçaları yapmak için paslanmaz çelik, alüminyum, titanyum gibi metaller kullanılabilir ve sızma malzemeleri olarak yaygın olarak bakır ve bronz kullanırız. Bu tekniğin güzelliği, karmaşık ve hareketli montajların bile çok hızlı bir şekilde üretilebilmesidir. Örneğin bir dişli takımı, bir alet olarak bir anahtar yapılabilir ve kullanıma hazır hareketli ve döner parçalara sahip olacaktır. Montajın farklı bileşenleri farklı renklerde ve hepsi bir arada üretilebilir. Broşürümüzü indirin:Metal 3D Baskı Temelleri • DOĞRUDAN ÜRETİM ve HIZLI TAKIM: Tasarım değerlendirmesi, sorun gidermenin yanı sıra, ürünlerin doğrudan üretimi veya ürünlere doğrudan uygulanması için hızlı prototipleme kullanıyoruz. Başka bir deyişle, hızlı prototipleme, onları daha iyi ve daha rekabetçi hale getirmek için geleneksel süreçlere dahil edilebilir. Örneğin, hızlı prototipleme, desenler ve kalıplar üretebilir. Hızlı prototipleme operasyonları ile oluşturulan bir eriyen ve yanan polimerin kalıpları, hassas döküm için birleştirilebilir ve yatırım yapılabilir. Bahsedilecek başka bir örnek, seramik döküm kabuk üretmek için 3DP kullanmak ve bunu kabuk döküm işlemleri için kullanmaktır. Enjeksiyon kalıpları ve kalıp ekleri bile hızlı prototipleme ile üretilebilir ve kalıp yapım süresinden haftalar veya aylarca tasarruf edilebilir. Sadece istenilen parçanın CAD dosyasını analiz ederek, yazılım kullanarak takım geometrisini üretebiliriz. İşte popüler hızlı takımlama yöntemlerimizden bazıları: RTV (Oda Sıcaklığında Vulkanizasyon) KALIPLAMA / ÜRETAN DÖKÜM : İstenilen parçanın kalıbını yapmak için hızlı prototipleme kullanılarak kullanılabilir. Daha sonra bu kalıp bir ayırma maddesi ile kaplanır ve kalıp yarımlarını oluşturmak için kalıbın üzerine sıvı RTV kauçuğu dökülür. Daha sonra, bu kalıp yarımları sıvı üretanların enjeksiyon kalıbı için kullanılır. Kalıp ömrü kısadır, yalnızca 0 veya 30 döngü gibi ancak küçük parti üretimi için yeterlidir. ACES (Acetal Clear Epoxy Solid) ENJEKSİYON KALIPLAMA : Stereolitografi gibi hızlı prototipleme tekniklerini kullanarak enjeksiyon kalıpları üretmekteyiz. Bu kalıplar, epoksi, alüminyum dolgulu epoksi veya metaller gibi malzemelerle doldurmaya izin veren açık uçlu kabuklardır. Yine kalıp ömrü onlarca veya maksimum yüzlerce parça ile sınırlıdır. PÜSKÜRTME METAL TAKIM PROSESİ : Hızlı prototipleme yaparak kalıp yapıyoruz. Desen yüzeyine çinko-alüminyum alaşımı püskürtüp kaplıyoruz. Metal kaplamalı desen daha sonra bir şişenin içine yerleştirilir ve bir epoksi veya alüminyum dolgulu epoksi ile kaplanır. Son olarak, çıkarılır ve bu tür iki yarım kalıp üreterek enjeksiyon kalıplama için eksiksiz bir kalıp elde ederiz. Bu kalıplar daha uzun ömürlüdür, bazı durumlarda malzeme ve sıcaklıklara bağlı olarak binlerce parça üretebilirler. KEELTOOL PROSESİ : Bu teknikle 100.000 ila 10 Milyon çevrim ömrüne sahip kalıplar üretilebilir. Hızlı prototipleme kullanarak bir RTV kalıbı üretiyoruz. Kalıp daha sonra A6 takım çeliği tozu, tungsten karbür, polimer bağlayıcıdan oluşan bir karışımla doldurulur ve kürlenmeye bırakılır. Bu kalıp daha sonra polimerin yanması ve metal tozlarının kaynaşması için ısıtılır. Bir sonraki adım, son kalıbı üretmek için bakır sızmasıdır. Gerekirse daha iyi boyutsal doğruluklar için kalıp üzerinde talaşlı imalat ve polisaj gibi ikincil işlemler yapılabilir. CLICK Product Finder-Locator Service ÖNCEKİ SAYFA
- Kompozitler, Kompozit Malzeme İmalatı, Elyaf Takviyeli Kompozitler, Metal Matris Kompozitleri, Nanokompozitler, Sandviç Paneller
Kompozitler, Kompozit Malzeme İmalatı, Elyaf Takviyeli Kompozitler, Metal Matris Kompozitleri, Nanokompozitler, Sandviç Paneller, Laminer Kompozitler, Pultrüzyon, Prepreg, Seramik Matrisli Kompozitler, Parçacık Takviyeli Kompozitler, Cermet, Sermet Kompozitler, Kompozit Parça İmalatı Basitçe tanımlanacak olursa, KOMPOZİTLER veya KOMPOZİT MALZEMELER, farklı fiziksel veya kimyasal özelliklere sahip iki veya daha fazla malzemeden oluşan ancak birleştirildiklerinde, kurucu malzemelerden farklı bir malzeme haline gelen malzemelerdir. Bileşen malzemelerin yapı içinde ayrı ve farklı kaldıklarına dikkat çekmeliyiz. Kompozit malzeme üretiminde amaç, bileşenlerinden daha üstün ve her bileşenin istenen özelliklerini birleştiren bir ürün elde etmektir. Örnek olarak; mukavemet, düşük ağırlık veya daha düşük fiyat, bir kompozit tasarlamanın ve üretmenin arkasındaki motivasyon olabilir. Sunduğumuz kompozit türleri, partikül takviyeli kompozitler, seramik matris / polimer matris / metal matris / karbon-karbon / hibrit kompozitler dahil fiber takviyeli kompozitler, yapısal ve lamine ve sandviç yapılı kompozitler ve nanokompozitlerdir. Kompozit malzeme imalatında uyguladığımız üretim teknikleri şunlardır: Pultrüzyon, prepreg üretim süreçleri, gelişmiş elyaf yerleştirme, filament sarma, özel elyaf yerleştirme, fiberglas sprey yerleştirme işlemi, tafting, lanksit işlemi, z-pinning. Birçok kompozit malzeme, sürekli olan ve diğer fazı çevreleyen matris olmak üzere iki fazdan oluşur; ve matris tarafından çevrelenen dağınık faz. için buraya tıklamanızı öneririz.AGS-TECH Inc. Bu, aşağıda size sağladığımız bilgileri daha iyi anlamanıza yardımcı olacaktır. • PARÇACIK TAKVİYELİ KOMPOZİTLER : Bu kategori iki türden oluşur: Büyük parçacıklı kompozitler ve dispersiyonla güçlendirilmiş kompozitler. Önceki tipte, parçacık-matris etkileşimleri atomik veya moleküler düzeyde ele alınamaz. Bunun yerine sürekli ortam mekaniği geçerlidir. Öte yandan, dispersiyonla güçlendirilmiş kompozitlerde parçacıklar genellikle onlarca nanometre aralığında çok daha küçüktür. Büyük parçacıklı kompozitin bir örneği, dolgu maddelerinin eklendiği polimerlerdir. Dolgu maddeleri malzemenin özelliklerini iyileştirir ve polimer hacminin bir kısmını daha ekonomik bir malzeme ile değiştirebilir. İki fazın hacim fraksiyonları kompozitin davranışını etkiler. Büyük parçacıklı kompozitler metaller, polimerler ve seramiklerle birlikte kullanılır. CERMETS, seramik / metal kompozit örnekleridir. En yaygın sermetimiz semente karbürdür. Kobalt veya nikel gibi bir metal matrisindeki tungsten karbür parçacıkları gibi refrakter karbür seramikten oluşur. Bu karbür kompozitler, sertleştirilmiş çelik için kesme aletleri olarak yaygın olarak kullanılmaktadır. Sert karbür partiküller kesme işleminden sorumludur ve toklukları sünek metal matris tarafından arttırılır. Böylece her iki malzemenin avantajlarını tek bir kompozitte elde ederiz. Kullandığımız büyük partiküllü bir kompozitin diğer bir yaygın örneği, yüksek gerilme mukavemeti, tokluk, yırtılma ve aşınma direncine sahip bir kompozit elde etmek için vulkanize kauçuk ile karıştırılmış karbon siyahı partiküllerdir. Dağılımla güçlendirilmiş bir kompozitin bir örneği, çok sert ve inert bir malzemenin ince parçacıklarının düzgün dağılımı ile güçlendirilmiş ve sertleştirilmiş metaller ve metal alaşımlarıdır. Alüminyum metal matrisine çok küçük alüminyum oksit pulları eklendiğinde, geliştirilmiş yüksek sıcaklık dayanımına sahip sinterlenmiş alüminyum tozu elde ederiz. • ELYAF TAKVİYELİ KOMPOZİTLER : Bu kompozit kategorisi aslında en önemlisidir. Hedef, birim ağırlık başına yüksek mukavemet ve sertliktir. Bu kompozitlerdeki lif bileşimi, uzunluğu, yönelimi ve konsantrasyonu, bu malzemelerin özelliklerini ve kullanışlılığını belirlemede kritik öneme sahiptir. Kullandığımız üç grup elyaf vardır: bıyık, elyaf ve teller. Bıyıklar çok ince ve uzun tek kristallerdir. En sağlam malzemeler arasındadırlar. Bazı örnek tüy malzemeleri grafit, silikon nitrür, alüminyum oksittir. FIBERS ise çoğunlukla polimer veya seramiktir ve polikristal veya amorf haldedir. Üçüncü grup, nispeten büyük çaplara sahip olan ve sıklıkla çelik veya tungstenden oluşan ince TELLERDİR. Tel takviyeli kompozitin bir örneği, kauçuk içinde çelik tel içeren araba lastikleridir. Matris malzemesine bağlı olarak aşağıdaki kompozitlere sahibiz: POLİMER MATRİS KOMPOZİTLERİ : Bunlar, takviye maddesi olarak bir polimer reçinesi ve liflerden yapılmıştır. Bunların Cam Elyaf Takviyeli Polimer (GFRP) Kompozitler olarak adlandırılan bir alt grubu, bir polimer matrisi içinde sürekli veya süreksiz cam elyafları içerir. Cam yüksek mukavemet sunar, ekonomiktir, liflere dönüştürülmesi kolaydır ve kimyasal olarak inerttir. Dezavantajları, sınırlı sertlik ve sertlikleri, servis sıcaklıklarının sadece 200 – 300 Santigrat'a kadar çıkmasıdır. Fiberglas, otomotiv gövdeleri ve nakliye ekipmanları, deniz aracı gövdeleri, saklama kapları için uygundur. Sınırlı sertlikleri nedeniyle havacılık ve köprü yapımı için uygun değildirler. Diğer alt grup ise Karbon Elyaf Takviyeli Polimer (CFRP) Kompozit olarak adlandırılır. Burada karbon, polimer matrisindeki fiber malzememizdir. Karbon, yüksek özgül modülü ve gücü ve bunları yüksek sıcaklıklarda tutma kabiliyeti ile bilinir. Karbon fiberler bize standart, orta, yüksek ve ultra yüksek çekme modülleri sunabilir. Ayrıca, karbon fiberler çeşitli fiziksel ve mekanik özellikler sunar ve bu nedenle çeşitli özel uyarlanmış mühendislik uygulamaları için uygundur. CFRP kompozitleri, spor ve eğlence ekipmanları, basınçlı kaplar ve havacılık yapısal bileşenleri üretmek için düşünülebilir. Yine bir başka alt grup olan Aramid Elyaf Takviyeli Polimer Kompozitler de yüksek mukavemetli ve modüllü malzemelerdir. Güç/ağırlık oranları olağanüstü derecede yüksektir. Aramid lifleri ayrıca KEVLAR ve NOMEX ticari isimleriyle de bilinir. Gerilim altında diğer polimerik fiber malzemelerden daha iyi performans gösterirler, ancak sıkıştırmada zayıftırlar. Aramid lifleri tok, darbeye dayanıklı, sürünme ve yorulmaya karşı dirençli, yüksek sıcaklıklarda kararlı, güçlü asitler ve bazlar dışında kimyasal olarak inerttir. Aramid elyaflar, spor malzemeleri, kurşun geçirmez yelekler, lastikler, ipler, fiber optik kablo kılıflarında yaygın olarak kullanılmaktadır. Diğer fiber takviye malzemeleri mevcuttur ancak daha az derecede kullanılmaktadır. Bunlar esas olarak bor, silisyum karbür, alüminyum oksittir. Öte yandan polimer matris malzemesi de kritiktir. Polimer genellikle daha düşük bir erime ve bozunma sıcaklığına sahip olduğundan, kompozitin maksimum hizmet sıcaklığını belirler. Polimer matris olarak polyesterler ve vinil esterler yaygın olarak kullanılmaktadır. Reçineler de kullanılır ve mükemmel nem direncine ve mekanik özelliklere sahiptirler. Örneğin poliimid reçinesi yaklaşık 230 Santigrat dereceye kadar kullanılabilir. METAL MATRİS KOMPOZİTLERİ : Bu malzemelerde sünek metal matris kullanıyoruz ve servis sıcaklıkları genellikle bileşenlerinden daha yüksektir. Polimer matrisli kompozitlerle karşılaştırıldığında, bunlar daha yüksek çalışma sıcaklıklarına sahip olabilir, yanıcı olmayabilir ve organik sıvılara karşı daha iyi bozunma direncine sahip olabilir. Ancak daha pahalıdırlar. Bıyıklar, parçacıklar, sürekli ve süreksiz lifler gibi takviye malzemeleri; ve bakır, alüminyum, magnezyum, titanyum, süper alaşımlar gibi matris malzemeleri yaygın olarak kullanılmaktadır. Örnek uygulamalar, alüminyum oksit ve karbon fiberlerle güçlendirilmiş alüminyum alaşımlı matristen yapılmış motor bileşenleridir. SERAMİK-MATRİSLİ KOMPOZİTLER : Seramik malzemeler olağanüstü iyi yüksek sıcaklık güvenilirliği ile bilinir. Ancak çok kırılgandırlar ve kırılma tokluğu için düşük değerlere sahiptirler. Bir seramiğin partiküllerini, liflerini veya kıllarını diğerinin matrisine gömerek daha yüksek kırılma tokluğuna sahip kompozitler elde edebiliyoruz. Bu gömülü malzemeler temel olarak, çatlak uçlarını saptırmak veya çatlak yüzleri arasında köprüler oluşturmak gibi bazı mekanizmalarla matris içinde çatlak yayılmasını engeller. Örnek olarak, SiC bıyıkları ile güçlendirilmiş alüminalar, sert metal alaşımlarını işlemek için kesici takım uçları olarak kullanılır. Bunlar, semente karbürlere kıyasla daha iyi performanslar ortaya çıkarabilir. KARBON-KARBON KOMPOZİTLERİ : Hem takviye hem de matris karbondur. 2000 Santigratın üzerindeki yüksek sıcaklıklarda yüksek çekme modülleri ve dayanımları, sürünme direnci, yüksek kırılma toklukları, düşük termal genleşme katsayıları, yüksek termal iletkenlikleri vardır. Bu özellikler onları termal şok direnci gerektiren uygulamalar için ideal kılar. Bununla birlikte, karbon-karbon kompozitlerinin zayıflığı, yüksek sıcaklıklarda oksidasyona karşı savunmasız olmasıdır. Tipik kullanım örnekleri, sıcak presleme kalıpları, gelişmiş türbin motoru bileşenleri imalatıdır. HİBRİT KOMPOZİTLER : İki veya daha fazla farklı tip lifin tek bir matriste karıştırılmasıdır. Böylece, özelliklerin bir kombinasyonu ile yeni bir malzeme uyarlanabilir. Bir örnek, hem karbon hem de cam fiberlerin bir polimerik reçineye dahil edilmesidir. Karbon fiberler düşük yoğunluklu sertlik ve mukavemet sağlar ancak pahalıdır. Öte yandan cam ucuzdur ancak karbon liflerinin sertliğinden yoksundur. Cam-karbon hibrit kompozit daha güçlü ve daha sağlamdır ve daha düşük maliyetle üretilebilir. ELYAF TAKVİYELİ KOMPOZİTLERİN İŞLENMESİ : Aynı yönde yönlendirilmiş, düzgün dağılmış elyaflara sahip sürekli elyaf takviyeli plastikler için aşağıdaki teknikleri kullanıyoruz. PULTRÜZYON: Sürekli uzunluklarda ve sabit kesitlerde çubuklar, kirişler ve borular üretilir. Kesintisiz elyaf fitilleri, ısıyla sertleşen bir reçine ile emprenye edilir ve arzu edilen bir şekle önceden şekillendirilmek üzere çelik bir kalıptan çekilir. Ardından, nihai şeklini elde etmek için hassas işlenmiş bir kürleme kalıbından geçerler. Kürleme kalıbı ısıtıldığı için reçine matrisini sertleştirir. Elcikler malzemeyi kalıplardan çeker. Yerleştirilen içi boş çekirdekler kullanarak borular ve içi boş geometriler elde edebiliyoruz. Pultrüzyon yöntemi otomatiktir ve bize yüksek üretim oranları sunar. Her uzunlukta ürün üretilebilir. PREPREG ÜRETİM SÜRECİ : Prepreg, kısmen kürlenmiş polimer reçine ile önceden emprenye edilmiş sürekli elyaf takviyesidir. Yapısal uygulamalar için yaygın olarak kullanılır. Malzeme bant şeklinde gelir ve bant olarak gönderilir. Üretici bunu doğrudan kalıplar ve herhangi bir reçine eklemeye gerek kalmadan tamamen kürler. Prepregler oda sıcaklığında sertleşme reaksiyonlarına girdiğinden 0 Santigrat veya daha düşük sıcaklıklarda depolanır. Kullanımdan sonra kalan bantlar düşük sıcaklıklarda saklanır. Termoplastik ve termoset reçineler kullanılır ve karbon, aramid ve camdan oluşan takviye lifleri yaygındır. Prepregleri kullanmak için, önce taşıyıcı arka kağıt çıkarılır ve daha sonra prepreg bandının aletli bir yüzey üzerine serilmesiyle fabrikasyon gerçekleştirilir (yayma işlemi). İstenen kalınlıkları elde etmek için birkaç kat döşenebilir. Sık uygulama, çapraz kat veya açılı kat laminat üretmek için fiber oryantasyonunu değiştirmektir. Son olarak kür için ısı ve basınç uygulanır. Prepregleri kesmek ve yerleştirmek için hem elle işleme hem de otomatik işlemler kullanılır. FILAMENT SARMA : Sürekli güçlendirici lifler, içi boş bir ve genellikle silindirik bir şekli takip etmek için önceden belirlenmiş bir modelde doğru bir şekilde konumlandırılır. Elyaflar önce reçine banyosundan geçer ve daha sonra otomatik bir sistemle mandrel üzerine sarılır. Birkaç sarım tekrarından sonra istenilen kalınlıklar elde edilir ve kürleme oda sıcaklığında veya fırın içinde gerçekleştirilir. Şimdi mandrel çıkarılır ve ürün kalıptan çıkarılır. Filament sarma, lifleri çevresel, sarmal ve kutupsal desenlerde sararak çok yüksek mukavemet-ağırlık oranları sunabilir. Borular, tanklar, muhafazalar bu teknik kullanılarak üretilir. • YAPISAL KOMPOZİTLER : Genellikle hem homojen hem de kompozit malzemelerden oluşurlar. Bu nedenle, bunların özellikleri, bileşenlerinin kurucu malzemeleri ve geometrik tasarımı tarafından belirlenir. İşte başlıca türler: LAMİNAR KOMPOZİTLER : Bu yapı malzemeleri, tercih edilen yüksek mukavemetli yönlere sahip iki boyutlu levha veya panellerden yapılır. Katmanlar istiflenir ve birbirine yapıştırılır. İki dik eksende yüksek mukavemetli yönleri değiştirerek, iki boyutlu düzlemde her iki yönde de yüksek mukavemete sahip bir kompozit elde ederiz. Katmanların açılarını ayarlayarak, tercih edilen yönlerde mukavemete sahip bir kompozit üretilebilir. Modern kayak bu şekilde üretilir. SANDVİÇ PANELLER : Bu yapısal kompozitler hafiftir ancak yine de yüksek sertlik ve mukavemete sahiptir. Sandviç paneller, alüminyum alaşımları, fiber takviyeli plastikler veya çelik gibi sert ve güçlü bir malzemeden yapılmış iki dış levhadan ve dış levhalar arasında bir çekirdekten oluşur. Çekirdeğin hafif olması ve çoğu zaman düşük bir esneklik modülüne sahip olması gerekir. Popüler çekirdek malzemeler sert polimerik köpükler, ahşap ve peteklerdir. Sandviç paneller, inşaat sektöründe çatı kaplama malzemesi, zemin veya duvar malzemesi olarak ve ayrıca havacılık endüstrisinde yaygın olarak kullanılmaktadır. • NANOKOMPOZİTLER : Bu yeni malzemeler, bir matris içine gömülü nano boyutlu parçacık parçacıklarından oluşur. Nanokompozitleri kullanarak, kauçuk özelliklerini değiştirmeden korurken hava penetrasyonuna karşı çok iyi bariyerler olan kauçuk malzemeler üretebiliriz. CLICK Product Finder-Locator Service ÖNCEKİ SAYFA
- Montaj, Parçaları Birleştirme, Kaynak, Lehim, Lehimleme, Yapıştırma, Pres Fitleme, Perçinleme, Ultrasonik Lehim
Montaj, Parçaları Birleştirme, Sabitleme, Kaynak, Lehim, Lehimleme, Sinter, Yapıştırma, Pres Fitleme, Perçinleme, Ultrasonik Lehim, Pres Takma, Zımbalama, Fırın Lehimleme, Indüksiyon Kaynak, Elektron Kaynak, Bağlantı Elemanları, AGS-TECH Birleştirme, Montaj, Sabitleme İşlemleri Üretilen parçalarınızı KAYNAK, LEHİM, LEHİM, SİNTER, YAPIŞTIRICI YAPIŞTIRMA, SABİTLEME, PRES FİTLEME kullanarak birleştirir, birleştirir ve sabitler ve bitmiş veya yarı mamul haline getiririz. En popüler kaynak süreçlerimizden bazıları ark, oksigaz, direnç, projeksiyon, dikiş, yığma, perküsyon, katı hal, elektron ışını, lazer, termit, endüksiyon kaynağıdır. Popüler lehimleme proseslerimiz torç, indüksiyon, fırın ve daldırma lehimlemedir. Lehimleme yöntemlerimiz demir, sıcak plaka, fırın, indüksiyon, daldırma, dalga, reflow ve ultrasonik lehimlemedir. Yapışkan bağlama için sıklıkla termoplastikler ve termoset, epoksiler, fenolikler, poliüretan, yapışkan alaşımlar ve ayrıca bazı diğer kimyasallar ve bantlar kullanıyoruz. Son olarak sabitleme işlemlerimiz; çivileme, vidalama, somun ve cıvata, perçinleme, perçinleme, iğneleme, dikiş ve zımbalama ve presle geçme işlemlerinden oluşmaktadır. • KAYNAK : Kaynak, iş parçalarının eritilerek ve aynı zamanda erimiş kaynak havuzunu da birleştiren dolgu malzemelerinin eklenmesiyle malzemelerin birleştirilmesini içerir. Alan soğuduğunda güçlü bir derz elde ederiz. Bazı durumlarda basınç uygulanır. Kaynaktan farklı olarak, lehimleme ve lehimleme işlemleri, iş parçaları arasında yalnızca erime noktası daha düşük olan bir malzemenin eritilmesini içerir ve iş parçaları erimez. için buraya tıklamanızı öneririz.AGS-TECH Inc. tarafından hazırlanan Kaynak İşlemleri Şematik Gösterimlerimizi İNDİRİN Bu, aşağıda size sağladığımız bilgileri daha iyi anlamanıza yardımcı olacaktır. ARK KAYNAĞI'nda metalleri eriten bir elektrik arkı oluşturmak için bir güç kaynağı ve bir elektrot kullanıyoruz. Kaynak noktası bir koruyucu gaz veya buhar veya başka bir malzeme ile korunur. Bu işlem, otomotiv parçalarının ve çelik yapıların kaynağı için popülerdir. Shelted metal ark kaynağında (SMAW) veya çubuk kaynağı olarak da bilinir, ana malzemeye bir elektrot çubuğu yaklaştırılır ve aralarında bir elektrik arkı oluşturulur. Elektrot çubuğu erir ve dolgu malzemesi görevi görür. Elektrot ayrıca bir cüruf tabakası görevi gören ve koruyucu gaz görevi gören buharlar veren akı içerir. Bunlar, kaynak alanını çevresel kirlilikten korur. Başka hiçbir dolgu maddesi kullanılmamaktadır. Bu işlemin dezavantajları, yavaşlığı, elektrotları sık sık değiştirme ihtiyacı, akıdan kaynaklanan artık cürufu ufalama ihtiyacıdır. Demir, çelik, nikel, alüminyum, bakır vb. gibi bir dizi metal. Kaynak yapılabilir. Avantajları, ucuz araçları ve kullanım kolaylığıdır. Metal inert gaz (MIG) olarak da bilinen gaz metal ark kaynağı (GMAW), bir sarf malzemesi elektrot tel dolgusu ve kaynak bölgesinin çevresel kirlenmesine karşı telin etrafında akan bir asal veya kısmen asal gazın sürekli beslenmesine sahibiz. Çelik, alüminyum ve diğer demir dışı metaller kaynaklanabilir. MIG'nin avantajları, yüksek kaynak hızları ve kaliteli olmasıdır. Dezavantajları, karmaşık ekipmanı ve rüzgarlı dış ortamlarda karşılaşılan zorluklardır, çünkü kaynak alanı çevresindeki koruyucu gazı sabit tutmamız gerekir. GMAW'ın bir varyasyonu, akı malzemeleriyle doldurulmuş ince bir metal borudan oluşan akı özlü ark kaynağıdır (FCAW). Bazen tüpün içindeki akı, çevresel kontaminasyondan korunmak için yeterlidir. Tozaltı Ark Kaynağı (SAW), yaygın olarak otomatikleştirilmiş bir işlemdir, sürekli tel beslemeyi ve bir akı örtüsü tabakasının altına vurulan arkı içerir. Üretim oranları ve kalitesi yüksek, kaynak cürufu kolayca çıkıyor ve dumansız bir çalışma ortamımız var. Dezavantajı ise sadece parts'ı belirli konumlarda kaynaklamak için kullanılabilmesidir. Gaz tungsten ark kaynağında (GTAW) veya tungsten inert gaz kaynağında (TIG) ayrı bir dolgu maddesi ve atıl veya yakın soy gazlarla birlikte bir Tungsten elektrot kullanırız. Bildiğimiz gibi Tungsten yüksek bir erime noktasına sahiptir ve çok yüksek sıcaklıklar için çok uygun bir metaldir. TIG'deki Tungsten, yukarıda açıklanan diğer yöntemlerin aksine tüketilmez. İnce malzemelerin kaynağında diğer tekniklere göre avantajlı, yavaş fakat kaliteli bir kaynak tekniğidir. Birçok metal için uygundur. Plazma ark kaynağı benzerdir ancak ark oluşturmak için plazma gazı kullanır. Plazma ark kaynağındaki ark, GTAW'a kıyasla nispeten daha yoğundur ve çok daha yüksek hızlarda daha geniş bir metal kalınlık aralığı için kullanılabilir. GTAW ve plazma ark kaynağı aşağı yukarı aynı malzemelere uygulanabilir. OXY-FUEL / OXYFUEL KAYNAK ayrıca oksiasetilen kaynağı, oksi kaynak, gaz kaynağı olarak da adlandırılan gaz yakıtları ve kaynak için oksijen kullanılarak gerçekleştirilir. Elektrik enerjisi kullanılmadığından portatiftir ve elektriğin olmadığı yerlerde kullanılabilir. Bir kaynak torcu kullanarak, ortak bir erimiş metal havuzu oluşturmak için parçaları ve dolgu malzemesini ısıtıyoruz. Asetilen, benzin, hidrojen, propan, bütan vb. gibi çeşitli yakıtlar kullanılabilir. Oksi-yakıt kaynağında biri yakıt, diğeri oksijen için olmak üzere iki kap kullanırız. Oksijen yakıtı oksitler (yakar). DİRENÇ KAYNAĞI: Bu kaynak türü, joule ısıtmasından yararlanır ve elektrik akımının uygulandığı yerde belirli bir süre ısı üretilir. Metalden yüksek akımlar geçirilir. Bu yerde erimiş metal havuzları oluşur. Direnç kaynağı yöntemleri, verimlilikleri ve az kirlilik potansiyeli nedeniyle popülerdir. Bununla birlikte dezavantajlar, ekipman maliyetlerinin nispeten önemli olması ve nispeten ince iş parçalarının doğasında bulunan sınırlamadır. PUNTA KAYNAK, ana direnç kaynağı türlerinden biridir. Burada, iki veya daha fazla örtüşen levhayı veya iş parçasını, levhaları birbirine kenetlemek ve aralarından yüksek akım geçirmek için iki bakır elektrot kullanarak birleştiriyoruz. Bakır elektrotlar arasındaki malzeme ısınır ve o yerde erimiş bir havuz oluşur. Daha sonra akım durdurulur ve elektrotlar su ile soğutulduğu için bakır elektrot uçları kaynak yerini soğutur. Doğru malzemeye ve kalınlığa doğru miktarda ısı uygulamak bu tekniğin anahtarıdır, çünkü yanlış uygulanırsa bağlantı zayıf olacaktır. Punta kaynağı, iş parçalarında önemli bir deformasyona neden olmaması, enerji verimliliği, otomasyon kolaylığı ve üstün üretim oranları ve herhangi bir dolgu maddesi gerektirmemesi gibi avantajlara sahiptir. Dezavantajı ise, kaynak sürekli bir dikiş oluşturmak yerine noktalarda gerçekleştiğinden, diğer kaynak yöntemlerine kıyasla toplam mukavemet nispeten daha düşük olabilir. DİKİŞ KAYNAĞI ise benzer malzemelerin dökülen yüzeylerinde kaynaklar üretir. Dikiş, alın veya üst üste binen eklem olabilir. Dikiş kaynağı bir uçtan başlar ve kademeli olarak diğerine doğru hareket eder. Bu yöntem ayrıca kaynak bölgesine basınç ve akım uygulamak için bakırdan iki elektrot kullanır. Disk şeklindeki elektrotlar, dikiş hattı boyunca sabit temasla döner ve sürekli bir kaynak yapar. Burada da elektrotlar su ile soğutulur. Kaynaklar çok güçlü ve güvenilirdir. Diğer yöntemler projeksiyon, flaş ve yığma kaynak teknikleridir. KATI HAL KAYNAK yukarıda açıklanan önceki yöntemlerden biraz farklıdır. Birleşme, birleştirilen metallerin erime sıcaklığının altındaki sıcaklıklarda ve metal dolgu maddesi kullanılmadan gerçekleşir. Bazı işlemlerde basınç kullanılabilir. Farklı metallerin aynı kalıptan ekstrüde edildiği KOEXTRÜZYON KAYNAK, yumuşak alaşımları erime noktalarının altında birleştirdiğimiz SOĞUK BASINÇ KAYNAĞI, görünür kaynak çizgileri olmayan bir teknik DİFÜZYON KAYNAK, farklı malzemelerin, örneğin korozyona dayanıklı alaşımların yapısal malzemelerle birleştirilmesi için PATLAMA KAYNAĞI çeşitli yöntemlerdir. çelikler, boru ve sacları elektromanyetik kuvvetlerle hızlandırdığımız ELEKTROMANYETİK DARBE KAYNAĞI, metallerin yüksek sıcaklıklara ısıtılıp bir araya getirilmesinden oluşan FORGE KAYNAĞI, yeterli sürtünme kaynağının yapıldığı SÜRTÜNME KAYNAĞI, Dönmeyen, dönmeyen bir sürtünme içeren SÜRTÜNME KAYNAĞI. bağlantı hattını geçen sarf malzemesi aracı, vakum veya soy gazlarda erime sıcaklığının altındaki yüksek sıcaklıklarda metalleri birbirine bastırdığımız SICAK BASINÇ KAYNAĞI, SICAK İZOSTATİK BASINÇ KAYNAĞI bir kap içinde soy gazlar kullanarak basınç uyguladığımız bir işlem, birleştiğimiz RULO KAYNAK aralarında zorlayarak farklı malzemeleri iki döner tekerlek, ince metal veya plastik levhaların yüksek frekanslı titreşim enerjisi kullanılarak kaynaklandığı ULTRASONİK KAYNAK. Diğer kaynak yöntemlerimiz, derin nüfuziyetli ve hızlı işlemeli ancak pahalı bir yöntem olduğunu düşündüğümüz derin nüfuziyetli ELEKTRON KAYNAK KAYNAĞI, sadece ağır kalın levhalar ve çelik iş parçaları için uygun bir yöntem olan ELEKTROSLAG KAYNAK, elektromanyetik indüksiyon kullandığımız İNDÜKSİYON KAYNAK ve elektriksel olarak iletken veya ferromanyetik iş parçalarımızı ısıtır, ayrıca derin penetrasyon ve hızlı işleme ile LAZER IŞIN KAYNAK, ancak pahalı bir yöntem, LBW ile GMAW'ı aynı kaynak kafasında birleştiren ve plakalar arasında 2 mm'lik boşlukları köprüleyebilen LAZER HİBRİT KAYNAK, VURMALI KAYNAK bu Malzemelerin uygulanan basınçla dövülmesinin ardından elektrik deşarjı, alüminyum ve demir oksit tozları arasındaki ekzotermik reaksiyonu içeren THERMIT KAYNAĞI, sarf elektrotlarla ve sadece dikey konumda kullanılan ELEKTROGAZ KAYNAĞI ve son olarak saplamayı tabana birleştirmek için SAPLAMA ARK KAYNAĞI içerir. ısı ve basınç ile malzeme. için buraya tıklamanızı öneririz.AGS-TECH Inc. tarafından sunulan Lehimleme, Lehimleme ve Yapıştırıcı Yapıştırma İşlemlerine ilişkin Şematik Çizimlerimizi İNDİRİN Bu, aşağıda size sağladığımız bilgileri daha iyi anlamanıza yardımcı olacaktır. • LEHİMLEME : İki veya daha fazla metali, aralarındaki dolgu metallerini erime noktalarının üzerinde ısıtarak ve yaymak için kılcal etki kullanarak birleştiririz. İşlem lehimlemeye benzer, ancak dolguyu eritmek için gerekli sıcaklıklar sert lehimlemede daha yüksektir. Kaynakta olduğu gibi, akı dolgu malzemesini atmosferik kirlenmeden korur. Soğuduktan sonra iş parçaları birleştirilir. Proses, aşağıdaki temel adımları içerir: İyi oturma ve boşluk, temel malzemelerin uygun şekilde temizlenmesi, uygun sabitleme, uygun akı ve atmosfer seçimi, montajın ısıtılması ve son olarak lehimli montajın temizlenmesi. Lehimleme süreçlerimizden bazıları, manuel veya otomatik bir şekilde gerçekleştirilen popüler bir yöntem olan TORCH LEHTARLAMADIR. Düşük hacimli üretim siparişleri ve özel durumlar için uygundur. Lehimlenen bağlantının yakınında gaz alevleri kullanılarak ısı uygulanır. FIRIN LEHİMLEME, daha az operatör becerisi gerektirir ve endüstriyel seri üretime uygun yarı otomatik bir işlemdir. Hem sıcaklık kontrolü hem de fırındaki atmosferin kontrolü bu tekniğin avantajlarıdır, çünkü birincisi kontrollü ısı döngülerine sahip olmamızı ve torç lehiminde olduğu gibi lokal ısıtmayı ortadan kaldırmamızı sağlar ve ikincisi parçayı oksidasyondan korur. Jigging kullanarak üretim maliyetlerini minimuma indirme yeteneğine sahibiz. Dezavantajları ise yüksek güç tüketimi, ekipman maliyetleri ve daha zorlu tasarım konularıdır. VAKUM LEHİMLEME, bir vakum fırınında gerçekleşir. Sıcaklık tekdüzeliği korunur ve çok az kalıntı gerilimi olan akıcı, çok temiz bağlantılar elde ederiz. Yavaş ısıtma ve soğutma döngüleri sırasında mevcut olan düşük kalıntı gerilimler nedeniyle, ısıl işlemler vakumlu sert lehimleme sırasında gerçekleştirilebilir. En büyük dezavantajı yüksek maliyetidir çünkü vakum ortamının oluşturulması pahalı bir işlemdir. Yine bir başka teknik DIP LEHTARLAMA, lehimleme bileşiğinin eşleşen yüzeylere uygulandığı sabitlenmiş parçaları birleştirir. Bundan sonra, fikstürlü parçalar, bir ısı transfer ortamı ve akış işlevi gören Sodyum Klorür (sofra tuzu) gibi bir erimiş tuz banyosuna daldırılır. Hava hariç tutulur ve bu nedenle oksit oluşumu gerçekleşmez. İNDÜKSİYON LEHİMİNDE, malzemeleri ana malzemelerden daha düşük bir erime noktasına sahip bir dolgu metali ile birleştiriyoruz. İndüksiyon bobininden gelen alternatif akım, çoğunlukla demir içeren manyetik malzemeler üzerinde indüksiyon ısıtmasını indükleyen bir elektromanyetik alan oluşturur. Yöntem, seçici ısıtma, dolgu maddelerinin sadece istenen alanlarda akan iyi derzler, alev olmadığı ve soğutmanın hızlı olması nedeniyle az oksidasyon, hızlı ısıtma, tutarlılık ve yüksek hacimli üretim için uygunluk sağlar. Süreçlerimizi hızlandırmak ve tutarlılığı sağlamak için sıklıkla preform kullanıyoruz. Seramikten metale bağlantı parçaları, hermetik sızdırmazlık, vakumlu geçişler, yüksek ve ultra yüksek vakum ve sıvı kontrol bileşenleri üreten lehimleme tesisimiz hakkında bilgiler burada bulunabilir: Lehimleme Fabrikası Broşürü • LEHİM : Lehimlemede iş parçalarının erimesi değil, birleşme yerine akan birleştirme parçalarından daha düşük erime noktasına sahip bir dolgu metali vardır. Lehimlemedeki dolgu metali, sert lehimlemeden daha düşük sıcaklıkta erir. Lehimleme için kurşunsuz alaşımlar kullanıyoruz ve RoHS uyumluluğumuz var ve farklı uygulama ve gereksinimler için gümüş alaşımı gibi farklı ve uygun alaşımlarımız var. Lehimleme bize gaz ve sıvı geçirmez bağlantılar sunar. YUMUŞAK LEHİM'de dolgu metalimizin erime noktası 400 Santigrat'ın altındayken, GÜMÜŞ LEHİM ve LEHİM'de daha yüksek sıcaklıklara ihtiyacımız var. Yumuşak lehimleme daha düşük sıcaklıklar kullanır, ancak yüksek sıcaklıklarda zorlu uygulamalar için güçlü bağlantılarla sonuçlanmaz. Gümüş lehimleme ise torç tarafından sağlanan yüksek sıcaklıklar gerektirir ve bize yüksek sıcaklık uygulamalarına uygun güçlü bağlantılar sağlar. Lehimleme en yüksek sıcaklıkları gerektirir ve genellikle bir torç kullanılır. Sert lehim bağlantıları çok güçlü olduğundan, ağır demir nesnelerin onarımı için iyi bir adaydır. Üretim hatlarımızda hem manuel el lehimleme hem de otomatik lehim hatları kullanıyoruz. İNDÜKSİYON LEHİM, indüksiyonla ısıtmayı kolaylaştırmak için bir bakır bobinde yüksek frekanslı AC akımı kullanır. Lehimli kısımda akımlar indüklenir ve bunun sonucunda yüksek direnç joint'te ısı üretilir. Bu ısı dolgu metalini eritir. Akı da kullanılır. İndüksiyon lehimleme, silindirleri ve boruları sürekli bir işlemde, bobinleri etraflarına sararak lehimlemek için iyi bir yöntemdir. Grafit ve seramik gibi bazı malzemelerin lehimlenmesi, lehimleme öncesinde iş parçalarının uygun bir metal ile kaplanmasını gerektirdiğinden daha zordur. Bu, arayüzey yapışmasını kolaylaştırır. Bu tür malzemeleri özellikle hermetik paketleme uygulamaları için lehimliyoruz. Baskılı devre kartlarımızı (PCB) çoğunlukla DALGA LEHİM kullanarak yüksek hacimde üretiyoruz. Sadece küçük miktarda prototipleme amacıyla havya kullanarak elle lehimleme kullanıyoruz. Hem açık delik hem de yüzeye monte PCB düzenekleri (PCBA) için dalga lehimleme kullanıyoruz. Geçici bir yapıştırıcı, bileşenleri devre kartına bağlı tutar ve düzenek bir konveyöre yerleştirilir ve erimiş lehim içeren bir ekipman boyunca hareket eder. Önce PCB flukslanır ve ardından ön ısıtma bölgesine girer. Erimiş lehim bir tavadadır ve yüzeyinde duran dalgalardan oluşan bir desene sahiptir. PCB bu dalgalar üzerinde hareket ettiğinde, bu dalgalar PCB'nin alt kısmına temas eder ve lehim pedlerine yapışır. Lehim, PCB'nin kendisinde değil, yalnızca pimlerde ve pedlerde kalır. Erimiş lehimdeki dalgalar iyi kontrol edilmelidir, böylece sıçrama olmaz ve dalga tepeleri dokunmaz ve levhaların istenmeyen alanlarını kirletmez. REFLOW SOLDERING'de elektronik bileşenleri panolara geçici olarak tutturmak için yapışkan bir lehim pastası kullanıyoruz. Daha sonra levhalar, sıcaklık kontrollü bir yeniden akış fırınından geçirilir. Burada lehim erir ve bileşenleri kalıcı olarak bağlar. Bu tekniği hem yüzeye monteli bileşenler hem de delikten geçen bileşenler için kullanıyoruz. Kart üzerindeki elektronik bileşenlerin, maksimum sıcaklık sınırlarının üzerine çıkarak aşırı ısınmasını önlemek için, uygun sıcaklık kontrolü ve fırın sıcaklıklarının ayarlanması çok önemlidir. Yeniden akışlı lehimleme sürecinde aslında, ön ısıtma aşaması, termal ıslatma aşaması, yeniden akış ve soğutma aşamaları gibi her biri farklı bir termal profile sahip birkaç bölge veya aşamaya sahibiz. Bu farklı adımlar, baskılı devre kartı düzeneklerinin (PCBA) hasarsız yeniden akış lehimlemesi için gereklidir. ULTRASONİK LEHİM, benzersiz özelliklere sahip, sıklıkla kullanılan bir başka tekniktir- Cam, seramik ve metalik olmayan malzemeleri lehimlemek için kullanılabilir. Örneğin, metalik olmayan fotovoltaik paneller, bu teknik kullanılarak yapıştırılabilen elektrotlara ihtiyaç duyar. Ultrasonik lehimlemede, aynı zamanda ultrasonik titreşimler yayan ısıtılmış bir lehim ucu kullanırız. Bu titreşimler, alt tabakanın erimiş lehim malzemesi ile ara yüzeyinde kavitasyon kabarcıkları üretir. Kavitasyonun patlayıcı enerjisi oksit yüzeyini değiştirir ve kiri ve oksitleri giderir. Bu süre zarfında bir alaşım tabakası da oluşur. Yapıştırma yüzeyindeki lehim oksijen içerir ve cam ile lehim arasında güçlü bir ortak bağ oluşmasını sağlar. DIP SOLDERING, sadece küçük ölçekli üretime uygun dalga lehimlemenin daha basit bir versiyonu olarak kabul edilebilir. Diğer işlemlerde olduğu gibi ilk temizleme akısı uygulanır. Monte edilmiş bileşenlere sahip PCB'ler, erimiş lehim içeren bir tanka manuel veya yarı otomatik bir şekilde daldırılır. Erimiş lehim, tahtadaki lehim maskesi tarafından korunmayan açıkta kalan metalik alanlara yapışır. Ekipman basit ve ucuzdur. • YAPIŞTIRICI YAPIŞTIRMA : Sık kullandığımız bir başka popüler tekniktir ve yapıştırıcılar, epoksiler, plastik maddeler veya diğer kimyasallar kullanılarak yüzeylerin yapıştırılmasını içerir. Yapışma, solventin buharlaştırılması, ısıyla kürleme, UV ışık kürleme, basınç kürleme veya belirli bir süre beklenerek gerçekleştirilir. Üretim hatlarımızda çeşitli yüksek performanslı yapıştırıcılar kullanılmaktadır. Uygun şekilde tasarlanmış uygulama ve kürleme süreçleriyle, yapıştırıcıyla yapıştırma, güçlü ve güvenilir olan çok düşük gerilimli bağlarla sonuçlanabilir. Yapışkan bağlar nem, kirleticiler, aşındırıcılar, titreşim vb. gibi çevresel faktörlere karşı iyi koruyucular olabilir. Yapıştırıcıyla birleştirmenin avantajları şunlardır: aksi takdirde lehimlenmesi, kaynaklanması veya sert lehimlenmesi zor olan malzemelere uygulanabilirler. Ayrıca kaynak veya diğer yüksek sıcaklık işlemlerinden zarar görecek ısıya duyarlı malzemeler için de tercih edilebilir. Yapıştırıcıların diğer avantajları, düzensiz şekilli yüzeylere uygulanabilmeleri ve diğer yöntemlere kıyasla montaj ağırlığını çok çok küçük miktarlarda artırabilmeleridir. Ayrıca parçalardaki boyutsal değişiklikler çok azdır. Bazı yapıştırıcılar, indeks eşleştirme özelliklerine sahiptir ve ışık veya optik sinyal gücünü önemli ölçüde azaltmadan optik bileşenler arasında kullanılabilir. Dezavantajları ise üretim hatlarını yavaşlatabilen daha uzun kürlenme süreleri, fikstür gereksinimleri, yüzey hazırlama gereksinimleri ve yeniden işleme gerektiğinde sökme zorluğudur. Yapıştırma operasyonlarımızın çoğu aşağıdaki adımları içerir: -Yüzey işleme: Deiyonize su temizliği, alkol temizliği, plazma veya korona temizliği gibi özel temizleme prosedürleri yaygındır. Temizledikten sonra, mümkün olan en iyi derzleri sağlamak için yüzeylere yapışma arttırıcılar uygulayabiliriz. - Parça Sabitleme: Hem yapıştırıcı uygulaması hem de kürleme için özel fikstürler tasarlıyor ve kullanıyoruz. -Yapıştırıcı Uygulaması: Yapıştırıcıları doğru yere ulaştırmak için bazen manuel, bazen de duruma bağlı olarak robotik, servo motor, lineer aktüatör gibi otomatik sistemler, doğru hacim ve miktarda dağıtmak için dispenserler kullanıyoruz. -Kürleme: Yapıştırıcıya bağlı olarak, basit kurutma ve kürlemenin yanı sıra katalizör görevi gören UV ışıkları altında kürleme veya bir fırında ısıl kürleme veya aparatlara ve fikstürlere monte edilmiş dirençli ısıtma elemanları kullanarak kürleme yapabiliriz. için buraya tıklamanızı öneririz.AGS-TECH Inc. Bu, aşağıda size sağladığımız bilgileri daha iyi anlamanıza yardımcı olacaktır. • BAĞLAMA SÜREÇLERİ : Mekanik birleştirme işlemlerimiz iki farklı kategoriye ayrılır: BAĞLANTI ELEMANLARI ve ENTEGRAL KAYNAKLAR. Kullandığımız bağlantı elemanları örnekleri vidalar, pimler, somunlar, cıvatalar, perçinlerdir. Kullandığımız yekpare bağlantı örnekleri, geçmeli ve büzüşmeli geçmeler, dikişler, kıvrımlardır. Çeşitli sabitleme yöntemleri kullanarak mekanik bağlantılarımızın uzun yıllar kullanım için güçlü ve güvenilir olmasını sağlıyoruz. VİDALAR ve CIVATALAR, nesneleri bir arada tutmak ve konumlandırmak için en yaygın kullanılan bağlantı elemanlarından bazılarıdır. Vidalarımız ve cıvatalarımız ASME standartlarını karşılamaktadır. Altıgen başlı vidalar ve altıgen cıvatalar, gecikmeli vidalar ve cıvatalar, çift uçlu vida, dübel vidası, delikli vida, ayna vidası, sac vida, ince ayar vidası, matkap uçlu ve kendinden diş açan vidalar dahil olmak üzere çeşitli vida ve cıvata türleri kullanılır. , ayar vidası, yerleşik rondelalı vidalar… ve daha fazlası. Havşa başlı, kubbeli, yuvarlak, flanşlı gibi çeşitli vida başlı tiplerimiz ve slot, phillips, kare, altıgen soket gibi çeşitli vidalı tahrik çeşitlerimiz bulunmaktadır. A RIVET ise düz silindirik bir şaft ve bir kafadan oluşan kalıcı bir mekanik bağlantı elemanıdır. Yerleştirme işleminden sonra perçinin diğer ucu deforme olur ve çapı genişletilerek yerinde kalması sağlanır. Başka bir deyişle, perçin kurulumdan önce bir başlı ve kurulumdan sonra iki başlıdır. Masif/yuvarlak başlı perçinler, yapısal, yarı borulu, kör, oscar, tahrikli, gömme, sürtünme kilitli, kendinden delen perçinler gibi uygulamaya, mukavemete, erişilebilirliğe ve maliyete bağlı olarak çeşitli perçin çeşitlerini kuruyoruz. Kaynak ısısından kaynaklanan ısıl deformasyon ve malzeme özelliklerinde değişiklik olmaması gereken durumlarda perçinleme tercih edilebilir. Perçinleme ayrıca hafiflik ve özellikle kesme kuvvetlerine karşı iyi mukavemet ve dayanıklılık sunar. Çekme yüklerine karşı ise vida, somun ve civata daha uygun olabilir. CLINCHING işleminde, birleştirilmekte olan sac metaller arasında mekanik bir kilit oluşturmak için özel zımba ve kalıplar kullanıyoruz. Zımba, sac levha katmanlarını kalıp boşluğuna iter ve kalıcı bir bağlantı oluşumuna neden olur. Perçinlemede ısıtma ve soğutma gerekmez ve soğuk bir çalışma işlemidir. Bazı durumlarda punta kaynağının yerini alabilecek ekonomik bir işlemdir. PİMLEMEde, makine parçalarının birbirlerine göre konumlarını sabitlemek için kullanılan makine elemanları olan pimler kullanıyoruz. Başlıca türleri çatal pimler, kopilya pimleri, yaylı pimler, kavelalar, ve ayrık pimlerdir. ZIMBALAMA'da malzemeleri birleştirmek veya bağlamak için kullanılan iki uçlu bağlantı elemanları olan zımba tabancaları ve zımbalar kullanıyoruz. Zımbalamanın aşağıdaki avantajları vardır: Ekonomik, basit ve kullanımı hızlıdır, zımbaların tepesi, birbirine kenetlenmiş malzemeleri köprülemek için kullanılabilir, Zımbanın tepesi, kablo gibi bir parçayı köprülemeyi ve delmeden veya delmeden bir yüzeye sabitlemeyi kolaylaştırabilir. zarar verici, nispeten kolay çıkarılması. PRES TAKMA, parçaların birbirine itilmesiyle gerçekleştirilir ve aralarındaki sürtünme parçaları birbirine bağlar. Büyük boyutlu bir şaft ve küçük boyutlu bir delikten oluşan pres geçme parçalar genellikle iki yöntemden biriyle monte edilir: Ya kuvvet uygulayarak ya da parçaların ısıl genleşmesinden veya büzülmesinden yararlanarak. Bir pres bağlantısı kuvvet uygulanarak kurulduğunda ya hidrolik pres ya da elle çalıştırılan pres kullanırız. Öte yandan termal genleşme ile pres bağlantı kurulduğunda, saran parçaları ısıtıyoruz ve sıcakken yerlerine monte ediyoruz. Soğuduklarında kasılırlar ve normal boyutlarına dönerler. Bu, iyi bir baskı uyumu sağlar. Buna alternatif olarak SHRINK-FITTING diyoruz. Bunu yapmanın diğer yolu, montajdan önce zarflı parçaları soğutmak ve ardından eşleşen parçalarına kaydırmaktır. Montaj ısındığında genişler ve sıkı bir uyum elde ederiz. Bu ikinci yöntem, ısıtmanın malzeme özelliklerini değiştirme riski oluşturduğu durumlarda tercih edilebilir. Bu durumlarda soğutma daha güvenlidir. Pnömatik & Hidrolik Bileşenler ve Montajlar • Valfler, O-ring, rondela, contalar, conta, halka, şim gibi hidrolik ve pnömatik bileşenler. Valfler ve pnömatik bileşenler çok çeşitli olduğu için burada her şeyi listeleyemeyiz. Uygulamanızın fiziksel ve kimyasal ortamlarına bağlı olarak size özel ürünlerimiz mevcuttur. Lütfen vanalarınız ve pnömatik bileşenlerinizle temas edecek uygulama, bileşen tipi, özellikler, basınç, sıcaklık, sıvı veya gazlar gibi ortam koşullarını belirtin; ve sizin için en uygun ürünü seçecek veya uygulamanıza özel üreteceğiz. CLICK Product Finder-Locator Service ÖNCEKİ SAYFA
- Cam ve Seramik Şekillendirme, Cam Üfleme, Üfleme Kalıpları, Optik Cam, Cam Borular, Sinterleme, Elmas Taşlama, Cam Ekstrüzyonu
Cam ve Seramik Şekillendirme, Cam Üfleme, Hermetik Paketleme, Sızdırmaz Cam Paketler, Kurşun geçirmez cam, Üfleme Kalıpları, Optik Cam, İletken Cam, Endüstriyel Cam İmalatı, Cam Borular, Cam Çubuk, Cam Kalıplama, Teknik Seramik, Elmas Taşlama, Sinterleme, Cam Ekstrüzyon, Cam Kaynak Cam ve Seramik Ürün Kalıpları ve Şekillendirme Sunduğumuz cam imalatı türleri, cam kap, cam üfleme, cam elyafı ve boru ve çubuk, evsel ve endüstriyel cam eşyalar, lamba ve ampul, hassas cam kalıplama, optik bileşenler ve düzenekler, düz ve levha ve düz camdır. Hem elle şekillendirme hem de makine şekillendirme yapıyoruz. Popüler teknik seramik üretim süreçlerimiz, kalıp presleme, izostatik presleme, sıcak izostatik presleme, sıcak presleme, kayar döküm, bant döküm, ekstrüzyon, enjeksiyonlu kalıplama, yeşil işleme, sinterleme veya ateşleme, elmas taşlama, hermetik montajlardır. için buraya tıklamanızı öneririz. AGS-TECH Inc. tarafından hazırlanan Cam Şekillendirme ve Şekillendirme Proseslerinin Şematik Gösterimlerini İNDİRİN. AGS-TECH Inc. tarafından hazırlanan Teknik Seramik Üretim Proseslerinin Şematik Gösterimlerini İNDİRİN. Fotoğraflar ve eskizler içeren bu indirilebilir dosyalar, aşağıda size sunduğumuz bilgileri daha iyi anlamanıza yardımcı olacaktır. • KONTEYNER CAM İMALATI: İmalat için otomatik PRES VE ÜFLEME ve ayrıca ÜFLEME ve ÜFLEME hatlarına sahibiz. Üfleme ve üfleme işleminde boş kalıba bir damla damlatıyoruz ve üstten basınçlı hava üfleyerek boyun oluşturuyoruz. Bunun hemen ardından, şişenin ön kalıbını oluşturmak için, konteyner boynundan diğer yönden basınçlı hava ikinci kez üflenir. Bu ön kalıp daha sonra asıl kalıba aktarılır, yumuşatmak için yeniden ısıtılır ve ön kalıba son kap şeklini vermek için basınçlı hava uygulanır. Daha açık bir ifadeyle, istenen şekli alması için basınçlandırılır ve üfleme kalıbı boşluğunun duvarlarına doğru itilir. Son olarak, üretilen cam kap, daha sonra yeniden ısıtma ve kalıplama sırasında üretilen gerilimlerin giderilmesi için bir tavlama fırınına aktarılır ve kontrollü bir şekilde soğutulur. Pres ve üfleme yönteminde, erimiş parçalar bir hamur kalıbına (boş kalıp) konur ve hamur şekline (boş şekil) preslenir. Boşluklar daha sonra üfleme kalıplarına aktarılır ve yukarıda "Üfleme ve Üfleme İşlemi" altında açıklanan işleme benzer şekilde üflenir. Tavlama ve gerilim giderme gibi sonraki adımlar benzer veya aynıdır. • CAM ÜFLEME : Konvansiyonel el üfleme ve otomatik ekipmanlarla basınçlı hava kullanarak cam ürünleri üretmekteyiz. Bazı siparişler için, cam sanatı içeren projeler veya gevşek toleranslı daha az sayıda parça gerektiren projeler, prototipleme / demo projeleri gibi geleneksel üfleme gereklidir. Geleneksel cam üfleme, içi boş bir metal borunun bir erimiş cam kabına daldırılmasını ve bir miktar cam malzemesinin toplanması için borunun döndürülmesini içerir. Borunun ucunda toplanan cam yassı demir üzerine haddelenir, istenildiği gibi şekillendirilir, uzatılır, tekrar ısıtılır ve hava üflenir. Hazır olduğunda bir kalıba yerleştirilir ve hava üflenir. Camın metalle temasını önlemek için kalıp boşluğu ıslaktır. Su filmi aralarında bir yastık görevi görür. Elle üfleme, emek yoğun bir yavaş süreçtir ve yalnızca prototipleme veya yüksek değerli ürünler için uygundur, parça başına pahalı olmayan yüksek hacimli siparişler için uygun değildir. • YERLİ & ENDÜSTRİYEL CAM MALZEME İMALATI : Çeşitli cam malzemeleri kullanılarak çok çeşitli cam eşyalar üretilmektedir. Bazı camlar ısıya dayanıklı ve laboratuvar kapları için uygundur, bazıları ise bulaşık makinelerine defalarca dayanacak kadar iyidir ve yerli ürünler yapmaya uygundur. Westlake makineleri kullanılarak günde on binlerce adet bardak üretilmektedir. Basitleştirmek için, erimiş cam vakumla toplanır ve ön formları yapmak için kalıplara yerleştirilir. Daha sonra kalıplara hava üflenir, bunlar başka bir kalıba aktarılır ve tekrar hava üflenir ve cam son şeklini alır. Elde üflemede olduğu gibi bu kalıplar su ile ıslanır. Daha fazla germe, boynun oluşturulduğu bitirme işleminin bir parçasıdır. Fazla cam yakılır. Daha sonra yukarıda açıklanan kontrollü yeniden ısıtma ve soğutma işlemi takip eder. • CAM TÜP & ÇUBUK ŞEKİLLENDİRME : Cam tüp imalatında kullandığımız ana prosesler DANNER ve VELLO prosesleridir. Danner Sürecinde, bir fırından çıkan cam, refrakter malzemelerden yapılmış eğimli bir manşonun üzerine akar ve düşer. Manşon, dönen bir içi boş mil veya üfleme borusu üzerinde taşınır. Cam daha sonra manşonun etrafına sarılır ve manşondan aşağıya ve şaftın ucuna doğru akan pürüzsüz bir tabaka oluşturur. Tüp oluşturma durumunda, içi boş uçlu bir üfleme borusundan hava üflenir ve çubuk oluşturma durumunda, şaft üzerinde katı uçlar kullanırız. Tüpler veya çubuklar daha sonra taşıma silindirleri üzerine çekilir. Manşon çapı ve üfleme hava basıncı istenilen değere ayarlanarak, sıcaklık, cam akış hızı ve çekme hızı ayarlanarak cam tüplerin et kalınlığı ve çapı gibi ölçüler istenilen değerlere ayarlanır. Öte yandan Vello cam tüp üretim süreci, bir fırından dışarı çıkan ve içi boş bir mandrel veya çan bulunan bir kaseye giren camı içerir. Cam daha sonra mandrel ve kase arasındaki hava boşluğundan geçer ve bir tüp şeklini alır. Daha sonra silindirler üzerinden bir çekme makinesine gider ve soğutulur. Soğutma hattının sonunda kesim ve son işleme gerçekleşir. Tüp boyutları, Danner prosesinde olduğu gibi ayarlanabilir. Danner ile Vello sürecini karşılaştırırken, Vello sürecinin büyük miktarda üretim için daha uygun olduğunu söyleyebiliriz, oysa Danner süreci daha küçük hacimli tüp siparişleri için daha uygun olabilir. • LEVHA & DÜZ & DÜZ CAM İŞLENMESİ : Milimetre altı kalınlıklardan birkaç santimetreye kadar değişen kalınlıklarda büyük miktarlarda düz camımız bulunmaktadır. Düz camlarımız neredeyse optik mükemmelliğe sahiptir. Yansıma önleyici veya ayna kaplama gibi kaplamaları koymak için kimyasal buhar biriktirme tekniğinin kullanıldığı optik kaplamalar gibi özel kaplamalara sahip camlar sunuyoruz. Ayrıca şeffaf iletken kaplamalar yaygındır. Ayrıca cam üzerinde hidrofobik veya hidrofilik kaplamalar ve camın kendi kendini temizlemesini sağlayan kaplamalar da mevcuttur. Temperli, kurşun geçirmez ve lamine camlar diğer popüler ürünlerdir. Camı istenilen toleranslarda istenilen şekilde kesiyoruz. Düz camı eğmek veya bükmek gibi diğer ikincil işlemler de mevcuttur. • HASSAS CAM KALIPLAMA : Bu tekniği çoğunlukla, taşlama, lepleme ve cilalama gibi daha pahalı ve zaman alıcı tekniklere ihtiyaç duymadan hassas optik bileşenlerin imalatında kullanıyoruz. Bu teknik her zaman en iyi optiğin en iyisini yapmak için yeterli değildir, ancak tüketici ürünleri, dijital kameralar, medikal optikler gibi bazı durumlarda yüksek hacimli üretim için daha ucuz ve iyi bir seçenek olabilir. Ayrıca asferler gibi karmaşık geometrilerin gerekli olduğu diğer cam şekillendirme tekniklerine göre bir avantajı vardır. Temel işlem, kalıbımızın alt tarafının boş cam ile yüklenmesini, oksijenin uzaklaştırılması için işlem odasının boşaltılmasını, kalıbın kapanmasına yakın, kalıbın ve camın kızılötesi ışıkla hızlı ve izotermal ısıtılmasını, kalıp yarımlarının daha fazla kapanmasını içerir. yumuşatılmış camın kontrollü bir şekilde istenen kalınlığa kadar yavaşça bastırılması ve son olarak camın soğutulması ve haznenin nitrojen ile doldurulması ve ürünün uzaklaştırılması. Hassas sıcaklık kontrolü, kalıp kapanma mesafesi, kalıp kapatma kuvveti, kalıbın ve cam malzemenin genleşme katsayılarının eşleştirilmesi bu süreçte çok önemlidir. • CAM OPTİK BİLEŞEN VE PARÇALARIN İMALATI: Hassas cam kalıplamanın yanı sıra, zorlu uygulamalar için yüksek kaliteli optik bileşenler ve düzenekler yapmak için kullandığımız bir dizi değerli işlem vardır. Optik dereceli camların ince özel aşındırıcı bulamaçlarda taşlanması, leplenmesi ve parlatılması, optik lensler, prizmalar, daireler ve daha fazlasını yapmak için bir sanat ve bilimdir. Yüzey düzlüğü, dalgalılık, pürüzsüzlük ve hatasız optik yüzeyler, bu tür işlemlerde çok fazla deneyim gerektirir. Ortamdaki küçük değişiklikler, spesifikasyon dışı ürünlerle sonuçlanabilir ve üretim hattını durdurabilir. Optik yüzeyde temiz bir bezle tek bir silme işleminin bir ürünün teknik özellikleri karşılamasını veya testi geçememesini sağlayabildiği durumlar vardır. Kullanılan bazı popüler cam malzemeler erimiş silika, kuvars, BK7'dir. Ayrıca bu tür bileşenlerin montajı özel bir niş deneyimi gerektirir. Bazen özel yapıştırıcılar kullanılıyor. Bununla birlikte, bazen optik temas adı verilen bir teknik en iyi seçimdir ve takılan optik camlar arasında hiçbir malzeme içermez. Tutkal olmadan birbirine tutturmak için fiziksel olarak temas eden düz yüzeylerden oluşur. Bazı durumlarda, optik bileşenleri belirli mesafelerde ve belirli geometrik yönlerde monte etmek için mekanik ara parçalar, hassas cam çubuklar veya bilyeler, kelepçeler veya işlenmiş metal bileşenler kullanılmaktadır. Son teknoloji optikleri üretmek için bazı popüler tekniklerimizi inceleyelim. TAŞLAMA & LEÇLEME & PARLATMA : Optik bileşenin kaba şekli, bir boş camın taşlanmasıyla elde edilir. Daha sonra optik bileşenlerin pürüzlü yüzeyleri döndürülerek ve istenilen yüzey şekillerine sahip aletlere sürtülerek lepleme ve polisaj gerçekleştirilir. Küçük aşındırıcı parçacıklar ve sıvı içeren bulamaçlar, optikler ve şekillendirme aletleri arasına dökülüyor. Bu tür bulamaçlardaki aşındırıcı parçacık boyutları, istenen düzlük derecesine göre seçilebilir. Kritik optik yüzeylerin istenen şekillerden sapmaları, kullanılan ışığın dalga boyları cinsinden ifade edilir. Yüksek hassasiyetli optiklerimiz dalga boyunun onda biri (Dalga Boyu/10) toleranslarına sahiptir veya daha da sıkı olması mümkündür. Yüzey profilinin yanı sıra, kritik yüzeyler taranır ve boyutlar, çizikler, talaşlar, çukurlar, lekeler...vb. diğer yüzey özellikleri ve kusurları için değerlendirilir. Optik üretim alanındaki çevresel koşulların sıkı kontrolü ve son teknoloji ekipmanlarla kapsamlı metroloji ve test gereksinimleri, bunu zorlu bir endüstri dalı haline getiriyor. • CAM İMALİNDE İKİNCİ İŞLEMLER: Yine camın ikincil ve bitirme işlemlerinde hayal gücünüzle sınırlıyız. İşte bunlardan bazılarını listeliyoruz: -Cam üzeri kaplamalar (optik, elektrik, tribolojik, termal, fonksiyonel, mekanik...). Örnek olarak, camın yüzey özelliklerini değiştirerek, örneğin ısıyı yansıtarak bina içlerini serin tutabilir veya nanoteknolojiyi kullanarak bir tarafı kızılötesi soğurucu hale getirebiliriz. Bu, binaların içini sıcak tutmaya yardımcı olur, çünkü en dış yüzeydeki cam tabakası, binanın içindeki kızılötesi radyasyonu emecek ve onu içeriye geri yayacaktır. -Cam üzerine aşındırma -Uygulamalı Seramik Etiketleme (ACL) -Oymak -Alev parlatma -Kimyasal parlatma -boyama TEKNİK SERAMİK İMALATI • KALIP PRESLEME : Bir kalıpta hapsedilmiş granüler tozların tek eksenli sıkıştırılmasından oluşur. • SICAK PRESLEME : Kalıp preslemeye benzer, ancak yoğunlaşmayı arttırmak için sıcaklık ilavesiyle. Toz veya sıkıştırılmış preform grafit kalıba yerleştirilir ve kalıp 2000 C gibi yüksek sıcaklıklarda tutulurken tek eksenli basınç uygulanır. Sıcaklıklar, işlenen seramik tozunun tipine göre farklılık gösterebilir. Karmaşık şekiller ve geometriler için elmas taşlama gibi sonraki işlemlere ihtiyaç duyulabilir. • İZOSTATİK PRESLEME : Granül toz veya pres preslenmiş parçalar hava geçirmez kaplara ve daha sonra içinde sıvı bulunan kapalı bir basınçlı kaba yerleştirilir. Daha sonra basınçlı kabın basıncı artırılarak sıkıştırılırlar. Kabın içindeki sıvı, basınç kuvvetlerini hava geçirmez kabın tüm yüzey alanı üzerinde eşit olarak aktarır. Malzeme böylece homojen bir şekilde sıkıştırılır ve esnek kabının şeklini ve iç profilini ve özelliklerini alır. • SICAK İZOSTATİK PRESLEME : İzostatik preslemeye benzer, ancak basınçlı gaz atmosferine ek olarak, kompaktı yüksek sıcaklıkta sinterliyoruz. Sıcak izostatik presleme, ek yoğunlaştırma ve artan mukavemet ile sonuçlanır. • SLIP DÖKÜM / DREN DÖKÜM : Kalıbı mikrometre boyutunda seramik partikül süspansiyonu ve taşıyıcı sıvı ile dolduruyoruz. Bu karışıma “kayma” denir. Kalıbın gözenekleri vardır ve bu nedenle karışımdaki sıvı kalıba süzülür. Sonuç olarak, kalıbın iç yüzeylerinde bir döküm oluşur. Sinterleme işleminden sonra parçalar kalıptan çıkarılabilir. • BANT DÖKÜM : Düz hareketli taşıyıcı yüzeyler üzerine seramik bulamaçlar dökülerek seramik bant imalatı yapmaktayız. Bulamaçlar, bağlama ve taşıma amacıyla diğer kimyasallarla karıştırılmış seramik tozları içerir. Çözücüler buharlaştıkça, geriye istenildiği gibi kesilebilen veya yuvarlanabilen yoğun ve esnek seramik levhalar kalır. • EKSTRÜZYON FORMLAMA : Diğer ekstrüzyon proseslerinde olduğu gibi, seramik tozunun bağlayıcılar ve diğer kimyasallarla yumuşak bir karışımı bir kalıptan geçirilerek kesit şekli elde edilir ve istenilen boylarda kesilir. Soğuk veya ısıtılmış seramik karışımları ile işlem yapılır. • DÜŞÜK BASINÇ ENJEKSİYON KALIPLAMA : Seramik tozu ile bağlayıcılar ve solventler karışımı hazırlıyoruz ve kolayca preslenip alet boşluğuna zorlayabileceği bir sıcaklığa ısıtıyoruz. Kalıplama döngüsü tamamlandıktan sonra parça çıkarılır ve bağlayıcı kimyasal yakılır. Enjeksiyon kalıplama kullanarak, karmaşık parçaları yüksek hacimlerde ekonomik olarak elde edebiliyoruz. 10 mm kalınlığındaki bir duvarda milimetrenin çok küçük bir kısmı olan delikler mümkündür, başka bir işleme gerekmeden diş açma mümkündür, +/- %0,5 kadar sıkı toleranslar mümkündür ve parçalar işlendiğinde daha da düşük olabilir 0,5 mm'den 12,5 mm'ye kadar et kalınlıkları ve 6,5 mm'den 150 mm'ye kadar et kalınlıkları mümkündür. • YEŞİL İŞLEME : Aynı metal işleme takımlarını kullanarak preslenmiş seramik malzemeleri tebeşir gibi yumuşakken işleyebiliriz. +/- %1 toleranslar mümkündür. Daha iyi toleranslar için elmas taşlama kullanıyoruz. • SİNTERLEME veya PİŞİRME : Sinterleme tam yoğunlaştırmayı mümkün kılar. Yeşil kompakt parçalarda önemli ölçüde büzülme meydana gelir, ancak parçayı ve takımları tasarlarken bu boyutsal değişiklikleri hesaba kattığımız için bu büyük bir sorun değildir. Toz partikülleri birbirine bağlanır ve sıkıştırma işleminin neden olduğu gözeneklilik büyük ölçüde giderilir. • ELMAS TAŞLAMA : Dünyanın en sert malzemesi olan “elmas” seramik gibi sert malzemelerin taşlanmasında kullanılmakta ve hassas parçalar elde edilmektedir. Mikrometre aralığında toleranslar ve çok düzgün yüzeyler elde edilmektedir. Maliyeti nedeniyle, bu tekniği yalnızca gerçekten ihtiyacımız olduğunda değerlendiriyoruz. • HERMETİK DÜZENLEMELER, pratik olarak, arayüzler arasında madde, katı, sıvı veya gaz alışverişine izin vermeyenlerdir. Hermetik sızdırmazlık hava geçirmezdir. Örneğin hermetik elektronik muhafazalar, paketlenmiş bir cihazın hassas iç içeriğini nem, kirletici maddeler veya gazlardan zarar görmeden tutanlardır. Hiçbir şey %100 hermetik değildir, ancak hermetiklikten bahsettiğimizde, pratik anlamda, sızıntı oranı o kadar düşük olduğu ölçüde hermetikliğin olduğunu kastediyoruz, bu yüzden cihazlar normal çevre koşullarında çok uzun süre güvenlidir. Hermetik tertibatlarımız metal, cam ve seramik bileşenler, metal-seramik, seramik-metal-seramik, metal-seramik-metal, metal-metal, metal-cam, metal-cam-metal, cam-metal-cam, cam- metal ve camdan cama ve diğer tüm metal-cam-seramik birleştirme kombinasyonları. Örneğin, seramik bileşenleri, montajdaki diğer bileşenlere güçlü bir şekilde bağlanabilmeleri ve mükemmel sızdırmazlık özelliklerine sahip olabilmeleri için metal kaplayabiliriz. Optik fiberleri veya geçişleri metalle kaplama ve bunları muhafazalara lehimleme veya lehimleme konusunda bilgi birikimine sahibiz, böylece muhafazalara gaz geçişi veya sızıntısı olmaz. Bu nedenle hassas cihazları kapsüllemek ve dış atmosferden korumak için elektronik muhafazaların imalatında kullanılırlar. Mükemmel sızdırmazlık özelliklerinin yanı sıra, ısıl genleşme katsayısı, deformasyon direnci, gaz çıkarmayan yapı, çok uzun ömür, iletken olmayan yapı, ısı yalıtım özellikleri, antistatik yapı gibi diğer özellikler...vb. cam ve seramik malzemeleri belirli uygulamalar için tercih edin. Seramikten metale bağlantı parçaları, hermetik sızdırmazlık, vakumlu geçişler, yüksek ve ultra yüksek vakum ve sıvı kontrol bileşenleri üreten tesisimize ilişkin bilgiler burada bulunabilir:Hermetik Bileşenler Fabrika Broşürü CLICK Product Finder-Locator Service ÖNCEKİ SAYFA
- Tel ve Yay Şekillendirme, Tel Çekme, Tel Şekillendirme, Yay Montajı, Burulma Yayı, Yaprak Yay, Konik Yaylar, Saat Yayları, Sabit ve Değişken Yaylar, Sıkıştırma Yayı
Tel ve Yay Şekillendirme, Fason Yay, Tel Çekme, Tel Şekillendirme, Yay Montajı, Burulma Yayı, Yaprak Yay, Konik Yaylar, Saat Yayları, Sabit ve Değişken Yaylar, Gerilim ve Sıkıştırma Yayı, Helisel Yaylar, Yay Formlama, AGS-TECH Tel ve Yay Şekillendirme Özel teller, tel montajı, istenilen 2D ve 3D şekillerde şekillendirilmiş teller, tel ağlar, ağlar, muhafazalar, sepet, çit, tel yay, yassı yay; burulma, sıkıştırma, germe, yassı yaylar ve daha fazlası. İşlemlerimiz tel ve yay şekillendirme, tel çekme, şekillendirme, bükme, kaynak, lehimleme, lehimleme, delme, dövme, delme, pah kırma, taşlama, diş açma, kaplama, dört kızak, kızak şekillendirme, sarma, sarma, altüst etmedir. için buraya tıklamanızı öneririz. AGS-TECH Inc. Fotoğraflar ve eskizler içeren bu indirilebilir dosya, aşağıda size sunduğumuz bilgileri daha iyi anlamanıza yardımcı olacaktır. • TEL ÇEKME : Çekme kuvvetlerini kullanarak metal stoğu gerdirir ve çapını küçültmek ve uzunluğunu artırmak için bir kalıptan çekeriz. Bazen bir dizi kalıp kullanırız. Her tel ölçüsü için kalıp yapma yeteneğine sahibiz. Yüksek çekme mukavemetli malzeme kullanarak çok ince teller çekiyoruz. Hem soğuk hem de sıcak işlenmiş teller sunuyoruz. • TEL ŞEKİLLENDİRME : Ölçülü bir tel rulosu bükülür ve kullanışlı bir ürün haline getirilir. Otomobil şasesi altında yay olarak kullanılanlar gibi kalın tellerin yanı sıra ince filamentler dahil tüm ölçülerden tel şekillendirme kabiliyetine sahibiz. Tel şekillendirme için kullandığımız ekipmanlar manuel ve CNC tel şekillendiriciler, sarıcılar, elektrikli presler, dörtlü, çoklu sürgülerdir. İşlemlerimiz çekme, bükme, doğrultma, düzleştirme, germe, kesme, yığma, lehimleme ve kaynak ve lehimleme, montaj, sarma, dövme (veya kanatlama), delme, tel diş açma, delme, pah kırma, taşlama, kaplama ve yüzey işlemleridir. Son teknoloji ekipmanımız, her şekilde ve sıkı toleranslarda çok karmaşık tasarımlar geliştirmek için kurulabilir. Telleriniz için çeşitli uç tipleri like küresel, sivri veya pahlı uçlar sunuyoruz. Tel şekillendirme projelerimizin çoğu, minimum ila sıfır takım maliyetine sahiptir. Numune geri dönüş süreleri genellikle günlerdir. Tel formlarının tasarımında/yapılandırılmasında değişiklikler çok hızlı bir şekilde yapılabilir. • YAY FORMLAMA : AGS-TECH, aşağıdakiler dahil olmak üzere çok çeşitli yaylar üretmektedir: -Burulma / Çift Burulma Yayı -Gerilim / Sıkıştırma Yayı -Sabit / Değişken Yay -Bobin ve Helisel Yay -Düz ve Yaprak Yay -Denge Yayı -Belleville Yıkayıcı -Olumsuz Yay -Aşamalı Hız Bobin Yayı -Dalga Yayı -Volüt Yay -Konik Yaylar -Yaylı Yüzükler -Saat Yayları -Klipler Yayları çeşitli malzemelerden üretiyoruz ve uygulamanıza göre size rehberlik edebiliriz. En yaygın malzemeler paslanmaz çelik, krom silikon, yüksek karbonlu çelik, yağla temperlenmiş düşük karbonlu, krom vanadyum, fosfor bronz, titanyum, berilyum bakır alaşımı, yüksek sıcaklık seramiktir. Yay üretiminde CNC sarma, soğuk sarma, sıcak sarma, sertleştirme, bitirme gibi çeşitli teknikler kullanıyoruz. Yukarıda tel şekillendirme altında bahsedilen diğer teknikler de yay üretim operasyonlarımızda yaygındır. • TEL VE YAY BİTİRME HİZMETLERİ : Tercih ve ihtiyaçlarınıza göre ürünlerinizi birçok şekilde bitirebiliriz. Sunduğumuz bazı yaygın işlemler şunlardır: boyama, toz kaplama, kaplama, vinil daldırma, anotlama, stres giderme, ısıl işlem, bilyalı dövme, tambur, kromat, electroless nikel, pasivasyon, fırınlanmış emaye, plastik kaplama , plazma temizleme. CLICK Product Finder-Locator Service ÖNCEKİ SAYFA
- Metal Dövme ve Toz Metalurjisi, Kalıp Dövme, Sıcak Dövme, Soğuk Dövme, Sinterleme, Presleme, Hobbing, Izostatik Presleme
Metal Dövme ve Toz Metalurjisi, Kalıp Dövme, Sıcak Dövme, Soğuk Dövme, Sinterleme, Presleme, Hobbing, Izostatik Presleme, Metal Enjeksiyon Kalıplama, Net Şekle Yakın İmalat, Swaging, Savurma, Metal Hobbing, Azdırma Işlemi, Perçinleme, Darplama, AGS-TECH Inc. Metal Dövme ve Toz Metalurjisi Sunduğumuz METAL DÖVME prosesleri sıcak ve soğuk kalıp, açık kalıp ve kapalı kalıp, ölçü kalıbı ve alevsiz dövme, cogging, dolgu, kenar ve hassas dövme, net şekle yakın, başlık , dövme, üzgün dövme, metal azdırma, pres & rulo & radyal & orbital & halka & izotermal dövme, basma, perçinleme, metal bilye dövme, metal delme, boyutlandırma, yüksek enerji oranlı dövme. TOZ METALURJİSİ ve TOZ İŞLEME tekniklerimiz, toz presleme ve sinterleme, emprenye etme, sızma, sıcak ve soğuk izostatik presleme, metal enjeksiyon kalıplama, rulo sıkıştırma, toz haddeleme, toz ekstrüzyon, gevşek sinterleme, kıvılcım sinterleme, sıcak preslemedir. için buraya tıklamanızı öneririz. AGS-TECH Inc.'den Dövme İşlemlerine İlişkin Şematik Çizimlerimizi İNDİRİN. AGS-TECH Inc.'den Toz Metalurjisi Proseslerinin Şematik Çizimlerini İNDİRİN. Fotoğraflar ve eskizler içeren bu indirilebilir dosyalar, aşağıda size sunduğumuz bilgileri daha iyi anlamanıza yardımcı olacaktır. Metal dövmede basma kuvvetleri uygulanarak malzeme deforme edilerek istenilen şekil elde edilir. Endüstride en yaygın dövme malzemeler demir ve çeliktir, ancak alüminyum, bakır, titanyum, magnezyum gibi çok sayıda diğerleri de yaygın olarak dövülür. Dövme metal parçalar, sızdırmaz çatlaklara ve kapalı boş alanlara ek olarak geliştirilmiş tane yapılarına sahiptir, bu nedenle bu işlemle elde edilen parçaların mukavemeti daha yüksektir. Dövme, döküm veya işleme ile yapılan parçalardan ağırlıkları açısından önemli ölçüde daha güçlü olan olan parçalar üretir. Dövme parçalar, metalin son şeklini alması sağlanarak şekillendirildiğinden, metal, parçaların üstün mukavemetini hesaba katan yönlü bir damar yapısı alır. Başka bir deyişle, dövme işlemi ile elde edilen parçalar, basit döküm veya işlenmiş parçalara göre daha iyi mekanik özellikler ortaya koymaktadır. Metal dövme parçaların ağırlığı, küçük hafif parçalardan yüz binlerce pound'a kadar değişebilir. Otomotiv parçaları, dişliler, ataşmanlar, el aletleri, türbin milleri, motosiklet dişlileri gibi parçalara yüksek gerilimlerin uygulandığı mekanik olarak zorlu uygulamalar için dövme parçalar üretiyoruz. Takım ve kurulum maliyetleri nispeten yüksek olduğundan, bu üretim sürecini yalnızca yüksek hacimli üretim ve havacılık iniş takımı gibi düşük hacimli ancak yüksek değerli kritik bileşenler için öneriyoruz. Takım maliyetinin yanı sıra, büyük miktardaki dövme parçalar için üretim sağlama süreleri, bazı basit işlenmiş parçalara kıyasla daha uzun olabilir, ancak teknik, cıvata, somun, özel uygulama gibi olağanüstü güç gerektiren parçalar için çok önemlidir. bağlantı elemanları, otomotiv, forklift, vinç parçaları. • SICAK KALIP ve SOĞUK KALIP DÖVME : Sıcak kalıp dövme, adından da anlaşılacağı gibi yüksek sıcaklıklarda yapılır, bu nedenle sünekliği yüksektir ve malzeme mukavemeti düşüktür. Bu, kolay deformasyon ve dövme işlemini kolaylaştırır. Aksine, soğuk kalıpta dövme daha düşük sıcaklıklarda gerçekleştirilir ve daha yüksek kuvvetler gerektirir, bu da gerinim sertleşmesi, daha iyi yüzey kalitesi ve üretilen parçaların doğruluğu ile sonuçlanır. • AÇIK KALIP ve GÖSTERİM DÖVME : Açık kalıp dövmede, kalıplar sıkıştırılmakta olan malzemeyi kısıtlamazken, baskı kalıbı dövmesinde kalıpların içindeki boşluklar, istenilen şekle getirilirken malzeme akışını kısıtlar. UPSET DÖVME veya aslında aynı olmayan ancak çok benzer bir süreç olan UPSETTING olarak da adlandırılan iş parçasının iki düz kalıp arasına sıkıştırıldığı ve bir sıkıştırma kuvvetinin yüksekliğini azalttığı bir açık kalıp işlemidir. Yükseklik, azaldıkça, iş parçası genişliği artar. BAŞLANGIÇ, bir yığma dövme işlemi, sonunda yığılmış ve kesiti yerel olarak arttırılmış silindirik bir stoğu içerir. Başlıkta, stok kalıptan beslenir, dövülür ve daha sonra boyuna kesilir. Operasyon, hızlı bir şekilde yüksek miktarlarda bağlantı elemanı üretebilir. Malzemenin güçlendirilmesi gereken çivi uçlarının, vida uçlarının, somun ve civataların yapımında kullanıldığı için çoğunlukla soğuk bir işlemdir. Başka bir açık kalıp işlemi, iş parçasının bir dizi adımda dövüldüğü, her adımın malzemenin sıkıştırılması ve ardından açık kalıbın iş parçasının uzunluğu boyunca hareketi ile sonuçlandığı COGGING'dir. Her adımda kalınlık azaltılır ve uzunluk az miktarda artırılır. Süreç, kalemini küçük adımlarla ısıran gergin bir öğrenciye benziyor. FULLERING adı verilen bir süreç, diğer metal dövme işlemleri gerçekleşmeden önce malzemeyi iş parçasına dağıtmak için genellikle daha erken bir adım olarak uyguladığımız başka bir açık kalıp dövme yöntemidir. İş parçası birkaç forging operasyonu gerektirdiğinde kullanırız. Operasyonda dışbükey yüzeyli kalıp deforme olur ve her iki tarafa metal akışına neden olur. Öte yandan dolgu işlemine benzer bir işlem olan KENARLAMA, iş parçasını deforme etmek için içbükey yüzeylere sahip açık kalıbı içerir. Kenar işleme ayrıca sonraki dövme işlemleri için bir hazırlık sürecidir ve malzemenin her iki taraftan merkezdeki bir alana akışını sağlar. IMPRESSION KALIP DÖVME veya KAPALI DÖVME olarak da adlandırıldığı üzere malzemeyi sıkıştıran ve akışını kendi içinde sınırlayan bir kalıp/kalıp kullanır. Kalıp kapanır ve malzeme kalıp/kalıp boşluğunun şeklini alır. HASSAS DÖVME, özel ekipman ve kalıp gerektiren bir işlemdir ve hiç veya çok az flaşlı parçalar üretir. Başka bir deyişle, parçalar nihai boyutlara yakın olacaktır. Bu işlemde, iyi kontrol edilen miktarda malzeme dikkatli bir şekilde kalıba yerleştirilir ve kalıba yerleştirilir. Bu yöntemi, ince kesitleri, küçük toleransları ve draft açıları olan karmaşık şekiller için ve miktarların kalıp ve ekipman maliyetlerini haklı çıkaracak kadar büyük olduğu durumlarda uyguluyoruz. • FLAŞSIZ DÖVME : İş parçası, boşluktan hiçbir malzeme akıp flaş oluşturmayacak şekilde kalıba yerleştirilir. Bu nedenle istenmeyen flaş kırpmaya gerek yoktur. Hassas bir dövme işlemidir ve bu nedenle kullanılan malzeme miktarının yakından kontrol edilmesini gerektirir. • METAL SWAGING veya RADYAL DÖVME : Bir iş parçasının çevresi boyunca kalıpla dövülür ve dövülür. İç iş parçası geometrisini oluşturmak için bir mandrel de kullanılabilir. Dövme işleminde iş parçası tipik olarak saniyede birkaç vuruş alır. Dövme ile üretilen tipik ürünler sivri uçlu aletler, konik çubuklar, tornavidalardır. • METAL DELME : Parça imalatında ek bir işlem olarak bu işlemi sıklıkla kullanıyoruz. İş parçası yüzeyinde delme işlemi ile kırılmadan bir delik veya boşluk oluşturulur. Lütfen delmenin, açık delik ile sonuçlanan delme işleminden farklı olduğunu unutmayın. • HOBBING : İstenilen geometride bir zımba iş parçasına bastırılır ve istenilen şekle sahip bir boşluk oluşturulur. Bu zımbaya HOB diyoruz. İşlem yüksek basınçlar içerir ve soğukta gerçekleştirilir. Sonuç olarak malzeme soğuk işlenir ve gerinimle sertleştirilir. Bu nedenle bu proses, diğer imalat prosesleri için kalıp, kalıp ve oyukların imalatı için çok uygundur. Ocak üretildikten sonra, tek tek işlemeye gerek kalmadan birçok özdeş boşluk kolayca üretilebilir. • RULO DÖVME veya RULO ŞEKİLLENDİRME : Metal parçaya şekil vermek için karşılıklı iki merdane kullanılır. İş parçası merdanelere beslenir, merdaneler döner ve işi boşluğa çeker, iş daha sonra merdanelerin yivli kısmından beslenir ve sıkıştırma kuvvetleri malzemeye istenilen şekli verir. Bu bir haddeleme işlemi değil, bir dövme işlemidir, çünkü sürekli bir işlemden ziyade ayrı bir işlemdir. Rulo yuvalarındaki geometri, malzemeyi gerekli şekil ve geometriye dönüştürür. Sıcak yapılır. Dövme işlemi olması nedeniyle üstün mekanik özelliklere sahip parçalar üretir ve bu nedenle zorlu çalışma ortamlarında olağanüstü dayanıklılığa sahip olması gereken şaft gibi otomotiv parçalarının üretiminde kullanırız. • Yörüngesel Dövme : İş parçası, bir dövme kalıbı boşluğuna konur ve eğik bir eksen üzerinde dönerken yörünge yolunda hareket eden bir üst kalıp tarafından dövülür. Her devirde, üst kalıp tüm iş parçasına baskı kuvvetleri uygulayarak tamamlar. Bu devirler birkaç kez tekrarlanarak yeterli dövme yapılır. Bu üretim tekniğinin avantajları, düşük gürültülü çalışması ve gereken daha düşük kuvvetlerdir. Başka bir deyişle, iş parçasının kalıpla temas halinde olan bir bölümüne büyük basınçlar uygulamak için ağır bir kalıbı bir eksen etrafında küçük kuvvetlerle döndürebilirsiniz. Disk veya konik şekilli parçalar bazen bu işlem için uygundur. • YÜZÜK DÖVME : Sıklıkla dikişsiz yüzük imalatında kullanıyoruz. Stok boyuna kesilir, alt üst edilir ve daha sonra merkezi bir delik oluşturmak için sonuna kadar delinir. Daha sonra bir mandrel üzerine konur ve halka istenen boyutlar elde edilene kadar yavaşça döndürülürken bir dövme kalıbı yukarıdan çekiçler. • Perçinleme : Parçaları birleştirmek için yaygın bir işlem, parçalar boyunca önceden yapılmış deliklere düz bir metal parçanın yerleştirilmesiyle başlar. Daha sonra metal parçanın iki ucu, bir üst ve alt kalıp arasındaki bağlantı sıkılarak dövülür. • PASLAMA : Kısa bir mesafe boyunca büyük kuvvetler uygulayan mekanik pres tarafından gerçekleştirilen bir diğer popüler işlemdir. Madeni paraların yüzeylerine dövülen ince detaylardan “sikkeleme” adı gelir. Çoğunlukla bir ürün için, bu detayları iş parçasına aktaran kalıbın uyguladığı büyük kuvvet sonucunda yüzeylerde ince detayların elde edildiği bir bitirme işlemidir. • METAL KÜRESEL DÖVME : Rulman gibi ürünler yüksek kaliteli, hassas üretilmiş metal bilyalar gerektirir. SKEW ROLLING adı verilen bir teknikte, stok sürekli olarak rulolara beslenirken sürekli dönen iki karşıt rulo kullanıyoruz. İki rulonun bir ucundan ürün olarak metal küreler çıkar. Metal bilye dövme için ikinci bir yöntem, aralarına yerleştirilen malzeme stokunu kalıp boşluğunun küresel şeklini alarak sıkıştıran kalıp kullanmaktır. Üretilen bilyeler çoğu zaman yüksek kaliteli bir ürün haline gelebilmek için bitirme ve cilalama gibi bazı ek adımlar gerektirir. • İZOTERMAL DÖVME / SICAK KALIPLI DÖVME : Sadece fayda/maliyet değeri haklı çıkarıldığında gerçekleştirilen pahalı bir işlemdir. Kalıbın iş parçasıyla yaklaşık olarak aynı sıcaklığa ısıtıldığı sıcak bir çalışma süreci. Hem kalıp hem de iş yaklaşık olarak aynı sıcaklıkta olduğundan soğutma olmaz ve metalin akış özellikleri iyileştirilir. İşlem, süper alaşımlar ve düşük dövülebilirliğe sahip malzemeler ve olan malzemeler için uygundur. mekanik özellikler, küçük sıcaklık değişimlerine ve değişikliklere karşı çok hassastır. • METAL EBATLAMA : Soğuk terbiye işlemidir. Malzeme akışı, kuvvetin uygulandığı yön dışında tüm yönlerde kısıtlanmaz. Sonuç olarak, çok iyi yüzey kalitesi ve doğru boyutlar elde edilir. • YÜKSEK ENERJİ HIZLI DÖVME : Bu teknik, bir yakıt-hava karışımı bir buji tarafından ateşlendiğinde hızla itilen bir piston koluna bağlı bir üst kalıp içerir. Bir araba motorundaki pistonların çalışmasına benzer. Kalıp, iş parçasına çok hızlı çarpar ve geri basınç sayesinde çok hızlı bir şekilde orijinal konumuna geri döner. İş birkaç milisaniye içinde dövülür ve bu nedenle işin soğuması için zaman yoktur. Bu, sıcaklığa çok duyarlı mekanik özelliklere sahip, dövülmesi zor parçalar için kullanışlıdır. Başka bir deyişle, süreç o kadar hızlıdır ki, parça boyunca sabit sıcaklık altında oluşturulur ve kalıp/iş parçası arayüzlerinde sıcaklık gradyanları olmaz. • KALIP DÖVME'de metal, içinde kalıp adı verilen özel şekillere sahip iki uyumlu çelik blok arasında dövülür. Metal, kalıplar arasına dövüldüğünde, kalıptaki şekillerle aynı şekli alır. Son şekline gelince soğumaya alınır. Bu işlem, kesin bir şekle sahip güçlü parçalar üretir, ancak özel kalıplar için daha büyük bir yatırım gerektirir. Üzgün dövme, bir metal parçasını düzleştirerek çapını arttırır. Genellikle küçük parçalar yapmak, özellikle civata ve çivi gibi bağlantı elemanlarında başlık oluşturmak için kullanılır. • TOZ METALURJİSİ / TOZ İŞLEME : Adından da anlaşılacağı gibi, tozlardan belirli geometri ve şekillerde katı parçaların yapılmasına yönelik imalat işlemlerini içerir. Bu amaçla metal tozları kullanılıyorsa toz metalurjisi, metal olmayan tozlar kullanılıyorsa toz işleme alanıdır. Tozlardan presleme ve sinterleme ile katı parçalar üretilir. TOZ PRESLEME, tozları istenilen şekillerde sıkıştırmak için kullanılır. İlk olarak, birincil malzeme fiziksel olarak toz haline getirilerek birçok küçük ayrı parçaya bölünür. Toz karışımı kalıba doldurulur ve bir zımba toza doğru hareket eder ve istenen şekle sıkıştırır. Çoğunlukla oda sıcaklığında gerçekleştirilen toz presleme ile katı bir parça elde edilir ve buna yeşil kompakt denir. Sıkıştırılabilirliği artırmak için bağlayıcılar ve yağlayıcılar yaygın olarak kullanılır. Birkaç bin ton kapasiteli hidrolik presler ile toz pres şekillendirme yapabilmekteyiz. Ayrıca karşıt üst ve alt zımbalara sahip çift etkili preslerimiz ve oldukça karmaşık parça geometrileri için çoklu hareketli preslerimiz var. Birçok toz metalurjisi / toz işleme tesisi için önemli bir zorluk olan tekdüzelik, uzun yıllardır bu tür parçaların özel üretimindeki geniş deneyimimiz nedeniyle AGS-TECH için büyük bir sorun değil. Tekdüzeliğin zorluk teşkil ettiği daha kalın parçalarda bile başardık. Projenizi taahhüt edersek, parçalarınızı yaparız. Herhangi bir potansiyel risk görürsek sizi bilgilendireceğiz in avans. İkinci aşama olan TOZ SİNTERLEME, preslenen parçadaki toz parçacıklarının birbirine bağlanabilmesi için sıcaklığın belirli bir dereceye yükseltilmesi ve sıcaklığın belirli bir süre bu seviyede tutulmasını içerir. Bu, çok daha güçlü bağlar ve iş parçasının güçlendirilmesi ile sonuçlanır. Sinterleme, tozun erime sıcaklığına yakın bir yerde gerçekleşir. Sinterleme sırasında büzülme meydana gelecek, malzeme mukavemeti, yoğunluğu, sünekliği, ısıl iletkenliği, elektrik iletkenliği artar. Sinterleme için toplu ve sürekli fırınlarımız var. Yeteneklerimizden biri, ürettiğimiz parçaların gözeneklilik seviyesini ayarlamaktır. Örneğin parçaları bir dereceye kadar gözenekli tutarak metal filtreler üretebiliyoruz. emprenye adı verilen bir teknik kullanarak metaldeki gözenekleri yağ gibi bir sıvı ile dolduruyoruz. Örneğin, kendi kendini yağlayan yağ emdirilmiş yataklar üretiyoruz. INFILTRATION işleminde, bir metalin gözeneklerini, temel malzemeden daha düşük erime noktasına sahip başka bir metalle doldururuz. Karışım, iki metalin erime sıcaklıkları arasındaki bir sıcaklığa ısıtılır. Sonuç olarak, bazı özel özellikler elde edilebilir. Ayrıca, özel özelliklerin veya özelliklerin elde edilmesi gerektiğinde veya parçanın daha az işlem adımıyla üretilebileceği durumlarda, tozla üretilen parçalar üzerinde işleme ve dövme gibi ikincil işlemleri de sıklıkla gerçekleştiriyoruz. İZOSTATİK PRESLEME : Bu işlemde parçayı sıkıştırmak için akışkan basıncı kullanılır. Metal tozları, sızdırmaz şekilde kapatılmış esnek bir kaptan yapılmış bir kalıba yerleştirilir. İzostatik preslemede, geleneksel preslemede görülen eksenel basıncın aksine, her taraftan basınç uygulanır. İzostatik preslemenin avantajları, özellikle daha büyük veya daha kalın parçalar için parça içinde homojen yoğunluk, üstün özelliklerdir. Dezavantajı, uzun çevrim süreleri ve nispeten düşük geometrik doğruluklardır. SOĞUK İZOSTATİK PRESLEME oda sıcaklığında gerçekleştirilir ve esnek kalıp kauçuk, PVC veya üretan veya benzeri malzemelerden yapılır. Basınçlandırma ve sıkıştırma için kullanılan sıvı yağ veya sudur. Bunu yeşil kompaktın geleneksel sinterlenmesi izler. SICAK İZOSTATİK PRES ise yüksek sıcaklıklarda gerçekleştirilir ve kalıp malzemesi, sıcaklıklara dayanıklı, yeterince yüksek erime noktasına sahip sac veya seramiktir. Basınçlandırma sıvısı genellikle inert bir gazdır. Presleme ve sinterleme işlemleri tek adımda gerçekleştirilir. Gözeneklilik neredeyse tamamen ortadan kaldırılır, uniform grain yapısı elde edilir. Sıcak izostatik preslemenin avantajı, döküm ve dövme için uygun olmayan malzemeleri kullanılabilir hale getirirken, döküm ve dövme ile karşılaştırılabilir parçalar üretebilmesidir. Sıcak izostatik preslemenin dezavantajı, yüksek çevrim süresi ve dolayısıyla maliyetidir. Düşük hacimli kritik parçalar için uygundur. METAL ENJEKSİYON KALIPLAMA : İnce cidarlı ve detaylı geometrilere sahip karmaşık parçaların üretimi için çok uygun bir prosestir. Daha küçük parçalar için en uygunudur. Tozlar ve polimer bağlayıcı karıştırılır, ısıtılır ve bir kalıba enjekte edilir. Polimer bağlayıcı, toz parçacıklarının yüzeylerini kaplar. Kalıplamadan sonra, bağlayıcı, bir çözücü kullanılarak çözünmüş maddenin düşük sıcaklıkta ısıtılmasıyla çıkarılır. RULO SIKIŞTIRMA / TOZ HADDELEME : Tozlar, sürekli şerit veya levha üretmek için kullanılır. Toz, bir besleyiciden beslenir ve iki döner rulo ile tabaka veya şeritler halinde sıkıştırılır. İşlem soğuk yapılır. Levha bir sinterleme fırınına taşınır. Sinterleme işlemi ikinci kez tekrarlanabilir. TOZ EKSTRÜZYONU : Büyük boy-çap oranlarına sahip parçalar, ince bir sac metal kabın toz ile ekstrüde edilmesiyle üretilir. GEVŞEK SİNTERLEME : Adından da anlaşılacağı gibi metal filtreler gibi çok gözenekli parçaların üretimine uygun, basınçsız bir sıkıştırma ve sinterleme yöntemidir. Toz, sıkıştırmadan kalıp boşluğuna beslenir. GEVŞEK SİNTERLEME : Adından da anlaşılacağı gibi metal filtreler gibi çok gözenekli parçaların üretimine uygun, basınçsız bir sıkıştırma ve sinterleme yöntemidir. Toz, sıkıştırmadan kalıp boşluğuna beslenir. Kıvılcım Sinterleme : Toz, karşılıklı iki zımba ile kalıpta sıkıştırılır ve zımbaya yüksek güçlü bir elektrik akımı uygulanır ve aralarına sıkıştırılan sıkıştırılmış tozdan geçer. Yüksek akım, toz partiküllerinden yüzey filmlerini yakar ve üretilen ısı ile onları sinterler. İşlem hızlıdır çünkü ısı dışarıdan uygulanmaz, bunun yerine kalıp içinden üretilir. SICAK PRESLEME : Tozlar, yüksek sıcaklıklara dayanabilecek bir kalıpta tek adımda preslenir ve sinterlenir. Kalıp sıkıştırılırken, ona toz ısısı uygulanır. Bu yöntemle elde edilen iyi doğruluklar ve mekanik özellikler, onu çekici bir seçenek haline getirir. Grafit gibi kalıp malzemeleri kullanılarak refrakter metaller bile işlenebilir. CLICK Product Finder-Locator Service ÖNCEKİ MENÜ
- Sac Metal Şekillendirme, Damgalama, Progresif Kalıplar, Derin Çekme, CNC, Abkant Press, Hidroformasyon, Tek Vuruşlu Kalıp
Sac Metal Şekillendirme, Damgalama, Punching, Derin Çekme, CNC, Abkant Press, Hidroformasyon, Kombine Sac Kesme Bükme İşlemleri, Tek Vuruşlu Kalıplar, Progresif Kalıplar, Eğirme Damgalama ve Sac Metal Parça İmalatı Sac metal damgalama, şekillendirme, biçimlendirme, bükme, delme, kesme, dilme, delme, çentik açma, diş açma, tıraş, pres işleme, fabrikasyon, tek zımba / tek vuruşlu kalıpların yanı sıra progresif kalıplar ve eğirme, kauçuk şekillendirme ve hidroforming; su jeti, plazma, lazer, testere, alev kullanarak sac kesme; kaynak kullanarak sac montajı, nokta kaynağı; sac boru şişkinliği ve bükülmesi; daldırma veya sprey boyama, elektrostatik toz kaplama, anotlama, kaplama, püskürtme ve daha fazlasını içeren sac yüzey bitirme. Hizmetlerimiz, hızlı sac metal prototiplemeden yüksek hacimli üretime kadar uzanmaktadır. için buraya tıklamanızı öneririz.AGS-TECH A.Ş. Bu, aşağıda size sağladığımız bilgileri daha iyi anlamanıza yardımcı olacaktır. • SAC KESME : KESİMLER ve PARÇALAR sunuyoruz. Kesikler sacı bir seferde bir yol üzerinde keser ve temelde malzeme israfı olmaz, oysa bölmeler ile şekil tam olarak yerleştirilemez ve bu nedenle belirli miktarda malzeme israf edilir. En popüler süreçlerimizden biri, sacdan yuvarlak veya başka bir şekle sahip bir malzeme parçasının kesildiği PUNCHING'dir. Kesilen parça çöp. Zımbalamanın başka bir versiyonu, dikdörtgen veya uzun deliklerin delindiği SLOTTING'dir. BLANKING ise zımbalama ile aynı işlemdir, kesilen parçanın farkı ile iştir ve tutulur. Körlemenin üstün bir versiyonu olan FINE BLANKING, yakın toleranslarda ve düz pürüzsüz kenarlarda kesimler oluşturur ve iş parçasının mükemmelliği için ikincil işlemler gerektirmez. Sıklıkla kullandığımız bir diğer işlem ise, sacın iki zıt dairesel bıçak tarafından düz veya kavisli bir yolda kesildiği bir kesme işlemi olan DİLME'dir. Konserve açacağı, dilme işleminin basit bir örneğidir. Bizim için bir başka popüler process, sac levhada belirli bir desende yuvarlak veya başka şekillerde birçok deliğin delindiği PERFORASYON'dur. Delikli bir ürün için tipik bir örnek, sıvılar için birçok deliği olan metal filtrelerdir. Diğer bir sac kesme işlemi olan KIRMIZI işleminde, bir iş parçasından malzemeyi kenardan veya başka bir yerden başlayarak istenen şekil elde edilene kadar içe doğru kesiyoruz. İstenilen kontur elde edilene kadar her işlemin başka bir parçayı çıkardığı aşamalı bir işlemdir. Küçük üretim çalışmaları için bazen daha büyük ve daha karmaşık bir kesim yapmak için üst üste binen birçok hızlı zımbadan oluşan NIBBLING adı verilen nispeten daha yavaş bir işlem kullanıyoruz. PROGRESSİF KESİM'de, tek bir kesim veya belirli bir geometri elde etmek için bir dizi farklı işlem kullanıyoruz. Son olarak, ikincil bir işlem olan TIRAŞLAMA, halihazırda yapılmış olan kesimlerin kenarlarını iyileştirmemize yardımcı olur. Sac işlerinde talaşları, pürüzlü kenarları kesmek için kullanılır. • LEVHA BÜKME : Kesmenin yanı sıra bükme de olmazsa olmaz bir işlemdir ve onsuz çoğu ürünü üretemeyiz. Çoğunlukla soğuk çalışma işlemidir, ancak bazen sıcak veya sıcakken de yapılır. Bu işlem için çoğu zaman kalıp ve pres kullanıyoruz. PROGRESİF BÜKME'de, tek bir büküm veya belirli bir geometri elde etmek için bir dizi farklı zımba ve kalıp işlemi kullanıyoruz. AGS-TECH çeşitli bükme işlemleri kullanır ve iş parçası malzemesine, boyutuna, kalınlığına, istenilen bükme boyutuna, yarıçapa, eğrilik ve bükme açısına, bükme konumuna, işletme ekonomisine, üretilecek miktarlara bağlı olarak seçim yapar… vb. V şekilli bir zımbanın sac metali V şekilli kalıba zorladığı ve büktüğü V-BENDING kullanıyoruz. 90 derece dahil olmak üzere hem çok dar hem de geniş açılar ve aradaki açılar için iyidir. Silme kalıplarını kullanarak KENAR BÜKME işlemi yapıyoruz. Ekipmanlarımız, 90 dereceden daha büyük açılar elde etmemizi sağlıyor. Kenar bükmede iş parçası bir baskı yastığı ve kalıp arasına sıkıştırılır, bükme alanı kalıp kenarında bulunur ve iş parçasının geri kalanı space bir konsol kirişi gibi tutulur. Zımba konsol kısmına etki ettiğinde, kalıbın kenarı üzerinde bükülür. FLANŞLAMA, 90 derecelik bir açıyla sonuçlanan bir kenar bükme işlemidir. Operasyonun temel amacı, keskin kenarların ortadan kaldırılması ve parçaların birleştirilmesini kolaylaştıracak geometrik yüzeyler elde edilmesidir. Bir diğer yaygın kenar bükme işlemi olan BEADING, bir parçanın kenarı üzerinde bir kıvrılma oluşturur. HEMMING ise, levhanın tamamen kendi üzerine eğilmiş bir kenarı ile sonuçlanır. DİKİŞTE iki parçanın kenarları birbiri üzerine bükülür ve birleştirilir. ÇİFT DİKİŞ ise su ve hava geçirmez sac birleştirmeler sağlar. Kenar bükmeye benzer şekilde, DÖNER BÜKME adı verilen bir işlem, istenen açıda kesilmiş ve zımba görevi gören bir silindiri dağıtır. Kuvvet zımbaya iletilirken iş parçası ile birlikte kapanır. Silindirin oluğu, konsol kısmına istenen açıyı verir. Oluk, 90 dereceden daha küçük veya daha büyük bir açıya sahip olabilir. HAVA BÜKME'de açılı bir oluğa sahip olmak için alt kalıba ihtiyacımız yoktur. Sac, karşılıklı kenarlarda ve belirli bir mesafede iki yüzey tarafından desteklenir. Zımba daha sonra doğru yere bir kuvvet uygular ve iş parçasını büker. KANAL BÜKME, kanal şeklinde bir zımba ve kalıp kullanılarak gerçekleştirilir ve U-BEND, U şeklinde bir zımba ile elde edilir. OFSET BÜKME, sac üzerinde ofsetler üretir. Büyük metal plakaların kalın işlenmesi ve bükülmesi için iyi bir teknik olan ROLL BENDING, plakaları istenen eğriliklere beslemek ve bükmek için üç rulo kullanır. Rulolar, işin istenilen bükümü elde edilecek şekilde dizilir. İstenilen sonucu elde etmek için rulolar arasındaki mesafe ve açı kontrol edilir. Hareketli bir rulo, eğriliği kontrol etmeyi mümkün kılar. TÜP ŞEKİLLENDİRME, çoklu kalıpları içeren bir başka popüler sac bükme işlemidir. Tüpler birden fazla işlemden sonra elde edilir. OLUKLU büküm işlemleri de yapılmaktadır. Temel olarak, tüm bir sac parçası boyunca düzenli aralıklarla simetrik bükülmedir. Oluklu mukavva için çeşitli şekiller kullanılabilir. Oluklu sac daha sert ve bükülmeye karşı daha iyi dirence sahiptir ve bu nedenle inşaat sektöründe uygulamaları vardır. LEVHA METAL RULO ŞEKİLLENDİRME, bir sürekli manufacturing işlemi, belirli bir geometrinin enine kesitlerini rulolar kullanarak bükmek için kullanılır ve iş, son rulo işi tamamlayacak şekilde sıralı adımlarla bükülür. Bazı durumlarda tek bir rulo ve bazı durumlarda bir dizi rulo kullanılır. • KOMBİNE SAC KESME BÜKME İŞLEMLERİ : Aynı anda hem kesen hem de büken işlemlerdir. PIERCING'de sivri uçlu bir zımba kullanılarak bir delik oluşturulur. Zımba levhadaki deliği genişletirken, malzeme aynı anda delik için bir iç flanşa doğru bükülür. Elde edilen flanşın önemli işlevleri olabilir. Öte yandan LANCING işlemi, yükseltilmiş bir geometri oluşturmak için levhayı keser ve büker. • METAL BORU ÇIKARTMA VE BÜKME : ÇÖKME'de içi boş bir borunun bazı iç kısımlarına basınç uygulanır ve borunun dışa doğru şişmesine neden olur. Tüp bir kalıbın içinde olduğundan, şişkinlik geometrisi kalıbın şekli ile kontrol edilir. STRETCH BENDING'de, bir metal boru, borunun eksenine paralel kuvvetler ve boruyu bir form bloğu üzerine çekmek için bükme kuvvetleri kullanılarak gerilir. DRAW BENDING'de boruyu ucuna yakın bir yerde, dönerken boruyu büken dönen bir form bloğuna kelepçeliyoruz. Son olarak, SIKIŞTIRMA BÜKME'de tüp, sabit bir kalıp bloğuna kuvvetle tutulur ve bir kalıp, onu kalıp bloğu üzerinde büker. • DERİN ÇEKİM : En popüler operasyonlarımızdan birinde zımba, uygun kalıp ve boş tutucu kullanılmaktadır. Sac levha, kalıp açıklığının üzerine yerleştirilir ve zımba, boş tutucu tarafından tutulan boşluğa doğru hareket eder. Temas ettiklerinde, zımba, ürünü oluşturmak için sac metali kalıp boşluğuna zorlar. Derin çekme işlemi kesmeye benzer, ancak zımba ile kalıp arasındaki boşluk sacın kesilmesini engeller. Sacın derin çekilmesini ve kesilmemesini sağlayan bir diğer faktör ise, kalıp ve zımba üzerindeki yuvarlatılmış köşelerdir, bu da kesme ve kesmeyi engeller. Daha büyük bir derin çekme büyüklüğünü elde etmek için, zaten bir derin çekme işleminden geçmiş bir parça üzerinde müteakip bir derin çekmenin gerçekleştiği bir YENİDEN ÇİZİM işlemi uygulanmaktadır. TERS ÇİZİMDE, derin çekilen kısım ters çevrilir ve zıt yönde çekilir. Derin çekme, kubbeli, konik veya kademeli kaplar gibi düzensiz şekilli nesneler sağlayabilir, GÖRÜNTÜLEME'de sac metali bir tasarım veya yazı ile etkilemek için bir erkek ve dişi kalıp çifti kullanırız. • SPINNING : Düz veya önceden oluşturulmuş bir iş parçasının dönen bir mandrel ve kuyruk stoku arasında tutulduğu ve bir aletin mandrelde kademeli olarak yukarı hareket ederken işe yerel basınç uyguladığı bir işlem. Sonuç olarak iş parçası mandrel üzerine sarılır ve şeklini alır. Bu tekniği, sipariş miktarının küçük olduğu, parçaların büyük olduğu (20 feet çapa kadar) ve benzersiz eğrilere sahip olduğu derin çekme işlemine alternatif olarak kullanıyoruz. Parça başı fiyatlar genellikle daha yüksek olsa da CNC eğirme işlemi için kurulum maliyetleri derin çekme ile karşılaştırıldığında düşüktür. Aksine, derin çekme, kurulum için yüksek bir ilk yatırım gerektirir, ancak yüksek miktarda parça üretildiğinde parça başına maliyetler düşüktür. Bu işlemin başka bir versiyonu, iş parçası içinde metal akışının da olduğu KAYNAKLI SPINNING'dir. İşlem gerçekleştirilirken metal akışı iş parçasının kalınlığını azaltacaktır. Bir diğer ilgili işlem ise silindirik parçalara uygulanan TÜP eğirme işlemidir. Ayrıca bu işlemde iş parçası içinde metal akışı vardır. Böylece kalınlık azalır ve borunun uzunluğu artar. Araç, tüpün içinde veya dışında özellikler oluşturmak için hareket ettirilebilir. • LEVHA KAUÇUK ŞEKİLLENDİRME : Kauçuk veya poliüretan malzeme bir kap kalıba konur ve iş parçası kauçuğun yüzeyine yerleştirilir. Daha sonra iş parçasına bir zımba uygulanır ve onu kauçuğa zorlar. Kauçuğun oluşturduğu basınç düşük olduğu için üretilen parçaların derinliği sınırlıdır. Takım maliyetleri düşük olduğundan, süreç düşük miktarlı üretim için uygundur. • HİDROFORMASYON : Kauçuk şekillendirmeye benzer şekilde, bu işlemde sac levha, bir hazne içinde basınçlı bir sıvıya bir zımba ile preslenir. Sac levha işi, zımba ile kauçuk diyafram arasına sıkıştırılmıştır. Diyafram iş parçasını tamamen çevreler ve sıvının basıncı onu zımba üzerinde oluşturmaya zorlar. Bu teknik ile derin çekme işleminde olduğundan daha derin çok derin çekmeler elde edilebilir. Parçanıza bağlı olarak tek zımbalı kalıpların yanı sıra progresif kalıplar üretiyoruz. Tek vuruşlu damgalama kalıpları, pullar gibi büyük miktarlarda basit sac parçaları hızlı bir şekilde üretmek için uygun maliyetli bir yöntemdir. Daha karmaşık geometriler üretmek için aşamalı kalıplar veya derin çekme tekniği kullanılır. Durumunuza bağlı olarak, sac metal parçalarınızı ucuz, hızlı ve doğru bir şekilde üretmek için su jeti, lazer veya plazma kesim kullanılabilir. Birçok tedarikçinin bu alternatif teknikler hakkında hiçbir fikri yoktur veya buna sahip değildir ve bu nedenle, müşterilerin zamanını ve parasını boşa harcayan uzun ve pahalı kalıplar ve aletler yapma yollarından geçerler. Muhafazalar, elektronik muhafazalar vb. gibi özel yapım sac bileşenlere birkaç gün içinde olduğu kadar hızlı ihtiyacınız varsa, HIZLI LEVHA PROTOTİPLEME hizmetimiz için bizimle iletişime geçin. CLICK Product Finder-Locator Service ÖNCEKİ MENÜ
- Döküm ve Talaşlı İmalat, CNC Üretim, Frezeleme, Tornalama, Isviçre Tipi CNC, Kalıpla Döküm, Harcanan Döküm, Sürekli Döküm
Metal Döküm, Talaşlı İmalat, CNC Üretim, Frezeleme, Tornalama, Isviçre Tipi CNC, Kalıpla Döküm, Harcanan Döküm, Sürekli Döküm, Hassas Döküm, Alaşım Dökümü, Santrifüj Döküm, Kum Döküm Metal ve Alaşım Döküm ve İşleme Özel döküm ve işleme tekniklerimiz, harcanabilir ve tükenmez dökümler, demirli ve demirsiz döküm, kum, kalıp, santrifüj, sürekli, seramik kalıp, revetman, kayıp köpük, net şekle yakın, kalıcı kalıp (yerçekimi döküm), alçıdır. kalıp (alçı döküm) ve kabuk dökümler, konvansiyonel ve CNC ekipmanları kullanılarak frezeleme ve tornalama ile üretilen işlenmiş parçalar, yüksek verimli ucuz küçük hassas parçalar için İsviçre tipi işleme, bağlantı elemanları için vida işleme, geleneksel olmayan işleme. Metallerin ve metal alaşımlarının yanı sıra, bazı durumlarda kalıp imalatının cazip olmadığı veya seçenek olmadığı durumlarda seramik, cam ve plastik bileşenleri de işliyoruz. Polimer malzemelerin işlenmesi, plastiklerin ve kauçuğun yumuşaklıkları, rijit olmamaları vb. nedeniyle sunduğu zorluklar nedeniyle sahip olduğumuz özel deneyim gerektirir. Seramik ve cam işleme için lütfen Konvansiyonel Olmayan İmalat sayfamıza bakın. AGS-TECH Inc. hem hafif hem de ağır dökümler üretir ve tedarik eder. Kazanlar, ısı eşanjörleri, otomobiller, mikro motorlar, rüzgar türbinleri, gıda paketleme ekipmanları ve daha fazlası için metal dökümler ve işlenmiş parçalar tedarik ediyoruz. Daha detaylı teknik bilgi sahibi olmak için buraya tıklamanızı tavsiye ederiz: AGS-TECH A.Ş.'de Talaşlı İmalat ve Metal Döküm İşlemlerinin Şematik Gösterimleri Bu, aşağıda size sağladığımız bilgileri daha iyi anlamanıza yardımcı olacaktır. Sunduğumuz çeşitli tekniklerden bazılarına ayrıntılı olarak bakalım: • HARCANAN KALIBA DÖKÜM : Bu geniş kategori, geçici ve tekrar kullanılamayan kalıpları içeren yöntemleri ifade eder. Örnekler kum, alçı, kabuk, revetman (kayıp mum da denir) ve alçı dökümdür. • KUM DÖKÜM : Kalıp malzemesi olarak kumun kullanıldığı bir işlemdir. Çok eski bir yöntem ve üretilen metal dökümlerin çoğunluğu bu teknikle yapıldığı ölçüde hala çok popüler. Düşük adetli üretimde bile düşük maliyet. Küçük ve büyük parça üretimi için uygundur. Teknik, çok az yatırımla günler veya haftalar içinde parça üretmek için kullanılabilir. Nemli kum, kil, bağlayıcılar veya özel yağlar kullanılarak birbirine yapıştırılır. Kum genellikle kalıp kutularında bulunur ve modellerin etrafındaki kumun sıkıştırılmasıyla boşluk ve geçit sistemi oluşturulur. Süreçler: 1.) Kalıbın yapılması için modelin kuma yerleştirilmesi 2.) Bir yolluk sistemine model ve kumun dahil edilmesi 3.) Modelin kaldırılması 4.) Kalıp boşluğunun erimiş metal ile doldurulması 5.) Metalin soğutulması 6.) Kum kalıbın kırılması ve dökümün çıkarılması • ALÇI KALIP DÖKÜM : Kum döküme benzer şekilde, kalıp malzemesi olarak kum yerine paris alçısı kullanılmaktadır. Kum dökümü gibi kısa üretim süreleri olur ve ucuzdur. İyi boyutsal toleranslar ve yüzey kalitesi. En büyük dezavantajı, yalnızca alüminyum ve çinko gibi düşük erime noktalı metallerle kullanılabilmesidir. • KABUK KALIP DÖKÜM : Kum döküme benzer. Kum döküm işleminde olduğu gibi kumla doldurulmuş şişe yerine sertleştirilmiş kum kabuğu ve termoset reçine bağlayıcı ile elde edilen kalıp boşluğu. olur Kumla dökülmeye uygun hemen hemen her metal, kabuk kalıplama ile dökülebilir. Süreç şu şekilde özetlenebilir: 1.) Kabuk kalıbı imalatı. Kullanılan kum, kum dökümde kullanılan kumla karşılaştırıldığında çok daha küçük tane boyutundadır. İnce kum, termoset reçine ile karıştırılır. Metal desen, kabuğun çıkarılmasını kolaylaştırmak için bir ayırıcı madde ile kaplanmıştır. Daha sonra metal kalıp ısıtılır ve kum karışımı sıcak döküm kalıbının üzerine gözeneklenir veya üflenir. Desenin yüzeyinde ince bir kabuk oluşur. Bu kabuğun kalınlığı, kum reçine karışımının metal desenle temas halinde olduğu sürenin uzunluğu değiştirilerek ayarlanabilir. Gevşek kum daha sonra kalan kabuk kaplı desen ile çıkarılır. 2.) Daha sonra kabuk ve desen bir fırında ısıtılarak kabuğun sertleşmesi sağlanır. Sertleşme tamamlandıktan sonra, kalıp içine yerleştirilmiş pimler kullanılarak kabuk kalıptan çıkarılır. 3.) Bu tür iki kabuk yapıştırılarak veya sıkıştırılarak birleştirilir ve tüm kalıbı oluşturur. Şimdi kabuk kalıp, döküm işlemi sırasında kum veya metal bilye ile desteklendiği bir kaba yerleştirilir. 4.) Artık sıcak metal kabuk kalıba dökülebilir. Kabuk dökümün avantajları, çok iyi yüzey kalitesine sahip ürünler, yüksek boyutsal doğrulukla karmaşık parçalar üretme imkanı, otomatikleştirme işlemi kolay, büyük hacimli üretim için ekonomiktir. Dezavantajları ise, erimiş metalin bağlayıcı kimyasal ile temas ettiğinde oluşan gazlar nedeniyle kalıpların iyi havalandırma gerektirmesi, termoset reçineler ve metal kalıpların pahalı olmasıdır. Metal kalıpların maliyeti nedeniyle, teknik, düşük miktarlı üretim çalışmaları için uygun olmayabilir. • YATIRIM DÖKÜM veya ERİYEN KALIPLA DÖKÜM ( KAYIP MUM DÖKÜM olarak da bilinir ): Ayrıca çok eski bir tekniktir ve birçok metalden, refrakter malzemelerden ve özel yüksek performanslı alaşımlardan yüksek doğruluk, tekrarlanabilirlik, çok yönlülük ve bütünlük ile kaliteli parça üretimi için uygundur. Küçük ve büyük boyutlu parçalar üretilebilir. Diğer yöntemlerden bazılarıyla karşılaştırıldığında pahalı bir süreç, ancak en büyük avantajı, neredeyse net şekle, karmaşık konturlara ve ayrıntılara sahip parçalar üretme olasılığıdır. Bu nedenle, bazı durumlarda yeniden işleme ve işlemenin ortadan kaldırılmasıyla maliyet bir şekilde dengelenir. Farklılıklar olsa da, genel hassas döküm sürecinin bir özeti aşağıdadır: 1.) Balmumu veya plastikten orijinal ana kalıbın oluşturulması. Her döküm, süreçte yok edildiğinden bir kalıba ihtiyaç duyar. Kalıpların üretildiği kalıba da ihtiyaç duyulur ve çoğu zaman kalıp dökülür veya işlenir. Kalıbın açılması gerekmediğinden, karmaşık dökümler elde edilebilir, birçok mum deseni bir ağacın dalları gibi birbirine bağlanabilir ve birlikte dökülebilir, böylece metal veya metal alaşımının tek bir dökümünden birden fazla parçanın üretilmesini sağlar. 2.) Daha sonra, desen, çok ince taneli silika, su, bağlayıcılardan oluşan bir ateşe dayanıklı bulamaç ile daldırılır veya üzerine dökülür. Bu, desenin yüzeyi üzerinde seramik bir tabaka ile sonuçlanır. Desen üzerindeki refrakter kaplama kurumaya ve sertleşmeye bırakılır. Bu adım, hassas döküm adının geldiği yerdir: Refrakter bulamaç, mum kalıbı üzerine yatırılır. 3.) Bu aşamada, sertleşen seramik kalıp ters çevrilir ve mum eriyip kalıptan dökülecek şekilde ısıtılır. Metal döküm için bir boşluk bırakılır. 4.) Mum çıktıktan sonra, seramik kalıp daha da yüksek bir sıcaklığa ısıtılır ve bu da kalıbın güçlenmesine neden olur. 5.) Metal döküm, tüm karmaşık bölümleri dolduran sıcak kalıba dökülür. 6.) Dökümün katılaşmasına izin verilir 7.) Son olarak seramik kalıp kırılır ve üretilen parçalar ağaçtan kesilir. Buraya Tıklayınız: Yatırım Döküm / Eriyen Kalıpla Döküm Tesisi Broşürü için bir link • EVAPORATİF MODEL DÖKÜM : Proses, kalıba sıcak erimiş metal döküldüğünde buharlaşacak olan polistiren köpük gibi bir malzemeden yapılmış bir model kullanır. Bu işlemin iki türü vardır: Bağsız kum kullanan KAYIP KÖPÜK DÖKÜM ve bağlı kum kullanan TAM KALIP DÖKÜM. İşte genel işlem adımları: 1.) Deseni polistiren gibi bir malzemeden üretin. Büyük miktarlarda üretilecekse, model kalıplanır. Parça karmaşık bir şekle sahipse, deseni oluşturmak için bu tür köpük malzemenin birkaç bölümünün birbirine yapıştırılması gerekebilir. Döküm üzerinde iyi bir yüzey kalitesi oluşturmak için kalıbı genellikle refrakter bir bileşikle kaplarız. 2.) Kalıp daha sonra kalıp kumu içine konur. 3.) Erimiş metal kalıba dökülür, köpük kalıbı buharlaştırılır, yani çoğu durumda polistiren kalıp boşluğundan akarken. 4.) Erimiş metal sertleşmesi için kum kalıpta bırakılır. 5.) Sertleştikten sonra dökümü çıkartıyoruz. Bazı durumlarda, ürettiğimiz ürün, kalıp içinde bir çekirdek gerektirir. Evaporatif dökümde, kalıp boşluğuna maça yerleştirmeye ve sabitlemeye gerek yoktur. Teknik, çok karmaşık geometrilerin üretimi için uygundur, yüksek hacimli üretim için kolayca otomatikleştirilebilir ve döküm parçada ayırma hatları yoktur. Temel işlemin uygulanması basit ve ekonomiktir. Büyük hacimli üretim için, desenleri polistirenden üretmek için bir kalıp veya kalıba ihtiyaç duyulduğundan, bu biraz maliyetli olabilir. • HARCANMAYAN KALIP DÖKÜMÜ : Bu geniş kategori, her üretim döngüsünden sonra kalıbın yeniden düzenlenmesinin gerekmediği yöntemleri ifade eder. Örnekler kalıcı, kalıp, sürekli ve santrifüj dökümdür. Tekrarlanabilirlik elde edilir ve parçalar YAKIN NET ŞEKİL olarak karakterize edilebilir. • KALICI KALIP DÖKÜM : Çoklu dökümler için metalden yapılmış tekrar kullanılabilir kalıplar kullanılmaktadır. Kalıcı bir kalıp genellikle eskimeden on binlerce kez kullanılabilir. Kalıbı doldurmak için genellikle yerçekimi, gaz basıncı veya vakum kullanılır. Kalıplar (kalıp olarak da adlandırılır) genellikle demir, çelik, seramik veya diğer metallerden yapılır. Genel süreç: 1.) Makineyi işleyin ve kalıbı oluşturun. Kalıbın birbirine uyan ve açılıp kapatılabilen iki metal bloktan işlenmesi yaygındır. Hem parça özellikleri hem de yolluk sistemi genellikle döküm kalıbına işlenir. 2.) İç kalıp yüzeyleri, refrakter malzemeler içeren bir bulamaç ile kaplanmıştır. Bu, ısı akışını kontrol etmeye yardımcı olur ve döküm parçanın kolayca çıkarılması için bir yağlayıcı görevi görür. 3.) Daha sonra kalıcı kalıp yarımları kapatılır ve kalıp ısıtılır. 4.) Erimiş metal kalıba dökülür ve katılaşması için dinlenmeye bırakılır. 5.) Fazla soğuma olmadan kalıp yarımları açıldığında ejektörler kullanarak parçayı kalıcı kalıptan çıkarıyoruz. Çinko ve alüminyum gibi düşük erime noktalı metaller için sıklıkla kalıcı kalıp dökümü kullanıyoruz. Çelik dökümler için kalıp malzemesi olarak grafit kullanıyoruz. Bazen kalıcı kalıplar içinde maçalar kullanarak karmaşık geometriler elde ederiz. Bu tekniğin avantajları, hızlı soğutma ile elde edilen iyi mekanik özelliklere sahip dökümler, özelliklerde homojenlik, iyi doğruluk ve yüzey kalitesi, düşük ıskarta oranları, prosesi otomatikleştirme ve ekonomik olarak yüksek hacimler üretme imkanıdır. Dezavantajları, düşük hacimli işlemler için uygun olmayan yüksek ilk kurulum maliyetleri ve üretilen parçaların boyutundaki sınırlamalardır. • KALIP DÖKÜM : Bir kalıp işlenir ve erimiş metal yüksek basınç altında kalıp boşluklarına itilir. Hem demir dışı hem de demirli metal kalıp dökümleri mümkündür. İşlem, ayrıntılara, son derece ince duvarlara, boyutsal tutarlılığa ve iyi yüzey kalitesine sahip küçük ila orta büyüklükteki parçaların yüksek miktarda üretim çalışmaları için uygundur. AGS-TECH A.Ş., bu tekniği kullanarak 0,5 mm'ye kadar küçük et kalınlıkları üretebilmektedir. Kalıcı kalıba dökümde olduğu gibi, üretilen parçanın çıkarılması için kalıbın açılıp kapanabilen iki yarıdan oluşması gerekir. Bir kalıp döküm kalıbı, her döngüde birden fazla dökümün üretilmesini sağlamak için birden fazla boşluğa sahip olabilir. Döküm kalıpları çok ağırdır ve ürettikleri parçalardan çok daha büyüktür, bu nedenle de pahalıdır. Üretilen parçalarını bizden sipariş eden müşterilerimiz için yıpranmış kalıpları ücretsiz olarak onarıyor ve değiştiriyoruz ve müşterilerimizin kalıplarını yıllarca muhafaza ediyoruz. Kalıplarımızın birkaç yüz bin döngü aralığında uzun ömürleri vardır. İşte basitleştirilmiş temel işlem adımları: 1.) Kalıbın genel olarak çelikten üretilmesi 2.) Kalıp döküm makinesine takılı kalıp 3.) Piston, erimiş metali, karmaşık özellikleri ve ince duvarları dolduran kalıp boşluklarında akmaya zorlar. 4.) Kalıbın ergimiş metal ile doldurulmasından sonra döküm basınç altında sertleşmeye bırakılır. 5.) Kalıp açılır ve ejektör pimleri yardımıyla döküm çıkarılır. 6.) Şimdi boş kalıp tekrar yağlanır ve bir sonraki çevrim için sıkıştırılır. Dökümde, kalıba ek bir parça eklediğimiz ve metali etrafına döktüğümüz sık sık geçmeli kalıplama kullanırız. Katılaşmadan sonra bu parçalar döküm ürünün bir parçası haline gelir. Pres dökümün avantajları, parçaların iyi mekanik özellikleri, karmaşık özellikler olasılığı, ince detaylar ve iyi yüzey kalitesi, yüksek üretim oranları, kolay otomasyondur. Dezavantajları: Yüksek kalıp ve ekipman maliyeti nedeniyle düşük hacim için çok uygun değildir, dökülebilecek şekillerdeki kısıtlamalar, döküm parçalar üzerinde ejektör pimlerinin temasından kaynaklanan küçük yuvarlak izler, ayırma hattında sıkılmış ince metal çapaklar, kalıp yarıları arasındaki ayırma hattı boyunca havalandırma delikleri için, su sirkülasyonu kullanarak kalıp sıcaklıklarını düşük tutma zorunluluğu. • SANTRİFÜJ DÖKÜM : Dönen kalıbın ortasına dönme ekseninde erimiş metal dökülür. Merkezkaç kuvvetleri metali çevreye doğru fırlatır ve kalıp dönmeye devam ettikçe katılaşmasına izin verilir. Hem yatay hem de dikey eksen dönüşleri kullanılabilir. Yuvarlak iç yüzeyli parçalar ve diğer yuvarlak olmayan şekiller dökülebilir. Süreç şu şekilde özetlenebilir: 1.) Erimiş metal santrifüj kalıba dökülür. Metal daha sonra kalıbın dönmesi nedeniyle dış duvarlara zorlanır. 2.) Kalıp döndükçe metal döküm sertleşir Santrifüj döküm, boru gibi içi boş silindirik parçaların üretimi için uygun bir tekniktir, yolluk, yükseltici ve yolluk elemanlarına ihtiyaç yoktur, iyi yüzey kalitesi ve detay özellikleri, büzülme sorunu yoktur, çok büyük çaplı uzun borular üretebilme imkanı, yüksek oranlı üretim kabiliyeti . • SÜREKLİ DÖKÜM ( SÜREKLİ DÖKÜM ) : Sürekli uzunluktaki metali dökmek için kullanılır. Temel olarak erimiş metal, kalıbın iki boyutlu profiline dökülür, ancak uzunluğu belirsizdir. Döküm, zamanla artan uzunluğu ile aşağı doğru hareket ederken, yeni erimiş metal sürekli olarak kalıba beslenir. Bakır, çelik, alüminyum gibi metaller, sürekli döküm işlemi kullanılarak uzun teller halinde dökülür. İşlem çeşitli konfigürasyonlara sahip olabilir, ancak ortak olanı şu şekilde basitleştirilebilir: 1.) Erimiş metal, kalıbın üzerinde bulunan bir kaba iyi hesaplanmış miktar ve debilerde dökülür ve su soğutmalı kalıbın içinden akar. Kalıbın içine dökülen metal döküm, kalıbın altına yerleştirilmiş bir başlangıç çubuğuna katılaşır. Bu başlangıç çubuğu, silindirlere başlangıçta tutunacak birşey verir. 2.) Uzun metal şerit, silindirler tarafından sabit bir hızda taşınır. Silindirler ayrıca metal telin akış yönünü dikeyden yataya değiştirir. 3.) Sürekli döküm, belirli bir yatay mesafe kat ettikten sonra, döküm ile birlikte hareket eden bir torç veya testere, hızlı bir şekilde istenen uzunluklarda keser. Sürekli döküm işlemi, sürekli olarak dökülen metalin I-Kirişler, T-Kirişler….vb. üretmek için doğrudan bir haddehaneye beslenebildiği HADDELEME PROSESİ ile entegre edilebilir. Sürekli döküm, ürün boyunca tek tip özellikler üretir, yüksek katılaşma hızına sahiptir, çok düşük malzeme kaybı nedeniyle maliyeti düşürür, metal yükleme, dökme, katılaştırma, kesme ve döküm çıkarma işlemlerinin sürekli bir operasyonda gerçekleştiği bir süreç sunar ve böylece yüksek verimlilik oranı ve yüksek kalite elde edilir. Ancak önemli bir husus, yüksek ilk yatırım, kurulum maliyetleri ve alan gereksinimleridir. • İŞLEME HİZMETLERİ : Üç, dört ve beş eksenli işleme sunuyoruz. TORNALAMA, FREZELEME, DELME, DELME, BROŞLEME, PLANLAMA, KESİM, TAŞLAMA, LAPLAMA, PARLATMA, PARLATMA ve GELENEKSEL OLMAYAN TALAŞLAMA talaşlı imalat yöntemlerini sitemizin farklı bir menüsü altında detaylandırıyoruz. İmalatımızın çoğunda CNC makineleri kullanıyoruz. Ancak bazı operasyonlar için geleneksel teknikler daha uygundur ve bu nedenle onlara da güveniyoruz. İşleme yeteneklerimiz mümkün olan en yüksek seviyeye ulaşır ve en zorlu parçaların bazıları AS9100 sertifikalı bir tesiste üretilir. Jet motoru kanatları, son derece uzmanlaşmış üretim deneyimi ve doğru ekipman gerektirir. Havacılık endüstrisinin çok katı standartları vardır. Karmaşık geometrik yapılara sahip bazı bileşenler, en kolay şekilde, bizimki de dahil olmak üzere bazı işleme tesislerinde bulunan beş eksenli işleme ile üretilir. Havacılık ve uzay sertifikalı tesisimiz, havacılık endüstrisinin kapsamlı dokümantasyon gereksinimlerine uygun gerekli deneyime sahiptir. TORNALAMA işlemlerinde, bir iş parçası döndürülür ve bir kesici takıma karşı hareket ettirilir. Bu işlem için torna adı verilen bir makine kullanılmaktadır. FREZELEME'de, freze makinesi adı verilen bir makinede, kesici kenarları bir iş parçasına dayanacak şekilde getirmek için dönen bir takım bulunur. DELME operasyonları, iş parçasıyla temas ettiğinde delikler oluşturan kesici kenarları olan dönen bir kesici içerir. Genellikle matkap presleri, torna tezgahları veya değirmenler kullanılır. BORALAMA operasyonlarında, deliği hafifçe büyütmek ve doğruluğu artırmak için tek bir bükülmüş sivri ucu olan bir takım, dönen bir iş parçasındaki kaba bir deliğe hareket ettirilir. İnce bitirme amaçları için kullanılır. BROŞLAMA, broşun (dişli alet) bir geçişinde bir iş parçasından malzemeyi çıkarmak için dişli bir alet içerir. Doğrusal broşlamada, broş, kesimi gerçekleştirmek için iş parçasının yüzeyine karşı doğrusal olarak ilerler, oysa döner broşlamada, broş döndürülür ve eksen simetrik bir şekil kesmek için iş parçasına bastırılır. SWISS TİPİ İŞLEME, küçük yüksek hassasiyetli parçaların yüksek hacimli üretimi için kullandığımız değerli tekniklerimizden biridir. İsviçre tipi torna tezgahı kullanarak küçük, karmaşık, hassas parçaları ucuza çeviriyoruz. İş parçasının sabit tutulduğu ve takımın hareket ettiği geleneksel torna tezgahlarından farklı olarak, İsviçre tipi tornalama merkezlerinde iş parçasının Z ekseninde hareket etmesine izin verilir ve takım sabittir. İsviçre tipi işlemede, çubuk stoğu makinede tutulur ve sadece işlenecek kısmı açığa çıkararak z eksenindeki bir kılavuz burç boyunca ilerletilir. Bu şekilde sıkı bir tutuş sağlanır ve doğruluk çok yüksektir. Hareketli takımların mevcudiyeti, kılavuz burçtan malzeme ilerledikçe frezeleme ve delme fırsatı sağlar. İsviçre tipi ekipmanın Y ekseni, tam frezeleme yetenekleri sağlar ve imalatta büyük miktarda zaman tasarrufu sağlar. Ayrıca makinelerimizde alt işmiline tutulduğunda parça üzerinde çalışan matkaplar ve delik işleme takımları bulunmaktadır. İsviçre Tipi işleme kabiliyetimiz, bize tek bir işlemde tam otomatik komple işleme fırsatı sunar. İşleme, AGS-TECH Inc. işinin en büyük bölümlerinden biridir. Tüm çizim özelliklerinin karşılanması için bir parçayı döktükten veya ekstrüde ettikten sonra birincil işlem veya ikincil işlem olarak kullanırız. • YÜZEY İŞLEM HİZMETLERİ : Yapışmayı artırmak için yüzey koşullandırma, kaplamanın yapışmasını artırmak için ince oksit tabakası yerleştirme, kum püskürtme, kimyasal film, anotlama (eloksal kaplama), nitrürleme, toz kaplama, sprey kaplama gibi çok çeşitli yüzey işlemleri ve yüzey bitirme işlemleri sunuyoruz. , püskürtme, elektron ışını, buharlaştırma, kaplama, elmas benzeri karbon (DLC) gibi sert kaplamalar veya delme ve kesme aletleri için titanyum kaplama dahil olmak üzere çeşitli gelişmiş metalizasyon ve kaplama teknikleri. • ÜRÜN MARKALAMA VE ETİKETLEME HİZMETLERİ : Müşterilerimizin birçoğu markalama ve etiketleme, lazer markalama, metal parçalar üzerine kazıma talep etmektedir. Böyle bir ihtiyacınız varsa, hangi seçeneğin sizin için en iyi olacağını tartışalım. İşte yaygın olarak kullanılan metal döküm ürünlerinden bazıları. Bunlar kullanıma hazır olduğundan, aşağıdakilerden herhangi birinin gereksinimlerinize uyması durumunda kalıp maliyetlerinden tasarruf edebilirsiniz: AGS-Electronics'ten 11 Serisi Döküm Alüminyum Kutularımızı İNDİRMEK İÇİN TIKLAYINIZ CLICK Product Finder-Locator Service ÖNCEKİ SAYFA
- Fason Parça Üretimi, Montaj Hizmetleri, Plastik Kalıpçılık, Metal Döküm,Talaşlı İmalat, Saç Metal Fabrikasyon, Cam ve Seramik Parça İmalatı, Yay İmalatı
Fason Parça Üretimi, Montaj Hizmetleri, Plastik Kalıpçılık, Metal Döküm,Talaşlı İmalat, Freze, Metal Dövme, Saç Metal Fabrikasyon, Cam ve Seramik Parça İmalatı, Teknik Seramik Parçalar, Yay İmalatı, Ekstrüzyon, Damgalama Özel Fason İmalat Parçalar, Montajlar ve Ürünler Devamını oku Plastik, Lastik, Kauçuk Kalıp ve Kalıplama Devamını oku Metal ve Alaşım Döküm ve İşleme Devamını oku Ekstrüzyonlar, Ekstrüde Ürünler Devamını oku Metal Damgalama ve Sac Ürünler İmalatı Devamını oku Metal Dövme ve Toz Metalurjisi Devamını oku Tel ve Yay Şekillendirme Devamını oku Cam ve Seramik Şekillendirme ve Parça Üretimi Devamını oku Eklemeli ve Hızlı İmalat Devamını oku Kompozitler, Kompozit Malzeme ve Ürünler İmalatı Devamını oku Parçaların Montajlanması, Montaj, Sabitleme İşlemleri Sizin için parça ve montajlar üretiyoruz ve aşağıdaki üretim süreçlerini sunuyoruz: • Plastik ve kauçuk kalıplar ve kalıplanmış parçalar. Enjeksiyonlu kalıplama, termoform, termoset kalıplama, vakumlu şekillendirme, üflemeli kalıplama, döner kalıplama, dökme kalıplama, insert kalıplama ve diğerleri. • Plastik, lastik, kauçuk ve metal ekstrüzyonlar • Freze ve tornalama teknikleri ile üretilen demirli ve demirsiz dökümler ve işlenmiş parçalar, İsviçre tipi işleme. • Toz metalurjisi parçaları • Metal ve ametal damgalamalar, sac şekillendirme, kaynaklı sac montajları • Soğuk ve sıcak dövme • Teller, kaynaklı tel grupları, tel şekillendirme • Çeşitli yay türleri, yay şekillendirme • Dişli imalatı, dişli kutusu, kaplin, sonsuz, hız düşürücü, silindir, transmisyon kayışları, transmisyon zincirleri, transmisyon bileşenleri • NATO ve askeri standartlara uygun özel temperli ve kurşun geçirmez cam • Bilyalar, yataklar, kasnaklar ve kasnak tertibatları • O-ring, pul ve contalar gibi valfler ve pnömatik bileşenler • Cam ve seramik parçalar ve tertibatlar, vakuma dayanıklı ve hermetik bileşenler, metal-seramik ve seramik-seramik yapıştırma. • Çeşitli mekanik, optomekanik, elektromekanik, optoelektronik düzenek türleri. • Metal-kauçuk, metal-plastik yapıştırma • Boru ve tüp, boru şekillendirme, büküm ve özel boru montajları, körük imalatı. • Fiberglas üretimi • Punta kaynağı, lazer kaynağı, MIG, TIG gibi çeşitli tekniklerin kullanıldığı kaynak. Plastik parçalar için ultrasonik kaynak. • Yapışmayı artırmak için yüzey koşullandırma, kaplamanın yapışmasını artırmak için ince oksit tabakası yerleştirme, kum püskürtme, kimyasal film, anotlama, nitrürleme, toz kaplama, sprey kaplama, çeşitli gelişmiş metalleştirme ve kaplama teknikleri gibi çok çeşitli yüzey işlemleri ve yüzey bitirme işlemleri kesme ve delme aletleri için püskürtme, elektron ışını, buharlaştırma, kaplama, elmas benzeri karbon (DLC) veya titanyum gibi sert kaplamalar dahil. • Markalama ve etiketleme, metal parçalara lazer markalama, plastik ve kauçuk parçalara baskı Tasarımcılar ve Mühendisler tarafından kullanılan Ortak Makine Mühendisliği Terimleri için broşürü indirin Özel spesifikasyonlarınıza ve gereksinimlerinize göre ürünler üretiyoruz. Size en iyi kaliteyi, teslimatı ve fiyatları sunmak için dünya çapında Çin, Hindistan, Tayvan, Filipinler, Güney Kore, Malezya, Sri Lanka, Türkiye, ABD, Kanada, Almanya, İngiltere ve Japonya'da ürünler üretiyoruz. Bu, bizi diğer tüm fason imalatçılardan çok daha güçlü ve küresel olarak daha rekabetçi kılıyor. Ürünlerimiz ISO9001:2000, QS9000, ISO14001, TS16949 sertifikalı ortamlarda üretilmektedir ve CE, UL işaretine sahiptir ve diğer endüstri standartlarını karşılamaktadır. Projeniz için görevlendirildikten sonra, tüm imalat, montaj, test, kalifikasyon, nakliye ve gümrük işlemlerini dilediğiniz gibi halledebiliriz. Dilerseniz parçalarınızı depolayabilir, özel kitleri monte edebilir, şirket adınızı ve markanızı yazdırabilir ve etiketleyebilir ve müşterilerinize sevkıyat yapabiliriz. Yani isterseniz depolama ve dağıtım merkeziniz de olabiliriz. Depolarımızın büyük limanlara yakın olması bize lojistik avantaj sağlıyor. Örneğin, ürünleriniz büyük bir ABD limanına ulaştığında, onu doğrudan yakındaki bir depoya nakliye edebiliriz, burada depolayabilir, monte edebilir, kitler yapabilir, yeniden etiketleyebilir, yazdırabilir, tercihinize göre paketleyebilir ve müşterilerinize nakledebiliriz. Biz sadece ürün tedarik etmiyoruz. Firmamız size gelip projenizi yerinde değerlendirip size özel proje teklifi geliştirdiğimiz özel kontratlar üzerinde de çalışmaktadır. Projeyi uygulamak için deneyimli ekibimizi gönderiyoruz. Mühendislik çalışmalarımız hakkında daha fazla bilgiyi aşağıdaki linkte bulabilirsiniz. http://www.ags-engineering.com -Endüstriyel ölçekte büyük projelerin yanı sıra küçük projeleri de kabul ediyoruz. İlk adım olarak, sizi uzman ekip üyelerimize telefon, telekonferans veya MSN messenger ile bağlayabiliriz, böylece bir uzmanla doğrudan iletişim kurabilir, soru sorabilir ve projenizi tartışabilirsiniz. Bizi arayın, gerekirse gelip sizi ziyaret edelim. ÖNCEKİ SAYFA
- Fason Üretim Fason İmalat | Türkiye | AGS-TECH, Inc.
AGS-TECH Inc., Fason Imalat, Kalıpçılık, Metal Döküm, Talaşlı İmalat, Metal Dövme, Saç Metal Fabrikasyon, Mekanik Parçalar, Elektrik Bileşenleri Elektronik Montaj, Optik Parçalar ve Montaj, PCBA, Toz Metalurjisi, CNC, Baskılı Devre, Kablo Aksamları, Fason Üretim AGS-TECH Inc. AGS-TECH Inc. Custom Manufacturing, Domestic & Global Outsourcing, Engineering Integration, Consolidation AGS-TECH Inc. 1/2 AGS-TECH, Inc. sizin: Çok Çeşitli Ürün ve Hizmetler için Küresel Özel Fason Üretici, Entegratör, Birleştirici, Küresel Dış Kaynak Kullanım Ortağı. Özel imal edilmiş ve hazır ürünlerin fason imalatı, mühendisliği, konsolidasyonu, dış kaynak kullanımı için tek durak kaynağınız biziz. HİZMETLER: Özel İmalat Yerli ve Global Fason Üretim İmalat Dış Kaynak Kullanımı Yurtiçi ve Küresel Tedarik Konsolidasyon Mühendislik Entegrasyonu AGS-TECH, Inc. HAKKINDA - Küresel Özel Fason Üreticiniz, Mühendislik Entegratörünüz, Konsolidatörünüz, Dış Kaynak İş Ortağınız AGS-TECH Inc., kalıplar, kalıplanmış plastik ve kauçuk parçalar, dökümler, ekstrüzyonlar, sac imalat, metal damgalama ve dövme, CNC işleme, makine elemanları, toz metalurjisi, seramik ve cam malzemeli dahil olmak üzere endüstriyel ürünlerin üreticisi, mühendislik entegratörü, küresel tedarikçisidir. Ayrıca cam şekillendirme, tel / yay şekillendirme, birleştirme ve montaj ve bağlantı elemanları, geleneksel olmayan imalat, mikrofabrikasyon, nanoteknoloji kaplamalar ve ince film, özel mekanik ve elektrik elektronik bileşenler ve düzenekler ve PCB ve PCBA baskılı devre ve kablo tesisatı, optik ve fiber optik bileşenler ve montaj bizim uzmanlık alanlarımızdandır. Bunların yanısıra , müşterilerimize, sertlik test cihazları, metalurjik mikroskoplar, ultrasonik arıza dedektörleri, endüstriyel bilgisayarlar, gömülü sistemler, otomasyon ve panel PC, tek kartlı bilgisayarlar, kalite kontrol ekipmanları gibi test ve metroloji ekipmanları sunmaktayız. Ürünlerimizin yanı sıra global mühendislik, tersine mühendislik, araştırma ve geliştirme, ürün geliştirme, eklemeli ve hızlı üretim, prototipleme, proje yönetimi yeteneklerimizle sizi küresel pazarlarda daha rekabetçi ve başarılı kılmak için teknik, lojistik ve iş desteği sunuyoruz. Misyonumuz basit: Müşterilerimizin başarılı olmasını ve büyümesini sağlamak. Nasıl ? 1.) Daha İyi Kalite 2.) Daha İyi Fiyat 3.) Daha İyi ve Hızlı Teslimat........ tek bir şirketten ve Dünyanın en çokçeşitli küresel mühendislik entegratörü ve tedarikçisi AGS-TECH Inc.'den sizlere ! Bize teknik çizimlerinizi gönderin ve biz parçalarınızı üretmek için kalıpları ve gerekli takımları üretebilir hazırlayabiliriz. Ürünlerinizi kalıplama, döküm, ekstrüzyon, dövme, saç imalatı, damgalama, toz metalurjisi, CNC işleme, şekillendirme ile üretiyoruz. Size parça ve bileşenleri gönderebilir veya tesislerimizde montaj, imalat ve komple imalat işlemlerini gerçekleştirebiliriz. Montaj operasyonlarımız mekanik, optik, elektronik, fiber optik ürünleri kapsamaktadır. Bağlantı elemanları, kaynak, lehimleme, lehimleme, yapıştırma ve daha birçok metod kullanarak birleştirme işlemlerini gerçekleştiriyoruz. Kalıplama proseslerimiz çeşitli plastik, kauçuk, seramik, cam, toz metalurjisi malzemeleri içindir. Metaller, alaşımlar, plastik, seramik içeren döküm, CNC işleme, dövme, saç imalatı, tel ve yay şekillendirme , hepsini bizden tedarik edebilirsiniz. Kaplamalar ve ince ve kalın film, taşlama, lepleme, cilalama gibi birçok son bitirme işlemleri sunuyoruz. Üretim kapasitemiz mekanik parça montajının çok ötesine geçmektedir. Teknik çizimlerinize, BOM, Gerber dosyalarınıza göre elektrik elektronik bileşenleri ve düzenekleri ve PCB ve PCBA devre ve kablo demeti, optik ve fiber optik bileşenlerl üretiyoruz ve montajlarını yapıyoruz. Diğerlerinin yanı sıra reflow lehimleme ve dalga lehimleme dahil olmak üzere çeşitli PCB ve PCBA üretim teknikleri uygulanmaktadır. Hermetik elektronik ve fiber optik paketlerin ve ürünlerin hassas birleştirilmesi, montajı ve sızdırmazlığı konusunda uzmanız. Pasif ve aktif mekanik montajın yanı sıra, Telcordia ve diğer endüstri standartlarına uygun ürünler üretmek için özel lehimleme ve lehimleme malzemeleri ve tekniklerinden yararlanıyoruz. Yüksek hacimli imalat ve fabrikasyon ile sınırlı değiliz. Hemen hemen her proje mühendislik, tersine mühendislik, araştırma-geliştirme, ürün geliştirme, eklemeli ve hızlı imalat, prototipleme ihtiyacı ile başlar. Dünyanın en geniş yelpazeli küresel özel imalatçısı, mühendislik entegratörü, konsolidatörü, küresel dış kaynak kullanım ortağı olarak, sadece bir fikir bile olsa bize ulaşmanızı bekliyoruz. Sizi bulunduğunuz noktadan alıyoruz ve başarılı ve eksiksiz bir ürün geliştirme ve üretim döngüsünün tüm aşamalarında size yardımcı oluyoruz. Hızlı metal saçtan ürün imalatı, hızlı kalıp işleme ve kalıplama, hızlı döküm, hızlı PCB ve PCBA devre montajı ve başka hertür hızlı prototipleme tekniği ile hizmetinizdeyiz. Size sunabileceğimiz diğer ürünlerden bazıları sertlik test cihazları, metalurjik mikroskoplar, ultrasonik arıza dedektörleri gibi özel üretim metroloji ekipmanlarının yanı sıra kullanıma hazır endüstriyel bilgisayarlar, gömülü sistemler, otomasyon ekipmanları, panel PC, tek kartlı bilgisayarlar ve üretim ve endüstriyel tesislerde yaygın olarak kullanılan kalite kontrol ekipmanlarıdır. Size son teknoloji metroloji ekipmanı ve endüstriyel bilgisayar bileşenleri sunarak, endüstriyel ihtiyacınız olan her şeyi temin edebileceğiniz tek bir tedarikçi olarak ihtiyaçlarınızı karşılıyoruz. Geniş bir mühendislik hizmetleri yelpazemiz olmasaydı, piyasada bulunan sınırlı imalat kabiliyetine sahip diğer sıradan üreticilerin ve satıcıların çoğundan farklı olmazdık. Mühendislik hizmetlerimizin kapsamı, bizi dünyanın en çokçeşitli özel imalatçısı, fason imalatçısı, mühendislik entegratörü, konsolidatörü ve küresel fason dış kaynak ortağı olarak farklı kılmaktadır. Mühendislik hizmetlerimizi size tek salt hizmet olarak veya yeni ürün ve süreç geliştirmenin bir parçası olarak veya mevcut bir ürün veya süreç geliştirmenin bir parçası olarak veya aklınıza gelen herhangi bir şekilde sunabiliriz. Esnek mühendislik hizmetlerimiz ihtiyaçlarınıza ve gereksinimlerinize en uygun şekli alabilir. Mühendislik hizmetlerimizin yelpazesi ve içeriği yalnızca hayal gücünüzle sınırlıdır ve size uygun her şekilde olabilir. Mühendislik hizmetlerimizden en yaygın çıktı biçimleri şunlardır: Danışma raporları, test sayfaları ve raporları, inceleme raporları, planlar, mühendislik çizimleri, montaj çizimleri, malzeme listesi listeleri, veri sayfaları, simülasyonlar, yazılım programları, grafikler ve çizelgeler, konunun uzmanlarından optik, termal veya diğer yazılım programları, örnekler ve prototipler, modeller, gösteriler…..vs. Mühendislik hizmetlerimiz, konusunda uzman ve yetkili, yetki belgesine sahip profesyonel mühendislerimizin imzaları ve mühürleri ile teslim edilebilir. Bazen işi imzalamak için farklı disiplinlerden bir takım profesyonel mühendisler gerekebilir. Mühendislik hizmetlerimiz size tam zamanlı bir mühendis veya mühendisler kiralamanın maliyetinden tasarruf ettirir, uzman mühendisi bulmak yerine zamanınızı ve bütçenizi size hızlı bir şekilde hizmet edecek işgücünü sağlamak gibi birçok fayda sağlayabilir. Projecizde ani veya acil değişiklik gerektiğinde, hızlı bir şekilde kendi mühendislerinizi işe alıp işten çıkarmanız durumunda bu çok maliyetlidir, farklı disiplinlerden ve geçmişlerden mühendisleri hızlı bir şekilde değiştirebilmenizin ve size istediğiniz zaman manevra yapma yeteneği kazandırılmasının, özel imalat ve montajın yanı sıra mühendislik hizmetlerininin dışarıdan temin edilmesinin birçok başka faydası vardır. Bu sitede ürünlerin özel imalatına, fason imalatına, montaj, entegrasyon, konsolidasyon ve dış kaynak kullanımına odaklanacağız. İşimizin mühendislik tarafı sizi daha çok ilgilendiriyorsa, mühendislik hizmetlerimiz hakkında detaylı bilgiye diğer sitemizi ziyaret ederek ulaşabilirsiniz.http://www.ags-engineering.com Biz AGS-TECH Inc. olarak, üretim, imalat, mühendislik ve küresel fason dış kaynak kullanımı ve konsolidasyonı için tek durak tedarikçiniziz. Size özel fason imalat, parçaların montaji, ürün montajı ve mühendislik hizmetleri sunan dünyanın en geniş yelpazeli mühendislik ve imalat entegratörüyüz. Contact Us First Name Last Name Email Write a message Submit Thanks for submitting!