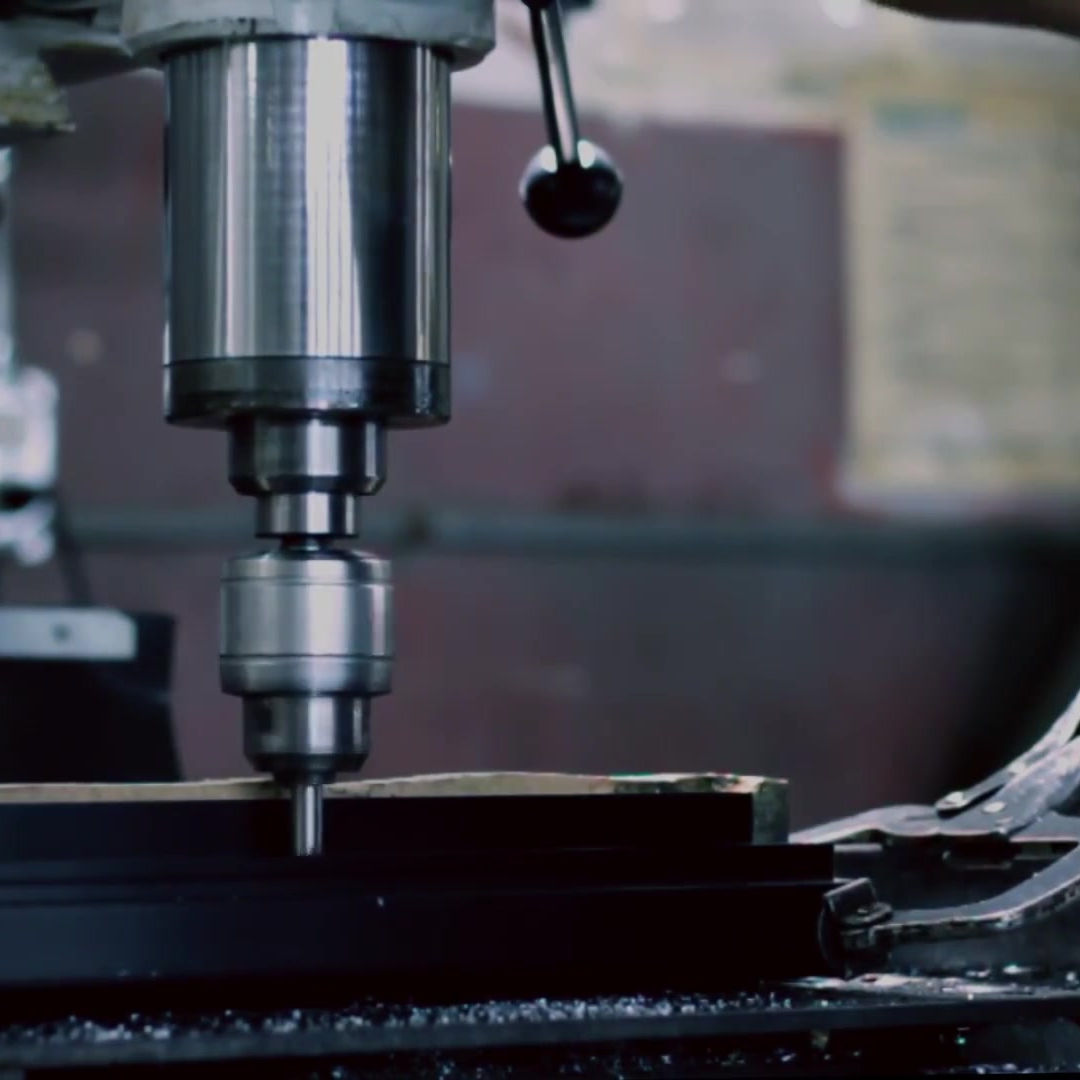
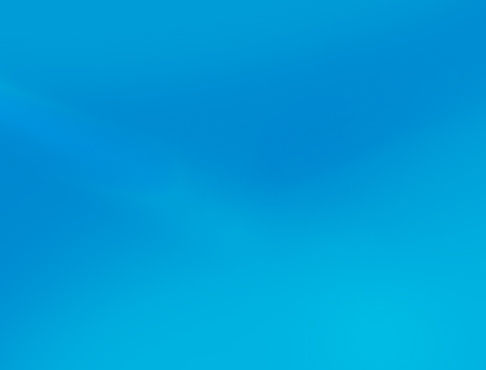
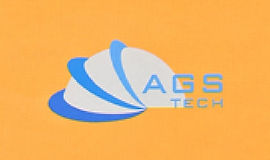
Глобальний індивідуальний виробник, інтегратор, консолідатор, аутсорсинговий партнер для широкого спектру продуктів і послуг.
Ми є вашим єдиним джерелом для виробництва, виготовлення, проектування, консолідації, інтеграції, аутсорсингу виготовлених на замовлення та готових продуктів і послуг.
Виберіть свою мову
-
Виготовлення на замовлення
-
Внутрішнє та глобальне контрактне виробництво
-
Аутсорсинг виробництва
-
Внутрішні та міжнародні закупівлі
-
Consolidation
-
Інженерна інтеграція
-
Інженерні послуги
ELECTRICAL DISCHARGE MACHINING (EDM), also referred to as SPARK-EROSION or ELECTRODISCHARGE MACHINING, SPARK ERODING, DIE SINKING_cc781905-5cde-3194-bb3b -136bad5cf58d_or WIRE EROSION, is a NON-CONVENTIONAL MANUFACTURING process where erosion of metals takes place and desired shape is obtained using electrical discharges in the form іскор. Ми також пропонуємо деякі різновиди електроерозійної обробки, а саме: NO-WEAR EDM, ДРОТОВА ЕДМ (WEDM), ЕДМ-ШЛІФУВАННЯ (EDG), ЕДМ-ПРИГРУЗКА, ЕЛЕКТРИЧНЕ ФРЕЗЕРУВАННЯ, мікро-ЕДМ, m-EDM_cc781905 -5cde-3194-bb3b-136bad5cf58d_and ЕЛЕКТРОХІМІЧНЕ РОЗРЯДНЕ ПОМЛЮВАННЯ (ECDG). Наші електроерозійні системи складаються з профільованих інструментів/електродів і заготовки, підключених до джерел живлення постійного струму та вставлених у електрично непровідну діелектричну рідину. Після 1940 року електроерозійна обробка стала однією з найважливіших і популярних виробничих технологій у обробній промисловості.
Коли відстань між двома електродами зменшується, напруженість електричного поля в об’ємі між електродами стає більшою, ніж міцність діелектрика в деяких точках, який розривається, зрештою утворюючи міст для проходження струму між двома електродами. Утворюється інтенсивна електрична дуга, що спричиняє значне нагрівання, щоб розплавити частину заготовки та частину інструментального матеріалу. У результаті матеріал видаляється з обох електродів. У той же час рідина діелектрика швидко нагрівається, що призводить до випаровування рідини в дуговому проміжку. Як тільки потік струму припиняється або він припиняється, тепло відводиться від газової бульбашки навколишньою діелектричною рідиною, і бульбашка порожниться (згортається). Ударна хвиля, створена колапсом бульбашки та потоком діелектричної рідини, змиває сміття з поверхні заготовки та захоплює будь-який розплавлений матеріал заготовки в діелектричну рідину. Частота повторення цих розрядів становить від 50 до 500 кГц, напруга від 50 до 380 В і струм від 0,1 до 500 Ампер. Новий рідкий діелектрик, такий як мінеральні масла, гас або дистильована та деіонізована вода, зазвичай транспортується в міжелектродний об’єм, забираючи тверді частинки (у формі сміття), і ізоляційні властивості діелектрика відновлюються. Після проходження струму різниця потенціалів між двома електродами відновлюється до рівня до пробою, тому може статися новий пробій рідкого діелектрика. Наші сучасні електроерозійні машини (EDM) пропонують рухи з числовим керуванням і оснащені насосами та системами фільтрації для діелектричних рідин.
Електроерозійна обробка (EDM) — це метод обробки, який в основному використовується для твердих металів або тих, які було б дуже важко обробити звичайними методами. EDM зазвичай працює з будь-якими матеріалами, які є електричними провідниками, хоча також були запропоновані методи механічної обробки ізоляційної кераміки за допомогою EDM. Температура плавлення та прихована теплота плавлення є властивостями, які визначають об’єм металу, видаленого за один розряд. Чим вище ці значення, тим повільніше швидкість видалення матеріалу. Оскільки процес електроерозійної обробки не включає жодної механічної енергії, твердість, міцність і в’язкість заготовки не впливають на швидкість видалення. Частота розряду або енергія на розряд, напруга та струм змінюються для контролю швидкості видалення матеріалу. Швидкість видалення матеріалу та шорсткість поверхні зростають зі збільшенням щільності струму та зменшенням частоти іскри. Ми можемо вирізати складні контури або порожнини в попередньо загартованій сталі за допомогою EDM без необхідності термічної обробки для їх розм’якшення та повторного загартування. Ми можемо використовувати цей метод з будь-яким металом або металевими сплавами, такими як титан, хастеллой, ковар та інконель. Застосування процесу EDM включає формування полікристалічних алмазних інструментів. EDM вважається нетрадиційним або нетрадиційним методом обробки разом із такими процесами, як електрохімічна обробка (ECM), водоструминне різання (WJ, AWJ), лазерне різання. З іншого боку, звичайні методи механічної обробки включають точіння, фрезерування, шліфування, свердління та інші процеси, механізм видалення матеріалу яких заснований на механічних силах. Електроди для електроерозійної обробки (ЕДМ) виготовляють із графіту, латуні, міді та медно-вольфрамового сплаву. Діаметр електрода можливий до 0,1 мм. Оскільки зношення інструменту є небажаним явищем, яке негативно впливає на точність розмірів при електроезії, ми використовуємо переваги процесу під назвою NO-WEAR EDM, змінюючи полярність і використовуючи мідні інструменти для мінімізації зносу інструменту.
В ідеалі електроерозійну обробку (ЕДМ) можна вважати серією пробою і відновлення діелектричної рідини між електродами. Насправді, однак, видалення сміття з міжелектродної зони майже завжди є частковим. Це призводить до того, що електричні властивості діелектрика в міжелектродній зоні відрізняються від номінальних значень і змінюються з часом. Відстань між електродами (іскровий проміжок) регулюється алгоритмами керування конкретної машини, що використовується. Іскровий проміжок в EDM, на жаль, іноді може бути коротким замиканням через сміття. Система керування електродом може не зреагувати достатньо швидко, щоб запобігти короткому замиканню двох електродів (інструмента та деталі). Це небажане коротке замикання сприяє видаленню матеріалу інакше, ніж в ідеальному випадку. Ми приділяємо велике значення дії промивання, щоб відновити ізоляційні властивості діелектрика, щоб струм завжди відбувався в точці міжелектродної зони, тим самим мінімізуючи можливість небажаної зміни форми (пошкодження) інструменту-електрода. і заготовки. Щоб отримати певну геометрію, EDM-інструмент направляється по бажаній траєкторії дуже близько до заготовки, не торкаючись її. Ми приділяємо максимальну увагу ефективності керування рухом під час використання. Таким чином, відбувається велика кількість струмових розрядів / іскор, і кожен сприяє видаленню матеріалу як з інструменту, так і з заготовки, де утворюються маленькі кратери. Розмір кратерів є функцією технологічних параметрів, встановлених для конкретної роботи, а розміри можуть варіюватися від нанорозміру (наприклад, у випадку операцій мікро-EDM) до кількох сотень мікрометрів у чорнових умовах. Ці невеликі кратери на інструменті викликають поступову ерозію електрода, яка називається «знос інструменту». Щоб протидіяти згубному впливу зносу на геометрію заготовки, ми постійно замінюємо інструмент-електрод під час операції обробки. Іноді ми досягаємо цього, використовуючи постійно замінюваний дріт як електрод (цей процес EDM також називається WIRE EDM ). Іноді ми використовуємо інструмент-електрод таким чином, що лише невелика його частина фактично бере участь у процесі обробки, і ця частина регулярно змінюється. Це, наприклад, при використанні обертового диска як інструмента-електрода. Цей процес називається EDM GRINDING. Ще одна техніка, яку ми використовуємо, полягає у використанні набору електродів різних розмірів і форм під час однієї операції EDM для компенсації зносу. Ми називаємо це багатоелектродною технікою, і найчастіше вона використовується, коли інструментальний електрод повторює в негативі бажану форму та просувається до заготовки в одному напрямку, зазвичай у вертикальному напрямку (тобто по осі z). Це нагадує занурення інструменту в діелектричну рідину, в яку занурена деталь, і тому це називається DIE-SINKING EDM (іноді називається_cc781905-5c 3194-bb3b-136bad5cf58d_CONVENTIONAL EDM or RAM EDM). Машини для цієї операції називаються SINKER EDM. Електроди для даного виду електроерозії мають складну форму. Якщо остаточна геометрія отримана за допомогою зазвичай простого електрода, який переміщується в кількох напрямках і також підлягає обертанню, ми називаємо це EDM ФРЕЗЕРУВАННЯ. Величина зносу строго залежить від технологічних параметрів, які використовуються в роботі (полярність, максимальний струм, напруга холостого ходу). Наприклад, у micro-EDM, також відомому як m-EDM, ці параметри зазвичай встановлюються на значення, що призводить до сильного зносу. Тому знос є основною проблемою в цій галузі, яку ми мінімізуємо, використовуючи наші накопичені ноу-хау. Наприклад, щоб мінімізувати знос графітових електродів, цифровий генератор, яким можна керувати протягом мілісекунд, змінює полярність, коли відбувається електроерозія. Це призводить до ефекту, схожого на гальванічне покриття, яке безперервно відкладає ерозійний графіт назад на електрод. В іншому методі, так званій схемі «нульового зношення», ми мінімізуємо частоту початку та припинення розряду, утримуючи його якомога довше. Швидкість знімання матеріалу при електроемісійній обробці можна оцінити за:
MRR = 4 x 10 досвіду (4) x I x Tw досвіду (-1,23)
Тут MRR – у мм3/хв, I – сила струму в Амперах, Tw – температура плавлення заготовки в K-273,15K. exp означає експоненту.
З іншого боку, швидкість зносу Wt електрода можна отримати з:
Wt = (1,1 x 10exp(11)) x I x Ttexp(-2,38)
Тут Wt у мм3/хв, а Tt — температура плавлення матеріалу електрода в K-273,15K
Нарешті, коефіцієнт зносу заготовки до електрода R можна отримати з:
R = 2,25 x Trexp (-2,38)
Тут Tr - відношення температур плавлення заготовки до електрода.
SINKER EDM :
Грузило EDM, також відоме як CAVITY TYPE EDM or EDM, складається з заготовки, що містить рідину та VOLUME EDM. Електрод і деталь підключаються до джерела живлення. Джерело живлення створює електричний потенціал між ними. Коли електрод наближається до заготовки, в рідині відбувається пробій діелектрика, утворюючи плазмовий канал, і проскакує маленька іскра. Іскри зазвичай випадають по одній, тому що дуже малоймовірно, що різні місця в міжелектродному просторі мають ідентичні локальні електричні характеристики, що дозволило б іскри виникнути в усіх таких місцях одночасно. Сотні тисяч цих іскор виникають у випадкових точках між електродом і деталлю за секунду. Оскільки основний метал руйнується, а іскровий проміжок згодом збільшується, наш верстат з ЧПК автоматично опускає електрод, щоб процес міг тривати безперервно. Наше обладнання має контрольні цикли, відомі як «час увімкнення» та «час вимкнення». Налаштування часу ввімкнення визначає тривалість іскри. Довший час утворює глибшу порожнину для цієї іскри та всіх наступних іскр для цього циклу, створюючи грубішу обробку заготовки, і навпаки. Час вимкнення — це період часу, протягом якого одна іскра замінюється іншою. Довший час вимкнення дозволяє діелектричній рідині промиватися через сопло, щоб очистити ерозійне сміття, таким чином уникаючи короткого замикання. Ці параметри регулюються за мікросекунди.
WIRE EDM :
In WIRE ELECTRICAL DISCHARGE MACHINING (WEDM), also called WIRE-CUT EDM or WIRE CUTTING, we feed a тонкий одножильний металевий дріт з латуні через заготовку, яка занурена в резервуар з діелектричною рідиною. Дротова електроерозія є важливою різновидом електроерозійної обробки. Час від часу ми використовуємо EDM для різання пластин товщиною до 300 мм, а також для виготовлення пуансонів, інструментів і матриць із твердих металів, які важко обробити іншими методами виробництва. У цьому процесі, який нагадує контурне різання стрічковою пилкою, дріт, яка постійно подається з котушки, утримується між верхньою та нижньою алмазними напрямними. Направляючі, керовані ЧПК, рухаються в площині x–y, а верхня напрямна також може рухатися незалежно по осі z–u–v, створюючи можливість вирізати конічні та перехідні форми (наприклад, коло знизу та квадрат у Топ). Верхня напрямна може керувати рухом осі в x–y–u–v–i–j–k–l–. Це дозволяє WEDM вирізати дуже складні та делікатні форми. Середня різьба нашого обладнання, яке забезпечує найкращу економічну вартість і час обробки, становить 0,335 мм при використанні Ø 0,25 латунного, мідного або вольфрамового дроту. Однак верхня та нижня алмазні напрямні нашого обладнання з ЧПК мають точність приблизно 0,004 мм і можуть мати траєкторію різання або проріз лише 0,021 мм за допомогою дроту Ø 0,02 мм. Тож можливі дійсно вузькі розрізи. Ширина різання більша за ширину дроту, тому що іскріння відбувається від сторін дроту до заготовки, спричиняючи ерозію. Це «надмірне скорочення» є необхідним, для багатьох застосувань воно передбачуване і тому може бути компенсоване (у мікро-EDM це не часто). Котушки дроту довгі — довжина котушки дроту 0,25 мм вагою 8 кг становить трохи більше 19 кілометрів. Діаметр дроту може становити всього 20 мікрометрів, а точність геометрії становить близько +/- 1 мікрометра. Зазвичай ми використовуємо дріт лише один раз і переробляємо його, оскільки він відносно недорогий. Він рухається з постійною швидкістю від 0,15 до 9 м/хв, і під час різання підтримується постійний проріз (проріз). У процесі електроерозійної обробки дротом ми використовуємо воду як діелектричну рідину, контролюючи її питомий опір та інші електричні властивості за допомогою фільтрів і деіонізаторів. Вода змиває відрізане сміття із зони різання. Промивка є важливим фактором у визначенні максимальної швидкості подачі для даної товщини матеріалу, тому ми підтримуємо її постійну. Швидкість різання в дротяній ерозії вказується як площа поперечного перерізу, що ріжеться за одиницю часу, наприклад 18 000 мм2/год для інструментальної сталі D2 товщиною 50 мм. Лінійна швидкість різання для цього випадку становитиме 18 000/50 = 360 мм/год.
MRR = Vf xhxb
Тут MRR – у мм3/хв, Vf – швидкість подачі дроту в заготовку в мм/хв, h – товщина або висота в мм, а b – пропил, який становить:
b = dw + 2s
Тут dw — діаметр дроту, а s — зазор між дротом і деталлю в мм.
Разом із жорсткішими допусками наші сучасні багатоосьові обробні центри EDM для різання дроту мають такі функції, як кілька головок для різання двох деталей одночасно, елементи керування для запобігання обриву дроту, функції автоматичного заправлення різьби у разі обриву дроту та програмування стратегії обробки для оптимізації роботи, можливості прямого та кутового різання.
Wire-EDM пропонує нам низькі залишкові напруги, оскільки не вимагає великих сил різання для видалення матеріалу. Коли енергія/потужність на імпульс відносно низька (як під час фінішної обробки), очікується невелика зміна механічних властивостей матеріалу через низькі залишкові напруги.
ЕЛЕКТРИЧНЕ ШЛІФУВАННЯ (EDG) : Шліфувальні круги не містять абразивів, вони виготовлені з графіту або латуні. Повторювані іскри між обертовим колесом і деталлю видаляють матеріал із поверхонь деталі. Швидкість знімання матеріалу становить:
MRR = K x I
Тут MRR у мм3/хв, I — струм в амперах, а K — коефіцієнт матеріалу заготовки в мм3/А-хв. Ми часто використовуємо електроерозійне шліфування, щоб випиляти вузькі щілини на компонентах. Іноді ми поєднуємо процес EDG (електророзрядне шліфування) з процесом ECG (електрохімічне шліфування), де матеріал видаляється хімічною дією, електричні розряди з графітового круга руйнують оксидну плівку та змиваються електролітом. Процес називається ELECTROCHEMICAL-DISCHARGE GRINDING (ECDG). Незважаючи на те, що процес ECDG споживає відносно більше енергії, це швидший процес, ніж EDG. В основному ми шліфуємо твердосплавні інструменти за цією технікою.
Застосування електроерозійної обробки:
Виробництво прототипу:
Ми використовуємо процес EDM у виготовленні прес-форм, інструментів і штампів, а також для виготовлення прототипів і виробничих деталей, особливо для аерокосмічної, автомобільної та електронної промисловості, де обсяги виробництва відносно низькі. У системі Sinker EDM графітовий, мідно-вольфрамовий або чистий мідний електрод обробляється у потрібну (негативну) форму та подається в заготовку на кінці вертикального штока.
Виготовлення штампа для карбування монет:
Для створення штампів для виробництва ювелірних виробів і значків способом карбування (карбування) позитивна майстерна може бути виготовлена зі срібла 928 проби, оскільки (при відповідних налаштуваннях машини) майстер значно потертий і використовується лише один раз. Отриманий негативний штамп потім загартовується та використовується в ударному молоті для виготовлення штампованих листів із вирізаних листових заготовок із бронзи, срібла або низькопробного золотого сплаву. Для бейджів ці пласки можуть бути додатково сформовані до вигнутої поверхні іншим штампом. Цей тип EDM зазвичай виконується зануреним у діелектрик на масляній основі. Готовий об’єкт можна додатково вдосконалити за допомогою твердої (скло) або м’якої (фарба) емалі та/або гальванічного покриття чистим золотом чи нікелем. М’які матеріали, такі як срібло, можна вигравірувати вручну для вишуканості.
Свердління малих отворів:
На наших електроерозійних верстатах для дротяної обробки ми використовуємо електроерозійну електророзійну трубу для свердління малих отворів, щоб зробити наскрізний отвір у заготовці, через який протягується дріт для операції електроерозійної різання. Окремі електроерозійні головки спеціально для свердління невеликих отворів встановлюються на наших верстатах для дротяної обробки, що дозволяє за потреби та без попереднього свердління витирати готові деталі з великих загартованих пластин. Ми також використовуємо EDM з малими отворами для свердління рядів отворів у краях турбінних лопаток, які використовуються в реактивних двигунах. Потік газу через ці невеликі отвори дозволяє двигунам використовувати вищі температури, ніж це можливо в іншому випадку. Високотемпературні, дуже тверді монокристалічні сплави, з яких виготовлені ці леза, роблять звичайну обробку цих отворів із високим співвідношенням сторін надзвичайно складною та навіть неможливою. Іншими областями застосування електроерозійної обробки з малими отворами є створення мікроскопічних отворів для компонентів паливної системи. Окрім інтегрованих електроерозійних головок, ми встановлюємо автономні електроерозійні верстати для свердління малих отворів з осями x–y для обробки глухих або наскрізних отворів. EDM свердлить отвори за допомогою довгого латунного або мідного трубчастого електрода, який обертається в патроні з постійним потоком дистильованої або деіонізованої води, що протікає через електрод як промивний агент і діелектрик. Деякі електроерозійні машини для свердління малих отворів можуть просвердлити 100 мм м’якої або навіть загартованої сталі менш ніж за 10 секунд. Під час цієї операції свердління можна отримати отвори розміром від 0,3 мм до 6,1 мм.
Механічна обробка дезінтеграції металу:
У нас також є спеціальні електроерозійні верстати для спеціальної мети видалення зламаних інструментів (свердел або мітчиків) із заготовок. Цей процес називається «механічна обробка дезінтеграції металу».
Переваги та недоліки електроемісійної обробки:
До переваг EDM можна віднести обробку:
- Складні форми, які інакше було б важко створити за допомогою звичайних ріжучих інструментів
- Надзвичайно твердий матеріал з дуже малими допусками
- Дуже маленькі заготовки, де звичайні ріжучі інструменти можуть пошкодити деталь від надмірного тиску ріжучого інструменту.
- Немає прямого контакту між інструментом і деталлю. Тому делікатні ділянки та слабкі матеріали можна обробляти без будь-яких деформацій.
- Можна отримати хорошу обробку поверхні.
- Дуже тонкі отвори можна легко просвердлити.
До недоліків EDM можна віднести:
- Повільна швидкість знімання матеріалу.
- Додатковий час і вартість, які використовуються для створення електродів для EDM плашечки/погрузчика.
- Відтворити гострі кути на заготовці важко через знос електродів.
- Високе споживання електроенергії.
- Утворюється «Надсічка».
- Під час обробки відбувається надмірний знос інструменту.
- Електронепровідні матеріали можна обробляти лише за допомогою спеціальної настройки процесу.