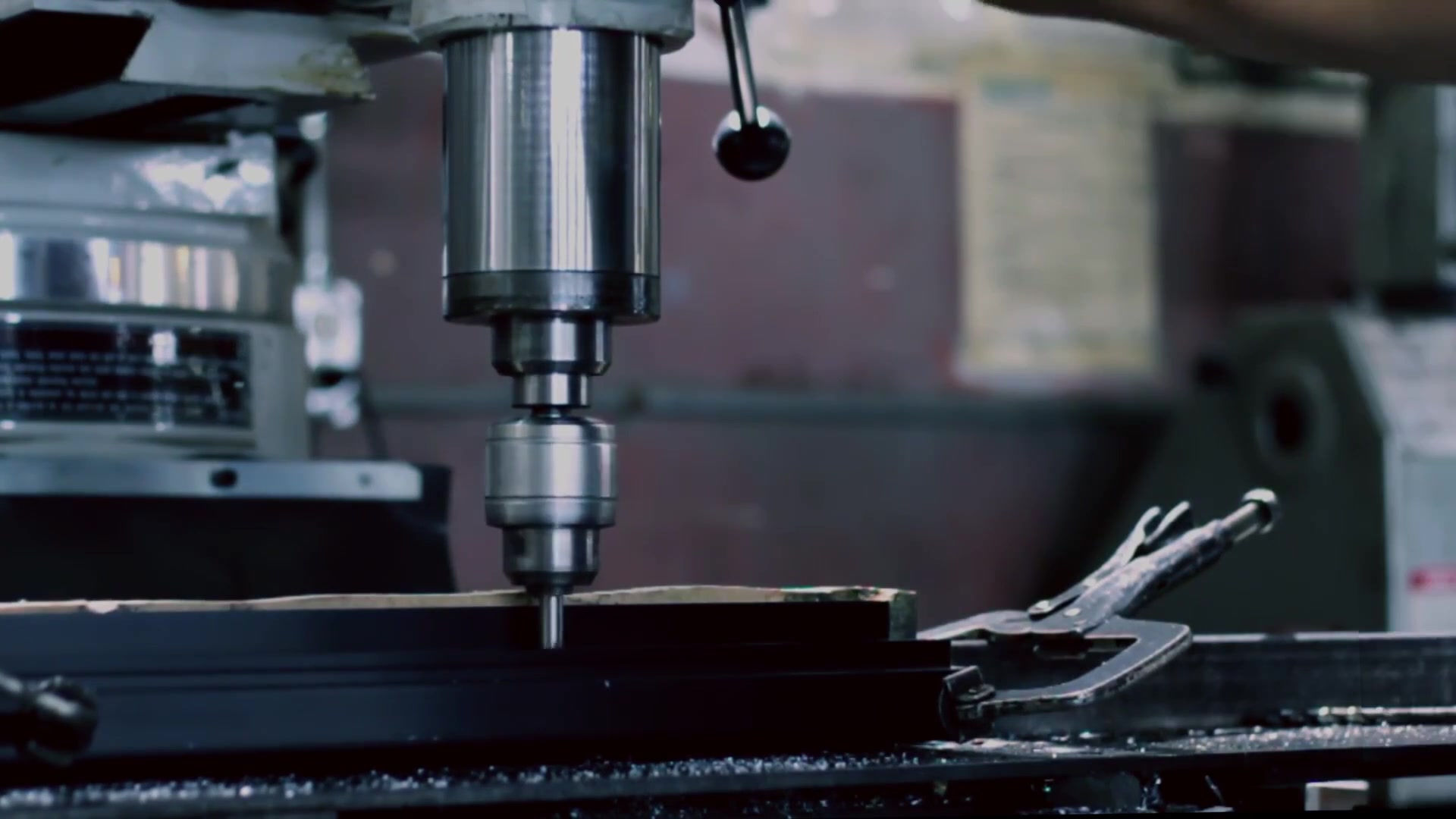
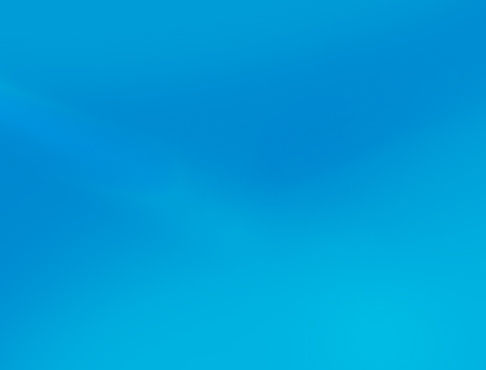
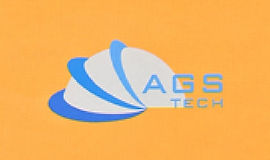
Глобальний індивідуальний виробник, інтегратор, консолідатор, аутсорсинговий партнер для широкого спектру продуктів і послуг.
Ми є вашим єдиним джерелом для виробництва, виготовлення, проектування, консолідації, інтеграції, аутсорсингу виготовлених на замовлення та готових продуктів і послуг.
Виберіть свою мову
-
Виготовлення на замовлення
-
Внутрішнє та глобальне контрактне виробництво
-
Аутсорсинг виробництва
-
Внутрішні та міжнародні закупівлі
-
Consolidation
-
Інженерна інтеграція
-
Інженерні послуги
Типи процесів КОВАННЯ МЕТАЛУ, які ми пропонуємо, включають гаряче та холодне штампування, відкриті штампування та закриті штампування, штампування та штампування без спалахів, cogging, фулінгування, окантовування та точне кування, майже чиста форма, заголовок , штампування, кування з висадкою, фрезерування металу, пресування та валкування, радіальне та орбітальне та кільце та ізотермічне кування, карбування, клепка, кування металевих кульок, проколювання металу, калібрування, кування з високим енергоспоживанням.
Наші методи ПОРОШКОВОЇ МЕТАЛУРГІЇ та ОБРОБКИ ПОРОШКУ включають пресування та спікання порошку, просочення, інфільтрацію, гаряче та холодне ізостатичне пресування, лиття під тиском, ущільнення валків, прокатку порошку, екструзію порошку, сипуче спікання, іскрове спікання, гаряче пресування.
Ми рекомендуємо вам натиснути тут, щоб
ЗАВАНТАЖИТИ наші схематичні ілюстрації процесів кування від AGS-TECH Inc.
ЗАВАНТАЖИТИ наші схематичні ілюстрації процесів порошкової металургії від AGS-TECH Inc.
Ці завантажувані файли з фотографіями та ескізами допоможуть вам краще зрозуміти інформацію, яку ми надаємо нижче.
Під час кування металу застосовуються сили стиснення, деформується матеріал і отримується необхідна форма. Найпоширенішими кованими матеріалами в промисловості є залізо та сталь, але багато інших, таких як алюміній, мідь, титан, магній, також широко куються. Ковані металеві деталі мають покращену зернисту структуру на додаток до герметичних тріщин і закритих порожніх просторів, тому міцність деталей, отриманих цим процесом, вища. Кування виготовляє деталі значно міцніші за свою вагу, ніж деталі, виготовлені литтям або механічною обробкою. Оскільки ковані деталі формуються шляхом приведення металу до остаточної форми, метал набуває спрямованої зернистої структури, що забезпечує високу міцність деталей. Іншими словами, деталі, отримані в процесі кування, демонструють кращі механічні властивості в порівнянні з простими литими або обробленими деталями. Вага металевих поковок може коливатися від невеликих легких деталей до сотень тисяч фунтів. Ми виготовляємо поковки здебільшого для механічно складних застосувань, де високі навантаження застосовуються до таких деталей, як автомобільні деталі, шестерні, робочі інструменти, ручні інструменти, вали турбін, мотоциклетний механізм. Оскільки витрати на інструменти та налаштування є відносно високими, ми рекомендуємо цей виробничий процес лише для великого виробництва та для невеликих обсягів, але високої вартості критичних компонентів, таких як аерокосмічне шасі. Крім вартості інструментів, час виготовлення великої кількості кованих деталей може бути довшим порівняно з деякими простими машинно обробленими деталями, але техніка має вирішальне значення для деталей, які вимагають надзвичайної міцності, як-от болти, гайки, спеціальне застосування кріплення, запчастини для автомобілів, навантажувачів, кранів.
• КОВКА ГАРЯЧОГО ШТАМПУ та ХОЛОДНОГО ШТАМПУ: гаряче кування, як випливає з назви, виконується при високих температурах, тому пластичність висока, а міцність матеріалу низька. Це полегшує деформацію та кування. Навпаки, холодне кування виконується при нижчих температурах і вимагає вищих зусиль, що призводить до зміцнення деформацією, кращої обробки поверхні та точності виготовлених деталей.
• КОВКА ВІДКРИТИМ штампом і штампом: при відкритому штампуванні штампи не обмежують стиснення матеріалу, тоді як при штампуванні порожнини всередині штампів обмежують потік матеріалу під час формування потрібної форми. КОВКА З ПЕРЕКЛАДАННЯМ або також званий КОВАННЯМ, що насправді не те саме, але дуже схожий процес, це процес відкритого штампування, де заготовку затискають між двома плоскими штампами, а сила стиснення зменшує її висоту. Оскільки висота is reduced, ширина заготовки збільшується. HEADING, процес кування осадкою включає циліндричну заготовку, яка висаджується на кінці, а її поперечний переріз локально збільшується. У заголовку матеріал подається через матрицю, кується, а потім розрізається на необхідну довжину. Операція здатна швидко виробляти велику кількість кріплень. Переважно це операція холодної обробки, оскільки вона використовується для виготовлення кінців цвяхів, кінців гвинтів, гайок і болтів, де матеріал потрібно зміцнити. Іншим процесом у відкритому штампі є ЗУБЧАННЯ, коли заготовку кують у ряд кроків, кожен з яких призводить до стиснення матеріалу та подальшого руху відкритої матриці вздовж заготовки. На кожному кроці товщина зменшується, а довжина трохи збільшується. Процес нагадує нервового учня, який дрібними кроками гризе свій олівець. Процес під назвою FULLERING — це ще один відкритий метод кування, який ми часто використовуємо як попередній етап для розподілу матеріалу в заготовці перед виконанням інших операцій кування металу. Ми використовуємо його, коли деталь вимагає кількох forging operations. В процесі роботи матриця з опуклою поверхнею деформується і викликає витікання металу в обидві сторони. З іншого боку, EDGING, подібний до обробки, включає відкриту матрицю з увігнутими поверхнями для деформації заготовки. Окантовка також є підготовчим процесом для наступних операцій кування, завдяки чому матеріал потік з обох сторін у зону в центрі. КОВКА ПІД ДИТМАННЯМ або ЗАКРИТА КОВАННЯ, як її ще називають, використовує матрицю/форму, яка стискає матеріал і обмежує його потік усередині себе. Матриця закривається, і матеріал приймає форму порожнини матриці/форми. ТОЧНЕ КОВУВАННЯ, процес, який потребує спеціального обладнання та прес-форми, виготовляє деталі без або з дуже незначним виплавленням. Іншими словами, деталі матимуть майже кінцеві розміри. У цьому процесі добре контрольована кількість матеріалу обережно вставляється та розміщується всередині форми. Ми застосовуємо цей метод для складних форм із тонкими перерізами, невеликими допусками та кутами осідання, а також коли кількість достатньо велика, щоб виправдати витрати на форму та обладнання.
• КОВКА БЕЗ ВСПЛАШУВАННЯ: заготівлю поміщають у матрицю таким чином, щоб жоден матеріал не міг витекти з порожнини, щоб утворити врізку. Таким чином, небажане обрізання спалаху не потрібне. Це процес точного кування, тому вимагає ретельного контролю кількості використовуваного матеріалу.
• ФОРМУВАННЯ МЕТАЛЮ або РАДІАЛЬНЕ КОВАННЯ: на заготовку по колу впливають штампи та кують. Оправка також може бути використана для кування внутрішньої геометрії заготовки. Під час обтискання деталь зазвичай отримує кілька ударів за секунду. Типовими виробами, виготовленими методом штампування, є інструменти із загостреним кінчиком, конічні стрижні, викрутки.
• ПРОКОЛЮВАННЯ МЕТАЛУ: ми часто використовуємо цю операцію як додаткову операцію при виготовленні деталей. Отвір або порожнина створюється проколюванням на поверхні заготовки без її прориву. Будь ласка, зверніть увагу, що проколювання відрізняється від свердління, яке призводить до наскрізного отвору.
• ФРЕЗЕРУВАННЯ: Пуансон з потрібною геометрією вдавлюється в оброблювану деталь і створює порожнину потрібної форми. Ми називаємо цей пунш HOB. Операція передбачає високий тиск і проводиться на холоді. В результаті матеріал піддається холодній обробці та зміцненню. Тому цей процес дуже підходить для виготовлення прес-форм, матриць і порожнин для інших виробничих процесів. Після виготовлення варильної панелі можна легко виготовити багато ідентичних порожнин, не обробляючи їх одну за одною.
• КОВКА ВАЛЦІВ або ФОРМУВАННЯ ВАЛЦІВ: два протилежні валки використовуються для формування металевої частини. Заготовка подається в валки, валки повертаються і втягують заготовку в зазор, потім заготовка подається через рифлену частину валків, і стискаючі сили надають матеріалу бажаної форми. Це не процес прокатки, а процес кування, оскільки це дискретна, а не безперервна операція. Геометрія на валках кує матеріал до необхідної форми та геометрії. Виконується в гарячому вигляді. Оскільки це процес кування, він виробляє деталі з видатними механічними властивостями, тому ми використовуємо його для виробництва автомобільних деталей, таких як вали, які потребують надзвичайної витривалості у важких робочих умовах.
• ОРБІТАЛЬНЕ КОВАННЯ: заготовку поміщають у порожнину ковальської форми та виковують верхньою матрицею, яка рухається по орбітальній траєкторії, коли обертається навколо похилої осі. Під час кожного оберту верхня матриця завершує дію стискаючої сили на всю заготовку. Повторюючи ці обороти кілька разів, виконується достатня кількість кування. Перевагами цієї технології виробництва є низький рівень шуму та низькі зусилля. Іншими словами, з невеликими зусиллями можна обертати важку матрицю навколо осі, щоб застосувати великий тиск до частини заготовки, яка контактує з матрицею. Деталі дискової або конічної форми іноді добре підходять для цього процесу.
• КОВКА КІЛЬЦЯ: ми часто використовуємо для виробництва безшовних кілець. Заготовка обрізається до потрібної довжини, вивертається, а потім проколюється до кінця, щоб створити центральний отвір. Потім його надягають на оправку, і ковальська матриця забиває його зверху, коли кільце повільно обертається до отримання бажаних розмірів.
• КЛЕПАННЯ: звичайний процес з’єднання деталей починається з прямої металевої деталі, яка вставляється в попередньо зроблені отвори крізь деталі. Після цього два кінці металевої частини виковуються шляхом стискання з’єднання між верхньою та нижньою матрицями.
• КАРБАННЯ: Ще один популярний процес, який виконується механічним пресом, який докладає великих зусиль на короткій відстані. Назва «карбування» походить від дрібних деталей, викуваних на поверхні металевих монет. Здебільшого це процес фінішної обробки виробу, коли на поверхнях утворюються дрібні деталі в результаті великої сили, що прикладається матрицею, яка передає ці деталі на заготовку.
• КОВАННЯ МЕТАЛЕВИХ КУЛЬК: Такі продукти, як кулькові підшипники, вимагають високоякісних точно виготовлених металевих кульок. В одній техніці під назвою КОСІЛЬНА ПРОКАТКА ми використовуємо два протилежні валки, які безперервно обертаються, коли матеріал безперервно подається в валки. На одному кінці двох валків металеві сфери викидаються як продукт. Другий спосіб кування металевої кульки полягає у використанні матриці, яка стискає заготовку матеріалу, розміщену між ними, набуваючи сферичну форму порожнини форми. Часто вироблені м’ячі вимагають деяких додаткових етапів, таких як фінішна обробка та полірування, щоб стати продуктом високої якості.
• ІЗОТЕРМІЧНЕ КУВАННЯ / ГАРЯЧЕ КОВАННЯ: Дорогий процес, який виконується лише тоді, коли співвідношення вигод/витрат виправдане. Процес гарячої обробки, при якому матриця нагрівається приблизно до тієї ж температури, що й заготовка. Оскільки температура матриці та виробу приблизно однакова, охолодження не відбувається, а характеристики текучості металу покращуються. Ця операція добре підходить для суперсплавів і матеріалів з нижчою ковкоздатністю та матеріалів, чий
механічні властивості дуже чутливі до малих температурних градієнтів і змін.
• КАЛІРМУВАННЯ МЕТАЛУ: це процес холодної обробки. Потік матеріалу необмежений у всіх напрямках, за винятком напрямку, в якому прикладена сила. У результаті виходить дуже гарна обробка поверхні та точні розміри.
• ВИСОКА ЕНЕРГЕТИЧНА ФОРМУВАННЯ: Техніка включає верхню форму, прикріплену до плеча поршня, який швидко штовхається, коли паливно-повітряна суміш запалюється свічкою запалювання. Це нагадує роботу поршнів у двигуні автомобіля. Форма дуже швидко вдаряється об деталь, а потім дуже швидко повертається у вихідне положення завдяки протитиску. Робота кується протягом кількох мілісекунд, тому у роботи немає часу охолонути. Це корисно для деталей, які важко кувати, які мають дуже чутливі до температури механічні властивості. Іншими словами, процес настільки швидкий, що деталь формується при постійній температурі протягом усього періоду, і не буде градієнтів температури на границях прес-форма/деталь.
• У КОВАННІ ШТАМПАМИ метал тиснуть між двома відповідними сталевими блоками зі спеціальними формами в них, які називаються штампами. Коли метал забивають між штампами, він приймає ту саму форму, що й форми в штампі. Коли він досягає остаточної форми, його виймають для охолодження. Цей процес виробляє міцні деталі точної форми, але вимагає більших інвестицій для спеціальних штампів. Кування осадкою збільшує діаметр шматка металу шляхом його сплющення. Зазвичай він використовується для виготовлення дрібних деталей, особливо для формування головок на кріпленнях, таких як болти та цвяхи.
• ПОРОШКОВА МЕТАЛУРГІЯ / ОБРОБКА ПОРОШКУ: як випливає з назви, це включає виробничі процеси для виготовлення твердих частин певної геометрії та форми з порошків. Якщо для цього використовуються металеві порошки, то це сфера порошкової металургії, а якщо використовуються неметалічні порошки, то це порошкова обробка. Суцільні деталі виготовляють із порошків шляхом пресування та спікання.
ПРЕСУВАННЯ ПОРОШКУ використовується для пресування порошків у бажану форму. Спочатку первинний матеріал фізично подрібнюють, розділяючи його на безліч дрібних окремих частинок. Порошкова суміш засипається в матрицю, і пуансон рухається до порошку та ущільнює його до потрібної форми. Здебільшого виконується при кімнатній температурі, при пресуванні порошку виходить тверда частина, яка називається зеленим компактом. Зв'язувальні та мастильні речовини зазвичай використовуються для підвищення компактності. Ми можемо виготовляти порошковий прес за допомогою гідравлічних пресів потужністю кілька тисяч тонн. Також у нас є преси подвійної дії з протилежними верхніми та нижніми пуансонами, а також преси з кількома діями для дуже складних геометрій деталей. Однорідність, яка є важливою проблемою для багатьох заводів порошкової металургії/порошкової обробки, не є великою проблемою для AGS-TECH через наш великий досвід виготовлення таких деталей на замовлення протягом багатьох років. Навіть із більш товстими деталями, де однорідність є проблемою, ми досягли успіху. Якщо ми візьмемо участь у вашому проекті, ми виготовимо ваші частини. Якщо ми побачимо будь-які потенційні ризики, ми повідомимо вас in
заздалегідь.
СПІКАННЯ ПОРОШКУ, яке є другим етапом, передбачає підвищення температури до певного ступеня та підтримку температури на цьому рівні протягом певного часу, щоб частинки порошку в спресованій частині могли з’єднатися разом. Це призводить до значно міцнішого з’єднання та зміцнення заготовки. Спікання відбувається близько до температури плавлення порошку. При спіканні відбувається усадка, підвищується міцність матеріалу, щільність, пластичність, теплопровідність, електропровідність. У нас є печі для спікання періодичної та безперервної дії. Однією з наших можливостей є регулювання рівня пористості деталей, які ми виготовляємо. Наприклад, ми можемо виготовляти металеві фільтри, зберігаючи деталі певною мірою пористими.
Використовуючи техніку, яка називається ПРОСОКУВАННЯ, ми заповнюємо пори в металі рідиною, такою як масло. Ми виробляємо, наприклад, просочені маслом підшипники, які є самозмащувальними. У процесі ІНФІЛЬТРАЦІЇ ми заповнюємо пори металу іншим металом з нижчою температурою плавлення, ніж основний матеріал. Суміш нагрівають до температури між температурами плавлення двох металів. В результаті можна отримати деякі особливі властивості. Ми також часто виконуємо допоміжні операції, такі як механічна обробка та кування деталей, виготовлених із порошку, коли потрібно отримати особливі характеристики чи властивості або коли деталь може бути виготовлена з меншою кількістю етапів процесу.
ІЗОСТАТИЧНЕ ПРЕСУВАННЯ: у цьому процесі тиск рідини використовується для ущільнення деталі. Металеві порошки поміщають у форму, виготовлену з герметичної гнучкої ємності. При ізостатичному пресуванні тиск прикладається з усіх боків, на відміну від осьового тиску, який спостерігається при звичайному пресуванні. Перевагами ізостатичного пресування є рівномірна щільність всередині деталі, особливо для більших або товстих деталей, чудові властивості. Його недоліком є довгий час циклу і відносно низька геометрична точність. ХОЛОДНЕ ІЗОСТАТИЧНЕ ПРЕСОВУВАННЯ здійснюється при кімнатній температурі, а гнучка форма виготовляється з гуми, ПВХ, уретану чи подібних матеріалів. Рідиною, яка використовується для створення тиску та ущільнення, є масло або вода. За цим слідує звичайне спікання зеленої пресовки. З іншого боку, ГАРЯЧЕ ІЗОСТАТИЧНЕ ПРЕСОВУВАННЯ здійснюється при високих температурах, а матеріалом форми є листовий метал або кераміка з достатньо високою температурою плавлення, яка стійка до високих температур. Рідина, що створює тиск, зазвичай є інертним газом. Операції пресування і спікання виконуються в один етап. Практично повністю усувається пористість, виходить однорідна зерниста структура. Перевага гарячого ізостатичного пресування полягає в тому, що він може виробляти деталі, подібні до комбінованого лиття та кування, одночасно роблячи можливим використання матеріалів, які не підходять для лиття та кування. Недоліком гарячого ізостатичного пресування є його велика тривалість циклу і, отже, вартість. Він підходить для критичних частин малого обсягу.
ЛИТТЯ ПИТАННЯМЕТАЛІВ: дуже підходить процес для виробництва складних деталей із тонкими стінками та детальною геометрією. Найкраще підходить для менших деталей. Порошки та полімерне сполучне змішують, нагрівають і вводять у форму. Полімерне сполучне покриває поверхні частинок порошку. Після формування сполучна речовина видаляється шляхом нагрівання при низькій температурі або розчиняється за допомогою розчинника.
УЩОКУВАННЯ В РУЛОНАХ / РУЛЬКУВАННЯ ПОРОШКУ: порошки використовуються для виробництва безперервних смуг або листів. Порошок подається з живильника і ущільнюється двома обертовими валками в листи або стрічки. Операція проводиться холодною. Лист переноситься в піч для спікання. Процес спікання можна повторити вдруге.
ЕКСТРУЗІЯ ПОРОШКУ: Деталі з великим відношенням довжини до діаметра виготовляються шляхом екструдування контейнера з тонкого листового металу з порошком.
РЕЗУЛЬТАТНЕ СПІКАННЯ: Як випливає з назви, це метод ущільнення та спікання без тиску, придатний для виготовлення дуже пористих деталей, таких як металеві фільтри. Порошок подається в порожнину форми без ущільнення.
РЕЗУЛЬТАТНЕ СПІКАННЯ: Як випливає з назви, це метод ущільнення та спікання без тиску, придатний для виготовлення дуже пористих деталей, таких як металеві фільтри. Порошок подається в порожнину форми без ущільнення.
ІСКРОВЕ СПІКАННЯ: порошок стискається у прес-формі двома протилежними пуансонами, і електричний струм високої потужності подається на пуансон і проходить через ущільнений порошок, затиснутий між ними. Сильний струм спалює поверхневі плівки з частинок порошку та спікає їх за допомогою тепла, що виділяється. Процес швидкий, оскільки тепло не подається ззовні, а генерується зсередини форми.
ГАРЯЧЕ ПРЕСОВУВАННЯ: порошки пресуються та спікаються за один етап у формі, яка витримує високі температури. Коли матриця ущільнюється, до неї піддається тепло порошку. Хороша точність і механічні властивості, досягнуті цим методом, роблять його привабливим варіантом. Навіть тугоплавкі метали можна обробляти за допомогою формових матеріалів, таких як графіт.