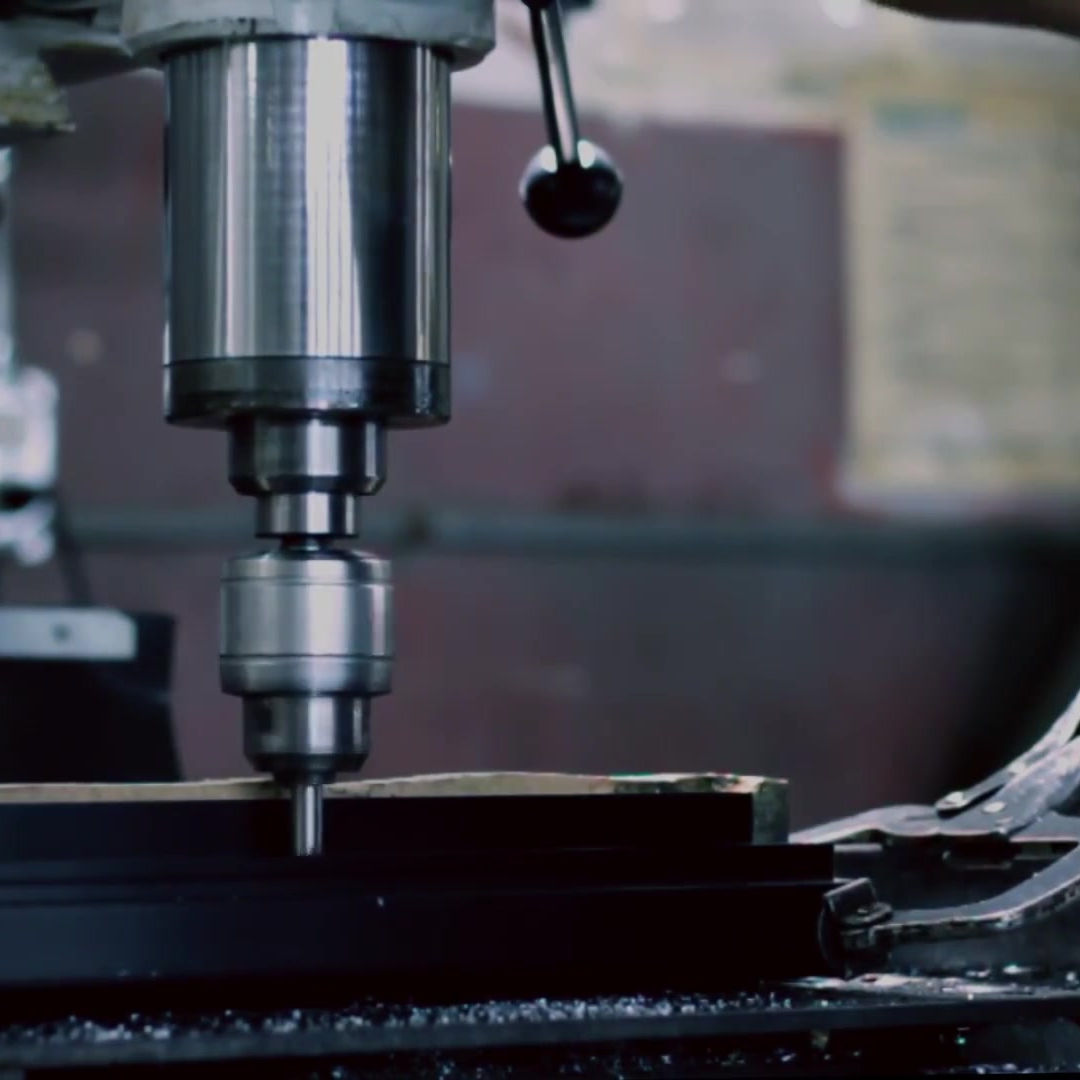
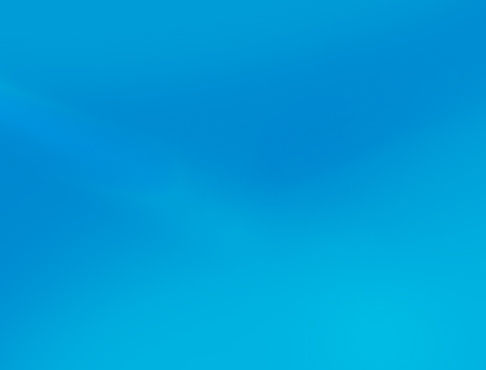
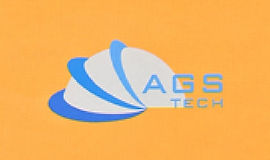
Глобальний індивідуальний виробник, інтегратор, консолідатор, аутсорсинговий партнер для широкого спектру продуктів і послуг.
Ми є вашим єдиним джерелом для виробництва, виготовлення, проектування, консолідації, інтеграції, аутсорсингу виготовлених на замовлення та готових продуктів і послуг.
Виберіть свою мову
-
Виготовлення на замовлення
-
Внутрішнє та глобальне контрактне виробництво
-
Аутсорсинг виробництва
-
Внутрішні та міжнародні закупівлі
-
Consolidation
-
Інженерна інтеграція
-
Інженерні послуги
Search Results
Знайдено 164 результати із порожнім запитом
- Transmission Components, Belts, Chains, Cable Drives, Pulleys,AGS-TECH
Transmission Components, Belts, Chains and Cable Drives, Conventional & Grooved or Serrated, Positive Drive, Pulleys Ремені, ланцюги та тросовий привод AGS-TECH Inc. пропонує вам компоненти для передачі енергії, включаючи ремені та ланцюги та кабельний привод. За роки вдосконалення наші гумові, шкіряні та інші ремінні передачі стали легшими та компактнішими, здатними переносити більші навантаження за менших витрат. Подібним чином наші ланцюгові передачі зазнали значного розвитку з часом і пропонують нашим клієнтам кілька переваг. Деякі переваги використання ланцюгових передач полягають у відносно необмежених відстанях між валами, компактністю, простотою збірки, пружністю при розтягуванні без ковзання або повзучості, здатністю працювати в середовищах з високими температурами. Наші кабельні приводи також пропонують такі переваги, як простота в деяких застосуваннях порівняно з іншими типами компонентів трансмісії. Доступні як стандартні ремінні, ланцюгові та тросові приводи, так і виготовлені та зібрані на замовлення версії. Ми можемо виготовити ці компоненти трансмісії потрібного розміру для вашого застосування та з найбільш підходящих матеріалів. РЕМНІ ТА РЕМНІ ПРИВОДИ: - Звичайні плоскі ремені: це прості плоскі ремені без зубців, канавок або зубців. Плоскі пасові передачі пропонують гнучкість, хорошу амортизацію, ефективну передачу потужності на високих швидкостях, стійкість до стирання та низьку вартість. Ремені можна зрощувати або з’єднувати для створення більших ременів. Інші переваги звичайних плоских пасів полягають у тому, що вони тонкі, вони не піддаються високим відцентровим навантаженням (що робить їх хорошими для високошвидкісних операцій з малими шківами). З іншого боку, вони створюють високі несучі навантаження, оскільки плоскі ремені потребують високого натягу. Іншими недоліками плоских пасових передач можуть бути ковзання, шумна робота та відносно нижча ефективність на низьких і помірних швидкостях роботи. У нас є два типи звичайних ременів: армовані та неармовані. Армовані пояси мають у своїй структурі елемент, що розтягується. Звичайні плоскі ремені випускаються у вигляді шкіри, прогумованої тканини або корду, неармованої гуми або пластику, тканини, армованої шкіри. Шкіряні ремені забезпечують тривалий термін служби, гнучкість, чудовий коефіцієнт тертя та легкість ремонту. Проте шкіряні ремені відносно дорогі, потребують обробки та чищення, і залежно від атмосфери вони можуть стискатися або розтягуватися. Ремені з прогумованої тканини або шнура стійкі до вологи, кислот і лугів. Ремені з прогумованої тканини складаються з шарів бавовни або синтетичного качука, просоченого гумою, і є найбільш економічними. Прогумовані кордові ремені складаються з ряду шарів просочених гумою шнурів. Прогумовані кордові ремені забезпечують високу міцність на розрив і невеликі розміри та масу. Неармовані гумові або пластикові ремені підходять для легких низькошвидкісних приводів. Неармовані гумові та пластикові ремені можна натягнути на їхні шківи. Пластикові неармовані ремені можуть передавати більшу потужність у порівнянні з гумовими. Посилені шкіряні ремені складаються з пластикового елемента, що розтягується, розміщеного між верхнім і нижнім шарами шкіри. Нарешті, наші тканинні пояси можуть складатися з одного шматка бавовни або качки, складеного та зшитого рядами поздовжніх стібків. Тканинні ремені здатні рівномірно рухатися та працювати на високій швидкості. - Рифлені або зубчасті ремені (наприклад, клинові ремені): це базові плоскі ремені, модифіковані для забезпечення переваг іншого типу продукту трансмісії. Це плоскі пояси з поздовжньою ребристою нижньою стороною. Поліклинові ремені — це плоский ремінь із поздовжніми канавками або зубцями з розтягнутим перетином і низкою суміжних V-подібних канавок для відстеження та стиснення. Потужність залежить від ширини стрічки. Клиновий ремінь є робочою конячкою промисловості. Він доступний у різноманітних стандартизованих розмірах і типах для передачі майже будь-якої потужності навантаження. Клинопасові приводи добре працюють при швидкості від 1500 до 6000 футів/хв, однак вузькі клинові паси працюватимуть до 10 000 футів/хв. Клинопасові передачі забезпечують тривалий термін служби, наприклад від 3 до 5 років, і мають високі коефіцієнти швидкості, їх легко встановлювати та демонтувати, пропонують тиху роботу, низькі витрати на технічне обслуговування, хорошу амортизацію між ремінним приводом і веденим валом. Недоліком клинових ременів є їх певне ковзання та повзання, тому вони можуть бути не найкращим рішенням там, де потрібні синхронні швидкості. У нас є промислові, автомобільні та сільськогосподарські ремені. Доступні ремені як стандартної довжини, так і нестандартної довжини. Усі стандартні перерізи клинових ременів доступні зі складу. Існують таблиці, у яких ви можете обчислити невідомі параметри, такі як довжина ременя, переріз ременя (ширина та товщина), якщо вам відомі деякі параметри вашої системи, такі як діаметри провідного та веденого шківів, міжцентрова відстань між шківами та швидкості обертання шківів. Ви можете скористатися такими таблицями або попросити нас вибрати правильний клиновий ремінь для вас. - Позитивні приводні паси (ремінь ГРМ): ці паси також плоского типу з низкою рівномірно розташованих зубців на внутрішній окружності. Позитивні приводні або зубчасті паси поєднують переваги плоских пасів із позитивними характеристиками зчеплення ланцюгів і передач. Позитивні приводні паси не виявляють ковзання або змін швидкості. Можливий широкий діапазон коефіцієнтів швидкості. Навантаження на підшипники низькі, тому що вони можуть працювати при низькій напрузі. Однак вони більш сприйнятливі до перекосів у шківах. - Шківи, шкиви, втулки для пасів: різні типи шківів використовуються з плоскими, ребристими (зубчастими) і позитивними приводними пасами. Ми виробляємо їх усі. Більшість наших плоских пасових шківів виготовляються шляхом лиття із заліза, але сталеві версії також доступні в різних комбінаціях обода та втулки. Наші шківи з плоским пасом можуть мати суцільні, зі спицями або роздільні втулки, або ми можемо виготовити їх за вашим бажанням. Ребристі та ремені позитивного приводу доступні в різних розмірах і ширині. Принаймні один шків у зубчастих пасових приводах має бути з фланцем, щоб утримувати ремінь на приводі. Для систем приводу з довгим центром рекомендується мати обидва шківи з фланцем. Шківи — це рифлені колеса шківів, які зазвичай виготовляються шляхом чавунного лиття, формування сталі або формування пластику. Формування сталі є придатним процесом для виробництва автомобільних та сільськогосподарських шкивів. Виготовляємо снопи із звичайними та глибокими канавками. Шківи з глибокими канавками добре підходять, коли клиновий ремінь входить у шків під кутом, як, наприклад, у чвертьобертових передачах. Глибокі канавки також добре підходять для приводів з вертикальним валом і застосувань, де вібрація ременів може бути проблемою. Наші натяжні шківи — це рифлені або плоскі шківи, які не служать для передачі механічної енергії. Натяжні шківи використовуються в основному для натягування пасів. - Одно- та багатопасові передачі: однопасові передачі мають одну канавку, тоді як багатопасові передачі мають кілька канавок. Натиснувши відповідний кольоровий текст нижче, ви можете завантажити наші каталоги: - Ремені передачі потужності (включаючи клинові ремені, зубчасті ремені, ремені з необробленими краями, ремені з обмоткою та спеціальні ремені) - Конвеєрні стрічки - V-подібні шківи - Шківи ГРМ ЛАНЦЮГИ ТА ЛАНЦЮГОВІ ПРИВОДИ: наші ланцюги передачі потужності мають деякі переваги, такі як відносно необмежена відстань між центрами валів, легке складання, компактність, еластичність під час розтягування без ковзання чи повзучості, здатність працювати за високих температур. Ось основні види наших мереж: - Знімні ланцюги: наші знімні ланцюги виготовляються в діапазоні розмірів, кроків і кінцевої міцності та, як правило, з ковкого чавуну або сталі. Ковкі ланцюги виготовляються в діапазоні розмірів від 0,902 (23 мм) до 4,063 дюйма (103 мм) кроку та кінцевої міцності від 700 до 17 000 фунтів на квадратний дюйм. З іншого боку, наші від’ємні сталеві ланцюги виготовляються з кроком від 0,904 дюйма (23 мм) до приблизно 3,00 дюйма (76 мм) із кінцевою міцністю від 760 до 5000 фунтів/квадратний дюйм._cc781905-5cde-3194-bb3b- 136bad5cf58d_ - Штифтові ланцюги: ці ланцюги використовуються для більших навантажень і трохи вищих швидкостей приблизно до 450 футів/хв (2,2 м/с). Штифтові ланцюги виготовлені з окремих литих ланок, які мають повний круглий кінець бочки зі зміщеними боковими планками. Ці ланки ланцюга з’єднані сталевими штифтами. Крок цих ланцюгів варіюється від приблизно 1,00 дюйма (25 мм) до 6,00 дюйма (150 мм) і граничної міцності від 3600 до 30 000 фунтів на квадратний дюйм. - Ланцюги зі зсувом бічної балки: вони популярні в приводних ланцюгах будівельних машин. Ці ланцюги працюють на швидкості до 1000 футів/хв і передають навантаження приблизно до 250 к.с. Зазвичай кожна ланка має дві зміщені бічні планки, одну втулку, один ролик, один штифт, шплінт. - Роликові ланцюги: доступні з кроком від 0,25 (6 мм) до 3,00 (75 мм) дюйма. Максимальна міцність роликових ланцюгів однієї ширини становить від 925 до 130 000 фунтів на квадратний дюйм. Доступні версії роликових ланцюгів різної ширини, які передають більшу потужність на вищих швидкостях. Роликові ланцюги різної ширини також забезпечують більш плавну роботу зі зниженим шумом. Роликові ланцюги збираються з роликових ланок і штифтових ланок. У роз’ємних роликових ланцюгах використовуються шплінти. Конструкція роликових ланцюгових передач вимагає предметних знань. У той час як пасові передачі базуються на лінійних швидкостях, ланцюгові передачі базуються на швидкості обертання меншої зірочки, яка в більшості установок є веденим елементом. Окрім потужності та швидкості обертання, конструкція ланцюгових передач базується на багатьох інших факторах. - Ланцюги з подвійним кроком: в основному те саме, що й роликові ланцюги, за винятком того, що крок у два рази довший. - Ланцюги з перевернутими зубцями (безшумні): високошвидкісні ланцюги, які використовуються переважно для приводів первинного двигуна та коробки відбору потужності. Перевернуті зубчасті ланцюгові передачі можуть передавати потужність до 1200 к.с. і складаються з ряду зубчастих ланок, по черзі зібраних або шпильками, або комбінацією з’єднаних компонентів. Центральний напрямний ланцюг має напрямні ланки для зачеплення канавок у зірочці, а бічний напрямний ланцюг має напрямні для зачеплення з боків зірочки. - Намистинний або повзунний ланцюги: ці ланцюги використовуються для низькошвидкісних приводів, а також у ручних операціях. Натиснувши відповідний кольоровий текст нижче, ви можете завантажити наші каталоги: - Привідні ланцюги - Конвеєрні ланцюги - Конвеєрні ланцюги великого кроку - Роликові ланцюги з нержавіючої сталі - Підйомні ланцюги - Мотоциклетні ланцюги - Ланцюги сільськогосподарських машин - Зірочки: наші стандартні зірочки відповідають стандартам ANSI. Пластинчасті зірочки — це плоскі зірочки без маточини. Наші малі та середні зірочки втулки виточуються з пруткової заготовки чи поковок або виготовляються шляхом зварювання втулки пруткової заготовки до гарячекатаного листа. AGS-TECH Inc. може постачати зірочки, виготовлені з чавунного лиття, литої сталі та зварних конструкцій втулки, спеченого порошкового металу, формованих або оброблених пластмас. Для плавної роботи на високих швидкостях необхідний правильний вибір розміру зірочок. Обмеження простору, звичайно, є фактором, який ми не можемо ігнорувати, вибираючи зірочку. Рекомендується, щоб співвідношення між ведучими та веденими зірочками було не більше 6:1, а кут намотування ланцюга на ведучому механізмі становив 120 градусів. Міжцентрові відстані між меншою та більшою зірочками, довжина ланцюга та натяг ланцюга також повинні бути обрані відповідно до деяких рекомендованих інженерних розрахунків та вказівок, а не випадково. Завантажте наші каталоги, натиснувши кольоровий текст нижче: - Зірочки та пластинчасті колеса - Втулки трансмісії - ланцюгова муфта - Ланцюгові замки КАБЕЛЬНІ ПРИВОДИ: у деяких випадках вони мають переваги перед пасовими та ланцюговими приводами. Кабельні приводи можуть виконувати ту саму функцію, що й ремені, а також можуть бути простішими та економічнішими для реалізації в деяких сферах застосування. Наприклад, нова серія Synchromesh Cable Drives розроблена для позитивної тяги, щоб замінити звичайні мотузки, прості троси та зубчасті приводи, особливо у вузьких місцях. Новий тросовий привід розроблено для забезпечення високоточного позиціонування в електронному обладнанні, такому як копіювальні машини, плотери, друкарські машинки, принтери тощо. Ключовою особливістю нового тросового приводу є його здатність використовуватися в тривимірних змієподібних конфігураціях, які дозволяють надзвичайно мініатюрні конструкції. Синхронізовані кабелі можна використовувати з меншим натягом порівняно з мотузками, що зменшує споживання електроенергії. Звертайтеся до компанії AGS-TECH, щоб отримати запитання та відгуки щодо ременів, ланцюгових та тросових передач. CLICK Product Finder-Locator Service ПОПЕРЕДНЯ СТОРІНКА
- Composites, Composite Materials Manufacturing, Fiber Reinforced
Composites, Composite Materials Manufacturing, Particle and Fiber Reinforced, Cermets, Ceramic & Metal Composite, Glass Fiber Reinforced Polymer, Lay-Up Process Виробництво композитів і композитних матеріалів Простіше кажучи, КОМПОЗИТИ або КОМПОЗИТНІ МАТЕРІАЛИ – це матеріали, що складаються з двох або кількох матеріалів з різними фізичними чи хімічними властивостями, але в поєднанні вони перетворюються на матеріал, який відрізняється від складових матеріалів. Ми повинні зазначити, що складові матеріали залишаються окремими та різними в структурі. Мета виробництва композитного матеріалу полягає в тому, щоб отримати продукт, який перевершує його складові та поєднує в собі бажані властивості кожного компонента. Як приклад; міцність, низька вага або низька ціна можуть бути мотиваторами розробки та виробництва композиту. Типи композитів, які ми пропонуємо, це зміцнені частинками композити, композити з армованою волокном, включаючи композити з керамічною матрицею/полімерною матрицею/метал-матрицею/вуглецево-вуглецеві/гібридні композити, структурні та ламіновані та сендвіч-структуровані композити та нанокомпозити. Технології виготовлення, які ми використовуємо у виробництві композитних матеріалів, це: пултрузія, процеси виробництва препрегів, розширене розміщення волокон, намотування ниток, індивідуальне розміщення волокон, процес укладання скловолокна розпиленням, тафтинг, процес ланксиду, z-піннінг. Багато композитних матеріалів складаються з двох фаз: матриці, яка є суцільною і оточує іншу фазу; і дисперсної фази, яка оточена матрицею. Ми рекомендуємо вам натиснути тут, щобЗАВАНТАЖИТИ наші схематичні ілюстрації виробництва композитів і композитних матеріалів компанією AGS-TECH Inc. Це допоможе вам краще зрозуміти інформацію, яку ми надаємо нижче. • КОМПОЗИТИ, ПОСИЛЕНІ ЧАСТИНКАМИ: Ця категорія складається з двох типів: композити з великими частинками та композити, зміцнені дисперсією. У першому типі взаємодії частинка-матриця не можна розглядати на атомному або молекулярному рівні. Натомість діє механіка континууму. З іншого боку, у дисперсно зміцнених композитах частинки, як правило, набагато менші в діапазоні десятків нанометрів. Прикладом великодисперсного композиту є полімери, до яких додано наповнювачі. Наповнювачі покращують властивості матеріалу і можуть замінити частину полімерного об'єму більш економічним матеріалом. Об'ємні частки двох фаз впливають на поведінку композиту. Композити з великими частинками використовуються з металами, полімерами та керамікою. CERMETS є прикладами композитів кераміка/метал. Наш найпоширеніший металокераміка - це твердий сплав. Він складається з вогнетривкої карбідної кераміки, наприклад частинок карбіду вольфраму, у матриці з такого металу, як кобальт або нікель. Ці твердосплавні композити широко використовуються як ріжучі інструменти для загартованої сталі. Частинки твердого сплаву відповідають за дію різання, а їх в'язкість підвищується за рахунок пластичної металевої матриці. Таким чином ми отримуємо переваги обох матеріалів в одному композиті. Іншим поширеним прикладом композиту з великими частинками, який ми використовуємо, є частинки сажі, змішані з вулканізованою гумою для отримання композиту з високою міцністю на розрив, міцністю, стійкістю до розриву та стирання. Прикладом дисперсно зміцненого композиту є метали і металеві сплави, зміцнені і зміцнені рівномірним диспергуванням дрібних частинок дуже твердого і інертного матеріалу. Коли дуже маленькі пластівці оксиду алюмінію додають до металевої алюмінієвої матриці, ми отримуємо спечений алюмінієвий порошок, який має підвищену міцність при високій температурі. • КОМПОЗИТИ, АРМОВАНІ ВОЛОКНАМИ: ця категорія композитів насправді є найважливішою. Метою, яку потрібно досягти, є висока міцність і жорсткість на одиницю ваги. Склад волокна, довжина, орієнтація та концентрація в цих композитах мають вирішальне значення для визначення властивостей і корисності цих матеріалів. Існує три групи волокон, які ми використовуємо: вуса, волокна та дроти. ВИСКИ — дуже тонкі і довгі монокристали. Вони є одними з найміцніших матеріалів. Деякими прикладами матеріалів для вусів є графіт, нітрид кремнію, оксид алюмінію. ВОЛОКНА, з іншого боку, в основному є полімерами або керамікою і знаходяться в полікристалічному або аморфному стані. Третя група - це тонкий ДРОТ, який має відносно великий діаметр і складається часто зі сталі або вольфраму. Прикладом армованого дротом композиту є автомобільні шини, які містять сталевий дріт усередині гуми. Залежно від матеріалу матриці ми маємо наступні композити: ПОЛІМЕРНО-МАТРИЧНІ КОМПОЗИТИ: виготовляються з полімерної смоли та волокон як армуючого інгредієнта. Підгрупа цих полімерних композитів, армованих скловолокном (GFRP), містить безперервні або розривні скляні волокна в полімерній матриці. Скло має високу міцність, економічність, легкість виготовлення волокон і хімічно інертне. Недоліками є їх обмежена твердість і жорсткість, робочі температури лише до 200-300 за Цельсієм. Скловолокно підходить для кузовів автомобілів і транспортного обладнання, кузовів морських транспортних засобів, складських контейнерів. Вони не підходять для аерокосмічної промисловості та виготовлення мостів через обмежену жорсткість. Інша підгрупа називається полімерним композитом, армованим вуглецевим волокном (CFRP). Тут вуглець є нашим волокнистим матеріалом у полімерній матриці. Вуглець відомий своїм високим питомим модулем і міцністю, а також здатністю підтримувати їх при високих температурах. Вуглецеві волокна можуть запропонувати нам стандартний, проміжний, високий і надвисокий модулі розтягування. Крім того, вуглецеві волокна мають різноманітні фізичні та механічні характеристики, а отже, підходять для різноманітних індивідуальних інженерних застосувань. Вуглепластикові композити можна розглядати для виготовлення спортивного та рекреаційного обладнання, посудин під тиском та аерокосмічних структурних компонентів. Ще одна підгрупа, полімерні композити, армовані арамідним волокном, також є високоміцними та модульними матеріалами. Їх співвідношення міцності до ваги надзвичайно високе. Арамідні волокна також відомі під торговими назвами KEVLAR і NOMEX. При розтягуванні вони працюють краще, ніж інші полімерні волокнисті матеріали, але вони слабкі при стисненні. Арамідні волокна міцні, стійкі до ударів, повзучості та втоми, стійкі до високих температур, хімічно інертні, за винятком сильних кислот і лугів. Арамідні волокна широко використовуються в спортивних товарах, бронежилетах, шинах, мотузках, оболонках оптоволоконних кабелів. Інші армуючі волокнисті матеріали існують, але використовуються в меншій мірі. В основному це бор, карбід кремнію, оксид алюмінію. З іншого боку, матеріал полімерної матриці також має вирішальне значення. Він визначає максимальну робочу температуру композиту, оскільки полімер зазвичай має нижчу температуру плавлення та деградації. В якості полімерної матриці широко використовуються поліефіри і вінілові ефіри. Також використовуються смоли, які мають відмінну вологостійкість і механічні властивості. Наприклад, поліімідна смола може використовуватися приблизно до 230 градусів за Цельсієм. КОМПОЗИТИ МЕТАЛУ І МАТРИЦІ: у цих матеріалах ми використовуємо пластичну металеву матрицю, і робочі температури зазвичай вищі, ніж їхні складові компоненти. У порівнянні з полімерно-матричними композитами, вони можуть мати вищі робочі температури, бути негорючими та можуть мати кращу стійкість до деградації від органічних рідин. Однак вони дорожчі. Зміцнюючі матеріали, такі як нитки, частинки, безперервні та розривні волокна; і широко використовуються такі матричні матеріали, як мідь, алюміній, магній, титан, суперсплави. Прикладом застосування є компоненти двигуна, виготовлені з матриці з алюмінієвого сплаву, посиленої оксидом алюмінію та вуглецевими волокнами. КЕРАМІЧНО-МАТРИЧНІ КОМПОЗИТИ: Керамічні матеріали відомі своєю надзвичайно хорошою високотемпературною надійністю. Однак вони дуже крихкі та мають низькі показники міцності на руйнування. Вбудовуючи частинки, волокна або волокна однієї кераміки в матрицю іншої, ми можемо отримувати композити з вищою в’язкістю до руйнування. Ці вбудовані матеріали в основному перешкоджають поширенню тріщини всередині матриці за допомогою деяких механізмів, таких як відхилення кінчиків тріщин або утворення містків через поверхні тріщин. Як приклад, оксид алюмінію, армований карбідними кристалами SiC, використовується як пластини для різання для обробки твердих металевих сплавів. Вони можуть продемонструвати кращі характеристики порівняно з цементованими карбідами. ВУГЛЕЦЕВО-ВУГЛЕЦЕВІ КОМПОЗИТИ: як армування, так і матриця є вуглецевими. Вони мають високі модулі розтягування та міцність при високих температурах понад 2000 за Цельсієм, опір повзучості, високу в’язкість до руйнування, низькі коефіцієнти теплового розширення, високу теплопровідність. Ці властивості роблять їх ідеальними для додатків, де потрібна стійкість до термічного удару. Однак недоліком вуглець-вуглецевих композитів є їх вразливість до окислення при високих температурах. Типовими прикладами використання є форми для гарячого пресування, виробництво передових компонентів турбінних двигунів. ГІБРИДНІ КОМПОЗИТИ: два або більше різних типів волокон змішані в одній матриці. Таким чином можна створити новий матеріал із комбінацією властивостей. Прикладом може бути те, що і вуглецеві, і скляні волокна включені в полімерну смолу. Вуглецеві волокна забезпечують жорсткість і міцність низької щільності, але коштують дорого. Скло, з іншого боку, недороге, але йому бракує жорсткості вуглецевих волокон. Скло-вуглецевий гібридний композит є міцнішим і міцнішим і може бути виготовлений за нижчою ціною. ОБРОБКА КОМПОЗИТІВ, АРМОВАНИХ ВОЛОКНАМИ: Для безперервних армованих волокнами пластмас з рівномірно розподіленими волокнами, орієнтованими в одному напрямку, ми використовуємо такі методи. PULTRUSION: Виготовляються прутки, балки та труби безперервної довжини та постійного поперечного перерізу. Рівниці безперервного волокна просочуються термореактивною смолою та протягуються через сталеву матрицю для попереднього формування бажаної форми. Далі вони проходять через прецизійну машинно-оброблену матрицю для набуття остаточної форми. Оскільки фільєра для затвердіння нагрівається, вона затверджує смоляну матрицю. Витягувачі витягують матеріал через матриці. Використовуючи вставлені порожнисті сердечники, ми можемо отримати труби та порожнисті геометричні форми. Метод пултрузії є автоматизованим і забезпечує високу продуктивність. Можливе виготовлення виробу будь-якої довжини. ПРОЦЕС ВИРОБНИЦТВА ПРЕПРЕГІВ: Препрег — це армування безперервним волокном, попередньо просочене частково затверділою полімерною смолою. Він широко використовується для конструкційних застосувань. Матеріал постачається у формі стрічки та поставляється у вигляді стрічки. Виробник формує його безпосередньо та повністю твердить без необхідності додавання смоли. Оскільки препреги затвердіють при кімнатній температурі, їх зберігають при 0 за Цельсієм або нижчих температурах. Після використання стрічки, що залишилися, зберігаються при низьких температурах. Використовуються термопластичні та термореактивні смоли, звичайні армуючі волокна з вуглецю, араміду та скла. Для використання препрегів спочатку видаляється папір-підкладка, а потім виконується виготовлення шляхом укладання стрічки препрега на оброблену поверхню (процес накладання). Для отримання потрібної товщини можна накласти кілька шарів. Частою практикою є чергування орієнтації волокон для виготовлення ламінату з перехресним або кутовим шаром. Нарешті для затвердіння застосовують тепло і тиск. Як ручна обробка, так і автоматизовані процеси використовуються для різання препрегів і укладання. НАМОТКА НИТКИ: безперервні армуючі волокна точно розташовані за заздалегідь визначеною схемою, щоб слідувати порожнистій і зазвичай круглій формі. Волокна спочатку проходять через смоляну ванну, а потім автоматизованою системою намотуються на оправку. Після кількох повторень намотування досягається необхідна товщина, і затвердіння відбувається при кімнатній температурі або в печі. Тепер оправку видаляють і виріб виймають з форми. Намотування ниток може запропонувати дуже високе співвідношення міцності до ваги, намотуючи волокна по окружності, спіралі та полярності. За цією технікою виготовляють труби, баки, корпуси. • СТРУКТУРНІ КОМПОЗИТИ: як правило, вони складаються як з однорідних, так і з композитних матеріалів. Тому їх властивості визначаються складовими матеріалами та геометричним дизайном їх елементів. Ось основні види: ЛАМІНАРНІ КОМПОЗИТИ: ці конструкційні матеріали виготовлені з двовимірних листів або панелей із переважними напрямками високої міцності. Шари укладаються і скріплюються між собою. Чергуючи напрямки високої міцності в двох перпендикулярних осях, ми отримуємо композит, який має високу міцність в обох напрямках у двовимірній площині. Регулюючи кути шарів, можна виготовити композит з міцністю в бажаних напрямках. Сучасні лижі виготовляються таким чином. СЕНДВІЧ-ПАНЕЛІ: ці конструкційні композити легкі, але мають високу жорсткість і міцність. Сендвіч-панелі складаються з двох зовнішніх листів, виготовлених із жорсткого та міцного матеріалу, такого як алюмінієві сплави, армований волокном пластик або сталь, і серцевини між зовнішніми листами. Серцевина повинна бути легкою і здебільшого мати низький модуль пружності. Популярними основними матеріалами є жорсткі пінополімери, дерево та стільники. Сендвіч-панелі широко використовуються в будівельній галузі як покрівельний матеріал, матеріал для підлоги або стін, а також в аерокосмічній промисловості. • НАНОКОМПОЗИТИ: ці нові матеріали складаються з частинок нанорозміру, вбудованих у матрицю. Використовуючи нанокомпозити, ми можемо виготовляти гумові матеріали, які є дуже хорошими бар’єрами для проникнення повітря, зберігаючи при цьому їхні гумові властивості незмінними. CLICK Product Finder-Locator Service ПОПЕРЕДНЯ СТОРІНКА
- Machine Elements Manufacturing, Gears, Gear Drives, Bearings, Keys, Splines
Machine Elements Manufacturing, Gears, Gear Drives, Bearings, Keys, Splines, Pins, Shafts, Seals, Fasteners, Clutch, Cams, Followers, Belts, Couplings, Shafts Виготовлення елементів машин Детальніше Ремені, ланцюги та тросовий привод Детальніше Зубчасті колеса та зубчастий привод Детальніше Виробництво муфт і підшипників Детальніше Виробництво ключів, шліців і шпильок Детальніше Виробництво кулачків, слідуючих механізмів, зв’язок і храпових коліс Детальніше Виготовлення валів Детальніше Виробництво торцевих ущільнень Детальніше Зчеплення та гальма в зборі Детальніше Виробництво кріплень Детальніше Складання Simple Machines ЕЛЕМЕНТИ МАШИНИ є елементарними складовими машини. Ці елементи складаються з трьох основних типів: 1.) Структурні компоненти, включаючи елементи рами, підшипники, осі, шліци, кріплення, ущільнення та мастила. 2.) Механізми, що контролюють рух різними способами, такі як зубчасті передачі, ремінні або ланцюгові передачі, зв’язки, системи кулачка та слідкуючої системи, гальма та зчеплення. 3.) Компоненти керування, такі як кнопки, перемикачі, індикатори, датчики, приводи та комп’ютерні контролери. Більшість машинних елементів, які ми пропонуємо вам, стандартизовані до загальних розмірів, але також доступні спеціальні машинні елементи для ваших спеціалізованих застосувань. Налаштування елементів машини може відбуватися на основі існуючих конструкцій, які є в наших каталогах, які можна завантажити, або на абсолютно нових конструкціях. Створення прототипів і виготовлення елементів машини може бути продовжено після схвалення проекту обома сторонами. Якщо потрібно спроектувати та виготовити нові елементи машини, наші клієнти або надсилають нам власні креслення, і ми розглядаємо їх для затвердження, або вони просять нас розробити елементи машини для їх застосування. В останньому випадку ми використовуємо всі дані наших клієнтів, розробляємо елементи машини та надсилаємо завершені креслення нашим клієнтам для затвердження. Після затвердження ми виготовляємо перші вироби, а потім виготовляємо елементи машини відповідно до остаточного проекту. На будь-якому етапі цієї роботи, якщо конструкція певного елемента машини незадовільно працює в польових умовах (що буває рідко), ми переглядаємо весь проект і за потреби спільно з нашими клієнтами вносимо зміни. Нашою стандартною практикою є підписання угод про нерозголошення (NDA) з нашими клієнтами щодо проектування елементів машини чи будь-якого іншого продукту, коли це необхідно чи потрібно. Після того, як елементи машини для конкретного клієнта розроблено та виготовлено на замовлення, ми присвоюємо йому код продукту та виробляємо та продаємо їх лише нашому клієнту, якому належить продукт. Ми відтворюємо елементи машин за допомогою розроблених інструментів, форм і процедур стільки разів, скільки потрібно, і щоразу, коли наш клієнт їх повторно замовляє. Іншими словами, після того, як індивідуальний елемент машини розроблено та виготовлено для вас, інтелектуальна власність, а також усі інструменти та прес-форми зарезервовані та зберігаються на невизначений термін для вас, а продукти відтворюються за вашим бажанням. Ми також пропонуємо нашим клієнтам послуги з інжинірингу, творчо поєднуючи елементи машини в компонент або вузол, який відповідає застосуванню та відповідає або перевершує очікування наших клієнтів. Заводи, що виготовляють наші елементи машин, сертифіковані відповідно до ISO9001, QS9000 або TS16949. Крім того, більшість наших продуктів мають позначку CE або UL і відповідають міжнародним стандартам, таким як ISO, SAE, ASME, DIN. Клацніть підменю, щоб отримати детальну інформацію про елементи нашої машини, зокрема: - Ремені, ланцюги та тросові приводи - Шестерні та зубчасті приводи - Муфти та підшипники - Ключі, шліци та шпильки - Кулачки та зв'язки - Вали - Механічні ущільнення - Промислове зчеплення та гальмо - Кріплення - Прості машини Ми підготували довідкову брошуру для наших клієнтів, конструкторів і розробників нових виробів, в тому числі елементів машин. Ви можете ознайомитися з деякими загальновживаними термінами в проектуванні компонентів машини: Завантажте брошуру з загальними термінами машинобудування, які використовуються дизайнерами та інженерами Наші машинні елементи знаходять застосування в різноманітних галузях, таких як промислове обладнання, системи автоматизації, випробувальне та метрологічне обладнання, транспортне обладнання, будівельні машини та практично будь-де, де ви тільки можете подумати. AGS-TECH розробляє та виготовляє елементи машин з різних матеріалів залежно від застосування. Матеріали, які використовуються для елементів машин, можуть варіюватися від формованого пластику для іграшок до загартованої сталі зі спеціальним покриттям для промислового обладнання. Наші дизайнери використовують сучасне професійне програмне забезпечення та інструменти проектування для розробки елементів машин, враховуючи такі деталі, як кути в зубах шестерень, напруги, інтенсивність зношування тощо. Будь ласка, прокрутіть наші підменю та завантажте наші брошури та каталоги продуктів, щоб дізнатися, чи можете ви знайти готові елементи машини для свого застосування. Якщо ви не можете знайти відповідний варіант для свого застосування, повідомте нам, і ми разом з вами розробимо та виготовимо елементи машини, які відповідатимуть вашим потребам. Якщо ви зацікавлені в наших інженерних і дослідницьких можливостях, а не у виробничих можливостях, тоді ми запрошуємо вас відвідати наш веб-сайт http://www.ags-engineering.com де ви можете знайти більш детальну інформацію про наш дизайн, розробку продукту, розробку процесів, інженерно-консультаційні послуги тощо CLICK Product Finder-Locator Service ПОПЕРЕДНЯ СТОРІНКА
- Joining & Assembly & Fastening Processes, Welding, Brazing, Soldering
Joining & Assembly & Fastening Processes, Welding, Brazing, Soldering, Sintering, Adhesive Bonding, Press Fitting, Wave and Reflow Solder Process, Torch Furnace Процеси з'єднання, складання та кріплення Ми з’єднуємо, збираємо та скріплюємо виготовлені вами деталі та перетворюємо їх у готові вироби чи напівфабрикати за допомогою ЗВАРЮВАННЯ, ПАЯННЯ, СПІКАННЯ, КЛЕЄННЯ, КРИПЛЕННЯ, ПРЕСОВОГО ФІТИНГУВАННЯ. Деякі з наших найпопулярніших процесів зварювання: дугове зварювання, зварювання кисневим газом, зварювання опором, проекційне зварювання, шовне зварювання, висадка, ударне зварювання, зварювання в твердому тілі, зварювання електронним променем, лазерне, термітне та індукційне зварювання. Наші популярні процеси пайки – пайка в факелі, індукція, печі та пайка зануренням. Наші методи пайки: залізо, гаряча плита, духовка, індукція, занурення, хвиля, оплавлення та ультразвукова пайка. Для клейового склеювання ми часто використовуємо термопласти та термореактивні, епоксидні, фенольні, поліуретанові, клейові сплави, а також деякі інші хімікати та стрічки. Нарешті, наші процеси кріплення складаються з прибивання цвяхів, закручування гвинтів, гайок і болтів, заклепок, закріплення, закріплення шпильками, зшивання та скобування, а також запресовування. • ЗВАРЮВАННЯ: зварювання передбачає з’єднання матеріалів шляхом плавлення заготовок і введення наповнювачів, які також з’єднують розплавлену зварювальну ванну. Коли ділянка охолоне, ми отримаємо міцний стик. У деяких випадках застосовується тиск. На відміну від зварювання, операції паяння твердим припоєм передбачають лише плавлення матеріалу з нижчою температурою плавлення між заготовками, а заготовки не плавляться. Ми рекомендуємо вам натиснути тут, щобЗАВАНТАЖИТИ наші схематичні ілюстрації зварювальних процесів від AGS-TECH Inc. Це допоможе вам краще зрозуміти інформацію, яку ми надаємо нижче. У ДУГОВОМУ ЗВАРЮВАННІ ми використовуємо джерело живлення та електрод для створення електричної дуги, яка плавить метали. Місце зварювання захищене захисним газом, парою чи іншим матеріалом. Цей процес популярний для зварювання автомобільних деталей і сталевих конструкцій. При дуговому зварюванні в закритому режимі (SMAW), або також відомому як стрижневе зварювання, стрижень електрода наближається до основного матеріалу, і між ними генерується електрична дуга. Стрижень електрода плавиться і виконує роль наповнювача. Електрод також містить флюс, який діє як шар шлаку та виділяє пари, які діють як захисний газ. Вони захищають зону зварювання від забруднення навколишнього середовища. Інші наповнювачі не використовуються. Недоліками цього процесу є його повільність, необхідність частої заміни електродів, необхідність відколу залишків шлаку, що утворюється від флюсу. Ряд металів, таких як залізо, сталь, нікель, алюміній, мідь… тощо. Можна зварювати. Його перевагами є недорогі інструменти та простота використання. Газове дугове зварювання металом (GMAW), також відоме як метал-інертний газ (MIG), ми маємо безперервну подачу наповнювача електродного дроту та інертного або частково інертного газу, який обтікає дріт проти забруднення навколишнього середовища області зварювання. Можна зварювати сталь, алюміній та інші кольорові метали. Перевагами MIG є висока швидкість зварювання і хороша якість. Недоліками є його складне обладнання та проблеми, які виникають у вітряному зовнішньому середовищі, оскільки ми повинні підтримувати стабільність захисного газу навколо зони зварювання. Різновидом GMAW є дугове зварювання порошковим сердечником (FCAW), яке складається з тонкої металевої труби, заповненої флюсовими матеріалами. Іноді флюсу всередині трубки достатньо для захисту від забруднення навколишнього середовища. Дугове зварювання під флюсом (SAW) – широко автоматизований процес, який передбачає безперервну подачу дроту та дугу, яка запалюється під шаром флюсу. Продуктивність і якість високі, зварювальний шлак легко відходить, а робоче середовище вільне від диму. Недоліком є те, що його можна використовувати лише для зварювання деталей у певних положеннях. Під час дугового зварювання вольфрамовим газом (GTAW) або зварювання вольфрамом в інертному газі (TIG) ми використовуємо вольфрамовий електрод разом із окремим наповнювачем та інертними або майже інертними газами. Як ми знаємо, вольфрам має високу температуру плавлення, і це дуже придатний метал для дуже високих температур. Вольфрам у TIG не витрачається, на відміну від інших описаних вище методів. Повільна, але високоякісна техніка зварювання, яка має перевагу перед іншими методами зварювання тонких матеріалів. Підходить для багатьох металів. Плазмодугове зварювання схоже, але для створення дуги використовується плазмовий газ. Дуга при плазмово-дуговому зварюванні є відносно більш концентрованою порівняно з GTAW і може використовуватися для більш широкого діапазону товщини металу на набагато вищих швидкостях. GTAW і плазмове дугове зварювання можна застосовувати до більш-менш однакових матеріалів. КИСНЕВО-ПАЛИВНЕ / OXYFUEL WELDING також називається оксиацетиленове зварювання, кисневе зварювання, газове зварювання здійснюється з використанням газового палива і кисню для зварювання. Оскільки не використовується електроенергія, він портативний і може використовуватися там, де немає електрики. За допомогою зварювального пальника ми нагріваємо деталі та наповнювач для отримання спільної ванни розплавленого металу. Можна використовувати різні види палива, такі як ацетилен, бензин, водень, пропан, бутан… тощо. У кисневому зварюванні ми використовуємо два контейнери, один для палива, а інший для кисню. Кисень окислює паливо (спалює його). КОНТРОЛЬНЕ ЗВАРЮВАННЯ: Цей тип зварювання використовує переваги джоулевого нагрівання, і тепло генерується в місці, де протягом певного часу подається електричний струм. Через метал пропускаються великі струми. У цьому місці утворюються басейни розплавленого металу. Методи контактного зварювання популярні завдяки їх ефективності, малому потенціалу забруднення. Однак недоліками є відносно значні витрати на обладнання та властиве обмеження щодо відносно тонких деталей. ТОЧКОВЕ ЗВАРЮВАННЯ є одним з основних видів контактного зварювання. Тут ми з’єднуємо два або більше листів або деталей, що перекриваються, за допомогою двох мідних електродів, щоб скріпити листи разом і пропускати через них великий струм. Матеріал між мідними електродами нагрівається, і в цьому місці утворюється розплавлена купа. Після цього струм припиняється, а наконечники мідних електродів охолоджують місце зварювання, оскільки електроди охолоджуються водою. Застосування потрібної кількості тепла до потрібного матеріалу та товщини є ключовим для цієї техніки, тому що при неправильному застосуванні з’єднання буде слабким. Перевагами точкового зварювання є відсутність суттєвої деформації заготовок, енергоефективність, легкість автоматизації та видатна продуктивність, а також відсутність потреби в наповнювачах. Недоліком є те, що оскільки зварювання відбувається точково, а не утворює суцільний шов, загальна міцність може бути відносно нижчою порівняно з іншими методами зварювання. ШОВНЕ ЗВАРЮВАННЯ, з іншого боку, утворює зварні шви на стикаються поверхнях подібних матеріалів. Шов може бути встик або внахлест. Зварювання швів починається з одного кінця і поступово переходить до іншого. Цей метод також використовує два електроди з міді для подачі тиску та струму на область зварювання. Електроди у формі диска обертаються з постійним контактом уздовж лінії шва і створюють безперервний зварний шов. Тут також електроди охолоджуються водою. Зварні шви дуже міцні та надійні. Інші методи - це проекція, спалах і методи зварювання з висадкою. ТВЕРДОТІЛЬНЕ ЗВАРЮВАННЯ дещо відрізняється від попередніх методів, описаних вище. Коалесценція відбувається при температурах нижче температури плавлення з'єднаних металів і без використання металевого наповнювача. У деяких процесах може використовуватися тиск. Різноманітними методами є СПІВЕКСТРУЗІЙНЕ ЗВАРЮВАННЯ, коли різнорідні метали екструдуються через один і той же прес-форму, ХОЛОДНЕ ЗВАРЮВАННЯ ПІД ТИСКОМ, де ми з’єднуємо м’які сплави з температурою нижче їхньої температури плавлення, ДИФУЗІЙНЕ ЗВАРЮВАННЯ без видимих ліній зварювання, ЗВАРЮВАННЯ ВИБУХОМ для з’єднання різнорідних матеріалів, наприклад, корозійностійких сплавів із конструкційними сталей, ЕЛЕКТРОМАГНІТНО-ІМПУЛЬСНЕ ЗВАРЮВАННЯ, де ми прискорюємо труби та листи електромагнітними силами, КОВАСЬКЕ ЗВАРЮВАННЯ, яке полягає в нагріванні металів до високих температур і збивання їх разом, ЗВАРЮВАННЯ ТЕРТТЕМ, де виконується зварювання тертям, ЗВАРЮВАННЯ ТЕРТТЕМ З ПЕРЕМІШУВАННЯМ, яке передбачає обертання без витратний інструмент, що перетинає лінію з’єднання, ГАРЯЧЕ ЗВАРЮВАННЯ ТИСКОМ, коли ми стискаємо метали разом за підвищених температур, нижчих за температуру плавлення, у вакуумі чи в інертних газах, ГАРЯЧЕ ЗВАРЮВАННЯ ТИСКОМ ІЗОСТАТИЧНОГО ТИСКУ, при якому ми застосовуємо тиск за допомогою інертних газів усередині посудини, РОЛКОВЕ ЗВАРЮВАННЯ, де ми з’єднуємо різнорідні матеріали, вставляючи їх між собою два обертових колеса, УЛЬТРАЗВУКОВЕ ЗВАРЮВАННЯ, де тонкі металеві або пластикові листи зварюються за допомогою високочастотної вібраційної енергії. Іншими нашими зварювальними процесами є ЕЛЕКТРОННО-ПРОМЕНЕВЕ ЗВАРЮВАННЯ з глибоким проплавленням і швидкою обробкою, але оскільки це дорогий метод, ми вважаємо його для особливих випадків, ЕЛЕКТРОШЛАКОВЕ ЗВАРЮВАННЯ метод, який підходить лише для важких товстих листів і заготовок зі сталі, ІНДУКЦІЙНЕ ЗВАРЮВАННЯ, де ми використовуємо електромагнітну індукцію та нагрівання наших електропровідних або феромагнітних заготовок, ЛАЗЕРНЕ ПРОМЕНЕВЕ ЗВАРЮВАННЯ також із глибоким проплавленням і швидкою обробкою, але дорогий метод, ЛАЗЕРНЕ ГІБРИДНЕ ЗВАРЮВАННЯ, яке поєднує LBW з GMAW в одній зварювальній головці та здатне перекрити проміжки 2 мм між пластинами, УДАРНЕ ЗВАРЮВАННЯ, що передбачає електричний розряд з подальшим куванням матеріалів із прикладеним тиском, ТЕРМІТНЕ ЗВАРЮВАННЯ, що включає екзотермічну реакцію між порошками оксиду алюмінію та заліза., ЕЛЕКТРОГАЗОВЕ ЗВАРЮВАННЯ плавкими електродами, яке використовується лише зі сталлю у вертикальному положенні, і, нарешті, ДУГОВЕ ЗВАРЮВАННЯ ШПИЛЬЦІ для приєднання шпильки до основи матеріал з теплом і тиском. Ми рекомендуємо вам натиснути тут, щобЗАВАНТАЖИТИ наші схематичні ілюстрації процесів паяння твердим припоєм і адгезивного склеювання від AGS-TECH Inc. Це допоможе вам краще зрозуміти інформацію, яку ми надаємо нижче. • ПАЯННЯ : ми з’єднуємо два або більше металів, нагріваючи присадки між ними вище точки плавлення та використовуючи капілярну дію для розподілу. Процес подібний до паяння, але температури, пов’язані з розплавленням наповнювача, вищі під час пайки. Як і при зварюванні, флюс захищає присадний матеріал від атмосферного забруднення. Після охолодження заготовки з'єднуються між собою. Процес включає в себе наступні ключові етапи: хороше підгонку та зазор, належне очищення основних матеріалів, належне кріплення, правильний вибір флюсу та атмосфери, нагрівання вузла та, нарешті, очищення паяного вузла. Деякі з наших процесів пайки — це пайка з факелом, популярний метод, який виконується вручну або автоматизованим способом. Підходить для невеликих виробничих замовлень і спеціальних випадків. Нагрівання подається за допомогою газового полум’я поблизу спаюваного з’єднання. ПАЯННЯ В ПЕЧІ вимагає меншої кваліфікації оператора та є напівавтоматичним процесом, придатним для масового промислового виробництва. Як контроль температури, так і контроль атмосфери в печі є перевагами цієї техніки, тому що перший дозволяє нам мати контрольовані теплові цикли та усунути локальне нагрівання, як у випадку з паянням факелом, а другий захищає деталь від окислення. Використовуючи відсадку, ми здатні знизити витрати на виробництво до мінімуму. Недоліками є високе енергоспоживання, вартість обладнання та більш складні міркування щодо конструкції. ВАКУУМНЕ ПАЯННЯ відбувається у вакуумній печі. Однорідність температури підтримується, і ми отримуємо безфлюсові, дуже чисті з’єднання з дуже невеликими залишковими напругами. Термічна обробка може відбуватися під час вакуумної пайки через низькі залишкові напруги, присутні під час повільних циклів нагрівання та охолодження. Основним недоліком є його висока вартість, оскільки створення вакуумного середовища є дорогим процесом. Ще одна технологія DIP BRAZING з’єднує нерухомі деталі, де пайка наноситься на сполучувані поверхні. Після цього фіксовані частини занурюють у ванну з розплавленою сіллю, такою як хлорид натрію (кухонна сіль), яка діє як теплоносій і флюс. Повітря виключається, тому не відбувається утворення оксиду. При ІНДУКЦІЙНОМУ ПАЯННІ ми з’єднуємо матеріали за допомогою присадного металу, який має нижчу температуру плавлення, ніж основні матеріали. Змінний струм від індукційної котушки створює електромагнітне поле, яке індукує індукційний нагрів переважно магнітних матеріалів із заліза. Метод забезпечує селективне нагрівання, хороші з’єднання з наповнювачем, що тече тільки в потрібних областях, невелике окислення, оскільки немає полум’я, і швидке охолодження, швидке нагрівання, консистенцію та придатність для виробництва великих обсягів. Щоб пришвидшити наші процеси та забезпечити послідовність, ми часто використовуємо преформи. Інформацію про наш паяльний завод, який виготовляє фітинги з кераміки та металу, герметичне ущільнення, вакуумні канали, компоненти для контролю високого та надвисокого вакууму та рідини можна знайти тут: Брошура паяльного заводу • ПАЯННЯ: під час пайки ми маємо не плавлення заготовок, а присадковий метал з нижчою температурою плавлення, ніж з’єднувані деталі, який вливається в з’єднання. Припайний метал плавиться при нижчій температурі, ніж при пайці. Ми використовуємо безсвинцеві сплави для паяння та відповідаємо RoHS, а для різних застосувань і вимог у нас є різні відповідні сплави, наприклад срібний сплав. Пайка пропонує нам з’єднання, які не пропускають газ і рідину. У М’ЯКОМУ ПАЯННІ температура плавлення нашого припою нижче 400 за Цельсієм, тоді як у СРІБНОМУ ПАЯННІ та ПАЯННІ нам потрібні вищі температури. М’яке паяння використовує нижчі температури, але не забезпечує міцних з’єднань для вимогливих застосувань при підвищених температурах. З іншого боку, паяння сріблом вимагає високих температур, що забезпечуються пальником, і дає нам міцні з’єднання, придатні для застосування при високих температурах. Для пайки потрібні найвищі температури, і зазвичай використовується пальник. Оскільки паяні з’єднання дуже міцні, вони є хорошими кандидатами для ремонту важких залізних предметів. На наших виробничих лініях ми використовуємо як ручне паяння, так і автоматизовані лінії паяння. ІНДУКЦІЙНА ПАЙКА використовує високочастотний змінний струм у мідній котушці для полегшення індукційного нагріву. У спаяній частині індукуються струми, в результаті чого на високому опорі joint утворюється тепло. Це тепло плавить присадний метал. Також використовується флюс. Індукційне паяння є хорошим методом пайки циліндрів і труб у безперервному процесі шляхом обмотування котушок навколо них. Пайка деяких матеріалів, наприклад графіту та кераміки, є складнішою, оскільки перед пайкою потрібно покрити заготовки відповідним металом. Це полегшує міжфазне з’єднання. Ми спаюємо такі матеріали спеціально для герметичної упаковки. Ми виготовляємо наші друковані плати (PCB) у великих обсягах переважно за допомогою ХВИЛЬОВОГО ПАЙЯННЯ. Лише для невеликої кількості прототипів ми використовуємо ручне паяння за допомогою паяльника. Ми використовуємо пайку хвилею як для наскрізних, так і для поверхневого монтажу друкованих плат (PCBA). Тимчасовий клей утримує компоненти прикріпленими до друкованої плати, а вузол розміщується на конвеєрі та рухається через обладнання, яке містить розплавлений припій. Спочатку друкована плата флюсується, а потім потрапляє в зону попереднього нагріву. Розплавлений припій знаходиться в каструлі і має візерунок стоячих хвиль на своїй поверхні. Коли друкована плата рухається над цими хвилями, ці хвилі стикаються з нижньою частиною друкованої плати та прилипають до паяльних майданчиків. Припій залишається лише на контактах і майданчиках, а не на самій друкованій платі. Хвилі в розплавленому припої потрібно добре контролювати, щоб не було розбризкування, а вершини хвиль не торкалися та не забруднювали небажані ділянки плат. У REFLOW SOLDERING ми використовуємо липку паяльну пасту для тимчасового кріплення електронних компонентів до плат. Потім дошки проходять через оплавлювальну піч з контролем температури. Тут припій плавиться і з’єднує компоненти назавжди. Ми використовуємо цю техніку як для компонентів поверхневого монтажу, так і для компонентів із наскрізним отвором. Належний контроль температури та регулювання температури духовки є важливими, щоб уникнути руйнування електронних компонентів на платі через їх перегрівання вище максимально допустимих температур. У процесі пайки оплавленням ми фактично маємо кілька областей або етапів, кожна з яких має чіткий тепловий профіль, наприклад, етап попереднього нагрівання, етап термічного замочування, етапи оплавлення та охолодження. Ці різні етапи є важливими для безпечного паяння оплавленням збірок друкованих плат (PCBA). УЛЬТРАЗВУКОВЕ ПАЯННЯ — це ще одна часто використовувана техніка з унікальними можливостями — її можна використовувати для пайки скла, кераміки та неметалічних матеріалів. Наприклад, фотоелектричні панелі, які є неметалевими, потребують електродів, які можна прикріпити за допомогою цієї техніки. Під час ультразвукового паяння ми використовуємо нагріте паяльне жало, яке також випромінює ультразвукові коливання. Ці вібрації створюють кавітаційні бульбашки на межі підкладки з розплавленим матеріалом припою. Імплозивна енергія кавітації модифікує поверхню оксиду та видаляє бруд і оксиди. За цей час також утворюється шар сплаву. Припій на поверхні з’єднання містить кисень і забезпечує утворення міцного спільного зв’язку між склом і припоєм. Пайку зануренням можна розглядати як більш простий варіант пайки хвилею, придатний лише для невеликого виробництва. Перший очисний флюс застосовується, як і в інших процесах. Плати із встановленими компонентами занурюють вручну або напівавтоматично в резервуар із розплавленим припоєм. Розплавлений припій прилипає до відкритих металевих ділянок, незахищених паяльною маскою на платі. Обладнання просте і недороге. • КЛЕЄННЯ: це ще одна популярна техніка, яку ми часто використовуємо, і вона передбачає склеювання поверхонь за допомогою клеїв, епоксидних смол, пластичних речовин або інших хімікатів. Склеювання здійснюється шляхом випаровування розчинника, термічного затвердіння, затвердіння УФ-світлом, затвердіння під тиском або очікування певного часу. На наших виробничих лініях використовуються різноманітні високоякісні клеї. Завдяки належним чином розробленим процесам нанесення та затвердіння клейове з’єднання може призвести до міцних і надійних з’єднань із дуже низьким напруженням. Адгезивні з’єднання можуть бути хорошим захистом від факторів навколишнього середовища, таких як волога, забруднення, корозійні речовини, вібрація тощо. Переваги клейового склеювання такі: їх можна наносити на матеріали, які інакше було б важко паяти, зварювати або паяти. Також це може бути кращим для термочутливих матеріалів, які можуть бути пошкоджені зварюванням або іншими високотемпературними процесами. Інші переваги клеїв полягають у тому, що їх можна наносити на поверхні неправильної форми та збільшувати вагу збірки на дуже дуже невеликі кількості порівняно з іншими методами. Крім того, зміни розмірів деталей дуже мінімальні. Деякі клеї мають властивості узгодження індексів і можуть використовуватися між оптичними компонентами без значного зменшення сили світла чи оптичного сигналу. Недоліками, з іншого боку, є довший час затвердіння, що може уповільнити виробничі лінії, вимоги до кріплення, вимоги до підготовки поверхні та складність розбирання, коли потрібна доопрацювання. Більшість наших операцій по склеюванню включають такі етапи: -Поверхнева обробка: загальними є спеціальні процедури очищення, такі як очищення деіонізованою водою, очищення спиртом, плазмове чи коронне очищення. Після очищення ми можемо нанести на поверхні прискорювачі адгезії, щоб забезпечити найкраще з’єднання. -Кріплення деталей: як для нанесення клею, так і для затвердіння ми розробляємо та використовуємо спеціальні кріплення. - Нанесення клею: іноді ми використовуємо ручні, а іноді, залежно від випадку, автоматизовані системи, такі як робототехніка, сервомотори, лінійні приводи, щоб доставити клей у потрібне місце, і ми використовуємо дозатори, щоб доставити його в потрібному об’ємі та кількості. - Затвердіння: Залежно від клею ми можемо використовувати просте сушіння та затвердіння, а також затвердіння під ультрафіолетовими лампами, які діють як каталізатори, або затвердіння під дією тепла в печі або за допомогою резистивних нагрівальних елементів, встановлених на пристосуваннях і пристосуваннях. Ми рекомендуємо вам натиснути тут, щобЗАВАНТАЖИТИ наші схематичні ілюстрації процесів кріплення від AGS-TECH Inc. Це допоможе вам краще зрозуміти інформацію, яку ми надаємо нижче. • ПРОЦЕСИ КРИПЛЕННЯ: наші процеси механічного з’єднання поділяються на дві категорії: КРИПЛЕННЯ та ІНТЕГРАЛЬНІ З’ЄДНАННЯ. Прикладами кріплень, які ми використовуємо, є гвинти, шпильки, гайки, болти, заклепки. Прикладами цілісних з’єднань, які ми використовуємо, є замикання та усадка, шви, гофри. Використовуючи різноманітні методи кріплення, ми забезпечуємо міцність і надійність наших механічних з’єднань протягом багатьох років використання. ГВИНТИ та БОЛТИ є одними з найбільш часто використовуваних кріпильних елементів для кріплення об’єктів разом і позиціонування. Наші гвинти та болти відповідають стандартам ASME. Використовуються різні типи гвинтів і болтів, включаючи гвинти з шестигранною головкою та болти з шестигранною головкою, гвинти та болти з двостороннім торцем, гвинти з дюбелями, гвинти з вушком, дзеркальні гвинти, гвинти для листового металу, гвинти для точного регулювання, самосвердлувальні та самонарізні гвинти , настановний гвинт, гвинти з вбудованими шайбами…і багато іншого. У нас є різні типи гвинтів, такі як потайні, куполоподібні, круглі, фланцеві, а також різні типи гвинтів, такі як шліц, хрестоподібний, квадратний, шестигранний. RIVET, з іншого боку, є постійним механічним кріпленням, що складається з гладкого циліндричного стрижня та головки, з одного боку. Після вставлення інший кінець заклепки деформується, а її діаметр розширюється, щоб вона залишалася на місці. Іншими словами, до установки заклепка має одну головку, а після установки - дві. Ми встановлюємо різні типи заклепок залежно від застосування, міцності, доступності та вартості, такі як заклепки з суцільною/круглою головкою, структурні, напівтрубчасті, глухі, оскар, приводні, фрикційні, самопроколюючі заклепки. Клепанню можна віддати перевагу у випадках, коли необхідно уникнути термічної деформації та зміни властивостей матеріалу внаслідок тепла зварювання. Клепка також забезпечує легку вагу та особливо хорошу міцність і витривалість проти сил зсуву. Проте проти розтягуючих навантажень краще підходять гвинти, гайки та болти. У процесі КЛІНЧУВАННЯ ми використовуємо спеціальні пуансони та матриці для формування механічного зчеплення між листами металу, що з’єднуються. Пуансон проштовхує шари листового металу в порожнину матриці та призводить до утворення нероз’ємного з’єднання. Під час клінчу не потрібне нагрівання та охолодження, і це процес холодної роботи. Це економічний процес, який у деяких випадках може замінити точкове зварювання. У ПІНІНГІ ми використовуємо штифти, які є елементами машини, які використовуються для фіксації позицій деталей машини відносно одна одної. Основними типами є шпильки, шплінти, пружинні шпильки, шпильки, та шплінти. У СТАПЛІНГІ ми використовуємо степлери та скоби, які є двосторонніми кріпленнями, які використовуються для з’єднання або зв’язування матеріалів. Зшивання має наступні переваги: Економічний, простий і швидкий у використанні, головка скоби може бути використана для з’єднання матеріалів, з’єднаних разом. Корона скоби може полегшити з’єднання шматка, як кабель, і кріплення його до поверхні без проколювання або пошкодження, відносно легке видалення. ПРЕСС-ФІТІНГ виконується шляхом зштовхування деталей разом, а тертя між ними скріплює деталі. Деталі з пресовою посадкою, що складаються з великого вала та заниженого отвору, зазвичай збираються одним із двох методів: або шляхом застосування сили, або використання теплового розширення чи звуження деталей. Коли прес-фітинг встановлюється шляхом застосування сили, ми використовуємо або гідравлічний прес, або ручний прес. З іншого боку, коли прес-фітинг встановлюється за рахунок теплового розширення, ми нагріваємо охоплюючі частини та збираємо їх на своє місце в гарячому стані. Коли вони охолонуть, вони стискаються і повертаються до своїх нормальних розмірів. Це забезпечує гарне прилягання до пресу. Ми називаємо це інакше Усадочним монтажем. Інший спосіб зробити це — охолодити частини в оболонці перед збиранням, а потім вставити їх у відповідні частини. Коли вузол нагрівається, вони розширюються, і ми отримуємо щільне прилягання. Цей останній метод може бути кращим у випадках, коли нагрівання створює ризик зміни властивостей матеріалу. У таких випадках охолодження безпечніше. Пневматичні та гідравлічні компоненти та вузли • Клапани, гідравлічні та пневматичні компоненти, такі як ущільнювальне кільце, шайба, ущільнення, прокладка, кільце, прокладка. Оскільки клапани та пневматичні компоненти представлені у великій різноманітності, ми не можемо перерахувати все тут. Залежно від фізичного та хімічного середовища вашої програми ми маємо спеціальні продукти для вас. Будь ласка, вкажіть нам застосування, тип компонента, технічні характеристики, умови навколишнього середовища, такі як тиск, температура, рідини або гази, які будуть контактувати з вашими клапанами та пневматичними компонентами; і ми підберемо для вас найбільш підходящий продукт або виготовимо його спеціально для вашого застосування. CLICK Product Finder-Locator Service ПОПЕРЕДНЯ СТОРІНКА
- Rapid Prototyping, Desktop Manufacturing, Additive Manufacturing, FDM
Rapid Prototyping, Desktop Manufacturing, Additive Manufacturing, Stereolithography, Polyjet, Fused Deposition Modeling, Selective Laser Sintering, FDM, SLS Адитивне та швидке виробництво Останніми роками ми спостерігаємо зростання попиту на ШВИДКЕ ВИГОТОВЛЕННЯ або ШВИДКЕ ПРОТОТИПУВАННЯ. Цей процес також можна назвати НАСТОЛЬНИМ ВИРОБНИЦТВОМ або ВИГОТОВЛЕННЯМ ДОВІЛЬНОЇ ФОРМИ. В основному твердотільну фізичну модель деталі створюють безпосередньо з тривимірного креслення САПР. Ми використовуємо термін АДДИТИВНЕ ВИРОБНИЦТВО для цих різних методів, коли ми створюємо деталі шарами. Використовуючи інтегроване комп’ютерне обладнання та програмне забезпечення, ми виконуємо адитивне виробництво. Наші технології швидкого створення прототипів і виробництва включають СТЕРЕОЛІТОГРАФІЮ, ПОЛІСТРУКЕВИЙ МОДЕЛЮВАННЯ, МОДЕЛЮВАННЯ ПЛАВЛЕНИМ ОСАДЖЕННЯМ, СЕЛЕКТИВНЕ ЛАЗЕРНЕ СПІКАННЯ, ПЛАВЛЕННЯ ЕЛЕКТРОННИМ ПРОМЕНЕМ, ТРИВИМІРНИЙ ДРУК, ПРЯМЕ ВИРОБНИЦТВО, ШВИДКЕ ІНСТРУМЕНТАЛЬНЕ ОБЛАДНАННЯ. Ми рекомендуємо вам натиснути тут, щобЗАВАНТАЖИТИ наші схематичні ілюстрації адитивного виробництва та процесів швидкого виробництва від AGS-TECH Inc. Це допоможе вам краще зрозуміти інформацію, яку ми надаємо нижче. Швидке створення прототипів забезпечує нам: 1.) Концептуальний дизайн продукту розглядається з різних кутів на моніторі за допомогою системи 3D / CAD. 2.) Прототипи з неметалевих і металевих матеріалів виготовляються і вивчаються з функціональних, технічних і естетичних аспектів. 3.) Виконується недороге прототипування за дуже короткий час. Адитивне виробництво можна нагадувати виготовлення буханця хліба шляхом укладання та склеювання окремих скибочок один на одного. Іншими словами, продукт виготовляється шматок за шматочком або шар за шаром, накладений один на одного. Більшість деталей можна виготовити протягом годин. Техніка хороша, якщо деталі потрібні дуже швидко або якщо необхідна кількість невелика, а виготовлення прес-форми та інструментів занадто дороге та займає багато часу. Однак вартість деталі висока через дорогу сировину. • СТЕРЕОЛІТОГРАФІЯ: Ця техніка, також скорочена як STL, заснована на затвердінні та затвердінні рідкого фотополімеру в певну форму шляхом фокусування на ньому лазерного променя. Лазер полімеризує фотополімер і полімеризує його. Шляхом сканування ультрафіолетового лазерного променя відповідно до запрограмованої форми вздовж поверхні фотополімерної суміші деталь виготовляється знизу вгору окремими зрізами, розташованими каскадом один на одному. Сканування лазерної плями повторюється багато разів для досягнення геометрії, запрограмованої в системі. Після того, як деталь повністю виготовлена, її знімають з платформи, промокають і очищають ультразвуком і спиртовою ванною. Потім він піддається УФ-опроміненню протягом декількох годин, щоб переконатися, що полімер повністю затвердів і затвердів. Підводячи підсумок процесу, платформа, занурена у фотополімерну суміш, і УФ-лазерний промінь контролюються та переміщуються через систему сервоконтролю відповідно до форми бажаної деталі, і деталь отримують шляхом фотозатвердіння полімеру шар за шаром. Звичайно, максимальні розміри виготовленої частини визначаються стереолітографічним обладнанням. • POLYJET: Подібно до струминного друку, у поліструменевому друку ми маємо вісім друкуючих голівок, які наносять фотополімер на робочий лоток. Ультрафіолетове світло, розміщене поруч із струменями, негайно затвердіє та зміцнить кожен шар. У polyjet використовуються два матеріали. Перший матеріал для виготовлення власне моделі. Другий матеріал, гелеподібна смола, використовується для підтримки. Обидва ці матеріали наносяться шар за шаром і одночасно отверждаются. Після завершення моделі опорний матеріал видаляється водним розчином. Використовувані смоли подібні до стереолітографії (STL). Поліструйний має наступні переваги перед стереолітографією: 1.) Немає необхідності очищати частини. 2.) Немає потреби в полімеризації після обробки. 3.) Можлива менша товщина шару, і, отже, ми отримуємо кращу роздільну здатність і можемо виготовляти більш тонкі деталі. • МОДЕЛЮВАННЯ ОСАДЖЕННЯ ПЛАВЛЕННЯМ: також скорочено FDM, у цьому методі головка екструдера, керована роботом, рухається над столом у двох основних напрямках. Трос опускається і піднімається в міру необхідності. З отвору нагрітої матриці на головці екструдується термопластична нитка, а початковий шар наноситься на пінопластову основу. Це досягається головкою екструдера, яка слідує заздалегідь визначеному шляху. Після початкового шару стіл опускається, а наступні шари накладаються один на одного. Іноді при виготовленні складної деталі потрібні опорні конструкції, щоб осадження могло продовжуватися в певних напрямках. У цих випадках опорний матеріал екструдується з менш щільним проміжком нитки на шарі, щоб він був слабшим, ніж матеріал моделі. Ці опорні конструкції пізніше можуть бути розпущені або відламані після завершення виготовлення деталі. Розміри матриці екструдера визначають товщину екструдованих шарів. Процес FDM виготовляє деталі зі ступінчастою поверхнею на похилих зовнішніх площинах. Якщо ця шорсткість є неприйнятною, для її згладжування можна використати полірування хімічним паром або нагрітий інструмент. Навіть полірувальний віск доступний як матеріал для покриття, щоб усунути ці кроки та досягти прийнятних геометричних допусків. • СЕЛЕКТИВНЕ ЛАЗЕРНЕ СПІКАННЯ: також позначається як SLS, процес заснований на спіканні полімерних, керамічних або металевих порошків вибірково в об'єкт. У нижній частині робочої камери є два циліндри: циліндр, що складається з деталей, і циліндр для подачі порошку. Перший поступово опускається до місця формування спеченої деталі, а другий поступово піднімається для подачі порошку в циліндр деталі через роликовий механізм. Спочатку тонкий шар порошку наноситься на циліндр деталі, а потім лазерний промінь фокусується на цьому шарі, простежуючи та плавлячи/спікаючи певний поперечний переріз, який потім знову твердне в тверду речовину. Порошок – це ділянки, на які не потрапляє лазерний промінь, залишаються пухкими, але все ще підтримують тверду частину. Потім наноситься ще один шар порошку, і процес повторюється багато разів, щоб отримати деталь. Наприкінці частинки порошку струшують. Усе це виконується комп’ютером керування процесом із використанням інструкцій, створених програмою 3D CAD деталі, що виготовляється. Різні матеріали, такі як полімери (такі як ABS, PVC, поліестер), віск, метали та кераміка з відповідними полімерними сполучними можуть бути нанесені. • ELECTRON-BEAM MELTING : Подібно до селективного лазерного спікання, але з використанням електронного променя для плавлення порошків титанового або кобальтового хрому для виготовлення прототипів у вакуумі. Деякі розробки були зроблені для виконання цього процесу на нержавіючих сталях, алюмінієвих і мідних сплавах. Якщо необхідно підвищити втомну міцність виготовлених деталей, ми використовуємо гаряче ізостатичне пресування після виготовлення деталей як допоміжний процес. • ТРИВИМІРНИЙ ДРУК: також позначається як 3DP, у цій техніці друкуюча головка наносить неорганічну сполучну речовину на шар неметалічного або металевого порошку. Поршень, що тримає шар порошку, поступово опускається, і на кожному кроці сполучна речовина наноситься шар за шаром і сплавляється зв’язуючою речовиною. Використовуються порошкові матеріали - суміші полімерів і волокон, ливарний пісок, метали. Використовуючи одночасно різні біндерні головки та різні кольорові біндери, ми можемо отримати різні кольори. Процес схожий на струменевий друк, але замість кольорового аркуша ми отримуємо кольоровий тривимірний об’єкт. Виготовлені деталі можуть бути пористими, і тому може знадобитися спікання та інфільтрація металу для підвищення його щільності та міцності. Спікання призведе до спалювання сполучного матеріалу та сплавлення металевих порошків разом. Для виготовлення деталей можна використовувати такі метали, як нержавіюча сталь, алюміній, титан, а як матеріали для інфільтрації ми зазвичай використовуємо мідь і бронзу. Принадність цієї техніки полягає в тому, що навіть складні та рухомі вузли можна виготовити дуже швидко. Наприклад, можна виготовити редуктор, гайковий ключ як інструмент, який матиме рухомі та поворотні частини, готові до використання. Різні компоненти вузла можна виготовити в різних кольорах і все одним знімком. Завантажте нашу брошуру на:Основи 3D-друку з металу • ПРЯМЕ ВИРОБНИЦТВО та ШВИДКЕ ВИРОБНИЦТВО: окрім оцінки дизайну, пошуку та усунення несправностей ми використовуємо швидке створення прототипів для безпосереднього виробництва продуктів або безпосереднього застосування в продуктах. Іншими словами, швидке прототипування можна включити в звичайні процеси, щоб зробити їх кращими та конкурентоспроможнішими. Наприклад, швидке прототипування може створювати шаблони та форми. Шаблони полімеру, що плавиться і горить, створені операціями швидкого прототипування, можуть бути зібрані для лиття по виплавленим моделям і вкладені. Ще один приклад, про який варто згадати, це використання 3DP для виробництва керамічної ливарної оболонки та використання її для операцій лиття оболонки. Навіть прес-форми для лиття під тиском і вставки для прес-форм можна виготовити шляхом швидкого створення прототипів, і можна заощадити багато тижнів або місяців часу на виготовлення форм. Лише проаналізувавши файл CAD потрібної деталі, ми можемо створити геометрію інструменту за допомогою програмного забезпечення. Ось деякі з наших популярних швидких методів інструментів: RTV (Вулканізація при кімнатній температурі) ФОРМУВАННЯ / ЛИТВО З УРЕТАНУ: використання швидкого прототипування може бути використано для створення шаблону бажаної деталі. Потім цей шаблон покривають розділовим засобом і рідку резину RTV виливають поверх шаблону для виготовлення половинок форми. Далі ці половинки форми використовуються для лиття під тиском рідких уретанів. Термін служби прес-форми короткий, лише 0 або 30 циклів, але його достатньо для невеликого серійного виробництва. ІНЖЕКЦІЙНЕ ЛИТТЯ ACES (Acetal Clear Epoxy Solid): Використовуючи методи швидкого створення прототипів, такі як стереолітографія, ми виготовляємо лиття під тиском. Ці форми являють собою оболонки з відкритим кінцем, які дозволяють заповнювати такі матеріали, як епоксидна смола, епоксидна смола з алюмінієвим наповненням або метали. Знову ж таки, термін служби форми обмежений десятками або максимум сотнями деталей. ПРОЦЕС ОБРАБОТКИ ІНСТРУМЕНТІВ ДЛЯ МЕТАЛУ НАПИЛЕНИМ: ми використовуємо швидке створення прототипів і створюємо шаблон. Розпилюємо цинк-алюмінієвий сплав на поверхню візерунка і покриваємо його. Потім візерунок із металевим покриттям поміщають у колбу та заповнюють епоксидною смолою або епоксидною смолою з алюмінієвим наповненням. Нарешті, його видаляють, і шляхом виготовлення двох таких половинок форми ми отримуємо повну форму для лиття під тиском. Ці прес-форми мають довший термін служби, у деяких випадках, залежно від матеріалу та температури, вони можуть виготовляти тисячі деталей. ПРОЦЕС KEELTOOL: Ця техніка може виробляти прес-форми з терміном служби від 100 000 до 10 мільйонів циклів. Використовуючи швидке прототипування, ми виготовляємо прес-форму RTV. Далі форму заповнюють сумішшю, що складається з порошку інструментальної сталі А6, карбіду вольфраму, полімерного сполучного, і дають затвердіти. Потім цю форму нагрівають, щоб полімер випалив, а металеві порошки сплавилися. Наступним кроком є інфільтрація міддю для виготовлення остаточної форми. За потреби на формі можна виконати додаткові операції, такі як механічна обробка та полірування, для кращої точності розмірів. CLICK Product Finder-Locator Service ПОПЕРЕДНЯ СТОРІНКА
- Glass and Ceramic Manufacturing, Hermetic Packages, Seals, Bonding
Glass and Ceramic Manufacturing, Hermetic Packages Seals and Bonding, Tempered Bulletproof Glass, Blow Moulding, Optical Grade Glass, Conductive Glass, Molding Формування скла та кераміки Види скла, які ми пропонуємо, включають тарне скло, склодувне скло, скловолокно, трубки та прутки, побутовий і промисловий скляний посуд, лампи та колби, точне формування скла, оптичні компоненти та вузли, плоске та листове та флоат-скло. Ми виконуємо як ручне, так і машинне формування. Нашими популярними процесами виробництва технічної кераміки є пресування під тиском, ізостатичне пресування, гаряче ізостатичне пресування, гаряче пресування, шликерне лиття, стрічкове лиття, екструзія, лиття під тиском, обробка без обробки, спікання або випал, алмазне шліфування, герметичні вузли. Ми рекомендуємо вам натиснути тут, щоб ЗАВАНТАЖИТИ наші схематичні ілюстрації процесів формування та формування скла від AGS-TECH Inc. ЗАВАНТАЖИТИ наші схематичні ілюстрації процесів виробництва технічної кераміки від AGS-TECH Inc. Ці завантажувані файли з фотографіями та ескізами допоможуть вам краще зрозуміти інформацію, яку ми надаємо нижче. • ВИРОБНИЦТВО СКЛОТАРНОЇ ТАРИ: ми маємо автоматизовані лінії ПРЕСУВАННЯ ТА ВИДУВАННЯ, а також лінії ВИДУВАННЯ ТА ВИДУВАННЯ для виробництва. У процесі видування й видування ми опускаємо шматочок у порожню форму та формуємо горловину, подаючи стиснене повітря зверху. Одразу після цього стиснене повітря вдруге продувається з іншого боку через горловину контейнера для формування попередньої форми пляшки. Потім цю попередню форму переносять у фактичну форму, знову нагрівають для пом’якшення та подають стиснене повітря, щоб надати заготовці остаточної форми контейнера. Точніше кажучи, на нього створюється тиск і притискається до стінок порожнини видувної форми, щоб він набув бажаної форми. Нарешті, виготовлений скляний контейнер переміщується в піч для відпалу для подальшого повторного нагрівання та зняття напруг, що виникли під час формування, і охолоджується контрольованим способом. У методі пресування та видування розплавлені шматки поміщають у форму для заготовки (заготовку) і пресують у форму заготовки (заготовку). Потім заготовки переносяться в видувні форми та видуваються, подібно до процесу, описаного вище в розділі «Процес видування й видування». Подальші етапи, такі як відпал і зняття напруги, подібні або однакові. • ВИДУВАННЯ СКЛА: ми виробляємо вироби зі скла за допомогою звичайного ручного видування, а також за допомогою стисненого повітря за допомогою автоматизованого обладнання. Для деяких замовлень потрібне звичайне видування, наприклад проекти, пов’язані з художнім оформленням скла, або проекти, які вимагають меншої кількості деталей із вільними допусками, створення прототипів/демо-проекти… тощо. Традиційне видування скла передбачає занурення порожнистої металевої труби в посудину з розплавленим склом і обертання труби для збору певної кількості скляного матеріалу. Скло, зібране на кінчику труби, прокочується на плоскому залізі, йому надається необхідна форма, подовжується, знову нагрівається та продувається повітрям. Після готовності його вставляють у форму і вдувають повітрям. Порожнина форми змочується, щоб уникнути контакту скла з металом. Водна плівка діє як подушка між ними. Видування вручну – це трудомісткий повільний процес, який підходить лише для створення прототипів або предметів високої вартості, не підходить для недорогих замовлень великого обсягу. • ВИРОБНИЦТВО ПОБУДОВОГО ТА ПРОМИСЛОВОГО СКЛЯНОГО ПОСУДУ: з використанням різних типів скляного матеріалу виготовляється велика різноманітність скляного посуду. Деякі склянки є термостійкими та придатними для лабораторного посуду, тоді як деякі досить добре витримують посудомийні машини багато разів і придатні для виготовлення домашніх виробів. За допомогою машин Westlake щодня виготовляються десятки тисяч склянок. Щоб спростити, розплавлене скло збирають за допомогою вакууму та вставляють у форми для виготовлення попередніх форм. Потім у форми вдувається повітря, вони переносяться в іншу форму, знову вдувається повітря, і скло набуває остаточної форми. Як і при ручному видуванні, ці форми змочують водою. Подальше розтягування є частиною фінішної операції, де формується горловина. Надлишки скла спалюються. Після цього слідує процес контрольованого повторного нагрівання та охолодження, описаний вище. • ФОРМУВАННЯ СКЛЯНИХ ТРУБОК ТА ПИТАНЬ: Основними процесами, які ми використовуємо для виробництва скляних трубок, є процеси DANNER і VELLO. У процесі Даннера скло з печі тече і падає на похилу муфту з вогнетривких матеріалів. Гільза тримається на обертовому порожнистому валу або надувній трубі. Потім скло обертається навколо гільзи та утворює гладкий шар, що стікає вниз по гільзі та над кінчиком древка. У разі формування труби повітря продувається через надувну трубу з порожнистим наконечником, а у випадку формування стрижня ми використовуємо суцільні наконечники на валу. Потім труби або стрижні натягуються на несучі ролики. Такі розміри, як товщина стінки та діаметр скляних трубок, регулюються до бажаних значень, встановлюючи бажаний діаметр рукава та тиск повітря, регулюючи температуру, швидкість потоку скла та швидкість витягування. З іншого боку, процес виготовлення скляної трубки Vello включає скло, яке виходить із печі та потрапляє в чашу за допомогою порожнистої оправки або дзвона. Потім скло проходить через повітряний простір між оправкою та чашею і набуває форму труби. Після цього він рухається через ролики до волочильної машини та охолоджується. Наприкінці лінії охолодження відбувається різання та остаточна обробка. Розміри труб можна регулювати так само, як у процесі Даннера. Порівнюючи процес Даннера з процесом Велло, ми можемо сказати, що процес Велло краще підходить для виробництва великої кількості, тоді як процес Даннера може краще підходити для точних замовлень на труби меншого обсягу. • ОБРОБКА ЛИСТОВОГО ТА ПЛОСКОГО ТА ФЛОАТ-СКЛА: у нас є велика кількість плоского скла товщиною від субміліметрів до кількох сантиметрів. Наші плоскі скла мають майже оптичну досконалість. Ми пропонуємо скло зі спеціальними покриттями, такими як оптичні покриття, де техніка хімічного осадження з парової фази використовується для нанесення таких покриттів, як антивідблиски або дзеркальне покриття. Також поширені прозорі електропровідні покриття. Також доступні гідрофобні або гідрофільні покриття на склі, а також покриття, яке робить скло самоочисним. Загартоване, куленепробивне та ламіноване скло є ще одними популярними товарами. Ми нарізаємо скло потрібної форми з необхідними допусками. Доступні інші вторинні операції, такі як викривлення або згинання плоского скла. • ТОЧНЕ ФОРМУВАННЯ СКЛА: ми використовуємо цю техніку здебільшого для виготовлення точних оптичних компонентів без потреби у більш дорогих і трудомістких техніках, таких як шліфування, притирка та полірування. Цій техніці не завжди достатньо для виготовлення найкращої оптики, але в деяких випадках, як-от споживчі товари, цифрові фотоапарати, медична оптика, це може бути менш дорогим хорошим варіантом для великого виробництва. Крім того, він має перевагу перед іншими методами формування скла, де потрібні складні геометрії, наприклад, у випадку асфер. Основний процес включає в себе завантаження нижньої сторони нашої прес-форми скляною заготовкою, вакуумування технологічної камери для видалення кисню, ближче до закриття форми, швидке та ізотермічне нагрівання матриці та скла інфрачервоним світлом, подальше закриття половинок форми. для повільного контрольованого пресування розм’якшеного скла до бажаної товщини, і, нарешті, охолодження скла та заповнення камери азотом і видалення продукту. Точний контроль температури, відстань до закриття форми, сила закриття форми, відповідність коефіцієнтів розширення форми та матеріалу скла є ключовими в цьому процесі. • ВИРОБНИЦТВО СКЛЯНИХ ОПТИЧНИХ КОМПОНЕНТІВ ТА ЗБОРОК: окрім прецизійного формування скла, існує низка цінних процесів, які ми використовуємо для виготовлення високоякісних оптичних компонентів і вузлів для вимогливих застосувань. Шліфування, притирання та полірування скла оптичного класу в тонкодисперсних спеціальних абразивних суспензіях є мистецтвом і наукою для виготовлення оптичних лінз, призм, плоских тощо. Рівність поверхні, хвилястість, гладкість і бездефектні оптичні поверхні вимагають великого досвіду з такими процесами. Невеликі зміни в навколишньому середовищі можуть призвести до того, що продукти не відповідають специфікаціям, і призвести до зупинки виробничої лінії. Бувають випадки, коли одне протирання оптичної поверхні чистою тканиною може призвести до того, що продукт відповідає специфікаціям або провалить тест. Деякі популярні скляні матеріали, що використовуються, це плавлений кремнезем, кварц, BK7. Крім того, збірка таких компонентів вимагає спеціального досвіду. Іноді використовують спеціальні клеї. Однак іноді найкращим вибором є техніка, яка називається оптичним контактом, і не передбачає використання матеріалу між прикріпленими оптичними стеклами. Він складається з фізичного контакту плоских поверхонь для кріплення одна до одної без клею. У деяких випадках для складання оптичних компонентів на певних відстанях і з певною геометричною орієнтацією один до одного використовуються механічні розпірки, прецизійні скляні стрижні або кульки, затискачі або оброблені металеві компоненти. Давайте розглянемо деякі з наших популярних технологій виготовлення високоякісної оптики. ШЛІФУВАННЯ ТА ПРИТРИВАННЯ ТА ПОЛІРУВАННЯ: Грубу форму оптичного компонента отримують шляхом шліфування скляної заготовки. Після цього виконується притирання та полірування шляхом обертання та тертя шорстких поверхонь оптичних компонентів об інструменти з бажаною формою поверхні. Суспензії з дрібними абразивними частинками та рідиною заливаються між оптикою та формуючими інструментами. Розмір абразивних частинок у таких суспензіях можна вибирати відповідно до бажаного ступеня площинності. Відхилення критичних оптичних поверхонь від бажаних форм виражаються через довжину хвилі світла, що використовується. Наша високоточна оптика має допуски на десяту частину довжини хвилі (довжина хвилі/10) або навіть більш жорсткі. Окрім профілю поверхні, критичні поверхні скануються та оцінюються на наявність інших характеристик поверхні та дефектів, таких як розміри, подряпини, відколи, ямки, цятки тощо. Жорсткий контроль умов навколишнього середовища в оптичному виробництві, а також суворі вимоги до метрології та тестування з найсучаснішим обладнанням роблять цю галузь промисловості складною. • ВТОРИННІ ПРОЦЕСИ У ВИРОБНИЦТВІ СКЛА: Знову ж таки, ми обмежені лише вашою уявою, коли йдеться про вторинні та фінішні процеси скла. Ось деякі з них: -Покриття на склі (оптичні, електричні, трибологічні, теплові, функціональні, механічні...). Як приклад, ми можемо змінити властивості поверхні скла, щоб воно, наприклад, відбивало тепло, зберігаючи прохолоду всередині будівлі, або зробити одну сторону інфрачервоного поглинання за допомогою нанотехнологій. Це допомагає зберігати тепло всередині будівель, оскільки зовнішній поверхневий шар скла поглинає інфрачервоне випромінювання всередині будівлі та випромінює його назад усередину. -Офорт на склі -Прикладне керамічне маркування (ACL) -Гравіювання -полум'яне полірування - Хімічне полірування -Фарбування ВИГОТОВЛЕННЯ ТЕХНІЧНОЇ КЕРАМІКИ • ПРЕСУВАННЯ ПОЛОШКИ: складається з одновісного ущільнення гранульованих порошків, укладених у форму. • ГАРЯЧЕ ПРЕСОВУВАННЯ: Подібне до пресування в штампах, але з додаванням температури для посилення ущільнення. Порошок або ущільнену преформу поміщають у графітову матрицю та застосовують одноосьовий тиск, у той час як матриця підтримується при високих температурах, таких як 2000 C. Температури можуть відрізнятися залежно від типу керамічного порошку, що обробляється. Для складних форм і геометрій може знадобитися інша подальша обробка, наприклад алмазне шліфування. • ІЗОСТАТИЧНЕ ПРЕСУВАННЯ: гранульований порошок або спресовані пресовані преси поміщають у герметичні контейнери, а потім у закриту ємність під тиском із рідиною всередині. Після цього вони ущільнюються шляхом збільшення тиску в резервуарі під тиском. Рідина всередині посудини рівномірно передає сили тиску по всій площі поверхні герметичної ємності. Таким чином, матеріал рівномірно ущільнюється і приймає форму свого гнучкого контейнера, його внутрішній профіль і особливості. • ГАРЯЧЕ ІЗОСТАТИЧНЕ ПРЕСОВУВАННЯ: Подібно до ізостатичного пресування, але на додаток до газової атмосфери під тиском ми спікаємо компакт при високій температурі. Гаряче ізостатичне пресування забезпечує додаткове ущільнення і підвищення міцності. • Шлікерне лиття/лиття: ми заповнюємо форму суспензією керамічних частинок мікрометрового розміру та рідини-носія. Ця суміш називається «сліп». Форма має пори, тому рідина в суміші фільтрується у форму. В результаті на внутрішніх поверхнях форми утворюється зліпок. Після спікання деталі можна виймати з форми. • ЛИТТЯ СТРИЧОК: ми виготовляємо керамічні стрічки шляхом відливання керамічних суспензій на плоскі рухомі поверхні носіїв. Суспензії містять керамічні порошки, змішані з іншими хімічними речовинами для зв’язування та транспортування. У міру випаровування розчинників залишаються щільні та гнучкі керамічні листи, які можна розрізати або скручувати за бажанням. • ЕКСТРУЗІЙНЕ ФОРМУВАННЯ: Як і в інших процесах екструзії, м’яка суміш керамічного порошку зі зв’язуючими речовинами та іншими хімікатами пропускається через головку для набуття форми поперечного перерізу, а потім розрізається на бажану довжину. Процес виконується холодними або нагрітими керамічними сумішами. • ЛИТВО ПІД НИЗЬКИМ ТИСКОМ: ми готуємо суміш керамічного порошку зі зв’язуючими речовинами та розчинниками та нагріваємо її до температури, при якій її можна легко пресувати та вставляти в порожнину інструменту. Після завершення циклу формування деталь викидається, а зв’язуюча речовина спалюється. Використовуючи лиття під тиском, ми можемо економічно отримувати складні деталі у великих обсягах. Можливі отвори , які становлять крихітні частки міліметра на стіні товщиною 10 мм, можливі різьби без додаткової обробки, можливі допуски +/- 0,5% і навіть нижче, коли деталі обробляються. можлива товщина стінки від 0,5 мм до 12,5 мм, а також товщина стінки від 6,5 мм до 150 мм. • ЕКОЛОГІЧНА ОБРОБКА: Використовуючи ті самі інструменти для обробки металу, ми можемо обробляти пресовані керамічні матеріали, поки вони ще м’які, як крейда. Можливі допуски +/- 1%. Для кращих допусків ми використовуємо алмазне шліфування. • СПІКАННЯ або ВИПІК: спікання робить можливим повне ущільнення. На зелених компактних деталях відбувається значна усадка, але це не є великою проблемою, оскільки ми беремо до уваги ці зміни розмірів, коли розробляємо деталь та інструменти. Частинки порошку з'єднуються разом, і пористість, викликана процесом пресування, значною мірою видаляється. • АЛМАЗНЕ ШЛІФУВАННЯ: найтвердіший у світі матеріал «алмаз» використовується для шліфування твердих матеріалів, таких як кераміка, і для отримання точних деталей. Досягаються допуски в мікрометровому діапазоні та дуже гладкі поверхні. Через її вартість ми розглядаємо цю техніку лише тоді, коли вона нам дійсно потрібна. • ГЕРМЕТИЧНІ ЗБОРКИ – це ті, які практично не допускають будь-якого обміну речовинами, твердими речовинами, рідинами чи газами між інтерфейсами. Герметичне ущільнення є герметичним. Наприклад, герметичні електронні корпуси – це ті, які зберігають чутливий внутрішній вміст упакованого пристрою без ушкодження вологи, забруднень або газів. Ніщо не є 100% герметичним, але коли ми говоримо про герметичність, ми маємо на увазі, що з практичної точки зору герметичність існує настільки, що рівень витоку настільки низький, що пристрої безпечні за нормальних умов навколишнього середовища протягом дуже тривалого часу. Наші герметичні вузли складаються з металевих, скляних і керамічних компонентів, металокераміки, кераміки-металокераміки, металокераміки-метал, метал-метал, метал-скло, метал-скло-метал, скло-метал-скло, скло- метал і скло до скла та всі інші комбінації склеювання метал-склокераміка. Ми можемо, наприклад, покрити керамічні компоненти металевим покриттям, щоб вони могли міцно з’єднатися з іншими компонентами в зборі та мати чудову герметичну здатність. Ми маємо ноу-хау покриття оптичних волокон або прохідних отворів металом і припаювання або припаювання їх до корпусів, щоб гази не проходили та не витокувались у корпуси. Тому вони використовуються для виготовлення електронних корпусів для інкапсуляції чутливих пристроїв і захисту їх від зовнішньої атмосфери. Крім відмінних характеристик ущільнення, інші властивості, такі як коефіцієнт теплового розширення, стійкість до деформації, невиділення газів, дуже тривалий термін служби, непровідність, теплоізоляційні властивості, антистатичні властивості тощо. зробити скляні та керамічні матеріали вибором для певних застосувань. Інформацію про наше підприємство, що виробляє фітинги з кераміки на метал, герметичне ущільнення, вакуумні канали, компоненти для контролю високого та надвисокого вакууму та рідини можна знайти тут:Брошура заводу Hermetic Components CLICK Product Finder-Locator Service ПОПЕРЕДНЯ СТОРІНКА
- Wire & Spring Forming, Shaping, Welding, Assembly of Wires, Coil, CNC
Wire & Spring Forming, Shaping, Welding, Assembly of Wires, Coil Compression Extension Torsion Flat Springs, Custom Wires, Helical Springs at AGS-TECH Inc. Дріт і формування пружин Ми виготовляємо нестандартні дроти, дроти в зборі, дроти, сформовані в потрібні 2D і 3D форми, дротяні сітки, сітки, корпуси, кошики, огорожі, дротяні пружини, плоскі пружини; кручення, стиснення, розтягування, плоскі пружини тощо. Наші процеси включають формування дроту та пружини, волочіння дроту, формування, згинання, зварювання, паяння, паяння, проколювання, обтискання, свердління, зняття фаски, шліфування, нарізання різьблення, нанесення покриття, ковзання, формування ковзання, намотування, згортання, висадка. Ми рекомендуємо вам натиснути тут, щоб ЗАВАНТАЖИТИ наші схематичні ілюстрації процесів формування дроту та пружини від AGS-TECH Inc. Цей завантажуваний файл із фотографіями та ескізами допоможе вам краще зрозуміти інформацію, яку ми надаємо нижче. • ВОЛОЖЕННЯ ДРОТУ: використовуючи сили розтягування, ми розтягуємо металеву заготовку та протягуємо її через матрицю, щоб зменшити діаметр і збільшити її довжину. Іноді ми використовуємо серію штампів. Ми можемо виготовляти штампи для дроту будь-якого калібру. Використовуючи матеріал з високою міцністю на розрив, ми протягуємо дуже тонкі дроти. Ми пропонуємо провід холодної та гарячої обробки. • ФОРМУВАННЯ ДРОТУ: Рулон калібрувального дроту згинають і формують у корисний продукт. Ми маємо можливість формувати дроти з будь-якого калібру, включаючи тонкі нитки, а також товсті дроти, такі як ті, що використовуються як пружини під шасі автомобіля. Обладнання, яке ми використовуємо для формування дроту, - це ручні та CNC-формувальники дроту, моталки, силові преси, чотирислайд, багатослайд. Наші процеси включають волочіння, згинання, випрямлення, сплющування, розтягування, різання, висадку, паяння, зварювання та паяння, складання, згортання, штампування (або крила), проколювання, нарізування дроту, свердління, зняття фаски, шліфування, покриття та обробка поверхні. Наше сучасне обладнання може бути налаштовано для розробки дуже складних конструкцій будь-якої форми з жорсткими допусками. Ми пропонуємо різні типи кінців як сферичні, загострені або скошені кінці для ваших проводів. Більшість наших проектів формування дроту мають мінімальні або нульові витрати на інструменти. Зразок часу виконання зазвичай становить дні. Зміни в конструкції/конфігурації дротяних форм можна внести дуже швидко. • ФОРМУВАННЯ ПРУЖИН: AGS-TECH виробляє велику різноманітність пружин, включаючи: -Пружина кручення/подвійна кручення - Пружина розтягування/стиску -Постійна / змінна пружина -Гвинтова пружина -Плоска та листова пружина -Пружина балансу -Бельвільська пральна машина -Негатор Весна - Пружина прогресивної швидкості -Весна хвилі -Волютна пружина - Конічні пружини - Весняні кільця - Годинникові пружини -Кліпи Ми виготовляємо пружини з різноманітних матеріалів і можемо надати вам відповідну допомогу. Найбільш поширеними матеріалами є нержавіюча сталь, хромований кремній, високовуглецева сталь, загартована в маслі низьковуглецева сталь, хромованадій, фосфориста бронза, титан, сплав берилієвої міді, високотемпературна кераміка. Ми використовуємо різні технології у виготовленні пружин, включаючи намотування з ЧПУ, холодне намотування, гаряче намотування, загартування, обробку. Інші методи, уже згадані вище під формуванням дроту, також поширені в наших операціях з виробництва пружин. • ПОСЛУГИ ОБРОБКИ ДРОТІВ ТА ПРУЖИН: ми можемо завершити ваші вироби різними способами залежно від вашого вибору та потреб. Деякі з поширених процесів, які ми пропонуємо, це: фарбування, порошкове покриття, покриття, занурення у вініл, анодування, зняття напруги, термічна обробка, дробеструйна обробка, барабан, хромування, безелектричний нікель, пасивація, запечена емаль, пластикове покриття , очищення плазмою. CLICK Product Finder-Locator Service ПОПЕРЕДНЯ СТОРІНКА
- Sheet Metal Forming Fabrication, Stamping, Punching, Deep Drawing, CNC
Sheet Metal Forming and Fabrication, Stamping, Punching, Bending, Progressive Die, Spot Welding, Deep Drawing, Metal Blanking and Slitting at AGS-TECH Inc. Штампування та виготовлення листового металу Ми пропонуємо штампування листового металу, формування, формування, згинання, штампування, вирубування, різання, перфорування, надсікання, вирізування, стругання, пресування, виготовлення, глибоке витягування з використанням одинарних пуансонів / однотактних штампів, а також прогресивних штампів і прядіння, формування гуми та гідроформування; різання листового металу водоструменем, плазмою, лазером, пилою, полум'ям; збірка листового металу за допомогою зварювання, точкового зварювання; труби з листового металу вибухають і згинаються; обробка поверхні листового металу, включаючи фарбування зануренням або розпиленням, електростатичне порошкове покриття, анодування, покриття, напилення тощо. Наші послуги варіюються від швидкого створення прототипів з листового металу до великосерійного виробництва. Ми рекомендуємо вам натиснути тут, щобЗАВАНТАЖИТИ наші схематичні ілюстрації процесів виготовлення та штампування листового металу від AGS-TECH Inc. Це допоможе вам краще зрозуміти інформацію, яку ми надаємо нижче. • РІЗАННЯ ЛИСТОВОГО МЕТАЛУ: Ми пропонуємо відрізи та відрізки. Відрізи розрізають листовий метал по одній траєкторії за один раз, і в основному немає відходів матеріалу, тоді як при відрізах форма не може бути точно розташована, і тому певна кількість матеріалу витрачається даремно. Одним із наших найпопулярніших процесів є штампування, коли з листового металу вирізається шматок матеріалу круглої або іншої форми. Вирізаний шматок є відходами. Іншим варіантом пробивання є ДОВІБЛЕННЯ, де пробивають отвори прямокутної або витягнутої форми. З іншого боку, ЗАГОТУВАННЯ — це той самий процес, що й штампування, з відмінністю того, що вирізаний шматок є роботою та зберігається. FINE BLANKING, покращена версія штампування, створює надрізи з малими допусками та прямими гладкими краями та не вимагає вторинних операцій для досконалості заготовки. Іншим процесом, який ми часто використовуємо, є РІЗАННЯ, що є процесом різання, коли листовий метал розрізається двома протилежними круглими лезами по прямій або вигнутій траєкторії. Консервний нож є простим прикладом процесу розрізання. Ще один популярний для нас процес процес — це ПЕРФОРАЦІЯ, коли багато отворів круглої або іншої форми пробиваються в листовому металі за певним шаблоном. Типовим прикладом для перфорованого виробу є металеві фільтри з безліччю отворів для рідин. У NOTCHING, ще одному процесі різання листового металу, ми видаляємо матеріал із заготовки, починаючи з краю або в іншому місці, і ріжемо всередину, доки не буде отримана бажана форма. Це поступовий процес, коли кожна операція видаляє інший шматок, доки не буде отримано бажаний контур. Для невеликих виробничих тиражів ми іноді використовуємо відносно повільніший процес, який називається НІББЛЮВАННЯ, який складається з багатьох швидких ударів отворів, що перекриваються, щоб зробити більший і складніший розріз. У ПРОГРЕСИВНОМУ РІЗАННІ ми використовуємо серію різних операцій для отримання єдиного різу або певної геометрії. І, нарешті, вторинний процес ГОЛІННЯ допомагає нам покращити краї вже зроблених порізів. Використовується для зрізання сколів, нерівних країв на листовому металі. • ЗГИНАННЯ ЛИСТОВОГО МЕТАЛУ: окрім різання, згинання є важливим процесом, без якого ми не змогли б виробляти більшість виробів. Переважно холодна обробка, але іноді також виконується в теплому або гарячому стані. Для цієї операції ми використовуємо матриці та преси. У ПРОГРЕСИВНОМУ ЗГИНАННІ ми використовуємо серію різних операцій пуансона та матриці для отримання одного згину або певної геометрії. AGS-TECH використовує різноманітні процеси згинання та робить вибір залежно від матеріалу заготовки, його розміру, товщини, бажаного розміру згинання, радіуса, кривизни та кута згинання, місця згинання, економічності роботи, обсягів виробництва… тощо Ми використовуємо V-подібне згинання, коли V-подібний пуансон вдавлює листовий метал у V-подібний штамп і згинає його. Підходить як для дуже гострих, так і для тупих кутів, а також для проміжних кутів, включаючи 90 градусів. За допомогою штампів виконуємо ЗГИНАННЯ КРОМКИ. Наше обладнання дозволяє отримувати кути навіть більше 90 градусів. Під час згинання краю заготовка затиснута між притискною площадкою та матрицею, зона для згинання розташована на краю матриці, а решта заготовки утримується над space як консольна балка. Коли пуансон діє на консольну частину, він загинається за край матриці. ФЛАНТУВАННЯ - це процес згинання кромок, що призводить до кута 90 градусів. Основні цілі операції - усунення гострих країв і отримання геометричних поверхонь для полегшення з'єднання деталей. БІСТЕРЕННЯ, ще один поширений процес згинання краю, утворює завиток над краєм деталі. З іншого боку, ПІДГІВАННЯ призводить до того, що край аркуша повністю загинається сам на себе. У ШТАЦІ краї двох деталей загинають один на одного і з’єднують. З іншого боку, ПОДВІЙНЕ ШВОВАННЯ забезпечує водонепроникні та повітронепроникні з’єднання листового металу. Подібно до згинання країв, процес, який називається РОТАЦІЙНЕ ЗГИНАННЯ, розгортає циліндр із вирізаним під потрібним кутом і служить пуансоном. Коли зусилля передається на пуансон, він змикається з заготовкою. Канавка циліндра надає консольній частині потрібний кут. Канавка може мати кут менше або більше 90 градусів. У AIR BENDING нам не потрібно, щоб нижня матриця мала кутовий паз. Листовий метал підтримується двома поверхнями з протилежних сторін і на певній відстані. Потім пуансон прикладає зусилля в потрібному місці та згинає заготовку. ЗГИНАННЯ КАНАЛІВ виконується за допомогою пуансона та матриці у формі каналу, а U-подібний вигин досягається за допомогою U-подібного пуансона. OFFSET BENDING створює зміщення на листовому металі. ЗГИНАННЯ ВАЛКА, техніка, яка підходить для обробки товщиною та згинання великих шматків металевих пластин, використовує три валки для подачі та згинання пластин до бажаної кривизни. Рулони розташовуються так, щоб вийшов потрібний вигин роботи. Відстань і кут між валками контролюються для отримання бажаного результату. Рухливий ролик дає можливість контролювати кривизну. ФОРМУВАННЯ ТРУБ – ще одна популярна операція згинання листового металу, яка включає кілька штампів. Труби виходять після кількох дій. ГОФРЮВАННЯ виконується також операціями згинання. В основному це симетричне згинання через рівні проміжки по всьому шматку листового металу. Для гофрування можна використовувати різні форми. Гофрований листовий метал більш жорсткий і має кращу стійкість до згинання, тому його можна використовувати в будівельній галузі. ФОРМУВАННЯ ЛИСТОВОГО МЕТАЛУ, безперервний процес виробництва розгортається для згинання поперечних перерізів певної геометрії за допомогою валків, і заготовка згинається послідовними кроками, завершуючи роботу останнім валком. У деяких випадках використовується один рулон, а в деяких випадках серія рулонів. • КОМБІНОВАНІ ПРОЦЕСИ РІЗАННЯ ТА ГИНАННЯ ЛИСТОВОГО МЕТАЛУ: це процеси, які ріжуть і згинають одночасно. У ПІРСИНГУ отвір створюється за допомогою гострого пробійника. Коли пуансон розширює отвір у аркуші, матеріал одночасно згинається у внутрішній фланець для отвору. Отриманий фланець може мати важливі функції. З іншого боку, операція LANCING розрізає та згинає аркуш для створення рельєфної геометрії. • ВИПУСКАННЯ ТА ВИГИНАННЯ МЕТАЛЕВОЇ ТРУБКИ: під час ВИПУСКАННЯ деяка внутрішня частина порожнистої труби створюється під тиском, що призводить до випирання труби назовні. Оскільки трубка знаходиться всередині матриці, геометрія опуклості контролюється формою матриці. Під час ВИГИНАННЯ НА РОЗТЯГ металева труба розтягується за допомогою сил, паралельних осі труби, і сил згину, щоб натягнути трубу на блок форми. У DRAW BENDING ми затискаємо трубу біля її кінця до обертового блоку форми, який згинає трубу під час обертання. Нарешті, під час ВИГИНАННЯ СТИСКОМ труба силою утримується на фіксованому блоці форми, а матриця згинає її над блоком форми. • ГЛИБОКА ВИТЯЖКА: в одній із наших найпопулярніших операцій використовуються пуансон, відповідна матриця та тримач заготовки. Заготовка з листового металу розміщується над отвором матриці, і пуансон рухається до заготовки, яку утримує тримач заготовки. Коли вони вступають у контакт, пуансон змушує листовий метал потрапляти в порожнину матриці для формування виробу. Операція глибокої витяжки нагадує різання, однак зазор між пуансоном і матрицею запобігає розрізанню листа. Іншим фактором, який гарантує глибоку витяжку листа, а не розрізання, є закруглені кути матриці та пуансона, що запобігає зрізу та різанню. Щоб досягти більшої величини глибокої витяжки, розгортається процес ПЕРЕМАЛЮВАННЯ, де наступне глибоке витягування відбувається на деталі, яка вже пройшла процес глибокого витягування. У ЗВОРОТНОМУ ПЕРЕМАЛЮВАННІ глибоко намальована частина перевертається та малюється у протилежному напрямку. Глибоке витягування може забезпечити об’єкти неправильної форми, такі як куполоподібні, звужені або ступінчасті чашки, У ТИСНЕННІ ми використовуємо пару штампів, щоб відбити на листовому металі дизайн або сценарій. • СПІННУВАННЯ: операція, під час якої плоска або попередньо сформована заготовка утримується між обертовою оправкою та хвостовою заготовкою, а інструмент застосовує локальний тиск до заготовки, поступово просуваючись вгору по оправці. В результаті заготовка обертається на оправку і приймає форму. Ми використовуємо цю техніку як альтернативу глибокій витяжці, коли кількість замовлення невелика, деталі великі (діаметром до 20 футів) і мають унікальні криві. Незважаючи на те, що ціни за штуку, як правило, вищі, витрати на налаштування прядіння з ЧПК є низькими порівняно з глибоким витягуванням. Навпаки, глибока витяжка вимагає великих початкових інвестицій для налаштування, але витрати на одну штуку є низькими, коли виготовляється велика кількість деталей. Інша версія цього процесу - це ПРЕДІЛЕННЯ ЗРУЧЕННЯМ, де також є потік металу всередині заготовки. Потік металу зменшить товщину заготовки під час виконання процесу. Ще один споріднений процес — це ПРЕДІЛЕННЯ ТРУБ, яке застосовується до циліндричних деталей. Також у цьому процесі відбувається потік металу всередині заготовки. Таким чином товщина труби зменшується, а довжина збільшується. Інструмент можна переміщувати, щоб створювати елементи всередині або ззовні трубки. • ФОРМУВАННЯ ЛИСТОВОГО МЕТАЛУ ГУМОЮ: Гуму або поліуретановий матеріал поміщають у контейнерну матрицю, а заготовку кладуть на поверхню гуми. Потім на оброблювану деталь діє удар, який вдавлює її в гуму. Оскільки тиск, створюваний гумою, низький, глибина виготовлених деталей обмежена. Оскільки витрати на інструменти низькі, процес підходить для виробництва невеликої кількості. • ГІДРОФОРМУВАННЯ: Подібно до формування гуми, у цьому процесі листовий метал вдавлюється пуансоном у рідину під тиском усередині камери. Деталь з листового металу затиснута між пуансоном і гумовою діафрагмою. Діафрагма повністю оточує деталь, і тиск рідини змушує її формуватися на пуансоні. За допомогою цієї техніки можна отримати дуже глибокі малюнки, навіть глибші, ніж у процесі глибокого малювання. Ми виготовляємо одноштампові матриці, а також прогресивні матриці залежно від вашої деталі. Однотактні штампи для штампування є економічно ефективним методом для швидкого виготовлення великої кількості простих деталей з листового металу, наприклад шайб. Прогресивні штампи або техніка глибокої витяжки використовуються для виготовлення більш складних геометрій. Залежно від вашого випадку, гідроабразивне, лазерне або плазмове різання можна використовувати для виготовлення деталей з листового металу недорого, швидко та точно. Багато постачальників не мають уявлення про ці альтернативні методи або не мають їх, тому вони йдуть через тривалі та дорогі способи виготовлення штампів та інструментів, які лише витрачають час і гроші клієнтів. Якщо вам потрібні виготовлені на замовлення компоненти з листового металу, такі як корпуси, корпуси для електроніки тощо, протягом кількох днів, зв’яжіться з нами, щоб отримати нашу послугу ШВИДКОГО ПРОТОТИПУВАННЯ З ЛИСТОВОГО МЕТАЛУ. CLICK Product Finder-Locator Service ПОПЕРЕДНЄ МЕНЮ
- Forging and Powdered Metallurgy, Die Forging, Heading, Hot Forging
Forging and Powdered Metallurgy, Die Forging, Heading, Hot Forging, Impression Die, Near Net Shape, Swaging, Metal Hobbing, Riveting, Coining from AGS-TECH Inc. Кування та порошкова металургія Типи процесів КОВАННЯ МЕТАЛУ, які ми пропонуємо, включають гаряче та холодне штампування, відкриті штампування та закриті штампування, штампування та штампування без спалахів, cogging, фулінгування, окантовування та точне кування, майже чиста форма, заголовок , штампування, кування з висадкою, фрезерування металу, пресування та валкування, радіальне та орбітальне та кільце та ізотермічне кування, карбування, клепка, кування металевих кульок, проколювання металу, калібрування, кування з високим енергоспоживанням. Наші методи ПОРОШКОВОЇ МЕТАЛУРГІЇ та ОБРОБКИ ПОРОШКУ включають пресування та спікання порошку, просочення, інфільтрацію, гаряче та холодне ізостатичне пресування, лиття під тиском, ущільнення валків, прокатку порошку, екструзію порошку, сипуче спікання, іскрове спікання, гаряче пресування. Ми рекомендуємо вам натиснути тут, щоб ЗАВАНТАЖИТИ наші схематичні ілюстрації процесів кування від AGS-TECH Inc. ЗАВАНТАЖИТИ наші схематичні ілюстрації процесів порошкової металургії від AGS-TECH Inc. Ці завантажувані файли з фотографіями та ескізами допоможуть вам краще зрозуміти інформацію, яку ми надаємо нижче. Під час кування металу застосовуються сили стиснення, деформується матеріал і отримується необхідна форма. Найпоширенішими кованими матеріалами в промисловості є залізо та сталь, але багато інших, таких як алюміній, мідь, титан, магній, також широко куються. Ковані металеві деталі мають покращену зернисту структуру на додаток до герметичних тріщин і закритих порожніх просторів, тому міцність деталей, отриманих цим процесом, вища. Кування виготовляє деталі значно міцніші за свою вагу, ніж деталі, виготовлені литтям або механічною обробкою. Оскільки ковані деталі формуються шляхом приведення металу до остаточної форми, метал набуває спрямованої зернистої структури, що забезпечує високу міцність деталей. Іншими словами, деталі, отримані в процесі кування, демонструють кращі механічні властивості в порівнянні з простими литими або обробленими деталями. Вага металевих поковок може коливатися від невеликих легких деталей до сотень тисяч фунтів. Ми виготовляємо поковки здебільшого для механічно складних застосувань, де високі навантаження застосовуються до таких деталей, як автомобільні деталі, шестерні, робочі інструменти, ручні інструменти, вали турбін, мотоциклетний механізм. Оскільки витрати на інструменти та налаштування є відносно високими, ми рекомендуємо цей виробничий процес лише для великого виробництва та для невеликих обсягів, але високої вартості критичних компонентів, таких як аерокосмічне шасі. Крім вартості інструментів, час виготовлення великої кількості кованих деталей може бути довшим порівняно з деякими простими машинно обробленими деталями, але техніка має вирішальне значення для деталей, які вимагають надзвичайної міцності, як-от болти, гайки, спеціальне застосування кріплення, запчастини для автомобілів, навантажувачів, кранів. • КОВКА ГАРЯЧОГО ШТАМПУ та ХОЛОДНОГО ШТАМПУ: гаряче кування, як випливає з назви, виконується при високих температурах, тому пластичність висока, а міцність матеріалу низька. Це полегшує деформацію та кування. Навпаки, холодне кування виконується при нижчих температурах і вимагає вищих зусиль, що призводить до зміцнення деформацією, кращої обробки поверхні та точності виготовлених деталей. • КОВКА ВІДКРИТИМ штампом і штампом: при відкритому штампуванні штампи не обмежують стиснення матеріалу, тоді як при штампуванні порожнини всередині штампів обмежують потік матеріалу під час формування потрібної форми. КОВКА З ПЕРЕКЛАДАННЯМ або також званий КОВАННЯМ, що насправді не те саме, але дуже схожий процес, це процес відкритого штампування, де заготовку затискають між двома плоскими штампами, а сила стиснення зменшує її висоту. Оскільки висота is reduced, ширина заготовки збільшується. HEADING, процес кування осадкою включає циліндричну заготовку, яка висаджується на кінці, а її поперечний переріз локально збільшується. У заголовку матеріал подається через матрицю, кується, а потім розрізається на необхідну довжину. Операція здатна швидко виробляти велику кількість кріплень. Переважно це операція холодної обробки, оскільки вона використовується для виготовлення кінців цвяхів, кінців гвинтів, гайок і болтів, де матеріал потрібно зміцнити. Іншим процесом у відкритому штампі є ЗУБЧАННЯ, коли заготовку кують у ряд кроків, кожен з яких призводить до стиснення матеріалу та подальшого руху відкритої матриці вздовж заготовки. На кожному кроці товщина зменшується, а довжина трохи збільшується. Процес нагадує нервового учня, який дрібними кроками гризе свій олівець. Процес під назвою FULLERING — це ще один відкритий метод кування, який ми часто використовуємо як попередній етап для розподілу матеріалу в заготовці перед виконанням інших операцій кування металу. Ми використовуємо його, коли деталь вимагає кількох forging operations. В процесі роботи матриця з опуклою поверхнею деформується і викликає витікання металу в обидві сторони. З іншого боку, EDGING, подібний до обробки, включає відкриту матрицю з увігнутими поверхнями для деформації заготовки. Окантовка також є підготовчим процесом для наступних операцій кування, завдяки чому матеріал потік з обох сторін у зону в центрі. КОВКА ПІД ДИТМАННЯМ або ЗАКРИТА КОВАННЯ, як її ще називають, використовує матрицю/форму, яка стискає матеріал і обмежує його потік усередині себе. Матриця закривається, і матеріал приймає форму порожнини матриці/форми. ТОЧНЕ КОВУВАННЯ, процес, який потребує спеціального обладнання та прес-форми, виготовляє деталі без або з дуже незначним виплавленням. Іншими словами, деталі матимуть майже кінцеві розміри. У цьому процесі добре контрольована кількість матеріалу обережно вставляється та розміщується всередині форми. Ми застосовуємо цей метод для складних форм із тонкими перерізами, невеликими допусками та кутами осідання, а також коли кількість достатньо велика, щоб виправдати витрати на форму та обладнання. • КОВКА БЕЗ ВСПЛАШУВАННЯ: заготівлю поміщають у матрицю таким чином, щоб жоден матеріал не міг витекти з порожнини, щоб утворити врізку. Таким чином, небажане обрізання спалаху не потрібне. Це процес точного кування, тому вимагає ретельного контролю кількості використовуваного матеріалу. • ФОРМУВАННЯ МЕТАЛЮ або РАДІАЛЬНЕ КОВАННЯ: на заготовку по колу впливають штампи та кують. Оправка також може бути використана для кування внутрішньої геометрії заготовки. Під час обтискання деталь зазвичай отримує кілька ударів за секунду. Типовими виробами, виготовленими методом штампування, є інструменти із загостреним кінчиком, конічні стрижні, викрутки. • ПРОКОЛЮВАННЯ МЕТАЛУ: ми часто використовуємо цю операцію як додаткову операцію при виготовленні деталей. Отвір або порожнина створюється проколюванням на поверхні заготовки без її прориву. Будь ласка, зверніть увагу, що проколювання відрізняється від свердління, яке призводить до наскрізного отвору. • ФРЕЗЕРУВАННЯ: Пуансон з потрібною геометрією вдавлюється в оброблювану деталь і створює порожнину потрібної форми. Ми називаємо цей пунш HOB. Операція передбачає високий тиск і проводиться на холоді. В результаті матеріал піддається холодній обробці та зміцненню. Тому цей процес дуже підходить для виготовлення прес-форм, матриць і порожнин для інших виробничих процесів. Після виготовлення варильної панелі можна легко виготовити багато ідентичних порожнин, не обробляючи їх одну за одною. • КОВКА ВАЛЦІВ або ФОРМУВАННЯ ВАЛЦІВ: два протилежні валки використовуються для формування металевої частини. Заготовка подається в валки, валки повертаються і втягують заготовку в зазор, потім заготовка подається через рифлену частину валків, і стискаючі сили надають матеріалу бажаної форми. Це не процес прокатки, а процес кування, оскільки це дискретна, а не безперервна операція. Геометрія на валках кує матеріал до необхідної форми та геометрії. Виконується в гарячому вигляді. Оскільки це процес кування, він виробляє деталі з видатними механічними властивостями, тому ми використовуємо його для виробництва автомобільних деталей, таких як вали, які потребують надзвичайної витривалості у важких робочих умовах. • ОРБІТАЛЬНЕ КОВАННЯ: заготовку поміщають у порожнину ковальської форми та виковують верхньою матрицею, яка рухається по орбітальній траєкторії, коли обертається навколо похилої осі. Під час кожного оберту верхня матриця завершує дію стискаючої сили на всю заготовку. Повторюючи ці обороти кілька разів, виконується достатня кількість кування. Перевагами цієї технології виробництва є низький рівень шуму та низькі зусилля. Іншими словами, з невеликими зусиллями можна обертати важку матрицю навколо осі, щоб застосувати великий тиск до частини заготовки, яка контактує з матрицею. Деталі дискової або конічної форми іноді добре підходять для цього процесу. • КОВКА КІЛЬЦЯ: ми часто використовуємо для виробництва безшовних кілець. Заготовка обрізається до потрібної довжини, вивертається, а потім проколюється до кінця, щоб створити центральний отвір. Потім його надягають на оправку, і ковальська матриця забиває його зверху, коли кільце повільно обертається до отримання бажаних розмірів. • КЛЕПАННЯ: звичайний процес з’єднання деталей починається з прямої металевої деталі, яка вставляється в попередньо зроблені отвори крізь деталі. Після цього два кінці металевої частини виковуються шляхом стискання з’єднання між верхньою та нижньою матрицями. • КАРБАННЯ: Ще один популярний процес, який виконується механічним пресом, який докладає великих зусиль на короткій відстані. Назва «карбування» походить від дрібних деталей, викуваних на поверхні металевих монет. Здебільшого це процес фінішної обробки виробу, коли на поверхнях утворюються дрібні деталі в результаті великої сили, що прикладається матрицею, яка передає ці деталі на заготовку. • КОВАННЯ МЕТАЛЕВИХ КУЛЬК: Такі продукти, як кулькові підшипники, вимагають високоякісних точно виготовлених металевих кульок. В одній техніці під назвою КОСІЛЬНА ПРОКАТКА ми використовуємо два протилежні валки, які безперервно обертаються, коли матеріал безперервно подається в валки. На одному кінці двох валків металеві сфери викидаються як продукт. Другий спосіб кування металевої кульки полягає у використанні матриці, яка стискає заготовку матеріалу, розміщену між ними, набуваючи сферичну форму порожнини форми. Часто вироблені м’ячі вимагають деяких додаткових етапів, таких як фінішна обробка та полірування, щоб стати продуктом високої якості. • ІЗОТЕРМІЧНЕ КУВАННЯ / ГАРЯЧЕ КОВАННЯ: Дорогий процес, який виконується лише тоді, коли співвідношення вигод/витрат виправдане. Процес гарячої обробки, при якому матриця нагрівається приблизно до тієї ж температури, що й заготовка. Оскільки температура матриці та виробу приблизно однакова, охолодження не відбувається, а характеристики текучості металу покращуються. Ця операція добре підходить для суперсплавів і матеріалів з нижчою ковкоздатністю та матеріалів, чий механічні властивості дуже чутливі до малих температурних градієнтів і змін. • КАЛІРМУВАННЯ МЕТАЛУ: це процес холодної обробки. Потік матеріалу необмежений у всіх напрямках, за винятком напрямку, в якому прикладена сила. У результаті виходить дуже гарна обробка поверхні та точні розміри. • ВИСОКА ЕНЕРГЕТИЧНА ФОРМУВАННЯ: Техніка включає верхню форму, прикріплену до плеча поршня, який швидко штовхається, коли паливно-повітряна суміш запалюється свічкою запалювання. Це нагадує роботу поршнів у двигуні автомобіля. Форма дуже швидко вдаряється об деталь, а потім дуже швидко повертається у вихідне положення завдяки протитиску. Робота кується протягом кількох мілісекунд, тому у роботи немає часу охолонути. Це корисно для деталей, які важко кувати, які мають дуже чутливі до температури механічні властивості. Іншими словами, процес настільки швидкий, що деталь формується при постійній температурі протягом усього періоду, і не буде градієнтів температури на границях прес-форма/деталь. • У КОВАННІ ШТАМПАМИ метал тиснуть між двома відповідними сталевими блоками зі спеціальними формами в них, які називаються штампами. Коли метал забивають між штампами, він приймає ту саму форму, що й форми в штампі. Коли він досягає остаточної форми, його виймають для охолодження. Цей процес виробляє міцні деталі точної форми, але вимагає більших інвестицій для спеціальних штампів. Кування осадкою збільшує діаметр шматка металу шляхом його сплющення. Зазвичай він використовується для виготовлення дрібних деталей, особливо для формування головок на кріпленнях, таких як болти та цвяхи. • ПОРОШКОВА МЕТАЛУРГІЯ / ОБРОБКА ПОРОШКУ: як випливає з назви, це включає виробничі процеси для виготовлення твердих частин певної геометрії та форми з порошків. Якщо для цього використовуються металеві порошки, то це сфера порошкової металургії, а якщо використовуються неметалічні порошки, то це порошкова обробка. Суцільні деталі виготовляють із порошків шляхом пресування та спікання. ПРЕСУВАННЯ ПОРОШКУ використовується для пресування порошків у бажану форму. Спочатку первинний матеріал фізично подрібнюють, розділяючи його на безліч дрібних окремих частинок. Порошкова суміш засипається в матрицю, і пуансон рухається до порошку та ущільнює його до потрібної форми. Здебільшого виконується при кімнатній температурі, при пресуванні порошку виходить тверда частина, яка називається зеленим компактом. Зв'язувальні та мастильні речовини зазвичай використовуються для підвищення компактності. Ми можемо виготовляти порошковий прес за допомогою гідравлічних пресів потужністю кілька тисяч тонн. Також у нас є преси подвійної дії з протилежними верхніми та нижніми пуансонами, а також преси з кількома діями для дуже складних геометрій деталей. Однорідність, яка є важливою проблемою для багатьох заводів порошкової металургії/порошкової обробки, не є великою проблемою для AGS-TECH через наш великий досвід виготовлення таких деталей на замовлення протягом багатьох років. Навіть із більш товстими деталями, де однорідність є проблемою, ми досягли успіху. Якщо ми візьмемо участь у вашому проекті, ми виготовимо ваші частини. Якщо ми побачимо будь-які потенційні ризики, ми повідомимо вас in заздалегідь. СПІКАННЯ ПОРОШКУ, яке є другим етапом, передбачає підвищення температури до певного ступеня та підтримку температури на цьому рівні протягом певного часу, щоб частинки порошку в спресованій частині могли з’єднатися разом. Це призводить до значно міцнішого з’єднання та зміцнення заготовки. Спікання відбувається близько до температури плавлення порошку. При спіканні відбувається усадка, підвищується міцність матеріалу, щільність, пластичність, теплопровідність, електропровідність. У нас є печі для спікання періодичної та безперервної дії. Однією з наших можливостей є регулювання рівня пористості деталей, які ми виготовляємо. Наприклад, ми можемо виготовляти металеві фільтри, зберігаючи деталі певною мірою пористими. Використовуючи техніку, яка називається ПРОСОКУВАННЯ, ми заповнюємо пори в металі рідиною, такою як масло. Ми виробляємо, наприклад, просочені маслом підшипники, які є самозмащувальними. У процесі ІНФІЛЬТРАЦІЇ ми заповнюємо пори металу іншим металом з нижчою температурою плавлення, ніж основний матеріал. Суміш нагрівають до температури між температурами плавлення двох металів. В результаті можна отримати деякі особливі властивості. Ми також часто виконуємо допоміжні операції, такі як механічна обробка та кування деталей, виготовлених із порошку, коли потрібно отримати особливі характеристики чи властивості або коли деталь може бути виготовлена з меншою кількістю етапів процесу. ІЗОСТАТИЧНЕ ПРЕСУВАННЯ: у цьому процесі тиск рідини використовується для ущільнення деталі. Металеві порошки поміщають у форму, виготовлену з герметичної гнучкої ємності. При ізостатичному пресуванні тиск прикладається з усіх боків, на відміну від осьового тиску, який спостерігається при звичайному пресуванні. Перевагами ізостатичного пресування є рівномірна щільність всередині деталі, особливо для більших або товстих деталей, чудові властивості. Його недоліком є довгий час циклу і відносно низька геометрична точність. ХОЛОДНЕ ІЗОСТАТИЧНЕ ПРЕСОВУВАННЯ здійснюється при кімнатній температурі, а гнучка форма виготовляється з гуми, ПВХ, уретану чи подібних матеріалів. Рідиною, яка використовується для створення тиску та ущільнення, є масло або вода. За цим слідує звичайне спікання зеленої пресовки. З іншого боку, ГАРЯЧЕ ІЗОСТАТИЧНЕ ПРЕСОВУВАННЯ здійснюється при високих температурах, а матеріалом форми є листовий метал або кераміка з достатньо високою температурою плавлення, яка стійка до високих температур. Рідина, що створює тиск, зазвичай є інертним газом. Операції пресування і спікання виконуються в один етап. Практично повністю усувається пористість, виходить однорідна зерниста структура. Перевага гарячого ізостатичного пресування полягає в тому, що він може виробляти деталі, подібні до комбінованого лиття та кування, одночасно роблячи можливим використання матеріалів, які не підходять для лиття та кування. Недоліком гарячого ізостатичного пресування є його велика тривалість циклу і, отже, вартість. Він підходить для критичних частин малого обсягу. ЛИТТЯ ПИТАННЯМЕТАЛІВ: дуже підходить процес для виробництва складних деталей із тонкими стінками та детальною геометрією. Найкраще підходить для менших деталей. Порошки та полімерне сполучне змішують, нагрівають і вводять у форму. Полімерне сполучне покриває поверхні частинок порошку. Після формування сполучна речовина видаляється шляхом нагрівання при низькій температурі або розчиняється за допомогою розчинника. УЩОКУВАННЯ В РУЛОНАХ / РУЛЬКУВАННЯ ПОРОШКУ: порошки використовуються для виробництва безперервних смуг або листів. Порошок подається з живильника і ущільнюється двома обертовими валками в листи або стрічки. Операція проводиться холодною. Лист переноситься в піч для спікання. Процес спікання можна повторити вдруге. ЕКСТРУЗІЯ ПОРОШКУ: Деталі з великим відношенням довжини до діаметра виготовляються шляхом екструдування контейнера з тонкого листового металу з порошком. РЕЗУЛЬТАТНЕ СПІКАННЯ: Як випливає з назви, це метод ущільнення та спікання без тиску, придатний для виготовлення дуже пористих деталей, таких як металеві фільтри. Порошок подається в порожнину форми без ущільнення. РЕЗУЛЬТАТНЕ СПІКАННЯ: Як випливає з назви, це метод ущільнення та спікання без тиску, придатний для виготовлення дуже пористих деталей, таких як металеві фільтри. Порошок подається в порожнину форми без ущільнення. ІСКРОВЕ СПІКАННЯ: порошок стискається у прес-формі двома протилежними пуансонами, і електричний струм високої потужності подається на пуансон і проходить через ущільнений порошок, затиснутий між ними. Сильний струм спалює поверхневі плівки з частинок порошку та спікає їх за допомогою тепла, що виділяється. Процес швидкий, оскільки тепло не подається ззовні, а генерується зсередини форми. ГАРЯЧЕ ПРЕСОВУВАННЯ: порошки пресуються та спікаються за один етап у формі, яка витримує високі температури. Коли матриця ущільнюється, до неї піддається тепло порошку. Хороша точність і механічні властивості, досягнуті цим методом, роблять його привабливим варіантом. Навіть тугоплавкі метали можна обробляти за допомогою формових матеріалів, таких як графіт. CLICK Product Finder-Locator Service ПОПЕРЕДНЄ МЕНЮ
- Casting and Machined Parts, CNC Manufacturing, Milling, Turning, Swiss
Casting and Machined Parts, CNC Manufacturing, Milling, Turning, Swiss Type Machining, Die Casting, Investment Casting, Lost Foam Cast Parts from AGS-TECH Inc. Лиття та механічна обробка Наші нестандартні технології лиття та механічної обробки включають виливки одноразового та одноразового використання, лиття з чорних та кольорових металів, пісок, штампування, відцентрові, безперервні, керамічні форми, виплавку, втрачену піну, майже чисту форму, постійну форму (гравітаційне лиття під тиском), гіпс прес-форми (гіпсове лиття) і корпусні відливки, оброблені деталі, виготовлені шляхом фрезерування та токарної обробки з використанням традиційного обладнання та обладнання з ЧПК, обробка швейцарського типу для високопродуктивних недорогих дрібних прецизійних деталей, гвинтова обробка для кріплень, нетрадиційна обробка. Майте на увазі, що окрім металів і металевих сплавів, ми також обробляємо керамічні, скляні та пластикові компоненти в деяких випадках, коли виготовлення прес-форм не є привабливим або недоцільним. Механічна обробка полімерних матеріалів вимагає спеціального досвіду, який ми маємо, оскільки пластмаси та гума представляють складність через їхню м’якість, нежорсткість... тощо. Для обробки кераміки та скла перегляньте нашу сторінку про нетрадиційне виготовлення. AGS-TECH Inc. виробляє та постачає як легкі, так і важкі виливки. Ми постачаємо металеве лиття та оброблені деталі для котлів, теплообмінників, автомобілів, мікромоторів, вітрових турбін, обладнання для пакування харчових продуктів тощо. Радимо натиснути тут, щоб ЗАВАНТАЖИТИ наші схематичні ілюстрації процесів обробки та лиття від AGS-TECH Inc. Це допоможе вам краще зрозуміти інформацію, яку ми надаємо нижче. Давайте детально розглянемо деякі з різноманітних технік, які ми пропонуємо: • ВИЛИВКА В ВИТРАТНІ ФОРМИ: Ця широка категорія відноситься до методів, які включають тимчасові та одноразові форми. Прикладами є пісок, гіпс, черепашка, виплавлений матеріал (також званий втраченим воском) і гіпсове лиття. • ЛИТВО З ПІСУ: процес, у якому пісок використовується як матеріал для форми. Дуже старий метод і все ще дуже популярний до такої міри, що більшість вироблених металевих виливків виготовляється за цією технікою. Низька вартість навіть при низькій кількості виробництва. Підходить для виготовлення дрібних і великих деталей. Цю техніку можна використовувати для виготовлення деталей протягом кількох днів або тижнів із дуже невеликими інвестиціями. Вологий пісок скріплюється глиною, в’яжучими або спеціальними маслами. Пісок, як правило, міститься в формах, а система порожнин і воріт створюється шляхом ущільнення піску навколо моделей. Це процеси: 1.) Розміщення моделі в піску для виготовлення форми 2.) Включення моделі та піску в систему литників 3.) Видалення моделі 4.) Заповнення порожнини форми розплавленим металом 5.) Охолодження металу 6.) Розбивання піщаної форми та видалення відливки • ВИТРИВАННЯ В ГІПСОВІ ФОРМИ: Подібно до виливання в пісок, але замість піску в якості матеріалу для форм використовується паризький гіпс. Короткі терміни виготовлення, наприклад лиття в пісок, і недорогі. Хороші допуски на розміри та обробку поверхні. Його основним недоліком є те, що його можна використовувати лише з металами з низькою температурою плавлення, такими як алюміній і цинк. • ВИТРИВАННЯ У ФОРМУ: також схоже на лиття в пісок. Порожнина прес-форми, отримана за допомогою затверділої оболонки з піску та зв’язуючої термореактивної смоли замість колби, заповненої піском, як у процесі лиття в пісок. Майже будь-який метал, придатний для лиття з піску, можна відлити за допомогою формування в оболонку. Процес можна коротко описати так: 1.) Виготовлення оболонкової форми. Використовуваний пісок має набагато менший розмір зерна порівняно з піском, який використовується для лиття в пісок. Дрібний пісок змішується з термореактивною смолою. Металевий візерунок покритий розділовим засобом для полегшення видалення оболонки. Після цього металевий малюнок нагрівають, а піщану суміш посипають або видувають на гарячий литий шаблон. На поверхні візерунка утворюється тонка оболонка. Товщину цієї оболонки можна регулювати, змінюючи тривалість контакту піщано-смолової суміші з металевим малюнком. Потім видаляють сипучий пісок, залишаючи візерунок, покритий мушлею. 2.) Далі шкаралупу і викрійку розігрівають у духовці, щоб шкаралупа затверділа. Після завершення затвердіння оболонка витягується з шаблону за допомогою штифтів, вбудованих у шаблон. 3.) Дві такі оболонки збираються разом шляхом склеювання або затискання та складають повну форму. Тепер форма-оболочка вставляється в контейнер, у якому вона підтримується піском або металевою дробом під час процесу лиття. 4.) Тепер розпечений метал можна вилити в форму. Перевагами корпусного лиття є вироби з дуже гарною обробкою поверхні, можливість виготовлення складних деталей з високою точністю розмірів, легкість автоматизації процесу, економічність для великого виробництва. Недоліки полягають у тому, що прес-форми потребують хорошої вентиляції через гази, які утворюються, коли розплавлений метал контактує зі сполучною речовиною, термореактивні смоли та металеві візерунки є дорогими. Через вартість металевих візерунків ця техніка може не підійти для виробництва малої кількості. • ЛИТВО ЗА ВИКОРИСТАННЯМ (також відоме як ЛИТВО ЗА ВИТРАЧЕННЯМ ВОСПКУ): також дуже стара технологія, придатна для виготовлення якісних деталей з високою точністю, повторюваністю, універсальністю та цілісністю з багатьох металів, вогнетривких матеріалів і спеціальних високоефективних сплавів. Можна виготовити деталі невеликого та великого розміру. Дорогий процес у порівнянні з деякими іншими методами, але головною перевагою є можливість виготовляти деталі майже чистої форми, складних контурів і деталей. Таким чином, вартість дещо компенсується усуненням переробки та механічної обробки в деяких випадках. Незважаючи на те, що можуть бути варіації, ось короткий виклад загального процесу лиття за виплавленими моделями: 1.) Створення оригінальної майстер-схеми з воску або пластику. Для кожного відливка потрібен один шаблон, оскільки він руйнується в процесі. Також потрібна форма, з якої виготовляють візерунки, і в більшості випадків форму відливають або обробляють. Оскільки прес-форму не потрібно відкривати, можна отримати складні виливки, багато воскових візерунків можна з’єднати, як гілки дерева, і залити разом, таким чином дозволяючи виготовляти кілька деталей з однієї заливки металу або металевого сплаву. 2.) Далі візерунок занурюють або заливають вогнетривкою суспензією, що складається з дуже дрібнозернистого кремнезему, води та сполучних речовин. Це призводить до утворення керамічного шару на поверхні малюнка. Вогнетривке покриття на викрійці залишають для висихання і твердіння. Саме з цього етапу походить назва лиття по виплавленим моделям: вогнетривкий шлам вкладається поверх воскової моделі. 3.) На цьому етапі загартована керамічна форма перевертається догори дном і нагрівається, щоб віск розплавився та вилився з форми. Позаду залишається порожнина для металевого лиття. 4.) Після виходу воску керамічна форма нагрівається до ще більш високої температури, що призводить до зміцнення форми. 5.) Металева відливка заливається в гарячу форму, заповнюючи всі складні секції. 6.) Виливку дають застигнути 7.) Нарешті керамічна форма розбивається, а виготовлені деталі вирізаються з дерева. Ось посилання на брошуру заводу лиття по моделлю • ВИПАРЮВАЛЬНИЙ МЕТАЛ ЛИТТЯ: у цьому процесі використовується шаблон, виготовлений із такого матеріалу, як пінополістирол, який випаровується, коли гарячий розплавлений метал заливається у форму. Існує два типи цього процесу: ВИТРИВАННЯ В ПІНУ, при якому використовується незв’язаний пісок, і ПОВНЕ ВИТРИВАННЯ, у якому використовується зв’язаний пісок. Ось загальні кроки процесу: 1.) Виготовте візерунок із такого матеріалу, як полістирол. Коли буде виготовлено велику кількість, викрійка ліпиться. Якщо деталь має складну форму, для формування візерунка може знадобитися склеїти кілька ділянок такого спіненого матеріалу. Ми часто покриваємо візерунок вогнетривким складом, щоб створити якісну поверхню виливка. 2.) Потім шаблон поміщають у формувальний пісок. 3.) Розплавлений метал заливається у форму, випаровуючи пінопласт, тобто полістирол у більшості випадків, коли він протікає через порожнину форми. 4.) Розплавлений метал залишають у піщаній формі для твердіння. 5.) Після застигання знімаємо лиття. У деяких випадках для виробу, який ми виготовляємо, потрібен стрижень у візерунку. У випарному литті немає необхідності розміщувати та закріплювати стрижень у порожнині форми. Технологія підходить для виготовлення дуже складних геометричних форм, її можна легко автоматизувати для виробництва великого обсягу, і в литій частині немає ліній розділення. Основний процес простий і економічний у реалізації. Для виробництва великих обсягів, оскільки для виготовлення візерунків з полістиролу потрібна матриця або прес-форма, це може бути дещо дорогим. • ВИЛИВКА В НЕРОЗШИРЮВАЛЬНУ ФОРМУ: Ця широка категорія відноситься до методів, за яких форму не потрібно переформовувати після кожного виробничого циклу. Прикладами є постійне лиття, лиття під тиском, безперервне та відцентрове лиття. Отримано повторюваність, і деталі можна охарактеризувати як БЛИЗЬКУ ЧИСТУ ФОРМУ. • ВИТРИВАННЯ В ПОСТІЙНУ ФОРМУ: багаторазові форми з металу використовуються для багаторазового лиття. Постійну форму зазвичай можна використовувати десятки тисяч разів, перш ніж вона зношується. Гравітація, тиск газу або вакуум зазвичай використовуються для заповнення форми. Прес-форми (також звані матрицями) зазвичай виготовляються із заліза, сталі, кераміки або інших металів. Загальний процес: 1.) Обробіть та створіть форму. Зазвичай форму виготовляють із двох металевих блоків, які підходять один до одного та можуть відкриватися та закриватися. Як деталі, так і ліберна система, як правило, обробляються у ливарну форму. 2.) Внутрішні поверхні форми покриті суспензією, що містить вогнетривкі матеріали. Це допомагає контролювати потік тепла та діє як мастило для легкого видалення литої частини. 3.) Далі постійні половини форми закриваються і форма нагрівається. 4.) Розплавлений метал виливають у форму та залишають для застигання. 5.) Перед тим, як настане значне охолодження, ми виймаємо деталь із постійної форми за допомогою ежекторів, коли половини форми відкриваються. Ми часто використовуємо постійне лиття в форму для металів з низькою температурою плавлення, таких як цинк і алюміній. Для сталевих відливок ми використовуємо графіт як матеріал для форм. Іноді ми отримуємо складну геометрію, використовуючи стрижні в постійних формах. Перевагами цієї технології є виливки з хорошими механічними властивостями, отриманими шляхом швидкого охолодження, однорідність властивостей, хороша точність і обробка поверхні, низький відсоток браку, можливість автоматизації процесу та економічне виробництво великих обсягів. Недоліками є високі початкові витрати на налаштування, що робить його непридатним для операцій з невеликим обсягом, і обмеження розміру виготовлених деталей. • ЛИТТЯ ПІД ПИТАННЯМ: матриця обробляється, а розплавлений метал проштовхується під високим тиском у порожнини форми. Можливе лиття під тиском як з кольорових, так і з чорних металів. Процес підходить для великої кількості виробничих партій малих і середніх деталей з деталями, надзвичайно тонкими стінками, постійністю розмірів і гарною обробкою поверхні. AGS-TECH Inc. здатна виготовляти стінки товщиною всього 0,5 мм за цією технікою. Як і в постійній ливарній формі, форма повинна складатися з двох половин, які можуть відкриватися та закриватися для видалення виготовленої частини. Прес-форма для лиття під тиском може мати кілька порожнин, щоб уможливити виготовлення кількох виливків під час кожного циклу. Прес-форми для лиття під тиском дуже важкі та набагато більші за деталі, які вони виготовляють, тому також дорогі. Ми безкоштовно ремонтуємо та замінюємо зношені матриці для наших клієнтів, якщо вони повторно замовляють у нас свої запчастини. Наші матриці мають тривалий термін служби в діапазоні кількох сотень тисяч циклів. Ось основні спрощені етапи процесу: 1.) Виготовлення форми, як правило, зі сталі 2.) Форма, встановлена на машині для лиття під тиском 3.) Поршень змушує розплавлений метал текти в порожнинах матриці, заповнюючи складні деталі та тонкі стінки 4.) Після заповнення ливарної форми розплавленим металом відливання дають затвердіти під тиском 5.) Форма відкривається і виливка виймається за допомогою виштовхувальних штифтів. 6.) Тепер порожні матриці знову змащуються та затискаються для наступного циклу. Під час лиття під тиском ми часто використовуємо вставку, коли ми вставляємо додаткову деталь у форму та відливаємо метал навколо неї. Після застигання ці деталі стають частиною литого виробу. Перевагами лиття під тиском є добрі механічні властивості деталей, можливість створення складних деталей, дрібні деталі та хороша обробка поверхні, високі показники виробництва, легка автоматизація. Недоліки: не дуже підходить для малого об’єму через високу вартість матриці та обладнання, обмеження у формах, які можна відлити, невеликі круглі сліди на литих деталях у результаті контакту виштовхувальних штифтів, тонкий шматок металу, видавлений на лінії роз’єднання, потреба для вентиляційних отворів уздовж лінії розділення між матрицею, необхідність підтримувати низьку температуру форми за допомогою циркуляції води. • ЦЕНТРОБІЖНЕ ЛИТТЯ: Розплавлений метал заливається в центр обертової форми на осі обертання. Відцентрові сили відкидають метал до периферії, і він застигає, оскільки форма продовжує обертатися. Можна використовувати як горизонтальне, так і вертикальне обертання осі. Можна відливати деталі з круглою внутрішньою поверхнею, а також інші некруглі форми. Процес можна коротко описати так: 1.) Розплавлений метал заливають у відцентрову форму. Потім метал витісняється до зовнішніх стінок завдяки обертанню форми. 2.) Коли форма обертається, металеве лиття твердне Відцентрове лиття є придатною технікою для виробництва порожнистих циліндричних деталей, таких як труби, немає потреби в литниках, стояках і литникових елементах, гарна обробка поверхні та деталі, відсутність проблем з усадкою, можливість виготовляти довгі труби з дуже великим діаметром, висока швидкість виробництва . • НЕПЕРЕРВНЕ ЛИТТЯ (ЛИТВО СТРУГИ): Використовується для безперервного лиття металу. В основному розплавлений метал відливають у двовимірний профіль прес-форми, але його довжина невизначена. Новий розплавлений метал постійно подається в форму, коли відливка рухається вниз, а її довжина з часом збільшується. Такі метали, як мідь, сталь, алюміній, відливають у довгі нитки за допомогою процесу безперервного лиття. Процес може мати різні конфігурації, але загальну можна спростити так: 1.) Розплавлений метал виливається в ємність, розташовану високо над прес-формою, з добре розрахованими кількостями та швидкістю потоку та протікає через охолоджувану водою форму. Металевий відливок, залитий у форму, твердне до стартового бруска, розміщеного на дні форми. Ця стартова планка дає роликам те, за що можна схопитися спочатку. 2.) Довге металеве пасмо переміщується роликами з постійною швидкістю. Ролики також змінюють напрямок потоку металевої пасма з вертикального на горизонтальний. 3.) Після того, як безперервне лиття пройде певну горизонтальну відстань, пальник або пила, яка рухається разом із литтям, швидко розрізає його на бажану довжину. Процес безперервного лиття можна інтегрувати з ПРОЦЕСОМ ПРОКАТКИ, коли безперервно литий метал можна подавати безпосередньо в прокатний стан для виготовлення двотаврових балок, таврових балок… тощо. Безперервне лиття забезпечує однакові властивості всього продукту, має високу швидкість затвердіння, знижує вартість завдяки дуже низьким втратам матеріалу, пропонує процес, у якому завантаження металу, заливка, затвердіння, різання та видалення лиття відбуваються в безперервній операції та що забезпечує високу продуктивність і високу якість. Однак основним фактором є високі початкові інвестиції, витрати на встановлення та вимоги до місця. • ПОСЛУГИ ОБРОБКИ: Ми пропонуємо три, чотири та п'яти осі обробки. Типи процесів обробки, які ми використовуємо, це ТОЧАРНА, ФРЕЗЕРНА, СВЕРДЛІВНА, РОЗТОЧУВАЛЬНА, ПРОШИКУВАЛЬНА ТЕХНІКА, СТРУГАННЯ, РОЗПИЛЮВАННЯ, ШЛІФУВАННЯ, ПРИТРИВАННЯ, ПОЛІРУВАННЯ та НЕТРАДИЦІЙНА ОБРОБКА, яка детальніше описана в іншому меню нашого веб-сайту. Для більшості наших виробництв ми використовуємо верстати з ЧПК. Однак для деяких операцій звичайні методи краще підходять, тому ми також покладаємося на них. Наші можливості обробки досягають найвищого можливого рівня, і деякі найвибагливіші деталі виготовляються на заводі, сертифікованому AS9100. Лопаті реактивних двигунів вимагають високоспеціалізованого досвіду виробництва та відповідного обладнання. Аерокосмічна промисловість має дуже жорсткі стандарти. Деякі компоненти зі складною геометричною структурою найпростіше виготовити за допомогою п’ятиосьової обробки, яка доступна лише на деяких обробних підприємствах, включаючи наш. Наш аерокосмічний сертифікований завод має необхідний досвід, щоб відповідати великим вимогам до документації аерокосмічної промисловості. Під час токарних операцій заготовка обертається та переміщується проти ріжучого інструменту. Для цього процесу використовується верстат під назвою токарний верстат. У ФРЕЗЕРУВАННІ верстат, який називається фрезерним верстатом, має інструмент, що обертається, щоб притиснути ріжучі кромки до заготовки. Операції СВЕРДЛІННЯ включають обертовий різець з ріжучими кромками, який створює отвори при контакті з заготовкою. Зазвичай використовуються свердлильні верстати, токарні верстати або фрези. Під час операцій РОЗТОЧУВАННЯ інструмент із одним зігнутим загостреним наконечником переміщується в грубий отвір у обертовій заготовці, щоб трохи збільшити отвір і підвищити точність. Використовується для тонкої обробки. ПРОТЯЖКА включає в себе зубчастий інструмент для видалення матеріалу із заготовки за один прохід протяжки (зубчастий інструмент). При лінійному протягуванні протяжка проходить лінійно до поверхні заготовки, щоб здійснити розріз, тоді як при ротаційному протягуванні протяжка обертається та вдавлюється в заготовку, щоб вирізати осесиметричну форму. ОБРОБКА ШВЕЙЦАРСЬКОГО ТИПУ — одна з наших цінних технік, які ми використовуємо для виробництва великих обсягів невеликих високоточних деталей. Використовуючи токарний верстат швейцарського типу, ми недорого точимо невеликі, складні, прецизійні деталі. На відміну від звичайних токарних верстатів, де деталь залишається нерухомою, а інструмент рухається, у токарних центрах швейцарського типу деталь може рухатися по осі Z, а інструмент нерухомий. При обробці швейцарського типу пруток утримується у верстаті та просувається через направляючу втулку по осі z, відкриваючи лише частину, яка підлягає обробці. Таким чином забезпечується щільне захоплення та висока точність. Наявність живих інструментів дає можливість фрезерувати та свердлити в міру просування матеріалу від направляючої втулки. Вісь Y обладнання швейцарського типу забезпечує повні можливості фрезерування та економить багато часу на виробництві. Крім того, наші верстати мають свердла та розточувальні інструменти, які працюють на деталі, коли вона утримується на допоміжному шпинделі. Наші можливості обробки швейцарського типу дають нам можливість повністю автоматизованої обробки за одну операцію. Механічна обробка є одним із найбільших сегментів бізнесу AGS-TECH Inc. Ми використовуємо це або як основну операцію, або як допоміжну операцію після лиття чи екструдування деталі, щоб відповідати всім специфікаціям креслення. • ПОСЛУГИ З ОБРОБКИ ПОВЕРХНІ: ми пропонуємо широкий спектр обробки поверхні та обробки поверхні, наприклад кондиціонування поверхні для покращення адгезії, нанесення тонкого оксидного шару для покращення адгезії покриття, піскоструминна обробка, хімічна плівка, анодування, азотування, порошкове покриття, напилення. , різноманітні вдосконалені методи металізації та покриття, включаючи напилення, електронний промінь, випаровування, покриття, тверді покриття, такі як алмазоподібний вуглець (DLC) або титанове покриття для свердлильних і ріжучих інструментів. • ПОСЛУГИ З МАРКУВАННЯ ТА ЕТИКУВАННЯ ПРОДУКЦІЇ: багато наших клієнтів потребують маркування та маркування, лазерного маркування, гравіювання на металевих частинах. Якщо у вас є така потреба, давайте обговоримо, який варіант буде найкращим для вас. Ось деякі з часто використовуваних металевих литих виробів. Оскільки вони є готовими, ви можете заощадити на витратах на форми, якщо будь-яка з них відповідає вашим вимогам: НАТИСНІТЬ ТУТ, ЩОБ ЗАВАНТАЖИТИ наші литі під тиском алюмінієві коробки 11 серії від AGS-Electronics CLICK Product Finder-Locator Service ПОПЕРЕДНЯ СТОРІНКА
- Custom Manufactured Parts, Assemblies, Plastic Mold, Casting,Machining
Custom Manufactured Parts, Assemblies, Plastic Mold, Rubber Molding, Metal Casting, CNC Machining, Turning, Milling, Electrical Electronic Optical Assembly PCBA Деталі, вузли та продукти, виготовлені на замовлення Детальніше Пластмасові та гумові форми та лиття Детальніше Лиття та механічна обробка Детальніше Екструзії, пресовані вироби Детальніше Штампування та виготовлення листового металу Детальніше Кування та порошкова металургія Детальніше Дріт і формування пружин Детальніше Формування скла та кераміки Детальніше Адитивне та швидке виробництво Детальніше Виробництво композитів і композитних матеріалів Детальніше Процеси з'єднання, складання та кріплення Ми виготовляємо для вас деталі та вузли та пропонуємо наступні процеси виробництва: • Пластикові та гумові форми та фасонні деталі. Лиття під тиском, термоформування, термореактивне формування, вакуумне формування, роздувне формування, ротаційне формування, лиття, формування вставками та інші. • Пластикові, гумові та металеві екструзії • Відливки з чорних і кольорових металів і оброблені деталі, виготовлені за допомогою фрезерних і токарних технологій, швейцарської обробки. • Деталі порошкової металургії • Металева і неметалева штамповка, формування листового металу, зварні вузли листового металу • Холодне та гаряче кування • Дріт, вузли зварні, формування дроту • Різні типи пружин, формування пружин • Виробництво зубчастих передач, коробка передач, муфта, черв'як, редуктор, циліндр, трансмісійні паси, трансмісійні ланцюги, компоненти трансмісії • Спеціальне загартоване та куленепробивне скло, що відповідає стандартам НАТО та військовим стандартам • Кульки, підшипники, шківи та вузли шківів • Клапани та пневматичні компоненти, такі як ущільнювальні кільця, шайби та ущільнення • Скляні та керамічні деталі та вузли, вакуумостійкі та герметичні компоненти, металокерамічне та кераміко-керамічне склеювання. • Різні види механічних, оптико-механічних, електромеханічних, оптико-електронних вузлів. • Склеювання метал-гума, метал-пластик • Труби та труби, формування труб, згинання та збірки труб на замовлення, виробництво сильфонів. • Виробництво склопластику • Зварювання різними способами, такими як точкове зварювання, лазерне зварювання, MIG, TIG. Ультразвукове зварювання пластикових деталей. • Величезний вибір поверхневих обробок і оздоблення, таких як кондиціонування поверхні для покращення адгезії, нанесення тонкого оксидного шару для покращення адгезії покриття, піскоструминна обробка, хімічна плівка, анодування, азотування, порошкове покриття, розпилення, різноманітні вдосконалені методи металізації та покриття включаючи напилення, електронний промінь, випаровування, покриття, тверді покриття, такі як алмазоподібний вуглець (DLC) або титан для ріжучих і свердлильних інструментів. • Маркування та маркування, лазерне маркування на металевих деталях, друк на пластикових та гумових деталях Завантажте брошуру з загальними термінами машинобудування, які використовуються дизайнерами та інженерами Ми створюємо продукти відповідно до ваших конкретних специфікацій і вимог. Щоб запропонувати вам найкращу якість, доставку та ціни, ми виробляємо продукцію по всьому світу в Китаї, Індії, Тайвані, Філіппінах, Південній Кореї, Малайзії, Шрі-Ланці, Туреччині, США, Канаді, Німеччині, Великобританії та Японії. Це робить нас набагато сильнішими та глобально конкурентоспроможнішими, ніж будь-який інший custom manufacturer. Наші продукти виробляються в сертифікованих середовищах ISO9001:2000, QS9000, ISO14001, TS16949, мають позначки CE, UL і відповідають іншим галузевим стандартам. Після того, як ми будемо призначені для вашого проекту, ми можемо подбати про все виробництво, складання, випробування, кваліфікацію, доставку та митницю за вашим бажанням. Якщо ви віддаєте перевагу, ми можемо зберігати ваші запчастини, складати індивідуальні набори, надрукувати та маркувати назву та бренд вашої компанії та відправляти вашим клієнтам. Іншими словами, ми також можемо бути вашим складським і розподільним центром, якщо бажаєте. Оскільки наші склади розташовані поблизу великих морських портів, це дає нам логістичну перевагу. Наприклад, коли ваша продукція прибуває до великого морського порту США, ми можемо транспортувати її безпосередньо на сусідній склад, де ми можемо зберігати, складати, виготовляти набори, змінювати етикетки, друкувати, пакувати відповідно до вашого вибору та відправляти відправити своїм клієнтам. Ми не тільки постачаємо продукцію. Наша компанія працює за спеціальними контрактами, коли ми приходимо на ваше місце, оцінюємо ваш проект на місці та розробляємо проектну пропозицію, розроблену спеціально для вас. Потім ми направляємо нашу досвідчену команду для реалізації проекту. Більше інформації про нашу інженерну роботу можна знайти на http://www.ags-engineering.com - Ми беремо невеликі проекти, а також великі проекти промислового масштабу. Як перший крок, ми можемо з’єднати вас за допомогою телефону, телеконференції чи MSN Messenger з членами нашої команди експертів, щоб ви могли безпосередньо спілкуватися з експертом, ставити запитання та обговорювати свій проект. Зателефонуйте нам, і якщо потрібно, ми приїдемо до вас. ПОПЕРЕДНЯ СТОРІНКА
- Plastic And Rubber Molding | United States | AGS-TECH, Inc.
AGS-TECH Inc., Molding, Casting, Machining, Forging, Sheet Metal Fabrication, Mechanical Electrical Electronic Optical Assembly, PCBA, Powder Metallurgy, CNC AGS-TECH Inc. AGS-TECH Inc. Custom Manufacturing, Domestic & Global Outsourcing, Engineering Integration, Consolidation AGS-TECH Inc. 1/2 AGS-TECH, Inc. це ваш: Глобальний індивідуальний виробник, інтегратор, консолідатор, аутсорсинговий партнер для широкого спектру продуктів і послуг. Ми є вашим єдиним джерелом для виробництва, виготовлення, проектування, консолідації, аутсорсингу виготовлених на замовлення та готових продуктів. ПОСЛУГИ: Виготовлення на замовлення Внутрішнє та глобальне контрактне виробництво Аутсорсинг виробництва Внутрішні та міжнародні закупівлі Consolidation Інженерна інтеграція ПРО AGS-TECH, Inc. - Ваш глобальний індивідуальний виробник, Інженерний інтегратор, Консолідатор, Аутсорсинговий партнер AGS-TECH Inc. є виробником, інженерним інтегратором, глобальним постачальником промислової продукції, включаючи прес-форми, формовані пластикові та гумові деталі, виливки, екструзії, виготовлення листового металу, штампування та кування, обробку з ЧПУ, елементи машин, порошкову металургію, кераміку та формування скла, формування дроту/пружини, з’єднання та складання та кріплення, нетрадиційне виготовлення, мікровиробництво, нанотехнологічні покриття та тонка плівка, спеціальні механічні та електричні електронні компоненти та вузли, друковані плати та друковані плати та кабельні джгути, оптичні та волоконно-оптичні компоненти та складання , випробувальне та метрологічне обладнання, таке як вимірювачі твердості, металургійні мікроскопи, ультразвукові детектори несправностей, промислові комп’ютери, вбудовані системи, автоматизація та панельні ПК, одноплатні комп’ютери, обладнання для контролю якості. Крім продуктів, ми пропонуємо технічну, логістичну та бізнес-допомогу, щоб зробити вас більш конкурентоспроможними та успішними на глобальних ринках, завдяки нашим глобальним інженерним розробкам, зворотній інженерії, дослідженням і розробкам, розробці продуктів, адитивному та швидкому виробництву, створенню прототипів, можливостям управління проектами. Наша місія проста: зробити так, щоб наші клієнти досягали успіху та розвивалися. як? Забезпечуючи 1.) Кращу якість 2.) Кращу ціну 3.) Кращу доставку........ усе від однієї компанії та найрізноманітнішого світового інженерного інтегратора та постачальника AGS-TECH Inc. Ви можете надати нам свої креслення, і ми зможемо виготовити прес-форми, штампи та інструменти для виготовлення ваших деталей. Ми виробляємо їх шляхом формування, лиття, екструзії, кування, виготовлення листового металу, штампування, порошкової металургії, обробки з ЧПУ, формування. Ми можемо відправити вам деталі та компоненти або виконати складання, виготовлення та повні виробничі операції на наших підприємствах. Наші монтажні операції включають механічні, оптичні, електронні та волоконно-оптичні вироби. Виконуємо роботи з’єднання за допомогою кріплення, зварювання, паяння, паяння, склеювання та інше. Наші процеси формування призначені для різноманітних матеріалів із пластику, гуми, кераміки, скла та порошкової металургії. Так само є наші лиття, обробка з ЧПУ, кування, виготовлення листового металу, формування дроту та пружин, які включають метали, сплави, пластик, кераміку. Ми пропонуємо завершальні фінішні операції, такі як покриття, тонка та товста плівка, шліфування, притирання, полірування тощо. Наші виробничі можливості виходять за рамки механічного складання. Ми виробляємо електричні електронні компоненти та збірки, друковані плати та друковані плати та кабельні джгути, оптичні та волоконно-оптичні компоненти та збірки відповідно до ваших технічних креслень, специфікації матеріалів, файлів Gerber. Застосовуються різні технології виробництва друкованих плат і друкованих плат, включаючи пайку оплавленням і пайку хвилею. Ми є експертами в прецизійному з'єднанні, з'єднанні, складанні та герметизації герметичних електронних і волоконно-оптичних пакетів і виробів. Окрім пасивного та активного механічного складання, ми використовуємо спеціальні матеріали та технології для пайки та паяння для виготовлення виробів, які відповідають стандартам Telcordia та іншим галузевим стандартам. Ми не обмежені великими обсягами виробництва та виготовлення. Майже кожен проект починається з потреби в проектуванні, зворотному проектуванні, дослідженнях і розробці, розробці продукту, адитивному та швидкому виробництві, створенні прототипів. Як найрізноманітніший у світі виробник на замовлення, інженерний інтегратор, консолідатор, аутсорсинговий партнер, ми вітаємо вас, навіть якщо у вас є лише ідеї. Ми беремо вас звідти та допомагаємо вам на всіх етапах успішної повної розробки продукту та циклу виробництва. Незалежно від того, чи йдеться про швидке виготовлення листового металу, швидку обробку прес-форм і формування, швидке лиття, швидке складання друкованих плат і друкованих плат або будь-яку техніку швидкого створення прототипів – до ваших послуг. Ми пропонуємо вам готове метрологічне обладнання, а також виготовлене на замовлення, таке як вимірювачі твердості, металургійні мікроскопи, ультразвукові дефектоскопи; промислові комп’ютери, вбудовані системи, автоматизація та панельні ПК, одноплатні комп’ютери та обладнання для контролю якості, які широко використовуються у виробництві та промислових об’єктах. Пропонуючи вам найсучасніше метрологічне обладнання та промислові комп’ютерні компоненти, ми доповнюємо ваші потреби як єдиного виробника та постачальника, де ви можете отримати все, що вам потрібно. Без широкого спектру інженерних послуг ми б нічим не відрізнялися від більшості інших виробників і продавців з обмеженими можливостями індивідуального виробництва та складання, які існують на ринку. Обсяг наших інженерних послуг виділяє нас як найрізноманітнішого у світі виробника на замовлення, контрактного виробника, інженерного інтегратора, консолідатора та аутсорсингового партнера. Інженерні послуги можна пропонувати як окремо, так і в рамках розробки нового продукту чи процесу, або як частину існуючого продукту чи процесу, або як будь-що інше, що спадає вам на думку. Ми гнучкі, і наші інженерні послуги можуть набувати форму, яка найкраще відповідає вашим потребам і вимогам. Результати та результати наших інженерних послуг обмежені лише вашою уявою та можуть приймати будь-яку форму, яка вам підходить. Найпоширенішими формами результатів наших інженерних послуг є: звіти про консультації, аркуші випробувань і звіти, звіти про перевірки, креслення, інженерні креслення, складальні креслення, переліки матеріалів, таблиці даних, моделювання, програмне забезпечення, графіки та діаграми, результати спеціалізованих оптичні, термічні чи інші програмні програми, зразки та прототипи, моделі, демонстрації… тощо. Наші інженерні послуги можуть бути надані за підписом або кількома підписами сертифікованих професійних інженерів у вашому штаті. Іноді для підписання роботи може знадобитися кілька професійних інженерів з різних дисциплін. Аутсорсинг інженерних послуг, наданий нам, може надати вам багато переваг, таких як економія коштів від найму інженера або інженерів на повний робочий день, швидке залучення досвідченого інженера, який обслуговуватиме вас у межах вашого терміну та бюджету, замість того, щоб шукати його найняти, даючи вам можливість звільнитися проект швидко, якщо ви зрозумієте, що це неможливо (це дуже дорого, якщо ви наймете та звільняєте власних інженерів), мати можливість швидко перемикати інженерів з різних дисциплін і досвіду, що дає вам можливість маневрувати в будь-який час і фазі ваших проектів…..і т.д. Існує багато інших переваг аутсорсингу інженерних послуг на додаток до індивідуального виробництва та складання. На цьому сайті ми зосередимося на виготовленні на замовлення, контрактному виробництві, складанні, інтеграції, консолідації та аутсорсингу продукції. Якщо вас більше цікавить інженерна сторона нашого бізнесу, ви можете знайти детальну інформацію про наші інженерні послуги, відвідавши http://www.ags-engineering.com Ми AGS-TECH Inc., ваше єдине джерело для виробництва, виробництва, проектування, аутсорсингу та консолідації. Ми є найрізноманітнішим інженерним інтегратором у світі, який пропонує вам індивідуальне виробництво, збірку, складання продуктів та інженерні послуги. Contact Us First Name Last Name Email Write a message Submit Thanks for submitting!