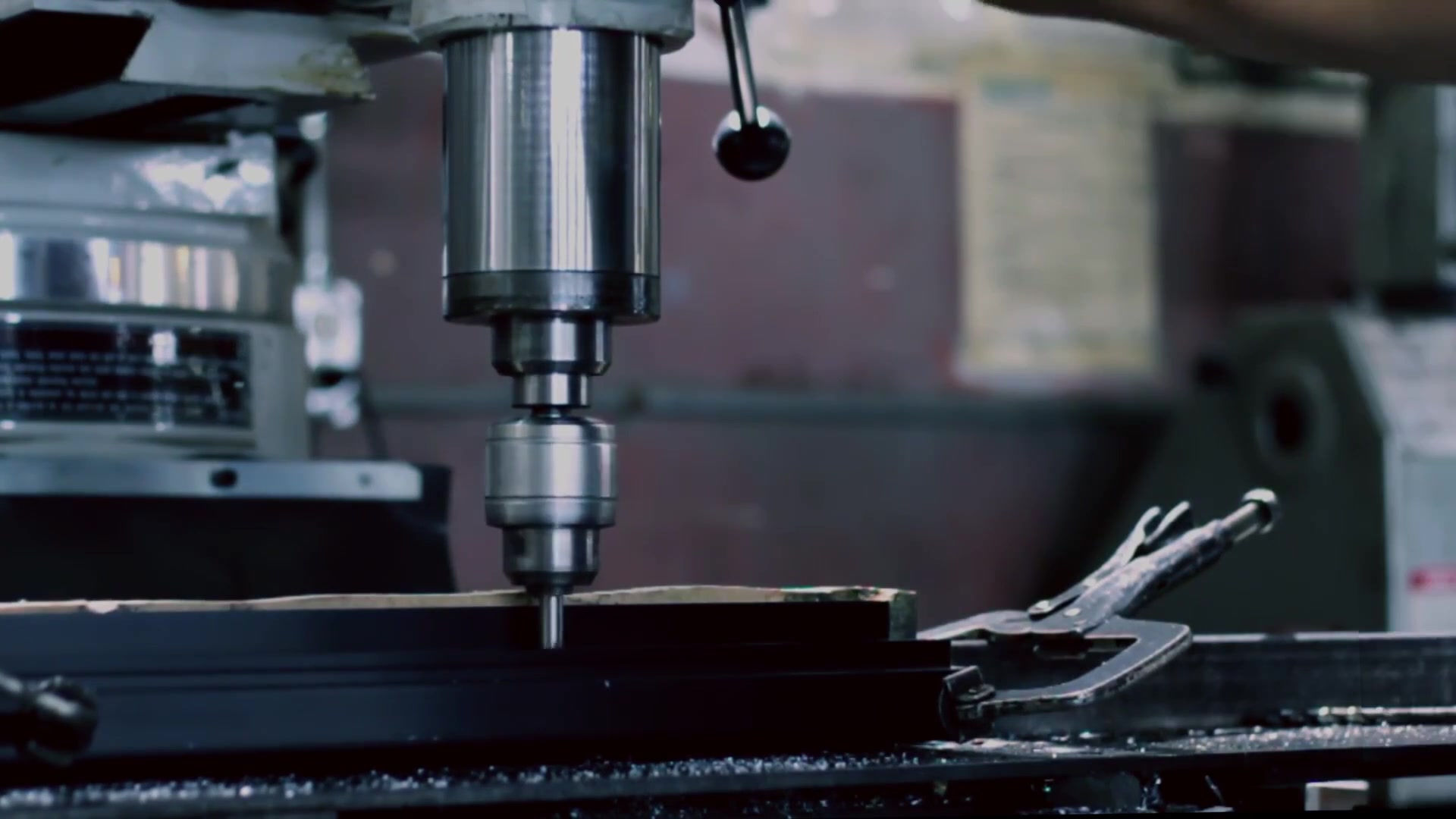
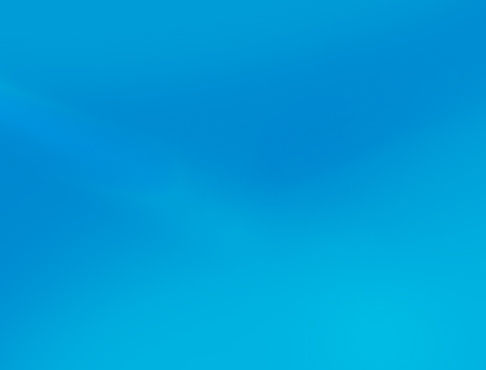
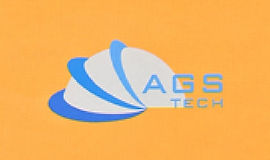
Глобальний індивідуальний виробник, інтегратор, консолідатор, аутсорсинговий партнер для широкого спектру продуктів і послуг.
Ми є вашим єдиним джерелом для виробництва, виготовлення, проектування, консолідації, інтеграції, аутсорсингу виготовлених на замовлення та готових продуктів і послуг.
Виберіть свою мову
-
Виготовлення на замовлення
-
Внутрішнє та глобальне контрактне виробництво
-
Аутсорсинг виробництва
-
Внутрішні та міжнародні закупівлі
-
Consolidation
-
Інженерна інтеграція
-
Інженерні послуги
Search Results
Знайдено 164 результати із порожнім запитом
- Cable & Connector Assembly, Wire Harness, Cable Management Accessories
Cable Assembly - Wire Harness - Cable Management Accessories - Connectorization - Cable Fan Out - Interconnects Електричні та електронні кабелі та з’єднання Ми пропонуємо: • Різноманітні види проводів, кабелів, кабельних збірок і аксесуарів для організації кабелів, неекрановані або екрановані кабелі для розподілу електроенергії, високої напруги, низького сигналу, телекомунікацій... тощо, з'єднувальні та з'єднувальні компоненти. • З’єднувачі, вилки, адаптери та відповідні муфти, патч-панель з роз’ємами, корпус для з’єднання. - Щоб завантажити наш каталог стандартних компонентів міжсистемних з’єднань і апаратного забезпечення, НАТИСНІТЬ ТУТ. - Клемні колодки та роз'єми - Загальний каталог клемників - Каталог гнізд-роз'ємів живлення - Брошура про кінцеву кабельну продукцію (Трубки, ізоляція, захист, термоусадка, ремонт кабелю, розривні черевики, затискачі, кабельні стяжки та кліпси, маркери проводів, стрічки, кабельні наконечники, розподільні слоти) - Інформацію про наше підприємство, що виробляє фітинги з кераміки на метал, герметичне ущільнення, вакуумні канали, компоненти з високим і надвисоким вакуумом, адаптери та з’єднувачі BNC, SHV, провідники та контактні штифти, клеми з’єднувачів можна знайти тут:_cc781905-5cde-3194-bb3b- 136bad5cf58d_ Брошура заводу Завантажте брошуру для нашогоПРОГРАМА ДИЗАЙН-ПАРТНЕРСТВА З’єднувачі та продукція для монтажу кабелів представлена у великому асортименті. Будь ласка, вкажіть нам тип, застосування, технічні характеристики, якщо такі є, і ми запропонуємо вам найбільш підходящий продукт. Ми можемо налаштувати їх для вас, якщо це не готовий продукт. Наші кабельні збірки та з’єднання мають маркування CE або UL уповноваженими організаціями та відповідають галузевим нормам і стандартам, таким як IEEE, IEC, ISO... тощо. Щоб дізнатися більше про наші інженерні та науково-дослідні можливості замість виробничих операцій, ми запрошуємо вас відвідати наш інженерний сайт http://www.ags-engineering.com CLICK Product Finder-Locator Service ПОПЕРЕДНЯ СТОРІНКА
- Optical Displays, Screen, Monitors Manufacturing - AGS-TECH Inc.
Optical Displays, Screen, Monitors, Touch Panel Manufacturing Виробництво та монтаж оптичних дисплеїв, екранів, моніторів Завантажте брошуру для нашого ПРОГРАМА ДИЗАЙН-ПАРТНЕРСТВА CLICK Product Finder-Locator Service ПОПЕРЕДНЯ СТОРІНКА
- Embedded Systems, Embedded Computer, Industrial Computers, Janz Tec
Embedded Systems - Embedded Computer - Industrial Computers - Janz Tec - Korenix - AGS-TECH Inc. - New Mexico - USA Вбудовані системи та комп'ютери Вбудована СИСТЕМА — це комп’ютерна система, розроблена для виконання певних функцій керування в рамках більшої системи, часто з обчислювальними обмеженнями в реальному часі. Він вбудований як частина повного пристрою, який часто включає апаратні та механічні частини. Навпаки, комп’ютер загального призначення, такий як персональний комп’ютер (ПК), розроблений таким чином, щоб бути гнучким і відповідати широкому спектру потреб кінцевого користувача. Архітектура вбудованої системи орієнтована на стандартний ПК, при цьому EMBEDDED PC складається лише з компонентів, які йому дійсно потрібні для відповідної програми. Вбудовані системи керують багатьма пристроями, які сьогодні широко використовуються. Серед ВСТРОЮВАНИХ КОМП'ЮТЕРІВ ми пропонуємо вам ATOP TECHNOLOGIES, JANZ TEC, KORENIX TECHNOLOGY, DFI-ITOX та інші моделі продукції. Наші вбудовані комп’ютери є міцними та надійними системами для промислового використання, де простої можуть бути катастрофічними. Вони енергоефективні, дуже гнучкі у використанні, мають модульну конструкцію, компактні, потужні, як повний комп’ютер, безвентиляторні та безшумні. Наші вбудовані комп’ютери мають надзвичайну температуру, герметичність, стійкість до ударів і вібрації в суворих умовах і широко використовуються в машинобудуванні та будівництві заводів, електростанціях і енергетичних установках, транспортній промисловості, медичній, біомедичній, біоінструментальній, автомобільній промисловості, військовій промисловості, гірничодобувній промисловості, флоті , морський, аерокосмічний тощо. Завантажте нашу компактну брошуру про продукт ATOP TECHNOLOGIES (Завантажити продукт ATOP Technologies List 2021) Завантажте брошуру про компактний продукт JANZ TEC Завантажте брошуру про компактний продукт KORENIX Завантажте нашу брошуру про модель вбудованих систем DFI-ITOX Завантажте нашу брошуру про моделі вбудованих одноплатних комп’ютерів DFI-ITOX Завантажте брошуру про бортові комп’ютерні модулі моделі DFI-ITOX Завантажте нашу брошуру про вбудовані контролери та DAQ моделі PAC ICP DAS Щоб перейти до нашого магазину промислових комп’ютерів, НАТИСНІТЬ ТУТ. Ось кілька найпопулярніших вбудованих комп’ютерів, які ми пропонуємо: Вбудований ПК з технологією Intel ATOM Z510/530 Вбудований ПК без вентилятора Вбудована система ПК із Freescale i.MX515 Надійні вбудовані ПК-системи Модульні вбудовані системи ПК Системи HMI та безвентиляторні промислові дисплеї Завжди пам’ятайте, що AGS-TECH Inc. є визнаним ІНЖЕНЕРНИМ ІНТЕГРАТОРОМ і ВИРОБНИКОМ НА ЗАМОВНИК. Тому, якщо вам знадобиться щось виготовлене на замовлення, повідомте нам, і ми запропонуємо вам готове рішення, яке зніме головоломку з вашого столу та полегшить вашу роботу. Завантажте брошуру для нашого ПРОГРАМА ДИЗАЙН-ПАРТНЕРСТВА Дозвольте коротко представити вам наших партнерів, які розробляють ці вбудовані комп’ютери: JANZ TEC AG: Janz Tec AG є провідним виробником електронних вузлів і повних промислових комп’ютерних систем з 1982 року. Компанія розробляє вбудовані обчислювальні продукти, промислові комп’ютери та пристрої промислового зв’язку відповідно до вимог замовника. Вся продукція JANZ TEC виробляється виключно в Німеччині з найвищою якістю. Завдяки більш ніж 30-річному досвіду роботи на ринку Janz Tec AG здатна задовольнити індивідуальні вимоги клієнтів – це починається з етапу концепції та продовжується через розробку та виробництво компонентів до доставки. Janz Tec AG встановлює стандарти у сферах вбудованих комп’ютерів, промислових ПК, промислових комунікацій, спеціального дизайну. Співробітники Janz Tec AG створюють, розробляють і виробляють вбудовані комп'ютерні компоненти та системи на основі світових стандартів, які індивідуально адаптуються до конкретних вимог замовника. Вбудовані комп’ютери Janz Tec мають додаткові переваги тривалої доступності та найвищої якості разом із оптимальним співвідношенням ціни та продуктивності. Вбудовані комп’ютери Janz Tec завжди використовуються, коли необхідні надзвичайно міцні та надійні системи через вимоги до них. Модульні та компактні промислові комп’ютери Janz Tec невибагливі в обслуговуванні, енергоефективні та надзвичайно гнучкі. Комп’ютерна архітектура вбудованих систем Janz Tec орієнтована на стандартний ПК, при цьому вбудований ПК складається лише з тих компонентів, які йому дійсно потрібні для відповідної програми. Це полегшує повністю незалежне використання в середовищах, де обслуговування інакше було б надзвичайно дорогим. Незважаючи на те, що вони є вбудованими комп’ютерами, багато продуктів Janz Tec настільки потужні, що можуть замінити повний комп’ютер. Перевагами вбудованих комп’ютерів марки Janz Tec є робота без вентилятора та низькі витрати на обслуговування. Вбудовані комп’ютери Janz Tec використовуються в машинобудуванні та будівництві заводів, виробництві електроенергії та енергії, транспорті та дорожньому русі, медичних технологіях, автомобільній промисловості, виробництві та виробництві та багатьох інших промислових застосуваннях. Процесори, які стають дедалі потужнішими, дають змогу використовувати вбудований ПК Janz Tec, навіть коли стикаються з особливо складними вимогами цих галузей. Однією з переваг цього є апаратне середовище, знайоме багатьом розробникам, і наявність відповідних середовищ розробки програмного забезпечення. Компанія Janz Tec AG накопичує необхідний досвід у розробці власних вбудованих комп’ютерних систем, які за потреби можна адаптувати до вимог замовника. Дизайнери Janz Tec у секторі вбудованих комп’ютерів зосереджуються на оптимальному рішенні, яке відповідає застосуванню та індивідуальним вимогам замовника. Метою Janz Tec AG завжди було забезпечення високої якості систем, міцної конструкції для тривалого використання та виняткового співвідношення ціни та продуктивності. Сучасні процесори, які зараз використовуються у вбудованих комп’ютерних системах, це Freescale Intel Core i3/i5/i7, i.MX5x і Intel Atom, Intel Celeron і Core2Duo. Крім того, промислові комп’ютери Janz Tec оснащені не тільки стандартними інтерфейсами, такими як Ethernet, USB і RS 232, але інтерфейс CANbus також доступний для користувача як функція. Вбудований ПК Janz Tec часто не має вентилятора, тому в більшості випадків його можна використовувати з носієм CompactFlash, тому він не потребує обслуговування. CLICK Product Finder-Locator Service ПОПЕРЕДНЯ СТОРІНКА
- Waterjet Machining, WJ Cutting, Abrasive Water Jet, WJM, AWJM, AJM
Waterjet Machining - WJ Cutting - Abrasive Water Jet - Hydrodynamic Machining - WJM - AWJM - AJM - AGS-TECH Inc. - USA Гідроабразивна обробка та абразивне водоструйне й абразивне оброблення та різання The principle of operation of WATER-JET, ABRASIVE WATER-JET and ABRASIVE-JET MACHINING & CUTTING is based на зміну імпульсу швидкоплинного потоку, який потрапляє на деталь. Під час цієї зміни імпульсу діє сильна сила, яка розрізає заготовку. Ці WATERJET CUTTING & MACHINING (WJM) техніки засновані на воді та високоочищених абразивах, які рухаються зі швидкістю в три рази швидше звуку, щоб робити неймовірно точні та точні розрізи практично будь-який матеріал. Для деяких матеріалів, таких як шкіра та пластик, можна не використовувати абразив, а різати можна лише водою. Гідроабразивна обробка може робити те, чого інші методи не можуть, від різання складних, дуже тонких деталей у камені, склі та металі; для швидкого свердління отворів з титану. Наші верстати для гідроабразивного різання можуть обробляти великий плоский матеріал розміром у багато футів без обмежень щодо типу матеріалу. Щоб зробити розрізи та виготовити деталі, ми можемо відсканувати зображення з файлів у комп’ютер, або наші інженери можуть підготувати комп’ютерне креслення (CAD) вашого проекту. Нам потрібно визначити тип матеріалу, який ріжеться, його товщину і бажану якість різу. Складні конструкції не створюють проблем, оскільки сопло просто слідує шаблону відтвореного зображення. Дизайни обмежені лише вашою уявою. Зв’яжіться з нами сьогодні зі своїм проектом, і ми надамо вам наші пропозиції та пропозицію. Розглянемо ці три типи процесів докладніше. ВОДОСТРУНЕВА ОБРОБКА (WJM): процес так само можна назвати ГІДРОДИНАМІЧНА ОБРОБКА. Високо локалізовані сили від водоструменя використовуються для операцій різання та видалення задирок. Простіше кажучи, струмінь води діє як пилка, яка прорізає вузьку гладку канавку в матеріалі. Рівень тиску при водоструминній обробці становить близько 400 МПа, що цілком достатньо для ефективної роботи. За потреби можна створити тиск, який у кілька разів перевищує це значення. Діаметри струменевих сопел знаходяться в межах від 0,05 до 1 мм. Ми ріжемо різні неметалічні матеріали, такі як тканини, пластмаси, гума, шкіра, ізоляційні матеріали, папір, композитні матеріали за допомогою гідроабразивних різців. Навіть складні форми, такі як покриття автомобільної панелі приладів з вінілу та пінопласту, можна вирізати за допомогою багатоосьового гідроабразивного обладнання з ЧПУ. Гідроабразивна обробка є ефективним і чистим процесом порівняно з іншими процесами різання. Деякі з основних переваг цієї техніки: -Різання можна починати з будь-якого місця на заготовці без необхідності попереднього свердління отворів. - Значного тепла не виробляється - Процес гідроабразивної обробки та різання добре підходить для гнучких матеріалів, оскільки не відбувається прогинання та згинання заготовки. -Задирки мінімальні -Водоструйне різання та обробка є екологічно чистим і безпечним процесом, який використовує воду. АБРАЗИВНА ВОДОСТРУНЕВА ОБРОБКА (AWJM): У цьому процесі абразивні частинки, такі як карбід кремнію або оксид алюмінію, містяться у струмені води. Це збільшує швидкість видалення матеріалу порівняно з чисто водоструминною обробкою. Металеві, неметалічні, композитні матеріали та інші можна різати за допомогою AWJM. Ця техніка особливо корисна для нас під час різання чутливих до тепла матеріалів, які ми не можемо розрізати за допомогою інших методів, що виробляють тепло. Ми можемо зробити отвори мінімальним розміром 3 мм і максимальною глибиною близько 25 мм. Швидкість різання може досягати кількох метрів за хвилину залежно від матеріалу, що обробляється. Для металів швидкість різання в AWJM менша порівняно з пластмасами. Використовуючи наші роботизовані машини з багатоосьовим керуванням, ми можемо обробляти складні тривимірні деталі до кінцевих розмірів без необхідності повторного процесу. Щоб підтримувати розміри та діаметр сопел постійними, ми використовуємо сапфірові насадки, що важливо для збереження точності та повторюваності операцій різання. АБРАЗИВНО-СТРУНЕВА ОБРОБКА (AJM) : у цьому процесі високошвидкісний струмінь сухого повітря, азоту або вуглекислого газу, що містить абразивні частинки, вдаряє та ріже заготовку в контрольованих умовах. Абразивно-струменева обробка використовується для різання невеликих отворів, прорізів і складних візерунків у дуже твердих і крихких металевих і неметалевих матеріалах, зняття задирок і видалення спалаху з деталей, обрізки та фаски, видалення поверхневих плівок, таких як оксиди, очищення компонентів з нерівною поверхнею. Тиск газу становить близько 850 кПа, а швидкість струменя абразиву близько 300 м/с. Абразивні частинки мають діаметр від 10 до 50 мікрон. Високошвидкісні абразивні частинки закруглюють гострі кути та зроблені отвори, як правило, звужуються. Тому розробники деталей, які будуть оброблятися абразивним струменем, повинні взяти це до уваги та переконатися, що виготовлені деталі не вимагають таких гострих кутів і отворів. Процеси водоструминної, абразивної водоструминної та абразивно-струминної обробки можна ефективно використовувати для операцій різання та видалення задирок. Ці техніки мають властиву гнучкість завдяки тому, що вони не використовують жорсткі інструменти. CLICK Product Finder-Locator Service ПОПЕРЕДНЯ СТОРІНКА
- Mechanical Testing Instruments - Tension Tester - Torsion Test Machine
Mechanical Testing Instruments - Tension Tester - Torsion Test Machine - Bending Tester - Impact Test Device - Concrete Tester - Compression Testing Machine - H Механічні випробувальні прилади Серед великої кількості mechanical test Instruments we evance revice reverms strects 31990cems stress3 , ТЕСТЕРИ НА РОЗТЯГ, МАШИНИ ДЛЯ ВИПРОБУВАННЯ НА СТИСК, ОБЛАДНАННЯ ДЛЯ ВИПРОБУВАННЯ НА КРУЧЕННЯ, МАШИНА ДЛЯ ВИПРОБУВАННЯ ВТОМИ, ТЕСТЕРИ НА ТРИ І ЧОТИРИ ТОЧКОВІ ВИГИНИ, ТЕСТЕРИ КОЕФІЦІЄНТА ТЕРТЯ, ТЕСТЕРИ ТВЕРДОСТІ ТА ТОВЩИНИ, ТЕСТЕРИ ВИМІРЮВАННЯ ВІБРОСТІ ПОВЕРХНІ ТОЧНІ АНАЛІТИЧНІ ВАГИ. Ми пропонуємо нашим клієнтам якісні бренди, такі як SADT, SINOAGE for за прейскурантними цінами. Щоб завантажити каталог метрологічного та випробувального обладнання бренду SADT, будь ласка, НАТИСНІТЬ ТУТ. Тут ви знайдете деякі з цього випробувального обладнання, наприклад тестери бетону та тестери шорсткості поверхні. Давайте розглянемо ці тестові пристрої більш детально: SCHMIDT HAMMER / CONCRETE TESTER : This test instrument, also sometimes called a SWISS HAMMER or a REBOUND HAMMER, це пристрій для вимірювання пружних властивостей або міцності бетону або гірської породи, головним чином поверхневої твердості та опору проникненню. Молоток вимірює відскок підпружиненої маси, яка вдаряється об поверхню зразка. Випробувальний молоток буде вдаряти по бетону із заданою енергією. Відскок молотка залежить від твердості бетону та вимірюється випробувальним обладнанням. Взявши діаграму перерахунку як еталон, значення відскоку можна використовувати для визначення міцності на стиск. Молот Шмідта — це довільна шкала від 10 до 100. Молотки Шмідта мають кілька різних діапазонів енергії. Діапазон їх енергії: (i) Тип L-0,735 Нм енергія удару, (ii) Тип N-2,207 Нм енергія удару; та (iii) енергія удару типу М-29,43 Нм. Локальні варіації зразка. Щоб звести до мінімуму локальні варіації зразків, рекомендується взяти вибірку показань і взяти їхнє середнє значення. Перед випробуванням молоток Шмідта необхідно відкалібрувати за допомогою калібрувальної випробувальної ковадла, що надається виробником. Необхідно зняти 12 показань, відкинувши найвище та найнижче, а потім узявши середнє з десяти вимірювань, що залишилися. Цей метод вважається непрямим вимірюванням міцності матеріалу. Він забезпечує індикацію на основі властивостей поверхні для порівняння між зразками. Цей метод випробування бетону регулюється ASTM C805. З іншого боку, стандарт ASTM D5873 описує процедуру випробування породи. У каталозі бренду SADT ви знайдете такі продукти: ЦИФРОВИЙ МОЛОТОК ДЛЯ ВИПРОБУВАННЯ БЕТОНУ Моделі SADT HT-225D/HT-75D/HT-20D - Модель SADT HT-225D — це інтегрований цифровий випробувальний молоток для бетону, який поєднує в собі процесор даних і випробувальний молоток. Він широко використовується для неруйнівного контролю якості бетону та будівельних матеріалів. За його значенням відскоку можна автоматично розрахувати міцність бетону на стиск. Усі тестові дані можна зберігати в пам’яті та передавати на ПК за допомогою USB-кабелю або бездротового зв’язку через Bluetooth. Моделі HT-225D і HT-75D мають діапазон вимірювання 10 – 70 Н/мм2, тоді як модель HT-20D має лише 1 – 25 Н/мм2. Енергія удару HT-225D становить 0,225 кгм і підходить для тестування звичайних будівельних і мостових конструкцій, енергія удару HT-75D становить 0,075 кгм і підходить для тестування невеликих і чутливих до ударів деталей з бетону та штучної цегли, і, нарешті, енергія удару HT-20D становить 0,020 кгм і підходить для тестування розчину або глиняних виробів. ТЕСТЕРИ НА УДАР: У багатьох виробничих операціях і протягом терміну служби багато компонентів повинні піддаватися ударному навантаженню. Під час випробування на удар зразок із надрізом поміщають у випробувальний пристрій і розбивають гойдальним маятником. Існує два основних типи цього тесту: The CHARPY TEST і the IZOD TEST. Для випробування Шарпі зразок підтримується з обох кінців, тоді як для випробування за Ізодом вони підтримуються лише з одного кінця, як консольна балка. З величини коливання маятника вираховується енергія, що розсіюється при руйнуванні зразка, ця енергія є ударною в’язкістю матеріалу. Використовуючи випробування на удар, ми можемо визначити температури пластично-крихкого переходу матеріалів. Матеріали з високою ударостійкістю, як правило, мають високу міцність і пластичність. Ці випробування також виявляють чутливість ударної в'язкості матеріалу до поверхневих дефектів, оскільки виїмку на зразку можна вважати поверхневим дефектом. TENSION TESTER : за допомогою цього випробування визначають характеристики міцності та деформації матеріалів. Тестовий зразок готується відповідно до стандартів ASTM. Як правило, випробовують тверді та круглі зразки, але плоскі листи та трубчасті зразки також можна випробовувати за допомогою випробування на розтяг. Початкова довжина зразка — це відстань між калібрувальними мітками на ньому і зазвичай становить 50 мм. Він позначається як lo. Залежно від зразків і продуктів можна використовувати довшу або коротшу довжину. Вихідна площа поперечного перерізу позначається як Ao. Інженерна напруга або також звана номінальною напругою тоді подається як: Сигма = P / Ao Інженерна деформація подається як: e = (l – lo) / lo У лінійно-пружній області зразок подовжується пропорційно навантаженню до пропорційної межі. Поза цією межею, навіть не лінійно, зразок продовжуватиме пружно деформуватися до межі текучості Y. У цій пружній області матеріал повернеться до своєї початкової довжини, якщо ми знімемо навантаження. У цій області застосовується закон Гука, який дає нам модуль Юнга: E = сигма / e Якщо ми збільшуємо навантаження і переходимо за межу текучості Y, матеріал починає прогинатися. Іншими словами, зразок починає піддаватися пластичній деформації. Пластична деформація означає остаточну деформацію. Площа поперечного перерізу зразка постійно і рівномірно зменшується. Якщо зразок розвантажується в цій точці, крива йде по прямій лінії вниз і паралельна вихідній лінії в еластичній області. При подальшому збільшенні навантаження крива досягає максимуму і починає знижуватися. Точка максимального напруження називається міцністю на розтяг або межею міцності на розрив і позначається UTS. UTS можна інтерпретувати як загальну міцність матеріалів. Коли навантаження перевищує UTS, на зразку виникає шийка, і подовження між мітками більше не є рівномірним. Іншими словами, зразок стає дуже тонким у місці, де виникає шийка. Під час шийки пружне напруження падає. Якщо випробування продовжувати, технічна напруга падає далі, і зразок ламається в області шийки. Рівень напруги при руйнуванні є напругою руйнування. Деформація в місці руйнування є показником пластичності. Деформація до UTS називається рівномірною деформацією, а подовження при розриві називається повним подовженням. Подовження = ((lf – lo) / lo) x 100 Зменшення площі = ((Ao – Af) / Ao) x 100 Подовження та зменшення площі є хорошими показниками пластичності. МАШИНА ДЛЯ ВИПРОБУВАННЯ НА СТИСК (КОМПРЕСІЙНИЙ ТЕСТЕР) : У цьому випробуванні зразок піддається навантаженню на стиск, що суперечить випробуванню на розтяг, де навантаження є розтягуючим. Як правило, твердий циліндричний зразок поміщають між двома плоскими пластинами і стискають. Використання мастильних матеріалів на контактних поверхнях запобігає явищу, відомому як бочка. Технічна швидкість деформації при стисненні визначається як: de / dt = - v / ho, де v швидкість матриці, ho вихідна висота зразка. З іншого боку, справжня швидкість деформації дорівнює: de = dt = - v/h, де h є миттєвою висотою зразка. Щоб підтримувати справжню швидкість деформації постійною під час випробування, кулачковий пластометр через кулачкову дію зменшує величину v пропорційно зі зменшенням висоти h зразка під час випробування. Використовуючи випробування на стиск, пластичність матеріалів визначається шляхом спостереження за тріщинами, утвореними на бочкоподібних циліндричних поверхнях. Іншим тестом із деякими відмінностями в геометрії матриці та заготовки є ВИПРОБУВАННЯ НА СТИСКУВАННЯ ПЛОСКОЇ ДЕФОРМАЦІЇ, яке дає нам межу текучості матеріалу в площинній деформації, яка широко позначається як Y'. Межу текучості матеріалів у площинній деформації можна оцінити як: Y' = 1,15 Y МАШИНИ ДЛЯ ВИПРОБУВАННЯ НА КРУЧЕННЯ (ВИПРОБУВАННЯ НА КРУЧЕННЯ) : The ВИПРОБУВАННЯ НА КРУЧЕННЯ ще один широко використовуваний метод визначення властивостей матеріалу У цьому тесті використовується трубчастий зразок зі зменшеним середнім перерізом. Напруга зсуву, T визначається як: T = T / 2 (пі) (квадрат r) t Тут T — прикладений крутний момент, r — середній радіус, а t — товщина зменшеної ділянки в середині труби. З іншого боку, деформація зсуву визначається як: ß = r Ø / л Тут l — довжина зменшеної ділянки, а Ø — кут закручування в радіанах. У діапазоні пружності модуль зсуву (модуль жорсткості) виражається як: G = T / ß Співвідношення між модулем зсуву та модулем пружності таке: G = E / 2( 1 + V ) Випробування на кручення застосовують до твердих круглих прутків при підвищених температурах, щоб оцінити здатність металів куватись. Чим більше скручувань матеріал може витримати до руйнування, тим краще він піддається ковці. THREE & FOUR POINT BENDING TESTERS : For brittle materials, the BEND TEST (also called FLEXURE TEST) підходить. Зразок прямокутної форми підтримується з обох кінців, і навантаження прикладається вертикально. Вертикальна сила прикладається або в одній точці, як у випадку триточкового тестера на згинання, або в двох точках, як у випадку чотириточкової випробувальної машини. Напруга при руйнуванні при згині називається модулем міцності на розрив або міцністю на поперечний розрив. Він надається як: Сигма = M c / I Тут M — згинальний момент, c — половина глибини зразка, I — момент інерції поперечного перерізу. Величина напруги однакова як у трьох, так і в чотирьох точках згинання, коли всі інші параметри залишаються постійними. Чотирьохточкове випробування, ймовірно, призведе до нижчого модуля розриву порівняно з трьома точковим випробуванням. Ще одна перевага чотириточкового тесту на згинання над триточковим тестом на згинання полягає в тому, що його результати більш узгоджуються з меншим статистичним розсіюванням значень. МАШИНА ДЛЯ ВИПРОБУВАННЯ НА ВТОМУ: У ВИПРОБУВАННЯ НА ВТОМУ зразок неодноразово піддається різним станам навантаження. Напруги, як правило, є комбінацією розтягу, стиснення та кручення. Процес випробування можна нагадувати згинання шматка дроту по черзі то в одному, то в іншому напрямку, поки він не зламається. Амплітуда напруги може бути різною і позначається буквою S. Кількість циклів, що призводять до повного руйнування зразка, записують і позначають як «N». Амплітуда напруги - це максимальне значення напруги при розтягуванні та стисненні, якому піддається зразок. Один із варіантів випробування на втому виконується на обертовому валу з постійним навантаженням, спрямованим вниз. Межа витривалості (межа втоми) визначається як макс. величина напруги, яку матеріал може витримати без втомного руйнування незалежно від кількості циклів. Втомна міцність металів пов'язана з їх межею міцності на розрив UTS. КОЕФІЦІЄНТ ТЕРТЯ TESTER : це випробувальне обладнання вимірює легкість, з якою дві контактні поверхні можуть ковзати одна повз одну. Існують дві різні величини, пов’язані з коефіцієнтом тертя, а саме статичний і кінетичний коефіцієнти тертя. Статичне тертя стосується сили, необхідної для ініціалізації руху між двома поверхнями, а кінетичне тертя — це опір ковзанню, коли поверхні знаходяться у відносному русі. Необхідно вжити відповідних заходів до та під час тестування, щоб забезпечити відсутність бруду, жиру та інших забруднень, які можуть негативно вплинути на результати тестування. ASTM D1894 є основним стандартом для визначення коефіцієнта тертя, який використовується багатьма галузями промисловості з різними застосуваннями та продуктами. Ми тут, щоб запропонувати вам найбільш відповідне тестове обладнання. Якщо вам потрібна спеціальна установка, спеціально розроблена для вашої програми, ми можемо змінити наявне обладнання відповідним чином, щоб відповідати вашим вимогам і потребам. ТЕСТЕРИ ТВЕРДОСТІ : Будь ласка, перейдіть на нашу відповідну сторінку, натиснувши тут ТЕСТЕРИ ТОВЩИНИ : Будь ласка, перейдіть на нашу відповідну сторінку, натиснувши тут ТЕСТЕРИ ШОРСТОСТІ ПОВЕРХНІ : Будь ласка, перейдіть на нашу відповідну сторінку, натиснувши тут ВІБРАЦІЙНІ МЕТЕРИ : Будь ласка, перейдіть на нашу відповідну сторінку, натиснувши тут ТАХОМЕТРИ : Будь ласка, перейдіть на нашу відповідну сторінку, натиснувши тут Для отримання додаткової інформації та іншого подібного обладнання відвідайте наш веб-сайт обладнання: http://www.sourceindustrialsupply.com CLICK Product Finder-Locator Service ПОПЕРЕДНЯ СТОРІНКА
- Metal and Metal Alloy Castings, Die Cast Parts, Custom Cast Parts
Metal and Metal Alloy Castings, Metal Castings, Custom Cast Parts, Alloy Casting, Steel Precision Die Cast Parts, Brass Copper Components Manufacturing Виливки з металу та металевих сплавів Суворий контроль якості литого металу та сплаву parts Точне лиття металу Металеве лиття на замовлення Литі та оброблені деталі транспортної промисловості Прецизійне лиття з металу та металевих сплавів із вторинними операціями - AGS-TECH Литі деталі із сірого чавуну Лиття з сірого чавуну виробництва AGS-TECH Inc. Чавунне та сталеве лиття від AGS-TECH Inc. Точне лиття під тиском з металу та сплавів - AGS-TECH Прецизійне лиття під тиском у поєднанні з іншими операціями - AGS-TECH Лиття та кування великих деталей Великі металеві виливки Металеві виливки, готові до додаткових операцій Завод металевого лиття Лиття металу ПОПЕРЕДНЯ СТОРІНКА
- Microelectronics Manufacturing, Semiconductor Fabrication, Foundry, IC
Microelectronics Manufacturing, Semiconductor Fabrication - Foundry - FPGA - IC Assembly Packaging - AGS-TECH Inc. Виробництво та виготовлення мікроелектроніки та напівпровідників Багато наших методів і процесів нано-, мікро- та мезо-виробництва, пояснених в інших меню, можна використовувати для MICROELECTRONICS MANUFACTURING too. Однак через важливість мікроелектроніки в наших продуктах ми зосередимося на конкретних предметних застосуваннях цих процесів. Процеси, пов’язані з мікроелектронікою, також широко називаються SEMICONDUCTOR FABRICATION processes. Наші послуги з проектування та виготовлення напівпровідникової техніки включають: - Дизайн, розробка та програмування плати FPGA - Ливарні послуги мікроелектроніки: проектування, створення прототипів і виробництво, сторонні послуги - Підготовка напівпровідникової пластини: нарізка, шліфування, розрідження, розміщення візирної сітки, сортування матриці, вибір і розміщення, перевірка - Дизайн і виготовлення мікроелектронної упаковки: стандартне та спеціальне проектування та виготовлення - Збірка та упаковка та випробування напівпровідникової мікросхеми: з’єднання матриць, проводів і мікросхем, інкапсуляція, складання, маркування та брендування - Свинцеві каркаси для напівпровідникових пристроїв: як готові, так і спеціальні конструкції та виготовлення - Проектування та виготовлення радіаторів для мікроелектроніки: як стандартне, так і індивідуальне проектування та виготовлення - Дизайн і виготовлення датчиків і приводів: як готові, так і індивідуальні дизайн і виготовлення - Проектування та виготовлення оптоелектронних і фотонних схем Давайте детальніше розглянемо технології виготовлення та тестування мікроелектроніки та напівпровідників, щоб ви могли краще зрозуміти послуги та продукти, які ми пропонуємо. Розробка та розробка плати FPGA та програмування: програмовані вентильні матриці (FPGA) — це кремнієві мікросхеми, які можна перепрограмувати. На відміну від процесорів, які ви знайдете в персональних комп’ютерах, програмування FPGA перемикає сам чіп, щоб реалізувати функціональність користувача, а не запускати програмне забезпечення. Використовуючи готові логічні блоки та програмовані ресурси маршрутизації, мікросхеми FPGA можна налаштувати для реалізації нестандартних апаратних функцій без використання макетної плати та паяльника. Цифрові обчислювальні завдання виконуються програмним забезпеченням і компілюються у файл конфігурації або бітовий потік, який містить інформацію про те, як компоненти мають бути з’єднані разом. ПЛІС можна використовувати для реалізації будь-якої логічної функції, яку може виконувати ASIC, вони повністю реконфігуруються та можуть отримати зовсім іншу «особистість» шляхом перекомпіляції іншої конфігурації схеми. ПЛІС поєднують у собі найкращі частини інтегральних схем (ASIC) і систем на основі процесорів. Ці переваги включають наступне: • Швидший час відгуку введення/виведення та спеціалізовані функції • Перевищення обчислювальної потужності цифрових сигнальних процесорів (DSP) • Швидке створення прототипів і перевірка без процесу виготовлення спеціальної ASIC • Реалізація спеціальної функціональності з надійністю виділеного детермінованого обладнання • Можливість оновлення на місці, що усуває витрати на користувальницький перепроектування та обслуговування ASIC ПЛІС забезпечують швидкість і надійність, не вимагаючи великих об’ємів, щоб виправдати великі початкові витрати на спеціальний дизайн ASIC. Перепрограмований мікросхема також має таку саму гнучкість програмного забезпечення, що працює на системах на базі процесора, і воно не обмежене кількістю доступних процесорних ядер. На відміну від процесорів, FPGA дійсно паралельні за своєю природою, тому різні операції обробки не повинні конкурувати за ті самі ресурси. Кожне незалежне завдання обробки призначається виділеній секції мікросхеми та може функціонувати автономно без будь-якого впливу з боку інших логічних блоків. Як наслідок, додавання додаткової обробки не впливає на продуктивність однієї частини програми. Деякі FPGA мають аналогові функції на додаток до цифрових функцій. Деякі загальні аналогові функції включають програмовану швидкість наростання та силу приводу на кожному вихідному виводі, що дозволяє інженеру встановлювати повільні швидкості на малонавантажених виводах, які інакше б неприйнятно дзвонили або з’єднувалися, а також встановлювати сильніші, швидші швидкості на сильно навантажених виводах на високій швидкості. канали, які інакше працювали б надто повільно. Іншою відносно поширеною аналоговою функцією є диференціальні компаратори на вхідних контактах, призначені для підключення до каналів диференціальної сигналізації. Деякі ПЛІС зі змішаним сигналом мають вбудовані периферійні аналого-цифрові перетворювачі (АЦП) і цифро-аналогові перетворювачі (ЦАП) з блоками формування аналогового сигналу, які дозволяють їм працювати як система на кристалі. Коротко, 5 основних переваг мікросхем FPGA: 1. Хороша продуктивність 2. Короткий час виходу на ринок 3. Низька вартість 4. Висока надійність 5. Можливість довгострокового обслуговування Хороша продуктивність – завдяки своїй здатності підтримувати паралельну обробку, FPGA мають кращу обчислювальну потужність, ніж цифрові сигнальні процесори (DSP), і не вимагають послідовного виконання, як DSP, і можуть виконувати більше за такт. Контроль входів і виходів (I/O) на апаратному рівні забезпечує швидший час відгуку та спеціалізовані функції, щоб точно відповідати вимогам програми. Короткий час виходу на ринок – ПЛІС пропонують гнучкість і можливості швидкого створення прототипів і, отже, коротший час виходу на ринок. Наші клієнти можуть випробувати ідею чи концепцію та перевірити її на апаратному забезпеченні, не проходячи довгий і дорогий процес виготовлення спеціального дизайну ASIC. Ми можемо впроваджувати поступові зміни та повторювати дизайн FPGA протягом годин замість тижнів. Комерційне готове обладнання також доступне з різними типами вводу/виводу, які вже підключені до програмованої користувачем мікросхеми FPGA. Зростаюча доступність програмних засобів високого рівня пропонує цінні IP-ядра (попередньо створені функції) для розширеного керування та обробки сигналів. Низька вартість. Одноразові витрати на розробку ASIC перевищують витрати на апаратне забезпечення на основі FPGA. Великі початкові інвестиції в ASIC можуть бути виправдані для OEM-виробників, які виробляють багато мікросхем на рік, однак багатьом кінцевим користувачам потрібна спеціальна апаратна функція для багатьох систем, що розробляються. Наша програмована кремнієва FPGA пропонує вам щось без витрат на виготовлення або тривалого часу для складання. Вимоги до системи часто змінюються з часом, і вартість внесення поступових змін до конструкцій FPGA є незначною порівняно з великими витратами на повторне обертання ASIC. Висока надійність - програмні засоби забезпечують середовище програмування, а схеми FPGA є справжньою реалізацією виконання програми. Системи на основі процесорів зазвичай включають кілька рівнів абстракції, щоб допомогти планувати завдання та розподіляти ресурси між кількома процесами. Рівень драйверів контролює апаратні ресурси, а ОС керує пам'яттю та пропускною здатністю процесора. Для будь-якого даного ядра процесора одночасно може виконуватися лише одна інструкція, і системи на основі процесора постійно ризикують випереджати критичні за часом завдання. ПЛІС, які не використовують ОС, створюють мінімальні проблеми щодо надійності завдяки їх справжньому паралельному виконанню та детермінованому апаратному забезпеченню, призначеному для кожного завдання. Можливість довгострокового технічного обслуговування - мікросхеми FPGA можна оновлювати в польових умовах і не вимагають часу та коштів, пов'язаних з перепроектуванням ASIC. Цифрові протоколи зв’язку, наприклад, мають специфікації, які можуть змінюватися з часом, а інтерфейси на основі ASIC можуть спричинити проблеми з обслуговуванням і подальшою сумісністю. Навпаки, реконфігуровані мікросхеми FPGA можуть йти в ногу з потенційно необхідними майбутніми модифікаціями. У міру розвитку продуктів і систем наші клієнти можуть удосконалювати функціональні можливості, не витрачаючи час на перепроектування апаратного забезпечення та зміну макетів плати. Послуги з ливарного виробництва мікроелектроніки: наші послуги з ливарного виробництва мікроелектроніки включають проектування, створення прототипів і виробництво, а також сторонні послуги. Ми надаємо нашим клієнтам допомогу протягом усього циклу розробки продукту - від підтримки проектування до прототипування та підтримки виробництва напівпровідникових мікросхем. Наша ціль у сфері послуг з підтримки проектування полягає в тому, щоб увімкнути правильний підхід до розробки цифрових, аналогових і змішаних сигналів напівпровідникових пристроїв. Наприклад, доступні спеціальні засоби моделювання MEMS. Фабрики, які можуть обробляти пластини розміром 6 і 8 дюймів для інтегрованих CMOS і MEMS, до ваших послуг. Ми пропонуємо нашим клієнтам підтримку проектування для всіх основних платформ автоматизації електронного проектування (EDA), надаючи правильні моделі, комплекти проектування процесів (PDK), аналогові та цифрові бібліотеки та підтримку проектування для виробництва (DFM). Ми пропонуємо два варіанти створення прототипів для всіх технологій: послугу Multi Product Wafer (MPW), де кілька пристроїв обробляються паралельно на одній пластині, і послугу Multi Level Mask (MLM) із чотирма рівнями маски, намальованими на тій самій сітці. Вони економніші, ніж повний набір масок. Послуга MLM відрізняється високою гнучкістю порівняно з фіксованими датами послуги MPW. Компанії можуть віддати перевагу аутсорсингу напівпровідникової продукції перед ливарним виробництвом мікроелектроніки з ряду причин, включаючи потребу в другому джерелі, використання внутрішніх ресурсів для інших продуктів і послуг, готовність перейти на безперебійне виробництво та зменшити ризик і тягар експлуатації напівпровідникової фабрики… тощо. AGS-TECH пропонує процеси виготовлення мікроелектроніки на відкритій платформі, які можна зменшити для невеликих тиражів пластин, а також для масового виробництва. За певних обставин ваші існуючі інструменти для виготовлення мікроелектроніки чи MEMS або повні набори інструментів можуть бути передані як надіслані інструменти чи продані інструменти з вашого заводу на наш заводський сайт, або ваші існуючі продукти мікроелектроніки та MEMS можуть бути перероблені за допомогою технологій відкритої платформи та перенесені на процес доступний на нашій фабриці. Це швидше та економніше, ніж передача технології на замовлення. Однак за бажанням існуючі процеси виробництва мікроелектроніки / MEMS клієнта можуть бути передані. Підготовка напівпровідникової пластини: За бажанням клієнтів після мікрофабрикації пластин ми виконуємо нарізання, шліфування, розрідження, розміщення візирної сітки, сортування матриці, підбір і розміщення, перевірку напівпровідникових пластин. Обробка напівпровідникових пластин включає метрологію між різними етапами обробки. Наприклад, методи тестування тонкої плівки, засновані на еліпсометрії або рефлектометрії, використовуються для суворого контролю товщини оксиду затвора, а також товщини, показника заломлення та коефіцієнта екстинкції фоторезисту та інших покриттів. Ми використовуємо обладнання для тестування напівпровідникових пластин, щоб переконатися, що пластини не були пошкоджені попередніми етапами обробки до тестування. Після завершення початкових процесів напівпровідникові мікроелектронні пристрої піддаються різноманітним електричним тестам, щоб визначити, чи вони функціонують належним чином. Ми називаємо частку мікроелектронних пристроїв на пластині, які, як виявилося, працюють належним чином, як «продуктивність». Випробування мікроелектронних чіпів на пластині проводяться електронним тестером, який притискає крихітні щупи до напівпровідникового чіпа. Автоматизована машина позначає кожен несправний мікроелектронний чіп краплею барвника. Дані випробувань пластин реєструються в центральній комп’ютерній базі даних, а напівпровідникові мікросхеми сортуються у віртуальні бункери відповідно до попередньо встановлених лімітів випробувань. Отримані дані групування можна відображати на графіку або реєструвати на карті пластин, щоб відстежувати виробничі дефекти та позначати погані мікросхеми. Цю карту також можна використовувати під час складання та пакування пластин. Під час остаточного тестування мікроелектронні мікросхеми перевіряються знову після упаковки, оскільки з’єднувальні дроти можуть бути відсутні або аналогова продуктивність може бути змінена упаковкою. Після випробування напівпровідникової пластини її, як правило, зменшують у товщині перед тим, як на пластині роблять надрізи, а потім розбивають на окремі матриці. Цей процес називається нарізанням напівпровідникової пластини. Ми використовуємо автоматичні машини, спеціально виготовлені для мікроелектронної промисловості, щоб сортувати хороші та погані напівпровідникові матриці. Упаковуються лише якісні напівпровідникові мікросхеми без маркування. Далі в процесі виготовлення мікроелектронної пластикової або керамічної упаковки ми встановлюємо напівпровідниковий кристал, підключаємо його до штифтів на упаковці та запечатуємо матрицю. Крихітні золоті дроти використовуються для з’єднання колодок зі штифтами за допомогою автоматизованих машин. Упаковка для мікроелектроніки (CSP) — ще одна технологія упаковки мікроелектроніки. Пластиковий подвійний вбудований корпус (DIP), як і більшість пакетів, у кілька разів більший за фактичний напівпровідниковий кристал, розміщений усередині, тоді як мікросхеми CSP мають розмір майже з мікроелектронний кристал; і CSP може бути побудований для кожного кристала до того, як напівпровідникова пластина буде нарізана. Упаковані мікроелектронні чіпи повторно перевіряються, щоб переконатися, що вони не пошкоджені під час пакування та що процес з’єднання матриці з контактом було завершено правильно. За допомогою лазера ми витравлюємо назви та номери мікросхем на упаковці. Розробка та виготовлення мікроелектронної упаковки: ми пропонуємо як готові, так і індивідуальні розробки та виготовлення мікроелектронної упаковки. В рамках цієї послуги також здійснюється моделювання та імітація корпусів мікроелектроніки. Моделювання та моделювання забезпечують віртуальне проектування експериментів (DoE) для досягнення оптимального рішення, а не тестування пакетів на полі. Це зменшує вартість і час виробництва, особливо для розробки нових продуктів у мікроелектроніці. Ця робота також дає нам можливість пояснити нашим клієнтам, як збірка, надійність і тестування вплинуть на їхні мікроелектронні продукти. Основною метою мікроелектронної упаковки є розробка електронної системи, яка задовольнить вимоги для конкретного застосування за прийнятною ціною. Через безліч варіантів, доступних для з’єднання та розміщення мікроелектронної системи, вибір технології упаковки для певного застосування потребує експертної оцінки. Критерії відбору для пакетів мікроелектроніки можуть включати деякі з наступних технологічних факторів: -Можливість підключення -Урожайність -Вартість -Тепловідвідні властивості -Ефективність електромагнітного екранування - Механічна міцність -Надійність Ці конструктивні міркування для корпусів мікроелектроніки впливають на швидкість, функціональність, температуру з’єднання, об’єм, вагу тощо. Основною метою є вибір найбільш економічно ефективної, але надійної технології з’єднання. Ми використовуємо складні методи аналізу та програмне забезпечення для розробки пакетів мікроелектроніки. Пакування мікроелектроніки займається проектуванням методів виготовлення взаємопов’язаних мініатюрних електронних систем і надійністю цих систем. Зокрема, упаковка мікроелектроніки передбачає маршрутизацію сигналів із збереженням цілісності сигналу, розподіл заземлення та живлення до напівпровідникових інтегральних схем, розсіювання розсіюваного тепла, зберігаючи структурну цілісність і цілісність матеріалу, а також захист схеми від небезпеки навколишнього середовища. Як правило, методи упаковки мікроелектронних мікросхем передбачають використання PWB з роз’ємами, які забезпечують реальний вхід/вихід електронної схеми. Традиційні підходи до упаковки мікроелектроніки передбачають використання окремих упаковок. Головною перевагою однокристального корпусу є можливість повністю перевірити мікроелектронну мікросхему перед тим, як підключити її до базової підкладки. Такі упаковані напівпровідникові пристрої встановлюються або через отвір, або поверхнево монтуються на PWB. Пакети мікроелектроніки для поверхневого монтажу не потребують наскрізних отворів для проходження через всю плату. Замість цього мікроелектронні компоненти поверхневого монтажу можна припаяти до обох боків PWB, що забезпечує більшу щільність схеми. Цей підхід називається технологією поверхневого монтажу (SMT). Додавання пакетів у стилі площинних масивів, таких як масиви з кульковою сіткою (BGA) і пакети масштабу мікросхем (CSP), робить SMT конкурентоспроможним з технологіями упаковки напівпровідникової мікроелектроніки найвищої щільності. Новіша технологія упаковки передбачає прикріплення кількох напівпровідникових пристроїв до підкладки з’єднання високої щільності, яка потім монтується у велику упаковку, забезпечуючи контакти введення/виведення та захист навколишнього середовища. Ця технологія багатокристального модуля (MCM) додатково характеризується технологіями підкладки, які використовуються для з’єднання приєднаних мікросхем. MCM-D являє собою наплавлені тонкоплівкові металеві та діелектричні мультишари. Підкладки MCM-D мають найвищу щільність проводки з усіх технологій MCM завдяки складним технологіям обробки напівпровідників. MCM-C відноситься до багатошарових «керамічних» підкладок, випалених із складених чергуючих шарів розсіяних металевих чорнил і необпалених керамічних листів. Використовуючи MCM-C, ми отримуємо помірно щільну розводку. MCM-L відноситься до багатошарових підкладок, виготовлених із багатошарових металізованих PWB «ламінатів», на які нанесено індивідуальний візерунок, а потім ламіновано. Раніше це була технологія з’єднання з низькою щільністю, однак зараз MCM-L швидко наближається до щільності технологій упаковки мікроелектроніки MCM-C і MCM-D. Технологія упаковки мікроелектроніки з прямим приєднанням мікросхеми (DCA) або мікросхеми на платі (COB) передбачає встановлення мікросхем мікроелектроніки безпосередньо на PWB. Пластиковий герметик, який наноситься на оголену мікросхему, а потім затверджується, забезпечує захист навколишнього середовища. Мікроелектронні мікросхеми можуть бути з’єднані з підкладкою за допомогою методів фліп-чіпа або дроту. Технологія DCA є особливо економічною для систем, які обмежені 10 або менше напівпровідниковими мікросхемами, оскільки більша кількість мікросхем може вплинути на продуктивність системи, а збірки DCA може бути важко переробити. Спільною перевагою варіантів упаковки DCA і MCM є усунення рівня взаємозв’язку корпусу напівпровідникової мікросхеми, що забезпечує більшу близькість (менші затримки передачі сигналу) і зменшену індуктивність виводу. Основним недоліком обох методів є труднощі з придбанням повністю перевірених мікроелектронних мікросхем. Інші недоліки технологій DCA і MCM-L включають погане управління температурою завдяки низькій теплопровідності ламінатів PWB і поганий коефіцієнт теплового розширення між напівпровідниковим кристалом і підкладкою. Вирішення проблеми невідповідності теплового розширення потребує проміжної підкладки, такої як молібден для матриці з дротяним скріпленням, і епоксидної смоли з нижньою заливкою для матриці з фліп-чіпом. Багатокристальний несучий модуль (MCCM) поєднує в собі всі позитивні сторони DCA з технологією MCM. MCCM — це просто невеликий MCM на тонкому металевому носії, який можна склеїти або механічно приєднати до PWB. Металеве дно діє як розсіювач тепла та компенсатор напруги для підкладки MCM. MCCM має периферійні дроти для з’єднання проводів, паяння або з’єднання вкладок з PWB. Оголені напівпровідникові мікросхеми захищені за допомогою матеріалу glob-top. Коли ви зв’яжетеся з нами, ми обговоримо вашу заявку та вимоги, щоб вибрати для вас найкращий варіант упаковки мікроелектроніки. Збірка та упаковка та випробування напівпровідникових мікросхем: у рамках наших послуг із виготовлення мікроелектроніки ми пропонуємо з’єднання матриць, проводів і мікросхем, інкапсуляцію, складання, маркування та брендування, тестування. Щоб напівпровідниковий чіп або інтегрована мікроелектронна схема працювали, їх потрібно підключити до системи, якою вони будуть керувати або надавати інструкції. Збірка мікроелектронної мікросхеми забезпечує з’єднання для живлення та передачі інформації між мікросхемою та системою. Це досягається підключенням мікроелектронної мікросхеми до корпусу або прямим підключенням до друкованої плати для виконання цих функцій. З’єднання між мікросхемою та корпусом або друкованою платою (PCB) здійснюється за допомогою з’єднання дротів, скрізного отвору або блоку фліп-чіпа. Ми є лідером у галузі пошуку мікроелектронних пакувальних рішень для мікросхем, які відповідають складним вимогам ринків бездротового зв’язку та Інтернету. Ми пропонуємо тисячі різних форматів і розмірів корпусів, починаючи від традиційних мікроелектронних корпусів IC для наскрізних отворів і поверхневого монтажу, до найновіших рішень для масштабування мікросхем (CSP) і матриці з кульковими сітками (BGA), необхідних для застосування з великою кількістю контактів і високою щільністю. . На складі доступний широкий вибір упаковок, включаючи CABGA (BGA з масивом мікросхем), CQFP, CTBGA (BGA з масивом мікросхем), CVBGA (BGA з дуже тонким масивом мікросхем), Flip Chip, LCC, LGA, MQFP, PBGA, PDIP, PLCC, PoP - Package on Package, PoP TMV - Through Mold Via, SOIC / SOJ, SSOP, TQFP, TSOP, WLP (Wafer Level Package)….. тощо. З’єднання проводів за допомогою міді, срібла або золота є одними з популярних у мікроелектроніці. Мідний (Cu) дріт був методом підключення кремнієвих напівпровідникових кристалів до терміналів корпусу мікроелектроніки. З огляду на нещодавнє збільшення вартості золотих (Au) дротів, мідні (Cu) дроти є привабливим способом управління загальною вартістю упаковки в мікроелектроніці. Він також нагадує золотий (Au) дріт через подібні електричні властивості. Власна індуктивність і власна ємність майже однакові для золотого (Au) і мідного (Cu) дроту, при цьому мідний (Cu) дріт має менший питомий опір. У застосуваннях мікроелектроніки, де опір зв’язаного дроту може негативно вплинути на продуктивність схеми, використання мідного (Cu) дроту може запропонувати покращення. Дроти зі сплавів міді, міді з паладієвим покриттям (PCC) і срібла (Ag) з’явилися як альтернатива дротам із золота через вартість. Провід на основі міді недорогий і має низький питомий електричний опір. Однак твердість міді ускладнює її використання в багатьох сферах застосування, наприклад, з крихкими структурами зв’язувальних прокладок. Для цих застосувань Ag-Alloy пропонує властивості, подібні до золота, а його вартість подібна до PCC. Дріт із Ag-Alloy м’якший, ніж PCC, що призводить до меншого розбризкування алюмінію та нижчого ризику пошкодження контактної площадки. Дріт із Ag-Alloy є найкращою недорогою заміною для застосувань, які потребують склеювання «плампа-до-пластинки», водоспадного склеювання, надтонкого кроку та малих отворів для скріплення, наднизької висоти петлі. Ми надаємо повний спектр послуг з тестування напівпровідників, включаючи тестування пластин, різні типи кінцевого тестування, тестування системного рівня, тестування стрічки та повні послуги наприкінці лінії. Ми тестуємо різноманітні типи напівпровідникових пристроїв у всіх наших сімействах упаковок, включаючи радіочастоти, аналогові та змішані сигнали, цифрові пристрої, керування живленням, пам’ять та різні комбінації, такі як ASIC, багатокристальні модулі, система в упаковці (SiP) і 3D-упаковка, датчики та MEMS-пристрої, такі як акселерометри та датчики тиску. Наше апаратне забезпечення для тестування та контактне обладнання підходить для пакетів спеціального розміру SiP, двосторонніх контактних рішень для Package on Package (PoP), TMV PoP, розеток FusionQuad, багаторядної MicroLeadFrame, Fine-Pitch Copper Pillar. Тестове обладнання та тестові підлоги інтегровані з інструментами CIM/CAM, аналізом продуктивності та моніторингом продуктивності, щоб забезпечити дуже високу продуктивність з першого разу. Ми пропонуємо численні адаптивні процеси тестування мікроелектроніки для наших клієнтів і пропонуємо розподілені потоки тестування для SiP та інших складних процесів складання. AGS-TECH надає повний спектр консультацій з тестування, розробки та інженерних послуг протягом усього життєвого циклу напівпровідникової та мікроелектронної продукції. Ми розуміємо унікальні ринки та вимоги до тестування для SiP, автомобільної промисловості, мереж, ігор, графіки, обчислень, радіочастотного/бездротового зв’язку. Процеси виробництва напівпровідників вимагають швидких і точно контрольованих рішень для маркування. Швидкість маркування понад 1000 символів/секунду та глибина проникнення матеріалу менше 25 мікрон є звичайним явищем у промисловості напівпровідникової мікроелектроніки з використанням сучасних лазерів. Ми можемо маркувати форми, пластини, кераміку тощо з мінімальним нагріванням і ідеальною повторюваністю. Ми використовуємо лазери з високою точністю, щоб розмітити навіть найдрібніші деталі без пошкоджень. Вивідні каркаси для напівпровідникових пристроїв: можливі як стандартні, так і індивідуальні конструкції та виготовлення. Вивідні рамки використовуються в процесах складання напівпровідникових пристроїв і являють собою, по суті, тонкі шари металу, які з’єднують проводку від крихітних електричних клем на поверхні напівпровідникової мікроелектроніки до великомасштабної схеми електричних пристроїв і друкованих плат. Вивідні рамки використовуються майже у всіх корпусах напівпровідникової мікроелектроніки. Більшість пакетів інтегральних мікросхем для мікроелектроніки виготовляються шляхом розміщення напівпровідникової кремнієвої мікросхеми на свинцевій рамці, потім дротом прикріплюють мікросхему до металевих проводів цієї свинцевої рамки, а потім накривають мікроелектронну мікросхему пластиковою кришкою. Цей простий і відносно недорогий пакет для мікроелектроніки все ще є найкращим рішенням для багатьох застосувань. Свинцеві рамки виготовляються у вигляді довгих смуг, що дозволяє швидко обробляти їх на автоматизованих складальних машинах, і зазвичай використовуються два виробничі процеси: фототравлення певного типу та штампування. У мікроелектроніці головна конструкція рами часто потребує індивідуальних специфікацій і функцій, конструкцій, які покращують електричні та теплові властивості, а також вимог до конкретного часу циклу. Ми маємо глибокий досвід виробництва мікроелектронних свинцевих рамок для цілої низки різних клієнтів із використанням лазерного фототравлення та штампування. Проектування та виготовлення радіаторів для мікроелектроніки: як стандартне, так і індивідуальне проектування та виготовлення. Зі збільшенням розсіювання тепла від мікроелектронних пристроїв і зменшенням загальних форм-факторів управління температурою стає все більш важливим елементом дизайну електронних виробів. Постійність продуктивності та очікуваний термін служби електронного обладнання обернено залежать від температури компонентів обладнання. Зв’язок між надійністю та робочою температурою типового кремнієвого напівпровідникового пристрою показує, що зниження температури відповідає експоненціальному збільшенню надійності та тривалості життя пристрою. Таким чином, тривалий термін служби та надійна робота компонента напівпровідникової мікроелектроніки можуть бути досягнуті шляхом ефективного контролю робочої температури пристрою в межах, встановлених розробниками. Радіатори — це пристрої, які посилюють розсіювання тепла від гарячої поверхні, як правило, зовнішнього корпусу компонента, що генерує тепло, до холоднішого навколишнього середовища, наприклад повітря. Для подальших обговорень повітря вважається охолоджувальною рідиною. У більшості ситуацій передача тепла через поверхню розділу між твердою поверхнею та повітрям охолоджувача є найменш ефективною в системі, а межа розділу тверде тіло – повітря є найбільшою перешкодою для розсіювання тепла. Радіатор знижує цей бар'єр головним чином за рахунок збільшення площі поверхні, яка безпосередньо контактує з теплоносієм. Це дозволяє розсіювати більше тепла та/або знижує робочу температуру напівпровідникового пристрою. Основне призначення радіатора — підтримувати температуру мікроелектронного пристрою нижче максимально допустимої температури, зазначеної виробником напівпровідникового пристрою. Ми можемо класифікувати радіатори з точки зору методів виробництва та їх форм. Найпоширеніші типи радіаторів з повітряним охолодженням включають: - Штампування: мідні або алюмінієві листові метали штампуються в потрібні форми. вони використовуються в традиційному повітряному охолодженні електронних компонентів і пропонують економічне вирішення проблем низької щільності тепла. Вони підходять для виробництва великих обсягів. - Екструзія: ці радіатори дозволяють формувати складні двовимірні форми, здатні розсіювати великі теплові навантаження. Їх можна вирізати, обробити та додати опції. Поперечне різання створить всеспрямовані прямокутні радіатори зі штифтовими ребрами, а використання зубчастих ребер покращує продуктивність приблизно на 10–20%, але з меншою швидкістю екструзії. Обмеження екструзії, такі як висота ребра до товщини зазору, зазвичай визначають гнучкість варіантів конструкції. Типове співвідношення між висотою ребер і зазором становить до 6 і мінімальну товщину ребер 1,3 мм можна досягти стандартними методами екструзії. Співвідношення сторін 10 до 1 і товщину ребра 0,8 дюйма можна отримати за допомогою спеціальних конструктивних особливостей матриці. Однак із збільшенням співвідношення сторін допуск екструзії знижується. - Склеєні/виготовлені ребра: більшість радіаторів з повітряним охолодженням мають обмежену конвекцію, і загальні теплові характеристики радіатора з повітряним охолодженням часто можна значно покращити, якщо більшу площу поверхні можна піддати впливу потоку повітря. У цих високоефективних радіаторах використовується теплопровідна епоксидна смола, наповнена алюмінієм, для прикріплення плоских ребер до рифленої екструзійної базової пластини. Цей процес дозволяє отримати набагато більше співвідношення висоти ребер до ширини зазору від 20 до 40, значно збільшуючи потужність охолодження без збільшення потреби в об’ємі. - Виливки: процеси лиття в пісок, лиття під тиском для алюмінію, міді/бронзи доступні з використанням вакууму або без нього. Ми використовуємо цю технологію для виготовлення радіаторів високої щільності, які забезпечують максимальну продуктивність при використанні ударного охолодження. - Складені ребра: гофрований листовий метал з алюмінію або міді збільшує площу поверхні та об'ємну продуктивність. Потім радіатор прикріплюється або до базової плити, або безпосередньо до нагрівальної поверхні за допомогою епоксидної смоли або пайки. Він не підходить для високопрофільних радіаторів через доступність і ефективність оребрення. Отже, це дозволяє виготовляти високоефективні радіатори. Вибираючи відповідний радіатор, який відповідає необхідним тепловим критеріям для ваших застосувань мікроелектроніки, нам потрібно вивчити різні параметри, які впливають не лише на саму продуктивність радіатора, але й на загальну продуктивність системи. Вибір конкретного типу радіатора в мікроелектроніці значною мірою залежить від теплового бюджету, дозволеного для радіатора, і зовнішніх умов навколо радіатора. Ніколи не існує єдиного значення термічного опору, призначеного для даного радіатора, оскільки термічний опір змінюється в залежності від зовнішніх умов охолодження. Конструкція та виготовлення датчиків і приводів: доступні як стандартні, так і спеціальні конструкції та виготовлення. Ми пропонуємо рішення з готовими до використання процесами для інерційних датчиків, датчиків тиску та відносного тиску та ІЧ-датчиків температури. Використовуючи наші IP-блоки для акселерометрів, ІЧ-датчиків і датчиків тиску або застосовуючи ваш дизайн відповідно до наявних специфікацій і правил проектування, ми можемо отримати сенсорні пристрої на основі MEMS протягом декількох тижнів. Крім MEMS, можна виготовити інші типи структур датчиків і приводів. Проектування та виготовлення оптоелектронних і фотонних схем. Фотонна або оптична інтегральна схема (PIC) — це пристрій, який об’єднує кілька фотонних функцій. Це можна нагадувати електронні інтегральні схеми в мікроелектроніці. Основна відмінність між ними полягає в тому, що фотонна інтегральна схема забезпечує функціональність для інформаційних сигналів, накладених на оптичні довжини хвиль у видимому спектрі або в ближньому інфрачервоному діапазоні 850-1650 нм. Технології виготовлення подібні до тих, що використовуються в інтегральних схемах мікроелектроніки, де фотолітографія використовується для створення візерунків на пластинах для травлення та нанесення матеріалу. На відміну від напівпровідникової мікроелектроніки, де первинним пристроєм є транзистор, в оптоелектроніці немає єдиного домінуючого пристрою. Фотонні мікросхеми включають в себе хвилеводи з низькими втратами, розгалужувачі потужності, оптичні підсилювачі, оптичні модулятори, фільтри, лазери та детектори. Ці пристрої вимагають різноманітних матеріалів і технологій виготовлення, тому важко реалізувати їх усі на одному чіпі. Наше застосування фотонних інтегральних схем в основному стосується волоконно-оптичних комунікацій, біомедичних і фотонних обчислень. Деякими прикладами оптоелектронних продуктів, які ми можемо розробити та виготовити для вас, є світлодіоди (світловипромінюючі діоди), діодні лазери, оптоелектронні приймачі, фотодіоди, лазерні дистанційні модулі, спеціальні лазерні модулі тощо. CLICK Product Finder-Locator Service ПОПЕРЕДНЯ СТОРІНКА
- Mesomanufacturing,Mesoscale Manufacturing,Miniature Device Fabrication
Mesomanufacturing - Mesoscale Manufacturing - Miniature Device Fabrication - Tiny Motors - AGS-TECH Inc. - New Mexico Мезомасштабне виробництво / Mesomanufacturing За допомогою звичайних технологій виробництва ми створюємо «макромасштабні» структури, які є відносно великими та видимими неозброєним оком. With MESOMANUFACTURING however ми виробляємо компоненти для мініатюрних пристроїв. Мезовиробництво також називається MESOSCALE MANUFACTURING or ME. Мезовиробництво перекриває як макро, так і мікровиробництво. Прикладами мезовиробництва є слухові апарати, стенти, дуже маленькі двигуни. Перший підхід у мезовиробництві полягає у зменшенні масштабу процесів макровиробництва. Наприклад, крихітний токарний верстат із розмірами в кілька десятків міліметрів і двигуном потужністю 1,5 Вт вагою 100 грамів є хорошим прикладом мезовиробництва, де відбулося зменшення масштабу. Другий підхід полягає в розширенні процесів мікровиробництва. Як приклад, процеси LIGA можна розширити й увійти в сферу мезовиробництва. Наші мезовиробничі процеси долають розрив між процесами MEMS на основі кремнію та традиційною мініатюрною обробкою. Мезомасштабні процеси дозволяють виготовляти дво- та тривимірні деталі мікронного розміру з традиційних матеріалів, таких як нержавіюча сталь, кераміка та скло. На даний момент доступні для нас процеси виробництва мезопродуктів, включаючи напилення сфокусованим іонним пучком (FIB), мікрофрезерування, мікротокарну роботу, ексимерну лазерну абляцію, фемтосекундну лазерну абляцію та мікроелектророзрядну (EDM) обробку. У цих мезомасштабних процесах використовуються субтрактивні технології механічної обробки (тобто видалення матеріалу), тоді як процес LIGA є додатковим мезомасштабним процесом. Процеси виробництва мезопродуктів мають різні можливості та специфікації продуктивності. Технічні характеристики механічної обробки, що представляють інтерес, включають мінімальний розмір елемента, допуск елемента, точність розташування елемента, обробку поверхні та швидкість зняття матеріалу (MRR). У нас є можливості мезовиробництва електромеханічних компонентів, для яких потрібні мезомасштабні деталі. Мезомасштабні деталі, виготовлені за допомогою субтрактивних процесів мезовиробництва, мають унікальні трибологічні властивості через різноманітність матеріалів і станів поверхні, створених різними процесами мезовиробництва. Ці субтрактивні мезомасштабні технології обробки викликають у нас занепокоєння щодо чистоти, складання та трибології. Чистота має життєво важливе значення в мезовиробництві, оскільки розмір частинок мезомасштабного бруду та сміття, що утворюється під час процесу мезообробки, можна порівняти з мезомасштабними характеристиками. Мезомасштабне фрезерування та токарна обробка можуть утворювати сколи та задирки, які можуть блокувати отвори. Морфологія поверхні та умови обробки поверхні значно відрізняються залежно від методу мезовиробництва. Мезомасштабні деталі важко використовувати та вирівнювати, що робить збірку проблемою, яку більшість наших конкурентів не в змозі подолати. Наші показники врожайності в мезовиробництві набагато вищі, ніж у наших конкурентів, що дає нам перевагу в тому, що ми можемо пропонувати кращі ціни. МЕЗОМАСШТАБНІ ПРОЦЕСИ ОБРОБКИ: наші основні методи мезовиробництва — це сфокусований іонний промінь (FIB), мікрофрезерування та мікротокарна обробка, лазерна мезообробка, мікро-EDM (електророзрядна обробка) Мезовиробництво з використанням сфокусованого іонного пучка (FIB), мікрофрезерування та мікроточіння: FIB розпилює матеріал із заготовки за допомогою бомбардування пучком іонів галію. Заготівлю монтують на набір точних ступенів і поміщають у вакуумну камеру під джерелом галію. Етапи трансляції та обертання у вакуумній камері роблять різні місця на заготовці доступними для пучка іонів галію для мезовиробництва FIB. Регульоване електричне поле сканує промінь, щоб охопити попередньо визначену спроектовану область. Потенціал високої напруги змушує джерело іонів галію прискорюватися та стикатися з деталлю. Зіткнення видаляють атоми з заготовки. Результатом процесу мезообробки FIB може бути створення майже вертикальних граней. Деякі доступні нам FIB мають діаметр променя всього 5 нанометрів, що робить FIB мезо- і навіть мікромасштабною машиною. Ми монтуємо мікрофрезерні інструменти на високоточних фрезерних верстатах до алюмінієвих каналів. Використовуючи FIB, ми можемо виготовляти мікротокарні інструменти, які потім можна використовувати на токарному верстаті для виготовлення стрижнів з тонкою різьбою. Іншими словами, FIB можна використовувати для обробки твердих інструментів, окрім безпосередньої мезообробки деталей на кінцевій заготовці. Повільна швидкість видалення матеріалу зробила FIB непрактичним для безпосередньої обробки великих елементів. Однак жорсткі інструменти можуть видаляти матеріал із вражаючою швидкістю та витривалі протягом кількох годин обробки. Незважаючи на це, FIB є практичним для безпосередньої мезообробки складних тривимірних форм, які не вимагають значної швидкості видалення матеріалу. Тривалість експозиції та кут падіння можуть значно вплинути на геометрію безпосередньо оброблених елементів. Лазерне мезовиробництво: ексимерні лазери використовуються для мезовиробництва. Ексимерний лазер обробляє матеріал, імпульсуючи його наносекундними імпульсами ультрафіолетового світла. Заготовка монтується на точних поступальних ступенях. Контролер координує рух заготовки відносно нерухомого УФ-лазерного променя та координує подачу імпульсів. Техніку проекції маски можна використовувати для визначення геометрії мезообробки. Маска вставляється в розширену частину променя, де плотність лазера надто низька для видалення маски. Геометрія маски зменшується через лінзу та проектується на деталь. Цей підхід можна використовувати для обробки кількох отворів (масивів) одночасно. Наші ексимерні та YAG-лазери можна використовувати для обробки полімерів, кераміки, скла та металів із розміром деталей до 12 мікрон. Хороший зв’язок між довжиною хвилі ультрафіолетового випромінювання (248 нм) і заготівлею при лазерному мезовиробництві / мезообробці призводить до вертикальних стінок каналу. Більш чистий підхід до лазерної мезообробки полягає у використанні титано-сапфірового фемтосекундного лазера. Сміття, яке можна виявити в таких процесах виробництва мезопродуктів, — це частинки нанорозміру. За допомогою фемтосекундного лазера можна мікроскопіювати елементи розміром в один мікрон. Процес фемтосекундної лазерної абляції унікальний тим, що він розриває атомні зв’язки замість термічної абляції матеріалу. Процес фемтосекундної лазерної мезо-/мікрообробки займає особливе місце в мезо-виробництві, тому що він чистіший, мікронний і не залежить від матеріалу. Мезовиробництво з використанням Micro-EDM (електророзрядна обробка): Електроерозрядна обробка видаляє матеріал за допомогою процесу іскрової ерозії. Наші електроелектронні машини можуть створювати елементи розміром до 25 мікрон. Для грузила та дротяної мікроерозійної машини двома основними міркуваннями для визначення розміру деталі є розмір електрода та проміжок над дугою. Використовуються електроди діаметром трохи більше 10 мікрон і товщиною всього кілька мікрон. Створення електрода складної геометрії для електроерозійної електророзійної машини вимагає ноу-хау. І графіт, і мідь популярні як електродні матеріали. Одним із підходів до виготовлення складного грузильного електроерозійного електрода для мезомасштабної деталі є використання процесу LIGA. Мідь, як матеріал електрода, може бути покрита у форми LIGA. Потім мідний електрод LIGA можна встановити на електроерозійний верстат для мезовиробництва деталі з іншого матеріалу, такого як нержавіюча сталь або ковар. Жоден мезовиробничий процес не є достатнім для всіх операцій. Деякі мезомасштабні процеси більш масштабні, ніж інші, але кожен процес має свою нішу. Здебільшого нам потрібні різноманітні матеріали для оптимізації роботи механічних компонентів, і нам зручно використовувати традиційні матеріали, такі як нержавіюча сталь, оскільки ці матеріали мають довгу історію та дуже добре охарактеризовані протягом багатьох років. Мезовиробничі процеси дозволяють використовувати традиційні матеріали. Субтрактивні мезомасштабні технології обробки розширюють нашу матеріальну базу. Заїдання може бути проблемою з деякими комбінаціями матеріалів у мезовиробництві. Кожен конкретний мезомасштабний процес обробки унікальним чином впливає на шорсткість і морфологію поверхні. Мікрофрезерування та мікроточіння можуть утворювати задирки та частинки, які можуть спричинити механічні проблеми. Micro-EDM може залишити перероблений шар, який може мати особливі характеристики зносу та тертя. Ефекти тертя між частинами мезомасштабу можуть мати обмежені точки контакту і не точно моделюються моделями поверхневого контакту. Деякі мезомасштабні технології обробки, такі як мікро-EDM, є досить зрілими, на відміну від інших, таких як фемтосекундна лазерна мезообробка, які все ще потребують додаткового розвитку. CLICK Product Finder-Locator Service ПОПЕРЕДНЯ СТОРІНКА