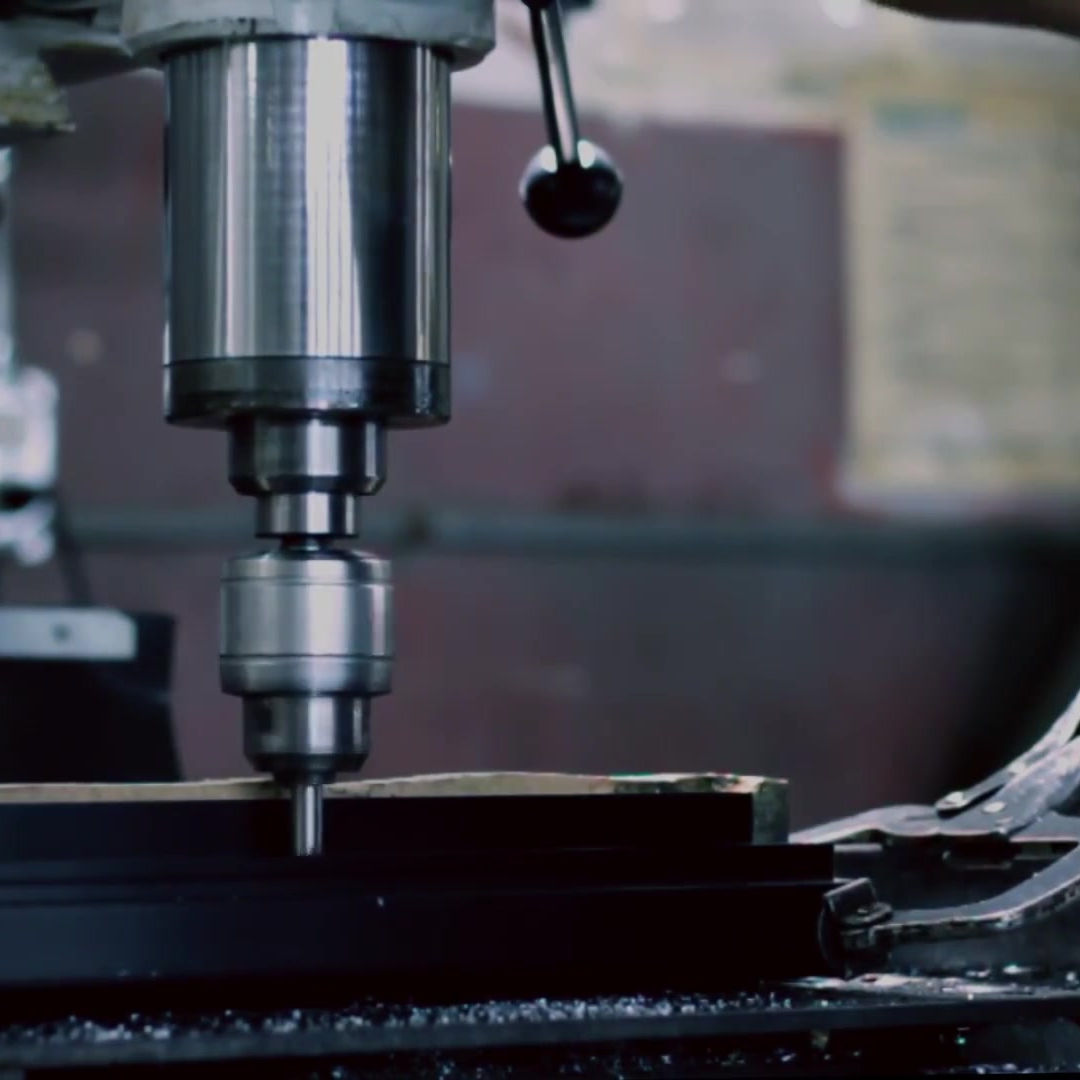
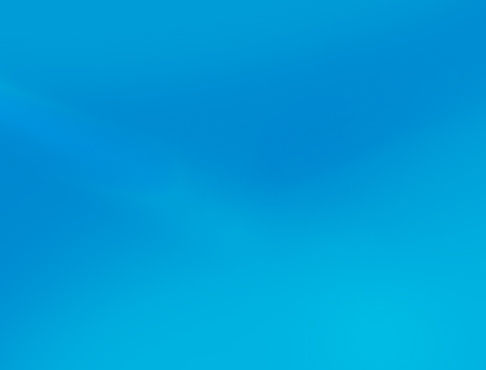
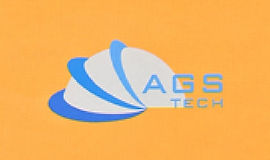
عالمی کسٹم مینوفیکچرر، انٹیگریٹر، کنسولیڈیٹر، مصنوعات اور خدمات کی وسیع اقسام کے لیے آؤٹ سورسنگ پارٹنر۔
ہم مینوفیکچرنگ، فیبریکیشن، انجینئرنگ، کنسولیڈیشن، انٹیگریشن، اپنی مرضی کے مطابق تیار کردہ اور آف شیلف پروڈکٹس اور خدمات کی آؤٹ سورسنگ کے لیے آپ کا واحد ذریعہ ہیں۔
Choose your Language
-
اپنی مرضی کے مطابق مینوفیکچرنگ
-
گھریلو اور عالمی کنٹریکٹ مینوفیکچرنگ
-
مینوفیکچرنگ آؤٹ سورسنگ
-
گھریلو اور عالمی خریداری
-
Consolidation
-
انجینئرنگ انٹیگریشن
-
انجینئرنگ سروسز
ہماری اپنی مرضی کے مطابق کاسٹنگ اور مشینی تکنیک قابل خرچ اور ناقابل خرچ کاسٹنگ ہیں، فیرس اور نان فیرس کاسٹنگ، ریت، ڈائی، سینٹری فیوگل، مسلسل، سیرامک مولڈ، انویسٹمنٹ، کھوئے ہوئے فوم، قریبی نیٹ شیپ، مستقل مولڈ (گریویٹی ڈائی کاسٹنگ)، پلاسٹر۔ مولڈ (پلاسٹر کاسٹنگ) اور شیل کاسٹنگ، روایتی نیز CNC آلات کا استعمال کرتے ہوئے ملنگ اور ٹرننگ کے ذریعے تیار کردہ مشینی حصے، اعلی تھرو پٹ سستے چھوٹے درست پرزوں کے لیے سوئس قسم کی مشینی، فاسٹنرز کے لیے سکرو مشین، غیر روایتی مشینی۔ براہ کرم ذہن میں رکھیں کہ دھاتوں اور دھات کے مرکب کے علاوہ، ہم سیرامک، شیشے اور پلاسٹک کے اجزاء کے ساتھ ساتھ بعض صورتوں میں جب سڑنا تیار کرنا پسند نہیں کرتا ہے یا آپشن نہیں ہے۔ پولیمر مٹیریل کی مشیننگ کے لیے ہمارے پاس خصوصی تجربے کی ضرورت ہوتی ہے کیونکہ پلاسٹک اور ربڑ کے تحفے ان کی نرمی، غیر سختی... وغیرہ کی وجہ سے چیلنج کرتے ہیں۔ سیرامک اور شیشے کی مشینی کے لیے، براہ کرم ہمارا صفحہ غیر روایتی فیبریکیشن پر دیکھیں۔ AGS-TECH Inc. ہلکے وزن اور بھاری دونوں کاسٹنگز تیار اور سپلائی کرتا ہے۔ ہم بوائلرز، ہیٹ ایکسچینجرز، آٹوموبائلز، مائیکرو موٹرز، ونڈ ٹربائنز، فوڈ پیکیجنگ کا سامان اور بہت کچھ کے لیے میٹل کاسٹنگ اور مشینی پرزے فراہم کرتے رہے ہیں۔ ہمارا مشورہ ہے کہ آپ یہاں کلک کریں AGS-TECH Inc کے ذریعے مشینی اور کاسٹنگ کے عمل کی ہماری اسکیمیٹک عکاسی ڈاؤن لوڈ کریں۔
اس سے آپ کو ان معلومات کو بہتر طور پر سمجھنے میں مدد ملے گی جو ہم آپ کو ذیل میں فراہم کر رہے ہیں۔ آئیے کچھ مختلف تکنیکوں کو دیکھتے ہیں جو ہم تفصیل سے پیش کرتے ہیں:
ایکسپینڈیبل مولڈ کاسٹنگ: اس وسیع زمرے سے مراد ایسے طریقے ہیں جن میں عارضی اور دوبارہ قابل استعمال مولڈ شامل ہیں۔ مثالیں ریت، پلاسٹر، خول، سرمایہ کاری (جسے لوسٹ ویکس بھی کہا جاتا ہے) اور پلاسٹر کاسٹنگ ہیں۔
• ریت کاسٹنگ: ایک ایسا عمل جہاں ریت کو مولڈ میٹریل کے طور پر استعمال کیا جاتا ہے۔ ایک بہت پرانا طریقہ اور اب بھی اس حد تک بہت مشہور ہے کہ زیادہ تر دھاتی کاسٹنگ اس تکنیک سے بنائی جاتی ہے۔ کم مقدار کی پیداوار پر بھی کم قیمت۔ چھوٹے اور بڑے حصوں کی تیاری کے لیے موزوں ہے۔ اس تکنیک کا استعمال بہت کم سرمایہ کاری کے ساتھ دنوں یا ہفتوں میں حصوں کی تیاری کے لیے کیا جا سکتا ہے۔ نم ریت کو مٹی، بائنڈر یا خصوصی تیل کا استعمال کرتے ہوئے ایک ساتھ جوڑا جاتا ہے۔ ریت عام طور پر مولڈ بکس میں ہوتی ہے اور ماڈلز کے گرد ریت کو کمپیکٹ کرکے کیویٹی اور گیٹ سسٹم بنایا جاتا ہے۔ عمل ہیں:
1.) سانچہ بنانے کے لیے ماڈل کو ریت میں رکھنا
2.) گیٹنگ سسٹم میں ماڈل اور ریت کو شامل کرنا
3.) ماڈل کو ہٹانا
4.) پگھلی ہوئی دھات سے مولڈ گہا کو بھرنا
5.) دھات کی ٹھنڈک
6.) ریت کے سڑنا کو توڑنا اور کاسٹنگ کو ہٹانا
• پلاسٹر مولڈ کاسٹنگ: ریت کاسٹنگ کی طرح، اور ریت کے بجائے، پلاسٹر آف پیرس کو مولڈ کے مواد کے طور پر استعمال کیا جا رہا ہے۔ مختصر پیداوار لیڈ ٹائم جیسے ریت کاسٹنگ اور سستا. اچھی جہتی رواداری اور سطح ختم۔ اس کا بڑا نقصان یہ ہے کہ اسے صرف کم پگھلنے والی دھاتوں جیسے ایلومینیم اور زنک کے ساتھ استعمال کیا جا سکتا ہے۔
• شیل مولڈ کاسٹنگ: ریت کاسٹنگ کی طرح بھی۔ مولڈ کیویٹی ریت کے سخت خول اور تھرموسیٹنگ رال بائنڈر سے حاصل کی گئی فلاسک کی بجائے ریت سے بھری ہوئی ریت کاسٹنگ کے عمل میں۔ ریت کے ذریعے کاسٹ کرنے کے لیے موزوں تقریباً کسی بھی دھات کو شیل مولڈنگ کے ذریعے کاسٹ کیا جا سکتا ہے۔ اس عمل کا خلاصہ اس طرح کیا جا سکتا ہے:
1.) شیل سڑنا کی تیاری. ریت کاسٹنگ میں استعمال ہونے والی ریت کے مقابلے میں استعمال ہونے والی ریت بہت چھوٹے دانے کے سائز کی ہوتی ہے۔ باریک ریت کو تھرموسیٹنگ رال کے ساتھ ملایا جاتا ہے۔ دھاتی پیٹرن کو الگ کرنے والے ایجنٹ کے ساتھ لیپت کیا جاتا ہے تاکہ شیل کو ہٹانا آسان ہو۔ اس کے بعد دھاتی پیٹرن کو گرم کیا جاتا ہے اور ریت کے مرکب کو گرم کاسٹنگ پیٹرن پر چھید یا اڑا دیا جاتا ہے۔ پیٹرن کی سطح پر ایک پتلا خول بنتا ہے۔ اس خول کی موٹائی کو ریت کے رال کے مرکب کے دھاتی پیٹرن کے ساتھ رابطے میں آنے کے وقت کی لمبائی کو مختلف کرکے ایڈجسٹ کیا جاسکتا ہے۔ پھر ڈھیلی ریت کو شیل سے ڈھکے ہوئے پیٹرن کے ساتھ ہٹا دیا جاتا ہے۔
2.) اگلا، شیل اور پیٹرن کو ایک تندور میں گرم کیا جاتا ہے تاکہ شیل سخت ہو جائے۔ سختی مکمل ہونے کے بعد، شیل کو پیٹرن میں بنے ہوئے پنوں کا استعمال کرتے ہوئے پیٹرن سے نکال دیا جاتا ہے۔
3.) اس طرح کے دو خولوں کو گلونگ یا کلیمپنگ کے ذریعے ایک ساتھ جوڑا جاتا ہے اور مکمل سانچہ بناتا ہے۔ اب شیل مولڈ کو ایک کنٹینر میں داخل کیا جاتا ہے جس میں اسے کاسٹنگ کے عمل کے دوران ریت یا دھاتی شاٹ سے سہارا دیا جاتا ہے۔
4.) اب گرم دھات کو شیل مولڈ میں ڈالا جا سکتا ہے۔
شیل کاسٹنگ کے فوائد بہت اچھی سطح کی تکمیل کے ساتھ مصنوعات ہیں، اعلی جہتی درستگی کے ساتھ پیچیدہ حصوں کی تیاری کا امکان، خود کار طریقے سے آسان عمل، بڑے حجم کی پیداوار کے لیے اقتصادی۔
نقصانات یہ ہیں کہ سانچوں کو اچھی وینٹیلیشن کی ضرورت ہوتی ہے کیونکہ ان گیسوں کی وجہ سے جو پگھلی ہوئی دھات بائنڈر کیمیکل سے رابطہ کرتی ہیں، تھرموسیٹنگ رال اور دھاتی پیٹرن مہنگے ہوتے ہیں۔ دھاتی پیٹرن کی لاگت کی وجہ سے، کم مقدار کی پیداوار کے رنز کے لیے یہ تکنیک مناسب نہیں ہوسکتی ہے۔
• انوسٹمنٹ کاسٹنگ (جسے لوسٹ-ویکس کاسٹنگ بھی کہا جاتا ہے): نیز ایک بہت پرانی تکنیک اور بہت سی دھاتوں، ریفریکٹری میٹریلز اور خاص اعلی کارکردگی والے مرکبات سے اعلیٰ درستگی، تکرار پذیری، استعداد اور سالمیت کے ساتھ معیاری پرزوں کی تیاری کے لیے موزوں ہے۔ چھوٹے اور بڑے سائز کے حصے بھی تیار کیے جا سکتے ہیں۔ کچھ دوسرے طریقوں کے مقابلے میں ایک مہنگا عمل ہے، لیکن بڑا فائدہ یہ ہے کہ قریب کی خالص شکل، پیچیدہ شکل اور تفصیلات کے ساتھ پرزے تیار کرنے کا امکان ہے۔ لہذا لاگت کچھ معاملات میں دوبارہ کام اور مشینی کے خاتمے سے کچھ حد تک آفسیٹ ہوتی ہے۔ اگرچہ تغیرات ہو سکتے ہیں، یہاں عام سرمایہ کاری کاسٹنگ عمل کا خلاصہ ہے:
1.) موم یا پلاسٹک سے اصل ماسٹر پیٹرن کی تخلیق. ہر کاسٹنگ کو ایک پیٹرن کی ضرورت ہوتی ہے کیونکہ یہ عمل میں تباہ ہو جاتے ہیں۔ سڑنا جس سے پیٹرن تیار کیے جاتے ہیں اس کی بھی ضرورت ہوتی ہے اور زیادہ تر وقت مولڈ کاسٹ یا مشینی ہوتا ہے۔ چونکہ مولڈ کو کھولنے کی ضرورت نہیں ہے، پیچیدہ کاسٹنگ حاصل کی جا سکتی ہے، موم کے بہت سے نمونوں کو درخت کی شاخوں کی طرح جوڑا جا سکتا ہے اور ایک ساتھ ڈالا جا سکتا ہے، اس طرح دھات یا دھات کے مرکب کے ایک ہی انڈیلنے سے متعدد حصوں کی پیداوار کو قابل بنایا جا سکتا ہے۔
2.) اس کے بعد، پیٹرن کو بہت باریک دانے دار سلیکا، پانی، بائنڈرز پر مشتمل ریفریکٹری سلوری کے ساتھ ڈبو یا ڈالا جاتا ہے۔ اس کے نتیجے میں پیٹرن کی سطح پر سیرامک پرت بنتی ہے۔ پیٹرن پر ریفریکٹری کوٹ کو خشک اور سخت ہونے کے لیے چھوڑ دیا گیا ہے۔ یہ مرحلہ وہ ہے جہاں سے سرمایہ کاری کا نام آتا ہے: ریفریکٹری سلوری کو موم کے انداز پر لگایا جاتا ہے۔
3.) اس مرحلے پر، سخت سیرامک مولڈ کو الٹا اور گرم کیا جاتا ہے تاکہ موم پگھل جائے اور سانچے سے باہر نکل جائے۔ دھاتی کاسٹنگ کے لیے ایک گہا پیچھے رہ گیا ہے۔
4.) موم کے باہر ہونے کے بعد، سیرامک مولڈ کو زیادہ درجہ حرارت پر گرم کیا جاتا ہے جس کے نتیجے میں سڑنا مضبوط ہوتا ہے۔
5.) دھاتی کاسٹنگ تمام پیچیدہ حصوں کو بھرنے والے گرم سانچے میں ڈالی جاتی ہے۔
6.) کاسٹنگ کو مضبوط کرنے کی اجازت ہے۔
7.) آخر میں سیرامک مولڈ ٹوٹ جاتا ہے اور تیار شدہ حصے درخت سے کاٹے جاتے ہیں۔
انویسٹمنٹ کاسٹنگ پلانٹ بروشر کا لنک یہ ہے۔
ایواپوریٹیو پیٹرن کاسٹنگ: اس عمل میں پولی اسٹیرین فوم جیسے مواد سے بنے پیٹرن کا استعمال کیا جاتا ہے جو گرم پگھلی ہوئی دھات کو سانچے میں ڈالنے پر بخارات بن جاتا ہے۔ اس عمل کی دو قسمیں ہیں: کھوئی ہوئی فوم کاسٹنگ جو بغیر بندھے ہوئے ریت کا استعمال کرتی ہے اور مکمل مولڈ کاسٹنگ جو بندھے ہوئے ریت کا استعمال کرتی ہے۔ یہاں عام عمل کے اقدامات ہیں:
1.) پولی اسٹیرین جیسے مواد سے پیٹرن تیار کریں۔ جب بڑی مقدار میں تیار کیا جائے گا، پیٹرن مولڈ کیا جاتا ہے. اگر حصہ پیچیدہ شکل رکھتا ہے، تو اس طرح کے جھاگ کے مواد کے کئی حصوں کو پیٹرن بنانے کے لیے ایک ساتھ جوڑنے کی ضرورت پڑسکتی ہے۔ ہم اکثر پیٹرن کو ایک ریفریکٹری کمپاؤنڈ کے ساتھ کوٹ کرتے ہیں تاکہ کاسٹنگ پر اچھی سطح کی تکمیل ہو۔
2.) پیٹرن پھر مولڈنگ ریت میں ڈال دیا جاتا ہے.
3.) پگھلی ہوئی دھات کو سانچے میں ڈالا جاتا ہے، فوم پیٹرن کو بخارات بناتا ہے، یعنی پولی اسٹیرین زیادہ تر معاملات میں جب یہ مولڈ گہا سے گزرتی ہے۔
4.) پگھلی ہوئی دھات کو سخت ہونے کے لیے ریت کے سانچے میں چھوڑ دیا جاتا ہے۔
5.) سخت ہونے کے بعد، ہم معدنیات سے متعلق ہٹا دیتے ہیں.
بعض صورتوں میں، ہم جس پروڈکٹ کو تیار کرتے ہیں اسے پیٹرن کے اندر ایک کور کی ضرورت ہوتی ہے۔ evaporative کاسٹنگ میں، مولڈ گہا میں کور رکھنے اور محفوظ کرنے کی ضرورت نہیں ہے۔ یہ تکنیک بہت پیچیدہ جیومیٹریوں کی تیاری کے لیے موزوں ہے، یہ اعلی حجم کی پیداوار کے لیے آسانی سے خودکار ہو سکتی ہے، اور کاسٹ کے حصے میں کوئی الگ کرنے والی لائنیں نہیں ہیں۔ بنیادی عمل سادہ اور لاگو کرنے کے لئے اقتصادی ہے. بڑے حجم کی پیداوار کے لیے، چونکہ پولی اسٹیرین سے پیٹرن تیار کرنے کے لیے ڈائی یا مولڈ کی ضرورت ہوتی ہے، اس لیے یہ کچھ مہنگا پڑ سکتا ہے۔
• غیر قابل توسیع مولڈ کاسٹنگ: اس وسیع زمرے سے مراد وہ طریقے ہیں جہاں ہر پیداواری دور کے بعد مولڈ کو درست کرنے کی ضرورت نہیں ہے۔ مثالیں مستقل، مرنے، مسلسل اور سینٹری فیوگل کاسٹنگ ہیں۔ تکرار کی صلاحیت حاصل کی جاتی ہے اور حصوں کو NEAR NET SHAPE کے طور پر نمایاں کیا جا سکتا ہے۔
• مستقل مولڈ کاسٹنگ: دھات سے بنے دوبارہ قابل استعمال سانچوں کو متعدد کاسٹنگ کے لیے استعمال کیا جاتا ہے۔ ایک مستقل سڑنا عام طور پر ختم ہونے سے پہلے دسیوں ہزار بار استعمال کیا جا سکتا ہے۔ کشش ثقل، گیس پریشر یا ویکیوم عام طور پر سڑنا بھرنے کے لیے استعمال ہوتے ہیں۔ سانچوں (جسے ڈائی بھی کہا جاتا ہے) عام طور پر لوہے، سٹیل، سیرامک یا دیگر دھاتوں سے بنے ہوتے ہیں۔ عام عمل ہے:
1.) مشین بنائیں اور سڑنا بنائیں۔ دو دھاتی بلاکس میں سے مولڈ کو مشین بنانا ایک عام بات ہے جو ایک ساتھ فٹ بیٹھتے ہیں اور کھولے اور بند کیے جا سکتے ہیں۔ دونوں حصے کی خصوصیات کے ساتھ ساتھ گیٹنگ سسٹم کو عام طور پر کاسٹنگ مولڈ میں مشین کیا جاتا ہے۔
2.) اندرونی سڑنا کی سطحوں کو ریفریکٹری مواد کو شامل کرتے ہوئے گارا کے ساتھ لیپت کیا گیا ہے۔ یہ گرمی کے بہاؤ کو کنٹرول کرنے میں مدد کرتا ہے اور کاسٹ کے حصے کو آسانی سے ہٹانے کے لیے چکنا کرنے والے کے طور پر کام کرتا ہے۔
3.) اگلا، سڑنا کے مستقل حصوں کو بند کر دیا جاتا ہے اور مولڈ کو گرم کیا جاتا ہے۔
4.) پگھلی ہوئی دھات کو سانچے میں ڈالا جاتا ہے اور اسے مستحکم کرنے کے لیے چھوڑ دیا جاتا ہے۔
5.) زیادہ ٹھنڈک ہونے سے پہلے، جب سڑنا کے آدھے حصے کھل جاتے ہیں تو ہم ایجیکٹرز کا استعمال کرتے ہوئے مستقل مولڈ سے حصہ نکال دیتے ہیں۔
ہم اکثر کم پگھلنے والی دھاتوں جیسے زنک اور ایلومینیم کے لیے مستقل مولڈ کاسٹنگ کا استعمال کرتے ہیں۔ سٹیل کاسٹنگ کے لیے، ہم گریفائٹ کو مولڈ میٹریل کے طور پر استعمال کرتے ہیں۔ ہم بعض اوقات مستقل سانچوں کے اندر کور کا استعمال کرتے ہوئے پیچیدہ جیومیٹریاں حاصل کرتے ہیں۔ اس تکنیک کے فوائد میں تیزی سے ٹھنڈک، خصوصیات میں یکسانیت، اچھی درستگی اور سطح کی تکمیل، کم مسترد ہونے کی شرح، عمل کو خودکار کرنے کا امکان اور اقتصادی طور پر زیادہ حجم پیدا کرنے کے ذریعے حاصل کی جانے والی اچھی میکانکی خصوصیات کے ساتھ کاسٹنگ ہیں۔ نقصانات اعلیٰ ابتدائی سیٹ اپ اخراجات ہیں جو اسے کم حجم کے آپریشنز کے لیے غیر موزوں بناتے ہیں، اور تیار کردہ پرزوں کے سائز پر پابندیاں۔
• ڈائی کاسٹنگ: ڈائی مشین کی جاتی ہے اور پگھلی ہوئی دھات کو زیادہ دباؤ کے تحت مولڈ گہاوں میں دھکیل دیا جاتا ہے۔ نان فیرس اور فیرس میٹل ڈائی کاسٹنگ دونوں ممکن ہیں۔ یہ عمل تفصیلات، انتہائی پتلی دیواروں، جہتی مستقل مزاجی اور اچھی سطح کی تکمیل کے ساتھ چھوٹے سے درمیانے سائز کے حصوں کی اعلیٰ مقدار میں پیداوار کے لیے موزوں ہے۔ AGS-TECH Inc. اس تکنیک کا استعمال کرتے ہوئے دیوار کی موٹائی 0.5 ملی میٹر تک تیار کرنے کے قابل ہے۔ مستقل مولڈ کاسٹنگ کی طرح، مولڈ میں دو حصوں پر مشتمل ہونا ضروری ہے جو پیدا ہونے والے حصے کو ہٹانے کے لیے کھل اور بند ہو سکتے ہیں۔ ایک ڈائی کاسٹنگ مولڈ میں ہر سائیکل کے ساتھ ایک سے زیادہ کاسٹنگ کی پیداوار کو قابل بنانے کے لیے متعدد گہا ہو سکتے ہیں۔ ڈائی کاسٹنگ مولڈ بہت بھاری ہوتے ہیں اور ان پرزوں سے بہت بڑے ہوتے ہیں، اس لیے مہنگے بھی ہوتے ہیں۔ جب تک وہ اپنے پرزہ جات ہم سے دوبارہ ترتیب دیتے ہیں ہم اپنے صارفین کے لیے بغیر کسی معاوضے کی مرمت اور تبدیل کرتے ہیں۔ ہمارے مرنے والوں کی کئی لاکھ سائیکلوں کی حد میں لمبی عمر ہوتی ہے۔
یہاں بنیادی آسان عمل کے اقدامات ہیں:
1.) عام طور پر سٹیل سے سڑنا کی پیداوار
2.) ڈائی کاسٹنگ مشین پر مولڈ نصب ہے۔
3.) پسٹن پیچیدہ خصوصیات اور پتلی دیواروں کو بھرتے ہوئے پگھلی ہوئی دھات کو ڈائی کیویٹیز میں بہنے پر مجبور کرتا ہے۔
4.) پگھلی ہوئی دھات سے سڑنا بھرنے کے بعد، کاسٹنگ کو دباؤ میں سخت ہونے دیا جاتا ہے۔
5.) مولڈ کو کھولا جاتا ہے اور ایجیکٹر پن کی مدد سے کاسٹنگ کو ہٹا دیا جاتا ہے۔
6.) اب خالی ڈائی کو دوبارہ چکنا کر دیا جاتا ہے اور اگلے چکر کے لیے کلیمپ کیا جاتا ہے۔
ڈائی کاسٹنگ میں، ہم اکثر انسرٹ مولڈنگ کا استعمال کرتے ہیں جہاں ہم مولڈ میں ایک اضافی حصہ شامل کرتے ہیں اور اس کے ارد گرد دھات ڈالتے ہیں۔ مضبوطی کے بعد، یہ حصے کاسٹ پروڈکٹ کا حصہ بن جاتے ہیں۔ ڈائی کاسٹنگ کے فوائد پرزوں کی اچھی مکینیکل خصوصیات، پیچیدہ خصوصیات کا امکان، عمدہ تفصیلات اور اچھی سطح کی تکمیل، اعلی پیداوار کی شرح، آسان آٹومیشن ہیں۔ نقصانات یہ ہیں: کم حجم کے لیے موزوں نہیں کیونکہ زیادہ ڈائی اور سامان کی لاگت، کاسٹ کی جا سکتی شکلوں میں محدودیت، ایجیکٹر پنوں کے رابطے کے نتیجے میں کاسٹ پرزوں پر چھوٹے گول نشان، الگ کرنے والی لائن پر دھات کی پتلی چمک، ضرورت ڈائی کے درمیان علیحدگی کی لکیر کے ساتھ وینٹ کے لیے، پانی کی گردش کا استعمال کرتے ہوئے سڑنا کا درجہ حرارت کم رکھنے کی ضرورت ہے۔
• سینٹرفیوگل کاسٹنگ: پگھلی ہوئی دھات کو گردش کے محور پر گھومنے والے سانچے کے مرکز میں ڈالا جاتا ہے۔ سینٹرفیوگل قوتیں دھات کو دائرہ کی طرف پھینکتی ہیں اور اسے مضبوط ہونے دیا جاتا ہے کیونکہ سانچہ گھومتا رہتا ہے۔ افقی اور عمودی محور دونوں گردشیں استعمال کی جا سکتی ہیں۔ گول اندرونی سطحوں کے ساتھ ساتھ دیگر غیر گول شکلوں والے حصے کاسٹ کیے جا سکتے ہیں۔ اس عمل کا خلاصہ اس طرح کیا جا سکتا ہے:
1.) پگھلی ہوئی دھات کو سینٹرفیوگل مولڈ میں ڈالا جاتا ہے۔ پھر دھات کو مولڈ کے گھومنے کی وجہ سے بیرونی دیواروں پر مجبور کیا جاتا ہے۔
2.) جیسے جیسے سڑنا گھومتا ہے، دھاتی کاسٹنگ سخت ہوتی جاتی ہے۔
سینٹرفیوگل کاسٹنگ پائپ جیسے کھوکھلے بیلناکار حصوں کی تیاری کے لیے ایک موزوں تکنیک ہے، اسپروز، رائزرز اور گیٹنگ عناصر کی ضرورت نہیں، سطح کی اچھی تکمیل اور تفصیلی خصوصیات، سکڑنے کا کوئی مسئلہ نہیں، بہت بڑے قطر کے ساتھ لمبے پائپ تیار کرنے کا امکان، اعلی شرح پیداواری صلاحیت۔ .
• مسلسل کاسٹنگ ( اسٹرینڈ کاسٹنگ ) : دھات کی مسلسل لمبائی کاسٹ کرنے کے لیے استعمال کیا جاتا ہے۔ بنیادی طور پر پگھلی ہوئی دھات کو مولڈ کے دو جہتی پروفائل میں ڈالا جاتا ہے لیکن اس کی لمبائی غیر متعین ہوتی ہے۔ نئی پگھلی ہوئی دھات کو مسلسل سانچے میں ڈالا جاتا ہے کیونکہ کاسٹنگ وقت کے ساتھ ساتھ اس کی لمبائی میں اضافے کے ساتھ نیچے کی طرف سفر کرتی ہے۔ کاپر، سٹیل، ایلومینیم جیسی دھاتوں کو مسلسل کاسٹنگ کے عمل کے ذریعے لمبے کناروں میں ڈالا جاتا ہے۔ اس عمل کی مختلف ترتیبیں ہو سکتی ہیں لیکن عام کو اس طرح آسان بنایا جا سکتا ہے:
1.) پگھلی ہوئی دھات کو ایک کنٹینر میں ڈالا جاتا ہے جو مولڈ کے اوپر واقع ہے اچھی طرح سے حساب شدہ مقدار اور بہاؤ کی شرح پر اور پانی کے ٹھنڈے سانچے میں سے بہتا ہے۔ سانچے میں ڈالی جانے والی دھاتی کاسٹنگ مولڈ کے نچلے حصے میں رکھی ہوئی اسٹارٹر بار میں مضبوط ہو جاتی ہے۔ یہ اسٹارٹر بار رولرس کو ابتدائی طور پر پکڑنے کے لیے کچھ دیتا ہے۔
2.) طویل دھاتی اسٹرینڈ کو رولرس کے ذریعے مسلسل رفتار سے اٹھایا جاتا ہے۔ رولر دھاتی پٹی کے بہاؤ کی سمت کو عمودی سے افقی تک بھی تبدیل کرتے ہیں۔
3.) مسلسل کاسٹنگ کے ایک مخصوص افقی فاصلہ طے کرنے کے بعد، ایک ٹارچ یا آری جو کاسٹنگ کے ساتھ حرکت کرتی ہے اسے تیزی سے مطلوبہ لمبائی تک کاٹ دیتی ہے۔
مسلسل کاسٹنگ کے عمل کو رولنگ پروسیس کے ساتھ مربوط کیا جا سکتا ہے، جہاں مسلسل کاسٹ شدہ دھات کو براہ راست رولنگ مل میں فیڈ کیا جا سکتا ہے تاکہ I-Beams، T-Beams…. وغیرہ۔ مسلسل کاسٹنگ پوری پروڈکٹ میں یکساں خصوصیات پیدا کرتی ہے، اس میں مضبوطی کی شرح بہت زیادہ ہے، مواد کے بہت کم نقصان کی وجہ سے لاگت میں کمی آتی ہے، ایک ایسا عمل پیش کرتا ہے جہاں دھات کو لوڈ کرنا، ڈالنا، ٹھوس بنانا، کاٹنا اور کاسٹنگ ہٹانا یہ سب ایک مسلسل آپریشن میں ہوتا ہے اور اس طرح اعلی پیداوری کی شرح اور اعلی معیار کے نتیجے میں. تاہم ایک اہم غور اعلیٰ ابتدائی سرمایہ کاری، سیٹ اپ کے اخراجات اور جگہ کی ضروریات ہیں۔
• مشینی خدمات: ہم تین، چار اور پانچ - محور مشینی پیش کرتے ہیں۔ ہم جس قسم کے مشینی عمل کا استعمال کرتے ہیں وہ ہیں ٹرننگ، ملنگ، ڈرلنگ، بورنگ، بروچنگ، پلاننگ، ساونگ، گرائنڈنگ، لیپنگ، پالشنگ اور غیر روایتی مشینیں جو ہماری ویب سائٹ کے ایک مختلف مینو کے تحت مزید تفصیل سے بیان کی گئی ہیں۔ ہماری زیادہ تر مینوفیکچرنگ کے لیے، ہم CNC مشینیں استعمال کرتے ہیں۔ تاہم کچھ آپریشنز کے لیے روایتی تکنیکیں بہتر ہیں اور اس لیے ہم ان پر بھی بھروسہ کرتے ہیں۔ ہماری مشینی صلاحیتیں ممکنہ حد تک بلند ترین سطح تک پہنچ جاتی ہیں اور کچھ انتہائی مطلوبہ پرزے AS9100 تصدیق شدہ پلانٹ میں تیار کیے جاتے ہیں۔ جیٹ انجن کے بلیڈ کے لیے انتہائی خصوصی مینوفیکچرنگ کے تجربے اور صحیح آلات کی ضرورت ہوتی ہے۔ ایرو اسپیس انڈسٹری کے بہت سخت معیارات ہیں۔ پیچیدہ جیومیٹریکل ڈھانچے کے ساتھ کچھ اجزاء پانچ محور مشینی کے ذریعہ سب سے زیادہ آسانی سے تیار کیے جاتے ہیں، جو صرف ہمارے بشمول کچھ مشینی پلانٹس میں پائے جاتے ہیں۔ ہمارے ایرو اسپیس سرٹیفائیڈ پلانٹ کے پاس ایرو اسپیس انڈسٹری کی وسیع دستاویزات کی ضروریات کو پورا کرنے کا ضروری تجربہ ہے۔
ٹرننگ آپریشنز میں، ایک ورک پیس کو گھمایا جاتا ہے اور اسے کاٹنے والے آلے کے خلاف منتقل کیا جاتا ہے۔ اس عمل کے لیے لیتھ نامی مشین استعمال کی جا رہی ہے۔
ملنگ میں، ملنگ مشین کہلانے والی مشین میں ایک گھومنے والا ٹول ہوتا ہے جو کٹنگ کناروں کو ورک پیس کے خلاف برداشت کرنے کے لیے لاتا ہے۔
ڈرلنگ کے کاموں میں ایک گھومنے والا کٹر ہوتا ہے جس میں کناروں کا کٹا ہوا ہوتا ہے جو ورک پیس کے ساتھ رابطے پر سوراخ پیدا کرتا ہے۔ ڈرل پریس، لیتھز یا ملز عام طور پر استعمال ہوتے ہیں۔
بورنگ آپریشنز میں ایک ٹول کو ایک ہی جھکی ہوئی نوک کے ساتھ گھومنے والی ورک پیس میں کسی کھردرے سوراخ میں منتقل کیا جاتا ہے تاکہ سوراخ کو تھوڑا بڑا کیا جا سکے اور درستگی کو بہتر بنایا جا سکے۔ یہ ٹھیک ختم کرنے کے مقاصد کے لئے استعمال کیا جاتا ہے.
بروچنگ میں بروچ کے ایک پاس میں ورک پیس سے مواد کو ہٹانے کے لیے دانتوں والا ٹول شامل ہوتا ہے۔ لکیری بروچنگ میں، بروچ کٹ کو متاثر کرنے کے لیے ورک پیس کی سطح کے خلاف لکیری طور پر چلتا ہے، جب کہ روٹری بروچنگ میں، بروچ کو گھما کر ورک پیس میں دبایا جاتا ہے تاکہ محور کی ہم آہنگی کی شکل کو کاٹ سکے۔
SWISS TYPE MACHINING ہماری قیمتی تکنیکوں میں سے ایک ہے جسے ہم چھوٹے اعلی صحت سے متعلق حصوں کی اعلی حجم کی تیاری کے لیے استعمال کرتے ہیں۔ سوئس قسم کی لیتھ کا استعمال کرتے ہوئے ہم چھوٹے، پیچیدہ، درست پرزوں کو سستے میں موڑ دیتے ہیں۔ روایتی لیتھز کے برعکس جہاں ورک پیس کو سٹیشنری اور ٹول حرکت میں رکھا جاتا ہے، سوئس قسم کے ٹرننگ سینٹرز میں، ورک پیس کو Z-axis میں منتقل کرنے کی اجازت ہے اور ٹول سٹیشنری ہے۔ سوئس قسم کی مشینی میں، بار سٹاک کو مشین میں رکھا جاتا ہے اور z-axis میں گائیڈ بشنگ کے ذریعے آگے بڑھایا جاتا ہے، صرف مشینی ہونے والے حصے کو بے نقاب کرتا ہے۔ اس طرح ایک سخت گرفت کو یقینی بنایا جاتا ہے اور درستگی بہت زیادہ ہوتی ہے۔ لائیو ٹولز کی دستیابی گائیڈ بشنگ سے مواد کی ترقی کے ساتھ مل اور ڈرل کرنے کا موقع فراہم کرتی ہے۔ سوئس قسم کے آلات کا Y-axis مکمل گھسائی کرنے کی صلاحیت فراہم کرتا ہے اور مینوفیکچرنگ میں بہت زیادہ وقت بچاتا ہے۔ مزید برآں، ہماری مشینوں میں ڈرلز اور بورنگ ٹولز ہوتے ہیں جو اس حصے پر کام کرتے ہیں جب اسے سب سپنڈل میں رکھا جاتا ہے۔ ہماری سوئس قسم کی مشینی صلاحیت ہمیں ایک ہی آپریشن میں مکمل طور پر خودکار مکمل مشیننگ کا موقع فراہم کرتی ہے۔
مشیننگ AGS-TECH Inc. کاروبار کے سب سے بڑے حصوں میں سے ایک ہے۔ ہم یا تو اسے پرائمری آپریشن کے طور پر استعمال کرتے ہیں یا کسی حصے کو کاسٹ کرنے یا نکالنے کے بعد ثانوی آپریشن کے طور پر استعمال کرتے ہیں تاکہ ڈرائنگ کی تمام وضاحتیں پوری ہوں۔
• سرفیس فنشنگ سروسز: ہم سطح کے علاج اور سطح کی فنشنگ کی وسیع اقسام پیش کرتے ہیں جیسے چپکنے کو بڑھانے کے لیے سطح کی کنڈیشنگ، کوٹنگ کے چپکنے کو بڑھانے کے لیے پتلی آکسائیڈ کی تہہ جمع کرنا، سینڈ بلاسٹنگ، کیم فلم، انوڈائزنگ، نائٹرائڈنگ، پاؤڈر کوٹنگ، سپرے کوٹنگ۔ , مختلف جدید میٹالائزیشن اور کوٹنگ کی تکنیکیں بشمول سپٹرنگ، الیکٹران بیم، بخارات، چڑھانا، سخت کوٹنگز جیسے ہیرے جیسے کاربن (DLC) یا ٹائٹینیم کوٹنگ ڈرلنگ اور کٹنگ ٹولز کے لیے۔
• پروڈکٹ مارکنگ اور لیبلنگ کی خدمات: ہمارے بہت سے صارفین کو مارکنگ اور لیبلنگ، لیزر مارکنگ، دھاتی حصوں پر کندہ کاری کی ضرورت ہوتی ہے۔ اگر آپ کو ایسی کوئی ضرورت ہے تو آئیے اس پر بات کریں کہ کون سا آپشن آپ کے لیے بہترین ہوگا۔
یہاں عام طور پر استعمال ہونے والی دھاتی کاسٹ مصنوعات میں سے کچھ ہیں۔ چونکہ یہ شیلف سے باہر ہیں، اگر ان میں سے کوئی بھی آپ کی ضروریات کے مطابق ہو تو آپ مولڈ کے اخراجات کو بچا سکتے ہیں:
AGS-Electronics سے ہمارے 11 سیریز کے ڈائی کاسٹ ایلومینیم باکسز ڈاؤن لوڈ کرنے کے لیے یہاں کلک کریں۔