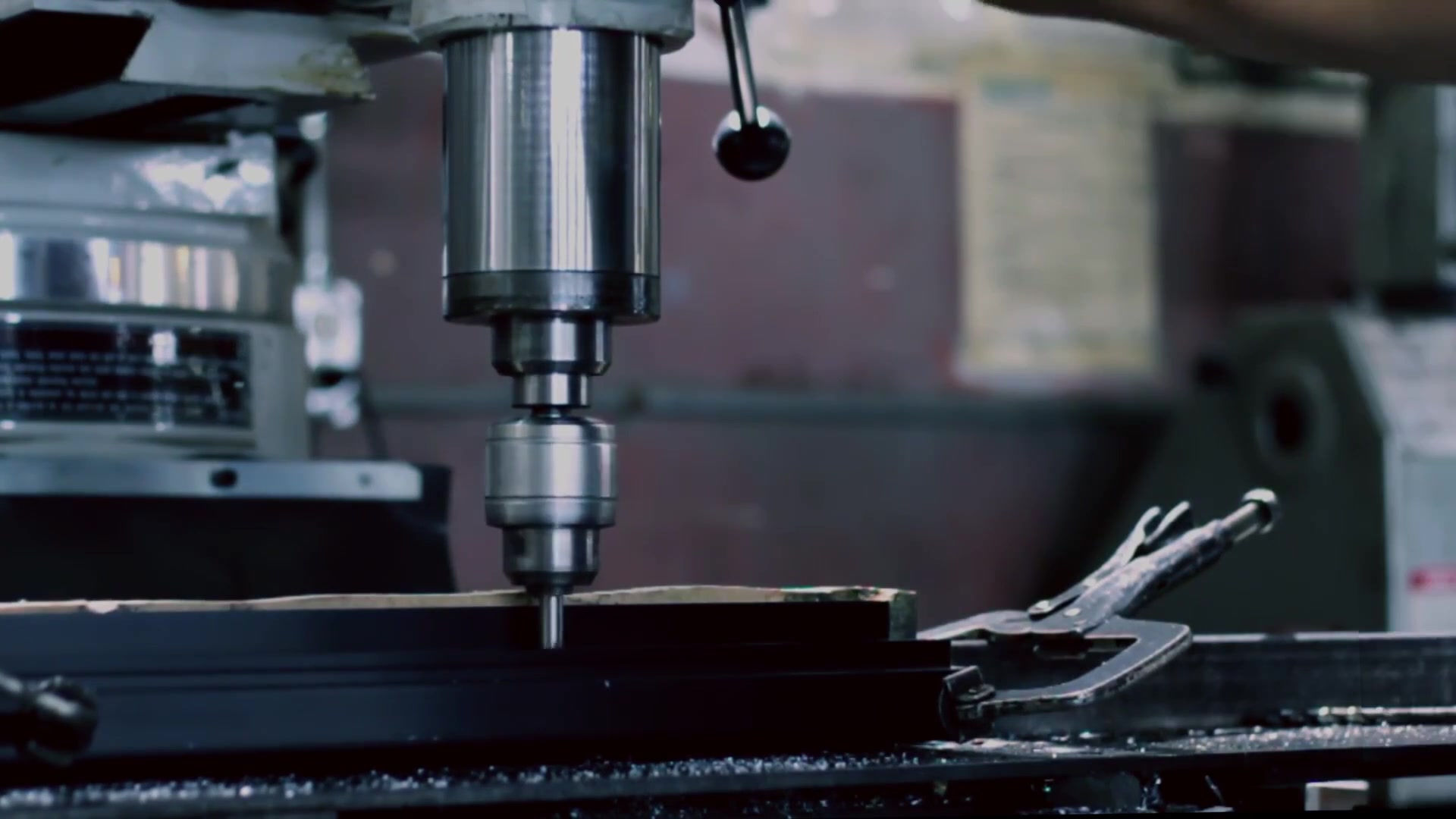
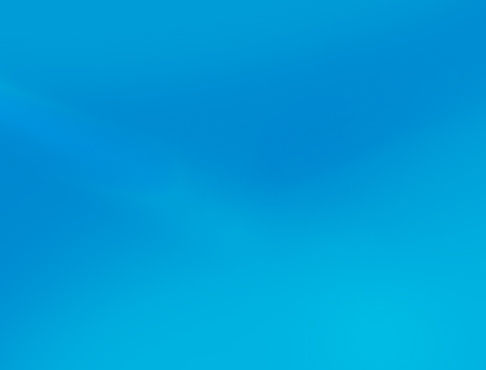
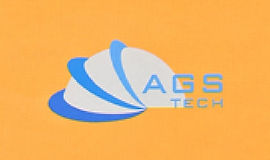
عالمی کسٹم مینوفیکچرر، انٹیگریٹر، کنسولیڈیٹر، مصنوعات اور خدمات کی وسیع اقسام کے لیے آؤٹ سورسنگ پارٹنر۔
ہم مینوفیکچرنگ، فیبریکیشن، انجینئرنگ، کنسولیڈیشن، انٹیگریشن، اپنی مرضی کے مطابق تیار کردہ اور آف شیلف پروڈکٹس اور خدمات کی آؤٹ سورسنگ کے لیے آپ کا واحد ذریعہ ہیں۔
Choose your Language
-
اپنی مرضی کے مطابق مینوفیکچرنگ
-
گھریلو اور عالمی کنٹریکٹ مینوفیکچرنگ
-
مینوفیکچرنگ آؤٹ سورسنگ
-
گھریلو اور عالمی خریداری
-
Consolidation
-
انجینئرنگ انٹیگریشن
-
انجینئرنگ سروسز
ELECTRICAL DISCHARGE MACHINING (EDM), also referred to as SPARK-EROSION or ELECTRODISCHARGE MACHINING, SPARK ERODING, DIE SINKING_cc781905-5cde-3194-bb3b -136bad5cf58d_or WIRE EROSION, is a NON-CONVENTIONAL MANUFACTURING process where erosion of metals takes place and desired shape is obtained using electrical discharges in the form چنگاریوں کی ہم EDM کی کچھ اقسام بھی پیش کرتے ہیں، یعنی NO-WEAR EDM، WIRE EDM (WEDM)، EDM GRINDING (EDG)، DIE-SINKING EDM، الیکٹریکل-ڈسچارج، mcc78-Micro-DISCHARGEDM58-Micro -5cde-3194-bb3b-136bad5cf58d_and ELECTROCHEMICAL-DISCHARGE GRINDING (ECDG)۔ ہمارے EDM سسٹم سائز والے ٹولز/الیکٹروڈ اور ورک پیس پر مشتمل ہوتے ہیں جو DC پاور سپلائیز سے منسلک ہوتے ہیں اور برقی طور پر نان کنڈکٹنگ ڈائی الیکٹرک فلوڈ میں داخل ہوتے ہیں۔ 1940 کے بعد الیکٹریکل ڈسچارج مشینی مینوفیکچرنگ انڈسٹریز میں سب سے اہم اور مقبول پروڈکشن ٹیکنالوجی بن گئی ہے۔
جب دو الیکٹروڈ کے درمیان فاصلہ کم ہو جاتا ہے تو، الیکٹروڈ کے درمیان حجم میں برقی فیلڈ کی شدت کچھ پوائنٹس میں ڈائی الیکٹرک کی طاقت سے زیادہ ہو جاتی ہے، جو ٹوٹ جاتی ہے، اور آخر کار دو الیکٹروڈ کے درمیان کرنٹ کے بہاؤ کے لیے ایک پل بنتا ہے۔ ایک شدید برقی قوس پیدا ہوتا ہے جس کی وجہ سے ورک پیس کے ایک حصے اور ٹولنگ کے کچھ مواد کو پگھلنے کے لیے اہم حرارت ہوتی ہے۔ نتیجے کے طور پر، مواد دونوں الیکٹروڈ سے ہٹا دیا جاتا ہے. ایک ہی وقت میں، ڈائی الیکٹرک سیال تیزی سے گرم ہوتا ہے، جس کے نتیجے میں آرک گیپ میں مائع بخارات بن جاتا ہے۔ ایک بار جب موجودہ بہاؤ رک جاتا ہے یا اسے روک دیا جاتا ہے تو آس پاس کے ڈائی الیکٹرک سیال کے ذریعہ گیس کے بلبلے سے گرمی کو ہٹا دیا جاتا ہے اور بلبلہ کاویٹیٹس (گر جاتا ہے)۔ بلبلے کے گرنے اور ورک پیس کی سطح سے ڈائی الیکٹرک فلو فلش ملبے کے بہاؤ سے پیدا ہونے والی صدمے کی لہر اور کسی بھی پگھلے ہوئے ورک پیس کے مواد کو ڈائی الیکٹرک سیال میں داخل کرتی ہے۔ ان ڈسچارجز کے لیے تکرار کی شرح 50 سے 500 kHz، 50 سے 380 V کے درمیان وولٹیج اور 0.1 اور 500 Amperes کے درمیان کرنٹ ہیں۔ نئے مائع ڈائی الیکٹرک جیسے معدنی تیل، مٹی کا تیل یا ڈسٹلڈ اور ڈیونائزڈ پانی کو عام طور پر انٹر الیکٹروڈ والیوم میں پہنچایا جاتا ہے جو ٹھوس ذرات (ملبے کی شکل میں) کو لے جاتا ہے اور ڈائی الیکٹرک کی موصلیت کو بحال کیا جاتا ہے۔ کرنٹ کے بہاؤ کے بعد، دو الیکٹروڈز کے درمیان ممکنہ فرق اس طرح بحال ہو جاتا ہے جو ٹوٹنے سے پہلے تھا، اس لیے ایک نیا مائع ڈائی الیکٹرک خرابی واقع ہو سکتی ہے۔ ہماری جدید الیکٹریکل ڈسچارج مشینیں (EDM) عددی طور پر کنٹرول شدہ حرکات پیش کرتی ہیں اور ڈائی الیکٹرک سیالوں کے لیے پمپ اور فلٹرنگ سسٹم سے لیس ہیں۔
الیکٹریکل ڈسچارج مشیننگ (EDM) ایک مشینی طریقہ ہے جو بنیادی طور پر سخت دھاتوں کے لیے استعمال ہوتا ہے یا جو روایتی تکنیک کے ساتھ مشین بنانا بہت مشکل ہوتا ہے۔ EDM عام طور پر کسی بھی ایسے مواد کے ساتھ کام کرتا ہے جو برقی کنڈکٹر ہوتے ہیں، حالانکہ EDM کے ساتھ انسولیٹنگ سیرامکس کو مشینی بنانے کے طریقے بھی تجویز کیے گئے ہیں۔ پگھلنے کا نقطہ اور پگھلنے کی اویکت حرارت وہ خصوصیات ہیں جو ہر خارج ہونے والی دھات کے حجم کا تعین کرتی ہیں۔ یہ قدریں جتنی زیادہ ہوں گی، مواد کو ہٹانے کی شرح اتنی ہی کم ہوگی۔ چونکہ الیکٹریکل ڈسچارج مشینی عمل میں کوئی میکانکی توانائی شامل نہیں ہوتی ہے، اس لیے ورک پیس کی سختی، طاقت اور سختی ہٹانے کی شرح کو متاثر نہیں کرتی ہے۔ ڈسچارج فریکوئنسی یا توانائی فی ڈسچارج، وولٹیج اور کرنٹ مواد کو ہٹانے کی شرح کو کنٹرول کرنے کے لیے مختلف ہوتے ہیں۔ موجودہ کثافت میں اضافہ اور چنگاری کی فریکوئنسی میں کمی کے ساتھ مواد کو ہٹانے اور سطح کی کھردری کی شرح میں اضافہ ہوتا ہے۔ ہم EDM کا استعمال کرتے ہوئے پہلے سے سخت اسٹیل میں پیچیدہ شکلوں یا گہاوں کو نرم اور دوبارہ سخت کرنے کے لیے گرمی کے علاج کی ضرورت کے بغیر کاٹ سکتے ہیں۔ ہم اس طریقہ کو کسی بھی دھات یا دھات کے مرکب جیسے ٹائٹینیم، ہیسٹیلوئے، کوور اور انکونل کے ساتھ استعمال کر سکتے ہیں۔ EDM کے عمل کی درخواستوں میں پولی کرسٹل لائن ہیرے کے اوزار کی تشکیل شامل ہے۔ EDM کو ایک غیر روایتی یا غیر روایتی مشینی طریقہ سمجھا جاتا ہے جس کے ساتھ الیکٹرو کیمیکل مشیننگ (ECM)، واٹر جیٹ کٹنگ (WJ، AWJ)، لیزر کٹنگ جیسے عمل ہوتے ہیں۔ دوسری طرف روایتی مشینی طریقوں میں موڑ، گھسائی، پیسنے، ڈرلنگ اور دیگر عمل شامل ہیں جن کے مواد کو ہٹانے کا طریقہ کار بنیادی طور پر مکینیکل قوتوں پر مبنی ہے۔ الیکٹریکل ڈسچارج مشیننگ (EDM) کے لیے الیکٹروڈ گریفائٹ، پیتل، تانبے اور تانبے کے ٹنگسٹن مرکب سے بنے ہیں۔ الیکٹروڈ قطر 0.1 ملی میٹر تک ممکن ہے۔ چونکہ ٹول پہننا ایک ناپسندیدہ رجحان ہے جو EDM میں جہتی درستگی کو بری طرح متاثر کرتا ہے، اس لیے ہم پولرٹی کو ریورس کرکے اور تانبے کے ٹولز کا استعمال کرکے کم سے کم پہننے کے لیے NO-WEAR EDM نامی عمل کا فائدہ اٹھاتے ہیں۔
مثالی طور پر، الیکٹریکل ڈسچارج مشیننگ (EDM) کو الیکٹروڈ کے درمیان ڈائی الیکٹرک مائع کی خرابی اور بحالی کا ایک سلسلہ سمجھا جا سکتا ہے۔ تاہم حقیقت میں، انٹر الیکٹروڈ ایریا سے ملبے کو ہٹانا تقریباً ہمیشہ ہی جزوی ہوتا ہے۔ اس کی وجہ سے انٹر الیکٹروڈ ایریا میں ڈائی الیکٹرک کی برقی خصوصیات ان کی برائے نام قدروں سے مختلف ہوتی ہیں اور وقت کے ساتھ مختلف ہوتی ہیں۔ انٹر الیکٹروڈ فاصلہ، (spark-gap)، استعمال شدہ مخصوص مشین کے کنٹرول الگورتھم کے ذریعے ایڈجسٹ کیا جاتا ہے۔ EDM میں چنگاری کا فرق بدقسمتی سے بعض اوقات ملبے سے شارٹ سرکٹ ہو سکتا ہے۔ الیکٹروڈ کا کنٹرول سسٹم دو الیکٹروڈ (ٹول اور ورک پیس) کو شارٹ سرکٹنگ سے روکنے کے لیے کافی تیزی سے رد عمل ظاہر کرنے میں ناکام ہو سکتا ہے۔ یہ ناپسندیدہ شارٹ سرکٹ مثالی کیس سے مختلف طریقے سے مواد کو ہٹانے میں معاون ہے۔ ہم ڈائی الیکٹرک کی موصلیت کی خصوصیات کو بحال کرنے کے لیے فلشنگ ایکشن کو انتہائی اہمیت دیتے ہیں تاکہ کرنٹ ہمیشہ انٹر الیکٹروڈ ایریا کے نقطہ پر ہوتا رہے، اس طرح ٹول الیکٹروڈ کی شکل (نقصان) کی ناپسندیدہ تبدیلی کے امکان کو کم سے کم کیا جائے۔ اور workpiece. ایک مخصوص جیومیٹری حاصل کرنے کے لیے، EDM ٹول کو مطلوبہ راستے پر بغیر چھوئے ورک پیس کے بالکل قریب کی رہنمائی کی جاتی ہے، ہم استعمال میں موشن کنٹرول کی کارکردگی پر پوری توجہ دیتے ہیں۔ اس طرح، بڑی تعداد میں کرنٹ ڈسچارج/چنگاری ہوتی ہے، اور ہر ایک ٹول اور ورک پیس دونوں سے مواد کو ہٹانے میں حصہ ڈالتا ہے، جہاں چھوٹے گڑھے بنتے ہیں۔ کریٹرز کا سائز ہاتھ میں مخصوص کام کے لیے مقرر کردہ تکنیکی پیرامیٹرز کا ایک فنکشن ہے اور اس کے طول و عرض نانوسکل (جیسے مائیکرو-EDM آپریشنز کے معاملے میں) سے لے کر کھردری حالت میں کچھ سینکڑوں مائیکرو میٹرز تک ہو سکتے ہیں۔ آلے پر یہ چھوٹے گڑھے الیکٹروڈ کے بتدریج کٹاؤ کا باعث بنتے ہیں جسے "ٹول پہن" کہا جاتا ہے۔ ورک پیس کی جیومیٹری پر پہننے کے نقصان دہ اثر کو روکنے کے لیے ہم مشینی آپریشن کے دوران ٹول الیکٹروڈ کو مسلسل تبدیل کرتے رہتے ہیں۔ بعض اوقات ہم اسے الیکٹروڈ کے طور پر مسلسل تبدیل شدہ تار کا استعمال کرکے حاصل کرتے ہیں (اس EDM عمل کو WIRE EDM بھی کہا جاتا ہے)۔ بعض اوقات ہم ٹول الیکٹروڈ کو اس طرح استعمال کرتے ہیں کہ اس کا صرف ایک چھوٹا سا حصہ دراصل مشینی عمل میں مصروف رہتا ہے اور یہ حصہ مستقل بنیادوں پر تبدیل ہوتا رہتا ہے۔ یہ، مثال کے طور پر، ایک ٹول الیکٹروڈ کے طور پر گھومنے والی ڈسک کا استعمال کرتے وقت ہوتا ہے۔ اس عمل کو EDM GRINDING کہا جاتا ہے۔ پھر بھی ایک اور تکنیک جو ہم تعینات کرتے ہیں وہ پہننے کی تلافی کے لیے ایک ہی EDM آپریشن کے دوران مختلف سائز اور اشکال کے ساتھ الیکٹروڈز کا ایک سیٹ استعمال کرتی ہے۔ ہم اسے ایک سے زیادہ الیکٹروڈ تکنیک کہتے ہیں، اور عام طور پر اس وقت استعمال ہوتا ہے جب ٹول الیکٹروڈ منفی میں مطلوبہ شکل میں نقل کرتا ہے اور ایک سمت کے ساتھ خالی جگہ کی طرف بڑھا جاتا ہے، عام طور پر عمودی سمت (یعنی z-axis)۔ یہ ڈائی الیکٹرک مائع میں ٹول کے سنک سے مشابہت رکھتا ہے جس میں ورک پیس ڈوبی ہوئی ہے، اور اس وجہ سے اسے DIE-SINKING EDM_cc781905-5cbb6-31-315dtime_cc781905-5cde-31-31_cbd-31_55-5905-1905 کہا جاتا ہے۔ 3194-bb3b-136bad5cf58d_CONVENTIONAL EDM or_cc781905-5cde-3194-bb3b-136bad5cf58d)۔ اس آپریشن کے لیے مشینیں SINKER EDM کہلاتی ہیں۔ اس قسم کے EDM کے الیکٹروڈ کی پیچیدہ شکلیں ہوتی ہیں۔ اگر حتمی جیومیٹری کو عام طور پر سادہ شکل والے الیکٹروڈ کا استعمال کرتے ہوئے حاصل کیا جاتا ہے جو کئی سمتوں میں منتقل ہوتا ہے اور یہ گردش کے تابع بھی ہوتا ہے، تو ہم اسے EDM ملنگ کہتے ہیں۔ پہننے کی مقدار آپریشن میں استعمال ہونے والے تکنیکی پیرامیٹرز پر سختی سے منحصر ہے (پولرٹی، زیادہ سے زیادہ کرنٹ، اوپن سرکٹ وولٹیج)۔ مثال کے طور پر، in micro-EDM، جسے m-EDM کے نام سے بھی جانا جاتا ہے، یہ پیرامیٹرز عام طور پر شدید جین کی قدروں پر سیٹ ہوتے ہیں۔ لہذا، اس علاقے میں پہننا ایک بڑا مسئلہ ہے جسے ہم اپنی جمع معلومات کا استعمال کرتے ہوئے کم کرتے ہیں۔ مثال کے طور پر گریفائٹ الیکٹروڈ کے لباس کو کم سے کم کرنے کے لیے، ایک ڈیجیٹل جنریٹر، جو ملی سیکنڈ میں کنٹرول کیا جا سکتا ہے، الیکٹرو کٹاؤ کے ہونے پر قطبیت کو الٹ دیتا ہے۔ اس کے نتیجے میں الیکٹروپلٹنگ کی طرح اثر ہوتا ہے جو مسلسل گرے ہوئے گریفائٹ کو الیکٹروڈ پر واپس جمع کرتا ہے۔ ایک اور طریقہ میں، ایک نام نہاد ''زیرو وئیر'' سرکٹ ہم اسے کم سے کم کرتے ہیں کہ کتنی بار خارج ہوتا ہے اور کتنی بار رکتا ہے، اسے زیادہ سے زیادہ دیر تک جاری رکھتے ہیں۔ الیکٹریکل ڈسچارج مشینی میں مواد کو ہٹانے کی شرح کا اندازہ اس سے لگایا جا سکتا ہے:
MRR = 4 x 10 exp(4) x I x Tw exp (-1.23)
یہاں MRR mm3/min میں ہے، I Amperes میں کرنٹ ہے، Tw K-273.15K میں ورک پیس میلٹنگ پوائنٹ ہے۔ exp کا مطلب ہے exponent۔
دوسری طرف، الیکٹروڈ کے پہننے کی شرح Wt سے حاصل کی جا سکتی ہے:
Wt = ( 1.1 x 10exp(11) ) x I x Ttexp (-2.38)
یہاں Wt mm3/min میں ہے اور Tt K-273.15K میں الیکٹروڈ مواد کا میلٹنگ پوائنٹ ہے۔
آخر میں، ورک پیس کا الیکٹروڈ R سے پہننے کا تناسب اس سے حاصل کیا جا سکتا ہے:
R = 2.25 x Trex(-2.38)
یہاں Tr ورک پیس کے الیکٹروڈ کے پگھلنے والے پوائنٹس کا تناسب ہے۔
SINKER EDM :
سنکر ایڈم ، AS_CC781905-5CDE-3194-3194-BB3B-136BAD5CF58D_CAVITY کی قسم EDM_CC781905-1315B3194B36B36CF5CF58D_OR_C781905-58_C781905-58_C781905-58_C781905-58_C781905-58D_OR_CC7819058D_CC781915CFF5CFINGENTBINGED-13194B35CF5B31315CFINGTENGTENGTENGENTGENTINGTENGTENGTINGENTINGENT-LINGSTINGINTINGSTINGINTING الیکٹروڈ اور ورک پیس بجلی کی فراہمی سے جڑے ہوئے ہیں۔ بجلی کی فراہمی دونوں کے درمیان برقی صلاحیت پیدا کرتی ہے۔ جیسے ہی الیکٹروڈ ورک پیس کے قریب آتا ہے، سیال میں ڈائی الیکٹرک خرابی واقع ہوتی ہے، ایک پلازما چینل بنتا ہے، اور ایک چھوٹی چنگاری اچھل پڑتی ہے۔ چنگاری عام طور پر ایک وقت میں ایک ہی ٹکراتی ہے کیونکہ اس بات کا بہت زیادہ امکان نہیں ہے کہ انٹر الیکٹروڈ اسپیس میں مختلف مقامات پر ایک جیسی مقامی برقی خصوصیات ہوں جو ان تمام جگہوں پر بیک وقت چنگاری پیدا کرنے کے قابل بنائے۔ ان میں سے لاکھوں کی تعداد میں چنگاریاں الیکٹروڈ اور ورک پیس فی سیکنڈ کے درمیان بے ترتیب پوائنٹس پر ہوتی ہیں۔ جیسے جیسے بنیادی دھات ختم ہوتی ہے، اور چنگاری کا فرق بعد میں بڑھتا جاتا ہے، الیکٹروڈ کو ہماری CNC مشین کے ذریعے خود بخود کم کیا جاتا ہے تاکہ یہ عمل بلا تعطل جاری رہ سکے۔ ہمارے آلات میں کنٹرولنگ سائیکل ہیں جنہیں ''وقت پر'' اور ''آف ٹائم'' کہا جاتا ہے۔ وقت کی ترتیب چنگاری کی لمبائی یا مدت کا تعین کرتی ہے۔ زیادہ وقت اس چنگاری کے لیے ایک گہرا گہا پیدا کرتا ہے اور اس سائیکل کے لیے اس کے بعد آنے والی تمام چنگارییں، ورک پیس پر اور اس کے برعکس ایک کھردرا پن پیدا کرتی ہے۔ آف ٹائم اس وقت کی مدت ہے جس میں ایک چنگاری کو دوسری سے بدل دیا جاتا ہے۔ لمبا وقت ڈیالیکٹرک سیال کو نوزل کے ذریعے خارج ہونے والے ملبے کو صاف کرنے کی اجازت دیتا ہے، اس طرح شارٹ سرکٹ سے بچتا ہے۔ ان ترتیبات کو مائیکرو سیکنڈز میں ایڈجسٹ کیا جاتا ہے۔
WIRE EDM :
In WIRE ELECTRICAL DISCHARGE MACHINING (WEDM), also called WIRE-CUT EDM or WIRE CUTTING, we feed a ورک پیس کے ذریعے پیتل کی پتلی سنگل اسٹرینڈ دھاتی تار، جو ڈائی الیکٹرک سیال کے ٹینک میں ڈوبی ہوئی ہے۔ وائر EDM EDM کی ایک اہم تبدیلی ہے۔ ہم کبھی کبھار وائر کٹ EDM کا استعمال پلیٹوں کو 300 ملی میٹر تک موٹی کاٹنے اور سخت دھاتوں سے پنچ، ٹولز اور ڈیز بنانے کے لیے کرتے ہیں جو کہ دیگر مینوفیکچرنگ طریقوں سے مشین میں مشکل ہے۔ اس عمل میں جو ایک بینڈ آری کے ساتھ کونٹور کٹنگ سے مشابہت رکھتا ہے، تار، جو مسلسل سپول سے کھلایا جاتا ہے، اوپری اور نچلے ہیرے کے گائیڈ کے درمیان رکھا جاتا ہے۔ CNC کے زیر کنٹرول گائیڈز x–y جہاز میں حرکت کرتے ہیں اور اوپری گائیڈ بھی آزادانہ طور پر z–u–v محور میں حرکت کر سکتی ہے، جس سے ٹیپرڈ اور تبدیل ہونے والی شکلیں کاٹنے کی صلاحیت پیدا ہوتی ہے (جیسے نیچے کی طرف دائرہ اور مربع پر سب سے اوپر). اوپری گائیڈ x–y–u–v–i–j–k–l– میں محور کی حرکت کو کنٹرول کر سکتا ہے۔ یہ WEDM کو بہت پیچیدہ اور نازک شکلیں کاٹنے کی اجازت دیتا ہے۔ ہمارے سامان کی اوسط کٹنگ کیرف جو بہترین اقتصادی لاگت اور مشینی وقت حاصل کرتا ہے Ø 0.25 پیتل، تانبے یا ٹنگسٹن تار کا استعمال کرتے ہوئے 0.335 ملی میٹر ہے۔ تاہم ہمارے CNC آلات کے اوپری اور زیریں ڈائمنڈ گائیڈز تقریباً 0.004 ملی میٹر تک درست ہیں، اور Ø 0.02 ملی میٹر تار کا استعمال کرتے ہوئے کٹنگ پاتھ یا 0.021 ملی میٹر تک چھوٹا کرف ہو سکتا ہے۔ تو واقعی تنگ کٹوتیاں ممکن ہیں۔ کاٹنے کی چوڑائی تار کی چوڑائی سے زیادہ ہے کیونکہ اسپارکنگ تار کے اطراف سے ورک پیس تک ہوتی ہے، جس سے کٹاؤ ہوتا ہے۔ یہ ''اوور کٹ'' ضروری ہے، بہت سی ایپلی کیشنز کے لیے یہ قابل قیاس ہے اور اس لیے اس کی تلافی کی جا سکتی ہے (مائیکرو-ای ڈی ایم میں ایسا اکثر نہیں ہوتا ہے)۔ تار کے سپول لمبے ہوتے ہیں — 0.25 ملی میٹر تار کے 8 کلوگرام اسپول کی لمبائی صرف 19 کلومیٹر سے زیادہ ہوتی ہے۔ تار کا قطر 20 مائکرو میٹر جتنا چھوٹا ہو سکتا ہے اور جیومیٹری کی درستگی +/- 1 مائکرو میٹر کے پڑوس میں ہے۔ ہم عام طور پر تار کو صرف ایک بار استعمال کرتے ہیں اور اسے ری سائیکل کرتے ہیں کیونکہ یہ نسبتاً سستا ہے۔ یہ 0.15 سے 9m/min کی مستقل رفتار سے سفر کرتا ہے اور کٹ کے دوران ایک مستقل کرف (سلاٹ) برقرار رہتا ہے۔ وائر کٹ EDM کے عمل میں ہم پانی کو ڈائی الیکٹرک سیال کے طور پر استعمال کرتے ہیں، اس کی مزاحمتی صلاحیت اور دیگر برقی خصوصیات کو فلٹرز اور ڈی آئنائزر یونٹس کے ساتھ کنٹرول کرتے ہیں۔ پانی کٹے ہوئے ملبے کو کٹنگ زون سے دور کرتا ہے۔ کسی مواد کی موٹائی کے لیے فیڈ کی زیادہ سے زیادہ شرح کا تعین کرنے کے لیے فلشنگ ایک اہم عنصر ہے اور اس لیے ہم اسے مستقل رکھتے ہیں۔ تار EDM میں کاٹنے کی رفتار کو کراس سیکشنل ایریا کٹ فی یونٹ ٹائم کے لحاظ سے بتایا جاتا ہے، جیسے کہ 50 ملی میٹر موٹی D2 ٹول اسٹیل کے لیے 18,000 mm2/hr۔ اس کیس کے لیے لکیری کاٹنے کی رفتار 18,000/50 = 360mm/hr ہوگی تار EDM میں مواد کو ہٹانے کی شرح یہ ہے:
MRR = Vf xhxb
یہاں MRR mm3/min میں ہے، Vf mm/min میں ورک پیس میں تار کی فیڈ ریٹ ہے، h ملی میٹر میں موٹائی یا اونچائی ہے، اور b کیرف ہے، جو یہ ہے:
b = dw + 2s
یہاں dw تار کا قطر ہے اور s تار اور ورک پیس کے درمیان mm میں فرق ہے۔
سخت رواداری کے ساتھ ساتھ، ہمارے جدید ملٹی ایکسس EDM وائر کٹنگ مشینی مراکز نے ایک ہی وقت میں دو حصوں کو کاٹنے کے لیے ملٹی ہیڈز، تار ٹوٹنے سے روکنے کے لیے کنٹرول، تار ٹوٹنے کی صورت میں خودکار سیلف تھریڈنگ کی خصوصیات، اور پروگرام شدہ خصوصیات شامل کی ہیں۔ آپریشن، سیدھے اور کونیی کاٹنے کی صلاحیتوں کو بہتر بنانے کے لیے مشینی حکمت عملی۔
وائر-EDM ہمیں کم بقایا دباؤ پیش کرتا ہے، کیونکہ اسے مواد کو ہٹانے کے لیے زیادہ کاٹنے والی قوتوں کی ضرورت نہیں ہوتی ہے۔ جب فی نبض کی توانائی/طاقت نسبتاً کم ہوتی ہے (جیسا کہ فنشنگ آپریشنز میں)، کم بقایا دباؤ کی وجہ سے کسی مواد کی مکینیکل خصوصیات میں بہت کم تبدیلی متوقع ہے۔
الیکٹریکل ڈسچارج پیسنے (EDG) : پیسنے والے پہیوں میں ابراسیوز نہیں ہوتے ہیں، وہ گریفائٹ یا پیتل سے بنے ہوتے ہیں۔ گھومنے والے پہیے اور ورک پیس کے درمیان بار بار آنے والی چنگاریاں ورک پیس کی سطحوں سے مواد کو ہٹا دیتی ہیں۔ مواد کو ہٹانے کی شرح ہے:
MRR = K x I
یہاں MRR mm3/min میں ہے، I Amperes میں کرنٹ ہے، اور K mm3/A-min میں ورک پیس میٹریل فیکٹر ہے۔ ہم اجزاء پر تنگ دھاروں کو دیکھنے کے لیے اکثر الیکٹریکل ڈسچارج پیسنے کا استعمال کرتے ہیں۔ ہم کبھی کبھی EDG (الیکٹریکل ڈسچارج پیسنے) کے عمل کو ECG (الیکٹرو کیمیکل پیسنے) کے عمل کے ساتھ جوڑ دیتے ہیں جہاں مواد کو کیمیائی عمل کے ذریعے ہٹا دیا جاتا ہے، گریفائٹ وہیل سے برقی مادہ آکسائیڈ فلم کو توڑ کر الیکٹرولائٹ کے ذریعے دھل جاتا ہے۔ اس عمل کو ELECTROCHEMICAL-DISCHARGE GRINDING (ECDG) کہا جاتا ہے۔ اگرچہ ECDG عمل نسبتاً زیادہ طاقت استعمال کرتا ہے، یہ EDG کے مقابلے میں تیز تر عمل ہے۔ ہم اس تکنیک کا استعمال کرتے ہوئے زیادہ تر کاربائیڈ ٹولز کو پیستے ہیں۔
الیکٹریکل ڈسچارج مشین کی درخواستیں:
پروٹوٹائپ کی پیداوار:
ہم EDM کے عمل کو مولڈ بنانے، ٹول اور ڈائی مینوفیکچرنگ کے ساتھ ساتھ پروٹوٹائپ اور پروڈکشن پارٹس بنانے کے لیے استعمال کرتے ہیں، خاص طور پر ایرو اسپیس، آٹوموبائل اور الیکٹرانکس کی صنعتوں کے لیے جن میں پیداوار کی مقدار نسبتاً کم ہے۔ سنکر EDM میں، ایک گریفائٹ، کاپر ٹنگسٹن یا خالص تانبے کے الیکٹروڈ کو مطلوبہ (منفی) شکل میں مشین بنایا جاتا ہے اور عمودی رام کے آخر میں ورک پیس میں کھلایا جاتا ہے۔
سکوں کی مرغی بنانا:
کوائنج (سٹیمپنگ) کے عمل سے زیورات اور بیج تیار کرنے کے لیے ڈیز کی تخلیق کے لیے، مثبت ماسٹر سٹرلنگ سلور سے بنایا جا سکتا ہے، کیونکہ (مناسب مشین سیٹنگ کے ساتھ) ماسٹر نمایاں طور پر ختم ہو جاتا ہے اور اسے صرف ایک بار استعمال کیا جاتا ہے۔ نتیجے میں آنے والی نیگیٹو ڈائی کو پھر سخت کیا جاتا ہے اور ڈراپ ہتھوڑے میں استعمال کیا جاتا ہے تاکہ کانسی، چاندی یا کم پروف سونے کے مرکب کے کٹ آؤٹ شیٹ خالی جگہوں سے سٹیمپڈ فلیٹ تیار کیے جا سکیں۔ بیجز کے لیے ان فلیٹوں کو ایک اور ڈائی کے ذریعے ایک خمیدہ سطح پر مزید شکل دی جا سکتی ہے۔ اس قسم کا EDM عام طور پر تیل پر مبنی ڈائی الیکٹرک میں ڈوب کر کیا جاتا ہے۔ تیار شدہ چیز کو سخت (شیشہ) یا نرم (پینٹ) انامیلنگ اور/یا خالص سونے یا نکل سے الیکٹروپلیٹ کے ذریعے مزید بہتر کیا جا سکتا ہے۔ نرم مواد جیسے چاندی کو ایک تطہیر کے طور پر ہاتھ سے کندہ کیا جا سکتا ہے۔
چھوٹے سوراخوں کی کھدائی:
ہماری وائر کٹ EDM مشینوں پر، ہم چھوٹے سوراخوں کی ڈرلنگ EDM کا استعمال کرتے ہیں تاکہ ایک ورک پیس میں تھرو ہول بنایا جا سکے جس کے ذریعے وائر کٹ EDM آپریشن کے لیے تار کو تھریڈ کیا جائے۔ ہماری وائر کٹ مشینوں پر چھوٹے سوراخوں کی ڈرلنگ کے لیے علیحدہ EDM ہیڈز لگائے گئے ہیں جو بڑی سخت پلیٹوں کو ضرورت کے مطابق اور پری ڈرلنگ کے بغیر ان سے تیار شدہ پرزوں کو ختم کرنے کی اجازت دیتے ہیں۔ ہم جیٹ انجنوں میں استعمال ہونے والے ٹربائن بلیڈ کے کناروں میں سوراخوں کی قطاروں کو ڈرل کرنے کے لیے چھوٹے سوراخ والے EDM کا بھی استعمال کرتے ہیں۔ ان چھوٹے سوراخوں سے گیس کا بہاؤ انجنوں کو دوسری صورت میں ممکن سے زیادہ درجہ حرارت استعمال کرنے کی اجازت دیتا ہے۔ اعلی درجہ حرارت، انتہائی سخت، سنگل کرسٹل مرکب سے بنے ہوئے یہ بلیڈ ان سوراخوں کی روایتی مشینی اعلیٰ تناسب کے ساتھ انتہائی مشکل اور ناممکن بنا دیتے ہیں۔ چھوٹے سوراخ والے EDM کے لیے دیگر ایپلی کیشن ایریاز ایندھن کے نظام کے اجزاء کے لیے خوردبینی سوراخ بنانا ہے۔ مربوط EDM ہیڈز کے علاوہ، ہم اسٹینڈ اکیلے چھوٹے سوراخوں کی سوراخ کرنے والی EDM مشینوں کو x–y محور کے ساتھ مشین بلائنڈ یا سوراخوں کے ذریعے تعینات کرتے ہیں۔ EDM ڈرلز میں ایک لمبے پیتل یا تانبے کی ٹیوب الیکٹروڈ کے ساتھ سوراخ ہوتے ہیں جو ایک چک میں گھومتا ہے جس میں الیکٹروڈ کے ذریعے فلشنگ ایجنٹ اور ڈائی الیکٹرک کے طور پر الیکٹروڈ کے ذریعے بہنے والے ڈسٹل یا ڈیونائزڈ پانی کا مسلسل بہاؤ ہوتا ہے۔ کچھ چھوٹے سوراخ کرنے والی EDMs 10 سیکنڈ سے بھی کم وقت میں 100 ملی میٹر نرم یا سخت سٹیل کے ذریعے ڈرل کرنے کے قابل ہوتے ہیں۔ اس ڈرلنگ آپریشن میں 0.3 ملی میٹر اور 6.1 ملی میٹر کے درمیان سوراخ حاصل کیے جا سکتے ہیں۔
دھاتی ٹوٹ پھوٹ کی مشین:
ہمارے پاس کام کے ٹکڑوں سے ٹوٹے ہوئے اوزار (ڈرل بٹس یا نلکوں) کو ہٹانے کے مخصوص مقصد کے لیے خصوصی EDM مشینیں بھی ہیں۔ اس عمل کو '' دھاتی ڈسائنٹیگریشن مشیننگ '' کہا جاتا ہے۔
الیکٹریکل ڈسچارج مشیننگ کے فوائد اور نقصانات:
EDM کے فوائد میں مشینی شامل ہیں:
- پیچیدہ شکلیں جو دوسری صورت میں روایتی کاٹنے والے اوزار کے ساتھ پیدا کرنا مشکل ہو گا۔
- انتہائی سخت مواد سے بہت قریب رواداری
- بہت چھوٹے کام کے ٹکڑے جہاں روایتی کاٹنے والے اوزار زیادہ کاٹنے والے آلے کے دباؤ سے حصے کو نقصان پہنچا سکتے ہیں۔
- ٹول اور ورک پیس کے درمیان کوئی براہ راست رابطہ نہیں ہے۔ لہذا نازک حصوں اور کمزور مواد کو بغیر کسی مسخ کے مشینی بنایا جا سکتا ہے۔
- ایک اچھی سطح ختم حاصل کی جا سکتی ہے.
- بہت باریک سوراخ آسانی سے ڈرل کیے جا سکتے ہیں۔
EDM کے نقصانات میں شامل ہیں:
- مواد کو ہٹانے کی سست رفتار۔
- رام/سنکر EDM کے لیے الیکٹروڈ بنانے کے لیے استعمال ہونے والا اضافی وقت اور لاگت۔
- الیکٹروڈ پہننے کی وجہ سے ورک پیس پر تیز کونوں کو دوبارہ بنانا مشکل ہے۔
- بجلی کی کھپت زیادہ ہے۔
- ''اوور کٹ'' بنتا ہے۔
- مشینی کے دوران ضرورت سے زیادہ ٹول پہننا ہوتا ہے۔
- برقی طور پر نان کنڈکٹیو مواد کو صرف عمل کے مخصوص سیٹ اپ کے ساتھ مشینی کیا جا سکتا ہے۔