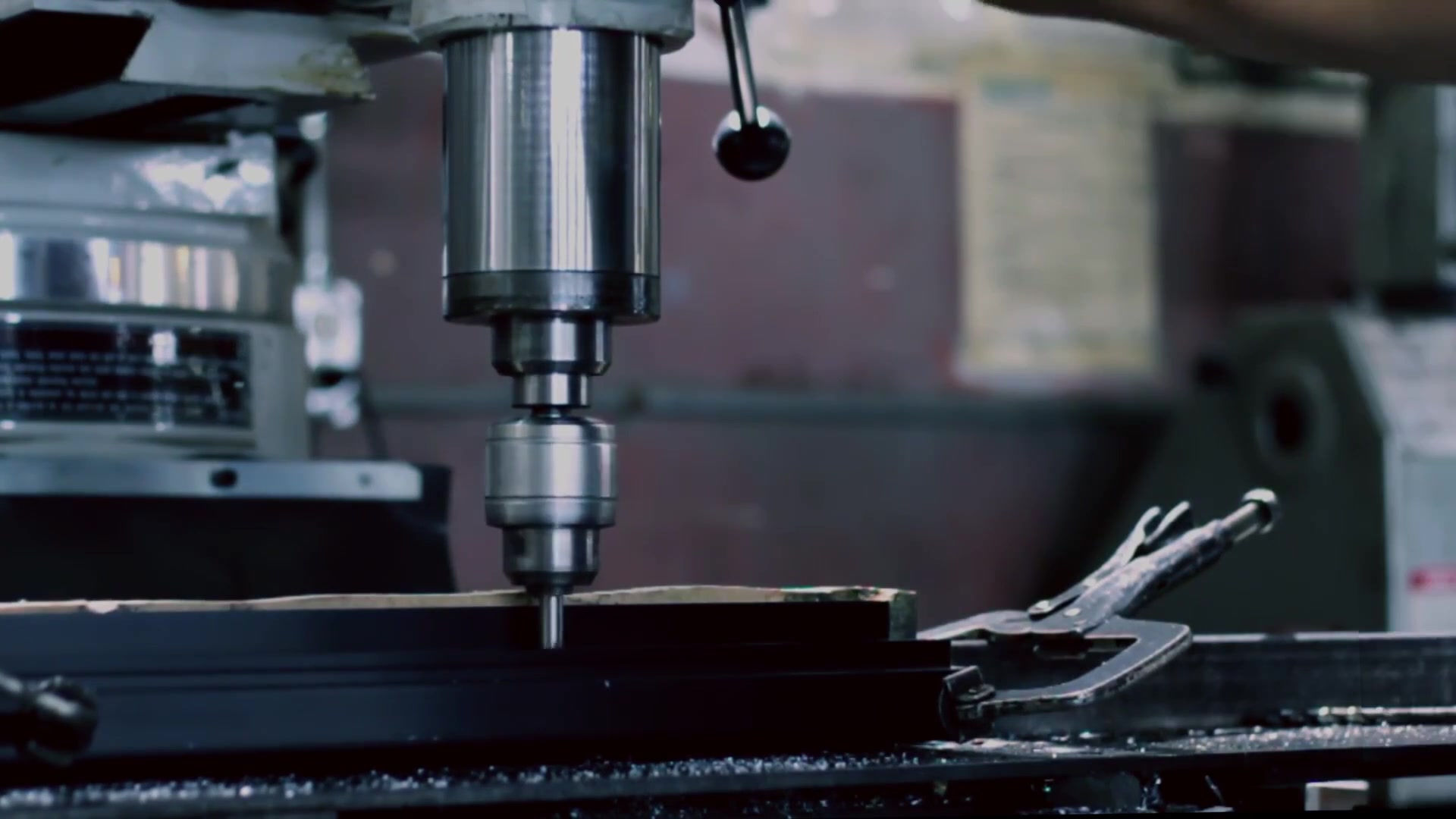
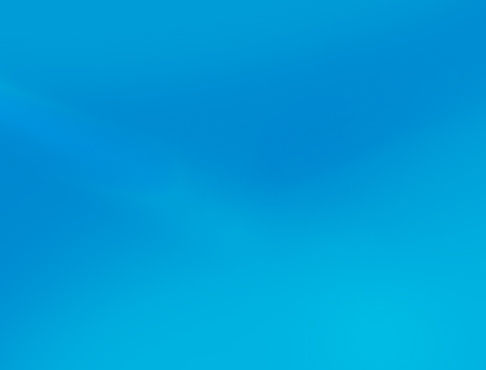
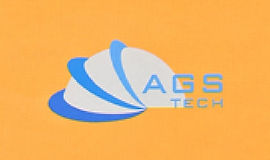
عالمی کسٹم مینوفیکچرر، انٹیگریٹر، کنسولیڈیٹر، مصنوعات اور خدمات کی وسیع اقسام کے لیے آؤٹ سورسنگ پارٹنر۔
ہم مینوفیکچرنگ، فیبریکیشن، انجینئرنگ، کنسولیڈیشن، انٹیگریشن، اپنی مرضی کے مطابق تیار کردہ اور آف شیلف پروڈکٹس اور خدمات کی آؤٹ سورسنگ کے لیے آپ کا واحد ذریعہ ہیں۔
Choose your Language
-
اپنی مرضی کے مطابق مینوفیکچرنگ
-
گھریلو اور عالمی کنٹریکٹ مینوفیکچرنگ
-
مینوفیکچرنگ آؤٹ سورسنگ
-
گھریلو اور عالمی خریداری
-
Consolidation
-
انجینئرنگ انٹیگریشن
-
انجینئرنگ سروسز
Search Results
164 results found with an empty search
- Rapid Prototyping, Desktop Manufacturing, Additive Manufacturing, FDM
Rapid Prototyping, Desktop Manufacturing, Additive Manufacturing, Stereolithography, Polyjet, Fused Deposition Modeling, Selective Laser Sintering, FDM, SLS اضافی اور تیز رفتار مینوفیکچرنگ حالیہ برسوں میں، ہم نے RAPID MANUFACTURING یا RAPID PROTOTYPING کی مانگ میں اضافہ دیکھا ہے۔ اس عمل کو ڈیسک ٹاپ مینوفیکچرنگ یا فری فارم فیبریکیشن بھی کہا جا سکتا ہے۔ بنیادی طور پر کسی حصے کا ٹھوس جسمانی ماڈل براہ راست تین جہتی CAD ڈرائنگ سے بنایا جاتا ہے۔ ہم ان مختلف تکنیکوں کے لیے ADDITIVE MANUFACTURING کی اصطلاح استعمال کرتے ہیں جہاں ہم تہوں میں پرزے بناتے ہیں۔ مربوط کمپیوٹر سے چلنے والے ہارڈویئر اور سافٹ ویئر کا استعمال کرتے ہوئے ہم اضافی مینوفیکچرنگ انجام دیتے ہیں۔ ہماری تیز رفتار پروٹو ٹائپنگ اور مینوفیکچرنگ کی تکنیکیں ہیں سٹیریو لیتھوگرافی، پولی جیٹ، فیوزڈ ڈیپوزیشن ماڈلنگ، سلیکٹیو لیزر سنٹرنگ، الیکٹران بیم میلٹنگ، تھری ڈائیمنشنل پرنٹنگ، ڈائریکٹ مینوفیکچرنگ، ریپنگ۔ ہمارا مشورہ ہے کہ آپ یہاں کلک کریں۔AGS-TECH Inc. کی طرف سے اضافی مینوفیکچرنگ اور تیز رفتار مینوفیکچرنگ کے عمل کی ہماری اسکیمیٹک عکاسی ڈاؤن لوڈ کریں۔ اس سے آپ کو ان معلومات کو بہتر طریقے سے سمجھنے میں مدد ملے گی جو ہم آپ کو ذیل میں فراہم کر رہے ہیں۔ ریپڈ پروٹو ٹائپنگ ہمیں فراہم کرتی ہے: 1.) تصوراتی مصنوعات کے ڈیزائن کو 3D/CAD سسٹم کا استعمال کرتے ہوئے مانیٹر پر مختلف زاویوں سے دیکھا جاتا ہے۔ 2.) غیر دھاتی اور دھاتی مواد سے پروٹوٹائپس تیار کی جاتی ہیں اور فنکشنل، تکنیکی اور جمالیاتی پہلوؤں سے مطالعہ کی جاتی ہیں۔ 3.) بہت کم وقت میں کم لاگت کی پروٹو ٹائپنگ مکمل ہو جاتی ہے۔ اضافی مینوفیکچرنگ کو ایک دوسرے کے اوپر انفرادی ٹکڑوں کو اسٹیک کرکے اور جوڑ کر روٹی کی روٹی کی تعمیر سے مشابہ کیا جاسکتا ہے۔ دوسرے لفظوں میں، پراڈکٹ کو سلائس کے ذریعے تیار کیا جاتا ہے، یا ایک دوسرے پر پرت کے ذریعے جمع کیا جاتا ہے۔ زیادہ تر حصے گھنٹوں میں تیار کیے جا سکتے ہیں۔ تکنیک اچھی ہے اگر پرزوں کی بہت جلد ضرورت ہو یا اگر ضرورت کی مقدار کم ہو اور مولڈ اور ٹولنگ بنانا بہت مہنگا اور وقت لگتا ہے۔ تاہم ایک حصے کی قیمت مہنگی خام مال کی وجہ سے مہنگی ہے۔ • سٹیریو لیتھوگرافی: اس تکنیک کو STL بھی کہا جاتا ہے، ایک لیزر بیم کو فوکس کر کے مائع فوٹو پولیمر کو ایک مخصوص شکل میں ٹھیک کرنے اور سخت کرنے پر مبنی ہے۔ لیزر فوٹو پولیمر کو پولیمرائز کرتا ہے اور اسے ٹھیک کرتا ہے۔ فوٹو پولیمر مکسچر کی سطح کے ساتھ پروگرام شدہ شکل کے مطابق یووی لیزر بیم کو اسکین کرنے سے یہ حصہ نیچے سے اوپر کی طرف سے انفرادی سلائسوں میں ایک دوسرے کے اوپر کاسکیڈ ہوتا ہے۔ لیزر اسپاٹ کی سکیننگ سسٹم میں پروگرام شدہ جیومیٹریوں کو حاصل کرنے کے لیے کئی بار دہرائی جاتی ہے۔ حصہ مکمل طور پر تیار ہونے کے بعد، اسے پلیٹ فارم سے ہٹا دیا جاتا ہے، الٹراسونک طریقے سے اور الکحل غسل کے ساتھ داغدار اور صاف کیا جاتا ہے۔ اس کے بعد، پولیمر مکمل طور پر ٹھیک اور سخت ہو گیا ہے اس بات کو یقینی بنانے کے لیے اسے چند گھنٹوں کے لیے UV شعاع ریزی کے سامنے رکھا جاتا ہے۔ اس عمل کا خلاصہ کرنے کے لیے، ایک پلیٹ فارم جسے فوٹو پولیمر مکسچر میں ڈبویا جاتا ہے اور یووی لیزر بیم کو مطلوبہ حصے کی شکل کے مطابق سروو کنٹرول سسٹم کے ذریعے کنٹرول اور منتقل کیا جاتا ہے اور اس حصے کو پولیمر کی تہہ کو تہہ در تہہ فوٹوکور کرکے حاصل کیا جاتا ہے۔ یقیناً تیار کردہ حصے کے زیادہ سے زیادہ جہت کا تعین سٹیریو لیتھوگرافی کے آلات سے کیا جاتا ہے۔ • پولی جیٹ : انک جیٹ پرنٹنگ کی طرح، پولی جیٹ میں ہمارے پاس آٹھ پرنٹ ہیڈز ہیں جو فوٹو پولیمر کو بلڈ ٹرے پر جمع کرتے ہیں۔ جیٹ طیاروں کے ساتھ رکھی ہوئی الٹرا وائلٹ روشنی ہر تہہ کو فوری طور پر ٹھیک اور سخت کرتی ہے۔ پولی جیٹ میں دو مواد استعمال ہوتے ہیں۔ پہلا مواد اصل ماڈل کی تیاری کے لیے ہے۔ دوسرا مواد، ایک جیل کی طرح رال حمایت کے لئے استعمال کیا جاتا ہے. یہ دونوں مواد تہہ در تہہ جمع ہوتے ہیں اور بیک وقت ٹھیک ہو جاتے ہیں۔ ماڈل کی تکمیل کے بعد، امدادی مواد کو پانی کے محلول سے ہٹا دیا جاتا ہے۔ استعمال شدہ رال سٹیریو لیتھوگرافی (STL) سے ملتی جلتی ہے۔ پولی جیٹ کے سٹیریو لیتھوگرافی پر درج ذیل فوائد ہیں: 1.) حصوں کی صفائی کی ضرورت نہیں۔ 2.) پوسٹ پروسیس کیورنگ کی ضرورت نہیں 3.) چھوٹی پرت کی موٹائی ممکن ہے اور اس طرح ہم بہتر ریزولوشن حاصل کرتے ہیں اور باریک پرزے تیار کر سکتے ہیں۔ • فیوزڈ ڈیپوزیشن ماڈلنگ: اسے مختصراً FDM بھی کہا جاتا ہے، اس طریقے میں ایک روبوٹ کے زیر کنٹرول ایکسٹروڈر ہیڈ میز پر دو اصولی سمتوں میں حرکت کرتا ہے۔ ضرورت کے مطابق کیبل کو نیچے اور اٹھایا جاتا ہے۔ سر پر گرم مرے کے سوراخ سے، تھرمو پلاسٹک فلیمینٹ نکالا جاتا ہے اور ابتدائی تہہ کو فوم فاؤنڈیشن پر جمع کیا جاتا ہے۔ یہ ایکسٹروڈر ہیڈ کے ذریعہ پورا ہوتا ہے جو پہلے سے طے شدہ راستے پر چلتا ہے۔ ابتدائی پرت کے بعد، میز کو نیچے کیا جاتا ہے اور بعد میں تہوں کو ایک دوسرے کے اوپر جمع کیا جاتا ہے. بعض اوقات جب کسی پیچیدہ حصے کو تیار کرتے ہیں، تو معاون ڈھانچے کی ضرورت ہوتی ہے تاکہ جمع مخصوص سمتوں میں جاری رہ سکے۔ ان صورتوں میں، ایک سپورٹ میٹریل کو تہہ پر کم گھنے فاصلہ کے ساتھ نکالا جاتا ہے تاکہ یہ ماڈل میٹریل سے کمزور ہو۔ یہ سپورٹ ڈھانچہ بعد میں حصہ کی تکمیل کے بعد تحلیل یا ٹوٹ سکتا ہے۔ ایکسٹروڈر ڈائی ڈائمینشنز باہر نکالی گئی پرتوں کی موٹائی کا تعین کرتے ہیں۔ FDM عمل ترچھے بیرونی طیاروں پر قدموں والی سطحوں کے ساتھ حصے تیار کرتا ہے۔ اگر یہ کھردرا پن ناقابل قبول ہے تو ان کو ہموار کرنے کے لیے کیمیائی بخارات پالش یا گرم آلے کا استعمال کیا جا سکتا ہے۔ یہاں تک کہ ان مراحل کو ختم کرنے اور معقول جیومیٹرک رواداری حاصل کرنے کے لیے ایک کوٹنگ مواد کے طور پر پالش کرنے والا موم بھی دستیاب ہے۔ • سلیکٹیو لیزر sintering: SLS کے طور پر بھی بیان کیا جاتا ہے، یہ عمل پولیمر، سیرامک یا دھاتی پاؤڈر کو منتخب طور پر کسی چیز میں ڈالنے پر مبنی ہوتا ہے۔ پروسیسنگ چیمبر کے نچلے حصے میں دو سلنڈر ہیں: ایک پارٹ بلڈ سلنڈر اور ایک پاؤڈر فیڈ سلنڈر۔ پہلے والے حصے کو بتدریج نیچے کیا جاتا ہے جہاں سنٹرڈ حصہ بن رہا ہوتا ہے اور بعد والے حصے کو رولر میکانزم کے ذریعے پارٹ بلڈ سلنڈر کو پاؤڈر کی فراہمی کے لیے بتدریج بڑھایا جاتا ہے۔ سب سے پہلے پاؤڈر کی ایک پتلی پرت کو پارٹ بلڈ سلنڈر میں جمع کیا جاتا ہے، پھر ایک لیزر بیم اس پرت پر مرکوز کی جاتی ہے، ایک خاص کراس سیکشن کو ٹریسنگ اور پگھلنا/سنٹر کرنا، جو پھر ٹھوس میں تبدیل ہو جاتا ہے۔ پاؤڈر وہ جگہیں ہیں جو لیزر بیم سے متاثر نہیں ہوتے ہیں لیکن پھر بھی ٹھوس حصے کو سہارا دیتے ہیں۔ پھر پاؤڈر کی ایک اور تہہ جمع کی جاتی ہے اور اس عمل کو کئی بار دہرایا جاتا ہے تاکہ حصہ حاصل کیا جا سکے۔ آخر میں، ڈھیلے پاؤڈر کے ذرات کو ہلا دیا جاتا ہے. یہ سب ایک پروسیس کنٹرول کمپیوٹر کے ذریعے تیار کیے جانے والے حصے کے 3D CAD پروگرام کے ذریعے تیار کردہ ہدایات کا استعمال کرتے ہوئے کیے جاتے ہیں۔ مختلف مواد جیسے پولیمر (جیسے ABS، PVC، پالئیےسٹر)، موم، دھاتیں اور سیرامکس مناسب پولیمر بائنڈر کے ساتھ جمع کیے جا سکتے ہیں۔ • ELECTRON-BEAM MELTING : سلیکٹیو لیزر سنٹرنگ کی طرح، لیکن ویکیوم میں پروٹو ٹائپ بنانے کے لیے ٹائٹینیم یا کوبالٹ کروم پاؤڈر کو پگھلانے کے لیے الیکٹران بیم کا استعمال۔ سٹینلیس سٹیل، ایلومینیم اور تانبے کے مرکب پر اس عمل کو انجام دینے کے لیے کچھ پیش رفت کی گئی ہے۔ اگر تیار کردہ حصوں کی تھکاوٹ کی طاقت کو بڑھانے کی ضرورت ہے، تو ہم ایک ثانوی عمل کے طور پر حصے کی تیاری کے بعد گرم آئسوسٹیٹک دبانے کا استعمال کرتے ہیں۔ • تین جہتی پرنٹنگ: 3DP سے بھی ظاہر ہوتا ہے، اس تکنیک میں پرنٹ ہیڈ ایک غیر نامیاتی بائنڈر کو غیر دھاتی یا دھاتی پاؤڈر کی تہہ پر جمع کرتا ہے۔ پاؤڈر بیڈ لے جانے والے پسٹن کو بتدریج نیچے کیا جاتا ہے اور ہر قدم پر بائنڈر کو layer بہ تہہ جمع کیا جاتا ہے اور بائنڈر کے ذریعے فیوز کیا جاتا ہے۔ استعمال شدہ پاؤڈر مواد پولیمر مرکبات اور ریشے، فاؤنڈری ریت، دھاتیں ہیں۔ بیک وقت مختلف بائنڈر ہیڈز اور مختلف کلر بائنڈر کا استعمال کرتے ہوئے ہم مختلف رنگ حاصل کر سکتے ہیں۔ یہ عمل انک جیٹ پرنٹنگ کی طرح ہے لیکن رنگین شیٹ حاصل کرنے کے بجائے ہم رنگین تین جہتی چیز حاصل کرتے ہیں۔ تیار کردہ حصے غیر محفوظ ہو سکتے ہیں اور اس وجہ سے اس کی کثافت اور طاقت کو بڑھانے کے لیے ان میں sintering اور دھات کی دراندازی کی ضرورت پڑ سکتی ہے۔ سینٹرنگ بائنڈر کو جلا دے گی اور دھاتی پاؤڈر کو ایک ساتھ فیوز کر دے گی۔ دھاتیں جیسے سٹینلیس سٹیل، ایلومینیم، ٹائٹینیم کا استعمال حصوں کو بنانے کے لیے کیا جا سکتا ہے اور دراندازی کے مواد کے طور پر ہم عام طور پر تانبے اور کانسی کا استعمال کرتے ہیں۔ اس تکنیک کی خوبصورتی یہ ہے کہ پیچیدہ اور حرکت پذیر اسمبلیاں بھی بہت جلد تیار کی جا سکتی ہیں۔ مثال کے طور پر گیئر اسمبلی، رینچ بطور ٹول بنایا جا سکتا ہے اور اس میں حرکت پذیر اور موڑنے والے پرزے استعمال کے لیے تیار ہوں گے۔ اسمبلی کے مختلف اجزاء مختلف رنگوں کے ساتھ تیار کیے جا سکتے ہیں اور سب ایک ہی شاٹ میں۔ ہمارا بروشر ڈاؤن لوڈ کریں:دھاتی 3D پرنٹنگ کی بنیادی باتیں • ڈائریکٹ مینوفیکچرنگ اور ریپڈ ٹولنگ: ڈیزائن کی تشخیص کے علاوہ، ٹربل شوٹنگ ہم مصنوعات کی براہ راست تیاری یا مصنوعات میں براہ راست اطلاق کے لیے تیز رفتار پروٹو ٹائپنگ کا استعمال کرتے ہیں۔ دوسرے الفاظ میں، تیز رفتار پروٹو ٹائپنگ کو روایتی عمل میں شامل کیا جا سکتا ہے تاکہ انہیں بہتر اور زیادہ مسابقتی بنایا جا سکے۔ مثال کے طور پر، تیز رفتار پروٹو ٹائپنگ پیٹرن اور سانچوں کو تیار کر سکتی ہے۔ تیزی سے پروٹو ٹائپنگ آپریشنز کے ذریعے پگھلنے اور جلنے والے پولیمر کے نمونوں کو سرمایہ کاری کے لیے جمع کیا جا سکتا ہے اور سرمایہ کاری کی جا سکتی ہے۔ ذکر کرنے کے لئے ایک اور مثال سیرامک کاسٹنگ شیل تیار کرنے کے لئے 3DP کا استعمال کرنا ہے اور اسے شیل کاسٹنگ آپریشنز کے لئے استعمال کرنا ہے۔ یہاں تک کہ انجیکشن مولڈز اور مولڈ انسرٹس بھی تیز رفتار پروٹو ٹائپنگ کے ذریعے تیار کیے جا سکتے ہیں اور مولڈ بنانے میں کئی ہفتوں یا مہینوں کی بچت ہو سکتی ہے۔ صرف مطلوبہ حصے کی CAD فائل کا تجزیہ کرکے، ہم سافٹ ویئر کا استعمال کرتے ہوئے ٹول جیومیٹری تیار کر سکتے ہیں۔ ہمارے تیز رفتار ٹولنگ کے کچھ طریقے یہ ہیں: آر ٹی وی (کمرے کا درجہ حرارت ولکنائزنگ) مولڈنگ / یوریتھین کاسٹنگ: تیز رفتار پروٹو ٹائپنگ کا استعمال کرتے ہوئے مطلوبہ حصے کا نمونہ بنایا جا سکتا ہے۔ پھر اس پیٹرن کو الگ کرنے والے ایجنٹ کے ساتھ لیپت کیا جاتا ہے اور مائع RTV ربڑ کو پیٹرن کے اوپر ڈالا جاتا ہے تاکہ مولڈ کے حصوں کو تیار کیا جاسکے۔ اگلا، یہ مولڈ آدھے حصے کو مولڈ مائع یوریتھین انجیکشن کرنے کے لیے استعمال کیا جاتا ہے۔ مولڈ کی زندگی مختصر ہے، صرف 0 یا 30 سائیکلوں کی طرح لیکن چھوٹے بیچ کی پیداوار کے لیے کافی ہے۔ ACES (Acetal Clear Epoxy Solid) انجیکشن مولڈنگ: تیز رفتار پروٹو ٹائپنگ تکنیک جیسے سٹیریو لیتھوگرافی کا استعمال کرتے ہوئے، ہم انجیکشن مولڈ تیار کرتے ہیں۔ یہ مولڈ کھلے سرے والے خول ہوتے ہیں جو ایپوکسی، ایلومینیم سے بھرے ایپوکسی یا دھاتوں جیسے مواد سے بھرنے کی اجازت دیتے ہیں۔ ایک بار پھر مولڈ لائف دسیوں یا زیادہ سے زیادہ سینکڑوں حصوں تک محدود ہے۔ اسپرےڈ میٹل ٹولنگ کا عمل: ہم تیز رفتار پروٹو ٹائپنگ کا استعمال کرتے ہیں اور ایک پیٹرن بناتے ہیں۔ ہم پیٹرن کی سطح پر زنک-ایلومینیم مرکب چھڑکتے ہیں اور اسے کوٹ دیتے ہیں۔ دھات کی کوٹنگ کے ساتھ پیٹرن کو پھر ایک فلاسک کے اندر رکھا جاتا ہے اور اسے ایپوکسی یا ایلومینیم سے بھرے ایپوکسی کے ساتھ برتن میں رکھا جاتا ہے۔ آخر میں، اسے ہٹا دیا جاتا ہے اور اس طرح کے دو مولڈ آدھے حصے بنا کر ہم انجیکشن مولڈنگ کے لیے ایک مکمل مولڈ حاصل کرتے ہیں۔ یہ سانچوں کی عمر لمبی ہوتی ہے، بعض صورتوں میں مواد اور درجہ حرارت پر منحصر ہوتے ہوئے یہ ہزاروں میں پرزے تیار کر سکتے ہیں۔ کیلٹول کا عمل: یہ تکنیک 100,000 سے 10 ملین سائیکل لائف کے ساتھ مولڈ تیار کر سکتی ہے۔ تیز رفتار پروٹو ٹائپنگ کا استعمال کرتے ہوئے ہم ایک RTV مولڈ تیار کرتے ہیں۔ اس کے بعد مولڈ کو A6 ٹول اسٹیل پاؤڈر، ٹنگسٹن کاربائیڈ، پولیمر بائنڈر پر مشتمل مرکب سے بھرا جاتا ہے اور اسے ٹھیک ہونے دیا جاتا ہے۔ اس مولڈ کو پھر گرم کیا جاتا ہے تاکہ پولیمر جل جائے اور دھاتی پاؤڈر فیوز ہو جائیں۔ اگلا مرحلہ فائنل مولڈ تیار کرنے کے لیے تانبے کی دراندازی ہے۔ اگر ضرورت ہو تو، بہتر جہتی درستگیوں کے لیے ثانوی آپریشنز جیسے کہ مشینی اور پالش کو مولڈ پر کیا جا سکتا ہے۔ _cc781905-5cde-3194-bb3b-1358bad_ CLICK Product Finder-Locator Service پچھلا صفحہ
- Composites, Composite Materials Manufacturing, Fiber Reinforced
Composites, Composite Materials Manufacturing, Particle and Fiber Reinforced, Cermets, Ceramic & Metal Composite, Glass Fiber Reinforced Polymer, Lay-Up Process کمپوزٹ اور کمپوزٹ میٹریل مینوفیکچرنگ سادہ الفاظ میں بیان کیا جائے تو، مرکب یا مرکب مواد وہ مواد ہیں جو دو یا ایک سے زیادہ مواد پر مشتمل ہوتے ہیں جن میں مختلف طبعی یا کیمیائی خصوصیات ہوتی ہیں، لیکن جب ان کو ملایا جائے تو وہ ایک ایسا مواد بن جاتا ہے جو اجزاء کے مواد سے مختلف ہوتا ہے۔ ہمیں اس بات کی نشاندہی کرنے کی ضرورت ہے کہ ساختی مواد الگ الگ اور الگ رہتے ہیں۔ ایک جامع مواد تیار کرنے کا مقصد ایک ایسی مصنوعات کو حاصل کرنا ہے جو اس کے اجزاء سے اعلیٰ ہو اور ہر جزو کی مطلوبہ خصوصیات کو یکجا کرتا ہو۔ ایک مثال کے طور؛ مضبوطی، کم وزن یا کم قیمت کسی مرکب کو ڈیزائن کرنے اور تیار کرنے کے پیچھے محرک ہوسکتی ہے۔ ہم جس قسم کی کمپوزٹ پیش کرتے ہیں وہ ہیں پارٹیکل ریئنفورسڈ کمپوزٹ، فائبر سے مضبوط کمپوزٹ بشمول سیرامک-میٹرکس/پولیمر-میٹرکس/میٹل-میٹرکس/کاربن-کاربن/ہائبرڈ کمپوزٹ، سٹرکچرل اور لیمینیٹڈ اور سینڈوچ-سٹرکچرڈ کمپوزٹ اور نینو کمپوزٹ۔ ہم مرکب مواد کی تیاری میں جو فیبریکیشن تکنیکیں لگاتے ہیں وہ ہیں: Pultrusion، prepreg پروڈکشن کے عمل، جدید فائبر پلیسمنٹ، filament winding، tailored fiber placement، fiberglass spray lay-up process، tufting، lanxide process، z-pinning۔ بہت سے مرکب مواد دو مرحلوں سے مل کر بنتے ہیں، میٹرکس، جو مسلسل ہے اور دوسرے مرحلے کو گھیرے ہوئے ہے۔ اور منتشر مرحلہ جو میٹرکس سے گھرا ہوا ہے۔ ہمارا مشورہ ہے کہ آپ یہاں کلک کریں۔AGS-TECH Inc کی طرف سے کمپوزٹ اور کمپوزٹ میٹریل مینوفیکچرنگ کی ہماری اسکیمیٹک عکاسی ڈاؤن لوڈ کریں۔ اس سے آپ کو ان معلومات کو بہتر طریقے سے سمجھنے میں مدد ملے گی جو ہم آپ کو ذیل میں فراہم کر رہے ہیں۔ • پارٹیکل-مضبوط مرکبات: یہ زمرہ دو قسموں پر مشتمل ہے: بڑے ذرہ مرکبات اور بازی سے مضبوط مرکبات۔ سابقہ قسم میں، ذرہ-میٹرکس تعاملات کو جوہری یا سالماتی سطح پر علاج نہیں کیا جا سکتا۔ اس کے بجائے تسلسل میکانکس درست ہے۔ دوسری طرف، بازی کو مضبوط بنانے والے مرکبات میں ذرات عام طور پر دسیوں نینو میٹر کی حدود میں بہت چھوٹے ہوتے ہیں۔ بڑے پارٹیکل کمپوزٹ کی ایک مثال پولیمر ہے جس میں فلرز شامل کیے گئے ہیں۔ فلرز مواد کی خصوصیات کو بہتر بناتے ہیں اور کچھ پولیمر والیوم کو زیادہ اقتصادی مواد سے بدل سکتے ہیں۔ دو مراحل کے حجم کے حصے جامع کے رویے کو متاثر کرتے ہیں۔ دھاتوں، پولیمر اور سیرامکس کے ساتھ بڑے پارٹیکل کمپوزٹ استعمال کیے جاتے ہیں۔ CERMETS سیرامک / دھاتی مرکبات کی مثالیں ہیں۔ ہمارا سب سے عام سرمیٹ سیمنٹڈ کاربائیڈ ہے۔ یہ ریفریکٹری کاربائیڈ سیرامک پر مشتمل ہوتا ہے جیسے کوبالٹ یا نکل جیسی دھات کے میٹرکس میں ٹنگسٹن کاربائیڈ کے ذرات۔ یہ کاربائیڈ کمپوزٹ بڑے پیمانے پر سخت سٹیل کے کاٹنے کے اوزار کے طور پر استعمال ہوتے ہیں۔ سخت کاربائیڈ ذرات کاٹنے کے عمل کے ذمہ دار ہیں اور ان کی سختی کو ڈکٹائل میٹل میٹرکس سے بڑھایا جاتا ہے۔ اس طرح ہم ایک ہی مرکب میں دونوں مواد کے فوائد حاصل کرتے ہیں۔ ایک بڑے پارٹیکل کمپوزٹ کی ایک اور عام مثال جسے ہم استعمال کرتے ہیں کاربن بلیک پارٹیکولٹس کو وولکنائزڈ ربڑ کے ساتھ ملایا جاتا ہے تاکہ اعلی تناؤ کی طاقت، سختی، آنسو اور کھرچنے کی مزاحمت کے ساتھ مرکب حاصل کیا جا سکے۔ بازی کو مضبوط بنانے والے مرکب کی ایک مثال دھاتیں اور دھاتی مرکبات ہیں جو بہت سخت اور غیر فعال مواد کے باریک ذرات کے یکساں پھیلاؤ سے مضبوط اور سخت ہوتے ہیں۔ جب ایلومینیم میٹل میٹرکس میں بہت چھوٹے ایلومینیم آکسائیڈ فلیکس شامل کیے جاتے ہیں تو ہم سنٹرڈ ایلومینیم پاؤڈر حاصل کرتے ہیں جس میں اعلی درجہ حرارت کی طاقت ہوتی ہے۔ FIBER-REINFORCED Composites : مرکبات کا یہ زمرہ درحقیقت سب سے اہم ہے۔ حاصل کرنے کا مقصد فی یونٹ وزن اعلی طاقت اور سختی ہے۔ ان مرکبات میں فائبر کی ساخت، لمبائی، واقفیت اور ارتکاز ان مواد کی خصوصیات اور افادیت کا تعین کرنے میں اہم ہے۔ ریشوں کے تین گروہ ہیں جو ہم استعمال کرتے ہیں: سرگوشیاں، ریشے اور تاریں۔ WHISKERS بہت پتلے اور لمبے سنگل کرسٹل ہوتے ہیں۔ وہ مضبوط ترین مواد میں سے ہیں۔ کچھ مثال کے طور پر سرگوشی کے مواد گریفائٹ، سلکان نائٹرائڈ، ایلومینیم آکسائڈ ہیں. دوسری طرف FIBERS زیادہ تر پولیمر یا سیرامکس ہیں اور پولی کرسٹل لائن یا بے ساختہ حالت میں ہیں۔ تیسرا گروپ باریک تاروں کا ہے جن کا قطر نسبتاً بڑا ہوتا ہے اور اکثر اسٹیل یا ٹنگسٹن پر مشتمل ہوتا ہے۔ وائر ری انفورسڈ کمپوزٹ کی ایک مثال کار کے ٹائر ہیں جو ربڑ کے اندر سٹیل کے تار کو شامل کرتے ہیں۔ میٹرکس مواد پر منحصر ہے، ہمارے پاس مندرجہ ذیل مرکبات ہیں: پولیمر-میٹرکس کمپوزائٹس: یہ ایک پولیمر رال اور ریشوں سے بنی ہوتی ہیں بطور انفورسمنٹ جزو۔ ان کا ایک ذیلی گروپ جسے Glass Fiber-Reinforced Polymer (GFRP) کمپوزٹ کہتے ہیں ایک پولیمر میٹرکس کے اندر مسلسل یا منقطع شیشے کے ریشے پر مشتمل ہوتا ہے۔ شیشہ اعلی طاقت پیش کرتا ہے، یہ اقتصادی ہے، ریشوں میں گھڑنے میں آسان ہے، اور کیمیائی طور پر غیر فعال ہے۔ نقصانات ان کی محدود سختی اور سختی ہیں، سروس کا درجہ حرارت صرف 200 - 300 سینٹی گریڈ تک ہے۔ فائبر گلاس آٹوموٹو باڈیز اور ٹرانسپورٹیشن کا سامان، سمندری گاڑیوں کی باڈیز، اسٹوریج کنٹینرز کے لیے موزوں ہے۔ یہ محدود سختی کی وجہ سے نہ ایرو اسپیس اور نہ ہی پل بنانے کے لیے موزوں ہیں۔ دوسرے ذیلی گروپ کو کاربن فائبر ریئنفورسڈ پولیمر (CFRP) کمپوزٹ کہا جاتا ہے۔ یہاں، پولیمر میٹرکس میں کاربن ہمارا فائبر مواد ہے۔ کاربن اپنے اعلی مخصوص ماڈیولس اور طاقت اور اعلی درجہ حرارت پر ان کو برقرار رکھنے کی صلاحیت کے لیے جانا جاتا ہے۔ کاربن فائبر ہمیں معیاری، انٹرمیڈیٹ، ہائی اور انتہائی ہائی ٹینسائل موڈیولی پیش کر سکتے ہیں۔ مزید برآں، کاربن فائبر متنوع جسمانی اور مکینیکل خصوصیات پیش کرتے ہیں اور اس لیے مختلف اپنی مرضی کے مطابق تیار کردہ انجینئرنگ ایپلی کیشنز کے لیے موزوں ہیں۔ CFRP کمپوزٹ کو کھیلوں اور تفریحی سامان، پریشر ویسلز اور ایرو اسپیس ساختی اجزاء کی تیاری کے لیے سمجھا جا سکتا ہے۔ پھر بھی، ایک اور ذیلی گروپ، ارامڈ فائبر ریئنفورسڈ پولیمر کمپوزائٹس بھی اعلیٰ طاقت اور ماڈیولس مواد ہیں۔ وزن کے تناسب سے ان کی طاقت بہت زیادہ ہے۔ ارامڈ ریشوں کو تجارتی ناموں KEVLAR اور NOMEX سے بھی جانا جاتا ہے۔ تناؤ کے تحت وہ دیگر پولیمرک فائبر مواد سے بہتر کارکردگی کا مظاہرہ کرتے ہیں، لیکن وہ کمپریشن میں کمزور ہیں۔ ارامڈ ریشے سخت، اثر مزاحم، رینگنے اور تھکاوٹ کے خلاف مزاحم، اعلی درجہ حرارت پر مستحکم، مضبوط تیزاب اور اڈوں کے علاوہ کیمیائی طور پر غیر فعال ہوتے ہیں۔ آرامڈ فائبر کھیلوں کے سامان، بلٹ پروف واسکٹ، ٹائر، رسی، فائبر آپٹک کیبل شیٹس میں بڑے پیمانے پر استعمال ہوتے ہیں۔ دیگر فائبر کو تقویت دینے والے مواد موجود ہیں لیکن کم حد تک استعمال ہوتے ہیں۔ یہ بنیادی طور پر بوران، سلکان کاربائیڈ، ایلومینیم آکسائیڈ ہیں۔ دوسری طرف پولیمر میٹرکس کا مواد بھی اہم ہے۔ یہ مرکب کے زیادہ سے زیادہ سروس درجہ حرارت کا تعین کرتا ہے کیونکہ پولیمر میں عام طور پر پگھلنے اور انحطاط کا درجہ حرارت کم ہوتا ہے۔ پولیسٹر اور ونائل ایسٹرز بڑے پیمانے پر پولیمر میٹرکس کے طور پر استعمال ہوتے ہیں۔ رال بھی استعمال ہوتی ہے اور ان میں نمی کے خلاف مزاحمت اور مکینیکل خصوصیات ہوتی ہیں۔ مثال کے طور پر پولیمائیڈ رال تقریباً 230 ڈگری سیلسیس تک استعمال کی جا سکتی ہے۔ میٹل-میٹرکس کمپوزائٹس: ان مواد میں ہم ڈکٹائل میٹل میٹرکس استعمال کرتے ہیں اور سروس کا درجہ حرارت عام طور پر ان کے اجزاء سے زیادہ ہوتا ہے۔ پولیمر-میٹرکس کمپوزائٹس کے مقابلے میں، ان کا آپریٹنگ درجہ حرارت زیادہ ہو سکتا ہے، غیر آتش گیر ہو سکتا ہے، اور نامیاتی سیالوں کے خلاف انحطاط کی بہتر مزاحمت ہو سکتی ہے۔ تاہم وہ زیادہ مہنگے ہیں۔ کمک کرنے والے مواد جیسے سرگوشی، ذرات، مسلسل اور منقطع ریشے؛ اور میٹرکس میٹریل جیسے کاپر، ایلومینیم، میگنیشیم، ٹائٹینیم، سپر ایلوائیز عام طور پر استعمال ہو رہے ہیں۔ مثال کے طور پر ایپلی کیشنز ایلومینیم الائے میٹرکس سے بنے ہوئے انجن کے پرزے ہیں جو ایلومینیم آکسائیڈ اور کاربن ریشوں سے تقویت یافتہ ہیں۔ سیرامک-میٹرکس کمپوزائٹس: سیرامک مواد ان کی شاندار اعلی درجہ حرارت کی قابل اعتمادی کے لیے جانا جاتا ہے۔ تاہم وہ بہت ٹوٹنے والے ہیں اور فریکچر کی سختی کے لیے کم قدر رکھتے ہیں۔ ایک سیرامک کے ذرات، ریشوں یا سروں کو دوسرے کے میٹرکس میں شامل کرکے ہم زیادہ فریکچر سختی کے ساتھ مرکبات حاصل کرنے کے قابل ہوتے ہیں۔ یہ سرایت شدہ مواد بنیادی طور پر میٹرکس کے اندر شگاف کے پھیلاؤ کو کچھ میکانزم کے ذریعے روکتا ہے جیسے کریک ٹپس کو ہٹانا یا کریک چہروں پر پل بنانا۔ مثال کے طور پر، ایلومیناس جو SiC سرگوشیوں سے تقویت یافتہ ہوتے ہیں سخت دھاتی مرکبات کو مشینی بنانے کے لیے کاٹنے والے آلے کے داخلوں کے طور پر استعمال ہوتے ہیں۔ یہ سیمنٹڈ کاربائیڈز کے مقابلے میں بہتر کارکردگی کو ظاہر کر سکتے ہیں۔ کاربن-کاربن مرکبات: کمک اور میٹرکس دونوں کاربن ہیں۔ ان میں 2000 سینٹی گریڈ سے زیادہ درجہ حرارت پر اعلی ٹینسائل ماڈیولی اور طاقت ہوتی ہے، رینگنے کی مزاحمت، زیادہ فریکچر سختی، کم تھرمل ایکسپینشن گتانک، اعلی تھرمل چالکتا۔ یہ خصوصیات انہیں ایپلی کیشنز کے لیے مثالی بناتی ہیں جن میں تھرمل جھٹکا مزاحمت کی ضرورت ہوتی ہے۔ کاربن کاربن مرکبات کی کمزوری تاہم اعلی درجہ حرارت پر آکسیکرن کے خلاف اس کی کمزوری ہے۔ استعمال کی عام مثالیں گرم دبانے والے سانچوں، جدید ترین ٹربائن انجن کے اجزاء کی تیاری ہیں۔ ہائبرڈ کمپوزائٹس: دو یا دو سے زیادہ مختلف قسم کے ریشوں کو ایک میٹرکس میں ملایا جاتا ہے۔ اس طرح کوئی بھی خصوصیات کے امتزاج کے ساتھ ایک نیا مواد تیار کرسکتا ہے۔ ایک مثال یہ ہے کہ جب کاربن اور شیشے کے ریشوں دونوں کو پولیمرک رال میں شامل کیا جاتا ہے۔ کاربن فائبر کم کثافت کی سختی اور طاقت فراہم کرتے ہیں لیکن مہنگے ہیں۔ دوسری طرف گلاس سستا ہے لیکن کاربن ریشوں کی سختی کی کمی ہے۔ گلاس کاربن ہائبرڈ مرکب زیادہ مضبوط اور سخت ہے اور اسے کم قیمت پر تیار کیا جا سکتا ہے۔ فائبر سے تقویت یافتہ مرکبات کی پروسیسنگ: ایک ہی سمت میں یکساں تقسیم شدہ ریشوں کے ساتھ مسلسل فائبر سے تقویت یافتہ پلاسٹک کے لیے ہم درج ذیل تکنیکوں کا استعمال کرتے ہیں۔ PULTRUSION: مسلسل لمبائی اور مسلسل کراس سیکشن کی سلاخیں، شہتیر اور ٹیوبیں تیار کی جاتی ہیں۔ مسلسل فائبر روونگز کو تھرموسیٹنگ رال سے رنگین کیا جاتا ہے اور انہیں اسٹیل ڈائی کے ذریعے کھینچا جاتا ہے تاکہ انہیں مطلوبہ شکل میں پیش کیا جا سکے۔ اس کے بعد، وہ اپنی حتمی شکل حاصل کرنے کے لیے ایک درست مشینی کیورنگ ڈائی سے گزرتے ہیں۔ چونکہ کیورنگ ڈائی کو گرم کیا جاتا ہے، یہ رال میٹرکس کو ٹھیک کرتا ہے۔ کھینچنے والے ڈیز کے ذریعے مواد کھینچتے ہیں۔ داخل شدہ کھوکھلی کور کا استعمال کرتے ہوئے، ہم ٹیوبیں اور کھوکھلی جیومیٹریاں حاصل کرنے کے قابل ہیں۔ pultrusion طریقہ خود کار ہے اور ہمیں اعلی پیداوار کی شرح پیش کرتا ہے. مصنوعات کی کسی بھی لمبائی کی پیداوار ممکن ہے۔ پری پریگ پروڈکشن کا عمل: پری پریگ ایک مسلسل فائبر ریانفورسمنٹ ہے جو جزوی طور پر ٹھیک شدہ پولیمر رال کے ساتھ پہلے سے تیار کیا جاتا ہے۔ یہ بڑے پیمانے پر ساختی ایپلی کیشنز کے لئے استعمال کیا جاتا ہے. مواد ٹیپ کی شکل میں آتا ہے اور اسے ٹیپ کے طور پر بھیجا جاتا ہے۔ مینوفیکچرر اسے براہ راست ڈھالتا ہے اور بغیر کسی رال ڈالنے کی ضرورت کے اسے مکمل طور پر ٹھیک کرتا ہے۔ چونکہ پری پریگس کمرے کے درجہ حرارت پر علاج کے رد عمل سے گزرتے ہیں، اس لیے انہیں 0 سینٹی گریڈ یا اس سے کم درجہ حرارت پر محفوظ کیا جاتا ہے۔ استعمال کے بعد بقیہ ٹیپس کو کم درجہ حرارت پر واپس محفوظ کیا جاتا ہے۔ تھرمو پلاسٹک اور تھرموسیٹنگ رال استعمال کی جاتی ہے اور کاربن، ارامیڈ اور شیشے کے ری انفورسمنٹ ریشے عام ہیں۔ پری پریگس کو استعمال کرنے کے لیے، پہلے کیریئر بیکنگ پیپر کو ہٹایا جاتا ہے اور پھر پری پریگ ٹیپ کو ٹول والی سطح پر بچھا کر تیار کیا جاتا ہے (بچھائی کا عمل)۔ مطلوبہ موٹائی حاصل کرنے کے لیے کئی پلائیاں رکھی جا سکتی ہیں۔ کراس پلائی یا اینگل پلائی لیمینیٹ تیار کرنے کے لیے فائبر اوریئنٹیشن کو بار بار استعمال کرنا ہے۔ آخر میں علاج کے لیے گرمی اور دباؤ کا اطلاق ہوتا ہے۔ ہینڈ پروسیسنگ کے ساتھ ساتھ خودکار عمل دونوں کا استعمال پری پریگس اور لیٹ اپ کے لیے کیا جاتا ہے۔ فلیمینٹ وائنڈنگ: مسلسل مضبوط کرنے والے ریشوں کو ایک کھوکھلی اور عام طور پر چکر دار شکل کی پیروی کرنے کے لیے پہلے سے طے شدہ پیٹرن میں درست طریقے سے رکھا جاتا ہے۔ ریشے پہلے رال کے غسل سے گزرتے ہیں اور پھر خودکار نظام کے ذریعے مینڈریل پر زخم لگائے جاتے ہیں۔ کئی بار سمیٹنے کے بعد مطلوبہ موٹائی حاصل کی جاتی ہے اور کیورنگ یا تو کمرے کے درجہ حرارت پر یا تندور کے اندر کی جاتی ہے۔ اب مینڈریل کو ہٹا دیا گیا ہے اور مصنوعات کو توڑ دیا گیا ہے۔ فلیمینٹ وائنڈنگ ریشوں کو گردشی، ہیلیکل اور قطبی نمونوں میں سمیٹ کر بہت زیادہ طاقت سے وزن کا تناسب پیش کر سکتی ہے۔ پائپ، ٹینک، کیسنگ اس تکنیک کا استعمال کرتے ہوئے تیار کیے جاتے ہیں۔ • ساختی مرکبات: عام طور پر یہ یکساں اور جامع مواد دونوں سے مل کر بنتے ہیں۔ لہٰذا ان کی خصوصیات کا تعین اجزاء کے مواد اور اس کے عناصر کے جیومیٹریکل ڈیزائن سے ہوتا ہے۔ یہاں اہم اقسام ہیں: لامینار کمپوزائٹس: یہ ساختی مواد دو جہتی شیٹس یا پینلز سے بنائے گئے ہیں جن میں ترجیحی اعلی طاقت کی سمت ہے۔ تہوں کو ایک ساتھ اسٹیک اور سیمنٹ کیا جاتا ہے۔ دو کھڑے محوروں میں اعلی طاقت کی سمتوں کو تبدیل کرکے، ہم ایک ایسا مرکب حاصل کرتے ہیں جس کی دو جہتی جہاز میں دونوں سمتوں میں زیادہ طاقت ہوتی ہے۔ تہوں کے زاویوں کو ایڈجسٹ کرکے کوئی بھی ترجیحی سمتوں میں طاقت کے ساتھ ایک مرکب تیار کرسکتا ہے۔ جدید سکی اس طرح تیار کی جاتی ہے۔ سینڈوچ پینلز: یہ ساختی مرکبات ہلکے ہیں لیکن پھر بھی ان میں سختی اور طاقت زیادہ ہے۔ سینڈوچ پینل دو بیرونی شیٹس پر مشتمل ہوتے ہیں جو ایک سخت اور مضبوط مواد سے بنی ہوتی ہیں جیسے ایلومینیم کے مرکب، فائبر سے تقویت یافتہ پلاسٹک یا اسٹیل اور بیرونی چادروں کے درمیان ایک کور۔ کور کو ہلکا ہونا ضروری ہے اور زیادہ تر وقت میں لچک کا کم ماڈیول ہوتا ہے۔ مقبول بنیادی مواد سخت پولیمرک جھاگ، لکڑی اور شہد کے چھتے ہیں۔ سینڈوچ پینل بڑے پیمانے پر تعمیراتی صنعت میں چھت سازی کے مواد، فرش یا دیوار کے مواد کے طور پر اور ایرو اسپیس صنعتوں میں بھی استعمال ہوتے ہیں۔ NANOCOMPOSITES : یہ نیا مواد میٹرکس میں سرایت شدہ نانوائزڈ پارٹیکلز پر مشتمل ہوتا ہے۔ نانوکومپوزائٹس کا استعمال کرتے ہوئے ہم ربڑ کا ایسا مواد تیار کر سکتے ہیں جو ہوا کے داخلے میں بہت اچھی رکاوٹیں ہیں اور ربڑ کی خصوصیات کو برقرار رکھتے ہوئے بغیر کسی تبدیلی کے۔ CLICK Product Finder-Locator Service پچھلا صفحہ
- Machine Elements Manufacturing, Gears, Gear Drives, Bearings, Keys, Splines
Machine Elements Manufacturing, Gears, Gear Drives, Bearings, Keys, Splines, Pins, Shafts, Seals, Fasteners, Clutch, Cams, Followers, Belts, Couplings, Shafts مشین عناصر مینوفیکچرنگ مزید پڑھ بیلٹ اور چینز اور کیبل ڈرائیو اسمبلی مزید پڑھ گیئرز اور گیئر ڈرائیو اسمبلی مزید پڑھ کپلنگ اور بیرنگ مینوفیکچرنگ مزید پڑھ چابیاں اور سپلائنز اور پن مینوفیکچرنگ مزید پڑھ کیمز اور فالورز اور لنکیجز اور ریچیٹ وہیل مینوفیکچرنگ مزید پڑھ شافٹ مینوفیکچرنگ مزید پڑھ مکینیکل سیل مینوفیکچرنگ مزید پڑھ کلچ اور بریک اسمبلی مزید پڑھ فاسٹنر مینوفیکچرنگ مزید پڑھ سادہ مشینیں اسمبلی MACHINE ELEMENTS ایک مشین کے ابتدائی اجزاء ہیں۔ یہ عناصر تین بنیادی اقسام پر مشتمل ہیں: 1.) ساختی اجزاء بشمول فریم ممبرز، بیرنگ، ایکسل، اسپلائنز، فاسٹنرز، سیل، اور چکنا کرنے والے مادے۔ 2.) مختلف طریقوں سے نقل و حرکت کو کنٹرول کرنے والے میکانزم جیسے گیئر ٹرین، بیلٹ یا چین ڈرائیوز، لنکیجز، کیم اور فالوور سسٹم، بریک اور کلچ۔ 3.) کنٹرول اجزاء جیسے بٹن، سوئچ، اشارے، سینسر، ایکچیوٹرز اور کمپیوٹر کنٹرولرز۔ زیادہ تر مشینی عناصر جو ہم آپ کو پیش کرتے ہیں وہ عام سائز کے لیے معیاری ہیں، لیکن اپنی مرضی کے مطابق مشین کے عناصر آپ کے مخصوص ایپلی کیشنز کے لیے بھی دستیاب ہیں۔ مشین عناصر کی حسب ضرورت موجودہ ڈیزائنوں پر ہو سکتی ہے جو ہمارے ڈاؤن لوڈ کے قابل کیٹلاگ میں ہیں یا بالکل نئے ڈیزائنوں پر۔ دونوں فریقوں کی طرف سے ڈیزائن کی منظوری کے بعد مشین کے عناصر کی پروٹو ٹائپنگ اور تیاری کو آگے بڑھایا جا سکتا ہے۔ اگر مشین کے نئے عناصر کو ڈیزائن اور تیار کرنے کی ضرورت ہے، تو ہمارے صارفین یا تو ہمیں اپنے بلیو پرنٹ ای میل کرتے ہیں اور ہم منظوری کے لیے ان کا جائزہ لیتے ہیں، یا وہ ہم سے اپنی درخواست کے لیے مشین کے عناصر کو ڈیزائن کرنے کے لیے کہتے ہیں۔ مؤخر الذکر صورت میں ہم اپنے صارفین کے تمام ان پٹ استعمال کرتے ہیں اور مشین کے عناصر کو ڈیزائن کرتے ہیں اور حتمی شکلیں اپنے کلائنٹس کو منظوری کے لیے بھیجتے ہیں۔ منظوری کے بعد، ہم پہلے آرٹیکل تیار کرتے ہیں اور اس کے بعد حتمی ڈیزائن کے مطابق مشین کے عناصر تیار کرتے ہیں۔ اس کام کے کسی بھی مرحلے پر، اگر کوئی خاص مشین عنصر ڈیزائن فیلڈ میں غیر اطمینان بخش کارکردگی کا مظاہرہ کرتا ہے (جو کہ شاذ و نادر ہے)، ہم پورے پروجیکٹ کا جائزہ لیتے ہیں اور ضرورت کے مطابق اپنے کلائنٹس کے ساتھ مشترکہ طور پر تبدیلیاں کرتے ہیں۔ جب بھی ضرورت ہو یا ضرورت ہو مشین کے عناصر یا کسی اور پروڈکٹ کے ڈیزائن کے لیے اپنے صارفین کے ساتھ غیر انکشافی معاہدے (NDA) پر دستخط کرنا ہمارا معیاری عمل ہے۔ ایک بار جب کسی مخصوص گاہک کے لیے مشین کے عناصر اپنی مرضی کے مطابق ڈیزائن اور تیار ہو جاتے ہیں، تو ہم اس کو ایک پروڈکٹ کوڈ تفویض کرتے ہیں اور انہیں صرف اپنے گاہک کو تیار اور فروخت کرتے ہیں جو پروڈکٹ کا مالک ہے۔ ہم مشین کے عناصر کو ترقی یافتہ ٹولز، مولڈز اور طریقہ کار کا استعمال کرتے ہوئے جتنی بار ضرورت ہو اور جب بھی ہمارا صارف انہیں دوبارہ ترتیب دیتا ہے۔ دوسرے لفظوں میں، ایک بار جب آپ کے لیے حسب ضرورت مشین کا عنصر تیار اور تیار ہو جاتا ہے، تو دانشورانہ املاک کے ساتھ ساتھ تمام ٹولنگ اور مولڈ آپ کے لیے محفوظ اور غیر معینہ مدت کے لیے ذخیرہ کیے جاتے ہیں اور آپ کی مرضی کے مطابق مصنوعات دوبارہ تیار کی جاتی ہیں۔ ہم مشین کے عناصر کو تخلیقی طور پر ایک جزو یا اسمبلی میں جوڑ کر اپنے کلائنٹس کو انجینئرنگ کی خدمات بھی پیش کرتے ہیں جو ایپلی کیشن پیش کرتا ہے اور ہمارے صارفین کی توقعات کو پورا کرتا ہے یا اس سے زیادہ ہے۔ ہمارے مشینی عناصر کو گھڑنے والے پلانٹس ISO9001، QS9000 یا TS16949 کے ذریعے اہل ہیں۔ اس کے علاوہ، ہماری زیادہ تر مصنوعات میں CE یا UL نشان ہوتا ہے اور وہ بین الاقوامی سطح پر متعلقہ معیارات جیسے ISO، SAE، ASME، DIN پر پورا اترتے ہیں۔ ہمارے مشین کے عناصر کے بارے میں تفصیلی معلومات حاصل کرنے کے لیے برائے مہربانی ذیلی مینیو پر کلک کریں بشمول: - بیلٹ، زنجیریں اور کیبل ڈرائیوز - گیئرز اور گیئر ڈرائیوز - جوڑے اور بیرنگ - چابیاں اور سپلائنز اور پن - کیمز اور روابط - شافٹ - مکینیکل سیل - صنعتی کلچ اور بریک - فاسٹنر - سادہ مشینیں۔ ہم نے اپنے صارفین، ڈیزائنرز اور مشین کے عناصر سمیت نئی مصنوعات کے ڈویلپرز کے لیے ایک ریفرنس بروشر تیار کیا ہے۔ آپ مشین کے اجزاء کے ڈیزائن میں عام طور پر استعمال ہونے والی کچھ اصطلاحات سے خود کو واقف کر سکتے ہیں: ڈیزائنرز اور انجینئرز کے ذریعہ استعمال ہونے والی عام مکینیکل انجینئرنگ کی شرائط کے لیے بروشر ڈاؤن لوڈ کریں۔ ہمارے مشینی عناصر مختلف شعبوں میں ایپلی کیشنز تلاش کرتے ہیں جیسے صنعتی مشینری، آٹومیشن سسٹم، ٹیسٹ اور میٹرولوجی کا سامان، نقل و حمل کا سامان، تعمیراتی مشینیں اور عملی طور پر جہاں بھی آپ سوچ سکتے ہیں۔ AGS-TECH درخواست کے لحاظ سے مختلف مواد سے مشینی عناصر تیار اور تیار کرتا ہے۔ مشینی عناصر کے لیے استعمال ہونے والے مواد میں کھلونوں کے لیے استعمال ہونے والے مولڈ پلاسٹک سے لے کر صنعتی مشینری کے لیے سخت اور خاص طور پر لیپت اسٹیل تک کا ہو سکتا ہے۔ ہمارے ڈیزائنرز مشینی عناصر کو تیار کرنے کے لیے جدید ترین پیشہ ورانہ سافٹ ویئر اور ڈیزائن ٹولز کا استعمال کرتے ہیں، تفصیلات کو مدنظر رکھتے ہوئے جیسے کہ گیئر کے دانتوں میں زاویہ، اس میں شامل دباؤ، پہننے کے نرخ وغیرہ۔ براہ کرم ہمارے ذیلی مینیو کے ذریعے اسکرول کریں اور ہمارے پروڈکٹ کے بروشرز اور کیٹلاگز کو ڈاؤن لوڈ کریں تاکہ یہ معلوم ہو سکے کہ آیا آپ اپنی درخواست کے لیے شیلف مشین کے عناصر کو تلاش کر سکتے ہیں۔ اگر آپ کو اپنی درخواست کے لیے کوئی اچھا میچ نہیں مل رہا ہے، تو براہ کرم ہمیں بتائیں اور ہم آپ کے ساتھ مل کر مشین کے عناصر کو تیار کرنے اور تیار کرنے کے لیے کام کریں گے جو آپ کی ضروریات کو پورا کریں گے۔ اگر آپ مینوفیکچرنگ کی صلاحیتوں کے بجائے ہماری انجینئرنگ اور تحقیق اور ترقی کی صلاحیتوں میں زیادہ دلچسپی رکھتے ہیں، تو ہم آپ کو ہماری ویب سائٹ ملاحظہ کرنے کی دعوت دیتے ہیں۔http://www.ags-engineering.com جہاں آپ ہمارے ڈیزائن، پروڈکٹ ڈویلپمنٹ، پروسیس ڈویلپمنٹ، انجینئرنگ مشاورتی خدمات اور مزید کے بارے میں مزید تفصیلی معلومات حاصل کر سکتے ہیں۔ CLICK Product Finder-Locator Service پچھلا صفحہ
- Joining & Assembly & Fastening Processes, Welding, Brazing, Soldering
Joining & Assembly & Fastening Processes, Welding, Brazing, Soldering, Sintering, Adhesive Bonding, Press Fitting, Wave and Reflow Solder Process, Torch Furnace شمولیت اور اسمبلی اور باندھنے کے عمل ہم آپ کے تیار کردہ پرزوں کو جوڑتے، اسمبل اور باندھتے ہیں اور ویلڈنگ، بریزنگ، سولڈرنگ، سنٹرنگ، چپکنے والی بانڈنگ، فاسٹننگ، پریس فٹنگ کا استعمال کرتے ہوئے انہیں تیار یا نیم تیار شدہ مصنوعات میں تبدیل کرتے ہیں۔ ہمارے کچھ مشہور ویلڈنگ کے عمل آرک، آکسی فیول گیس، ریزسٹنس، پروجیکشن، سیون، اپ سیٹ، ٹککر، سالڈ سٹیٹ، الیکٹران بیم، لیزر، تھرمیٹ، انڈکشن ویلڈنگ ہیں۔ بریزنگ کے ہمارے مقبول عمل ٹارچ، انڈکشن، فرنس اور ڈِپ بریزنگ ہیں۔ ہمارے سولڈرنگ کے طریقے آئرن، ہاٹ پلیٹ، اوون، انڈکشن، ڈِپ، ویو، ری فلو اور الٹراسونک سولڈرنگ ہیں۔ چپکنے والی بانڈنگ کے لیے ہم اکثر تھرموپلاسٹک اور تھرمو سیٹنگ، ایپوکس، فینولک، پولی یوریتھین، چپکنے والی مرکبات کے ساتھ ساتھ کچھ دوسرے کیمیکلز اور ٹیپس کا استعمال کرتے ہیں۔ آخر میں ہمارے باندھنے کے عمل میں کیل لگانے، اسکرونگ، نٹ اور بولٹ، ریوٹنگ، کلینچنگ، پننگ، سلائی اور اسٹیپلنگ اور پریس فٹنگ شامل ہیں۔ • ویلڈنگ: ویلڈنگ میں کام کے ٹکڑوں کو پگھلا کر مواد کو جوڑنا اور فلر مواد متعارف کرانا شامل ہے، جو پگھلے ہوئے ویلڈ پول میں بھی شامل ہوتا ہے۔ جب علاقہ ٹھنڈا ہوجاتا ہے، تو ہم ایک مضبوط جوڑ حاصل کرتے ہیں۔ بعض صورتوں میں دباؤ ڈالا جاتا ہے۔ ویلڈنگ کے برعکس، بریزنگ اور سولڈرنگ کی کارروائیوں میں صرف ایسے مواد کا پگھلنا شامل ہوتا ہے جس میں ورک پیسز کے درمیان کم پگھلنے کا مقام ہوتا ہے، اور ورک پیس پگھلتے نہیں ہیں۔ ہمارا مشورہ ہے کہ آپ یہاں کلک کریں۔AGS-TECH Inc کی طرف سے ویلڈنگ کے عمل کی ہماری اسکیمیٹک تصویریں ڈاؤن لوڈ کریں۔ اس سے آپ کو ان معلومات کو بہتر طریقے سے سمجھنے میں مدد ملے گی جو ہم آپ کو ذیل میں فراہم کر رہے ہیں۔ ARC ویلڈنگ میں، ہم بجلی کی فراہمی اور الیکٹروڈ کا استعمال کرتے ہوئے ایک الیکٹرک آرک بناتے ہیں جو دھاتوں کو پگھلاتا ہے۔ ویلڈنگ پوائنٹ کو شیلڈنگ گیس یا بخارات یا دیگر مواد سے محفوظ کیا جاتا ہے۔ یہ عمل آٹوموٹو حصوں اور سٹیل کے ڈھانچے کی ویلڈنگ کے لیے مقبول ہے۔ شیلڈ میٹل آرک ویلڈنگ (SMAW) میں یا اسٹک ویلڈنگ کے نام سے بھی جانا جاتا ہے، ایک الیکٹروڈ اسٹک کو بنیادی مواد کے قریب لایا جاتا ہے اور ان کے درمیان ایک برقی قوس پیدا ہوتا ہے۔ الیکٹروڈ راڈ پگھل جاتا ہے اور فلر مواد کے طور پر کام کرتا ہے۔ الیکٹروڈ میں بہاؤ بھی ہوتا ہے جو سلیگ کی پرت کے طور پر کام کرتا ہے اور بخارات کو چھوڑتا ہے جو بچانے والی گیس کا کام کرتا ہے۔ یہ ویلڈ ایریا کو ماحولیاتی آلودگی سے بچاتے ہیں۔ کوئی دوسرا فلر استعمال نہیں کیا جا رہا ہے۔ اس عمل کے نقصانات اس کی سست روی ہیں، الیکٹروڈ کو کثرت سے تبدیل کرنے کی ضرورت ہے، بہاؤ سے پیدا ہونے والے بقایا سلیگ کو دور کرنے کی ضرورت ہے۔ متعدد دھاتیں جیسے لوہا، سٹیل، نکل، ایلومینیم، تانبا... وغیرہ۔ ویلڈیڈ کیا جا سکتا ہے. اس کے فوائد اس کے سستے اوزار اور استعمال میں آسانی ہیں۔ گیس میٹل آرک ویلڈنگ (GMAW) جسے میٹل انارٹ گیس (MIG) بھی کہا جاتا ہے، ہمارے پاس ایک قابل استعمال الیکٹروڈ وائر فلر اور ایک غیر فعال یا جزوی طور پر غیر فعال گیس ہے جو ویلڈ کے علاقے کی ماحولیاتی آلودگی کے خلاف تار کے گرد بہتی ہے۔ اسٹیل، ایلومینیم اور دیگر الوہ دھاتوں کو ویلڈیڈ کیا جا سکتا ہے۔ MIG کے فوائد اعلی ویلڈنگ کی رفتار اور اچھے معیار ہیں۔ نقصانات اس کے پیچیدہ آلات اور ہوا کے بیرونی ماحول میں درپیش چیلنجز ہیں کیونکہ ہمیں ویلڈنگ ایریا کے ارد گرد شیلڈنگ گیس کو مستحکم رکھنا ہوتا ہے۔ GMAW کی ایک تبدیلی فلوکس کورڈ آرک ویلڈنگ (FCAW) ہے جو فلوکس میٹریل سے بھری ایک باریک دھاتی ٹیوب پر مشتمل ہوتی ہے۔ بعض اوقات ٹیوب کے اندر کا بہاؤ ماحولیاتی آلودگی سے تحفظ کے لیے کافی ہوتا ہے۔ ڈوب جانے والی آرک ویلڈنگ (SAW) وسیع پیمانے پر ایک خودکار عمل ہے، جس میں تاروں کو لگاتار فیڈنگ اور آرک شامل ہوتا ہے جو فلوکس کور کی ایک تہہ کے نیچے مارا جاتا ہے۔ پیداوار کی شرح اور معیار زیادہ ہے، ویلڈنگ کا سلیگ آسانی سے ختم ہو جاتا ہے، اور ہمارے پاس دھواں سے پاک کام کا ماحول ہے۔ نقصان یہ ہے کہ اسے صرف parts کو مخصوص پوزیشنوں میں ویلڈ کرنے کے لیے استعمال کیا جا سکتا ہے۔ گیس ٹنگسٹن آرک ویلڈنگ (GTAW) یا tungsten-inert gas welding (TIG) میں ہم ٹنگسٹن الیکٹروڈ کے ساتھ ایک الگ فلر اور غیر فعال یا قریب غیر فعال گیسوں کا استعمال کرتے ہیں۔ جیسا کہ ہم جانتے ہیں کہ ٹنگسٹن کا پگھلنے کا نقطہ زیادہ ہے اور یہ بہت زیادہ درجہ حرارت کے لیے بہت موزوں دھات ہے۔ TIG میں ٹنگسٹن اوپر بیان کردہ دیگر طریقوں کے برعکس استعمال نہیں کیا جاتا ہے۔ ایک سست لیکن اعلیٰ معیار کی ویلڈنگ کی تکنیک جو پتلے مواد کی ویلڈنگ میں دیگر تکنیکوں کے مقابلے میں فائدہ مند ہے۔ بہت سی دھاتوں کے لیے موزوں ہے۔ پلازما آرک ویلڈنگ اسی طرح کی ہے لیکن آرک بنانے کے لیے پلازما گیس استعمال کرتی ہے۔ پلازما آرک ویلڈنگ میں آرک GTAW کے مقابلے میں نسبتاً زیادہ مرتکز ہے اور اسے دھات کی موٹائی کی وسیع رینج کے لیے بہت زیادہ رفتار پر استعمال کیا جا سکتا ہے۔ GTAW اور پلازما آرک ویلڈنگ کو کم و بیش ایک ہی مواد پر لگایا جا سکتا ہے۔ OXY-FUEL / OXYFUEL ویلڈنگ کو oxyacetylene ویلڈنگ بھی کہا جاتا ہے، آکسی ویلڈنگ، ویلڈنگ کے لیے گیس کے ایندھن اور آکسیجن کا استعمال کرتے ہوئے گیس ویلڈنگ کی جاتی ہے۔ چونکہ کوئی برقی طاقت استعمال نہیں کی جاتی ہے یہ پورٹیبل ہے اور جہاں بجلی نہیں ہے وہاں استعمال کی جاسکتی ہے۔ ویلڈنگ ٹارچ کا استعمال کرتے ہوئے ہم ٹکڑوں اور فلر مواد کو گرم کرتے ہیں تاکہ مشترکہ پگھلا ہوا دھاتی پول تیار کیا جا سکے۔ مختلف ایندھن استعمال کیے جا سکتے ہیں جیسے ایسٹیلین، پٹرول، ہائیڈروجن، پروپین، بیوٹین... وغیرہ۔ آکسی ایندھن کی ویلڈنگ میں ہم دو کنٹینرز استعمال کرتے ہیں، ایک ایندھن کے لیے اور دوسرا آکسیجن کے لیے۔ آکسیجن ایندھن کو آکسائڈائز کرتی ہے (اسے جلا دیتی ہے)۔ ریزسٹنس ویلڈنگ: اس قسم کی ویلڈنگ جول ہیٹنگ کا فائدہ اٹھاتی ہے اور حرارت اس جگہ پر پیدا ہوتی ہے جہاں ایک خاص وقت کے لیے برقی رو لگائی جاتی ہے۔ دھات سے تیز دھارے گزرتے ہیں۔ اس مقام پر پگھلی ہوئی دھات کے تالاب بنتے ہیں۔ مزاحمتی ویلڈنگ کے طریقے اپنی کارکردگی، کم آلودگی کی صلاحیت کی وجہ سے مقبول ہیں۔ تاہم نقصانات یہ ہیں کہ سامان کی لاگت نسبتاً اہم ہے اور نسبتاً پتلے کام کے ٹکڑوں کی موروثی حد۔ سپاٹ ویلڈنگ مزاحمتی ویلڈنگ کی ایک بڑی قسم ہے۔ یہاں ہم دو یا دو سے زیادہ اوور لیپنگ شیٹس یا ورک پیسز کو جوڑتے ہیں دو تانبے کے الیکٹروڈس کا استعمال کرتے ہوئے چادروں کو ایک ساتھ باندھتے ہیں اور ان میں سے ایک تیز کرنٹ گزرتے ہیں۔ تانبے کے الیکٹروڈ کے درمیان مواد گرم ہو جاتا ہے اور اس جگہ پر ایک پگھلا ہوا تالاب پیدا ہوتا ہے۔ اس کے بعد کرنٹ کو روک دیا جاتا ہے اور تانبے کے الیکٹروڈ ٹپس ویلڈ کی جگہ کو ٹھنڈا کرتے ہیں کیونکہ الیکٹروڈ پانی کو ٹھنڈا کرتے ہیں۔ اس تکنیک کے لیے صحیح مواد اور موٹائی میں گرمی کی صحیح مقدار کا استعمال کلیدی حیثیت رکھتا ہے، کیونکہ اگر غلط طریقے سے لگایا جائے تو جوڑ کمزور ہو جائے گا۔ اسپاٹ ویلڈنگ کے فوائد ہیں کہ ورک پیس میں کوئی خاص خرابی پیدا نہیں ہوتی، توانائی کی بچت، آٹومیشن میں آسانی اور پیداوار کی بقایا شرح، اور کسی فلر کی ضرورت نہیں ہوتی۔ نقصان یہ ہے کہ چونکہ ویلڈنگ مسلسل سیون بنانے کے بجائے جگہوں پر ہوتی ہے، اس لیے ویلڈنگ کے دیگر طریقوں کے مقابلے مجموعی طاقت نسبتاً کم ہو سکتی ہے۔ دوسری طرف سیون ویلڈنگ اسی طرح کے مواد کی پھیکی ہوئی سطحوں پر ویلڈز تیار کرتی ہے۔ سیون بٹ یا اوورلیپ جوائنٹ ہو سکتا ہے۔ سیون ویلڈنگ ایک سرے سے شروع ہوتی ہے اور آہستہ آہستہ دوسرے سرے تک جاتی ہے۔ یہ طریقہ ویلڈ کے علاقے میں دباؤ اور کرنٹ لگانے کے لیے تانبے سے دو الیکٹروڈ بھی استعمال کرتا ہے۔ ڈسک کی شکل والے الیکٹروڈ سیون لائن کے ساتھ مسلسل رابطے کے ساتھ گھومتے ہیں اور ایک مسلسل ویلڈ بناتے ہیں۔ یہاں بھی الیکٹروڈ کو پانی سے ٹھنڈا کیا جاتا ہے۔ ویلڈز بہت مضبوط اور قابل اعتماد ہیں۔ دوسرے طریقے پروجیکشن، فلیش اور پریشان ویلڈنگ کی تکنیک ہیں۔ سالڈ اسٹیٹ ویلڈنگ اوپر بیان کیے گئے پچھلے طریقوں سے تھوڑا مختلف ہے۔ ہم آہنگی دھاتوں کے پگھلنے والے درجہ حرارت سے کم درجہ حرارت پر ہوتی ہے اور دھاتی فلر کا استعمال نہیں ہوتا ہے۔ دباؤ کچھ عمل میں استعمال کیا جا سکتا ہے. مختلف طریقے COEXTRUSION WELDING ہیں جہاں مختلف دھاتوں کو ایک ہی ڈائی کے ذریعے نکالا جاتا ہے، کولڈ پریشر ویلڈنگ جہاں ہم نرم مرکب دھاتوں کو ان کے پگھلنے کے مقامات کے نیچے جوڑتے ہیں، DIFFUSION WELDING بغیر مرئی ویلڈ لائنوں کے ایک تکنیک، EXPLOSION WELDING تاکہ مختلف قسم کے مواد کو دوبارہ جوڑنے کے لیے استعمال کیا جا سکے۔ اسٹیلز، الیکٹرومیگنیٹک پلس ویلڈنگ جہاں ہم برقی مقناطیسی قوتوں کے ذریعے ٹیوبوں اور شیٹس کو تیز کرتے ہیں، فورج ویلڈنگ جس میں دھاتوں کو زیادہ درجہ حرارت پر گرم کرنا اور ان کو ایک ساتھ ہتھوڑا کرنا شامل ہے، FRICTION WELDING جہاں کافی رگڑ والی ویلڈنگ کی جاتی ہے، FRICTION STIRWELD میں شامل ہوتی ہے استعمال کے قابل ٹول جوائنٹ لائن سے گزرتا ہے، ہاٹ پریشر ویلڈنگ جہاں ہم دھاتوں کو ویکیوم یا انیرٹ گیسوں میں پگھلنے والے درجہ حرارت سے نیچے بلند درجہ حرارت پر ایک ساتھ دباتے ہیں، ہاٹ آئیسوسٹیٹک پریشر ویلڈنگ ایک ایسا عمل ہے جہاں ہم برتن کے اندر غیر فعال گیسوں کا استعمال کرتے ہوئے دباؤ ڈالتے ہیں، رول ویلڈنگ جہاں ہم شامل ہوتے ہیں۔ ان کے درمیان زبردستی کرکے مختلف مواد دو گھومنے والے پہیے، الٹراسونک ویلڈنگ جہاں پتلی دھات یا پلاسٹک کی چادروں کو ہائی فریکوئنسی کمپن توانائی کا استعمال کرتے ہوئے ویلڈ کیا جاتا ہے۔ ہمارے دوسرے ویلڈنگ کے عمل میں الیکٹرون بیم ویلڈنگ ہے جس میں گہری رسائی اور تیز رفتار پروسیسنگ ہوتی ہے لیکن ایک مہنگا طریقہ ہونے کی وجہ سے ہم اسے خاص معاملات کے لیے سمجھتے ہیں، الیکٹروسلاگ ویلڈنگ ایک طریقہ ہے جو بھاری موٹی پلیٹوں اور صرف اسٹیل کے کام کے ٹکڑوں کے لیے موزوں ہے، انڈکشن ویلڈنگ جہاں ہم الیکٹرو میگنیٹک انڈکشن کا استعمال کرتے ہیں۔ ہمارے برقی طور پر کنڈکٹیو یا فیرو میگنیٹک ورک پیس کو گرم کریں، لیزر بیم ویلڈنگ بھی گہری دخول اور تیز پروسیسنگ کے ساتھ لیکن ایک مہنگا طریقہ، لیزر ہائبرڈ ویلڈنگ جو LBW کو اسی ویلڈنگ ہیڈ میں GMAW کے ساتھ جوڑتی ہے اور پلیٹوں کے درمیان 2 ملی میٹر کے فاصلوں کو پورا کرنے کی صلاحیت رکھتی ہے، PERCUSS کہ اس میں الیکٹرک ڈسچارج شامل ہوتا ہے جس کے بعد لاگو دباؤ کے ساتھ مواد کی جعل سازی ہوتی ہے، تھرمٹ ویلڈنگ جس میں ایلومینیم اور آئرن آکسائیڈ پاؤڈرز کے درمیان ایکزتھرمک رد عمل شامل ہوتا ہے۔ گرمی اور دباؤ کے ساتھ مواد. ہمارا مشورہ ہے کہ آپ یہاں کلک کریں۔AGS-TECH Inc کی طرف سے بریزنگ، سولڈرنگ اور چپکنے والی بانڈنگ کے عمل کی ہماری اسکیمیٹک تصویریں ڈاؤن لوڈ کریں۔ اس سے آپ کو ان معلومات کو بہتر طریقے سے سمجھنے میں مدد ملے گی جو ہم آپ کو ذیل میں فراہم کر رہے ہیں۔ • بریزنگ: ہم دو یا دو سے زیادہ دھاتوں کو ان کے درمیان فلر دھاتوں کو ان کے پگھلنے کے مقامات کے اوپر گرم کرکے اور پھیلنے کے لیے کیپلیری عمل کا استعمال کرتے ہوئے جوڑتے ہیں۔ یہ عمل سولڈرنگ کی طرح ہے لیکن بریزنگ میں فلر کو پگھلانے میں شامل درجہ حرارت زیادہ ہوتا ہے۔ ویلڈنگ کی طرح، بہاؤ فلر مواد کو ماحولیاتی آلودگی سے بچاتا ہے۔ ٹھنڈا ہونے کے بعد ورک پیس ایک ساتھ جوڑ دیے جاتے ہیں۔ اس عمل میں درج ذیل کلیدی مراحل شامل ہیں: اچھی فٹ اور کلیئرنس، بنیادی مواد کی مناسب صفائی، مناسب فکسچر، مناسب بہاؤ اور ماحول کا انتخاب، اسمبلی کو گرم کرنا اور آخر میں بریزڈ اسمبلی کی صفائی۔ بریزنگ کے ہمارے کچھ عمل ٹارچ بریزنگ ہیں، ایک مقبول طریقہ جو دستی طور پر یا خودکار طریقے سے کیا جاتا ہے۔ یہ کم والیوم پروڈکشن آرڈرز اور خصوصی کیسز کے لیے موزوں ہے۔ جوائنٹ بریزڈ ہونے کے قریب گیس کے شعلوں کا استعمال کرتے ہوئے گرمی لگائی جاتی ہے۔ فرنس بریزنگ کے لیے آپریٹر کی کم مہارت کی ضرورت ہوتی ہے اور یہ ایک نیم خودکار عمل ہے جو صنعتی بڑے پیمانے پر پیداوار کے لیے موزوں ہے۔ بھٹی میں درجہ حرارت کا کنٹرول اور ماحول کا کنٹرول دونوں اس تکنیک کے فوائد ہیں، کیونکہ سابقہ ہمیں حرارت کے چکر کو کنٹرول کرنے اور مقامی حرارت کو ختم کرنے کے قابل بناتا ہے جیسا کہ ٹارچ بریزنگ میں ہوتا ہے، اور بعد والا حصہ کو آکسیڈیشن سے بچاتا ہے۔ جگنگ کا استعمال کرتے ہوئے ہم مینوفیکچرنگ لاگت کو کم سے کم کرنے کے قابل ہیں۔ نقصانات اعلی بجلی کی کھپت، سازوسامان کے اخراجات اور زیادہ چیلنجنگ ڈیزائن کے تحفظات ہیں۔ ویکیوم بریزنگ ویکیوم کی بھٹی میں ہوتی ہے۔ درجہ حرارت کی یکسانیت برقرار ہے اور ہم بہت کم بقایا دباؤ کے ساتھ بہاؤ سے پاک، بہت صاف ستھرے جوڑ حاصل کرتے ہیں۔ ویکیوم بریزنگ کے دوران ہیٹ ٹریٹمنٹ ہو سکتا ہے، کیونکہ سست حرارتی اور کولنگ سائیکل کے دوران کم بقایا تناؤ موجود ہیں۔ بڑا نقصان اس کی زیادہ قیمت ہے کیونکہ ویکیوم ماحول کی تخلیق ایک مہنگا عمل ہے۔ پھر بھی ایک اور تکنیک DIP BRAZING فکسچرڈ حصوں کو جوڑتی ہے جہاں بریزنگ کمپاؤنڈ ملاوٹ کی سطحوں پر لگایا جاتا ہے۔ اس کے بعد fixtured حصوں کو پگھلے ہوئے نمک جیسے سوڈیم کلورائیڈ (ٹیبل نمک) کے غسل میں ڈبو دیا جاتا ہے جو گرمی کی منتقلی کے ذریعہ اور بہاؤ کے طور پر کام کرتا ہے۔ ہوا کو خارج کر دیا گیا ہے اور اس وجہ سے کوئی آکسائیڈ نہیں بنتا۔ انڈکشن بریزنگ میں ہم مواد کو فلر میٹل سے جوڑتے ہیں جس کا پگھلنے کا نقطہ بنیادی مواد سے کم ہوتا ہے۔ انڈکشن کوائل سے متبادل کرنٹ ایک برقی مقناطیسی فیلڈ بناتا ہے جو زیادہ تر فیرس مقناطیسی مواد پر انڈکشن ہیٹنگ کا باعث بنتا ہے۔ یہ طریقہ سلیکٹیو ہیٹنگ فراہم کرتا ہے، فلرز کے ساتھ اچھے جوڑ صرف مطلوبہ علاقوں میں بہتے ہیں، تھوڑا آکسیڈیشن ہے کیونکہ کوئی شعلے موجود نہیں ہیں اور کولنگ تیز، تیز حرارت، مستقل مزاجی اور اعلی حجم کی تیاری کے لیے موزوں ہے۔ اپنے عمل کو تیز کرنے اور مستقل مزاجی کو یقینی بنانے کے لیے ہم اکثر پرفارمز کا استعمال کرتے ہیں۔ سیرامک سے دھاتی فٹنگز، ہرمیٹک سیلنگ، ویکیوم فیڈ تھرو، ہائی اور الٹرا ہائی ویکیوم اور فلوئڈ کنٹرول اجزاء کے بارے میں معلومات یہاں حاصل کی جا سکتی ہیں:_cc781905-5cf58d_بریزنگ فیکٹری بروشر سولڈرنگ: سولڈرنگ میں ہمارے پاس کام کے ٹکڑوں کو پگھلنے کی ضرورت نہیں ہے، لیکن ایک فلر دھات ہے جو جوائنٹ میں بہتے ہوئے حصوں کے مقابلے میں کم پگھلنے کا مقام رکھتی ہے۔ سولڈرنگ میں فلر دھات بریزنگ کی نسبت کم درجہ حرارت پر پگھلتی ہے۔ ہم سولڈرنگ کے لیے لیڈ فری الائے استعمال کرتے ہیں اور RoHS کی تعمیل کرتے ہیں اور مختلف ایپلی کیشنز اور ضروریات کے لیے ہمارے پاس مختلف اور موزوں مرکبات ہیں جیسے سلور الائے۔ سولڈرنگ ہمیں جوڑوں کی پیشکش کرتا ہے جو گیس اور مائع سے تنگ ہیں۔ سوفٹ سولڈرنگ میں، ہماری فلر میٹل کا پگھلنے کا نقطہ 400 سینٹی گریڈ سے نیچے ہوتا ہے، جبکہ سلور سولڈرنگ اور بریزنگ میں ہمیں زیادہ درجہ حرارت کی ضرورت ہوتی ہے۔ نرم سولڈرنگ کم درجہ حرارت کا استعمال کرتا ہے لیکن اعلی درجہ حرارت پر ایپلی کیشنز کی مانگ کے لئے مضبوط جوڑوں کا نتیجہ نہیں ہوتا ہے۔ دوسری طرف سلور سولڈرنگ، ٹارچ کے ذریعہ فراہم کردہ اعلی درجہ حرارت کی ضرورت ہوتی ہے اور ہمیں اعلی درجہ حرارت کے استعمال کے لئے موزوں مضبوط جوڑ فراہم کرتی ہے۔ بریزنگ کے لیے سب سے زیادہ درجہ حرارت کی ضرورت ہوتی ہے اور عام طور پر ٹارچ استعمال کی جاتی ہے۔ چونکہ بریزنگ جوڑ بہت مضبوط ہوتے ہیں، اس لیے وہ لوہے کی بھاری چیزوں کی مرمت کے لیے اچھے امیدوار ہیں۔ ہماری مینوفیکچرنگ لائنوں میں ہم دستی ہینڈ سولڈرنگ کے ساتھ ساتھ خودکار سولڈر لائنز دونوں استعمال کرتے ہیں۔ INDUCTION سولڈرنگ انڈکشن ہیٹنگ کی سہولت کے لیے تانبے کے کوائل میں ہائی فریکوئنسی AC کرنٹ کا استعمال کرتی ہے۔ کرنٹ کو سولڈرڈ حصے میں شامل کیا جاتا ہے اور اس کے نتیجے میں ہائی ریزسٹنس joint پر حرارت پیدا ہوتی ہے۔ یہ گرمی فلر دھات کو پگھلا دیتی ہے۔ بہاؤ بھی استعمال کیا جاتا ہے. انڈکشن سولڈرنگ سائکلنڈرز اور پائپوں کے ارد گرد کنڈلیوں کو لپیٹ کر مسلسل عمل میں سولڈرنگ کا ایک اچھا طریقہ ہے۔ کچھ مواد جیسے گریفائٹ اور سیرامکس کو سولڈرنگ کرنا زیادہ مشکل ہے کیونکہ اس کے لیے سولڈرنگ سے پہلے کسی مناسب دھات کے ساتھ ورک پیس کو چڑھانا ضروری ہوتا ہے۔ یہ انٹرفیشل بانڈنگ کو آسان بناتا ہے۔ ہم خاص طور پر ہرمیٹک پیکیجنگ ایپلی کیشنز کے لیے ایسے مواد کو ٹانکا لگاتے ہیں۔ ہم زیادہ تر ویو سولڈرنگ کا استعمال کرتے ہوئے اپنے پرنٹ شدہ سرکٹ بورڈز (PCB) کو زیادہ حجم میں تیار کرتے ہیں۔ صرف پروٹو ٹائپنگ کے مقاصد کی تھوڑی مقدار کے لیے ہم سولڈرنگ آئرن کا استعمال کرتے ہوئے ہینڈ سولڈرنگ کا استعمال کرتے ہیں۔ ہم تھرو ہول کے ساتھ ساتھ سطح کے ماؤنٹ پی سی بی اسمبلیوں (PCBA) دونوں کے لیے ویو سولڈرنگ کا استعمال کرتے ہیں۔ ایک عارضی گوند اجزاء کو سرکٹ بورڈ سے منسلک رکھتا ہے اور اسمبلی کو کنویئر پر رکھا جاتا ہے اور ایک ایسے سامان سے گزرتا ہے جس میں پگھلا ہوا سولڈر ہوتا ہے۔ پہلے پی سی بی کو بہایا جاتا ہے اور پھر پری ہیٹنگ زون میں داخل ہوتا ہے۔ پگھلا ہوا ٹانکا ایک پین میں ہے اور اس کی سطح پر کھڑی لہروں کا نمونہ ہے۔ جب پی سی بی ان لہروں پر حرکت کرتا ہے تو یہ لہریں پی سی بی کے نیچے سے رابطہ کرتی ہیں اور سولڈرنگ پیڈ سے چپک جاتی ہیں۔ ٹانکا لگانا صرف پنوں اور پیڈوں پر رہتا ہے نہ کہ خود پی سی بی پر۔ پگھلے ہوئے سولڈر میں لہروں کو اچھی طرح سے کنٹرول کرنا ہوتا ہے تاکہ کوئی چھڑکاؤ نہ ہو اور لہروں کی چوٹی بورڈ کے ناپسندیدہ علاقوں کو چھونے اور آلودہ نہ کرے۔ REFLOW سولڈرنگ میں، ہم بورڈز کے ساتھ الیکٹرانک اجزاء کو عارضی طور پر منسلک کرنے کے لیے ایک چپچپا سولڈر پیسٹ استعمال کرتے ہیں۔ پھر بورڈز کو ریفلو اوون کے ذریعے درجہ حرارت کنٹرول کے ساتھ ڈالا جاتا ہے۔ یہاں سولڈر پگھل جاتا ہے اور اجزاء کو مستقل طور پر جوڑتا ہے۔ ہم اس تکنیک کو سطح کے ماؤنٹ اجزاء کے ساتھ ساتھ سوراخ والے اجزاء کے لیے استعمال کرتے ہیں۔ بورڈ پر الیکٹرانک اجزاء کو ان کی زیادہ سے زیادہ درجہ حرارت کی حد سے زیادہ گرم کرکے تباہ ہونے سے بچنے کے لیے تندور کے درجہ حرارت کا مناسب کنٹرول اور ایڈجسٹمنٹ ضروری ہے۔ ریفلو سولڈرنگ کے عمل میں ہمارے پاس دراصل کئی علاقے یا مراحل ہوتے ہیں جن میں سے ہر ایک کا ایک الگ تھرمل پروفائل ہوتا ہے، جیسے پری ہیٹنگ سٹیپ، تھرمل سوکنگ سٹیپ، ری فلو اور کولنگ سٹیپ۔ پرنٹ شدہ سرکٹ بورڈ اسمبلیوں (PCBA) کے نقصان سے پاک ری فلو سولڈرنگ کے لیے یہ مختلف اقدامات ضروری ہیں۔ ULTRASONIC سولڈرنگ منفرد صلاحیتوں کے ساتھ کثرت سے استعمال ہونے والی ایک اور تکنیک ہے- اسے گلاس، سیرامک اور غیر دھاتی مواد کو ٹانکا لگانے کے لیے استعمال کیا جا سکتا ہے۔ مثال کے طور پر فوٹو وولٹک پینل جو غیر دھاتی ہوتے ہیں ان کو الیکٹروڈ کی ضرورت ہوتی ہے جو اس تکنیک کا استعمال کرتے ہوئے چسپاں ہو سکتے ہیں۔ الٹراسونک سولڈرنگ میں، ہم ایک گرم سولڈرنگ ٹپ لگاتے ہیں جو الٹراسونک کمپن بھی خارج کرتی ہے۔ یہ کمپن پگھلے ہوئے سولڈر مواد کے ساتھ سبسٹریٹ کے انٹرفیس پر cavitation بلبلے پیدا کرتی ہے۔ کاویٹیشن کی دھماکا خیز توانائی آکسائڈ کی سطح کو تبدیل کرتی ہے اور گندگی اور آکسائڈز کو ہٹاتی ہے۔ اس دوران ایک کھوٹ کی تہہ بھی بنتی ہے۔ بانڈنگ سطح پر ٹانکا لگانا آکسیجن کو شامل کرتا ہے اور شیشے اور سولڈر کے درمیان ایک مضبوط مشترکہ بانڈ کی تشکیل کے قابل بناتا ہے۔ ڈپ سولڈرنگ کو لہر سولڈرنگ کا ایک آسان ورژن سمجھا جا سکتا ہے جو صرف چھوٹے پیمانے پر پیداوار کے لیے موزوں ہے۔ پہلے صفائی کا بہاؤ دوسرے عمل کی طرح لگایا جاتا ہے۔ نصب اجزاء کے ساتھ PCBs کو دستی طور پر یا نیم خودکار انداز میں ایک ٹینک میں ڈبو دیا جاتا ہے جس میں پگھلا ہوا سولڈر ہوتا ہے۔ پگھلا ہوا ٹانکا لگا ہوا دھاتی علاقوں سے چپک جاتا ہے جو بورڈ پر ٹانکا لگانے والے ماسک سے غیر محفوظ ہوتا ہے۔ سامان سادہ اور سستا ہے۔ • چپکنے والی بانڈنگ: یہ ایک اور مقبول تکنیک ہے جسے ہم اکثر استعمال کرتے ہیں اور اس میں گوندوں، ایپوکس، پلاسٹک ایجنٹوں یا دیگر کیمیکلز کا استعمال کرتے ہوئے سطحوں کو جوڑنا شامل ہے۔ بانڈنگ یا تو سالوینٹ کو بخارات بنا کر، ہیٹ کیورنگ کے ذریعے، یووی لائٹ کیورنگ کے ذریعے، پریشر کیورنگ کے ذریعے یا کسی خاص وقت کے انتظار کے ذریعے مکمل کیا جاتا ہے۔ ہماری پروڈکشن لائنوں میں مختلف اعلی کارکردگی والے گلوز استعمال کیے جاتے ہیں۔ مناسب طریقے سے انجینئرڈ ایپلی کیشن اور علاج کے عمل کے ساتھ، چپکنے والی بانڈنگ کے نتیجے میں بہت کم تناؤ والے بانڈ ہوسکتے ہیں جو مضبوط اور قابل اعتماد ہیں۔ چپکنے والے بانڈز ماحولیاتی عوامل جیسے نمی، آلودگی، corrosives، کمپن... وغیرہ کے خلاف اچھے محافظ ہو سکتے ہیں۔ چپکنے والی بانڈنگ کے فوائد ہیں: وہ ایسے مواد پر لاگو کیے جا سکتے ہیں جو دوسری صورت میں ٹانکا لگانا، ویلڈ یا بریز کرنا مشکل ہو گا۔ اس کے علاوہ یہ گرمی کے حساس مواد کے لیے بھی بہتر ہو سکتا ہے جو ویلڈنگ یا دیگر اعلی درجہ حرارت کے عمل سے خراب ہو جائیں گے۔ چپکنے والی چیزوں کے دیگر فوائد یہ ہیں کہ ان کو فاسد شکل کی سطحوں پر لگایا جا سکتا ہے اور دیگر طریقوں کے مقابلے میں اسمبلی کے وزن میں بہت کم مقدار میں اضافہ کیا جا سکتا ہے۔ اس کے علاوہ حصوں میں جہتی تبدیلیاں بہت کم ہیں۔ کچھ گلوز میں انڈیکس مماثل خصوصیات ہیں اور روشنی یا آپٹیکل سگنل کی طاقت کو نمایاں طور پر کم کیے بغیر آپٹیکل اجزاء کے درمیان استعمال کیا جا سکتا ہے۔ دوسری طرف نقصانات طویل علاج کے اوقات ہیں جو مینوفیکچرنگ لائنوں، فکسچرنگ کی ضروریات، سطح کی تیاری کے تقاضوں اور دوبارہ کام کی ضرورت پڑنے پر الگ کرنے میں دشواری کا باعث بن سکتے ہیں۔ ہمارے زیادہ تر چپکنے والی بانڈنگ آپریشنز میں درج ذیل اقدامات شامل ہیں: سطح کا علاج: صفائی کے خصوصی طریقہ کار جیسے ڈیونائزڈ پانی کی صفائی، الکحل کی صفائی، پلازما یا کورونا کی صفائی عام ہے۔ صفائی کے بعد ہم بہترین ممکنہ جوڑوں کو یقینی بنانے کے لیے سطحوں پر آسنجن پروموٹرز لگا سکتے ہیں۔ -پارٹ فکسچرنگ: چپکنے والی ایپلی کیشن کے ساتھ ساتھ علاج کے لیے ہم اپنی مرضی کے مطابق فکسچر ڈیزائن اور استعمال کرتے ہیں۔ چپکنے والی ایپلی کیشن: ہم بعض اوقات دستی استعمال کرتے ہیں، اور بعض اوقات کیس آٹومیٹڈ سسٹمز جیسے کہ روبوٹکس، سروو موٹرز، لکیری ایکچویٹرز پر انحصار کرتے ہوئے چپکنے والی چیزوں کو صحیح جگہ پر پہنچاتے ہیں اور ہم اسے صحیح حجم اور مقدار میں پہنچانے کے لیے ڈسپنسر کا استعمال کرتے ہیں۔ -کیورنگ: چپکنے والی چیز پر منحصر ہے، ہم سادہ خشک کرنے اور کیورنگ کے ساتھ ساتھ UV لائٹس کے نیچے کیورنگ کا استعمال کر سکتے ہیں جو تندور میں کیٹالسٹ یا ہیٹ کیورنگ کے طور پر کام کرتی ہیں یا جیگس اور فکسچر پر نصب مزاحمتی حرارتی عناصر کا استعمال کرتی ہیں۔ ہمارا مشورہ ہے کہ آپ یہاں کلک کریں۔AGS-TECH Inc کے ذریعے بندھن کے عمل کی ہماری اسکیمیٹک تصویریں ڈاؤن لوڈ کریں۔ اس سے آپ کو ان معلومات کو بہتر طریقے سے سمجھنے میں مدد ملے گی جو ہم آپ کو ذیل میں فراہم کر رہے ہیں۔ • باندھنے کے عمل: ہمارے مکینیکل جوائننگ کے عمل دو بریڈ کیٹیگریز میں آتے ہیں: فاسٹنرز اور انٹیگرل جوائنٹس۔ فاسٹنرز کی مثالیں جو ہم استعمال کرتے ہیں وہ ہیں پیچ، پن، نٹ، بولٹ، ریوٹس۔ انٹیگرل جوڑوں کی مثالیں جو ہم استعمال کرتے ہیں وہ ہیں سنیپ اور سکڑ فٹ، سیون، کرمپس۔ باندھنے کے مختلف طریقوں کا استعمال کرتے ہوئے ہم اس بات کو یقینی بناتے ہیں کہ ہمارے مکینیکل جوڑ کئی سالوں کے استعمال کے لیے مضبوط اور قابل اعتماد ہیں۔ SCREWS اور BOLTS اشیاء کو ایک ساتھ رکھنے اور پوزیشننگ کے لیے سب سے زیادہ استعمال ہونے والے فاسٹنر ہیں۔ ہمارے پیچ اور بولٹ ASME معیارات پر پورا اترتے ہیں۔ مختلف قسم کے سکرو اور بولٹ لگائے گئے ہیں جن میں ہیکس کیپ سکرو اور ہیکس بولٹ، لگ سکرو اور بولٹ، ڈبل اینڈڈ اسکرو، ڈویل اسکرو، آئی اسکرو، مرر اسکرو، شیٹ میٹل اسکرو، فائن ایڈجسٹمنٹ اسکرو، سیلف ڈرلنگ اور سیلف ٹیپنگ اسکرو شامل ہیں۔ ، سیٹ سکرو، بلٹ ان واشرز کے ساتھ پیچ، اور مزید۔ ہمارے پاس اسکرو ہیڈ کی مختلف اقسام ہیں جیسے کاؤنٹر سنک، ڈوم، گول، فلینجڈ ہیڈ اور مختلف اسکرو ڈرائیو کی اقسام جیسے سلاٹ، فلپس، اسکوائر، ہیکس ساکٹ۔ دوسری طرف ایک RIVET ایک مستقل مکینیکل فاسٹنر ہے جس میں ایک طرف ہموار بیلناکار شافٹ اور ایک سر ہوتا ہے۔ داخل کرنے کے بعد، rivet کے دوسرے سرے کو بگاڑ دیا جاتا ہے اور اس کے قطر کو پھیلایا جاتا ہے تاکہ یہ اپنی جگہ پر قائم رہے۔ دوسرے لفظوں میں، تنصیب سے پہلے ایک ریوٹ کا ایک سر ہوتا ہے اور تنصیب کے بعد اس کے دو ہوتے ہیں۔ ہم استعمال، طاقت، رسائی اور لاگت کے لحاظ سے مختلف قسم کے rivets انسٹال کرتے ہیں جیسے کہ ٹھوس/گول ہیڈ ریوٹس، سٹرکچرل، نیم نلی نما، بلائنڈ، آسکر، ڈرائیو، فلش، رگڑ لاک، خود چھیدنے والے rivets۔ ریوٹنگ کو ان صورتوں میں ترجیح دی جا سکتی ہے جہاں گرمی کی خرابی اور ویلڈنگ کی گرمی کی وجہ سے مادی خصوصیات میں تبدیلی سے گریز کرنا ضروری ہے۔ Riveting ہلکے وزن اور خاص طور پر اچھی طاقت اور قینچ کی قوتوں کے خلاف برداشت بھی پیش کرتا ہے۔ ٹینسائل بوجھ کے خلاف تاہم پیچ، نٹ اور بولٹ زیادہ موزوں ہو سکتے ہیں۔ کلینچنگ کے عمل میں ہم شیٹ میٹلز کو جوڑنے کے درمیان ایک مکینیکل انٹر لاک بنانے کے لیے خصوصی پنچ اور ڈیز کا استعمال کرتے ہیں۔ پنچ شیٹ میٹل کی تہوں کو ڈائی کیویٹی میں دھکیلتا ہے اور اس کے نتیجے میں مستقل جوڑ بن جاتا ہے۔ کلینچنگ میں نہ ہیٹنگ اور نہ ہی کولنگ کی ضرورت ہوتی ہے اور یہ ایک ٹھنڈا کام کرنے والا عمل ہے۔ یہ ایک اقتصادی عمل ہے جو کچھ معاملات میں اسپاٹ ویلڈنگ کی جگہ لے سکتا ہے۔ پننگ میں ہم پنوں کا استعمال کرتے ہیں جو مشین کے عناصر ہیں جو ایک دوسرے کے نسبت مشین کے پرزوں کی پوزیشن کو محفوظ کرنے کے لیے استعمال ہوتے ہیں۔ کلیویس پن، کوٹر پن، اسپرنگ پن، ڈوول پن، اور اسپلٹ پن کی بڑی اقسام ہیں۔ STAPLING میں ہم سٹیپلنگ گن اور سٹیپل استعمال کرتے ہیں جو کہ دو جہتی فاسٹنر ہیں جو مواد کو جوڑنے یا باندھنے کے لیے استعمال ہوتے ہیں۔ اسٹیپلنگ کے درج ذیل فوائد ہیں: اقتصادی، آسان اور استعمال میں تیز، اسٹیپل کا تاج ایک ساتھ بٹے ہوئے مواد کو پُلانے کے لیے استعمال کیا جا سکتا ہے، اسٹیپل کا تاج کسی کیبل جیسے ٹکڑے کو پلنے اور اسے پنکچر یا پنکچر کیے بغیر کسی سطح پر باندھنے میں سہولت فراہم کرتا ہے۔ نقصان دہ، نسبتاً آسان ہٹانا۔ پریس فٹنگ حصوں کو ایک ساتھ دھکیل کر انجام دی جاتی ہے اور ان کے درمیان رگڑ حصوں کو مضبوط کرتی ہے۔ بڑے سائز کے شافٹ اور چھوٹے سوراخ پر مشتمل پریس فٹ حصوں کو عام طور پر دو طریقوں میں سے ایک کے ذریعے جمع کیا جاتا ہے: یا تو طاقت کا استعمال کرتے ہوئے یا تھرمل توسیع یا حصوں کے سنکچن کا فائدہ اٹھا کر۔ جب طاقت کا استعمال کرکے پریس فٹنگ قائم کی جاتی ہے، تو ہم یا تو ہائیڈرولک پریس یا ہاتھ سے چلنے والی پریس کا استعمال کرتے ہیں۔ دوسری طرف جب تھرمل توسیع کے ذریعے پریس فٹنگ قائم کی جاتی ہے تو ہم لفافے کے حصوں کو گرم کرتے ہیں اور گرم ہونے پر انہیں اپنی جگہ پر جمع کرتے ہیں۔ جب وہ ٹھنڈا ہو جاتے ہیں تو وہ سکڑ جاتے ہیں اور اپنے معمول کے طول و عرض پر واپس آجاتے ہیں۔ اس کے نتیجے میں ایک اچھی پریس فٹ ہوتی ہے۔ ہم اسے متبادل طور پر SHRINK-FITTING کہتے ہیں۔ ایسا کرنے کا دوسرا طریقہ یہ ہے کہ لفافے والے حصوں کو اسمبلی سے پہلے ٹھنڈا کریں اور پھر ان کے ملن حصوں میں سلائیڈ کریں۔ جب اسمبلی گرم ہوتی ہے تو وہ پھیل جاتی ہیں اور ہم ایک مضبوط فٹ حاصل کرتے ہیں۔ یہ مؤخر الذکر طریقہ ان صورتوں میں بہتر ہو سکتا ہے جہاں حرارت سے مادی خصوصیات میں تبدیلی کا خطرہ ہو۔ ان صورتوں میں کولنگ زیادہ محفوظ ہے۔ نیومیٹک اور ہائیڈرولک اجزاء اور اسمبلیاں • والوز، ہائیڈرولک اور نیومیٹک اجزاء جیسے O-ring، واشر، سیل، گسکیٹ، انگوٹی، شیم۔ چونکہ والوز اور نیومیٹک اجزاء ایک بڑی قسم میں آتے ہیں، ہم یہاں ہر چیز کی فہرست نہیں دے سکتے۔ آپ کی درخواست کے جسمانی اور کیمیائی ماحول پر منحصر ہے، ہمارے پاس آپ کے لیے خصوصی مصنوعات ہیں۔ براہ کرم ہمیں درخواست، اجزاء کی قسم، وضاحتیں، ماحولیاتی حالات جیسے دباؤ، درجہ حرارت، مائعات یا گیسیں بتائیں جو آپ کے والوز اور نیومیٹک اجزاء کے ساتھ رابطے میں ہوں گی۔ اور ہم آپ کے لیے موزوں ترین پروڈکٹ کا انتخاب کریں گے یا آپ کی درخواست کے لیے اسے خاص طور پر تیار کریں گے۔ CLICK Product Finder-Locator Service پچھلا صفحہ
- Transmission Components, Belts, Chains, Cable Drives, Pulleys,AGS-TECH
Transmission Components, Belts, Chains and Cable Drives, Conventional & Grooved or Serrated, Positive Drive, Pulleys بیلٹ اور چینز اور کیبل ڈرائیو اسمبلی AGS-TECH Inc. آپ کو بیلٹ اور چینز اور کیبل ڈرائیو اسمبلی سمیت پاور ٹرانسمیشن کے اجزاء پیش کرتا ہے۔ برسوں کی تطہیر کے ساتھ، ہماری ربڑ، چمڑے اور دیگر بیلٹ ڈرائیوز ہلکی اور زیادہ کمپیکٹ ہو گئی ہیں، جو کم قیمت پر زیادہ بوجھ اٹھانے کی صلاحیت رکھتی ہیں۔ اسی طرح، ہماری چین ڈرائیوز وقت کے ساتھ ساتھ بہت زیادہ ترقی سے گزری ہیں اور وہ ہمارے صارفین کو کئی فوائد فراہم کرتی ہیں۔ چین ڈرائیوز کے استعمال کے کچھ فوائد ان کے نسبتاً غیر محدود شافٹ سینٹر کے فاصلے، کمپیکٹ پن، اسمبلی میں آسانی، پھسلن یا رینگنے کے بغیر تناؤ میں لچک، اعلی درجہ حرارت والے ماحول میں کام کرنے کی صلاحیت ہیں۔ ہماری کیبل ڈرائیوز دیگر قسم کے ٹرانسمیشن اجزاء پر کچھ ایپلی کیشنز میں سادگی جیسے فوائد بھی پیش کرتی ہیں۔ آف شیلف بیلٹ، چین اور کیبل ڈرائیوز کے ساتھ ساتھ حسب ضرورت من گھڑت اور اسمبل شدہ ورژن دونوں دستیاب ہیں۔ ہم ان ٹرانسمیشن اجزاء کو آپ کی درخواست کے لیے صحیح سائز میں اور انتہائی موزوں مواد سے تیار کر سکتے ہیں۔ بیلٹس اور بیلٹ ڈرائیوز: - روایتی فلیٹ بیلٹ: یہ دانتوں، نالیوں یا سیریشن کے بغیر سادہ فلیٹ بیلٹ ہیں۔ فلیٹ بیلٹ ڈرائیوز لچک، اچھا جھٹکا جذب، تیز رفتاری پر موثر پاور ٹرانسمیشن، رگڑنے کے خلاف مزاحمت، کم قیمت پیش کرتے ہیں۔ بڑی بیلٹ بنانے کے لیے بیلٹ کو الگ کیا جا سکتا ہے یا جوڑا جا سکتا ہے۔ روایتی فلیٹ بیلٹ کے دیگر فوائد یہ ہیں کہ وہ پتلے ہوتے ہیں، وہ زیادہ سینٹری فیوگل بوجھ کے تابع نہیں ہوتے ہیں (چھوٹی پلیوں کے ساتھ تیز رفتار آپریشن کے لیے انہیں اچھا بناتا ہے)۔ دوسری طرف وہ زیادہ بیئرنگ بوجھ لگاتے ہیں کیونکہ فلیٹ بیلٹ کو زیادہ تناؤ کی ضرورت ہوتی ہے۔ فلیٹ بیلٹ ڈرائیوز کے دیگر نقصانات پھسلنا، شور والا آپریشن، اور آپریشن کی کم اور درمیانی رفتار پر نسبتاً کم افادیت ہو سکتا ہے۔ ہمارے پاس دو قسم کے روایتی بیلٹ ہیں: مضبوط اور غیر مضبوط۔ مضبوط بیلٹ کی ساخت میں تناؤ کا رکن ہوتا ہے۔ روایتی فلیٹ بیلٹ چمڑے، ربڑ والے کپڑے یا ڈوری، غیر مضبوط ربڑ یا پلاسٹک، فیبرک، مضبوط چمڑے کے طور پر دستیاب ہیں۔ چمڑے کی بیلٹ لمبی زندگی، لچک، رگڑ کا بہترین گتانک، آسان مرمت پیش کرتے ہیں۔ تاہم چمڑے کی بیلٹ نسبتاً مہنگی ہوتی ہیں، بیلٹ کو ڈریسنگ اور صفائی کی ضرورت ہوتی ہے، اور ماحول کے لحاظ سے وہ سکڑ یا پھیل سکتے ہیں۔ ربڑ کے بنے ہوئے تانے بانے یا ہڈی کے بیلٹ نمی، تیزاب اور الکلیس کے خلاف مزاحم ہوتے ہیں۔ ربڑ کے بنے ہوئے فیبرک بیلٹس کپاس کے پلیز یا ربڑ سے رنگین مصنوعی بطخ سے بنے ہوتے ہیں اور سب سے زیادہ کفایتی ہوتے ہیں۔ ربڑ کی ڈوری کی بیلٹ ربڑ کی رنگدار ڈوریوں کی ایک سیریز پر مشتمل ہوتی ہے۔ ربڑ کی ہڈی کے بیلٹ اعلی تناؤ کی طاقت اور معمولی سائز اور بڑے پیمانے پر پیش کرتے ہیں۔ غیر مضبوط ربڑ یا پلاسٹک کی بیلٹ لائٹ ڈیوٹی، کم رفتار ڈرائیو ایپلی کیشنز کے لیے موزوں ہیں۔ غیر مضبوط ربڑ اور پلاسٹک کی بیلٹوں کو ان کی پلیوں پر جگہ پر پھیلایا جا سکتا ہے۔ ربڑ بیلٹ کے مقابلے میں پلاسٹک کے غیر مضبوط بیلٹ زیادہ طاقت منتقل کر سکتے ہیں۔ مضبوط چمڑے کے بیلٹ چمڑے کے اوپر اور نیچے کی تہوں کے درمیان سینڈویچ والے پلاسٹک کے ٹینسائل ممبر پر مشتمل ہوتے ہیں۔ آخر میں، ہمارے تانے بانے کی بیلٹ روئی کے ایک ٹکڑے پر مشتمل ہو سکتی ہے یا بطخ کو جوڑ کر اور طولانی سلائیوں کی قطاروں کے ساتھ سلائی ہوئی ہے۔ فیبرک بیلٹ یکساں طور پر ٹریک کرنے اور تیز رفتاری سے کام کرنے کے قابل ہیں۔ - نالیوں والی یا سیرٹیڈ بیلٹس (جیسے V-Belts): یہ بنیادی فلیٹ بیلٹ ہیں جن میں کسی اور قسم کی ٹرانسمیشن پروڈکٹ کے فوائد فراہم کرنے کے لیے ترمیم کی گئی ہے۔ یہ فلیٹ بیلٹ ہیں جن کے نیچے طولانی طور پر پسلی لگی ہوئی ہے۔ Poly-V بیلٹ طولانی طور پر نالیوں والی یا سیرٹیڈ فلیٹ بیلٹ ہوتی ہے جس میں ٹینسائل سیکشن ہوتا ہے اور ٹریکنگ اور کمپریشن کے مقاصد کے لیے ملحقہ V کے سائز کے نالیوں کی ایک سیریز ہوتی ہے۔ بجلی کی صلاحیت بیلٹ کی چوڑائی پر منحصر ہے۔ وی بیلٹ انڈسٹری کا ورک ہارس ہے اور تقریباً کسی بھی لوڈ پاور کی ترسیل کے لیے مختلف قسم کے معیاری سائز اور اقسام میں دستیاب ہے۔ وی بیلٹ ڈرائیو 1500 سے 6000 فٹ فی منٹ کے درمیان اچھی طرح چلتی ہے، تاہم تنگ وی بیلٹ 10,000 فٹ فی منٹ تک کام کرے گی۔ وی بیلٹ ڈرائیوز 3 سے 5 سال کی لمبی زندگی پیش کرتی ہیں اور بڑی رفتار کے تناسب کی اجازت دیتی ہیں، وہ انسٹال اور ہٹانے میں آسان ہیں، بیلٹ ڈرائیور اور چلنے والی شافٹ کے درمیان پرسکون آپریشن، کم دیکھ بھال، اچھا جھٹکا جذب کرنے کی پیشکش کرتے ہیں۔ وی بیلٹس کا نقصان ان کی مخصوص پھسلنا اور رینگنا ہے اور اس لیے وہ بہترین حل نہیں ہو سکتے جہاں ہم وقت ساز رفتار کی ضرورت ہو۔ ہمارے پاس صنعتی، آٹوموٹو اور زرعی بیلٹ ہیں۔ اسٹاک شدہ معیاری لمبائی کے ساتھ ساتھ بیلٹ کی اپنی مرضی کی لمبائی دستیاب ہیں۔ تمام معیاری وی بیلٹ کراس سیکشن اسٹاک سے دستیاب ہیں۔ ایسی میزیں ہیں جہاں آپ نامعلوم پیرامیٹرز جیسے بیلٹ کی لمبائی، بیلٹ سیکشن (چوڑائی اور موٹائی) کا حساب لگا سکتے ہیں بشرطیکہ آپ اپنے سسٹم کے کچھ پیرامیٹرز کو جانتے ہوں جیسے ڈرائیونگ اور چلائے گئے پللی کے قطر، پلیوں کے درمیان درمیانی فاصلہ اور پلیوں کی گردش کی رفتار۔ آپ ایسی میزیں استعمال کر سکتے ہیں یا ہم سے اپنے لیے صحیح V-بیلٹ منتخب کرنے کے لیے کہہ سکتے ہیں۔ - مثبت ڈرائیو بیلٹس (ٹائمنگ بیلٹ): یہ بیلٹ بھی فلیٹ قسم کے ہوتے ہیں جن کے اندر کے فریم پر یکساں فاصلے والے دانتوں کی ایک سیریز ہوتی ہے۔ مثبت ڈرائیو یا ٹائمنگ بیلٹس فلیٹ بیلٹ کے فوائد کو زنجیروں اور گیئرز کی مثبت گرفت کی خصوصیات کے ساتھ جوڑتی ہیں۔ مثبت ڈرائیو بیلٹ کسی پھسلن یا رفتار کے تغیرات کو ظاہر نہیں کرتے ہیں۔ رفتار کے تناسب کی ایک وسیع رینج ممکن ہے۔ بیئرنگ بوجھ کم ہیں کیونکہ وہ کم تناؤ پر کام کر سکتے ہیں۔ تاہم وہ پلیوں میں غلط ترتیب کے لیے زیادہ حساس ہوتے ہیں۔ - پلیاں، شیوز، بیلٹ کے لیے حب: فلیٹ، پسلیوں والی (سیریٹڈ) اور مثبت ڈرائیو بیلٹ کے ساتھ مختلف قسم کی پلیاں استعمال کی جاتی ہیں۔ ہم ان سب کو تیار کرتے ہیں۔ ہماری زیادہ تر فلیٹ بیلٹ پللیاں لوہے کو ڈال کر بنائی جاتی ہیں، لیکن اسٹیل کے ورژن بھی مختلف رم اور حب کے امتزاج میں دستیاب ہیں۔ ہماری فلیٹ بیلٹ پللیوں میں ٹھوس، بولڈ یا سپلٹ ہب ہو سکتے ہیں یا ہم آپ کی مرضی کے مطابق تیار کر سکتے ہیں۔ Ribbed اور مثبت ڈرائیو بیلٹ مختلف قسم کے اسٹاک سائز اور چوڑائی میں دستیاب ہیں۔ ٹائمنگ بیلٹ ڈرائیوز میں کم از کم ایک گھرنی کو بیلٹ کو ڈرائیو پر رکھنے کے لیے فلانگ کیا جانا چاہیے۔ لانگ سینٹر ڈرائیو سسٹمز کے لیے، یہ تجویز کیا جاتا ہے کہ دونوں پلیوں کو فلانگ کیا جائے۔ شیو پللیوں کے نالے ہوئے پہیے ہیں اور عام طور پر لوہے کی کاسٹنگ، اسٹیل کی تشکیل یا پلاسٹک مولڈنگ کے ذریعہ تیار کیے جاتے ہیں۔ اسٹیل کی تشکیل آٹوموٹو اور زرعی شیفوں کی تیاری کے لیے موزوں عمل ہے۔ ہم باقاعدہ اور گہری نالیوں کے ساتھ شیو تیار کرتے ہیں۔ جب وی بیلٹ شیو میں کسی زاویے سے داخل ہوتی ہے تو گہری نالی والی شیو مناسب ہوتی ہیں، جیسا کہ کوارٹر ٹرن ڈرائیوز میں ہوتا ہے۔ گہری نالی عمودی شافٹ ڈرائیوز اور ایپلی کیشنز کے لیے بھی موزوں ہیں جہاں بیلٹ کی کمپن ایک مسئلہ ہو سکتی ہے۔ ہماری بے کار پلیاں نالیوں والی شیو یا چپٹی پلیاں ہیں جو میکانکی طاقت کی ترسیل کا کام نہیں کرتی ہیں۔ آئیڈلر پلیاں زیادہ تر بیلٹ کو سخت کرنے کے لیے استعمال ہوتی ہیں۔ - سنگل اور ایک سے زیادہ بیلٹ ڈرائیوز: سنگل بیلٹ ڈرائیوز میں ایک ہی نالی ہوتی ہے جبکہ ایک سے زیادہ بیلٹ ڈرائیوز میں ایک سے زیادہ گرووز ہوتے ہیں۔ ذیل میں متعلقہ رنگین متن پر کلک کر کے آپ ہمارے کیٹلاگ ڈاؤن لوڈ کر سکتے ہیں: - پاور ٹرانسمیشن بیلٹس (جس میں وی بیلٹس، ٹائمنگ بیلٹس، را ایج بیلٹس، لپیٹے ہوئے بیلٹ اور خاص بیلٹ شامل ہیں) - کنویئر بیلٹس --.وی پلیز n - ٹائمنگ پلیز زنجیریں اور زنجیریں: ہماری پاور ٹرانسمیشن چینز کے کچھ فوائد ہیں جیسے کہ نسبتاً غیر محدود شافٹ سینٹر کے فاصلے، آسان اسمبلی، کمپیکٹ پن، بغیر پھسلن یا رینگنے کے تناؤ میں لچک، زیادہ درجہ حرارت میں کام کرنے کی صلاحیت۔ یہاں ہماری زنجیروں کی اہم اقسام ہیں: - ڈیٹیچ ایبل چینز: ہماری ڈیٹیچ ایبل زنجیریں مختلف سائز، پچ اور حتمی طاقت اور عام طور پر خراب آئرن یا اسٹیل سے بنی ہیں۔ قابل عمل زنجیریں 0.902 (23 ملی میٹر) سے 4.063 انچ (103 ملی میٹر) پچ اور حتمی طاقت 700 سے 17,000 پونڈ/مربع انچ تک مختلف سائز میں بنائی جاتی ہیں۔ دوسری طرف ہماری الگ ہونے والی سٹیل کی زنجیریں پچ میں 0.904 انچ (23 ملی میٹر) سے تقریباً 3.00 انچ (76 ملی میٹر) کے سائز میں بنائی گئی ہیں، جس کی حتمی طاقت 760 سے 5000 پونڈ/مربع انچ تک ہے۔_cc781905-5cde-3194-3bb-3 136bad5cf58d_ - پنٹل چینز: یہ زنجیریں زیادہ بوجھ اور قدرے زیادہ رفتار کے لیے تقریباً 450 فٹ فی منٹ (2.2 میٹر/سیکنڈ) استعمال ہوتی ہیں۔ پنٹل چینز انفرادی کاسٹ لنکس سے بنی ہوتی ہیں جن میں مکمل، گول بیرل اینڈ آف سیٹ سائڈبارز ہوتے ہیں۔ یہ زنجیر کے لنکس اسٹیل پنوں کے ساتھ جڑے ہوئے ہیں۔ یہ زنجیریں پچ میں تقریباً 1.00 انچ (25 ملی میٹر) سے 6.00 انچ (150 ملی میٹر) اور حتمی طاقت 3600 سے 30,000 پونڈ/مربع انچ کے درمیان ہوتی ہیں۔ - آفسیٹ سائڈبار چینز: یہ تعمیراتی مشینری کی ڈرائیو چینز میں مقبول ہیں۔ یہ زنجیریں 1000 فٹ فی منٹ کی رفتار سے کام کرتی ہیں اور بوجھ کو تقریباً 250 ایچ پی تک منتقل کرتی ہیں۔ عام طور پر ہر لنک میں دو آفسیٹ سائڈبارز ہوتے ہیں، ایک بشنگ، ایک رولر، ایک پن، ایک کوٹر پن۔ - رولر چینز: یہ 0.25 (6 ملی میٹر) سے 3.00 (75 ملی میٹر) انچ تک کی پچوں میں دستیاب ہیں۔ واحد چوڑائی والی رولر زنجیروں کی حتمی طاقت 925 سے 130,000 lb/مربع انچ کے درمیان ہوتی ہے۔ رولر زنجیروں کے متعدد چوڑائی والے ورژن دستیاب ہیں اور زیادہ رفتار سے زیادہ طاقت منتقل کرتے ہیں۔ ایک سے زیادہ چوڑائی والی رولر زنجیریں کم شور کے ساتھ ہموار کارروائی بھی پیش کرتی ہیں۔ رولر زنجیروں کو رولر لنکس اور پن لنکس سے جمع کیا جاتا ہے۔ کوٹر پنوں کو ڈیٹیچ ایبل ورژن رولر چینز میں استعمال کیا جاتا ہے۔ رولر چین ڈرائیوز کے ڈیزائن کو موضوع کی مہارت کی ضرورت ہوتی ہے۔ جہاں بیلٹ ڈرائیوز لکیری رفتار پر مبنی ہوتی ہیں، چین ڈرائیوز چھوٹے سپروکیٹ کی گردشی رفتار پر مبنی ہوتی ہیں، جو زیادہ تر تنصیبات میں چلنے والے رکن کی ہوتی ہے۔ ہارس پاور کی درجہ بندی اور گردشی رفتار کے علاوہ، چین ڈرائیوز کا ڈیزائن بہت سے دوسرے عوامل پر مبنی ہے۔ - ڈبل پچ زنجیریں: بنیادی طور پر رولر چینز جیسی ہی ہوتی ہیں سوائے اس کے کہ پچ دو گنا لمبی ہو۔ - الٹا دانت (خاموش) زنجیریں: تیز رفتار زنجیریں زیادہ تر پرائم موور، پاور ٹیک آف ڈرائیوز کے لیے استعمال ہوتی ہیں۔ الٹی ٹوتھ چین ڈرائیوز 1200 ایچ پی تک طاقتیں منتقل کر سکتی ہیں اور دانتوں کے لنکس کی ایک سیریز سے بنی ہوتی ہیں، باری باری پنوں یا مشترکہ اجزاء کے مجموعہ کے ساتھ جمع ہوتی ہیں۔ سینٹر گائیڈ چین میں اسپروکیٹ میں گرووز کو شامل کرنے کے لیے گائیڈ لنکس ہوتے ہیں، اور سائیڈ گائیڈ چین میں سپروکیٹ کے اطراف کو منسلک کرنے کے لیے گائیڈز ہوتے ہیں۔ - بیڈ یا سلائیڈر چینز: یہ زنجیریں سست رفتار ڈرائیوز اور دستی آپریشنز میں بھی استعمال ہوتی ہیں۔ ذیل میں متعلقہ رنگین متن پر کلک کر کے آپ ہمارے کیٹلاگ ڈاؤن لوڈ کر سکتے ہیں: - ڈرائیونگ چینز - کنویئر چینز - بڑی پچ کنویئر چینز - سٹینلیس سٹیل رولر چینز - زنجیروں کو لہرانا - موٹر سائیکل کی زنجیریں۔ - زرعی مشین کی زنجیریں۔ - سپروکیٹس: ہمارے معیاری سپروکیٹ ANSI معیارات کے مطابق ہیں۔ پلیٹ سپروکیٹ فلیٹ، ہبل لیس سپروکیٹ ہیں۔ ہمارے چھوٹے اور درمیانے سائز کے حب سپروکیٹس کو بار اسٹاک یا فورجنگ سے تبدیل کیا جاتا ہے یا بار اسٹاک ہب کو گرم رولڈ پلیٹ میں ویلڈنگ کرکے بنایا جاتا ہے۔ AGS-TECH Inc. گرے آئرن کاسٹنگ، کاسٹ اسٹیل اور ویلڈیڈ ہب کنسٹرکشنز، سنٹرڈ پاؤڈر میٹل، مولڈ یا مشینی پلاسٹک سے مشینی اسپراکٹس فراہم کر سکتا ہے۔ تیز رفتاری پر ہموار آپریشن کے لیے، سپروکیٹس کے سائز کا مناسب انتخاب ضروری ہے۔ خلائی حدود یقیناً ایک ایسا عنصر ہے جسے ہم سپروکیٹ کا انتخاب کرتے وقت نظر انداز نہیں کر سکتے۔ یہ تجویز کیا جاتا ہے کہ ڈرائیور سے چلنے والے سپروکیٹس کا تناسب 6:1 سے زیادہ نہیں ہونا چاہیے، اور ڈرائیور پر زنجیر کی لپیٹ 120 ڈگری ہے۔ چھوٹے اور بڑے اسپراکیٹس کے درمیان درمیانی فاصلے، زنجیر کی لمبائی اور زنجیر کے تناؤ کا انتخاب بھی کچھ تجویز کردہ انجینئرنگ حسابات اور رہنما خطوط کے مطابق کیا جانا چاہیے نہ کہ تصادفی طور پر۔ نیچے رنگین متن پر کلک کرکے ہمارے کیٹلاگ ڈاؤن لوڈ کریں: - سپروکیٹس اور پلیٹ پہیے - ٹرانسمیشن بشنگس - زنجیر کا جوڑا - زنجیر کے تالے کیبل ڈرائیوز: کچھ معاملات میں بیلٹ اور چین ڈرائیوز پر ان کے فوائد ہیں۔ کیبل ڈرائیوز بیلٹ کی طرح کام انجام دے سکتی ہیں اور کچھ ایپلی کیشنز میں لاگو کرنا آسان اور زیادہ اقتصادی بھی ہوسکتی ہیں۔ مثال کے طور پر، Synchromesh Cable Drives کی ایک نئی سیریز کو مثبت کرشن کے لیے ڈیزائن کیا گیا ہے تاکہ روایتی رسیوں، سادہ کیبلز اور کوگ ڈرائیوز کو تبدیل کیا جا سکے، خاص طور پر تنگ جگہوں پر۔ نئی کیبل ڈرائیو کو الیکٹرانک آلات جیسے کاپی کرنے والی مشینوں، پلاٹرز، ٹائپ رائٹرز، پرنٹرز وغیرہ میں اعلیٰ درستگی کی پوزیشننگ فراہم کرنے کے لیے ڈیزائن کیا گیا ہے۔ نئی کیبل ڈرائیو کی ایک اہم خصوصیت اس کی 3D سرپینٹائن کنفیگریشنز میں استعمال کرنے کی صلاحیت ہے جو اسے قابل بناتی ہے۔ انتہائی چھوٹے ڈیزائن. سنکرومیش کیبلز کو کم تناؤ کے ساتھ استعمال کیا جا سکتا ہے جب رسیوں کے مقابلے میں بجلی کی کھپت کو کم کرتی ہے۔ بیلٹ، چین اور کیبل ڈرائیوز پر سوالات اور رائے کے لیے AGS-TECH سے رابطہ کریں۔ CLICK Product Finder-Locator Service پچھلا صفحہ
- Glass and Ceramic Manufacturing, Hermetic Packages, Seals, Bonding
Glass and Ceramic Manufacturing, Hermetic Packages Seals and Bonding, Tempered Bulletproof Glass, Blow Moulding, Optical Grade Glass, Conductive Glass, Molding شیشہ اور سرامک کی تشکیل اور تشکیل ہم جس قسم کے شیشے کی تیاری کی پیشکش کرتے ہیں وہ ہیں کنٹینر گلاس، گلاس اڑانے، گلاس فائبر اور نلیاں اور راڈ، گھریلو اور صنعتی شیشے کا سامان، لیمپ اور بلب، عین مطابق گلاس مولڈنگ، آپٹیکل پرزے اور اسمبلیاں، فلیٹ اور شیٹ اور فلوٹ گلاس۔ ہم ہاتھ بنانے کے ساتھ ساتھ مشین کی تشکیل بھی کرتے ہیں۔ ہمارے مشہور تکنیکی سیرامک مینوفیکچرنگ کے عمل میں ڈائی پریسنگ، آئسوسٹیٹک پریسنگ، ہاٹ آئسوسٹیٹک پریسنگ، ہاٹ پریسنگ، سلپ کاسٹنگ، ٹیپ کاسٹنگ، اخراج، انجکشن مولڈنگ، گرین مشیننگ، سنٹرنگ یا فائرنگ، ڈائمنڈ گرائنڈنگ، ہرمیٹک اسمبلیاں ہیں۔ ہمارا مشورہ ہے کہ آپ یہاں کلک کریں۔ AGS-TECH Inc کی طرف سے شیشے کی تشکیل اور تشکیل کے عمل کی ہماری اسکیمیٹک عکاسی ڈاؤن لوڈ کریں۔ AGS-TECH Inc کے ذریعے تکنیکی سیرامک مینوفیکچرنگ کے عمل کی ہماری اسکیمیٹک عکاسی ڈاؤن لوڈ کریں۔ تصاویر اور خاکوں کے ساتھ ڈاؤن لوڈ کے قابل یہ فائلیں آپ کو ان معلومات کو بہتر طور پر سمجھنے میں مدد کریں گی جو ہم آپ کو ذیل میں فراہم کر رہے ہیں۔ کنٹینر گلاس مینوفیکچر: ہم نے مینوفیکچرنگ کے لیے پریس اور بلو کے ساتھ ساتھ بلو اور بلو لائنز کو خودکار بنایا ہے۔ بلو اور بلو کے عمل میں ہم ایک گوب کو خالی سانچے میں ڈالتے ہیں اور اوپر سے کمپریسڈ ہوا کا ایک جھونکا لگا کر گردن بناتے ہیں۔ اس کے فوراً بعد، کمپریسڈ ہوا دوسری بار دوسری سمت سے کنٹینر کی گردن کے ذریعے اڑائی جاتی ہے تاکہ بوتل کی پری شکل بن سکے۔ اس پری فارم کو پھر اصل مولڈ میں منتقل کیا جاتا ہے، اسے نرم کرنے کے لیے دوبارہ گرم کیا جاتا ہے اور پری فارم کو اس کے آخری کنٹینر کی شکل دینے کے لیے کمپریسڈ ہوا لگائی جاتی ہے۔ مزید واضح طور پر، اس پر دباؤ ڈالا جاتا ہے اور اسے بلو مولڈ گہا کی دیواروں کے خلاف دھکیل دیا جاتا ہے تاکہ اس کی مطلوبہ شکل اختیار کی جا سکے۔ آخر میں، تیار کردہ شیشے کے کنٹینر کو بعد میں دوبارہ گرم کرنے اور مولڈنگ کے دوران پیدا ہونے والے دباؤ کو دور کرنے کے لیے اینیلنگ اوون میں منتقل کیا جاتا ہے اور اسے کنٹرول شدہ انداز میں ٹھنڈا کیا جاتا ہے۔ پریس اور بلو کے طریقہ کار میں، پگھلے ہوئے گوبس کو پیریسن مولڈ (خالی مولڈ) میں ڈالا جاتا ہے اور پیریسن شکل (خالی شکل) میں دبایا جاتا ہے۔ اس کے بعد خالی جگہوں کو بلو مولڈ میں منتقل کیا جاتا ہے اور "بلو اینڈ بلو پروسیس" کے تحت اوپر بیان کردہ عمل کی طرح اڑا دیا جاتا ہے۔ اینیلنگ اور تناؤ سے نجات جیسے بعد کے اقدامات ایک جیسے یا ایک جیسے ہیں۔ • گلاس اڑانا: ہم روایتی ہینڈ اڑانے کے ساتھ ساتھ خودکار آلات کے ساتھ کمپریسڈ ہوا کا استعمال کرتے ہوئے شیشے کی مصنوعات تیار کر رہے ہیں۔ کچھ آرڈرز کے لیے روایتی اڑانا ضروری ہوتا ہے، جیسے پراجیکٹس جن میں شیشے کا آرٹ ورک شامل ہوتا ہے، یا ایسے پروجیکٹس جن میں ڈھیلے برداشت والے حصوں کی ایک چھوٹی تعداد کی ضرورت ہوتی ہے، پروٹوٹائپنگ/ڈیمو پروجیکٹس.... وغیرہ۔ روایتی شیشے کو اڑانے میں کھوکھلی دھات کے پائپ کو پگھلے ہوئے شیشے کے برتن میں ڈبونا اور شیشے کے مواد کی کچھ مقدار جمع کرنے کے لیے پائپ کو گھمانا شامل ہے۔ پائپ کی نوک پر جمع ہونے والے شیشے کو فلیٹ لوہے پر لپیٹ دیا جاتا ہے، جس کی شکل مطلوبہ، لمبا، دوبارہ گرم اور ہوا سے اڑا دیا جاتا ہے۔ تیار ہونے پر اسے ایک سانچے میں ڈالا جاتا ہے اور ہوا اڑا دی جاتی ہے۔ دھات کے ساتھ شیشے کے رابطے سے بچنے کے لیے سڑنا گہا گیلا ہے۔ پانی کی فلم ان کے درمیان ایک کشن کی طرح کام کرتی ہے۔ دستی اڑانا ایک محنتی سست عمل ہے اور صرف پروٹو ٹائپنگ یا زیادہ قیمت والی اشیاء کے لیے موزوں ہے، سستے فی ٹکڑا ہائی والیوم آرڈرز کے لیے موزوں نہیں ہے۔ گھریلو اور صنعتی شیشے کے سامان کی مینوفیکچرنگ: مختلف قسم کے شیشے کے مواد کا استعمال کرتے ہوئے شیشے کے سامان کی ایک بڑی قسم تیار کی جا رہی ہے۔ کچھ شیشے گرمی سے بچنے والے اور لیبارٹری کے شیشے کے سامان کے لیے موزوں ہوتے ہیں جبکہ کچھ کئی بار ڈش واشرز کو برداشت کرنے کے لیے کافی اچھے ہوتے ہیں اور گھریلو مصنوعات بنانے کے لیے موزوں ہوتے ہیں۔ ویسٹ لیک مشینوں کے استعمال سے روزانہ پینے کے شیشے کے دسیوں ہزار ٹکڑے تیار کیے جا رہے ہیں۔ آسان بنانے کے لیے، پگھلے ہوئے شیشے کو ویکیوم کے ذریعے اکٹھا کیا جاتا ہے اور اسے پہلے کی شکلیں بنانے کے لیے سانچوں میں ڈالا جاتا ہے۔ پھر ہوا کو سانچوں میں اڑا دیا جاتا ہے، یہ دوسرے سانچے میں منتقل ہو جاتے ہیں اور ہوا دوبارہ اڑا دی جاتی ہے اور شیشہ اپنی آخری شکل اختیار کر لیتا ہے۔ ہاتھ سے اڑانے کی طرح، یہ سانچوں کو پانی سے گیلا رکھا جاتا ہے۔ مزید اسٹریچنگ فنشنگ آپریشن کا حصہ ہے جہاں گردن بن رہی ہے۔ اضافی شیشہ جل گیا ہے۔ اس کے بعد اوپر بیان کردہ کنٹرول شدہ ری ہیٹنگ اور کولنگ کا عمل مندرجہ ذیل ہے۔ شیشے کی ٹیوب اور چھڑی کی تشکیل: شیشے کی ٹیوبوں کی تیاری کے لیے جو اہم عمل ہم استعمال کرتے ہیں وہ ہیں DANNER اور VELLO کے عمل۔ ڈینر کے عمل میں، بھٹی سے شیشہ بہتا ہے اور ریفریکٹری مواد سے بنی مائل آستین پر گرتا ہے۔ آستین کو گھومنے والی کھوکھلی شافٹ یا بلو پائپ پر لے جایا جاتا ہے۔ اس کے بعد شیشے کو آستین کے گرد لپیٹ دیا جاتا ہے اور آستین کے نیچے اور شافٹ کی نوک پر بہتی ہوئی ایک ہموار تہہ بن جاتی ہے۔ ٹیوب بننے کی صورت میں، ہوا کو کھوکھلی نوک کے ساتھ بلو پائپ کے ذریعے اڑایا جاتا ہے، اور چھڑی بننے کی صورت میں ہم شافٹ پر ٹھوس ٹپس استعمال کرتے ہیں۔ اس کے بعد نلیاں یا سلاخیں لے جانے والے رولرس کے اوپر کھینچی جاتی ہیں۔ شیشے کی ٹیوبوں کی دیوار کی موٹائی اور قطر جیسے طول و عرض کو آستین کے قطر کو ترتیب دے کر اور ہوا کے دباؤ کو مطلوبہ قدر پر اڑا کر، درجہ حرارت، شیشے کے بہاؤ کی شرح اور ڈرائنگ کی رفتار کو ایڈجسٹ کر کے مطلوبہ اقدار کے مطابق کیا جاتا ہے۔ دوسری طرف ویلو گلاس ٹیوب مینوفیکچرنگ کے عمل میں شیشہ شامل ہوتا ہے جو بھٹی سے باہر اور کھوکھلی مینڈریل یا گھنٹی کے ساتھ پیالے میں جاتا ہے۔ شیشہ پھر مینڈریل اور پیالے کے درمیان ہوا کی جگہ سے گزرتا ہے اور ایک ٹیوب کی شکل اختیار کر لیتا ہے۔ اس کے بعد یہ رولرس کے اوپر سے ایک ڈرائنگ مشین تک جاتا ہے اور اسے ٹھنڈا کیا جاتا ہے۔ کولنگ لائن کے اختتام پر کٹنگ اور فائنل پروسیسنگ ہوتی ہے۔ ٹیوب کے طول و عرض کو ڈینر کے عمل کی طرح ایڈجسٹ کیا جاسکتا ہے۔ ڈینر کا ویلو پروسیس سے موازنہ کرتے وقت، ہم کہہ سکتے ہیں کہ ویلو پروسیس بڑی مقدار میں پیداوار کے لیے ایک بہتر فٹ ہے جب کہ ڈینر کا عمل درست چھوٹے والیوم ٹیوب آرڈرز کے لیے بہتر فٹ ہو سکتا ہے۔ • شیٹ اور فلیٹ اور فلوٹ شیشے کی پروسیسنگ: ہمارے پاس سب ملی میٹر موٹائی سے لے کر کئی سینٹی میٹر تک موٹائی میں فلیٹ شیشے کی بڑی مقدار ہے۔ ہمارے فلیٹ شیشے تقریبا آپٹیکل کمال کے ہیں۔ ہم خصوصی کوٹنگز کے ساتھ گلاس پیش کرتے ہیں جیسے آپٹیکل کوٹنگز، جہاں کیمیائی بخارات جمع کرنے کی تکنیک کا استعمال کوٹنگز جیسے اینٹی ریفلیکشن یا آئینے کی کوٹنگ کے لیے کیا جاتا ہے۔ اس کے علاوہ شفاف conductive ملعمع کاری عام ہیں. شیشے پر ہائیڈرو فوبک یا ہائیڈرو فیلک کوٹنگز بھی دستیاب ہیں، اور کوٹنگ جو شیشے کو خود سے صاف کرتی ہے۔ ٹیمپرڈ، بلٹ پروف اور پرتدار شیشے ابھی تک دیگر مقبول اشیاء ہیں۔ ہم نے شیشے کو مطلوبہ رواداری کے ساتھ مطلوبہ شکل میں کاٹ دیا۔ دیگر ثانوی آپریشنز جیسے مڑے ہوئے یا موڑنے والے فلیٹ گلاس دستیاب ہیں۔ • PRECISION GLASS MOLDING: ہم اس تکنیک کو زیادہ تر درست نظری اجزاء کی تیاری کے لیے استعمال کرتے ہیں بغیر زیادہ مہنگی اور وقت لینے والی تکنیک جیسے پیسنے، لیپنگ اور پالش کرنے کی ضرورت کے۔ یہ تکنیک ہمیشہ بہترین آپٹکس کو بہترین بنانے کے لیے کافی نہیں ہوتی، لیکن کچھ معاملات جیسے صارفین کی مصنوعات، ڈیجیٹل کیمرے، میڈیکل آپٹکس میں یہ اعلی حجم کی تیاری کے لیے ایک کم مہنگا اچھا اختیار ہو سکتا ہے۔ اس کے علاوہ اس کا شیشہ بنانے کی دوسری تکنیکوں پر ایک فائدہ ہے جہاں پیچیدہ جیومیٹریوں کی ضرورت ہوتی ہے، جیسے اسفیئرز کے معاملے میں۔ بنیادی عمل میں شیشے کے خالی حصے کے ساتھ ہمارے مولڈ کے نچلے حصے کو لوڈ کرنا، آکسیجن کو ہٹانے کے لیے پراسیس چیمبر کا انخلا، مولڈ کو بند کرنے کے قریب، ڈائی اور شیشے کو اورکت روشنی کے ساتھ تیز اور آئسو تھرمل گرم کرنا، مولڈ کے حصوں کو مزید بند کرنا شامل ہے۔ نرم شیشے کو آہستہ آہستہ کنٹرول انداز میں مطلوبہ موٹائی تک دبانے کے لیے، اور آخر میں شیشے کو ٹھنڈا کرنا اور چیمبر کو نائٹروجن سے بھرنا اور مصنوعات کو ہٹانا۔ درست درجہ حرارت کنٹرول، مولڈ بند کرنے کا فاصلہ، سڑنا بند کرنے کی قوت، مولڈ اور شیشے کے مواد کی توسیع کے گتانک کا ملاپ اس عمل میں کلیدی حیثیت رکھتا ہے۔ • شیشے کے آپٹیکل اجزاء اور اسمبلیوں کی تیاری: عین مطابق شیشے کی مولڈنگ کے علاوہ، بہت سے قیمتی عمل ہیں جو ہم اعلیٰ معیار کے آپٹیکل پرزہ جات بنانے کے لیے استعمال کرتے ہیں اور ایپلی کیشنز کی مانگ کے لیے اسمبلیاں بناتے ہیں۔ آپٹیکل گریڈ کے شیشوں کو باریک خاص کھرچنے والی سلریوں میں پیسنا، لیپ کرنا اور پالش کرنا آپٹیکل لینز، پرزم، فلیٹ وغیرہ بنانے کے لیے ایک فن اور سائنس ہے۔ سطح کی ہمواری، لہرائی، ہمواری اور خرابی سے پاک آپٹیکل سطحوں کو اس طرح کے عمل کے ساتھ بہت زیادہ تجربے کی ضرورت ہوتی ہے۔ ماحول میں چھوٹی تبدیلیوں کا نتیجہ تصریح کی مصنوعات سے باہر ہو سکتا ہے اور مینوفیکچرنگ لائن کو روک سکتا ہے۔ ایسے معاملات ہیں جہاں صاف کپڑے سے آپٹیکل سطح پر ایک ہی وائپ کسی پروڈکٹ کو تصریحات پر پورا اتر سکتا ہے یا ٹیسٹ میں ناکام ہو سکتا ہے۔ استعمال ہونے والے کچھ مشہور شیشے کے مواد میں فیوزڈ سلکا، کوارٹج، BK7 ہیں۔ نیز اس طرح کے اجزاء کی اسمبلی کے لیے مخصوص تجربہ کی ضرورت ہوتی ہے۔ بعض اوقات خصوصی گلوز کا استعمال کیا جاتا ہے۔ تاہم، بعض اوقات آپٹیکل کانٹیکٹنگ نامی تکنیک بہترین انتخاب ہوتی ہے اور اس میں منسلک آپٹیکل شیشوں کے درمیان کوئی مواد شامل نہیں ہوتا ہے۔ یہ بغیر کسی گلو کے ایک دوسرے سے منسلک ہونے کے لیے فلیٹ سطحوں سے جسمانی طور پر رابطہ کرنے پر مشتمل ہوتا ہے۔ بعض صورتوں میں مکینیکل اسپیسرز، عین مطابق شیشے کی سلاخیں یا گیندیں، کلیمپ یا مشینی دھاتی اجزاء آپٹیکل اجزاء کو مخصوص فاصلوں پر اور ایک دوسرے سے مخصوص جیومیٹرک واقفیت کے ساتھ جمع کرنے کے لیے استعمال کیے جا رہے ہیں۔ آئیے ہم ہائی اینڈ آپٹکس بنانے کے لیے اپنی کچھ مشہور تکنیکوں کا جائزہ لیتے ہیں۔ پیسنا اور لیپ کرنا اور پالش کرنا: آپٹیکل جزو کی کھردری شکل شیشے کو خالی پیسنے سے حاصل کی جاتی ہے۔ اس کے بعد آپٹیکل اجزاء کی کھردری سطحوں کو مطلوبہ سطح کی شکلوں والے ٹولز کے خلاف گھما کر اور رگڑ کر لیپنگ اور پالش کی جاتی ہے۔ آپٹکس اور شکل دینے والے ٹولز کے درمیان چھوٹے کھرچنے والے ذرات اور سیال کے ساتھ گارا ڈالا جا رہا ہے۔ اس طرح کے گارے میں کھرچنے والے ذرات کے سائز کو مطلوبہ ہمواری کی ڈگری کے مطابق منتخب کیا جا سکتا ہے۔ مطلوبہ شکلوں سے اہم آپٹیکل سطحوں کے انحراف کو استعمال ہونے والی روشنی کی طول موج کے لحاظ سے ظاہر کیا جاتا ہے۔ ہمارے اعلی درستگی والے آپٹکس میں طول موج کا دسواں حصہ (طول موج/10) رواداری ہے یا اس سے بھی زیادہ سخت ممکن ہے۔ سطحی پروفائل کے علاوہ، اہم سطحوں کو اسکین کیا جاتا ہے اور سطح کی دیگر خصوصیات اور نقائص جیسے کہ طول و عرض، خروںچ، چپس، گڑھے، دھبے وغیرہ کا جائزہ لیا جاتا ہے۔ آپٹیکل مینوفیکچرنگ فلور میں ماحولیاتی حالات پر سخت کنٹرول اور جدید ترین آلات کے ساتھ وسیع میٹرولوجی اور جانچ کی ضروریات اسے صنعت کی ایک چیلنجنگ شاخ بناتی ہیں۔ • گلاس مینوفیکچرنگ میں ثانوی عمل: ایک بار پھر، جب شیشے کے ثانوی اور تکمیلی عمل کی بات آتی ہے تو ہم صرف آپ کی تخیل تک محدود ہیں۔ یہاں ہم ان میں سے کچھ کی فہرست دیتے ہیں: شیشے پر کوٹنگز (آپٹیکل، الیکٹریکل، ٹرائبلوجیکل، تھرمل، فنکشنل، مکینیکل...) مثال کے طور پر ہم شیشے کی سطح کی خصوصیات کو تبدیل کر سکتے ہیں جس سے یہ مثال کے طور پر گرمی کی عکاسی کرتا ہے تاکہ یہ عمارت کے اندرونی حصوں کو ٹھنڈا رکھے، یا نینو ٹیکنالوجی کا استعمال کرتے ہوئے ایک طرف اورکت کو جذب کر سکے۔ اس سے عمارتوں کے اندرونی حصے کو گرم رکھنے میں مدد ملتی ہے کیونکہ شیشے کی سب سے باہری سطح عمارت کے اندر انفراریڈ شعاعوں کو جذب کر کے اسے واپس اندر تک پھیر دے گی۔ -ایچنگ on گلاس - اپلائیڈ سیرامک لیبلنگ (ACL) - کندہ کاری - شعلہ پالش کرنا -کیمیکل پالش - داغ لگانا تکنیکی سیرامکس کی مینوفیکچرنگ • ڈائی پریسنگ: ڈائی میں بند دانے دار پاؤڈر کے غیر محوری کمپیکشن پر مشتمل ہوتا ہے • ہاٹ پریسنگ: ڈائی پریسنگ کی طرح لیکن کثافت کو بڑھانے کے لیے درجہ حرارت کے اضافے کے ساتھ۔ پاؤڈر یا کمپیکٹڈ پرفارم کو گریفائٹ ڈائی میں رکھا جاتا ہے اور غیر محوری دباؤ لگایا جاتا ہے جب کہ ڈائی کو اعلی درجہ حرارت جیسے 2000 C پر رکھا جاتا ہے۔ سیرامک پاؤڈر کی پروسیسنگ کی قسم کے لحاظ سے درجہ حرارت مختلف ہو سکتا ہے۔ پیچیدہ شکلوں اور جیومیٹریوں کے لیے بعد میں دیگر پروسیسنگ جیسے ہیرے کی پیسنے کی ضرورت ہو سکتی ہے۔ • آئی ایس او سٹیٹک پریسنگ: دانے دار پاؤڈر یا ڈائی پریسڈ کمپیکٹ کو ایئر ٹائٹ کنٹینرز میں اور پھر ایک بند پریشر برتن میں رکھا جاتا ہے جس کے اندر مائع ہوتا ہے۔ اس کے بعد وہ دباؤ والے برتن کے دباؤ کو بڑھا کر کمپیکٹ کیے جاتے ہیں۔ برتن کے اندر مائع دباؤ والی قوتوں کو یکساں طور پر ایئر ٹائٹ کنٹینر کے پورے سطحی علاقے پر منتقل کرتا ہے۔ اس طرح مواد کو یکساں طور پر کمپیکٹ کیا جاتا ہے اور اس کے لچکدار کنٹینر اور اس کے اندرونی پروفائل اور خصوصیات کی شکل اختیار کر لیتا ہے۔ • ہاٹ آئیسوسٹیٹک پریسنگ: آئسوسٹیٹک پریسنگ کی طرح، لیکن دباؤ والے گیس کے ماحول کے علاوہ، ہم اعلی درجہ حرارت پر کمپیکٹ کو سنٹر کرتے ہیں۔ گرم آئسوسٹیٹک دبانے کے نتیجے میں اضافی کثافت اور طاقت میں اضافہ ہوتا ہے۔ • سلپ کاسٹنگ / ڈرین کاسٹنگ : ہم مولڈ کو مائیکرو میٹر سائز کے سیرامک پارٹیکلز اور کیریئر مائع کے سسپنشن سے بھرتے ہیں۔ اس مرکب کو "پرچی" کہا جاتا ہے۔ سڑنا میں سوراخ ہوتے ہیں اور اس وجہ سے مرکب میں موجود مائع کو مولڈ میں فلٹر کیا جاتا ہے۔ نتیجے کے طور پر، سڑنا کی اندرونی سطحوں پر ایک کاسٹ بنتا ہے۔ sintering کے بعد، حصوں کو سڑنا سے باہر لے جایا جا سکتا ہے. • ٹیپ کاسٹنگ: ہم فلیٹ حرکت پذیر کیریئر کی سطحوں پر سیرامک سلریز کاسٹ کر کے سیرامک ٹیپ تیار کرتے ہیں۔ سلریوں میں سیرامک پاؤڈر ہوتے ہیں جو بائنڈنگ اور لے جانے کے مقاصد کے لیے دوسرے کیمیکلز کے ساتھ ملتے ہیں۔ جب سالوینٹس بخارات بنتے ہیں تو سیرامک کی گھنی اور لچکدار چادریں پیچھے رہ جاتی ہیں جنہیں حسب منشا کاٹا یا رول کیا جا سکتا ہے۔ • اخراج کی تشکیل: دوسرے اخراج کے عمل کی طرح، بائنڈر اور دیگر کیمیکلز کے ساتھ سیرامک پاؤڈر کا ایک نرم مرکب ڈائی سے گزر کر اس کی کراس سیکشنل شکل حاصل کرتا ہے اور پھر اسے مطلوبہ لمبائی میں کاٹا جاتا ہے۔ یہ عمل سرد یا گرم سرامک مرکب کے ساتھ کیا جاتا ہے۔ • لو پریشر انجیکشن مولڈنگ: ہم بائنڈر اور سالوینٹس کے ساتھ سیرامک پاؤڈر کا مرکب تیار کرتے ہیں اور اسے ایسے درجہ حرارت پر گرم کرتے ہیں جہاں اسے آسانی سے دبایا جا سکتا ہے اور ٹول کیویٹی میں زبردستی لایا جا سکتا ہے۔ مولڈنگ سائیکل مکمل ہونے کے بعد، حصہ نکال دیا جاتا ہے اور بائنڈنگ کیمیکل کو جلا دیا جاتا ہے۔ انجکشن مولڈنگ کا استعمال کرتے ہوئے، ہم اقتصادی طور پر اعلی حجم میں پیچیدہ حصوں کو حاصل کر سکتے ہیں. سوراخ جو کہ 10 ملی میٹر موٹی دیوار پر ایک ملی میٹر کا ایک چھوٹا سا حصہ ہے ممکن ہے، دھاگے بغیر مشینی کے ممکن ہیں، جتنی سخت برداشت +/- 0.5% ممکن ہو اور مشین کے پرزے بھی کم ہوں ، دیوار کی موٹائی 0.5 ملی میٹر سے 12.5 ملی میٹر کی لمبائی کے ساتھ ساتھ 6.5 ملی میٹر سے 150 ملی میٹر کی لمبائی تک دیوار کی موٹائی ممکن ہے۔ • گرین مشیننگ: اسی دھاتی مشینی ٹولز کا استعمال کرتے ہوئے، ہم دبائے ہوئے سیرامک مواد کو مشین بنا سکتے ہیں جب وہ چاک کی طرح نرم ہوں۔ +/- 1٪ کی رواداری ممکن ہے۔ بہتر رواداری کے لیے ہم ڈائمنڈ پیسنے کا استعمال کرتے ہیں۔ • SINTERING یا FIRING : sintering مکمل کثافت کو ممکن بناتا ہے۔ گرین کمپیکٹ حصوں پر نمایاں سکڑاؤ ہوتا ہے، لیکن یہ کوئی بڑا مسئلہ نہیں ہے کیونکہ جب ہم حصے اور ٹولنگ کو ڈیزائن کرتے ہیں تو ہم ان جہتی تبدیلیوں کو مدنظر رکھتے ہیں۔ پاؤڈر کے ذرات آپس میں بندھے ہوئے ہیں اور کمپیکشن کے عمل سے پیدا ہونے والی پورسٹی کو کافی حد تک ہٹا دیا جاتا ہے۔ • ڈائمنڈ پیسنا: دنیا کا سب سے مشکل مواد "ہیرا" سیرامکس جیسے سخت مواد کو پیسنے کے لیے استعمال کیا جا رہا ہے اور درست حصے حاصل کیے جاتے ہیں۔ مائیکرو میٹر رینج میں رواداری اور بہت ہموار سطحیں حاصل کی جا رہی ہیں۔ اس کے اخراجات کی وجہ سے، ہم صرف اس تکنیک پر غور کرتے ہیں جب ہمیں واقعی اس کی ضرورت ہوتی ہے۔ ہرمیٹک اسمبلیاں وہ ہیں جو عملی طور پر بات کرتے ہوئے انٹرفیس کے درمیان مادے، ٹھوس، مائعات یا گیسوں کے تبادلے کی اجازت نہیں دیتی ہیں۔ ہرمیٹک سگ ماہی ہوا بند ہے۔ مثال کے طور پر ہرمیٹک الیکٹرانک انکلوژرز وہ ہوتے ہیں جو پیکڈ ڈیوائس کے حساس اندرونی مواد کو نمی، آلودگی یا گیسوں سے نقصان نہ پہنچاتے ہیں۔ کوئی بھی چیز 100% ہرمیٹک نہیں ہے، لیکن جب ہم ہرمیٹی کی بات کرتے ہیں تو عملی طور پر ہمارا مطلب یہ ہے کہ اس حد تک ہرمیٹیسیٹی ہے کہ رساو کی شرح اتنی کم ہے کہ آلات عام ماحولیاتی حالات میں بہت لمبے عرصے تک محفوظ رہتے ہیں۔ ہماری ہرمیٹک اسمبلیاں دھات، شیشے اور سیرامک اجزاء، دھاتی سیرامک، سیرامک دھاتی سیرامک، دھاتی سیرامک دھات، دھات سے دھات، دھاتی گلاس، دھاتی گلاس، دھاتی شیشے، دھاتی شیشے، شیشے کے شیشے پر مشتمل ہوتی ہیں۔ دھات اور شیشے سے شیشے اور دھاتی گلاس سیرامک بانڈنگ کے دیگر تمام امتزاج۔ ہم مثال کے طور پر سیرامک کے اجزاء کو دھاتی کوٹ کر سکتے ہیں تاکہ وہ اسمبلی میں موجود دیگر اجزاء کے ساتھ مضبوطی سے منسلک ہو سکیں اور ان میں سگ ماہی کی بہترین صلاحیت ہو۔ ہمارے پاس آپٹیکل ریشوں یا فیڈ تھرو کو دھات کے ساتھ کوٹنگ کرنے اور ان کو انکلوژرز میں سولڈرنگ یا بریز کرنے کا طریقہ معلوم ہے، اس لیے کوئی گیس ان انکلوژرز میں نہیں گزرتی اور نہ ہی لیک ہوتی ہے۔ اس لیے ان کا استعمال الیکٹرانک انکلوژرز تیار کرنے کے لیے کیا جاتا ہے تاکہ حساس آلات کو گھیر لیا جا سکے اور انہیں بیرونی ماحول سے محفوظ رکھا جا سکے۔ ان کی بہترین سگ ماہی خصوصیات کے علاوہ، دیگر خصوصیات جیسے تھرمل ایکسپینشن گتانک، اخترتی مزاحمت، نان آؤٹ گیسنگ فطرت، بہت طویل زندگی، غیر موصل نوعیت، تھرمل موصلیت کی خصوصیات، اینٹی سٹیٹک نوعیت... وغیرہ۔ شیشے اور سیرامک مواد کو مخصوص ایپلی کیشنز کے لیے انتخاب بنائیں۔ سیرامک سے دھاتی فٹنگز، ہرمیٹک سیلنگ، ویکیوم فیڈ تھرو، ہائی اور انتہائی ہائی ویکیوم اور فلوئڈ کنٹرول اجزاء کی تیاری کی ہماری سہولت کے بارے میں معلومات یہاں مل سکتی ہیں:ہرمیٹک اجزاء فیکٹری بروشر CLICK Product Finder-Locator Service پچھلا صفحہ
- Wire & Spring Forming, Shaping, Welding, Assembly of Wires, Coil, CNC
Wire & Spring Forming, Shaping, Welding, Assembly of Wires, Coil Compression Extension Torsion Flat Springs, Custom Wires, Helical Springs at AGS-TECH Inc. تار اور بہار کی تشکیل ہم اپنی مرضی کے مطابق تاریں، وائر اسمبلی، مطلوبہ 2D اور 3D شکلوں میں بنی ہوئی تاریں، تاروں کے جال، جالی، انکلوژرز، ٹوکری، باڑ، وائر اسپرنگ، فلیٹ اسپرنگ تیار کرتے ہیں۔ ٹورشن، کمپریشن، تناؤ، فلیٹ اسپرنگس اور بہت کچھ۔ ہمارے عمل تار اور بہار کی تشکیل، وائر ڈرائنگ، شیپنگ، موڑنے، ویلڈنگ، بریزنگ، سولڈرنگ، پیئرنگ، سویجنگ، ڈرلنگ، چیمفرنگ، گرائنڈنگ، تھریڈنگ، کوٹنگ، فور سلائیڈ، سلائیڈنگ، وائنڈنگ، کوائلنگ، اپ سیٹنگ ہیں۔ ہمارا مشورہ ہے کہ آپ یہاں کلک کریں۔ AGS-TECH Inc کی طرف سے وائر اور اسپرنگ بنانے کے عمل کی ہماری اسکیمیٹک تصویریں ڈاؤن لوڈ کریں۔ تصاویر اور خاکوں کے ساتھ ڈاؤن لوڈ کے قابل یہ فائل آپ کو ان معلومات کو بہتر طور پر سمجھنے میں مدد کرے گی جو ہم آپ کو ذیل میں فراہم کر رہے ہیں۔ • وائر ڈرائنگ: ٹینسائل قوتوں کا استعمال کرتے ہوئے ہم دھاتی اسٹاک کو کھینچتے ہیں اور اسے ڈائی کے ذریعے کھینچتے ہیں تاکہ قطر کو کم کیا جا سکے اور اس کی لمبائی میں اضافہ کیا جا سکے۔ بعض اوقات ہم ڈائی کا ایک سلسلہ استعمال کرتے ہیں۔ ہم تار کے ہر گیج کے لیے ڈیز بنانے کے قابل ہیں۔ ہائی ٹینسائل طاقت والے مواد کا استعمال کرتے ہوئے ہم بہت پتلی تاریں کھینچتے ہیں۔ ہم سرد اور گرم دونوں طرح کی تاریں پیش کرتے ہیں۔ • تار کی تشکیل: گیجڈ تار کے رول کو موڑ کر ایک مفید پروڈکٹ کی شکل دی جاتی ہے۔ ہمارے پاس تمام گیجز سے تاریں بنانے کی صلاحیت ہے، بشمول پتلی تاروں کے ساتھ ساتھ موٹی تاریں جیسے کہ آٹوموبائل چیسس کے نیچے چشموں کے طور پر استعمال ہوتی ہیں۔ تار بنانے کے لیے ہم جو سامان استعمال کرتے ہیں وہ دستی اور CNC وائر فارمرز، کوائلر، پاور پریس، فور سلائیڈ، ملٹی سلائیڈ ہیں۔ ہمارے عمل ہیں ڈرائنگ، موڑنے، سیدھا کرنا، چپٹا کرنا، کھینچنا، کاٹنا، اپ سیٹ کرنا، سولڈرنگ اور ویلڈنگ اور بریزنگ، اسمبلی، کوائلنگ، سویجنگ (یا پنکھ)، چھیدنا، وائر تھریڈنگ، ڈرلنگ، چیمفرنگ، گرائنڈنگ، کوٹنگ اور سطح کے علاج۔ ہمارے جدید ترین آلات کو کسی بھی شکل اور سخت رواداری کے انتہائی پیچیدہ ڈیزائن تیار کرنے کے لیے ترتیب دیا جا سکتا ہے۔ ہم آپ کے تاروں کے لیے مختلف قسم کے سروں کی پیشکش کرتے ہیں۔ ہمارے زیادہ تر تار بنانے والے پراجیکٹس میں ٹولنگ کی کم سے کم سے صفر لاگت آتی ہے۔ نمونے کی تبدیلی کے اوقات عام طور پر دن ہوتے ہیں۔ وائر فارمز کے ڈیزائن/ کنفیگریشن میں تبدیلیاں بہت جلد کی جا سکتی ہیں۔ • اسپرنگ فارمنگ: AGS-TECH اسپرنگس کی ایک بڑی قسم تیار کرتا ہے بشمول: -ٹارشن / ڈبل ٹورسن اسپرنگ تناؤ / کمپریشن بہار -مستقل / متغیر موسم بہار کوائل اور ہیلیکل اسپرنگ -Flat & Leaf Spring - توازن بہار -بیلیویل واشر -منفی بہار پروگریسو ریٹ کوائل اسپرنگ -موسم بہار - Volute Spring ٹیپرڈ اسپرنگس - بہار کے حلقے -کلاک اسپرنگس -کلپس ہم مختلف قسم کے مواد سے چشمے تیار کرتے ہیں اور آپ کی درخواست کے مطابق آپ کی رہنمائی کر سکتے ہیں۔ سب سے زیادہ عام مواد سٹینلیس سٹیل، کروم سلکان، ہائی کاربن سٹیل، تیل کے مزاج والے کم کاربن، کروم وینڈیم، فاسفر کانسی، ٹائٹینیم، بیریلیم تانبے کا مرکب، اعلی درجہ حرارت والے سرامک ہیں۔ ہم چشموں کی تیاری میں مختلف تکنیکوں کا استعمال کرتے ہیں جن میں CNC کوائلنگ، کولڈ وائنڈنگ، ہاٹ وائنڈنگ، ہارڈننگ، فنشنگ شامل ہیں۔ تار بنانے کے تحت اوپر بیان کردہ دیگر تکنیکیں بھی ہمارے موسم بہار کے مینوفیکچرنگ آپریشنز میں عام ہیں۔ • تاروں اور چشموں کے لیے فنشنگ سروسز: ہم آپ کی پسند اور ضروریات کے مطابق آپ کی مصنوعات کو کئی طریقوں سے ختم کر سکتے ہیں۔ کچھ عام عمل جو ہم پیش کرتے ہیں وہ ہیں: پینٹنگ، پاؤڈر کوٹنگ، پلاٹنگ، ونائل ڈپنگ، انوڈائزنگ، تناؤ سے نجات، گرمی کا علاج، شاٹ پین، ٹمبل، کرومیٹ، electroless نکل، پاسیویشن، پلاسٹک کوٹنگ , پلازما کی صفائی۔ CLICK Product Finder-Locator Service پچھلا صفحہ
- Forging and Powdered Metallurgy, Die Forging, Heading, Hot Forging
Forging and Powdered Metallurgy, Die Forging, Heading, Hot Forging, Impression Die, Near Net Shape, Swaging, Metal Hobbing, Riveting, Coining from AGS-TECH Inc. میٹل فورجنگ اور پاؤڈر میٹالرجی میٹل فورجنگ پروسیس کی قسم جو ہم پیش کرتے ہیں وہ ہیں ہاٹ اینڈ کولڈ ڈائی، اوپن ڈائی اور کلوزڈ ڈائی، امپریشن ڈائی اینڈ فلیش لیس فورجنگز، cogging، فلرنگ، ایجنگ اور پریزیشن فورجنگ، ہیڈ شیپنگ، قریب۔ , سویجنگ، اپ سیٹ فورجنگ، میٹل ہوبنگ، پریس اینڈ رول اور ریڈیل اور آربیٹل اور رنگ اور آئسوتھرمل فورجنگ، کوائننگ، ریوٹنگ، میٹل بال فورجنگ، میٹل پیئرسنگ، سائزنگ، ہائی انرجی ریٹ فورجنگ۔ ہماری پاؤڈر میٹلرجی اور پاؤڈر پروسیسنگ کی تکنیک پاؤڈر پریسنگ اور سنٹرنگ، امپریگنیشن، انفلٹریشن، ہاٹ اینڈ کولڈ آئسوسٹیٹک پریسنگ، میٹل انجیکشن مولڈنگ، رول کمپیکشن، پاؤڈر رولنگ، پاؤڈر ایکسٹروشن، لوز سنٹرنگ، اسپارک ہاٹ سنٹرنگ، ہیں۔ ہمارا مشورہ ہے کہ آپ یہاں کلک کریں۔ AGS-TECH Inc. کے ذریعے ہمارے فورجنگ پراسیسز کی اسکیمیٹک تصویریں ڈاؤن لوڈ کریں۔ AGS-TECH Inc. کی طرف سے پاؤڈر میٹلرجی کے عمل کی ہماری اسکیمیٹک عکاسی ڈاؤن لوڈ کریں۔ تصاویر اور خاکوں کے ساتھ ڈاؤن لوڈ کے قابل یہ فائلیں آپ کو ان معلومات کو بہتر طور پر سمجھنے میں مدد کریں گی جو ہم آپ کو ذیل میں فراہم کر رہے ہیں۔ دھاتی جعل سازی میں، کمپریسیو قوتیں لگائی جاتی ہیں اور مواد کو درست شکل دے کر مطلوبہ شکل حاصل کی جاتی ہے۔ صنعت میں سب سے زیادہ عام جعلی مواد لوہے اور سٹیل ہیں، لیکن متعدد دیگر جیسے ایلومینیم، تانبا، ٹائٹینیم، میگنیشیم بھی بڑے پیمانے پر جعلی ہیں۔ جعلی دھاتی حصوں نے مہر بند شگافوں اور بند خالی جگہوں کے علاوہ اناج کے ڈھانچے کو بہتر کیا ہے، اس طرح اس عمل سے حاصل ہونے والے حصوں کی طاقت زیادہ ہے۔ فورجنگ ایسے پرزے تیار کرتی ہے جو کاسٹنگ یا مشیننگ کے ذریعے بنائے گئے پرزوں سے اپنے وزن کے لحاظ سے نمایاں طور پر مضبوط ہوتے ہیں۔ چونکہ جعلی حصوں کو دھات کے بہاؤ کو اس کی آخری شکل میں بنا کر شکل دی جاتی ہے، اس لیے دھات ایک دشاتمک اناج کا ڈھانچہ اختیار کرتی ہے جو حصوں کی اعلیٰ طاقت کا باعث بنتی ہے۔ دوسرے الفاظ میں، جعل سازی کے عمل سے حاصل کیے گئے حصے سادہ کاسٹ یا مشینی پرزوں کے مقابلے میں بہتر مکینیکل خصوصیات کو ظاہر کرتے ہیں۔ دھاتی جعل سازی کا وزن چھوٹے ہلکے پرزوں سے لے کر لاکھوں پاؤنڈز تک ہوسکتا ہے۔ ہم زیادہ تر میکانکی طور پر مانگنے والی ایپلی کیشنز کے لیے فورجنگ تیار کرتے ہیں جہاں آٹوموٹیو پارٹس، گیئرز، ورک ٹولز، ہینڈ ٹولز، ٹربائن شافٹ، موٹرسائیکل گیئر جیسے پرزوں پر زیادہ دباؤ ڈالا جاتا ہے۔ چونکہ ٹولنگ اور سیٹ اپ کی لاگت نسبتاً زیادہ ہے، اس لیے ہم اس مینوفیکچرنگ کے عمل کو صرف اعلیٰ حجم کی پیداوار اور کم حجم لیکن اعلیٰ قیمت والے اہم اجزاء جیسے ایرو اسپیس لینڈنگ گیئر کے لیے تجویز کرتے ہیں۔ ٹولنگ کی لاگت کے علاوہ، بڑی مقدار میں جعلی پرزوں کی تیاری کا وقت کچھ سادہ مشینی پرزوں کے مقابلے میں لمبا ہو سکتا ہے، لیکن یہ تکنیک ان حصوں کے لیے بہت اہم ہے جن کے لیے غیر معمولی طاقت کی ضرورت ہوتی ہے جیسے بولٹ، گری دار میوے، خصوصی ایپلی کیشن۔ فاسٹنرز، آٹوموٹو، فورک لفٹ، کرین کے حصے۔ • ہاٹ ڈائی اور کولڈ ڈائی فورجنگ: ہاٹ ڈائی فورجنگ، جیسا کہ نام سے ظاہر ہوتا ہے کہ زیادہ درجہ حرارت پر کیا جاتا ہے، اس لیے لچک زیادہ ہے اور مواد کی طاقت کم ہے۔ یہ آسانی سے اخترتی اور جعل سازی کی سہولت فراہم کرتا ہے۔ اس کے برعکس، کولڈ ڈائی فورجنگ کم درجہ حرارت پر کی جاتی ہے اور اس کے لیے زیادہ قوتوں کی ضرورت ہوتی ہے جس کے نتیجے میں تناؤ سخت ہوتا ہے، سطح کی بہتر تکمیل ہوتی ہے اور تیار شدہ حصوں کی درستگی ہوتی ہے۔ • اوپن ڈائی اور امپریشن ڈائی فورجنگ: اوپن ڈائی فورجنگ میں، ڈائی کمپریس کیے جانے والے مواد کو محدود نہیں کرتی، جب کہ امپریشن میں ڈائی فورجنگ ڈائی کے اندر موجود گہا مواد کے بہاؤ کو محدود کرتی ہے جب کہ اسے مطلوبہ شکل میں جعلی بنایا جاتا ہے۔ UPSET FORGING یا اسے UPSETTING بھی کہا جاتا ہے، جو درحقیقت ایک جیسا نہیں ہے بلکہ بہت ملتا جلتا عمل ہے، ایک کھلا ڈائی عمل ہے جہاں ورک پیس کو دو فلیٹ ڈیز کے درمیان سینڈویچ کیا جاتا ہے اور ایک دبانے والی قوت اس کی اونچائی کو کم کرتی ہے۔ جیسا کہ اونچائی reduced ہے، کام کے ٹکڑے کی چوڑائی بڑھ جاتی ہے۔ HEADING، ایک پریشان فورجنگ عمل میں بیلناکار اسٹاک شامل ہوتا ہے جو اپنے اختتام پر پریشان ہوتا ہے اور اس کے کراس سیکشن کو مقامی طور پر بڑھایا جاتا ہے۔ سرخی میں اسٹاک کو ڈائی کے ذریعے کھلایا جاتا ہے، جعلی اور پھر لمبائی میں کاٹ دیا جاتا ہے۔ آپریشن تیزی سے فاسٹنرز کی زیادہ مقدار پیدا کرنے کے قابل ہے۔ زیادہ تر یہ ایک ٹھنڈا کام کرنے والا آپریشن ہے کیونکہ اس کا استعمال کیل کے سروں، سکرو کے سروں، نٹ اور بولٹ کو بنانے کے لیے کیا جاتا ہے جہاں مواد کو مضبوط کرنے کی ضرورت ہوتی ہے۔ ایک اور اوپن ڈائی کا عمل COGGING ہے، جہاں کام کے ٹکڑے کو ہر قدم کے ساتھ کئی مراحل میں جعل سازی کی جاتی ہے جس کے نتیجے میں مواد کی کمپریشن ہوتی ہے اور اس کے نتیجے میں کام کے ٹکڑے کی لمبائی کے ساتھ اوپن ڈائی کی حرکت ہوتی ہے۔ ہر قدم پر، موٹائی کو کم کیا جاتا ہے اور لمبائی میں تھوڑی مقدار میں اضافہ ہوتا ہے۔ یہ عمل ایک گھبرائے ہوئے طالب علم سے مشابہت رکھتا ہے جو چھوٹے چھوٹے قدموں میں اپنی پنسل کو کاٹتا ہے۔ فلرنگ نامی ایک عمل ایک اور اوپن ڈائی فورجنگ طریقہ ہے جسے ہم اکثر دھاتی جعل سازی کے دیگر آپریشنز ہونے سے پہلے ورک پیس میں مواد کو تقسیم کرنے کے لیے پہلے قدم کے طور پر تعینات کرتے ہیں۔ ہم اسے اس وقت استعمال کرتے ہیں جب ورک پیس کو کئی فورجنگ operations کی ضرورت ہوتی ہے۔ آپریشن میں، محدب سطحوں کی خرابی کے ساتھ مر جائیں اور دونوں اطراف میں دھات کے بہاؤ کا سبب بنیں۔ فلرنگ سے ملتا جلتا عمل، دوسری طرف EDGING میں کام کے ٹکڑے کو درست کرنے کے لیے مقعر کی سطحوں کے ساتھ کھلی ڈائی شامل ہوتی ہے۔ ایجنگ بعد میں فورجنگ آپریشنز کے لیے ایک تیاری کا عمل بھی ہے جو مواد کو دونوں طرف سے بیچ میں ایک علاقے میں بہا دیتا ہے۔ امپریشن ڈائی فورجنگ یا بند ڈائی فورجنگ جیسا کہ اسے ڈائی / مولڈ کا استعمال بھی کہا جاتا ہے جو مواد کو کمپریس کرتا ہے اور اپنے اندر اس کے بہاؤ کو محدود کرتا ہے۔ ڈائی بند ہو جاتی ہے اور مواد ڈائی/مولڈ گہا کی شکل اختیار کر لیتا ہے۔ PRECISION FORGING، ایک ایسا عمل جس میں خصوصی آلات اور مولڈ کی ضرورت ہوتی ہے، بغیر یا بہت کم فلیش کے پرزے تیار کرتی ہے۔ دوسرے الفاظ میں، حصوں کے قریب حتمی طول و عرض ہوں گے. اس عمل میں مواد کی ایک اچھی طرح سے کنٹرول شدہ مقدار کو احتیاط سے ڈالا جاتا ہے اور مولڈ کے اندر رکھا جاتا ہے۔ ہم اس طریقہ کو پیچیدہ شکلوں کے لیے پتلے حصوں، چھوٹی رواداری اور مسودے کے زاویوں کے لیے استعمال کرتے ہیں اور جب مقدار اتنی زیادہ ہو کہ مولڈ اور آلات کی لاگت کو درست ثابت کر سکے۔ • بغیر فلیش فورجنگ: ورک پیس کو ڈائی میں اس طرح رکھا جاتا ہے کہ کوئی بھی مواد گہا سے باہر نہ نکل کر فلیش بنا سکے۔ اس طرح کسی ناپسندیدہ فلیش ٹرمنگ کی ضرورت نہیں ہے۔ یہ ایک درست طریقے سے جعل سازی کا عمل ہے اور اس طرح استعمال شدہ مواد کی مقدار پر قریبی کنٹرول کی ضرورت ہوتی ہے۔ • میٹل سویگنگ یا ریڈیل فورجنگ: کام کے ٹکڑے پر ڈائی اور جعلی کے ذریعے کام کیا جاتا ہے۔ اندرونی ورک پیس جیومیٹری کو جعل سازی کے لیے ایک مینڈرل بھی استعمال کیا جا سکتا ہے۔ سویجنگ آپریشن میں کام کا ٹکڑا عام طور پر فی سیکنڈ میں کئی اسٹروک حاصل کرتا ہے۔ swaging کے ذریعہ تیار کردہ عام اشیاء نوک دار ٹپ ٹولز، ٹیپرڈ بارز، سکریو ڈرایور ہیں۔ • دھاتی چھیدنا: ہم اس آپریشن کو پرزوں کی تیاری میں ایک اضافی آپریشن کے طور پر اکثر استعمال کرتے ہیں۔ کام کے ٹکڑے کی سطح پر سوراخ کیے بغیر سوراخ یا گہا بنایا جاتا ہے۔ براہ کرم نوٹ کریں کہ سوراخ کرنا ڈرلنگ سے مختلف ہے جس کے نتیجے میں سوراخ ہوتا ہے۔ • ہوبنگ: مطلوبہ جیومیٹری کے ساتھ ایک مکے کو ورک پیس میں دبایا جاتا ہے اور مطلوبہ شکل کے ساتھ ایک گہا بناتا ہے۔ ہم اس پنچ کو HOB کہتے ہیں۔ آپریشن میں ہائی پریشر شامل ہوتا ہے اور سردی میں کیا جاتا ہے۔ نتیجے کے طور پر مواد ٹھنڈا کام کرتا ہے اور تناؤ سخت ہوتا ہے۔ اس لیے یہ عمل دیگر مینوفیکچرنگ عملوں کے لیے سانچوں، ڈائی اور گہاوں کی تیاری کے لیے بہت موزوں ہے۔ ایک بار ہوب تیار ہوجانے کے بعد، کوئی ایک ایک کرکے مشین بنانے کی ضرورت کے بغیر بہت سی ایک جیسی گہا آسانی سے تیار کرسکتا ہے۔ • رول فورجنگ یا رول فارمنگ: دھات کے حصے کو شکل دینے کے لیے دو مخالف رول استعمال کیے جاتے ہیں۔ ورک پیس کو رولز میں کھلایا جاتا ہے، رولز گھماتے ہیں اور کام کو خلا میں کھینچتے ہیں، اس کے بعد کام کو رولز کے نالی والے حصے سے کھلایا جاتا ہے اور کمپریسیو قوتیں مواد کو اس کی مطلوبہ شکل دیتی ہیں۔ یہ رولنگ کا عمل نہیں ہے بلکہ ایک جعل سازی کا عمل ہے، کیونکہ یہ ایک مسلسل آپریشن کے بجائے مجرد ہے۔ رولز گرووز پر جیومیٹری مواد کو مطلوبہ شکل اور جیومیٹری میں جعلسازی کرتی ہے۔ یہ گرم کارکردگی کا مظاہرہ کیا جاتا ہے. جعل سازی کا عمل ہونے کی وجہ سے یہ شاندار مکینیکل خصوصیات کے ساتھ پرزے تیار کرتا ہے اور اس لیے ہم اسے آٹو موٹیو پرزوں کی تیاری کے لیے استعمال کرتے ہیں جیسے شافٹ جن کو مشکل کام کے ماحول میں غیر معمولی برداشت کی ضرورت ہوتی ہے۔ • ORBITAL FORGING: ورک پیس کو ایک فورجنگ ڈائی کیویٹی میں ڈالا جاتا ہے اور اوپری ڈائی کے ذریعے جعلی بنایا جاتا ہے جو مداری راستے میں سفر کرتا ہے کیونکہ یہ ایک مائل محور پر گھومتا ہے۔ ہر انقلاب پر، اوپری ڈائی پورے کام کے ٹکڑے پر دبانے والی قوتوں کو استعمال کرتی ہے۔ ان انقلابات کو کئی بار دہرانے سے، کافی جعل سازی کی جاتی ہے۔ اس مینوفیکچرنگ تکنیک کے فوائد اس کا کم شور آپریشن اور کم قوتوں کی ضرورت ہے۔ دوسرے لفظوں میں چھوٹی قوتوں کے ساتھ ایک ہیوی ڈائی کو ایک محور کے گرد گھوم سکتا ہے تاکہ ورک پیس کے اس حصے پر بڑا دباؤ ڈالا جا سکے جو ڈائی کے ساتھ رابطے میں ہو۔ ڈسک یا مخروطی شکل والے حصے بعض اوقات اس عمل کے لیے موزوں ہوتے ہیں۔ • رِنگ فورجنگ: ہم اکثر ہموار انگوٹھیاں بنانے کے لیے استعمال کرتے ہیں۔ اسٹاک کو لمبائی میں کاٹا جاتا ہے، پریشان کیا جاتا ہے اور پھر ایک مرکزی سوراخ بنانے کے لیے پورے راستے میں سوراخ کیا جاتا ہے۔ پھر اسے مینڈریل پر ڈالا جاتا ہے اور ایک فورجنگ ڈائی اس پر اوپر سے ہتھوڑا لگاتا ہے کیونکہ انگوٹھی کو آہستہ آہستہ گھمایا جاتا ہے جب تک کہ مطلوبہ سائز حاصل نہ ہوجائے۔ • RIVETING: حصوں کو جوڑنے کا ایک عام عمل، پرزوں کے ذریعے پہلے سے بنائے گئے سوراخوں میں ڈالے جانے والے سیدھے دھات کے ٹکڑے سے شروع ہوتا ہے۔ اس کے بعد دھات کے ٹکڑے کے دونوں سروں کو اوپری اور زیریں ڈائی کے درمیان جوڑ کو نچوڑ کر جعلی بنایا جاتا ہے۔ • کوائننگ: ایک اور مقبول عمل جو مکینیکل پریس کے ذریعے کیا جاتا ہے، تھوڑے فاصلے پر بڑی قوتیں لگاتے ہیں۔ نام "سکے بنانا" دھاتی سکوں کی سطحوں پر جعلی تفصیلات سے آتا ہے۔ یہ زیادہ تر کسی پروڈکٹ کے لیے مکمل کرنے کا عمل ہے جہاں ڈائی کے ذریعے لگائی جانے والی بڑی قوت کے نتیجے میں سطحوں پر باریک تفصیلات حاصل کی جاتی ہیں جو ان تفصیلات کو ورک پیس میں منتقل کرتی ہے۔ • میٹل بال فورجنگ: بال بیرنگ جیسی مصنوعات کو اعلیٰ معیار کے عین مطابق دھاتی گیندوں کی ضرورت ہوتی ہے۔ SKEW ROLLING کہلانے والی ایک تکنیک میں، ہم دو مخالف رول استعمال کرتے ہیں جو مسلسل گھومتے رہتے ہیں کیونکہ اسٹاک کو رولز میں مسلسل فیڈ کیا جا رہا ہے۔ دو رولوں کے ایک سرے پر دھات کے دائرے بطور مصنوعہ نکالے جاتے ہیں۔ میٹل بال فورجنگ کا دوسرا طریقہ ڈائی کا استعمال کر رہا ہے جو ان کے درمیان رکھے ہوئے مواد کو نچوڑ کر مولڈ گہا کی کروی شکل اختیار کر لیتا ہے۔ اکثر اوقات تیار کی جانے والی گیندوں کو اعلیٰ معیار کی مصنوعات بننے کے لیے کچھ اضافی اقدامات کی ضرورت ہوتی ہے جیسے فنشنگ اور پالش کرنا۔ • ISOTHERMAL FORGING / HOT DIE FORGING : ایک مہنگا عمل صرف اس وقت انجام دیا جاتا ہے جب فائدہ / لاگت کی قیمت جائز ہو۔ ایک گرم کام کرنے کا عمل جہاں ڈائی کو کام کے ٹکڑے کے برابر درجہ حرارت پر گرم کیا جاتا ہے۔ چونکہ ڈائی اور کام دونوں ایک ہی درجہ حرارت کے بارے میں ہیں، کوئی ٹھنڈک نہیں ہے اور دھات کے بہاؤ کی خصوصیات میں بہتری آئی ہے۔ یہ آپریشن انتہائی کم از کم فورجیبلٹی اور ایسے مواد کے لیے موزوں ہے جن کے مکینیکل خصوصیات چھوٹے درجہ حرارت کے میلان اور تبدیلیوں کے لیے بہت حساس ہوتی ہیں۔ • دھاتی سائز: یہ ایک ٹھنڈا ختم کرنے کا عمل ہے۔ مادی بہاؤ تمام سمتوں میں غیر محدود ہے ماسوائے اس سمت کے جس میں قوت کا اطلاق ہوتا ہے۔ نتیجے کے طور پر، بہت اچھی سطح کی تکمیل اور درست طول و عرض حاصل کیے جاتے ہیں. • ہائی انرجی ریٹ فورجنگ: اس تکنیک میں پسٹن کے بازو سے منسلک ایک اوپری مولڈ شامل ہوتا ہے جسے تیز رفتاری سے دھکیل دیا جاتا ہے کیونکہ ایندھن اور ہوا کے مکسچر کو spark کے ذریعے بھڑکایا جاتا ہے۔ یہ کار کے انجن میں پسٹن کے آپریشن سے مشابہت رکھتا ہے۔ مولڈ کام کے ٹکڑے کو بہت تیزی سے ٹکراتا ہے اور پھر بیک پریشر کی بدولت بہت تیزی سے اپنی اصل پوزیشن پر واپس آجاتا ہے۔ کام چند ملی سیکنڈ میں جعلی ہو جاتا ہے اور اس لیے کام کو ٹھنڈا ہونے کا وقت نہیں ملتا۔ یہ ان حصوں کے لیے مفید ہے جو بہت زیادہ درجہ حرارت کے لیے حساس مکینیکل خصوصیات رکھتے ہیں۔ دوسرے لفظوں میں یہ عمل اتنا تیز ہے کہ حصہ مسلسل درجہ حرارت کے تحت بنتا ہے اور مولڈ/ ورک پیس انٹرفیس پر درجہ حرارت کے گریڈینٹ نہیں ہوں گے۔ • DIE FORGING میں، دھات کو دو مماثل سٹیل کے بلاکس کے درمیان پیٹا جاتا ہے جس میں خاص شکلیں ہوتی ہیں، جنہیں ڈائی کہتے ہیں۔ جب دھات کو ڈائی کے درمیان ہتھوڑا لگایا جاتا ہے، تو یہ وہی شکل اختیار کرتی ہے جو ڈائی میں موجود شکلوں کی ہوتی ہے۔ جب یہ اپنی آخری شکل تک پہنچ جاتا ہے تو اسے ٹھنڈا کرنے کے لیے باہر نکالا جاتا ہے۔ اس عمل سے مضبوط پرزے تیار ہوتے ہیں جو بالکل درست شکل کے ہوتے ہیں، لیکن خصوصی مرنے والوں کے لیے بڑی سرمایہ کاری کی ضرورت ہوتی ہے۔ پریشان فورجنگ دھات کے ٹکڑے کو چپٹا کرکے اس کے قطر کو بڑھاتا ہے۔ یہ عام طور پر چھوٹے حصوں کو بنانے کے لیے استعمال ہوتا ہے، خاص طور پر بولٹ اور ناخن جیسے فاسٹنرز پر سر بنانے کے لیے۔ • پاؤڈر میٹلرجی / پاؤڈر پروسیسنگ: جیسا کہ نام سے ظاہر ہوتا ہے، اس میں پاؤڈر سے مخصوص جیومیٹری اور شکلوں کے ٹھوس حصے بنانے کے لیے مینوفیکچرنگ کے عمل شامل ہیں۔ اگر دھاتی پاؤڈر اس مقصد کے لیے استعمال کیے جائیں تو یہ پاؤڈر میٹالرجی کا دائرہ ہے اور اگر نان میٹل پاؤڈر استعمال کیے جائیں تو یہ پاؤڈر پروسیسنگ ہے۔ پاؤڈر سے ٹھوس پرزے دبانے اور سنٹرنگ کے ذریعے تیار کیے جاتے ہیں۔ پاؤڈر پریسنگ کا استعمال پاؤڈر کو مطلوبہ شکلوں میں کمپیکٹ کرنے کے لیے کیا جاتا ہے۔ سب سے پہلے، بنیادی مواد کو جسمانی طور پر پاؤڈر کیا جاتا ہے، اسے بہت سے چھوٹے انفرادی ذرات میں تقسیم کیا جاتا ہے۔ پاؤڈر کا مرکب ڈائی میں بھرا جاتا ہے اور ایک پنچ پاؤڈر کی طرف بڑھتا ہے اور اسے مطلوبہ شکل میں کمپیکٹ کرتا ہے۔ زیادہ تر کمرے کے درجہ حرارت پر انجام دیا جاتا ہے، پاؤڈر دبانے سے ٹھوس حصہ حاصل ہوتا ہے اور اسے گرین کمپیکٹ کہا جاتا ہے۔ بائنڈر اور چکنا کرنے والے مادوں کو عام طور پر کمپیکٹیبلٹی کو بڑھانے کے لیے استعمال کیا جاتا ہے۔ ہم کئی ہزار ٹن صلاحیت کے ساتھ ہائیڈرولک پریس کا استعمال کرتے ہوئے پاؤڈر پریس بنانے کے قابل ہیں۔ اس کے علاوہ ہمارے پاس مخالف اوپر اور نیچے کے مکے کے ساتھ ڈبل ایکشن پریسز کے ساتھ ساتھ انتہائی پیچیدہ پارٹ جیومیٹریز کے لیے متعدد ایکشن پریس بھی ہیں۔ یکسانیت جو کہ بہت سے پاؤڈر میٹلرجی/پاؤڈر پروسیسنگ پلانٹس کے لیے ایک اہم چیلنج ہے، AGS-TECH کے لیے کوئی بڑا مسئلہ نہیں ہے کیونکہ اس طرح کے پرزوں کی تیاری میں ہمارے وسیع تجربے کی وجہ سے کئی سالوں سے۔ یہاں تک کہ موٹے حصوں کے ساتھ جہاں یکسانیت ایک چیلنج ہے ہم کامیاب ہوئے ہیں۔ اگر ہم آپ کے پراجیکٹ کا عہد کرتے ہیں تو ہم آپ کے پرزے بنائیں گے۔ اگر ہمیں کوئی ممکنہ خطرہ نظر آتا ہے، تو ہم آپ کو میں مطلع کریں گے۔ ایڈوانس. پاؤڈر سائنٹرنگ، جو کہ دوسرا مرحلہ ہے، اس میں درجہ حرارت کو ایک خاص ڈگری تک بڑھانا اور اس سطح پر ایک خاص وقت کے لیے درجہ حرارت کو برقرار رکھنا شامل ہے تاکہ دبائے ہوئے حصے میں پاؤڈر کے ذرات آپس میں بانڈ کر سکیں۔ اس کے نتیجے میں بہت زیادہ مضبوط بانڈز اور کام کے ٹکڑے کو مضبوط بنایا جاتا ہے۔ سنٹرنگ پاؤڈر کے پگھلنے والے درجہ حرارت کے قریب ہوتی ہے۔ sintering کے دوران سکڑ جائے گا، مواد کی طاقت، کثافت، لچک، تھرمل چالکتا، برقی چالکتا میں اضافہ ہوتا ہے. ہمارے پاس sintering کے لیے بیچ اور مسلسل بھٹیاں ہیں۔ ہماری صلاحیتوں میں سے ایک یہ ہے کہ ہم جو پرزہ تیار کرتے ہیں ان کی پورسٹی کی سطح کو ایڈجسٹ کرنا۔ مثال کے طور پر ہم پرزوں کو کچھ حد تک غیر محفوظ رکھ کر دھاتی فلٹر تیار کرنے کے قابل ہیں۔ IMPREGNATION نامی تکنیک کا استعمال کرتے ہوئے، ہم دھات کے سوراخوں کو تیل جیسے مائع سے بھرتے ہیں۔ ہم مثال کے طور پر تیل کے رنگدار بیرنگ تیار کرتے ہیں جو خود چکنا ہوتے ہیں۔ انفلٹریشن کے عمل میں ہم ایک دھات کے سوراخوں کو بنیادی مواد سے کم پگھلنے والے نقطہ کی دوسری دھات سے بھرتے ہیں۔ مرکب کو دو دھاتوں کے پگھلنے والے درجہ حرارت کے درمیان درجہ حرارت پر گرم کیا جاتا ہے۔ اس کے نتیجے میں کچھ خاص خصوصیات حاصل کی جا سکتی ہیں۔ ہم اکثر ثانوی کارروائیاں بھی کرتے ہیں جیسے کہ پاؤڈر کے تیار کردہ پرزوں پر مشینی اور فورجنگ جب خاص خصوصیات یا خصوصیات حاصل کرنے کی ضرورت ہوتی ہے یا جب حصے کو کم عمل کے مراحل کے ساتھ تیار کیا جا سکتا ہے۔ ISOSTATIC پریسنگ: اس عمل میں حصہ کو کمپیکٹ کرنے کے لیے سیال کا دباؤ استعمال کیا جا رہا ہے۔ دھاتی پاؤڈر مہر بند لچکدار کنٹینر سے بنے مولڈ میں رکھے جاتے ہیں۔ آئسوسٹیٹک دبانے میں، چاروں طرف سے دباؤ لگایا جاتا ہے، روایتی دبانے میں نظر آنے والے محوری دباؤ کے برعکس۔ isostatic دبانے کے فوائد حصے کے اندر یکساں کثافت ہیں، خاص طور پر بڑے یا موٹے حصوں کے لیے، اعلی خصوصیات۔ اس کا نقصان طویل چکر کا وقت اور نسبتاً کم ہندسی درستگی ہے۔ کولڈ ISOSTATIC پریسنگ کمرے کے درجہ حرارت پر کی جاتی ہے اور لچکدار مولڈ ربڑ، PVC یا urethane یا اسی طرح کے مواد سے بنا ہوتا ہے۔ دباؤ ڈالنے اور کمپیکٹ کرنے کے لیے استعمال ہونے والا سیال تیل یا پانی ہے۔ گرین کمپیکٹ کی روایتی sintering اس کی پیروی کرتی ہے۔ دوسری طرف گرم ISOSTATIC پریسنگ اعلی درجہ حرارت پر کی جاتی ہے اور مولڈ میٹریل شیٹ میٹل یا سیرامک ہے جس میں کافی زیادہ پگھلنے والا نقطہ ہے جو درجہ حرارت کے خلاف مزاحمت کرتا ہے۔ دباؤ ڈالنے والا سیال عام طور پر ایک غیر فعال گیس ہوتا ہے۔ دبانے اور sintering آپریشن ایک قدم میں کئے جاتے ہیں. پوروسیٹی تقریباً مکمل طور پر ختم ہو گئی ہے، ایک یونیفارم grain ڈھانچہ حاصل کیا گیا ہے۔ ہاٹ آئسوسٹیٹک پریسنگ کا فائدہ یہ ہے کہ یہ کاسٹنگ اور فورجنگ کے ساتھ مل کر ایسے پرزے تیار کر سکتا ہے جو کاسٹنگ اور فورجنگ کے لیے موزوں نہیں ہیں اور استعمال کیے جا سکتے ہیں۔ گرم isostatic دبانے کا نقصان اس کا زیادہ سائیکل وقت اور اس وجہ سے لاگت ہے۔ یہ کم حجم والے اہم حصوں کے لیے موزوں ہے۔ دھاتی انجیکشن مولڈنگ: پتلی دیواروں اور تفصیلی جیومیٹریوں کے ساتھ پیچیدہ حصوں کی تیاری کے لیے بہت موزوں عمل۔ چھوٹے حصوں کے لئے سب سے زیادہ مناسب. پاؤڈر اور پولیمر بائنڈر کو ملایا جاتا ہے، گرم کیا جاتا ہے اور ایک سانچے میں انجکشن لگایا جاتا ہے۔ پولیمر بائنڈر پاؤڈر کے ذرات کی سطحوں پر کوٹ کرتا ہے۔ مولڈنگ کے بعد، بائنڈر کو سالوینٹس کا استعمال کرتے ہوئے تحلیل کے کم درجہ حرارت کو گرم کرکے ہٹا دیا جاتا ہے۔ رول کمپیکشن / پاؤڈر رولنگ: پاؤڈر مسلسل سٹرپس یا شیٹ بنانے کے لیے استعمال ہوتے ہیں۔ پاؤڈر کو فیڈر سے کھلایا جاتا ہے اور دو گھومنے والے رولوں سے شیٹ یا سٹرپس میں کمپیکٹ کیا جاتا ہے۔ آپریشن سردی سے کیا جاتا ہے۔ شیٹ ایک sintering بھٹی میں لے جایا جاتا ہے. sintering کے عمل کو دوسری بار دہرایا جا سکتا ہے. پاؤڈر کا اخراج: بڑی لمبائی سے قطر کے تناسب والے حصے پاؤڈر کے ساتھ ایک پتلی شیٹ میٹل کنٹینر کو نکال کر تیار کیے جاتے ہیں۔ لوز سائنٹرنگ: جیسا کہ نام سے ظاہر ہوتا ہے، یہ ایک دباؤ کے بغیر کمپیکشن اور سنٹرنگ کا طریقہ ہے، جو دھاتی فلٹرز جیسے بہت غیر محفوظ حصوں کو تیار کرنے کے لیے موزوں ہے۔ پاؤڈر کو کمپیکٹ کیے بغیر مولڈ گہا میں کھلایا جاتا ہے۔ لوز سائنٹرنگ: جیسا کہ نام سے ظاہر ہوتا ہے، یہ ایک دباؤ کے بغیر کمپیکشن اور سنٹرنگ کا طریقہ ہے، جو دھاتی فلٹرز جیسے بہت غیر محفوظ حصوں کو تیار کرنے کے لیے موزوں ہے۔ پاؤڈر کو کمپیکٹ کیے بغیر مولڈ گہا میں کھلایا جاتا ہے۔ اسپارک سائنٹرنگ: پاؤڈر کو دو مخالف پنچوں سے مولڈ میں کمپریس کیا جاتا ہے اور ایک ہائی پاور برقی کرنٹ کو پنچ پر لگایا جاتا ہے اور ان کے درمیان سینڈویچ کیے ہوئے کمپیکٹڈ پاؤڈر سے گزرتا ہے۔ زیادہ کرنٹ پاؤڈر کے ذرات سے سطحی فلموں کو جلا دیتا ہے اور پیدا ہونے والی گرمی سے انہیں سنٹر کرتا ہے۔ یہ عمل تیز ہے کیونکہ گرمی باہر سے نہیں لگائی جاتی بلکہ یہ سانچے کے اندر سے پیدا ہوتی ہے۔ گرم دبانے: پاؤڈرز کو ایک ہی قدم میں ایک سانچے میں دبایا اور سنٹر کیا جاتا ہے جو زیادہ درجہ حرارت کو برداشت کر سکتا ہے۔ جیسے ہی ڈائی کمپیکٹ ہوتی ہے اس پر پاؤڈر ہیٹ لگائی جاتی ہے۔ اچھی درستگی اور مکینیکل خصوصیات جو اس طریقے سے حاصل کی جاتی ہیں اسے ایک پرکشش آپشن بناتی ہیں۔ یہاں تک کہ ریفریکٹری دھاتوں پر بھی مولڈ میٹریل جیسے گریفائٹ کا استعمال کرکے کارروائی کی جاسکتی ہے۔ CLICK Product Finder-Locator Service پچھلا مینو
- Sheet Metal Forming Fabrication, Stamping, Punching, Deep Drawing, CNC
Sheet Metal Forming and Fabrication, Stamping, Punching, Bending, Progressive Die, Spot Welding, Deep Drawing, Metal Blanking and Slitting at AGS-TECH Inc. سٹیمپنگ اور شیٹ میٹل فیبریکیشن ہم شیٹ میٹل سٹیمپنگ، شیپنگ، فارمنگ، موڑنے، پنچنگ، بلیننگ، سلٹنگ، سوراخ کرنے، نوچنگ، نبلنگ، شیونگ، پریس ورکنگ، فیبریکیشن، سنگل پنچ / سنگل اسٹروک ڈائز کے ساتھ گہری ڈرائنگ کے ساتھ ساتھ پروگریسو ڈائی اور اسپننگ، ربڑ بنانے اور بنانے کی پیشکش کرتے ہیں۔ ہائیڈروفارمنگ واٹر جیٹ، پلازما، لیزر، آری، شعلہ کا استعمال کرتے ہوئے شیٹ میٹل کاٹنا؛ ویلڈنگ، اسپاٹ ویلڈنگ کا استعمال کرتے ہوئے شیٹ میٹل اسمبلی؛ شیٹ میٹل ٹیوب ابھار اور موڑنے؛ شیٹ میٹل کی سطح کی فنشنگ بشمول ڈپ یا سپرے پینٹنگ، الیکٹرو اسٹیٹک پاؤڈر کوٹنگ، انوڈائزنگ، پلیٹنگ، سپٹرنگ اور بہت کچھ۔ ہماری خدمات تیز رفتار شیٹ میٹل پروٹو ٹائپنگ سے لے کر ہائی والیوم مینوفیکچرنگ تک ہیں۔ ہمارا مشورہ ہے کہ آپ یہاں کلک کریں۔AGS-TECH Inc کی طرف سے شیٹ میٹل فیبریکیشن اور سٹیمپنگ کے عمل کی ہماری اسکیمیٹک عکاسی ڈاؤن لوڈ کریں۔ اس سے آپ کو ان معلومات کو بہتر طور پر سمجھنے میں مدد ملے گی جو ہم آپ کو ذیل میں فراہم کر رہے ہیں۔ • شیٹ میٹل کٹنگ: ہم کٹ آف اور پارٹنگز پیش کرتے ہیں۔ کٹ آف شیٹ میٹل کو ایک وقت میں ایک ہی راستے پر کاٹتے ہیں اور بنیادی طور پر مواد کا کوئی ضیاع نہیں ہوتا ہے، جب کہ تقسیم کے ساتھ شکل کو درست طریقے سے نہیں لگایا جا سکتا اور اس لیے مواد کی کچھ مقدار ضائع ہو جاتی ہے۔ ہمارے سب سے مشہور عمل میں سے ایک Punching ہے، جہاں شیٹ میٹل سے گول یا دوسری شکل کے مواد کا ایک ٹکڑا کاٹا جاتا ہے۔ جو ٹکڑا کاٹا جاتا ہے وہ فضلہ ہے۔ چھدرن کا ایک اور ورژن SLOTTING ہے، جہاں مستطیل یا لمبے سوراخوں کو ٹھونس دیا جاتا ہے۔ دوسری طرف BLANKING وہی عمل ہے جیسا کہ گھونسہ لگانا، اس امتیاز کے ساتھ کہ ٹکڑے کاٹنا کام ہے اور رکھا جاتا ہے۔ FINE BLANKING، blanking کا ایک اعلیٰ ورژن، قریبی رواداری اور سیدھے ہموار کناروں کے ساتھ کٹ تخلیق کرتا ہے اور ورک پیس کو مکمل کرنے کے لیے ثانوی آپریشن کی ضرورت نہیں ہوتی ہے۔ ایک اور عمل جسے ہم کثرت سے استعمال کرتے ہیں وہ ہے SLITTING، جو کہ شیئرنگ کا عمل ہے جہاں شیٹ میٹل کو دو مخالف سرکلر بلیڈوں سے سیدھے یا خمیدہ راستے میں کاٹا جاتا ہے۔ کین اوپنر سلٹنگ کے عمل کی ایک سادہ مثال ہے۔ ہمارے لیے ایک اور مقبول process PERFORATING ہے، جہاں ایک خاص پیٹرن میں شیٹ میٹل میں گول یا دوسری شکل میں کئی سوراخ کیے جاتے ہیں۔ سوراخ شدہ مصنوعات کی ایک عام مثال دھات کے فلٹر ہیں جن میں سیالوں کے لیے بہت سے سوراخ ہوتے ہیں۔ نوچنگ میں، شیٹ میٹل کاٹنے کے ایک اور عمل میں، ہم ورک پیس سے مواد کو ہٹاتے ہیں، کنارے سے یا کسی اور جگہ سے شروع ہو کر اندر کی طرف کاٹتے ہیں جب تک کہ مطلوبہ شکل حاصل نہ ہو جائے۔ یہ ایک ترقی پسند عمل ہے جہاں ہر آپریشن دوسرے ٹکڑے کو ہٹاتا ہے جب تک کہ مطلوبہ سموچ حاصل نہ ہوجائے۔ چھوٹے پروڈکشن رنز کے لیے ہم بعض اوقات نسبتاً سست عمل کا استعمال کرتے ہیں جسے NIBBLING کہا جاتا ہے جس میں اوور لیپنگ ہولز کے بہت سے تیز پنچ ہوتے ہیں تاکہ زیادہ پیچیدہ کٹ بنایا جا سکے۔ پراگریسو کٹنگ میں ہم ایک ہی کٹ یا ایک مخصوص جیومیٹری حاصل کرنے کے لیے مختلف آپریشنز کا ایک سلسلہ استعمال کرتے ہیں۔ آخر میں ایک ثانوی عمل کو مونڈنے سے ہمیں کٹوتیوں کے کناروں کو بہتر بنانے میں مدد ملتی ہے جو پہلے ہی کیے جا چکے ہیں۔ یہ شیٹ میٹل کے کام پر چپس، کھردرے کناروں کو کاٹنے کے لیے استعمال کیا جاتا ہے۔ • شیٹ میٹل موڑنا: کاٹنے کے علاوہ، موڑنا ایک ضروری عمل ہے جس کے بغیر ہم زیادہ تر مصنوعات تیار نہیں کر سکیں گے۔ زیادہ تر سرد کام کرنے والا آپریشن لیکن بعض اوقات گرم یا گرم ہونے پر بھی کیا جاتا ہے۔ ہم اس آپریشن کے لیے زیادہ تر وقت ڈیز اور دباتے ہیں۔ پروگریسو بینڈنگ میں ہم ایک ہی موڑ یا ایک مخصوص جیومیٹری حاصل کرنے کے لیے مختلف پنچ اور ڈائی آپریشنز کا ایک سلسلہ استعمال کرتے ہیں۔ AGS-TECH مختلف قسم کے موڑنے کے عمل کا استعمال کرتا ہے اور ورک پیس کے مواد، اس کے سائز، موٹائی، موڑ کا مطلوبہ سائز، رداس، گھماؤ اور موڑ کا زاویہ، موڑ کا مقام، آپریشن کی معیشت، تیار کی جانے والی مقداروں کی بنیاد پر انتخاب کرتا ہے۔ وغیرہ ہم V-BENDING استعمال کرتے ہیں جہاں ایک V سائز کا پنچ شیٹ میٹل کو V شکل والی ڈائی میں مجبور کرتا ہے اور اسے موڑ دیتا ہے۔ بہت ہی شدید اور اونداز زاویوں اور درمیان میں، بشمول 90 ڈگری دونوں کے لیے اچھا ہے۔ وائپنگ ڈیز کا استعمال کرتے ہوئے ہم EDGE BENDING انجام دیتے ہیں۔ ہمارا سامان ہمیں 90 ڈگری سے بھی بڑا زاویہ حاصل کرنے کے قابل بناتا ہے۔ کنارے موڑنے میں ورک پیس کو پریشر پیڈ اور ڈائی کے درمیان سینڈویچ کیا جاتا ہے، موڑنے کا علاقہ ڈائی ایج پر واقع ہوتا ہے اور باقی ورک پیس کو space کی طرح کینٹیلیور بیم پر رکھا جاتا ہے۔ جب پنچ کینٹیلیور والے حصے پر کام کرتا ہے، تو یہ ڈائی کے کنارے پر جھک جاتا ہے۔ FLANGING ایک کنارے موڑنے کا عمل ہے جس کے نتیجے میں 90 ڈگری کا زاویہ ہوتا ہے۔ آپریشن کے اہم اہداف تیز کناروں کا خاتمہ اور پرزوں کو جوڑنے میں آسانی کے لیے جیومیٹرک سطحیں حاصل کرنا ہیں۔ بیڈنگ، کنارے کو موڑنے کا ایک اور عام عمل حصے کے کنارے پر کرل بناتا ہے۔ دوسری طرف ہیمنگ کا نتیجہ شیٹ کے ایک کنارے کے ساتھ ہوتا ہے جو خود پر مکمل طور پر جھکا ہوا ہے۔ SEAMING میں، دو حصوں کے کناروں کو ایک دوسرے پر جھکا کر جوڑ دیا جاتا ہے۔ دوسری طرف ڈبل سیمنگ واٹر ٹائٹ اور ایئر ٹائٹ شیٹ میٹل جوڑ فراہم کرتی ہے۔ کنارے موڑنے کی طرح، ROTARY BENDING نامی ایک عمل مطلوبہ زاویہ کے ساتھ ایک سلنڈر تعینات کرتا ہے اور پنچ کے طور پر کام کرتا ہے۔ جیسا کہ طاقت کو کارٹون میں منتقل کیا جاتا ہے، یہ ورک پیس کے ساتھ بند ہوجاتا ہے۔ سلنڈر کی نالی کینٹیلیور حصے کو مطلوبہ زاویہ دیتی ہے۔ نالی کا زاویہ 90 ڈگری سے چھوٹا یا بڑا ہوسکتا ہے۔ ایئر بینڈنگ میں، ہمیں زاویہ کی نالی کے لیے لوئر ڈائی کی ضرورت نہیں ہے۔ شیٹ میٹل کو مخالف سمتوں اور ایک مخصوص فاصلے پر دو سطحوں سے تعاون حاصل ہے۔ کارٹون پھر صحیح جگہ پر طاقت کا اطلاق کرتا ہے اور ورک پیس کو موڑ دیتا ہے۔ چینل موڑنے کا عمل ایک چینل کے سائز کے پنچ اور ڈائی کا استعمال کرتے ہوئے کیا جاتا ہے، اور U-BEND کو U-شکل والے پنچ سے حاصل کیا جاتا ہے۔ آف سیٹ بینڈنگ شیٹ میٹل پر آفسیٹ تیار کرتی ہے۔ ROLL BENDING، ایک تکنیک جو موٹے کام اور دھاتی پلیٹوں کے بڑے ٹکڑوں کو موڑنے کے لیے اچھی ہے، پلیٹوں کو مطلوبہ گھماؤ تک کھانا کھلانے اور موڑنے کے لیے تین رولز کا استعمال کرتی ہے۔ رولز کو ترتیب دیا جاتا ہے تاکہ کام کا مطلوبہ موڑ حاصل کیا جاسکے۔ رولز کے درمیان فاصلہ اور زاویہ مطلوبہ نتیجہ حاصل کرنے کے لیے کنٹرول کیا جاتا ہے۔ حرکت پذیر رول گھماؤ کو کنٹرول کرنا ممکن بناتا ہے۔ ٹیوب فارمنگ ایک اور مقبول شیٹ میٹل موڑنے والا آپریشن ہے جس میں متعدد ڈائی شامل ہیں۔ ٹیوبیں متعدد کارروائیوں کے بعد حاصل کی جاتی ہیں۔ CORRUGATION موڑنے کے عمل سے بھی کیا جاتا ہے۔ بنیادی طور پر یہ شیٹ میٹل کے پورے ٹکڑے میں باقاعدہ وقفوں پر موڑنے والا سڈول ہے۔ کوروگیٹنگ کے لیے مختلف شکلیں استعمال کی جا سکتی ہیں۔ نالیدار شیٹ میٹل زیادہ سخت ہے اور موڑنے کے خلاف بہتر مزاحمت رکھتی ہے اور اس وجہ سے تعمیراتی صنعت میں اس کا اطلاق ہوتا ہے۔ شیٹ میٹل رول فارمنگ، ایک مسلسل مینوفیکچرنگ کا عمل رولز کا استعمال کرتے ہوئے ایک مخصوص جیومیٹری کے کراس سیکشنز کو موڑنے کے لیے لگایا جاتا ہے اور کام کو ترتیب وار مراحل میں موڑ دیا جاتا ہے، حتمی کام مکمل کرنے کے ساتھ۔ کچھ معاملات میں ایک ہی رول اور کچھ معاملات میں رولز کی ایک سیریز کا استعمال کیا جاتا ہے۔ • مشترکہ شیٹ میٹل کٹنگ اور موڑنے کے عمل: یہ وہ عمل ہیں جو ایک ہی وقت میں کاٹتے اور موڑتے ہیں۔ PIERCING میں، ایک سوراخ ایک نوک دار پنچ کا استعمال کرتے ہوئے بنایا جاتا ہے۔ جیسے جیسے پنچ شیٹ کے سوراخ کو چوڑا کرتا ہے، مواد بیک وقت سوراخ کے لیے اندرونی فلینج میں جھک جاتا ہے۔ حاصل کردہ فلاج میں اہم کام ہو سکتے ہیں۔ دوسری طرف LANCING آپریشن اوپری جیومیٹری بنانے کے لیے شیٹ کو کاٹتا اور موڑتا ہے۔ • میٹل ٹیوب بلجنگ اور بینڈنگ: بلجنگ میں کھوکھلی ٹیوب کے کچھ اندرونی حصے پر دباؤ پڑتا ہے، جس کی وجہ سے ٹیوب باہر کی طرف بڑھ جاتی ہے۔ چونکہ ٹیوب ڈائی کے اندر ہوتی ہے، اس لیے بلج جیومیٹری کو ڈائی کی شکل سے کنٹرول کیا جاتا ہے۔ اسٹریچ بینڈنگ میں، ایک دھاتی ٹیوب کو ٹیوب کے محور کے متوازی قوتوں اور ٹیوب کو ایک فارم بلاک پر کھینچنے کے لیے موڑنے والی قوتوں کا استعمال کرتے ہوئے پھیلایا جاتا ہے۔ ڈرا موڑنے میں، ہم ٹیوب کو اس کے سرے کے قریب ایک گھومنے والے فارم بلاک کے ساتھ باندھتے ہیں جو گھومنے کے دوران ٹیوب کو موڑ دیتا ہے۔ آخر میں، کمپریشن موڑنے میں ٹیوب کو طاقت کے ذریعے ایک مقررہ شکل کے بلاک پر رکھا جاتا ہے، اور ایک ڈائی اسے فارم بلاک پر موڑ دیتی ہے۔ • ڈیپ ڈرائنگ: ہمارے مقبول ترین آپریشنز میں سے ایک میں، ایک پنچ، ایک میچنگ ڈائی اور ایک خالی ہولڈر استعمال کیا جاتا ہے۔ شیٹ میٹل خالی کو ڈائی اوپننگ کے اوپر رکھا جاتا ہے اور پنچ خالی ہولڈر کے پاس رکھے ہوئے خالی جگہ کی طرف بڑھتا ہے۔ ایک بار جب وہ رابطے میں آجائیں تو، پنچ شیٹ میٹل کو ڈائی کیویٹی میں پروڈکٹ بنانے پر مجبور کرتا ہے۔ گہری ڈرائنگ آپریشن کٹنگ سے مشابہت رکھتا ہے، تاہم پنچ اور ڈائی کے درمیان کلیئرنس شیٹ کو کاٹنے سے روکتی ہے۔ ایک اور عنصر جو اس بات کو یقینی بناتا ہے کہ شیٹ گہری کھنچی ہوئی ہے اور نہ کٹی ہوئی ہے وہ ڈائی اور پنچ کے گول کونے ہیں جو موندنے اور کاٹنے سے روکتے ہیں۔ گہری ڈرائنگ کی ایک بڑی مقدار کو حاصل کرنے کے لیے، ایک ری ڈرائنگ عمل کو تعینات کیا جا رہا ہے جہاں اس کے بعد گہری ڈرائنگ اس حصے پر ہوتی ہے جو پہلے سے ہی گہری ڈرائنگ کے عمل سے گزر چکا ہے۔ REVERSE REDRAWING میں، گہرا کھینچا ہوا حصہ پلٹ کر مخالف سمت میں کھینچا جاتا ہے۔ گہرا ڈرائنگ فاسد شکل کی اشیاء فراہم کر سکتا ہے جیسے کہ گنبد، ٹیپرڈ یا سٹیپڈ کپ، ایمبوسنگ میں ہم شیٹ میٹل کو ڈیزائن یا اسکرپٹ سے متاثر کرنے کے لیے مرد اور خواتین کے ڈائی جوڑے کا استعمال کرتے ہیں۔ • SPINNING : ایک آپریشن جہاں ایک فلیٹ یا پہلے سے تیار شدہ ورک پیس کو گھومنے والے مینڈریل اور ٹیل اسٹاک کے درمیان رکھا جاتا ہے اور ایک ٹول کام پر مقامی دباؤ کا اطلاق کرتا ہے کیونکہ یہ آہستہ آہستہ مینڈریل کو اوپر لے جاتا ہے۔ نتیجے کے طور پر، ورک پیس مینڈریل پر لپیٹا جاتا ہے اور اس کی شکل لیتا ہے. ہم اس تکنیک کو گہری ڈرائنگ کے متبادل کے طور پر استعمال کرتے ہیں جہاں آرڈر کی مقدار کم ہوتی ہے، پرزے بڑے ہوتے ہیں (20 فٹ تک قطر) اور منفرد منحنی خطوط ہوتے ہیں۔ اگرچہ فی ٹکڑا قیمتیں عام طور پر زیادہ ہوتی ہیں، CNC اسپننگ آپریشن کے لیے سیٹ اپ کی لاگت گہری ڈرائنگ کے مقابلے میں کم ہے۔ اس کے برعکس، گہری ڈرائنگ کے لیے سیٹ اپ کے لیے ابتدائی سرمایہ کاری کی ضرورت ہوتی ہے، لیکن جب زیادہ مقدار میں پرزے تیار کیے جاتے ہیں تو فی ٹکڑا لاگت کم ہوتی ہے۔ اس عمل کا ایک اور ورژن شیئر اسپننگ ہے، جہاں ورک پیس کے اندر دھات کا بہاؤ بھی ہوتا ہے۔ دھات کا بہاؤ ورک پیس کی موٹائی کو کم کردے گا جیسا کہ عمل کیا جاتا ہے۔ ابھی تک ایک اور متعلقہ عمل ٹیوب سپننگ ہے، جو بیلناکار حصوں پر لاگو کیا جاتا ہے. نیز اس عمل میں ورک پیس کے اندر دھات کا بہاؤ ہوتا ہے۔ اس طرح موٹائی کم ہو جاتی ہے اور ٹیوب کی لمبائی بڑھ جاتی ہے۔ ٹول کو ٹیوب کے اندر یا باہر خصوصیات بنانے کے لیے منتقل کیا جا سکتا ہے۔ • شیٹ میٹل کی ربڑ کی تشکیل: ربڑ یا پولی یوریتھین مواد کو ایک کنٹینر ڈائی میں ڈالا جاتا ہے اور ورک پیس کو ربڑ کی سطح پر رکھا جاتا ہے۔ اس کے بعد کام کے ٹکڑے پر ایک مکے سے کام کیا جاتا ہے اور اسے ربڑ میں زبردستی ڈال دیا جاتا ہے۔ چونکہ ربڑ سے پیدا ہونے والا دباؤ کم ہوتا ہے، اس لیے پیدا ہونے والے حصوں کی گہرائی محدود ہوتی ہے۔ چونکہ ٹولنگ کی لاگت کم ہے، اس لیے یہ عمل کم مقدار میں پیداوار کے لیے موزوں ہے۔ • ہائیڈروفارمنگ: ربڑ کی تشکیل کی طرح، اس عمل میں شیٹ میٹل کے کام کو ایک مکے کے ذریعے چیمبر کے اندر دباؤ والے مائع میں دبایا جاتا ہے۔ شیٹ میٹل کا کام پنچ اور ربڑ کے ڈایافرام کے درمیان سینڈوچ کیا جاتا ہے۔ ڈایافرام ورک پیس کو مکمل طور پر گھیر لیتا ہے اور سیال کا دباؤ اسے پنچ پر بننے پر مجبور کرتا ہے۔ اس تکنیک سے گہری ڈرائنگ کے عمل سے بھی زیادہ گہری ڈرا حاصل کی جاسکتی ہے۔ ہم آپ کے حصے کے لحاظ سے سنگل پنچ ڈیز کے ساتھ ساتھ پروگیسیو ڈائز تیار کرتے ہیں۔ سنگل اسٹروک اسٹیمپنگ ڈیز شیٹ میٹل کے سادہ پرزہ جات کی بڑی مقدار جیسے واشر جلدی سے تیار کرنے کا ایک مؤثر طریقہ ہے۔ پروگریسو ڈیز یا گہری ڈرائنگ تکنیک کو زیادہ پیچیدہ جیومیٹریز بنانے کے لیے استعمال کیا جاتا ہے۔ آپ کے کیس پر منحصر ہے، واٹر جیٹ، لیزر یا پلازما کٹنگ آپ کے شیٹ میٹل کے حصوں کو سستے، تیز اور درست طریقے سے تیار کرنے کے لیے استعمال کی جا سکتی ہے۔ بہت سے سپلائرز کو ان متبادل تکنیکوں کے بارے میں کوئی علم نہیں ہے یا ان کے پاس نہیں ہے اور اس وجہ سے وہ ڈائز اور ٹولز بنانے کے طویل اور مہنگے طریقوں سے گزرتے ہیں جس سے صرف صارفین کا وقت اور پیسہ ضائع ہوتا ہے۔ اگر آپ کو اپنی مرضی کے مطابق شیٹ میٹل پرزے کی ضرورت ہے جیسے انکلوژرز، الیکٹرانک ہاؤسنگز...وغیرہ دنوں کے اندر اندر، تو ہماری ریپڈ شیٹ میٹل پروٹو ٹائپنگ سروس کے لیے ہم سے رابطہ کریں۔ CLICK Product Finder-Locator Service پچھلا مینو
- Casting and Machined Parts, CNC Manufacturing, Milling, Turning, Swiss
Casting and Machined Parts, CNC Manufacturing, Milling, Turning, Swiss Type Machining, Die Casting, Investment Casting, Lost Foam Cast Parts from AGS-TECH Inc. کاسٹنگ اور مشیننگ ہماری اپنی مرضی کے مطابق کاسٹنگ اور مشینی تکنیک قابل خرچ اور ناقابل خرچ کاسٹنگ ہیں، فیرس اور نان فیرس کاسٹنگ، ریت، ڈائی، سینٹری فیوگل، مسلسل، سیرامک مولڈ، انویسٹمنٹ، کھوئے ہوئے فوم، قریبی نیٹ شیپ، مستقل مولڈ (گریویٹی ڈائی کاسٹنگ)، پلاسٹر۔ مولڈ (پلاسٹر کاسٹنگ) اور شیل کاسٹنگ، روایتی نیز CNC آلات کا استعمال کرتے ہوئے ملنگ اور ٹرننگ کے ذریعے تیار کردہ مشینی حصے، اعلی تھرو پٹ سستے چھوٹے درست پرزوں کے لیے سوئس قسم کی مشینی، فاسٹنرز کے لیے سکرو مشین، غیر روایتی مشینی۔ براہ کرم ذہن میں رکھیں کہ دھاتوں اور دھات کے مرکب کے علاوہ، ہم سیرامک، شیشے اور پلاسٹک کے اجزاء کے ساتھ ساتھ بعض صورتوں میں جب سڑنا تیار کرنا پسند نہیں کرتا ہے یا آپشن نہیں ہے۔ پولیمر مٹیریل کی مشیننگ کے لیے ہمارے پاس خصوصی تجربے کی ضرورت ہوتی ہے کیونکہ پلاسٹک اور ربڑ کے تحفے ان کی نرمی، غیر سختی... وغیرہ کی وجہ سے چیلنج کرتے ہیں۔ سیرامک اور شیشے کی مشینی کے لیے، براہ کرم ہمارا صفحہ غیر روایتی فیبریکیشن پر دیکھیں۔ AGS-TECH Inc. ہلکے وزن اور بھاری دونوں کاسٹنگز تیار اور سپلائی کرتا ہے۔ ہم بوائلرز، ہیٹ ایکسچینجرز، آٹوموبائلز، مائیکرو موٹرز، ونڈ ٹربائنز، فوڈ پیکیجنگ کا سامان اور بہت کچھ کے لیے میٹل کاسٹنگ اور مشینی پرزے فراہم کرتے رہے ہیں۔ ہمارا مشورہ ہے کہ آپ یہاں کلک کریں AGS-TECH Inc کے ذریعے مشینی اور کاسٹنگ کے عمل کی ہماری اسکیمیٹک عکاسی ڈاؤن لوڈ کریں۔ اس سے آپ کو ان معلومات کو بہتر طور پر سمجھنے میں مدد ملے گی جو ہم آپ کو ذیل میں فراہم کر رہے ہیں۔ آئیے کچھ مختلف تکنیکوں کو دیکھتے ہیں جو ہم تفصیل سے پیش کرتے ہیں: ایکسپینڈیبل مولڈ کاسٹنگ: اس وسیع زمرے سے مراد ایسے طریقے ہیں جن میں عارضی اور دوبارہ قابل استعمال مولڈ شامل ہیں۔ مثالیں ریت، پلاسٹر، خول، سرمایہ کاری (جسے لوسٹ ویکس بھی کہا جاتا ہے) اور پلاسٹر کاسٹنگ ہیں۔ • ریت کاسٹنگ: ایک ایسا عمل جہاں ریت کو مولڈ میٹریل کے طور پر استعمال کیا جاتا ہے۔ ایک بہت پرانا طریقہ اور اب بھی اس حد تک بہت مشہور ہے کہ زیادہ تر دھاتی کاسٹنگ اس تکنیک سے بنائی جاتی ہے۔ کم مقدار کی پیداوار پر بھی کم قیمت۔ چھوٹے اور بڑے حصوں کی تیاری کے لیے موزوں ہے۔ اس تکنیک کا استعمال بہت کم سرمایہ کاری کے ساتھ دنوں یا ہفتوں میں حصوں کی تیاری کے لیے کیا جا سکتا ہے۔ نم ریت کو مٹی، بائنڈر یا خصوصی تیل کا استعمال کرتے ہوئے ایک ساتھ جوڑا جاتا ہے۔ ریت عام طور پر مولڈ بکس میں ہوتی ہے اور ماڈلز کے گرد ریت کو کمپیکٹ کرکے کیویٹی اور گیٹ سسٹم بنایا جاتا ہے۔ عمل ہیں: 1.) سانچہ بنانے کے لیے ماڈل کو ریت میں رکھنا 2.) گیٹنگ سسٹم میں ماڈل اور ریت کو شامل کرنا 3.) ماڈل کو ہٹانا 4.) پگھلی ہوئی دھات سے مولڈ گہا کو بھرنا 5.) دھات کی ٹھنڈک 6.) ریت کے سڑنا کو توڑنا اور کاسٹنگ کو ہٹانا • پلاسٹر مولڈ کاسٹنگ: ریت کاسٹنگ کی طرح، اور ریت کے بجائے، پلاسٹر آف پیرس کو مولڈ کے مواد کے طور پر استعمال کیا جا رہا ہے۔ مختصر پیداوار لیڈ ٹائم جیسے ریت کاسٹنگ اور سستا. اچھی جہتی رواداری اور سطح ختم۔ اس کا بڑا نقصان یہ ہے کہ اسے صرف کم پگھلنے والی دھاتوں جیسے ایلومینیم اور زنک کے ساتھ استعمال کیا جا سکتا ہے۔ • شیل مولڈ کاسٹنگ: ریت کاسٹنگ کی طرح بھی۔ مولڈ کیویٹی ریت کے سخت خول اور تھرموسیٹنگ رال بائنڈر سے حاصل کی گئی فلاسک کی بجائے ریت سے بھری ہوئی ریت کاسٹنگ کے عمل میں۔ ریت کے ذریعے کاسٹ کرنے کے لیے موزوں تقریباً کسی بھی دھات کو شیل مولڈنگ کے ذریعے کاسٹ کیا جا سکتا ہے۔ اس عمل کا خلاصہ اس طرح کیا جا سکتا ہے: 1.) شیل سڑنا کی تیاری. ریت کاسٹنگ میں استعمال ہونے والی ریت کے مقابلے میں استعمال ہونے والی ریت بہت چھوٹے دانے کے سائز کی ہوتی ہے۔ باریک ریت کو تھرموسیٹنگ رال کے ساتھ ملایا جاتا ہے۔ دھاتی پیٹرن کو الگ کرنے والے ایجنٹ کے ساتھ لیپت کیا جاتا ہے تاکہ شیل کو ہٹانا آسان ہو۔ اس کے بعد دھاتی پیٹرن کو گرم کیا جاتا ہے اور ریت کے مرکب کو گرم کاسٹنگ پیٹرن پر چھید یا اڑا دیا جاتا ہے۔ پیٹرن کی سطح پر ایک پتلا خول بنتا ہے۔ اس خول کی موٹائی کو ریت کے رال کے مرکب کے دھاتی پیٹرن کے ساتھ رابطے میں آنے کے وقت کی لمبائی کو مختلف کرکے ایڈجسٹ کیا جاسکتا ہے۔ پھر ڈھیلی ریت کو شیل سے ڈھکے ہوئے پیٹرن کے ساتھ ہٹا دیا جاتا ہے۔ 2.) اگلا، شیل اور پیٹرن کو ایک تندور میں گرم کیا جاتا ہے تاکہ شیل سخت ہو جائے۔ سختی مکمل ہونے کے بعد، شیل کو پیٹرن میں بنے ہوئے پنوں کا استعمال کرتے ہوئے پیٹرن سے نکال دیا جاتا ہے۔ 3.) اس طرح کے دو خولوں کو گلونگ یا کلیمپنگ کے ذریعے ایک ساتھ جوڑا جاتا ہے اور مکمل سانچہ بناتا ہے۔ اب شیل مولڈ کو ایک کنٹینر میں داخل کیا جاتا ہے جس میں اسے کاسٹنگ کے عمل کے دوران ریت یا دھاتی شاٹ سے سہارا دیا جاتا ہے۔ 4.) اب گرم دھات کو شیل مولڈ میں ڈالا جا سکتا ہے۔ شیل کاسٹنگ کے فوائد بہت اچھی سطح کی تکمیل کے ساتھ مصنوعات ہیں، اعلی جہتی درستگی کے ساتھ پیچیدہ حصوں کی تیاری کا امکان، خود کار طریقے سے آسان عمل، بڑے حجم کی پیداوار کے لیے اقتصادی۔ نقصانات یہ ہیں کہ سانچوں کو اچھی وینٹیلیشن کی ضرورت ہوتی ہے کیونکہ ان گیسوں کی وجہ سے جو پگھلی ہوئی دھات بائنڈر کیمیکل سے رابطہ کرتی ہیں، تھرموسیٹنگ رال اور دھاتی پیٹرن مہنگے ہوتے ہیں۔ دھاتی پیٹرن کی لاگت کی وجہ سے، کم مقدار کی پیداوار کے رنز کے لیے یہ تکنیک مناسب نہیں ہوسکتی ہے۔ • انوسٹمنٹ کاسٹنگ (جسے لوسٹ-ویکس کاسٹنگ بھی کہا جاتا ہے): نیز ایک بہت پرانی تکنیک اور بہت سی دھاتوں، ریفریکٹری میٹریلز اور خاص اعلی کارکردگی والے مرکبات سے اعلیٰ درستگی، تکرار پذیری، استعداد اور سالمیت کے ساتھ معیاری پرزوں کی تیاری کے لیے موزوں ہے۔ چھوٹے اور بڑے سائز کے حصے بھی تیار کیے جا سکتے ہیں۔ کچھ دوسرے طریقوں کے مقابلے میں ایک مہنگا عمل ہے، لیکن بڑا فائدہ یہ ہے کہ قریب کی خالص شکل، پیچیدہ شکل اور تفصیلات کے ساتھ پرزے تیار کرنے کا امکان ہے۔ لہذا لاگت کچھ معاملات میں دوبارہ کام اور مشینی کے خاتمے سے کچھ حد تک آفسیٹ ہوتی ہے۔ اگرچہ تغیرات ہو سکتے ہیں، یہاں عام سرمایہ کاری کاسٹنگ عمل کا خلاصہ ہے: 1.) موم یا پلاسٹک سے اصل ماسٹر پیٹرن کی تخلیق. ہر کاسٹنگ کو ایک پیٹرن کی ضرورت ہوتی ہے کیونکہ یہ عمل میں تباہ ہو جاتے ہیں۔ سڑنا جس سے پیٹرن تیار کیے جاتے ہیں اس کی بھی ضرورت ہوتی ہے اور زیادہ تر وقت مولڈ کاسٹ یا مشینی ہوتا ہے۔ چونکہ مولڈ کو کھولنے کی ضرورت نہیں ہے، پیچیدہ کاسٹنگ حاصل کی جا سکتی ہے، موم کے بہت سے نمونوں کو درخت کی شاخوں کی طرح جوڑا جا سکتا ہے اور ایک ساتھ ڈالا جا سکتا ہے، اس طرح دھات یا دھات کے مرکب کے ایک ہی انڈیلنے سے متعدد حصوں کی پیداوار کو قابل بنایا جا سکتا ہے۔ 2.) اس کے بعد، پیٹرن کو بہت باریک دانے دار سلیکا، پانی، بائنڈرز پر مشتمل ریفریکٹری سلوری کے ساتھ ڈبو یا ڈالا جاتا ہے۔ اس کے نتیجے میں پیٹرن کی سطح پر سیرامک پرت بنتی ہے۔ پیٹرن پر ریفریکٹری کوٹ کو خشک اور سخت ہونے کے لیے چھوڑ دیا گیا ہے۔ یہ مرحلہ وہ ہے جہاں سے سرمایہ کاری کا نام آتا ہے: ریفریکٹری سلوری کو موم کے انداز پر لگایا جاتا ہے۔ 3.) اس مرحلے پر، سخت سیرامک مولڈ کو الٹا اور گرم کیا جاتا ہے تاکہ موم پگھل جائے اور سانچے سے باہر نکل جائے۔ دھاتی کاسٹنگ کے لیے ایک گہا پیچھے رہ گیا ہے۔ 4.) موم کے باہر ہونے کے بعد، سیرامک مولڈ کو زیادہ درجہ حرارت پر گرم کیا جاتا ہے جس کے نتیجے میں سڑنا مضبوط ہوتا ہے۔ 5.) دھاتی کاسٹنگ تمام پیچیدہ حصوں کو بھرنے والے گرم سانچے میں ڈالی جاتی ہے۔ 6.) کاسٹنگ کو مضبوط کرنے کی اجازت ہے۔ 7.) آخر میں سیرامک مولڈ ٹوٹ جاتا ہے اور تیار شدہ حصے درخت سے کاٹے جاتے ہیں۔ انویسٹمنٹ کاسٹنگ پلانٹ بروشر کا لنک یہ ہے۔ ایواپوریٹیو پیٹرن کاسٹنگ: اس عمل میں پولی اسٹیرین فوم جیسے مواد سے بنے پیٹرن کا استعمال کیا جاتا ہے جو گرم پگھلی ہوئی دھات کو سانچے میں ڈالنے پر بخارات بن جاتا ہے۔ اس عمل کی دو قسمیں ہیں: کھوئی ہوئی فوم کاسٹنگ جو بغیر بندھے ہوئے ریت کا استعمال کرتی ہے اور مکمل مولڈ کاسٹنگ جو بندھے ہوئے ریت کا استعمال کرتی ہے۔ یہاں عام عمل کے اقدامات ہیں: 1.) پولی اسٹیرین جیسے مواد سے پیٹرن تیار کریں۔ جب بڑی مقدار میں تیار کیا جائے گا، پیٹرن مولڈ کیا جاتا ہے. اگر حصہ پیچیدہ شکل رکھتا ہے، تو اس طرح کے جھاگ کے مواد کے کئی حصوں کو پیٹرن بنانے کے لیے ایک ساتھ جوڑنے کی ضرورت پڑسکتی ہے۔ ہم اکثر پیٹرن کو ایک ریفریکٹری کمپاؤنڈ کے ساتھ کوٹ کرتے ہیں تاکہ کاسٹنگ پر اچھی سطح کی تکمیل ہو۔ 2.) پیٹرن پھر مولڈنگ ریت میں ڈال دیا جاتا ہے. 3.) پگھلی ہوئی دھات کو سانچے میں ڈالا جاتا ہے، فوم پیٹرن کو بخارات بناتا ہے، یعنی پولی اسٹیرین زیادہ تر معاملات میں جب یہ مولڈ گہا سے گزرتی ہے۔ 4.) پگھلی ہوئی دھات کو سخت ہونے کے لیے ریت کے سانچے میں چھوڑ دیا جاتا ہے۔ 5.) سخت ہونے کے بعد، ہم معدنیات سے متعلق ہٹا دیتے ہیں. بعض صورتوں میں، ہم جس پروڈکٹ کو تیار کرتے ہیں اسے پیٹرن کے اندر ایک کور کی ضرورت ہوتی ہے۔ evaporative کاسٹنگ میں، مولڈ گہا میں کور رکھنے اور محفوظ کرنے کی ضرورت نہیں ہے۔ یہ تکنیک بہت پیچیدہ جیومیٹریوں کی تیاری کے لیے موزوں ہے، یہ اعلی حجم کی پیداوار کے لیے آسانی سے خودکار ہو سکتی ہے، اور کاسٹ کے حصے میں کوئی الگ کرنے والی لائنیں نہیں ہیں۔ بنیادی عمل سادہ اور لاگو کرنے کے لئے اقتصادی ہے. بڑے حجم کی پیداوار کے لیے، چونکہ پولی اسٹیرین سے پیٹرن تیار کرنے کے لیے ڈائی یا مولڈ کی ضرورت ہوتی ہے، اس لیے یہ کچھ مہنگا پڑ سکتا ہے۔ • غیر قابل توسیع مولڈ کاسٹنگ: اس وسیع زمرے سے مراد وہ طریقے ہیں جہاں ہر پیداواری دور کے بعد مولڈ کو درست کرنے کی ضرورت نہیں ہے۔ مثالیں مستقل، مرنے، مسلسل اور سینٹری فیوگل کاسٹنگ ہیں۔ تکرار کی صلاحیت حاصل کی جاتی ہے اور حصوں کو NEAR NET SHAPE کے طور پر نمایاں کیا جا سکتا ہے۔ • مستقل مولڈ کاسٹنگ: دھات سے بنے دوبارہ قابل استعمال سانچوں کو متعدد کاسٹنگ کے لیے استعمال کیا جاتا ہے۔ ایک مستقل سڑنا عام طور پر ختم ہونے سے پہلے دسیوں ہزار بار استعمال کیا جا سکتا ہے۔ کشش ثقل، گیس پریشر یا ویکیوم عام طور پر سڑنا بھرنے کے لیے استعمال ہوتے ہیں۔ سانچوں (جسے ڈائی بھی کہا جاتا ہے) عام طور پر لوہے، سٹیل، سیرامک یا دیگر دھاتوں سے بنے ہوتے ہیں۔ عام عمل ہے: 1.) مشین بنائیں اور سڑنا بنائیں۔ دو دھاتی بلاکس میں سے مولڈ کو مشین بنانا ایک عام بات ہے جو ایک ساتھ فٹ بیٹھتے ہیں اور کھولے اور بند کیے جا سکتے ہیں۔ دونوں حصے کی خصوصیات کے ساتھ ساتھ گیٹنگ سسٹم کو عام طور پر کاسٹنگ مولڈ میں مشین کیا جاتا ہے۔ 2.) اندرونی سڑنا کی سطحوں کو ریفریکٹری مواد کو شامل کرتے ہوئے گارا کے ساتھ لیپت کیا گیا ہے۔ یہ گرمی کے بہاؤ کو کنٹرول کرنے میں مدد کرتا ہے اور کاسٹ کے حصے کو آسانی سے ہٹانے کے لیے چکنا کرنے والے کے طور پر کام کرتا ہے۔ 3.) اگلا، سڑنا کے مستقل حصوں کو بند کر دیا جاتا ہے اور مولڈ کو گرم کیا جاتا ہے۔ 4.) پگھلی ہوئی دھات کو سانچے میں ڈالا جاتا ہے اور اسے مستحکم کرنے کے لیے چھوڑ دیا جاتا ہے۔ 5.) زیادہ ٹھنڈک ہونے سے پہلے، جب سڑنا کے آدھے حصے کھل جاتے ہیں تو ہم ایجیکٹرز کا استعمال کرتے ہوئے مستقل مولڈ سے حصہ نکال دیتے ہیں۔ ہم اکثر کم پگھلنے والی دھاتوں جیسے زنک اور ایلومینیم کے لیے مستقل مولڈ کاسٹنگ کا استعمال کرتے ہیں۔ سٹیل کاسٹنگ کے لیے، ہم گریفائٹ کو مولڈ میٹریل کے طور پر استعمال کرتے ہیں۔ ہم بعض اوقات مستقل سانچوں کے اندر کور کا استعمال کرتے ہوئے پیچیدہ جیومیٹریاں حاصل کرتے ہیں۔ اس تکنیک کے فوائد میں تیزی سے ٹھنڈک، خصوصیات میں یکسانیت، اچھی درستگی اور سطح کی تکمیل، کم مسترد ہونے کی شرح، عمل کو خودکار کرنے کا امکان اور اقتصادی طور پر زیادہ حجم پیدا کرنے کے ذریعے حاصل کی جانے والی اچھی میکانکی خصوصیات کے ساتھ کاسٹنگ ہیں۔ نقصانات اعلیٰ ابتدائی سیٹ اپ اخراجات ہیں جو اسے کم حجم کے آپریشنز کے لیے غیر موزوں بناتے ہیں، اور تیار کردہ پرزوں کے سائز پر پابندیاں۔ • ڈائی کاسٹنگ: ڈائی مشین کی جاتی ہے اور پگھلی ہوئی دھات کو زیادہ دباؤ کے تحت مولڈ گہاوں میں دھکیل دیا جاتا ہے۔ نان فیرس اور فیرس میٹل ڈائی کاسٹنگ دونوں ممکن ہیں۔ یہ عمل تفصیلات، انتہائی پتلی دیواروں، جہتی مستقل مزاجی اور اچھی سطح کی تکمیل کے ساتھ چھوٹے سے درمیانے سائز کے حصوں کی اعلیٰ مقدار میں پیداوار کے لیے موزوں ہے۔ AGS-TECH Inc. اس تکنیک کا استعمال کرتے ہوئے دیوار کی موٹائی 0.5 ملی میٹر تک تیار کرنے کے قابل ہے۔ مستقل مولڈ کاسٹنگ کی طرح، مولڈ میں دو حصوں پر مشتمل ہونا ضروری ہے جو پیدا ہونے والے حصے کو ہٹانے کے لیے کھل اور بند ہو سکتے ہیں۔ ایک ڈائی کاسٹنگ مولڈ میں ہر سائیکل کے ساتھ ایک سے زیادہ کاسٹنگ کی پیداوار کو قابل بنانے کے لیے متعدد گہا ہو سکتے ہیں۔ ڈائی کاسٹنگ مولڈ بہت بھاری ہوتے ہیں اور ان پرزوں سے بہت بڑے ہوتے ہیں، اس لیے مہنگے بھی ہوتے ہیں۔ جب تک وہ اپنے پرزہ جات ہم سے دوبارہ ترتیب دیتے ہیں ہم اپنے صارفین کے لیے بغیر کسی معاوضے کی مرمت اور تبدیل کرتے ہیں۔ ہمارے مرنے والوں کی کئی لاکھ سائیکلوں کی حد میں لمبی عمر ہوتی ہے۔ یہاں بنیادی آسان عمل کے اقدامات ہیں: 1.) عام طور پر سٹیل سے سڑنا کی پیداوار 2.) ڈائی کاسٹنگ مشین پر مولڈ نصب ہے۔ 3.) پسٹن پیچیدہ خصوصیات اور پتلی دیواروں کو بھرتے ہوئے پگھلی ہوئی دھات کو ڈائی کیویٹیز میں بہنے پر مجبور کرتا ہے۔ 4.) پگھلی ہوئی دھات سے سڑنا بھرنے کے بعد، کاسٹنگ کو دباؤ میں سخت ہونے دیا جاتا ہے۔ 5.) مولڈ کو کھولا جاتا ہے اور ایجیکٹر پن کی مدد سے کاسٹنگ کو ہٹا دیا جاتا ہے۔ 6.) اب خالی ڈائی کو دوبارہ چکنا کر دیا جاتا ہے اور اگلے چکر کے لیے کلیمپ کیا جاتا ہے۔ ڈائی کاسٹنگ میں، ہم اکثر انسرٹ مولڈنگ کا استعمال کرتے ہیں جہاں ہم مولڈ میں ایک اضافی حصہ شامل کرتے ہیں اور اس کے ارد گرد دھات ڈالتے ہیں۔ مضبوطی کے بعد، یہ حصے کاسٹ پروڈکٹ کا حصہ بن جاتے ہیں۔ ڈائی کاسٹنگ کے فوائد پرزوں کی اچھی مکینیکل خصوصیات، پیچیدہ خصوصیات کا امکان، عمدہ تفصیلات اور اچھی سطح کی تکمیل، اعلی پیداوار کی شرح، آسان آٹومیشن ہیں۔ نقصانات یہ ہیں: کم حجم کے لیے موزوں نہیں کیونکہ زیادہ ڈائی اور سامان کی لاگت، کاسٹ کی جا سکتی شکلوں میں محدودیت، ایجیکٹر پنوں کے رابطے کے نتیجے میں کاسٹ پرزوں پر چھوٹے گول نشان، الگ کرنے والی لائن پر دھات کی پتلی چمک، ضرورت ڈائی کے درمیان علیحدگی کی لکیر کے ساتھ وینٹ کے لیے، پانی کی گردش کا استعمال کرتے ہوئے سڑنا کا درجہ حرارت کم رکھنے کی ضرورت ہے۔ • سینٹرفیوگل کاسٹنگ: پگھلی ہوئی دھات کو گردش کے محور پر گھومنے والے سانچے کے مرکز میں ڈالا جاتا ہے۔ سینٹرفیوگل قوتیں دھات کو دائرہ کی طرف پھینکتی ہیں اور اسے مضبوط ہونے دیا جاتا ہے کیونکہ سانچہ گھومتا رہتا ہے۔ افقی اور عمودی محور دونوں گردشیں استعمال کی جا سکتی ہیں۔ گول اندرونی سطحوں کے ساتھ ساتھ دیگر غیر گول شکلوں والے حصے کاسٹ کیے جا سکتے ہیں۔ اس عمل کا خلاصہ اس طرح کیا جا سکتا ہے: 1.) پگھلی ہوئی دھات کو سینٹرفیوگل مولڈ میں ڈالا جاتا ہے۔ پھر دھات کو مولڈ کے گھومنے کی وجہ سے بیرونی دیواروں پر مجبور کیا جاتا ہے۔ 2.) جیسے جیسے سڑنا گھومتا ہے، دھاتی کاسٹنگ سخت ہوتی جاتی ہے۔ سینٹرفیوگل کاسٹنگ پائپ جیسے کھوکھلے بیلناکار حصوں کی تیاری کے لیے ایک موزوں تکنیک ہے، اسپروز، رائزرز اور گیٹنگ عناصر کی ضرورت نہیں، سطح کی اچھی تکمیل اور تفصیلی خصوصیات، سکڑنے کا کوئی مسئلہ نہیں، بہت بڑے قطر کے ساتھ لمبے پائپ تیار کرنے کا امکان، اعلی شرح پیداواری صلاحیت۔ . • مسلسل کاسٹنگ ( اسٹرینڈ کاسٹنگ ) : دھات کی مسلسل لمبائی کاسٹ کرنے کے لیے استعمال کیا جاتا ہے۔ بنیادی طور پر پگھلی ہوئی دھات کو مولڈ کے دو جہتی پروفائل میں ڈالا جاتا ہے لیکن اس کی لمبائی غیر متعین ہوتی ہے۔ نئی پگھلی ہوئی دھات کو مسلسل سانچے میں ڈالا جاتا ہے کیونکہ کاسٹنگ وقت کے ساتھ ساتھ اس کی لمبائی میں اضافے کے ساتھ نیچے کی طرف سفر کرتی ہے۔ کاپر، سٹیل، ایلومینیم جیسی دھاتوں کو مسلسل کاسٹنگ کے عمل کے ذریعے لمبے کناروں میں ڈالا جاتا ہے۔ اس عمل کی مختلف ترتیبیں ہو سکتی ہیں لیکن عام کو اس طرح آسان بنایا جا سکتا ہے: 1.) پگھلی ہوئی دھات کو ایک کنٹینر میں ڈالا جاتا ہے جو مولڈ کے اوپر واقع ہے اچھی طرح سے حساب شدہ مقدار اور بہاؤ کی شرح پر اور پانی کے ٹھنڈے سانچے میں سے بہتا ہے۔ سانچے میں ڈالی جانے والی دھاتی کاسٹنگ مولڈ کے نچلے حصے میں رکھی ہوئی اسٹارٹر بار میں مضبوط ہو جاتی ہے۔ یہ اسٹارٹر بار رولرس کو ابتدائی طور پر پکڑنے کے لیے کچھ دیتا ہے۔ 2.) طویل دھاتی اسٹرینڈ کو رولرس کے ذریعے مسلسل رفتار سے اٹھایا جاتا ہے۔ رولر دھاتی پٹی کے بہاؤ کی سمت کو عمودی سے افقی تک بھی تبدیل کرتے ہیں۔ 3.) مسلسل کاسٹنگ کے ایک مخصوص افقی فاصلہ طے کرنے کے بعد، ایک ٹارچ یا آری جو کاسٹنگ کے ساتھ حرکت کرتی ہے اسے تیزی سے مطلوبہ لمبائی تک کاٹ دیتی ہے۔ مسلسل کاسٹنگ کے عمل کو رولنگ پروسیس کے ساتھ مربوط کیا جا سکتا ہے، جہاں مسلسل کاسٹ شدہ دھات کو براہ راست رولنگ مل میں فیڈ کیا جا سکتا ہے تاکہ I-Beams، T-Beams…. وغیرہ۔ مسلسل کاسٹنگ پوری پروڈکٹ میں یکساں خصوصیات پیدا کرتی ہے، اس میں مضبوطی کی شرح بہت زیادہ ہے، مواد کے بہت کم نقصان کی وجہ سے لاگت میں کمی آتی ہے، ایک ایسا عمل پیش کرتا ہے جہاں دھات کو لوڈ کرنا، ڈالنا، ٹھوس بنانا، کاٹنا اور کاسٹنگ ہٹانا یہ سب ایک مسلسل آپریشن میں ہوتا ہے اور اس طرح اعلی پیداوری کی شرح اور اعلی معیار کے نتیجے میں. تاہم ایک اہم غور اعلیٰ ابتدائی سرمایہ کاری، سیٹ اپ کے اخراجات اور جگہ کی ضروریات ہیں۔ • مشینی خدمات: ہم تین، چار اور پانچ - محور مشینی پیش کرتے ہیں۔ ہم جس قسم کے مشینی عمل کا استعمال کرتے ہیں وہ ہیں ٹرننگ، ملنگ، ڈرلنگ، بورنگ، بروچنگ، پلاننگ، ساونگ، گرائنڈنگ، لیپنگ، پالشنگ اور غیر روایتی مشینیں جو ہماری ویب سائٹ کے ایک مختلف مینو کے تحت مزید تفصیل سے بیان کی گئی ہیں۔ ہماری زیادہ تر مینوفیکچرنگ کے لیے، ہم CNC مشینیں استعمال کرتے ہیں۔ تاہم کچھ آپریشنز کے لیے روایتی تکنیکیں بہتر ہیں اور اس لیے ہم ان پر بھی بھروسہ کرتے ہیں۔ ہماری مشینی صلاحیتیں ممکنہ حد تک بلند ترین سطح تک پہنچ جاتی ہیں اور کچھ انتہائی مطلوبہ پرزے AS9100 تصدیق شدہ پلانٹ میں تیار کیے جاتے ہیں۔ جیٹ انجن کے بلیڈ کے لیے انتہائی خصوصی مینوفیکچرنگ کے تجربے اور صحیح آلات کی ضرورت ہوتی ہے۔ ایرو اسپیس انڈسٹری کے بہت سخت معیارات ہیں۔ پیچیدہ جیومیٹریکل ڈھانچے کے ساتھ کچھ اجزاء پانچ محور مشینی کے ذریعہ سب سے زیادہ آسانی سے تیار کیے جاتے ہیں، جو صرف ہمارے بشمول کچھ مشینی پلانٹس میں پائے جاتے ہیں۔ ہمارے ایرو اسپیس سرٹیفائیڈ پلانٹ کے پاس ایرو اسپیس انڈسٹری کی وسیع دستاویزات کی ضروریات کو پورا کرنے کا ضروری تجربہ ہے۔ ٹرننگ آپریشنز میں، ایک ورک پیس کو گھمایا جاتا ہے اور اسے کاٹنے والے آلے کے خلاف منتقل کیا جاتا ہے۔ اس عمل کے لیے لیتھ نامی مشین استعمال کی جا رہی ہے۔ ملنگ میں، ملنگ مشین کہلانے والی مشین میں ایک گھومنے والا ٹول ہوتا ہے جو کٹنگ کناروں کو ورک پیس کے خلاف برداشت کرنے کے لیے لاتا ہے۔ ڈرلنگ کے کاموں میں ایک گھومنے والا کٹر ہوتا ہے جس میں کناروں کا کٹا ہوا ہوتا ہے جو ورک پیس کے ساتھ رابطے پر سوراخ پیدا کرتا ہے۔ ڈرل پریس، لیتھز یا ملز عام طور پر استعمال ہوتے ہیں۔ بورنگ آپریشنز میں ایک ٹول کو ایک ہی جھکی ہوئی نوک کے ساتھ گھومنے والی ورک پیس میں کسی کھردرے سوراخ میں منتقل کیا جاتا ہے تاکہ سوراخ کو تھوڑا بڑا کیا جا سکے اور درستگی کو بہتر بنایا جا سکے۔ یہ ٹھیک ختم کرنے کے مقاصد کے لئے استعمال کیا جاتا ہے. بروچنگ میں بروچ کے ایک پاس میں ورک پیس سے مواد کو ہٹانے کے لیے دانتوں والا ٹول شامل ہوتا ہے۔ لکیری بروچنگ میں، بروچ کٹ کو متاثر کرنے کے لیے ورک پیس کی سطح کے خلاف لکیری طور پر چلتا ہے، جب کہ روٹری بروچنگ میں، بروچ کو گھما کر ورک پیس میں دبایا جاتا ہے تاکہ محور کی ہم آہنگی کی شکل کو کاٹ سکے۔ SWISS TYPE MACHINING ہماری قیمتی تکنیکوں میں سے ایک ہے جسے ہم چھوٹے اعلی صحت سے متعلق حصوں کی اعلی حجم کی تیاری کے لیے استعمال کرتے ہیں۔ سوئس قسم کی لیتھ کا استعمال کرتے ہوئے ہم چھوٹے، پیچیدہ، درست پرزوں کو سستے میں موڑ دیتے ہیں۔ روایتی لیتھز کے برعکس جہاں ورک پیس کو سٹیشنری اور ٹول حرکت میں رکھا جاتا ہے، سوئس قسم کے ٹرننگ سینٹرز میں، ورک پیس کو Z-axis میں منتقل کرنے کی اجازت ہے اور ٹول سٹیشنری ہے۔ سوئس قسم کی مشینی میں، بار سٹاک کو مشین میں رکھا جاتا ہے اور z-axis میں گائیڈ بشنگ کے ذریعے آگے بڑھایا جاتا ہے، صرف مشینی ہونے والے حصے کو بے نقاب کرتا ہے۔ اس طرح ایک سخت گرفت کو یقینی بنایا جاتا ہے اور درستگی بہت زیادہ ہوتی ہے۔ لائیو ٹولز کی دستیابی گائیڈ بشنگ سے مواد کی ترقی کے ساتھ مل اور ڈرل کرنے کا موقع فراہم کرتی ہے۔ سوئس قسم کے آلات کا Y-axis مکمل گھسائی کرنے کی صلاحیت فراہم کرتا ہے اور مینوفیکچرنگ میں بہت زیادہ وقت بچاتا ہے۔ مزید برآں، ہماری مشینوں میں ڈرلز اور بورنگ ٹولز ہوتے ہیں جو اس حصے پر کام کرتے ہیں جب اسے سب سپنڈل میں رکھا جاتا ہے۔ ہماری سوئس قسم کی مشینی صلاحیت ہمیں ایک ہی آپریشن میں مکمل طور پر خودکار مکمل مشیننگ کا موقع فراہم کرتی ہے۔ مشیننگ AGS-TECH Inc. کاروبار کے سب سے بڑے حصوں میں سے ایک ہے۔ ہم یا تو اسے پرائمری آپریشن کے طور پر استعمال کرتے ہیں یا کسی حصے کو کاسٹ کرنے یا نکالنے کے بعد ثانوی آپریشن کے طور پر استعمال کرتے ہیں تاکہ ڈرائنگ کی تمام وضاحتیں پوری ہوں۔ • سرفیس فنشنگ سروسز: ہم سطح کے علاج اور سطح کی فنشنگ کی وسیع اقسام پیش کرتے ہیں جیسے چپکنے کو بڑھانے کے لیے سطح کی کنڈیشنگ، کوٹنگ کے چپکنے کو بڑھانے کے لیے پتلی آکسائیڈ کی تہہ جمع کرنا، سینڈ بلاسٹنگ، کیم فلم، انوڈائزنگ، نائٹرائڈنگ، پاؤڈر کوٹنگ، سپرے کوٹنگ۔ , مختلف جدید میٹالائزیشن اور کوٹنگ کی تکنیکیں بشمول سپٹرنگ، الیکٹران بیم، بخارات، چڑھانا، سخت کوٹنگز جیسے ہیرے جیسے کاربن (DLC) یا ٹائٹینیم کوٹنگ ڈرلنگ اور کٹنگ ٹولز کے لیے۔ • پروڈکٹ مارکنگ اور لیبلنگ کی خدمات: ہمارے بہت سے صارفین کو مارکنگ اور لیبلنگ، لیزر مارکنگ، دھاتی حصوں پر کندہ کاری کی ضرورت ہوتی ہے۔ اگر آپ کو ایسی کوئی ضرورت ہے تو آئیے اس پر بات کریں کہ کون سا آپشن آپ کے لیے بہترین ہوگا۔ یہاں عام طور پر استعمال ہونے والی دھاتی کاسٹ مصنوعات میں سے کچھ ہیں۔ چونکہ یہ شیلف سے باہر ہیں، اگر ان میں سے کوئی بھی آپ کی ضروریات کے مطابق ہو تو آپ مولڈ کے اخراجات کو بچا سکتے ہیں: AGS-Electronics سے ہمارے 11 سیریز کے ڈائی کاسٹ ایلومینیم باکسز ڈاؤن لوڈ کرنے کے لیے یہاں کلک کریں۔ CLICK Product Finder-Locator Service پچھلا صفحہ
- Custom Manufactured Parts, Assemblies, Plastic Mold, Casting,Machining
Custom Manufactured Parts, Assemblies, Plastic Mold, Rubber Molding, Metal Casting, CNC Machining, Turning, Milling, Electrical Electronic Optical Assembly PCBA حسب ضرورت تیار کردہ پرزے & اسمبلیاں اور مصنوعات مزید پڑھ پلاسٹک اور ربڑ کے سانچے اور مولڈنگ مزید پڑھ کاسٹنگ اور مشیننگ مزید پڑھ Extrusions، Extruded مصنوعات مزید پڑھ سٹیمپنگ اور شیٹ میٹل فیبریکیشن مزید پڑھ میٹل فورجنگ اور پاؤڈر میٹالرجی مزید پڑھ تار اور بہار کی تشکیل مزید پڑھ شیشہ اور سرامک کی تشکیل اور تشکیل مزید پڑھ اضافی اور تیز رفتار مینوفیکچرنگ مزید پڑھ کمپوزٹ اور کمپوزٹ میٹریل مینوفیکچرنگ مزید پڑھ شمولیت اور اسمبلی اور باندھنے کے عمل ہم آپ کے لیے پرزے اور اسمبلیاں تیار کرتے ہیں اور مینوفیکچرنگ کے درج ذیل عمل پیش کرتے ہیں: • پلاسٹک اور ربڑ کے سانچوں اور ڈھلے ہوئے حصے۔ انجکشن مولڈنگ، تھرموفارمنگ، تھرموسیٹ مولڈنگ، ویکیوم فارمنگ، بلو مولڈنگ، روٹیشنل مولڈنگ، پوور مولڈنگ، انسرٹ مولڈنگ اور دیگر۔ • پلاسٹک، ربڑ اور دھات کے اخراج • فیرس اور نان فیرس کاسٹنگ اور مشینی حصے جو گھسائی کرنے اور موڑنے کی تکنیکوں، سوئس قسم کی مشینی سے تیار ہوتے ہیں۔ • پاؤڈر دھات کاری کے حصے • دھاتی اور نان میٹل سٹیمپنگ، شیٹ میٹل کی تشکیل، ویلڈیڈ شیٹ میٹل اسمبلیاں • ٹھنڈا اور گرم فورجنگ • تاریں، ویلڈیڈ تار اسمبلیاں، تار بنانا • مختلف قسم کے چشمے، بہار کی تشکیل • گیئر مینوفیکچرنگ، گیئر باکس، کپلنگ، کیڑا، رفتار کم کرنے والا، سلنڈر، ٹرانسمیشن بیلٹ، ٹرانسمیشن چینز، ٹرانسمیشن کے اجزاء • نیٹو اور فوجی معیارات کے مطابق حسب ضرورت اور بلٹ پروف گلاس • بالز، بیرنگ، گھرنی اور گھرنی اسمبلیاں • والوز اور نیومیٹک اجزاء جیسے O-ring، واشر اور سیل • شیشے اور سیرامک کے حصے اور اسمبلیاں، ویکیوم پروف اور ہرمیٹک اجزاء، دھاتی سیرامک اور سیرامک-سیرامک بانڈنگ۔ • مختلف قسم کے مکینیکل، آپٹو مکینیکل، الیکٹرو مکینیکل، آپٹو الیکٹرانک اسمبلیاں۔ • دھاتی-ربڑ، دھاتی-پلاسٹک بانڈنگ • پائپ اور ٹیوب، پائپ کی تشکیل، موڑنے اور اپنی مرضی کے مطابق پائپ اسمبلیاں، بیلو مینوفیکچرنگ۔ • فائبر گلاس مینوفیکچرنگ • مختلف تکنیکوں کا استعمال کرتے ہوئے ویلڈنگ جیسے اسپاٹ ویلڈنگ، لیزر ویلڈنگ، MIG، TIG۔ پلاسٹک کے حصوں کے لئے الٹراسونک ویلڈنگ۔ • سطح کے علاج اور سطح کی تکمیل کی وسیع اقسام جیسے چپکنے کو بڑھانے کے لیے سطح کی کنڈیشنگ، کوٹنگ کے چپکنے کو بڑھانے کے لیے پتلی آکسائیڈ کی تہہ جمع کرنا، سینڈ بلاسٹنگ، کیم فلم، انوڈائزنگ، نائٹرائڈنگ، پاؤڈر کوٹنگ، سپرے کوٹنگ، مختلف جدید میٹلائزیشن اور کوٹنگ تکنیک۔ جس میں پھٹنا، الیکٹران بیم، بخارات، چڑھانا، سخت کوٹنگز جیسے ہیرے جیسے کاربن (DLC) یا ٹائٹینیم کو کاٹنے اور سوراخ کرنے کے اوزار شامل ہیں۔ • مارکنگ اور لیبلنگ، دھاتی حصوں پر لیزر مارکنگ، پلاسٹک اور ربڑ کے پرزوں پر پرنٹنگ ڈیزائنرز اور انجینئرز کے ذریعہ استعمال ہونے والی عام مکینیکل انجینئرنگ کی شرائط کے لیے بروشر ڈاؤن لوڈ کریں۔ ہم آپ کی مخصوص وضاحتیں اور ضروریات کے مطابق مصنوعات بناتے ہیں۔ آپ کو بہترین معیار، ترسیل اور قیمتیں پیش کرنے کے لیے، ہم چین، بھارت، تائیوان، فلپائن، جنوبی کوریا، ملائیشیا، سری لنکا، ترکی، امریکہ، کینیڈا، جرمنی، برطانیہ اور جاپان میں عالمی سطح پر مصنوعات تیار کرتے ہیں۔ یہ ہمیں کسی بھی دوسرے کسٹم manufacturer سے زیادہ مضبوط اور عالمی سطح پر زیادہ مسابقتی بناتا ہے۔ ہماری مصنوعات ISO9001:2000, QS9000, ISO14001, TS16949 مصدقہ ماحول میں تیار کی جاتی ہیں اور CE، UL نشان کے مالک ہیں اور صنعت کے دیگر معیارات پر پورا اترتے ہیں۔ ایک بار جب ہم آپ کے پروجیکٹ کے لیے مقرر ہو جاتے ہیں، ہم آپ کی مرضی کے مطابق پوری مینوفیکچرنگ، اسمبلی، ٹیسٹنگ، اہلیت، شپنگ اور کسٹم کا خیال رکھ سکتے ہیں۔ اگر آپ چاہیں تو ہم آپ کے پرزے گودام کر سکتے ہیں، اپنی مرضی کے مطابق کٹس جمع کر سکتے ہیں، آپ کی کمپنی کا نام اور برانڈ پرنٹ اور لیبل کر سکتے ہیں اور آپ کے گاہکوں کو جہاز بھیج سکتے ہیں۔ دوسرے الفاظ میں، اگر ترجیح دی جائے تو ہم آپ کے گودام اور تقسیم کا مرکز بھی بن سکتے ہیں۔ چونکہ ہمارے گودام بڑے بندرگاہوں کے قریب واقع ہیں، اس سے ہمیں لاجسٹک فائدہ ملتا ہے۔ مثال کے طور پر، جب آپ کی مصنوعات امریکہ کے کسی بڑے بندرگاہ پر پہنچتی ہیں، تو ہم اسے براہ راست قریبی گودام میں لے جا سکتے ہیں، جہاں ہم آپ کی پسند کے مطابق اسٹور، اسمبل، کٹس، ریبل، پرنٹ، پیکج اور ڈراپ کر سکتے ہیں۔ اپنے صارفین کو بھیجیں۔ ہم نہ صرف مصنوعات فراہم کرتے ہیں۔ ہماری کمپنی اپنی مرضی کے معاہدوں پر کام کرتی ہے جہاں ہم آپ کی سائٹ پر آتے ہیں، سائٹ پر آپ کے پروجیکٹ کا جائزہ لیتے ہیں اور آپ کے لیے ڈیزائن کردہ اپنی مرضی کے مطابق پروجیکٹ پروپوزل تیار کرتے ہیں۔ اس کے بعد ہم اس منصوبے کو نافذ کرنے کے لیے اپنی تجربہ کار ٹیم بھیجتے ہیں۔ ہمارے انجینئرنگ کے کام کے بارے میں مزید معلومات پر مل سکتی ہیں۔ http://www.ags-engineering.com ہم چھوٹے منصوبوں کے ساتھ ساتھ صنعتی پیمانے پر بڑے منصوبے بھی لیتے ہیں۔ پہلے قدم کے طور پر، ہم آپ کو یا تو فون، ٹیلی کانفرنسنگ یا MSN میسنجر کے ذریعے اپنی ماہر ٹیم کے اراکین سے جوڑ سکتے ہیں، تاکہ آپ کسی ماہر سے براہ راست بات چیت کر سکیں، سوالات پوچھیں اور اپنے پروجیکٹ پر گفتگو کر سکیں۔ ہمیں کال کریں اور ضرورت پڑنے پر ہم آپ سے ملیں گے۔ پچھلا صفحہ
- Plastic And Rubber Molding | United States | AGS-TECH, Inc.
AGS-TECH Inc., Molding, Casting, Machining, Forging, Sheet Metal Fabrication, Mechanical Electrical Electronic Optical Assembly, PCBA, Powder Metallurgy, CNC AGS-TECH Inc. AGS-TECH Inc. Custom Manufacturing, Domestic & Global Outsourcing, Engineering Integration, Consolidation AGS-TECH Inc. 1/2 AGS-TECH, Inc. آپ کا ہے: عالمی کسٹم مینوفیکچرر، انٹیگریٹر، کنسولیڈیٹر، مصنوعات اور خدمات کی وسیع اقسام کے لیے آؤٹ سورسنگ پارٹنر۔ ہم مینوفیکچرنگ، فیبریکیشن، انجینئرنگ، کنسولیڈیشن، اپنی مرضی کے مطابق تیار کردہ اور آف شیلف پروڈکٹس کی آؤٹ سورسنگ کے لیے آپ کا ون اسٹاپ ذریعہ ہیں۔ SERVICES: اپنی مرضی کے مطابق مینوفیکچرنگ گھریلو اور عالمی کنٹریکٹ مینوفیکچرنگ مینوفیکچرنگ آؤٹ سورسنگ گھریلو اور عالمی خریداری Consolidation انجینئرنگ انٹیگریشن AGS-TECH، Inc. کے بارے میں - آپ کا عالمی کسٹم مینوفیکچرر، انجینئرنگ انٹیگریٹر، کنسولیڈیٹر، آؤٹ سورسنگ پارٹنر AGS-TECH Inc. ایک صنعت کار، انجینئرنگ انٹیگریٹر، صنعتی مصنوعات کا عالمی سپلائر ہے جس میں سانچوں، مولڈ پلاسٹک اور ربڑ کے پرزے، کاسٹنگ، ایکسٹروشن، شیٹ میٹل فیبریکیشن، میٹل سٹیمپنگ اور فورجنگ، CNC مشینی، مشین عناصر، پاؤڈر دھات کاری، سیرامک اور شیشے کی تشکیل، تار/اسپرنگ فارمنگ، جوائننگ اور اسمبلی اور فاسٹنرز، غیر روایتی فیبریکیشن، مائیکرو فیبریکیشن، نینو ٹیکنالوجی کوٹنگز اور پتلی فلم، کسٹم مکینیکل اور الیکٹرک الیکٹرانک پرزے اور اسمبلیاں اور پی سی بی اور پی سی بی اے اور کیبل ہارنس، آپٹیکل اور فائبر آپٹک اجزاء اور اسمبلی ٹیسٹ اور میٹرولوجی کا سامان جیسے سختی ٹیسٹرز، میٹالرجیکل مائکروسکوپس، الٹراسونک فالٹ ڈیٹیکٹر، انڈسٹریل کمپیوٹرز، ایمبیڈڈ سسٹمز، آٹومیشن اور پینل پی سی، سنگل بورڈ کمپیوٹرز، کوالٹی کنٹرول کا سامان۔ مصنوعات کے علاوہ، ہماری عالمی انجینئرنگ، ریورس انجینئرنگ، تحقیق اور ترقی، مصنوعات کی ترقی، اضافی اور تیز رفتار مینوفیکچرنگ، پروٹو ٹائپنگ، پراجیکٹ مینجمنٹ کی صلاحیتوں کے ساتھ، ہم آپ کو عالمی منڈیوں میں مزید مسابقتی اور کامیاب بنانے کے لیے تکنیکی، لاجسٹک اور کاروباری مدد فراہم کرتے ہیں۔ ہمارا مشن آسان ہے: اپنے صارفین کو کامیاب بنانا اور ترقی کرنا۔ کیسے ؟ فراہم کر کے 1.) بہتر معیار 2.) بہتر قیمت 3.) بہتر ڈیلیوری........ سب ایک کمپنی سے اور دنیا کے سب سے متنوع عالمی انجینئرنگ انٹیگریٹر اور سپلائر AGS-TECH Inc. آپ ہمیں اپنے بلیو پرنٹس فراہم کر سکتے ہیں اور ہم آپ کے پرزوں کی تیاری کے لیے مولڈز، ڈیز اور ٹولز مشین بنا سکتے ہیں۔ ہم انہیں یا تو مولڈنگ، کاسٹنگ، اخراج، فورجنگ، شیٹ میٹل فیبریکیشن، سٹیمپنگ، پاؤڈر میٹلرجی، CNC مشینی، تشکیل کے ذریعے تیار کرتے ہیں۔ ہم یا تو آپ کو پرزے اور پرزے بھیج سکتے ہیں یا اپنی سہولیات پر اسمبلی، فیبریکیشن اور مکمل مینوفیکچرنگ آپریشن کر سکتے ہیں۔ ہمارے اسمبلی آپریشن میں مکینیکل، آپٹیکل، الیکٹرانک، فائبر آپٹک مصنوعات شامل ہیں۔ ہم فاسٹنرز، ویلڈنگ، بریزنگ، سولڈرنگ، چپکنے والی بانڈنگ اور مزید کا استعمال کرتے ہوئے جوائننگ آپریشن انجام دیتے ہیں۔ ہمارے مولڈنگ کے عمل مختلف قسم کے پلاسٹک، ربڑ، سیرامک، شیشے، پاؤڈر دھات کاری کے مواد کے لیے ہیں۔ اسی طرح ہماری کاسٹنگ، سی این سی مشیننگ، فورجنگ، شیٹ میٹل فیبریکیشن، تار اور بہار بنانے کے عمل ہیں جن میں دھاتیں، الائے، پلاسٹک، سیرامک شامل ہیں۔ ہم حتمی فنشنگ آپریشنز پیش کرتے ہیں جیسے کوٹنگز اور پتلی اور موٹی فلم، پیسنے، لیپنگ، پالش اور مزید۔ ہماری مینوفیکچرنگ کی صلاحیتیں مکینیکل اسمبلی سے باہر ہیں۔ ہم آپ کی تکنیکی ڈرائنگ، BOM، Gerber فائلوں کے مطابق الیکٹرک الیکٹرانک پرزے اور اسمبلیاں اور PCB اور PCBA اور کیبل ہارنس، آپٹیکل اور فائبر آپٹک اجزاء اور اسمبلی تیار کرتے ہیں۔ پی سی بی اور پی سی بی اے مینوفیکچرنگ کی مختلف تکنیکیں بشمول ریفلو سولڈرنگ اور ویو سولڈرنگ کے علاوہ دیگر کو تعینات کیا گیا ہے۔ ہم ہرمیٹک الیکٹرانک اور فائبر آپٹیکل پیکجوں اور مصنوعات کے درست کنیکٹرائزیشن، جوائننگ، اسمبلی اور سیل کرنے کے ماہر ہیں۔ غیر فعال اور فعال مکینیکل اسمبلی کے علاوہ، ہم Telcordia اور دیگر صنعتی معیارات کے مطابق مصنوعات تیار کرنے کے لیے خصوصی بریزنگ اور سولڈرنگ مواد اور تکنیک سے فائدہ اٹھاتے ہیں۔ ہم اعلی حجم مینوفیکچرنگ اور من گھڑت تک محدود نہیں ہیں۔ تقریباً ہر پروجیکٹ کا آغاز انجینئرنگ، ریورس انجینئرنگ، ریسرچ اینڈ ڈویلپمنٹ، پروڈکٹ ڈویلپمنٹ، اضافی اور تیز رفتار مینوفیکچرنگ، پروٹو ٹائپنگ کی ضرورت سے ہوتا ہے۔ دنیا کے سب سے متنوع عالمی کسٹم مینوفیکچرر، انجینئرنگ انٹیگریٹر، کنسولیڈیٹر، آؤٹ سورسنگ پارٹنر کے طور پر، ہم آپ کو خوش آمدید کہتے ہیں چاہے آپ کے پاس صرف خیالات ہوں۔ ہم آپ کو وہاں سے لے جاتے ہیں اور کامیاب مکمل پروڈکٹ ڈویلپمنٹ اور مینوفیکچرنگ سائیکل کے تمام مراحل میں آپ کی مدد کرتے ہیں۔ چاہے وہ تیز رفتار شیٹ میٹل فیبریکیشن، تیز مولڈ مشیننگ اور مولڈنگ، تیز رفتار کاسٹنگ، تیز پی سی بی اور پی سی بی اے اسمبلی ہو یا کوئی بھی تیز رفتار پروٹو ٹائپنگ تکنیک آپ کی خدمت میں حاضر ہے۔ ہم آپ کو آف دی شیلف کے ساتھ ساتھ اپنی مرضی کے مطابق میٹرولوجی کا سامان بھی پیش کرتے ہیں جیسے سختی کے ٹیسٹرز، میٹالرجیکل مائکروسکوپ، الٹراسونک فالٹ ڈیٹیکٹر؛ صنعتی کمپیوٹر، ایمبیڈڈ سسٹم، آٹومیشن اور پینل پی سی، سنگل بورڈ کمپیوٹرز اور کوالٹی کنٹرول کا سامان جو مینوفیکچرنگ اور صنعتی سہولیات میں بڑے پیمانے پر استعمال ہوتے ہیں۔ آپ کو جدید ترین میٹرولوجی آلات اور صنعتی کمپیوٹر کے اجزاء کی پیشکش کر کے ہم آپ کی ضروریات کو ایک واحد ماخذ کارخانہ دار اور سپلائر کے طور پر پورا کرتے ہیں جہاں آپ اپنی ضرورت کی تمام چیزیں حاصل کر سکتے ہیں۔ انجینئرنگ خدمات کے وسیع میدان کے بغیر، ہم مارکیٹ میں موجود محدود کسٹم مینوفیکچرنگ اور اسمبلی کی صلاحیتوں کے ساتھ دوسرے مینوفیکچررز اور فروخت کنندگان کی اکثریت سے مختلف نہیں ہوں گے۔ ہماری انجینئرنگ خدمات کا دورانیہ ہمیں دنیا کے سب سے متنوع کسٹم مینوفیکچرر، کنٹریکٹ مینوفیکچرر، انجینئرنگ انٹیگریٹر، کنسولیڈیٹر اور آؤٹ سورسنگ پارٹنر کے طور پر ممتاز کرتا ہے۔ انجینئرنگ خدمات اکیلے یا نئی مصنوعات یا عمل کی ترقی کے حصے کے طور پر، یا موجودہ مصنوعات یا عمل کی ترقی کے حصے کے طور پر یا آپ کے ذہن میں آنے والی کسی بھی چیز کے طور پر پیش کی جا سکتی ہیں۔ ہم لچکدار ہیں اور ہماری انجینئرنگ خدمات وہ شکل اختیار کر سکتی ہیں جو آپ کی ضروریات اور ضروریات کے مطابق ہو۔ ہماری انجینئرنگ خدمات کی ڈیلیور ایبلز اور آؤٹ پٹ صرف آپ کے تخیل تک محدود ہے اور آپ کے مطابق کوئی بھی شکل اختیار کر سکتے ہیں۔ ہماری انجینئرنگ خدمات سے آؤٹ پٹ کی سب سے عام شکلیں ہیں: مشاورتی رپورٹس، ٹیسٹ شیٹس اور رپورٹس، معائنہ رپورٹس، بلیو پرنٹس، انجینئرنگ ڈرائنگ، اسمبلی ڈرائنگ، مواد کی فہرستوں کا بل، ڈیٹا شیٹس، سمولیشنز، سوفٹ ویئر پروگرام، گرافکس اور چارٹس، خصوصی سے آؤٹ پٹ آپٹیکل، تھرمل یا دیگر سافٹ ویئر پروگرام، نمونے اور پروٹو ٹائپس، ماڈلز، مظاہرے ….. وغیرہ۔ ہماری انجینئرنگ خدمات آپ کی ریاست میں تصدیق شدہ پیشہ ور انجینئروں کے دستخط یا متعدد دستخطوں کے ساتھ فراہم کی جا سکتی ہیں۔ بعض اوقات مختلف شعبوں سے تعلق رکھنے والے کئی پیشہ ور انجینئروں کو کام پر دستخط کرنے کی ضرورت پڑ سکتی ہے۔ ہمارے پاس انجینئرنگ کی خدمات کو آؤٹ سورس کرنے سے آپ کو بہت سے فوائد مل سکتے ہیں جیسے کہ کل وقتی انجینئر یا انجینئرز کی خدمات حاصل کرنے سے لاگت کی بچت، فوری طور پر ماہر انجینئر کو آپ کے ٹائم فریم اور بجٹ کے اندر آپ کی خدمات حاصل کرنے کے لیے حاصل کرنا، آپ کو ملازمت چھوڑنے کی صلاحیت فراہم کرنا۔ ایک پروجیکٹ اگر آپ کو یہ احساس ہو کہ یہ قابل عمل نہیں ہے (یہ بہت مہنگا ہے اگر آپ اپنے انجینئروں کو ملازمت پر رکھیں اور ان کو فارغ کریں)، فوری طور پر مختلف شعبوں اور پس منظر کے انجینئروں کو تبدیل کرنے کے قابل ہو جائیں جو آپ کو کسی بھی وقت پینتریبازی کرنے کی صلاحیت فراہم کرتے ہیں اور آپ کے پروجیکٹس کا مرحلہ ….. اپنی مرضی کے مطابق مینوفیکچرنگ اور اسمبلی کے علاوہ انجینئرنگ خدمات کو آؤٹ سورس کرنے کے بہت سے دوسرے فوائد ہیں۔ اس سائٹ پر ہم کسٹم مینوفیکچرنگ، کنٹریکٹ مینوفیکچرنگ، اسمبلی، انضمام، انضمام اور مصنوعات کی آؤٹ سورسنگ پر توجہ مرکوز کریں گے۔ اگر ہمارے کاروبار کا انجینئرنگ پہلو آپ کے لیے زیادہ دلچسپی کا حامل ہے، تو آپ پر جا کر ہماری انجینئرنگ خدمات کے بارے میں تفصیلی معلومات حاصل کر سکتے ہیں۔http://www.ags-engineering.com ہم AGS-TECH Inc.، مینوفیکچرنگ اور فیبریکیشن اور انجینئرنگ اور آؤٹ سورسنگ اور کنسولیڈیشن کے لیے آپ کا واحد ذریعہ ہیں۔ ہم دنیا کے سب سے متنوع انجینئرنگ انٹیگریٹر ہیں جو آپ کو اپنی مرضی کے مطابق مینوفیکچرنگ، ذیلی اسمبلی، مصنوعات کی اسمبلی اور انجینئرنگ خدمات پیش کرتے ہیں۔ Contact Us First Name Last Name Email Write a message Submit Thanks for submitting!