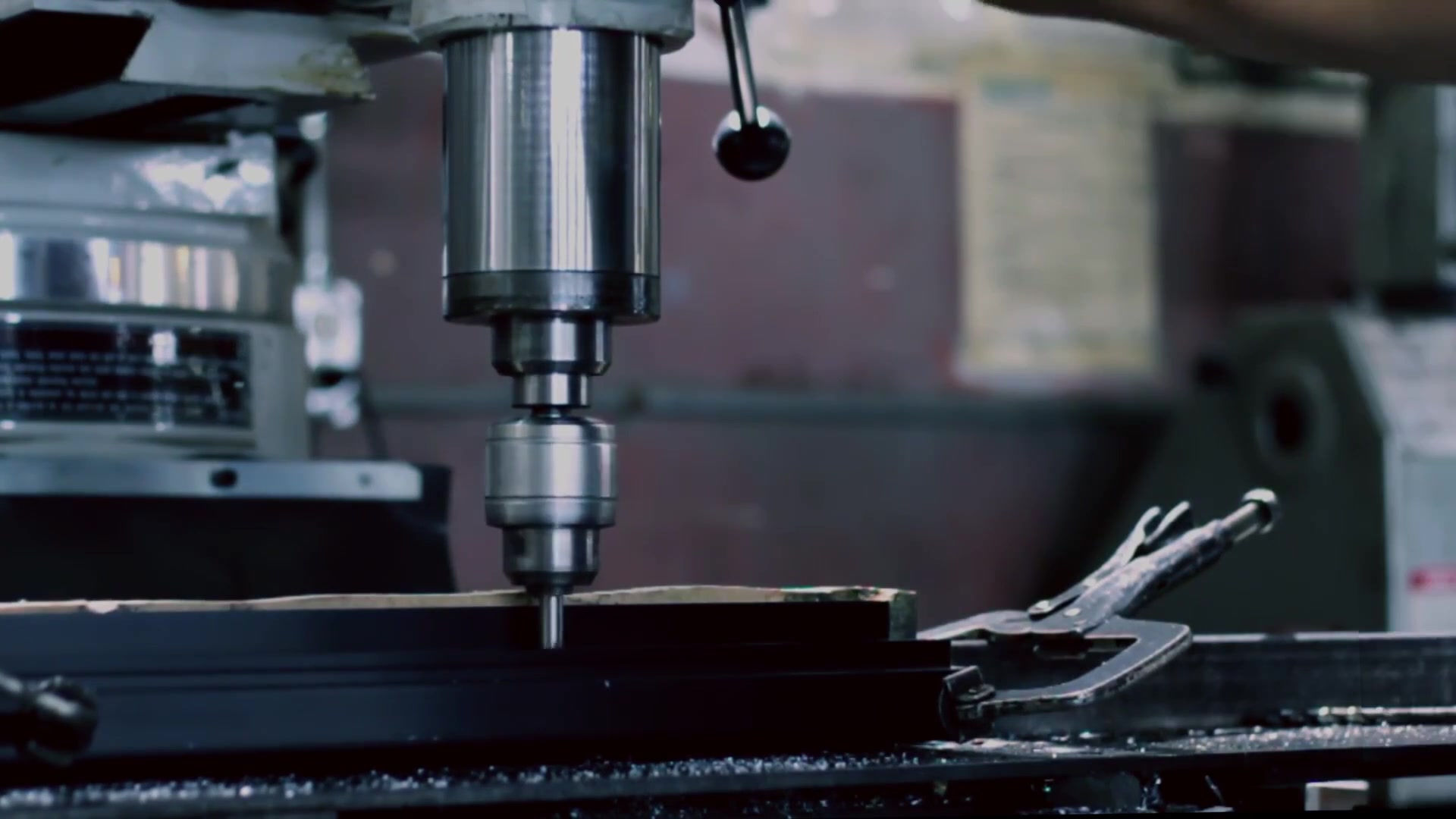
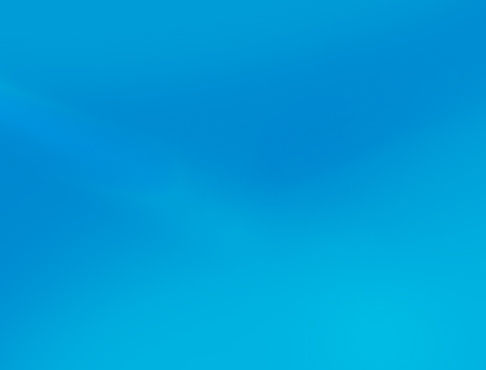
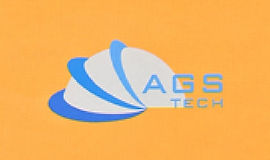
Nhà sản xuất tùy chỉnh toàn cầu, Người tích hợp, Người hợp nhất, Đối tác gia công cho nhiều loại Sản phẩm & Dịch vụ.
Chúng tôi là nguồn một cửa của bạn để sản xuất, chế tạo, kỹ thuật, hợp nhất, tích hợp, gia công các sản phẩm & dịch vụ được sản xuất tùy chỉnh và bán sẵn.
Chọn ngôn ngữ của bạn
-
Sản xuất tùy chỉnh
-
Sản xuất theo hợp đồng trong nước & toàn cầu
-
Gia công phần mềm sản xuất
-
Mua sắm trong nước & toàn cầu
-
Hợp nhất
-
Tích hợp Kỹ thuật
-
Dịch vụ kỹ thuật
Search Results
Tìm thấy 164 kết quả với một nội dung tìm kiếm trống
- Transmission Components, Belts, Chains, Cable Drives, Pulleys,AGS-TECH
Transmission Components, Belts, Chains and Cable Drives, Conventional & Grooved or Serrated, Positive Drive, Pulleys Thắt lưng & dây xích & lắp ráp ổ cáp AGS-TECH Inc. cung cấp cho bạn các thành phần truyền tải điện bao gồm Thắt lưng & Dây xích & Lắp ráp ổ cáp. Với nhiều năm cải tiến, các bộ truyền động bằng cao su, da và dây đai khác của chúng tôi đã trở nên nhẹ hơn và nhỏ gọn hơn, có khả năng chịu tải cao hơn với chi phí thấp hơn. Tương tự, bộ truyền động xích của chúng tôi đã trải qua nhiều quá trình phát triển theo thời gian và chúng mang lại cho khách hàng một số lợi thế. Một số ưu điểm của việc sử dụng bộ truyền động xích là khoảng cách tâm trục tương đối không bị hạn chế, nhỏ gọn, dễ lắp ráp, đàn hồi khi căng mà không bị trượt hoặc dão, khả năng hoạt động trong môi trường nhiệt độ cao. Ổ cáp của chúng tôi cũng mang lại những lợi thế như tính đơn giản trong một số ứng dụng so với các loại thành phần truyền dẫn khác. Cả truyền động dây đai, dây xích và dây cáp cũng như các phiên bản chế tạo và lắp ráp tùy chỉnh đều có sẵn. Chúng tôi có thể sản xuất các thành phần truyền dẫn này với kích thước phù hợp với ứng dụng của bạn và từ các vật liệu phù hợp nhất. BELTS & BELT DRIVES: - Thắt lưng dẹt thông thường: Là loại đai dẹt trơn không có răng, rãnh hoặc răng cưa. Truyền động đai dẹt có tính linh hoạt, khả năng hấp thụ sốc tốt, truyền lực hiệu quả ở tốc độ cao, chống mài mòn, giá thành rẻ. Thắt lưng có thể được nối hoặc nối để tạo thành thắt lưng lớn hơn. Các ưu điểm khác của dây đai dẹt thông thường là chúng mỏng, không phải chịu tải trọng ly tâm cao (làm cho chúng tốt cho các hoạt động tốc độ cao với các puli nhỏ). Mặt khác, chúng áp đặt tải trọng chịu lực cao vì đai phẳng yêu cầu lực căng cao. Các nhược điểm khác của truyền động đai dẹt có thể là trượt, hoạt động ồn ào và hiệu quả tương đối thấp hơn ở tốc độ vận hành thấp và trung bình. Chúng tôi có hai loại dây đai thông thường: Có gia cố và không gia cố. Đai gia cố có một bộ phận chịu kéo trong cấu trúc của chúng. Thắt lưng phẳng thông thường có sẵn như da, vải hoặc dây cao su, cao su không gia cố hoặc nhựa, vải, da gia cố. Dây da có tuổi thọ cao, tính linh hoạt, hệ số ma sát tuyệt vời, dễ dàng sửa chữa. Tuy nhiên, thắt lưng da tương đối đắt tiền, cần thay và làm sạch thắt lưng, và tùy thuộc vào môi trường mà chúng có thể co lại hoặc giãn ra. Vải cao su hoặc dây đai có khả năng chống ẩm, axit và kiềm. Thắt lưng vải cao su được tạo thành từ những sợi bông hoặc sợi vịt tổng hợp tẩm cao su và là loại tiết kiệm nhất. Đai dây cao su bao gồm một loạt các sợi dây được tẩm cao su. Đai dây cao su cung cấp độ bền kéo cao, kích thước và khối lượng khiêm tốn. Đai cao su hoặc nhựa không gia cố phù hợp cho các ứng dụng truyền động nhẹ, tốc độ thấp. Các đai nhựa và cao su không gia cố có thể được kéo căng vào vị trí trên các ròng rọc của chúng. Đai nhựa không gia cố có thể truyền công suất cao hơn so với đai cao su. Thắt lưng da gia cố bao gồm một bộ phận chịu lực bằng nhựa được kẹp giữa lớp da trên và dưới. Cuối cùng, thắt lưng vải của chúng tôi có thể bao gồm một miếng bông hoặc một con vịt được gấp lại và khâu bằng các hàng mũi may dọc. Đai vải có thể theo dõi đồng nhất và hoạt động ở tốc độ cao. - Thắt lưng có rãnh hoặc có răng cưa (chẳng hạn như Đai chữ V): Đây là những loại đai dẹt cơ bản được sửa đổi để mang lại những ưu điểm của một loại sản phẩm truyền động khác. Đây là những loại đai dẹt có mặt dưới có gân dọc. Đai Poly-V là đai phẳng có rãnh dọc hoặc có răng cưa với phần chịu kéo và một loạt các rãnh hình chữ V liền kề nhằm mục đích theo dõi và nén. Công suất nguồn phụ thuộc vào chiều rộng dây đai. Dây đai chữ V là dây curoa của ngành công nghiệp và có nhiều loại và kích thước được tiêu chuẩn hóa khác nhau để truyền tải hầu hết mọi năng lượng tải. Bộ truyền động dây đai V hoạt động tốt trong khoảng 1500 đến 6000 ft / phút, tuy nhiên dây đai V hẹp sẽ hoạt động lên đến 10.000 ft / phút. Bộ truyền động đai chữ V có tuổi thọ cao từ 3 đến 5 năm và cho phép tỷ số tốc độ lớn, chúng dễ dàng lắp đặt và tháo gỡ, vận hành êm ái, ít bảo trì, hấp thụ sốc tốt giữa bộ truyền động đai và trục dẫn động. Nhược điểm của đai chữ V là độ trượt và độ dão nhất định của chúng và do đó chúng có thể không phải là giải pháp tốt nhất khi yêu cầu tốc độ đồng bộ. Chúng tôi có vành đai công nghiệp, ô tô và nông nghiệp. Có sẵn độ dài tiêu chuẩn cũng như độ dài tùy chỉnh của thắt lưng. Tất cả các mặt cắt ngang đai chữ V tiêu chuẩn đều có sẵn từ kho. Có các bảng mà bạn có thể tính toán các thông số chưa biết như chiều dài đai, tiết diện đai (chiều rộng và độ dày) miễn là bạn biết một số thông số của hệ thống của mình như đường kính puli dẫn động và dẫn động, khoảng cách tâm giữa các puli và tốc độ quay của puli. Bạn có thể sử dụng các bảng như vậy hoặc yêu cầu chúng tôi chọn thắt lưng chữ V phù hợp cho bạn. - Đai truyền động dương (Đai định thời): Các đai này cũng là loại dẹt với một loạt các răng cách đều nhau về chu vi bên trong. Đai truyền động dương hoặc đai thời gian kết hợp ưu điểm của đai dẹt với đặc tính bám dương của xích và bánh răng. Dây đai truyền động tích cực không để lộ sự trượt hoặc thay đổi tốc độ. Có thể có một loạt các tỷ lệ tốc độ. Tải trọng vòng bi thấp vì chúng có thể hoạt động ở sức căng thấp. Tuy nhiên, chúng dễ bị lệch hơn trong puli. - Ròng rọc, puly, dây curoa: Các loại ròng rọc khác nhau được sử dụng với các dây đai truyền động phẳng, có gân (răng cưa) và dương. Chúng tôi sản xuất tất cả. Hầu hết các ròng rọc đai dẹt của chúng tôi được chế tạo bằng cách đúc sắt, nhưng các phiên bản thép cũng có sẵn trong các kết hợp vành và trục khác nhau. Các ròng rọc đai dẹt của chúng tôi có thể có các trung tâm rắn, có móc hoặc chia hoặc chúng tôi có thể sản xuất theo ý muốn của bạn. Dây curoa và đai truyền động dương có sẵn với nhiều kích cỡ và chiều rộng cổ phiếu. Ít nhất một puli trong bộ truyền động đai thời gian phải được lắp bích để giữ đai trên bộ truyền động. Đối với hệ thống truyền động trung tâm dài, nên có mặt bích của cả hai puli. Rọc là bánh xe có rãnh của ròng rọc và thường được sản xuất bằng cách đúc sắt, tạo hình thép hoặc đúc nhựa. Thép hình là quy trình thích hợp để sản xuất máy cắt ô tô và nông nghiệp. Chúng tôi sản xuất các loại puly có rãnh đều đặn và sâu. Các puly có rãnh sâu rất thích hợp khi đai V đi vào puly theo một góc, chẳng hạn như trường hợp của các bộ truyền động một phần tư. Các rãnh sâu cũng rất thích hợp cho các ổ trục đứng và các ứng dụng mà ở đó dây đai có thể là một vấn đề. Các puli không tải của chúng tôi là puli có rãnh hoặc puli phẳng không dùng để truyền công suất cơ học. Các ròng rọc của người làm việc được sử dụng hầu hết để thắt chặt dây đai. - Truyền động đai đơn và nhiều đai: Truyền động đai đơn có một rãnh duy nhất trong khi truyền động đai nhiều có nhiều rãnh. Bằng cách nhấp vào văn bản màu có liên quan bên dưới, bạn có thể tải xuống các danh mục của chúng tôi: - Thắt lưng truyền điện (bao gồm Thắt lưng chữ V, Thắt lưng định thời, Thắt lưng thô, Thắt lưng quấn và Thắt lưng đặc biệt) - Băng tải - Ròng rọc V - Ròng rọc định thời CHUỖI & BỘ TRUYỀN ĐỘNG: Xích truyền lực của chúng tôi có một số ưu điểm như khoảng cách tâm trục tương đối hạn chế, dễ lắp ráp, nhỏ gọn, đàn hồi khi căng mà không bị trượt hoặc dão, khả năng hoạt động dưới nhiệt độ cao. Dưới đây là các loại chuỗi chính của chúng tôi: - Dây xích có thể tháo rời: Dây xích có thể tháo rời của chúng tôi được sản xuất với nhiều kích cỡ, độ cao và độ bền cao nhất và thường được làm từ sắt hoặc thép dễ uốn. Xích dễ uốn được làm với nhiều kích cỡ từ 0,902 (23 mm) đến 4,063 inch (103 mm) và độ bền tối đa từ 700 đến 17.000 lb / inch vuông. Mặt khác, dây xích thép có thể tháo rời của chúng tôi được làm với kích thước từ 0,904 inch (23 mm) đến khoảng 3,00 inch (76 mm), với độ bền tối đa từ 760 đến 5000 lb / inch vuông._cc781905-5cde-3194-bb3b- 136bad5cf58d_ - Xích Pintle: Loại xích này được sử dụng cho tải nặng hơn và tốc độ cao hơn một chút đến khoảng 450 feet / phút (2,2 m / giây). Xích panh được làm bằng các liên kết đúc riêng lẻ có đầu nòng tròn, đầy đủ với thanh bên bù trừ. Các mắt xích này được ghép với nhau bằng các chốt thép. Những dây xích này có cao độ từ khoảng 1,00 inch (25 mm) đến 6,00 inch (150 mm) và cường độ cuối cùng trong khoảng 3600 đến 30.000 lb / inch vuông. - Chuỗi lệch thanh bên: Đây là loại phổ biến trong chuỗi truyền động của máy móc xây dựng. Các dây chuyền này hoạt động ở tốc độ 1000 ft / phút và truyền tải tới khoảng 250 mã lực. Nói chung, mỗi liên kết có hai thanh bên bù đắp, một ống lót, một con lăn, một chốt, một chốt cotter. - Xích con lăn: Chúng có các cao độ từ 0,25 (6 mm) đến 3,00 (75 mm) inch. Sức mạnh cuối cùng của chuỗi con lăn một chiều rộng nằm trong khoảng từ 925 đến 130.000 lb / inch vuông. Có sẵn nhiều phiên bản chiều rộng của xích con lăn và truyền công suất lớn hơn ở tốc độ cao hơn. Xích con lăn nhiều chiều rộng cũng mang lại hành động êm ái hơn với tiếng ồn giảm. Xích con lăn được lắp ráp từ các liên kết con lăn và liên kết chốt. Chốt cotter được sử dụng trong chuỗi con lăn phiên bản có thể tháo rời. Việc thiết kế bộ truyền động xích con lăn đòi hỏi chuyên môn. Trong khi bộ truyền động đai dựa trên tốc độ tuyến tính, bộ truyền động xích dựa trên tốc độ quay của đĩa xích nhỏ hơn, trong hầu hết các cơ sở lắp đặt bộ phận dẫn động. Bên cạnh xếp hạng mã lực và tốc độ quay, việc thiết kế bộ truyền động xích còn dựa trên nhiều yếu tố khác. - Double-Pitch Chains: Về cơ bản giống như xích con lăn ngoại trừ bước dài gấp đôi. - Xích răng ngược (Im lặng): Xích tốc độ cao được sử dụng chủ yếu cho động cơ chính, bộ truyền động cất cánh. Bộ truyền động xích răng ngược có thể truyền công suất lên đến 1200 mã lực và được tạo thành từ một loạt các liên kết răng, được lắp ráp xen kẽ bằng một trong hai chốt hoặc kết hợp các thành phần ăn khớp. Xích dẫn hướng trung tâm có các liên kết dẫn hướng để khớp các rãnh trong đĩa xích và xích dẫn hướng bên có các thanh dẫn để khớp các mặt của đĩa xích. - Chuỗi hạt hoặc chuỗi trượt: Những chuỗi này được sử dụng cho các ổ đĩa tốc độ chậm và cả trong các hoạt động thủ công. Bằng cách nhấp vào văn bản màu có liên quan bên dưới, bạn có thể tải xuống các danh mục của chúng tôi: - Chuỗi lái xe - Chuỗi băng tải - Chuỗi băng tải sân lớn - Chuỗi con lăn bằng thép không gỉ - Dây xích cẩu - Xích xe máy - Chuỗi máy nông nghiệp - Nhông xích: Nhông xích tiêu chuẩn của chúng tôi phù hợp với tiêu chuẩn ANSI. Đĩa xích là loại đĩa xích phẳng, không có trục. Đĩa xích trung tâm cỡ vừa và nhỏ của chúng tôi được sản xuất từ nguyên liệu thanh hoặc rèn hoặc được chế tạo bằng cách hàn trục trung tâm dạng thanh vào một tấm cán nóng. AGS-TECH Inc. có thể cung cấp nhông xích được gia công từ các vật đúc gang xám, thép đúc và các cấu kiện trung tâm hàn, kim loại bột nung kết, nhựa đúc hoặc gia công. Để vận hành trơn tru ở tốc độ cao, việc lựa chọn kích thước nhông xích phù hợp là điều cần thiết. Hạn chế về không gian tất nhiên là yếu tố chúng ta không thể bỏ qua khi lựa chọn nhông xích. Khuyến nghị rằng tỷ lệ bộ truyền động và nhông xích được dẫn động không được nhiều hơn 6: 1 và vòng quấn xích trên bộ lái là 120 độ. Khoảng cách tâm giữa các đĩa xích nhỏ hơn và lớn hơn, chiều dài xích và độ căng của xích cũng phải được chọn theo một số tính toán và hướng dẫn kỹ thuật được khuyến nghị chứ không phải ngẫu nhiên. Tải xuống danh mục của chúng tôi bằng cách nhấp vào văn bản màu bên dưới: - Đĩa xích và Bánh xe đĩa - Ống lót truyền động - Khớp nối chuỗi - Ổ khóa chuỗi TRUYỀN ĐỘNG CÁP: Những loại này có ưu điểm hơn so với truyền động dây đai và xích trong một số trường hợp. Bộ truyền động cáp có thể thực hiện chức năng tương tự như dây đai và cũng có thể đơn giản hơn và kinh tế hơn để thực hiện trong một số ứng dụng. Ví dụ, một loạt Ổ đĩa cáp Synchromesh mới được thiết kế cho lực kéo tích cực để thay thế các loại dây thông thường, cáp đơn giản và ổ đĩa bánh răng, đặc biệt là trong không gian chật hẹp. Ổ cáp mới được thiết kế để cung cấp khả năng định vị chính xác cao trong các thiết bị điện tử như máy sao chép, máy vẽ, máy đánh chữ, máy in,… .. vv Một tính năng chính của ổ cáp mới là khả năng được sử dụng trong các cấu hình serpentine 3D cho phép kiểu dáng cực kỳ thu nhỏ. Cáp đồng bộ có thể được sử dụng với độ căng thấp hơn khi so sánh với dây thừng, do đó giảm tiêu thụ điện năng. Liên hệ với AGS-TECH nếu có câu hỏi và ý kiến về dây đai, dây xích và truyền động cáp. CLICK Product Finder-Locator Service TRANG TRƯỚC
- Joining & Assembly & Fastening Processes, Welding, Brazing, Soldering
Joining & Assembly & Fastening Processes, Welding, Brazing, Soldering, Sintering, Adhesive Bonding, Press Fitting, Wave and Reflow Solder Process, Torch Furnace Tham gia & lắp ráp & quá trình buộc Chúng tôi tham gia, lắp ráp và gắn chặt các bộ phận đã sản xuất của bạn và biến chúng thành các sản phẩm hoàn chỉnh hoặc bán thành phẩm bằng cách sử dụng HÀN, VÒNG, BÁN BẢNG, INOX, TRÁI PHIẾU KEO, NHANH CHÓNG, NỐI ÉP. Một số quy trình hàn phổ biến nhất của chúng tôi là hồ quang, khí oxyfuel, điện trở, chiếu, đường nối, khó chịu, bộ gõ, trạng thái rắn, chùm điện tử, laser, nhiệt, hàn cảm ứng. Các quy trình hàn phổ biến của chúng tôi là hàn bằng đuốc, cảm ứng, lò nung và hàn nhúng. Các phương pháp hàn của chúng tôi là hàn sắt, tấm nóng, lò nướng, cảm ứng, nhúng, sóng, nóng chảy và hàn siêu âm. Đối với liên kết kết dính, chúng tôi thường sử dụng nhựa nhiệt dẻo và nhiệt rắn, epoxit, phenol, polyurethane, hợp kim kết dính cũng như một số hóa chất và băng khác. Cuối cùng, các quy trình buộc của chúng tôi bao gồm đóng đinh, vặn vít, đai ốc và bu lông, tán đinh, kẹp kim, ghim, khâu & ghim và bấm khớp. • HÀN: Hàn liên quan đến việc nối các vật liệu bằng cách nấu chảy các miếng gia công và đưa vật liệu phụ vào, vật liệu này cũng tham gia vào nhóm hàn nóng chảy. Khi khu vực này nguội đi, chúng ta sẽ có được một mối nối chắc chắn. Áp suất được áp dụng trong một số trường hợp. Trái ngược với hàn, các hoạt động hàn và hàn chỉ liên quan đến việc nấu chảy vật liệu có điểm nóng chảy thấp hơn giữa các phôi và các phôi không nóng chảy. Chúng tôi khuyên bạn nên nhấp vào đây đểTẢI XUỐNG Các Minh Họa Sơ Đồ Quy Trình Hàn của AGS-TECH Inc. Điều này sẽ giúp bạn hiểu rõ hơn về thông tin chúng tôi đang cung cấp cho bạn bên dưới. Trong ARC WELDING, chúng tôi sử dụng nguồn điện và điện cực để tạo ra hồ quang điện làm nóng chảy kim loại. Điểm hàn được bảo vệ bằng khí hoặc hơi hoặc vật liệu khác che chắn. Quá trình này phổ biến để hàn các bộ phận ô tô và kết cấu thép. Trong hàn hồ quang kim loại mạ vàng (SMAW) hay còn được gọi là hàn que, que điện cực được đưa đến gần vật liệu cơ bản và một hồ quang điện được tạo ra giữa chúng. Thanh điện cực nóng chảy và đóng vai trò như vật liệu độn. Điện cực cũng chứa chất từ thông hoạt động như một lớp xỉ và tỏa ra hơi đóng vai trò như khí bảo vệ. Những chất này bảo vệ khu vực mối hàn khỏi bị nhiễm bẩn từ môi trường. Không có chất độn nào khác đang được sử dụng. Nhược điểm của quá trình này là diễn ra chậm, phải thay điện cực thường xuyên, cần loại bỏ xỉ dư có nguồn gốc từ thông lượng. Một số kim loại như sắt, thép, niken, nhôm, đồng… vv. Có thể được hàn. Ưu điểm của nó là các công cụ rẻ tiền và dễ sử dụng. Hàn hồ quang kim loại khí (GMAW) còn được gọi là khí trơ kim loại (MIG), chúng ta liên tục cấp chất độn dây điện cực tiêu hao và khí trơ hoặc một phần khí trơ chảy xung quanh dây để chống lại sự ô nhiễm môi trường của vùng hàn. Thép, nhôm và các kim loại màu khác có thể được hàn. Ưu điểm của MIG là tốc độ hàn cao và chất lượng tốt. Nhược điểm của nó là thiết bị phức tạp và những thách thức phải đối mặt trong môi trường ngoài trời nhiều gió vì chúng tôi phải duy trì khí che chắn xung quanh khu vực hàn ổn định. Một biến thể của GMAW là hàn hồ quang có dòng chảy (FCAW) bao gồm một ống kim loại mịn chứa đầy vật liệu thông lượng. Đôi khi thông lượng bên trong ống là đủ để bảo vệ khỏi ô nhiễm môi trường. Hàn hồ quang chìm (SAW) rộng rãi là một quy trình tự động, liên quan đến việc cấp dây liên tục và hồ quang được đánh dưới một lớp vỏ thông lượng. Tỷ lệ và chất lượng sản xuất cao, xỉ hàn dễ dàng thoát ra và chúng tôi có một môi trường làm việc không khói thuốc. Điểm bất lợi là nó chỉ có thể được sử dụng để hàn parts ở một số vị trí nhất định. Trong hàn hồ quang vonfram khí (GTAW) hoặc hàn khí trơ vonfram (TIG), chúng tôi sử dụng điện cực vonfram cùng với chất độn riêng biệt và khí trơ hoặc gần trơ. Như chúng ta đã biết Vonfram có nhiệt độ nóng chảy cao và nó là kim loại rất thích hợp với nhiệt độ rất cao. Vonfram trong TIG không được tiêu thụ trái ngược với các phương pháp khác được giải thích ở trên. Kỹ thuật hàn chậm nhưng chất lượng cao có lợi thế so với các kỹ thuật hàn vật liệu mỏng khác. Thích hợp với nhiều kim loại. Hàn hồ quang plasma cũng tương tự nhưng sử dụng khí plasma để tạo hồ quang. Hồ quang trong hàn hồ quang plasma tương đối tập trung hơn so với GTAW và có thể được sử dụng cho nhiều độ dày kim loại hơn với tốc độ cao hơn nhiều. GTAW và hàn hồ quang plasma có thể được áp dụng cho nhiều hoặc ít vật liệu giống nhau. HÀN OXY-NHIÊN LIỆU / OXYFUEL còn được gọi là hàn oxyacetylene, hàn oxy, hàn khí được thực hiện bằng cách sử dụng nhiên liệu khí và oxy để hàn. Vì không sử dụng điện nên nó có thể di động và có thể sử dụng ở những nơi không có điện. Sử dụng mỏ hàn, chúng tôi đốt nóng các mảnh và vật liệu phụ để tạo ra một bể kim loại nóng chảy chung. Nhiều loại nhiên liệu khác nhau có thể được sử dụng như axetylen, xăng, hydro, propan, butan ... vv. Trong hàn nhiên liệu oxy, chúng tôi sử dụng hai thùng chứa, một thùng chứa nhiên liệu và thùng chứa còn lại chứa oxy. Oxy sẽ oxy hóa nhiên liệu (đốt cháy nó). HÀN ĐIỆN TRỞ: Kiểu hàn này tận dụng sự gia nhiệt của jun và nhiệt được sinh ra tại vị trí có dòng điện chạy qua trong một thời gian nhất định. Dòng điện cao được truyền qua kim loại. Các bể chứa kim loại nóng chảy được hình thành tại vị trí này. Các phương pháp hàn điện trở là phổ biến do hiệu quả của chúng, ít tiềm ẩn ô nhiễm. Tuy nhiên, nhược điểm là chi phí thiết bị tương đối đáng kể và hạn chế cố hữu đối với các chi tiết gia công tương đối mỏng. SPOT WELDING là một loại hàn điện trở chính. Ở đây chúng tôi nối hai hoặc nhiều tấm chồng lên nhau hoặc các chi tiết gia công bằng cách sử dụng hai điện cực đồng để kẹp các tấm lại với nhau và cho dòng điện cao qua chúng. Vật liệu giữa các điện cực đồng nóng lên và một vũng nóng chảy được tạo ra tại vị trí đó. Dòng điện sau đó được dừng lại và các đầu điện cực đồng làm mát vị trí mối hàn vì các điện cực được làm mát bằng nước. Áp dụng nhiệt lượng phù hợp cho vật liệu và độ dày phù hợp là chìa khóa cho kỹ thuật này, bởi vì nếu áp dụng sai khớp sẽ yếu. Hàn điểm có ưu điểm là không gây ra biến dạng đáng kể cho phôi, hiệu quả năng lượng, dễ tự động hóa và tốc độ sản xuất vượt trội, và không yêu cầu bất kỳ chất độn nào. Điểm bất lợi là vì hàn diễn ra tại các điểm thay vì tạo thành một đường nối liên tục, độ bền tổng thể có thể tương đối thấp hơn so với các phương pháp hàn khác. Mặt khác, SEAM WELDING tạo ra các mối hàn ở bề mặt bong tróc của các vật liệu tương tự. Đường may có thể là mối nối đối đầu hoặc chồng lên nhau. Đường hàn bắt đầu ở một đầu và di chuyển dần dần sang đầu kia. Phương pháp này cũng sử dụng hai điện cực từ đồng để tạo áp lực và dòng điện vào vùng hàn. Các điện cực hình đĩa quay với sự tiếp xúc liên tục dọc theo đường nối và tạo ra một mối hàn liên tục. Ở đây cũng vậy, các điện cực được làm mát bằng nước. Các mối hàn rất chắc chắn và đáng tin cậy. Các phương pháp khác là chiếu, chớp và kỹ thuật hàn đảo ngược. HÀN RẮN-STATE có một chút khác biệt so với các phương pháp trước đây được giải thích ở trên. Sự kết tụ xảy ra ở nhiệt độ thấp hơn nhiệt độ nóng chảy của các kim loại tham gia và không sử dụng chất độn kim loại. Áp suất có thể được sử dụng trong một số quy trình. Các phương pháp khác nhau là HÀN DỆT trong đó các kim loại khác nhau được đùn qua cùng một khuôn đúc, HÀN ÁP LẠNH nơi chúng tôi nối các hợp kim mềm dưới điểm nóng chảy của chúng, HÀN KHÁC NHAU một kỹ thuật mà không có đường hàn nhìn thấy được, HÀN NỔ để nối các vật liệu khác nhau, ví dụ như hợp kim chống ăn mòn với cấu trúc thép, HÀN XUNG ĐIỆN TỪ trong đó chúng tôi gia tốc ống và tấm bằng lực điện từ, HÀN LỰC bao gồm nung nóng kim loại đến nhiệt độ cao và đập chúng lại với nhau, HÀN FRICTION ở nơi thực hiện hàn với đủ ma sát, HÀN DÂY HÌNH ẢNH bao gồm việc quay không quay Dụng cụ tiêu hao đi qua đường nối, HÀN ÁP LỰC NÓNG nơi chúng ta ép kim loại với nhau ở nhiệt độ cao hơn nhiệt độ nóng chảy trong chân không hoặc khí trơ, HÀN ÁP SUẤT NÓNG là một quá trình mà chúng ta tạo áp suất bằng cách sử dụng khí trơ bên trong một bình, HÀN LĂN nơi chúng ta tham gia vật liệu khác nhau bằng cách buộc chúng giữa hai bánh xe quay, HÀN SIÊU ÂM trong đó các tấm kim loại hoặc nhựa mỏng được hàn bằng cách sử dụng năng lượng dao động tần số cao. Các quy trình hàn khác của chúng tôi là HÀN ELECTRON BEAM với độ thâm nhập sâu và xử lý nhanh nhưng là một phương pháp đắt tiền mà chúng tôi coi là phương pháp này cho các trường hợp đặc biệt, HÀN ELECTROSLAG là một phương pháp chỉ phù hợp với các tấm thép dày và các mảnh gia công bằng thép, HÀN INDUCTION khi chúng tôi sử dụng cảm ứng điện từ và gia nhiệt các phôi dẫn điện hoặc sắt từ của chúng tôi, LASER BEAM WELDING cũng có khả năng thâm nhập sâu và xử lý nhanh nhưng là một phương pháp đắt tiền, LASER HYBRID WELDING kết hợp LBW với GMAW trong cùng một đầu hàn và có khả năng bắc cầu các khe hở 2 mm giữa các tấm, PERCUSSION WELDING đó liên quan đến phóng điện tiếp theo là rèn vật liệu với áp lực tác dụng, HÀN NHIỆT liên quan đến phản ứng tỏa nhiệt giữa bột nhôm và sắt oxit., HÀN ĐIỆN với các điện cực tiêu hao và chỉ sử dụng với thép ở vị trí thẳng đứng, và cuối cùng là HÀN NGHIÊN CỨU để nối đinh với đế vật liệu với nhiệt và áp suất. Chúng tôi khuyên bạn nên nhấp vào đây đểTẢI XUỐNG Hình minh họa sơ đồ của chúng tôi về các quy trình hàn, hàn và kết dính của AGS-TECH Inc Điều này sẽ giúp bạn hiểu rõ hơn về thông tin chúng tôi đang cung cấp cho bạn bên dưới. • KHẮC PHỤC: Chúng tôi nối hai hoặc nhiều kim loại bằng cách đốt nóng các kim loại phụ ở giữa chúng trên điểm nóng chảy của chúng và sử dụng tác động mao dẫn để lan truyền. Quá trình này tương tự như hàn nhưng nhiệt độ liên quan đến làm tan chảy chất độn cao hơn trong hàn. Giống như trong hàn, chất trợ dung bảo vệ vật liệu độn khỏi bị nhiễm bẩn trong khí quyển. Sau khi làm nguội các phôi được liên kết với nhau. Quy trình này bao gồm các bước chính sau: Độ khít và độ hở tốt, làm sạch vật liệu nền thích hợp, lắp ráp thích hợp, lựa chọn thông lượng và bầu không khí thích hợp, làm nóng cụm và cuối cùng là làm sạch cụm hàn. Một số quy trình hàn của chúng tôi là TORCH BRAZING, một phương pháp phổ biến được thực hiện thủ công hoặc theo cách tự động. Có phù hợp với các đơn hàng sản xuất số lượng ít và các trường hợp chuyên dụng. Nhiệt được áp dụng bằng cách sử dụng ngọn lửa khí gần khớp được hàn. FURNACE BRAZING đòi hỏi ít kỹ năng của người vận hành hơn và là một quy trình bán tự động thích hợp cho sản xuất hàng loạt trong công nghiệp. Cả kiểm soát nhiệt độ và kiểm soát bầu không khí trong lò đều là những ưu điểm của kỹ thuật này, bởi vì kỹ thuật trước cho phép chúng tôi kiểm soát chu trình nhiệt và loại bỏ hiện tượng nóng cục bộ như trường hợp hàn mỏ hàn và kỹ thuật này bảo vệ bộ phận khỏi quá trình oxy hóa. Sử dụng đồ gá, chúng tôi có thể giảm chi phí sản xuất đến mức tối thiểu. Những bất lợi là tiêu thụ điện năng cao, chi phí thiết bị và các cân nhắc thiết kế khó khăn hơn. VACUUM BRAZING diễn ra trong lò chân không. Nhiệt độ đồng nhất được duy trì và chúng tôi có được các mối nối không có thông lượng, rất sạch với rất ít ứng suất dư. Xử lý nhiệt có thể diễn ra trong quá trình hàn chân không, vì ứng suất dư thấp xuất hiện trong các chu kỳ làm nóng và làm mát chậm. Nhược điểm lớn là giá thành cao vì việc tạo môi trường chân không là một quá trình tốn kém. Tuy nhiên, một kỹ thuật khác DIP BRAZING kết hợp các bộ phận cố định nơi hợp chất hàn được áp dụng cho bề mặt giao phối. Sau đó, các phần kết cấu được nhúng vào bể muối nóng chảy như Natri Clorua (muối ăn), hoạt động như một môi trường truyền nhiệt và chất trợ dung. Không khí bị loại trừ và do đó không có sự hình thành oxit nào diễn ra. Trong VÒNG TAY KẾT CẤU, chúng tôi nối các vật liệu bằng kim loại độn có nhiệt độ nóng chảy thấp hơn so với các vật liệu cơ bản. Dòng điện xoay chiều từ cuộn dây cảm ứng tạo ra một trường điện từ gây ra hiện tượng đốt nóng cảm ứng trên các vật liệu chủ yếu là từ tính màu. Phương pháp này cung cấp nhiệt chọn lọc, các mối nối tốt với chất độn chỉ chảy ở những khu vực mong muốn, ít bị oxy hóa vì không có ngọn lửa và làm mát nhanh, gia nhiệt nhanh, nhất quán và phù hợp với sản xuất khối lượng lớn. Để tăng tốc các quy trình của chúng tôi và để đảm bảo tính nhất quán, chúng tôi thường sử dụng preforms. Thông tin về cơ sở hàn của chúng tôi sản xuất phụ kiện từ gốm đến kim loại, niêm phong kín, chân không cấp liệu, chân không cao và siêu cao và các thành phần kiểm soát chất lỏng có thể được tìm thấy tại đây: Sách giới thiệu về nhà máy hàn • SOLDERING: Trong quá trình hàn, chúng ta không có sự nóng chảy của các chi tiết gia công, mà là kim loại phụ có nhiệt độ nóng chảy thấp hơn so với các bộ phận tham gia chảy vào mối nối. Kim loại phụ trong quá trình hàn nóng chảy ở nhiệt độ thấp hơn so với hàn. Chúng tôi sử dụng các hợp kim không chứa chì để hàn và tuân thủ RoHS và đối với các ứng dụng và yêu cầu khác nhau, chúng tôi có các hợp kim khác nhau và phù hợp như hợp kim bạc. Hàn cung cấp cho chúng ta các khớp nối kín bằng khí và lỏng. Trong MỀM SOLDERING, kim loại phụ của chúng tôi có điểm nóng chảy dưới 400 độ C, trong khi trong SILVER SOLDERING và BRAZING, chúng tôi cần nhiệt độ cao hơn. Hàn mềm sử dụng nhiệt độ thấp hơn nhưng không tạo ra các mối nối chắc chắn cho các ứng dụng đòi hỏi ở nhiệt độ cao. Mặt khác, hàn bạc đòi hỏi nhiệt độ cao do mỏ hàn cung cấp và mang lại cho chúng ta các mối nối chắc chắn phù hợp với các ứng dụng nhiệt độ cao. Quá trình hàn yêu cầu nhiệt độ cao nhất và thường sử dụng một ngọn đuốc. Vì các khớp hàn rất bền, chúng là một ứng cử viên tốt để sửa chữa các vật nặng bằng sắt. Trong dây chuyền sản xuất của chúng tôi, chúng tôi sử dụng cả dây chuyền hàn tay thủ công cũng như dây chuyền hàn tự động. INDUCTION SOLDERING sử dụng dòng điện xoay chiều tần số cao trong cuộn dây đồng để tạo điều kiện gia nhiệt cảm ứng. Dòng điện được tạo ra trong phần được hàn và do đó nhiệt được tạo ra ở điện trở cao joint. Nhiệt này làm nóng chảy kim loại phụ. Flux cũng được sử dụng. Hàn cảm ứng là một phương pháp tốt để hàn các ống dẫn và đường ống trong một quá trình liên tục bằng cách quấn các cuộn dây xung quanh chúng. Việc hàn một số vật liệu như than chì và gốm sứ khó hơn vì nó đòi hỏi phải mạ các phôi bằng một kim loại thích hợp trước khi hàn. Điều này tạo điều kiện cho liên kết giao diện. Chúng tôi hàn các vật liệu như vậy đặc biệt cho các ứng dụng đóng gói kín. Chúng tôi sản xuất bảng mạch in (PCB) với khối lượng lớn chủ yếu sử dụng SÓNG SÓNG. Chỉ cho mục đích tạo mẫu với số lượng nhỏ, chúng tôi sử dụng hàn tay bằng mỏ hàn. Chúng tôi sử dụng phương pháp hàn sóng cho cả cụm PCB xuyên lỗ cũng như bề mặt (PCBA). Keo tạm thời giữ các thành phần gắn với bảng mạch và cụm được đặt trên băng tải và di chuyển qua thiết bị có chứa chất hàn nóng chảy. Đầu tiên, PCB được thông lượng và sau đó đi vào vùng gia nhiệt sơ bộ. Chất hàn nóng chảy nằm trong chảo và có dạng sóng đứng trên bề mặt của nó. Khi PCB di chuyển qua các sóng này, các sóng này tiếp xúc với đáy của PCB và dính vào các miếng hàn. Chất hàn chỉ nằm trên các chân và miếng đệm chứ không phải trên chính PCB. Các sóng trong vật hàn nóng chảy phải được kiểm soát tốt để không bị bắn tung tóe và các đỉnh sóng không chạm vào và làm ô nhiễm các khu vực không mong muốn của bảng. Trong REFLOW SOLDERING, chúng tôi sử dụng keo hàn dính để gắn tạm thời các thành phần điện tử vào bo mạch. Sau đó, các bảng được đưa qua lò nung nóng lại có kiểm soát nhiệt độ. Tại đây chất hàn nóng chảy và kết nối các thành phần vĩnh viễn. Chúng tôi sử dụng kỹ thuật này cho cả các thành phần gắn kết bề mặt cũng như các thành phần xuyên lỗ. Kiểm soát nhiệt độ thích hợp và điều chỉnh nhiệt độ lò là điều cần thiết để tránh phá hủy các linh kiện điện tử trên bo mạch do làm chúng quá nóng trên giới hạn nhiệt độ tối đa của chúng. Trong quá trình hàn nóng chảy lại, chúng ta thực sự có một số vùng hoặc giai đoạn, mỗi vùng có một đặc điểm nhiệt riêng biệt, chẳng hạn như bước gia nhiệt sơ bộ, bước ngâm nhiệt, bước nấu chảy lại và bước làm mát. Các bước khác nhau này là cần thiết để hàn lại các cụm bảng mạch in (PCBA) không bị hư hại. ULTRASONIC SOLDERING là một kỹ thuật thường được sử dụng khác với các khả năng độc đáo- Nó có thể được sử dụng để hàn các vật liệu thủy tinh, gốm và phi kim loại. Ví dụ các tấm quang điện là phi kim loại cần điện cực có thể được dán bằng kỹ thuật này. Trong quá trình hàn siêu âm, chúng tôi triển khai một đầu hàn được làm nóng cũng phát ra các rung động siêu âm. Những rung động này tạo ra các bong bóng tạo lỗ hổng tại bề mặt tiếp xúc của chất nền với vật liệu hàn nóng chảy. Năng lượng bùng nổ của sự xâm thực làm thay đổi bề mặt oxit và loại bỏ bụi bẩn và oxit. Trong thời gian này một lớp hợp kim cũng được hình thành. Chất hàn ở bề mặt liên kết kết hợp với oxy và cho phép hình thành một liên kết chung bền chặt giữa thủy tinh và vật hàn. DIP SOLDERING có thể được coi là một phiên bản đơn giản hơn của hàn sóng, chỉ phù hợp cho sản xuất quy mô nhỏ. Thông lượng làm sạch đầu tiên được áp dụng như trong các quy trình khác. PCB với các thành phần được gắn kết được nhúng thủ công hoặc bán tự động vào bể chứa chất hàn nóng chảy. Chất hàn nóng chảy dính vào các khu vực kim loại tiếp xúc mà không được bảo vệ bằng mặt nạ hàn trên bảng. Thiết bị đơn giản và rẻ tiền. • KEO TRÁI CÂY: Đây là một kỹ thuật phổ biến khác mà chúng tôi thường xuyên sử dụng và nó liên quan đến việc kết dính các bề mặt bằng keo, epoxit, chất dẻo hoặc các hóa chất khác. Việc kết dính được thực hiện bằng cách làm bay hơi dung môi, bằng cách đóng rắn bằng nhiệt, bằng tia UV, bằng cách đóng rắn bằng áp suất hoặc chờ một thời gian nhất định. Nhiều loại keo hiệu suất cao khác nhau được sử dụng trong dây chuyền sản xuất của chúng tôi. Với các quy trình ứng dụng và đóng rắn được thiết kế phù hợp, liên kết kết dính có thể tạo ra các liên kết ứng suất rất thấp, bền và đáng tin cậy. Các liên kết kết dính có thể là chất bảo vệ tốt chống lại các yếu tố môi trường như độ ẩm, chất gây ô nhiễm, chất ăn mòn, rung động ... vv. Ưu điểm của liên kết kết dính là: chúng có thể được áp dụng cho các vật liệu khó hàn, hàn hoặc hàn. Ngoài ra, nó có thể thích hợp hơn cho các vật liệu nhạy cảm với nhiệt sẽ bị hỏng do hàn hoặc các quá trình nhiệt độ cao khác. Các ưu điểm khác của chất kết dính là chúng có thể được áp dụng cho các bề mặt có hình dạng không đều và tăng trọng lượng lắp ráp lên một lượng rất nhỏ khi so sánh với các phương pháp khác. Ngoài ra những thay đổi về kích thước trong các bộ phận là rất nhỏ. Một số loại keo có đặc tính khớp chỉ số và có thể được sử dụng giữa các thành phần quang học mà không làm giảm đáng kể cường độ ánh sáng hoặc tín hiệu quang học. Mặt khác, nhược điểm là thời gian đóng rắn lâu hơn có thể làm chậm dây chuyền sản xuất, yêu cầu cố định, yêu cầu chuẩn bị bề mặt và khó tháo rời khi cần gia công lại. Hầu hết các hoạt động liên kết kết dính của chúng tôi bao gồm các bước sau: - Xử lý bề mặt: Các quy trình làm sạch đặc biệt như làm sạch bằng nước khử ion, làm sạch bằng cồn, làm sạch bằng plasma hoặc corona là phổ biến. Sau khi làm sạch, chúng tôi có thể bôi chất xúc tiến bám dính lên bề mặt để đảm bảo các mối nối tốt nhất có thể. -Part Fixturing: Đối với cả ứng dụng kết dính cũng như để bảo dưỡng, chúng tôi thiết kế và sử dụng đồ đạc tùy chỉnh. -Ứng dụng bổ sung: Đôi khi chúng tôi sử dụng thủ công và đôi khi tùy trường hợp các hệ thống tự động như rô bốt, động cơ servo, bộ truyền động tuyến tính để cung cấp chất kết dính đến đúng vị trí và chúng tôi sử dụng máy phân phối để phân phối chất kết dính đúng khối lượng và số lượng. - Đóng rắn: Tùy thuộc vào chất kết dính, chúng tôi có thể sử dụng sấy khô và đóng rắn đơn giản cũng như đóng rắn dưới đèn UV hoạt động như chất xúc tác hoặc đóng rắn nhiệt trong lò hoặc sử dụng các bộ phận gia nhiệt điện trở gắn trên đồ gá và đồ đạc. Chúng tôi khuyên bạn nên nhấp vào đây đểTẢI XUỐNG Các minh họa sơ đồ về các quy trình buộc chặt của AGS-TECH Inc. Điều này sẽ giúp bạn hiểu rõ hơn về thông tin chúng tôi đang cung cấp cho bạn bên dưới. • CÁC QUÁ TRÌNH GIA CÔNG NHANH: Các quá trình gia công cơ khí của chúng tôi được chia thành hai loại nhỏ: NHANH CHÓNG và GIA NHẬP. Ví dụ về ốc vít chúng tôi sử dụng là vít, ghim, đai ốc, bu lông, đinh tán. Ví dụ về các khớp nối tích hợp mà chúng tôi sử dụng là khớp nối nhanh và khớp co lại, đường nối, đường gấp khúc. Sử dụng nhiều phương pháp buộc, chúng tôi đảm bảo các khớp cơ của chúng tôi chắc chắn và đáng tin cậy trong nhiều năm sử dụng. VÍT và CHỐT là một số loại ốc vít được sử dụng phổ biến nhất để giữ các vật lại với nhau và định vị. Vít và bu lông của chúng tôi đáp ứng tiêu chuẩn ASME. Nhiều loại vít và bu lông khác nhau được triển khai bao gồm vít nắp lục giác và bu lông lục giác, vít trễ và bu lông, vít hai đầu, vít chốt, vít mắt, vít gương, vít kim loại tấm, vít điều chỉnh tinh, vít tự khoan và tự khai thác , vít định vị, vít có vòng đệm tích hợp,… và hơn thế nữa. Chúng tôi có nhiều loại đầu vít khác nhau như đầu chìm, vòm, tròn, đầu bích và nhiều loại ổ vít khác nhau như khe cắm, phillips, vuông, ổ cắm hex. Mặt khác, A RIVET là một dây buộc cơ học vĩnh cửu bao gồm một trục hình trụ trơn và một mặt là đầu. Sau khi lắp vào, đầu kia của đinh tán bị biến dạng và đường kính của nó được mở rộng để nó giữ nguyên vị trí. Nói cách khác, trước khi lắp đặt, đinh tán có một đầu và sau khi lắp đặt, nó có hai đầu. Chúng tôi lắp đặt nhiều loại đinh tán khác nhau tùy thuộc vào ứng dụng, độ bền, khả năng tiếp cận và chi phí như đinh tán đầu tròn / đặc, kết cấu, bán ống, mù, oscar, ổ đĩa, xả, khóa ma sát, đinh tán tự xuyên. Tán đinh có thể được ưu tiên trong các trường hợp cần tránh biến dạng nhiệt và thay đổi tính chất vật liệu do nhiệt hàn. Tán đinh cũng mang lại trọng lượng nhẹ và đặc biệt là chịu lực tốt và chịu được lực cắt. Chống lại tải trọng kéo tuy nhiên vít, đai ốc và bu lông có thể phù hợp hơn. Trong quá trình ĐÓNG CỬA, chúng tôi sử dụng đột dập và khuôn dập đặc biệt để tạo thành một khóa liên động cơ học giữa các tấm kim loại được nối với nhau. Cú đấm đẩy các lớp kim loại tấm vào trong khuôn và dẫn đến việc hình thành một mối nối vĩnh viễn. Không cần sưởi ấm và không cần làm mát trong clinching và đó là một quá trình làm việc lạnh. Đây là một quá trình kinh tế có thể thay thế hàn điểm trong một số trường hợp. Trong PINNING, chúng tôi sử dụng các chân là các phần tử máy được sử dụng để cố định vị trí của các bộ phận máy tương đối với nhau. Các loại chính là chốt khóa, chốt cotter, chốt lò xo, chốt chốt, and pin chia. Trong STAPLING, chúng tôi sử dụng súng bắn ghim và kim ghim là những chốt hai đầu được sử dụng để nối hoặc buộc các vật liệu. Ghim có những ưu điểm sau: Tiết kiệm, sử dụng đơn giản và nhanh chóng, vương miện của ghim có thể được sử dụng để kết nối các vật liệu với nhau. làm hỏng, loại bỏ tương đối dễ dàng. ÉP NỐI được thực hiện bằng cách đẩy các bộ phận lại với nhau và ma sát giữa chúng sẽ gắn chặt các bộ phận lại. Các bộ phận phù hợp ép bao gồm một trục quá khổ và một lỗ nhỏ hơn thường được lắp ráp bằng một trong hai phương pháp: Bằng cách tác dụng lực hoặc tận dụng sự giãn nở hoặc co lại vì nhiệt của các bộ phận. Khi một bộ phận ép được thiết lập bằng cách tác động một lực, chúng tôi sử dụng máy ép thủy lực hoặc máy ép vận hành bằng tay. Mặt khác, khi khớp nối ép được thiết lập bằng cách giãn nở nhiệt, chúng tôi đốt nóng các bộ phận bao bọc và lắp ráp chúng vào vị trí của chúng khi còn nóng. Khi nguội, chúng co lại và trở lại kích thước bình thường. Điều này dẫn đến một sự phù hợp báo chí tốt. Chúng tôi gọi cách khác là SHRINK-FITTING. Cách khác để làm điều này là làm mát các bộ phận được bao bọc trước khi lắp ráp và sau đó trượt chúng vào các bộ phận giao phối của chúng. Khi lắp ráp nóng lên, chúng sẽ nở ra và chúng ta có được một sự vừa vặn chặt chẽ. Phương pháp thứ hai này có thể thích hợp hơn trong trường hợp gia nhiệt có nguy cơ làm thay đổi tính chất vật liệu. Làm mát an toàn hơn trong những trường hợp đó. Các thành phần và cụm lắp ráp khí nén & thủy lực • Van, các bộ phận thủy lực và khí nén như vòng chữ O, vòng đệm, vòng đệm, miếng đệm, vòng đệm, miếng đệm. Vì van và các thành phần khí nén có rất nhiều loại, chúng tôi không thể liệt kê tất cả mọi thứ ở đây. Tùy thuộc vào môi trường vật lý và hóa học trong ứng dụng của bạn, chúng tôi có các sản phẩm đặc biệt dành cho bạn. Vui lòng chỉ rõ cho chúng tôi ứng dụng, loại thành phần, thông số kỹ thuật, điều kiện môi trường như áp suất, nhiệt độ, chất lỏng hoặc khí sẽ tiếp xúc với van và các bộ phận khí nén của bạn; và chúng tôi sẽ chọn sản phẩm phù hợp nhất cho bạn hoặc sản xuất nó đặc biệt cho ứng dụng của bạn. CLICK Product Finder-Locator Service TRANG TRƯỚC
- Machine Elements Manufacturing, Gears, Gear Drives, Bearings, Keys, Splines
Machine Elements Manufacturing, Gears, Gear Drives, Bearings, Keys, Splines, Pins, Shafts, Seals, Fasteners, Clutch, Cams, Followers, Belts, Couplings, Shafts Sản xuất phần tử máy móc Đọc thêm Thắt lưng & dây xích & lắp ráp ổ cáp Đọc thêm Lắp ráp bánh răng & truyền động bánh răng Đọc thêm Sản xuất khớp nối & vòng bi Đọc thêm Sản xuất phím & Splines & Ghim Đọc thêm Cams & Followers & Linkages & Ratchet Wheels Sản xuất Đọc thêm Sản xuất trục Đọc thêm Sản xuất con dấu cơ khí Đọc thêm Lắp ráp ly hợp & phanh Đọc thêm Sản xuất Chốt Đọc thêm Lắp ráp máy đơn giản MACHINE ELEMENTS là thành phần cơ bản của máy. Các yếu tố này bao gồm ba loại cơ bản: 1.) Các thành phần kết cấu bao gồm các bộ phận khung, ổ trục, trục, trục, ốc vít, con dấu và chất bôi trơn. 2.) Các cơ cấu điều khiển chuyển động theo nhiều cách khác nhau như bộ truyền động bánh răng, bộ truyền động dây đai hoặc xích, các liên kết, hệ thống cam và bánh sau, phanh & ly hợp. 3.) Các thành phần điều khiển như nút, công tắc, đèn báo, cảm biến, bộ truyền động và bộ điều khiển máy tính. Hầu hết các phần tử máy mà chúng tôi cung cấp cho bạn đều được tiêu chuẩn hóa theo kích thước phổ biến, nhưng các phần tử máy được chế tạo tùy chỉnh cũng có sẵn cho các ứng dụng chuyên biệt của bạn. Việc tùy chỉnh các thành phần máy có thể diễn ra trên các thiết kế hiện có trong danh mục có thể tải xuống của chúng tôi hoặc trên các thiết kế hoàn toàn mới. Việc tạo mẫu và chế tạo các chi tiết máy có thể được tiến hành sau khi thiết kế được cả hai bên chấp thuận. Nếu các phần tử máy mới cần được thiết kế và sản xuất, khách hàng của chúng tôi có thể gửi email cho chúng tôi bản thiết kế của riêng họ và chúng tôi sẽ xem xét chúng để phê duyệt hoặc họ yêu cầu chúng tôi thiết kế các phần tử máy cho ứng dụng của họ. Trong trường hợp thứ hai, chúng tôi sử dụng tất cả thông tin đầu vào từ khách hàng và thiết kế các chi tiết máy và gửi bản thiết kế cuối cùng cho khách hàng của chúng tôi để phê duyệt. Sau khi được chấp thuận, chúng tôi sản xuất các sản phẩm đầu tiên và sau đó sản xuất các chi tiết máy theo thiết kế cuối cùng. Ở bất kỳ giai đoạn nào của công việc này, trong trường hợp một thiết kế phần tử máy cụ thể hoạt động không đạt yêu cầu tại hiện trường (điều này hiếm khi xảy ra), chúng tôi sẽ xem xét toàn bộ dự án và thực hiện các sửa đổi cùng với khách hàng của chúng tôi nếu cần. Thông lệ tiêu chuẩn của chúng tôi là ký các thỏa thuận không tiết lộ (NDA) với khách hàng để thiết kế các chi tiết máy hoặc bất kỳ sản phẩm nào khác bất cứ khi nào cần hoặc được yêu cầu. Khi các phần tử máy móc cho một khách hàng cụ thể được thiết kế và sản xuất theo yêu cầu, chúng tôi chỉ định mã sản phẩm cho nó và chỉ sản xuất và bán chúng cho khách hàng sở hữu sản phẩm của chúng tôi. Chúng tôi tái tạo các chi tiết máy bằng cách sử dụng các công cụ, khuôn mẫu và quy trình đã phát triển nhiều lần nếu cần và bất cứ khi nào khách hàng của chúng tôi đặt hàng lại chúng. Nói cách khác, một khi một phần tử máy tùy chỉnh được thiết kế và sản xuất cho bạn, tài sản trí tuệ cũng như tất cả dụng cụ và khuôn mẫu sẽ được chúng tôi bảo lưu và dự trữ vô thời hạn cho bạn và các sản phẩm được sao chép theo ý muốn của bạn. Chúng tôi cũng cung cấp cho khách hàng các dịch vụ kỹ thuật bằng cách kết hợp một cách sáng tạo các phần tử máy vào một thành phần hoặc cụm lắp ráp phục vụ một ứng dụng và đáp ứng hoặc vượt quá mong đợi của khách hàng. Các nhà máy chế tạo các phần tử máy của chúng tôi đạt tiêu chuẩn ISO9001, QS9000 hoặc TS16949. Ngoài ra, hầu hết các sản phẩm của chúng tôi đều có dấu CE hoặc UL và đáp ứng các tiêu chuẩn quốc tế có liên quan như ISO, SAE, ASME, DIN. Vui lòng nhấp vào menu con để nhận thông tin chi tiết về các phần tử máy của chúng tôi bao gồm: - Thắt lưng, dây xích và ổ cáp - Bánh răng và Ổ đĩa bánh răng - Khớp nối & Vòng bi - Phím & Splines & ghim - Cams & liên kết - Trục - Con dấu cơ khí - Ly hợp & Phanh công nghiệp - Chốt - Nhưng cô may đơn giản Chúng tôi đã chuẩn bị một tài liệu tham khảo cho khách hàng, nhà thiết kế và nhà phát triển các sản phẩm mới bao gồm các yếu tố máy móc. Bạn có thể tự làm quen với một số thuật ngữ thường dùng trong thiết kế linh kiện máy: Tải xuống tài liệu quảng cáo cho các Thuật ngữ Cơ khí Phổ biến được các Nhà thiết kế và Kỹ sư sử dụng Các yếu tố máy móc của chúng tôi được ứng dụng trong nhiều lĩnh vực khác nhau như máy móc công nghiệp, hệ thống tự động hóa, thiết bị đo lường và kiểm tra, thiết bị giao thông vận tải, máy xây dựng và thực tế ở mọi nơi bạn có thể nghĩ đến. AGS-TECH phát triển và sản xuất các chi tiết máy từ các vật liệu khác nhau tùy thuộc vào ứng dụng. Vật liệu được sử dụng cho các bộ phận của máy có thể bao gồm từ nhựa đúc được sử dụng cho đồ chơi đến vỏ thép cứng và thép phủ đặc biệt cho máy móc công nghiệp. Các nhà thiết kế của chúng tôi sử dụng phần mềm chuyên nghiệp hiện đại và các công cụ thiết kế để phát triển các chi tiết máy, xem xét các chi tiết như góc trong răng bánh răng, ứng suất liên quan, tốc độ mòn… .v.v. Vui lòng cuộn qua menu con của chúng tôi và tải xuống tài liệu quảng cáo và danh mục sản phẩm của chúng tôi để xem liệu bạn có thể xác định vị trí các phần tử máy sẵn có cho ứng dụng của mình hay không. Nếu bạn không thể tìm thấy ứng dụng phù hợp, vui lòng cho chúng tôi biết và chúng tôi sẽ làm việc với bạn để phát triển và sản xuất các phần tử máy đáp ứng nhu cầu của bạn. Nếu bạn chủ yếu quan tâm đến khả năng kỹ thuật và nghiên cứu & phát triển của chúng tôi thay vì khả năng sản xuất, thì chúng tôi mời bạn truy cập trang web của chúng tôi http://www.ags-engineering.com ở đâu bạn có thể tìm thấy thông tin chi tiết hơn về thiết kế, phát triển sản phẩm, phát triển quy trình, dịch vụ tư vấn kỹ thuật và hơn thế nữa của chúng tôi CLICK Product Finder-Locator Service TRANG TRƯỚC
- Composites, Composite Materials Manufacturing, Fiber Reinforced
Composites, Composite Materials Manufacturing, Particle and Fiber Reinforced, Cermets, Ceramic & Metal Composite, Glass Fiber Reinforced Polymer, Lay-Up Process Sản xuất vật liệu tổng hợp & vật liệu tổng hợp Định nghĩa một cách đơn giản, PHỐI HỢP hay VẬT LIỆU COMPOSITE là vật liệu bao gồm hai hoặc nhiều vật liệu có tính chất vật lý hoặc hóa học khác nhau, nhưng khi kết hợp lại với nhau chúng trở thành một vật liệu khác với các vật liệu cấu thành. Chúng ta cần chỉ ra rằng các vật liệu cấu thành vẫn tách biệt và khác biệt trong cấu trúc. Mục tiêu trong sản xuất vật liệu composite là thu được một sản phẩm vượt trội hơn các thành phần của nó và kết hợp các tính năng mong muốn của từng thành phần. Như một ví dụ; sức mạnh, trọng lượng thấp hoặc giá thấp hơn có thể là động lực thúc đẩy thiết kế và sản xuất composite. Loại vật liệu tổng hợp chúng tôi cung cấp là vật liệu tổng hợp được gia cố bằng hạt, vật liệu tổng hợp được gia cố bằng sợi bao gồm vật liệu tổng hợp gốm-ma trận / polyme-ma trận / ma trận kim loại / carbon-carbon / hỗn hợp, vật liệu tổng hợp cấu trúc & nhiều lớp & có cấu trúc bánh sandwich và vật liệu tổng hợp nano. Các kỹ thuật chế tạo mà chúng tôi triển khai trong sản xuất vật liệu composite là: Đùn, quy trình sản xuất prereg, đặt sợi tiên tiến, cuộn sợi, đặt sợi phù hợp, quy trình xếp lớp phun sợi thủy tinh, quy trình chần, quy trình lanxide, ghim z. Nhiều vật liệu composite được tạo thành từ hai pha, ma trận, liên tục và bao quanh pha kia; và pha phân tán được bao quanh bởi chất nền. Chúng tôi khuyên bạn nên nhấp vào đây đểTẢI XUỐNG Hình minh họa sơ đồ của chúng tôi về Sản xuất vật liệu tổng hợp và vật liệu tổng hợp của AGS-TECH Inc. Điều này sẽ giúp bạn hiểu rõ hơn về thông tin chúng tôi đang cung cấp cho bạn bên dưới. • CÁC THÀNH PHẦN TÁI TẠO CỘNG PHẦN: Loại này bao gồm hai loại: Vật liệu tổng hợp hạt lớn và vật liệu tổng hợp tăng cường phân tán. Trong loại trước đây, tương tác ma trận hạt không thể được xử lý ở cấp độ nguyên tử hoặc phân tử. Thay vào đó, cơ học liên tục là hợp lệ. Mặt khác, trong vật liệu tổng hợp tăng cường phân tán, các hạt thường nhỏ hơn nhiều trong phạm vi hàng chục nanomet. Một ví dụ về composite hạt lớn là polyme mà chất độn đã được thêm vào. Chất độn cải thiện các đặc tính của vật liệu và có thể thay thế một phần thể tích polyme bằng vật liệu kinh tế hơn. Phần thể tích của hai giai đoạn ảnh hưởng đến hoạt động của hỗn hợp. Vật liệu tổng hợp hạt lớn được sử dụng với kim loại, polyme và gốm sứ. CERMETS là ví dụ về vật liệu tổng hợp gốm / kim loại. Gốm kim loại phổ biến nhất của chúng tôi là cacbua xi măng. Nó bao gồm gốm cacbua chịu lửa như các hạt cacbua vonfram trong ma trận kim loại như coban hoặc niken. Các vật liệu tổng hợp cacbua này được sử dụng rộng rãi làm công cụ cắt thép cứng. Các hạt cacbua cứng chịu trách nhiệm cho hoạt động cắt và độ dẻo dai của chúng được tăng cường nhờ ma trận kim loại dễ uốn. Vì vậy, chúng tôi có được những lợi thế của cả hai vật liệu trong một hỗn hợp duy nhất. Một ví dụ phổ biến khác của composite hạt lớn mà chúng tôi sử dụng là các hạt carbon đen trộn với cao su lưu hóa để thu được composite có độ bền kéo cao, dẻo dai, chống rách và mài mòn. Một ví dụ về composite tăng cường phân tán là kim loại và hợp kim kim loại được tăng cường và làm cứng bằng sự phân tán đồng đều của các hạt mịn của một vật liệu rất cứng và trơ. Khi các mảnh oxit nhôm rất nhỏ được thêm vào ma trận kim loại nhôm, chúng tôi thu được bột nhôm thiêu kết có độ bền nhiệt độ cao được nâng cao . • CÁC THÀNH PHẦN TÁI TẠO SỢI: Loại vật liệu tổng hợp này trên thực tế là quan trọng nhất. Mục tiêu cần đạt được là độ bền và độ cứng cao trên một đơn vị trọng lượng. Thành phần sợi, chiều dài, định hướng và nồng độ trong các vật liệu tổng hợp này là rất quan trọng trong việc xác định các đặc tính và tính hữu dụng của những vật liệu này. Có ba nhóm sợi chúng tôi sử dụng: râu, sợi và dây. WHISKERS là những tinh thể đơn rất mỏng và dài. Chúng là một trong những vật liệu mạnh nhất. Một số vật liệu đánh trứng ví dụ là than chì, nitrua silic, ôxít nhôm. FIBERS mặt khác chủ yếu là polyme hoặc gốm sứ và ở trạng thái đa tinh thể hoặc vô định hình. Nhóm thứ ba là DÂY mịn có đường kính tương đối lớn và thường bao gồm thép hoặc vonfram. Một ví dụ về composite gia cố bằng dây là lốp xe ô tô kết hợp dây thép bên trong cao su. Tùy thuộc vào vật liệu ma trận, chúng tôi có các vật liệu tổng hợp sau: THÀNH PHẦN POLYMER-MATRIX: Chúng được làm từ nhựa polyme và sợi làm thành phần gia cố. Một nhóm con trong số này được gọi là Vật liệu tổng hợp polyme gia cố bằng sợi thủy tinh (GFRP) chứa các sợi thủy tinh liên tục hoặc không liên tục trong một nền polyme. Thủy tinh có độ bền cao, kinh tế, dễ chế tạo thành sợi và trơ về mặt hóa học. Nhược điểm của chúng là độ cứng và độ cứng hạn chế, nhiệt độ phục vụ chỉ lên đến 200 - 300 độ C. Sợi thủy tinh thích hợp cho thân ô tô và thiết bị vận tải, thân xe hàng hải, thùng chứa. Chúng không thích hợp cho hàng không vũ trụ cũng như chế tạo cầu do độ cứng hạn chế. Nhóm con còn lại được gọi là Vật liệu tổng hợp polyme gia cố bằng sợi carbon (CFRP). Ở đây, carbon là vật liệu sợi của chúng ta trong ma trận polyme. Carbon được biết đến với mô đun và độ bền cụ thể cao và khả năng duy trì chúng ở nhiệt độ cao. Sợi carbon có thể cung cấp cho chúng ta các modul độ bền kéo tiêu chuẩn, trung bình, cao và siêu cao. Hơn nữa, sợi carbon cung cấp các đặc tính vật lý và cơ học đa dạng và do đó thích hợp cho các ứng dụng kỹ thuật tùy chỉnh khác nhau. Vật liệu tổng hợp CFRP có thể được coi là để sản xuất thiết bị thể thao và giải trí, bình chịu áp lực và các thành phần cấu trúc hàng không vũ trụ. Tuy nhiên, một nhóm phụ khác, Vật liệu tổng hợp polyme được gia cố bằng sợi Aramid cũng là vật liệu có độ bền cao và mô đun. Tỷ lệ sức mạnh trên trọng lượng của chúng rất cao. Sợi Aramid còn được gọi với tên thương mại KEVLAR và NOMEX. Dưới sức căng, chúng hoạt động tốt hơn các vật liệu sợi polyme khác, nhưng chúng chịu nén yếu. Sợi Aramid dẻo dai, chịu va đập, chống rung và mỏi, ổn định ở nhiệt độ cao, trơ về mặt hóa học ngoại trừ axit và bazơ mạnh. Sợi Aramid được sử dụng rộng rãi trong đồ thể thao, áo chống đạn, lốp xe, dây thừng, vỏ bọc cáp quang. Các vật liệu gia cố bằng sợi khác cũng tồn tại nhưng được sử dụng ở mức độ thấp hơn. Đó là chủ yếu là bo, cacbua silic, ôxít nhôm. Mặt khác, vật liệu nền polyme cũng rất quan trọng. Nó xác định nhiệt độ phục vụ tối đa của composite vì polyme nói chung có nhiệt độ nóng chảy và phân huỷ thấp hơn. Polyeste và vinyl este được sử dụng rộng rãi làm nền polyme. Nhựa cũng được sử dụng và chúng có khả năng chống ẩm và tính chất cơ học tuyệt vời. Ví dụ: nhựa polyimide có thể được sử dụng lên đến khoảng 230 độ Celcius. THÀNH PHẦN KIM LOẠI-MATRIX: Trong những vật liệu này, chúng tôi sử dụng ma trận kim loại dễ uốn và nhiệt độ sử dụng thường cao hơn các thành phần cấu thành của chúng. Khi so sánh với vật liệu tổng hợp nền polyme, chúng có thể có nhiệt độ hoạt động cao hơn, không bắt lửa và có thể có khả năng chống phân hủy tốt hơn so với chất lỏng hữu cơ. Tuy nhiên chúng đắt hơn. Vật liệu gia cố như râu, hạt, sợi liên tục và không liên tục; và các vật liệu ma trận như đồng, nhôm, magiê, titan, siêu hợp kim đang được sử dụng phổ biến. Các ứng dụng ví dụ là các thành phần động cơ được làm bằng ma trận hợp kim nhôm được gia cố bằng nhôm oxit và sợi carbon. THÀNH PHẦN CERAMIC-MATRIX: Vật liệu gốm được biết đến với độ tin cậy nhiệt độ cao vượt trội. Tuy nhiên, chúng rất giòn và có giá trị thấp về độ dẻo dai khi gãy. Bằng cách nhúng các hạt, sợi hoặc râu của một gốm này vào ma trận của gốm khác, chúng tôi có thể tạo ra vật liệu tổng hợp có độ bền đứt gãy cao hơn. Các vật liệu nhúng này về cơ bản ức chế sự lan truyền vết nứt bên trong ma trận bằng một số cơ chế như làm lệch các đỉnh vết nứt hoặc tạo cầu qua các mặt vết nứt. Ví dụ, alumin được gia cố bằng ria SiC được sử dụng làm bộ chèn dụng cụ cắt để gia công các hợp kim kim loại cứng. Chúng có thể cho thấy hiệu suất tốt hơn so với cacbua xi măng. THÀNH PHẦN CACBON-CACBON: Cả chất gia cố cũng như chất nền đều là cacbon. Chúng có mô đun kéo cao và cường độ ở nhiệt độ cao trên 2000 độ C. Những đặc tính này làm cho chúng trở nên lý tưởng cho các ứng dụng yêu cầu khả năng chống sốc nhiệt. Tuy nhiên, điểm yếu của vật liệu tổng hợp cacbon-cacbon là tính dễ bị oxy hóa ở nhiệt độ cao. Các ví dụ điển hình về việc sử dụng là khuôn ép nóng, sản xuất linh kiện động cơ tuabin tiên tiến. THÀNH PHẦN HYBRID: Hai hoặc nhiều loại sợi khác nhau được trộn trong một ma trận duy nhất. Do đó, người ta có thể điều chỉnh một vật liệu mới với sự kết hợp của các đặc tính. Một ví dụ là khi cả sợi carbon và sợi thủy tinh được kết hợp vào một loại nhựa cao phân tử. Sợi carbon cung cấp độ cứng và độ bền mật độ thấp nhưng đắt tiền. Mặt khác, kính không đắt nhưng thiếu độ cứng của sợi carbon. Vật liệu hỗn hợp thủy tinh-carbon cứng hơn và cứng hơn và có thể được sản xuất với chi phí thấp hơn. CHẾ BIẾN THÀNH PHẦN TÁI TẠO SỢI: Đối với chất dẻo gia cường sợi liên tục với các sợi phân bố đồng đều, định hướng theo cùng một hướng chúng ta sử dụng các kỹ thuật sau. ĐA NĂNG: Sản xuất các thanh, dầm và ống có chiều dài liên tục và tiết diện không đổi. Các ống sợi liên tục được ngâm tẩm với một loại nhựa nhiệt rắn và được kéo qua khuôn thép để định hình chúng thành hình dạng mong muốn. Tiếp theo, chúng đi qua một khuôn đóng rắn được gia công chính xác để đạt được hình dạng cuối cùng. Vì khuôn đóng rắn được làm nóng, nó đóng rắn ma trận nhựa. Máy kéo kéo vật liệu qua khuôn. Sử dụng lõi rỗng được chèn vào, chúng tôi có thể thu được các ống và hình dạng rỗng. Phương pháp ép đùn được tự động hóa và mang lại cho chúng tôi tỷ lệ sản xuất cao. Có thể sản xuất bất kỳ độ dài nào của sản phẩm. QUY TRÌNH SẢN XUẤT PREPREG: Prepreg là chất gia cường dạng sợi liên tục được ngâm tẩm trước với nhựa polyme đã đóng rắn một phần. Nó được sử dụng rộng rãi cho các ứng dụng kết cấu. Vật liệu có dạng băng và được vận chuyển dưới dạng băng. Nhà sản xuất tạo khuôn trực tiếp và đóng rắn hoàn toàn mà không cần thêm bất kỳ loại nhựa nào. Vì preregs trải qua phản ứng đóng rắn ở nhiệt độ phòng, chúng được bảo quản ở 0 độ C hoặc nhiệt độ thấp hơn. Sau khi sử dụng, phần băng còn lại được bảo quản ở nhiệt độ thấp. Nhựa nhiệt dẻo và nhựa nhiệt rắn được sử dụng và sợi gia cường của cacbon, aramid và thủy tinh là phổ biến. Để sử dụng preregs, trước tiên người ta lấy giấy lót nền của tàu sân bay ra và sau đó việc chế tạo được thực hiện bằng cách đặt băng prereg lên bề mặt dụng cụ (quy trình xếp lớp). Có thể đặt một số lớp bột để có được độ dày mong muốn. Thực hành thường xuyên là thay đổi hướng sợi để tạo ra một lớp cán chéo hoặc lớp góc. Cuối cùng, nhiệt và áp suất được áp dụng để đóng rắn. Cả quy trình xử lý thủ công cũng như quy trình tự động đều được sử dụng để cắt sơ chế và xếp lớp. CỬA SỔ LINH KIỆN: Các sợi gia cường liên tục được định vị chính xác theo một mô hình định trước để tuân theo một và thường có hình dạng chu kỳ. Đầu tiên, các sợi đi qua bể nhựa và sau đó được quấn vào trục gá bằng hệ thống tự động. Sau một số lần lặp lại cuộn dây sẽ đạt được độ dày mong muốn và quá trình đóng rắn được thực hiện ở nhiệt độ phòng hoặc bên trong tủ sấy. Bây giờ trục gá được tháo ra và sản phẩm được bán lại. Cuộn dây tóc có thể cung cấp tỷ lệ độ bền trên trọng lượng rất cao bằng cách cuộn sợi theo các mô hình chu vi, xoắn ốc và phân cực. Ống, bể chứa, vỏ được sản xuất bằng kỹ thuật này. • CÁC THÀNH PHẦN CẤU TRÚC: Nói chung chúng được tạo thành từ cả vật liệu đồng nhất và vật liệu tổng hợp. Do đó, các thuộc tính của chúng được xác định bởi vật liệu cấu thành và thiết kế hình học của các phần tử của nó. Dưới đây là các loại chính: THÀNH PHẦN LAMINAR: Các vật liệu kết cấu này được làm từ các tấm hoặc tấm hai chiều với các hướng có độ bền cao được ưu tiên. Các lớp được xếp chồng lên nhau và kết dính với nhau. Bằng cách xen kẽ các hướng cường độ cao theo hai trục vuông góc, chúng ta thu được hỗn hợp có cường độ cao theo cả hai hướng trong mặt phẳng hai chiều. Bằng cách điều chỉnh góc của các lớp, người ta có thể tạo ra một hỗn hợp có độ bền theo các hướng ưu tiên. Đồ trượt tuyết hiện đại được sản xuất theo cách này. SANDWICH PANELS: Những vật liệu tổng hợp cấu trúc này có trọng lượng nhẹ nhưng vẫn có độ cứng và độ bền cao. Tấm bánh sandwich bao gồm hai tấm bên ngoài được làm bằng vật liệu cứng và chắc như hợp kim nhôm, nhựa hoặc thép được gia cố bằng sợi và một lõi ở giữa các tấm bên ngoài. Lõi cần phải nhẹ và hầu hết thời gian có mô đun đàn hồi thấp. Vật liệu cốt lõi phổ biến là bọt polyme cứng, gỗ và tổ ong. Tấm bánh sandwich được sử dụng rộng rãi trong ngành xây dựng như vật liệu lợp mái, vật liệu sàn hoặc tường, và cả trong ngành hàng không vũ trụ. • NANOCOMPOSITES: Những vật liệu mới này bao gồm các hạt có kích thước nano được nhúng trong một ma trận. Sử dụng vật liệu nanocompozit, chúng tôi có thể sản xuất các vật liệu cao su có khả năng ngăn cản sự xâm nhập của không khí rất tốt trong khi vẫn duy trì các đặc tính cao su của chúng không thay đổi. CLICK Product Finder-Locator Service TRANG TRƯỚC
- Rapid Prototyping, Desktop Manufacturing, Additive Manufacturing, FDM
Rapid Prototyping, Desktop Manufacturing, Additive Manufacturing, Stereolithography, Polyjet, Fused Deposition Modeling, Selective Laser Sintering, FDM, SLS Sản xuất phụ gia và nhanh chóng Trong những năm gần đây, chúng tôi đã nhận thấy sự gia tăng nhu cầu về SẢN XUẤT RAPID hoặc RAPID PROTOTYPING. Quá trình này cũng có thể được gọi là SẢN XUẤT DESKTOP hoặc VẢI MẪU TỰ DO. Về cơ bản, một mô hình vật lý rắn của một bộ phận được tạo trực tiếp từ bản vẽ CAD ba chiều. Chúng tôi sử dụng thuật ngữ SẢN XUẤT BỔ SUNG cho các kỹ thuật khác nhau trong đó chúng tôi xây dựng các bộ phận trong các lớp. Sử dụng phần cứng và phần mềm điều khiển máy tính tích hợp, chúng tôi thực hiện sản xuất phụ gia. Các kỹ thuật sản xuất và tạo mẫu nhanh của chúng tôi là STEREOLITHOGRAPHY, POLYJET, FUSED-DEPOSITION, CHỌN LASER SINTERING, ELECTRON BEAM MELTING, IN BA-DIMENSIONAL, SẢN XUẤT TRỰC TIẾP, RAPID TOOLING. Chúng tôi khuyên bạn nên nhấp vào đây đểTẢI XUỐNG Hình minh họa Sơ đồ của chúng tôi về Sản xuất Phụ gia và Quy trình Sản xuất Nhanh của AGS-TECH Inc. Điều này sẽ giúp bạn hiểu rõ hơn về thông tin chúng tôi đang cung cấp cho bạn bên dưới. Tạo mẫu nhanh cung cấp cho chúng tôi: 1.) Thiết kế sản phẩm khái niệm được xem từ các góc độ khác nhau trên màn hình sử dụng hệ thống 3D / CAD. 2.) Nguyên mẫu từ vật liệu phi kim loại và kim loại được sản xuất và nghiên cứu từ các khía cạnh chức năng, kỹ thuật và thẩm mỹ. 3.) Việc tạo mẫu với chi phí thấp trong một thời gian rất ngắn được hoàn thành. Quá trình sản xuất phụ gia có thể giống như việc chế tạo một ổ bánh mì bằng cách xếp chồng và dán các lát riêng lẻ lên nhau. Nói cách khác, sản phẩm được sản xuất theo từng lát, hoặc từng lớp lắng đọng lên nhau. Hầu hết các bộ phận có thể được sản xuất trong vòng vài giờ. Kỹ thuật này là tốt nếu các bộ phận cần rất nhanh hoặc nếu số lượng cần ít và việc chế tạo khuôn và dụng cụ quá tốn kém và mất nhiều thời gian. Tuy nhiên, chi phí của một bộ phận rất đắt do nguyên liệu thô đắt tiền. • STEREOLITHOGRAPHY: Kỹ thuật này còn được viết tắt là STL, dựa trên việc đóng rắn và làm cứng một photopolyme lỏng thành một hình dạng cụ thể bằng cách tập trung một chùm tia laze vào nó. Laser polyme hóa photopolymer và đóng rắn. Bằng cách quét chùm tia laser UV theo hình dạng được lập trình dọc theo bề mặt của hỗn hợp photopolymer, bộ phận được tạo ra từ dưới lên theo từng lát riêng lẻ xếp chồng lên nhau. Việc quét điểm laser được lặp lại nhiều lần để đạt được các dạng hình học được lập trình trong hệ thống. Sau khi bộ phận được sản xuất hoàn chỉnh, nó được tháo ra khỏi bệ, thấm và làm sạch bằng sóng siêu âm và ngâm rượu. Tiếp theo, nó được chiếu xạ UV trong vài giờ để đảm bảo polyme được đóng rắn hoàn toàn và cứng lại. Để tóm tắt quá trình, một nền tảng được nhúng vào hỗn hợp photopolymer và chùm tia laser UV được điều khiển và di chuyển qua hệ thống điều khiển servo theo hình dạng của bộ phận mong muốn và bộ phận này thu được bằng cách định vị lớp polyme theo từng lớp. Tất nhiên kích thước tối đa của bộ phận được tạo ra được xác định bởi thiết bị chụp ảnh lập thể. • POLYJET: Tương tự như in phun, trong polyjet, chúng tôi có tám đầu in có tác dụng lắng đọng photopolymer trên khay xây dựng. Tia cực tím được đặt bên cạnh các tia lửa ngay lập tức đóng rắn và cứng lại từng lớp. Hai vật liệu được sử dụng trong polyjet. Vật liệu đầu tiên là để sản xuất mô hình thực tế. Vật liệu thứ hai, một loại nhựa giống như gel được sử dụng để hỗ trợ. Cả hai vật liệu này đều được lắng từng lớp và đóng rắn đồng thời. Sau khi hoàn thành mô hình, vật liệu hỗ trợ được loại bỏ bằng dung dịch nước. Nhựa được sử dụng tương tự như kỹ thuật in lập thể (STL). Polyjet có những ưu điểm sau so với kỹ thuật in lập thể: 1.) Không cần làm sạch các bộ phận. 2.) Không cần bảo dưỡng sau quá trình xử lý 3.) Có thể có độ dày lớp nhỏ hơn và do đó chúng tôi có được độ phân giải tốt hơn và có thể sản xuất các bộ phận tốt hơn. • MÔ HÌNH PHỤ GIA FUSED: Còn được viết tắt là FDM, trong phương pháp này, đầu máy đùn điều khiển bằng rô-bốt di chuyển theo hai hướng nguyên tắc trên bàn. Cáp được hạ xuống và nâng lên khi cần thiết. Từ lỗ của một khuôn nung nóng trên đầu, một sợi nhựa nhiệt dẻo được đùn ra và một lớp ban đầu được lắng đọng trên nền xốp. Điều này được thực hiện nhờ đầu đùn đi theo một đường dẫn định trước. Sau lớp ban đầu, bàn được hạ xuống và các lớp tiếp theo được xếp chồng lên nhau. Đôi khi khi chế tạo một bộ phận phức tạp, cần có các cấu trúc hỗ trợ để quá trình lắng đọng có thể tiếp tục theo những hướng nhất định. Trong những trường hợp này, vật liệu hỗ trợ được ép đùn với khoảng cách giữa các sợi nhỏ hơn trên một lớp để nó yếu hơn vật liệu mô hình. Các cấu trúc hỗ trợ này sau đó có thể bị giải thể hoặc bị phá vỡ sau khi hoàn thành bộ phận. Kích thước khuôn của máy đùn xác định độ dày của các lớp đùn. Quy trình FDM sản xuất các bộ phận có bề mặt bậc trên mặt phẳng bên ngoài xiên. Nếu độ nhám này là không thể chấp nhận được, có thể sử dụng phương pháp đánh bóng bằng hơi hóa chất hoặc dụng cụ đã được gia nhiệt để làm mịn chúng. Ngay cả sáp đánh bóng cũng có sẵn làm vật liệu phủ để loại bỏ các bước này và đạt được dung sai hình học hợp lý. • CHỌN LASER SINTERING: Còn được ký hiệu là SLS, quá trình này dựa trên quá trình thiêu kết một cách chọn lọc polyme, gốm hoặc bột kim loại vào một vật thể. Đáy của buồng chế biến có hai xi lanh: Một xi lanh chế tạo một phần và một xi lanh cấp bột. Cái trước được hạ xuống từng bước đến nơi bộ phận thiêu kết đang được tạo thành và cái sau được nâng lên từng bước để cung cấp bột cho xi lanh chế tạo bộ phận thông qua một cơ cấu con lăn. Đầu tiên, một lớp bột mỏng được lắng đọng trong hình trụ xây dựng một phần, sau đó một chùm tia laze được tập trung vào lớp đó, truy tìm và nung chảy / thiêu kết một mặt cắt cụ thể, sau đó phân giải thành chất rắn. Bột là những vùng không bị tia laze chiếu vào vẫn lỏng lẻo nhưng vẫn hỗ trợ phần rắn. Sau đó, một lớp bột khác được lắng xuống và quá trình lặp lại nhiều lần để thu được phần. Cuối cùng, các hạt bột rời được lắc ra. Tất cả những điều này được thực hiện bởi một máy tính điều khiển quá trình sử dụng các hướng dẫn được tạo bởi chương trình CAD 3D của bộ phận đang được sản xuất. Các vật liệu khác nhau như polyme (như ABS, PVC, polyeste), sáp, kim loại và gốm sứ với chất kết dính polyme thích hợp có thể được lắng đọng. • ELECTRON-BEAM MELTING: Tương tự như thiêu kết bằng laser chọn lọc, nhưng sử dụng chùm tia điện tử để làm tan chảy titan hoặc bột crôm coban để tạo nguyên mẫu trong chân không. Một số phát triển đã được thực hiện để thực hiện quá trình này trên thép không gỉ, hợp kim nhôm và đồng. Nếu độ bền mỏi của các bộ phận được sản xuất cần tăng lên, chúng tôi sử dụng phương pháp ép đẳng nhiệt nóng sau khi chế tạo bộ phận như một quy trình thứ cấp. • IN BA MẬT ĐỘ: Cũng được ký hiệu là 3DP, trong kỹ thuật này, đầu in lắng đọng chất kết dính vô cơ lên một lớp bột phi kim loại hoặc bột kim loại. Một piston mang lớp bột được hạ xuống từng bước và ở mỗi bước, chất kết dính được lắng layer theo từng lớp và được hợp nhất bởi chất kết dính. Vật liệu bột được sử dụng là hỗn hợp polyme và sợi, cát đúc, kim loại. Sử dụng đồng thời các đầu chất kết dính khác nhau và các chất kết dính màu khác nhau, chúng ta có thể thu được nhiều màu sắc khác nhau. Quá trình này tương tự như in phun nhưng thay vì thu được một tờ màu, chúng ta thu được một vật thể ba chiều có màu. Các bộ phận được sản xuất có thể xốp và do đó có thể yêu cầu thiêu kết và thấm kim loại để tăng mật độ và độ bền của nó. Quá trình thiêu kết sẽ đốt cháy chất kết dính và hợp nhất các bột kim loại lại với nhau. Các kim loại như thép không gỉ, nhôm, titan có thể được sử dụng để chế tạo các bộ phận và làm vật liệu thấm chúng ta thường sử dụng đồng và đồng. Vẻ đẹp của kỹ thuật này là ngay cả những lắp ráp phức tạp và chuyển động cũng có thể được sản xuất rất nhanh chóng. Ví dụ, một cụm bánh răng, một cờ lê như một công cụ có thể được chế tạo và sẽ có các bộ phận chuyển động và quay sẵn sàng được sử dụng. Các thành phần khác nhau của bộ lắp ráp có thể được sản xuất với các màu sắc khác nhau và tất cả chỉ trong một lần chụp. Tải xuống tài liệu quảng cáo của chúng tôi trên:Khái niệm cơ bản về in 3D kim loại • SẢN XUẤT TRỰC TIẾP và CÔNG CỤ RAPID: Bên cạnh đánh giá thiết kế, xử lý sự cố, chúng tôi sử dụng tạo mẫu nhanh để sản xuất trực tiếp sản phẩm hoặc ứng dụng trực tiếp vào sản phẩm. Nói cách khác, tạo mẫu nhanh có thể được kết hợp vào các quy trình thông thường để làm cho chúng tốt hơn và cạnh tranh hơn. Ví dụ, tạo mẫu nhanh có thể tạo ra các mẫu và khuôn mẫu. Các mẫu polyme nóng chảy và cháy được tạo ra bằng các hoạt động tạo mẫu nhanh có thể được lắp ráp để đúc đầu tư và đầu tư. Một ví dụ khác cần đề cập là sử dụng 3DP để sản xuất vỏ đúc gốm và sử dụng nó cho các hoạt động đúc vỏ. Ngay cả khuôn ép và khuôn chèn có thể được sản xuất bằng cách tạo mẫu nhanh và người ta có thể tiết kiệm nhiều tuần hoặc nhiều tháng thời gian tạo khuôn. Bằng cách chỉ phân tích một tệp CAD của phần mong muốn, chúng tôi có thể tạo ra hình dạng công cụ bằng phần mềm. Dưới đây là một số phương pháp gia công nhanh phổ biến của chúng tôi: RTV (Lưu hóa nhiệt độ phòng) MOLDING / URETHANE CASTING: Sử dụng tạo mẫu nhanh có thể được sử dụng để tạo mẫu của bộ phận mong muốn. Sau đó, mẫu này được phủ một lớp chất phân tách và cao su RTV lỏng được đổ lên trên mẫu để tạo ra các nửa khuôn. Tiếp theo, những nửa khuôn này được sử dụng để ép uretan lỏng vào khuôn. Tuổi thọ khuôn ngắn, chỉ như 0 hoặc 30 chu kỳ nhưng đủ để sản xuất hàng loạt nhỏ. Khuôn đúc khuôn ACES (Acetal Clear Epoxy Solid): Sử dụng kỹ thuật tạo mẫu nhanh như kỹ thuật lập thể, chúng tôi sản xuất khuôn ép. Những khuôn này là những chiếc vỏ có một đầu mở để cho phép đổ đầy các vật liệu như nhựa epoxy, epoxy đầy nhôm hoặc kim loại. Một lần nữa, tuổi thọ khuôn được giới hạn ở hàng chục hoặc tối đa hàng trăm bộ phận. QUY TRÌNH GIA CÔNG KIM LOẠI PHUN: Chúng tôi sử dụng phương pháp tạo mẫu nhanh và tạo mẫu. Chúng tôi phun hợp kim nhôm kẽm lên bề mặt hoa văn và phủ lên trên. Mẫu với lớp phủ kim loại sau đó được đặt vào bên trong một bình và được phủ một lớp nhựa epoxy hoặc nhôm đầy nhựa. Cuối cùng, nó được lấy ra và bằng cách tạo ra hai nửa khuôn như vậy, chúng tôi có được một khuôn hoàn chỉnh để ép phun. Những khuôn này có tuổi thọ cao hơn, trong một số trường hợp, tùy thuộc vào vật liệu và nhiệt độ, chúng có thể sản xuất các bộ phận trong hàng nghìn. QUY TRÌNH KEELTOOL: Kỹ thuật này có thể sản xuất khuôn có vòng đời từ 100.000 đến 10 triệu chu kỳ. Sử dụng tạo mẫu nhanh, chúng tôi sản xuất khuôn RTV. Tiếp theo, khuôn được đổ đầy hỗn hợp bao gồm bột thép công cụ A6, cacbua vonfram, chất kết dính polyme và để đóng rắn. Khuôn này sau đó được làm nóng để làm cho polyme bị đốt cháy và bột kim loại để nung chảy. _cc781905-5cde-3194-bb3b-136bad5cf58d Bước tiếp theo là thấm đồng để tạo ra khuôn cuối cùng. Nếu cần, các hoạt động thứ cấp như gia công và đánh bóng có thể được thực hiện trên khuôn để có độ chính xác về kích thước tốt hơn. CLICK Product Finder-Locator Service TRANG TRƯỚC
- Glass and Ceramic Manufacturing, Hermetic Packages, Seals, Bonding
Glass and Ceramic Manufacturing, Hermetic Packages Seals and Bonding, Tempered Bulletproof Glass, Blow Moulding, Optical Grade Glass, Conductive Glass, Molding Tạo hình & định hình thủy tinh & gốm Loại sản xuất thủy tinh mà chúng tôi cung cấp là thủy tinh chứa, thổi thủy tinh, sợi thủy tinh & ống & que, thủy tinh gia dụng và công nghiệp, đèn và bóng đèn, đúc thủy tinh chính xác, các bộ phận và cụm quang học, kính phẳng & tấm & nổi. Chúng tôi thực hiện cả tạo hình bằng tay cũng như tạo hình bằng máy. Các quy trình sản xuất gốm kỹ thuật phổ biến của chúng tôi là ép khuôn, ép đẳng nhiệt, ép đẳng nhiệt nóng, ép nóng, đúc trượt, đúc băng, ép đùn, ép phun, gia công xanh, thiêu kết hoặc nung, mài kim cương, lắp ráp kín. Chúng tôi khuyên bạn nên nhấp vào đây để TẢI XUỐNG Hình minh họa Sơ đồ của chúng tôi về Quy trình Tạo hình và Tạo hình Thủy tinh của AGS-TECH Inc. TẢI XUỐNG Các Minh Họa Sơ Đồ Về Quy Trình Sản Xuất Gốm Kỹ Thuật Của AGS-TECH Inc. Các tệp có thể tải xuống này kèm theo ảnh và bản phác thảo sẽ giúp bạn hiểu rõ hơn về thông tin mà chúng tôi đang cung cấp cho bạn dưới đây. • SẢN XUẤT KÍNH CONTAINER: Chúng tôi có các dây chuyền ÉP VÀ THỔI tự động cũng như các dây chuyền THỔI VÀ THỔI để sản xuất. Trong quá trình thổi và thổi, chúng tôi thả một con gob vào khuôn trống và tạo thành cổ bằng cách thổi một luồng khí nén từ trên xuống. Ngay sau đó, khí nén được thổi lần thứ hai từ hướng khác qua cổ bình chứa để tạo thành dạng trước của chai. Sau đó, mẫu sơ bộ này được chuyển đến khuôn thực tế, được hâm nóng để làm mềm và khí nén được đưa vào để tạo ra hình dạng thùng chứa cuối cùng của mẫu sơ bộ. Nói một cách rõ ràng hơn, nó được điều áp và đẩy vào các thành của khoang khuôn thổi để có hình dạng mong muốn. Cuối cùng, hộp thủy tinh đã sản xuất được chuyển vào lò ủ để hâm nóng tiếp theo và loại bỏ các ứng suất sinh ra trong quá trình đúc và được làm mát theo cách có kiểm soát. Trong phương pháp ép và thổi, gob nóng chảy được đưa vào khuôn hình khuôn (khuôn trống) và được ép thành hình dạng khuôn (hình trống). Các khoảng trống sau đó được chuyển sang thổi khuôn và thổi tương tự như quy trình được mô tả ở trên trong “Quy trình thổi và thổi”. Các bước tiếp theo như ủ và xả stress tương tự hoặc giống nhau. • LÀM MÁT KÍNH: Chúng tôi đã và đang sản xuất các sản phẩm thủy tinh bằng cách thổi thủ công thông thường cũng như sử dụng khí nén với các thiết bị tự động. Đối với một số đơn hàng, việc thổi thông thường là cần thiết, chẳng hạn như các dự án liên quan đến tác phẩm nghệ thuật bằng kính, hoặc các dự án yêu cầu số lượng bộ phận nhỏ hơn với dung sai lỏng lẻo, dự án tạo mẫu / demo… .v.v. Thổi thủy tinh thông thường bao gồm việc nhúng một ống kim loại rỗng vào một nồi thủy tinh nóng chảy và xoay ống để thu thập một lượng vật liệu thủy tinh. Thủy tinh thu được trên đầu ống được cán trên sắt phẳng, tạo hình theo ý muốn, kéo dài, gia nhiệt lại và thổi khí. Khi đã sẵn sàng, nó được đưa vào khuôn và thổi không khí. Khoang khuôn bị ướt để tránh sự tiếp xúc của kính với kim loại. Màng nước đóng vai trò như một tấm đệm giữa chúng. Thổi thủ công là một quá trình chậm đòi hỏi nhiều lao động và chỉ thích hợp để tạo mẫu hoặc các mặt hàng có giá trị cao, không thích hợp cho các đơn hàng có khối lượng lớn và rẻ. • SẢN XUẤT KÍNH TRONG NƯỚC & CÔNG NGHIỆP: Sử dụng các loại vật liệu thuỷ tinh, nhiều loại thuỷ tinh đang được sản xuất. Một số loại thủy tinh có khả năng chịu nhiệt và phù hợp với đồ thủy tinh trong phòng thí nghiệm trong khi một số loại đủ tốt để chịu được máy rửa bát trong nhiều lần và phù hợp để sản xuất các sản phẩm trong nước. Sử dụng máy Westlake, hàng chục nghìn chiếc cốc uống nước đang được sản xuất mỗi ngày. Để đơn giản hóa, thủy tinh nóng chảy được thu thập bằng chân không và đưa vào khuôn để tạo ra các mẫu sẵn. Sau đó, không khí được thổi vào khuôn, chúng được chuyển sang khuôn khác và không khí được thổi lại và thủy tinh sẽ có hình dạng cuối cùng. Giống như thổi bằng tay, những khuôn này được giữ ướt bằng nước. Kéo dài thêm là một phần của hoạt động hoàn thiện nơi cổ đang được hình thành. Kính thừa bị cháy hết. Sau đó, quá trình làm nóng và làm mát lại có kiểm soát được mô tả ở trên như sau. • ỐNG KÍNH & ĐỊNH HÌNH ROD: Quy trình chính mà chúng tôi sử dụng để sản xuất ống thủy tinh là quy trình DANNER và VELLO. Trong Quy trình Danner, thủy tinh từ lò nung chảy và rơi xuống ống bọc nghiêng làm bằng vật liệu chịu lửa. Ống bọc được thực hiện trên một trục rỗng quay hoặc ống thổi. Sau đó, thủy tinh được quấn quanh ống bọc và tạo thành một lớp mịn chảy xuống ống bọc và trên đầu trục. Trong trường hợp tạo hình ống, không khí được thổi qua một ống thổi có đầu rỗng, và trong trường hợp tạo hình thanh, chúng tôi sử dụng các đầu đặc trên trục. Sau đó, các ống hoặc thanh được kéo qua các con lăn mang. Các kích thước như độ dày thành và đường kính của ống thủy tinh được điều chỉnh đến các giá trị mong muốn bằng cách đặt đường kính của ống bọc và thổi áp suất không khí đến một giá trị mong muốn, điều chỉnh nhiệt độ, tốc độ dòng chảy của thủy tinh và tốc độ vẽ. Mặt khác, quy trình sản xuất ống thủy tinh Vello liên quan đến thủy tinh đi ra khỏi lò và vào một cái bát có trục hoặc chuông rỗng. Sau đó, thủy tinh đi qua khoảng không khí giữa trục gá và bát và có hình dạng của một cái ống. Sau đó, nó di chuyển qua các con lăn đến máy vẽ và được làm nguội. Vào cuối của dây chuyền làm mát, quá trình cắt và xử lý cuối cùng diễn ra. Kích thước ống có thể được điều chỉnh giống như trong quy trình Danner. Khi so sánh quy trình Danner với Vello, chúng ta có thể nói rằng quy trình Vello phù hợp hơn để sản xuất số lượng lớn trong khi quy trình Danner có thể phù hợp hơn với các đơn đặt hàng ống thể tích nhỏ hơn chính xác . • GIA CÔNG TẤM & KÍNH CƯỜNG LỰC: Chúng tôi có số lượng lớn kính phẳng với các độ dày từ độ dày dưới mét đến vài cm. Kính phẳng của chúng tôi gần như hoàn hảo về mặt quang học. Chúng tôi cung cấp kính với các lớp phủ đặc biệt như lớp phủ quang học, trong đó kỹ thuật lắng đọng hơi hóa học được sử dụng để đặt các lớp phủ như chống phản xạ hoặc lớp phủ gương. Ngoài ra, các lớp phủ dẫn điện trong suốt cũng phổ biến. Ngoài ra còn có các lớp phủ kỵ nước hoặc ưa nước trên kính và lớp phủ giúp kính tự làm sạch. Kính cường lực, chống đạn và kính nhiều lớp là những mặt hàng phổ biến khác. Chúng tôi cắt kính thành hình dạng mong muốn với dung sai mong muốn. Các hoạt động phụ khác như làm cong hoặc uốn kính phẳng đều có sẵn. • KHUÔN KÍNH CHÍNH XÁC: Chúng tôi sử dụng kỹ thuật này chủ yếu để sản xuất các bộ phận quang học chính xác mà không cần đến các kỹ thuật tốn kém và tốn thời gian hơn như mài, mài và đánh bóng. Kỹ thuật này không phải lúc nào cũng đủ để tạo ra quang học tốt nhất, nhưng trong một số trường hợp như sản phẩm tiêu dùng, máy ảnh kỹ thuật số, quang học y tế, nó có thể là một lựa chọn tốt ít tốn kém hơn cho sản xuất số lượng lớn. Ngoài ra, nó có lợi thế hơn so với các kỹ thuật tạo hình thủy tinh khác khi yêu cầu hình học phức tạp, chẳng hạn như trong trường hợp hình cầu. Quy trình cơ bản liên quan đến việc nạp mặt dưới của khuôn của chúng tôi với trống kính, hút chân không của buồng xử lý để loại bỏ oxy, gần đóng khuôn, làm nóng nhanh và đẳng nhiệt của khuôn và thủy tinh với ánh sáng hồng ngoại, tiếp tục đóng các nửa khuôn để ép từ từ kính đã làm mềm theo cách có kiểm soát đến độ dày mong muốn, và cuối cùng là làm nguội kính và nạp nitơ vào khoang chứa và loại bỏ sản phẩm. Kiểm soát nhiệt độ chính xác, khoảng cách đóng khuôn, lực đóng khuôn, khớp với hệ số giãn nở của khuôn và vật liệu thủy tinh là chìa khóa trong quá trình này. • SẢN XUẤT CÁC LINH KIỆN VÀ LẮP RÁP QUANG KÍNH: Bên cạnh việc đúc thủy tinh chính xác, có một số quy trình có giá trị mà chúng tôi sử dụng để chế tạo các bộ phận và cụm quang học chất lượng cao cho các ứng dụng đòi hỏi khắt khe. Mài, mài và đánh bóng kính quang học bằng bùn mài mòn đặc biệt tốt là một nghệ thuật và khoa học để chế tạo thấu kính quang học, lăng kính, tấm phẳng và hơn thế nữa. Bề mặt phẳng, mịn, nhẵn và bề mặt quang học không có khuyết tật đòi hỏi nhiều kinh nghiệm với các quy trình như vậy. Những thay đổi nhỏ trong môi trường có thể dẫn đến các sản phẩm không đạt đặc điểm kỹ thuật và khiến dây chuyền sản xuất phải dừng lại. Có những trường hợp chỉ một lần lau trên bề mặt quang học bằng vải sạch có thể làm cho sản phẩm đáp ứng các thông số kỹ thuật hoặc không đạt yêu cầu trong thử nghiệm. Một số vật liệu thủy tinh phổ biến được sử dụng là silica nung chảy, thạch anh, BK7. Ngoài ra, việc lắp ráp các thành phần như vậy đòi hỏi kinh nghiệm chuyên ngành thích hợp. Đôi khi các loại keo đặc biệt đang được sử dụng. Tuy nhiên, đôi khi một kỹ thuật được gọi là tiếp xúc quang học là lựa chọn tốt nhất và không liên quan đến vật liệu giữa các kính quang học được gắn vào. Nó bao gồm các bề mặt phẳng tiếp xúc vật lý để gắn vào nhau mà không cần keo. Trong một số trường hợp, bộ đệm cơ khí, thanh thủy tinh chính xác hoặc quả bóng, kẹp hoặc các bộ phận kim loại đã được gia công đang được sử dụng để lắp ráp các bộ phận quang học ở những khoảng cách nhất định và với những định hướng hình học nhất định với nhau. Hãy để chúng tôi xem xét một số kỹ thuật phổ biến của chúng tôi để sản xuất quang học cao cấp. MÀI & LÁT & ĐÁNH BÓNG: Hình dạng thô của bộ phận quang học thu được khi mài một mẫu trống thủy tinh. Sau đó, việc phủ và đánh bóng được thực hiện bằng cách xoay và cọ xát bề mặt thô ráp của các bộ phận quang học với các dụng cụ có hình dạng bề mặt mong muốn. Bùn với các hạt mài mòn nhỏ và chất lỏng đang được đổ vào giữa quang học và các công cụ tạo hình. Kích thước hạt mài trong các loại bùn như vậy có thể được lựa chọn theo mức độ phẳng mong muốn. Độ lệch của các bề mặt quang học quan trọng so với các hình dạng mong muốn được biểu thị theo bước sóng của ánh sáng được sử dụng. Quang học chính xác cao của chúng tôi có dung sai bằng 1/10 bước sóng (Bước sóng / 10) hoặc thậm chí có thể chặt chẽ hơn. Bên cạnh hồ sơ bề mặt, các bề mặt quan trọng được quét và đánh giá các tính năng và khuyết tật bề mặt khác như kích thước, vết xước, phoi, rỗ, vết ... vv. Việc kiểm soát chặt chẽ các điều kiện môi trường trong tầng sản xuất quang học cũng như các yêu cầu đo lường và thử nghiệm rộng rãi với thiết bị hiện đại khiến đây trở thành một ngành đầy thách thức của ngành. • CÁC QUÁ TRÌNH THỨ HAI TRONG SẢN XUẤT KÍNH: Một lần nữa, chúng tôi chỉ giới hạn với trí tưởng tượng của bạn khi nói đến các quy trình thứ cấp và hoàn thiện của kính. Dưới đây chúng tôi liệt kê một số trong số chúng: - Lớp phủ trên thủy tinh (quang học, điện, tri giác, nhiệt, cơ năng, cơ học ...). Ví dụ, chúng ta có thể thay đổi các đặc tính bề mặt của kính, ví dụ như phản xạ nhiệt để giúp nội thất tòa nhà luôn mát mẻ hoặc làm cho một mặt hấp thụ tia hồng ngoại bằng công nghệ nano. Điều này giúp giữ ấm bên trong các tòa nhà vì lớp kính bề mặt ngoài cùng sẽ hấp thụ bức xạ hồng ngoại bên trong tòa nhà và bức xạ trở lại bên trong. -Etching on kính - Dán nhãn gốm được áp dụng (ACL) -Tranh điêu khắc - Đánh bóng bằng ngọn lửa - Đánh bóng hóa học - Còn SẢN XUẤT GỐM KỸ THUẬT • ÉP DIE: Bao gồm nén một trục của bột dạng hạt được giới hạn trong khuôn • ÉP NÓNG: Tương tự như ép khuôn nhưng có thêm nhiệt độ để tăng cường độ đông đặc. Bột hoặc phôi nén được đặt vào khuôn graphit và áp suất một trục được áp dụng trong khi khuôn được giữ ở nhiệt độ cao như 2000 C. Nhiệt độ có thể khác nhau tùy thuộc vào loại bột gốm được xử lý. Đối với các hình dạng và hình học phức tạp, có thể cần các quá trình xử lý tiếp theo khác như mài kim cương. • ÉP ISOSTATIC: Bột nén dạng hạt hoặc máy nén ép chết được đặt trong các thùng chứa kín khí và sau đó vào một bình áp suất kín có chất lỏng bên trong. Sau đó, chúng được nén chặt bằng cách tăng áp suất của bình áp suất. Chất lỏng bên trong bình truyền lực áp suất đồng đều trên toàn bộ diện tích bề mặt của bình chứa kín khí. Do đó, vật liệu được nén chặt đồng nhất và có hình dạng của hộp đựng linh hoạt cũng như cấu hình và tính năng bên trong của nó. • ÉP NÓNG ISOSTATIC: Tương tự như ép đẳng áp, nhưng ngoài khí quyển có áp suất, chúng tôi thiêu kết nén ở nhiệt độ cao. Quá trình ép đẳng áp nóng dẫn đến sự đông đặc hơn và tăng cường độ. • ĐÚC TRƯỢT / ĐÚC LÁT: Chúng tôi đổ đầy khuôn bằng huyền phù của các hạt gốm có kích thước micromet và chất lỏng mang. Hỗn hợp này được gọi là "trượt". Khuôn có các lỗ rỗng và do đó chất lỏng trong hỗn hợp được lọc vào khuôn. Kết quả là, một vật đúc được hình thành trên các bề mặt bên trong của khuôn. Sau khi thiêu kết, các bộ phận có thể được lấy ra khỏi khuôn. • ĐÚC BĂNG: Chúng tôi sản xuất băng gốm bằng cách đúc bùn gốm lên bề mặt vật mang chuyển động phẳng. Các loại bùn có chứa bột gốm trộn với các hóa chất khác cho các mục đích kết dính và mang theo. Khi dung môi bay hơi, các tấm gốm dày đặc và linh hoạt sẽ bị bỏ lại phía sau có thể được cắt hoặc cuộn theo ý muốn. • HÌNH THÀNH BÊN NGOÀI: Như trong các quy trình đùn khác, một hỗn hợp mềm của bột gốm với chất kết dính và các hóa chất khác được đưa qua khuôn để có được hình dạng mặt cắt ngang của nó và sau đó được cắt theo chiều dài mong muốn. Quá trình được thực hiện với hỗn hợp gốm lạnh hoặc nung nóng. • KHUÔN THUỐC ÉP ÁP LỰC THẤP: Chúng tôi chuẩn bị một hỗn hợp bột sứ với chất kết dính và dung môi rồi nung đến nhiệt độ có thể dễ dàng ép và ép vào khoang dụng cụ. Khi chu trình đúc hoàn tất, bộ phận được đẩy ra và hóa chất liên kết bị đốt cháy. Sử dụng ép phun, chúng tôi có thể có được các bộ phận phức tạp với khối lượng lớn một cách kinh tế. Có thể có các lỗ đó là một phần nhỏ của milimet trên bức tường dày 10mm, có thể có ren mà không cần gia công thêm, dung sai càng chặt càng tốt +/- 0,5% và thậm chí còn thấp hơn khi các bộ phận được gia công , có thể có độ dày của tường theo thứ tự từ 0,5mm đến chiều dài 12,5 mm cũng như độ dày của tường từ 6,5mm đến chiều dài 150mm. • GIA CÔNG XANH: Sử dụng các công cụ gia công kim loại tương tự, chúng tôi có thể ép vật liệu gốm bằng máy mà chúng vẫn mềm như phấn. Có thể có dung sai +/- 1%. Để có dung sai tốt hơn, chúng tôi sử dụng phương pháp mài kim cương. • SINTERING hoặc FIRING: Quá trình thiêu kết có thể tạo ra sự đông đặc hoàn toàn. Sự co ngót đáng kể xảy ra trên các bộ phận nhỏ gọn màu xanh lá cây, nhưng đây không phải là vấn đề lớn vì chúng tôi tính đến những thay đổi kích thước này khi chúng tôi thiết kế bộ phận và dụng cụ. Các hạt bột được liên kết với nhau và độ xốp do quá trình đầm nén được loại bỏ ở mức độ lớn .. • MÀI KIM CƯƠNG: Vật liệu cứng nhất thế giới "kim cương" đang được sử dụng để mài các vật liệu cứng như gốm sứ và thu được các bộ phận chính xác. Đang đạt được dung sai trong phạm vi micromet và bề mặt rất nhẵn. Do chi phí của nó, chúng tôi chỉ xem xét kỹ thuật này khi chúng tôi thực sự cần nó. • LẮP RÁP HERMETIC là những loại mà nói một cách thực tế là không cho phép bất kỳ sự trao đổi vật chất, chất rắn, chất lỏng hoặc chất khí nào giữa các mặt phân cách. Gioăng kín kín gió. Ví dụ, các thùng điện tử kín là những thùng giữ cho các vật dụng bên trong nhạy cảm của một thiết bị được đóng gói không bị ảnh hưởng bởi độ ẩm, chất gây ô nhiễm hoặc khí. Không có gì là kín 100%, nhưng khi chúng ta nói về độ kín, chúng ta có nghĩa là về mặt thực tế, có độ kín đến mức tỷ lệ rò rỉ thấp đến mức các thiết bị an toàn trong điều kiện môi trường bình thường trong thời gian rất dài. Các tổ hợp kín của chúng tôi bao gồm các thành phần kim loại, thủy tinh và gốm, kim loại-gốm, gốm-kim loại-gốm, kim loại-gốm-kim loại, kim loại đến kim loại, kim loại-thủy tinh, kim loại-thủy tinh-kim loại, thủy tinh-kim loại-thủy tinh, thủy tinh- kim loại và thủy tinh đến thủy tinh và tất cả các kết hợp khác của liên kết kim loại-thủy tinh-gốm. Ví dụ, chúng ta có thể phủ kim loại lên các thành phần gốm để chúng có thể được liên kết chặt chẽ với các thành phần khác trong bộ phận lắp ráp và có khả năng bịt kín tuyệt vời. Chúng tôi có bí quyết về cách phủ các sợi quang học hoặc ống dẫn bằng kim loại và hàn hoặc hàn chúng vào thùng loa, để không có khí đi qua hoặc rò rỉ vào thùng loa. Do đó chúng được sử dụng để sản xuất vỏ điện tử để bao bọc các thiết bị nhạy cảm và bảo vệ chúng khỏi môi trường bên ngoài. Bên cạnh các đặc tính làm kín tuyệt vời của chúng, các đặc tính khác như hệ số giãn nở nhiệt, khả năng chống biến dạng, bản chất không thoát ra ngoài, tuổi thọ rất cao, bản chất không dẫn điện, đặc tính cách nhiệt, tính chất chống tĩnh điện ... vv. làm cho vật liệu thủy tinh và gốm trở thành sự lựa chọn cho các ứng dụng nhất định. Thông tin về cơ sở của chúng tôi sản xuất phụ kiện từ gốm đến kim loại, niêm phong kín, chân không cấp liệu, chân không cao và siêu cao và các thành phần kiểm soát chất lỏng có thể được tìm thấy tại đây:Sách giới thiệu về nhà máy sản xuất linh kiện Hermetic CLICK Product Finder-Locator Service TRANG TRƯỚC
- Wire & Spring Forming, Shaping, Welding, Assembly of Wires, Coil, CNC
Wire & Spring Forming, Shaping, Welding, Assembly of Wires, Coil Compression Extension Torsion Flat Springs, Custom Wires, Helical Springs at AGS-TECH Inc. Hình thành dây & lò xo Chúng tôi sản xuất dây tùy chỉnh, dây lắp ráp, dây được tạo thành các hình dạng 2D và 3D mong muốn, lưới thép, lưới, thùng, giỏ, hàng rào, dây lò xo, lò xo phẳng; xoắn, nén, căng, lò xo phẳng và hơn thế nữa. Các quy trình của chúng tôi là tạo dây và lò xo, kéo dây, định hình, uốn, hàn, hàn, hàn, xuyên, uốn, khoan, vát mép, mài, ren, phủ, bốn tấm, tạo hình trượt, cuộn, cuộn, đảo trộn. Chúng tôi khuyên bạn nên nhấp vào đây để TẢI XUỐNG Hình ảnh minh họa sơ đồ của chúng tôi về các quy trình hình thành dây và lò xo của AGS-TECH Inc. Tệp có thể tải xuống này kèm theo ảnh và bản phác thảo sẽ giúp bạn hiểu rõ hơn về thông tin mà chúng tôi đang cung cấp cho bạn dưới đây. • VẼ DÂY: Sử dụng lực kéo, chúng tôi kéo căng cổ phiếu kim loại và kéo nó qua một khuôn để giảm đường kính và tăng chiều dài của nó. Đôi khi chúng tôi sử dụng một loạt các khuôn. Chúng tôi có khả năng chế tạo khuôn cho mọi khổ dây. Sử dụng vật liệu có độ bền kéo cao, chúng tôi kéo dây rất mỏng. Chúng tôi cung cấp cả dây làm việc nguội và nóng. • ĐỊNH HÌNH DÂY: Một cuộn dây đo được uốn cong và tạo hình thành một sản phẩm hữu ích. Chúng tôi có khả năng tạo dây từ tất cả các đồng hồ đo, bao gồm cả dây mảnh cũng như dây dày như dây được sử dụng làm lò xo dưới khung ô tô. Thiết bị chúng tôi sử dụng để tạo hình dây là máy ép dây thủ công và CNC, lò hơi, máy ép điện, tấm trượt bốn chiều, tấm trượt đa năng. Các quy trình của chúng tôi là vẽ, uốn, nắn, làm phẳng, kéo dài, cắt, làm phẳng, hàn & hàn & hàn, lắp ráp, cuộn, uốn (hoặc uốn), xuyên, luồn dây, khoan, vát mép, mài, sơn phủ và xử lý bề mặt. Thiết bị hiện đại của chúng tôi có thể được thiết lập để phát triển các thiết kế rất phức tạp với bất kỳ hình dạng nào và dung sai chặt chẽ. Chúng tôi cung cấp nhiều loại đầu cuối khác nhau like đầu hình cầu, đầu nhọn hoặc đầu vát cho dây của bạn. Hầu hết các dự án tạo hình dây của chúng tôi có chi phí dụng cụ tối thiểu đến 0. Thời gian quay vòng mẫu thường là ngày. Các thay đổi đối với thiết kế / cấu hình của các dạng dây có thể được thực hiện rất nhanh chóng. • SPRING FORMING: AGS-TECH sản xuất nhiều loại lò xo bao gồm: -Torsion / Double Torsion Spring -Tension / Compression Spring -Constant / Variable Spring -Conil & Helical Spring -Flat & Leaf Spring - Mùa xuân cân bằng -Máy giặt Belleville -Negator Spring - Mùa xuân cuộn dây tốc độ tiến bộ -Sóng mùa xuân -Volute Spring -Tapered Springs - Nhẫn dây -Khóa lò xo -Phim Chúng tôi sản xuất lò xo từ nhiều loại vật liệu khác nhau và có thể hướng dẫn bạn theo ứng dụng của bạn. Các vật liệu phổ biến nhất là thép không gỉ, crôm silicon, thép cacbon cao, cacbon thấp được tôi luyện trong dầu, crôm vanadi, đồng phốt pho, titan, hợp kim đồng berili, gốm nhiệt độ cao. Chúng tôi sử dụng các kỹ thuật khác nhau trong sản xuất lò xo, bao gồm cuộn CNC, cuộn nguội, cuộn nóng, làm cứng, hoàn thiện. Các kỹ thuật khác đã được đề cập ở trên trong quá trình tạo hình dây cũng rất phổ biến trong các hoạt động sản xuất lò xo của chúng tôi. • DỊCH VỤ HOÀN THIỆN DÂY & XUÂN: Chúng tôi có thể hoàn thiện sản phẩm của bạn theo nhiều cách tùy theo sự lựa chọn và nhu cầu của bạn. Một số quy trình phổ biến mà chúng tôi cung cấp là: sơn, sơn tĩnh điện, mạ, nhúng vinyl, anodizing, giảm căng thẳng, xử lý nhiệt, bắn peen, nhào lộn, cromat, electroless niken, thụ động hóa, men nung, áo nhựa , làm sạch plasma. CLICK Product Finder-Locator Service TRANG TRƯỚC
- Sheet Metal Forming Fabrication, Stamping, Punching, Deep Drawing, CNC
Sheet Metal Forming and Fabrication, Stamping, Punching, Bending, Progressive Die, Spot Welding, Deep Drawing, Metal Blanking and Slitting at AGS-TECH Inc. Dập & Chế tạo kim loại tấm Chúng tôi cung cấp dịch vụ dập kim loại tấm, tạo hình, tạo hình, uốn, đục lỗ, đục lỗ, rạch, đục lỗ, khía, mài, cạo, gia công ép, chế tạo, vẽ sâu bằng cách sử dụng khuôn dập một lần / khuôn một nét cũng như khuôn dập và kéo sợi liên tục, tạo hình cao su và tạo hình thuỷ tức; cắt kim loại tấm bằng tia nước, plasma, laser, cưa, ngọn lửa; lắp ráp kim loại tấm sử dụng hàn, hàn điểm; ống kim loại tấm phồng và uốn cong; hoàn thiện bề mặt kim loại tấm bao gồm sơn nhúng hoặc phun, sơn tĩnh điện, anot hóa, mạ, phún xạ và hơn thế nữa. Các dịch vụ của chúng tôi bao gồm từ tạo mẫu kim loại tấm nhanh chóng đến sản xuất khối lượng lớn. Chúng tôi khuyên bạn nên nhấp vào đây đểTẢI XUỐNG Các Minh Họa Sơ Đồ Về Quy Trình Dập và Chế Tạo Kim Loại Tấm của AGS-TECH Inc. Điều này sẽ giúp bạn hiểu rõ hơn về những thông tin mà chúng tôi đang cung cấp cho bạn dưới đây. • MẶT CẮT KIM LOẠI TẤM: Chúng tôi cung cấp CẮT MÓC và MẶT BẰNG PHẦN. Các vết cắt cắt kim loại tấm trên một đường dẫn tại một thời điểm và về cơ bản không gây lãng phí vật liệu, trong khi với các đường cắt, hình dạng không thể được lồng vào nhau một cách chính xác và do đó một số lượng vật liệu nhất định bị lãng phí. Một trong những quy trình phổ biến nhất của chúng tôi là PUNCHING, nơi một mảnh vật liệu hình tròn hoặc hình dạng khác được cắt ra từ tấm kim loại. Phần bị cắt ra là chất thải. Một phiên bản khác của đột lỗ là SLOTTING, trong đó các lỗ hình chữ nhật hoặc hình dài được đục. Mặt khác, BLANKING là quá trình tương tự như đột dập, với sự phân biệt của mảnh được cắt ra là tác phẩm và được giữ lại. FINE BLANKING, một phiên bản cao cấp của phương pháp gia công, tạo ra các vết cắt với dung sai gần và các cạnh thẳng mịn và không yêu cầu các thao tác thứ cấp để hoàn thiện phôi. Một quy trình khác mà chúng tôi thường sử dụng là SLITTING, là quy trình cắt kim loại tấm được cắt bằng hai lưỡi dao tròn đối diện nhau theo đường thẳng hoặc đường cong. Dụng cụ mở hộp là một ví dụ đơn giản của quá trình rạch. Một quy trình phổ biến khác process cho chúng tôi là PERFORATING, trong đó nhiều lỗ hình tròn hoặc hình dạng khác được đục trên kim loại tấm theo một mẫu nhất định. Ví dụ điển hình cho sản phẩm đục lỗ là bộ lọc kim loại có nhiều lỗ cho chất lỏng. Trong NOTCHING, một quy trình cắt kim loại tấm khác, chúng tôi loại bỏ vật liệu khỏi một chi tiết gia công, bắt đầu từ cạnh hoặc nơi khác và cắt vào trong cho đến khi có được hình dạng mong muốn. Đó là một quá trình tiến triển trong đó mỗi thao tác loại bỏ một mảnh khác cho đến khi có được đường viền mong muốn. Đối với các hoạt động sản xuất nhỏ, đôi khi chúng tôi sử dụng một quy trình tương đối chậm hơn được gọi là NIBBLING bao gồm nhiều lỗ đục nhanh các lỗ chồng lên nhau để tạo ra một đường cắt lớn hơn và phức tạp hơn. Trong CẮT TIẾN BỘ, chúng tôi sử dụng một loạt các phép toán khác nhau để có được một hình cắt hoặc một hình học nhất định. Cuối cùng, LƯU một quy trình thứ cấp giúp chúng tôi cải thiện các cạnh của vết cắt đã được thực hiện. Nó được sử dụng để cắt các phoi, các cạnh thô trên gia công kim loại tấm. • UỐN KIM LOẠI TẤM: Bên cạnh việc cắt, uốn là một quá trình thiết yếu mà nếu không có chúng tôi sẽ không thể sản xuất hầu hết các sản phẩm. Chủ yếu là hoạt động làm việc lạnh nhưng đôi khi cũng được thực hiện khi ấm hoặc nóng. Chúng tôi sử dụng khuôn và nhấn hầu hết thời gian cho hoạt động này. Trong UỐN TIẾN BỘ, chúng tôi sử dụng một loạt các thao tác đột dập khác nhau để có được một lần uốn cong hoặc một dạng hình học nhất định. AGS-TECH sử dụng nhiều quy trình uốn và lựa chọn tùy thuộc vào vật liệu phôi, kích thước, độ dày, kích thước uốn cong mong muốn, bán kính, độ cong và góc uốn, vị trí uốn, tính kinh tế của hoạt động, số lượng được sản xuất… vân vân. Chúng tôi sử dụng V-BENDING trong đó một cú đấm hình chữ V ép tấm kim loại vào khuôn hình chữ V và uốn cong nó. Tốt cho cả góc rất nhọn và góc tù và ở giữa, bao gồm cả 90 độ. Sử dụng khuôn lau, chúng tôi thực hiện UỐN CẠNH. Thiết bị của chúng tôi cho phép chúng tôi có được các góc thậm chí lớn hơn 90 độ. Khi uốn mép, phôi được kẹp giữa một miếng đệm áp lực và khuôn, khu vực để uốn nằm trên mép khuôn và phần còn lại của phôi được giữ trên space giống như một dầm đúc hẫng. Khi cú đấm tác động lên phần công xôn, nó sẽ bị uốn cong trên mép của khuôn. FLANGING là một quá trình uốn cạnh tạo ra một góc 90 độ. Mục tiêu chính của hoạt động là loại bỏ các cạnh sắc và có được các bề mặt hình học để dễ dàng ghép các bộ phận. BEADING, một quy trình uốn cạnh phổ biến khác tạo thành một đường cong trên cạnh của một bộ phận. Mặt khác, HEMMING dẫn đến một cạnh của tờ giấy bị uốn cong hoàn toàn trên chính nó. Trong SEAMING, các cạnh của hai phần được uốn cong lên nhau và nối lại. Mặt khác, DOUBLE SEAMING cung cấp các mối nối tấm kim loại kín nước và kín hơi. Tương tự như uốn cạnh, một quy trình được gọi là UỐN XOAY triển khai một hình trụ với góc cắt mong muốn và đóng vai trò như một cú đấm. Khi lực được truyền đến cú đấm, nó sẽ đóng lại với phôi. Rãnh của hình trụ tạo cho phần công xôn một góc mong muốn. Rãnh có thể có góc nhỏ hơn hoặc lớn hơn 90 độ. Trong MÁY UỐN KHÔNG KHÍ, chúng ta không cần khuôn dưới có rãnh góc cạnh. Tấm kim loại được hỗ trợ bởi two bề mặt ở các mặt đối diện và ở một khoảng cách nhất định. Sau đó, cú đấm sẽ tác dụng một lực vào đúng vị trí và làm cong phôi. UỐN KÊNH được thực hiện bằng cách sử dụng một cú đấm và khuôn hình kênh và U-BEND đạt được bằng một cú đấm hình chữ U. UỐN CẮT TẮT tạo ra các khoảng lệch trên tấm kim loại. UỐN ROLL, một kỹ thuật tốt cho công việc dày và uốn các tấm kim loại lớn, sử dụng ba cuộn để nạp và uốn các tấm theo độ cong mong muốn. Các cuộn được sắp xếp để có được độ uốn mong muốn của tác phẩm. Khoảng cách và góc giữa các cuộn được kiểm soát để có được kết quả mong muốn. Một cuộn có thể di chuyển giúp bạn có thể kiểm soát độ cong. ĐỊNH HÌNH ỐNG là một hoạt động uốn kim loại tấm phổ biến khác liên quan đến nhiều khuôn. Các ống thu được sau nhiều lần thực hiện. LỖI cũng được thực hiện bằng các hoạt động uốn cong. Về cơ bản, nó là sự uốn cong đối xứng trong những khoảng thời gian đều đặn trên toàn bộ một tấm kim loại. Nhiều hình dạng khác nhau có thể được sử dụng để uốn nếp. Tấm kim loại dạng sóng cứng hơn và có khả năng chống uốn tốt hơn do đó có ứng dụng trong ngành xây dựng. Quá trình sản xuất TẤM KIM LOẠI, một quy trình sản xuất liên tục được triển khai để uốn các mặt cắt ngang của một hình dạng nhất định bằng cách sử dụng các cuộn và công việc được uốn theo các bước tuần tự, với cuộn cuối cùng hoàn thành công việc. Trong một số trường hợp, một cuộn duy nhất và trong một số trường hợp, một loạt các cuộn được sử dụng. • QUÁ TRÌNH CẮT & UỐN KIM LOẠI TẤM LIÊN HỢP: Đây là những quá trình cắt và uốn cùng một lúc. Trong PIERCING, một lỗ được tạo ra bằng cách sử dụng một cú đấm nhọn. Khi đục lỗ rộng trên tấm, vật liệu được uốn đồng thời thành một mặt bích bên trong cho lỗ. Mặt bích thu được có thể có các chức năng quan trọng. Mặt khác, hoạt động LANCING sẽ cắt và uốn cong trang tính để tạo ra một hình học nhô cao. • NỐI VÀ UỐN ỐNG KIM LOẠI: Khi NUÔI một số phần bên trong của một ống rỗng bị áp lực, làm cho ống phồng ra bên ngoài. Vì ống nằm bên trong khuôn, nên hình dạng khối phồng được kiểm soát bởi hình dạng của khuôn. Trong STRETCH BENDING, một ống kim loại được kéo căng bằng cách sử dụng các lực song song với trục của ống và lực uốn để kéo ống qua một khối dạng. Trong VẼ B UỐN, chúng tôi kẹp ống gần đầu của nó vào một khối dạng xoay để uốn ống trong khi quay. Cuối cùng, trong UỐN NÉN, ống được giữ bằng lực vào một khối dạng cố định và một khuôn uốn cong nó trên khối dạng. • VẼ SÂU: Trong một trong những hoạt động phổ biến nhất của chúng tôi, một cú đấm, một khuôn phù hợp và một giá đỡ trống được sử dụng. Tấm kim loại trống được đặt trên lỗ mở khuôn và cú đấm di chuyển về phía trống được giữ bởi người giữ trống. Khi chúng tiếp xúc với nhau, cú đấm sẽ ép tấm kim loại vào khoang khuôn để tạo thành sản phẩm. Thao tác vẽ sâu tương tự như thao tác cắt, tuy nhiên khoảng hở giữa đột và khuôn ngăn không cho cắt tấm. Một yếu tố khác đảm bảo tấm được kéo sâu và không bị cắt là các góc tròn trên khuôn và đột dập giúp ngăn cản việc cắt và cắt. Để đạt được mức độ lớn hơn của bản vẽ sâu, quy trình RÚT ĐỎ đang được triển khai trong đó một bản vẽ sâu tiếp theo diễn ra trên một bộ phận đã trải qua quá trình vẽ sâu. Trong REVERSE REDRAWING, phần vẽ sâu được lật lại và vẽ theo hướng ngược lại. Vẽ sâu có thể cung cấp các vật thể có hình dạng bất thường như hình vòm, hình côn hoặc ly bậc, Trong EMBOSSING, chúng tôi sử dụng một cặp khuôn nam và nữ để tạo ấn tượng cho tấm kim loại bằng thiết kế hoặc chữ viết. • SPINNING: Một hoạt động trong đó phôi phẳng hoặc phôi được tạo hình sẵn được giữ giữa trục quay và cổ trục và một công cụ tác dụng áp lực cục bộ lên nguyên công khi nó dần dần di chuyển lên trên trục gá. Kết quả là, phôi được bọc qua trục gá và có hình dạng. Chúng tôi sử dụng kỹ thuật này để thay thế cho việc vẽ sâu khi số lượng đơn đặt hàng ít, các bộ phận lớn (đường kính lên đến 20 feet) và có các đường cong độc đáo. Mặc dù giá mỗi mảnh nhìn chung cao hơn, nhưng chi phí thiết lập cho hoạt động kéo sợi CNC thấp so với kéo sâu. Ngược lại, bản vẽ sâu đòi hỏi đầu tư ban đầu cao cho việc thiết lập, nhưng chi phí trên mỗi mảnh sẽ thấp khi sản xuất số lượng lớn các bộ phận. Một phiên bản khác của quá trình này là KHẮC PHỤC, nơi cũng có dòng chảy kim loại bên trong phôi. Dòng chảy kim loại sẽ làm giảm độ dày của phôi khi quá trình này được thực hiện. Tuy nhiên, một quy trình liên quan khác là NỐI ỐNG, được áp dụng trên các bộ phận hình trụ. Cũng trong quá trình này có dòng chảy kim loại bên trong phôi. Do đó, độ dày được giảm xuống và chiều dài của ống được tăng lên. Công cụ có thể được di chuyển để tạo các tính năng ở bên trong hoặc bên ngoài ống. • CAO SU HÌNH THÀNH KIM LOẠI TẤM: Vật liệu cao su hoặc polyurethane được cho vào khuôn chứa và chi tiết gia công được đặt trên bề mặt của cao su. Một cú đấm sau đó được tác động lên phần gia công và ép nó vào cao su. Vì áp suất tạo ra bởi cao su thấp, độ sâu của các bộ phận được tạo ra bị hạn chế. Vì chi phí dụng cụ thấp nên quy trình này phù hợp với sản xuất số lượng ít. • THỦY LỰC: Tương tự như quá trình tạo hình cao su, trong quy trình này, kim loại tấm được ép bằng một cú đấm vào chất lỏng có áp suất bên trong buồng. Sản phẩm kim loại tấm được kẹp giữa quả đấm và màng chắn cao su. Màng chắn bao quanh phôi hoàn toàn và áp suất của chất lỏng buộc nó phải hình thành trên cú đấm. Các bản vẽ rất sâu thậm chí còn sâu hơn trong quá trình vẽ sâu bằng kỹ thuật này. Chúng tôi sản xuất khuôn dập một lỗ cũng như khuôn dập lỗ tùy thuộc vào bộ phận của bạn. Khuôn dập một lần là một phương pháp hiệu quả về chi phí để sản xuất số lượng lớn các bộ phận kim loại tấm đơn giản như vòng đệm một cách nhanh chóng. Khuôn dập tiến bộ hoặc kỹ thuật vẽ sâu được sử dụng để sản xuất các hình học phức tạp hơn. Tùy thuộc vào trường hợp của bạn, cắt tia nước, laser hoặc plasma có thể được sử dụng để sản xuất các bộ phận kim loại tấm của bạn với chi phí thấp, nhanh chóng và chính xác. Nhiều nhà cung cấp không có ý tưởng về các kỹ thuật thay thế này hoặc không có nó và do đó họ làm theo các cách chế tạo khuôn và các công cụ tốn kém và dài dòng chỉ khiến khách hàng lãng phí thời gian và tiền bạc. Nếu bạn yêu cầu các thành phần kim loại tấm được chế tạo tùy chỉnh như thùng máy, vỏ điện tử ... vv nhanh nhất trong ngày, thì hãy liên hệ với chúng tôi để được cung cấp dịch vụ GIA CÔNG KIM LOẠI RAPID SHEET. CLICK Product Finder-Locator Service MENU TRƯỚC
- Forging and Powdered Metallurgy, Die Forging, Heading, Hot Forging
Forging and Powdered Metallurgy, Die Forging, Heading, Hot Forging, Impression Die, Near Net Shape, Swaging, Metal Hobbing, Riveting, Coining from AGS-TECH Inc. Rèn kim loại & luyện kim bột Loại quy trình QUÊN KIM LOẠI mà chúng tôi cung cấp là khuôn dập nóng và nguội, khuôn bế và khuôn bế, khuôn dập và rèn không chớp, cogging, rèn hoàn thiện, viền và rèn chính xác, hình gần như lưới, tiêu đề , uốn, rèn khó chịu, lắc kim loại, nhấn & cuộn & xuyên tâm & quỹ đạo & vòng & rèn đẳng nhiệt, rèn, tán đinh, rèn bóng kim loại, xuyên kim loại, định cỡ, rèn tốc độ năng lượng cao. Kỹ thuật BỘT VÀ CHẾ BIẾN BỘT của chúng tôi là ép và thiêu kết bột, ngâm tẩm, thấm, ép đẳng nhiệt nóng và lạnh, ép kim loại, nén cuộn, cán bột, đùn bột, thiêu kết lỏng, thiêu kết bằng tia lửa, ép nóng. Chúng tôi khuyên bạn nên nhấp vào đây để TẢI XUỐNG Hình minh họa sơ đồ về quy trình rèn của AGS-TECH Inc. TẢI XUỐNG Hình minh họa sơ đồ về các quy trình luyện kim bột của AGS-TECH Inc. Các tệp có thể tải xuống này kèm theo ảnh và bản phác thảo sẽ giúp bạn hiểu rõ hơn về thông tin mà chúng tôi đang cung cấp cho bạn dưới đây. Trong rèn kim loại, lực nén được áp dụng và vật liệu bị biến dạng và thu được hình dạng mong muốn. Các vật liệu rèn phổ biến nhất trong công nghiệp là sắt và thép, nhưng nhiều vật liệu khác như nhôm, đồng, titan, magiê cũng được rèn rộng rãi. Các bộ phận kim loại rèn có cấu trúc hạt được cải thiện ngoài các vết nứt kín và không gian trống đóng, do đó độ bền của các bộ phận thu được bằng quá trình này cao hơn. Rèn tạo ra các bộ phận siged đáng kể về trọng lượng của chúng so với các bộ phận được làm bằng cách đúc hoặc gia công. Vì các bộ phận rèn được tạo hình bằng cách làm cho kim loại chảy thành hình dạng cuối cùng của nó, nên kim loại có cấu trúc hạt định hướng nên độ bền vượt trội của các bộ phận. Nói cách khác, các bộ phận thu được bằng quá trình rèn bộc lộ các tính chất cơ học tốt hơn so với các bộ phận được đúc hoặc gia công đơn giản. Trọng lượng của vật rèn kim loại có thể từ các bộ phận nhỏ nhẹ đến hàng trăm nghìn pound. Chúng tôi sản xuất đồ rèn hầu hết cho các ứng dụng đòi hỏi cơ học, nơi ứng suất cao được áp dụng trên các bộ phận như bộ phận ô tô, bánh răng, công cụ lao động, dụng cụ cầm tay, trục tuabin, bánh xe máy. Vì chi phí thiết lập và dụng cụ tương đối cao, chúng tôi khuyến nghị quy trình sản xuất này chỉ dành cho sản xuất khối lượng lớn và cho các bộ phận quan trọng có khối lượng thấp nhưng có giá trị cao như thiết bị hạ cánh hàng không vũ trụ. Bên cạnh chi phí gia công, thời gian sản xuất đối với các bộ phận rèn số lượng lớn có thể lâu hơn so với một số bộ phận được gia công đơn giản, nhưng kỹ thuật là rất quan trọng đối với các bộ phận ốc vít, phụ tùng ô tô, xe nâng, cầu trục. • NÓNG DIE và LẠNH DIE FORGING: Rèn khuôn nóng, như tên gọi của nó, được thực hiện ở nhiệt độ cao, do đó độ dẻo cao và độ bền của vật liệu thấp. Điều này tạo điều kiện cho việc biến dạng và rèn dễ dàng. Ngược lại, rèn khuôn nguội được thực hiện ở nhiệt độ thấp hơn và yêu cầu lực cao hơn dẫn đến độ cứng biến dạng, độ hoàn thiện bề mặt tốt hơn và độ chính xác của các bộ phận được sản xuất . • MỞ DIE và ẤN TƯỢNG DIE QUÊN: Trong quá trình rèn khuôn hở, khuôn dập không hạn chế vật liệu bị nén, trong khi khuôn dập ấn tượng rèn các lỗ trong khuôn hạn chế dòng chảy của vật liệu trong khi nó được rèn thành hình dạng mong muốn. UPSET FORGING hay còn được gọi là UPSETTING, thực ra không giống nhau mà là một quy trình rất giống nhau, là một quy trình khuôn mở trong đó chi tiết gia công được kẹp giữa hai khuôn phẳng và một lực nén làm giảm chiều cao của nó. Khi chiều cao is red giảm xuống, chiều rộng phần gia công tăng lên. HEADING, một quá trình rèn khó khăn liên quan đến cổ phiếu hình trụ bị đảo lộn ở cuối và tiết diện của nó được tăng lên cục bộ. Trong tiêu đề, cổ phiếu được đưa qua khuôn, rèn và sau đó cắt theo chiều dài. Hoạt động này có khả năng tạo ra số lượng ốc vít nhanh chóng. Chủ yếu là hoạt động gia công nguội vì nó được sử dụng để làm đầu đinh, đầu vít, đai ốc và bu lông ở những nơi vật liệu cần được tăng cường. Một quy trình khuôn mở khác là COGGING, trong đó chi tiết gia công được rèn theo một loạt các bước với mỗi bước dẫn đến việc nén vật liệu và chuyển động tiếp theo của khuôn mở dọc theo chiều dài của chi tiết gia công. Ở mỗi bước, độ dày được giảm đi và chiều dài được tăng lên một lượng nhỏ. Quá trình này giống như một học sinh lo lắng cắn bút chì của mình theo từng bước nhỏ. Quy trình được gọi là FULLERING là một phương pháp rèn khuôn hở khác mà chúng tôi thường triển khai như một bước trước đó để phân phối vật liệu trong chi tiết gia công trước khi các hoạt động rèn kim loại khác diễn ra. Chúng tôi sử dụng nó khi công việc yêu cầu vài rèn operations. Trong quá trình vận hành, khuôn có bề mặt lồi lõm biến dạng và gây chảy kim loại ra hai bên. Mặt khác, một quy trình tương tự như làm đầy, EDGING liên quan đến khuôn mở với các bề mặt lõm để làm biến dạng chi tiết gia công. Viền cũng là một quá trình chuẩn bị cho các hoạt động rèn tiếp theo làm cho vật liệu chảy từ cả hai phía vào một khu vực ở trung tâm. IMPRESSION DIE FORGING hoặc CLOSED DIE FORGING vì nó còn được gọi là khuôn ép / khuôn nén vật liệu và hạn chế dòng chảy của nó trong chính nó. Khuôn đóng lại và vật liệu có hình dạng của khuôn / khoang khuôn. QUÊN CHÍNH XÁC, một quy trình đòi hỏi thiết bị và khuôn đặc biệt, tạo ra các bộ phận không có hoặc có rất ít chớp cháy. Nói cách khác, các bộ phận sẽ có kích thước gần như cuối cùng. Trong quá trình này, một lượng vật liệu được kiểm soát tốt sẽ được đưa vào và định vị cẩn thận bên trong khuôn. Chúng tôi triển khai phương pháp này cho các hình dạng phức tạp với mặt cắt mỏng, dung sai nhỏ và góc kéo và khi số lượng đủ lớn để phù hợp với chi phí khuôn và thiết bị. • QUÊN LỖ CHÂN LÔNG: Phôi được đặt vào khuôn sao cho không vật liệu nào có thể chảy ra khỏi khoang để tạo thành chớp. Do đó, không cần cắt bớt đèn flash không mong muốn. Đây là một quá trình rèn chính xác và do đó yêu cầu kiểm soát chặt chẽ lượng vật liệu được sử dụng. • KIM LOẠI KIẾM hoặc QUÊN XẠ: Một chi tiết gia công được tác động theo chu vi bằng khuôn và rèn. Một trục gá cũng có thể được sử dụng để rèn hình học phần nội thất. Trong hoạt động swaging, bộ phận gia công thường nhận được vài lần vuốt mỗi giây. Các mặt hàng điển hình được sản xuất theo phương pháp swaging là dụng cụ đầu nhọn, thanh côn, tua vít. • CỌC KIM LOẠI: Chúng tôi sử dụng hoạt động này thường xuyên như một hoạt động bổ sung trong sản xuất các bộ phận. Một lỗ hoặc hốc được tạo ra bằng cách xuyên qua bề mặt chi tiết gia công mà không xuyên qua nó. Xin lưu ý rằng xỏ lỗ khác với khoan dẫn đến một lỗ xuyên qua. • SỞ THÍCH: Một cú đấm có hình dạng mong muốn được ấn vào chi tiết gia công và tạo ra một khoang có hình dạng mong muốn. Chúng tôi gọi cú đấm này là HOB. Hoạt động bao gồm áp suất cao và được thực hiện ở nhiệt độ lạnh. Kết quả là vật liệu được gia công nguội và biến dạng cứng lại. Do đó quy trình này rất thích hợp để chế tạo khuôn mẫu, khuôn dập và các khoang cho các quy trình sản xuất khác. Khi bếp được sản xuất, người ta có thể dễ dàng sản xuất nhiều khoang giống hệt nhau mà không cần phải gia công từng cái một. • ROLL FORGING hoặc ROLL FORMING: Hai cuộn đối nhau được sử dụng để định hình phần kim loại. Chi tiết gia công được đưa vào các cuộn, các cuộn quay và kéo sản phẩm vào khe hở, sau đó sản phẩm được đưa qua phần có rãnh của các cuộn và lực nén tạo ra hình dạng mong muốn của vật liệu. Nó không phải là một quá trình cán mà là một quá trình rèn, bởi vì nó là một quá trình rời rạc chứ không phải là một hoạt động liên tục. Hình dạng hình học trên trục cuộn rèn vật liệu theo hình dạng và hình học cần thiết. Nó được thực hiện nóng. Vì là một quá trình rèn nên nó tạo ra các bộ phận có đặc tính cơ học vượt trội và do đó chúng tôi sử dụng nó cho sản xuất các bộ phận ô tô như trục cần có độ bền đặc biệt trong môi trường làm việc khắc nghiệt. • QUÊN HỮU CƠ: Chi tiết gia công được đặt trong một khuôn đúc và được rèn bởi một khuôn phía trên chuyển động theo quỹ đạo khi nó quay trên một trục nghiêng. Tại mỗi vòng quay, khuôn trên hoàn thành việc tạo lực nén lên toàn bộ chi tiết gia công. Bằng cách lặp lại các vòng quay này một số lần, quá trình rèn đủ được thực hiện. Ưu điểm của kỹ thuật sản xuất này là hoạt động ít tiếng ồn và lực cần thiết thấp hơn. Nói cách khác, với lực nhỏ, người ta có thể quay một khuôn nặng quanh một trục để tạo áp lực lớn lên một phần của chi tiết gia công tiếp xúc với khuôn. Các bộ phận hình đĩa hoặc hình nón đôi khi rất phù hợp cho quá trình này. • RING FORGING: Chúng tôi thường sử dụng để sản xuất nhẫn liền mạch. Cổ phiếu được cắt theo chiều dài, lộn xộn và sau đó xuyên qua tất cả các con đường để tạo ra một lỗ trung tâm. Sau đó, nó được đặt trên một trục gá và một khuôn đúc rèn nó từ trên cao xuống khi chiếc vòng được quay từ từ cho đến khi đạt được kích thước mong muốn. • RIVETING: Một quy trình phổ biến để nối các bộ phận, bắt đầu bằng việc một miếng kim loại thẳng được đưa vào các lỗ được tạo sẵn qua các bộ phận. Sau đó, hai đầu của miếng kim loại được rèn bằng cách ép khớp giữa khuôn trên và khuôn dưới. • KẾT NỐI: Một quá trình phổ biến khác được thực hiện bằng máy ép cơ học, tác động lực lớn trong một khoảng cách ngắn. Cái tên "coining" xuất phát từ những chi tiết tinh xảo được rèn trên bề mặt của đồng xu kim loại. Nó chủ yếu là một quá trình hoàn thiện một sản phẩm mà ở đó các chi tiết nhỏ trên bề mặt thu được do lực tác dụng của khuôn lớn truyền các chi tiết này đến chi tiết gia công. • QUÊN BÓNG KIM LOẠI: Các sản phẩm như ổ bi đòi hỏi chất lượng cao là những viên bi kim loại được sản xuất chính xác. Trong một kỹ thuật được gọi là SKEW ROLLING, chúng tôi sử dụng hai cuộn đối diện xoay liên tục khi nguyên liệu được nạp liên tục vào các cuộn. Ở một đầu của hai cuộn, quả cầu kim loại được đẩy ra như một sản phẩm. Phương pháp thứ hai để rèn bi kim loại là sử dụng khuôn ép khối vật liệu đặt ở giữa chúng theo hình cầu của khoang khuôn. Thông thường, bóng được sản xuất yêu cầu một số bước bổ sung như hoàn thiện và đánh bóng để trở thành sản phẩm chất lượng cao. • QUÊN BẤT NGỜ / QUÊN CHẾT NÓNG: Một quá trình tốn kém chỉ được thực hiện khi giá trị lợi ích / chi phí là hợp lý. Một quá trình làm việc nóng trong đó khuôn được nung nóng đến cùng nhiệt độ với chi tiết gia công. Vì cả hai khuôn và làm việc ở cùng một nhiệt độ, không có quá trình làm mát và các đặc tính chảy của kim loại được cải thiện. Hoạt động này phù hợp tốt với siêu hợp kim và vật liệu có khả năng giả mạo kém hơn và vật liệu có Các đặc tính cơ học rất nhạy cảm với các thay đổi và độ dốc nhiệt độ nhỏ. • KÍCH THƯỚC KIM LOẠI: Là một quá trình hoàn thiện nguội. Dòng vật liệu không bị hạn chế theo mọi hướng ngoại trừ hướng tác dụng lực. Kết quả là thu được độ hoàn thiện bề mặt rất tốt và kích thước chính xác. • HIGH NĂNG LƯỢNG TỶ LỆ QUÊN: Kỹ thuật này liên quan đến một khuôn trên gắn với cánh tay của một pít-tông được đẩy nhanh khi hỗn hợp nhiên liệu-không khí được đánh lửa bằng bugi. Nó giống như hoạt động của các piston trong động cơ ô tô. Khuôn chạm vào chi tiết gia công rất nhanh và sau đó trở lại vị trí ban đầu rất nhanh nhờ áp suất ngược. Tác phẩm được rèn trong vòng vài mili giây và do đó không có thời gian để tác phẩm nguội đi. Điều này rất hữu ích cho các bộ phận khó rèn có các đặc tính cơ học rất nhạy cảm với nhiệt độ. Nói cách khác, quá trình này diễn ra nhanh đến mức chi tiết được tạo thành trong điều kiện nhiệt độ không đổi trong suốt và sẽ không có độ dốc nhiệt độ ở các giao diện khuôn / bộ phận gia công. • Trong DIE FORGING, kim loại được đập giữa hai khối thép phù hợp với hình dạng đặc biệt, được gọi là khuôn. Khi kim loại được rèn giữa các khuôn, nó có hình dạng giống như các hình dạng trong khuôn. Khi đạt đến hình dạng cuối cùng, nó được đưa ra ngoài để làm mát. Quá trình này tạo ra các bộ phận chắc chắn có hình dạng chính xác, nhưng đòi hỏi đầu tư lớn hơn cho các khuôn chuyên dụng. Rèn ngược chiều làm tăng đường kính của một miếng kim loại bằng cách làm phẳng nó. Nó thường được sử dụng để chế tạo các bộ phận nhỏ, đặc biệt là để tạo các đầu trên ốc vít như bu lông và đinh. • POWDER METALLURGY / POWDER PROCESSING: Như tên gọi của nó, nó liên quan đến các quy trình sản xuất để tạo ra các bộ phận rắn có dạng hình học và hình dạng nhất định từ bột. Nếu bột kim loại được sử dụng cho mục đích này thì đó là lĩnh vực luyện kim bột và nếu bột phi kim loại được sử dụng thì đó là chế biến bột. Các bộ phận rắn được sản xuất từ bột bằng cách ép và nung kết. ÉP BỘT dùng để nén các loại bột thành hình dạng mong muốn. Đầu tiên, vật liệu chính có dạng bột, phân chia thành nhiều hạt nhỏ. Hỗn hợp bột được đổ đầy vào khuôn và một cú đấm di chuyển về phía bột và nén nó thành hình dạng mong muốn. Chủ yếu được thực hiện ở nhiệt độ phòng, với việc ép bột, thu được một phần rắn và nó được gọi là nén màu xanh lá cây. Chất kết dính và chất bôi trơn thường được sử dụng để tăng cường khả năng nén chặt. Chúng tôi có khả năng ép bột tạo hình bằng máy ép thủy lực với công suất vài nghìn tấn. Ngoài ra, chúng tôi có các cú nhấn hành động kép với các cú đấm trên và dưới đối lập cũng như nhiều động tác nhấn cho các hình học có phần phức tạp cao. Tính đồng nhất vốn là một thách thức quan trọng đối với nhiều nhà máy luyện kim / chế biến bột không phải là vấn đề lớn đối với AGS-TECH vì chúng tôi có nhiều kinh nghiệm trong việc sản xuất các bộ phận như vậy theo yêu cầu trong nhiều năm. Ngay cả với các bộ phận dày hơn, nơi mà sự đồng nhất đặt ra một thách thức, chúng tôi đã thành công. Nếu chúng tôi cam kết với dự án của bạn, chúng tôi sẽ thực hiện các phần của bạn. Nếu chúng tôi thấy bất kỳ rủi ro tiềm ẩn nào, chúng tôi sẽ thông báo cho bạn trong Advance. LẮP RÁP BỘT, là bước thứ hai, bao gồm việc nâng nhiệt độ lên một mức nhất định và duy trì nhiệt độ ở mức đó trong một thời gian nhất định để các hạt bột trong bộ phận được ép có thể liên kết với nhau. Điều này dẫn đến các liên kết bền chặt hơn nhiều và tăng cường sức mạnh của bộ phận làm việc. Quá trình thiêu kết diễn ra gần với nhiệt độ nóng chảy của bột. Trong quá trình thiêu kết sẽ xảy ra hiện tượng co ngót, độ bền vật liệu, mật độ, độ dẻo, độ dẫn nhiệt, độ dẫn điện đều tăng lên. Chúng tôi có hàng loạt và lò liên tục để thiêu kết. Một trong những khả năng của chúng tôi là điều chỉnh mức độ xốp của các bộ phận mà chúng tôi sản xuất. Ví dụ: chúng tôi có thể sản xuất bộ lọc kim loại bằng cách giữ cho các bộ phận xốp ở một mức độ nào đó. Sử dụng một kỹ thuật gọi là IMPREGNATION, chúng tôi lấp đầy các lỗ rỗng trên kim loại bằng một chất lỏng như dầu. Chúng tôi sản xuất ví dụ như vòng bi ngâm tẩm dầu có khả năng tự bôi trơn. Trong quá trình LẠM PHÁT, chúng tôi lấp đầy các lỗ rỗng của kim loại bằng một kim loại khác có nhiệt độ nóng chảy thấp hơn vật liệu cơ bản. Đun nóng hỗn hợp đến nhiệt độ giữa nhiệt độ nóng chảy của hai kim loại. Kết quả là một số thuộc tính đặc biệt có thể thu được. Chúng tôi cũng thường xuyên thực hiện các hoạt động thứ cấp như gia công và rèn trên các bộ phận được sản xuất bằng bột khi cần có các tính năng hoặc đặc tính đặc biệt hoặc khi bộ phận đó có thể được sản xuất với ít bước quy trình hơn. ÉP MẬT ONG: Trong quy trình này, áp suất chất lỏng được sử dụng để nén chặt chi tiết. Bột kim loại được đặt trong khuôn làm bằng hộp dẻo kín. Trong quá trình ép đẳng áp, áp suất được áp dụng từ khắp nơi, trái ngược với áp suất dọc trục được thấy trong quá trình ép thông thường. Ưu điểm của phương pháp ép đẳng áp là mật độ đồng đều trong bộ phận, đặc biệt đối với các bộ phận lớn hơn hoặc dày hơn, các đặc tính ưu việt. Nhược điểm của nó là thời gian chu kỳ dài và độ chính xác hình học tương đối thấp. ÉP LẠNH ISO được thực hiện ở nhiệt độ phòng và khuôn dẻo được làm bằng cao su, PVC hoặc uretan hoặc các vật liệu tương tự. Chất lỏng được sử dụng để điều áp và nén chặt là dầu hoặc nước. Quá trình thiêu kết thông thường của máy nén màu xanh lá cây tuân theo điều này. Mặt khác, ÉP NÓNG ISOSTATIC được thực hiện ở nhiệt độ cao và vật liệu khuôn là kim loại tấm hoặc gốm có nhiệt độ nóng chảy đủ cao để chống lại nhiệt độ. Chất lỏng điều áp thường là khí trơ. Các hoạt động ép và thiêu kết được thực hiện trong một bước. Độ xốp gần như bị loại bỏ hoàn toàn, cấu trúc đồng nhất grain thu được. Ưu điểm của phương pháp ép đẳng nhiệt nóng là nó có thể sản xuất các bộ phận tương đương với đúc và rèn kết hợp trong khi chế tạo các vật liệu không thích hợp để đúc và rèn có thể được sử dụng. Nhược điểm của phương pháp ép đẳng nhiệt nóng là thời gian chu kỳ cao và do đó chi phí. Nó phù hợp cho các bộ phận quan trọng có âm lượng thấp. KHUÔN INOX KIM LOẠI: Quy trình rất thích hợp để sản xuất các chi tiết phức tạp có thành mỏng và chi tiết hình học. Thích hợp nhất cho các bộ phận nhỏ hơn. Bột và chất kết dính polyme được trộn, đun nóng và bơm vào khuôn. Chất kết dính polyme bao phủ bề mặt của các hạt bột. Sau khi đúc, chất kết dính được loại bỏ bằng cách làm nóng ở nhiệt độ thấp của dung môi hòa tan. ROLL COMPACTION / POWDER ROLLING: Bột được sử dụng để sản xuất dải hoặc tấm liên tục. Bột được nạp từ một bộ nạp và được nén chặt bằng hai cuộn quay thành tấm hoặc dải. Các hoạt động được thực hiện lạnh. Tấm được đưa vào lò thiêu kết. Quá trình thiêu kết có thể được lặp lại lần thứ hai. ĐÀO TẠO BỘT: Các bộ phận có tỷ lệ chiều dài và đường kính lớn được sản xuất bằng cách đùn một hộp kim loại tấm mỏng với bột. LẮP RÁP: Như tên của nó, nó là một phương pháp nén và thiêu kết không áp suất, thích hợp để sản xuất các bộ phận rất xốp như bộ lọc kim loại. Bột được đưa vào khoang khuôn mà không cần nén chặt . LẮP RÁP: Như tên của nó, nó là một phương pháp nén và thiêu kết không áp suất, thích hợp để sản xuất các bộ phận rất xốp như bộ lọc kim loại. Bột được đưa vào khoang khuôn mà không cần nén chặt . NÉN ĐỐT NÉN: Bột được nén trong khuôn bằng hai quả đấm ngược nhau và một dòng điện công suất cao được tác động vào quả đấm và đi qua bột nén được kẹp ở giữa chúng. Dòng điện cao đốt cháy các màng bề mặt khỏi các hạt bột và thiêu kết chúng bằng nhiệt sinh ra. Quá trình này diễn ra nhanh chóng vì nhiệt không được tác động từ bên ngoài mà thay vào đó nó được tạo ra từ bên trong khuôn. ÉP NÓNG: Bột được ép và thiêu kết trong một bước duy nhất trong khuôn có thể chịu được nhiệt độ cao. Khi khuôn nén chặt, nhiệt của bột sẽ được áp dụng cho nó. Độ chính xác tốt và các đặc tính cơ học đạt được bằng phương pháp này làm cho nó trở thành một lựa chọn hấp dẫn. Ngay cả kim loại chịu lửa cũng có thể được xử lý bằng cách sử dụng vật liệu khuôn như than chì. CLICK Product Finder-Locator Service MENU TRƯỚC
- Plastic Rubber Metal Extrusions, Extrusion Dies, Aluminum Extruding
Plastic Rubber Metal Extrusions, Extrusion Dies, Aluminum Extruding, Pipe Tube Forming, Plastic Profiles, Metal Profiles Manufacturing, PVC at AGS-TECH Inc. Máy ép đùn, Sản phẩm ép đùn, Máy đùn Chúng tôi sử dụng quy trình EXTRUSION để sản xuất các sản phẩm có tiết diện cố định như ống, ống dẫn và tản nhiệt. Mặc dù nhiều vật liệu có thể được ép đùn, nhưng các vật liệu đùn phổ biến nhất của chúng tôi được làm bằng kim loại, polyme / nhựa, gốm thu được bằng phương pháp đùn lạnh, ấm hoặc nóng. Chúng tôi gọi các bộ phận được ép đùn là đùn hoặc đùn nếu là số nhiều. Một số phiên bản chuyên biệt của quy trình chúng tôi cũng thực hiện là bán quá nhiều, ép đùn và ép đùn hợp chất. Chúng tôi khuyên bạn nên nhấp vào đây để TẢI XUỐNG Hình minh họa sơ đồ của chúng tôi về các quy trình đùn nhựa và gốm kim loại của AGS-TECH Inc. Điều này sẽ giúp bạn hiểu rõ hơn về những thông tin mà chúng tôi đang cung cấp cho bạn dưới đây. Trong ép đùn, vật liệu được ép đùn được đẩy hoặc kéo qua khuôn có mặt cắt ngang mong muốn. Quy trình này có thể được sử dụng để sản xuất các mặt cắt phức tạp có bề mặt hoàn thiện tốt và gia công trên vật liệu giòn. Người ta có thể sản xuất bất kỳ độ dài nào của các bộ phận bằng cách sử dụng quy trình này. Để đơn giản hóa các bước của quy trình: 1.) Ở dạng ép đùn ấm hoặc nóng, vật liệu được làm nóng và được nạp vào thùng chứa trong máy ép. Vật liệu được ép và đẩy ra khỏi khuôn. 2.) Máy đùn được sản xuất được kéo dài để làm thẳng, xử lý nhiệt hoặc gia công nguội để tăng cường các đặc tính của nó. Mặt khác COLD EXTRUSION đặt ở xung quanh nhiệt độ phòng và có ưu điểm là ít bị ôxy hóa, độ bền cao, dung sai gần hơn, độ bền và hoàn thiện bề mặt tốt. WARM EXTRUSION được thực hiện trên nhiệt độ phòng nhưng dưới điểm kết tinh lại. Nó cung cấp một sự thỏa hiệp và cân bằng cho các lực cần thiết, độ dẻo và tính chất vật liệu và do đó là sự lựa chọn cho một số ứng dụng. HOT EXTRUSION diễn ra trên nhiệt độ kết tinh lại của vật liệu. Bằng cách này, dễ dàng hơn để đẩy vật liệu qua khuôn. Tuy nhiên chi phí thiết bị cao. Hồ sơ đùn càng phức tạp thì chi phí cho khuôn (dụng cụ) càng cao và tốc độ sản xuất càng thấp. Mặt cắt khuôn cũng như độ dày có những hạn chế phụ thuộc vào vật liệu được ép đùn. Các góc nhọn trong khuôn ép đùn luôn là điều không mong muốn và cần tránh trừ khi cần thiết. Theo vật liệu đang được ép đùn, chúng tôi cung cấp: • MỞ RỘNG KIM LOẠI : Hầu hết các loại phổ biến mà chúng tôi sản xuất là nhôm, đồng thau, kẽm, đồng, thép, titan, magiê • PLASTIC EXTRUSION : Nhựa được nấu chảy và tạo thành dạng liên tục. Các vật liệu phổ biến của chúng tôi được xử lý là polyethylene, nylon, polystyrene, polyvinyl chloride, polypropylene, nhựa ABS, polycarbonate, acrylic. Sản phẩm tiêu biểu chúng tôi sản xuất bao gồm ống và ống, khung nhựa. Trong quá trình này, các hạt nhựa nhỏ / hạt nhựa được đưa trọng lực từ phễu vào thùng của máy đùn. Thông thường, chúng tôi cũng trộn chất tạo màu hoặc các chất phụ gia khác vào phễu để cung cấp cho sản phẩm các thông số kỹ thuật và đặc tính cần thiết. Vật liệu đi vào thùng đã được làm nóng được trục vít quay buộc phải rời khỏi thùng ở cuối và di chuyển qua bộ lọc để loại bỏ các chất gây ô nhiễm trong nhựa nóng chảy. Sau khi vượt qua gói màn hình, nhựa đi vào khuôn ép đùn. Khuôn làm cho nhựa mềm chuyển động có hình dạng như khi nó đi qua. Bây giờ chất đùn đi qua một bể cách thủy để làm mát. Các kỹ thuật khác mà AGS-TECH Inc. đã sử dụng trong nhiều năm là: • PIPE & TUBING EXTRUSION : Ống và ống nhựa được hình thành khi nhựa được đùn qua khuôn định hình tròn và làm nguội trong nồi cách thủy, sau đó cắt theo chiều dài hoặc cuộn / cuộn. Rõ ràng hoặc có màu, sọc, tường đơn hoặc tường kép, linh hoạt hoặc cứng, PE, PP, polyurethane, PVC, nylon, PC, silicone, vinyl hoặc loại khác, chúng tôi có tất cả. Chúng tôi có sẵn các ống cũng như khả năng sản xuất theo thông số kỹ thuật của bạn. AGS-TECH sản xuất ống theo yêu cầu của FDA, UL và LE cho các ứng dụng y tế, điện & điện tử, công nghiệp và các ứng dụng khác. • OVERJACKETING / OVER JACKETING EXTRUSION : Kỹ thuật này áp dụng một lớp nhựa bên ngoài lên dây hoặc cáp hiện có. Dây cách điện của chúng tôi được sản xuất bằng phương pháp này. • COEXTRUSION : Nhiều lớp vật liệu được ép đùn đồng thời. Nhiều lớp được phân phối bởi nhiều máy đùn. Các độ dày lớp khác nhau có thể được điều chỉnh để đáp ứng các thông số kỹ thuật của khách hàng. Quá trình này làm cho nó có thể sử dụng nhiều polyme, mỗi polyme có một chức năng khác nhau trong sản phẩm. Kết quả là, người ta có thể tối ưu hóa một loạt các thuộc tính. • HẤP THỤ HỢP CHẤT: Một hoặc nhiều polyme được trộn với các chất phụ gia để thu được một hợp chất dẻo. Máy đùn trục vít đôi của chúng tôi sản xuất đùn ép hỗn hợp. Khuôn ép đùn nói chung không đắt so với khuôn kim loại. Nếu bạn đang trả nhiều hơn vài nghìn đô la cho một khuôn nhôm đùn ép đùn cỡ nhỏ hoặc trung bình, có lẽ bạn đang phải trả quá nhiều. Chúng tôi là những chuyên gia trong việc xác định kỹ thuật nào tiết kiệm chi phí nhất, nhanh nhất và phù hợp nhất cho ứng dụng của bạn. Đôi khi ép đùn và sau đó gia công một bộ phận có thể giúp bạn tiết kiệm rất nhiều tiền mặt. Trước khi đưa ra quyết định chắc chắn, hãy hỏi ý kiến của chúng tôi trước. Chúng tôi đã giúp nhiều khách hàng đưa ra quyết định đúng đắn. Đối với một số vật liệu đùn kim loại được sử dụng rộng rãi, bạn có thể tải xuống tài liệu quảng cáo và danh mục của chúng tôi bằng cách nhấp vào văn bản màu bên dưới. Nếu đó là một sản phẩm ngoài kệ đáp ứng yêu cầu của bạn thì sẽ tiết kiệm hơn. Tải xuống ống y tế và khả năng đùn ống của chúng tôi Tải xuống tản nhiệt đùn của chúng tôi • QUY TRÌNH SẢN XUẤT & VẢI THỨ HAI CHO EXTRUSIONS : Trong số các quy trình giá trị gia tăng mà chúng tôi cung cấp cho các sản phẩm đùn là: -Ống & uốn ống tùy chỉnh, tạo hình và định hình, cắt ống, tạo hình đầu ống, cuộn ống, gia công và hoàn thiện, khoan lỗ & xuyên & đục lỗ, -Phụ hợp ống và ống tùy chỉnh, lắp ráp ống, hàn, hàn và hàn - Uốn đùn tùy chỉnh, tạo hình và định hình -Làm sạch, tẩy dầu mỡ, tẩy gỉ, thụ động hóa, đánh bóng, anốt hóa, mạ, sơn, xử lý nhiệt, ủ và làm cứng, đánh dấu, khắc và dán nhãn, đóng gói tùy chỉnh. CLICK Product Finder-Locator Service TRANG TRƯỚC
- Casting and Machined Parts, CNC Manufacturing, Milling, Turning, Swiss
Casting and Machined Parts, CNC Manufacturing, Milling, Turning, Swiss Type Machining, Die Casting, Investment Casting, Lost Foam Cast Parts from AGS-TECH Inc. Đúc và Gia công Các kỹ thuật đúc và gia công tùy chỉnh của chúng tôi là đúc có thể sử dụng và không tiêu hao, đúc kim loại và đúc kim loại, cát, khuôn, ly tâm, liên tục, khuôn gốm, đầu tư, bọt bị mất, hình dạng gần lưới, khuôn vĩnh viễn (đúc khuôn trọng lực), thạch cao khuôn (đúc thạch cao) và đúc vỏ, các bộ phận gia công được sản xuất bằng cách phay và tiện sử dụng thiết bị CNC cũng như thông thường, gia công kiểu Thụy Sĩ cho thông lượng cao các bộ phận chính xác nhỏ rẻ tiền, gia công vít cho ốc vít, gia công phi thông thường. Xin lưu ý rằng ngoài kim loại và hợp kim kim loại, chúng tôi gia công các thành phần gốm, thủy tinh và nhựa trong một số trường hợp khi sản xuất khuôn không hấp dẫn hoặc không phải là tùy chọn. Gia công vật liệu polyme đòi hỏi kinh nghiệm chuyên môn mà chúng tôi có do thách thức đối với nhựa và cao su do độ mềm, không cứng của chúng ... vv. Để gia công gốm và thủy tinh, vui lòng xem trang của chúng tôi về Chế tạo phi thông thường. AGS-TECH Inc. sản xuất và cung cấp cả vật đúc nhẹ và nặng. Chúng tôi đã và đang cung cấp các bộ phận đúc và gia công kim loại cho nồi hơi, bộ trao đổi nhiệt, ô tô, động cơ vi mô, tuabin gió, thiết bị đóng gói thực phẩm và hơn thế nữa. Chúng tôi khuyên bạn nên nhấp vào đây để TẢI XUỐNG Các Minh Họa Sơ Đồ Về Quy Trình Gia Công Và Đúc của AGS-TECH Inc. Điều này sẽ giúp bạn hiểu rõ hơn về những thông tin mà chúng tôi đang cung cấp cho bạn dưới đây. Hãy xem xét một số kỹ thuật khác nhau mà chúng tôi cung cấp chi tiết: • ĐÚC KHUÔN XUẤT XỨ: Loại rộng này đề cập đến các phương pháp liên quan đến khuôn tạm thời và không thể tái sử dụng. Ví dụ như cát, thạch cao, vỏ, đầu tư (còn gọi là sáp bị mất) và đúc thạch cao. • ĐÚC CÁT: Một quá trình sử dụng cát làm vật liệu làm khuôn. Một phương pháp rất cũ và vẫn còn rất phổ biến đến mức phần lớn các vật đúc kim loại được sản xuất bằng kỹ thuật này. Chi phí thấp ngay cả khi sản xuất số lượng ít. Thích hợp cho sản xuất các bộ phận nhỏ và lớn. Kỹ thuật này có thể được sử dụng để sản xuất các bộ phận trong vòng vài ngày hoặc vài tuần với vốn đầu tư rất ít. Cát ẩm được kết dính với nhau bằng đất sét, chất kết dính hoặc dầu đặc biệt. Cát thường được chứa trong các hộp khuôn và hệ thống hốc & cổng được tạo ra bằng cách nén chặt cát xung quanh các mô hình. Các quy trình là: 1.) Đặt mô hình vào cát để làm khuôn 2.) Sự kết hợp của mô hình và cát trong một hệ thống gating 3.) Loại bỏ mô hình 4.) Làm đầy khoang khuôn bằng kim loại nóng chảy 5.) Làm mát kim loại 6.) Phá vỡ khuôn cát và loại bỏ vật đúc • ĐÚC KHUÔN NHỰA: Tương tự như đúc cát, và thay vì cát, thạch cao của paris đang được sử dụng làm vật liệu khuôn. Thời gian sản xuất ngắn như đúc cát và không tốn kém. Dung sai kích thước tốt và bề mặt hoàn thiện. Nhược điểm chính của nó là nó chỉ có thể được sử dụng với các kim loại có nhiệt độ nóng chảy thấp như nhôm và kẽm. • ĐÚC VỎ KHUÔN: Cũng tương tự như đúc cát. Khoang khuôn thu được bằng vỏ cứng của cát và chất kết dính nhựa nhiệt rắn thay vì bình chứa đầy cát như trong quá trình đúc cát. Hầu hết mọi kim loại thích hợp để đúc bằng cát đều có thể được đúc bằng cách đúc vỏ. Quá trình này có thể được tóm tắt như sau: 1.) Sản xuất khuôn vỏ. Cát được sử dụng có kích thước hạt nhỏ hơn nhiều so với cát được sử dụng trong đúc cát. Cát mịn được trộn với nhựa nhiệt rắn. Hoa văn kim loại được phủ một lớp chất chống phân tách giúp việc tháo vỏ dễ dàng hơn. Sau đó, mẫu kim loại được nung nóng và hỗn hợp cát được nghiền hoặc thổi lên mẫu đúc nóng. Một lớp vỏ mỏng hình thành trên bề mặt của hoa văn. Độ dày của lớp vỏ này có thể được điều chỉnh bằng cách thay đổi khoảng thời gian hỗn hợp nhựa cát tiếp xúc với mẫu kim loại. Sau đó, cát rời được loại bỏ với lớp vỏ còn lại. 2.) Tiếp theo, vỏ và hoa văn được làm nóng trong lò để vỏ cứng lại. Sau khi quá trình cứng hoàn tất, vỏ được đẩy ra khỏi mẫu bằng cách sử dụng các chốt gắn trên mẫu. 3.) Hai vỏ như vậy được lắp ráp với nhau bằng cách dán hoặc kẹp và tạo thành khuôn hoàn chỉnh. Bây giờ, khuôn vỏ được đưa vào một thùng chứa, trong đó nó được hỗ trợ bởi cát hoặc kim loại bắn trong quá trình đúc. 4.) Bây giờ kim loại nóng có thể được đổ vào khuôn vỏ. Ưu điểm của đúc vỏ là sản phẩm có độ hoàn thiện bề mặt rất tốt, khả năng chế tạo các chi tiết phức tạp với độ chính xác kích thước cao, quá trình tự động hóa dễ dàng, tiết kiệm cho sản xuất khối lượng lớn. Nhược điểm là khuôn cần thông gió tốt vì khí được tạo ra khi kim loại nóng chảy tiếp xúc với hóa chất kết dính, nhựa nhiệt rắn và các mẫu kim loại đắt tiền. Do chi phí của các mẫu kim loại, kỹ thuật này có thể không phù hợp với các hoạt động sản xuất số lượng ít. • ĐÚC ĐẦU TƯ (hay còn gọi là ĐÚC SÁP MẤT): Cũng là một kỹ thuật rất lâu đời và phù hợp để sản xuất các bộ phận chất lượng với độ chính xác cao, độ lặp lại, tính linh hoạt và tính toàn vẹn từ nhiều kim loại, vật liệu chịu lửa và hợp kim đặc biệt hiệu suất cao. Các bộ phận có kích thước nhỏ cũng như lớn đều có thể được sản xuất. Một quy trình đắt tiền khi so sánh với một số phương pháp khác, nhưng ưu điểm chính là khả năng sản xuất các bộ phận có hình dạng gần giống lưới, đường viền và chi tiết phức tạp. Vì vậy, chi phí được bù đắp phần nào bằng cách loại bỏ việc làm lại và gia công trong một số trường hợp. Mặc dù có thể có các thay đổi, đây là tóm tắt về quy trình đúc vốn đầu tư chung: 1.) Tạo mẫu gốc ban đầu từ sáp hoặc nhựa. Mỗi lần đúc cần một mẫu vì chúng sẽ bị phá hủy trong quá trình này. Khuôn mà từ đó các mẫu được sản xuất cũng cần thiết và hầu hết thời gian khuôn được đúc hoặc gia công. Do không cần mở khuôn nên có thể đúc phức tạp, nhiều mẫu sáp có thể được kết nối như các cành cây và đổ vào nhau, do đó có thể sản xuất nhiều bộ phận từ một lần đổ kim loại hoặc hợp kim kim loại. 2.) Tiếp theo, hoa văn được nhúng hoặc đổ lên với một loại bùn chịu lửa bao gồm silica hạt rất mịn, nước, chất kết dính. Điều này dẫn đến một lớp gốm trên bề mặt của hoa văn. Lớp sơn chịu lửa trên mẫu được để khô và cứng lại. Bước này là nơi bắt nguồn của tên đầu tư đúc: Bùn chịu lửa được đầu tư trên mẫu sáp. 3.) Ở bước này, úp ngược khuôn gốm đã cứng và đun nóng để sáp chảy ra và trào ra khỏi khuôn. Một khoang được để lại phía sau để đúc kim loại. 4.) Sau khi hết sáp, khuôn gốm được nung nóng đến nhiệt độ cao hơn nữa để làm cứng khuôn. 5.) Đúc kim loại được đổ vào khuôn nóng lấp đầy tất cả các phần phức tạp. 6.) Đúc được phép đóng rắn 7.) Cuối cùng, khuôn gốm bị hỏng và các bộ phận sản xuất được cắt từ cây. Đây là một liên kết đến Tài liệu giới thiệu về nhà máy đúc đầu tư • ĐÚC MẪU ÁO DÀI: Quy trình sử dụng một mẫu làm từ vật liệu như bọt polystyrene sẽ bay hơi khi đổ kim loại nóng chảy vào khuôn. Có hai loại quy trình này: ĐÚC BỌT MỎ sử dụng cát không kết dính và ĐÚC ĐÚC ĐẦY ĐỦ sử dụng cát ngoại quan. Dưới đây là các bước quy trình chung: 1.) Sản xuất mô hình từ vật liệu như polystyrene. Khi số lượng lớn sẽ sản xuất theo khuôn mẫu. Nếu một phần có hình dạng phức tạp, một số phần của vật liệu xốp như vậy có thể cần được kết dính với nhau để tạo thành mẫu. Chúng tôi thường phủ lên hoa văn một hợp chất chịu lửa để tạo ra một bề mặt hoàn thiện tốt trên vật đúc. 2.) Mô hình sau đó được đưa vào cát đúc. 3.) Kim loại nóng chảy được đổ vào khuôn, làm bay hơi mô hình bọt, tức là polystyrene trong hầu hết các trường hợp khi nó chảy qua khoang khuôn. 4.) Kim loại nóng chảy được để trong khuôn cát để cứng lại. 5.) Sau khi nó được làm cứng, chúng tôi loại bỏ vật đúc. Trong một số trường hợp, sản phẩm chúng tôi sản xuất yêu cầu cốt lõi trong khuôn mẫu. Trong đúc bay hơi, không cần đặt và cố định lõi trong lòng khuôn. Kỹ thuật này phù hợp để sản xuất các hình dạng rất phức tạp, nó có thể dễ dàng tự động hóa để sản xuất khối lượng lớn và không có đường phân đoạn trong bộ phận đúc. Quá trình cơ bản là đơn giản và tiết kiệm để thực hiện. Đối với sản xuất số lượng lớn, vì cần khuôn hoặc khuôn để sản xuất các mẫu từ polystyrene, điều này có thể hơi tốn kém. • ĐÚC KHUÔN KHÔNG MỞ RỘNG: Loại rộng này đề cập đến các phương pháp mà khuôn không cần phải cải tạo sau mỗi chu kỳ sản xuất. Ví dụ như đúc vĩnh viễn, chết, liên tục và ly tâm. Độ lặp lại thu được và các bộ phận có thể được đặc trưng như HÌNH DẠNG MẠNG GẦN. • ĐÚC KHUÔN VĨNH VIỄN: Khuôn có thể tái sử dụng được làm từ kim loại được sử dụng cho nhiều vật đúc. Khuôn vĩnh viễn thường có thể được sử dụng hàng chục nghìn lần trước khi bị mòn. Trọng lực, áp suất khí hoặc chân không thường được sử dụng để làm đầy khuôn. Khuôn (còn gọi là khuôn) thường được làm bằng sắt, thép, gốm hoặc các kim loại khác. Quy trình chung là: 1.) Máy và tạo khuôn. Người ta thường gia công khuôn từ hai khối kim loại ăn khớp với nhau và có thể đóng mở được. Cả hai tính năng của bộ phận cũng như hệ thống gating thường được gia công vào khuôn đúc. 2.) Các bề mặt bên trong khuôn được phủ một lớp bùn kết hợp vật liệu chịu lửa. Điều này giúp kiểm soát dòng nhiệt và hoạt động như một chất bôi trơn để dễ dàng tháo bộ phận đúc. 3.) Tiếp theo, các nửa khuôn vĩnh viễn được đóng lại và khuôn được làm nóng. 4.) Kim loại nóng chảy được đổ vào khuôn và để yên cho đông đặc. 5.) Trước khi quá trình làm mát xảy ra nhiều, chúng tôi lấy bộ phận ra khỏi khuôn vĩnh viễn bằng cách sử dụng ống đẩy khi các nửa khuôn được mở. Chúng tôi thường sử dụng đúc khuôn vĩnh viễn cho các kim loại có nhiệt độ nóng chảy thấp như kẽm và nhôm. Đối với các vật đúc bằng thép, chúng tôi sử dụng than chì làm vật liệu khuôn. Đôi khi chúng tôi thu được các hình dạng phức tạp bằng cách sử dụng lõi trong khuôn vĩnh cửu. Ưu điểm của kỹ thuật này là vật đúc có cơ tính tốt nhờ làm nguội nhanh, đồng nhất về tính chất, độ chính xác và độ hoàn thiện bề mặt tốt, tỷ lệ loại bỏ thấp, khả năng tự động hóa quy trình và sản xuất kinh tế khối lượng lớn. Nhược điểm là chi phí thiết lập ban đầu cao khiến nó không phù hợp với các hoạt động khối lượng thấp và hạn chế về kích thước của các bộ phận được sản xuất. • ĐÚC DIE: Một khuôn được gia công và kim loại nóng chảy được đẩy dưới áp suất cao vào các khoang khuôn. Cả đúc khuôn kim loại màu cũng như kim loại màu đều có thể thực hiện được. Quy trình này thích hợp cho việc sản xuất số lượng lớn, chạy các bộ phận có kích thước vừa và nhỏ với các chi tiết, thành cực mỏng, tính nhất quán về kích thước và bề mặt hoàn thiện tốt. AGS-TECH Inc. có khả năng sản xuất tường có độ dày nhỏ đến 0,5 mm bằng kỹ thuật này. Giống như trong đúc khuôn vĩnh cửu, khuôn cần bao gồm hai nửa có thể mở và đóng để loại bỏ một phần được sản xuất. Một khuôn đúc có thể có nhiều khoang để có thể sản xuất nhiều vật đúc với mỗi chu kỳ. Khuôn đúc rất nặng và lớn hơn nhiều so với các bộ phận mà chúng sản xuất, do đó cũng đắt tiền. Chúng tôi sửa chữa và thay thế các khuôn bị mòn miễn phí cho khách hàng miễn là họ đặt hàng lại các bộ phận của họ từ chúng tôi. Những cái chết của chúng ta có tuổi thọ dài trong khoảng vài trăm nghìn chu kỳ. Dưới đây là các bước quy trình đơn giản hóa cơ bản: 1.) Sản xuất khuôn nói chung từ thép 2.) Khuôn được lắp trên máy đúc khuôn 3.) Piston buộc kim loại nóng chảy chảy trong các hốc khuôn lấp đầy các tính năng phức tạp và thành mỏng 4.) Sau khi lấp đầy khuôn bằng kim loại nóng chảy, vật đúc được để cứng dưới áp suất 5.) Khuôn được mở và tháo khuôn đúc với sự trợ giúp của các chốt đẩy. 6.) Bây giờ khuôn trống được bôi trơn một lần nữa và được kẹp lại cho chu kỳ tiếp theo. Trong quá trình đúc khuôn, chúng tôi thường sử dụng đúc chèn trong đó chúng tôi kết hợp một bộ phận bổ sung vào khuôn và đúc kim loại xung quanh nó. Sau khi đông đặc, các bộ phận này trở thành một phần của sản phẩm đúc. Ưu điểm của đúc khuôn là tính chất cơ học của các bộ phận tốt, khả năng có các tính năng phức tạp, chi tiết đẹp và bề mặt hoàn thiện tốt, tỷ lệ sản xuất cao, dễ dàng tự động hóa. Nhược điểm là: Không phù hợp lắm với khối lượng nhỏ vì chi phí khuôn và thiết bị cao, hạn chế về hình dạng có thể đúc, các vết tròn nhỏ trên các bộ phận đúc do tiếp xúc của các chân đẩy, tia chớp mỏng của kim loại bị ép ra ở đường phân chia, cần Đối với các lỗ thông hơi dọc theo đường phân chia giữa khuôn, cần phải giữ cho nhiệt độ khuôn thấp bằng cách sử dụng tuần hoàn nước. • ĐÚC TRUNG TÂM: Kim loại nóng chảy được đổ vào tâm của khuôn quay theo trục quay. Lực ly tâm ném kim loại về phía ngoại vi và nó sẽ đông đặc lại khi khuôn tiếp tục quay. Cả hai phép quay trục ngang và trục dọc đều có thể được sử dụng. Các bộ phận có bề mặt bên trong tròn cũng như các hình dạng không tròn khác có thể được đúc. Quá trình này có thể được tóm tắt như sau: 1.) Kim loại nóng chảy được đổ vào khuôn ly tâm. Sau đó, kim loại bị ép vào các bức tường bên ngoài do sự quay của khuôn. 2.) Khi khuôn quay, vật đúc kim loại cứng lại Đúc ly tâm là một kỹ thuật phù hợp để sản xuất các bộ phận hình trụ rỗng như ống, không cần trục, rãnh và các bộ phận gating, bề mặt hoàn thiện tốt và các tính năng chi tiết, không có vấn đề co ngót, khả năng sản xuất ống dài với đường kính rất lớn, khả năng sản xuất tốc độ cao . • ĐÚC LIÊN TỤC (STRAND CASTING): Dùng để đúc kim loại có chiều dài liên tục. Về cơ bản, kim loại nóng chảy được đúc thành hình dạng hai chiều của khuôn nhưng chiều dài của nó là không xác định. Kim loại nóng chảy mới liên tục được đưa vào khuôn khi vật đúc đi xuống với chiều dài tăng dần theo thời gian. Các kim loại như đồng, thép, nhôm được đúc thành sợi dài bằng quá trình đúc liên tục. Quy trình có thể có nhiều cấu hình khác nhau nhưng cấu hình chung có thể được đơn giản hóa như: 1.) Kim loại nóng chảy được đổ vào một thùng chứa nằm cao trên khuôn với lượng và tốc độ dòng chảy đã được tính toán kỹ lưỡng và chảy qua khuôn được làm mát bằng nước. Vật đúc bằng kim loại đổ vào khuôn đóng rắn thành một thanh khởi động đặt ở đáy khuôn. Thanh khởi động này cung cấp cho các con lăn thứ gì đó để bám vào ban đầu. 2.) Sợi kim loại dài được các con lăn cuốn với tốc độ không đổi. Các con lăn cũng thay đổi hướng của dòng chảy của sợi kim loại từ dọc sang ngang. 3.) Sau khi vật đúc liên tục đã đi được một khoảng ngang nhất định, một ngọn đuốc hoặc cưa di chuyển với vật đúc sẽ nhanh chóng cắt vật đúc theo chiều dài mong muốn. Quy trình đúc liên tục có thể được tích hợp với QUY TRÌNH LĂN, nơi kim loại đúc liên tục có thể được đưa trực tiếp vào máy cán để sản xuất Dầm chữ I, Dầm chữ T… .v.v. Đúc liên tục tạo ra các đặc tính đồng nhất trong toàn bộ sản phẩm, nó có tỷ lệ hóa rắn cao, giảm chi phí do thất thoát vật liệu rất thấp, cung cấp một quy trình nơi tải kim loại, đổ, hóa rắn, cắt và loại bỏ đúc đều diễn ra trong một hoạt động liên tục và do đó dẫn đến tỷ lệ năng suất cao và chất lượng cao. Tuy nhiên, một điều cần cân nhắc chính là vốn đầu tư ban đầu cao, chi phí thiết lập và yêu cầu về không gian. • DỊCH VỤ GIA CÔNG: Chúng tôi cung cấp gia công ba, bốn và năm trục. Loại quy trình gia công mà chúng tôi sử dụng là GIA CÔNG BÓNG, PHAY, KHOAN, KHOAN, BÓNG, LÁT, CẮT, MÀI, LÁ, ĐÁNH BÓNG và GIA CÔNG KHÔNG TRUYỀN THỐNG được xây dựng chi tiết hơn trong một menu khác trên trang web của chúng tôi. Đối với hầu hết các hoạt động sản xuất của chúng tôi, chúng tôi sử dụng máy CNC. Tuy nhiên đối với một số hoạt động, các kỹ thuật thông thường phù hợp hơn và do đó chúng tôi cũng dựa vào chúng. Khả năng gia công của chúng tôi đạt đến mức cao nhất có thể và một số bộ phận khắt khe nhất được sản xuất tại nhà máy được chứng nhận AS9100. Cánh động cơ phản lực đòi hỏi kinh nghiệm sản xuất chuyên môn cao và thiết bị phù hợp. Ngành hàng không vũ trụ có những tiêu chuẩn rất khắt khe. Một số thành phần có cấu trúc hình học phức tạp dễ dàng được sản xuất nhất bằng phương pháp gia công năm trục, điều này chỉ có ở một số nhà máy gia công bao gồm cả của chúng tôi. Nhà máy được chứng nhận hàng không vũ trụ của chúng tôi có kinh nghiệm cần thiết tuân thủ yêu cầu tài liệu mở rộng của ngành hàng không vũ trụ. Trong các hoạt động TURNING, một phôi được quay và di chuyển trên một dụng cụ cắt. Đối với quá trình này, một máy được gọi là máy tiện đang được sử dụng. Trong PHAY, một máy được gọi là máy phay có một công cụ quay để đưa các cạnh cắt chịu lực vào phôi. Các hoạt động KHOAN bao gồm một máy cắt quay với các cạnh cắt tạo ra các lỗ khi tiếp xúc với phôi. Máy ép khoan, máy tiện hoặc máy xay thường được sử dụng. Trong các hoạt động BORING, một công cụ có một đầu nhọn uốn cong được di chuyển vào một lỗ thô trên phôi đang quay để mở rộng lỗ một chút và cải thiện độ chính xác. Nó được sử dụng cho mục đích hoàn thiện tốt. BROACHING liên quan đến một công cụ có răng để loại bỏ vật liệu khỏi phôi trong một lần lướt qua (dụng cụ có răng). Trong chuốt thẳng, dao kéo chạy tuyến tính với bề mặt của phôi để tạo hiệu ứng cắt, trong khi chuốt quay, chổi được xoay và ép vào phôi để cắt một hình dạng đối xứng trục. GIA CÔNG KIỂU SWISS là một trong những kỹ thuật có giá trị của chúng tôi, chúng tôi sử dụng để sản xuất khối lượng lớn các bộ phận nhỏ có độ chính xác cao. Sử dụng máy tiện kiểu Thụy Sĩ, chúng tôi gia công các chi tiết nhỏ, phức tạp, chính xác với giá thành rẻ. Không giống như các máy tiện thông thường nơi phôi được giữ cố định và dao chuyển động, trong các tâm tiện kiểu Thụy Sĩ, phôi được phép di chuyển theo trục Z và dao đứng yên. Trong gia công kiểu Thụy Sĩ, cổ phiếu thanh được giữ trong máy và nâng cao thông qua ống lót dẫn hướng theo trục z, chỉ để lộ phần cần gia công. Cách này đảm bảo độ chặt và độ chính xác rất cao. Sự sẵn có của các công cụ sống mang lại cơ hội để nghiền và khoan khi vật liệu tiến bộ từ ống lót dẫn hướng. Trục Y của thiết bị kiểu Thụy Sĩ cung cấp đầy đủ khả năng phay và tiết kiệm rất nhiều thời gian trong sản xuất. Hơn nữa, máy của chúng tôi có máy khoan và công cụ doa hoạt động trên bộ phận khi nó được giữ ở trục chính phụ. Khả năng gia công Swiss-Type của chúng tôi mang đến cho chúng tôi cơ hội gia công hoàn toàn tự động trong một thao tác duy nhất. Gia công là một trong những mảng kinh doanh lớn nhất của AGS-TECH Inc. Chúng tôi sử dụng nó như một hoạt động chính hoặc một hoạt động phụ sau khi đúc hoặc đùn một bộ phận để đáp ứng tất cả các thông số kỹ thuật của bản vẽ. • DỊCH VỤ HOÀN THIỆN BỀ MẶT: Chúng tôi cung cấp rất nhiều phương pháp xử lý bề mặt và hoàn thiện bề mặt như xử lý bề mặt để tăng cường độ bám dính, lắng lớp oxit mỏng để tăng cường độ bám dính của lớp phủ, phun cát, màng hóa học, anodizing, thấm nitơ, sơn tĩnh điện, phun sơn , các kỹ thuật phủ và tráng kim loại tiên tiến khác nhau bao gồm phún xạ, tia điện tử, bay hơi, mạ, lớp phủ cứng như kim cương như carbon (DLC) hoặc lớp phủ titan cho các dụng cụ khoan và cắt. • DỊCH VỤ TIẾP THỊ & NHÃN SẢN PHẨM: Nhiều khách hàng của chúng tôi yêu cầu đánh dấu và dán nhãn, khắc laser, khắc trên các bộ phận kim loại. Nếu bạn có bất kỳ nhu cầu nào như vậy, hãy để chúng tôi thảo luận xem lựa chọn nào sẽ là tốt nhất cho bạn. Dưới đây là một số sản phẩm đúc kim loại thường được sử dụng. Vì đây là những sản phẩm không có sẵn, bạn có thể tiết kiệm chi phí khuôn trong trường hợp bất kỳ chi phí nào trong số này phù hợp với yêu cầu của bạn: BẤM VÀO ĐÂY ĐỂ TẢI XUỐNG Hộp nhôm đúc 11 Series của chúng tôi từ AGS-Electronics CLICK Product Finder-Locator Service TRANG TRƯỚC
- Custom Manufactured Parts, Assemblies, Plastic Mold, Casting,Machining
Custom Manufactured Parts, Assemblies, Plastic Mold, Rubber Molding, Metal Casting, CNC Machining, Turning, Milling, Electrical Electronic Optical Assembly PCBA Các bộ phận & cụm & sản phẩm được sản xuất tùy chỉnh Đọc thêm Khuôn và khuôn nhựa & cao su Đọc thêm Đúc và Gia công Đọc thêm Máy ép đùn, Sản phẩm ép đùn Đọc thêm Dập & Chế tạo kim loại tấm Đọc thêm Rèn kim loại & luyện kim bột Đọc thêm Dây & hình thành lò xo Đọc thêm Tạo hình & định hình thủy tinh & gốm Đọc thêm Sản xuất phụ gia và nhanh chóng Đọc thêm Sản xuất vật liệu tổng hợp & vật liệu tổng hợp Đọc thêm Tham gia & lắp ráp & quá trình buộc Chúng tôi sản xuất các bộ phận và bộ phận lắp ráp cho bạn và cung cấp các quy trình sản xuất sau: • Khuôn và các bộ phận đúc bằng nhựa và cao su. Đúc phun, tạo hình nhiệt, đúc nhiệt rắn, tạo hình chân không, đúc thổi, đúc quay, đúc đổ, đúc chèn và các loại khác. • Đùn nhựa, cao su và kim loại • Các bộ phận được đúc và gia công bằng kim loại và kim loại màu được sản xuất bằng kỹ thuật phay và tiện, gia công kiểu Thụy Sĩ. • Các bộ phận luyện kim bột • Dập kim loại và phi kim loại, tạo hình kim loại tấm, cụm kim loại tấm hàn • Rèn nóng và nguội • Dây điện, cụm dây hàn, dây tạo hình • Nhiều loại lò xo, lò xo tạo hình • Sản xuất bánh răng, hộp số, khớp nối, con sâu, hộp giảm tốc, xi lanh, dây đai truyền động, xích truyền động, linh kiện truyền động • Kính cường lực và kính chống đạn tùy chỉnh phù hợp với tiêu chuẩn quân sự và NATO • Bi, ổ trục, ròng rọc và cụm ròng rọc • Van và các bộ phận khí nén như vòng chữ O, vòng đệm và vòng đệm • Các bộ phận và cụm lắp ráp bằng thủy tinh và gốm, các thành phần chống chân không và kín, liên kết kim loại-gốm và gốm-sứ. • Các loại cụm cơ khí, cơ quang, cơ điện, quang điện tử. • Kim loại-cao su, kim loại-nhựa liên kết • Ống và ống, tạo hình ống, uốn cong và các cụm ống tùy chỉnh, sản xuất dưới đây. • Sản xuất sợi thủy tinh • Hàn sử dụng các kỹ thuật khác nhau như hàn điểm, hàn laser, MIG, TIG. Hàn siêu âm cho các bộ phận bằng nhựa. • Có rất nhiều phương pháp xử lý bề mặt và hoàn thiện bề mặt như dưỡng bề mặt để tăng cường độ bám dính, lắng đọng lớp oxit mỏng để tăng cường độ bám dính của lớp phủ, phun cát, màng hóa học, anodizing, thấm nitơ, sơn tĩnh điện, sơn phun, các kỹ thuật phủ và tráng kim loại tiên tiến khác nhau bao gồm phún xạ, tia điện tử, bay hơi, mạ, các lớp phủ cứng như kim cương như carbon (DLC) hoặc titan cho các dụng cụ cắt và khoan. • Đánh dấu và dán nhãn, khắc laser trên các bộ phận kim loại, in trên các bộ phận bằng nhựa và cao su Tải xuống tài liệu quảng cáo cho các Thuật ngữ Cơ khí Phổ biến được các Nhà thiết kế và Kỹ sư sử dụng Chúng tôi xây dựng các sản phẩm theo thông số kỹ thuật và yêu cầu cụ thể của bạn. Để cung cấp cho bạn chất lượng, giao hàng và giá cả tốt nhất, chúng tôi sản xuất sản phẩm trên toàn cầu tại Trung Quốc, Ấn Độ, Đài Loan, Philippines, Hàn Quốc, Malaysia, Sri Lanka, Thổ Nhĩ Kỳ, Mỹ, Canada, Đức, Anh và Nhật Bản. Điều này làm cho chúng tôi mạnh mẽ hơn và cạnh tranh toàn cầu hơn nhiều so với bất kỳ tùy chỉnh nào khác manosystem. Sản phẩm của chúng tôi được sản xuất trong môi trường được chứng nhận ISO9001: 2000, QS9000, ISO14001, TS16949 và có dấu CE, UL và đáp ứng các tiêu chuẩn công nghiệp khác. Khi chúng tôi được chỉ định cho dự án của bạn, chúng tôi có thể đảm nhận toàn bộ quá trình sản xuất, lắp ráp, thử nghiệm, kiểm tra chất lượng, vận chuyển và hải quan như bạn muốn. Nếu bạn thích, chúng tôi có thể nhập kho các bộ phận của bạn, lắp ráp các bộ dụng cụ tùy chỉnh, in và dán nhãn tên công ty và thương hiệu của bạn và giao hàng cho khách hàng của bạn. Nói cách khác, chúng tôi cũng có thể là trung tâm lưu kho và phân phối của bạn nếu được ưu tiên. Vì các kho hàng của chúng tôi nằm gần các cảng biển lớn, điều này mang lại cho chúng tôi lợi thế về mặt hậu cần. Ví dụ: khi sản phẩm của bạn đến một cảng biển lớn của Hoa Kỳ, chúng tôi có thể transport trực tiếp đến một nhà kho gần đó, nơi chúng tôi có thể lưu trữ, lắp ráp, sản xuất bộ dụng cụ, dán nhãn lại, in, đóng gói theo lựa chọn của bạn và thả giao hàng cho khách hàng của bạn. Chúng tôi không chỉ cung cấp sản phẩm. Công ty của chúng tôi làm việc trên các hợp đồng tùy chỉnh khi chúng tôi đến trang web của bạn, đánh giá dự án của bạn trên trang web và phát triển một đề xuất dự án tùy chỉnh được thiết kế cho bạn. Sau đó, chúng tôi cử nhóm có kinh nghiệm của mình để thực hiện dự án. Thông tin thêm về công việc kỹ thuật của chúng tôi có thể được tìm thấy trên http://www.ags-engineering.com -Chúng tôi nhận các dự án nhỏ cũng như các dự án lớn ở quy mô công nghiệp. Bước đầu tiên, chúng tôi có thể kết nối bạn qua điện thoại, hội nghị từ xa hoặc MSN messenger với các thành viên trong nhóm chuyên gia của chúng tôi, vì vậy bạn có thể liên lạc trực tiếp với chuyên gia, đặt câu hỏi và thảo luận về dự án của mình. Hãy gọi cho chúng tôi và nếu cần chúng tôi sẽ đến thăm bạn. TRANG TRƯỚC