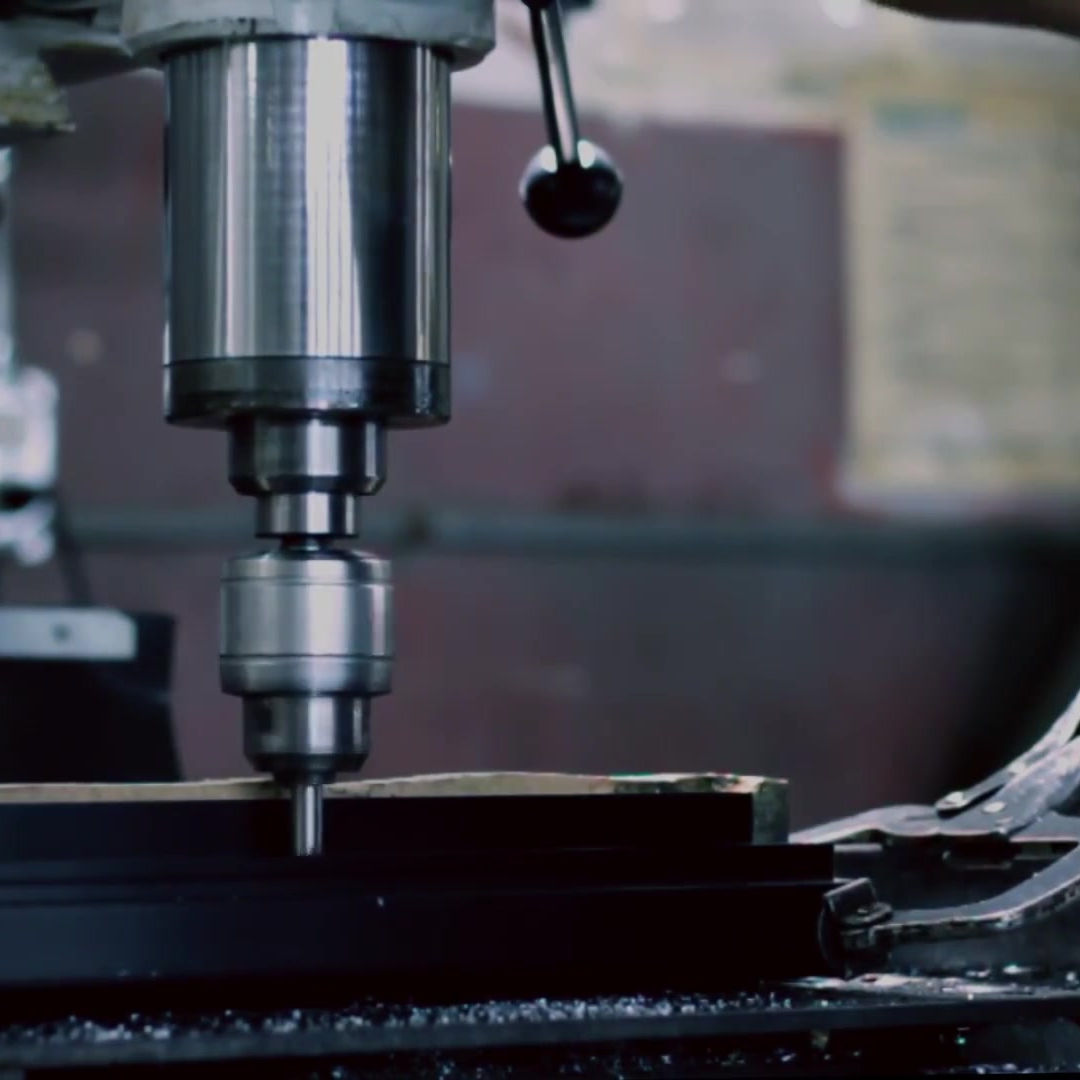
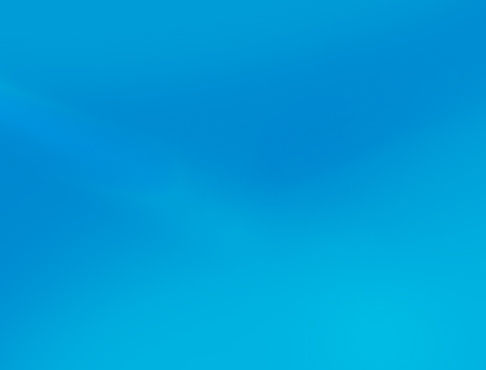
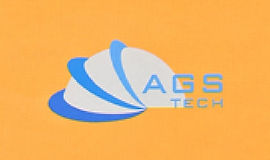
全球定制制造商、集成商、整合商、各种产品和服务的外包合作伙伴。
我们是您定制制造和现成产品和服务的制造、制造、工程、整合、集成、外包的一站式来源。
Choose your Language
-
定制制造
-
国内和全球合同制造
-
制造外包
-
国内及全球采购
-
Consolidation
-
工程集成
-
工程服务
ELECTRICAL DISCHARGE MACHINING (EDM), also referred to as SPARK-EROSION or ELECTRODISCHARGE MACHINING, SPARK ERODING, DIE SINKING_cc781905-5cde-3194-bb3b -136bad5cf58d_or WIRE EROSION, is a NON-CONVENTIONAL MANUFACTURING process where erosion of metals takes place and desired shape is obtained using electrical discharges in the form的火花。我们还提供电火花加工的一些品种,即 NO-WEAR EDM, WIRE EDM (WEDM), EDM GRINDING (EDG), DIE-SINKING EDM, ELECTRICAL-DISCHARGE MILLING, micro-EDM, m-EDM_cc781905 -5cde-3194-bb3b-136bad5cf58d_and 电化学放电研磨 (ECDG)。我们的 EDM 系统由成型工具/电极和连接到直流电源并插入不导电介电流体中的工件组成。 1940年后,电火花加工已成为制造业中最重要、最流行的生产技术之一。
当两个电极之间的距离减小时,电极之间的体积中的电场强度在某些点变得大于电介质的强度,电介质发生断裂,最终形成了电流在两个电极之间流动的桥。产生强烈的电弧,导致显着加热以熔化一部分工件和一些工具材料。结果,从两个电极上去除了材料。同时,介电流体被快速加热,导致电弧间隙中的流体蒸发。一旦电流停止或停止,热量就会被周围的介电流体从气泡中带走,气泡就会空化(塌陷)。由气泡破裂产生的冲击波和介电流体的流动将碎屑从工件表面冲走,并将任何熔化的工件材料带入介电流体中。这些放电的重复频率在 50 到 500 kHz 之间,电压在 50 到 380 V 之间,电流在 0.1 到 500 安培之间。新的液体电介质如矿物油、煤油或蒸馏水和去离子水通常被输送到电极间体积中,带走固体颗粒(以碎屑的形式)并恢复电介质的绝缘特性。电流通过后,两个电极之间的电位差恢复到击穿前的水平,因此会发生新的液体介质击穿。我们的现代放电加工机 (EDM) 提供数控运动,并配备了用于介电流体的泵和过滤系统。
电火花加工 (EDM) 是一种主要用于硬质金属或传统技术难以加工的加工方法。 EDM 通常适用于任何作为电导体的材料,尽管也有人提出了用 EDM 加工绝缘陶瓷的方法。熔点和熔化潜热是决定每次放电去除的金属体积的属性。这些值越高,材料去除率越慢。由于电火花加工过程不涉及任何机械能,工件的硬度、强度和韧性不影响去除率。放电频率或每次放电的能量、电压和电流变化以控制材料去除率。材料去除率和表面粗糙度随着电流密度的增加和火花频率的降低而增加。我们可以使用 EDM 在预硬化钢中切割复杂的轮廓或空腔,而无需进行热处理以软化和重新硬化它们。我们可以将此方法用于任何金属或金属合金,例如钛、哈氏合金、可伐合金和铬镍铁合金。 EDM 工艺的应用包括多晶金刚石工具的成型。 EDM与电化学加工(ECM)、水射流切割(WJ、AWJ)、激光切割等工艺一起被认为是一种非传统或非传统的加工方法。另一方面,传统的加工方法包括车削、铣削、磨削、钻孔等工艺,其材料去除机制主要基于机械力。用于放电加工 (EDM) 的电极由石墨、黄铜、铜和铜钨合金制成。电极直径小至 0.1 毫米是可能的。由于刀具磨损是一种不希望出现的现象,会对 EDM 中的尺寸精度产生不利影响,因此我们利用称为 NO-WEAR EDM 的工艺,通过反转极性和使用铜刀具来最大限度地减少刀具磨损。
理想情况下,放电加工(EDM)可以被认为是电极之间介电液体的一系列击穿和恢复。然而实际上,从电极间区域去除碎片几乎总是部分的。这导致电极间区域中电介质的电气特性与其标称值不同,并随时间变化。电极间距离(火花间隙)由所使用的特定机器的控制算法进行调整。不幸的是,EDM 中的火花隙有时会被碎屑短路。电极的控制系统可能无法迅速做出反应以防止两个电极(工具和工件)短路。这种不希望的短路对材料去除的贡献与理想情况不同。我们非常重视冲洗动作,以恢复电介质的绝缘特性,使电流始终发生在电极间区域的点,从而最大限度地减少工具电极形状(损坏)的不必要变化的可能性和工件。为了获得特定的几何形状,EDM 工具沿着所需的路径引导,非常靠近工件而不接触工件,我们非常注意使用中运动控制的性能。这样,就会发生大量电流放电/火花,每一次都有助于从工具和工件上去除材料,从而形成小坑。陨石坑的大小是为手头的特定工作设置的技术参数的函数,尺寸范围可以从纳米级(例如在微型 EDM 操作的情况下)到粗加工条件下的数百微米。工具上的这些小陨石坑会导致电极逐渐腐蚀,称为“工具磨损”。为了抵消磨损对工件几何形状的不利影响,我们在加工操作期间不断更换工具电极。有时我们通过使用连续更换的导线作为电极来实现这一点(这种 EDM 工艺也称为 WIRE EDM )。有时我们使用工具电极的方式是只有一小部分实际参与加工过程,并且这部分会定期更换。例如,当使用旋转盘作为工具电极时就是这种情况。这个过程称为 EDM GRINDING。我们部署的另一种技术包括在同一 EDM 操作期间使用一组具有不同尺寸和形状的电极来补偿磨损。我们称之为多电极技术,最常用于工具电极以负向复制所需形状并沿单个方向(通常是垂直方向(即 z 轴))向坯料前进时使用。这类似于工具沉入其中浸入工件的介电液体中,因此称为 DIE-SINKING EDM (有时称为_cc781905-5cde- 3194-bb3b-136bad5cf58d_CONVENTIONAL EDM or RAM EDM)。此操作的机器称为 SINKER EDM。这种类型的 EDM 的电极具有复杂的形式。如果使用通常形状简单的电极沿多个方向移动并进行旋转获得最终几何形状,我们将其称为 EDM MILLING。磨损量严格取决于操作中使用的技术参数(极性、最大电流、开路电压)。例如,in micro-EDM,也称为 m-EDM,这些参数通常设置为产生严重磨损的值。因此,磨损是该领域的一个主要问题,我们利用我们积累的专业知识将其最小化。例如,为了最大限度地减少对石墨电极的磨损,可在毫秒内控制的数字发生器会在发生电腐蚀时反转极性。这会产生类似于电镀的效果,将腐蚀的石墨连续沉积回电极上。在另一种方法中,即所谓的“零磨损”电路,我们将放电开始和停止的频率降至最低,使其保持尽可能长的时间。放电加工中的材料去除率可以通过以下方式估算:
MRR = 4 x 10 exp(4) x I x Tw exp (-1.23)
这里 MRR 以 mm3/min 为单位,I 是以安培为单位的电流,Tw 是以 K-273.15K 为单位的工件熔点。 exp 代表指数。
另一方面,电极的磨损率 Wt 可由下式获得:
Wt = ( 1.1 x 10exp(11) ) x I x Ttexp(-2.38)
这里 Wt 的单位是 mm3/min,Tt 是电极材料的熔点,单位为 K-273.15K
最后,工件与电极 R 的磨损比可由下式获得:
R = 2.25 x Trexp(-2.38)
此处 Tr 是工件与电极的熔点之比。
SINKER EDM :
Sinker EDM,也称为 CAVITY TYPE EDM or VOLUME EDM,由电极和工件组成,浸没在绝缘液体中。电极和工件连接到电源。电源在两者之间产生电位。随着电极接近工件,流体中发生介电击穿,形成等离子体通道,并产生小火花跳跃。火花通常一次触发一个,因为电极间空间中的不同位置极不可能具有相同的局部电特性,这将使火花同时在所有这些位置发生。每秒在电极和工件之间的随机点发生数十万个这样的火花。随着基底金属的腐蚀,火花间隙随之增加,我们的 CNC 机床会自动降低电极,以便工艺可以不间断地继续进行。我们的设备具有控制周期,称为“准时”和“关时间”。开启时间设置决定了火花的长度或持续时间。更长的时间会为该火花和该循环的所有后续火花产生更深的空腔,从而在工件上产生更粗糙的光洁度,反之亦然。关闭时间是一个火花被另一个火花替代的时间段。较长的关闭时间允许介电流体通过喷嘴冲洗以清除被侵蚀的碎屑,从而避免短路。这些设置在微秒内调整。
电线 EDM :
In WIRE ELECTRICAL DISCHARGE MACHINING (WEDM), also called WIRE-CUT EDM or WIRE CUTTING, we feed a黄铜的细单股金属线穿过工件,工件浸没在介电流体中。电火花线切割是电火花加工的一个重要变体。我们偶尔会使用线切割 EDM 切割 300 毫米厚的板材,并使用其他制造方法难以加工的硬质金属制造冲头、工具和模具。在这个类似于使用带锯进行轮廓切割的过程中,不断从线轴送入的线材被固定在上下金刚石导轨之间。 CNC 控制的导轨在 x-y 平面上移动,上导轨也可以在 z-u-v 轴上独立移动,从而可以切割锥形和过渡形状(例如底部的圆形和底部的方形)顶端)。上导轨可以控制 x–y–u–v–i–j–k–l– 的轴运动。这允许 WEDM 切割非常复杂和精致的形状。使用 Ø 0.25 黄铜、铜或钨丝,我们的设备实现最佳经济成本和加工时间的平均切割切口为 0.335 毫米。然而,我们的 CNC 设备的上下金刚石导轨精确到大约 0.004 毫米,并且使用 Ø 0.02 毫米线材可以具有小至 0.021 毫米的切割路径或切口。所以非常窄的削减是可能的。切割宽度大于线材宽度,因为从线材侧面到工件会产生火花,造成腐蚀。这种“过切”是必要的,对于许多应用来说,它是可预测的,因此可以进行补偿(在微型 EDM 中,这种情况并不常见)。线轴很长——一个 8 公斤的 0.25 毫米线轴的长度刚刚超过 19 公里。线径可小至 20 微米,几何精度约为 +/- 1 微米。我们通常只使用一次电线并回收它,因为它相对便宜。它以 0.15 到 9m/min 的恒定速度行进,并且在切割过程中保持恒定的切口(槽)。在电火花线切割工艺中,我们使用水作为介电流体,通过过滤器和去离子装置控制其电阻率和其他电气特性。水将切割碎屑冲离切割区域。冲洗是确定给定材料厚度的最大进给率的重要因素,因此我们保持一致。线切割 EDM 中的切割速度以每单位时间切割的横截面积表示,例如 18,000 mm2/hr 用于 50mm 厚的 D2 工具钢。这种情况下的线性切削速度为 18,000/50 = 360mm/hr 线切割加工中的材料去除率是:
MRR = Vf xhxb
这里 MRR 的单位是 mm3/min,Vf 是线材进入工件的进给速度,单位是 mm/min,h 是厚度或高度,单位是 mm,b 是切缝,即:
b = dw + 2s
其中 dw 为线材直径,s 为线材与工件之间的间隙,单位为 mm。
除了更严格的公差外,我们的现代多轴 EDM 线切割加工中心还增加了一些功能,例如用于同时切割两个零件的多头、防止断线的控制、断线时的自动自攻丝功能以及编程加工策略以优化操作、直线和角切削能力。
Wire-EDM 为我们提供了低残余应力,因为它不需要高切削力来去除材料。当每个脉冲的能量/功率相对较低时(如在精加工操作中),由于残余应力低,预计材料的机械性能几乎不会发生变化。
放电磨削 (EDG) :砂轮不含磨料,它们由石墨或黄铜制成。旋转轮和工件之间的重复火花从工件表面去除材料。材料去除率是:
MRR = K x I
这里 MRR 的单位是 mm3/min,I 是电流,单位是安培,K 是工件材料系数,单位是 mm3/A-min。我们经常使用放电磨削来锯出组件上的窄缝。我们有时将 EDG(放电研磨)工艺与 ECG(电化学研磨)工艺相结合,通过化学作用去除材料,石墨轮的放电会破坏氧化膜并被电解质冲走。该过程称为 ELECTROCHEMICAL-DISCHARGE GRINDING (ECDG)。尽管 ECDG 过程消耗的功率相对较多,但它比 EDG 更快。我们主要使用这种技术磨削硬质合金工具。
电火花加工的应用:
原型制作:
我们在模具制造、工具和模具制造以及原型和生产零件的制造中使用 EDM 工艺,特别是在产量相对较低的航空航天、汽车和电子行业。在 Sinker EDM 中,石墨、铜钨或纯铜电极被加工成所需的(负)形状,并在垂直冲头的末端送入工件。
铸币模具制作:
对于通过铸币(冲压)工艺制造用于生产珠宝和徽章的模具,正面母版可以由纯银制成,因为(通过适当的机器设置)母版被严重腐蚀并且仅使用一次。然后将得到的阴模硬化并在落锤中使用,以从青铜、银或低强度金合金的切割板坯中生产冲压平面。对于徽章,这些平面可以通过另一个模具进一步成型为曲面。这种类型的 EDM 通常在浸没在油基电介质中进行。成品可以通过硬(玻璃)或软(油漆)搪瓷和/或电镀纯金或镍进一步精制。较软的材料(例如银)可以手工雕刻以作为改进。
小孔钻孔:
在我们的线切割 EDM 机器上,我们使用小孔钻孔 EDM 在工件上制造一个通孔,通过该孔将线穿过以进行线切割 EDM 操作。我们的线切割机床上安装了专门用于小孔钻孔的单独 EDM 头,这使得大型硬化板可以根据需要从其上腐蚀出成品零件,而无需进行预钻孔。我们还使用小孔 EDM 在喷气发动机中使用的涡轮叶片边缘钻出成排的孔。通过这些小孔的气流允许发动机使用比其他方式更高的温度。这些刀片是由高温、非常坚硬的单晶合金制成的,因此对这些具有高纵横比的孔进行常规加工极其困难,甚至是不可能的。小孔 EDM 的其他应用领域是为燃料系统组件创建微观孔口。除了集成的 EDM 头外,我们还部署了带有 x-y 轴的独立小孔钻孔 EDM 机床来加工盲孔或通孔。 EDM 使用长黄铜或铜管电极钻孔,该电极在卡盘中旋转,蒸馏水或去离子水作为冲洗剂和电介质流过电极。一些小孔钻孔电火花加工机能够在不到 10 秒的时间内钻穿 100 毫米的软钢甚至硬化钢。在这种钻孔操作中可以实现 0.3 毫米和 6.1 毫米之间的孔。
金属解体加工:
我们也有特殊的 EDM 机器,用于从工件上去除损坏的工具(钻头或丝锥)。这个过程被称为“金属分解加工”。
电火花加工的优缺点:
EDM 的优点包括:
- 使用传统切削工具难以生产的复杂形状
- 极其坚硬的材料,公差非常小
- 非常小的工件,传统切削工具可能会因切削工具压力过大而损坏零件。
- 工具和工件之间没有直接接触。因此,可以加工精细的部分和脆弱的材料而不会产生任何变形。
- 可以获得良好的表面光洁度。
- 可以轻松钻出非常细的孔。
EDM的缺点包括:
- 材料去除速度慢。
- 用于为冲压/沉降 EDM 创建电极的额外时间和成本。
- 由于电极磨损,难以再现工件上的尖角。
- 功耗很高。
- ''过切'' 形成。
- 加工过程中出现过度的刀具磨损。
- 非导电材料只能通过特定的工艺设置进行加工。